加工余量-尺寸链生产率与经济性
加工余量的确定..

1. 加工余量概念
(1)总加工余量
总加工余量是指零件加工过 程中,某加工表面所切去的 金属层总厚度。是毛坯尺寸 与零件图样的设计尺寸之差。
(2)工序余量
工序余量是一道工序内切除的 金属层厚度,为相邻两工序的 工序尺寸之差。
(3)总余量为各工序余量之和
(4)公称余量
公称余量是指相邻两 工序的基本尺寸之差。
(5)余量公差
Tz Z max Z min Ti Ti 1
2. 影响加工余量的因素
1、上工序的表面粗糙度和表面缺陷层(图7-24) 2、上工序的尺寸公差(图7-25) 3、上工序各表面间相互位置的空间偏差(图7-26) 4、本工序安装误差(图7-27)
的尺寸及公差。
解: 1)确定封闭环、建立尺寸链、判别增减环。
假废品的出现
只要测量尺寸的超差量小于或等于其余组成环 尺寸公差之和,就有可能出现假废品,为此应对该 零件各有关尺寸进行复检和验算,以免将实际合格 的零件报废而导致浪费。 假废品的出现,给生产质量管理带来诸多麻烦, 因此,不到非不得已,不要使工艺基准与设计基准 不重合。
3.有关余量的尺寸换算
图9-29 精加工余量校核示例 (1)精加工余量校核 当多次加工某一表面时, 由于所采用的工艺基准可能相同,因此,本工 序的余量的变动量不仅与本工序的公差及前一 工序的公差有关,而且还与其它有关工序的公 差有关。在以工序余量为封闭环的工艺尺寸链 中,如果组成环数目较多,由于误差累积原因, 有可能使工序余量过大或过小,因此须对余量 进行校核, 这在制订工艺规程时是一个不可忽 视的问题。由于粗加工的余量一般取值较大, 故粗加工余量一般不进行校核而仅对精加工余 量进行校核。
《机械制造技术基础》教学大纲

《机械制造技术基础》教学大纲习惯专业:机械类各专业课程性质:必修课总学时:108总学分:6一、课程性质、目的与任务《机械制造技术基础》是模具设计与制造专业必修的一门专业基础课。
是一门集“教、学、做”一体化的课程。
该课程是以“典型零件机械加工工作过程”为主线,惯穿工艺规程制定与实施,有机融合了金属切削加工的基本知识及常用机床夹具的基本知识,而建设的一门综合性课程。
课程讲授了常用刀具的结构与选择、机械加工工艺规程、典型零件的加工工艺的编制、机械加工的质量分析、机械装配工艺、常用夹具的设计方法等内容。
并对各类刀具的特点,金属切削过程及其有关规律,工艺规程的制定,机械加工质量的概念,机械加工精度及其影响因素、装配工艺及其与机械加工工艺的关系,保证装配精度的方法,装配尺寸链的建立,进行了简要的介绍。
本课程在内容方面侧重于基础知识、基础理论与基本分析方法的讲授,在培养实践能力方面着重机械加工技能的基本训练。
使学生能正确地选择刀具与夹具,培养学生“机械加工工艺规程的制定与实施”的能力。
二、教学基本要求(一)知识教学目标1、掌握金属切削的基本原理、刀具几何参数的表示、切削用量的选择原则,熟悉各类刀具的特点,认识金属切削过程及其有关规律。
2、熟悉机床的要紧类型、性能特点及其工艺范围,具有合理选用机床的基本知识。
3、熟悉生产过程的基本概念;掌握工艺路线拟订的原则与步骤及零件加工工艺规程编制的通常方法;4、掌握“六点定位原则”及机械加工中零件的定位基准的选择;5、掌握“工艺尺寸链原理”及加工余量的确定与工艺尺寸链的计算,熟悉机械加工生产率与经济性,并能够进行工艺文件的初步规划。
6、掌握工件在夹具中定位与夹紧的基本原理及方法,掌握各类机床夹具的设计要点。
7、熟悉机械加工质量的概念,机械加工精度及其影响因素、机械加工表面质量及其影响因素。
8、熟悉装配工艺及其与机械加工工艺的关系,掌握保证装配精度的方法,熟悉装配尺寸链的建立,初步掌握装配工艺规程的制订。
机械加工余量标准

机械加工余量标准25EQY —19-19991. 主题内容与适用范围本标准规定了磨削加工的加工余量。
本标准适用于磨削各类材料时的加工余量。
2. 技术内容加工余量表(一)说明:1.二次平面磨削余量乘系数1.52.三次平面磨削余量乘系数23.厚度4以上者单面余量不小于0.5-0.84.橡胶模平板单面余量不小于0.7毛坯加工余量表(二)I:园棒类:(1)的凸模、凹模、凸凹模以及推杆、推销、限制器、托杆、各种螺钉、螺栓、螺塞、螺帽外径必须滚花者。
(毫米)当D <36时并不适应于调头夹加工,在加工单个工件时,应在L 上加夹头量10-15。
(2)凹模,挡料销、肩台须磨加工的凸模或凸凹模等。
当D <36时,不适合调头加工,在加工单个零件时,应加夹头量10-15。
毛坯加工余量表(三)(1)例如:固定板、退料板等。
注:表中的加工余量为最小余量,其最大余量不得超过厂规定标准。
毛坯加工余量表(四)Ⅲ:矩形锻件类:表内的加工余量为最小余量,其最大余量不得超过厂规定标准。
平面、端面磨削加工余量表(五)一、平面二、端面第 3 页共18页注:20-40%如需磨两次的零件,其磨量应适当增加10-20%环形工件磨削加工余量表(六)注:φ50以下,壁厚10以上者,或长度为100-300者,用上限φ50-φ100,壁厚20以下者,或长度为200-500者,用上限φ100以上者,壁厚30以下者,或长度为300-600者,用上限1.30.5φ6以下小孔研磨量表(七)注:本表只适用于淬火件当长度e 小于15毫米时,表内数值应加大20-30%导柱衬套磨削加工余量表(八)镗孔加工余量表(九)附注:当一次镗削时,加工余量应该是粗加工余量加工精加工余量。
第 5 页共18页表7-1 模具常用加工方法的加工余量、加工精度、表面粗糙度第 7 页 共 18页前道工序的加工结果等具体情况而定。
第9 页共18页第 11 页 共 18页第13 页共18页第15 页共18页1. 加工总余量的确定(1)加工总余量和工序余量加工总余量(毛坯余量)—毛坯尺寸与零件图设计尺寸之差。
机械制造基础
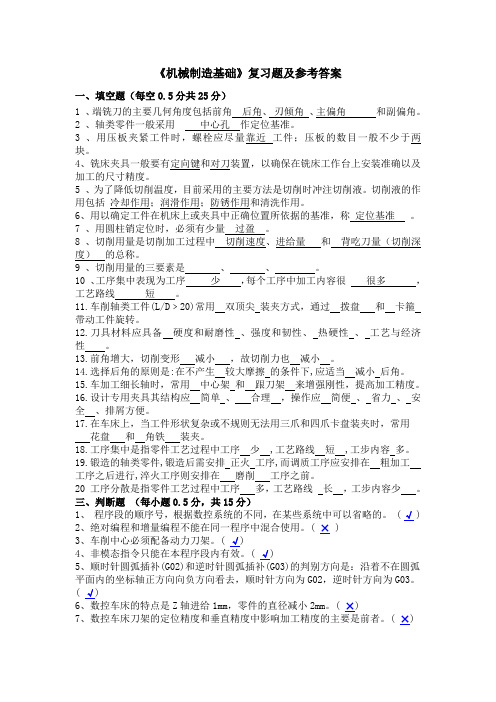
8、数控车床加工球面工件是按照数控系统编程的格式要求,写出相应的圆弧插补程序段。
( √)9、数控车床的刀具功能字T既指定了刀具数,又指定了刀具号。
( ×)10、螺纹指令G32 X41.0 W-43.0 F1.5是以每分钟1.5mm的速度加工螺纹。
( ×)11、车床的进给方式分每分钟进给和每转进给两种,一般可用G94和G95区分。
( √)12、数控车床可以车削直线、斜线、圆弧、公制和英制螺纹、圆柱管螺纹、圆锥螺纹,但是不能车削多头螺纹。
( ×)13、固定循环是预先给定一系列操作,用来控制机床的位移或主轴运转。
( √)14、数控车床的刀具补偿功能有刀尖半径补偿与刀具位置补偿。
( √)15、外圆粗车循环方式适合于加工棒料毛坯除去较大余量的切削。
( √)16、编制数控加工程序时一般以机床坐标系作为编程的坐标系。
( ×)17、一个主程序中只能有一个子程序。
(×)18、子程序的编写方式必须是增量方式。
( ×)19、G00、G01指令都能使机床坐标轴准确到位,因此它们都是插补指令( ×)20、当数控加工程序编制完成后即可进行正式加工。
( ×)21 、刀具前角越大,切屑越不易流出,切削力越大,但刀具的强度越高。
(×)22 、定位误差包括工艺误差和设计误差。
(×)23 、在批量生产的情况下,用直接找正装夹工件比较合适。
(×)24 、刀具磨损分为初期磨损、正常磨损、急剧磨损三种形式。
(×)25 、在加工过程中形成的相互有关的封闭尺寸图形,称为工艺尺寸链图。
(√)26 、为了防止工件变形,夹紧部位要与支承对应,不能在工件悬空处夹紧。
(√)27 、切削中,对切削力影响较小的是前角和主偏角。
(×)28 、同一工件,无论用数控机床加工还是用普通机床加工,其工序都一样。
(×)29 、工件在夹具中与各定位元件接触,虽然没有夹紧尚可移动,但由于其已取造得确定的位置,所以可以认为工件已定位。
《机械制造工艺学》课程标准

《机械制造工艺学》课程标准一、课程基本信息二、课程定位与作用《机械制造工艺学》是机械设计制造及其自动化专业的一门综合性专业课。
课程归纳总结机械制造工艺的有关科学理论与实践,探索解决工艺过程中遇到的实际问题,其作用为培养高素质机制专业人才从事机械加工工艺设计、机械装配工艺设计等工作岗位所必须的实用技能。
三、课程教学目标及要求《机械制造工艺学》课程教学基本要求:通过本课程的学习,使学生掌握机械制造过程中有关工艺问题的基本理论和方法,使学生初步具有分析和解决工艺等制造技术问题的能力及自学工艺理论和新工艺、新技术的能力。
(一)知识目标1)掌握机械加工工艺规程制定的有关理论和方法;2)掌握保证零件加工质量有关理论和方法;3)理解典型零件的机械加工工艺规程;4)掌握装配工艺规程的制定方法;5)了解现代制造技术。
(二)职业技术能力目标1)能制定中等复杂程度零件的机械加工工艺规程;2)分析影响零件加工精度的有关因素,提出相应措施保证零件加工精度;五、主要教学内容及要求:(注明:●代表重点★代表难点)第一部分教学内容(一)机械加工工艺规程的制定和工艺尺寸链 24学时[主要内容]1. 基本概念●2. 零件结构工艺性分析3.确定毛坯●4.定位基准的选择●5.工艺路线的拟定●6. 确定加工余量、工序尺寸及其公差7. 时间定额和提高劳动生产率的工艺途径8. 工艺过程的技术经济分析★9. 工艺尺寸链[教学要求]:1. 了解机械加工工艺过程基本概念,掌握制定机械加工工艺规程内容、步骤;2. 会分析零件结构工艺性的好坏,掌握零件毛坯的选择方法;3. 掌握工艺规程制定中的主要问题和内容确定;4. 理解工艺尺寸链的概念,掌握工艺尺寸链极值法解算公式并能应用其解决常见工艺尺寸链的问题;5. 了解机械加工生产率和经济性的基本知识。
(二)机械加工精度 8学时[主要内容]1. 基本概念●2. 工艺系统的几何误差●3. 工艺系统的受力变形●4. 工艺系统的受热变形5. 工艺系统的残余应力引起的加工误差★6. 加工误差的统计分析方法7. 提高和保证加工精度的方法和途径[教学要求]:1. 理解精度、误差、工艺系统及原始误差的概念;2. 掌握工艺系统的几何误差;3. 掌握工艺系统受力变形对加工精度的影响;4. 掌握工艺系统的热源及工艺系统热变形的影响;5. 理解工件残余内应力的概念及产生过程和消除方法;6. 了解提高加工精度的主要途径,能够对实例进行加工误差分析。
机械加工工艺过程的组成

一.机械加工工艺过程的组成1.工序——工人,在工作地对工件所连续完成的工艺过程。
2.安装——经一次装夹后所完成的工序内容装夹——定位——加工前工件在机床或夹具上占据一正确的位置夹紧——使正确位置不发生变化增加安装误差增加装夹时间——应尽量减少安装次数3.工位——工件与工装可动部分相对工装固定部分所占的位置多工位加工——提高生产率、保证加工面间的相互位置精度4.工步——加工表面和加工工具不变条件下所完成的工艺过程一次安装中连续进行的若干相同的工步→1个工步用几把不同刀具或复合刀具加工→复合工步5.走刀——每进行一次切削——1次走刀二.工艺规程1.工艺规程的作用——①指导生产②组织生产和管理生产③新建、扩建或改建工厂及车间2.工艺规程的设计原则——①技术上的先进性②经济上的合理性③良好的劳动条件§机械加工工艺规程设计一.零件的工艺分析1.零件技术要求分析①加工表面的尺寸精度②主要加工表面的形状精度③主要加工表面之间的相互位置精度④各加工表面粗糙度以及表面质量方面的其他要求⑤热处理要求及其它技术要求(如动平衡等)。
1)零件的视图、技术要求是否齐全——主要技术要求和加工关键2)零件图所规定的加工要求是否合理3)零件的选材是否恰当,热处理要求是否合理2.零件结构及其工艺性分析①结构组成——内外圆柱面、圆锥面、平面、螺旋面、齿形面、成形面②结构组合——轴类、套筒类、盘环类、叉架类、箱体类★分析刚度及其方向③结构工艺性——保证使用要求的前提下,能否以高生产率和低成本制造二.毛坯的选择1.毛坯种类的选择铸件、锻件、焊接件、型材、冲压件、粉末冶金件和工程塑料件2.确定毛坯的形状和尺寸——尽量与零件接近毛坯加工余量——毛坯制造尺寸与零件相应尺寸的差值——加工总余量毛坯公差——毛坯制造尺寸的公差①为工件安装稳定,有些毛坯需工艺凸台②为加工方便,一些零件作整体毛坯——半圆形零件→合成整圆小零件(垫圈)→合成1件3.选择毛坯时应考虑的问题①零件的材料及力学性能要求——铸铁、有色金属→铸重要件→锻②零件的结构形状与尺寸——复杂件→铸小台阶轴→棒料,大台阶轴→锻③生产纲领的大小——大批量→先进方法④现有生产条件⑤采用新工艺、新技术、新材料三.定位基准选择1.基准的概念——确定其他点、线、面的位置所依据的点、线、面(1)设计基准——零件图上的基准——尺寸→尺寸线的起点相互位置→基准符号(2)工艺基准——工艺中用的基准——①工序基准②定位基准③测量基准④装配基准2.定位基准的选择——毛坯面定位→粗基准已加工面定位→精基准(1)精基准的选择——可靠保证主要加工表面间的相互位置精度1)基准重合原则——选设计基准为定位基准2)基准统一原则——尽可能在多数工序中用一组精基准定位3)定位稳定准确,简单方便的原则——选面大、精度高的面为精基准4)互为基准原则——为加工余量均匀,位置精度高——反复加工5)自为基准原则——要求余量小而均匀——选加工面本身为精基准●辅助基准——人为制造的基准——工艺需要而作的工艺凸台、中心孔提高精度——一面两孔定位(2)粗基准选择——可靠方便地加工精基准1)保证不加工面与加工面间的位置关系——选择不加工面作粗基准2)定位稳定可靠,简单方便——选大面、平整面,无缺陷3)合理分配各面加工余量——①应保证各加工面有足够的余量②某些重要面使其加工余量均匀4)同一方向上的粗基准原则上只允许使用一次●基准选择——具体情况具体分析,综合考虑,灵活运用,正确选择【例】选择支架零件的精基准和粗基准◆零件分析——加工面——底面、顶面、φ16H7孔、2-φ10孔、直槽、圆弧槽主要加工要求——φ16H7、对称度0.1、32±0.1、28±0.1◆基准分析——底面——顶面、φ16H7孔高度方向的设计基准φ16H7孔轴线——直槽、圆弧槽、2-φ10孔的设计基准。
机械制造技术基础--习题

《机械制造技术基础》思考题与习题0.1什么是制造和制造技术?0.2机械制造业在国民经济中有何地位?为什么说机械制造业是国民经济的基础?0.3如何理解制造系统的物料流、能量流和信息流?0.4什么是机械制造工艺过程?机械制造工艺过程主要包括哪些内容?0.5什么是生产纲领,如何确定企业的生产纲领?0.6什么是生产类型?如何划分生产类型?各生产类型各有什么工艺特点?0.7企业组织产品的生产有几种模式?各有什么特点?0.8按照加工过程中质量m的变化,制造工艺方法可分为几种类型?并说明各类方法的应用范围和工艺特点。
1.1解释下列机床型号的含义:X6132,CG6125B,Z3040,MG1432,Y3150E,T6112。
1.2机床的主要技术参数有哪些?1.3各类机床中能加工外圆、孔及平面的机床有哪些?它们的适用范围有何区别?1.4列出CA6140型卧式车床最高和最低转速的传动路线表达式。
1.5何谓外联传动链?何谓内联传动链?其本质区别是什么?1.6写出在CA6140型卧式车床上车削米制螺纹P=3mm,k=1的传动路线表达式。
1.7简述数控机床的特点、分类、及组成。
说明开环、闭环、半闭环伺服系统的区别及适用场合。
1.8简述刀具材料应具备的基本要求和刀具材料的种类。
1.9常用的高速钢刀具材料有哪几种?适用的范围是什么? 硬质合金的牌号种类很多,它们各有何特点?试述陶瓷、金刚石、立方氮化硼刀具材料的优缺点及适用的场合。
1.10刀具正交平面参考系中,各参考平面Pr、Ps、Po及刀具角度γo、αo、κr、λs是如何定义的?γo和λs、kr和αo、κr和λs分别确定了哪些刀具构成要素(切削部分)在空间的位置?1.11已知刀具角度γo=30°、αo=10°、αo′=8°、κr=45°、κr′=15°、λs=-30°,请绘出刀具切削部分。
1.12镗削内孔时,如果刀具安装(刀尖)低于机床主轴中心线,在不考虑合成运动的前提下,试分析刀具工作前、后角的变化情况.1.13外圆车削直径为80mm,长度180mm的45钢棒料,在机床CA6140上选用的切削用量为a P=4mm,f=0.5mm/r,n =240r/min。
汽车专业:汽车制造工艺学试卷

汽车专业:汽车制造工艺学试卷1、问答题精加工阶段的主要任务是什么?正确答案:使各主要表面达到图纸规定的质量要求。
2、问答?在小轴上铣槽,保证尺寸H和L 。
指出工件定位应限制的自由度。
正确答案:3、填空题表面残余拉应力会()疲劳裂纹的扩展。
正确答案:加剧4、判断题辅助支承在每次卸下工件后,必须松开,装上工件后再调整和锁紧。
正确答案:对5、判断题单件、小批生产多采用工序集中原则。
正确答案:对6、填空题主轴回转作()及漂移时,所镗出的孔是椭圆形。
正确答案:纯径向跳动7、问答题试述表面粗糙度对零件的使用性能有何影响?正确答案:对耐磨性;耐疲劳性;抗腐蚀性;零件配合质量有影响。
8、判断题普通车床导轨在垂直面内的直线度误差对加工精度影响不大。
正确答案:对9、问答?下图所示零件,各平面和孔已加工完毕,现在工件上铣槽,试:⑴指出必须限制的自由度有哪些;⑵选择定位基准面;⑶选择定位元件,并指出各定位元件限制的自由度数目。
正确答案:⑴必须限制的自由度:⑵选择定位基准面:第一基准:工件底平面A;第二基准:工件上侧面B;第三基准C:孔(允许不选)⑶选择定位元件:第一基准采用支承板定位(限制了3个自由度);第二基准采用两个支承销定位(限制了2个自由度);第三基准采用削边销定位(限制了1个自由度)。
10、判断题加工误差主要由刀具,工件的安装造成。
正确答案:错11、判断题增加零件间隙可以提高机床刚度。
正确答案:错12、判断题第一类自由度必须限制,而第二类自由度无关紧要。
正确答案:错13、填空题工艺系统的变形包括()、()、()。
正确答案:机床夹具变形;刀具变形;工件变形14、填空题加工原理误差是指由于采用了近似的()或近似的()进行加工所产生的误差。
正确答案:加工方法;成形方法15、填空题零件的加工精度包含尺寸精度,形状精度和()三方面的内容。
正确答案:位置精度16、判断题符合产品标准的刀具不会有误差。
正确答案:错17、填空题根据误差出现的规律不同可以分为系统误差、()。
14-4 加工余量、工序间尺寸及公差的确定
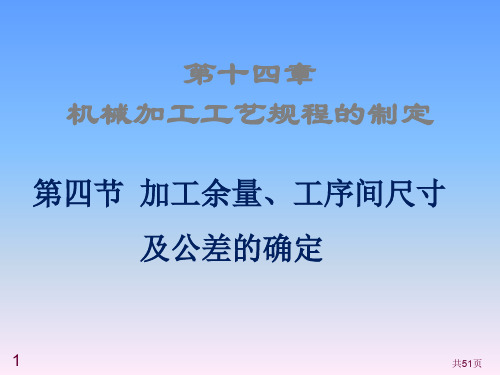
TZ = Zmax – Zmin=Tb+Ta
TZ :工序余量公差; Zmax :工序最大余量;
本道工序基本尺寸
Zmin:工序最小余量; Tb:本道工序的工序尺寸公差;
上道工序基本尺寸
Ta:上道工序的工序尺寸公差。
12
加工方向
共51页
工序尺寸及偏差
一般情况下,工序尺寸的公差按“入体原 则”标注。即 ——对被包容尺寸(轴的外径、实际长、宽、 高),其最大加工尺寸就是基本尺寸,上偏差 为零。 ——对包容尺寸(孔的直径、槽的宽度),其最 小加工尺寸就是基本尺寸,下偏差为零。 ——毛坯尺寸公差按双向对称偏差形式标注。
机床夹具的选择主要考虑生产类型。 (1)单件小批量生产应尽量选用通用夹具; (2)大批大量生产时,应采用高生产效率的专 用机床夹具;
此外,夹具的精度应与零件的加工精度相适应。
42
共51页
3.刀具的选择
刀具的选择主要取决于: 工序所采用的加工方法 加工表面的尺寸大小 工件材料 要求的加工精度 表面粗糙度 生产率 经济性
二、加工余量的确定
3. 经验法
由一些有经验的工程技术人员或工人根 据经验确定加工余量的大小。由经验法 确定的加工余量往往偏大,这主要是因 为主观上怕出废品的缘故。这种方法多 在单件小批生产中采用。
31
共51页
三、工序尺寸与公差的确定
生产上绝大部分加工面都是在基准重合(工艺基准和设计基 准重合)的情况下进行加工。现介绍如下: 1. 确定各加工工序的加工余量
6
共51页
双边余量
2Zi = li–1 – li
式中
Zi——本道工序的工序余量; li——本道工序的基本尺寸; li–1——上道工序的基本尺寸。
机械制造工艺学第三版王先奎习题解答(1-2)

A
25
46 32 12 15
莫式6号 0.008 A-B
1.6 12±0.015 φ89f6
习图1-1 CA6140车床主轴结构
2
MM工T序号
习表1-1 CA6140车床主轴加工工艺过程
工序名称及内容
定位基准
设备
1 锻造(模锻)
立式精锻机
2 热处理(正火)
3 铣端面钻中心孔
毛坯外圆
铣钻联合机床
4 粗车外圆
2)精基准,两种选择:
R
Ⅰ Ⅱ
①选择主轴箱体安装面M和N;
l1 l2 l3
②选择顶面R及顶面2个工艺孔。
详见2.7.2节。
Ⅲ
l5 l4
M
N
图2-73
9
MMT 2-6 试分别选择图2-74所示各零件的粗、精基准(其中,图2-74a为齿轮
零件简图,毛坯为模锻件;图2-74 b为液压缸体零件简图,毛坯为铸件; 图2-74c为飞轮简图,毛坯为铸件)
锥堵顶尖孔
花键铣床
17 铣键槽
φ80h5外圆
立式铣床
18 车三处螺纹(与螺母配车)
锥堵顶尖孔
卧式车床
19 精磨各外圆及E、F两端面
锥堵顶尖孔
外圆磨床
20 粗、精磨两处1∶12外锥面、D端面及短锥面 锥堵顶尖孔
专用组合磨床
21 精磨大端莫氏6号内锥孔(卸堵,涂色法检查) 主轴颈及φ75h5外圆 专用锥孔磨床
顶尖孔
多刀半自动车床
5 热处理(调质220-240HBS)
6 半精车大端各部
顶尖孔
卧式车床
7 仿形车小端各部外圆
顶尖孔
仿形车床
8 钻通孔
两端支承轴颈
机械制造工艺学复习笔记

1、工件的安装方式 :(1)直接找正安装(2)划线找正安装(3)采用夹具安装2、工艺装备:指为实现工艺过程所需的各种刃具、夹具、量具、模具、辅具、工位器具等的总称3、粗基准选择原则?精基准选择原则?粗基准:1.保证相互位置要求的原则;2.保证加工表面加工余量合理分配的原则;3.便于工件装夹的原则;4.粗基准一般不得重复使用的原则精基准:1.基准重合原则;2.统一基准原则;3.互为基准原则;4.自为基准原则;5.便于装夹原则工艺顺序按排有哪些原则?{ 1.先加工基准面,再加工其他表面;2.一半情况下,先加工表面,后加工孔;3.先加工主要表面,后加工次要表面;4.先安排粗加工工序,后安排精加工工序 }4、装配精度一般包括哪些内容?{1.相互位置精度;2.相互运动精度;3.相互配合精度}5、机床夹具的组成及功用?组成部分有:1.定位元件或装置.2.刀具导向元件或装置.3.夹紧元件或装置.4.联接元件5.夹具体6.其它元件或装置..主要功能1.保证加工质量2.提高生产效率.3.扩大机床工艺范围4.减轻工人劳动强度保证生产安全.}6、对工件夹紧装置设计的基本要求。
{1.在夹紧过程中应能保持工件定位时所获得的正确位置. 2.夹紧力大小适当,夹紧机构应能保证在加工过程中工件不产生松动或振动,同时又要避免工件产生不适当的变形和表面损伤,夹紧机构一般应有自锁作用3.夹紧装置应操作方便,省力,安全。
4.夹紧装置的复杂程度和自动化程度应与生产批量和生产方式相适应。
结构设计应力求简单,紧凑并尽量采用标准化元件7、夹紧力确定的三要素?夹紧力方向和作用点选择分别有哪些原则?{ 大小方向作用点夹紧力方向的选择一般应遵循以下原则: 1、夹紧力的作用方向应有利于工件的准确定位,而不破坏定位,为此一般要求主要夹紧力垂直指向定位面 2、夹紧力作用方向应尽量与工件刚度大的方向相一致,以减小工件夹紧变形 3、夹紧力作用方向应尽量与切削力、工件重力方向一致,以减小所需夹紧力夹紧力作用点选择一般原则:1、夹紧力作用点应正对支承元件所形成的支承面内,以保证工件已获得的定位不变 2、夹紧力作用点应处于刚性较好的部位以减小工件夹紧变形3、夹紧力作用点应尽量靠近加工表面以减小切削力对工件造成的翻转力矩}8、机械制造工艺学的研究对象主要是机械加工中的三大问题?加工质量、生产率、经济性设计装配工艺规程的原则:(1)保证装配质量;(2)尽量减少钳工装配工作量;(3)尽量缩短装配周期;4)尽量减少装配车间面积。
确定各工序的加工余量

粗 车 IT12~13 Ra 10~80
半 精 车 IT8~11 Ra 2.5~10 精 拉 IT6~9 Ra 0.32~2.5
精 车 IT6~8 Ra 1.25~5
粗 拉 IT10~11 Ra 5~20
平面典型加工工艺路线
• ②决定加工方法时要考虑被加工材料的性质。例如,淬火 钢用磨削的方法加工;而有色金属则磨削困难,一般采用 金刚镗或高速精密车削的方法进行精加工。 • ③选择加工方法要考虑到生产类型,即要考虑生产率和经 济性的问题。在大批、大量生产中可采用专用的高效率设 备和专用工艺装备。例如,平面和孔可用拉削加工,轴类 零件可采用半自动液压仿型车床加工,盘类或套类零件可 用单能车床加工等。甚至在大批、大量生产中可以从根本 上改变毛坯的形态,大大减少切削加工的工作量。例如, 用粉末冶金制造的油泵齿轮,用失蜡浇注制造柴油机上的 小尺寸零件等。在单件小批生产中,就采用通用设备、通 用工艺装备及一般的加工方法。提高单件小批生产的生产 率亦是目前机械制造工艺的研究课题之一。例如,在车床 上装液压仿型刀架,采用数控车床或采用成组加工方法, 单件试制新产品时,甚至采用加工中心机床等。
• (5)应能使工作装夹稳定可靠、夹具简单
• 一般常采用面积大、精度较高和粗糙度较 低的表面为精基准。 • 加工箱体类和支架类零件时常选用装配基 准为精基准,因为装配基准多数面积大、 装夹稳定、方便,设计夹具也较简单。 •
• 上述有关粗、精基准选择原则中的每一项, 只说明某一方面问题,在实际应用中,有 时不能同时兼顾。因此要根据零件的生产 类型及具体的生产条件,并结合整个的工 艺路线进行全面考虑,抓住主要矛盾,灵 活运用上述原则,正确选择粗、精基准。
• 1、粗基准的选择 • 在零件加工过程的第一道工序,定位基准 必然是毛坯表面,即粗基准。选择粗基准 时应从以下几个方面考虑:
40加工余量的确定 - 40加工余量的确定

除淬火钢外的各种钢 材,毛坯上已有铸出或 锻出的孔
主要用于淬火钢,不 宜用于有色金属
主要用于精度要求高 的有色金属
钻→(扩)→粗铰→精铰→珩磨 └→拉→珩磨 粗镗→半精镗→精镗→珩磨
IT6~7 IT6~7 IT6~7
0.025~0.20 0.025~0.20 0.025~0.20
精度要求很高的孔,
机械制造 技术基础
第五章 机械加工工艺规程的制定
第五章 机械加工工艺规程的制定
机械制造 技术基础
5.5 加工余量的确定
5.5.1 加工余量的确定
为了达到零件图上某表面的精度和粗糙度值要求,需要从 其毛坯表面上切去全部多余的金属层,这一金属层的总厚度称 为该表面的加工总余量。每一工序所切除的金属层厚度称为工 序余量。
若以研磨代替珩磨,精 度 可 达 IT6 以 上 , Ra 可 减小到0.l~0.01μm
第五章 机械加工工艺规程的制定
机械制造 技术基础
5.4 工艺路线的拟定
表5.9 平面加工方法及其经济精度
加工方案
粗车 └→半精车 │ └→精车 └────→磨 粗刨(或粗铣) └→精刨(或精铣)
└→刮研 粗刨(或粗铣)→精刨(或精铣)→宽 刃精刨 粗刨(或粗铣)→精刨(或精铣)→磨
(5.2) (5.3)
图5.12(b)为内表面(包容面)加工,则有:
Zb=Lb-La
(5.4)
Zbmax=Lbmax-Lamin (5.5)
Zbmin=Lbmin-Lamax (5.6)
从图5.12(a)、(b)可看出,上工序的尺寸 公差将影响本工序基本余量和最大余量的数值。
第五章 机械加工工艺规程的制定
第五章 机械加工工艺规程的制定
机械加工工艺-加工余量、工序尺寸及公差
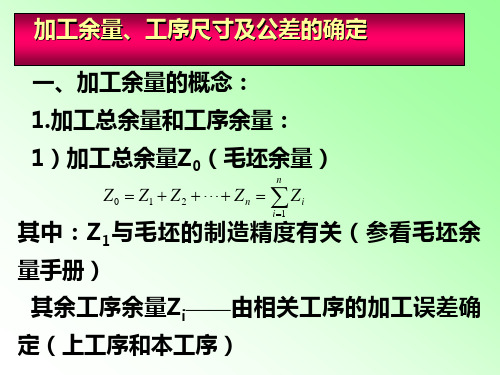
(一)设计 1、合理的结构工艺性、加工精度、表面
粗糙等。 2、零件、部件、产品的三化程度(通用、
标准、系列) (二)先进的工艺及设备
1、毛坯 2、机加工 3、装配
(三)先进的管理:计划、准备、服务、技术、
质量、经济分析等。
提高机加工生产率的工艺途径:
(一)缩短t基 1、(V、F、ap)↑。 2、多刀、多刃、及单刀多件等。
加工余量、工序尺寸及公差的确定
一、加工余量的概念: 1.加工总余量和工序余量: 1)加工总余量Z0(毛坯余量)
n
Z0 Z1 Z2 Zn Zi i 1
其中:Z1与毛坯的制造精度有关(参看毛坯余 量手册)
其余工序余量Zi——由相关工序的加工误差确 定(上工序和本工序)
2)工序余量Zi——相邻两工序基本尺寸之差;
求:本工序工序尺寸L2(渗碳深度) 分析:渗碳层保留深度L0 —单边值(图面尺寸)
渗碳深度L2—单边值。 按尺寸链图,代入公式求解得:L2=0.7+0.025
+0.008
(四)、余量校核 各工序中加工余量由查表及经验确定。 因为各工序尺寸的公差存在,实际余量是变化 的。 例图1-49,
1、工艺路线 1)精车A面,由B处切断。 2)以A面定位,精车B面。 3)以B面定位,磨A面。 4)以A面定位,磨B面。
三、用图表法确定工序尺寸及余量 适用于当零件同一方向尺寸较多的复杂情况。 如:工序多,工序基准转换多,工序中基准不 重合需用尺寸链计算,公差,余量确定复杂。 步骤: (一)绘制加工过程尺寸联系图
1、画出工件简图,标注相关设计尺寸。 2、按加工工序列表填写工艺过程,画加工符 号(箭头等)。 (二)工艺尺寸链查找
尺寸链中封闭环只有一个,用L0表示。 工艺尺寸链中的封闭环的定义见P.53倒10行。
机械制造工艺题库

一、填空题1、机械制造工艺学的研究对象主要是机械加工中的三大问题即(加工质量),(生产率),(经济性)。
2、机械加工工艺系统包括(机床),(夹具),(工件),(刀具)等四个方面。
3、工艺过程划分加工阶段的原因是:(提高加工质量),(合理利用机床),(安排热处理工序),(及早发现毛坯缺陷)。
4、在机械制造中,通常将生产方式划分为(单件小批),(中批),(大批大量生产)三种类型。
5、确定毛坯加工余量的方法有三种即(计算法),(查表法),(经验估计法)。
大批量生产用(计算法)。
6、根据作用的不同,基准通常可分为(设计基准)和(工艺基准)两大类,定位基准属于(工艺基准)。
7、为了保证加工质量,安排机加工顺序的原则是(先面后孔),(先粗后精),(先主后次),(先基面后其它)。
8、选择定位粗基准要考虑(1)使各加工面都有一定的和比较均匀的(加工余量);(2)保证加工面与非加工面的(相互位置精度)。
9、零件的加工精度包括三方面的内容即(尺寸精度),(几何形状精度),(表面相互位置精度)。
10、零件表层的机械物理性质包括(表面冷硬),(表层残余应力),(表层金相组织)。
11、刀具磨损属于(变值系统误差)误差,可以通过计算后输入(等值异号的误差)来补偿。
12、零件的表面质量包括(表面粗糙度及波度),(表面冷硬),(表层残余应力)、(表层金相组织)。
13、工艺系统的振动分为两大类即(强迫振动)(自激振动),其中振幅随切削用量而变的是(自激振动)。
14、切削加工后,引起表面残余应力的主要原因有(塑性变形),(温度变化),(金相组织变化)。
15、精密机床加工精度零件为了减少热变形,加工前应具备两条:(热平衡),(恒温室)。
16、弯曲的轴进行冷校直后,原来凸出处会产生(拉)应力,原来凹下处产生(压)应力。
17、磨削长薄片状工件时若在长度方向两端顶住,在热影响下工件发生(上凸)的变形,冷后具有(下凹)的形状误差。
18、解释自激振动的原理主要有两条(再生振动),(振型耦合)。
机械制造基础教学大纲

机械制造基础教学大纲内部编号:(YUUT-TBBY-MMUT-URRUY-UOOY-DBUYI-0128)《机械制造基础》课程教学大纲一、课程简介(二)课程名称:机械制造基础(Machinery Manufacturing Base)(三)修读对象:机械设计制造及其自动化(三)总学时数:63学时(理论54学时,实验9学时)(四)修课学分:3.5学分(五)考核方式:考试(笔试占80% + 平时成绩占20% )(六)相关课程:《金工实习》、《公差配合与测量技术》、《工程材料》、《材料力学》(七)内容提要:机械制造基础是一门理论性、技术性、实践性、综合性很强的专业基础课。
课程以传统与现代制造技术结合为内容,以加工原理为基础,方法与工艺为主线,质量、效率、经济性三者之间的协调发展为目标,主要讲授零件毛坯的制造方法、工艺规程设计、机床夹具设计、机械加工精度与控制、机械加工表面质量及其控制、机器的装配工艺过程设计、先进制造技术简介等内容。
二、教学目的和教学方法1、教学目的通过本课程学习,使学生掌握机械制造的基本原理和方法,掌握零件毛坯制造方法的选择、工艺规程设计、加工质量分析与控制、零件结构工艺性和机器装配工艺性设计等方面的基本能力,了解先进制造技术与生产模式。
为学生将来从事机械制造工程技术工作,奠定扎实的专业知识和能力基础。
2、教学方法结合课程特点,紧扣“厚基础、重应用、强能力、高素质”教学目标,以基础理论为重心、工程应用为根本,采取课堂教学、现场教学、实验教学、网上辅导、课外练习、课程设计等教学形式,运用叙述式与案例式讲授基本内容及解释基本原理;运用启发式和探究式激发学生的学习热情;运用任务式和练习式明确知识的价值及巩固理解和记忆。
且教与学相结合,老师只讲重点难点(约70%),学生自学易学点(约30%),共同完成教学任务。
三、理论与实验教学学时分配四、选用教材和主要教学参考书教材:[1]《金属工艺学》(上),邓文英主编,高等教育出版社.2009[2]《机械制造工艺学》(第3版),王先逵主编,机械工业出版社.2013参考书:[1]《机械制造技术基础》,周宏甫编着,高等教育出版社[2]《机械制造工艺学》,常同立,杨家武、佟志忠编着,清华大学出版社五、理论教学内容(一)第一章金属材料及其毛坯成形基础教学时数:10学时(理论8学时,视频2学时)主要内容:金属材料性能,铸造工艺,金属塑性加工工艺,焊接工艺。
机械制造工艺学》试题库及答案
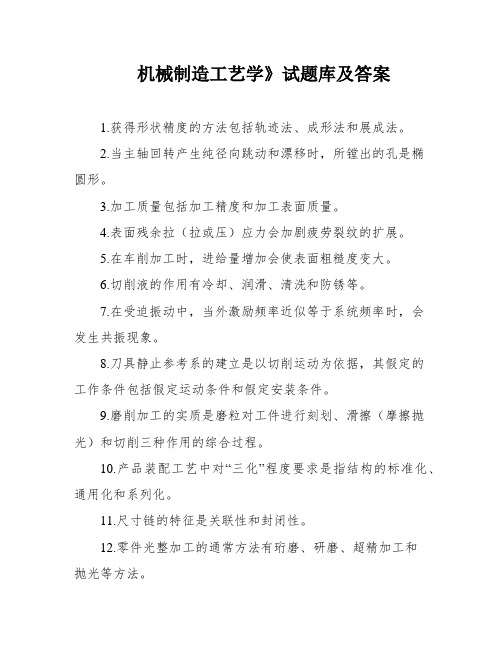
机械制造工艺学》试题库及答案1.获得形状精度的方法包括轨迹法、成形法和展成法。
2.当主轴回转产生纯径向跳动和漂移时,所镗出的孔是椭圆形。
3.加工质量包括加工精度和加工表面质量。
4.表面残余拉(拉或压)应力会加剧疲劳裂纹的扩展。
5.在车削加工时,进给量增加会使表面粗糙度变大。
6.切削液的作用有冷却、润滑、清洗和防锈等。
7.在受迫振动中,当外激励频率近似等于系统频率时,会发生共振现象。
8.刀具静止参考系的建立是以切削运动为依据,其假定的工作条件包括假定运动条件和假定安装条件。
9.磨削加工的实质是磨粒对工件进行刻划、滑擦(摩擦抛光)和切削三种作用的综合过程。
10.产品装配工艺中对“三化”程度要求是指结构的标准化、通用化和系列化。
11.尺寸链的特征是关联性和封闭性。
12.零件光整加工的通常方法有珩磨、研磨、超精加工和抛光等方法。
13.机械加工工艺规程实际上就是指规定零件机械加工工艺过程和操作方法等的工艺文件。
14.工艺过程是指生产过程中,直接改变生产对象形状、尺寸、相对位置及性质的过程。
15.零件的几何精度、表面质量、物理机械性能是评定机器零件质量的主要指标。
16.加工经济精度是指在正常加工条件下(采用符合标准的设备、工艺装备和标准技术等级的工人,不延长加工时间)所能保证的加工精度。
17.工艺系统的几何误差主要包括加工方法的原理误差、制造和磨损所产生的机床几何误差和传动误差、调整误差、工件的安装误差、刀具、夹具和量具的制造误差与磨损引起。
18.轴类零件加工中常用两端中心孔作为统一的定位基准。
19.零件的加工误差越小,加工精度就越高。
20.粗加工阶段的主要任务是获得高的生产率。
21.工艺系统的几何误差包括加工方法的原理误差、制造和磨损所产生的机床几何误差和传动误差、调整误差、刀具、夹具和量具的制造误差、工件的安装误差。
22.精加工阶段的主要任务是使各主要表面达到图纸规定的质量要求。
23.零件的加工误差值越小,加工精度就越高。
机械制造工艺学习题及答案填空选择
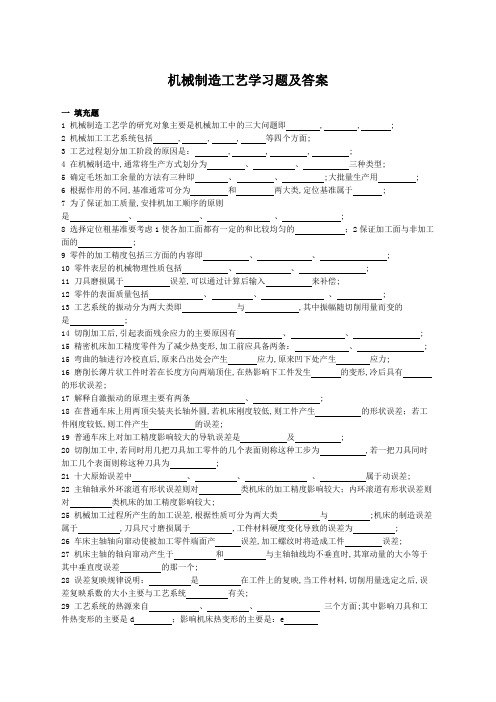
机械制造工艺学习题及答案一填充题1 机械制造工艺学的研究对象主要是机械加工中的三大问题即 , , ;2 机械加工工艺系统包括 , , , 等四个方面;3 工艺过程划分加工阶段的原因是: , , , ;4 在机械制造中,通常将生产方式划分为、、三种类型;5 确定毛坯加工余量的方法有三种即、、 ;大批量生产用 ;6 根据作用的不同,基准通常可分为和两大类,定位基准属于 ;7 为了保证加工质量,安排机加工顺序的原则是、、、 ;8 选择定位粗基准要考虑1使各加工面都有一定的和比较均匀的;2保证加工面与非加工面的 ;9 零件的加工精度包括三方面的内容即、、 ;10 零件表层的机械物理性质包括、、 ;11 刀具磨损属于误差,可以通过计算后输入来补偿;12 零件的表面质量包括、、、 ;13 工艺系统的振动分为两大类即与 ,其中振幅随切削用量而变的是 ;14 切削加工后,引起表面残余应力的主要原因有、、 ;15 精密机床加工精度零件为了减少热变形,加工前应具备两条:、 ;15 弯曲的轴进行冷校直后,原来凸出处会产生应力,原来凹下处产生应力;16 磨削长薄片状工件时若在长度方向两端顶住,在热影响下工件发生的变形,冷后具有的形状误差;17 解释自激振动的原理主要有两条、 ;18 在普通车床上用两顶尖装夹长轴外圆,若机床刚度较低,则工件产生的形状误差;若工件刚度较低,则工件产生的误差;19 普通车床上对加工精度影响较大的导轨误差是及 ;20 切削加工中,若同时用几把刀具加工零件的几个表面则称这种工步为 ,若一把刀具同时加工几个表面则称这种刀具为 ;21 十大原始误差中、、、属于动误差;22 主轴轴承外环滚道有形状误差则对类机床的加工精度影响较大;内环滚道有形状误差则对类机床的加工精度影响较大;25 机械加工过程所产生的加工误差,根据性质可分为两大类与 ;机床的制造误差属于 ,刀具尺寸磨损属于 ,工件材料硬度变化导致的误差为 ;26 车床主轴轴向窜动使被加工零件端面产误差,加工螺纹时将造成工件误差;27 机床主轴的轴向窜动产生于和与主轴轴线均不垂直时,其窜动量的大小等于其中垂直度误差的那一个;28 误差复映规律说明:是在工件上的复映,当工件材料,切削用量选定之后,误差复映系数的大小主要与工艺系统有关;29 工艺系统的热源来自、、三个方面;其中影响刀具和工件热变形的主要是d ;影响机床热变形的主要是:e30 为了保证细长轴的加工精度,常采用4点措施:、、、 ;31 机床刚度是刀具位置的函数,一般以刀具在位置的刚度值作为机床的平均刚度,测定机床刚度的方法有法与法;32 机械加工中获得尺寸精度的方法有四种、、、 ;33 光整加工常用的方法有四种即、、、 ;其中既能提高尺寸精度又能减少表面粗糙度的是和 ;34 提高机床传动链精度的措施是 ; 35 剃齿能提高精度 ,减少 ;但不能提高精度,因此剃前加工以加工为好;36 滚齿时影响齿轮运动精度的主要机床精度 , ;37 选择定位粗基准要考虑1使各加工面都有一定的和比较均匀的;2保证加工面与非加工面的 ;38 误差统计分析法中常用的有、 ;其中能平行指导生产过程的是 ;39 在X---R点图中,若点在X点图控制界内,在R点图控制界外,则说明机床好大,建议找出的原因;若点在X点图控制界外,而在R点图控制界内,则说明机床和不稳, 较小,建议调整机床使与重合;40 达到装配精度的方法有、、、、 ;41 保证装配精度的修配法中,选择修配环的原则是、、 ;42 使用辅助支承的目的是为了 ,它不起作用;43 形成表面压应力的方法有:、、、、、 ;44 X均值点图有连续大于7点的上升趋势,说明工艺系统存在着明显的误差;当点子分布在中线一侧过多时说明存在着误差;45 加工深孔的钻头有、、、、 ;46 零件图上进行尺寸标注时有、、 3种类型,正确的方法是 ;47 尺寸标注的步骤是:、、、、 ;48 夹具总图上应标注的尺寸及公差有:、、、、 ;二、选择题1 整体式箱体时应采用的粗基准是:a.顶面;b.主轴承孔;c.底面;d.侧面;2 中批量生产中用以确定机加工余量的方法是:a.查表法;b.计算法;c.经验估算法3 车床主轴产生轴向窜动,其原因可能是:a.主轴承端面跳动量大;b.主轴轴肩端面跳动量大;b.c.两者都有较大的端面跳动量;d.主轴后端紧固螺母松动;4 用三爪卡盘夹持镗削工件短孔,产生了倒锥,其原因可能是:a.刀具磨损b.工件热变形c.机床导轨误差d.床头箱因连接螺栓松动,使轴线与导轨不平行;5 滚齿与插齿相比,滚齿的a.运动精度高;b.齿形精度高;c.基节精度高;d.生产率高;e.齿面粗糙度值低;6 使用三点式自位支承所限制的自由度数目是:a.三个自由度;b. 二个自由度;c. 一个自由度;个自由度7 机床主轴承内环滚道有形状误差,对加工精度影响较大的是:a.外圆磨床;b.平面磨床;c.卧式镗床;d.车床8 车床上加工大刚度轴外圆产生中凹的原因可能是:a.机床刚度差;b.刀具热变形;c.工件热变形;d.刀具磨损;e.工件刚度差9 当装配尺寸链组成环多,装配精度高于IT6大批量生产时,达到装配精度的方法宜选用:a.完全互换法;b.大数互换法;c.选配法;d.修配法;e.调节法;10 铣削箱体剖分面时,必须限制的自由度是:个;个;个;个11 材料为20CnMnTi,6 ~7级精度的齿轮渗碳淬火后,齿形精加工的方法是:a.剃齿;b.滚齿;c.珩齿;d.磨齿12 选配法适用的条件是:a.形位公差精度要求高;b.装配精度要求高;c.组成环数多;d.相关件2~3件;13 滚齿时影响齿轮运动精度的机床误差主要有:a.分齿传动挂轮误差;b.刀架进给误差;c.分度蜗轮误差;d.分度蜗杆误差;14 车削一长轴外圆,其产生锥度误差原因可能是:a.工件热变形;b.刀具热变形;c.刀具磨损;d.机床水平面导轨与主轴轴线不平行;e.机床垂直面导轨与主轴不平行;15 大批量生产中用以确定机加工余量的方法是:a.查表法;b.计算法;c.经验估算法;16 车床的静刚度应该用:a.床头箱处的刚度;b.尾架处的刚度;c.工件中点位置的刚度作为机床的平均刚度;17 保证装配精度的修配法适用于:a.大批量生产;b.单件小批生产;c.组成环数多;d.组成环数少;e.装配精度要求高;18 比较只有少数工序不同的工艺方案的经济性应比较:a.全年工艺成本;b.单件工艺成本;c.投资回收期的长短;19 研磨和珩磨加工计算工序余量时只需考虑:a.上工序尺寸公差;b.上工序表面粗糙度;c.本工序安装误差;d.本工序需单独考虑的形位公差;e.上工序金属破坏层;20 减轻磨削烧伤的措施有:a.提高砂轮转速;b.提高工件转速;c.提高纵向移动速度;d.降低纵向移动速度;e.减少切削深度;21 展成法加工锥齿轮时,我国除加工等高齿的机床外,都是按设计的机床;a.平面轮原理;b.平顶轮原理;22 加工精度误差分析时分布曲线法和点图法中能平行指导生产过程的是:a. 分布曲线法;b. 点图法;23 除非连续切削之外,振幅随切削用量的改变而改变者属于:a.强迫振动,b.自激振动;填空题答案:1、加工质量、生产率、经济性;2、机床、夹具、工件、刀具;3、提高加工质量、合理利用机床、安排热处理工序、及早发现毛坯缺陷;4、单件小批、中批、大批大量生产;5、计算法、查表法、经验估计法、计算法;6、设计基准、工艺基准、工艺基准;7、先面后孔、先粗后精、先主后次、先基面后其它;8、加工余量、相互位置精度;9、尺寸精度、几何形状精度、表面相互位置精度10、表面冷硬、表层残余应力、表层金相组织11、变值系统误差、等值异号的误差12、表面粗糙度及波度、表面冷硬、表层残余应力、表层金相组织13、强迫振动、自激振动、自激振动14、塑性变形、温度变化、金相组织变化15、热平衡、恒温室15、拉、压16、上凸、下凹17、再生振动、振型耦合18、中凹、腰鼓形19、水平面内的平行度、导轨的平直度20、复合工步、复合刀具21、热变形、内应力变形、弹塑性变形、磨损22、镗床、车床25、系统误差、偶然误差、常值系统误差、变值系统误差、偶然误差26、端跳误差、螺距误差27、主轴承端面、主轴轴肩、误差较小28、工件误差、毛坯误差、刚度29、切削热、传动热、环境辐射热、切削热、传动热;30、增加跟刀架面积、改变走刀方向、改变装夹方法、使用弹簧顶尖31、工件中点、静态测定法、生产测定法32、试切法、调整法、定尺寸刀具法、自动获得法33、研磨、珩磨、超精加工、抛光34、提高传动件、特别是末端件精度;减少元件数量、缩短尺寸链;降速设计、采用补偿装置35、齿形精度、基节精度、表面粗糙度、运动精度、滚齿36、分度蜗轮精度、分齿挂轮的精度37、加工余量、相互位置精度38、分布曲线法、点图法、点图法39、调整中心好、尺寸分散大、尺寸分散;调整中心、平均尺寸,尺寸分散;调整中心,平均尺寸40、完全互换法,大数互换法,选配法、修配法、调整法41、易装拆,易加工,不是公共环42、提高支承刚度,定位作用43、滚压,喷丸,高频淬火,渗碳,渗氮,氰化44、变值系统误差,常值系统误差45、接长麻花钻,扁钻、内排屑深孔钻、外排屑深孔钻,套料刀46、根据设计要求标注,根据工艺要求标注,根据设计和工艺要求标注,第3种47、查找装配尺寸链,解装配尺寸链,按设计要求标注主要尺寸和公差,按工艺要求修改,标注自由尺寸和公差48、最大轮廓尺寸,与定位有关的尺寸及公差,与夹具在机床上安装有关的技术要求,刀具与定位元件的位置尺寸和公差,其它装配尺寸及技术要求。
- 1、下载文档前请自行甄别文档内容的完整性,平台不提供额外的编辑、内容补充、找答案等附加服务。
- 2、"仅部分预览"的文档,不可在线预览部分如存在完整性等问题,可反馈申请退款(可完整预览的文档不适用该条件!)。
- 3、如文档侵犯您的权益,请联系客服反馈,我们会尽快为您处理(人工客服工作时间:9:00-18:30)。
4)增减环的判定 a)用定义判定
b)箭头法判定(图1-46a)
一、直线尺寸链的基本计算公式: 极法计算公式值
1、封闭环的基本尺寸
n 1
L0 Li i 1
注:减环的基本尺寸为负值。 n——尺寸链总环数。 n-1——组成环环数。
m
n1
例:浮动镗、无心磨、抛光等。 2.查表法(机械加工工艺手册) 3.经验法
三、工序尺寸和公差的确定 同一表面基准重合(或基准不变)多次
加工时的工序尺寸和公差。 1、确定余量(查表等) 2、计算各工序的基本尺寸(看表1-18) 3、按经济加工精度确定工序公差。 4、填写工序尺寸和公差(入体原则)。
例题: 某轴直径φ50mm,其尺寸精度为IT5,表
4、封闭环的下偏差EI0
m
n1
EI0 EIp ESq
p1
qm1
EIP——增环下偏差 ESq——减环上偏差 m——增环环数
二、直线尺寸链在工艺过程中的应用
(一)工艺基准与设计基准不重合时的工 序尺寸计算。
1、测量基准与设计基准不重合,图1-43。
设计基准: 孔Ⅲ-Ⅳ中心距离,12 (方法:从一个尺寸出发,到尺寸的基准后
转入相接的下一个尺寸链,通过所有相关联尺 寸,最终返回出发点。)P53
其中,键槽深为由本工序和终工序而间接获得, 为封闭环。 解得:L2=53.7(本工序工序尺寸及公差)
图1-46表示,考虑位置误差(同轴度)时的尺 寸链。 当其误差很小时,(小于一个数字级)可忽略。
但同时若:L1=30.000或L1=29.965 L0实际=L1-L2=30.00-18.070=11.930∴合格 L0实际=L1-L2=29.965-17.965=12.000∴合格
核验:合格(需按零件图检验) 这时称L2超差为假废品。 所以计算出的尺寸,实测尺寸超差时,应测其 它组成环,按零件图检验是否为假废品。
2)工序余量Zi——相邻两工序基本尺寸之差;
即上工序基本尺寸与本工序基本尺寸之差。
非对称表面,单边余量。
Zi li1 li
对称表面,双边余量。
(图4-18a)
2Zi li1 li
(图b)
轴、孔的双边余量。
2Zi di1 di
(图c、d) 2Zi Di Di1
偏差为零(单向偏差)。 孔类(包容件):最小尺寸为基本尺寸,下偏
差为零(单向偏差)。 毛坯:双向对称偏差形式(或双向非对称偏
差形式)。 与零件公差的选择与标注有区别。(零件
公差的选择与标注按:公差等级、配合种类来 确定上下偏差)。
工序余量示意图(图1-40) 1) 轴类尺寸,毛坯 2) 孔类尺寸:毛坯:
5.5.4 时间定额的确定
1.时间定额的概念
时间定额是在一定生产条件下,规定生产一件产品或 完成一道工序所需消耗的时间。
•时间定额是安排生产计划,进行成本核算的主要依据。 •在设计新厂时,时间定额是计算设备数量、布置车间、 计算工人数量的依据。 •时间定额的确定一般由两种方式,一种是工艺人员与 熟练技术工人相结合,通过总结过去加工实践的经验、 并参考有关的技术资料综合估计确定;另一种是工艺 人员以同类产品的工艺或工序时间为依据,进行类比
已知封闭环尺寸及公差,求各组成环尺
寸及公差。
求多环公差时的分配原则:
(1)等公差法
Ti=T平均
(2)等精度原则(设各组成环精度相等)
按精度等级、尺寸分段查公差表确定。
(3)调整法
按等公差法分配后,合理调整。
(难加工表面,尺寸段大的环,增加其公差
值。)
按等公差法
解:
取T1
T2
T0 2
0.035mm
测量基准: 孔Ⅲ -Ⅳ的内侧母线距离,L2 。
工艺过程中的测量方法: 游标卡尺测量
求:工艺尺寸L2 解题步骤:
1)画尺寸链图。 2)确定封闭环 3)确定增减环。 4)代入公式求解。
L1、L3——孔的半径尺寸,由前工序获 得。其公差值取直径公差的一半。
L2——孔Ⅲ-Ⅳ的内侧母线,由测量获 得尺寸。
L0——由L1 、L2 、L3间接获得尺寸,所 以是工艺尺寸链中的封闭环。
2.影响加工余量的因素:
1)上工序的尺寸公差参看图4-21(工序1
余量与毛坯精度有关) 2)上工序的粗糙度Ry和缺陷层Ha(表4-
10) 3)上工序的空间误差ea(形状位置误差)
例:图4-22轴线弯曲造成的余量不均匀误差。
各项位置误差造成的影响参看表4-11
4)本工序的装夹误差εb 包括定位误差、夹紧误差。
5)余量计算公式 由于空间位置误差和装夹误差的
方向性,所以用矢量相加表示。 单边余量
Zmin Ta Ry Ha ea b
双边余量
Zmin Ta / 2 Ry Ha ea b
二、加工余量的确定 1.计算法 准确、合理,其数据由实验确定。 收集数据工作量大,适于大量生产。 计算过程可按实际情况的简化
3)工序余量公差(TZ)——余量的变动范围 Ta ——上工序的基本尺寸公差 Tb ——本工序的基本尺寸公差
TZ Zmax Zmin Tb Ta
图4-19 被包容件…
机加械工余制量造的工确定艺与机床夹具
总加工余量:指零件从毛坯变为成品时从 某一表面所切除的金属层总厚度。即毛坯 尺寸与零件图样的设计尺寸之差
取:L1=30-0.035 (L1 —增环)
L2=L1-L0=18 (L2 —减环)
L0=12
0 -0.07
代入公式;
m
n1
ES0 ESp EIq
p1
qm1
0 0 EIq
EIq 0
m
n 1
EI0 EIp ESq
p 1
q m1
0.070 0.035 ESq
三、用图表法确定工序尺寸及余量 适用于当零件同一方向尺寸较多的复杂情况。 如:工序多,工序基准转换多,工序中基准不 重合需用尺寸链计算,公差,余量确定复杂。 步骤: (一)绘制加工过程尺寸联系图
1、画出工件简图,标注相关设计尺寸。 2、按加工工序列表填写工艺过程,画加工符 号(箭头等)。 (二)工艺尺寸链查找
加工余量、工序尺寸及公差的确定
一、加工余量的概念:
1.加工总余量和工序余量:
1)加工总余量Z0(毛坯余量)
n
Z0 Z1 Z2 Zn Zi i 1
其中:Z1与毛坯的制造精度有关(参看毛坯余 量手册)
其 余 工 序 余 量 Zi—— 由 相 关 工 序 的 加 工 误 差 确定(上工序和本工序)
• 前道工序的工序尺寸公差(Ta) • 前道工序的位置误差(ρa ) • 本工序工件的安装误差(εb) • 本工序的加工余量必须满足下式:
»用于双边余量:Z ≥ 2( Ha + Sa)+ Ta + 2|ρa +εb |
»单边余量:Z ≥ Ha + Sa + Ta + |ρa +εb |
4)工序尺寸的公差按“入体原则”标注 轴类(被包容件):最大尺寸为基本尺寸,上
总余量等于该表面各工序余量之和:Z总 n Zi
总加工余量对工艺过程的影响:
i 1
• 总余量不够,质量得不到保证
• 总余量太大,增加劳动量、消耗、成本
• 总余量与毛坯精度、生产类型、批量大小 有关
机加械工余制量造的工确定艺与机床夹具
2.影响加工余量的因素
• 上道工序的表面质量(包括表面粗糙度Ha 和表面破坏层深度Sa)
1、与设计尺寸有关的工序尺寸L01¨、L1¨。 2、中间工序尺寸(与余量有关)Z4、Z5、Z6 3、查找工艺尺寸链,画尺寸链图¨ (三)计算项目 1、确定公差与余量(经济精度与调整) 2、计算余量变动量,平均余量,平均工序尺 寸。 注:粗加工工序毛坯余量较大,可不计算。 3、按“入体”原则标注工序尺寸。
3、已知:L1=31±0.1mm; L2=30.4±0.05mm; L3=30.15±0.02mm; L1=30±0.02mm;
求(校核)Z2、、Z3、Z4 解得:Z2、、Z3、Z4,
Z4=0.15 ±0.04mm 即:Z4max=0.19、 Z4min=0.11
磨削余量偏大,进行适当调整。(过程略)
+0.008
(四)、余量校核 各工序中加工余量由查表及经验确定。 因为各工序尺寸的公差存在,实际余量是变化 的。 例图1-49,
1、工艺路线 1)精车A面,由B处切断。 2)以A面定位,精车B面。 3)以B面定位,磨A面。 4)以A面定位,磨B面。
2、尺寸链图(b)为关联尺寸链
分解为基本尺寸链尺寸链图(c)
面 粗 糙 度 为 Ra0.04μm, 并 要 求 高 频 淬 火 , 毛坯为锻件。其工艺路线为:粗车-半精 车-高频淬火-粗磨-精磨-研磨,计算 轴的各工序尺寸及公差 解:
加工余量:由工艺手册确定。 工序尺寸:研磨工序尺寸即零件的设计 尺寸50-0.011 、Ra0.04μm
其它各工序基本尺寸的确定: 上工序基本尺寸等于本工序尺寸加上本工 序余量。 以零件设计尺寸50-0.011、Ra0.04开始,计算 的各工序。(注:区分轴类或孔类尺寸) 工序公差的确定: 查表(表1-13)确定公差等级, 查表确定公差值,按“入体”标注为单向偏 差。
代入公式,计算结果:
L2=54.5-0.061
注意:偏差计算公式中,偏差按正负值代入
2、定位基准与设计基准不重合 例:加工阶梯表面C 图1-44
本工序分析:
加工时选用A面为定位基准,加工C面。 ∴设计基准与工艺基准不重合。
例中,已知L0 ,求L1、L2 的尺寸及公差。 尺寸链分析: