氰化钠生产工艺
轻油裂解法生产氰化钠的危险性分析

轻油裂解法生产氰化钠的危险性分析氰化钠属剧毒危险化学品,主要用于冶金、电镀、医药及一些精细化工生产。
轻油裂解法生产氰化钠是我国研究开发的生产工艺,为目前国内部分中小企业所采用。
由于该生产工艺中采用的原料、中间产品和最终产品多为易燃易爆或剧毒有害物质,生产操作中潜在的危险性较大,加之有些中小企业资金短缺,设备简陋,人员素质低下,事故隐患很多。
因此,有必要对其安全性进行深入分析,采取有效措施控制和减少事故发生。
一、生产工艺简介轻油裂解法生产氰化钠工艺流,主要原料为轻油(或汽油)、液氨和烧碱。
产品为液体氰化钠(简称液氰)、固体氰化钠(简称固氰)。
生产过程主要分为三个阶段:氰化氢气体的制备与净化、液氰制备、固氰制备。
1.氰化氢气体的制备与净化液氨经汽化器汽化后与汽油在文丘里管中混合,然后通过预热器加热到250℃~280℃进入裂解炉底部。
炉内三相石墨电极浸入石油焦粒沸腾床层中,由于大电流导电发热作用,原料气在1450℃高温、微负压条件下发生裂解反应: CnH2n+n+nNH3→nNCN+(2n+1)H22NH3→N2+3H2CnH2n+2→nC+(n+1)H2生成以氰化氢、氢气为主并含有少量氮气和炭粉的裂解物,经换热冷却及旋风、布袋除尘器先后脱除炭粉,得到纯净裂解炉气。
2.液氰制备纯净裂解炉气通入中和罐,与其中的液体氢氧化钠发生中和反应:HCN+NaOH→NaCH+H2O生成液氰。
未反应的气体进入尾气吸收罐用液碱进一步吸收后,通过真空泵排至烟囱。
尾气的主要成分是氢气。
3.固氰制备液氰被送入节发器中,在负压条件下加热蒸发,蒸出的水蒸气用水冷凝,不凝气用真空泵抽送至烟囱。
经蒸发浓缩后的母液进入结晶器,用水冷却降温,固液混合物排放到离心机中进行固液分离,固体产品称重装桶。
为进一步减少固氰含水量,有的厂家在离心分离后增加一道烘干除水工序。
二、生产过程的危险性分析1.火灾爆炸危险性生产中火灾爆炸危险性大且数量钦的物料主要有汽油、氨、氢气、氰化氢。
轻油裂解法生产氰化钠的危险性分析及管理措施

编号:AQ-JS-02225( 安全技术)单位:_____________________审批:_____________________日期:_____________________WORD文档/ A4打印/ 可编辑轻油裂解法生产氰化钠的危险性分析及管理措施Risk analysis and management measures of sodium cyanide production by light oil cracking轻油裂解法生产氰化钠的危险性分析及管理措施使用备注:技术安全主要是通过对技术和安全本质性的再认识以提高对技术和安全的理解,进而形成更加科学的技术安全观,并在新技术安全观指引下改进安全技术和安全措施,最终达到提高安全性的目的。
引言(1)氰化钠属剧毒危险化学品,主要用于冶金、电镀、医药及一些精细化工生产。
轻油裂解法生产氰化钠是我国研究开发的生产工艺,为目前国内部分中小企业所采用。
由于该生产工艺中采用的原料、中间产品和最终产品多为易燃易爆或剧毒有害物质,生产操作中潜在的危险性较大,加之有些中小企业资金短缺,设备简陋,人员素质低下,事故隐患很多。
因此,有必要对其安全性进行深入分析,采取有效措施控制和减少事故发生。
生产工艺简介(2)轻油裂解法生产氰化钠工艺流程见图1。
主要原料为轻油(或汽油)、液氨和烧碱。
产品为液体氰化钠(简称液氰)、固体氰化钠(简称固氰)。
生产过程主要分为三个阶段:氰化氢气体的制备与净化、液氰制备、固氰制备。
图1轻油裂解法生产氰化钠工艺流程简图1.氰化氢气体的制备与净化液氨经汽化器汽化后与汽油在文丘里管中混合,然后通过预热器加热到250℃~280℃进入裂解炉底部。
炉内三相石墨电极浸入石油焦粒沸腾床层中,由于大电流导电发热作用,原料气在1450℃高温、微负压条件下发生裂解反应:CnH2n+n+nNH3→nNCN+(2n+1)H22NH3→N2+3H2CnH2n+2→nC+(n+1)H2生成以氰化氢、氢气为主并含有少量氮气和炭粉的裂解物,经换热冷却及旋风、布袋除尘器先后脱除炭粉,得到纯净裂解炉气。
氰化钠生产工艺
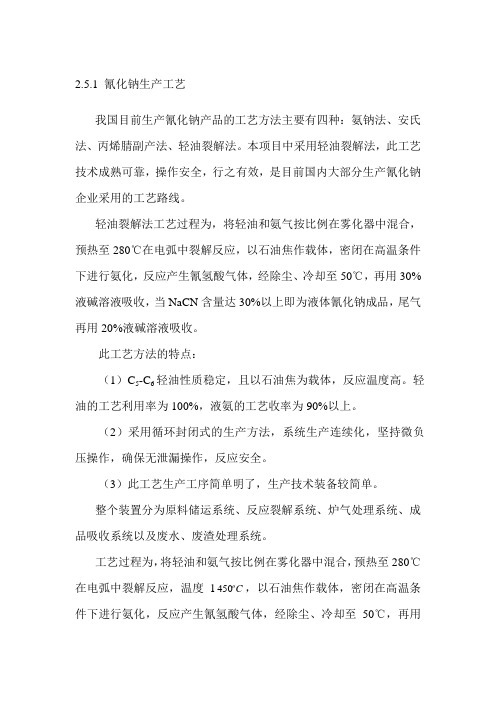
2.5.1 氰化钠生产工艺我国目前生产氰化钠产品的工艺方法主要有四种:氨钠法、安氏法、丙烯腈副产法、轻油裂解法。
本项目中采用轻油裂解法,此工艺技术成熟可靠,操作安全,行之有效,是目前国内大部分生产氰化钠企业采用的工艺路线。
轻油裂解法工艺过程为,将轻油和氨气按比例在雾化器中混合,预热至280℃在电弧中裂解反应,以石油焦作载体,密闭在高温条件下进行氨化,反应产生氰氢酸气体,经除尘、冷却至50℃,再用30%液碱溶液吸收,当NaCN含量达30%以上即为液体氰化钠成品,尾气再用20%液碱溶液吸收。
此工艺方法的特点:(1)C5-C6轻油性质稳定,且以石油焦为载体,反应温度高。
轻油的工艺利用率为100%,液氨的工艺收率为90%以上。
(2)采用循环封闭式的生产方法,系统生产连续化,坚持微负压操作,确保无泄漏操作,反应安全。
(3)此工艺生产工序简单明了,生产技术装备较简单。
整个装置分为原料储运系统、反应裂解系统、炉气处理系统、成品吸收系统以及废水、废渣处理系统。
工艺过程为,将轻油和氨气按比例在雾化器中混合,预热至280℃在电弧中裂解反应,温度1C o450,以石油焦作载体,密闭在高温条件下进行氨化,反应产生氰氢酸气体,经除尘、冷却至50℃,再用30%液碱溶液吸收,当NaCN 含量达30%以上即为液体氰化钠成品,尾气再用20%液碱溶液吸收。
其主要反应方程式如下:C 5H 12+5NH 3电弧C o14505HCN+11H 2-243.3千卡HCN + NaOHNaCN+H 2O 工艺流程示意图如图3-1所示:图3-1 工艺流程示意图2.5.2 主要设备及布置主要设备见表2-3:表2-3主要设备一览表3.l 危险化学品物料的危险、有害性分析3.1.1 危险化学品识别XXXXXXXXX公司生产氰化钠(30%液体)产品中,使用的原料列入国家安全生产监督管理局2003年第1号公告《危险化学品名录》的有: 氰化钠、氰化氢、氢气、氢氧化钠、液氨等6种。
氰化钠生产工艺

2.5.1 氰化钠生产工艺我国目前生产氰化钠产品的工艺方法主要有四种:氨钠法、安氏法、丙烯腈副产法、轻油裂解法。
本项目中采用轻油裂解法,此工艺技术成熟可靠,操作安全,行之有效,是目前国内大部分生产氰化钠企业采用的工艺路线。
轻油裂解法工艺过程为,将轻油和氨气按比例在雾化器中混合,预热至280℃在电弧中裂解反应,以石油焦作载体,密闭在高温条件下进行氨化,反应产生氰氢酸气体,经除尘、冷却至50℃,再用30%液碱溶液吸收,当NaCN含量达30%以上即为液体氰化钠成品,尾气再用20%液碱溶液吸收。
此工艺方法的特点:(1)C5-C6轻油性质稳定,且以石油焦为载体,反应温度高。
轻油的工艺利用率为100%,液氨的工艺收率为90%以上。
(2)采用循环封闭式的生产方法,系统生产连续化,坚持微负压操作,确保无泄漏操作,反应安全。
(3)此工艺生产工序简单明了,生产技术装备较简单。
整个装置分为原料储运系统、反应裂解系统、炉气处理系统、成品吸收系统以及废水、废渣处理系统。
工艺过程为,将轻油和氨气按比例在雾化器中混合,预热至280℃在电弧中裂解反应,温度1C o450,以石油焦作载体,密闭在高温条件下进行氨化,反应产生氰氢酸气体,经除尘、冷却至50℃,再用30%液碱溶液吸收,当NaCN 含量达30%以上即为液体氰化钠成品,尾气再用20%液碱溶液吸收。
其主要反应方程式如下:C 5H 12+5NH 3电弧C o14505HCN+11H 2-243.3千卡HCN + NaOHNaCN+H 2O 工艺流程示意图如图3-1所示:图3-1 工艺流程示意图2.5.2 主要设备及布置主要设备见表2-3:表2-3主要设备一览表3.l 危险化学品物料的危险、有害性分析3.1.1 危险化学品识别XXXXXXXXX公司生产氰化钠(30%液体)产品中,使用的原料列入国家安全生产监督管理局2003年第1号公告《危险化学品名录》的有: 氰化钠、氰化氢、氢气、氢氧化钠、液氨等6种。
氰化钠生产工艺设计
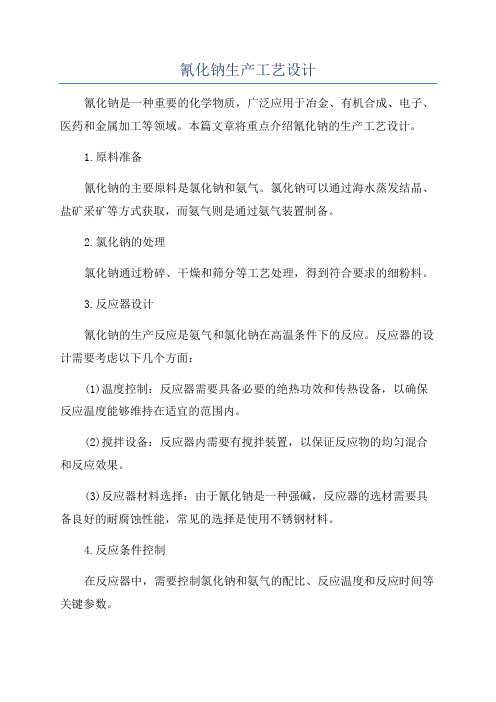
氰化钠生产工艺设计氰化钠是一种重要的化学物质,广泛应用于冶金、有机合成、电子、医药和金属加工等领域。
本篇文章将重点介绍氰化钠的生产工艺设计。
1.原料准备氰化钠的主要原料是氯化钠和氨气。
氯化钠可以通过海水蒸发结晶、盐矿采矿等方式获取,而氨气则是通过氨气装置制备。
2.氯化钠的处理氯化钠通过粉碎、干燥和筛分等工艺处理,得到符合要求的细粉料。
3.反应器设计氰化钠的生产反应是氨气和氯化钠在高温条件下的反应。
反应器的设计需要考虑以下几个方面:(1)温度控制:反应器需要具备必要的绝热功效和传热设备,以确保反应温度能够维持在适宜的范围内。
(2)搅拌设备:反应器内需要有搅拌装置,以保证反应物的均匀混合和反应效果。
(3)反应器材料选择:由于氰化钠是一种强碱,反应器的选材需要具备良好的耐腐蚀性能,常见的选择是使用不锈钢材料。
4.反应条件控制在反应器中,需要控制氯化钠和氨气的配比、反应温度和反应时间等关键参数。
(1)配比控制:氯化钠和氨气的配比对于氰化钠的产率和纯度有着重要的影响,需要通过实验和调整来确定最佳的配比。
(2)温度控制:反应温度的选择要考虑到反应速率和选择率,一般在300-400°C之间。
(3)反应时间控制:反应时间的长短也会对氰化钠的产率和纯度产生影响,需要通过实验和控制来确定最佳的反应时间。
5.反应产物处理反应结束后,需要对反应产物进行处理,包括过滤、洗涤和结晶等步骤,以得到高纯度的氰化钠产品。
6.尾气处理在氰化钠的生产过程中,会产生大量的尾气,其中包含了含氯化物和氨气的废气。
这些废气需要进行处理,以防止对环境造成污染。
(1)氯化物回收:废气中的氯化物可以通过干湿法、吸收等方式进行回收,以减少对环境的影响。
(2)氨气回收:废气中的氨气可以通过吸收、蓄热和净化等工艺进行回收,以提高资源利用率。
7.安全措施在氰化钠生产过程中,由于氨气和氰化钠的性质,需要采取一系列的安全措施,包括压力监控、泄漏报警、装置防腐蚀等,以确保生产过程的安全可靠。
我国氰化钠生产现状及未来发展

我国氰化钠生产现状及未来发展作者:无出处:无加入时间:2008-3-14 17:54:17点击数:566次氰化钠是一种重要的化工原料,被广泛应用于冶金、矿山、农药、医药、电镀及有机会成中,作为淬火剂、络合剂及将氰基引入到化合物中。
我国自20世纪60年代开始生产液体氰化钠产品,1978年由上海石化引进日本生产专利技术,建成了第一套固体氰化钠生产装置,20世纪90年代以后随着丙烯睛生产装置的建设,我国氰化钠生产能力、产品质量和规格牌号等都得到了长足的发展。
目前,国内现有氰化钠生产企业10多家,总生产能力大于10万t/a(折纯100%)。
1 国内氰化钠生产工艺情况氰化钠产品是由氢氰酸和液体氢氧化钠反应而成的,目前国内合成氰化钠主要有3种方法。
1.1 安氏法以天然气、氨和空气为原料,在铂铑合金为催化剂,于1070~1120℃温度下,反应生成含2.5%~3.0%的混合气体,经冷却后进行氨吸收,再用低温水吸收氰化氢,然后经解吸塔解吸后,与液碱反应,生成氰化钠溶液,经蒸发、结晶、干燥、成型和包装成产品。
CH4+NH3→HCN+3H2 HCN+NaOH→NaCN+H2O1.2轻油裂解法将轻油和氨按比例在雾化器中混合,预热280℃,在电弧炉中裂解反应,温度1450℃时反应生成氰化氢气体,经除尘、冷却后,再与液碱吸收生成氰化钠。
C6H14+6NH3→6HCN+13H2 HCN+NaOH→NaCN+H2O1.3 丙烯腈副产法在丙烯氢氧化法制丙烯腈的过程中,副产氰化氢气体(其量相当于丙烯腈产量的4%~10%),经液碱吸收,再经蒸发、结晶、分离、干燥、成型和包装制得成品。
HCN+Na OH→NaCN+H2O 上述会成氰化钠的方法,前2种由于生成的氰化氢纯度较丙烯腈副产氰化氢纯度低,因此,丙烯腈副产法是合成高纯度氰化钠产品的最好方法。
2 我国氰化钠生产现状我国氰化钠生产始于1960年,当时主要靠吉化公司4500t 的氰熔体法生产来供应全国,产品供不应求,供需矛盾比较突出,由于市场销路好,各地上马了一批氨钠法和轻油裂解法生产装置,但产品都为液体,且质量较差。
轻油裂解法生产氰化钠工艺中裂解余热利用
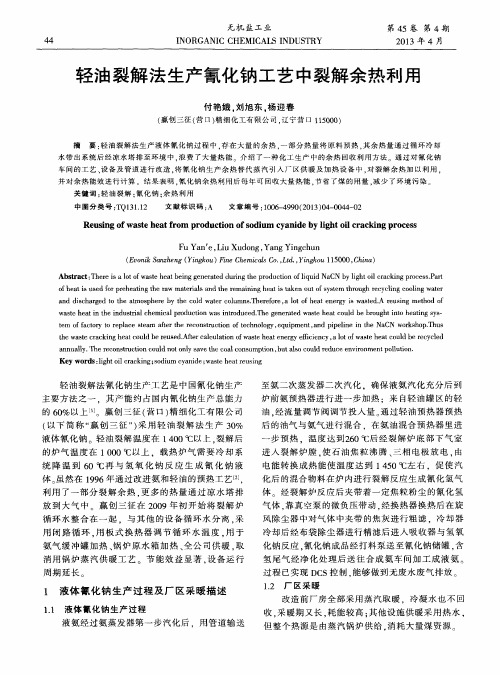
摘 要 : 轻 油 裂 解法 生 产 液 体 氰 化 钠 过 程 中 , 存在大量的余热 , 一部分热量将原料预热 , 其 余 热 量 通 过 循 环 冷 却
水 带 出系 统 后 经 凉水 塔 排 至 环 境 中 . 浪 费 了 大 量热 能 介 绍 了一 种 化 工生 产 中 的余 热 回 收 利用 方 法 。通 过 对 氰化 钠
中 图分 类 号 : T Q1 3 1 . 1 2
文 献标 识 码 : A
文章编号 : 1 0 0 6 — 4 9 9 0 ( 2 0 1 3 ) 0 4 — 0 0 4 4 — 0 2
Re u s i n g o f wa s t e h e a t f r o m p r o d u c t i o n o f s o d i u m c y a n i d e b y l i g h t o i l c r a c k i n g p r o c e s s
a n d d i s c h a r g e d t o t h e a t mo s p h e r e b y t h e c o l d wa t e r c o l u mn s . T h e r e f o r e , a l o t o f h e a t e n e r g y i s w a s t e d . A r e u s i n g me t h o d o f wa s t e h e a t i n t h e i n d u s t r i a l c h e mi c a l p r o d u c t i o n w a s i n t r o d u c e d . T h e g e n e r a t e d wa s t e h e a t c o u l d b e b r o u g h t i n t o h e a t i n g s y s —
氰化钠生产工艺设计
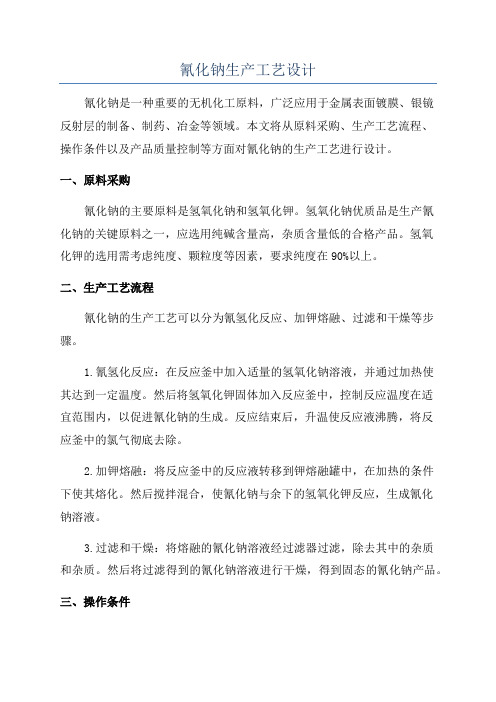
氰化钠生产工艺设计氰化钠是一种重要的无机化工原料,广泛应用于金属表面镀膜、银镜反射层的制备、制药、冶金等领域。
本文将从原料采购、生产工艺流程、操作条件以及产品质量控制等方面对氰化钠的生产工艺进行设计。
一、原料采购氰化钠的主要原料是氢氧化钠和氢氧化钾。
氢氧化钠优质品是生产氰化钠的关键原料之一,应选用纯碱含量高,杂质含量低的合格产品。
氢氧化钾的选用需考虑纯度、颗粒度等因素,要求纯度在90%以上。
二、生产工艺流程氰化钠的生产工艺可以分为氰氢化反应、加钾熔融、过滤和干燥等步骤。
1.氰氢化反应:在反应釜中加入适量的氢氧化钠溶液,并通过加热使其达到一定温度。
然后将氢氧化钾固体加入反应釜中,控制反应温度在适宜范围内,以促进氰化钠的生成。
反应结束后,升温使反应液沸腾,将反应釜中的氯气彻底去除。
2.加钾熔融:将反应釜中的反应液转移到钾熔融罐中,在加热的条件下使其熔化。
然后搅拌混合,使氰化钠与余下的氢氧化钾反应,生成氰化钠溶液。
3.过滤和干燥:将熔融的氰化钠溶液经过滤器过滤,除去其中的杂质和杂质。
然后将过滤得到的氰化钠溶液进行干燥,得到固态的氰化钠产品。
三、操作条件1.反应温度:氰化钠的生成是在一定温度下进行的,一般考虑到反应速度和产率的影响,反应温度可控制在100-200摄氏度之间。
2.混合速度:在加钾熔融的过程中,搅拌应均匀稳定,避免产生不均匀反应。
混合速度一般应控制在150-300转/分钟。
3.过滤条件:过滤时应选用合适的过滤介质和压力,以确保过滤效果良好,并有效去除杂质。
4.干燥条件:干燥时应掌握适当的温度和时间,以充分除去溶液中的水分,提高产品纯度。
四、产品质量控制对生产得到的氰化钠产品进行质量控制是非常重要的。
其中包括以下几个方面:1.纯度检验:通过抽样取样,使用化学分析方法进行检测,确保产品纯度符合要求。
2.杂质检测:检测氰化钠中的杂质含量,确保产品质量。
3.颗粒度检测:检测产品的颗粒度分布情况,确保产品达到所需的颗粒度要求。
氰化钠生产工艺范文

氰化钠生产工艺范文
到位
一、引言
氰化钠的生产工艺涉及到钠氧化、气体吸收、氰化、除铅、除湿等,
由于各种原料和添加剂的种类和比例,以及生产工艺的不同,可以生产出
不同性质的氰化钠。
氰化钠是一种具有危险性的化学物质,如果不慎接触,可能会对人体健康造成危害,因此,生产过程中必须慎重,及时监控参数,确保安全生产。
二、氰化钠生产情况介绍
1、原料准备
氰化钠是以钠氧化物(如钠及碳酸钠)为原料,配以甲醛、硫酸亚铁
等添加剂,使氧化钠在水中生成氰酸钠。
一般来说,原料的选择非常重要,因为原料的质量会直接影响产品质量。
2、气体吸收
吸收器是氰化钠生产工艺中一个重要的组成部分,它负责将氰化钠中
的气体吸收,以减少对环境的影响。
常用的气体吸收器有溶液吸收器、膜
式吸收器和填料吸收器等。
3、氰化
氰化涉及到使用氧化钠反应,将氧化钠反应为氰酸钠,将温度控制在
给定条件下,温度可以在60-85摄氏度之间,一般来说温度越高,产率越高。
4、除铅
除铅是氰化钠生产过程中的一个过程,其主要目的是去除氰化钠中的金属离子,如铅离子、铜离子、镁离子等,以避免对人体健康造成危害。
5、除湿。
固体氰化钠生产新工艺[发明专利]
![固体氰化钠生产新工艺[发明专利]](https://img.taocdn.com/s3/m/4e5f92579a6648d7c1c708a1284ac850ad020492.png)
〔19〕中华人民共和国专利局〔12〕发明专利申请公开说明书[11]公开号CN 1057819A〔43〕公开日1992年1月15日[21]申请号90103439.8[22]申请日90.7.6[71]申请人天津市华北氧气厂地址300220天津市陈塘庄工业区[72]发明人杜尧礼[74]专利代理机构天津市化学工业局专利代理事务所代理人安延伦[51]Int.CI 5C01C 3/10权利要求书 1 页 说明书 4 页 附图 1 页[54]发明名称固体氰化钠生产新工艺[57]摘要一种生产固体氰化钠的降低温度析出结晶固化工艺是将液体氰化钠降温结晶,经离心分离后得氰化钠的水合物(NaCN·2H 2O)晶体,分离出母液,将晶体在100℃至150℃,压力为0至-0.093MPa下干燥1至3分钟,再经造粒后用80℃至170℃空气直接加热30至60分钟,可获得氰化钠含量96%或更高纯度的粒状氰化钠成品。
该工艺连续生产,基本不产生含氰废水。
90103439.8权 利 要 求 书第1/1页 1、一种生产固体氰化钠工艺,其特征为该工艺是降低液体氰化钠的温度,析出氰化钠的水合物(NaCN.2H2O)结晶,再干燥固化的工艺。
其工艺流程由液体氰化钠降低温度析出结晶。
晶体与母液的离心分离、晶体的瞬间真空干燥、造粒、深度(二次)干燥几个工序组成。
2、如权利要求1所述的瞬间真空干燥工序,其特征为干燥温度由10 0℃至150℃,压力由0至-0.093M P a,停留时间为1至3分钟。
3、如权利要求1所述的深度(二次)干燥工序,其特征为干燥温度由80℃至170℃,停留时间为30至60分钟。
90103439.8说 明 书第1/4页固体氰化钠生产新工艺本发明涉及一种生产固体氰化钠的工艺。
目前国内外生产氰化钠均采用氰氢酸与液体烧碱中和制成液体氰化钠。
再经蒸发、结晶、离心分离。
干燥成型等工序制成固体氰化钠。
反应方程式:HCN+NaOH→NaCN+H2O从液体氰化钠制成固体氰化钠一般采用蒸发工艺。
氰化钠生产工艺

2.5.1 氰化钠生产工艺我国目前生产氰化钠产品的工艺方法主要有四种:氨钠法、安氏法、丙烯腈副产法、轻油裂解法。
本项目中采用轻油裂解法,此工艺技术成熟可靠,操作安全,行之有效,是目前国内大部分生产氰化钠企业采用的工艺路线。
轻油裂解法工艺过程为,将轻油和氨气按比例在雾化器中混合,预热至280℃在电弧中裂解反应,以石油焦作载体,密闭在高温条件下进行氨化,反应产生氰氢酸气体,经除尘、冷却至50℃,再用30%液碱溶液吸收,当NaCN含量达30%以上即为液体氰化钠成品,尾气再用20%液碱溶液吸收。
此工艺方法的特点:(1)C5-C6轻油性质稳定,且以石油焦为载体,反应温度高。
轻油的工艺利用率为100%,液氨的工艺收率为90%以上。
(2)采用循环封闭式的生产方法,系统生产连续化,坚持微负压操作,确保无泄漏操作,反应安全。
(3)此工艺生产工序简单明了,生产技术装备较简单。
整个装置分为原料储运系统、反应裂解系统、炉气处理系统、成品吸收系统以及废水、废渣处理系统。
工艺过程为,将轻油和氨气按比例在雾化器中混合,预热至280℃在电弧中裂解反应,温度1C o450,以石油焦作载体,密闭在高温条件下进行氨化,反应产生氰氢酸气体,经除尘、冷却至50℃,再用30%液碱溶液吸收,当NaCN 含量达30%以上即为液体氰化钠成品,尾气再用20%液碱溶液吸收。
其主要反应方程式如下:C 5H 12+5NH 3电弧C o14505HCN+11H 2-243.3千卡HCN + NaOHNaCN+H 2O 工艺流程示意图如图3-1所示:图3-1 工艺流程示意图2.5.2 主要设备及布置主要设备见表2-3:表2-3主要设备一览表3.l 危险化学品物料的危险、有害性分析3.1.1 危险化学品识别XXXXXXXXX公司生产氰化钠(30%液体)产品中,使用的原料列入国家安全生产监督管理局2003年第1号公告《危险化学品名录》的有: 氰化钠、氰化氢、氢气、氢氧化钠、液氨等6种。
氰化钠生产工艺设计

氰化钠生产工艺设计
需要有总体概述,原料及设备准备,生产过程,质量控制方面的内容一、总体概述
氰化钠是以氯化钠和过氧化氢的反应而得到的,是最常用的除去水中钠离子的药剂。
氰化钠也是紫外光检测中最重要的试剂,广泛应用于各个领域。
本文描述的是一种新的氰化钠生产工艺,以氯化钠和过氧化氢为原料,在确保生产安全的前提下,进行可控化学反应,以符合不同客户要求的技术标准,生产出所需要的氰化钠产品。
二、原料及设备准备
1、原料:氯化钠和过氧化氢。
2、设备:溶剂罐,反应罐,冷却罐,烘干罐,冷凝罐,储存罐,离心机,搅拌机,真空泵,流量计,电磁阀,传感器,液位计,加热丝分切机,控制柜等。
三、生产过程
1、把一定量的氯化钠精细粉末倒入溶剂罐,加入合适的溶剂,搅拌溶解,并加入抗凝剂。
2、将溶解液注入反应罐中,加入适量的过氧化氢,启动搅拌机,按照预定的反应条件进行反应,并通过温度和浓度的控制实现反应的完全吸收。
3、将反应罐的液体放到冷却罐中,用液位计监控液位,冷却后进行离心分离。
氰化钠安全生产要点

氰化钠安全生产要点1工艺简述以丙烯腈生产的副产物氢氰酸(含HCN大于99.6%)与浓度为45%的氢氧化钠溶液,在反应器中于温度50~55℃条件下,进行液相中和反应,迅速生成氰化钠。
氰化钠溶液经蒸发、结晶、离心脱水、干燥、成型压片、包装即为含水量小于0.2%的氰化钠产品。
防毒是本装置安全生产的主要特点。
原料氢氰和产品氰化钠均系剧毒物质,该装置属有毒、有害生产。
氢氰酸还属一级易燃液体。
2重点部位 2.1氰化钠反应器该反应器是本装置的关键设备。
危险因素较多,进出反应器的物料均为剧毒品,且反应前有易燃性质。
生产控制条件要求比较苛刻,稍有失误即可产生不良后果,甚至发生事故。
如液体氢氰酸在碱性条件下会很快发生自聚反应,不仅放出大量的热量导致反应温度、压力的突然升高,而且生成棕色的粘稠液体使生产无法进行下去,严重时也可造成管道堵塞或设备爆炸事故;氰化钠在60℃以上的温度下很容易水解,在反应过程中稍不注意即可突破,由此造成操作紊乱状态,处理过程不仅麻烦且很危险。
3安全要点 3.1氰化钠反应器 3.1.1由于氢氰酸的沸点较低、毒性极大,且易燃、易爆,所以对装置投料前的系统气密性试验要严格认真地进行检查。
所有涉及氢氰酸的设备和管道上的密封点,均不允许有渗漏现象。
生产中要经常巡检,发现有泄漏时,应立即切断物料来源或做停车处理。
不准在有泄漏的情况下生产,防止中毒或爆炸着火。
3.1.2氰化钠反应器的生产操作,要按控制程序进行,经常检查是否有控制机构失灵等异常现象,发现异常应及时处理,避免反应热不能及时导出发生氢氰酸自聚或爆炸事故。
3.1.3氢氰酸和氰化钠的含水物对金属的腐蚀性很强,对镍、铜、金、银等耐腐蚀金属也有腐蚀作用,而且有的还能产生晶间腐蚀。
因此,应定期对该装置的设备、管道的腐蚀情况检测,进行必要的监督,防止由于腐蚀造成的设备泄漏损坏而出现严重事故。
3.2其它部位 3.2.1装置停车后要检查系统中的危险物料的排空置换情况,排出物料是否进行了安全处理,装置中不准存留剧毒物料,特别是装置停车检修时更要仔细的进行处理。
如何设计氰化钠项目可行性研究报告投资方案

如何设计氰化钠项目可行性研究报告投资方案氰化钠项目可行性研究报告一、项目背景及意义氰化钠是一种广泛应用于化工、冶金、电镀等行业的重要的化工原料,其市场需求量大且稳定。
本项目旨在建设一座氰化钠生产厂,以满足市场对氰化钠的需求并实现利润最大化。
二、技术工艺氰化钠的生产工艺一般包括焙烧法、碱石法和电解法。
鉴于电解法能够达到较高的纯度和产品质量,本项目选择了电解法作为主要生产工艺。
具体工艺流程如下:1.原料准备:将天然氯化钠经过精煮、脱水等工序处理,得到高纯度的氯化钠。
2.电解:将高纯度氯化钠溶液通过电解槽进行电解,产生氢氧化钠和氯气。
3.氢氧化钠浓缩:将产生的氢氧化钠溶液进行多级浓缩,得到浓缩的氰化钠溶液。
4.结晶:将浓缩溶液进行结晶,得到氰化钠晶体。
5.干燥和粉碎:将氰化钠晶体进行干燥和粉碎,得到最终产品。
三、设备选型本项目所需设备包括氯化钠处理设备、电解槽、浓缩设备、结晶设备、干燥和粉碎设备等。
设备选型应根据生产工艺和产能需求进行选择,并考虑设备的品牌、性能、可靠性以及维修保养等方面。
四、财务概算本项目的财务概算应包括项目建设投资、生产运营成本和预计收益等方面。
1.项目建设投资:包括土地购买、厂房建设、设备采购、环保设备等的投资。
2.生产运营成本:包括原材料、能源、劳动力、生产耗材以及日常维修保养等成本。
3.预计收益:根据市场调研和产品销售预测,估计项目的销售收入和利润,并进行财务分析评估。
五、厂区规划厂区规划应考虑生产设备的布置、原材料进出、产品储存与运输、工人生活设施等方面,确保生产工艺的顺利进行和员工的工作环境。
同时应考虑环保要求,合理规划废水、废气的处理设施,并确保厂区安全。
六、投资方案基于上述可行性研究,建议采取以下投资方案:1.寻找可靠的合作伙伴或投资者,共同投资氰化钠项目。
2.根据项目需求,寻找合适的厂址,并购买土地建设厂房。
3.选择优质的设备供应商,进行设备选购和设备安装调试。
4.配备专业的技术团队,负责项目的工艺设计、生产管理和技术支持。
氰化钠生产残液的分析

氰化钠生产残液的分析氰化钠,俗称山奈、山奈钠,是氰化物中的一种无机盐,属于剧毒品。
其下游产品覆盖面非常大,涉及到塑料、染料、医药、农药、电镀等行业。
目前氰化钠是非常重要的一种化工原料。
氰化钠生产的方法有布哈法、氨钠法和氢氰酸法。
布哈法以氮气、木炭和纯碱为原料在氧化铁的催化下高温合成,再用液氨浸取,经过滤、浓缩和析晶得到,现已淘汰此工艺;氨钠法是以金属钠、石油焦和氨为原料,在高温下合成,过滤除去炭后,浇铸成型即得成品。
该法可以直接得到固体氰化钠,并且含量高、质量好,但由于成本太高,目前也基本无人在使用; 氢氰酸法包括氰熔体法、安氏法、轻油裂解法、甲醇氨氧化法和丙烯腈副产法。
目前国内生产主要是氢氰酸法。
1 氰化钠的物化性质氰化钠分子式: NaCN; 相对分子质量: 49.01; 熔点:563.7℃; 沸点: 1497℃。
固体相对密度( 水= 1 ) : 1.60( 25℃) ; 液体相对密度( 水= 1) : 1.19 ( 25℃) ; 相对蒸气密度: 1.7( 相对空气) ; 有微弱的苦杏仁味,剧毒。
固体氰化钠为白色片状、块状或结晶状颗粒。
氰化钠溶液为无色或浅黄色透明的水溶液。
固体氰化钠易潮解,能溶于水、氨、乙醇和甲醇中。
2 氰化钠的应用随着国内经济的快速发展,近年来,氰化钠的应用越来越广泛。
在选矿和电镀方面的市场需求呈每年递增的情况;而在染料、医药和农药方面的需求量明显增大; 近几年来特别是在黄金提取和农药方面需求量猛增; 另外氰化钠还可以制备大家日常生活需要的精细化工产品。
目前氰化钠的下游产品已经被应用到人们生活中的方方面面,由此可见氰化钠的重要性。
2.1 染料方面氰化钠可以用来合成染料,目前可以合成的染料主要有黄139、黄150、靛蓝、华兰、荧光增白剂VBL、分散翠兰GL、60 号蓝等。
2.2 医药方面氰化钠可以用来合成医药中间体,为最终的成品药提供必需的原料。
常见的药品有青霉素、普瑞巴林、酮基布洛芬、止血环酸、维生素B6、叶酸、鸟嘌呤、阿昔洛韦、加巴喷丁、保泰松、巴比妥、氟哌酸、咖啡因、咳美切、胃安、美散痛、黄连素、阿伐他汀、苯氧布洛芬等。
工业固体氰化钠烘干工艺闪蒸干燥机

工业固体氰化钠烘干工艺闪蒸干燥机The following text is amended on 12 November 2020.购买工业固体氰化钠烘干机选常州干燥,专业为客户提供全套氰化钠专用干燥机,氰化钠闪蒸干燥机等技术设计方案,并有相关的成熟精验与使用单位,技术力量雄厚,加工设备精良,产品质量可靠,服务设施完善,免费安装,代培技术指导,在管理和售后服务上更加完善和周到。
欢迎来电咨询洽谈一三六一六一一二九八八!项目概述:目前世界上用于固体氰化钠生产的干燥技术主要有气流干燥、流化床干燥和沸腾床干燥工艺,相对而言以旋转闪蒸干燥工艺为最好,是一种先进、节约能源的干燥技术,为高含量固体氰化钠生产值得推荐采用的干燥工艺技术。
氰化钠生产工艺条件:〈1)进旋转闪蒸干燥器氰化钠湿基含水质量百分数:10%(2)旋转闪蒸干燥器热风进口温度:350℃〈3)旋转闪蒸干燥器热风出口温度:150℃(5)旋转闪蒸干燥器热风出口压力:-8kPa(6)旋转闪蒸干燥器热风进口压力:3kPa(7)旋转闪蒸干燥器中部压力:0kPa(8)旋转闪蒸干燥器下搅拌机转速:350rpm一、工业固体氰化钠烘干机,氰化钠专用干燥机,氰化钠闪蒸干燥机工作原理:旋风式闪蒸干燥机属对流干燥的一种。
热风从干燥塔的底部吹入,物料进入干燥塔经破碎后被热风吹起并呈悬浮态上升,悬浮状的物料与热风充分接触,瞬间完成干燥过程(一般2秒以内),干燥塔上部装有分级器,颗粒较大或未充分干燥的物料被分级器挡住,沿塔壁回落,重新参加干燥过程.颗粒较小并充分干燥的物料由塔顶排出,再经后面的分离机构分离后,成为成品。
现在常用的干燥方式是箱式干燥,除耗能较大外,干燥后还要再粉碎.与箱式干燥方式比,本装置可节约能源30-50%,另外工艺简单,省工,省时,产品质量优良与箱式及其它干燥方式比,本干燥装置是干燥技术上的一次革新。
二、工业固体氰化钠烘干机,氰化钠专用干燥机,氰化钠闪蒸干燥机主要特点:1.颗粒在气流中高速分散,同时采用高温干燥介质,强化干燥过程,所以干燥时间极短,干燥速度极快,热效率极高。
- 1、下载文档前请自行甄别文档内容的完整性,平台不提供额外的编辑、内容补充、找答案等附加服务。
- 2、"仅部分预览"的文档,不可在线预览部分如存在完整性等问题,可反馈申请退款(可完整预览的文档不适用该条件!)。
- 3、如文档侵犯您的权益,请联系客服反馈,我们会尽快为您处理(人工客服工作时间:9:00-18:30)。
2.5.1 氰化钠生产工艺我国目前生产氰化钠产品的工艺方法主要有四种:氨钠法、安氏法、丙烯腈副产法、轻油裂解法。
本项目中采用轻油裂解法,此工艺技术成熟可靠,操作安全,行之有效,是目前国内大部分生产氰化钠企业采用的工艺路线。
轻油裂解法工艺过程为,将轻油和氨气按比例在雾化器中混合,预热至280℃在电弧中裂解反应,以石油焦作载体,密闭在高温条件下进行氨化,反应产生氰氢酸气体,经除尘、冷却至50℃,再用30%液碱溶液吸收,当NaCN含量达30%以上即为液体氰化钠成品,尾气再用20%液碱溶液吸收。
此工艺方法的特点:(1)C5-C6轻油性质稳定,且以石油焦为载体,反应温度高。
轻油的工艺利用率为100%,液氨的工艺收率为90%以上。
(2)采用循环封闭式的生产方法,系统生产连续化,坚持微负压操作,确保无泄漏操作,反应安全。
(3)此工艺生产工序简单明了,生产技术装备较简单。
整个装置分为原料储运系统、反应裂解系统、炉气处理系统、成品吸收系统以及废水、废渣处理系统。
工艺过程为,将轻油和氨气按比例在雾化器中混合,预热至280℃在电弧中裂解反应,温度1C o450,以石油焦作载体,密闭在高温条件下进行氨化,反应产生氰氢酸气体,经除尘、冷却至50℃,再用30%液碱溶液吸收,当NaCN 含量达30%以上即为液体氰化钠成品,尾气再用20%液碱溶液吸收。
其主要反应方程式如下:C 5H 12+5NH 3电弧C o14505HCN+千卡HCN + NaOHNaCN+H 2O 工艺流程示意图如图3-1所示:图3-1 工艺流程示意图2.5.2 主要设备及布置主要设备见表2-3:表2-3主要设备一览表危险化学品物料的危险、有害性分析3.1.1 危险化学品识别XXXXXXXXX公司生产氰化钠(30%液体)产品中,使用的原料列入国家安全生产监督管理局2003年第1号公告《危险化学品名录》的有: 氰化钠、氰化氢、氢气、氢氧化钠、液氨等6种。
根据GB50016《建筑设计防火规范》、GB50160《石油化工企业设计防火规范》、GB5044《职业性接触毒物危害程度分级》、HG24001《化工行业职业性接触毒物危害程度分级》等规范和标准,上述危险化学品分类编号及其火灾危险、职业危害汇总于表3-1。
表3-1 产品及原料危险、危害特性系统内物质按《建筑设计防火规范》的火灾危险性分类,属于甲类物质的有氰化氢、氢气,这些物质火灾危险性最大;氨为乙类物质。
系统内会产生职业危害物质:属极度危害(Ⅰ级)的有氰化氢和氰化钠;轻度危害(Ⅳ级)的有氢氧化钠和液氨。
氰化氢和液氨属于腐蚀品,对人体会造成灼烫伤害。
分析结果:系统内危险化学品涉及易燃液体、有毒品和腐蚀品,其主要危险、有害特性为:火灾、爆炸、中毒和灼烫。
3.1.2 理化性质和危险性分析本项目涉及的危险化学品都具有不同程度的火灾、爆炸、中毒等危险特性。
同时,还有一些非危化品目录中的物质,也具有一定的危险特性。
了解这些物质的理化特性,有助于分析其危险特性。
各种物质具体的理化性质和危险性见【附件】危险、有害物质特性介绍。
现分类总结如下,见表3-2:表3-2主要火灾爆炸危险物料的燃烧爆炸相关参数表生产工艺过程危险、有害性分析结果3.2.1 氰化钠(30%液体)产品生产过程中的危险性分析一、装卸工段(1) 液氨接卸、气化接卸:液氨由汽车槽车运来后,分别将汽车槽车的气液相管与液氨贮槽的气液相管相连,开启液氨泵,将汽车槽车中的液氨卸入液氨贮槽中,直至卸完,关闭液氨泵。
或者可以利用氨气将汽车槽车内液氨压入贮槽内,直到槽车内液氨压完,关闭氨气阀门。
当液氨全部卸完后,关闭贮槽的气液相阀门,卸车结束。
气化:液氨由液氨泵从液氨贮槽中打至氨计量槽,经计量后利用高位差送入氨蒸发器。
氨蒸发器内液面由液面计自动控制。
当裂解炉要求送氨时,打开蒸发器进水阀进行加热,打开出氨阀,气氨经氨分离器,氨缓冲器罐后,压力调节至后送出。
液氨防火等级为乙类,属于易燃易爆物质。
液氨贮槽的储存压力为,属于中压容器,液氨储罐区是火灾重点防范区,使用中应加强对此压力容器的监察管理。
(2) 轻油接卸轻油由汽车槽车运来后,将汽车槽车的气液相管与轻油贮槽的气液相管相连,开启轻油泵,将汽车槽车中的轻油卸入贮槽中,直至卸完,关闭轻油泵,关闭贮槽的气液相阀门,卸车结束。
当裂解炉要求输送轻油时,打开轻油贮槽的出液阀,打开轻油计量槽的进液阀,开启轻油泵,或者打开贮槽内。
轻油经计量后送至裂解炉参加反应。
轻油(C5—C6)防火等级为甲类,属于易燃易爆物质。
轻油储罐区也是火灾重点防范区,使用中应加强对此容器的监察管理。
(3) 液碱接卸液碱由槽车运来后,打开碱槽进碱阀,开启碱泵将液碱打入碱槽中,同时根据需加水量进行加水,与液碱混合,待水量加到规定数值后(看水表读数)关闭碱槽进水阀,当槽车内液碱卸完后,关闭碱泵,卸车完毕。
当吸收工段需送碱时,打开碱槽出液阀,利用位差送入碱地槽,开启碱液下泵,将碱液送至吸收工段。
二、裂解反应工段由原料工段送来的气氨和轻油同时进入预热器预热至250℃左右后,混合气体进入三相电极浸入石油焦层导电发热的裂解炉进行裂解反应。
开启循环冷却水阀门,进行冷却,以保护炉体。
裂解生成的混合气体,从裂解炉出来,经冷却套管冷却后,经第一旋风除尘器、第二旋风除尘器后,进入列管冷却器冷却至50℃左右,再经过布袋除尘器进一步除尘后送至吸收工段。
根据安监总管三(2009)116号的文件要求,该单元的化学反应主要是裂解反应。
此工段主要危险性,裂解温度高达1C o450,设备保护不好,有烫伤的危险;同时裂解电流大,存在触电的危险。
裂解气、连同部分石油焦,对管壁有冲刷作用,由于部分管段冷却介质为气氨和轻油,如果管壁发生泄漏,将导致燃烧、爆炸事故的发生。
如果由于断电或引风机机械故障而使引风机突然停转,则炉膛内很快变成正压,会从窥视孔或烧嘴等处向外喷火,严重时会引起炉膛爆炸;如果燃料系统大幅度波动,燃料气压力过低,则可能造成裂解炉烧嘴回火,使烧嘴烧坏,甚至会引起爆炸;三、吸收工段裂解工段来的炉气进入吸收器,与碱液发生中和反应,生成氰化钠溶液,吸收后的氰化钠溶液,经中和液下泵打入成品贮槽中。
从吸收器出来的气体(N2、H2、NH3等),再经尾气吸收器二次碱吸收后,通过真空泵抽至烟囱高空排放。
产品送入氰化钠贮罐,成品液体氰化钠的贮存量为450m3,贮存天数为8-14天。
此工段危险因素较多,进出反应器的物料均为剧毒品,且反应前有易燃性质。
生产控制条件要求比较苛刻,稍有失误即可产生不了后果,甚至发生事故。
如液体氢氰酸在碱性条件下会很快发生自聚反应,不仅放出大量的热量导致反应温度、压力的突然升高,而且生成棕色的粘稠液体使生产无法进行下去,严重时也可能造成管道堵塞或设备爆炸事故;另外,紧急情况下的放空装置,所排出的气体有中毒和爆炸的可能性,要控制放空速度。
3.2.2 中毒危险性分析生产过程中主要有毒有害物料种类、分布及危害性如表3-3所示。
由表3-3可见,剧毒物质氰化氢和氰化钠在厂区分布广泛。
剧毒气体氰化氢作为中间产物,主要存在于氰化氢制备与净化单元和液氰制备单元;在液氰制备单元和液氰库房中,氰化钠易吸收空气中的水气和二氧化碳,释放出氰化氢剧毒气体。
有毒物质的泄漏、飞溅均会对人造成不同程度的毒害。
表3-3 有毒有害物质种类、危害性及分布表3.2.3 其他危险性分析粉尘危害:裂解炉气夹带的炭粉,由于和HCN接触,吸附HCN,毒性很大。
生产中定期或不定期排放炭粉时会飘浮于作业场所空气中,导致中毒。
固氰生产车间和固氰库房存在剧毒氰化钠粉尘。
灼伤危害:存在两类灼伤,一类是化学灼伤,一类是高温灼伤。
生产中大量使用的氢氧化钠、液氨等碱性物质,容易对皮肤、眼睛、呼吸道造成伤害;生产系统中的高温设备、装置、管道若不采取隔热防护措施,也有灼伤的危险。
3.2.4 工艺过程危险、有害性分析小结综上所述,XXXXXXXXX公司氰化钠(30%液体)产品生产过程中存在火灾、爆炸、灼烫、中毒和粉尘、机械伤害、起重伤害、物体打击、高处坠落等危险、有害性。
其主要的危险性是火灾、爆炸、中毒、粉尘和灼伤。
系统主要危险危害因素辨识3.3.1 火灾、爆炸本建设项目中所涉及的化工原料、中间产物或产品,有火灾爆炸危险性较大的甲、乙类物质:如原料轻油(甲B)、液氨(乙类)等;生产过程中产生的甲类可燃气体:如氰化氢和氢气等。
它们大多数具有易燃、易爆和易蒸发特性。
由于化工原料或产品在装卸、储运、生产过程中不可完全避免地暴露于空气之中或与空气接触,当蒸发或产生的气体达到一定浓度,与空气形成可燃性或爆炸性混合系时,一旦遇到点火源,就会发生燃烧爆炸事故。
液氨在管线或装置破裂泄漏时还会发生蒸气爆炸。
裂解气、连同部分石油焦,对管壁有冲刷作用,由于部分管段冷却介质为气氨和轻油,如果管壁发生泄漏,将导致燃烧、爆炸事故的发生。
生产原料中,轻油(C5—C6)防火等级为甲类,液氨防火等级为乙类,轻油和液氨都是属于易燃易爆物质,因此轻油储罐区和液氨储罐区是火灾重点防范区。
3.3.2 泄漏、扩散液体化工品,同时还具有易蒸发、易流淌和易扩散等特点,在装卸及生产使用过程中因设备故障或损坏,以及其它一些人为因素的原因,有可能发生泄漏、蒸发及扩散事故,进而造成人员中毒,并可能导致火灾爆炸事故的发生。
如果发生较大规模的泄漏事故,还将对周围环境造成严重污染。
本项目中液氨、液碱及氰化钠具有上述危险。
轻油与氨蒸发器出来的气氨进入预热混合器,然后在裂解炉中以石油焦粒作载体进行裂解反应,反应生成氢氰酸气体,氢氰酸气体经套管冷却、旋风除尘、列管冷却器冷却和布袋除尘后至吸收器,用氢氧化钠溶液吸收,生成成品液体氰化钠。
氰化氢和氰化钠都是剧毒物品,因而整个生产车间内的设备、管道、阀门如泄漏就可能有剧毒物质流出。
3.3.3 中毒液体化工品,多为有毒物质,本项目中的氰化钠、氰化氢为剧毒品,另外生产储运中的液氨也可引起人体中毒。
由于上述化工产品或化学物品生产储运过程中的一些作业环节仍需人工完成,这些岗位的作业人员与毒物(液体或其蒸气)相接触,不同程度地受到毒物危害。
严重者会引起作业人员中毒甚至死亡事故。
3.3.4 灼伤、冻伤本建设项目中烧碱及液氨的存在,生产使用过程中一旦发生泄漏,液体会溅溢接触到操作人员的皮肤或身体,烧碱会导致人体灼伤;由于液氨瞬间的汽化需要吸收大量的汽化热,会导致人体表面的局部温度迅速下降,从而形成冻伤事故。
在生产过程中由于高温反应条件的存在,操作中处理不当也会对人体造成烫伤。
3.3.5 噪声由于生产中使用真空泵和水泵,因而产生了噪声,现场噪声值为50分贝。
对现场短暂操作的人员,不会产生影响。
但对长期在真空泵房、水泵房及现场的工作人员会产生一定的危害。