V17, N7 Snooks
Acer Aspire V17 Nitro Black Edition VN7-792G-75RU

w Windows 10 w 17.3" Full HD (1920 x 1080) widescreen LED-backlit IPS display w 16GB DDR4 Dual Channel Memory w NVIDIA® GeForce® GTX 960M with 4 GB of dedicated GDDR5 VRAM w 1TB 5400RPM SATA Hard Drive w 6X Blu-ray DiscTM w HD Webcam (1280 x 720)
User's Guide
Let the Aspire V Nitro series be your gaming and entertainment hub with its impressive 17.3" Full HD Widescreen LED-backlit IPS Display with a true 16:9 cinematic format. From game play to watching a movie, you’ll experience consistent, brilliant color and a full viewing experience from any perspective.
4-speaker surround sound system, Acer TrueHarmony Plus and Dolby® Audio surround sound delivers rich audio that brings the big screen experience to wherever you are. The one-of-a-kind speaker design limits audio distortion, delivers a wide range of bass, and boosts volume so that it fills the room ensuring movies come to life, songs have more depth, and games are even more engaging.
NI sbRIO-9627单板RIO OEM设备技术规格说明说明书
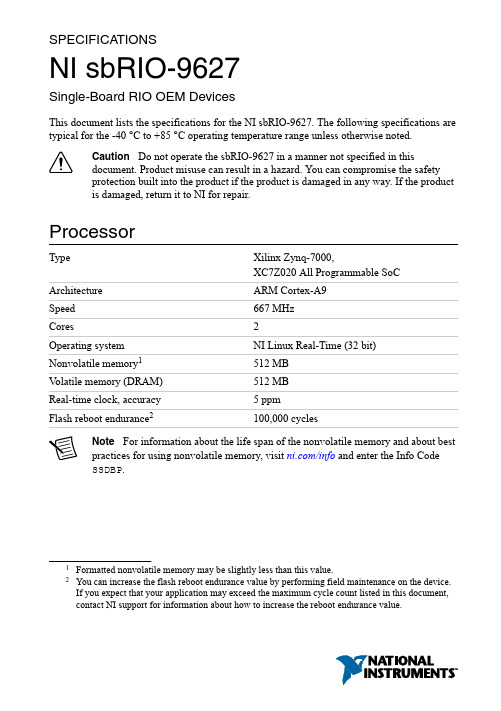
SPECIFICA TIONSNI sbRIO-9627Single-Board RIO OEM DevicesThis document lists the specifications for the NI sbRIO-9627. The following specifications are typical for the -40 °C to +85 °C operating temperature range unless otherwise noted.Caution Do not operate the sbRIO-9627 in a manner not specified in thisdocument. Product misuse can result in a hazard. You can compromise the safetyprotection built into the product if the product is damaged in any way. If the productis damaged, return it to NI for repair.ProcessorType Xilinx Zynq-7000,XC7Z020 All Programmable SoC Architecture ARM Cortex-A9Speed667 MHzCores2Operating system NI Linux Real-Time (32 bit)Nonvolatile memory1512 MBV olatile memory (DRAM)512 MBReal-time clock, accuracy 5 ppmFlash reboot endurance2100,000 cyclesNote For information about the life span of the nonvolatile memory and about bestpractices for using nonvolatile memory, visit /info and enter the Info CodeSSDBP.1Formatted nonvolatile memory may be slightly less than this value.2You can increase the flash reboot endurance value by performing field maintenance on the device.If you expect that your application may exceed the maximum cycle count listed in this document, contact NI support for information about how to increase the reboot endurance value.Operating SystemNote For minimum software support information, visit /info and enter theInfo Code swsupport.Supported operating system NI Linux Real-Time (32-bit)Minimum software requirementsApplication softwareLabVIEW LabVIEW 2015,LabVIEW 2015 Real-Time Module,LabVIEW 2015 FPGA ModuleEclipse Edition 2014C/C++ Development Tools forNI Linux Real-Time3Driver software NI CompactRIO Device Drivers August 2015 Reconfigurable FPGAType Xilinx Zynq-7000,XC7Z020 All Programmable SoCNumber of logic cells85,000Number of flip-flops106,400Number of 6-input LUTs53,200220Number of DSP slices(18 x 25 multipliers)Available block RAM560 KBNumber of DMA channels16Number of logical interrupts32Network/Ethernet PortNumber of interfacesFront Panel Ethernet 1 (Eth0)RMC Ethernet 1 (Eth1)3C/C++ Development Tools for NI Linux Real-Time is an optional interface for C/C++programming of the sbRIO-9627 processor. Visit /info and enter Info Code RIOCdev for more information about the C/C++ Development Tools for NI Linux Real-Time.2| | NI sbRIO-9627 SpecificationsNetwork interface10Base-T, 100Base-TX, and1000Base-T Ethernet4Compatibility IEEE 802.3Communication rates10 Mbps, 100 Mbps,1000 Mbps auto-negotiated, half-/full-duplex Maximum cabling distance100 m/segmentRS-232 (DTE) Serial PortNumber of interfacesOnboard RS-232 2 (Serial1, Serial2)RMC RS-232 via FPGA 3.3 V DIO 4 (Serial4, Serial5, Serial6, Serial7)Baud rate support ArbitraryMaximum baud rate230,400 bpsData bits5, 6, 7, 8Stop bits1, 2Parity Odd, Even, Mark, SpaceFlow control RTS/CTS, XON/XOFF, DTR/DSR, NoneRS-485 Serial PortNumber of interfacesOnboard RS-485 1 (Serial3)RMC RS-485 via FPGA 3.3 V DIO 2 (Serial8, Serial9)Maximum baud rate460,800 bpsData bits5, 6, 7, 8Stop bits1, 1.5, 2Parity Odd, Even, Mark, SpaceFlow control XON/XOFF4For revision D and earlier, 1000Base-T Ethernet link and communication is not guaranteed forprimary or secondary Ethernet ports below -20 °C. If you expect ambient temperatures below-20 °C, NI recommends using a 10/100 network infrastructure or assigning 10/100Mbpscommunication speeds to the Ethernet Adapter in NI Measurement & Automation Explorer(MAX).NI sbRIO-9627 Specifications| © National Instruments| 3Wire mode4-wire, 2-wire, 2-wire auto Isolation voltage, port to earth ground NoneEmbedded CANNumber of interfacesOnboard CAN 1 (CAN0)RMC CAN via FPGA 3.3 V DIO 1 (CAN1)Onboard CAN transceiver NXP PCA82C251T Maximum baud rate 1 MbpsMinimum baud rate10 kbpsUSB PortNumber of interfacesFront Panel USB Host 1 (USB0)RMC USB Host/Device 1 (USB1) Compatibility USB 2.0, Hi-Speed Maximum data rate480 Mb/sMaximum front panel USB current900 mASD Card SlotNumber of interfacesFront Panel SD 1 (SDIO0)RMC SD via FPGA 3.3 V DIO 1 (SDIO1)Supported Standards SD, SDHC5Front Panel SD ThroughputRead12.0 MB/s maximumWrite9.0 MB/s maximum5Both standard SD and microSD interfaces are supported.4| | NI sbRIO-9627 SpecificationsRMC SD via FPGA DIO ThroughputRead8.0 MB/s maximumWrite 6.5 MB/s maximumNote RMC SD has slower throughputs as the Xilinx Zynq-7000 requires SDinterfaces through the FPGA to operate at standard speed rather than at high speed.3.3 V Digital I/O on RMC ConnectorNumber of DIO channels96Maximum tested current per channel±3 mANote The performance of the RMC DIO pins is bounded by the FPGA, signalintegrity, the application timing requirements, and the RMC design. A general SPIapplication will typically be able to meet these requirements and achieve frequenciesof up to 10 MHz. For more information on using DIO to connect to RMCs, visit/info and enter the Info Code RMCDIO.Input logic levelsInput low voltage, V IL-0.3 V minimum; 0.8 V maximumInput high voltage, V IH 2.0 V minimum; 3.45 V maximumOutput logic levels2.4 V minimum;3.45 V maximumOutput high voltage, V OHwhen sourcing 3 mA0.0 V minimum; 0.4 V maximumOutput low voltage, V OLwhen sinking 3 mA3.3 V Digital I/O on 50-Pin IDC ConnectorNumber of DIO channels4Maximum tested current per channel±3 mAInput logic levelsInput low voltage, V IL-0.3 V minimum; 0.8 V maximumInput high voltage, V IH 2.0 V minimum; 5.25 V maximumNI sbRIO-9627 Specifications| © National Instruments| 5Output logic levelsOutput high voltage, V OH2.4 V minimum;3.45 V maximumwhen sourcing 3 mA0.0 V minimum; 0.4 V maximumOutput low voltage, V OLwhen sinking 3 mAAnalog Input CharacteristicsNumber of channels16 single-ended or 8 differential ADC resolution16 bitsMaximum aggregate sampling rate200 kS/sInput range±10 V, ±5 V, ±2 V, ±1 V Maximum working voltage (signal + common mode)10 V range±11 V5 V range±10.5 V2 V range±9 V1 V range±8.5 VInput impedancePowered on> 1 GΩ in parallel with 100 pFPowered off/overload 2.3 kΩ minimumOvervoltage protectionPowered on±25 V, for up to 2 AI pinsPowered off±15VAI accuracy6| | NI sbRIO-9627 SpecificationsGain drift 12 ppm of reading/°C Offset drift 4 ppm of range/°C AI noise10 V range 200 μVrms 5 V range 105 μVrms 2 V range 45 μVrms 1 V range 30 μVrmsINL ±64 ppm of range, maximum DNLNo missing codes guaranteed CMRR, DC to 60 Hz -80 dB Input bandwidth (-3 dB)540 kHz, typical Settling error (multichannel scanning)±60 ppm step size, typical Crosstalk (10 kHz)-70 dBTypical performanceFigure 1. Common Mode Rejection Ratio versus FrequencyC M R R (d B )Frequency (Hz)NI sbRIO-9627 Specifications | © National Instruments | 7Figure 2. Normalized Signal Amplitude versus FrequencyN o r m a l i z e d S i g n a l A m p l i t u d e (d B )Frequency (Hz)Figure 3. Settling Error versus Source ImpedanceE r r o r (p p m o f S t e p S i z e )Source Impedance (Ω)10010001000010000010000010000100010010Analog Output CharacteristicsNumber of channels 4DAC resolution16 bits8 | | NI sbRIO-9627 SpecificationsMaximum update rate6336 kS/sRange±10 VOverrange operating voltageMinimum10.3 VTypical10.6 VMaximum10.9 VOutput impedance0.4 Ω typicalCurrent drive±3 mA/channel maximumProtection Short-circuit to groundPower-on state70 VAO accuracyGain drift23 ppm of reading/°COffset drift 5.4 ppm of range/°CINL±194 ppm of range, maximumDNL±16 ppm of range, maximumCapacitive drive 1.5 nF, typicalSlew rate 3.7 V / μsec, typicalSettling time (100 pF load to 320 μV)FS step50 μs2 V step12 μs0.2 V step9 μs6This is the maximum update rate when running one AO channel in a loop with the FPGA top-level clock set to 40 MHz.7When the analog output initializes, a voltage glitch occurs for about 20 μs, peaking at 1.3 V,typical.8Range is 5 V.NI sbRIO-9627 Specifications| © National Instruments| 9CMOS BatteryNote The battery is user-replaceable. The NI sbRIO device ships with a BR1225coin cell battery from RAYOV AC, which is industrial-rated. Ensure that powerremains connected to the NI sbRIO device while you replace the battery so thattime-keeping is not disrupted. Refer to the Battery Replacement and Disposalsection for information about replacing the battery.10 yearsTypical battery life with power applied topower connectorTypical battery life in storage at 55 °C 2.5 years9Power Outputs on RMCCaution Exceeding the power limits may cause unpredictable device behavior.+5 V power outputOutput voltage 5 V ±5%Maximum current 1.5 AMaximum ripple and noise50 mV+3.3 V_AUX power outputOutput voltage 3.3 V ±5%Maximum current0.33 AMaximum ripple and noise50 mVFPGA_VIO power outputOutput voltage 3.3 V ±5%Maximum current0.33 AMaximum ripple and noise50 mVPower RequirementsThe NI sbRIO device requires a power supply connected either to the power connector or through the VIN_filtered pins through the RMC. Refer to the Powering On the NI sbRIO Device section in the NI sbRIO-9627 Getting Started Guide on /manuals for information about connecting the power supply. Refer to the NI sbRIO-9607/9627 RMC9Battery life may drop dramatically in extreme temperatures.10| | NI sbRIO-9627 SpecificationsDesign Guide on /manuals for more information about how to power the NI sbRIO device through the RMC.Caution Exceeding the power limits may cause unpredictable device behavior.Recommended power supply55 W, 30 VDC maximumPower supply voltage range9 VDC to 30 VDCReversed-voltage protection30 VDCPower consumption with RMC29 W maximumEnvironmentalCaution Clean the sbRIO-9627 with a soft, nonmetallic brush. Make sure that thedevice is completely dry and free from contaminants before returning it to service.-40 °C to 85 °C10Local ambient operating temperature neardevice (IEC 60068-2-1, IEC 60068-2-2)Maximum reported onboard sensor temperatureCPU/FPGA temperature98 °CPrimary System temperature85 °CSecondary System temperature85 °CTable 1. Component Maximum Case TemperatureThe sbRIO-9627 includes three onboard temperature monitoring sensors to simplify validation of a thermal solution by indicating thermal performance during validation and deployment.10If you expect ambient temperatures below -20 °C, NI recommends using a 10/100 network infrastructure or assigning 10/100Mbps communication speeds to the Ethernet Adapter in NI MAX.Refer to the Network/Ethernet Port section of this document for more information.11Use digital approach to ensure the on-chip temperature reading is below 98°C.NI sbRIO-9627 Specifications| © National Instruments| 11The sensors measure the CPU/FPGA junction temperature and printed circuit board temperatures that can be used to approximate the primary and secondary side local ambient temperatures. This approach is called digital validation. Alternatively, the traditional analog approach using thermocouples can be used to validate thermal performance. The digital approach is more accurate for determining the performance of the CPU/FPGA but is more conservative for determining the local ambient temperatures. NI recommends using digital validation.For digital validation, ensure that the reported CPU/FPGA, reported Primary System, and reported Secondary System temperatures do not exceed any of the maximum temperatures listed in this document. Thermal validation is complete if the reported temperatures are within specifications. For more information about how to access the onboard sensors, visit / info and enter the Info Code sbriosensors. If the reported Primary System temperature or reported Secondary System temperature exceed the maximum temperatures listed in this document then analog validation may be used for further verification.For analog validation, measure the local ambient temperature by placing thermocouples on both sides of the PCB, 5 mm (0.2 in.) from the board surface. Avoid placing thermocouples next to hot components such as the CPU/FPGA or near board edges, which can cause inaccurate temperature measurements. In addition to the local ambient temperature, the case temperature of the components should not exceed the recommended maximum case temperature.Note Some systems may require a heat sink or air flow to remain within themaximum allowed temperature ranges. You can mount the Thermal Kit forNI sbRIO-9607/9627/9637 (153901-02) heat spreader on the NI sbRIO device.Note The NI sbRIO device thermal performance is greatly influenced by severalfactors, including resource utilization, mounting, and adjacent power dissipation.These factors can substantially affect the achievable external ambient temperature atwhich the maximum local and reported temperatures are reached. NI recommendsadditional thermal design to remain within the maximum allowed temperatureranges. For information about and examples of environmental and design factors thatcan affect the thermal performance of NI sbRIO systems, visit /info and enterthe Info Code sbriocooling. For device-specific guidelines about enablingproper thermal design, refer to the NI sbRIO-9627 User Manual on /manuals.-40 °C to 85 °CStorage temperature(IEC 60068-2-1, IEC 60068-2-2)Operating humidity (IEC 60068-2-78)10% RH to 90% RH, noncondensing Storage humidity (IEC 60068-2-78)5% RH to 95% RH, noncondensing Maximum altitude5,000 mPollution Degree (IEC 60664)2The NI sbRIO device is intended for indoor use only.12| | NI sbRIO-9627 SpecificationsPhysical CharacteristicsWeight131.3 g (4.631 oz)Safety VoltagesConnect only voltages that are below these limits.V terminal to C terminal30 VDC maximum, Measurement Category I Measurement Category I is for measurements performed on circuits not directly connected to the electrical distribution system referred to as MAINS voltage. MAINS is a hazardous live electrical supply system that powers equipment. This category is for measurements of voltages from specially protected secondary circuits. Such voltage measurements include signal levels, special equipment, limited-energy parts of equipment, circuits powered by regulated low-voltage sources, and electronics.Caution Do not connect the sbRIO-9627 to signals or use for measurements withinMeasurement Categories II, III, or IV.Environmental ManagementNI is committed to designing and manufacturing products in an environmentally responsible manner. NI recognizes that eliminating certain hazardous substances from our products is beneficial to the environment and to NI customers.For additional environmental information, refer to the Minimize Our Environmental Impact web page at /environment. This page contains the environmental regulations and directives with which NI complies, as well as other environmental information not included in this document.Waste Electrical and Electronic Equipment (WEEE)EU Customers At the end of the product life cycle, all NI products must bedisposed of according to local laws and regulations. For more information abouthow to recycle NI products in your region, visit /environment/weee.Battery Replacement and DisposalBattery Directive This device contains a long-life coin cell battery. If you need toreplace it, use the Return Material Authorization (RMA) process or contact anNI sbRIO-9627 Specifications| © National Instruments| 13authorized National Instruments service representative. For more information aboutcompliance with the EU Battery Directive 2006/66/EC about Batteries andAccumulators and Waste Batteries and Accumulators, visit /environment/batterydirective.电子信息产品污染控制管理办法(中国RoHS)中国客户National Instruments符合中国电子信息产品中限制使用某些有害物质指令(RoHS)。
海底管道外腐蚀复合材料水下缠绕补强修复技术应用

至关重要由于海上服役环境比较恶劣海底管道
=!引!言
本身也会存在一定的缺陷同时运行期间还会存
随着海上油气资源产量的增长海底管道作为 在第三方破坏自然灾害海底管道服役期间的腐
油气资源输送的重要设施其安全和可靠的服役将 蚀等诸多因素影响海底管道的运行寿命其中
!作者简介刘军!'.,!男学士中级工程师主要从事海底管道材料性能研究WOA7K%+'%%",!$"ee-S/O
关键词!海底管道服役寿命复合材料补强修复
中图分类号 文献标志码 文章编号 DW',&-'" ,"',"$"&$$"% $(
!"#!$-!"$.,/001-"$'+ ,"',-"$"&-$%-$%
822/#)'4#"-"0G-!%(<'4%($%#-0"()%7%-4$%2'#(6%)*-#MB%<#4* 5('2 ."72"%J'4%(#'/&"0NO4%(-'/."(("&#"-0"(1B97'(#-%+#2%/#-%
89&4(')4!DH0LA@0L0NQ7S0/@L?JOAN790I7I0K790L79/7K;:ALA98MA10N1NA9LI/N1A17/97LQ0NP7OI/N1A91;A981H0 K/9:XL1A9879:S/NN/L7/9 IN/JK0O AKL/A@@0S1L1H0L0NQ7S0K7@0/@L?JOAN790I7I0K790LRDH0S/OI/L710 OA10N7AK N079@/NS0O091A98N0IA7N10SH9/K/:PHALJ009M780KP?L0879/9LH/N0I7I0K790L;J?171HAL9/1J009AIIK708791H0 N0IA7N/@L?JOAN790I7I0K790LR*L?JOAN790I7I0K790A8/I1L1H0S/OI/L710OA10N7AK?980NMA10NM79879:N079@/NS0O091A98 N0IA7N10SH9/K/:P1/SANNP/?1INAS17SAKAIIK7SA17/9RDH0INAS17SAKAIIK7SA17/9IN/Q0L1HA11H0S/OI/L710 OA10N7AK ?980NMA10NM79879:N079@/NS0O091A98N0IA7N10SH9/K/:P7LALA@0A98N0K7AJK0N079@/NS0O091A98N0IA7N10SH9/K/:PR DH7LIAI0NM7KK791N/8?S01H0N0IA7NOA10N7AKIN/I0N170L/@1H0S/OI/L710?980NMA10NM79879:N079@/NS0O091N0IA7N 10SH9/K/:P;1H0AIIK7SA17/980L7:9/@1H0N0IA7NLPL10O;A981H0S/9L1N?S17/910SH9/K/:P/@1H0N0IA7NLPL10OR :%;<"(!&!L?JL0AI7I0K790VL0NQ7S0K7@0VS/OI/L710OA10N7AKLVN079@/NS0O091N0IA7N
NUVOTON NM1817系列微控制器数据手册说明书
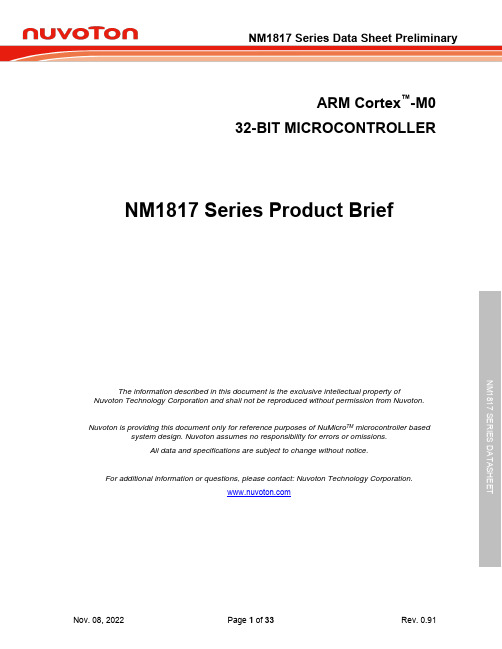
ARM Cortex™-M032-BIT MICROCONTROLLER NM1817 Series Product BriefNM1817 SERIES DATASHEET The information described in this document is the exclusive intellectual property ofNuvoton Technology Corporation and shall not be reproduced without permission from Nuvoton.Nuvoton is providing this document only for reference purposes of NuMicro TM microcontroller basedsystem design. Nuvoton assumes no responsibility for errors or omissions.All data and specifications are subject to change without notice.For additional information or questions, please contact: Nuvoton Technology Corporation.TABLE OF CONTENTS1GENERAL DESCRIPTION (3)2FEATURES (4)3PARTS INFORMATION LIST AND PIN CONFIGURATION (8)3.1Selection Guide (8)3.2Pin Configuration (8)3.2.1LQFP44-pin (8)3.3Pin Description (9)4BLOCK DIAGRAM (13)4.1NM1817 Block Diagram (13)5NM1817 ELECTRICAL CHARACTERISTICS (14)5.1NM1120 Absolute Maximum Ratings (14)5.2NM1120 DC Electrical Characteristics (15)5.3NM1120 AC Electrical Characteristics (20)5.3.1**External Input Clock (function has been reserved in NM1817) (20)5.3.2**External 4~24MHz High Speed Crystal (HXT)(function has been reserved in NM1817)215.3.3**Typical Crystal Application Circuits (function has been reserved in NM1817) (21)5.3.448MHz Internal High Speed RC Oscillator (HIRC) (21)5.3.510kHz Internal Low Speed RC Oscillator (LIRC) (21)5.4NM1120 Analog Characteristics (22)5.4.112-bit SAR ADC (22)5.4.2LDO & Power Management (23)5.4.3Brown-out Detector (23)5.4.4Power-on Reset (24)5.4.5Comparator (24)NM1817 SERIES DATASHEET5.4.6PGA (24)5.4.7Temperature Sensor (25)5.5NPT23011 Absolute Maximum Ratings (25)5.6NPT23011 Recommended Operating Conditions (26)5.7NPT23011 Static Electrical Characteristics (26)5.8NPT23011 Dynamic Electrical Characteristics (27)5.9DC Electrical Characteristic for LDO_5V_OUT (27)6PACKAGE DIMENSION (28)6.1LQFP 44-pin(10mm x 10mm) (28)7ORDERING INFORMATION (30)8REVISION HISTORY (31)1 GENERAL DESCRIPTIONThe NM1817 series 32-bit microcontroller(MCU) is embedded with ARM®Cortex™-M0 core andthree phase half-bridge power MOSFET and IGBT drivers with independent high and low sidereferenced output channels for motor driver applications which require high performance andintegration. The Cortex™-M0 is the ARM® embedded processor with 32-bit performance at a costequivalent to the traditional 8-bit microcontroller.The MCU of NM1817 series can run up to 48MHz and offers 29.5K-bytes embedded program flash,size configurable Data Flash (shared with program flash), 2K-byte flash for the ISP, 1.5K-byteSPROM for security, and 4K-byte SRAM. Plentiful system level peripheral functions, such as I/OPort, Timer, UART, SPI, I2C, PWM, ADC, Watchdog Timer, Analog Comparator and Brown-outDetector, have been incorporated into the NM1817 series in order to reduce component count,board space and system cost. These useful functions make the NM1817 series powerful for a widerange of motor driver applications.The floating channel can be used to drive an N-channel power MOSFET or IGBT in the high sideconfiguration which operates up to 600 volts. It’s also built-in the temperature sense output signalfor MCU detection & one comparator for over current protectionAdditionally, the NM1817 is equipped with ISP (In-System Programming) and ICP (In-CircuitProgramming) functions, which allow the user to update the program memory without removing thechip from the actual end product.NM1817 is the combination of NM1120 and NPT23011 Gate Driver. User may refer to the TRM ofNM1120 and the datasheet of NPT23011 for the detailed specification. The NM1120 BSP is alsofor NM1817 software developing.NM1120NPT23011NM1817NM1817 SERIES DATASHEETNM1817 SERIES DATASHEET2 FEATURES● Gate Driver⏹ Programmable enable/disable gate driver by MCU I/O of PC.4⏹ Floating channel designed for bootstrap operation up to + 600V⏹ Gate driver supply range from 12 to 18V⏹ VCC/VBS Under-voltage lock-out⏹ Cross conduction prevention⏹ High side output in phase with HIN● MCU Core⏹ ARM ® Cortex™-M0 core running up to 48MHz⏹ One 24-bit system timer⏹ Supports Low Power idle mode.⏹ A single-cycle 32-bit hardware multiplier⏹ NVIC for the 32 interrupt inputs, each with 4-level of priority⏹ Supports Serial Wire Debug (SWD) interface and two watch points/fourbreakpoints● Memory⏹ 29.5Kbytes Flash memory for program memory (APROM)⏹ Configurable Flash memory for data memory (Data Flash)⏹ 2KB Flash memory for loader (LDROM)⏹ Three 0.5KB Flash memory for security protection (SPROM)⏹ 4KB SRAM for internal scratch-pad RAM (SRAM)● Clock Control⏹ 48MHz internal oscillator (HIRC) (±1% accuracy at 250C, 5V)⏹ 10kHz internal low-power oscillator (LIRC) for Watchdog Timer and idle wake-up ● I/O Port⏹ Up to 15 general-purpose I/O (GPIO) pins⏹ Four I/O modes:◆ Quasi-bidirectional input/output◆ Push-Pull output◆ Open-Drain output◆ Input only with high impedance⏹ Optional TTL/Schmitt trigger input⏹ I/O pin can be configured as interrupt source with edge/level setting ⏹ Supports high driver and high sink I/O mode⏹ GPIO built-in Pull-up/Pull-low resistor for selection.● Timer⏹ Provides two channel 32-bit Timers; one 8-bit pre-scalar counter with 24-bit up-NM1817 SERIES DATASHEETtimer for each timer⏹ Independent clock source for each timer⏹ Provides One-shot, Periodic, Toggle and Continuous operation modes ⏹ 24-bit up counter value is readable through TDR (Timer Data Register) ⏹ Provides trigger counting/free counting/counter reset function triggered byexternal capture pin or internal comparator signal⏹ Supports event counter function⏹ Supports Toggle Output mode⏹ Supports wake-up from Idle or Power-down mode● Continuous Capture⏹ Timer0, Timer1 and Systick support Continuous Capture function which cancontinuously capture at most 4 edges on one signal● Enhanced Input Capture⏹ One unit of 24-bit input capture counter.⏹ Capture source:◆ I/O inputs: ECAP0, ECAP1 and ECAP2◆ ACMP Trigger◆ ADC Trigger● WDT (Watchdog Timer)⏹ Programmable clock source and time-out period⏹ Supports wake-up function in Power-down mode and Idle mode⏹ Interrupt or reset selectable on watchdog time-out● EPWM(Enhanced PWM Generator)⏹ Support a built-in 16-bit PWM clock generators, providing six PWM outputs orthree complementary paired PWM outputs⏹ Shared same clock source, clock divider, period and dead-zone generator ⏹ Supports group/independent/complementary modes⏹ Supports One-shot or Auto-reload mode⏹ Supports Edge-aligned and Center-aligned type⏹ Support Asymmetric mode⏹ Programmable dead-zone insertion between complementary channels ⏹ Each output has independent polarity setting control⏹ Hardware fault brake and software brake protections⏹ Supports rising, falling, central, period, and fault break interrupts⏹ Supports duty/period trigger A/D conversion⏹ Timer comparing matching event trigger PWM to do phase change⏹ Supports comparator event trigger PWM to force PWM output low for currentperiod⏹ Provides interrupt accumulation function⏹ Gate driver PWM output by MCU PWM controlif the ENGD pin of NM1817 is set to high level, then the output status ofNM1120 and gate driver is as the following table.MCU PWM Control Gate Driver PWM OutputPWM0/2/4 PWM1/3/5 UHO/VHO/WHO ULO/VLO/WLOH L ON OFFL H OFF ONL L OFF OFFH H OFF OFFOtherwise, if the ENGD pin of NM1817 is set to low level, then the output of gate driver is all off.●BPWM (Basic PWM Generator)⏹One 16-bit PWM generator which supports one 8-bit pre-scalar, one clock divider,two PWM timers (down counter) and one dead-zone generator⏹Two independent outputs or one complementary paired outputs.⏹PWM Interrupt request synchronized with PWM period⏹Edge-aligned type or Center-aligned type option●USCI (Universal Serial Control Interface Controller)⏹Two USCI devices⏹Supports to be configured as UART, SPI, I²C individually⏹Supports programmable baud-rate generator●ADC (Analog-to-Digital Converter)⏹12-bit ADC with 1M SPS⏹Supports 2 sample/holdNM1817 SERIES DATASHEET⏹Up to 8-ch single-end inputfrom I/O and one internal input from band-gap.⏹Conversion started either by software trigger, PWM trigger, ACMP trigger orexternal pin trigger⏹Supports temperature sensor for measureing chip temperature⏹Support Simultaneous and Sequential function to continuous conversion 4channels maximum.●Programmable Gain Amplifier (PGA)⏹Supports 8 level gain selects from 1, 2, 3, 5, 7, 9, 11 and 13.⏹Unity gain frequency up to 8MHz●Analog Comparator⏹Two analog comparators with programmable 16-level internal voltage reference⏹Build-in CRV (comparator reference voltage)⏹Supports Hysteresis function⏹Interrupt when compared results changed●Hardware Divider⏹Signed (two’s complement) integer calculation⏹32-bit dividend with 16-bit divisor calculation capacity⏹32-bit quotient and 32-bit remainder outputs (16-bit remainder with sign extendsto 32-bit)⏹Divided by zero warning flag⏹ 6 HCLK clocks taken for one cycle calculation⏹Waiting for calculation ready automatically when reading quotient and remainder●ISP (In-System Programming) and ICP (In-Circuit Programming)●BOD (Brown-out Detector)⏹8 programmable threshold levels:4.3V/4.0V/3.7V/3.0V/2.7V/2.4V/2.2V/2.0V⏹Supports Brown-out interrupt and reset option●96-bit unique ID●LVR (Low Voltage Reset)●Operating Temperature: -40℃~105℃●Packages:⏹44-pin LQFP (10x10mm)⏹Package is Halogen-free, RoHS-compliant and TSCA-compliant.NM1817 SERIES DATASHEETNM1817 SERIES DATASHEET3 PARTS INFORMATION LIST AND PIN CONFIGURATION3.1 Selection Guide P a r t N u m b e rF l a s h (K B ) S R A M (K B )I S PL o a d e r R O M(K B ) D a t a F l a s h I /O T im e r Connectivity I R C 48 M H z * B O D P W M An a l o g C o m p .P G A A D C (12-B it )Te m p er a t u r eS e n s orIC P /I S P I /A PPac k a geUSCI U A R T * I 2C S P I NM1817NT 29.5 4 2 √ 15 2 2 2 2 1 1 6 2 1 8x12bit 1 √ LQFP44Table 3.1-1 NM1817 Series Selection Guide3.2 Pin Configuration3.2.1 LQFP44-pin2401436587109114438373635342930272825262324121314151718192021162231323342433941NM1817LQFP 44-pin PB.1/ADC0_CH1/ACMP0_P1/ECAP_P1PB.2/ADC0_CH2/BPWM_CH1/ACMP0_P2/ECAP_P2PC.1/ADC0_CH4/STADC/ACMP0_P3/ACMP1_P1/SPI0_MOSI/SPI1_MISO /RESET PC.3/ACMP1_O/PGA_O/SPI0_CLK/SPI1_SS PD.1/ICE_CLK/ACMP1_P2/I2C0_SCL/SPI0_CLK/SPI1_SS/UART0_TXD PC.0/ADC0_CH3/BPWM_CH0/ACMP1_P0/I2C1_SCL/SPI0_SS/SPI1_CLK/UART1_TXDNCPD.5/UART0_TXDU_VS NC V_LOW_LOU_LO W_HOPC.2/ADC1_CH2/BRAKE/CCAP_P1/I2C1_SDA/SPI0_MISO/SPI1_MOSI/UART1_RXD W_VB NCNCCOMVCCNC PB.3/ACMP1_N/PGA_I/TM0U_VB PD.6/UART0_RXD VDD PB.0/ADC0_CH0/ACMP0_P0/ECAP_P0VSS ENGD V_HO NC V_VS NC NCLDO_CAP NC PB.4/ADC1_CH0/ACMP0_N/TM1U_HO PD.4/BPWM_CH0/UART1_RXD V_VB W_VSLDO_5V_OUT PD.2/ICE_DAT/ADC1_CH1/CCAP_P0/I2C0_SDA/SPI0_MOSI/SPI1_MISO/UART0_RXD PD.3/BPWM_CH1/UART1_TXDFigure 3.2-1 NM1817 LQFP 44-pin Diagram3.3 Pin DescriptionNM1120 NPT23011 NM1817NTPin Name Pin Type Description TSSOP28 SOP-20 LQFP 44-pin2 LDO_5V_OUT A 5V LDO output26 4 ENGD I Gate driver enable pin. The pin is also internally connected to PC.4 of NM1120.27 5 LDO_CAP P LDO output pin28 6 VSS P Ground pin for digital circuit 1 7 VDD P Power supply for digital circuit2 8 PD.6 I/O General purpose digital I/O pin UART0_RXD I Data receiver input pin for UART0.3 9 PB.0 I/O General purpose digital I/O pin.ADC0_CH0 A ADC0 channel0 analog input.ACMP0_P0 A Analog comparator0 positive input pin. ECAP_P0 I Enhanced Input Capture input pin4 10 PB.1 I/O General purpose digital I/O pin.ADC0_CH1 A ADC0 channel1 analog input.ACMP0_P1 A Analog comparator0 positive input pin. ECAP_P1 I Enhanced Input Capture input pin5 11 PB.2 I/O General purpose digital I/O pin.ADC0_CH2 A ADC0 channel2 analog input.BPWM_CH1 I/O PWM channel1 output/capture input. ACMP0_P2 A Analog comparator0 positive input pin. ECAP_P2 I Input capture channel 26 12 PB.4 I/O General purpose digital I/O pin.ADC1_CH0 A ADC1 channel0 analog input.ACMP0_N A Analog comparator0 negative input pin. TM1 I/OTimer1 event counter input / toggleoutput7 13 PC.1 I/O General purpose digital I/O pin.ADC0_CH4 A ADC0 channel4 analog input.STADC I ADC external trigger input.ACMP0_P3 A Analog comparator0 positive input pin.ACMP1_P1 A Analog comparator1 positive input pin.SPI0_MOSI I/O SPI0 1st MOSI (Master Out, Slave In)pin.SPI1_MISO I/O SPI1 MISO (Master In, Slave Out) pin.NM1817 SERIES DATASHEET8 14 nRESET I External reset input: active LOW, withan internal pull-up. Set this pin low resetto initial state.9 15 PB.3 I/O General purpose digital I/O pin. ACMP1_N A Analog comparator1 negative input pin. PGA_I A PGA input pinTM0 I/O Timer0 event counter input / toggleoutput10 16 PC.2 I/O General purpose digital I/O pin.ADC1_CH2 A ADC1 channel2 analog input.BRAKE I Brake input pin of EPWM.CCAP_P1 I Timer Continuous Capture input pinI2C1_SDA I/O I2C1 data input/output pin.SPI0_MISO I/O SPI0 1st MISO (Master In, Slave Out)pin.SPI1_MOSI I/O SPI1 MOSI (Master Out, Slave In) pin. UART1_RXD I Data receiver input pin for UART1.11 17 PD.2 I/O General purpose digital I/O pin.ICE_DAT I/O Serial wired debugger data pinADC1_CH1 A ADC1 channel1 analog input.CCAP_P0 I Timer Continuous Capture input pinI2C0_SDA I/O I2C0 data input/output pin.SPI0_MOSI I/O SPI0 1st MOSI (Master Out, Slave In)pin.SPI1_MISO I/O SPI1 MISO (Master In, Slave Out) pin. UART0_RXD I Data receiver input pin for UART0.12 18 PD.3 I/O General purpose digital I/O pin. BPWM_CH1 I/O PWM channel1 output/capture input. UART1_TXD O Data transmitter output pin for UART1.18 19 PC.3 I/O General purpose digital I/O pin. ACMP1_O O Analog comparator1 output. PGA_O A PGA output pinSPI0_CLK I/O SPI0 serial clock pin.SPI1_SS I/O SPI1 slave select pin17 20 PD.1 I/O General purpose digital I/O pin.ICE_CLK I Serial wired debugger clock pinACMP1_P2 A Analog comparator1 positive input pin.I2C0_SCL I/O I2C0 clock pin.NM1817 SERIES DATASHEETSPI0_CLK I/O SPI0 serial clock pin.SPI1_SS I/O SPI1 slave select pinUART0_TXD O Data transmitter output pin for UART0.16 21 PD.4 I/O General purpose digital I/O pin. BPWM_CH0 I/O PWM channel0 output/capture input. UART1_RXD I Data receiver input pin for UART1.15 22 PC.0 I/O General purpose digital I/O pin.ADC0_CH3 A ADC0 channel3 analog input.BPWM_CH0 I/O PWM channel0 output/capture input. ACMP1_P0 A Analog comparator1 positive input pin. I2C1_SCL I/O I2C1 clock pin.SPI0_SS I/O SPI0 slave select pin.SPI1_CLK I/O SPI1 serial clock pinUART1_TXD O Data transmitter output pin for UART1.19 23 PD.5 I/O General purpose digital I/O pin. UART0_TXD O Data transmitter output pin for UART0.7 24 W_LO HO Low side gate driver output8 26 W_VS HP High side floating supply return9 27 W_HO HO High side gate driver output10 28 W_VB HP High side floating supply11 31 COM HP Low side power supply return12 32 VCC HP Low side and logic fixed power supply13 33 V_LO HO Low side gate driver output14 35 V_VS HP High side floating supply return15 36 V_HO HO High side gate driver output16 37 V_VB HP High side floating supply17 40 U_LO HO Low side gate driver output18 42 U_VS HP High side floating supply return19 43 U_HO HO High side gate driver output20 44 U_VB HP High side floating supply25 1 HIN1 PWM0 connect to HIN124 2 LIN1 PWM1 connect to LIN123 3 HIN2 PWM2 connect to HIN222 4 LIN2 PWM3 connect to LIN221 5 HIN3 PWM4 connect to HIN320 6 LIN3 PWM5 connect to LIN3NM1817 SERIES DATASHEET13,14 1,3,25,29,30,34,38,39,41 No connected[1] Low voltage I/O type description. I: input, O: output, I/O: quasi bi-direction, D: open-drain, P:power pin, ST: Schmitt trigger, A: Analog input.[2] High voltage I/O type description. HI: input, HO: output, HP: power pin.NM1817 SERIES DATASHEETNM1817 SERIES DATASHEET 4 BLOCK DIAGRAM4.1 NM1817 Block Diagram Cortex-M048 MHz Clock Controller AHB APB-Bridge GPIO PA~PD ADC 8ch/12bit Watch Dog Timer Advanced Capture Serial Port UART/SPI/I2C EPWM 0~5Timer 0/1Flash Control ISP 4KB Info Option LDROM 2KB CONFIG SRAM 4KB 2 sets *ComparatorHW Divider 4~24MHz XTAL 32.768kHz XTAL 48MHz RC OSC10kHz RC OSC VHin VLin WHin WLinULin UHinBPWM 0~1MCU AP ROM29.5KB SP ROM 1.5KB Configurable Data FLASH (Share with AP ROM)PWM2PWM3PWM4PWM5PWM1PWM0Gate DriverPULSE GEN RSQU_VBU_HOU_VSU_LOR VCC 100K DRIVERDRIVER UVLOU Phase DriverV Phase Driver V_VB V_HO V_VS V_LO W Phase Driver W_VB W_HOW_VS W_LOCOMUHIN VCC_UVLO VCC ULIN VCC VHINVLIN VCC WHIN WLIN NOISE FILTER CROSS CONDUCTION PREVENTION CONTROL LOGICLDO VCCLDO_5V_OUTVCCEnhanced Input Capture ENGDPC.4En VSS 100KFigure 4.1-1 NM1817 Block Diagram5 NM1817 ELECTRICAL CHARACTERISTICSThe electrical characteristics refer to both MCU NM1120 and Gate Driver NPT23011.According to Figure 4.1-1, we can list a table of pin definition in NM1817 as below:Alternative function , MFP_0 means setting MFP[3:0]=0x0, MFP_5 means MFP[3:0]=0x5GPIO ICE XTAL ADC PWM_BRAKE ACMP0ACMP1PGA(OP)TIMER I2C SPIO SPI1UARTMFP_0MFP_1MFP_2MFP_3MFP_4MFP_5MFP_6MFP_7MFP_8MFP_9MFP_A MFP_BGPA0CLKO O EPWM_CH0O I²C1_SCL I/O SPI0_SS I/O SPI1_CLK I/O UART1_TXD OGPA1EPWM_CH1O I²C1_SDA I/O SPI0_MISO I/O SPI1_MOSI I/O UART1_RXD IGPA2EPWM_CH2O I²C0_SDA I/O SPI0_MOSI I/O SPI1_MISO I/O UART0_RX D IGPA3EPWM_CH3O I²C0_SCL I/O SPI0_CLK I/O SPI1_SS I/O UART0_TX D OGPA4XT_IN A EPWM_CH4OGPA5XT_OUT A EPWM_CH5O ACMP0_O OGPB0ADC0_CH0A ACMP0_P0A ICAP0IGPB1ADC0_CH1A ACMP0_P1A ICAP1IGPB2ADC0_CH2A BPWM_CH1O ACMP0_P2A ICAP2IGPB3ACMP1_N A PGA_I A T0I/OGPB4ADC1_CH0A ACMP0_N A T1I/OGPC0ADC0_CH3A BPWM_CH0O ACMP1_P0A I²C1_SCL I/O SPI0_SS I/O SPI1_CLK I/O UART1_TXD OGPC1ADC0_CH4A STADC I ACMP0_P3A ACMP1_P1A SPI0_MOSI I/O SPI1_MISO I/OGPC2ADC1_CH2A PWM_BRAKE I CCAP I I²C1_SDA I/O SPI0_MISO I/O SPI1_MOSI I/O UART1_RXD IGPC3ACMP1_O O PGA_O A SPI0_CLK I/O SPI1_SS I/OGPC4ICAP0InRESETGPD1ICE_CLK I ACMP1_P2A I²C0_SCL I/O SPI0_CLK I/O SPI1_SS I/O UART0_TX D OGPD2ICE_DAT I/O ADC1_CH1A CCAP I I²C0_SDA I/O SPI0_MOSI I/O SPI1_MISO I/O UART0_RX D IGPD3BPWM_CH1O UART1_TX D OGPD4BPWM_CH0O UART1_RXD IGPD5UART0_TX D OGPD6UART0_RX D IVDDVSS: Function has been reserved for another usage.Attention :a. Some functions would be prohibition because of the limitation of pin definition in NM1817.b. GPA0 ~ GPA5 should be set as EPWM0 ~ EPWM5, GPC4 should be set as GPIO.NM1817 SERIES DATASHEET5.1 NM1120 Absolute Maximum RatingsSymbol Parameter Min Max UnitV DD-V SS DC Power Supply-0.3+7.0V V IN Input Voltage V SS -0.3V DD +0.3V 1/t CLCL Oscillator Frequency424MHz T A Operating Temperature-40+105℃T ST Storage Temperature-55+150℃I DD Maximum Current into VDD-120mAI SS Maximum Current out of VSS-120mAI IO Maximum Current sunk by an I/O pin-35mA Maximum Current sourced by an I/O pin-35mA Maximum Current sunk by total I/O pins-100mA Maximum Current sourced by total I/O pins-100mAaffects the life and reliability of the device.5.2 NM1120 DC Electrical Characteristics(V DD - V SS = 2.1 ~ 5.5 V, T A = 25︒C)Symbol Parameter Min Typ Max Unit Test ConditionsNM1817 SERIES DATASHEETV DD Operation voltage 2.1 - 5.5 V V DD = 2.1V ~ 5.5V up to 48 MHz V SS/A VSS Power Ground -0.3 - - VV LDO LDO Output Voltage 1.5 VV BG Band-gap Voltage3 1.14 1.20 1.24 V V DD = 3.0V ~ 5.5V, T A = -40︒C~105︒CI DD5Operating CurrentNormal Run ModeHCLK = 48 MHz - 9.7 - mAV DD**HXT HIRCAll DigitalModules5.5V X 48 MHz VI DD6- 7.4 - mA 5.5V X 48 MHz X I DD7- 9.7 - mA 3V X 48 MHz V I DD8- 7.4 - mA 3V X 48 MHz XI DD1Operating CurrentNormal Run ModeHCLK = 24 MHz - 5.4 - mAV DD**HXT HIRCAll DigitalModules5.5V 24 MHz X VI DD2- 4.4 - mA 5.5V 24 MHz X X I DD3- 5.4 - mA 3V 24 MHz X V I DD4- 4.4 - mA 3V 24 MHz X XI DD9Operating CurrentNormal Run ModeHCLK = 16 MHz -3.7- mAV DD**HXT HIRCAll DigitalModules5.5V 16 MHz X VI DD10- 3.0 - mA 5.5V 16 MHz X X I DD11- 3.7 - mA 3V 16 MHz X V I DD12- 3.1 - mA 3V 16 MHz X XI DD9Operating CurrentNormal Run ModeHCLK = 12 MHz - 2.8 - mAV DD**HXT HIRCAll DigitalModules5.5V 12 MHz X VI DD10- 2.3 - mA 5.5V 12 MHz X XI DD11- 2.8 - mA 3V 12 MHz X VI DD12- 2.3 - mA 3V 12 MHz X XNM1817 SERIES DATASHEETI DD13Operating CurrentNormal Run ModeHCLK = 4 MHz - 1.2 - mAV DD**HXT HIRCAll DigitalModules5.5V 4 MHz X VI DD14- 1.0 - mA 5.5V 4 MHz X X I DD15- 1.2 - mA 3V 4 MHz X V I DD16- 1.0 - mA 3V 4 MHz X XI DD17Operating CurrentNormal Run ModeHCLK = 32 kHz - 291.7 - μAV DD**LXT LIRCAll DigitalModules5.5V 32 KHz V V[1]I DD18- 290.7 - μA 5.5V 32 KHz V X I DD19- 280.8 - μA3V 32 KHz V V[1] I DD20- 281.4 - μA3V 32 KHz V XI DD17Operating CurrentNormal Run ModeHCLK = 10 kHz - 248.0 - μAV DD**HXT LIRCAll DigitalModules5.5V X 10 KHz V[2]I DD18- 247.7 - μA 5.5V X 10 KHz X I DD19- 237.9 - μA3V X 10 KHz V[2] I DD20- 237.5 - μA3V X 10 KHz XI IDLE5Operating CurrentIdle ModeHCLK= 48 MHz - 4.9 - mAV DD**HXT HIRCAll DigitalModules5.5V X V VI IDLE6- 2.6 - mA 5.5V X V X I IDLE7- 4.9 - mA 3V X V V I IDLE8- 2.6 - mA 3V X V XI IDLE1Operating CurrentIdle ModeHCLK = 24 MHz - 2.8 - mAV DD**HXT HIRCAll DigitalModules5.5V 24 MHz X VI IDLE2- 1.9 - mA 5.5V 24 MHz X XI IDLE3- 2.8 - mA 3V 24 MHz X VI IDLE4- 1.9 - mA 3V 24 MHz X XNM1817 SERIES DATASHEETI IDLE9Operating CurrentIdle ModeHCLK = 16 MHz - 2.0 - mAV DD**HXT HIRCAll DigitalModules5.5V V X VI IDLE10- 1.3 - mA 5.5V V X X I IDLE11- 2.0 - mA 3V V X V I IDLE12- 1.4 - mA 3V V X XI IDLE9Operating CurrentIdle ModeHCLK = 12 MHz - 1.5 - mAV DD**HXT HIRCAll DigitalModules5.5V V X VI IDLE10- 1.0 - mA 5.5V V X X I IDLE11- 1.5 - mA 3V V X V I IDLE12- 1.0 - mA 3V V X XI IDLE13Operating CurrentIdle ModeHCLK = 4 MHz - 0.8 - mAV DD**HXT HIRCAll DigitalModules5.5V V X VI IDLE14- 0.6 - mA 5.5V V X X I IDLE15- 0.7 - mA 3V V X V I IDLE16- 0.6 - mA 3V V X XI DD17Operating CurrentIdle ModeHCLK = 32 kHz - 274.3 - μAV DD**HXT LIRCAll DigitalModules5.5V X V V[1]I DD18- 273.0 - μA 5.5V X V X I DD19- 265.0 - μA3V X V V[1] I DD20- 263.9 - μA3V X V XI DD17Operating CurrentIdle ModeHCLK = 10 kHz - 232.6 - μAV DD**HXT LIRCAll DigitalModules5.5V X V V[2]I DD18- 232.2 - μA 5.5V X V XI DD19- 222.5 - μA3V X V V[2]I DD20- 222.1 - μA3V X V XNM1817 SERIES DATASHEETI PWD1Standby CurrentPower-down Mode(Deep Sleep Mode) - 1.9 - μAV DD = 5.5V, All oscillators and analogblocks turned off.I PWD2- 1.7 - μA V DD= 3V, All oscillators and analog blocks turned off.I LK Input LeakageCurrentPA/PB/PC/PD-1 - +1 μAV DD = 5.5V, 0 < V IN< V DDOpen-drain or input only modeV IL1Input Low VoltagePA/PB/PC/PD (TTLInput)-0.3 1.33VV DD = 5.5 V-0.3 1 V DD = 3.3 VV IH1Input High VoltagePA/PB/PC/PD (TTLInput)1.47V DD +0.3VV DD = 5.5 V1.08V DD +0.3V DD = 3.3 VV ILS Negative-goingThreshold(Schmitt Input),nRESET- - 0.3V DD V -V IHS Positive-goingThreshold(Schmitt Input),nRESET0.7V DD- - V -R RST Internal nRESETPin Pull-up Resistor48 148 kΩV DD = 2.1 V ~ 5.5VV ILS Negative-goingThreshold(Schmitt input),PA/PB/PC/PD- - 0.3V DD V -V IHS Positive-goingThreshold(Schmitt input),PA/PB/PC/PD0.7V DD- - V -I IL Logic 0 InputCurrentPA/PB/PC/PD(Quasi-bidirectionalMode)- -63.65 μA V DD = 5.5 V, V IN = 0VI TL Logic 1 to 0Transition CurrentPA/PB/PC/PD- -566.7 - μA V DD = 5.5 VI SR11Source CurrentPA/PB/PC/PD(Quasi-bidirectionalMode) - -372 - μA V DD = 4.5 V, V IN = 2.4 VI SR12- -76.8 - μA V DD = 2.7 V, V IN = 2.2 V I SR13- -37.3 - μA V DD = 2.1 V, V IN = 1.8 VI SR21Source CurrentPA/PB/PC/PD - -19.2 - mA V DD = 4.5 V, V IN = 2.4 VI SR22- -4 - mA V DD = 2.7 V, V IN = 2.2 VNM1817 SERIES DATASHEETNM1817 SERIES DATASHEET I SR23 (Push-pull Mode) - -2 - mA V DD = 2.1 V, V IN = 1.8 V I SK11 Sink Current PA/PB/PC/PD(Quasi-bidirectional,Open-Drain andPush-pull Mode) - 12.8 - mA V DD = 4.5 V, V IN = 0.4 V I SK12 - 8.1 - mA V DD = 2.7 V, V IN = 0.4 VI SK13 - 6 - mA V DD = 2.1 V, V IN = 0.4 V Notes:1. Only enable modules which support 32kHz LIRC clock source2. Only enable modules which support 10kHz LIRC clock source3. Guaranteed by design, not test in production.** : The function has been reserved in NM1817.5.3 NM1120 AC Electrical Characteristics5.3.1 **External Input Clock (function has been reserved in NM1817)Symbol Parameter Min Typ Max Unit Test Conditions t CHCX Clock High Time 10 - - ns - t CLCX Clock Low Time 10 - - ns - t CLCH Clock Rise Time 2 - 15 ns - t CHCL Clock Fall Time 2 - 15 ns -t CHCX90%10%t CLCHt CHCL t CLCXt CLCL0.3 V DD0.7 V DDNM1817 SERIES DATASHEET5.3.2 **External 4~24MHz High Speed Crystal (HXT)(function has been reserved in NM1817) Symbol Parameter Min. Typ. Max Unit Test Conditions V HXT Operation Voltage 2.1 - 5.5 V -T A Temperature -40 - 105 ℃ -I HXT Operating Current - 414 - uA 12MHz, V DD = 5.5V f HXT Clock Frequency 4 - 24 MHz -5.3.3 **Typical Crystal Application Circuits (function has been reserved in NM1817) Crystal C1 C24MHz ~ 24MHz 10~20 pF 10~20pFFigure 5-1 NM1120 Typical Crystal Application Circuit5.3.4 48MHz Internal High Speed RC Oscillator (HIRC)Symbol Parameter Min Typ Max Unit Test Conditions V HRC Supply Voltage - 1.5 - V -f HRC Center Frequency - 48 - MHz -Calibrated Internal Oscillator Frequency -1 - +1 % T A = 25 ℃V DD = 5.5 V2% % T A = -40℃~105℃V DD =2.5 V~ 5.5 VI HRC Operating Current - 1090 - μA T A = 25 ℃,V DD = 5 V5.3.5 10kHz Internal Low Speed RC Oscillator (LIRC)Symbol Parameter Min Typ Max Unit Test ConditionsXTAL1C1C2XTAL24~24 MHzCrystal Vss VssNM1817 SERIES DATASHEET V LRC Supply Voltage - 1.5V - V -f LRCCenter Frequency - 10 - kHz -Oscillator Frequency -50[1] - +50[1] % V DD = 2.1 V ~ 5.5 VT A = -40℃ ~ +105℃I LRC Operating Current - 0.4 - μA T A = 25 ℃,V DD = 5 V5.4 NM1120 Analog Characteristics5.4.1 12-bit SAR ADC Symbol Parameter Min Typ Max Unit Test Condition - Resolution - - 12 Bit -DNL Differential Nonlinearity Error - ±2 - LSB VDD = 5.5V INL Integral Nonlinearity Error - ±1 - LSB VDD = 5.5V E O Offset Error - -0.33 - LSB VDD = 5.5V E G Gain Error (Transfer Gain) - 0.33 - LSB VDD = 5.5V E A Absolute Error - -2.62 - LSB VDD = 5.5V - Monotonic Guaranteed - -F ADC ADC Clock Frequency 12 16 MHz V DD = 3.0 ~5.5 VT ACQ Acquisition Time (Sample Stage) N+11/F ADC V DD = 3.0 ~5.5 VN is sampling counter, N=1~1024200 ns V DD = 3.0~5.5 VT CONV Conversion Time 3 1000 1050 ns V DD = 3.0~5.5 V V DD Supply Voltage 3.0 - 5.5 V -I DDA Supply Current (Avg.) - 1 - mA V DD = 5.5 V V IN Analog Input Voltage 0 - AV DD V -C IN Input Capacitance 2 - 1.6 - pF -R IN Input Load 2 - 2.5 - kΩ -1. ADC voltage reference is the same with V DD .2. It’s for sample and hold. The maximum value depends on process variation. Basically, the variation of CIN is less than about 10% of typical value and the variation of RIN is less about 20% of typical value.3. Guaranteed by design, not test in production.The conversion time is up to auto-completion of analog comparison in ADC IP and the typical value is about 1000ns at V DD = 5V.。
Motorola 3.5 kHz 产品说明书
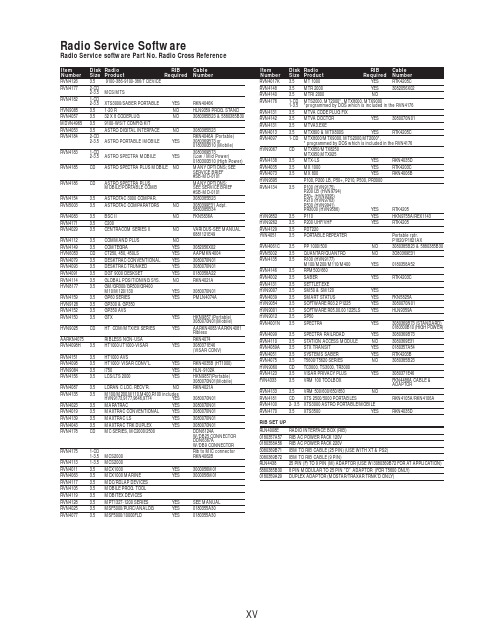
RVN4126 3.59100-386-9100-386/T DEVICERVN41772-CD2-3.5MCS/MTSRVN41821-CD2-3.5XTS3000/SABER PORTABLE YES RKN4046KHVN9085 3.51-20 R NO HLN9359 PROG. STAND RVN4057 3.532 X 8 CODEPLUG NO3080385B23 & 5880385B30 MDVN4965 3.59100-WS/T CONFIG KITRVN4053 3.5ASTRO DIGITAL INTERFACE NO3080385B23RVN41842-CD RKN4046A (Portable) 2-3.5ASTRO PORTABLE /MOBILE YES3080369B73 or0180300B10 (Mobile) RVN41831-CD3080369B732-3.5ASTRO SPECTRA MOBILE YES(Low / Mid Power)0180300B10 (High Power) RVN4185CD ASTRO SPECTRA PLUS MOBILE NO MANY OPTIONS; SEESERVICE BRIEF#SB-MO-0101RVN4186CD ASTRO SPECTRA PLUS MANY OPTIONS;MOBILE/PORTABLE COMB SEE SERVICE BRIEF#SB-MO-0101RVN4154 3.5ASTROTAC 3000 COMPAR.3080385B23RVN5003 3.5ASTROTAC COMPARATORS NO3080399E31 Adpt.5880385B34RVN4083 3.5BSC II NO FKN5836ARVN4171 3.5C200RVN4029 3.5CENTRACOM SERIES II NO VARIOUS-SEE MANUAL6881121E49RVN4112 3.5COMMAND PLUS NORVN4149 3.5COMTEGRA YES3082056X02HVN6053CD CT250, 450, 450LS YES AAPMKN4004RVN4079 3.5DESKTRAC CONVENTIONAL YES3080070N01RVN4093 3.5DESKTRAC TRUNKED YES3080070N01RVN4091 3.5DGT 9000 DESKSET YES0180358A22RVN4114 3.5GLOBAL POSITIONING SYS.NO RKN4021AHVN8177 3.5GM/GR300/GR500/GR400M10/M120/130YES3080070N01RVN4159 3.5GP60 SERIES YES PMLN4074AHVN9128 3.5GP300 & GP350RVN4152 3.5GP350 AVSRVN4150 3.5GTX YES HKN9857 (Portable)3080070N01(Mobile) HVN9025CD HT CDM/MTX/EX SERIES YES AARKN4083/AARKN4081RiblessAARKN4075RIBLESS NON-USA RKN4074RVN4098H 3.5HT1000/JT1000-VISAR YES3080371E46(VISAR CONV)RVN4151 3.5HT1000 AVSRVN4098 3.5HT1000/ VISAR CONV’L.YES RKN4035B (HT1000) HVN9084 3.5i750YES HLN-9102ARVN4156 3.5LCS/LTS 2000YES HKN9857(Portable)3080070N01(Mobile) RVN4087 3.5LORAN C LOC. RECV’R.NO RKN4021ARVN4135 3.5M100/M200,M110,M400,R100 includesHVN9173,9177,9646,9774YES3080070N01RVN4023 3.5MARATRAC YES3080070N01RVN4019 3.5MAXTRAC CONVENTIONAL YES3080070N01RVN4139 3.5MAXTRAC LS YES3080070N01RVN4043 3.5MAXTRAC TRK DUPLEX YES3080070N01RVN4178CD MC SERIES, MC2000/2500DDN6124AW/DB25 CONNECTORDDN6367AW/DB9 CONNECTOR RVN41751-CD Rib to MIC connector 1-3.5MCS2000 RKN4062BRVN41131-3.5MCS2000RVN4011 3.5MCX1000YES3000056M01RVN4063 3.5MCX1000 MARINE YES3000056M01RVN4117 3.5MDC/RDLAP DEVICESRVN4105 3.5MOBILE PROG. TOOLRVN4119 3.5MOBITEX DEVICESRVN4128 3.5MPT1327-1200 SERIES YES SEE MANUALRVN4025 3.5MSF5000/PURC/ANALOG YES0180355A30RVN4077 3.5MSF5000/10000FLD YES0180355A30RVN4017K 3.5MT 1000YES RTK4205CRVN4148 3.5MTR 2000YES3082056X02RVN4140 3.5MTRI 2000NORVN41761-CD MTS2000, MT2000*, MTX8000, MTX90001-3.5*programmed by DOS which is included in the RVN4176RVN4131 3.5MTVA CODE PLUG FIXRVN4142 3.5MTVA DOCTOR YES3080070N01RVN4131 3.5MTVA3.EXERVN4013 3.5MTX800 & MTX800S YES RTK4205CRVN4097 1-CD MTX8000/MTX9000,MTS2000,MT2000*,* programmed by DOS which is included in the RVN4176HVN9067CD MTX850/MTX8250MTX950,MTX925RVN4138 3.5MTX-LS YES RKN4035DRVN4035 3.5MX 1000YES RTK4203CRVN4073 3.5MX 800YES RKN4006BHVN9395 P100, P200 LB, P50+, P210, P500, PR3000RVN4134 3.5P100 (HVN9175)P200 LB (HVN9794)P50+ (HVN9395)P210 (HVN9763)P500 (HVN9941)PR3000 (HVN9586)YES RTK4205HVN9852 3.5P110YES HKN9755A/REX1143 HVN9262 3.5P200 UHF/VHF YES RTK4205RVN4129 3.5PDT220YVN4051 3.5PORTABLE REPEATER Portable rptr.P1820/P1821AXRVN4061C 3.5PP 1000/500NO3080385B23 & 5880385B30 RVN5002 3.5QUANTAR/QUANTRO NO3O80369E31RVN4135 3.5R100 (HVN9177)M100/M200/M110/M400YES0180358A52RVN4146 3.5RPM500/660RVN4002 3.5SABER YES RTK4203CRVN4131 3.5SETTLET.EXEHVN9007 3.5SM50 & SM120YESRVN4039 3.5SMART STATUS YES FKN5825AHVN9054 3.5SOFTWARE R03.2 P1225YES3080070N01HVN9001 3.5SOFTWARE R05.00.00 1225LS YES HLN9359AHVN9012 3.5SP50RVN4001N 3.5SPECTRA YES3080369B73 (STANDARD)0180300B10 (HIGH POWER) RVN4099 3.5SPECTRA RAILROAD YES3080369B73RVN4110 3.5STATION ACCESS MODULE NO3080369E31RVN4089A 3.5STX TRANSIT YES0180357A54RVN4051 3.5SYSTEMS SABER YES RTK4203BRVN4075 3.5T5600/T5620 SERIES NO3080385B23HVN9060CD TC3000, TS3000, TR3000RVN4123 3.5VISAR PRIVACY PLUS YES3080371E46FVN4333 3.5VRM 100 TOOLBOX FKN4486A CABLE &ADAPTORRVN4133 3.5VRM 500/600/650/850NORVN4181CD XTS 2500/5000 PORTABLES RKN4105A/RKN4106A RVN41002- 3.5XTS3000 ASTRO PORTABLE/MOBILERVN4170 3.5XTS3500YES RKN4035DRIB SET UPRLN4008E RADIO INTERFACE BOX (RIB)0180357A57RIB AC POWER PACK 120V0180358A56RIB AC POWER PACK 220V3080369B71IBM TO RIB CABLE (25 PIN) (USE WITH XT & PS2)3080369B72IBM TO RIB CABLE (9 PIN)RLN443825 PIN (F) TO 9 PIN (M) ADAPTOR (USE W/3080369B72 FOR AT APPLICATION) 5880385B308 PIN MODULAR TO 25 PIN ”D” ADAPTOR (FOR T5600 ONLY)0180359A29DUPLEX ADAPTOR (MOSTAR/TRAXAR TRNK’D ONLY)Item Disk Radio RIB Cable Number Size Product Required Number Item Disk Radio RIB Cable Number Size Product Required NumberUtilizing your personal computer, Radio Service Software (RSS)/Customer Programming Software (CPS)/CustomerConfiguration Software (CCS) enables you to add or reprogram features/parameters as your requirements change. RSS/CPS/CCS is compatible with IBM XT, AT, PS/2 models 30, 50, 60 and 80.Requires 640K RAM. DOS 3.1 or later. Consult the RSS users guide for the computer configuration and DOS requirements. (ForHT1000, MT/MTS2000, MTX838/8000/9000, Visar and some newer products —IBM model 386, 4 MEG RAM and DOS 5.0 or higher are recommended.) A Radio Interface Box (RIB) may be required as well as the appropriate cables. The RIB and cables must be ordered separately.Licensing:A license is required before a software (RVN) order is placed. The software license is site specific (customer number and ultimate destination tag). All sites/locations must purchase their own software.Be sure to place subsequent orders using the original customer number and ship-to-tag or other licensed sites; ordering software without a licensed customer number and ultimate tag may result in unnecessary delays. To obtain a no charge license agreement kit, order RPX4719. To place an order in the U.S. call 1-800-422-4210. Outside the U.S., FAX 847-576-3023.Subscription Program:The purchase of Radio ServiceSoftware/Customer Programming/Customer ConfigurationSoftware (RVN & HVN kits) entitles the buyer/subscriber to three years of free upgrades. At the end of these three years, the sub-scriber must purchase the same Radio Service Software kit to receive an additional three years of free upgrades. If the sub-scriber does not elect to purchase the same Radio Service Software kit, no upgrades will be sent. Annually a subscription status report is mailed to inform subscribers of the RSS/CPS/CCS items on our database and their expiration dates.Notes:1)A subscription service is offered on “RVN”-Radio Service Software/Customer Programming/Customer Configuration Software kits only.2)“RVN” software must only be procured through Radio Products and Services Division (RPSD). Software not procured through the RPSD will not be recorded on the subscription database; upgrades will not be mailed.3)Upgrades are mailed to the original buyer (customer number & ultimate tag).4)SP software is available through the radio product groups.The Motorola General Radio Service Software Agreement is now available on Motorola Online. If you need assistance please feel free to submit a “Contact Us” or call 800-422-4210.SMART RIB SET UPRLN1015D SMART RIB0180302E27 AC POWER PACK 120V 2580373E86 AC POWER PACK 220V3080390B49SMARTRIB CABLE (9 PIN (F) TO 9 PIN (M) (USE WITH AT)3080390B48SMARTRIB CABLE (25 PIN (F) TO 9 PIN (M) (USE WITH XT)RLN4488ASMART RIB BATTERY PACKWIRELESS DATA GROUP PRODUTS SOFTWARERVN4126 3.59100-386/9100T DEVICES MDVN4965 3.59100-WS/T CONFIG’TN RVN41173.5MDC/RDLAP DEVICESPAGING PRODUCTS MANUALS6881011B54 3.5ADVISOR6881029B90 3.5ADVISOR ELITE 6881023B20 3.5ADVISOR GOLD 6881020B35 3.5ADVISOR PRO FLX 6881032B30 3.5BR8506881032B30 3.5LS3506881032B30 3.5LS5506881032B30 3.5LS7506881033B10 3.5LS9506881035B20 3.5MINITOR III8262947A15 3.5PAGEWRITER 20008262947A15 3.5PAGEWRITER 2000X 6881028B10 3.5TALKABOUT T3406881029B35 3.5TIMEPORT P7308262947A15 3.5TIMEPORT P930NLN3548BUNIVERSAL INTERFACE KITItem Disk Radio NumberSize Product。
NC7SV17中文资料

元器件交易网
NC7SV17
Logic Symbol
IEEE/IEC
Connection Diagrams
Pin Assignments for SC70
Pin Descriptions
Pin Name A Y NC Description Input Output No Connect Pad Assignments for MicroPak (Top View)
±24 mA @ 3.00V VCC ±18 mA @ 2.30V VCC ±6 mA 1.4V VCC @ 1.1V VCC
±0.1 mA @ 0.9V VCC
s Uses patented Quiet Series noise/EMI reduction circuitry s Ultra small MicroPak leadfree package s Ultra low dynamic power
Function Table
Y=A Input A L H
H = HIGH Logic Level L = LOW Logic Level
Output Y L H (Top Thru View)
2
元器件交易网
NC7SV17
Absolute Maximum Ratings(Note 1)
Ordering Code:
Order Number NC7SV17P5X NC7SV17L6X Package Number MAA05A MAC06A Product Code Top Mark V17 G5 Package Description 5-Lead SC70, EIAJ SC-88a, 1.25mm Wide 6-Lead MicroPak, 1.0mm Wide Supplied As 3k Units on Tape and Reel 5k Units on Tape and Reel
HE17x Series USB Data Logger User Manual

1HE17x SeriesUSB Data Logger UserManualCONTENTSB Data Logger Hardware (3)1.1Introduction (3)1.2Features (3)1.3Application (3)1.4USB Data Logger Model (3)1.5USB Temperature Data Logger Appearance(HE170/HE171/HE172) (4)1.6USB Temperature Data Logger Screen(HE170/HE171/HE172) (4)1.7USB Temperature&Humidity Data Logger Appearance(HE173/HE174) (5)1.8USB Temperature&Humidity Data Logger Screen(HE173/HE174) (5)1.9Button (6)1.10Install Battery (6)1.11Fix USB Data Logger (6)Chapter2.Logpro Software (7)2.1The Requirement of the Computer Hardware (7)2.2Install Driver&Software (7)2.3Setting the logger’s properties to start a new measurement (8)2.4Properties Description (9)2.5Start record time description (10)2.6Download the Records after a Measurement (10)2.7Data Listing Window (12)2.8Exporting Logs from Logpro (12)2.9Delete Records in the Logger (13)2.10Check the Save File in File List (13)Chapter3.Attention (14)Chapter4.FAQ (14)4.1LCD Screen Dim (14)4.2Data&Time Error (14)4.3Software"Runtime Error" (14)4.4Check COM Port Number (14)B Data Logger Hardware1.1IntroductionHE170USB series has USB interface,enjoying elegant appearance and compact construction,specially designed for refrigerator and cold-chain transportation as well as container transport applications.HE170USB series adopts friendly USB interface,friendly mounting bracket and the screws.HE170USB series can show temperature/temperature and humidity simultaneously as well as the battery indication.The OK key can help to check the Max/Min/Current value and the upper and lower limits.1.2Features⏹Waterproof and dustproof standard IP67,resisting moisture and dust.⏹Can set temperature and humidity limit value and LED lights will flash when the valuebeing exceeded.⏹Lower consumption design,1/2AA3.6V Lithium battery,working for12months and easyto replace.(Logging Interval:600s)⏹Transfer logging data to PC through software and can be saved as different types toensure the existence.⏹Use high sensitivity sensor,fast reaction and high precision.⏹Size(L x H x D):126mm x34mm x28mm1.3ApplicationWildly use in cold chain Transportation,Containers.1.4USB Data Logger Model1.5USB Temperature Data Logger Appearance(HE170/HE171/HE172)8①LCD Screen⑥Battery Replacement Position.②Button⑦Waterproof Transparent Cover③LED Warming Light When the⑧Fixed BracketTemperature Value Exceeds SettingLimits.④USB Connection Port⑨Model Label⑤Waterproof Ring1.6USB Temperature Data Logger Screen(HE170/HE171/HE172)①Display the High Limit⑤Display the Maximum Value inRecords②Display the Low Limit⑥symbol display shows being thelogging status.③Battery power indication.⑦Temperature Value④Display the Minimum Value in⑧Temperature Unit(℃or℉)Records1.7USB Temperature&Humidity Data Logger Appearance(HE173/HE174)8①LCD Screen⑥Battery Replacement Position.②Button⑦Waterproof Transparent Cover③LED Warming light When the⑧Fixed BracketTemperature or Humidity ValueExceeds the Setting Limits.④USB Connection Port⑨Model Label⑤Waterproof Ring1.8USB Temperature&Humidity Data Logger Screen(HE173/HE174)①Display the High Limit⑤Battery power indication.②Display the Low Limit⑥Units symbol display℃or℉,%RH③Display the Maximum Value in⑦ValueRecords④Display the Minimum Value inRecords1.9ButtonOK Button1.Press this button for long to 5seconds can turn on/off the logger.2.Check the MAX;MIN;High &Low values as well as the current value in the working status.1.10Install Battery1.Open the Battery Cover2.Remove shell3.Install Battery1.11Fix USB Data Loggere Screw to Fix the Bracket onto the Wall.2.Install the Data Logger.Chapter 2.Logpro Software2.1The Requirement of the Computer Hardware1.OS:Windows2000/XP/Vista/Win7/Win8/Win10(32/64-bit ),nonsupport Linux/UnixOS.2.CPU:1.6GHz3.Physical Memory:512MB4.Hard-drive Space:4GBB Port:12.2Install Driver &Software1.Install DriverPut the assigned software disc into the computer driver and open the file tofindand select the driver based on the operating system.OS Win7/Win8/Win10-64select “CH341SER[64bit]”.OS Win XP;Vista;Win7-32select “CH341SER[32bit]”(1)Click 【CH341SER 】;(2)Click 【INSTALL 】—【Confirm】2.Install Logpro SoftwareNotice:Please Install Logpro Software inD:\2.3Setting the logger’s properties to start a new measurement.1.Connect the data logger to the computer.12.Running Logpro software on the PC.3.From the toolbar select Connect.24.Read the logger’s properties.5.Set the properties.6.Sync the properties &time.(The PC time will be synchronized to the logger as well.)7.From the toolbar select Disconnect8.Unplug the logger from the Computer,and then the logger is in Standby mode 3.9.Press OK button on the logger,turn on the Data Logger and start recording.1The windows operating system cannot handle USB devices being unplugged and plugged back too fast.When unplugging the logger,wait for about 5seconds before plugging it in again.If you unplug and plug back a device too quickly,the computer may stop recognizing any USB devices on that port.If this happens you will have to restart the computer.This is a windows USB problem and is not related to Logpro.2If more than one logger is connected to your computer at the same time,the program will ask you to choose COM port manually.3The logger has three modes:1.LOG:In the mode,the logger samples and records data timely.2.Standby:In the mode,the logger stops to sample and record,and the LCD display is OFF.3.OFF:In the mode,the logger stops to sample and record,and the LCD display is off.Logpro cannot connect to the logger also.654732.4Properties DescriptionProperty Text DescriptionName English letters orNumbersName of the loggerSN10Characters Must be the same as the one in the label oflogger.Sampling Interval(s)Number from1to240Sampling frequency in LCD screenLogging Interval(s)Number from2to86400Logging frequency.Logs The count of records in the memory.Capacity The total capacity of the logger’s storage. Temperature type℃The unit of temperature is centigrade℉The unit for Fahrenheit temperatureStart Mode Start Now Start log when the Logger was turn ON.Delay Start Wait Delay Time then start log.Timing Start Start log when Delay Time:HHMMSSe.g.170000means17:00:00Delay Time Input a Delay Time or Timing Time.High&Low Limit CH1:TemperatureCH2:Humidity When the value over the limit,the buzz will sounds and alarm.Offset4CH1:TemperatureCH2:Humidity Input positive number to decrease the value. Input negative number to increase the value.4Calibrate the logger:The logger is factory calibrated to an accuracy given in the device specifications.However, there may be times when you wish to adjust the calibration of your logger.Logpro provides you with the ability to perform a single point offset calibration.This calibration can be used to increase the accuracy of the logger for a restricted data range.2.5Start record time description1.Select the mode to start the record in the property bar:Start Now:the recorder starts immediately to record the data.Delay start:the recorder starts to record the data after the set delay time.Timing start:the recorder starts recording data at the specified time point.(Note:the recorder will start at the turn on state and the recorder will not start the record automatically when the logger at the turn off state).2,Entry delay time or timing time in the property bar.Start Now:the default is0.Delay start:fill in the delay time,the unit is second.For example,fill in120indicates that the instrument starts to record the data after turn on logger two minutesTiming start:fill in the timing time and fill in the format of HHMMSS.For example,fill180000 indicates that the instrument starts to record the data at6:00:00pm3,Synchronization property and time(The PC time will also be synchronized to the recorder).2.6Download the Records after a Measurement.10.Connect the data logger to a free USB port on the computer.11.Running Logpro software on the PC.12.From the toolbar select Connect.13.From the toolbar select Download1213Once the data is transferred from the logger to the PC,the data graph will be displayed.The graph display will be blank if there are not any logs.Tips:Press and hold the left mouse button to drag a box,when the left mouse button is released,the graph will be redraw with the data in the selected rectangle area(Magnified data table).Click right button,then the graph will be redrawing with all the data in thelogs file.2.7Data Listing WindowClick"Data List"button on the toolbar,and then the data listing window is shown below. Channel3unit is Dew Point.The Value is calculated from temperature&humidity.The data pane lists the data samples collected by the logging device.The column width of each column is adjustable by using the left mouse button and dragging the column the desired width.2.8Exporting Logs from Logpro●:Export data list to an Excel file.●:Export data list to a PDF file.●:Export graph to a BMP file.2.9Delete Records in the Logger14.From the toolbar select Delete 5142.10Check the Save File in File List15.From the toolbar select Filelist.616.Click to open the file.1516●Double click left mouse button,then the selected file is opened.●Click right mouse button,a popup menu is shown as below,you can rename or delete orlog file.●The save file is saved in the Logpro software’s installation path in the PC’s hard driver.5Clear the logger's memory.It will not affect downloaded file.6These files are located in the installed path of Logpro.Chapter3.Attention●HE17x water proof level is IP67.Do not put it into the water.●HE17x plastic shell is ABS,flame retardant,not resistant to acid and alkali.●If repair is needed,only authorized technician could do the repair.●The instrument configuration by1x ER14250lithium battery(3.7V)is not rechargeable.●USB power supply(5V)cannot let the Data Logger work.Chapter4.FAQ4.1LCD Screen DimReason:●Insufficient battery or the environment temperature is too low or too high.Solution:●In the case of insufficient battery,please replace the battery.If resulted from environmenttemperature,please immediately take the logger out of the environment.4.2Data&Time ErrorReason:●The battery level is low●The data logger is not synchronous properties,before start recording.Solution:●Replace the battery.●Please sync the properties,before start recording.4.3Software"Runtime Error"Reason:●OS forbid software creating files.Solution:●Run the program(software)as an administrator.●Install software in Disk D:\●A data logger name cannot contain any of the following characters:\/:*?"<>|●Software’s installation path cannot include Chinese character or garbage character.4.4Check COM Port Number●Press“Win”+“R”in keyboard->Run"devmgmt.msc"to Open"Device Manager"inWindows->Expand"Ports(COM&LPT)"->"USB-SERIAL CH340(COM No.)"is the Data Logger。
施耐德变频器选型手册
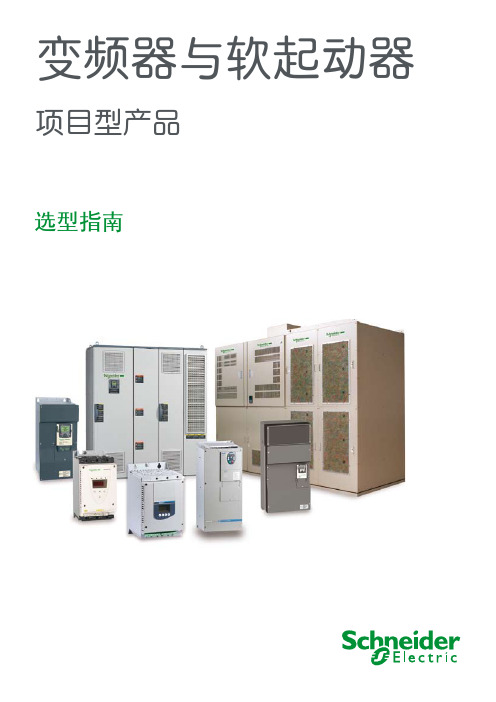
1
选型指导
产品类型
软起动器
通用型变频器
C 应用:
C 应用:
C 应用:
压缩机、泵、风机等 压缩机、泵、风机、 泵、风机等 大惯性机械、传送 装置。
耐德电气从一个优秀的产品和设备供应商逐步成长为整体解决方案提供商。今年,施耐德电气首
次集成其在建筑楼宇、IT、安防、电力及工业过程和设备等五大领域的专业技术和经验,将其高
质量的产品和解决方案融合在一个统一的架构下,通过标准的界面为各行业客户提供一个开放、
透明、节能、高效的 运营成本。
能效管理平台,为企业客户节省高达30%的投资成本和
电机功率 变频器
输出频率
4...400 kW –
控制类型 异步电机 可配置的电压斜坡 控制
同步电机 –
瞬时过转矩
–
功能
功能数量
预置多段速度的数目
I/O 的数目 模拟输入
逻辑输入
模拟输出
逻辑输出
继电器输出
通讯
集成通讯协议
可选配件
36 – 1 PTC 探头 3 – – 2 Modbus –
卡 (可选配件)
2
复杂、大功率变频器
C 应用:
泵、多泵、风机、压缩机 风机、泵、压缩机,各种标准 转矩应用
C 应用:
传送带、搅拌机、挤出机、 起重等
C 应用:
电力、采矿和选矿、石油和天 然气、水处理等中压系统中的 风机、泵、压缩机等
C 应用:
起重应用、下坡输送带、绞盘、自动扶 梯、高动态驱动器、泵/涡轮组合等
亨特风扇公司59397贵族青铜型号59398刷镍型号51473平板哑黑色安装手册说明书

Installation ManualModel: 59397 Noble Bronze59398 Brushed Nickel51473 Flat Matte BlackFan weight ±2 lbs: 24.9 lbs (11.3 kg)©2021 Hunter Fan Co.PG3630 r031121c.1 - All wiring must be in accordance with national and local electrical codes ANSI/NFPA 70. If you are unfamiliar with wiring, use a qualified electrician.c.2 - Use only Hunter replacement parts.This equipment has been tested and found to comply with the limits for a Class B digital device, pursuant to part 15 of the FCC Rules. These limits are designed to provide reasonable protection against harmful interference in a residential installation. This equipment generates, uses and can radiate radio frequency energy and if not installed and used in accordance with the instructions may cause harmful interference to radio communications.However, there is no guarantee that interference will not occur in a particular installation. If this equipment does cause harmful interference to radio or television reception, which can be determined by turning the equipment off and on, the user is encouraged to try to correct the interference by one or more of the following measures:• Reorient or relocate the receiving antenna.• Increase the separation between the equipment and receiver.• Connect the equipment into an outlet on a circuit different from that to which the receiver is connected.• Consult the dealer or an experienced radio/TV technician for help.Caution: modifications not approved by the party responsible for compliance could void user’s authority to operate the equipment.This device complies with Part 15 of the FCC Rules. Operation is subject to the following two conditions: (1) This device may not cause harmful interference, and (2) this device must accept any interference received, including interference that may cause undesired operation.This product conforms to UL Standard 507.2We recommend that you pull everything out of the box and lay it out. We have grouped the drawn components below with the hardware you’ll need for those parts. The screws below are drawn to scale to make it easier to identify what piece of hardware is needed to install each component.Adapter CoverM3695-01 r101920If you have an angled or vaulted ceiling:1. You will need a longer downrod. (sold separately at )2. If your ceiling angle is greater than 34°, you will also need anAngled Mounting Kit. (Sold separately at )If you have a flat ceiling:Hang your fan by a standard downrod. Some fans comewith a shorter downrod for a Low Profile installation.Standard Mountingbracket with hardware foundin the hardware bag.Pass all wires to one side of horizontal barLED/GlassRemoteDRSKY-01 r091420We know wiring is hard. Let’s make it easier.4 Wire Nuts (these are in theFollow these steps to get your fan wired quickly and safely. Follow the route below that best matches your wall switch setup. If you are unfamiliar with wiring or uncomfortable doing it yourself, please contact a qualifi ed electrician.Insert the two canopy screwsfound in the hardware bag. hardware bag.81886Installing the Glass Lift the globe and align the notches in the globe with the tabs in the light kit.NOTE: Check to ensure proper engagement.Attach the globe by lifting and turning clockwise one third of a full turn of the glass until it stops.NotchTabWARNINGGLASS FALL HAZARDTo prevent SERIOUS INJURY or DEATH , make sure that glass is properly secured.Assembling the Light KitAlign the keyhole slots in the top of the light kit assembly with the partially installed assemblyscrews. Rotate the keyhole slots around the screws and twist counterclockwise. Install the third light kit screw. Tighten all three screws securely.Partially install two light kitassembly screws, found in the hardware bag, halfway into the motor housing as shown. It does not matter which two screw holes you choose.2 of 3Light Kit Screw bag1 of 3Light Kit ScrewbagRaise cap to the LED assembly. Align the notches on the sides of the cap with the screw holes in the LED assembly. Install the two light cap screws which can be found in the hardware bag.Connect the single-pin connectors from the LED assembly to the connectors from the fan. Connect the white wires together. Connect the blue and black wires together.2 of 2Light Cap ScrewbagCeiling Bracket Downrod Hanging Fan Wiring Canopy Blades Light LED/Glass RemoteWARNINGFAN FALL HAZARDMake sure screws are tight to secure the light fixture.ONT u rn Po w e r918861886Ceiling Bracket DownrodHanging FanWiringCanopyBladesLightLED/GlassRemotePreparing the Wall ControlEnsure the power is OFF at the outlet box and wall switch location before proceeding with installation.T ur n P o w e r OFF1Turning off the power2Installing the batteryTo access the batterycompartment, slide the battery door up.Replace the used battery with two AAA batteries when needed.3Wiring the Wall ControlConnect the grounding wire from the wall control to the ground control from the switch box using the provided wire nuts.Connect the “LIVE IN” from the switch box to the “~VAC” from the wall control using the provided wire nuts.Connect the “LIVE OUT” from the switch box to the “FAN” out from the wall control using the provided wire nuts.Push all wires into the switch box.4Installing the Wall ControlInstall the longer screws through the slots in the wall control into the switch box screw holes.Use the pull-chain switch on the fan to set the fan speed to the HIGH position before operation.Turning on the powerONT ur n P o w e r IMPORTANT65Installing the Wall PlateInstall the shorter screws through the wall control plate and into the screw holes in the wall control.The remote transmitter is already paired to the receiver and ready to use. If you need to pair your remote, cycle power to the fan by turning power off and back on at the wall switch (or circuit breaker if necessary). Within three minutes, do the following:Reference the included remote function card for information on how to use your wall control!78NOTICEThis device complies with Part 15 of the FCCRules. Operation is subject to the followingconditions: (1) this device may not cause harmful interference, and (2) this device must accept any interference received, including interference that may cause undesired operation.KEY PRESS FUNCTIONLIGHT FUNCTIONS FAN FUNCTIONSKEY PRESSFUNCTIONLight Dimming ControlDimming Mode On/Off+Light On/Off Light High Light LowLong PressLong Press Long Press Key Press FunctionFan On/Off On/OffFan High Fan Low Fan ReversePressLong Press Long PressLong Press Fan Speed ControlBattery Door10Hunter Pro Tip:Hunter Fan Company grants this limited warranty to the original purchaser of this Hunter ceiling fan. This document can be found at . Thank you for choosing Hunter!How Can Warranty Service Be Obtained?Proof of purchase is required when requesting warranty service. The original purchaser must present a sales receipt or other document that establishes proof of purchase. Hunter, at its sole discretion, may accept a gift receipt. To obtain service, contact Hunter Fan Company online or by phone./Support/Contact-Us/1-888-830-1326Please do not ship your fan or any fan parts to Hunter. Delivery will be refused.What Does This Warranty Cover?Motor — Limited Lifetime WarrantyIf any part of your ceiling fan motor fails during your ownership of the fan due to a defect in material or workmanship, as determined solely by Hunter, Hunter will provide you with a replacement fan free of charge.* The foregoing limited warranty applies only to the motor itself and does not apply to electronic controls – such as remote control transmitters, remote control receivers, or capacitors – used in conjunction with the motor. Such electronic control items are included in the one-year limited warranty below.Other — One-Year Limited WarrantyExcept as otherwise indicated throughout this warranty, if any part of your Hunter ceiling fan fails at any time within one year of the date of purchase due to a defect in material or workmanship, as determined solely by Hunter, Hunter will provide a replacement part free of charge.*Light Kits — Warranty May VaryLight kits are included in the one-year limited warranty. However, you may qualify for additional warranty coverage if your fan includes one of the following:• LED Light Kits — Three-Year Limited WarrantyIf your LED light kit module (not including glass components) or LED bulb fails at any time within three years of the date of purchase due to a defect in material or workmanship, as determined solely by Hunter, Hunter will provide a replacement part free of charge.** If no replacement product/part can be provided for your fan, we will provide a comparable or superior replacement product/part at the sole discretion of Hunter.What Does This Warranty NOT Cover?Labor Excluded. This warranty does not cover any costs or fees associated with the labor (including electrician’s fees) required to install, remove, or replace a fan or any fan parts. There is no warranty for light bulbs (except where otherwise noted); remote control batteries; fans purchased or installed outside the United States; fans owned bysomeone other than the original purchaser; fans for which proof of purchase has not been established; fans purchased from an unauthorized dealer; ordinary wear and tear; minor cosmetic blemishes; refurbished fans; and fans that are damaged due to any of the following: improper installation, misuse, abuse, improper care, failure to follow Hunter instructions, accidental damage caused by the fan owner or related parties, modifications to the fan, improper or incorrectly performed maintenance or repair,improper voltage supply or power surge, use of improper parts or accessories, failure to provide maintenance to the fan, or acts of God (e.g. flood).ORIGINAL PURCHASER’S SOLE AND EXCLUSIVE REMEDY FOR A CLAIM OF ANY KIND WITH RESPECT TO THIS PRODUCT SHALL BE THE REMEDIES SET FORTH HEREIN. HUNTER FAN COMPANY IS NOT RESPONSIBLE FOR CONSEQUENTIAL OR INCIDENTAL DAMAGES, DUE TO PRODUCT FAILURE, WHETHER ARISING OUT OF BREACH OF WARRANTY , BREACH OF CONTRACT, OR OTHERWISE. Some States do not allow the exclusion or limitation of incidental or consequential damages, so the above limitation or exclusion may not apply to you.ANY IMPLIED WARRANTIES OF MERCHANTABILITY OR FITNESS FOR A PARTICULAR PURPOSE APPLICABLE TO THIS PRODUCT ARE LIMITED IN DURATION TO THE PERIOD OF COVERAGE OF THE APPLICABLE LIMITED WARRANTIES SET FORTH ABOVE. Some States do not allow limitations on how long an implied warranty lasts, so the above limitation may not apply to you.How Does State Law Affect Warranty Coverage?This warranty gives you specific legal rights. You may also have other rights which vary from state to state.Limited Lifetime WarrantyFan Doesn’t Work • Make sure power switch is on.• Check the circuit breaker to ensure the power is turned on.• Make sure the blades spin freely.• Check the plug connection in the switch housing.• Make sure the blades are properly installed on the blade iron posts.• Turn the power off, support the fan carefully, and check that the hanger ball is properly seated.• Use the provided balancing kit and instructions to balance the fan.• Make sure the battery is installed correctly.• Install a fresh battery.Noisy Operation• Make sure the blades are properly installed.• Check to see if any of the blades are cracked. If so, replace all of theblades.• If you have multiple remotes or multiple remote-controlled fans installed on the same circuit breaker and you are experiencing interference or faulty operation of your remote controls, please go to/FAQs and click “How do I properly install multiple remote-controlled fans?” for information on how to correct this issue.11If you need a different downrod length follow these steps:Assembled downrod should look like thisHere is another view of the downrod assembly unassembled.Follow steps 1-5 to remove standard downrod pipeFollow steps 6-10 to reassemble with new downrod。
BONDTECH Ender-7 LGX Lite 和 Mosquito 安装指南说明书
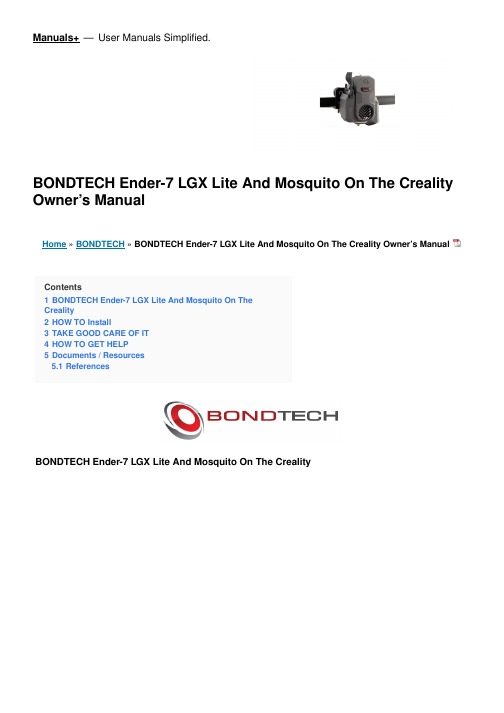
Manuals+— User Manuals Simplified.BONDTECH Ender-7 LGX Lite And Mosquito On The Creality Owner’s ManualHome » BONDTECH » BONDTECH Ender-7 LGX Lite And Mosquito On The Creality Owner’s ManualContents1 BONDTECH Ender-7 LGX Lite And Mosquito On TheCreality2 HOW TO Install3 TAKE GOOD CARE OF IT4 HOW TO GET HELP5 Documents / Resources5.1 ReferencesBONDTECH Ender-7 LGX Lite And Mosquito On The Creality7. Loosen the three M3 screws holding the extruder to the motor using a 2 mm hex key.Pull away the extruder gear.Fasten the three M3 screws holding the extruder to the motor.Undo the four M3 screws on the bottom of the gantry front side using a 2 mm hex key.11. Undo the four M3 screws on the bottom of the gantry back side using a 2 mm hex key.12. Use a flathead screwdriver or something similar to pop off the gantry cowling.13. Cut the zipties securing the wire loom coming from the toolhead.14. Disconnect all wires coming from the toolhead.15. Pull the toolhead wiring loom through the gantry cowling.16. Undo the two M3 screws holding the toolhead to the x-carriage using a 2.5 mm hex key.17. Remove the wires from the conduit.18. Undo the two M3 screws holding the fan using a 2 mm hex key.19. Undo the four M3 screws holding the hotend using a 2 mm hex key.20. Add the conduit holder to the LGX lite using two low profile M3x8 screws and a 2 mm hex key.21. Add the mount to the bottom of the LGX lite using three low profile M3x8 screws.22. Add the mount to the hotend using two M2.5×6 SHCS screws and a 2 mm hex key.23. Add the included 40 mm PTFE insert and a collet clip.24. Remove the heater cartridge and thermistor from the original hotend and add to the Mosquito.25. Route wires as shown.26. Add the LGX lite and hotend to the x-carriage by pushing them from the front.27. Fasten the hotend to the x-carriage using included low profile M3x8 screws and a 2 mm hex key.28. Fasten the fan to the hotend using the included M2.5×16 screws and a 2 mm hex key.29. Fasten the cowling to the x-carriage back using the same SHCS screws and a 2.5mm hex key.30. Push and pull the wiring loom through the conduit.31. Using some tape and a spare piece of filament or string helps with this step.32. Secure the conduit to the side of the LGX lite using the two included zip ties.33. Place the gantry cowling loosely on the gantry and feed the conduit into it.34. Reconnect all the connectors unplugged previously.35. Click the gantry cowling back in place and secure it using the same screws on the back.36. Attach the bowden tube.’37. Unscrew all screws holding the bottom cover on.38. Remove the bottom cover.39. Power on the printer and be careful around the now live wires during the following step.40. With a multimeter, measure between PSU ground and the extruder trimpot.It should be aboout 1.25 volts from factory. Dial this down to 0.90 volts.41. Power it down and close it back up and you are done with the hardware configuration.Please see the Quick Start Guide for software configuration and print profiles.TAKE GOOD CARE OF ITEvery 6 months, or sooner if you have a higher than 15h per week average usage, perform the following maintenance operations:1. With a tooth brush and alcohol:a. Clean the double gear and the drive gearsb. Clean the needle bearings2. With a fine brush and lubricanta. Lubricate the needle bearings3. With compressed aira. Blow the housing plastic parts to remove dust and dirt particlesHOW TO GET HELPWe are available to help you with any questions or issues you may have. Simply go to our website where you can access our customer support and send us your questions or follow the provided link:https://www.bondtech.se/contact/#tab_technical-support-requestswww.bondtech.seDocuments / ResourcesBONDTECH Ender-7 LGX Lite And Mosquito On The Creality [pdf] Owner's ManualEnder-7 LGX Lite And Mosquito On The Creality, Ender-7, LGX Lite And Mosquito On The Creality, Lite And Mosquito On The Creality, And Mosquito On The Creality, Mosquito On The Creality, On The Creality, The CrealityReferencesBondtech Dual Drive Extruders and Extrusion Upgrade KitsContact Bondtech for support or to send us a messageManuals+,。
Telemecanique 产品系列说明书

A complete range ofinnovative and moresimple to use sensorsBenefit from Telemecanique’s major innovation:A worldwide detection first for improving productivity:b product selection simplifiedb product availability simplifiedb installation and setting-up simplifiedb maintenance simplifiedb detection simplified using a single supplier.Improved simplicity for improved productivity. Osi conceptImprove performance bymaking your selection andassembly lesscomplicated andmore intelligent.Improve serviceexpertise with anefficient product lineoffering simplifiedselection and improvedselling potential.Reduce maintenancetime with products thatare simpler andunequalled in flexibility.“Universal” series: Multi-purpose products providing multiple functions. Osi concept products are included in this series.“Optimum” series:Designed foressential andrepetitive functions.“Application” series:Offers functionsspecifically forspecialist needs, thusproviding the idealsolution for your morecomplex applications.Select the sensor according to your specific requirements> A single product that automatically adapts to all conditions> A single product that automatically adapts to all installation environ-ments> Availability of more than 5,000 interchange-able configurations within 24 hours> A user-friendly product at last; easy to parameter prior to installation and to modify during operation> A single product that automatically learns both its detection mode and detection zone> Simple parametering of many differentresolutions on the same product1/11Contentsb Osiris ™ Photo-electric sensors .......................1/2 to 1/11Detection without contact of objects whatever their shape or material> Detection from a few millimeters to several tens of meters> 3D adjustable fixing accessories> Specific products for particular applicationsb Osiprox ™ Inductive proximity sensors ......1/12 to 1/22Detection without contact of metal objects> Sensor / object distance - 60 mm> Generic cylindrical and flat form products > Specific products for particular applicationsb Osiprox Capacitive proximity sensors ....................1/23b Osiprox Ultrasonic sensors ............................1/24 to 1/33Detection without contact of any object of any material> Detection from a few millimeters up to 8 meters > Extra large range to ensure finding the right product > Specific products for particular applicationsb Osiswitch ™ Limit switches ..........................1/34 to 1/39Detection by contact of rigid objects> Positive opening operation of electrical contacts > Object speed - 1.5 m/s> Specific products for particular applicationsb Nautilus Sensors for pressure control .......1/40 to 1/41Detection by contact with fluid> Electronic pressure and vacuum switches > Analog pressure sensors> Electromechanical pressure and vacuum switches1/2For other versions, please consult with your local Schneider Electric/Square D sales office: visit 1/3For other versions, please consult with your local Schneider Electric/Square D sales office: visit 1/7For other versions, please consult with your local Schneider Electric/Square D sales office: visit 1L = 20 m M4 / M2.6 (1)M4 / L = 90 mm M6M4 / M6M6 / L = 90 mm M4 / M2.6M4 / L = 90 mm es u f f i D ma eb -u r h T 250 to 900(3)200 or 1500(1)1807060601518Ø 1Ø 1Ø 1Ø 1Ø 1+16 Ø 0.265Ø 1Ø 0.5 + 4 Ø 0.23Ø 0.5Ø 2.2Ø 2.2Ø 2.2Ø 2.2 x 2Ø 2.2 x 2Ø 2.2 x 2Ø 1 x 2Ø 1 x 2- 25 to + 60- 25 to + 60 - 25 to + 60- 25 to + 60- 25 to + 60- 25 to + 60- 25 to + 60- 25 to + 60XUFZ920XUFN12301XUFN12311XUFN05321XUFN05323XUFN05331XUFN02323XUFN01331(2)M4 x 0.7M4 x 0.7M6 x 0.75M6 x 0.75 / M4 x 0.7M6 x 0.75M4 x 0.7M4 x 0.7Long distance fibers Flexible fibers for t n e m e v o m l a c o r p i c e r s r e b i f e c n a t s i d g n o L sn e l l a r g e t n i h t i w M3 / M2.6 (1)M3 / L = 90 mm M8 / L = 20 mm M4 / M2.6M3 / L = 15 mm M6 / L = 15 mm M6 / L = 17 mm es u f f i D ma eb -u r h T 50 or 1000 (1)55596810052031 Ø5.1 Ø562.0 Ø5.0 Ø1 Ø5.0 Ø5.0 ØØ 1Ø 1Ø 2.2Ø 1 x 2Ø 1 x 2Ø 2.2 x 2Ø 2.2 x 2- 25 to + 60- 25 to + 60- 25 to + 60- 25 to + 60- 25 to + 60- 25 to + 60- 25 to + 60XUFN35301XUFN35311XUFN2L01L2XUFN01321XUFN04331XUFN5P01L2XUFN5S01L2M3 x 0.5M3 x 0.5M8 x 1.25M4 x 0.7M3 x 0.5M6 x 0.75M6 x 0.75Long distance fibers Flexible fibers Teflon fibers M4 / M2.6 (1)M4 / M2.6 (1)Ø 5 / L = 20 mm4C R U X r o s n e s r o l o c l l u f r o f d e s u c o f e s u f f iD ma eb -u r h T 300 or 2000(1)100 or 750(1)302010001Ø 1.5Ø 1Ø 1Transmitter Ø 1Receiver Ø 1.5Transmitter Ø 1.5Receiver Ø 1.5Transmitter and Receiver Ø 1.52 x 2.2 Ø2 x 2.2 Ø2 x 2.2 Ø2.2 Ø2.2 Ø2.2 Ø55 + o t 01 -55 + o t 01 -55 + o t 01 -06 + o t 52 -06 + o t 52 -06 + o t 52 -2L 30L 5N F U X 2L 20L 5N F U X 2L 10L 5N F U X 2L 10T 2N F U X 2L 10S 2N F U X 2L 10P 2N F U X M2.6 x 0.45 / M4 x 0.7M2.6 x 0.45 / M4 x 0.7by clip (included)2 elongated holes Ø 3.2 x 6.7 for M3 screws / fixing centers = 9.8 mmPlastic fiber optic light guides (length 2 m)Osiris1/8For other versions, please consult with your local Schneider Electric/Square D sales office: visit 1Optical frames for detection of passage of objectsXURZ01distanceFor other versions, please consult with your local Schneider Electric/ Square D sales office: visit a t s i dgn i s ne s l an i moN)5(wo l ebe l bagn i l dnahs l a i r e t aseries processingAnalog output1/9ForksNO/NC programmablePB100 In-line accessorypushbutton for teachingwindow limits (for Virtu TMVirtu Analog1/28For other versions, please consult with your local Schneider Electric/Square D sales office: visit 1(continued)Model Number*Accessories for SM602 Seriesh t g n e L e p y t n o i t c e n n o C °09ht g n e L e p y t n o i t c e n n o C t h g i a r t S XSCD101YM12 connector2 m XSCD111YM12 connector2 mAdditional cable lengths are available(*) All possible sensor configurations are not listed hereCharacteristicsHousing Style/Material 18 mm ULTEM ®Stainless Steel Flat-profile ULTEM ®18 mm ULTEM ®Stainless Steel Flat-profile ULTEM ®r o t c e n n o C e l b a C m3e p y T n o i t c e n n o C Supply Voltage CD V 42-21CD V 42-21RangeWindow178 mm 1.6 mmNO SM600A-701-00SM600A-701-00S SM600A-701-00FP SM650A-701-00SM650A-701-00S SM650A-701-00FP NCSM600A-701-10SM600A-701-10SSM600A-701-10FPSM650A-701-10SM650A-701-10SSM650A-701-10FP13 mmNO SM600A-708-00SM600A-708-00S SM600A-708-00FP SM650A-708-00SM650A-708-00S SM650A-708-00FP NCSM600A-708-10SM600A-708-10SSM600A-708-10FPSM650A-708-10SM650A-708-10SSM650A-708-10FP9 mmNO SM600A-712-00SM600A-712-00S SM600A-712-00FP SM650A-712-00SM650A-712-00S SM650A-712-00FP NCSM600A-712-10SM600A-712-10SSM600A-712-10FPSM650A-712-10SM650A-712-10SSM650A-712-10FP25 mmNO SM600A-716-00SM600A-716-00S SM600A-716-00FP SM650A-716-00SM650A-716-00S SM650A-716-00FP NCSM600A-716-10SM600A-716-10SSM600A-716-10FPSM650A-716-10SM650A-716-10SSM650A-716-10FP51 mmNO SM600A-732-00SM600A-732-00S SM600A-732-00FP SM650A-732-00SM650A-732-00S SM650A-732-00FP NCSM600A-732-10SM600A-732-10SSM600A-732-10FPSM650A-732-10SM650A-732-10SSM650A-732-10FP77 mmNO SM600A-748-00SM600A-748-00S SM600A-748-00FP SM650A-748-00SM650A-748-00S SM650A-748-00FP NCSM600A-748-10SM600A-748-10SSM600A-748-10FPSM650A-748-10SM650A-748-10SSM650A-748-10FP127 mmNO SM600A-780-00SM600A-780-00S SM600A-780-00FP SM650A-780-00SM650A-780-00S SM650A-780-00FP NCSM600A-780-10SM600A-780-10SSM600A-780-10FPSM650A-780-10SM650A-780-10SSM650A-780-10FPSM600 Series Ultrasonic Sensors18 mm & Flat-profile (continued)1/29For other versions, please consult with your local Schneider Electric/Square D sales office: visit 1(*) All possible sensor configurations are not listed hereSM602 Dual-levelSM600 SeriesFor other versions, please consult with your local Schneider Electric/1Osiswitch ™Limit switchesUniversal, complete switchesP ositive opening operation1OsiswitchFor other versions, please consult with your local Schneider Electric/1Osiswitch Limit switchesFor customized assembly of miniature1ver Sprwith plastic tipCat whiskerglass fiberrod leverL = 125 mmMetalspringle verL = 2 m4-pinand compact switchesOsiswitchFor other versions, please consult with your local Schneider Electric/1Osiswitch Limit swtichesClassic - XCKJ, complete switches1Complete switch Body/contact Head Le verwith reinforced with metal with thermoplastic with steel with steel roller with steelsteel roller end plunger roller le ver plunger,roller lever plunger,end plunger ball bear ingend plunger 1 direct. or actuation 1 direct.of actuation end plungerlever (2)Catalog number ZCKE09ZCKY71ZCKY61(1) Adjustable throughout 360° in 5° steps, or in 45° steps by reversing the le ver mounting.(2) Adjustable throughout 360° in 5° steps, or in 90° steps by reversing the notched washer.Customized assembly of Classic XCKJswitchesOperating heads, complete or for customer assemblyOsiswitchFor other versions, please consult with your local Schneider Electric/1/41For other versions, please consult with your local Schneider Electric/Square D sales office: visit 1NautilusSensors for pressure controlElectronic sensors XMLF。
Vaisala WMT700系列风速传感器用户指南说明书
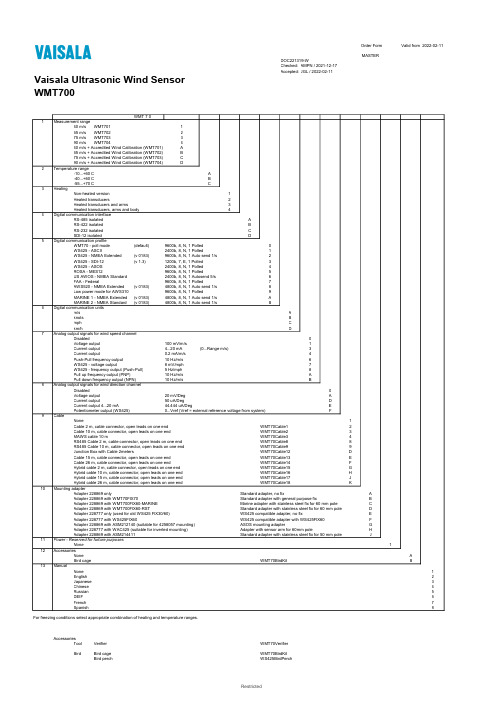
Order Form Valid from2022-02-11MASTERDOC221319-WChecked: AMPN / 2021-12-17Accepted: JGL / 2022-02-11Vaisala Ultrasonic Wind SensorWMT700WMT 7 01Measurement range40 m/s WMT701165 m/s WMT702275 m/s WMT703390 m/s WMT704440 m/s + Accredited Wind Calibration (WMT701)A65 m/s + Accredited Wind Calibration (WMT702)B75 m/s + Accredited Wind Calibration (WMT703)C90 m/s + Accredited Wind Calibration (WMT704)D2Temperature range-10...+60 C A-40...+60 C B-55...+70 C C3HeatingNon-heated version1Heated transducers2Heated transducers and arms3Heated transducers, arms and body44Digital communication interfaceRS-485 isolated ARS-422 isolated BRS-232 isolated CSDI-12 isolated D5Digital communication profileWMT70 - poll mode (default)9600b, 8, N, 1 Polled0WS425 - ASCII 2400b, 8, N, 1 Polled1WS425 - NMEA Extended(v 0183)9600b, 8, N, 1 Auto send 1/s2WS425 - SDI-12 (v 1.3)1200b, 7, E, 1 Polled3WS425 - ASOS 2400b, 8, N, 1 Polled4ROSA - MES12 9600b, 8, N, 1 Polled5US AWOS - NMEA Standard2400b, 8, N, 1 Autosend 5/s6FAA - Federal9600b, 8, N, 1 Polled7AWS520 - NMEA Extended(v 0183)4800b, 8, N, 1 Auto send 1/s8Low power mode for AWS3109600b, 8, N, 1 Polled9MARINE 1 - NMEA Extended(v 0183)4800b, 8, N, 1 Auto send 1/s AMARINE 2 - NMEA Standard(v 0183)4800b, 8, N, 1 Auto send 1/s B6Digital communication unitsm/s Aknots Bmph Ckm/h D7Analog output signals for wind speed channelDisabled0Voltage output100 mV/m/s1Current output 4...20 mA(0...Range m/s)3Current output0.2 mA/m/s4Push-Pull frequency output10 Hz/m/s6WS425 - voltage output8 mV/mph7WS425 - frequency output (Push-Pull) 5 Hz/mph8Pull up frequency output (PNP)10 Hz/m/s APull down frequency output (NPN)10 Hz/m/s B8Analog output signals for wind direction channelDisabled0Voltage output20 mV/Deg ACurrent output50 uA/Deg DCurrent output 4...20 mA44.444 uA/Deg EPotentiometer output (WS425)0...Vref (Vref = external reference voltage from system)F9CableNone1Cable 2 m, cable connector, open leads on one end WMT70Cable12Cable 10 m, cable connector, open leads on one end WMT70Cable23MAWS cable 10 m WMT70Cable34RS485 Cable 2 m, cable connector, open leads on one end WMT70Cable88RS485 Cable 10 m, cable connector, open leads on one end WMT70Cable99Junction Box with Cable 2meters WMT70Cable12DCable 15 m, cable connector, open leads on one end WMT70Cable13ECable 26 m, cable connector, open leads on one end WMT70Cable14FHybrid cable 2 m, cable connector, open leads on one end WMT70Cable15GHybrid cable 10 m, cable connector, open leads on one end WMT70Cable16HHybrid cable 15 m, cable connector, open leads on one end WMT70Cable17JHybrid cable 26 m, cable connector, open leads on one end WMT70Cable18K 10Mounting adapterAdapter 228869 only Standard adapter, no fix AAdapter 228869 with WMT70FIX70Standard adapter with general purpose fix BAdapter 228869 with WMT700FIX60-MARINE Marine adapter with stainless steel fix for 60 mm pole CAdapter 228869 with WMT700FIX60-RST Standard adapter with stainless steel fix for 60 mm pole DAdapter 228777 only (used for old WS425 FIX30/60)WS425 compatible adapter, no fix EAdapter 228777 with WS425FIX60WS425 compatible adapter with WS425FIX60FAdapter 228869 with ASM212140 (suitable for 4258057 mounting)ASOS mounting adapter GAdapter 228777 with WAC425 (suitable for inverted mounting)Adapter with sensor arm for 60mm pole HAdapter 228869 with ASM214411Standard adapter with stainless steel fix for 50 mm pole J 11Power - Reserved for furture purposesNone1 12AccessoriesNone ABird cage WMT70BirdKit B 13ManualNone1English2Japanese3Chinese4Russian5DEIF6French7Spanish8For freezing conditions select appropriate combination of heating and temperature ranges.AccessoriesTool Verifier WMT70VerifierBird Bird cage WMT70BirdKitBird perch WS425BirdPerchCable Cable 2 m, cable connector, open leads on one end227567SP Cable 10 m, cable connector, open leads on one end227568SPCable 15 m, cable connector, open leads on one end237890SPCable 26 m, cable connector, open leads on one end237889SPRS485 Cable 2 m, cable connector, open leads on one end228259SPRS485 Cable 10 m, cable connector, open leads on one end228260SPMAWS cable 10 m227565SPROSA analog cable 10 m, cable connector, open leads on one end231425SPAdapter cable for WS425 serial227569SPAdapter cable for WS425 analog frequency output227570SPJunction Box with Cable 2meters ASM210719SPWMT700 USB service cable240855Universal USB service cable with screw terminal for RS485 or RS232240884Hybrid cable 2 m, cable connector, open leads on one end CBL210706-2MSPHybrid cable 10 m, cable connector, open leads on one end CBL210706-10MSPHybrid cable 15 m, cable connector, open leads on one end CBL210706-15MSPHybrid cable 26 m, cable connector, open leads on one end CBL210706-26MSP Mounting WMT700 Mounting Accessories:Adapter for FIX70228869Fix70 (suitable also for inverted mounting)WMT70FixSPMounting adapter 60mm POM WMT700FIX60-POMSP Mounting adapter 60mm RST WMT700FIX60-RSTSP Cross-arm (40x40x850mm)WMT70CROSSARMMounting adapter between 228869 and 4258057ASM212140Mounting adapter 50mm RST ASM214411WS425 Mounting Accessories:Adapter for old WS425 FIX30/60228777FIX30WS425Fix30FIX60WS425Fix60Sensor support arm for 60mm pole (655mm with integrated fix for item 228777)WAC425Power Outdoor AC (mains) power supply for arm heated and fully heated WMT700PJB480Display Wind display XDi-N 144 (5’’ display) for ship navigation252307 Wind display XDi-N 192 (7’ display) for ship navigation252321。
17S705

17S705IntroductionThe 17S705 is a model of a computer processor developed by a leading technology company. This processor is specifically designed to deliver high performance and efficiency, making it suitable for a wide range of applications including gaming, multimedia, and data processing. In this document, we will explore the key features and specifications of the 17S705 processor, highlighting its advantages, and discussing its potential use cases.FeaturesThe 17S705 processor boasts several impressive features that set it apart from its competitors. Some of the prominent features include:1.High Clock Speed: The 17S705 is equipped with ahigh clock speed of 3.5 GHz, allowing for fast andresponsive computing. This makes it ideal for tasks thatrequire real-time processing, such as gaming andmultimedia editing.2.Multiple Cores: Built with multiple cores, the17S705 processor maximizes multitasking capabilities.Each core can perform independent tasks simultaneously, enhancing overall performance and efficiency.3.Advanced Architecture: The 17S705 utilizes anadvanced architecture, incorporating cutting-edgetechnologies to optimize performance. This includesfeatures such as branch prediction, speculative execution, and out-of-order execution, all of which contribute to faster and smoother operation.4.Enhanced Graphics: With integrated graphicsprocessing units (GPUs), the 17S705 processor deliversimpressive visual performance. It supports high-resolution displays and provides smooth graphics rendering, making it suitable for gaming and multimedia applications.5.Power Efficiency: The 17S705 processor isdesigned to be power-efficient, striking a balance between performance and energy consumption. This makes itsuitable for desktop computers, laptops, and other devices where power efficiency is a priority.SpecificationsLet’s dive deeper into the specifications of the 17S705 processor:1.Processor Type: 17S705 is a x86-64 processor,compatible with 64-bit operating systems.2.Number of Cores: The 17S705 processor has 8cores, allowing for efficient multitasking and parallelprocessing.3.Cache Size: It features a 12 MB L3 cache, whichhelps reduce memory access latency and improve overall system performance.4.Graphics: The integrated GPU supports DirectX 12and OpenGL 4.5, enabling smooth and high-quality graphics rendering.5.Socket Type: The 17S705 processor utilizes theAM4 socket, providing compatibility with a wide range of motherboards.6.Power Consumption: With a maximum thermaldesign power of 95 W, the 17S705 strikes a balancebetween performance and power efficiency.Use CasesThe 17S705 processor can be utilized in various scenarios. Some common use cases include:1.Gaming: With its high clock speed, advancedgraphics capabilities, and multiple cores, the 17S705processor can handle resource-intensive games with ease.It provides smooth gameplay, high frame rates, andrealistic graphics rendering.2.Multimedia Editing: The 17S705 processor’spowerful performance and integrated GPU make it ideal for multimedia editing tasks. It can effortlessly handle videorendering, image processing, and other multimedia-related tasks, reducing processing time.3.Data Processing: Thanks to its multiple cores andadvanced architecture, the 17S705 processor excels in data processing tasks. It can perform complex calculations,handle large datasets, and run multiple parallel tasksefficiently, making it suitable for data analysis and scientific computations.4.Software Development: Developers can benefitfrom the 17S705 processor’s fast proc essing speed andmultitasking capabilities. It can compile code quickly, run resource-intensive development environments, andsupport virtualization technologies.ConclusionThe 17S705 processor is a high-performance and power-efficient processor designed to cater to the demands of modern computing. Its impressive features, including high clock speed, multiple cores, advanced architecture, and enhanced graphics capabilities, make it suitable for a wide range of applications. Whether you are a gamer, multimedia professional, data analyst, or software developer, the 17S705 processor promises to deliver exceptional performance and efficiency, revolutionizing your computing experience.。
VS7 无缝切换器 用户手册说明书

版权所有©2019 西安诺瓦星云科技股份有限公司。
保留一切权利。
非经本公司书面许可,任何单位和个人不得擅自摘抄、复制本文档内容的部分或全部,并不得以任何形式传播。
商标声明是诺瓦科技的注册商标。
声明欢迎您选用西安诺瓦星云科技股份有限公司(以下简称诺瓦科技)的产品,如果本文档为您了解和使用产品带来帮助和便利,我们深感欣慰。
我们在编写文档时力求精确可靠,随时可能对内容进行修改或变更,恕不另行通知。
如果您在使用中遇到任何问题,或者有好的建议,请按照文档提供的联系方式联系我们。
对您在使用中遇到的问题,我们会尽力给予支持,对您提出的建议,我们衷心感谢并会尽快评估采纳。
目录1产品概述 (1)产品简介 (1)产品特性 (1)2外观说明 (3)前面板 (3)后面板 (4)产品尺寸 (5)3应用场景 (6)4液晶屏菜单操作 (7)操作说明 (7)主界面 (7)屏体配置 (9)4.3.2 输出模式 (9)4.3.3 屏体结构 (9)4.3.4 输出设置 (10)4.3.5 输出接口配置 (10)窗口设置 (11)4.4.1 窗口分屏模板 (11)4.4.2 BKG配置 (11)4.4.3 窗口配置 (12)场景设置 (13)输入设置 (14)画面控制 (14)测试画面 (14)预监选择 (15)高级设置 (16)4.10.1 同步模式 (16)4.10.2 Fn键设置 (16)4.10.3 返回主界面时长 (17)4.10.4 工厂复位 (17)4.10.5 HDCP开关 (17)4.10.6 硬件版本 (17)4.10.7 设备自检 (17)4.10.8 关于我们 (17)通讯设置 (18)语言设置 (19)5 V-CAN控制 (20)6常见问题 (21)7规格参数 (22)1 产品概述产品简介VS7是由诺瓦科技自主研发的集视频处理,画面拼接,特效切换和多画面显示的高性能无缝切换器。
VS7具备强大的视频信号接收和处理能力,支持4K×2K@30Hz视频输入,并最大可同时支持7路输入和5个独立窗口,并由4路DVI拼接输出,单机最大带载可达8KK。
KT-17SH1NMY电动杯子说明书

ELECTRIC KETTLE MODEL: KT-17SH1NMYPlease follow all the safety precautions listed below for safety and to reduce the risk of injury or electrical shock.● Do not touch the body of the kettle when it is hot.Alwayshold the appliance by the handle when using it.●Always ensure the lid is closed when in use. Failure toclose the lid will prevent the thermostat from switching offand cause the kettle to boil dry.● Keep the appliance well away from hot surfaces, andobjects that can be damaged by heat.● Ensure there is at least 20 cm space left to operate the kettle and that steam can escape safely. Never use the kettle undera cupboard or shelf where the steam may damage the surface.● A void contact with the steam from the spout when the wateris boiling or just after it has switched off.● Be careful when opening the lid for re-filling when the kettleis hot.● Ensure that the kettle cannot fall into water.● Do not fill or pour water from the kettle while it is on the base.● Disconnect the kettle at the mains supply before filling or emptying the jug, before cleaning any of its components,and when it is not in use.● Do not immerse the connecting cord in water or other liquids.● Do not allow liquids to come into contact with the body connector of the kettle, its base or the connecting cord.● Do not let the connecting cord overhang the edge of thework surface or allow it to touch hot surfaces or sources of heat or flame.● If any part of this appliance is damaged or malfunctioned in any way, or the connecting cord or mains plug is broken, do not continue to use it. Seek expert assistance.WARNING: Some accessible surfaces may be hot during operation of this applianceCAUTIONS● Do not place the power base unit on a metal tray or metal surface when plugged into power source.●This appliance is for indoor domestic use only. Do not use it at outdoor.●This kettle jug and power base form an integral appliance. Do not use other kettle jugs with this power base, or this kettle jug with other base.●The switch on this appliance must be readily operable at anytimes. Do not hinder its operation by incorrectplacement or by placing obstacles that may restrict its free movement.● This appliance is not intended for use by young children or infirmed persons unless they have been adequatelysupervised by a responsible person to ensure they can use the appliance safely.● This appliance is not intended for use by persons (including children below 8 years old) with reduced physical, sensory or mental capabilities, or lack of experience and knowledge, unless they have been given supervision or instructionconcerning use of the appliance by a person responsible for their safety.● Children should be supervised to ensure that they do not play with appliance.● Cleaning and user maintenance shall not be performed by children unless they are older than 8 years old and be supervised.● Keep the appliance and its cord out of reach for children less than 8 years old.PARTS NAMES AND HANDLING INSTRUCTIONSPRELIMINARIES Unpack your kettle and any accessories carefully. Retain the packaging so that you can transport the appliance safely. If you dispose of it please do so with regard to any recycling regulations in your area.Before using your kettle: Check that the voltage marked on the rating plate under the kettle or the base matches your mains voltage. Please read all the instructions in this User Guide with particular reference to the safety notes.OPERATION ●●●●●●●Separate the kettle from the base. Ensure that the mains socket is switched off at the wall. Lead the power cord out through the recess in the base. Place the kettle base on a stable level surface and connect the power cord to the wall socket. Excess cord may be safely stowed by feeding it carefully into the stowage compartment in the base. Ensure the power cable exits the cut out slot otherwise the kettle base will not be stable.Pour away previously boiled water.Push the lid release button to lift up the lid.Fill the kettle with fresh water. The MIN and MAX marks are located on the water scale . The water level must always cover the MIN (0.5 litres) mark . Do NO T fill the kettle above the MAX mark (1.7 litres) , or boiling water may be ejected. Close the lid, place the filled kettle correctly on the power base.How to Boil Water Switch on the power at the wall socket.The kettle ON/OFF switch is located below the handle. Press●●●●●●●the switch down to switch the kettle on.The power switch will illuminate showing the kettle is in operation. When the water has reached the correct temperature, the power switch will switch off.Y ou can stop the boiling at anytime by lifting the switch up. T o re-boil, press the switch again. If the water is very hot, it maybe necessary to wait until the switch resets.Always ensure the lid is tightly fitted and never lift it while the kettle is boiling or you run the risk of scalding. If the lid is not correctly fitted while boiling, the automatic cut-out will not operate, you may boil the kettle dry and cause damage due to excessive steam emissions.After boiling, switch off the appliance at the mains. The kettle now could be safely removed from its base and pour out the boiled water. Always pour boiling water slowly and carefully without tipping the kettle too quickly.Never leave hot water in the kettle while it is unattended.After use, replace the kettle on its base.Before first use or after storage:Fill the kettle with fresh water. Boil the water. Pour away the boiled water. Repeat this two or three times.The kettle is now ready for use.Boil Switch with Auto Shut-offWhen boiling water, do NO T hold the switch down or steam will be ejected from the lid and you may damage the automatic shut off mechanism.Always ensure that theON/OFF switch is clear of obstructions, readily operable and is not prevented from switching off.Boil Dry ProtectionY our kettle is fitted with a safety device which switches it off if the appliance is operated with insufficient water. If this occurs, the kettle should be switched off at the mains and allowed to cool thoroughly before refilling with cold water.The safety device will then reset.Overheating Shut -OffIn the status of gross overheating, your kettle will automatical l y shut down status to prevent further damage.Should this occur, take it to a qualified service person for examination and repair.CLEANINGlifespan,●●●●●THIS APPLIANCE MUST BE EARTHEDTHIS APPLIANCE MUST BE ATTENDED AT ALL TIMES WHEN IN OPERATIONSTORAGE Excess cord can be stowed by feeding the cord into the storage cavity in the base of the unit. When the kettle is not in use, it should be stored on its base and out of the reach of children and pets.。
Keychron K17 Pro Bluetooth Mechanical Keyboard 用户手

Manuals+— User Manuals Simplified.Keychron K17 Pro Bluetooth Mechanical Keyboard User Guide Home » Keychron » Keychron K17 Pro Bluetooth Mechanical Keyboard User GuideContents1 Keychron K17 Pro Bluetooth Mechanical Keyboard UserGuide2 IN THE BOX:3 QUICK START GUIDE4 K17 PRO BLUETOOTH MECHANICAL KEYBOARD OVERVIEW5 KEY DESCRIPTION6 LED STATUS OVERVIEW7 FUNCTION DESCRIPTION:8 TROUBLESHOOTING9 Documents / ResourcesKeychron K17 Pro Bluetooth Mechanical Keyboard User GuideIN THE BOX:Keychron K17 Pro Bluetooth Mechanical Keyboard x 1 Type-C Cable x 1Manual x 1Quick Start Guide x 1Extra Keycaps Set x 1QUICK START GUIDEIf you are a Windows user, please find the appropriate keycaps in the box, then follow the instructions below to find and replace the following keycaps.* Step by step guide can be found on our website.K17 PRO BLUETOOTH MECHANICAL KEYBOARD SPECIFICATIONSNumber of keys: 103Switch type: MechanicalBattery: 2000mAhCharging time: Around 3 hoursCharging port: USB Type-CMode: Bluetooth / WiredBluetooth operating distance: Within 10 meters (open space)Name of Bluetooth device: Keychron K17 ProOperating environment: -10 to 50°CTechnical specifications can be subjected to change without notice, we apologize for any inconvenience caused. K17 PRO BLUETOOTH MECHANICAL KEYBOARD OVERVIEWDEFAULT KEY LAYOUT:LAYER 0: This layer will be activated when your keyboard’s system toggle is switched to Mac.LAYER 1: This layer will be activated when your keyboard’s system toggle is switched to Mac and press the fn/M0(1) key.LAYER 2: This layer will be activated when your keyboard’s system toggle is switched to Windows.LAYER 3: This layer will be activated when your keyboard’s system toggle is switched to Windows and press the fn/M0(3) key.KEY DESCRIPTIONLED STATUS OVERVIEWFUNCTION DESCRIPTION:CHARGINGPlug the cable into a USB port and plug the other end into the keyboard port. Charging Indicator: When battery is below 15%, a red battery blinking indicator will be triggered. A red light will stay on while charging; Fully charged in around 3 hours, a green battery indicator will appear.*The Keychron keyboard is compatible with all USB ports. Please use a SV 1A adapter or USB 3.0 for the best performance. The Keychron K17 Pro can be charged in Bluetooth/ OFF/Cable mode. **This product supports upto SV charging voltage and 1A charging current. We are not responsible for any problems caused by improper charging.BLUETOOTH / WIRED MODE (MODE TOGGLE SWITCH)WIRED MODE1. Switch the toggle switch to the Cable option (it only works when a USB cable is plugged in).2. Connect our cable with your PC and keyboard.3. Backlighting will be turned on.*Under Wired Mode, keyboard will not enter into Battery Saver Mode.BLETOOTH MODE1. Switch the toggle switch to the Bluetooth option.2. Backlighting will be turned on.3. Hold “fn+1” key for 4 seconds to activate Bluetooth pairing (the Bluetooth indicator fast flashes for 3 minutes todetect pairing).4. Search for the Bluetooth device “Keychron K17 Pro” on your device and connect it (the Bluetooth indicatorgoes off after successful pairing).Note: This keyboard supports pairing up to 3 devices simultaneously via key combination “fn” + “1” I “fn” + “2” I “fn”+ “3”.*The Bluetooth indicator will continue to flash for 3 minutes.**Slow or failed connections may exist due to different Bluetooth versions, please make sure all the settings are correct.SWITCH BLUETOOTH DEVICESShort press key combination “fn” + “1” / “fn” + “2” / “fn” + “3” to switch to other device.RECONNECT:1. Switch the keyboard to the Bluetooth option to activate the keyboard.2. The Bluetooth indicator flashes for 4 seconds and automatically pairs with the last paired device.3. If the Bluetooth indicator is off, press any button to enter the connection again.* The keyboard must have been paired with the device to perform this function.TURN OFF THE KEYBOARDSwitch the keyboard to the OFF option.3 – INPUT METHOD SWITCHFor iOS:Input method switch: Ctrl + SpaceCaps Lock: Caps (Enable General>Keyboards>Hardware Keyboard>Caps Lock Language Switch)For Android:Input method switch: Shift+ SpaceNOTE: Functions of certain multimedia key may be disabled due to compatibility, versions, brands and drivers of Windows/ Android OS. We also recommend not to switch OS frequently as it may impact keyboard operations. TROUBLESHOOTINGIf unable to pair keyboard to device, confirm that the device you’re trying to pair with isBluetooth-capable. If so, restart the device and try pairing it with the keyboard again.Note: On a Windows computer, a new Bluetooth connection will sometimes require additional software updates-a process that may still be ongoing after a message appears indicating a successful completion. Wait at least 20 minutes after pairing to make sure all updates are completed before restarting the computer.Confirm that the device is configured to accept Bluetooth connections (Windows) and supports an external keyboard (HID profile).Go to Bluetooth Devices > Open Settings and select the following:Allow Bluetooth devices to find this computerAllow Bluetooth devices to connect to this computerAlert me when a Bluetooth device wants to connectMy keyboard isn’t working.For the computer/smartphone:Go to your device Bluetooth settings>Select the keyboard and remove/delete/unpair it.Then restart your device.For the keyboard:Turn the keyboard off and back on. Then reconnect it to your device.Bluetooth connection is interrupted even within 10 meters.Check if the keyboard is resting on a metal surface that can interfere with the Bluetooth signal.Third-party input tools are not compatible with the keyboard.Due to compatibility, versions, brands and drivers of Windows/Android OS, functions of third-party input tools may be affected while using the keyboard. Please make sure your operating system and drivers are up to date. Certain multimedia keys or function keys do not work.Functions of certain multimedia keys may be disabled due to compatibility, versions, brands, and drivers of devices.Safety Precaution:Keep the product, accessories and packaging parts out of the reach of children to prevent any accidents and choking hazards. Always keep the product dry to avoid corrosion. Do not expose the product to extreme temperatures below -10°C(S°F) or above 50°C(131 °F) to preserve the lifespan of the keyboard.Keychron, Inc.Dover, DE 19901, United StatesFind us at:https://********************IJ@keychron@@keychronW’@keychronMKDesigned by KeychronMade in ChinaRead More About This Manual & Download PDF:Documents / ResourcesKeychron K17 Pro Bluetooth Mechanical Keyboard [pdf] User GuideK17 Pro, K17 Pro Bluetooth Mechanical Keyboard, Bluetooth Mechanical Keyboard,Mechanical Keyboard, KeyboardManuals+,。
索爱V-17说明书

目录功能概述 (2)注意事项 (2)认识机型 (4)按键功能定义说明 (5)主要界面显示说明 (5)基本操作 (8)系统菜单 (8)音乐模式 (8)视频模式 (10)图片浏览器 (10)电子书 (11)收音机 (12)录音机 (13)文件浏览器 (14)工具箱 (15)系统设置 (15)使用USB磁盘 (16)MINISD扩充卡使用 (16)AV OUT输出功能 (17)机器充电说明 (17)故障解决 (18)申明 (19)为了您能尽快轻松自如地操作索爱数码播放器,我们随机配备了内容详尽的用户手册,从中您可以获取有关的产品介绍,使用方法等方面的知识,在您开始使用MP5数码播放器之前,请仔细阅读我们随机提供的所有资料,以便您能正确使用产品。
功能概述●高清晰真彩TFT彩屏显示,支持480×272分辨率●支持MP3、WMA、WAV、FLAC等音乐格式●支持MPEG-4(AVI)、RMVB、RM 720P高清视频格式不需转换,有些格式需转换。
●支持插卡功能MININ SD卡128M/256M/512M/1GB/2GB/4GB 等●支持高清晰JPEG和GIF格式图片浏览●数码录音,A-B复读功能●节能设置:亮度可自由调节,定时关机时间●支持3D音效设置,均衡音效。
●多种循环风格:单曲循环、全部循环、单曲播放、顺序播放、随机播放●支持多国语言●支持桌面背景设置,桌面模式设置,桌面时间设置等各性化设置。
●支持游戏功能●USB2.0高速传输●支持电子书阅读,书签功能●具备世界时间查询日历功能时间显示●AV OUT输出功能:LCD、AV_PAL、AV_NTSC●移动U盘功能,支持固件升级●支持操作系统:Windows98/SE/ME/2K/XP●使用温度:-5至40摄氏度注意事项本手册含有重要的安全措施和正确使用产品的信息,为避免事故发生,请在使用该产品之前仔细阅读该手册。
●请不要将产品放在高温度、潮湿或灰尘多的地方使用,以免影响产品寿命●避免摔落或强烈碰撞产品,不要让TFT屏遭到猛烈震动,否则可能导致TFT屏损坏或显示不正常●请选择合适的音量,使用耳机不宜过大音量,若感到耳鸣,请调小音量或停止使用●在下列情况下请充电:A、电池电量图标显示空时B、系统自动关机,再次开机后很快关机C、操作按键没有反应●本播放器采用的是高容量锂电池,可重复充电使用. 在前几次充电必须充够8小时,并且每次用完电量再进行充电,以保证电池的使用寿命。
Enphase IQ 7, IQ 7+ 和 IQ 7X 微逆变器安装指南说明书

Installing Enphase IQ 7, IQ 7+ and IQ 7X MicroinvertersTo install Enphase IQ Series Microinverters, read and follow all warnings and instructions in this guide and in the Enphase IQ 7 and IQ 7+ Microinverter Installation and Operation Manual at: /support . Safety warnings are listed on the back of this guide.The Enphase Microinverter models listed in this guide do not require grounding electrode conductors (GEC), equipment grounding conductors (EGC), or grounded conductor (neutral). The microinverter has a Class II double-insulated rating, which includes ground fault protection (GFP). To support GFP , use only PV modules equipped with DC cables labeled PV Wire or PV Cable .IMPORTANT: Enphase IQ Series Microinverters require the Q Cable and are not compatible with previous Enphase cabling. An IQ Envoy is required to monitor performance of the IQ Microinverters . The Q Accessories work only with Enphase IQ Series Microinverters.D ) Check that you have these other items:• AC junction box.• Tools: screwdrivers, wire cutter, voltmeter, torque wrench, sockets, and wrenches for mounting hardware E ) Protect your system with lightning and/or surge suppression devices. Itis also important to have insurance that protects against lightning and electrical surges. F ) Plan your AC branch circuits to meet the following limits for maximumnumber of microinverters per branch when protected with a 20-amp over-current protection device (OCPD).Maximum* IQ Micros per AC branch circuitIQ 7 Micros(240V single phase)IQ 7+ Micros(240V single phase)IQ 7X Micros(240V single phase)161312IQ 7 Micros (208V single phase)IQ 7+ Micros (208V single phase)IQ 7X Micros (208V single phase)131110* Limits may vary. Refer to local requirements to define the number of microinverters per branch in your area.G ) Size the AC wire gauge to account for voltage rise. Select the correctwire size based on the distance from the beginning of the Enphase Q Cable to the breaker in the load center. Design for a voltage rise total of less than 2% for the sections from the Enphase Q Cable to the breaker in the load center. Refer to the Voltage Rise Technical Brief at /support for more information.PREPARATIONA ) Download the Enphase Installer Toolkit mobile app andopen it to log in to your Enlighten account. With this app, you can scan microinverter serial numbers and connect to the Enphase IQ Envoy to track system installation progress. To download, go to /toolkit or scan the QR code at right.B ) Refer to the following table and check PV module electrical compati-bility at: /en-us/support/module-compatibility .ModelDC connectorPV module cell countIQ7-60-2-US MC-4 locking type Pair only with 60-cell modules.IQ7PLUS-72-2-US MC-4 locking type Pair with 60- or 72-cell modules.IQ7X-96-2-USMC-4 locking typePair only with 96-cell modules.C ) In addition to the Enphase Microinverters, PV modules and racking,you will need these Enphase items :• Enphase IQ Envoy (model ENV-IQ-AM1-240) communications gateway or IQ Combiner+ (model X-IQ-AM1-240-2): required to monitor solar production• Tie wraps or cable clips (Q-CLIP-100)• Enphase Sealing Caps (Q-SEAL-10): for any unused connectors on the Enphase Q Cable• Enphase Terminator (Q-TERM-10): one needed at the end of each AC cable segment• Enphase Disconnect Tool (Q-DISC-10) • Enphase Q Cable:Manage the Cabling A )Use cable clips or tie wraps to attach thecable to the racking. The cable must be supported at least every 1.8 m (6 feet).B ) Dress any excess cabling in loops sothat it does not contact the roof. Do not form loops smaller than 12 cm (4.75 inches) in diameter.Create an Installation Map Create a paper installation map to record microinverter serial numbers and position in the array.A ) Peel the removable serial number label from each microinverterand affix it to the respective location on the paper installation map.B ) Peel the label from the IQ Envoy and affix it to the installation map.C ) Always keep a copy of the installation map for your records.Mount the Microinverters A ) If the Enphase DC bulkhead connectors are not already attached tothe microinverters, attach them now. Make sure they are fully seated.B ) Mount the microinverter bracket side up (as shown) and under thePV module, away from rain and sun. Allow a minimum of 1.9 cm (0.75 inches) between the roof and the microinverter. Also allow 1.3 cm (0.50 inches) between the back of the PV module and the top ofthe microinverter.C ) Torque the mounting fasteners (1/4-inch or 5/16-inch) as follows.Do not over torque.3654INSTALLATIONPosition the Enphase Q Cable A ) Plan each cable segment to allow connectors on the Enphase Q Cableto align with each PV module. Allow extra length for slack, cable turns, and any obstructions.B ) Mark the approximate centers of each PV module on the PV racking.C ) Lay out the cabling along the installed racking for the AC branch circuit.D ) Cut each segment of cable to meet your planned needs.1Position the Junction Box A ) Verify that AC voltage at the site is within range:Service Type and Voltage: L1 - L2240 V Split-Phase 211 to 264 VAC 208 V Single Phase183 to 229 VACB ) Install a junction box at a suitable location on the racking.C ) Provide an AC connection from the junction box back to the electricitynetwork connection using equipment and practices as required by local jurisdictions.2Affix serial number labelsConnect the Microinverters A ) Connect the microinverter. Listen for a click as the connectorsengage.B ) Cover any unused connectors on the AC cable with EnphaseSealing Caps. Listen for a click as the sealing caps engage.To remove a sealing cap or AC connector, you must use an Enphase disconnect tool.Cable clip: Install sealing caps on all unused AC connectors as these connectors become live when the system is energized.Terminate the Unused End of the CableA ) Remove 13 mm (1/2”) of the cable sheath fromthe conductors. Use the terminator loop to measure.B ) Slide the hex nut onto the cable. There is a grommet inside of theterminator body that should remain in place.C )Insert the cable into the terminator body so that each of the twowires land on opposite sides of the internal separator.D ) Insert a screwdriver into the slot on the top of the terminator tohold it in place, and torque the nut to 7 Nm.E ) Hold the terminator body stationary withthe screwdriver and turn only the hex nutto prevent the conductors from twistingout of the separator.F ) Attach the terminated cable end to thePV racking with a cable clip or tie wrapso that the cable and terminator do nottouch the roof.Connect the PV ModulesA ) Connect the DC leads of each PV module to the DC input connectorsof the corresponding microinverter.B ) Check the LED on the connector side of the microinverter. The LEDis applied.C)microinverters.ACTIVATE MONITORING AND CONTROLS7WARNINGAfter you have installed the microinverters, follow the procedures in theEnphase IQ Envoy Quick Install Guide to activate system monitoring, setup grid management functions, and complete the installation.• Connecting the IQ Envoy• Detecting devices• Connecting to Enlighten• Registering the system• Building the virtual arrayEnergize the SystemA ) Turn ON the AC disconnect or circuit breaker for the branch circuit.B ) Turn ON the main utility-grid AC circuit breaker. Your system will startproducing power after a five-minute wait time.C )Check the LED on the connector side of the microinverter:LED IndicatesFlashing green Normal operation. AC grid function is normal andthere is communication with the IQ Envoy.Flashing orange The AC grid is normal but there is nocommunication with the IQ Envoy.Flashing red The AC grid is either not present or not withinspecification.Solid red There is an active “DC Resistance Low, Power Off”condition. To reset, refer to the Enphase IQ EnvoyInstallation and Operation Manual at:/support.910Terminator Body13mmComplete Installation of the Junction BoxA) Connect the Enphase Q Cable into the junction box.The Q Cable uses the following wiring color code:Wire ColorsBlack – L1Red – L28Internal ViewSafety Symbols +*;✓T o S h e e t / A l a h o j a d e _______。
VESSEL威威No.700螺丝刀和No.730的区别

1. No.980 系列冲击式螺丝刀☆产品说明:①手柄内部采用独特的贯通回旋设计,敲击螺丝刀底部,前端瞬间反向回旋12 °,尤其适用于生锈,破损螺丝的拆卸②手柄采用三面细纹防滑设计,并有效防止油渍附着附带视频介绍,请详细参考③前端强力磁性加工④螺丝刀身采用混合钒元素的超硬钢材,避免螺丝刀头打滑,崩裂 ⑤全身硬化加工,通过 ECO, RoHS 环保认证2. No. 700 (不可敲击)No.730 系列弹性手柄贯通可敲击螺刀☆产品说明:①柄部配有GEL 弹性软垫,使用时GEL 软垫会随伴握转方向同时移动,明显降低手的劳累感,手感极佳。
②螺丝刀身采用混合钒元素的超硬钢材,避免螺丝刀头打滑,崩裂③全身硬化加工,通过ECO, RoHS 环保认证④前端强力磁性加工⑤螺丝刀刀身采用黑铬元素镀膜,防止生锈⑥尺寸齐全,适用于各种工序。
十字系列采用红色,一字系列采用紫色搭配螺丝刀手柄,视觉感分明,容易区分。
使用实例照片注明 No.730 贯通可敲击螺丝刀握柄后部配有银色五角星No.700 螺丝刀握柄后部没有配有银色五角星避免螺丝刀头打滑,崩裂,全身硬化加工,通过 ECO, RoHS 环 保认证,螺丝刀刀身采用黑铬元素镀膜,防止生锈。
最适合狭窄空 间使用附带视频介绍,请详细参考深圳市 杉本 贸易有限公司 联系人:张 生 手 机: 13 430480777 QQ : 285 0148 5994. No. 内六角扳手 8806BP (6 组套), 8809BP (9 组套) ☆3. No. 720 系列弹性手柄圆球型螺丝刀产品说明:柄部配有 GEL 弹性软垫,螺丝刀身采用混合钒元素的超硬钢材,产品说明:①全身硬化处理,采用国际色标,现场使用时可通过颜色快速区分前端尺寸,采用开合式套装设计,便于使用和保存。
②ball 端采用特殊削切加工,最大可倾斜35 °③内六角端短轴设计,非常适用于狭小空间的使用④实际使用实例工,增加与螺丝的摩擦,降低螺丝前端自身磨损。
- 1、下载文档前请自行甄别文档内容的完整性,平台不提供额外的编辑、内容补充、找答案等附加服务。
- 2、"仅部分预览"的文档,不可在线预览部分如存在完整性等问题,可反馈申请退款(可完整预览的文档不适用该条件!)。
- 3、如文档侵犯您的权益,请联系客服反馈,我们会尽快为您处理(人工客服工作时间:9:00-18:30)。
Essays on Teaching Excellence Toward the Best in the AcademyVolume 17, Number 7, 2005-06A publication of The Professional & Organizational Development Network in Higher Education ().Practice Tests: a Practical Teaching Method Margaret K. Snooks, University of Houston-Clear LakeThe use of practice tests has been around for decades. This essay describes the development, implementation, and evaluation of short daily tests on assigned readings. Giving daily practice tests over the past several years has resulted in higher end-of-semester grade averages in my classes, increased reliability of students’ exam scores, and more positive student satisfaction with teaching. I have found student responses to practice tests to be overwhelmingly positive; and, most importantly, learning improves.College Students and Reading Assignments Daily practice tests are a method aimed at (1) encouraging students to complete reading assignments on a regular basis, (2) clearing up student misconceptions about what an instructor believes is important in textbooks, (3) at least partially allaying students’ anxiety about reading assignment material on which they will be tested, and (4) improving student learning. Daily practice tests are related to Classroom Assessment Techniques (Angelo & Cross, 1993) but focus on reading assignments rather than on content or skills covered in class. Practice tests include the “pair and share” and “peer tutoring” components of some CATs. In a study of faculty and studentexperiences with classroom assessment, Steadman (1998) found that most faculty members believe such practices improve student learning and give them feedback on student comprehension. For the students, assessment “…involves students in active mental processing of new information and makes them more aware of themselves as learners” (Steadman, 1998, p. 23). Practice tests, as assessment instruments, accomplish the same goals. Practice tests are also a form of diagnostic assessment or a test being used to identify students’ strengths and weaknesses on particular topics (Gall, Borg & Gall, 1996). An additional benefit of using practice tests is their inclusion in faculty members’ annual reports or portfolios as evidence of special concern with student learning.Developing Practice Tests The first step is for instructors to be clear about learning objectives and how the information in textbooks contributes to essential knowledge and skills. There must be complete coordination among course objectives, the course content to be covered both inside and outside of class, and questions on examinations.The second step is for instructors to read textbooks carefully to identify important content and skills that will not be covered in class due to lack of time. It is also a good idea if students receive a set of take-home short answer essay questions based on what instructors believe to be important in the reading assignments. Students can then read chapters each week, answer the short essay questions based on the reading, and research any information they encountered but did not understand. The last question I use for every set of chapter questions is: “What was not clear?”Not all in-class practice test questions will appear on exams, but practice tests provide students with a clear understanding of the type of exam questions that may be included and theform they will take. Some textbook publishers provide test questions with instructor manuals or on CDs, but instructors should first list what issues in each chapter are significant and only thereafter consider sample questions. I usually end up devising about 90% of my practice test questions in spite of publisher-provided questions.Implementation of Practice Tests On the first class day I tell my students that there are at least 3 sources for learning in the course: the instructor, the textbook author(s), and the students themselves. Students also hear and read on the syllabus that class participation is welcome and encouraged. Students earn points for participation in class discussions. My students know that I will not insult them by reading the textbook aloud in class or by giving lectures based entirely on the textbook. The material in textbooks is a supplement to what is covered in class. Students will demonstrate mastery of knowledge and skills by participation in class discussions and by answers on examinations. Exam questions will include material from the textbooks. The material covered in class (and not covered in the textbook) will also appear on tests.At the beginning of every class meeting, I ask students if they have any questions about the reading assignment for the day. This is likely to be the only time the students and I discuss what is in the textbook. The practice tests, containing about five multiple-choice questions, are then handed to the students. These tests are the means by which attendance is taken, and students get credit for being present whether or not they do well on the test. The point of the tests is the practice of taking tests on assigned readings and participation in discussions of questions taken from reading material. Having the tests at the beginning of class has the added benefit of discouraging late arrivals. No class time is lost to roll taking since students confirm their presence through their practice tests.Students first take the practice test individually and then compare and discuss their answers with a peer. Finally, there is a class discussion about the best answers and, more importantly, why they are best. We also discuss why other answers are not as effective. This helps me discover possible misunderstandings stemming from the wording of test questions. As is true of questions on the regular tests, the questions on practice tests are authentic, academically sound, and essential to learning course content. The practice test innovation is not about “teaching the test” or drilling or learning by rote. It is about critically analyzing questions, recalling important aspects of assigned readings, and developing expertise with regard to course content and its application. Evaluation of the Impact of Practice Tests My original goal of using practice tests was to improve student learning and student grades. Based on a 10 year comparison of data from 80 classes with approximately 2400 students, final averages have increased by 5 points (Snooks, 2005).In addition, three years of analyses indicate a direct positive relationship between the number of practice tests taken and my students’ final course grades. Reliability on all exams is .85 or above. Practice tests increase students’ critical thinking about the purpose of questions while increasing student proficiency for taking tests. When using objective tests instructors can easily see the numbers of students who missed each question and the “wrong” answers they selected. With this information, instructors can learn precisely what concepts or skills should be re-taught and the likely causes of student confusion.Student satisfaction is another measure of teaching effectiveness. Gretes and Green (2000) found that 90% of students believed practice tests helped them study for “real” exams. Thorne (2000) used practice tests to encouragepreparation for class. Another group found practice tests to be a good review strategy (Kulik, Kulik, & Bangert, 1984). On both mid-term and end-of-semester evaluations, my students have indicated that they like taking daily practice tests and find them beneficial. In response to the question “What does your instructor do in this class that helps you learn?” the option “class discussion/lectures” is ranked as most helpful while “practice tests” is listed second. Students usually answer “excellent” to questions about “Instructor’s interest in whether students learn.” My most recent student evaluations averaged 4.9 out of 5.0.An unintended consequence of practice tests is that students exhibit less hostility during discussions following the return of major exams. A student may say a test question was “tricky”, but other students will typically say things like “There was a similar question on a practice test.” One of my students recently wrote on an anonymous evaluation: “Your test questions are straightforward for any student who has read the chapters, comes to class, and has participated.”Summary Daily practice tests improve student learning and course grades by encouraging students to do reading assignments in advance of class meetings. Such tests also encourage students to come to class on time while increasing student test-taking skills and defusing post-exam hostility. Devising practice tests helps instructors clarify their course goals, better coordinate relationships between reading assignments and class discussion/lectures, and hone their test-writing skills.ReferencesAngelo, T. A., & Cross, K. P. (1993). Classroom assessment techniques: A handbook for college teachers (2nd ed.). San Francisco, CA: Jossey-Bass.Gall, M. D., Borg, W. R. & Gall, J. P. (1996). Educational research: An introduction (6th ed.). NY: Longman.Gretes, J. A., & Green, M. (2000). Improving undergraduate learning with computer-assisted assessment. Journal of Research on Computing in Education, 33(1), 46-55. Kulik, J. A., Kulik, C. C., & Bangert, R. L. (1984). Effects of practice on aptitude and achievement test scores. American Educational Research Journal, 21, 435-447.Snooks, M. K. (2005). Unpublished raw data based on comparisons of test scores over the past ten years among 8 courses taught each academic year with approximately 2400 students total.Steadman, M. (1998). Using classroom assessment to change both teaching and learning. New directions for teaching and learning, 75. San Francisco, CA: Jossey-Bass.Thorne, B. M. (2000). Extra credit exercise: A painless pop quiz. Teaching of Psychology, 27, 204-206.Margaret K. Snooks (Ph. D., University of Texas at Austin) is a fulltime faculty member at the University of Houston-Clear Lake, where she also serves as co-convener of the Teaching-Learning Enhancement Center.。