总装车间SPS系统的优化设计与实现方法
SPS系统总装车间运行方式分析
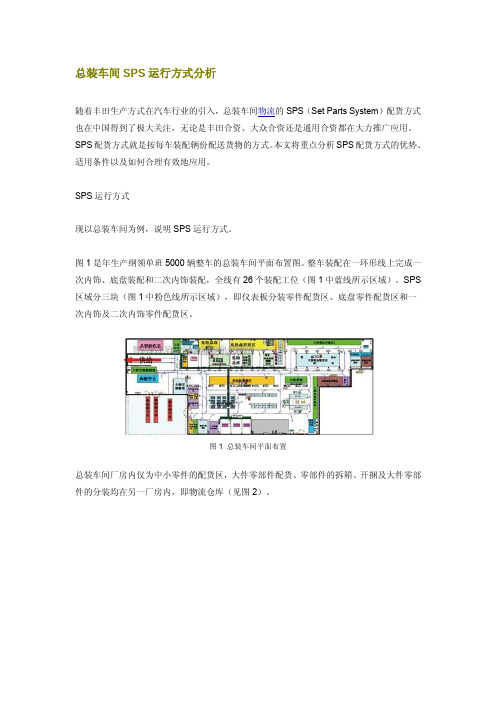
总装车间SPS运行方式分析随着丰田生产方式在汽车行业的引入,总装车间物流的SPS(Set Parts System)配货方式也在中国得到了极大关注,无论是丰田合资、大众合资还是通用合资都在大力推广应用。
SPS配货方式就是按每车装配辆份配送货物的方式。
本文将重点分析SPS配货方式的优势、适用条件以及如何合理有效地应用。
SPS运行方式现以总装车间为例,说明SPS运行方式。
图1是年生产纲领单班5000辆整车的总装车间平面布置图。
整车装配在一环形线上完成一次内饰、底盘装配和二次内饰装配,全线有26个装配工位(图1中蓝线所示区域)。
SPS 区域分三块(图1中粉色线所示区域),即仪表板分装零件配货区、底盘零件配货区和一次内饰及二次内饰零件配货区。
图1 总装车间平面布置总装车间厂房内仅为中小零件的配货区,大件零部件配货、零部件的拆箱、开捆及大件零部件的分装均在另一厂房内,即物流仓库(见图2)。
图2 物流仓库平面布置1.配货顺序总装车间的物流系统在信息控制系统指导下,有条不紊地从仓库货架取出所需零件,按SPS 配货方式送到指定工位,配货顺序如下:(1)中央控制室(CCR)根据市场分析及订单情况安排生产计划,并将生产计划的车辆顺序信息向总装车间情报中心传递。
(2)车辆顺序信息传到总装车间情报中心,由情报信息员根据实际工位查找相应信息指示卡。
(3)情报信息员将信息指示卡投递到SPS供应管理板处。
(4)物流配货人员从SPS供给管理板处获取信息选取配货指示票,配货指示票上标有某个车型在某个工程装配零件的种类和数量。
(5)物流人员按照配货指示票到SPS区配货,放在相应的台车上,物流人员将部品放到运输台车上。
(6)配完后放在供给待发区,物流人员将零件供给到生产线的起始位置。
(7)物流人员将空台车返回到零件供给待发区,通过SPS方式配货完成。
2. 物料配送的四个步骤在图3的SPS物料及信息流程图中我们可以看到,所有的物料都是经过四个步骤完成运送的:接收物料需求信息(图3中①);按需求信息进行配货(图3中②);将配货送到装配线的接收端(图3中③);随装配线完成装配工序(图3中④)。
基于精益思想的汽车生产物流“SPS系统”方案设计研究

2016年12月基于精益思想的汽车生产物流“SPS 系统”方案设计研究梁飞陈进军(湖南现代物流职业技术学院,湖南长沙410131)摘要:基于精益思想,在汽车生产物流中通过“SPS 系统”方案设计和实施,可以提高装配线的柔性和工作效率。
通过分析“SPS 系统”设计的意义、原理、具体要求和设计原则,并以某汽车生产物流的“SPS 系统”设计为例,充分说明“SPS 系统”的运用对物流效率的改善明显。
关键词:SPS ;方案;设计1绪论在汽车生产制造中,如何利用并不宽裕的物料存储区域,提高装配线的柔性和工作效率,是一个必须思考的课题。
日本的丰田公司于上世纪50年代创建一种全新的生产方式——精益生产,在其精益生产的理念中提出一个利于配料供给的方式——随行配料系统(Stochastic proportioning system ),以下随行配料系统简写为“SPS 系统”,该系统能减少配料者取件距离,减少工作工时,提高工作效率。
2SPS 系统方案设计的意义汽车生产物流的复杂性是行业公认的,多品种混流生产下,车型增多,使得线边的货架不断增多,车间现场拥挤、视野受限。
在这种混流生产方式下的物流也更为复杂,在总装车间采用SPS 系统,走精益物流之路,是汽车生产物流发展的方向。
XX 公司A 工厂的建厂理念是紧凑型工厂、精益型工厂,为解决因车位减少而导致的零件无法在线边布置,以及大量采用同步造成物流成本的大幅上升的问题,XX 公司A 工厂决定导入集配方式以实现零件上线。
这一集配方式的运用,可以解决线边物流面积不足的问题,减少线上员工拿取零件外移距离,降低劳动强度,降低位移及包装拆卸等带来的不增值时间,降低装配员工拿取零件出错率,提高装配质量。
3SPS 系统概述3.1SPS 系统组成SPS 系统由平面布局、AGV 物料传输系统、料车设计以及亮灯配货系统组成,是一种在生产物流中面向生产线成组供料的一种物料配送方式。
通过系统规划布局集配区的面积和位置,设计适宜的料车,优化AGV 物料传输系统的程序,并通过亮灯配货系统对零件的差错进行警示,防止出差错,从而系统性的提高物料配送效率。
商用车总装内饰线SPS物料供给应用研究
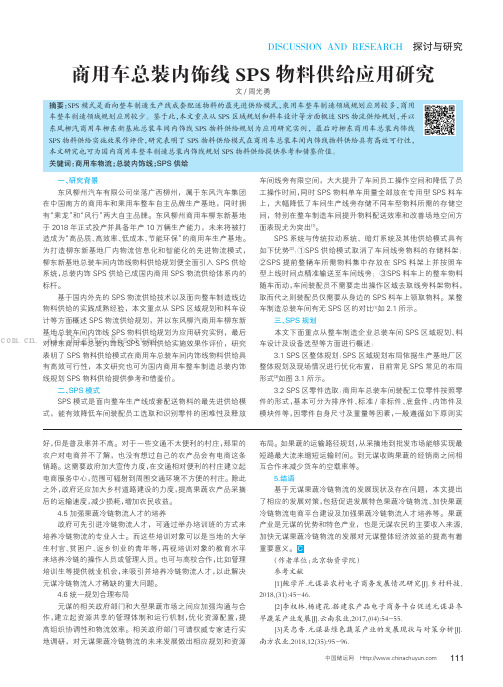
中国储运网H t t p ://w w w .c h i n a c h u y u n .c o mD I S C U S S I O N A N D RE S E A R C H 探讨与研究好,但是普及率并不高。
对于一些交通不太便利的村庄,那里的农户对电商并不了解,也没有想过自己的农产品会有电商这条销路。
这需要政府加大宣传力度,在交通相对便利的村庄建立起电商服务中心,范围可辐射到周围交通环境不方便的村庄。
除此之外,政府还应加大乡村道路建设的力度,提高果蔬农产品采摘后的运输速度,减少损耗,增加农民收益。
4.5加强果蔬冷链物流人才的培养政府可先引进冷链物流人才,可通过举办培训班的方式来培养冷链物流的专业人士。
而这些培训对象可以是当地的大学生村官、贫困户、返乡创业的青年等,再视培训对象的教育水平来培养冷链的操作人员或管理人员。
也可与高校合作,比如管理培训生等提供就业机会,来吸引并培养冷链物流人才,以此解决元谋冷链物流人才稀缺的重大问题。
4.6统一规划合理布局元谋的相关政府部门和大型果蔬市场之间应加强沟通与合作,建立起资源共享的管理体制和运行机制,优化资源配置,提高组织协调性和物流效率。
相关政府部门可请权威专家进行实地调研,对元谋果蔬冷链物流的未来发展做出相应规划和资源布局。
如果蔬的运输路径规划,从采摘地到批发市场能够实现最短路最大流来缩短运输时间。
到元谋收购果蔬的经销商之间相互合作来减少货车的空载率等。
5.结语基于元谋果蔬冷链物流的发展现状及存在问题,本文提出了相应的发展对策,包括促进发展特色果蔬冷链物流、加快果蔬冷链物流电商平台建设及加强果蔬冷链物流人才培养等。
果蔬产业是元谋的优势和特色产业,也是元谋农民的主要收入来源,加快元谋果蔬冷链物流的发展对元谋整体经济效益的提高有着重要意义。
C(作者单位:北京物资学院)参考文献[1]鲍学芹.元谋县农村电子商务发展情况研究[J ].乡村科技,2018,(31):45-46.[2]李权林,杨建花.搭建农产品电子商务平台促进元谋县冬早蔬菜产业发展[J ].云南农业,2017,(04):54-55.[3]吴忠香.元谋县绿色蔬菜产业的发展现状与对策分析[J ].南方农业,2018,12(35):95-96.一、研究背景东风柳州汽车有限公司坐落广西柳州,属于东风汽车集团在中国南方的商用车和乘用车整车自主品牌生产基地,同时拥有“乘龙”和“风行”两大自主品牌。
物流--“SPS推进”步骤
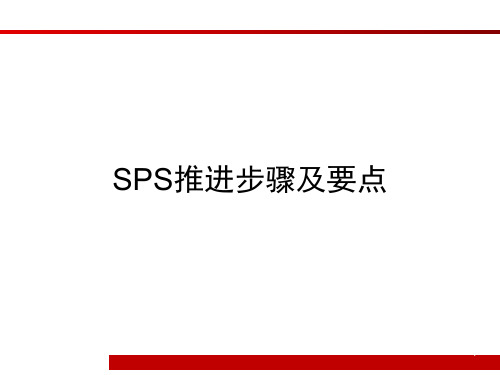
5
三、SPS推进步骤二:前期调研
1.设备情况 ① 随行台车与生产线联动 板链:台车置于两台车身之间 非板链:台车置于线侧,与生产线联动 ② PVC板、线棒的提供商,用于器具制作
2.T-A储存线在制情况 用于计算SPS配台提前期,判断SPS实施的生产线范围
3.物流仓库 确定SPS配台区域
4.IT系统 现有生产系统、物流系统的功能
2S0PS台2划.车 要开 连 员计接 包划时 :装间袋口(一袋)
0
秒/回
3秒
2空 2 箱返开还关时器 间 具门(包含0四8/1个 月 开1周关2)周 25月3周
秒/箱 3月10 秒
4周 1周 2周 3周 4周 1周
4月
2周 3周
4周
1周
5月
2周 3周
4周
1周
6月
2周 3周
4周
1周
7月
2周 3周
4周
7
四、SPS推进步骤三:基础数据的建立(SPS前提)
3.实施SPS部品明细筛选 ① 生产线选择:底盘线不可;生产提前期<物流周期不可 ② 部品选择:大物、标准件不可
4.部品明细的维护管理 ① 专门部门、专门担当负责部品明细的管理 ② 前期建立流程贯彻实施
此步骤是实施SPS的前提,也是保证配送准确率的前提
确定质量检查 时间
确定标准 在制品
编制标准作业 组合表
确定节拍内工 作顺序
确定安全注意 事项
编制标准 作业卡
细化操作 要点
编制标准 要领书
14
类别 1.行走
序号
操作描述பைடு நூலகம்
14 行走(每米)
15 行走(每步)
原单位 0.9 秒 0.6 秒
SGMW总装车间SPS运行分析
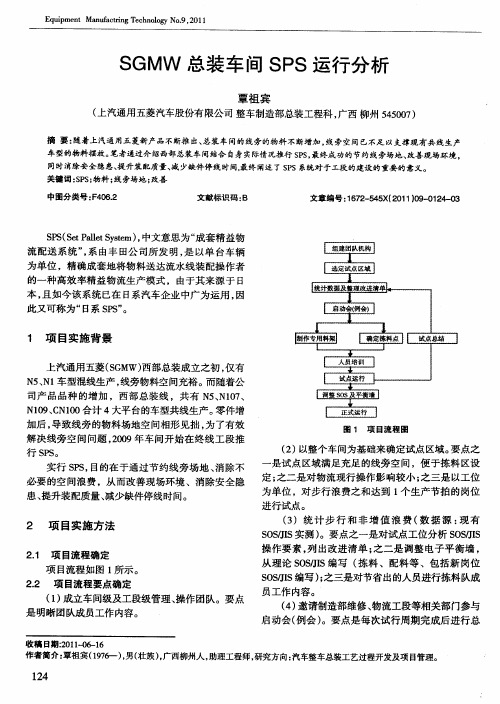
《 装备制造技术)0 1 ) 1 年第 9 2 期
结例会 , 为下次试行作准备 。 () 5 制作专用料架 。要点之一是确定试点物料 ; 同时 , 节约 出来 的空 间 , 建立起 了班组 园地 , 在 班组 园地内放 置了一些桌凳 ,让员工能在一些 短暂 0 n m 能够坐下休息 , 消除 之二是按试点物料形态制作专用料架及料盒 ( 注意 的停线和 2 i 停线休息时间 , 保护零件质量 ) ;之三是 由于线旁料架减少或取消 , 了坐在料架的安全隐患 。 需要为试点工位制作专用料架 、 工具盒 、 腰包等 。 32 提 升装 配品质 - () 6 确定 SS拣料点。 I 要点之一是规划拣料点料 在未实行 S 之前 , S I 每个 岗位都是 自己拿物料 、
架摆放 ; 之二是与物流确定料架上物料摆放 , 便于物
料 配送 。
自己装 配 、 自己检查 , 所有 的品质控制环节 , 全部 由 本 岗位的员工来执行 。而单纯依靠一个人员来 保障
一
道工序的品质 ,尤其对一些劳动强度 比较 大的岗 是 S 拣员工 S s I 操作培训 ; S I O ,S J 之三是各试点工位 位 , 在每天数 百次的重复操 作 中 , 相对而言 , 出错 的 s s I 操作培训。 o /S J 几率还是 比较高的。 () 8 试点运行。 要点之一是初次试点运行使用班 而通过进行 S , S I 将一些关键 岗位和十分消耗体
此又 可称 为 “ 日系 S s 。 P ”
1 项 目实施背景
上汽通用五菱(G w) s M 西部总装 成立之初 , 仅有
N 、1 5 N 车型混线生产 , 线旁物料空间充裕 。 而随着公 司产品品种 的增加 ,西部总装 线 ,共有 N 、 17 5N 0 、 Nl9 C 0 o 、 N10合计 4大平 台的车型 共 线生 产 。 件 增 零 加后 , 导致线旁 的物料场地空间相形见拙 , 了有效 为
随行配料系统(SPS)布局方案设计
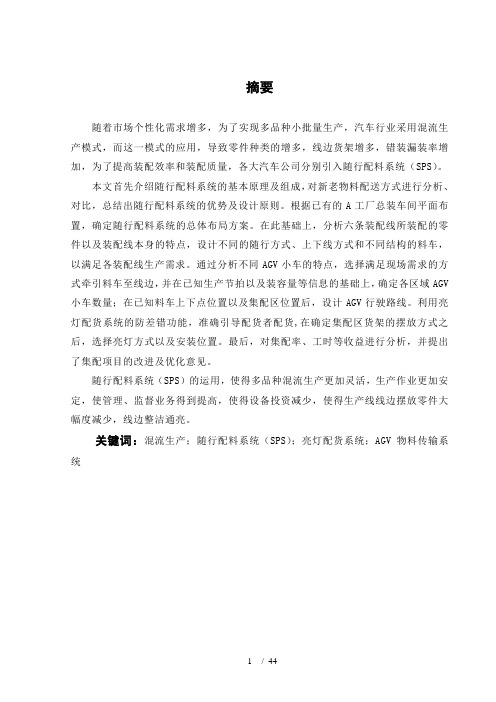
摘要随着市场个性化需求增多,为了实现多品种小批量生产,汽车行业采用混流生产模式,而这一模式的应用,导致零件种类的增多,线边货架增多,错装漏装率增加,为了提高装配效率和装配质量,各大汽车公司分别引入随行配料系统(SPS)。
本文首先介绍随行配料系统的基本原理及组成,对新老物料配送方式进行分析、对比,总结出随行配料系统的优势及设计原则。
根据已有的A工厂总装车间平面布置,确定随行配料系统的总体布局方案。
在此基础上,分析六条装配线所装配的零件以及装配线本身的特点,设计不同的随行方式、上下线方式和不同结构的料车,以满足各装配线生产需求。
通过分析不同AGV小车的特点,选择满足现场需求的方式牵引料车至线边,并在已知生产节拍以及装容量等信息的基础上,确定各区域AGV 小车数量;在已知料车上下点位置以及集配区位置后,设计AGV行驶路线。
利用亮灯配货系统的防差错功能,准确引导配货者配货,在确定集配区货架的摆放方式之后,选择亮灯方式以及安装位置。
最后,对集配率、工时等收益进行分析,并提出了集配项目的改进及优化意见。
随行配料系统(SPS)的运用,使得多品种混流生产更加灵活,生产作业更加安定,使管理、监督业务得到提高,使得设备投资减少,使得生产线线边摆放零件大幅度减少,线边整洁通亮。
关键词:混流生产;随行配料系统(SPS);亮灯配货系统;AGV物料传输系统AbstractWith the increasing market demand for personalized, in order to achieve more varieties of small batch production, the automotive industry using mixed production mode, and the application of this model, leading to an increase in types of parts, wire shelf edge increases, the wrong equipment installed leak rate increase, in order to improve assembly efficiency and assembly quality, the major car companies were introducing set part supply (SPS).This article introduces the basic principles of the set part supply (SPS) and its composition, comparing and analyzing the new and old material distribution methods, summarizing as well the advantages and design principles of the system (SPS). The overall layout of the set part supply (SPS) program is determined on the basis of the existing a factory assembly shop layout. Six assembly lines and their characteristics are analyzed with the aim of designing different patterns and structures to meet the demand of production lines. The characteristics of different AGV cars are analyzed, the AGV car with the pattern top traction is selected, sending the materials to the line by using the mode of tape navigation.Based on the known production rhythm and assembly capacity, the number of AGV cars is fixed. The AGV route is designed after confirming the position of the points on the material cars and the assembly location. The workers can accurately distribute the parts by making use of the light picking system. After fixing the mode of arrangement, the light-on pattern and installation position can be selected. Finally, the earnings such as assembly rates, working hours are calculated, and then some ideas and suggestions are proposed towards the assembly project.With the use of the set part supply (SPS), the multi-species mixed production becomes more flexible, the operation more stable, and the management and supervision business is improved. Meanwhile, reduce greatly the equipment investment and the number of the parts on the line side, which make the line side more clean and tidy.Keywords:mixed production; set part supply (SPS); the lights picking system; AGV cars目录第一章概论................................................... - 1 -1.1 论文研究的意义............................................. - 1 -1.2 随行配料系统(SPS)国内外现状.............................. - 1 -1.3 论文的主要内容............................................. - 2 - 第二章随行配料系统(SPS)介绍................................ - 3 -2.1 随行配料系统(SPS)组成.................................... - 4 -2.2 随行配料系统(SPS)原理.................................... - 4 -2.3 随行配料系统(SPS)优势分析................................ - 5 -2.4 随行配料系统(SPS)设计要求................................ - 5 -2.5 本章小结................................................... - 6 - 第三章随行配料系统(SPS)布局方案设计........................ - 6 -3.1 A工厂总装车间平面布置图.................................... - 7 -3.2 随行配料系统(SPS)布局设计方案............................ - 7 -3.3 本章小结................................................... - 8 - 第四章料车设计............................................... - 9 -4.1 料车的设计原则............................................. - 9 -4.2 六个区域料车设计........................................... - 9 -4.2.1 HC1料车.............................................. - 9 -4.2.2 HC2料车............................................. - 11 -4.2.3 PDB料车............................................. - 12 -4.2.4 POR料车............................................. - 13 -4.2.5 MV1料车............................................. - 15 -4.2.6 MV2料车............................................. - 16 -4.3 本章小结.................................................. - 17 - 第五章 AGV物料传输系统....................................... - 17 -5.1 AGV物料传输系统设计原则................................... - 17 -5.2 AGV小车设计............................................... - 18 -5.2.1 AGV小车选择......................................... - 18 -5.2.2 AGV数量确定......................................... - 18 -5.3 AGV行驶路线确定........................................... - 20 -5.4 本章小结.................................................. - 21 - 第六章亮灯配货系统.......................................... - 22 -6.1 亮灯配货系统应用背景及原理................................ - 22 -6.2 集配区零件布置............................................ - 23 -6.2.1 布置原则............................................. - 23 -6.2.2 布置信息............................................. - 23 -6.2.3 平面布置图确定....................................... - 24 -6.3 亮灯方式及安装位置........................................ - 26 -6.4 本章小结.................................................. - 28 - 第七章随行配料系统(SPS)成效............................... - 29 -7.1 XX公司A工厂总装车间集配信息.............................. - 29 -7.2 总体收益.................................................. - 30 - 第八章结论.................................................. - 31 -结束语....................................................... - 32 -致谢......................................................... - 33 -参考文献..................................................... - 34 -附录1 ....................................................... - 34 -第一章概论在现今汽车生产中,如何利用并不宽裕的物料存储区域,提高装配线的柔性和工作效率,这是现如今每一个汽车公司未来发展的方向。
汽车总装车间SPS实施运行探讨

1 ) 按 零部 件种 类摆 放 : 是在 S P S 集 配 区 内将 所 有车 型 的零 部 件 按 照种 类 进行 区分 , 比如 , 所 有车 型 的 C柱饰 板 都 在某 一 区域集 中放 置 。这种 布置 可 使得 部品放 置 比较 紧密 , 节 省空 间 , 但 作业 者选 取部 品时 的步 行距 离 比较 长。 2) 按 车 型摆 放 : 是在 S P S 集 配 区内将部 品按 车型摆 放 的方 式, 具体讲 , 就 是 把 某一 车 型 的所 有 零 部件 都 放 在 一 个 区 域 , 另外 车 型 的零 部 件 放置 在 另外 的区 域 。这种 置 方 式可 使 得 零部 件放 置 比较 宽松 , 浪费 空 间 , 但作 业 者选 取 零 部件 时 的步 行距 离较 短 。
一
种先进 的 物流输 送 方式 。
关键词
S P S ; 物料 ; 信 息化 : 防错 文 献标 识码 : A 文 章编 号 : 1 6 7 1 — 7 5 9 7( 2 0 1 3 )1 2 — 0 1 6 8 一 O 1
中图分 类号 : 0 4 6 8 . 2
S P S( S E T P A R T S S U P P L Y) 来 自于 日本 丰 田 , 是一 种 物料 单 辆 份 向生产 线 准 时化 配 送 的 方式 ,由于 S P S区临 近 生 产 线 , S P S区 的物 流 作 业人 员 按 照 生 产 指示 ( 该 指示 根 据 车辆 顺 序 生 成 并 按 下线 实绩 控 制 进度 )在 货架 上 拣 取 一套 零 部件 放 于专 用 的物 流 周转 台 车 中 , 并送 到线 边 , 实 现零 部 件 小批 量 多 频 次 的 输送 , 循 环流转 。
ห้องสมุดไป่ตู้
物流--“SPS推进”步骤
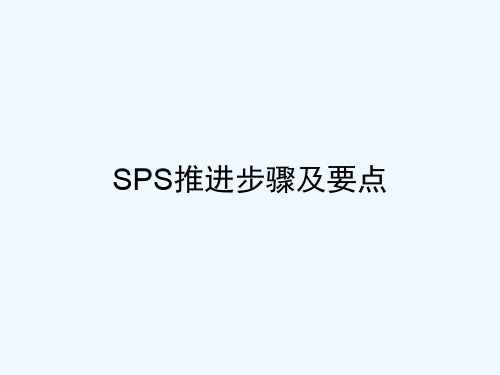
② 大日程点检是项目推进的手段
纲领 计划 目标 里程碑
大日程点检是确保项目按计划顺利推进的手段,以大日程点检为 载体,使信息在各领域充分共享,达到沟通、协调的目的
③ 以周为单位的推进日程
④ “五步工作法”
提出
物流项目第 一次大会
明确提 出∶“五步工 作法是物流项 目推进的工作 方法”
五步工作法
SPS推进步骤及要点
一、SPS推进条件
1.体制保障:公司全体部门统一认识·参与 ① SPS对公司的优势 ② SPS带来的人员、设备设施的投入
2.对部分业务流程的现状进行变革 SPS是内物流方式的一种,最为精确,要求基础管理的水平 ① 部品明细管理 ② 生产管理 ③ 设变管理 ④ 装配工艺管理 ⑤ 部品质量管理
二、SPS推进步骤一:推进方法建立
1.推进体制搭建 ① 直管生产副总作为项目组领导 ② 制造技术部作为推进部门 ③ 体制含:总装、技术、质量、IT、人力、采购部门,确定负责人
2.推进方法的建立 ① 会议:月度例会+周例会 月度例会:副总及高级经理参加 周例会:项目担当参加 ② 大日程+课题管理表
3.大日程编制 ① 大日程管理是项目推进的工具
李项
杨熙宏 殷学龙
日期 2008.4.6 2008.4.6 2008.4.6 2008.4.6 2008.4.6 2008.4.6 2008.4.6 2008.4.6 2008.04.06 物流项项目 目主主查查HQ3生管物流科人H事 Q3总部装车间 工工 业工业程工 科 程整科车物流组供应计物划信流息组组 供应构物内 流组物流内组物流组 主担 主担当当
1.信息指示类别: 是指示物流作业的一种信息表达方式,包括:零件配货指示、配货作业节拍
汽车行业厂内精益物流、精益生产(三) SPS规划要点

汽车行业厂内精益物流、精益生产(三) SPS规划要点精益管理顾问 宋文强 (原创)SPS单辆份成套供应是一种非常符合精益理念的物料上线方式,与批量补货、线边暂存相比,更有小批量(单辆份)、准时化(同步上线、物料随行)等特点。
但是,SPS在企业中的应用不是一蹴而就的,需要进行详细规划、精心准备才行。
第一,确定需要实施SPS的零部件不是所有零件都适用SPS,一般讲,体积较小或中等,有装配关系,且质量稳定的专用零部件比较合适。
通用零部件和标准件不容易拿错,所以可以不采用SPS。
因为SPS是一种管理成本比较高的补货方式,所以SPS同步台车容量有限的情况下,可以不优先考虑。
体积太大,像座椅等,不适合物料随行,可以采用JIS同步顺序上线方式。
质量稳定很重要,由于一次只供应单辆份零部件,发现质量问题后没有可供更换的同种零部件。
考虑到零部件的这些特点,一般来讲,企业先推进SPS的生产线是内饰线和车门线中的一部分工位。
第二,设计物料台车和料箱确定了要推进SPS的工位和物料,就要考虑设计物料台车和料箱。
由于是单辆份供应,所以数量不需要太多计算,但放置方法是个大问题。
总体来讲,料箱的外部大小要基本一致或只有几种规格,这样便于料箱与台车的配载。
需要精心设计的是料箱内部的隔断方法或衬垫形式。
首先,质量总是最重要的,汽车行业尤其如此,所以物料在拣配过程、搬运过程、拿取装配过程,要不容易磕碰。
其次,零部件放置既要放置整齐、节省体积,又要便于配载、拿取。
再次,类似零部件不能容易拿错,所以,车身左侧零部件和车身右侧零部件有时需要用可视化的方法进行区分。
比如:在丰田,绿色料箱放置车身左侧的零部件,蓝色料箱放置车身右侧的零部件。
物料台车的设计也很重要,一般为多层设计,既要容纳较多料箱,又要保证在搬运、随行的过程中保持稳定性和通过性。
第三,确定拣配区域位置SPS拣配区域的确定是个较大的决策,需要高层领导拍板。
SPS拣配区域的位置决策有两种:一种是相对集中式,另一种是分散式。
车间sps运作流程
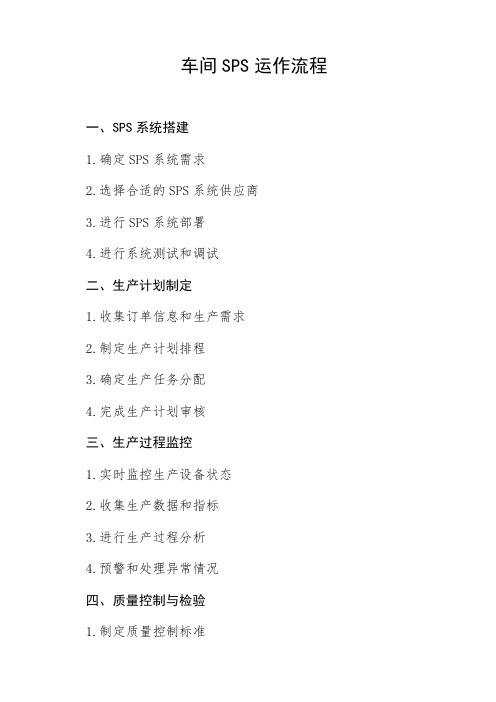
车间SPS运作流程
一、SPS系统搭建
1.确定SPS系统需求
2.选择合适的SPS系统供应商
3.进行SPS系统部署
4.进行系统测试和调试
二、生产计划制定
1.收集订单信息和生产需求
2.制定生产计划排程
3.确定生产任务分配
4.完成生产计划审核
三、生产过程监控
1.实时监控生产设备状态
2.收集生产数据和指标
3.进行生产过程分析
4.预警和处理异常情况
四、质量控制与检验
1.制定质量控制标准
2.进行生产过程质量监控
3.进行产品质量检验
4.处理质量异常问题
五、故障排除与维护
1.实施设备故障排查
2.进行设备维护保养
3.制定设备维护计划
4.处理设备故障和修复
六、数据分析与优化
1.收集生产数据
2.进行数据分析和挖掘
3.发现生产优化机会
4.实施生产流程优化措施。
总装车间SPS运行方式分析
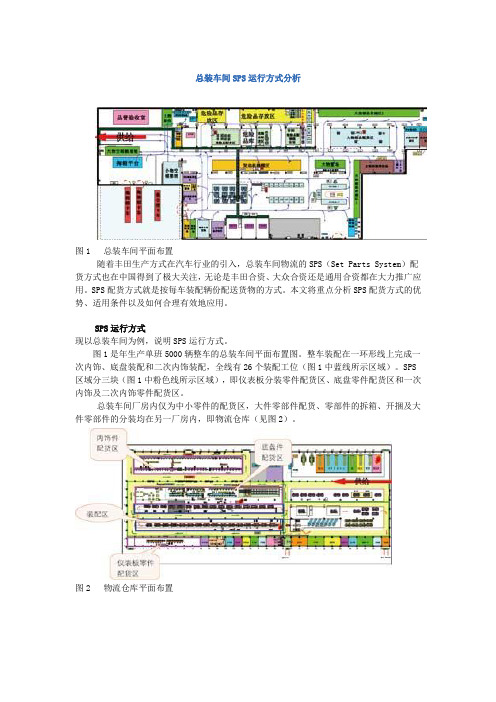
总装车间SPS运行方式分析图1 总装车间平面布置随着丰田生产方式在汽车行业的引入,总装车间物流的SPS(Set Parts System)配货方式也在中国得到了极大关注,无论是丰田合资、大众合资还是通用合资都在大力推广应用。
SPS配货方式就是按每车装配辆份配送货物的方式。
本文将重点分析SPS配货方式的优势、适用条件以及如何合理有效地应用。
SPS运行方式现以总装车间为例,说明SPS运行方式。
图1是年生产单班5000辆整车的总装车间平面布置图。
整车装配在一环形线上完成一次内饰、底盘装配和二次内饰装配,全线有26个装配工位(图1中蓝线所示区域)。
SPS 区域分三块(图1中粉色线所示区域),即仪表板分装零件配货区、底盘零件配货区和一次内饰及二次内饰零件配货区。
总装车间厂房内仅为中小零件的配货区,大件零部件配货、零部件的拆箱、开捆及大件零部件的分装均在另一厂房内,即物流仓库(见图2)。
图2 物流仓库平面布置1.配货顺序总装车间的物流系统在信息控制系统指导下,有条不紊地从仓库货架取出所需零件,按SPS配货方式送到指定工位,配货顺序如下:(1)中央控制室(CCR)根据市场分析及订单情况安排生产计划,并将生产计划的车辆顺序信息向总装车间情报中心传递。
(2)车辆顺序信息传到总装车间情报中心,由情报信息员根据实际工位查找相应信息指示卡。
(3)情报信息员将信息指示卡投递到SPS供应管理板处。
(4)物流配货人员从SPS供给管理板处获取信息选取配货指示票,配货指示票上标有某个车型在某个工程装配零件的种类和数量。
(5)物流人员按照配货指示票到SPS区配货(KITTTING),放在相应的台车上,物流人员将部品放到运输台车上。
(6)配完后放在供给待发区,物流人员将零件供给到生产线的起始位置。
(更先进的方式是AGV 自动输送至相应工位。
(7)物流人员将空台车返回到零件供给待发区,通过SPS方式配货完成。
2. 物料配送的四个步骤在图3的SPS物料及信息流程图中我们可以看到,所有的物料都是经过四个步骤完成运送的:接收物料需求信息(图3中①);按需求信息进行配货(图3中②);将配货送到装配线的接收端(图3中③);随装配线完成装配工序(图3中④)。
总装车间SPS系统的优化设计与实现方法
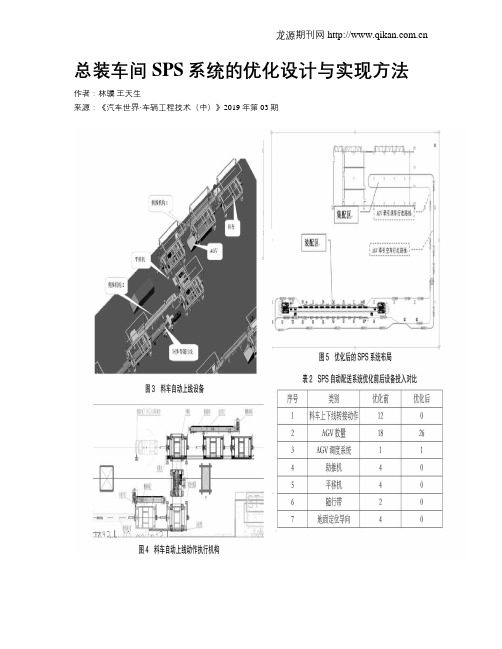
总装车间SPS系统的优化设计与实现方法作者:林骥王天生来源:《汽车世界·车辆工程技术(中)》2019年第03期摘要:介绍了汽车制造业总装车间SPS(Set Parts Supply 零部件成套供应)自动实现配送、随行的原理、案例与运行过程中的问题,通过对存在的问题进行深入分析,文章提出了一种提高SPS自动配送系统运行可靠性的优化设计方法。
关键词:SPS系统;设计;优化0 引言在当今个性化的时代,汽车厂家生产的品类越来越多,专线生产单一规格车型的生产模式由于不具有经济性已经退出历史的舞台。
当今主流的汽车生产线,通常混线生产3种以上的车型。
为了解决生产线混流生产与操作工位边物流存储区域不足的矛盾,丰田公司最先在其精益生产模式中提出了有效解决该问题的方法——零部件成套供应(SPS),目前国内的大部分汽车厂也开始学习应用该方法用于总装混流生产中。
1 典型SPS自动配送系统组成与原理介绍在SPS系统布局中,集配区的功能是实现物料的分拣,拣料员按照生产序列单,在集配区将同一台车的各种物料分拣并放置在同一台料车上。
满载的料车从拣料区出发,被送到装配区,装配区的功能是实现物料的装配,装配工按照安装工艺,从料车拿取物料并将其安装在车身上。
每台车的物料拿取装配完成后,空料车被从装配区送返回集配区,进行后续待装配车辆的分拣。
见附图1所示。
料车从集配区到装配区的配送,随着生产智能化的发展,已由人工配送的方式转向采用AGV全自动配送的模式,其流程描述如下:(1)AGV牵引空料车进入集配区域,通过人工进行配料;(2)当人工配料完成后,工作人員通过按钮盒给AGV发送所配物料上线点(在最后一个分拣工位装2键按钮盒,分别是车门右侧上线点和车门左侧上线点),AGV牵引2台满料车至上线点缓存区;(3)当上线点行程开关检测到没料车,发送信号给缓存区的AGV,AGV接到信号自动启动,运行至上线点,AGV与料车自动脱钩分离;(4)分离后的AGV单机自动启动,运行至下线处的AGV等待点进行等待;(5)上线点通过自动上线机构把料车送上随行同步带,让料车跟着生产线同步运行,料车随随同步带运行至下线点,通过下线点自动下线机构使料车与随行线分离;(6)料车下线后,通过自动下线机构使料车之间安全连接,发送信号给在等待点的AGV,使AGV自动启动,AGV运行至下线点,升降销自动启动与第一台空料车挂钩,挂钩完成,AGV自动启动,牵引2台空料车沿既定的路线进入集配区,完成一个循环;(7)循环。
SPS实施方案
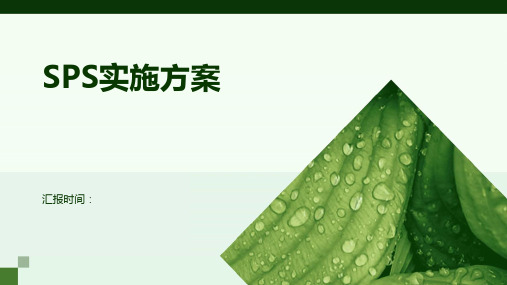
案例三
03
某电信运营商实施SPS项目,通过对网络资源进行精
细管理和优化配置,提高了网络质量和客户满意度。
失败案例分析
案例一
某服装品牌在实施SPS项目时 ,未充分考虑到供应链的复 杂性,导致项目实施过程中 出现物流配送不及时、库存 积压等问题。
案例二
某电子产品制造商实施SPS项 目时,过分追求技术的先进 性,忽略了实际应用场景的 需求,导致项目效果不佳。
方案设计
基于需求分析的结果,进行方案设计,明确 技术路线、系统架构、功能模块等。
系统开发
按照方案设计的要求,进行系统开发和测试 。
项目实施流程设计
数据迁移
如果需要,进行数据迁移,保 证数据的完整性和准确性。
系统测试
完成系统的测试和调试,确保 系统的稳定性和性能。
上线部署
完成系统的部署和上线,进行 上线前的最后调试和测试,确 保系统的顺利运行。
数据迁移和接口对接
如果需要,进行数据迁移和接口对接,保证数据的完整 性和系统的正常运行。
系统上线与部署
完成系统的部署和上线,进行上线前的最后调试和测试 ,确保系统的顺利运行。
用户培训和服务支持
为用户提供培训服务,解决用户使用中的问题,提供持 续的技术支持。
项目实施流程设计
需求分析
对业务需求进行详细了解和分析,确定系统 升级或替换的具体目标和要求。
用户培训
为用户提供培训服务,解决用 户使用中的问题,提供持续的
技术支持。
项目时间表与里程碑
01
第一阶段(1-3 个月)
初步调查和评估现有系统 ,进行需求分析和方案设 计。
02
总装车间小规模物料随行系统的分析与应用
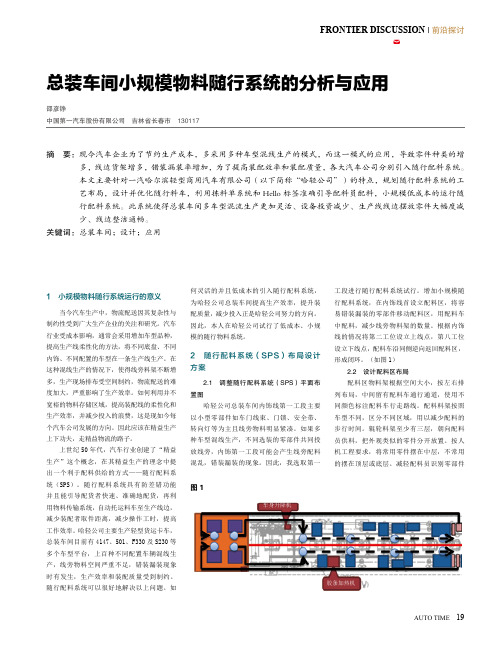
FRONTIER DISCUSSION | 前沿探讨 时代汽车 www.cnautotime.com总装车间小规模物料随行系统的分析与应用邵彦铮中国第一汽车股份有限公司 吉林省长春市 130117摘 要: 现今汽车企业为了节约生产成本,多采用多种车型混线生产的模式,而这一模式的应用,导致零件种类的增多,线边货架增多,错装漏装率增加,为了提高装配效率和装配质量,各大汽车公司分别引入随行配料系统。
本文主要针对一汽哈尔滨轻型商用汽车有限公司(以下简称“哈轻公司”)的特点,规划随行配料系统的工艺布局,设计并优化随行料车,利用拣料单系统和Hello标签准确引导配料员配料,小规模低成本的运行随行配料系统。
此系统使得总装车间多车型混流生产更加灵活、设备投资减少、生产线线边摆放零件大幅度减少、线边整洁通畅。
关键词:总装车间;设计;应用1 小规模物料随行系统运行的意义当今汽车生产中,物流配送因其复杂性与制约性受到广大生产企业的关注和研究。
汽车行业受成本影响,通常会采用增加车型品种,提高生产线柔性化的方法,将不同底盘、不同内饰、不同配置的车型在一条生产线生产。
在这种混线生产的情况下,使得线旁料架不断增多,生产现场排布受空间制约,物流配送的难度加大,严重影响了生产效率。
如何利用并不宽裕的物料存储区域,提高装配线的柔性化和生产效率,并减少投入的浪费,这是现如今每个汽车公司发展的方向。
因此应该在精益生产上下功夫,走精益物流的路子。
上世纪50年代,汽车行业创建了“精益生产”这个概念,在其精益生产的理念中提出一个利于配料供给的方式——随行配料系统(SPS)。
随行配料系统具有防差错功能并且能引导配货者快速、准确地配货,再利用物料传输系统,自动托运料车至生产线边,减少装配者取件距离,减少操作工时,提高工作效率。
哈轻公司主要生产轻型货运卡车,总装车间目前有4147、501、F330及S230等多个车型平台,上百种不同配置车辆混线生产,线旁物料空间严重不足,错装漏装现象时有发生,生产效率和装配质量受到制约。
总装车间智能制造系统的优化
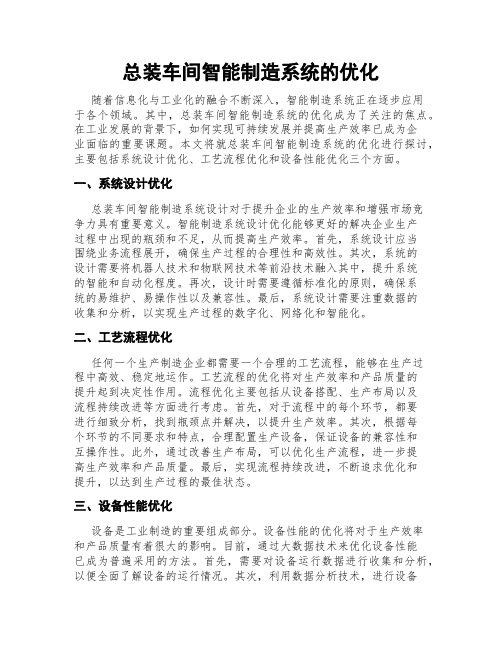
总装车间智能制造系统的优化随着信息化与工业化的融合不断深入,智能制造系统正在逐步应用于各个领域。
其中,总装车间智能制造系统的优化成为了关注的焦点。
在工业发展的背景下,如何实现可持续发展并提高生产效率已成为企业面临的重要课题。
本文将就总装车间智能制造系统的优化进行探讨,主要包括系统设计优化、工艺流程优化和设备性能优化三个方面。
一、系统设计优化总装车间智能制造系统设计对于提升企业的生产效率和增强市场竞争力具有重要意义。
智能制造系统设计优化能够更好的解决企业生产过程中出现的瓶颈和不足,从而提高生产效率。
首先,系统设计应当围绕业务流程展开,确保生产过程的合理性和高效性。
其次,系统的设计需要将机器人技术和物联网技术等前沿技术融入其中,提升系统的智能和自动化程度。
再次,设计时需要遵循标准化的原则,确保系统的易维护、易操作性以及兼容性。
最后,系统设计需要注重数据的收集和分析,以实现生产过程的数字化、网络化和智能化。
二、工艺流程优化任何一个生产制造企业都需要一个合理的工艺流程,能够在生产过程中高效、稳定地运作。
工艺流程的优化将对生产效率和产品质量的提升起到决定性作用。
流程优化主要包括从设备搭配、生产布局以及流程持续改进等方面进行考虑。
首先,对于流程中的每个环节,都要进行细致分析,找到瓶颈点并解决,以提升生产效率。
其次,根据每个环节的不同要求和特点,合理配置生产设备,保证设备的兼容性和互操作性。
此外,通过改善生产布局,可以优化生产流程,进一步提高生产效率和产品质量。
最后,实现流程持续改进,不断追求优化和提升,以达到生产过程的最佳状态。
三、设备性能优化设备是工业制造的重要组成部分。
设备性能的优化将对于生产效率和产品质量有着很大的影响。
目前,通过大数据技术来优化设备性能已成为普遍采用的方法。
首先,需要对设备运行数据进行收集和分析,以便全面了解设备的运行情况。
其次,利用数据分析技术,进行设备故障诊断和预测,以避免因设备故障导致的生产中断等问题。
精细车间排产SaaS系统设计与实现

精细车间排产SaaS系统设计与实现随着科技的不断进步和智能制造的不断发展,精细车间排产SaaS 系统的设计与实现已经成为了企业优化生产过程、提高效率和降低成本的重要工具。
本文将介绍精细车间排产SaaS系统的设计原则、功能模块以及实施过程。
一、设计原则在设计精细车间排产SaaS系统时,必须遵循以下原则:1. 用户友好性:系统设计应简单易用,对于普通用户而言,能够迅速上手操作,并实现快速排产。
2. 灵活性:系统应具备灵活性,能够适应不同类型企业的生产需求以及不同规模的生产车间。
同时,能够随时应对生产线调整和变更。
3. 数据可靠性:系统应保证排产数据的准确性和可靠性,避免因为排产错误而导致的生产中断和资源浪费。
4. 即时性:系统应能够实时处理生产车间的排产任务,实现生产计划的即时调整,以应对异常情况和紧急任务。
二、功能模块精细车间排产SaaS系统的核心功能模块包括:1. 生产计划管理:系统支持生产计划的制定、调整和执行监控,能够根据生产任务和资源情况进行排产,确保生产计划的合理性和稳定性。
2. 资源管理:系统能够管理车间的各种资源,包括设备、人力资源、原材料的调配和分配,确保资源的合理使用和优化配置。
3. 订单管理:系统能够管理客户订单和交付时间,并与生产计划进行实时同步。
同时能够根据订单和交货期自动进行排产和调整。
4. 进度监控:系统能够实时监控生产车间的生产进度,及时发现和纠正生产中断和异常情况,确保生产任务按时完成。
5. 数据分析与报表:系统能够对生产过程进行数据采集、分析和报表生成,提供生产效率、资源利用率等数据指标的分析和评估。
三、实施过程精细车间排产SaaS系统的实施过程包括以下几个阶段:1. 需求调研:与企业相关部门以及生产车间的管理人员进行沟通,了解其需求、问题和期望。
根据实际情况确定系统的功能需求和实施计划。
2. 系统设计与开发:根据需求调研的结果,进行系统设计和开发工作。
确定系统的架构、模块和界面设计,以及数据库的设计和构建。
车间智能化生产系统的设计与优化
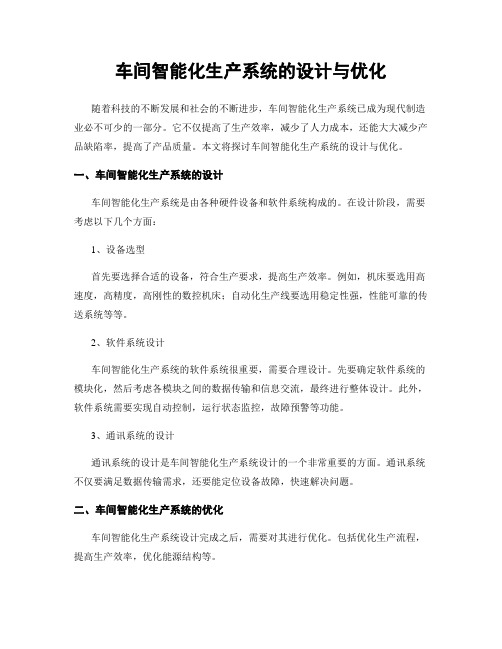
车间智能化生产系统的设计与优化随着科技的不断发展和社会的不断进步,车间智能化生产系统已成为现代制造业必不可少的一部分。
它不仅提高了生产效率,减少了人力成本,还能大大减少产品缺陷率,提高了产品质量。
本文将探讨车间智能化生产系统的设计与优化。
一、车间智能化生产系统的设计车间智能化生产系统是由各种硬件设备和软件系统构成的。
在设计阶段,需要考虑以下几个方面:1、设备选型首先要选择合适的设备,符合生产要求,提高生产效率。
例如,机床要选用高速度,高精度,高刚性的数控机床;自动化生产线要选用稳定性强,性能可靠的传送系统等等。
2、软件系统设计车间智能化生产系统的软件系统很重要,需要合理设计。
先要确定软件系统的模块化,然后考虑各模块之间的数据传输和信息交流,最终进行整体设计。
此外,软件系统需要实现自动控制,运行状态监控,故障预警等功能。
3、通讯系统的设计通讯系统的设计是车间智能化生产系统设计的一个非常重要的方面。
通讯系统不仅要满足数据传输需求,还要能定位设备故障,快速解决问题。
二、车间智能化生产系统的优化车间智能化生产系统设计完成之后,需要对其进行优化。
包括优化生产流程,提高生产效率,优化能源结构等。
1、优化生产流程生产流程的优化能够提高生产效率,降低生产成本。
可以通过运营商模型,开展就近生产,实现物流协同,从而优化物流流程,并最终提高生产效率。
2、提高生产效率提高生产效率是车间智能化生产系统优化的核心部分。
车间智能化生产系统本身就是为提高生产效率而设计的,但还可以通过精益生产、制造执行系统、数据挖掘等方法来提高生产效率。
3、优化能源结构车间智能化生产系统的优化还包括优化能源结构。
现代智能化车间应该使用高效节能的设备,减少用电量,通过降低能源浪费来降低生产成本,同时也减少了对环境的影响。
三、结语为了适应市场的不断变化和提升企业竞争力,车间智能化生产系统的设计和优化至关重要。
合理的设计和优化可以降低生产成本,达到高效生产的目的。
生产计划调度系统的设计与改进

生产计划调度系统的设计与改进一、引言随着现代企业规模的不断扩大和市场竞争的加剧,生产计划调度系统(Production Planning and Scheduling System,PPSS)的重要性越来越凸显出来。
通过合理地安排生产计划与任务分配,能够提升企业的生产效率和生产质量,并减少生产成本和库存风险。
本文旨在探讨生产计划调度系统的设计与改进,以期提高企业的生产效益。
二、生产计划调度系统的设计生产计划调度系统的设计包括以下几个方面:1.系统架构的设计PPSS需要从三个方面考虑架构设计。
首先是数据的管理,需要设计出合理的数据应用模式,协调相关数据的使用,实现高效数据交互和共享。
其次是技术框架的选择,对于一个高效的PPSS系统,后台需要支持多节点架构,满足多用户同时访问系统的需求。
最后是独立的应用程序,需要选择一种通用的技术架构进行搭建,以方便不同的企业在其基础上进行修改和定制。
2.生产计划的制定企业在生产计划制定的过程中,需要考虑公司的规模、生产能力以及员工的专业能力等因素,以便于制定出合理的生产计划。
生产计划的制定需要综合考虑订单情况、设备能力、库存状况以及配合供货商的生产能力。
增加企业与供货商的协调机制,能够有效地解决生产过程中的协调难题,促进生产计划中资源利用率的提升,提高生产效益。
3.任务分配的设计任务分配是一个关键的环节。
生产任务的分配需要考虑生产设备的利用情况、员工的实际情况以及生产计划的情况。
高效的生产计划调度系统需要实时监测生产状况,分析实时反馈的数据,并快速调整生产计划,保证任务分配得以顺利进行。
4.调度决策的设计生产计划调度系统的核心在于调度决策,生产任务的实现和顺利完成全靠调度决策。
对于复杂的PPSS系统,基于规则引擎的高级调度决策可以优化调度模型,实现决策智能化。
即在人工调度基础上,利用规则和数据分析调度系统,自动实现处理、监控和决策,更加准确和高效地完成生产计划任务。
- 1、下载文档前请自行甄别文档内容的完整性,平台不提供额外的编辑、内容补充、找答案等附加服务。
- 2、"仅部分预览"的文档,不可在线预览部分如存在完整性等问题,可反馈申请退款(可完整预览的文档不适用该条件!)。
- 3、如文档侵犯您的权益,请联系客服反馈,我们会尽快为您处理(人工客服工作时间:9:00-18:30)。
车辆工程技术
111
机械电子
0 引言
在当今个性化的时代,汽车厂家生产的品类越来越多,专线生产单一规格车型的生产模式由于不具有经济性已经退出历史的舞台。
当今主流的汽车生产线,通常混线生产3种以上的车型。
为了解决生产线混流生产与操作工位边物流存储区域不足的矛盾,丰田公司最先在其精益生产模式中提出了有效解决该问题的方法——零部件成套供应(SPS),目前国内的大部分汽车厂也开始学习应用该方法用于总装混流生产中。
1 典型SPS 自动配送系统组成与原理介绍
在SPS 系统布局中,集配区的功能是实现物料的分拣,拣料员按照生产序列单,在集配区将同一台车的各种物料分拣并放置在同一台料车上。
满载的料车从拣料区出发,被送到装配区,装配区的功能是实现物料的装配,装配工按照安装工艺,从料车拿取物料并将其安装在车身上。
每台车的物料拿取装配完成后,空料车被从装配区送返回集配区,进行后续待装配车辆的分拣。
见附图1所示。
总装车间SPS 系统的优化设计与实现方法
林 骥,王天生
(上汽通用五菱汽车股份有限公司,广西 柳州 545007)
摘 要:介绍了汽车制造业总装车间SPS(Set Parts Supply 零部件成套供应)自动实现配送、随行的原理、案例与运行过程中的问题,通过对存在的问题进行深入分析,文章提出了一种提高SPS 自动配送系统运行可靠性的优化设计方法。
关键词:SPS
系统;设计;优化
料车从集配区到装配区的配送,随着生产智能化的发展,已由人工配送的方式转向采用AGV 全自动配送的模式,其流程描述如下: (1)AGV 牵引空料车进入集配区域,通过人工进行配料; (2)当人工配料完成后,工作人员通过按钮盒给AGV 发送所配物料上线点(在最后一个分拣工位装2键按钮盒,分别是车门右侧上线点和车门左侧上线点),AGV 牵引2台满料车至上线点缓存区; (3)当上线点行程开关检测到没料车,发送信号给缓存区的AGV,AGV 接到信号自动启动,运行至上线点,AGV 与料车自动脱钩分离;
(4)分离后的AGV 单机自动启动,运行至下线处的AGV 等待点进行等待;
(5)上线点通过自动上线机构把料车送上随行同步带,让料车跟着生产线同步运行,料车随随同步带运行至下线点,通过下线点自
图1 SPS 系统布局
动下线机构使料车与随行线分离;
(6)料车下线后,通过自动下线机构使料车之间安全连接,发送信号给在等待点的AGV,使AGV 自动启动,AGV 运行至下线点,升降销自动启动与第一台空料车挂钩,挂钩完成,AGV 自动启动,牵引2台空料车沿既定的路线进入集配区,完成一个循环;
(7)循环。
SPS 料车自动上下线系统分为左侧上线、左侧下线、右侧上线、右侧下线及同步带随行线五大部分,如图2
所示。
2 典型SPS 自动配送系统运行问题分析
以本公司某生产线的典型SPS 自动配送系统为例,在实际生产运营中,料车上线点、下线点出现故障频率最多,见表1所示。
图2 料车自动上下线系统
表1 SPS
自动配送系统运行故障统计
可见,料车上下线点的故障为典型SPS 自动配送系统的主要故障,在本文中,通过对料车上下线点设备构成与流程动作逻辑分解,提出问题的解决方案并进行系统的优化设计。
某生产线SPS 上线点采用侧推机构+平移机+AGV 的实现料车的自动上线功能,其主要设备包括:侧推机构、平移机、导向护栏、脱钩机构等,如图3所示。
料车自动上线机构的各动作执行设备,按PLC 预设定的程序逻辑实现全自动转接,如图4所示。
①AGV 带动料车到达指定位置,AGV 脱钩并离开;
②行程开关检测到AGV 安全离开,侧推机构1启动,利用拨杆机构带动2台料车前进,待到第1台料车到达平移位时停止;
车辆工程技术
112
机械电子
图3 料车自动上线设备
③侧推动作的同时,利用脱钩挡块将2台料车分开,使第2台料车停在原有第1台料车的位置;
④行程开关检测到平移位处料车到位,自行启动并运行至平移位;平移机的举升机构上升,托起料车进行平移(与此同时,侧推的拨杆机构退回原位),将料车平移至预上线位并退回原位;
⑤同时,行程开关检测到第1台料车离开平移位,侧推机构1启动,将第2台料车移送至平移位;
⑥行程开关检测到预上线位处料车到位,侧推机构2启动,利用拨杆机构带动料车前进,待到料车到达同步带随行线上线位时停止,侧推的拨杆机构退回原位;
⑦同时,行程开关检测到第2台料车到达平移位,平移机自行启动运行至平移位;平移机的举升机构上升,托起料车进行平移,将料车平移至原位等待;
⑧行程开关检测到第1台料车离开预上线位,平移机再次启动,将第2台料车移送至预上线位;
⑨行程开关检测预上线位料车到位,第1台料车离开同步带随行线上线位,侧推机构2启动,利用拨杆机构带动料车前进,待到料车到达同步带随行线上线位时停止,侧推的拨杆机构退回原位; ⑩行程开关检测到第2台料车离开平移位,AGV 由等待位启动,带动料车到达指定位置,AGV 脱钩并离开;依照①②③④⑤⑥⑦⑧⑨
⑩循环。
本文作者认为,典型SPS 自动配送系统由于:(1)动作机构种类数量多;(2)各执行机构转接动作精度要求高;(3)料车底框精度控制不佳,这三个是导致故障频发的主要原因。
由于料车的使用范围广,提高其精度控制难度与成本投入都非常大,而降低自动设备执行机构的精度要求,会导致一系列的安全隐患,所以本文将从减少自动机构种类数量进行系统的优化设计。
3 SPS 自动配送系统优化设计
图4 料车自动上线动作执行机构
在某生产线的新型SPS 自动配送系统中,经过优化设计,采用AGV 与装配线同速驱动料框实现随行,取消料车与AGV 脱钩分离、挂钩结合动作,优化后的自动流程描述如下:
(1)AGV 牵引空料车进入集配区域,通过人工进行配料; (2)当人工配料完成后,工作人员通过按钮盒给AGV 发送所配物料上线点(在最后一个分拣工位装2键按钮盒,分别是车门右侧上线点和车门左侧上线点),AGV 牵引2台满料车至上线点缓存区; (3)当上线点行程开关检测到没料车,发送信号给缓存区的AGV,AGV 接到信号自动启动,运行至上线点,在随行起始工位,上位系统控制AGV 自动调速至与装配线同步,生产线同步运行,料车随随同步带运行至下线点;
(4)AGV 带着料车下线后,上位系统发送信号给AGV,AGV 自动加速,牵引2台空料车沿既定的路线进入集配区,完成一个循环; (5)循环。
如图5
所示。
通过此创新方法,增加少量的AGV 台量,可以减少助推机、平移机、同步随机带、地面导向定位机构这几大类设备,如附表2所示。
图5 优化后的SPS 系统布局
表2 SPS 自动配送系统优化前后设备投入对比序号类别
优化前优化后1
料车上下线转接动作
1202AGV 数量18263AGV 调度系统
114助推机405平移机406随行带207
地面定位导向
4
4 结束语
通过已经投产的生产线来看,在实际使用中,该优化设计后的新型SPS 自动配送系统运行稳定,有较好的系统鲁棒性,有效的提高了
生产系统的柔性,具有良好的推广意义。
参考文献:
[1]于永刚等.基于工业无线以太网的AGV 自动控制系统[J].冶金自动化,2009(33).
[2]侯炜.SPS 在汽车总装生产过程中的应用[J].上海汽车,2010(10).作者简介:林骥(1972-),男,广西富川人,硕士,高级工程师,研究方向:汽车生产制造。