加工余量和工序尺寸确定
3-5加工余量、工序间尺寸及其公差的确定

例: 某车床主轴箱箱体的主轴孔的设计要求是:
180
,R 0.018
0.007
a
1.25m,试确定孔加工的加工方案及
工序尺寸。
解:从孔的最终要求 Ra 1.25m
T 0.018 (0.007) 0.025
可确定孔的终加工方法。
180 0.018 0.007
内孔表面加工方案及其经济精度
加工总余量与工序余量的关系
n
Z0 Z1 Z2 Zn Zi i 1
● 单边余量与双边余量
双边余量:对于外圆和孔等旋转表面而言,加工余量
是从直径上考虑的,即加工余量在直径方向上是对称
分布的,实际所切除的金属层厚度是直径上加工余量
的一半,故称为对称余量(即双边余量)。
双边余量
工序尺寸及 偏差
浮动镗
0.2
IT6 T=0.025
Φ180
180 0.018 0.007
精镗孔
0.6
IT7 T=0.04
Φ179.800 179 .800.040
半精镗孔
3.2
粗镗孔
6
毛坯孔
IT9 T=0.10 IT11 T=0.25
Φ179.200 Φ176.000
Φ168.000
179 .200.100
双边余量
轴
z1 2
50
0 0.011
z1 2
54
0 0.10
被包容尺寸
孔
z1
50
0.10 0
z1
2
54
0.011 0
2
包容尺寸
单边余量:对于平面的加工, 余量则是单边余量,它等于实 际所切除的金属层厚度。
加工余量及工序尺

尺寸链图
2.2、基准不重合的计算
尺寸链图
工艺尺寸链的构成,取决于工艺方案和加工方法, 确定封闭环是关键; 一个尺寸链只能解一个封闭环;
请注意箭头方向:
与封闭环同向者为减环 与封闭环异向者为增环
2.2、基准不重合的计算
尺寸链图
2.2、基准不重合的计算
尺寸链图
2.2、基准不重合的计算
2.2、基准不重合的计算
尺寸链的组成
封闭坏——最终被间接保证精度的那个环 组成环——除封闭环之外的所有其他环
A1
A1
设计基准
A2
A2
A1
A3
定位基准
2.2、基准不重合的计算
尺寸链的组成
增环——当其余各组成环不变,而该环增大时使封闭环也 增大者,及该环减小时使封闭环也减小者 减环——当其余各组成环不变,而该环增大时使封闭环反 而减小者,及该环减小时使封闭环反而增大者
1.3、加工余量的确定
3)计算公式
公称余量(简称余量):
大尺寸基本尺寸-小尺寸基本尺寸
最大余量Zmax:
大尺寸基本尺寸+大尺寸上偏差-小尺寸基本尺寸-小尺寸下偏差
最小余量Zmin:
大尺寸基本尺寸+大尺寸下偏差-小尺寸基本尺寸-小尺寸上偏差
1.3、加工余量的确定
3)计算例子
1.3、加工余量的确定
加工余量及工序尺寸和公差的确定
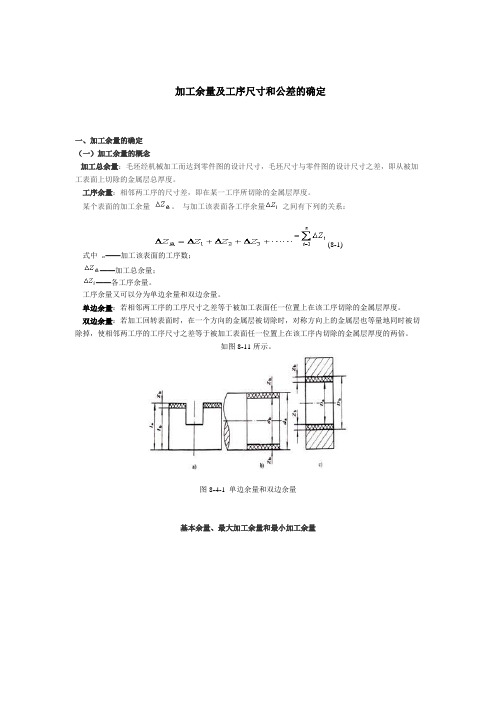
加工余量及工序尺寸和公差的确定一、加工余量的确定(一)加工余量的概念加工总余量:毛坯经机械加工而达到零件图的设计尺寸,毛坯尺寸与零件图的设计尺寸之差,即从被加工表面上切除的金属层总厚度。
工序余量:相邻两工序的尺寸差,即在某一工序所切除的金属层厚度。
某个表面的加工余量。
与加工该表面各工序余量之间有下列的关系:(8-1)式中——加工该表面的工序数;——加工总余量;——各工序余量。
工序余量又可以分为单边余量和双边余量。
单边余量:若相邻两工序的工序尺寸之差等于被加工表面任一位置上在该工序切除的金属层厚度。
双边余量:若加工回转表面时,在一个方向的金属层被切除时,对称方向上的金属层也等量地同时被切除掉,使相邻两工序的工序尺寸之差等于被加工表面任一位置上在该工序内切除的金属层厚度的两倍。
如图8-11所示。
图8-4-1 单边余量和双边余量基本余量、最大加工余量和最小加工余量a) b)图8-4-2 基本余量、最大余量和最小余量加工余量变化的公差等于上道工序的工序尺寸公差与本工序的工序尺寸公差之和。
即(8-2)各个加工余量与相应加工尺寸的关系如图8-4-3所示。
图8-4-3 加工余量与相应加工尺寸(二)影响加工余量的因素1.上道工序加工表面(或毛坯表面)的表面质量包括表面粗糙度高度和表面缺陷层深度;2.上道工序的尺寸公差3.上道工序的位置误差4.本工序的安装误差(三)确定加工余量的方法1. 计算法此法是根据一定的资料,对影响加工余量的各项因素进行分析计算,然后综合考虑计算出来的,多用于大批大量生产,计算公式如下:对双边余量:(8-3)对单边余量:(8-4)一般取2. 查表法以工厂的实际生产经验及工艺实践积累的有关加工余量的资料数据为基础,结合具体加工方法进行适当修正而得到加工余量的方法。
3. 经验法根据工艺人员的经验来确定加工余量的方法。
二、工序尺寸和公差的确定一般情况下,加工某表面的最终工序的尺寸及公差可直接按零件图的要求来确定。
加工余量与工序尺寸的确定
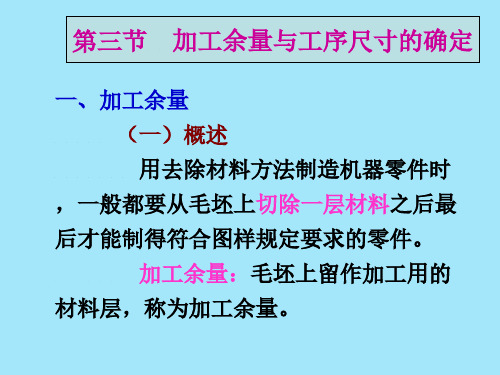
定位基准或工序基准与设计基准不重合时工 序尺寸及其公差的确定(要通过尺寸链计 算,下一章讲述)。
0.054 99.9 0 0.14 99.4 0
0.054
) Ra1.25 100-0.1=99.9 Ra2.5 ) 99.9-0.5=99.4 Ra16 ) 99.4-2.4=97.0 975=92.0
0.14 (0 0.54 (0
0.54 97 0
1 2
1 92 2
表 7 - 7 工序尺寸及公差的计 算
各工序经济精度 工序名称 工序间余量 /mm 经济精度 表面粗糙 度 /μm /mm H7 ( 0 H8 ( 0 H10 H13
0.035
工序 间尺寸
工序尺寸 公差
浮动镗 精镗孔 半精镗孔 粗镗 孔 毛坯孔
0.1 0.5 2.4 5
Ra0.8 )
பைடு நூலகம்
100
0.035 1000
正确规定加工余量的数值是十分重 要的,加工余量规定得过大,不仅浪费材 料而且耗费机时、刀具和电力; 但加工余量也不能规定得过小,如果 加工余量留得过小,则本工序加工就不能 完全切除上工序留在加工表面上的缺陷层 ,因而也就没有达到设置这道工序的目的 。
(二)影响加工余量的因素 为了合理确定加工余量,必须深入 了解影响加工余量的各项因素。影响加工余 量的因素有以下四个方面:
思考题: P261 : 4
三、工序尺寸及其公差的确定 零件图上所标注的尺寸公差是零 件加工最终所要求达到的尺寸要求,工艺 过程中许多中间工序的尺寸及公差,必须 在设计工艺规程中予以确定。 工序尺寸及其公差一般都是通过 定位基准或工序基准与设计基准是否重合 ,采用不同的方法确定。
定位基准或工序基准与设计基准重合时工序 尺寸及其公差的确定。 例:设计尺寸为 ø100H7 的某箱体孔,加工工 序为:粗镗 - 半精镗 - 精镗 - 浮动镗。请 确定各工序尺寸及其公差。 解:由最后一道工序开始向前推。 P245
加工余量与工序尺寸的确定

例7.1
某轴毛坯为锻件,其直径尺寸为
Байду номын сангаас
50
0 0.016
mm
,加工精度要
求为IT6,表面粗糙度Ra为0.8μm,并要求高频淬火。若采用加工
方法为粗车-半精车-高频淬火-粗磨-精磨。试确定各机械加工工序
机械制造工艺与设备
加工余量与工序 尺寸的确定
加工余量与工序尺寸的确定
1.1 加工余量的确定
1.加工余量的概念 用去除材料的方法制造机器零件时,一般都要从毛坯上切除一
层层材料后最后才能制得符合图样规定要求的零件。毛坯上被切除 的金属层,称为加工余量。
加工余量有加工总余量和工序余量之分。 工序余量是相邻两工序的工序尺寸之差,加工总余量是毛坯尺 寸与零件图样的设计尺寸之差。
如图所示,平面的加工余量是单边余量,它等于实际切削 的金属层厚度。对于外圆与内圆这样的对称表面的加工余量用 双边余量表示,即以直径方向计算,其实际切削的金属层厚度 为加工余量的一半。
单边余量与双边余量
1.上工序留下的表面 粗糙度(表面轮廓的 最大高度)和表面缺 陷层深度 。
2.上工序的尺寸公差。
(4)根据加工精度查公差表,并将公差按“入体原则”标注 在工序基本尺寸上。计算结果汇总见教材表7.6。
机械制造工艺与设备
谢谢观看!
(3)确定各工序加工精度和表面粗糙度。查工艺设计手册 可确定:精磨加工精度选定为IT6,尺寸公差为0.016 mm,表面 粗糙度Ra为0.4 μm;粗磨加工精度选定为IT8,尺寸公差为 0.039 mm,表面粗糙度Ra为1.6 μm;半精车加工精度选定为 IT11,尺寸公差为0.16 mm,表面粗糙度Ra为3.2 μm;粗车加 工精度选定为IT13,尺寸公差为0.39 mm,表面粗糙度Ra为 12.5 μm;查工艺设计手册可得锻件毛坯公差为±2 mm。
加工余量与工序尺寸确定
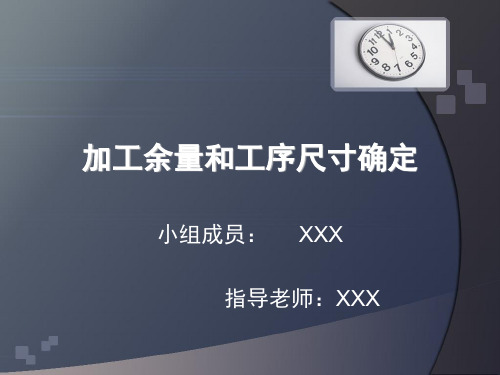
2 .工艺尺寸链的特征
( 1 )尺寸链有一个自然形成的尺寸与 若干个直接得到的尺寸所组成。 • 图 9-33中,尺寸 A1 、 A2 是直接得 到的尺寸,而 A0 是自然形成的。其中自 然形成的尺寸大小和精度受直接得到的尺 寸大小和精度的影响。并且自然形成的尺 寸精度必然低于任何一个直接得到的尺寸 的精度。 • ( 2 )尺寸链一定是封闭的且各尺寸 按一定的顺序首尾相接。
3 .尺寸链的组成
• 组成尺寸链的各个尺寸称为尺寸链的环。图 9-33 中 A 1 、 A 2 、 A 0 都是尺寸链的环,它们可以分为: • ( 1 )封闭环 在加工(或测量)过程中最后自然形成的环称为 • 封闭环。如图 9-33 中的 A 0 。每个尺寸链必须有且仅能有一个封闭 环,用 A 0 来表示。 • ( 2 )组成环 在加工(或测量)过程中直接得到的环称为组成环。 尺寸链中除了封闭环外,都是组成环。按其对封闭环的影响,组成环 可分为增环和减环。 • ①增环 尺寸链中,由于该类组成环的变动引起封闭环同向变动, 则该类组成环称为增环,如图 9-33中的 A 1 ,增环用来表示。 • ②减环 尺寸链中,由于该类组成环的变动引起封闭环反向变动, 则该类组成环称为减环,如图9-33中的 A 2 。减环用来示
总余量与工序余量之间的关系:
Z总 Z1 Z 2 Z n Z i
i 1 n
•式中: • Zs—某加工表面的总余量; • n —该表面的机械加工工序数; • Zi—该表面第i个工序的加工余量。
工序余量有单边余量和双边余量之分
• 1.单边余量,即非对称表面的工序余量
• • • • • 对于外表面(图a) Zb=a-b 对于内表面(图b) Zb=b-a 式中 Zb—本工序的加工余量; a—前工序的工余尺寸; b—本工序的工余尺寸。
1-4 加工余量、工序间尺寸及公差的确定

n
tm ta 1 tsu 100
2、提高生产率的措施
(1) 缩短基本时间: 1)采用精铸、精锻的毛坯件,实施无切屑或少 切屑加工; 2)合理选择切削条件,确定合理的切削用量; 3)采用多刀多刃切削,多件同时加工; 4) 缩短工作行程; 5)在可行条件下,采用先进切削技术,如高速 切削、强力切削与大进给切削等。
1.0 IT9 0.062
1.7 IT12 0.250 47.7-1.0=46.7 3.0 IT15 1.0 46.7-1.7=45.0
0
Φ 45 ±0.5
四、工艺装备的选择
工艺装备: 机床、夹具、量具、刀具、辅具
1.机床的选择
(1) (2) (3) (4) (5) 机床的尺寸规格要与被加工的零件尺寸相适; 机床精度要与被加工零件的加工要求相适应; 机床的生产率与被加工零件的生产纲领相适应; 机床的选用要考虑节省投资和适当考虑生产的发展; 改(扩)建车间,要充分利用原有设备。
1.时间定额的组成
(2)辅助时间ta(单位:min) 如: 装卸工件、 开停机床、 改变切削用量、 进退刀具、 测量工件等 基本时间+辅助时间=工序作业时间
1.时间定额的组成
(3)布置工作地时间ts(单位:min) 如:更换刀具、 润滑机床、 清理切屑、 收拾工具等 布置工作地时间ts=工序作业时间×α %
二、工序余量的确定
3。经验法 由工艺技术人员和有经验的操作工人,根 据经验确定的工序余量。这种方法往往具 有某些不确定性,不够准确。通常用于单 件或临时性零件的加工。
三、工序尺寸与公差的确定
1。确定各加工工序的加工余量
加工余量工序尺寸与工序公差的确定

加工余量工序尺寸与工序公差的确定加工余量是指在零件加工过程中为了保证零件尺寸精度而故意留下的一定尺寸余量。
而工序尺寸和工序公差的确定则是指在加工零件时,根据零件的设计要求和加工工艺,确定每个加工工序的尺寸和公差范围。
这两个问题在零件加工过程中起着非常重要的作用,对于保证零件的质量和精度具有至关重要的意义。
首先,我们来看看加工余量的作用。
在零件加工过程中,由于材料的变形、工艺的限制、加工设备的精度等因素,很难保证每个零件的尺寸都能精确到设计要求的尺寸。
因此,为了保证零件的尺寸精度,加工余量就显得非常重要了。
通过在零件尺寸上留下一定的余量,可以在后续的加工工序中进行修正,从而保证零件的最终尺寸能够达到设计要求。
同时,加工余量还可以在一定程度上弥补加工过程中可能出现的误差,提高零件的加工精度。
而工序尺寸和工序公差的确定则是在加工零件的每个工序中,根据零件的设计要求和加工工艺,确定每个工序的尺寸和公差范围。
这一步工作对于保证零件的加工精度和质量至关重要。
在确定工序尺寸和公差时,需要考虑到材料的性质、加工工艺的特点、加工设备的精度等因素。
只有合理确定了工序尺寸和公差,才能保证每个工序加工出来的零件都能满足设计要求,从而保证整个零件的质量和精度。
在实际的零件加工过程中,确定加工余量、工序尺寸和公差是一个比较复杂的工作。
首先,需要对零件的设计要求进行充分的了解和分析,明确每个尺寸的重要性和影响因素。
其次,需要对加工工艺和加工设备进行全面的评估,了解其加工精度和加工能力。
最后,需要根据实际情况,结合经验和技术,确定合理的加工余量、工序尺寸和公差范围。
在确定加工余量时,需要考虑到零件的材料、加工工艺和加工设备的精度等因素。
一般来说,对于精密零件,加工余量要尽量小,以减少修正工序的次数,提高加工效率和精度;而对于一般零件,加工余量可以适当放大,以提高加工的容错能力。
在确定工序尺寸和公差时,需要充分考虑到每个工序的加工精度和工艺特点,尽量减小工序间的误差传递,保证每个工序加工出来的零件都能满足设计要求。
14-4 加工余量、工序间尺寸及公差的确定
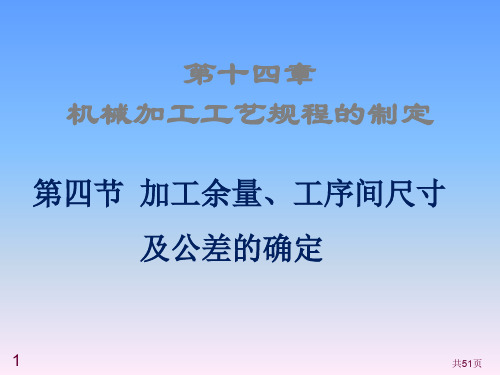
TZ = Zmax – Zmin=Tb+Ta
TZ :工序余量公差; Zmax :工序最大余量;
本道工序基本尺寸
Zmin:工序最小余量; Tb:本道工序的工序尺寸公差;
上道工序基本尺寸
Ta:上道工序的工序尺寸公差。
12
加工方向
共51页
工序尺寸及偏差
一般情况下,工序尺寸的公差按“入体原 则”标注。即 ——对被包容尺寸(轴的外径、实际长、宽、 高),其最大加工尺寸就是基本尺寸,上偏差 为零。 ——对包容尺寸(孔的直径、槽的宽度),其最 小加工尺寸就是基本尺寸,下偏差为零。 ——毛坯尺寸公差按双向对称偏差形式标注。
机床夹具的选择主要考虑生产类型。 (1)单件小批量生产应尽量选用通用夹具; (2)大批大量生产时,应采用高生产效率的专 用机床夹具;
此外,夹具的精度应与零件的加工精度相适应。
42
共51页
3.刀具的选择
刀具的选择主要取决于: 工序所采用的加工方法 加工表面的尺寸大小 工件材料 要求的加工精度 表面粗糙度 生产率 经济性
二、加工余量的确定
3. 经验法
由一些有经验的工程技术人员或工人根 据经验确定加工余量的大小。由经验法 确定的加工余量往往偏大,这主要是因 为主观上怕出废品的缘故。这种方法多 在单件小批生产中采用。
31
共51页
三、工序尺寸与公差的确定
生产上绝大部分加工面都是在基准重合(工艺基准和设计基 准重合)的情况下进行加工。现介绍如下: 1. 确定各加工工序的加工余量
6
共51页
双边余量
2Zi = li–1 – li
式中
Zi——本道工序的工序余量; li——本道工序的基本尺寸; li–1——上道工序的基本尺寸。
加工余量及工序尺寸课件
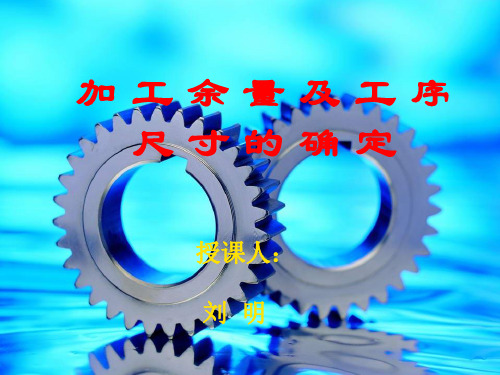
授课人: 授课人: 刘 明
一、加工余量
★ 定义:零件从毛坯成为成品的整个 加工过程中,某表面所切除的材料层厚度 称为该表面的加工余量。 加工余量有工序余量和加工总余量之分。 工序余量 加工总余量 ★工序余量:某一表面在一道工序中 所切除的材料层厚度,称为该表面的工 序余量。或者说同一表面相邻的前后工 序尺寸之差。
最终工序的工序尺寸及其公差 的工序尺寸及其公差, 1 最终工序的工序尺寸及其公差,按零件 图样规定的基本尺寸和公差确定。 基本尺寸和公差确定 图样规定的基本尺寸和公差确定。 中间各工序的工序尺寸 的工序尺寸, 2 中间各工序的工序尺寸,根据加工余量 先确定各工序的工序尺寸, 先确定各工序的工序尺寸,再由后向前逐 个推算,直到毛坯尺寸。 个推算,直到毛坯尺寸 具体推算方法如下: 具体推算方法如下: 前工序的工序尺寸=本工序的工序尺寸± 前工序的工序尺寸=本工序的工序尺寸± 本工序的工序余量 式中,“十”用于外表面,“一”用于内 表面。 3 工序尺寸的公差则按各道工序的经济
二、影响加工余量的因素
加工余量的大小对工件的加工质量和生产率均 有较大的影响。余量过大浪费材料,工作量大, 有较大的影响。余量过大浪费材料,工作量大, 生产率低,成本增加等。 生产率低,成本增加等。余量过小毛坯制造精度 毛坯制造困难, 高,毛坯制造困难,加工困难或因毛坯表面缺陷 未能切除即达到尺寸要求而造成工件报废。 未能切除即达到尺寸要求而造成工件报废。因此 应当合理地确定加工余量,要做到这些, 应当合理地确定加工余量,要做到这些,必须先 分析影响加工余量的因素,这些因素有: 分析影响加工余量的因素,这些因素有:
课堂检测: 课堂检测:
工序的基本余量用公式表示是,外表面_______ 1 工序的基本余量用公式表示是,外表面_______ __,内表面________。 __,内表面________。 内表面
加工余量与工序尺寸

加工余量与工序尺寸
目录
contents
加工余量概述 工序尺寸确定 加工余量与工序尺寸的关系 加工余量与工序尺寸的实例分析 加工余量与工序尺寸的未来发展
01
加工余量概述
加工余量的定义
加工余量是指工件在加工过程中,为了去除工件表面的材料或修正误差而预留的额外材料。
它通常由工序前后的尺寸差值来表示,是评价加工精度和工艺水平的重要参数。
偏差
工序尺寸的公差与偏差
03
加工余量与工序尺寸的关系
加工余量对工序尺寸的影响
加工余量决定了工件在加工过程中的尺寸变化,是影响工序尺寸的主要因素之一。
加工余量的大小直接影响到加工精度和表面质量,因此需要合理控制加工余量,以保证工件的质量和性能。
VS
工序尺寸是工件在加工过程中需要达到的尺寸要求,是确定加工余量的重要依据。
智能化控制技术
通过传感器和监测设备,实时获取加工过程中的数据,对加工余量和工序尺寸进行动态调整,确保加工过程的稳定性和一致性。
实时监测与反馈
研发和应用环保、低毒、高效的切削液,减少对环境的污染和对人体的危害。
采用新型的加工设备和工艺,降低能耗和减少废弃物排放,实现
总结词:铣削加工余量与工序尺寸的确定对于提高加工效率和加工质量具有重要意义。
实例三:磨削加工余量与工序尺寸
总结词:磨削加工余量与工序尺寸的确定对于提高零件的耐磨性和疲劳强度至关重要。
05
加工余量与工序尺寸的未来发展
加工余量与工序尺寸的智能化控制
利用人工智能、机器学习等技术,实现加工余量和工序尺寸的智能预测和控制,提高加工精度和效率。
经验法
根据加工理论、材料力学和热力学等理论知识,结合加工工艺参数,计算出工序尺寸。理论法具有较高的精度和可重复性,但需要扎实的理论基础和计算能力。
加工余量、工序尺寸与及公差的确定
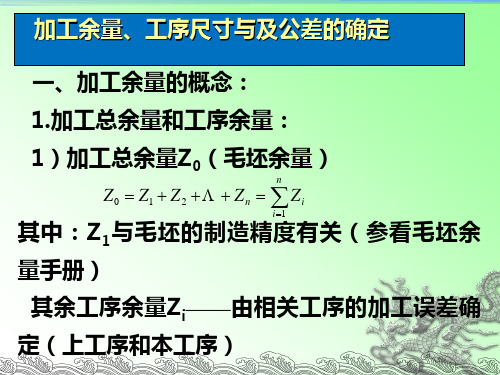
差的选择与标注按:公差等级、配合种类来确 定上下偏差)。
工序余量示意图(图1-40) 1) 轴类尺寸,毛坯 2) 孔类尺寸:毛坯:
2.影响加工余量的因素: 1)上工序的尺寸公差参看图4-21(工序1
余量与毛坯精度有关) 2)上工序的粗糙度Ry和缺陷层Ha(表4-10) 3)上工序的空间误差ea(形状位置误差)
i 1
• 总余量不够,质量得不到保证
• 总余量太大,增加劳动量、消耗、成本
• 总余量与毛坯精度、生产类型、批量大小 有关
机加械工余制量造的工确定艺与机床夹具
2.影响加工余量的因素
• 上道工序的表面质量(包括表面粗糙度Ha 和表面破坏层深度Sa)
• 前道工序的工序尺寸公差(Ta) • 前道工序的位置误差(ρa ) • 本工序工件的安装误差(εb) • 本工序的加工余量必须满足下式:
1、与设计尺寸有关的工序尺寸L01¨、L1¨。 2、中间工序尺寸(与余量有关)Z4、Z5、Z6 3、查找工艺尺寸链,画尺寸链图¨ (三)计算项目 1、确定公差与余量(经济精度与调整) 2、计算余量变动量,平均余量,平均工序尺 寸。 注:粗加工工序毛坯余量较大,可不计算。 3、按“入体”原则标注工序尺寸。
尺寸链中封闭环只有一个,用L0表示。 工艺尺寸链中的封闭环的定义见P.53倒10行。
⑴封闭环一定是工艺过程中间接保证的尺 寸。
⑵封闭环公差值最大,它等于各组成环公 差之和。
3)组成环——尺寸链除封闭外其余各环, 组成环分为增环和减环。
⑴增环—该环变动引起封闭环同向变动。 ⑵减环—该环变动引起封闭环反向变动。
例:图4-22轴线弯曲造成的余量不均匀误差。 各项位置误差造成的影响参看表4-11
加工余量、工序尺寸与工序公差的确定
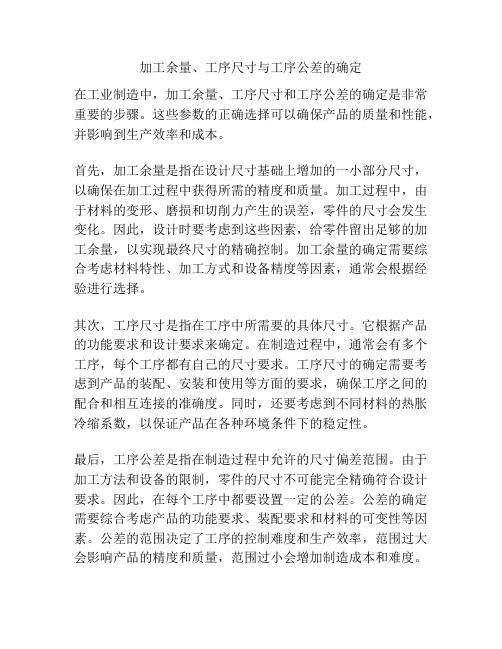
加工余量、工序尺寸与工序公差的确定在工业制造中,加工余量、工序尺寸和工序公差的确定是非常重要的步骤。
这些参数的正确选择可以确保产品的质量和性能,并影响到生产效率和成本。
首先,加工余量是指在设计尺寸基础上增加的一小部分尺寸,以确保在加工过程中获得所需的精度和质量。
加工过程中,由于材料的变形、磨损和切削力产生的误差,零件的尺寸会发生变化。
因此,设计时要考虑到这些因素,给零件留出足够的加工余量,以实现最终尺寸的精确控制。
加工余量的确定需要综合考虑材料特性、加工方式和设备精度等因素,通常会根据经验进行选择。
其次,工序尺寸是指在工序中所需要的具体尺寸。
它根据产品的功能要求和设计要求来确定。
在制造过程中,通常会有多个工序,每个工序都有自己的尺寸要求。
工序尺寸的确定需要考虑到产品的装配、安装和使用等方面的要求,确保工序之间的配合和相互连接的准确度。
同时,还要考虑到不同材料的热胀冷缩系数,以保证产品在各种环境条件下的稳定性。
最后,工序公差是指在制造过程中允许的尺寸偏差范围。
由于加工方法和设备的限制,零件的尺寸不可能完全精确符合设计要求。
因此,在每个工序中都要设置一定的公差。
公差的确定需要综合考虑产品的功能要求、装配要求和材料的可变性等因素。
公差的范围决定了工序的控制难度和生产效率,范围过大会影响产品的精度和质量,范围过小会增加制造成本和难度。
综上所述,加工余量、工序尺寸和工序公差是工业制造中至关重要的参数。
它们的合理选择对于确保产品质量、提高生产效率和降低生产成本具有重要意义。
在确定这些参数时,需要考虑到材料特性、加工方式、设备精度、产品功能要求和装配要求等因素,并结合经验和实际情况进行综合分析和决策。
只有在合适的条件下,才能达到最佳的加工效果和产品性能。
加工余量、工序尺寸和工序公差是工业制造中重要的三个参数。
它们的选择直接影响产品的质量、性能和生产效率。
在制造过程中,合理确定这些参数非常关键,需要综合考虑多种因素。
加工余量与工序尺寸的确定和基准--2011
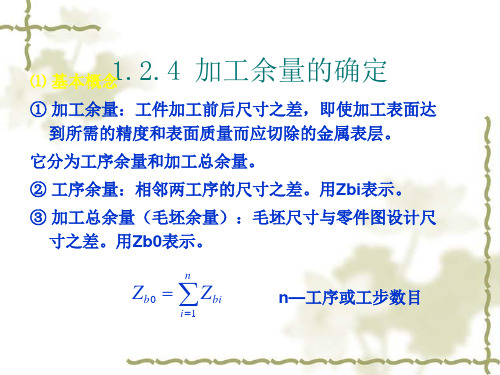
③ 尺寸链的分类 a) 按应用场合来分 工艺尺寸链:全部组成环为同一零件的设 计尺寸所形成的尺寸链,如图2。 特点:所有尺寸都在一个零件上 装配尺寸链:全部组成环为不同零件的工 艺尺寸所形成的尺寸链,如图1。 特点:每一个尺寸都分布在不同的零件上
b) 按各环所处的空间位置来分 直线尺寸链:尺寸链中各环位于同一平面内 且相互平行,最为常规最基本的尺寸链。 平面尺寸链:尺寸链中各环位于同一平面或 几个相互平行平面内,但某些组成环不平行 于封闭环的尺寸链。 空间尺寸链:尺寸链中各环不在同一平面且 互不平行。
极限尺寸的计算:
A0max Az max Aj min
A0min Az min Aj max
⑵ 工序尺寸及其公差的确定 ① 工序基准与设计基准重合,即对同一表面进行多
次加工
这种工序尺寸计算较简单,只需根据各工序的加 工余量就可以算出各工序的基本尺寸。其计算顺 序是由最后一道工序开始逐步向前推算。 例:加工某一个钢制零件上的一个孔,其设计尺 0 寸为 72.50.03 mm,表面粗糙度为Ra0.4。现经过 粗镗、半精镗、精镗、粗磨和精磨五次加工,计 算各次加工的工序尺寸及其公差。
尺寸链中在装配过程或加工过程最后形成 的一环。
c) 组成环:加工或装配时直接影响封闭环 精度的各原始尺寸。
尺寸链中对封闭环有影响的全部环。
增环:尺寸链中的组成环,由于该环的变 动引起封闭环同向变动。 减环:尺寸链中的组成环,由于该环的变 动引起封闭环反向变动。
d) 尺寸链的两个主要功能 公差分配(反计算):已知封闭环基本尺寸 及公差,组成环基本尺寸,求解组成环的公 差。 公差控制(正计算):已知组成环基本尺寸 及公差,核算封闭环尺寸及公差。
加工余量、工序尺寸与工序公差的确定

61.5
61.500.018 61.500.018 0.4
细镗
0.3
H
6(
0.018 0
)
0.8
61.5-0.003=61.497 61.49700.018
61.500..001053
0.8
精镗
0.7
H
9(
0.046 0
)
1.6
61.497-0.3=61.2
61.200.046
61.200.05 1.6
5.4.1加工余量的概念
总余量与工步余量 之间的关系:
n
Zs Zi i1
粗刨Z1 精刨Z2 磨Z3
H1 H2
Zs H设 H坯
式中:Zs—某加工表面的总余量; n—该表面的机械加工工序(工步)数; Zi—该表面第i个工序(工步)的加工余量。
5.4.1加工余量的概念
设某加工表面上道工序的尺寸为a,本道工序的 尺寸为b,则本道工序的基本余量Zb可以表示为:
Zmin Ta 2(Ry H a )
5.4.2确定加工余量的方法
1.分析计算法
2)无心磨床磨外圆时无装夹误差,公式可简化
为:
Zmin Ta 2(Ry H a ) 2 | a |
砂轮 工件
导轮
托板
5.4.2确定加工余量的方法
3)精密加工方法如研磨、珩磨、 超精加工等,加工时仅去掉上 工序留下的加工痕迹,公式可 简化为:
3)除终加工工序外,根据各工序的加工方法及其经 济加工精度,确定其工序公差和粗糙度。
4)按入体原则以单向偏差方式标注工序尺寸,并可 作适当调整。
5.4.3工序尺寸及公差的确定
例5.1
某连杆大头孔的设计尺
加工余量、工序尺寸与工序公差的确定

加工余量、工序尺寸与工序公差的确定加工余量、工序尺寸与工序公差的确定是制造过程中非常重要的环节。
这些参数的正确选择可以确保产品的质量和性能符合设计要求,同时也可以提高生产效率和减少成本。
首先,加工余量是指工件的最终尺寸与设计尺寸之间的差值。
加工余量的大小会直接影响到零件的相对尺寸和形状。
通常情况下,在加工过程中需要保留适当的加工余量,以确保加工后的尺寸与设计要求相符。
加工余量的选择需要考虑材料的收缩率、热胀冷缩等因素,并结合加工方法和机械设备的精度要求进行确定。
其次,工序尺寸是指在制造过程中每个工序中所需达到的尺寸要求。
在多道工序的加工中,每个工序所要求的尺寸有时会与前后工序有关。
因此,确定工序尺寸时需要考虑工序之间的配合要求,以确保各工序之间的相互协调和流畅。
最后,工序公差是指在加工过程中允许的尺寸偏差范围。
工序公差可以直接影响到产品的装配性能、运转精度和可靠性。
确定工序公差时需要综合考虑产品的功能要求、装配及使用条件、工艺能力等因素。
通常情况下,工序公差需要在确保产品质量和性能的前提下尽量缩小,以提高生产效率和降低成本。
总而言之,加工余量、工序尺寸和工序公差的确定是制造过程中十分重要的环节。
正确选择和确定这些参数,可以确保产品符合设计要求,同时提高生产效率和降低成本。
因此,在进行加工过程中,工程师和技术人员需要综合考虑多种因素,并依据实际情况进行合理的确定。
加工余量、工序尺寸与工序公差的确定是制造过程中非常重要的环节。
这些参数的正确选择可以确保产品的质量和性能符合设计要求,同时也可以提高生产效率和减少成本。
加工余量是在加工过程中需要保留的尺寸差值。
加工余量的大小会直接影响到零件的相对尺寸和形状。
加工过程中的各种因素,如材料的物理特性、工件的几何形状、加工方法的选择等都会影响到加工余量的确定。
首先,材料的收缩率是影响加工余量选择的重要因素。
不同材料的收缩率不同,加工后的尺寸会有所变化。
在设计零件时,需要预留一定的加工余量,以弥补加工过程中材料收缩产生的尺寸变化。
12.4 加工余量和工序尺寸的确定_配机械制造基础(第2版)
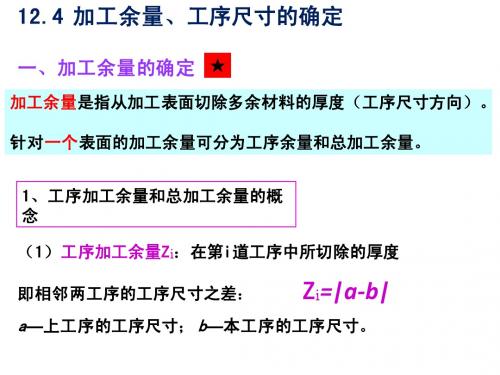
ES2 = EI1+ES0 = -0.15+0 = −0.15 mm;
由公式EI0 = EI2−ES1 得: EI2 = ES1+EI0 = −0.05+(−0.15) =- 0.2 mm; 因此A2= 6 0 0 .1 5 0 .2
mm
6 0 0 .2
0 .1 5
mm
列竖式法解尺寸链 口诀:封闭环、增环照抄;减环取反,上下偏差对调。 方法:求组成环各项之和等于封闭环。
尺寸链(环)
基 本 尺 寸
-10 (60) 50
上偏差ES
0.15 ( - 0.15) 0
下偏差EI
0.05 (−0.2) −0.15
A1 A2 A0
6 0 0 .2
0 .1 5
mm
A1
A 0 6 0 .1 5
0 .1
A 2 1 0 0 .0 3
0 .0 5
A 3 2 0 0 .0 3
0 .1
mm,按入体原则表示为A2 = 20.1 0 0 . 4 mm。 0 .3
2)测量基准与设计基准不重合的尺寸换算
加工一轴承座,设计尺寸为A1和A0。由于设计尺寸A0加工时无法直接测量,只 好通过测量A2尺寸来间接保证它,求A2的工序尺寸和公差。
A0为封闭环,A1为减环,A2为增环。 由公式A0 = A2−A1 得: A2 = A1+A0 = 10+50 = 60 mm; 由公式ES0 = ES2−EI1得:
2、尺寸链极值法计算的基本公式
1)封闭环的基本尺寸 封闭环的基本尺寸等于所有增环基本尺寸之和减去所有减 环基本尺寸之和,即:
m n
A0
机械加工工艺-加工余量、工序尺寸及公差
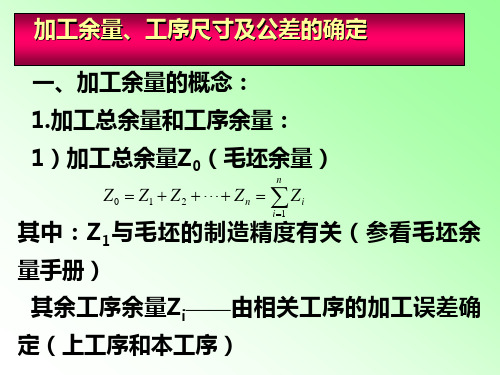
(一)设计 1、合理的结构工艺性、加工精度、表面
粗糙等。 2、零件、部件、产品的三化程度(通用、
标准、系列) (二)先进的工艺及设备
1、毛坯 2、机加工 3、装配
(三)先进的管理:计划、准备、服务、技术、
质量、经济分析等。
提高机加工生产率的工艺途径:
(一)缩短t基 1、(V、F、ap)↑。 2、多刀、多刃、及单刀多件等。
加工余量、工序尺寸及公差的确定
一、加工余量的概念: 1.加工总余量和工序余量: 1)加工总余量Z0(毛坯余量)
n
Z0 Z1 Z2 Zn Zi i 1
其中:Z1与毛坯的制造精度有关(参看毛坯余 量手册)
其余工序余量Zi——由相关工序的加工误差确 定(上工序和本工序)
2)工序余量Zi——相邻两工序基本尺寸之差;
求:本工序工序尺寸L2(渗碳深度) 分析:渗碳层保留深度L0 —单边值(图面尺寸)
渗碳深度L2—单边值。 按尺寸链图,代入公式求解得:L2=0.7+0.025
+0.008
(四)、余量校核 各工序中加工余量由查表及经验确定。 因为各工序尺寸的公差存在,实际余量是变化 的。 例图1-49,
1、工艺路线 1)精车A面,由B处切断。 2)以A面定位,精车B面。 3)以B面定位,磨A面。 4)以A面定位,磨B面。
三、用图表法确定工序尺寸及余量 适用于当零件同一方向尺寸较多的复杂情况。 如:工序多,工序基准转换多,工序中基准不 重合需用尺寸链计算,公差,余量确定复杂。 步骤: (一)绘制加工过程尺寸联系图
1、画出工件简图,标注相关设计尺寸。 2、按加工工序列表填写工艺过程,画加工符 号(箭头等)。 (二)工艺尺寸链查找
尺寸链中封闭环只有一个,用L0表示。 工艺尺寸链中的封闭环的定义见P.53倒10行。
第三、五、六节 加工余量、工序尺寸及其.ppt

[例5-2] 某机床主轴箱体的主轴孔设计尺寸要求
工。对于成批单件生产,目前大部分工厂都采
用查表法或经验法来确定工序余量和总余量。
查表法
查表法是根据《机械加工工艺手册》提供的资
料查出各表面的总余量以及不同加工方法的工序余 量,方便迅速,使用广泛。 需要注意的是:
1)目前国内各种手册所给的余量多数为标称
余量,标称余量等于最小余量与上一工序尺寸公差 之和,即标称余量中包含了上一工序尺寸公差。 2)各种手册提供的数据不一定与具体加工情 况完全相符,余量值大多偏大,须根据工厂的具体 情况加以修正。
第三节加工余量、工序尺寸及其公差的确定
一、加工余量的概念
加工总余量与工序余量 加工总余量即毛坯余量,是指毛坯尺寸与零 件设计尺寸之差,也就是某加工表面上切除的金属 层总厚度。工序余量是指相邻两工序的尺寸之差, 也就是某道工序所切除的金属层厚度。显然有:
Z0
Z
i 1
n
i
Z0 -- 某表面加工总余量; Zi -- 该表面第i个工序加工余量 n -- 该表面的机械加工工序数;
100 0
0.035
Ra0.8 Ra1.6 Ra3.2 Ra6.3
——
99.9 0
0.054
99.4 0
0.14
97 0
0 .3 5
8
9 2 -2
加工余量、工序尺寸及其公差的确定
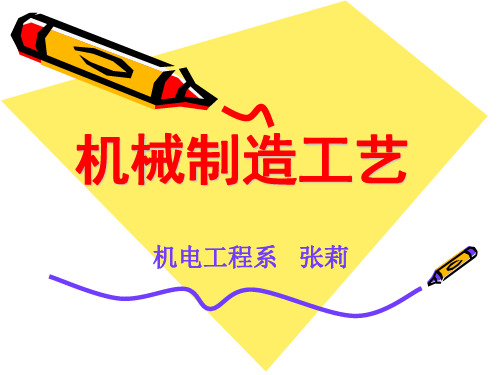
2、影响加工余量的因素
在确定工序的具体内容时,其工作之一就是合理地确定 工序加工余量。加工余量的大小对零件的加工质量和制造的 经济性均有较大的影响。加工余量过大,必然增加机械加工 的劳动量、降低生产率;增加原材料、设备、工具及电力等 的消耗。加工余量过小,又不能确保切除上工序形成的各种 误差和表面缺陷,影响零件的质量,甚至产生废品。
机械制造工艺
机电工程系 张莉
第二章 机械加工工艺基础知识
2.1 机械加工工艺过程的基本概念及常用术语 2.2 机械加工工艺规程和工艺文件 2.3 零件的工艺性分析 2.4 零件表面加工方法的选择与工艺路线的
拟订
2.4.4 加工余量、工序尺寸及其公差的确定
1、加工余量的概念
为了保证零件的质量(精度和粗糙度值), 在加工过程中,需要从工件表面上切除的金属层 厚度,称为加工余量。
4.工序尺寸及其公差的确定
1)基准重合时,工序尺寸及其公差的计算 生产上绝大部分加工面都是在基准重合(工艺基准和设计
基准重合)的情况下进行加工的,基准重合情况下工序尺寸与 公差的确定过程如下:
(1)确定毛坯总余量和各加工工序的工序余量(查表修正法) (2)确定工序基本尺寸
从最终加工工序开始,即从零件图上的设计尺寸开始,一 直往前推算到毛坯尺寸。最终工序基本尺寸等于零件图上 的基本尺寸,某工序基本尺寸等于后道工序基本尺寸加上 或减去后道工序余量。
毛坯: ±2mm
工序尺寸及其公差的确定实例1 (4)确定工序尺寸及其公差
研磨:50
5000.011
精磨:50+0.01=50.01
粗磨:50.01+0.1=50.11
半精车:50.11+0.3=50.41
- 1、下载文档前请自行甄别文档内容的完整性,平台不提供额外的编辑、内容补充、找答案等附加服务。
- 2、"仅部分预览"的文档,不可在线预览部分如存在完整性等问题,可反馈申请退款(可完整预览的文档不适用该条件!)。
- 3、如文档侵犯您的权益,请联系客服反馈,我们会尽快为您处理(人工客服工作时间:9:00-18:30)。
加工的具体方案,紧紧抓住“自然形 成”这一要领。
2 .组成环的查找
• 组成环查找的方法,从构成封闭的两表面开始,同步地按 照工艺过程的顺序,分别向前查找各表面最后一次加工的 尺寸,之后再进一步查找此加工尺寸的工序基准的最后一 次加工时的尺寸,如此继续向前查找,直到两条路线最后 得到的加工尺寸的工序基准重合(即两者的工序基准为同 一表面),至此上述尺寸系统即形成封闭轮廓,从而构成 了工艺尺寸链。
成本增加;余量小时,难以消除前工序的
各种误差和表面缺陷,甚至产生废品。因
此,应合理确定各工序的加工余量。
1)前工序的尺寸公差Ta 上工序的尺寸公差越大,本工序的余量越
大。本道工序应切除上道工序尺寸公差中包含 的各种可能产生的误差。
2)前工序留下的表面粗糙度Ra和表面缺陷层深 度Ha在本道工序中应该切除。
• 对于孔(图d)2Zb db da (孔)
• 式中 Zb—直径、半径上的加工余量;
•
da—前工序的工余尺寸(直径);
•
db—本工序的工余尺寸(直径)。
Zi
• 图9-29 加工余量
影响加工余量的因素
•
加工余量的大小对于工件的加工质量
和生产率有较大的影响。余量大时,加工
时间增加,生产率降低,能源消耗增大,
•
在机械加工过程中,同一
工件的各有关尺寸组成的尺寸
链称为工艺尺寸链。
2 .工艺尺寸链的特征
( 1 )尺寸链有一个自然形成的尺寸与 若干个直接得到的尺寸所组成。
•
图 9-33中,尺寸 A1 、 A2 是直接得到
的尺寸,而 A0 是自然形成的。其中自然形
成的尺寸大小和精度受直接得到的尺寸大
小和精度的影响。并且自然形成的尺寸精
•
毛坯尺寸与零件图的设计尺寸之差称为加工
总余量。
•
某一工序所切除的金属层厚度或相邻两工序
的基本尺寸之差称为工序余量。
总余量与工序余量之间的关系:
n
Z总 Z1 Z2 Zn Zi i1
•式中: • Zs—某加工表面的总余量; • n —该表面的机械加工工序数; • Zi—该表面第i个工序的加工余量。
度必然低于任何一个直接得到的尺寸的精
度。
• ( 2 )尺寸链一定是封闭的且各尺寸 按一定的顺序首尾相接。
3 .尺寸链的组成
• 组成尺寸链的各个尺寸称为尺寸链的环。图 9-33 中 A 1 、 A 2 、 A 0 都是尺寸链的环,它们可以分为:
•
( 1 )封闭环 在加工(或测量)过程中最后自然形成的环称为
加工余量和工序尺寸确定
小组成员: XXX 指导老师:XXX
加工余量及工序间尺寸的确定
• 一、加工余量及其影响因素 • 二、确定加工余量的方法 • 三、工序尺寸及其公差的确定
一、加工余量的概念
• 1.加工余量的概念:
• 使加工表面达到所需的精度和表面质量而应切除的金 属层.
• (1)总余量和工序余量:
过程中自然形成的尺寸。因此,封闭 环是随着零件加工方案的变化而变化 的。以图所示的零件,当以表面 3 定 位加工表面 1 而获得尺寸 A 1 ,然后 以表面 1 为测量基准加工表面 2 而直 接获得尺寸 A 2 ,则自然形成的尺寸 A 0 为封闭环;但以加工过的表面 1 为测量基准加工表面 2 ,直接获得尺 寸 A 2 ,再以表面 2 为定位基准加工 表面 3 直接获得尺寸 A 0 ,此时尺寸 A 1 便为自然形成而成为封闭环。
• ②以端面 D 定位,精车大 端面 A 获得尺寸 A2 ,并 在车大孔时车端面 C ,获 得孔深尺寸 A3 (图c )
• ③以端面 D 定位, 磨大端面 A 保证 全长尺寸 ,同时 保证孔深尺寸为 (图 d )
• 由以上工艺过程可知,孔深设计尺寸是自然形成的,应为封闭环。 从构成封闭环的两界面 A 和 C 面开始查找组成环, A 面的最近 一次加工是磨削,工艺基准是 D 面,直接获得的尺寸是; C 面 最近的一次的加工是车孔时的车削,测量基准是 A 面,直接获 得的尺寸是 A3 。显然上述两尺寸的变化都会引起封闭环的变化, 是欲查找的组成环。但此两环的的工序基准各为 D 面与 A 面, 不重合。为此要进一步查找最近一次加工 D 面和 A 面的加工尺 寸。 A 面的最近一次加工是精车 A 面,直接获得的尺寸是 A2 , 工序基准为 D 面,正好与加工尺寸的工序基准重合,而且 A2 的 变化也会引起封闭环的变化,应为组成环。至此,找出A2 、A3 、 为组成环, 为封闭环,它们组成了一个封闭的尺寸链(图e )
• 封闭环。如图 9-33 中的 A 0 。每个尺寸链必须有且仅能有一个封闭环, 用 A 0 来表示。
•
( 2 )组成环 在加工(或测量)过程中直接得到的环称为组成环。
尺寸链中除了封闭环外,都是组成环。按其对封闭环的影响,组成环
可分为增环和减环。
•
①增环 尺寸链中,由于该类组成环的变动引起封闭环同向变动,
则该类组成环称为增环,如图 9-33中的 A 1 ,增环用来表示。
•
②减环 尺寸链中,由于该类组成环的变动引起封闭环反向变动,
则该类组成环称为减环,如图9-33中的 A 2 。减环用来示
增环和减环的判别
• 为了简易地判别增环和
减环,可在尺寸链图上先 给封闭环任意定出方向并 画出箭头,然后以此方向 环绕尺寸链回路,顺次给 每个组成环画出箭头。此 时凡与封闭环箭头相反的 组成环为增环,相同的为 减环。如图所示。
工序余量有单边余量和双边余量之分
• 1.单边余量,即非对称表面的工序余量
• 对于外表面(图a) Zb=a-b
• 对于内表面(图b) Zb=b-a
• 式中 Zb—本工序的加工余量;
•
a—前工序的工余尺寸;
•
b—本工序的工余尺寸。
2.双边余量,即回转表面的加工余量
• 对于轴(图c)2Zb da db (轴)
对于双边余量:
Zmin Ta 2(Ry H a ) 2 | a b |
二、确定加工余量的方法
1.分析计算法
1)采用浮动镗刀镗孔或浮动铰刀铰孔或拉刀拉孔, 由于这些方法不能纠正位置误差,公式可简化为:
Zmin Ta 2(Ry H a )
• 2)无心磨床磨外圆时无装夹误差,公 式可简化为:
其公差即为工序尺寸公差,各工序的加工余量确
定后,即可确定工序尺寸及公差。
•
零件从毛坯逐步加工至成品的过程中,无论
在一个工序内,还是在各个工序间,也不论是加
工表面本身,还是各表面之间,他们的尺寸都在
变化,并存在相应的内在联系。运用尺寸链的知
识去分析这些关系,是合理确定工序尺寸及其公
差的基础。
工艺尺寸链的概念及计算公式
•
查找组成环必须掌握的基本特点为:组成环是加工过
程中“直接获得”的,而且对封闭环有影响。下面以图 3-
81 为例,说明尺寸链建立的具体过程。图 3-81 为套类零
件,为便于讨论问题,图中只标出轴向设计尺寸,轴向尺
寸加工顺序安排如下。
• ①以大端面 A 定位,车端 面 D 获得 A 1 ;并车小外 圆至 B 面,保证长度 mm (图 b );
• (一)工艺尺寸链的概念
•
1 .尺寸链的定义
•
在机器装配或零件加工过
程中,由相互连接的尺寸形成
的封闭尺寸组,称为尺寸链。
如图 9-33 所示,用零件的表面
1 定位加工表面 2 得尺寸 A1 , 再加工表面 3 ,得尺寸 A2 ,自 然形成 A0 ,于是 A1 — A2 — A0 连接成了一个封闭的尺寸组 (图 9-33b ),形成尺寸链。
步骤: 1)确定该加工表面的总余量,再根据加工路线确定各工序
的基本余量,并核对第一道工序的加工余量是否合理。 2)自终加工工序起,即从设计尺寸开始,至第一道工序,
逐次加上(对被包容面)或减去(对包容面)各工序的基 本余量,便可得到各道工序的基本工序尺寸。 3)除终加工工序外,根据各工序的加工方法及其经济加工 精度,确定其工序公差和粗糙度。 4)按入体原则以单向偏差方式标注工序尺寸,并可作适当 调整。
(二)工艺尺寸链的建立
•
工艺尺寸链的建立并不复杂,但
在尺寸链的建立中,封闭环的判定和
组成环的查找却应引起初学者的重视。
因为封闭环的判定错误,整个尺寸链
的解算将得出错误的结果;组成环查
找不对,将得不到最少链环的尺寸链,
解算的结果也是错误的。下面将分别
予以讨论。
1 .封闭环的判定
在工艺尺寸链中,封闭环是加工
Zmin 2Ry (双边)
Zmin Ry (单边)
2.查表法
根据《机械加工工艺手册》提供的资料查出 各表面的总余量及不同加工方法的工序余 量,方便迅速,使用广泛。
3.经验法
由一些有经验的工艺设计人员或工人根据经 验确定余量。一般用于单件小批生产。
三、工序尺寸及其公差的确定
•
工序尺寸是指某一工序加工应达到的尺寸,
3)前工序留下的需单独考虑的空间误差εa • a.包括轴线直线度误差和各种位置误差; • b.这些误差可能是上工序加工方法带来的,也可
能是热处理后产生的,也可能是毛坯带来的。
• 4)本工序的安装误差εb。包括工件的定位误差 和夹紧误差。
工序余量的计算公式:
对于单边余量:
Z min Ta Ry H a | a b |
Zmin Ta 2(Ry H a ) 2 | a |
• 3)精密加工方法 如研磨、珩磨、 超精加工等,加 工时仅去掉上工 序留下的加工痕 迹,公式可简化 为:
Zmin Ry H a (单边)
Zmin 2(Ry H a )(双边)