轮胎制造加工
轮胎工艺知识点总结
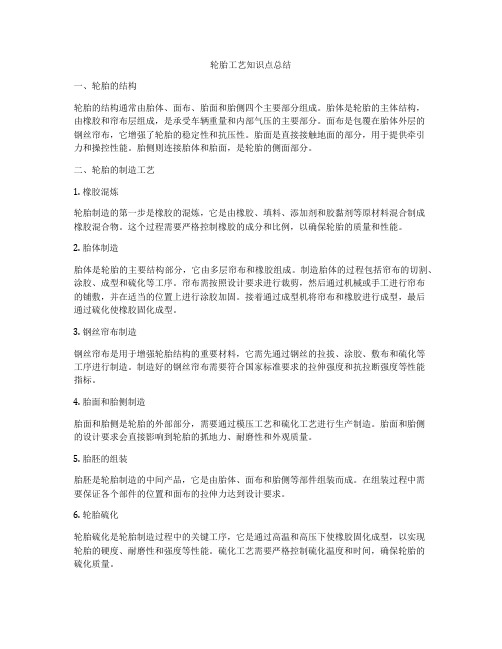
轮胎工艺知识点总结一、轮胎的结构轮胎的结构通常由胎体、面布、胎面和胎侧四个主要部分组成。
胎体是轮胎的主体结构,由橡胶和帘布层组成,是承受车辆重量和内部气压的主要部分。
面布是包覆在胎体外层的钢丝帘布,它增强了轮胎的稳定性和抗压性。
胎面是直接接触地面的部分,用于提供牵引力和操控性能。
胎侧则连接胎体和胎面,是轮胎的侧面部分。
二、轮胎的制造工艺1. 橡胶混炼轮胎制造的第一步是橡胶的混炼,它是由橡胶、填料、添加剂和胶黏剂等原材料混合制成橡胶混合物。
这个过程需要严格控制橡胶的成分和比例,以确保轮胎的质量和性能。
2. 胎体制造胎体是轮胎的主要结构部分,它由多层帘布和橡胶组成。
制造胎体的过程包括帘布的切割、涂胶、成型和硫化等工序。
帘布需按照设计要求进行裁剪,然后通过机械或手工进行帘布的铺敷,并在适当的位置上进行涂胶加固。
接着通过成型机将帘布和橡胶进行成型,最后通过硫化使橡胶固化成型。
3. 钢丝帘布制造钢丝帘布是用于增强轮胎结构的重要材料,它需先通过钢丝的拉拔、涂胶、敷布和硫化等工序进行制造。
制造好的钢丝帘布需要符合国家标准要求的拉伸强度和抗拉断强度等性能指标。
4. 胎面和胎侧制造胎面和胎侧是轮胎的外部部分,需要通过模压工艺和硫化工艺进行生产制造。
胎面和胎侧的设计要求会直接影响到轮胎的抓地力、耐磨性和外观质量。
5. 胎胚的组装胎胚是轮胎制造的中间产品,它是由胎体、面布和胎侧等部件组装而成。
在组装过程中需要保证各个部件的位置和面布的拉伸力达到设计要求。
6. 轮胎硫化轮胎硫化是轮胎制造过程中的关键工序,它是通过高温和高压下使橡胶固化成型,以实现轮胎的硬度、耐磨性和强度等性能。
硫化工艺需要严格控制硫化温度和时间,确保轮胎的硫化质量。
7. 轮胎检验和包装轮胎制造完成后需要进行严格的质量检验,包括外观质量、尺寸测量、硫化性能和性能测试等。
合格的轮胎在包装之前还需要进行气密性试验和动平衡试验等。
三、轮胎的检验和测试轮胎制造过程中的检验和测试是确保轮胎质量的重要环节。
轮胎是怎么加工的原理
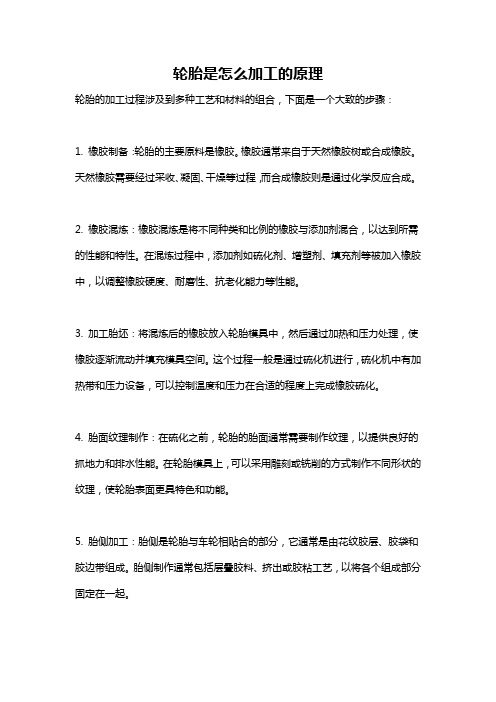
轮胎是怎么加工的原理轮胎的加工过程涉及到多种工艺和材料的组合,下面是一个大致的步骤:1. 橡胶制备:轮胎的主要原料是橡胶。
橡胶通常来自于天然橡胶树或合成橡胶。
天然橡胶需要经过采收、凝固、干燥等过程,而合成橡胶则是通过化学反应合成。
2. 橡胶混炼:橡胶混炼是将不同种类和比例的橡胶与添加剂混合,以达到所需的性能和特性。
在混炼过程中,添加剂如硫化剂、增塑剂、填充剂等被加入橡胶中,以调整橡胶硬度、耐磨性、抗老化能力等性能。
3. 加工胎坯:将混炼后的橡胶放入轮胎模具中,然后通过加热和压力处理,使橡胶逐渐流动并填充模具空间。
这个过程一般是通过硫化机进行,硫化机中有加热带和压力设备,可以控制温度和压力在合适的程度上完成橡胶硫化。
4. 胎面纹理制作:在硫化之前,轮胎的胎面通常需要制作纹理,以提供良好的抓地力和排水性能。
在轮胎模具上,可以采用雕刻或铣削的方式制作不同形状的纹理,使轮胎表面更具特色和功能。
5. 胎侧加工:胎侧是轮胎与车轮相贴合的部分,它通常是由花纹胶层、胶袋和胶边带组成。
胎侧制作通常包括层叠胶料、挤出或胶粘工艺,以将各个组成部分固定在一起。
6. 胎壁构建:胎壁是连接轮胎胎面和胎侧的部分。
它通常有多个层次和不同的构造,以提供更好的耐磨性、支撑性和稳定性。
胎壁的构建过程中,需要将各种橡胶层、钢丝帘子层、尼龙帘子层和帘子胶层等材料按照一定的顺序和结构贴合在一起。
7. 花纹图案压花:硫化前,轮胎的胎面通常需要通过压花技术制作更复杂的花纹特征。
这通常是通过将轮胎模具上的花纹设计压在胎面上,以使花纹更加鲜明和具有良好的抓地力和排水性能。
8. 硫化:硫化是轮胎加工中最重要的一个步骤,也是决定轮胎最终性能的关键环节。
硫化是指将模具中的轮胎胎坯加热到一定的温度,并在高压下与硫化剂反应,使橡胶永久性地交联,以提高轮胎的强度、耐磨性和弹性。
9. 后处理:硫化后的轮胎需要经过多道工序进行后处理。
这包括拆模、胶料修整、质检、修补、刮除多余橡胶等环节。
轮胎生产工艺流程

轮胎生产工艺流程轮胎是车辆行驶中直接接触地面的组件,其质量和性能直接影响着车辆的安全性和舒适性。
轮胎的生产工艺流程是一个复杂的过程,涉及多个工序和设备。
本文将介绍轮胎生产的主要工艺流程,帮助读者了解轮胎是如何制造出来的。
原材料准备阶段天然橡胶和合成橡胶的混炼轮胎的主要原材料是橡胶,通常使用天然橡胶和合成橡胶的混合物。
在这一阶段,将天然橡胶和合成橡胶按照配方混合,并加入各种添加剂和增强剂,如硫化剂、炭黑、增塑剂等,经过混炼工艺,获得均匀的橡胶混合物。
钢丝帘布和带线的加工轮胎的骨架通常由钢丝帘布和带线构成,这些材料需要进行预处理,如涂胶、整条、切断等工艺,以确保骨架的质量和性能。
脚模制备和胎胚制造阶段胎胚制造胎胚是轮胎的主体结构,通常包括胎体和胎面两部分。
在这一阶段,将橡胶混合物放入模具中,经过压制、硫化等工艺,制成胎体和胎面。
脚模制备脚模是将轮胎胎胚放入的模具,用于成型轮胎。
通常需要根据轮胎的尺寸和形状设计和制造相应的脚模。
成型和硫化工艺阶段胎体和胎面的成型在成型阶段,将胎体和胎面放入脚模中,并通过加热和压制等工艺,使其形成轮胎的整体结构。
硫化硫化是轮胎制造中至关重要的一个工艺环节,通过硫化可以使轮胎获得良好的耐磨性和弹性。
轮胎放入硫化机中,受热硫化处理一段时间,使橡胶混合物发生交联反应,形成耐磨耐压的轮胎结构。
检验和包装阶段质量检验在生产完成后,需要对轮胎进行质量检验,包括外观检验、尺寸检验、硬度检验等,以确保轮胎符合相关标准和要求。
包装最后一道工序是轮胎的包装,通常采用塑料袋包装或纸箱包装,保护轮胎表面免受污染和损坏。
结语通过以上工艺流程的介绍,我们了解到轮胎的生产过程是一个复杂而精细的工艺流程,每一个环节都需要严格控制,以确保最终产品的质量和性能。
希望本文对读者有所帮助,更深入了解轮胎的生产工艺流程。
轮胎制造工艺流程

轮胎制造工艺流程轮胎是汽车的重要组成部分,是汽车行驶的基础保障之一。
轮胎的制造过程从原材料的加工开始,经过多个工序完成最终的成品。
以下是轮胎制造的大致工艺流程。
1. 原材料的准备:轮胎制造的原材料主要包括橡胶、纤维材料和钢丝等。
这些原材料需要经过加工处理,以达到符合轮胎制造过程的要求。
橡胶是轮胎最主要的原材料之一,需要在橡胶混炼机中将各种添加剂和硫化药剂加入到橡胶中,经过混合、摇匀、切割和挤压等工序,最终制成符合要求的橡胶条。
2. 胎体和胎面的制造:车胎的主要结构部分是胎体和胎面,它们是轮胎性能的决定因素。
胎体是由一层层的帘子布通过缠绕、融合而成,而胎面则是采用硫化面层和胶料进行压制而成的。
制造胎体和胎面需要使用专门的机器设备,并且需要根据每个车型的要求进行设计、调整。
3. 胎面加工和组装:制成的胎体和胎面需要进行进一步的加工和组装。
其中,胎面需要进行花纹图案打印、切割、冲孔、铆钉等加工工序,以达到良好的抓地性和耐用性。
在此基础上,胎体和胎面经过组装粘接、裁切、堆叠、卷曲等工序,最终形成半成品轮胎。
4. 硫化:硫化是轮胎制造过程中最重要的工序之一。
半成品轮胎通过进入硫化胶压机,经过热压、硫化、降温等复杂的物理和化学反应,最终形成具有强度、柔韧性、耐磨性等性能的成品轮胎。
硫化的温度、时间和压力等参数需要进行精密的控制,以满足不同车型、用途和环境的要求。
5. 最后的质检和包装:制成的成品轮胎需要进行严格的质量检验和测试,以确保轮胎的性能和使用寿命。
轮胎的外观、尺寸、硬度、强度等多个参数需要进行检测,并制定相关标准和规范。
最后,符合质量要求的轮胎将进行包装和运输,以便在全球范围内进行销售和使用。
总的来说,轮胎制造是一项技术要求很高的工艺,需要经历多个工序进行组装和加工。
其专业化程度较高,除了对原材料的品质要求较高外,对设备、技术和环境等方面也有较高的要求。
当前,随着汽车行业的发展和需求的变化,轮胎制造技术和工艺也在不断更新和发展,以迎合市场和用户的需求。
轮胎加工工艺

轮胎加工工艺轮胎是汽车的重要部件之一,它直接与路面接触,对于行驶安全和舒适性都有着重要的影响。
轮胎的加工工艺对于轮胎的质量和性能有着至关重要的影响。
在本文中,我们将介绍一下轮胎加工的工艺流程和主要工艺步骤。
轮胎的加工工艺主要包括胎面成型、帘布加工、硫化成型等几个关键步骤。
首先,我们来看一下胎面成型工艺。
胎面是轮胎与地面接触的部分,因此其成型对于轮胎的抓地性和操控性有着重要的影响。
胎面成型的主要工艺步骤包括胎带整形、帘布涂胶、胎面成型等。
胎带整形是指在轮胎制作的初始阶段,将帘布加工成胎带的形状,以便后续的帘布加工和胎面成型。
帘布涂胶是指在帘布经过整形之后,使用胶水将胎带和帘布黏合在一起。
胎面成型是指通过热压和模具的作用,将帘布形成胎面的正面曲率。
接下来,我们来看一下帘布加工的工艺流程。
帘布是轮胎的重要组成部分,直接影响轮胎的抗拉强度和耐磨性。
帘布加工的主要步骤包括布料裁剪、帘布涂胶、帘布纳带等。
布料裁剪是指将帘布按照一定的尺寸和形状进行裁剪,以便后续的帘布涂胶和纳带。
帘布涂胶是指将胶水均匀地涂敷在帘布上,使其具有黏合性和强度。
帘布纳带是指将帘布经过一定的工艺过程,与其他组件进行黏合,形成轮胎的骨架。
最后,我们来看一下轮胎的硫化成型工艺。
硫化是指将轮胎放入硫化炉中进行加热和固化,使轮胎具备足够的硬度和强度。
硫化成型的主要步骤包括炉温控制、硫化时间控制和冷却处理。
炉温控制是指控制硫化炉内的温度,以保证轮胎在硫化过程中能够达到所需的硬度和强度。
硫化时间控制是指控制硫化的时间,以保证轮胎能够充分硫化。
冷却处理是指在硫化完成之后,对轮胎进行冷却处理,使其固化得更加完全。
综上所述,轮胎的加工工艺是一个非常复杂和精细的过程,它直接影响到轮胎的质量和性能。
胎面成型、帘布加工和硫化成型是轮胎加工的三个主要工艺步骤,每个步骤都有着其独特的工艺要求和技术要点。
只有在合理控制和优化这些工艺步骤的基础上,才能生产出高质量和高性能的轮胎产品。
轮胎的生产流程是什么样的

轮胎的生产流程是什么样的第一步:橡胶配方橡胶配方是轮胎生产的第一步,它是根据轮胎的用途和规格来确定的。
在这个阶段,橡胶将与其他材料进行混合,如碳黑、纤维增强剂和添加剂。
配方的目的是提供材料的强度、耐磨性和耐用性。
第二步:混炼成型在橡胶配方准备好之后,将会进行混炼成型。
首先将橡胶放入混合机中进行混合,然后添加其他材料。
混合的目的是使橡胶、碳黑和其他添加剂均匀地混合在一起,形成一个均匀的橡胶胶状物。
接下来,将橡胶胶状物放入压延机中进行分条和切割。
分条是将橡胶压成长条形状,以便于后续的轮胎成型。
然后,将条状物切割成所需的长度。
第三步:胎侧镶嵌胎侧是轮胎的侧面部分,通常用于放置品牌名称、尺寸和其他标识。
在胎侧镶嵌的过程中,轮胎制造商将使用特殊的材料和设备将胎侧上的标识添加到轮胎上。
这可以通过固化、热封或其他方法完成。
第四步:硫化硫化是轮胎生产的关键步骤之一、在硫化过程中,温度和压力将橡胶加工到所需的形状和强度。
首先,将轮胎放入模具中,并使用加热和压力将其加工成所需的形状。
然后,将轮胎放入硫化炉中,以便于橡胶与空气中的硫反应,增加轮胎的耐磨性和耐用性。
第五步:检验在硫化之后,轮胎将被检验以确保其质量和性能达到标准。
轮胎将经过外观检查、尺寸测量、平衡和强度测试等一系列的检验。
如果不合格,将会进行修复或返工,直至达到要求。
第六步:包装在检验后,合格的轮胎将被送往包装区域进行最后的包装。
轮胎将根据尺寸和类型进行分类,并用包装材料如塑料袋或纸箱进行包装,以便储存和运输。
综上所述,轮胎的生产流程包括橡胶配方、混炼成型、胎侧镶嵌、硫化、检验和包装等多个阶段。
每个阶段都必须严格控制和检验,以确保轮胎的质量和性能达到标准要求。
这些步骤的顺序和流程可能会略有不同,具体取决于个别制造商的生产方式和设备。
轮胎几大加工工艺流程

轮胎几大加工工艺流程英文回答:There are several major processing techniques involved in tire manufacturing. These processes are essential for producing high-quality and durable tires. Let me explain each of them in detail.1. Mixing and Compounding: This is the initial stage where raw materials such as natural rubber, synthetic rubber, carbon black, and various chemicals are mixed together. The mixture is then processed in a machine called a Banbury mixer, which ensures uniformity and proper dispersion of the ingredients. This process is crucial for achieving the desired properties of the tire, such as elasticity, strength, and resistance to wear.For example, when I worked at a tire manufacturing company, I witnessed the mixing and compounding process firsthand. The operators would carefully measure and addthe required amount of raw materials into the mixer. They would then adjust the mixing time and temperature to ensure proper compounding. This step was crucial as any deviation in the mixing process could lead to inferior tire quality.2. Tire Building: Once the rubber compound is ready, it is transferred to the tire-building machine. In this process, the rubber compound is layered onto a drum or a bladder, forming the tire's basic structure. The layers are carefully positioned to ensure proper alignment and strength. Additional components such as steel belts, fabric plies, and bead wires are also incorporated during this stage.To illustrate, imagine a tire builder at work. They would place the first layer of rubber compound onto the drum and then add the steel belts for reinforcement. They would repeat this process for each layer, ensuring that the tire's structure is sturdy and well-balanced. This step requires precision and attention to detail to create a tire with optimal performance.3. Curing: After the tire is built, it undergoes the curing process, which involves applying heat and pressure to shape and bond the tire components. The tire is placed in a mold and heated in a curing press. The heat and pressure cause the rubber compound to vulcanize, resulting in a solid and durable tire.Let's say you're observing the curing process in a tire factory. You would see the tires being loaded into the curing press and then subjected to high temperature and pressure for a specific duration. This step is crucial asit determines the tire's final shape, strength, and overall performance.中文回答:轮胎制造过程中有几个主要的加工工艺流程。
轮胎的制造工艺

轮胎制造工艺简介轮胎是一种在各种车辆或机械上装配的接地滚动的圆环形弹性橡胶制品。
它能支承车身,缓冲外界冲击,实现与路面的接触并保证车辆的行驶性能。
轮胎常在复杂和苛刻的条件下使用,它在行驶时承受着各种变形、负荷、力以及高低温作用,因此必须具有较高的承载性能、牵引性能、缓冲性能。
同时,还要求具备高耐磨性和耐屈挠性,以及低的滚动阻力与生热性。
轮胎的制造工艺是指将橡胶、帘线、钢丝等原材料经过一系列的加工过程,最终形成具有一定规格和结构的轮胎的过程。
轮胎的制造工艺主要包括以下几个步骤:1. 橡胶配方制作橡胶配方是指将橡胶和各种添加剂按照一定的比例混合在一起,以得到具有不同性能和用途的橡胶复合物。
橡胶配方的设计是轮胎制造工艺中非常重要的一个环节,它直接影响着轮胎的质量和性能。
橡胶配方的设计需要根据轮胎的使用条件和要求,以及原材料的特性和供应情况,进行科学合理的选择和优化。
橡胶配方主要包括以下几类原料:橡胶:是轮胎制造中最基本和最重要的原料,它决定了轮胎的弹性、强度、耐磨性等基本性能。
橡胶分为天然橡胶和合成橡胶两大类,常用的有天然橡胶、丁苯橡胶、丁腈橡胶、丁基橡胶等。
不同种类和牌号的橡胶具有不同的特点和用途,通常需要按照一定的比例进行混合使用,以达到最佳的效果。
炭黑:是轮胎制造中最重要的填充剂,它能够提高轮胎的强度、硬度、耐磨性、耐老化性等性能。
炭黑分为多种类型和等级,不同类型和等级的炭黑具有不同的结构和表面特性,对轮胎性能有不同的影响。
通常需要根据轮胎部件的功能和要求,选择合适类型和等级的炭黑,并控制好用量。
油料:是轮胎制造中常用的软化剂和增塑剂,它能够降低橡胶混合物的粘度和硬度,提高其加工性能和延展性。
油料分为芳香油、石蜡油、萘油等多种类型,不同类型的油料对橡胶混合物的物理性能和化学稳定性有不同的影响。
通常需要根据橡胶种类和配方要求,选择合适类型和用量的油料。
硫化剂:是轮胎制造中必不可少的交联剂,它能够使橡胶分子之间形成硫化键,从而提高橡胶的弹性、强度、耐热性等性能。
轮胎生产工艺流程

轮胎生产工艺流程轮胎是交通运输的重要组成部分,它能承受车辆荷载,提供弹性支撑,降低震动和噪声,保障行车安全。
轮胎生产工艺流程是一个复杂的系统工程,包含多个环节,需要高度的自动化和精细化操作。
本文将详细介绍轮胎生产工艺的流程及其各个环节的特点和技术要点。
一、预处理1.原材料筛选:轮胎生产的原材料主要包括橡胶、纤维品、钢丝等。
在生产之前,要对这些原材料进行筛选和质量检测,确保其符合生产要求。
2.原材料预处理:橡胶等原材料需要进行预处理,包括挤出、混炼、过滤等步骤。
预处理可以使原材料更易于使用和加工,提高生产效率和产品质量。
二、缓冲层生产缓冲层位于轮胎内部,主要起到减震和支撑的作用。
它由多层材料叠加而成,包括橡胶、尼龙布、合成纤维等。
缓冲层的生产流程如下:1.面板生产:面板是缓冲层的基础材料,是由橡胶和合成纤维叠压而成的板材。
生产面板时,要把橡胶混合均勻,然后通过挤压设备将其压制成板材形状。
2.加工:面板加工包括冷延、割裁、涂胶等步骤。
冷延是将面板按照一定厚度和规格拉伸,使其变薄而且均匀。
割裁是将冷延后的面板按照要求的大小和形状切割成片。
涂胶是将面板表面涂上胶水,以便后续的拼接和粘合。
3.拼接:拼接是将多个面板拼接起来,形成一个完整的缓冲层。
拼接是靠人工完成的,根据轮胎的具体规格进行定制。
三、骨架层生产骨架层是轮胎的重要组成部分,它主要由钢丝、尼龙布等材料组成,能够承受车辆的荷载,提供弹性支撑。
骨架层的生产流程如下:1.编织:编织是将尼龙布和钢丝按照一定规格和方式编织而成。
钢丝经过拉伸和折弯后,变成一种蜘蛛网状的结构,形成稳定的骨架框架。
尼龙布则被覆盖在钢丝上面,用于缓解重量和摩擦力。
2.定位:定位是将编织好的骨架放在预定的位置上,并进行调整和定位。
这个过程需要精度高、操作严谨,以确保轮胎的整体结构紧密和稳定。
四、胎面层生产胎面层是轮胎的外部覆盖层,它由橡胶、合成纤维等制成,承载着车辆行驶的阻力和摩擦力。
轮胎的加工工艺
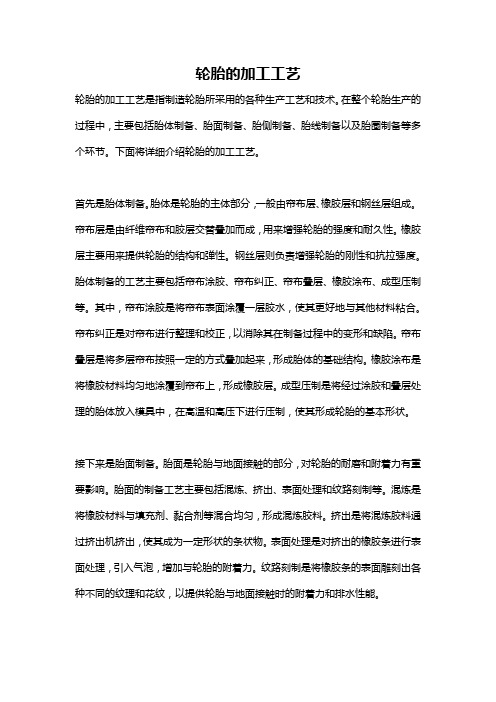
轮胎的加工工艺轮胎的加工工艺是指制造轮胎所采用的各种生产工艺和技术。
在整个轮胎生产的过程中,主要包括胎体制备、胎面制备、胎侧制备、胎线制备以及胎圈制备等多个环节。
下面将详细介绍轮胎的加工工艺。
首先是胎体制备。
胎体是轮胎的主体部分,一般由帘布层、橡胶层和钢丝层组成。
帘布层是由纤维帘布和胶层交替叠加而成,用来增强轮胎的强度和耐久性。
橡胶层主要用来提供轮胎的结构和弹性。
钢丝层则负责增强轮胎的刚性和抗拉强度。
胎体制备的工艺主要包括帘布涂胶、帘布纠正、帘布叠层、橡胶涂布、成型压制等。
其中,帘布涂胶是将帘布表面涂覆一层胶水,使其更好地与其他材料粘合。
帘布纠正是对帘布进行整理和校正,以消除其在制备过程中的变形和缺陷。
帘布叠层是将多层帘布按照一定的方式叠加起来,形成胎体的基础结构。
橡胶涂布是将橡胶材料均匀地涂覆到帘布上,形成橡胶层。
成型压制是将经过涂胶和叠层处理的胎体放入模具中,在高温和高压下进行压制,使其形成轮胎的基本形状。
接下来是胎面制备。
胎面是轮胎与地面接触的部分,对轮胎的耐磨和附着力有重要影响。
胎面的制备工艺主要包括混炼、挤出、表面处理和纹路刻制等。
混炼是将橡胶材料与填充剂、黏合剂等混合均匀,形成混炼胶料。
挤出是将混炼胶料通过挤出机挤出,使其成为一定形状的条状物。
表面处理是对挤出的橡胶条进行表面处理,引入气泡,增加与轮胎的附着力。
纹路刻制是将橡胶条的表面雕刻出各种不同的纹理和花纹,以提供轮胎与地面接触时的附着力和排水性能。
然后是胎侧制备。
胎侧是轮胎侧面的部分,一般由橡胶材料和帘布组成。
胎侧的制备工艺主要包括打胎侧料、贴胎侧带、成型压制等。
打胎侧料是将橡胶材料经过一系列的处理和整形,形成胎侧的基础结构。
贴胎侧带是将胎侧料与胎侧带材料粘合在一起,以增强轮胎的结构和强度。
成型压制是将经过贴胎侧带处理的胎侧放入模具中,在高温和高压下进行压制,使其形成轮胎的侧面结构。
接着是胎线制备。
胎线是轮胎内部的一组钢丝,用于增强轮胎的刚性和抗拉强度。
轮胎生产技术及原材料材料

橡胶助剂是用来改善橡胶加工性能和物理性能的添加剂。高品质的橡胶助剂应具 有优良的分散性、稳定性和相容性,能够提高轮胎的性能和加工效率。
填充剂
填充剂主要用于改善橡胶的物理性能和降低生产成本。高品质的填充剂应具有高 纯度、低挥发性和良好的分散性,能够提高轮胎的耐磨性和降低油耗。
其他辅助材料的品质与性能
橡胶助剂与填充剂的配比
在轮胎制造中,橡胶助剂和填充剂的配比通常根据生产工艺和产品性能要求来确定,一般占轮胎质量 的2%-10%。
其他辅助材料的选用与配比
其他辅助材料的作用
其他辅助材料如炭黑、增塑剂等可以改善轮胎的性能和加工性。
其他辅助材料的配比
在轮胎制造中,其他辅助材料的配比通常根据产品性能要求和生产工艺来确定,一般占轮胎质量的1%-5%。
合成橡胶的选用与配比
合成橡胶的种类
合成橡胶的配比
合成橡胶主要来源于石油化工原料, 常见的合成橡胶有丁苯橡胶、顺丁橡 胶、异戊橡胶等。
在轮胎制造中,合成橡胶的配比通常 根据轮胎性能要求和生产工艺来确定, 一般占轮胎质量的20%-40%。
合成橡胶的性能
合成橡胶具有较好的耐油、耐高温和 耐老化性能,可以提高轮胎的耐磨性 和抗疲劳性能。
天然橡胶的品质和产量受到气候、土壤和种植条件的影响,因此其价格波动较大。
为了确保天然橡胶的供应稳定,许多轮胎制造商开始转向合成橡胶的研发和应用。
合成橡胶
合成橡胶是由石油化工产品经 过聚合反应生成的,其性能和 天然橡胶相似,但不受气候和 环境因素的影响。
合成橡胶的种类繁多,如丁苯 橡胶、顺丁橡胶、乙丙橡胶等, 广泛应用于各种轮胎制造。
性能
天然橡胶在轮胎制造中主要提供弹性 和耐磨性,使轮胎能够适应不同的路 况和行驶条件。
轮胎加工工艺
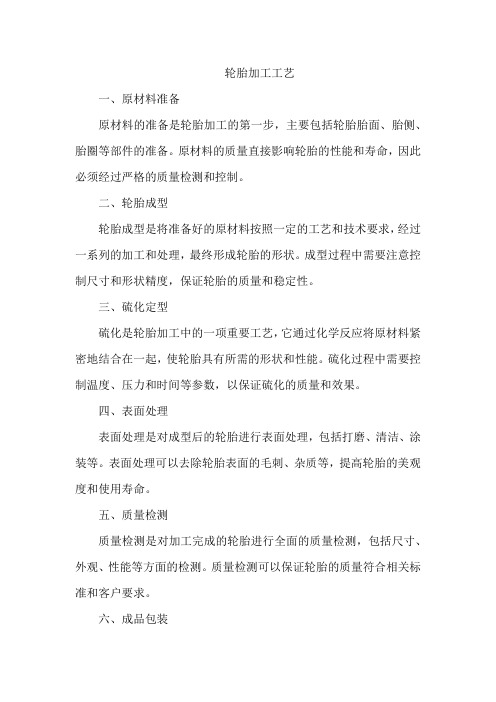
轮胎加工工艺
一、原材料准备
原材料的准备是轮胎加工的第一步,主要包括轮胎胎面、胎侧、胎圈等部件的准备。
原材料的质量直接影响轮胎的性能和寿命,因此必须经过严格的质量检测和控制。
二、轮胎成型
轮胎成型是将准备好的原材料按照一定的工艺和技术要求,经过一系列的加工和处理,最终形成轮胎的形状。
成型过程中需要注意控制尺寸和形状精度,保证轮胎的质量和稳定性。
三、硫化定型
硫化是轮胎加工中的一项重要工艺,它通过化学反应将原材料紧密地结合在一起,使轮胎具有所需的形状和性能。
硫化过程中需要控制温度、压力和时间等参数,以保证硫化的质量和效果。
四、表面处理
表面处理是对成型后的轮胎进行表面处理,包括打磨、清洁、涂装等。
表面处理可以去除轮胎表面的毛刺、杂质等,提高轮胎的美观度和使用寿命。
五、质量检测
质量检测是对加工完成的轮胎进行全面的质量检测,包括尺寸、外观、性能等方面的检测。
质量检测可以保证轮胎的质量符合相关标准和客户要求。
六、成品包装
成品包装是将检测合格的轮胎进行包装,以方便运输和存储。
包装要求根据不同轮胎的类型和用途而定,一般要求包装牢固、美观、环保等。
七、环境控制
环境控制是轮胎加工过程中的一项重要环节,包括对加工环境的温度、湿度、清洁度等方面的控制。
环境控制可以有效减少环境污染和产品不良率,提高生产效率和产品质量。
子午线轮胎的生产流程
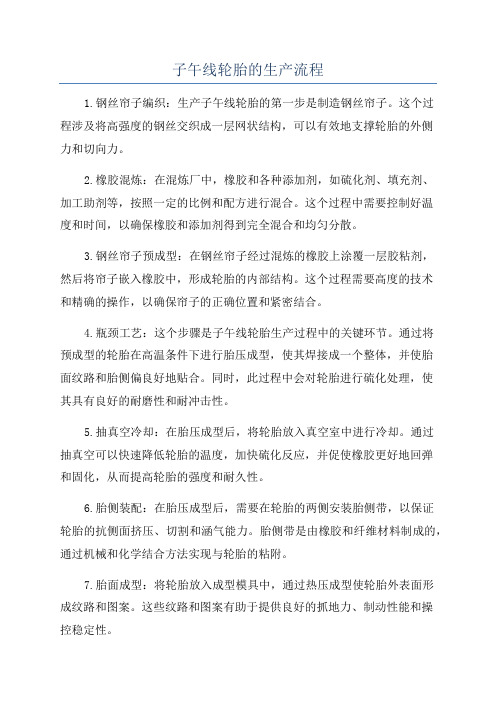
子午线轮胎的生产流程1.钢丝帘子编织:生产子午线轮胎的第一步是制造钢丝帘子。
这个过程涉及将高强度的钢丝交织成一层网状结构,可以有效地支撑轮胎的外侧力和切向力。
2.橡胶混炼:在混炼厂中,橡胶和各种添加剂,如硫化剂、填充剂、加工助剂等,按照一定的比例和配方进行混合。
这个过程中需要控制好温度和时间,以确保橡胶和添加剂得到完全混合和均匀分散。
3.钢丝帘子预成型:在钢丝帘子经过混炼的橡胶上涂覆一层胶粘剂,然后将帘子嵌入橡胶中,形成轮胎的内部结构。
这个过程需要高度的技术和精确的操作,以确保帘子的正确位置和紧密结合。
4.瓶颈工艺:这个步骤是子午线轮胎生产过程中的关键环节。
通过将预成型的轮胎在高温条件下进行胎压成型,使其焊接成一个整体,并使胎面纹路和胎侧偏良好地贴合。
同时,此过程中会对轮胎进行硫化处理,使其具有良好的耐磨性和耐冲击性。
5.抽真空冷却:在胎压成型后,将轮胎放入真空室中进行冷却。
通过抽真空可以快速降低轮胎的温度,加快硫化反应,并促使橡胶更好地回弹和固化,从而提高轮胎的强度和耐久性。
6.胎侧装配:在胎压成型后,需要在轮胎的两侧安装胎侧带,以保证轮胎的抗侧面挤压、切割和涵气能力。
胎侧带是由橡胶和纤维材料制成的,通过机械和化学结合方法实现与轮胎的粘附。
7.胎面成型:将轮胎放入成型模具中,通过热压成型使轮胎外表面形成纹路和图案。
这些纹路和图案有助于提供良好的抓地力、制动性能和操控稳定性。
8.胎面胶覆:在轮胎的胎面上喷涂一层胎面胶。
这一层胎面胶不仅能够降低胎面表面的温度,还可以提高轮胎的抓地力和减少轮胎的噪音。
9.胎侧胶覆:在轮胎的两侧涂覆一层胎侧胶,以提高轮胎的抗侧面老化和耐磨性。
10.胎面和胎侧烘干:将胎面和胎侧喷涂的胶层进行烘干,以使其完全固化和粘附到轮胎上。
11.动平衡:使用专用的设备对轮胎进行动平衡测试,以消除轮胎运转过程中的不平衡,确保其安全稳定的运行。
12.质检:对轮胎进行严格的质量检验,包括外观检查、尺寸测量、强度测试等。
轮胎胎面制造加工

轮胎胎面制造加工是现代汽车工业不可或缺的一环。
轮胎可以视为汽车的“鞋子”,直接关系到汽车的行驶质量、安全性和舒适性。
目前市面上的轮胎种类非常丰富,不同种类的轮胎对行驶的路况、速度、气温等条件有不同的要求。
胎面制造加工是轮胎生产过程中比较重要的一环,它直接影响到轮胎的使用寿命、性能和舒适性。
1. 胎面制造加工的主要工艺胎面制造加工是指对轮胎的胎面进行加工,以满足轮胎对路面的附着力、排水等要求。
目前,的主要工艺包括模切、刮痕、印刷和涂胶等四种工艺。
(1)模切模切是指在轮胎胎面上刻印和切割出需要的花纹和凹槽来,以提高轮胎的附着力和排水能力。
模切工艺是胎面制造加工中最常用的一种,也是最基础的一种。
在模切之前,需要先设计好轮胎胎面花纹的形状和规格,并制作成模具。
模具中的花纹和凹槽的形状和排列方式,直接决定了轮胎的附着力和排水能力。
模切工艺需要非常高的制模技术和切割精度,以保证胎面花纹的规格和形状的准确度。
(2)刮痕刮痕是指用刮刀将橡胶表层刮成不同形状的图案。
这种工艺可以改变胎面橡胶的表面形态,增强胎面橡胶的粘附力和抓地力,提高轮胎的附着力和稳定性。
刮痕工艺需要刮刀的切割效果非常准确,同时需要对橡胶的硬度、粘度等参数进行细致调控,才能制造出高质量的轮胎胎面。
(3)印刷印刷是指将色浆进行印刷,制造出不同颜色和形状的图案和文字。
这种工艺通常用来印制生产厂商的商标、轮胎的使用规格、速度等信息。
印刷工艺需要对色浆的粘度、流动性要求非常高,同时对印版的制作和印刷机的调试也需要非常细致和精确。
(4)涂胶涂胶是指在轮胎表面涂上一层胶液,以增强轮胎的附着力和抓地力。
涂胶可以把橡胶的粘附力和摩擦力增强到最大,从而提高轮胎在高速行驶、急转弯等情况下的稳定性和安全性。
涂胶工艺需要对胶液粘度、流动性有非常高的要求,同时也需要对涂胶温度进行精准控制,以避免胶液的变质和影响轮胎的质量。
2. 轮胎胎面设计的要点轮胎胎面设计是轮胎生产过程中的一个非常重要的环节。
橡胶轮胎和内胎的制造工艺
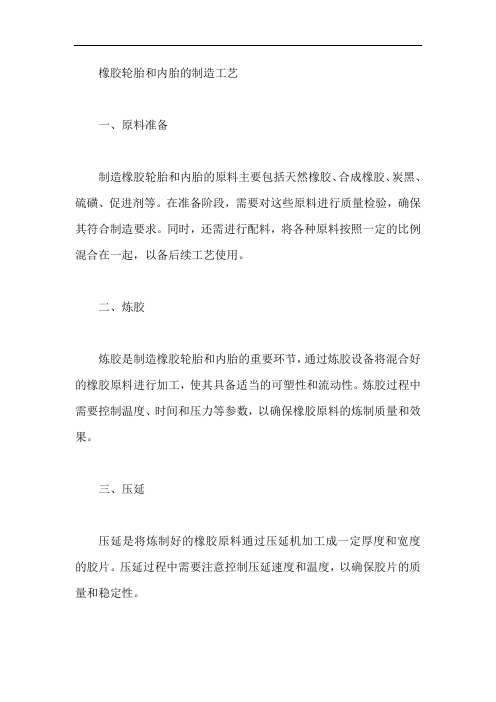
橡胶轮胎和内胎的制造工艺
一、原料准备
制造橡胶轮胎和内胎的原料主要包括天然橡胶、合成橡胶、炭黑、硫磺、促进剂等。
在准备阶段,需要对这些原料进行质量检验,确保其符合制造要求。
同时,还需进行配料,将各种原料按照一定的比例混合在一起,以备后续工艺使用。
二、炼胶
炼胶是制造橡胶轮胎和内胎的重要环节,通过炼胶设备将混合好的橡胶原料进行加工,使其具备适当的可塑性和流动性。
炼胶过程中需要控制温度、时间和压力等参数,以确保橡胶原料的炼制质量和效果。
三、压延
压延是将炼制好的橡胶原料通过压延机加工成一定厚度和宽度的胶片。
压延过程中需要注意控制压延速度和温度,以确保胶片的质量和稳定性。
四、裁断
裁断是将压延好的胶片按照所需形状和尺寸进行切割。
在裁断过程中,需要精确控制裁断尺寸和精度,以确保轮胎和内胎的制造质量。
五、硫化
硫化是制造橡胶轮胎和内胎的关键步骤,即将裁断好的胶片在一定温度和压力下进行化学反应,使橡胶原料固化成具有特定形状和性能的轮胎或内胎。
硫化过程中需要控制温度、时间和压力等参数,以确保轮胎或内胎的硫化质量和性能。
六、贴合
贴合是将硫化好的轮胎或内胎与相应的衬里或保护层进行粘贴。
贴合过程中需要注意控制贴合温度和压力,以确保衬里或保护层与轮胎或内胎的粘合牢固性和稳定性。
七、成型
成型是将贴合好的轮胎或内胎通过成型机加工成所需的形状和尺寸。
成型过程中需要控制成型温度和压力,以确保轮胎或内胎的形
状和尺寸精度。
同时,还需进行质量检验,确保成型后的轮胎或内胎符合产品要求。
轮胎加工工艺流程
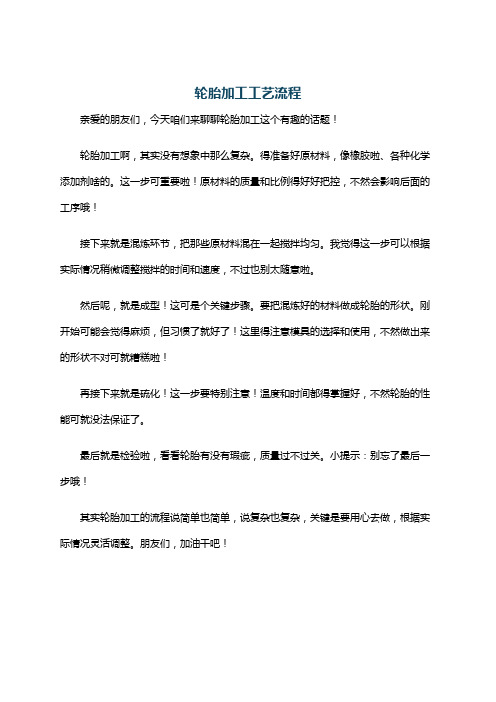
轮胎加工工艺流程
亲爱的朋友们,今天咱们来聊聊轮胎加工这个有趣的话题!
轮胎加工啊,其实没有想象中那么复杂。
得准备好原材料,像橡胶啦、各种化学添加剂啥的。
这一步可重要啦!原材料的质量和比例得好好把控,不然会影响后面的工序哦!
接下来就是混炼环节,把那些原材料混在一起搅拌均匀。
我觉得这一步可以根据实际情况稍微调整搅拌的时间和速度,不过也别太随意啦。
然后呢,就是成型!这可是个关键步骤。
要把混炼好的材料做成轮胎的形状。
刚开始可能会觉得麻烦,但习惯了就好了!这里得注意模具的选择和使用,不然做出来的形状不对可就糟糕啦!
再接下来就是硫化!这一步要特别注意!温度和时间都得掌握好,不然轮胎的性能可就没法保证了。
最后就是检验啦,看看轮胎有没有瑕疵,质量过不过关。
小提示:别忘了最后一步哦!
其实轮胎加工的流程说简单也简单,说复杂也复杂,关键是要用心去做,根据实际情况灵活调整。
朋友们,加油干吧!。
废旧轮胎加工流程

废旧轮胎加工流程
废旧轮胎加工流程如下:
1.利用轮胎劈顶机将轮胎切割成两半,便于后面破碎工作。
2.利用轮胎切条机将轮胎切成条状,方便后面轮胎切成块状。
3.利用轮胎打块机将轮胎打成胶块,轮胎胶块大小不一样,用途不一,需要的厂家也不一样。
4.轮胎颗粒机将轮胎打成颗粒,主要用于运动场所的填料,还可以做橡胶地砖、橡胶卷材等。
5.橡胶磨粉机将轮胎磨粉,轮胎胶粉可以用于再生胶、橡胶沥青添加剂,还可以用于橡胶产品的原材料。
6.钢丝分离机分离钢丝,分离出来的钢丝可以熔炉再造,或者钢丝切丸。
轮胎胎侧制造加工
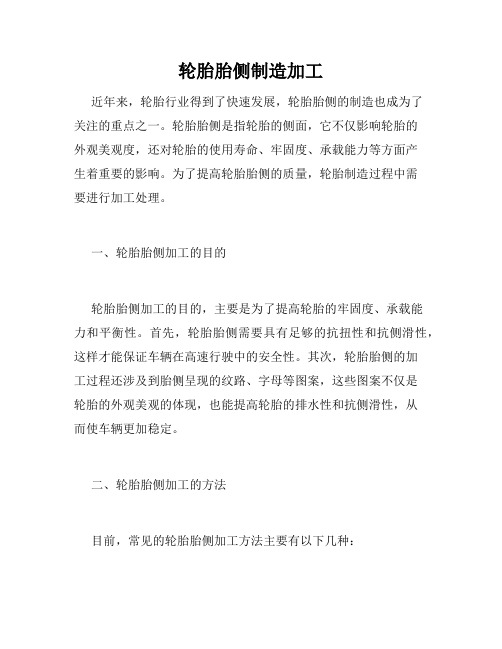
轮胎胎侧制造加工近年来,轮胎行业得到了快速发展,轮胎胎侧的制造也成为了关注的重点之一。
轮胎胎侧是指轮胎的侧面,它不仅影响轮胎的外观美观度,还对轮胎的使用寿命、牢固度、承载能力等方面产生着重要的影响。
为了提高轮胎胎侧的质量,轮胎制造过程中需要进行加工处理。
一、轮胎胎侧加工的目的轮胎胎侧加工的目的,主要是为了提高轮胎的牢固度、承载能力和平衡性。
首先,轮胎胎侧需要具有足够的抗扭性和抗侧滑性,这样才能保证车辆在高速行驶中的安全性。
其次,轮胎胎侧的加工过程还涉及到胎侧呈现的纹路、字母等图案,这些图案不仅是轮胎的外观美观的体现,也能提高轮胎的排水性和抗侧滑性,从而使车辆更加稳定。
二、轮胎胎侧加工的方法目前,常见的轮胎胎侧加工方法主要有以下几种:1. 胎侧成型:轮胎制造前,通过成型模具模压胎侧的形状、花纹和贴标,让轮胎胎侧呈现出生产制造的特定形状和外观。
2. 胎侧切割:轮胎制造的过程中,在确定轮胎胎侧尺寸和花纹后,使用专业设备对轮胎胎侧进行精确的切割加工,以保证胎侧的平整度和规格标准。
3. 胎侧刻字:根据轮胎制造商的要求,在胎侧进行钢印刻字或用橡胶挤出字芯的方法进行刻字,以达到生产要求和品牌宣传的效果。
4. 胎侧涂料:在轮胎制造完成后,对胎侧进行喷塑或涂抹,以达到美观效果和创造品牌识别度的目的。
以上几种方法各有优缺点,具体可以根据制造商要求和生产成本来选择适合的加工方法。
三、轮胎制造中的胎侧加工注意事项在轮胎制造中,胎侧加工的质量直接影响着轮胎的性能和使用寿命。
因此,轮胎制造中需要注意以下几个方面:1. 加工精度:轮胎胎侧的加工精度应该保证在规格范围内,以免因加工不当导致轮胎的使用安全问题。
2. 轮毂匹配性:轮胎的胎侧和轮毂之间的间隙应该合适,以提高轮胎与车轮的粘合度和牢固度。
3. 胎侧图案一致性:轮胎的每个胎侧花纹和字母应该完全一致,以保证轮胎的品质和外观。
4. 胎侧硬度一致性:在轮胎制造的过程中,胎侧硬度应该一致,以保证车辆平衡和稳定性。
轮胎轮辋制造加工
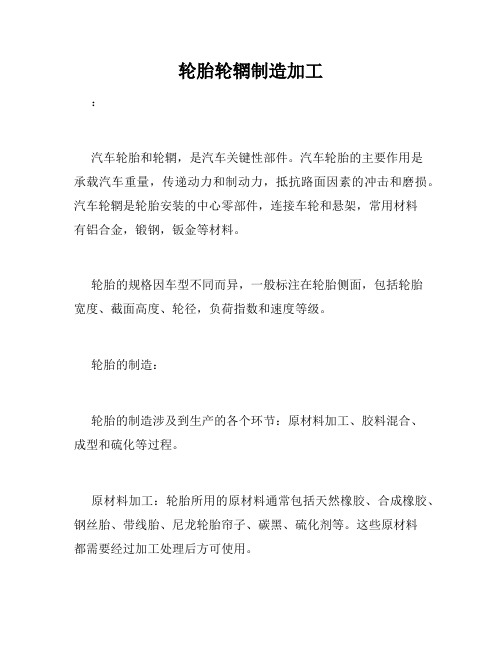
轮胎轮辋制造加工:汽车轮胎和轮辋,是汽车关键性部件。
汽车轮胎的主要作用是承载汽车重量,传递动力和制动力,抵抗路面因素的冲击和磨损。
汽车轮辋是轮胎安装的中心零部件,连接车轮和悬架,常用材料有铝合金,锻钢,钣金等材料。
轮胎的规格因车型不同而异,一般标注在轮胎侧面,包括轮胎宽度、截面高度、轮径,负荷指数和速度等级。
轮胎的制造:轮胎的制造涉及到生产的各个环节:原材料加工、胶料混合、成型和硫化等过程。
原材料加工:轮胎所用的原材料通常包括天然橡胶、合成橡胶、钢丝胎、带线胎、尼龙轮胎帘子、碳黑、硫化剂等。
这些原材料都需要经过加工处理后方可使用。
胶料混合:将橡胶磨粉和其他原材料混合成胶料,满足制造轮胎的工艺要求。
成型:胶料混合成型后,轮胎制造厂家采用高科技的成型技术将其制成一些充满空气的轮胎组件。
包括带钢圈,配重块,冲孔夹板等组件。
硫化:轮胎组件在压力和温度的作用下进行硫化。
硫化的目的是使胶料加热,挤压成型,锻造成为硫化过程中的终质。
轮辋的制造:汽车轮辋的制造一般分为铸造、锻造、压铸和焊接等类别。
铸造:铸造一般应用于大中型车辆的制造过程中,产生较大的压力和负载,铸造出来的轮辋强度高,性能好。
锻造:锻造一般应用于小型车辆的制造过程中,较轻易被扭曲变形的地方。
锻造的轮辋重量轻,强度也高。
压铸:压铸一般应用于高性能轮辋的制造,轻便而强度高。
焊接:焊接一般应用于特种车辆,比如坦克。
需要进行高比例的负载应用。
制造加工技术的发展差异:轮胎和轮辋这两个衔接部件,在制造上的使用了来自的不同加工技术。
行业需求、材料进步、科技发展、政策调动等因素均有所不同。
轮胎的制造工艺在灵活性和控制性方面卓越,包括芳香族化学、成型、硫化和smart轮胎技术。
尽管米其林的轮胎壁厚厚于其他生产商的轮胎,但是该公司增加了其轮胎的寿命以及轮胎刚性所产生的优势,这是其制造技术的特定示范。
轮辋的制造技术,则趋于通过精密制造技术和材料科学来提高产品性能,挑战是降低产量成本,并进一步增强其强度和扭转能力,同时提供高单元负荷和压缩等持续性的承载能力。
- 1、下载文档前请自行甄别文档内容的完整性,平台不提供额外的编辑、内容补充、找答案等附加服务。
- 2、"仅部分预览"的文档,不可在线预览部分如存在完整性等问题,可反馈申请退款(可完整预览的文档不适用该条件!)。
- 3、如文档侵犯您的权益,请联系客服反馈,我们会尽快为您处理(人工客服工作时间:9:00-18:30)。
山东大王职业学院毕业设计(论文)学系:机电工程系班级:08电气班姓名:徐加贵指导老师:李金花目录1、……………………………………………………引言2、……………………………………………………标题3、……………………………………………………正文4、………………………………………………参考文献5、…………………………………………………致谢词引言目前世界轮胎的发展方向主要体现在如下三个方面:①操控性更好(追求车人合一,即随心所欲的境界);②环境友好(轮胎生产、使用、报废均不污染环境);③跑气保用(或非充气)+智能化。
与此同时,世界轮胎新技术在如下三个方面也获得了许多突破性进展:④设计方法;⑤生产工艺;⑥测试方法。
轮胎设计新方法IT技术的发展与普及应用,促进了轮胎设计方法的研发,如今轮胎设计已进入了基於计算机平台的新时代。
在上世纪中叶,研发一种新的设计方法,从理念(亦即创新概念)到实用工具一般需要8年时间,而现在只需平均2年时间甚至更短。
现代轮胎设计引进了许多新技术元素,包括大型计算机、有限元分析、仿真模拟,从而改变了轮胎研发过程。
从图1可见,传统的研发过程中的前五个阶段(设计、样胎、试验、分析、确定)都与实物制造有关,而优化的研发过程中的前五个阶段(设计、工程建模、分析、确定)只需在计算机平台上进行,结果是节省了时间、成本,提高了工作效率,同时提高了结果可控度。
目前,轮胎制造业的加工工艺十分复杂,生产周期较长,既有连续的生产过程,又有离散的生产过程。
闭,目前尚处于粗放的生产经营管理模式阶段。
管理能力的不足和管理方式的低效是制约我国轮胎产业发展的一大瓶颈。
虽然有相当的轮胎生产企业拥有了企业资源计划系统(ERP)和过程轮胎的成型与新技术应用轮胎是汽车上最重要的组成部件之一,它的作用主要有:支持车辆的全部重量,承受汽车的负荷;传送牵引和制动的扭力,保证车轮与路面的附着力;减轻和吸收汽车在行驶时的震动和冲击力,防止汽车零部件受到剧烈震动和早期损坏,适应车辆的高速性能并降低行驶时的噪音,保证行驶的安全性、操纵稳定性、舒适性和节能经济性。
轮胎按照用途和组成分很多种,如下1、轮胎的分类1.1 按轮胎用途来分(1)轿车轮胎;(2)轻型载重汽车轮胎;(3)载重和公共汽车轮胎;(4)工程机械轮胎;(5)越野汽车轮胎;(6)农业和林业机械轮胎。
1.2 按胎体结构分(1)充气轮胎;(2)实心轮胎。
1.3 按胎体中帘线排列的方向分(1)普通斜交轮胎。
其外胎由胎面、帘布层、缓冲层及胎圈组成。
帘布层是外胎的骨架,用以保持外胎的形状和尺寸,通常由成双数的多层挂胶布用橡胶贴合而成,帘布的帘线与轮胎子午断面的交角一般为52~54度,相邻层帘线相交排列。
帘布层数愈多强度愈大,但弹性降低。
特点是胎面和胎侧的强度大,但胎侧刚度较大,舒适性差,由于高速时帘布层间移动与磨擦大,并不适合高速行驶。
随着子午线轮胎的不断改进,斜交轮胎将基本上被淘汰。
(2)子午线轮胎。
(在轮胎上用Redial表示)的特点是:帘布层帘线的排列方向与轮胎的子午断面一致。
由于帘线的这种排列,使帘线的强度能得到充分利用,因此,子午线轮胎的帘布层数一般比普通斜交轮胎的帘布层数可减少40~50%。
由于行驶时轮胎要承受较大的切向作用力,为保证帘线的稳固,在其外部又有若干层由高强度、不易拉伸的材料制成的带束层(又称箍紧层),其帘线方向与子午断面呈较大的交角。
优点是:接地面积大,附着性能好,胎面滑移小,对地面单位压力也小,因而滚动阻力小,使用寿命长;胎冠较厚且有坚硬的带束层,不易刺穿;行驶时变形小,可降低油耗3%~8%;径向弹性大,缓冲性能好,负荷能力较大。
缺点是:因胎侧较薄,胎冠较厚,在其与胎侧的过渡区易产生裂口。
侧面变形大,导致汽车的侧向稳定性差,制造技术要求高,成本也高。
(3)带束斜交轮胎。
带束斜交轮胎是介于普通斜交轮胎和子午线轮胎之间的一种折衷结构方案。
其帘布层的帘线与子午断面的交角比普通斜交轮胎小,比子午线轮胎的大。
因此,带束斜交轮胎的寿命和滚动阻力也介于上述两种轮胎之间,但是汽车侧向稳定性比子午线轮胎更好1.4 充气轮胎按组成结构分(1)有内胎的充气轮胎由内胎、外胎和胎垫组成。
内胎中充满压缩空气,外胎是用以保护内胎使不受外来损害的强度高而富有弹性的外壳,胎垫放在内胎和轮辋之间,防止内胎被轮辋及外胎的胎圈擦伤。
其主要缺点是行驶温度高,不适应高速行驶,不能充分保证行驶的安全性,使用时内胎在轮胎中处于伸张状态,略受穿刺便形成小孔,而使轮胎迅速降压。
(2)无内胎轮胎(俗称真空胎,在轮胎上用Tubeless表示)在外观上和结构上与有内胎轮胎近似,不同的是无内胎轮胎的内壁上附加了一层厚约2~3毫米的橡胶密封层,在密封层下面贴着一层用未硫化橡胶的特殊混合物制成的自粘层。
无内胎轮胎的构造见图③。
空气直接充入外胎内腔。
这样消除了内外胎之间的磨擦,并使热量直接从轮辋散出,比普通轮胎降温20%以上。
无内胎轮胎提高了行驶安全性,在穿孔较小时能够继续行驶,中途修理比有内胎轮胎容易,不需拆卸轮辋,因为有较好的柔软性,所以可改善轮胎的缓冲性能,提高轮胎的使用寿命。
2、轮胎型号的表示方法充气轮胎尺寸目前一般用英制为单位,但欧洲国家则常用公制。
高压胎一般用D ×B来表示,其中D表示轮胎直径的英寸数,B表示轮胎断面宽度的英寸数。
例如,34×7即表示轮胎外径D为34英寸,断面宽度B为7英寸。
汽车上常用的是低压胎,其尺寸标记用B—d表示,例如9.00—20,(B—d)即表示断面宽度B为9英寸,而轮辋直径d为20英寸。
高压胎、低压胎、超低压胎过去是按轮胎用标准气压来分类:一般0.5Mpaf至0.7Mpaf为高压轮胎;0.25-0.5Mpaf为低压轮胎;0.15Mpaf以下的为超低压轮胎。
但由于制造轮胎用的骨架材料的不断发展,如尼龙芳纶、钢丝帘布线的使用,轮胎负荷量的大幅度提高,相应的气压也提高了,而轮胎的缓冲性能仍在某种程度保留了原来同种规格低压胎的传统。
因此国内外还是把这种胎归于“低压胎”这一类,如国产9.00-20-14层级尼龙胎负荷2185kg,气压0.67Mpa仍归“低压胎”这一类。
凡轮胎轮辋15英寸以下的均为超低压轮胎。
我国的子午线轮胎的表示方法则用9.00R20,11.00R20,12.00R20等表示。
由于轮胎断面轮廓不断演变和发展,原来的传统标记法已经不能适应新的要求,所以国际标准做出明确规定,采用新的轮胎规格标记法。
除保留规格仍用原标记外,在ISO 国际标准中,轮胎编号表示为(断面宽度)/(扁平率)(轮胎结构标记号)(适用轮胎直径)(载荷指数)(速度记号)。
比如某轮胎标识为“P225/65R1689H”,其中:“P”是指轿车轮胎(用以区别卡车或其他车型适用的轮胎)。
“225”指的是轮胎断面的宽度,是两个胎侧之间的宽度(以毫米为单位)。
此宽度随轮胎所匹配轮辋宽度的不同而不同:宽轮辋配宽轮胎,窄轮辋配窄轮胎。
一般在胎侧上所标示的胎宽,是指当轮胎安装到所建议宽度的轮辋时的宽度。
“65”是轮胎的扁平比,是胎宽与胎高的比例,这里指胎高占胎宽的65%,数值越小,越显扁平。
“R”是指轮胎的结构,表示此轮胎为子午线结构,也就是说它的帘布层是呈辐射状排布在胎体内的。
“B”表示轮胎为斜交结构,目前斜交结构的轿车轮胎已不复存在。
“16”表示轮辋直径(以英寸为单位),此轮胎必须匹配16英寸的轮辋,否则无法安装。
“89”表示载重指数:此轮胎最高载重为580kg。
不同的载重指数代表不同的最高载重。
“H”是速度标记号,速度代号最高时速(km/h)详见下表:轮胎表面都带有胎面磨损标志,一般情况下,每一条轮胎上每隔60°就在它的胎侧上有一个小“△”符号,共有6个小“△”,在小“△”符号所对着的胎冠部分,花纹下刻有花纹的磨损残留深度极限。
就是告诉轮胎使用者轮胎使用磨耗不能超过的危险信号,否则轮胎不耐刺扎是伤及缓冲层和带束层,降低轮胎使用的安全系数和翻新次数。
在轮胎的胎侧部位有一组重要的组字标记,它是生产时间、生产班组的编号。
这组编号有两方面的作用:一是轮胎出现质量问题便于检查轮胎是什么时间、哪个班组生产的,便于追查责任;另一方面给翻新提供时限要求。
轮胎工业发展到如今已逾百年。
走过上百年的历程,传统轮胎生产工艺至今已日臻完善,从胶料混炼、部件准备(压延、压出)、成型、硫化到成品质量检验,各个阶段的自动化程度都非常高。
任何事物在发展到一定历史高度之后,再继续往更高的目标迈进,其难度将非常大。
这时,若能够从另一个角度或换一种方法去思考和突破,则往往会有更好的效果和较大的收获。
全新概念轮胎制造工艺技术就是在这样的背景下,遵循这样的思路开发出来的。
与传统的轮胎制造工艺技术相比,上述全新概念工艺技术普遍具有节省投资、设备占地面积少、生产效率高、降低成本的优势。
下面,介绍几种全新概念轮胎制造工艺技术经济指标:一、米其林C3M技术C3M的全称为:Command+Control+Communication&Manufacture;建议译为:指挥、控制、通讯及制造一体化系统。
C3M有如下5项技术要点:①连续低温混炼;②直接压出橡胶件;③成型鼓上编织/缠绕骨架层;④预硫化环状胎面;⑤轮胎电热硫化。
C3M的关键设备是特种编织机和挤出机。
C3M技术通过以成型鼓为核心,合理配置特种编织机组和挤出机组而得以实现。
特种编织机环绕成型鼓编织无接头环形胎体帘布层和带束层,并环绕成型鼓缠绕钢丝得到钢丝圈。
挤出机组连续低温(90℃以下)混炼胶料,压出胎侧、三角胶条以及其他橡胶件。
C3M的工艺特点是:部件既不经过冷却/停放,也不需要再加工或预装配,直接送到成型鼓上一次性完成轮胎成型。
在成型过程中,成型鼓一直处于加热状态,胎胚在成型的同时被预硫化从而达到定型。
米其林于1982年开始研究C3M技术,1992年宣布研究成功,次年在总部所在地--克莱蒙费朗(Clermont-Ferrand)建第一间C3M厂,1998年底已发展到7间厂,如图2所示,C3M技术通过以成型鼓为核心配置特种编织机组和挤出机组,实现节能、高效、高精度的生产模式。
二、大陆MMP技术MMP的全称为:Modular Manufacturing Process;建议译为:积木式成型法。
众所周知,传统的轮胎生产工艺由四大工序组成:①塑/混炼;②压延和压出;③成型;④硫化。
现有的轮胎厂,除部分通过购人成品混炼胶而省缺第一道工序外,大多数是上述四道工序全部齐备。
MMP打破传统轮胎厂四大工序齐备的模式,将四大工序分割成两大块来操作。
第一块包括了传统工艺的第一道工序(塑/混炼)、第二道工序(压延和压出)以及第三道工序的前半部分(胎体成型),第二块包括了传统工艺的第三道工序的后半部分(贴带束层、上胎面)和第四道工序(硫化);执行第一块生产任务的工厂被称之为"平台",执行第二块生产任务的工厂被称之为"卫星厂"。