甲醛水溶液的加压精留分离
双效精馏分离不同浓度甲醇水溶液的节能分析

(a) 1.013×105Pa[12]
(b) 4.270×105Pa [13]
多效精馏广泛应用于甲醇和水的分离过程[3,9-11], 然而对于高低压双塔的串并联问题,依然需要根据 甲醇水溶液的不同组成进行优化选择。本文针对不
同的甲醇进料浓度对甲醇水溶液精馏过程的影响, 分别采用顺流串联精馏、逆流串联精馏和并联精馏 3 种双效精馏过程进行模拟计算和优化。以最小年 度总费用(TAC)为目标,探索不同甲醇浓度下的 最佳双效精馏方案,并且,为了说明节能程度,对 各方案进行有效能分析。
甲醇是一种重要的工业原料,其产品有甲醛、 醋酸、碳酸二甲酯等;还是一种良好的有机溶剂, 可用作大规模集成电路中的去油剂和许多无机盐的 溶解剂[1]。2018 年上半年,我国甲醇新投产产能约 为 180 万吨,但国内甲醇供需失衡的局面依然存在, 即使有新增产能,甲醇市场依然供不应求[2]。在甲 醇的工业生产和应用过程中,往往存在具有不同成 分的甲醇溶液,如甲醇合成过程中产生的粗甲醇质 量分数约为 80%~95%[3-7],油气田天然气水化物抑 制剂形成的甲醇废液中,甲醇质量分数为 1%~ 50%[8]。虽然不同来源的工业甲醇溶液的浓度不同, 但其中最主要的成分都是甲醇和水。不管是甲醇提 纯还是甲醇回收的精馏系统中,甲醇和水的分离都 是能耗的主要环节。因此,关于甲醇水溶液精馏过 程的节能研究,对甲醇工业节能降耗和降低污染尤 为必要。
ZHANG Ting, WEI Shun’an, SHEN Weifeng
(School of Chemistry and Chemical Engineering, Chongqing University, Chongqing 400044, China)
Abstract: Methanol-water mixtures with different compositions exist in many industrial processes, and the main consideration is energy consumption when separating methanol and water. In view of the separation process of methanol-water with methanol concentration of 10%–90%(mass fraction), different distillation models with light split forward, light split reverse and feed splitting were adopted. Using “Design Spec/Vary” function to find the values of distillate flowrate and reflux ratio that the distillate composition to 99.85%(mass fraction) methanol and the bottoms composition to 10–5 methanol. The sensitivity analysis method was used to optimize the number of trays and the feed trays to obtain the minimum annual total cost(TAC). Furthermore, the energy loss of each process under the minimum TAC condition is compared and analyzed. When the methanol concentration of the raw methanol-water mixtures is 30% or less, the TAC of the feed splitting is the smallest; when the methanol concentration of the raw methanol-water mixtures is 50% or more, the TAC of light split reverse configuration is the smallest. In the case of minimum TAC for each process, the exergy loss of feed splitting process is the smallest when the methanol concentration of the raw methanol-water mixtures is 10% or less; the exergy loss of light split reverse process is the smallest when the methanol concentration of the raw
分离甲醇水溶液的精馏系统设计冷凝器的工艺设计

理工大学化工课程设计说明书作者:学号:学院(系):化工学院专业:化学工程与工艺题目:分离甲醇水溶液的精馏系统设计——回流系统的设计指导者:评阅者:年月化工课程设计任务书一、设计题目分离甲醇水溶液的精馏系统设计——回流系统的设计二、设计任务1、精馏系统处理能力:4500kg/h;2、精馏系统进料组成:甲醇含量28%(质量,下同),温度为25℃;3、精馏系统工艺要求:甲醇回收率为97.5%,塔底甲醇含量为1%;4、精馏塔操作条件:常压;三、设计内容1、回流系统工艺设计条件的确定;2、回流系统的工艺设计;3、冷凝器的设结构设计;4、冷凝器的强的设计;四、设计要求1、设计说明书一份;2、设计图纸:a、精馏系统工艺流程图一张(采用AutoCAD绘制);b、回流系统主要设备总装配图一张(A1);3、答辩。
五、设计完成时间2007.9.3~2007.9.28目录第一章冷凝器的工艺设计 (1)1.1设计任务和操作条件 (1)1.2设计方案的确定 (1)1.3确定物性数据 (1)1.4计算传热面积 (2)1.4.1计算冷凝器的热负荷 (2)1.4.2计算平均温差Δt m (3)1.4.3假定传热系数 (5)1.4.4计算传热面积 (5)1.5工艺结构尺寸 (5)1.6换热器核算 (8)1.7阻力计算 (10)1.8工艺设计汇总表 (13)第二章冷凝器结构及强度设计2.1壳体、管箱壳体和封头的计算 (14)2.1.1壳体管箱的设计 (14)2.1.2封头的设计 (14)2.1.3封头的强度计算 (14)2.1.4筒体的强度计算 (15)2.2进出口的设计 (16)2.2.1接管外伸长度 (16)2.2.2接管最小位置 (16)2.2.3接管与筒体、管箱壳体的连接 (17)2.1.4筒体的强度计算 (18)2.3管板 (18)2.3.1管板的结构 (18)2.3.2管板的尺寸 (18)2.3.3固定管板的强度计算 (19)2.4换热管 (21)2.5法兰的选定 (23)2.5.1管板法兰盖的选定 (23)2.5.2接管法兰的选定 (24)2.6管子与管板的连接 (25)2.7膨胀节 (25)2.8折流板 (25)2.9拉杆、定距管 (26)2.10鞍式支座的选择 (27)2.11分程隔板 (28)2.12防冲挡板 (28)2.13泵的选择 (29)2.14主要零部件汇总表 (30)心得体会 (31)参考文献 (32)第一章再沸器设计任务书一,设计题目分离甲醇水溶液的精馏系统设计——再沸器的设计二,设计任务1)精馏系统的处理能力:4500kg/h;2)精馏系统的进料的组成:甲醇含量28%(质量,下同),温度为25℃;3)精馏系统的工艺要求:甲醇的回收率为97 .5,塔底甲醇含量1%;4)精馏塔操作条件:常压三,设计内容1)再沸器工艺条件的确定2)再沸器的工艺设计3)再沸器的结构设计4)再沸器的强度设计四,设计要求1)设计说明书一份2)设计图纸:a.精馏系统工艺流程图一张(采用AutoCAD绘制)b.再沸器总装配图一张(AI)3)答辩五设计完成时间2007.9.3——2007.9.28第二章再沸器的设计工艺2.1.1塔釜物料基本数据精馏塔计算结果有塔釜釜液的数据:塔釜的组成与流量:Xw=0.565%(摩尔分数)气相摩尔流量= 136(kmol/h)气相体积流量= 4062.27(m3/h)塔釜的温度:=99.86℃塔底气相温度:twv=99.24℃塔底液相温度:twL塔釜的压强:精馏段每块塔板压降398.4pa 塔板数:18提馏段每块塔板压降417.37pa 塔板数:10设塔顶的表压为2000Pa.则塔釜压强(表压):p=2000+398.4×18+417.37×10=13344.9(pa)由于塔底气相,液相的温度相差不是很大,故在设计的时候可以看成他们的温度相同,为了计算的方便以及物性常数的查找,在设计的时候我们选取的温度为100℃。
分离甲醇-水混合物化工设计
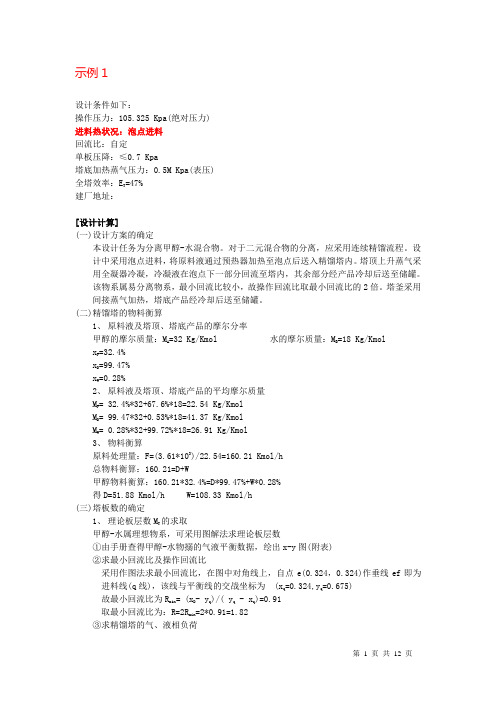
示例1设计条件如下:操作压力:105.325 Kpa(绝对压力)进料热状况:泡点进料回流比:自定单板压降:≤0.7 Kpa塔底加热蒸气压力:0.5M Kpa(表压)全塔效率:E T=47%建厂地址:[设计计算](一)设计方案的确定本设计任务为分离甲醇-水混合物。
对于二元混合物的分离,应采用连续精馏流程。
设计中采用泡点进料,将原料液通过预热器加热至泡点后送入精馏塔内。
塔顶上升蒸气采用全凝器冷凝,冷凝液在泡点下一部分回流至塔内,其余部分经产品冷却后送至储罐。
该物系属易分离物系,最小回流比较小,故操作回流比取最小回流比的2倍。
塔釜采用间接蒸气加热,塔底产品经冷却后送至储罐。
(二)精馏塔的物料衡算1、原料液及塔顶、塔底产品的摩尔分率甲醇的摩尔质量:M A=32 Kg/Kmol 水的摩尔质量:M B=18 Kg/Kmolx F=32.4%x D=99.47%x W=0.28%2、原料液及塔顶、塔底产品的平均摩尔质量M F= 32.4%*32+67.6%*18=22.54 Kg/KmolM D= 99.47*32+0.53%*18=41.37 Kg/KmolM W= 0.28%*32+99.72%*18=26.91 Kg/Kmol3、物料衡算原料处理量:F=(3.61*103)/22.54=160.21 Kmol/h总物料衡算:160.21=D+W甲醇物料衡算:160.21*32.4%=D*99.47%+W*0.28%得D=51.88 Kmol/h W=108.33 Kmol/h(三)塔板数的确定1、理论板层数M T的求取甲醇-水属理想物系,可采用图解法求理论板层数①由手册查得甲醇-水物搦的气液平衡数据,绘出x-y图(附表)②求最小回流比及操作回流比采用作图法求最小回流比,在图中对角线上,自点e(0.324,0.324)作垂线ef即为进料线(q线),该线与平衡线的交战坐标为 (x q=0.324,y q=0.675)故最小回流比为R min= (x D- y q)/( y q - x q)=0.91取最小回流比为:R=2R min=2*0.91=1.82③求精馏塔的气、液相负荷L=RD=1.82*51.88=94.42 Kmol/hV=(R+1)D=2.82*51.88=146.30 Kmol/hL ′=L+F=94.42+160.21=254.63 Kmol/h (非泡点进料要注意q 值) V ′=V=146.30 Kmol/h ④精馏段操作线方程为:y =(L/V)x + (D/V)x D =(99.42/146.30)x+(51.88/146.30)*99.47%=0.6454x+0.3527 提馏段操作线方程为:y ′=(L ′/V ′)x ′ + (W/V ′)x W =(254.63/146.30) x ′-(108.33/146.30)*0.28% =1.7405 x ′-0.0021 ⑤图解法求理论板层数采用图解法求理论板层数(附图),求解结果为: 总理论板层数:N T =13(包括再沸器) 进料板位置: N F =10 2、实际板层数的求取)1()1(A A A A --=y x x y αα%47E 047.1*(345.00= 故= 见后) μαμ=精馏段实际板层数:N 精=9/47%=20 N 提=4/47%=9(四) 精馏塔的工艺条件及有关物性数据的计算以精馏段为例进行计算1、 塔顶操作压力:P D =101.3 Kpa每层塔板压降:△P =0.7 Kpa进料板压力:P F =105.3+0.7*20=119.3 Kpa 精馏段平均压力:(105.3+119.3)/2=112.3 Kpa 2、 操作温度计算依据操作压力,由泡点方程通过试差法计算出泡点温度,其中甲醇、水的饱和蒸气压由安托尼方程计算,计算过程略,计算结果如下:塔顶温度:t D =64.6℃ 进料板温度:t F =76.3℃ 精馏段平均温度:t M =70.45℃ 3、 平均摩尔质量计算塔顶平均摩尔质量计算:由x D =y 1=0.9947,查y-x 曲线(附表),得x 1=0.986M VDm =0.9947*32+(1-0.9947)*18=31.93 M LDm =0.9860*32+(1-0.9860)*18=31.80 进料板平均摩尔质量计算 由图解理论板(附图),得 y f =0.607 x F =0.229M VFm =0.607*32+(1-0.607)*18=26.50 M LFm =0.229*32+(1-0.229)*18=21.21 所以精馏段平均摩尔质量: M Vm =(31.93+26.50)/2=29.22 M Lm = (31.80+21.21)/2=26.51 4、 平均密度计算 ⑴气相密度计算由理想气体状态方程计算,即3/15.1)45.70273(*314.822.29*3.112M Kg RT M P mV m V m m=+==ρ(这里也可以分别计算进料板与塔顶第一板的密度再取平均值) ⑵液相平均密度计算液相平均密度依下式计算,即∑=iiLmραρ1塔顶液相平均密度的计算 由t D =64.6℃ 查手册得,3B 3/K 3.980/K 745m g m g A = ρρ=3/K 7460053.09947.01m g BA LD m=+=ρρρ进料板液相平均密度的计算 由t F =76.3℃ 查手册得,3B 3/K 978/K 735m g m g A = ρρ=进料板液相的质量分量%56.3418*771.032*229.032*229.0=+=A α3/K 7.8776544.03456.01m g BA LF m=+=ρρρ⑶精馏段液相平均密度为:321/K 8122)(m g mL =+=ρρρ5、 液体平均表面张力计算⑴液相平均表面张力依下式计算,即∑=i i L x mσσ(苯、甲苯体系可用此式,醇水体系请用公式4/14/14/1o so w sw m σϕσϕσ+=来计算)塔顶液相平均表面张力的计算 由t D =64.6℃,查手册得mmN m mN m mN B A A m/ 05.190053.09947.0/ 2.65/ 8.18LD B =+===σσσσσ ⑵进料板液相平均表面张力的计算 由t F =76.3℃,查手册得mmN m mN m mN B A A m/ 35.52771.0229.0/ 7.62/ 5.17LF B =+===σσσσσ ⑶精馏段液相平均表面张力为:m mN m m mLF LD L / 7.352)(=+=σσσ6、 平均粘度的计算液相平均粘度依下式计算,即∑=iiL x m μμlg lg⑴塔顶液相平均粘度的计算 由t D =64.6℃ 查手册得,smpa smpa s mpa mmL B A L /34.0lg 0053.0lg 9947.0lg /437.0/34.0D D B A = 解得= =μμμμμμ+=⑵进料板液相平均粘度的计算 由t F =76.3℃ 查手册得smpa smpa s mpa mmL B A L /53.0lg 771.0lg 229.0lg /374.0/28.0F F B A = 解得= =μμμμμμ+=⑶精馏段液相平均表面张力为s mpa /345.0221A =)(=μμμ+(五)精馏塔的塔体工艺尺寸计算1、 塔径的计算精馏段的气、液相体积流率为:021.0)15.1812(08.110*56.8)(L )(L 20C C /10*856812*360051.26*42.94*3600/033.115.1*360022.29*30.146*360021421212.0L 20max343===-=======--V L s s V L h h V V L Lm Lm s Vm Vm s V V C u sm LM L sm VM V ρρρρσρρρρρ)(= 其中由取板间距H T =0.4m ,板上液层高度h L =0.06m ,则H T -h L =0.40-0.06=0.34m 查史密斯关联图得,C 20=0.074sm u / 204.215.115.1812083.0083.0207.35074.020C C max 2.02.0L20=-=== )()(=σ取安全系数为0.7,则空塔气速为sm sm u u / 948.0543.1*1.033*4u 4V D / 543.1204.2*7.0s max ======ππ 按标准塔径圆整后,为D=1.0m 塔截面积为22785.04m D A T ==π实际空塔气速为u=1.033/0.785=1.316s m /2、 精馏塔有效高度的计算(实际高度要注意人孔处、进料板、再沸器、塔顶空间等)精馏段有效高度为Z 精=(N 精-1)H T =(20-1)*0.4=7.6m 提馏段有效高度为Z 提=(N 提-1)H T =(9-1)*0.4=3.2m 在进料板上方开2人孔,其高度为0.8m故精馏塔有效高度为Z =N 精+N 提+0.8*2=12.4m(六)塔板主要工艺尺寸的计算1、 溢流装置计算因塔径D =1.0m ,可选用单溢流弓形降液管,采用凹形受液盘,各项计算如下:⑴塔长l W =0.66D=0.66m⑵溢流堰高度h W 由h W =h L -h OW选用平直堰,堰上液层高度h OW32)(100084.2wh ow l L E h =近似取E =1,则m h ow 93.7)66.03600*10*56.8(*1*100084.2324==-取板上清液层高度h L =60mm故m h w 33310*07.5210*93.710*60---=-=⑶弓形降液管宽度W d 和截面积A f由l w /D=0.66,查图得 A f /A T =0.0722 W d /D=0.124mD W m A A d T f 124.0124.00567.0*0722.02====验算液体在降液管中停留时间 s s L H A hTf 55.263600*10*56.840.0*0567.0*360036004>===-θ 故降液管设计合理⑷降液管底隙高度h 0mm h s m u u l L h w h006.0016.008.0*66.0*36003600*10*56.8/ 08.0*36004000>==''=-则=取故降液管底隙设计合理选用凹形受液盘,深度wh '=50mm 2、 塔板布置⑴塔板的分块因D ≥800mm ,故塔板采用分块式,且分为3块⑵边缘区宽度确定取m W m W W C S S 035.0065.0=='= ⑶开孔面积A a212221222a 532.0)465.0311.0sin 180465.0*311.0465.0311.0(2465.0035.05.02311.0)065.0124.0(5.0)(2sin 180(2A m A mW Dr m W W Dx rx r x r x a c s d =+-==-=-==+-=+-=+-=--ππ故 其中,⑷筛孔计算及其排列本例所处理的物系无腐蚀性,可选用δ=3mm 碳钢板,取筛孔直径d 0=5mm 筛孔按正三角形排列,取孔中心距t 为 t =3d 0=15 mm筛孔数目n 为个2731015.0532.0*155.1155.122===t A n a 开孔率为%1.10)015.0005.0*907.0)907.0220==((=t d ϕ气体通过阀孔的气速为 s m A V u s / 23.19532.0*101.0033.100===(七)筛板的液体力学验算1、 塔板压降⑴干板阻力h c 计算 干板阻力 )()(051.0200LVc C u h ρρ= 由d 0/δ=3/5=1.667, 得C 0=0.772 故液注0448.0)81215.1()772.023.19(051.02==c h ⑵气体通过液层的阻力h l 计算 h l =βh L21210 52.115.1418.1/418.10567.0785.0033.1ms Kgu F sm A A V u v af T s a ====-=-=ρ查图得,β=0.59故液柱m h h h h ow w L l 0354.0)10*93.710*07.52(59.0)(33=+=+==--ββ⑶液体表面张力的阻力σh 计算液体表面张力所产生的阻力σh 由下式计算液柱m gd h L L 00359.0005.0*81.9*81210*7.35*4430===-ρσσ 气体通过每层塔板的液柱高度h P 可按下式计算,即 h P =h c +h l +h σh P =0.0448+0.0354+0.00359=0.084m 液柱 气体通过每层塔板的压降为设计允许值)(7.045.66781.9*812*084.0h P p KPa g L <===∆ρ2、 液面落差对于筛板塔,液面落差很小,且本例的塔径和液流量均不大,故可忽略液面落差的影响。
多聚甲醛的生产工艺及技术进展
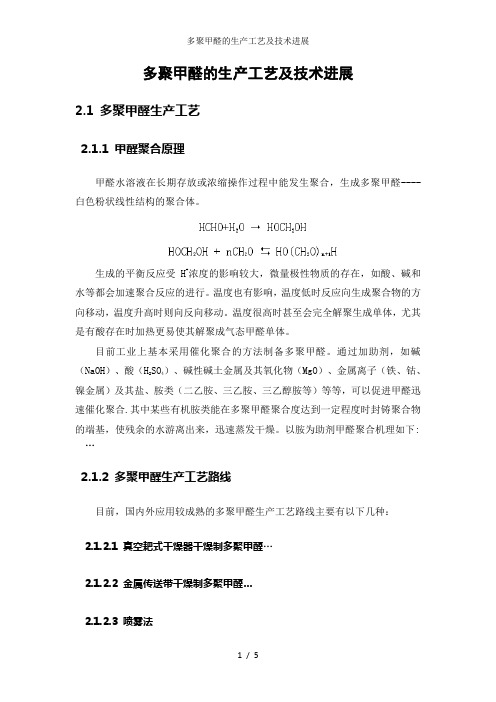
多聚甲醛的生产工艺及技术进展2.1 多聚甲醛生产工艺2.1.1 甲醛聚合原理甲醛水溶液在长期存放或浓缩操作过程中能发生聚合,生成多聚甲醛----白色粉状线性结构的聚合体。
生成的平衡反应受 H+浓度的影响较大,微量极性物质的存在,如酸、碱和水等都会加速聚合反应的进行。
温度也有影响,温度低时反应向生成聚合物的方向移动,温度升高时则向反向移动。
温度很高时甚至会完全解聚生成单体,尤其是有酸存在时加热更易使其解聚成气态甲醛单体。
目前工业上基本采用催化聚合的方法制备多聚甲醛。
通过加助剂,如碱(NaOH)、酸(H2SO4)、碱性碱土金属及其氧化物(MgO)、金属离子(铁、钴、镍金属)及其盐、胺类(二乙胺、三乙胺、三乙醇胺等)等等,可以促进甲醛迅速催化聚合.其中某些有机胺类能在多聚甲醛聚合度达到一定程度时封铸聚合物的端基,使残余的水游离出来,迅速蒸发干燥。
以胺为助剂甲醛聚合机理如下: …2.1.2 多聚甲醛生产工艺路线目前,国内外应用较成熟的多聚甲醛生产工艺路线主要有以下几种:2.1.2.1 真空耙式干燥器干燥制多聚甲醛…2.1.2.2 金属传送带干燥制多聚甲醛…2.1.2.3 喷雾法78-85%浓甲醛加助剂后,在干燥室 30-40℃惰性气体(N)条件下喷雾造粒2得到细颗粒、水溶性好、具有流动性的多聚甲醛。
要制得高含量多聚甲醛,可再转入流化床两段干燥,第一段控温 45-70℃可得醛含量 90-91%多聚甲醛;第二段控温 70-100℃强化干燥后醛含量达 95%以上。
喷雾干燥法干燥时间短,制得的多聚甲醛颗粒大小可调,具有流动性,操作灵活。
缺点:气固分离困难,细颗粒粉尘回收难,热效率不高,设备容积大。
2.1.2.4 共沸精馏法甲醛浓缩后的浓醛导入装有惰性有机液的反应釜,共沸脱水,最后过滤有沉淀的釜液,将固体干燥,蒸去低沸点有机液,可制得醛含量 91-99%的多聚甲醛产品。
共沸精馏法制备工艺尽管也可以制备较好的产品,由于共沸剂的种类、回收以及工艺放大等问题,目前只有少数厂家生产。
低浓度甲醛提浓技术探讨

o f d i l u t e f o m a r l d e h y d e o f p r e s s u r e r e c t i i f c a t i o n c o n c e n t r a t i o n t e c h n o l o y ,r g e d u c e d p r e s s u r e c y c l o n e s e p a r a t i o n t e c h n o l o y , g a n d me t h y l a l o x i d a t i o n t e c h n o l o y. T g h e t h r e e c o n c e n t r a t i o n t e c h n o l o g i e s w e r e i n t r o d u c e d a n d t h e a d v a n t a g e s a n d d i s a d v a n t a g e s we r e c o mp a r e d . Ke y wo r d s :f o m a r l d e h y d e ;c o n c e n t r a t i o n;t e c h n o l o g y
甲醛是 一种 重要 的基本 有机 化工 原料 ,其下 游 产品 很多 。
在我 国 ,甲醛 主要用于生产三醛树 脂 ( 包括脲 醛树脂 、酚醛 树
脂和三 聚氰胺 甲醛树脂 ) ,其 占甲醛 消费 总量 的 5 0 % 以上 。此 外 ,甲醛 还 用 于 生 产 季 戊 四 醇 、新 戊 二 醇 、1 , 4一丁 二 醇
L I N X i a o —y a n ,W A N G Q i ( P o l y f o r m a l d e h y d e P l a n t , S h e n h u a N i n g x i a C o a l I n d u s t r y G r o u p ,N i n g x i a L i n g w u 7 5 1 4 0 0, C h i n a )
甲醛装置工艺流程简述

(1)甲醛装置工艺流程简述从甲醇缓冲罐来的甲醇用泵送入本装置,先进入甲醇预蒸发器,在此与风机出口侧的新鲜空气以及吸收塔顶来的循环气进行混合、预热。
甲醇预蒸发器提高了进入反应器的甲醇-空气混合气的温度,也增加了(导热油冷凝器)所产生的热量。
预热后的气体进入甲醇蒸发器,在此与主反应器出来的产品进行换热,甲醇/空气混合气被进一步加热后的进入主反应器。
反应器类似一个管壳式的换热器,管程是催化剂,壳程是为用于撤热的导热油。
气体混合物进入反应器流经催化剂管时,反应式如下:少量甲醇被进一步氧化生成一氧化碳,发生如下副反应:此外,少量的甲醇脱水生成二甲醚:这些反应为放热反应,混合气通过催化剂管时,温度升高。
大部分甲醇反应完毕后,温度降低,催化剂管出口气体的温度接近导热油的沸点温度。
每根催化剂管内的最高温度称为“热点”温度,“热点”温度时甲醇反应控制过程中的一个重要参数。
为保持最佳反应温度条件和限制副产品生成,在反应期间通过壳程导热油蒸发而将热移出反应器,气-液导热油在导热油冷凝器中冷凝,冷凝热产生的蒸汽并减压至0.8送出界外。
导热油回路设计成一个热虹吸系统,一旦反应开始,循环开始,不需要泵。
工厂开车时,通过导热油泵将导热油从贮槽经电加热器升温送入反应器。
一旦稳定状态的条件达到后,停下导热油循环泵和加热器,依靠热虹吸作用维持导热油自身循环。
反应器出口气在甲醛蒸发器中与甲醇-空气混合器进行热交换后被冷却,然后进入吸收塔和,在吸收塔内,甲醛气体与工艺水逆流接触,二台吸收塔串联操作。
工艺气从吸收一塔底部进入,从顶部出来后进入吸收二塔底部,脱盐水从吸收二塔顶部加入。
从底部抽出所要求浓度的甲醛溶液,部分甲醛循环使用,余下的送入甲醛贮罐。
产品管线上安装有质量流量计,自动控制甲醛浓度。
产品甲醛在板式换热器中冷却。
离开顶部的气体一部分通过循环风机和进行循环进入反应工段,一部分经过催化焚烧系统处理后排入大气。
排放控制系统将尾气中有机物质的浓度降至环保要求的排放指标之内。
聚甲醛工艺简介3

共聚甲醛生产主要工艺环节
一、甲醛浓缩 二、三聚甲醛(TOX)生产 三、二氧五(戊)环(DOX)生产 四、聚甲醛(POM)生产 五、POM脱气造粒
一、甲醛浓缩
1、浓缩目旳:将40%wt工业甲醛浓缩至60%左右,用
作TOX和DOX生产旳原料。
2、原料起源:生产浓甲醛(60%)旳原料来自两方面:
(1)甲醛合成车间 煤或天然气 →合成气(CO,H2)→甲醇(CH3OH)→
HO(CH2O)3H + CH2(OH)2
HO(CH2O)4 H + H2O
②生成TOX (熔点63 ℃)
HO(CH2O)3H
(CH2O)3 + H2O
(3)副反应:生成下列低沸点副产物
CH2O + H2O
HCOOH(100.5℃)+ CH3OH (64.7 ℃)
HCOOH + CH3OH CH2(OH)2 + 2CH3OH
聚甲醛工艺简介
性能与用途 共聚甲醛生产主要工艺
性能&用途
聚甲醛树脂,又称聚氧甲撑树脂(polyoxymethylene Resins ,POM ),于50年代由杜邦企业研制开发, 是目前世界三大通用工程塑料之一。 聚甲醛作为性能优异旳工程塑料,可分为两大类: 一是三聚甲醛或甲醛旳均聚体,称为均聚甲醛。均聚 甲醛具有优异旳刚性,拉伸强度高,单位质量旳拉伸 强度高于锌和黄铜,接近钢材,而且耐磨性能好、摩 擦系数小,但是热稳定性差、不耐酸碱。
(2)三聚甲醛共聚
①反应过程:采用两级反应机,预反应机 → 主反应机串联反应,在
预反应机内主要完毕原料混合、反应引起,在主反应机内完毕链增长。
②温度控制:反应机(器)为双螺杆输送机,采用外部夹套冷却
聚甲醛工艺简介3
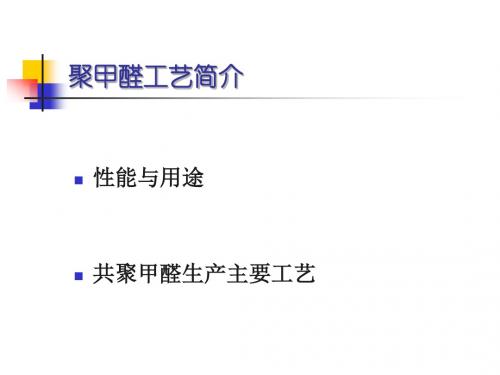
2.挥发分分离和TOX浓缩
主要杂质:甲缩醛、甲醇、甲酸、甲酸甲酯 稀HCHO溶液送往 “甲醛浓缩”
水分和低沸 TOX 17%wt HCHO43%wt 来自反应器
点副产物 含TOX 32%wt 的 甲醛溶液
浓缩塔
蒸馏塔
65%wt TOX溶液
3.TOX结晶,离心分离和熔融
理论基础:TOX和水形成共沸组成为69.8% TOX, 30.2%H2O的共沸物, 不能通过精馏制得高纯TOX。 结晶分离:TOX m.p. 62-63℃, 可溶于水,溶解度随温度升高而 增大,采用结晶分离方法,得到90-95%wt TOX。(-9℃乙二醇 水溶液,冷冻结晶,离心分离) 过程:65%wt TOX溶液 → 冷却结晶 → 离心过滤 → 冷冻脱 盐水洗涤 → 晶体熔融器熔融 → 螺杆泵输送 → 去萃取 特殊设备:三聚甲醛结晶器、三聚甲醛晶体熔融器、 TOX结晶悬浮液输送泵(螺杆泵),离心机 。
从塔顶脱除溶液中的甲醇,馏出液 为90.15%wt甲醇溶液,釜液送TOX、 DOX生产。
二、三聚甲醛(TOX)生产
1.三聚甲醛合成 2.挥发分分离和TOX浓缩 3.TOX结晶,离心分离和熔融 4.TOX萃取和精馏
1.三聚甲醛合成
CH2O+H2O n HO-CH2O-H
(1)多步反应
HO-CH2O-H
3、工艺理论基础
(1)在水溶液中,几乎所有甲醛都以单水合物和聚合 水合物形式存在。 60℃时,甲醛水溶液中游离HCHO占总量的0.1%wt; 100℃时,甲醛水溶液中游离HCHO占总量的1%wt。 CH2O+H2O n HO-CH2O-H HO-CH2O-H 甲二醇 HO ( CH2O)nH+ ( n-1)H2O 聚合水合物
甲醇-水分离连续精馏塔工艺流程
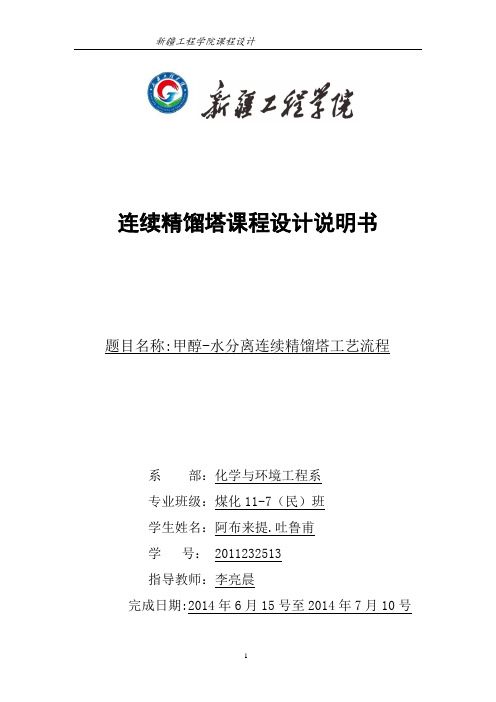
连续精馏塔课程设计说明书题目名称:甲醇-水分离连续精馏塔工艺流程系部:化学与环境工程系专业班级:煤化11-7(民)班学生姓名:阿布来提.吐鲁甫学号: 2011232513指导教师:李亮晨完成日期:2014年6月15号至2014年7月10号精馏是借助回流技术来实现高纯度和高回收率的分离操作,在抗生素药物生产中,需要甲醇溶媒洗涤晶体,洗涤过滤后产生废甲醇溶媒,然后对甲醇溶媒进行精馏。
操作一般在塔设备中进行,塔设备分为两种,板式塔和填料塔。
符合性能图,它对自行设计, 改进现有设备生产状况都较为重要。
随着对填料塔的研究和开发,性能优良的填料塔必将大量用于工业生产中。
关键词:精馏,填料塔,设备设计。
1、设计任务书 (5)2、设计的方案介绍 (5)2.1、操作压力的确定 (5)2.2、板式塔的分类与要求 (5)2.3、回流比的确定 (6)3、工艺流程图及其简单说明 (6)3.1、精馏塔的冷凝方式和加热 (6)3.2、工艺流程图 (7)4、精馏塔的工艺条件 (7)5、精馏塔物料衡算 (8)5.1、溢流装置的设计 (8)5.2、甲醇摩尔分率的转换 (9)5.3、塔板版面布置............................. 错误!未定义书签。
5.4、塔板校核 (10)6、塔板负荷性能图............................. 错误!未定义书签。
6.1、漏液线 (12)6.2、液体流量下限线 (12)6.3、液体流量上限线 (12)6.4、液沫夹带 (12)6.5、液泛线 (13)7、操作流程 (15)8、设计评述 (16)9、符号说明 (17)10、参考文献 (19)11、总结 (20)新疆工程学院课程设计评定意见设计题目系部_________________ 专业班级学生姓名_________________ 学生学号评定意见:评定成绩:指导教师(签名):年月日新疆工程学院化学与环境工程系系(部)课程设计任务书2013-2014学年2 学期2014年7月10日教师(签名)系(部)主任(签名)年月1、 设计任务书甲醇散堆填料精馏塔设计原料液状态处理量:100=F kmol/h ,常温常压 ,塔顶温度为65℃,塔釜温度为93.5℃进料浓度: 35.0=F x (甲醇的质量分数),塔顶出料浓度: 95.0=D x (甲醇的质量分数), 塔釜出料浓度:04.0=W x (甲醇的质量分数),323=OH CH M kg/kmol 182=O H M kg/kmol填料类型:DN25金属环矩鞍散堆填料2、设计的方案介绍2.1、操作压力的确定在精馏操作中,压力的影响非常大。
浅谈低浓度甲醛提浓技术

浅谈低浓度甲醛提浓技术作者:王国琴张璐来源:《中国化工贸易·下旬刊》2018年第07期摘要:甲醛是在化工产业来说是常见的原料,由于下游产品的甲醛聚合物行业的快速发展,浓缩甲醛已被用作其生产的重要组成部分,其使用量有所增加,并制定了新的甲醛浓缩的质量规定,也指出在甲醛稀释和浓缩的过程需要更精确的标准。
目前我国稀释甲醛浓缩过程由三个过程组成:加压蒸馏,真空旋风分离和甲缩醛氧化。
本文将介绍这三个过程并比较它们的优缺点。
关键词:低浓度;甲醛;提浓技术1 引言甲醛是重要的基础有机化工原料,并且也有很多的子产品出现。
在中国,甲醛一般会在三醛树脂的生产,占总甲醛消耗量的50%以上。
此外,甲醛用于季戊四醇,新戊二醇,1,4-丁二醇(BDO),三羟甲基丙烷及其化合物等化学产品以及肥料,药品和日用化学品。
在众多的子产品中,甲醛聚合物是一个尤为重要的产品。
根据它们聚合度的不同,主要有两大类多聚甲醛和聚甲醛。
在多聚甲醛和聚甲醛的生产中,甲醇的浓度必须是高的。
但目前甲醛是以甲醇为原料,采用银或铁-钼法生产的。
但是,产生的甲醛浓度要低于55%,并且需要去除很多的水份。
不仅能量消耗很大,还有设备腐蚀和回收稀释甲醛的等问题的存在。
甲醛作为生产原料必须使用浓度高的,可以显着提高反应设备的反应速度和利用率,节约能源,降低消耗,经济效益有所提高,生产成本有所降低。
目前国内甲醛浓缩工艺比较常见的工艺包括甲缩醛氧化工艺和加压蒸馏浓缩工艺。
本文将重点介绍这三个集中过程并比较它们的优缺点。
2 加压精馏浓缩工艺在常压下,聚甲醛水合物和水合物是甲醛在甲醛水溶液中主要存在的形式,二者的数量级相同,甲醛浓度很低,在大气压下不可能从液相挥发甲醛。
在实验中已知,压力和甲醛水溶液的相对挥发度是成正比例的关系,并且在较大的气压下,反应如下:nCH2O+H2O↔nHOCH2OH在压力作用下,这个反应会逆向进行,使得甲醛浓度在溶液会增加。
大气压越高,水的脱出与甲醛在溶液中的蒸发速度之差越高。
催化反应精馏法制甲缩醛(实验指导书)

实验十催化反应精馏法制甲缩醛反应精馏法是集反应与分离为一体的一种特殊精馏技术,该技术将反应过程的工艺特点与分离设备的工程特性有机结合在一起,既能利用精馏的分离作用提高反应的平衡转化率,抑制串联副反应的发生,又能利用放热反应的热效应降低精馏的能耗,强化传质。
因此,在化工生产中得到越来越广泛的应用。
一、实验目的(1) 了解反应精馏工艺过程的特点,增强工艺与工程相结合的观念。
(2) 掌握反应精馏装置的操作控制方法,学会通过观察反应精馏塔内的温度分布,判断浓度的变化趋势,采取正确调控手段。
(3) 学会用正交设计的方法,设计合理的实验方案,进行工艺条件的优选。
(4) 获得反应精馏法制备甲缩醛的最优工艺条件,明确主要影响因素。
二、实验原理本实验以甲醛与甲醇缩合生产甲缩醛的反应为对象进行反应精馏工艺的研究。
合成甲缩醛的反应为:2CH 3OH CH 2O C3H6O 2H2O (1)该反应是在酸催化条件下进行的可逆放热反应,受平衡转化率的限制,若采用传统的先反应后分离的方法,即使以高浓度的甲醛水溶液( 38—40%)为原料,甲醛的转化率也只能达到60%左右,大量未反应的稀甲醛不仅给后续的分离造成困难,而且稀甲醛浓缩时产生的甲酸对设备的腐蚀严重。
而采用反应精馏的方法则可有效地克服平衡转化率这一热力学障碍,因为该反应物系中各组分相对挥发度的大小次序为:甲缩醛甲醇甲醛水,可见,由于产物甲缩醛具有最大的相对挥发度,利用精馏的作用可将其不断地从系统中分离出去,促使平衡向生成产物的方向移动,大幅度提高甲醛的平衡转化率,若原料配比控制合理,甚至可达到接近平衡转化率。
此外,采用反应精馏技术还具有如下优点:(1) 在合理的工艺及设备条件下,可从塔顶直接获得合格的甲缩醛产品。
(2) 反应和分离在同一设备中进行,可节省设备费用和操作费用。
(3) 反应热直接用于精馏过程,可降低能耗。
(4) 由于精馏的提浓作用,对原料甲醛的浓度要求降低,浓度为7%—38%的甲醛水溶液均可直接使用。
甲醇和水筛板精馏塔分离

摘要本次设计采用板式精馏塔(筛孔塔)分离甲醇——水溶液。
采用筛板精馏塔,进行甲醇-水的分离。
明确设计条件后确定设计方案以及设计步骤。
首先进行精馏塔的工艺设计,做全塔物料衡算求气液流量,利用excel求实际回流比为,操作线方程,实际塔板数以及塔径。
其次进行塔板工艺尺寸的计算,分别求出精馏段和提馏段的堰高、弓降液管的宽度和横截面积、降液管底隙高度再确定塔板上筛孔数目,并采用正三角形排列。
对塔板的流体力学性能验算检验均符合要求。
最后确定精馏塔的结构中的人孔、管道、封头、筒体、支座等的尺寸;以及附属设备冷凝器、预热器,泵的型号。
关键词:板式精馏塔;甲醇--水;设计计算AbstractThe d esign uses a fl oat valve column(sieve tower)to separate methanol – water. After und erstanding the conditions of d esign, we need to list the d esign steps. First of all, d esigning the distillation process .In this step, we calculated the liquid and vapor fl ow by whol e tower material balance equation, got actual reflux ratio by excel ,acquired operating line equation, and found the actual plate number and the column diameter round .Second, calculating process dimensions for plates. Checking on the tray hydrodynamics test are in line with requirements. Finally, finding proper distillation manhol e structure, pipes, head, cylind er, bearings and other dimensions; and ancillary equipment cond ensers, heater, pump mod el.Keywords: Plate distillation column; methanol - water; d esign cal culations目录摘要 (I)Abstract (Ⅱ)引言 (1)第1章设计条件与任务 (2)1.1设计条件 (2)1.2设计任务 (2)第2章设计方案的确定 (3)2.1操作条件的确定 (3)2.1.1操作压力 (3)2.1.2进料状态 (3)2.1.3加热方式 (3)2.2确定设计方案的原则 (4)2.2.1满足工艺和操作的要求 (4)2.2.2满足经济上的要求 (4)2.2.3保证安全生产 (4)第3章精馏塔的工艺设计 (5)3.1 物料衡算 (5)3.2实际回流比 (5)3.2 .1相平衡曲线的确定 (5)3.2.2操作线方程的建立 (6)3.3理论塔板数的确定 (8)3.4实际塔板数的计算 (10)3.4.1 总板效率E T的计算 (10)3.4.2 实际塔板数的计算 (10)3.5精馏塔的工艺条件及有关物性数据计算123.5.1 操作温度的确定 (12)3.5.2操作压强的确定 (12)3.5.3 气体密度的计算: (12)3.5.4 平均密度的计算 (12)3.5.5 表面张力的计算 (13)3.5.6液体平均粘度计算 (15)3.6精馏塔的塔体工艺尺寸计算 (15)第4章塔板工艺尺寸的计算 (18)4.1精馏段以及提留段塔板工艺尺寸的计算 (18)4.1.1堰高的计算 (18)4.1.2 降液管底隙高度h o的计算 (18)4.1.3弓降液管的宽度和横截面积的计算 (20)4.2塔板的分布及筛孔排列 (20)4.2.1 塔板分布 (20)4.2.2筛孔排列 (21)4.3筛板的流体力学性能检验 (22)4.3.1塔板压降 (22)4.3.2液沫夹带 (22)4.3.3.漏液 (23)4.3.4液泛 (23)4.4塔板负荷性能图 (24)4.4.1 漏液线 (24)4.4.2 液沫夹带线 (25)4.4.3液相负荷下限线 (25)4.4.4液相负荷上限线 (26)4.4.5.液泛线 (27)第5章板式塔的结构 (31)5.1塔体结构 (31)5.1.1 塔顶空间 (31)5.1.2 人孔 (31)5.1.3塔釜高度H B (31)第6章附属设备 (32)6.1冷凝器 (32)6.2预热器 (32)6.3离心泵的选用 (33)第7章接管尺寸的确定 (34)7.1液流管 (34)7.1.1进料管 (34)7.1.2回流管 (34)7.1.3塔釜出料管 (34)7.2汽流管 (35)7.2.1塔顶蒸汽出料管 (35)7.2.2塔釜进气管 (35)第8章附属高度确定 (35)8.1筒体 (35)8.2封头 (36)8.3吊柱 (36)8.4支座 (37)8.5除沫器388.6塔总体高38第9章附属设备设计结果汇总 (37)第10章设计评价 (41)参考文献 (42)引言甲醇最大的用途是制造其他化学品。
甲醛萃取方法

1 I2)=0.1mol/L]标准溶液 2 配制: 用移液管吸取 0.1mol/L 碘溶液 100ML 于 1L 棕色容量瓶中,加水稀释到 刻度,摇匀,储存于暗处。 标定:此溶液不作预先标定。使用时,借助与试液同时进行的空白试验以 0.01mol/L 硫代硫酸钠标准溶液定之。 4.11.5.2.9 乙酰丙酮(CH2COCH2COCH3,体积百分浓度 0.4%)溶液 配制:用移液管吸取 4ML 乙酰丙酮于 1L 棕色容量瓶中,并加蒸馏水稀释到刻 度,摇匀,储存于暗处。 4.11.5.2.10 乙酸铵(CH3COONH4,质量百分浓度 20%)溶液
1
4.11.3 试剂 ------甲苯(C2H8) ,分析纯; ------碘化钾(KI) ;分析纯; ------重铬酸钾(K2 Cr2 O7),优级纯; -----碘化汞(HgI2),优级纯; ------无水碳酸钠(Na2S2O3·5H2O),分析纯; ----碘化汞(HGI2) ,分析纯; ----无水碳酸纳(Na2S2CO3),分析纯; ----硫酸(H2SO4) ,ρ=1.84g/ml,分析纯; ----盐酸(HCI) ,ρ=.1.19g/ml,分析纯; ----氢氧化钠(NaOH) ,分板纯; ----碘(I2) ,分析纯; ----可溶性淀粉,分析纯; ----乙酰丙酮(CH3COCH2COCH3) ,优级纯; ----乙酸铵(CH3COONH4) ,优级纯; ----甲醛溶液(CH2O) ,浓度 35%-40%) 。 4.11.4 试件尺寸 长 l=20+0 ㎜;宽 b=20+0 ㎜。 4.11.5 方法 4.11.5.1 仪器校验 先将仪器如图 14 所示安装,并固定在铁座上。采用套式恒温器加热烧瓶,将 500ML 甲苯加入 1000ML 具有标准磨口的圆底烧瓶中,另将 100ML 甲苯及 1000ML 蒸馏水加入萃取管内,然后开始蒸馏。调查节加热器,使回流速度保持为每分钟 30ML,回流时萃取管中液体温度不得超过 40℃,若温度超过 40℃,必须采取降 温措施,以保证甲醛在水中的溶解。 4.11.5.2 溶液配制 4.11.5.2.1 硫酸(1:1 体积浓度) :量取 1 体积硫酸(ρ=1.84g/ml)在搅拌下缓 缓倒入 1 体积蒸馏水中,搅匀,冷却后放置在细口瓶中。 4.11.5.2.2 硫酸(1mol/L):量取约 54ML 硫酸(ρ=1.84g/ml)在搅拌下缓缓倒 入适量蒸馏水中,搅匀,冷却后放置在 1L 容量瓶中,加蒸馏水稀释至刻度,摇 匀。 4.11.5.2.3 氢氧化钠(1mol/L) :称取 1G 可溶性淀粉,加入 10ML 蒸馏水中,搅 拌下注入 200ML 沸水中,再微沸 2min,放置待用(此试剂使用前配制).
甲醇--水分离填料精馏

甲醇--水分离填料精馏课程设计课程名称:化工原理课程设计设计题目:甲醇-水分离过程填料精馏塔设计院系:化学工程学院学生姓名:张雪晗学号:0121020390229专业班级:化工1002班指导教师:史彬2013 年01 月12 日甲醇-水分离过程填料精馏塔设计目录前言 (3)1设计方案的确定 (3)2精馏塔的物料衡算 (4)2.1原料液及塔顶、塔底产品的摩尔分率 (4)2.2 原料液及塔顶、塔底产品的平均摩尔质量 (5)2.3物料衡算 (5)3塔板数的确定 (5)3.1解析法求理论板层数 (6)3.2全塔效率E (7)3.3实际塔板数的求取 (9)4 精馏塔的工艺条件及物性数据的计算 (9)4.1工艺条件 (9)4.2平均摩尔质量 (9)4.3平均密度计算 (10)4.4液体平均表面张力计算 (11)4.5液体平均粘度计算 (12)5精馏塔的塔体工艺尺寸计算 (12)5.1 塔径的计算 (12)5.2填料层高度计算 (14)6填料层压降计算 (14)7附属设备及主要附件的选型计算 (14)7.1,塔顶出料口管径的计算 (14)7.2,回流管径的计算 (15)7.3, 进料口的管径的计算 (15)7.4塔釜出料口的管径的计算 (15)7.5筒体厚度 (15)7.6 封头 (17)7.7冷凝器 (17)7.8加热器 (17)8小结 (17)9全章主要符号说明 (19)前言填料塔操作时,液体自塔上部进入,通过液体分布装置均匀淋洒于填料层上,继而沿填料表面缓慢下流。
气体自塔下部进入,穿过栅板沿着填料间隙上升。
这样,气液两相沿着塔高在填料表面与填料自由空间连续逆流接触,进行传质和传热。
甲醇-水属于难分离物系,选用填料精馏塔的分离效率较高,容易满足生产要求。
1设计方案的确定本设计任务为。
分离甲醇-水混合物,对于二元混合物的分离,一般采用连续精馏流程。
精馏是分离液体混合物最常用的一种操作,它通过汽、液两相的直接接触,利用组分挥发度的不同,使易挥发组分由液相向汽相传递,难挥发组分由汽相向液相传递,是汽、液两相之间的传质过程。