定宽压力模块无冒口铸造工艺的模拟试验
精密铸造铸件工艺及浇冒口系统设计

第六章铸件工艺设计第一节概述为了生产优质而价廉的包模铸件,做好工艺设计是十分重要的。
在做工艺设计之前,首先要考虑选用包模铸造工艺生产时,在质量、工艺和经济方面的几个问题。
1.铸件质量的可靠性对于铸件质量上的要求,一般是包括两个方面,一是保证技术要求的尺寸精度、几何精度和表面光洁度,二是保证机械性能和其它工作性能等内在质量方面的要求。
包模铸造具有少切削、无切削的突出优点。
近年来,由于冶金技术、制模、制壳材料和工艺以及检测技术等方面的发展,包模铸件的外部和内在质量不断提高,所以它的应用范围愈来愈广。
不少锻件、焊接件、冲压件和切削加工件,都可以用熔模铸造方法生产。
这对于节约机械加工工时和费用,节约金属材料,提高劳动生产率和降低成本都具有很大意义。
但是,熔模铸造生产的铸件,由于冶金质量、热型浇注引起的晶粒粗大、表面脱碳以及内部缩松等方面的原因,铸件的机械性能(尤其是塑性),还存在一些缺陷。
对于某些受力大和气密性要求高的铸件,采用包模铸造时,应充分考虑零件在产品上的作用和性能要求,以确保其使用可靠。
有些结构件改用包模铸造生产时,必须考虑原用合金的铸造性能是否能满足零件的质量要求,否则就需要更改材质。
2.生产工艺上的可能性和简易性熔模铸造虽然可以铸造形状十分复杂的、加工量甚少甚至不加工的零件,但零件的材质、结构形状、尺寸大小和重量等,必须符合熔模铸造本身的工艺要求。
如铸件最小壁厚、最大重量、最大平面面积、最小孔槽以及精度和光洁度要求等,都要考虑到工艺上的可能性和简易性。
3.经济上的合理性采用包模铸造在经济上是否合理,要从多方面考虑。
按每公斤的价格来说,包模铸件与同类型锻件相近甚至还高些,但是由于大幅度减少了加工量,因而零件最终成本还是低的。
但也有些零件,可以利用机械化程度较高的方法生产,例如用自动机床高速加工、精密锻造、冷挤压、压力铸造等等,这时,用包模铸造法生产在经济上的优越性就不一定显著,甚至成本还可能高一些,所以在这种情况下,就不一定选用这种方法了。
无冒口铸造工艺改进及模具设计构思

无冒口重力铸造工艺改进及模具设计构思二分析铸造过程产生的原因摘要:通过对铝合金无冒口重力铸件结构特点补缩缺陷的分析,并使用ViewCast 软件对初始方案进行了数值模拟。
原采用重力铸造工艺,铸件存在缩孔、缩松和浇不足等缺陷。
针对上述问题进行工艺改进,设计并制造了挤压铸造成形模具,并用改制的挤压铸造设备进行工艺试验。
结果表明,通过优化铸造工艺,可大大改善不足和缩松铸件质量。
关键词:挤压铸造;无冒口模具(个别地方有和专家相同地方完全属巧合,还请见谅)。
供稿:华益铝轮—伍春华1 工艺设计前的模拟在初始方案设计前,对铸件进行一次模拟,观察金属液在铸型内的模拟凝固过程和温度分布状态,找出孤立液相区出现的位置以及金属液补缩量不足的部位,可以为安放浇注系统与冒口提供依据,为初始方案的制定提供参考。
将铸件的三维模型图保存为STL 格式文件后,导入ViewCast 模拟软件进行凝固模拟,网格剖分设定为200 万,该部分模拟参数可以在初始方案制定前确定:浇注温度720℃,模具初始温度280 ℃,凝固模拟过程深色表示铸型内金属液未凝固或呈半固态,浅色或透明部分表示铸型内部的金属液已经完全凝固。
结合铸件凝固过程模拟图,对这些缺陷产生的原因就能做动态的分析,在凝固过程中t=220 s 时,可以看出铸件厚度较薄的部位已经凝固,铸型内左右两部分的金属液出现了断开的趋势;在t=230 s 时,铸型内左右两部分的金属液已经完全断开,形成两部分的孤立液相区,孤立液相区的形成为铸件内缺陷的产生提供了条件;在236 s 时刻,铸件内孤立液相区范围加大,数目增多,由大范围的孤立液相区分化成小范围的孤岛区域,这些小的孤立液相区在凝固结束后就形成了缩孔、缩松缺陷,铸件的中间边的凸台处金属液形成了缩孔、缩松缺陷,铸件的R角处金属液持连通,这种连通会有助于铸件内部金属液的补缩,在该处较适宜放置保温棉,对于产生孤立液相区的部位,可以使用外保温消除。
铸造PFMEA

P.A.预防措施C .A.检查措施覆模砂强度不合格砂芯报废或铸件形状不完整,产生多肉或缺肉缺陷。
4供应商供应的覆模砂不合格而又未能检出从而入库备用4每批一次按供应商质保单进厂复验348无生铁断面有白口铸件化学成份、机械性能不合格6供应商供应的生铁不合格而又未能检出从而入库备用。
4每批一次,每次检验3块断口质量372无生铁成份不合格铸件化学成份、机械性能不合格6供应商供应的生铁不合格而又未能检出从而入库备用。
4每批一次按供应商质保单进厂复验372无废钢成份不合格铸件化学成份、机械性能不合格6供应商供应的废钢不合格而又未能检出从而入库备用。
4每批一次按供应商质保单进厂复验372无锰铁成份不合格铸件化学成份、机械性能不合格6供应商供应的锰铁不合格而又未能检出从而入库备用4每批一次按供应商质保单进厂复验496无铬铁成份不合格铸件化学成份、机械性能不合格6供应商供应的铬铁不合格而又未能检出从而入库备用4每批一次按供应商质保单进厂复验496无电解铜成份不合格铸件化学成份、机械性能不合格6供应商供应的电解铜不合格而又未能检出从而入库备用4每批一次按供应商质保单进厂复验496无球化剂成份不合格铸件化学成份、机械性能不合格6供应商供应的球化剂不合格而又未能检出从而入库备用5每批一次按供应商质保单进厂复验4120无孕育剂成份不合格铸件化学成份、机械性能不合格6供应商供应的孕育剂不合格而又未能检出从而入库备用5每批一次按供应商质保单进厂复验4120无硅砂成份不合格铸件出现机械粘砂,砂孔,表面粗糙等缺陷6供应商供应的硅砂不合格而又未能检出从而入库备用5每批一次按供应商质保单进厂复验4120无Actions Taken 采取的措施严重度(S)频度数(O)不测度(D)风险顺序数RPN 频度数(O)不易探测度(D)风险顺序数RPN Recommende d Actions 建议的措施Responsibility &Target CompletionDate责任及目标完成日期级别(C)Potential Cause(s) /Mechanism(s) of Failure 潜在失效起因/机理严重度(S)Potential Effect(s)of Failure 潜在失效后果Potential Failure Mode 潜在失效模式A-1原材料进厂检验-进厂原材料应符合企业文件(四)《铸造业验收标准》Q/GJ Z8.2-01-2006的规定,以保证铸件产品质量。
铸件缺陷形成的PROCAST数值模拟
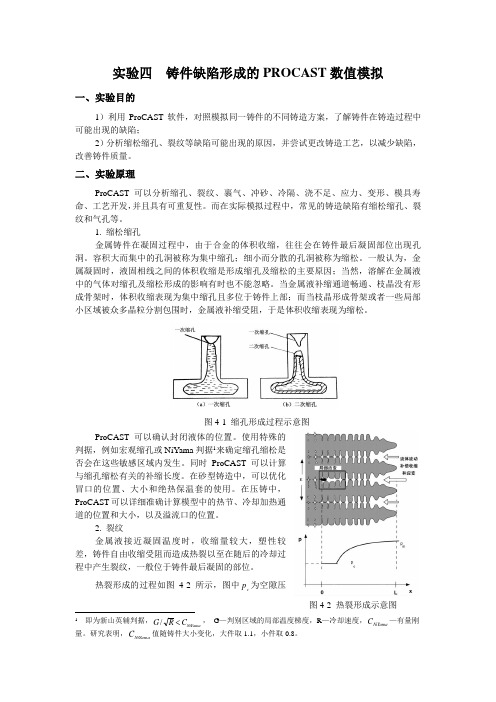
实验四 铸件缺陷形成的PROCAST 数值模拟一、实验目的1)利用ProCAST 软件,对照模拟同一铸件的不同铸造方案,了解铸件在铸造过程中可能出现的缺陷;2)分析缩松缩孔、裂纹等缺陷可能出现的原因,并尝试更改铸造工艺,以减少缺陷,改善铸件质量。
二、实验原理ProCAST 可以分析缩孔、裂纹、裹气、冲砂、冷隔、浇不足、应力、变形、模具寿命、工艺开发,并且具有可重复性。
而在实际模拟过程中,常见的铸造缺陷有缩松缩孔、裂纹和气孔等。
1. 缩松缩孔金属铸件在凝固过程中,由于合金的体积收缩,往往会在铸件最后凝固部位出现孔洞。
容积大而集中的孔洞被称为集中缩孔;细小而分散的孔洞被称为缩松。
一般认为,金属凝固时,液固相线之间的体积收缩是形成缩孔及缩松的主要原因;当然,溶解在金属液中的气体对缩孔及缩松形成的影响有时也不能忽略。
当金属液补缩通道畅通、枝晶没有形成骨架时,体积收缩表现为集中缩孔且多位于铸件上部;而当枝晶形成骨架或者一些局部小区域被众多晶粒分割包围时,金属液补缩受阻,于是体积收缩表现为缩松。
图4-1 缩孔形成过程示意图ProCAST 可以确认封闭液体的位置。
使用特殊的判据,例如宏观缩孔或NiYama 判据1来确定缩孔缩松是否会在这些敏感区域内发生。
同时ProCAST 可以计算与缩孔缩松有关的补缩长度。
在砂型铸造中,可以优化冒口的位置、大小和绝热保温套的使用。
在压铸中,ProCAST 可以详细准确计算模型中的热节、冷却加热通道的位置和大小,以及溢流口的位置。
2. 裂纹金属液接近凝固温度时,收缩量较大,塑性较差,铸件自由收缩受阻而造成热裂以至在随后的冷却过程中产生裂纹,一般位于铸件最后凝固的部位。
热裂形成的过程如图4-2所示,图中c p 为空隙压1即为新山英辅判据,NiYam a C R G /, G —判别区域的局部温度梯度,R —冷却速度,NiYama C —有量刚量。
研究表明,NiYama C 值随铸件大小变化,大件取1.1,小件取0.8。
MAGMASOFT 铸造仿真软件 介绍

【软件介绍】MAGMA SOFT铸造仿真软件MAGMA SOFT铸造仿真软件是全球最佳的压铸铸造软件工具,为铸造业提供改善铸品品质,制程条件,降低成本,增加竞争力的唯一选择。
铸型的充填、凝固、机械性能、残余应力及扭曲变形等的模拟为全面最佳化铸造工程提供了最可靠的保证。
以往只有对铸造工程参数及铸造质量的影响因素有透彻的了解,才能使铸造工程师对生产高质量的铸件拥有信心。
传统的方法对铸造工程的最佳化工作既耗资又费时,时程的压力使得很多铸造工程无法发挥全面的潜力。
MAGMASOFT软件中的专用模块满足您独特的需求。
MAGMA standard 标准模块 包括 :Project management module 项目管理模块Pre - processor 分析前处理模块MAGMA fill 流体流动分析模块MAGMA solid 热传及凝固分析模块MAGMA batch 制程仿真分析模块Post - processer 后处理显示模块Thermophysical Database 热物理材料数据库MAGMA lpdc 低压铸造专业模块MAGMA hpdc高压铸造专业模块MAGMA iron铸铁铸造专业模块MAGMA tilt 倾转浇铸铸造专业模块MAGMA roll-over浇铸翻转铸造专业模块MAGMA thixo 半凝固射出专业模块MAGMA stress 应力应变分析模块MAGMA disa 制程模块使用MAGMASOFT铸造仿真软件则是最经济、最方便的方式,它为以最低的成本生产高质量的铸件提供正确有效的解决方案。
MAGMASOFT铸造仿真软件的应用︰;铸造部件设计的开发;最佳化生产制程;新模具的生产;现有模具及铸型的更新;能源及材料方面的需求;清理工耗及费用;质量控制及完善工程档案;报价交货及时;以模拟结果获致客户信心,取得市场利基MAGMA SOFT直接协助工程师达成下列目标︰;铸造工艺及铸造材料的最佳化选择。
数值模拟结合实验验证克服铸件疏松缺陷-精选资料

数值模拟结合实验验证克服铸件疏松缺陷DOI:10.15938/j.jhust.2016.03.0170引言镁合金因其高比强度、高比刚度、高阻尼性能和优异的切削性能,在航空装备制造领域得到越来越多的应用,尤其是直升机或飞机传动系统的机匣壳体类铸件多为镁合金。
其中做为8 t级直升机的主减速器机匣,材质为ZM6,铸件重量为137 kg。
铸造方法为砂型重力铸造,铸件高度达846 mm。
对于浇注如此高的ZM6铸件,采用原始的随形冒口。
往往在冒口根部的法兰内部易产生疏松缺陷。
关于镁合金铸件缺陷的克服,国内外学者已进行了大量研究工作,从熔体处理、浇注工艺参数、热处理等工序人手,运用数值模拟和实验验证方法进行了研究,但缺少在真实铸件上应用的实例。
在此基础上,本文以8 t级直升机的主减速器机匣为例,针对原冒口下方易产生的疏松缺陷,提出一种新方案,旨在节约合金液用量,并减少过多合金液流经铸件对其产生的过热影响。
新方案将采用分散式保温冒口,保温冒口之间放置冷铁,得到修改后的铸件及其浇注系统的3D数模。
利用Magma5.2数值模拟软件,对修改后的3D数模进行数值模拟,然后自组装测温系统对数值模拟结果进行实验验证。
1研究方法与过程1.1合金材料主机匣材质为ZM6合金,见表1。
图1所示为ZM6的实测DSC 曲线,利用切线法标定出其凝固温度范围为(580~656)℃。
1.2研究方法利用Magma5.2对主机匣上法兰边的新方案进行数值模拟,根据数值模拟结果分析新方案的合理性,修理模具投产,再进行射线探伤验证。
1.3研究过程如图2为实验研究过程,针对现有主机匣随形常规冒口根部法兰内部的疏松问题,制定分散式保温冒口配合冷铁的模具修理方案,然后对新方案进行数值模拟,后对数值模拟结果进行温度场实验验证,最终确定模具修理方案。
2结果与分析2.1新方案的提出如图3(a)所示,为原主机匣的顶冒口结构,冒口截面相似于法兰边形状,在相邻的冒口之间设置小冷铁。
铸造CAD-CAE智能冒口工艺优化设计

铸造CAD/CAE智能冒口工艺优化设计2010-10-29 23:15:39 作者:廖敦明,陈立亮,周建新,魏鹏程,龚雪丹来源:互联网基于华铸CAE和UG平台,开发了铸造CAD/CAE铸钢件智能冒口优化设计CAD系统,实现铸造工艺设计(CAD)与模拟仿真(CAE)的紧密结合。
首先,使用CAE模拟得到不带冒口工艺的铸钢件的孤立液相区信息;接着应用二次开发技术,在UG显示孤立液相区,然后结合周界商法,自动建立冒口的三维模型;最后以简单铸件为例,进行了实际浇注实验.设计结果基本合理。
系统实现了冒口工艺的自动设计。
为模拟验证乃至实际生产提供较佳的推荐方案。
该技术能提高冒口工艺设计效率与精度,缩短设计周期,保证产品质量.提高工艺出品率。
铸造凝固模拟(CAE)技术可以在铸件实际浇注前对多个铸造工艺方案进行验证,预测缩孔、缩松、卷气、夹杂、裂纹、应力集中等常见铸造缺陷,为优化铸造工艺提供参考。
因为CAE的前提是必须要有一个初始工艺方案,所以目前CAE的作用还基本体现在对已有工艺方案的验证,不能智能地设计铸造工艺。
一个合理的铸造工艺依赖工艺人员丰富的专业知识和宝贵的经验,而对经验不足者,很难在短时间内得到合理的工艺方案。
即便借助CAE软件,由于对模拟显示结果的理解程度不同,基于模拟结果进行工艺优化的能力也因人而异。
专业技能知识,现场经验积累、软件的正确使用和熟练程度等,都决定了凝固模拟(CAE)与工艺优化设计(CAD)的有效衔接。
本研究以铸钢件的冒口智能优化为突破口,结合CAE模拟得到的铸件孤立液相区信息与周界商法,进行了铸钢件冒口的自动优化设计研究,实现了CAD与CAE 的耦合,开发出了一套基于UG(UniGraphics)和孤立液相区的铸钢件智能冒口优化设计系统。
1 智能化冒口工艺设计路线冒口的选择是铸造工艺设计中非常重要的一部分,同时是铸造工艺设计的难点所在。
常用的冒口设计方法包括模数法、补缩液量法、比例法、Q参数法、三次方程法、周界商法。
铸造成形工艺过程的数值模拟仿真及其应用

铸造成形工艺过程的数值模拟仿真及其应用王华侨;张颖;费久灿;王德跃【摘要】本文对国内外常用的几款铸造成形工艺模拟仿真软件的功能进行了简要介绍,希望对从事铸造行业的产品设计师、模具设计师、铸造工艺师提供一定的参考借鉴作用,从而为提高企业的铸造工艺水平搭建一个更好的优化设计,以及成形工艺的数字化工艺优化设计、制造、仿真集成的先进平台.【期刊名称】《金属加工:热加工》【年(卷),期】2011(000)005【总页数】6页(P59-64)【作者】王华侨;张颖;费久灿;王德跃【作者单位】中国三江航天集团国营红阳机械厂,湖北孝感,432100;中国三江航天集团国营红阳机械厂,湖北孝感,432100;中国三江航天集团国营红阳机械厂,湖北孝感,432100;中国三江航天集团国营红阳机械厂,湖北孝感,432100【正文语种】中文铸造仿真模拟优化软件是为评价和优化铸造产品与铸造工艺而开发的,借助于铸造仿真模拟优化软件系统平台,铸造工程师在完成铸造工艺编制之前,就能够对铸件在形成过程中的流场、温度场和应力场进行仿真分析并预测铸件的质量、优化铸造设备参数和工艺方案。
通过模拟金属铸造过程中的流动过程,精确显示充填不足、冷隔、裹气和热节的位置,以及残余应力与变形,准确地预测缩孔、缩松和铸造过程中微观组织的变化。
图1所示为铸造仿真模拟分析的典型过程。
本文对国内外常用的几款铸造成形工艺模拟仿真软件华铸CAE/InteCAST、AnyCasting、ProCAST等软件的功能与实例应用进行了简要介绍,希望对铸造行业的产品设计师、模具设计师、铸造工艺师提供一定的参考借鉴作用,从而为提高企业的铸造工艺水平搭建一个更好的优化设计,以及成形工艺的数字化工艺优化设计、制造、仿真集成的先进平台。
HZCAE/InteCAST是中国铸造领域著名的模拟分析系统,是分析和优化铸件铸造工艺的重要工具。
它以铸件充型过程、凝固过程数值模拟技术为核心对铸件进行铸造工艺分析。
NOVACAST模拟技术对压铸完整排气系统的验证

文章来源:安世亚太官方订阅号(搜索:peraglobal)本文描述了模拟金属液通过薄壁截面时,由于冷却和高背压导致的金属液停止流动,活塞不能推动金属液通过这些区域。
控制体积法这种新技术允许几乎任何设计的几何形状进行网格划分。
利用该仿真技术可以在非常合理的时间内再现铸件生产过程。
关键模拟技术:●使用体积分数精确定义几何模型(CVM-控制体积法)●结构化有限差分网格(FDM-有限差分法)●使用体数分数和N-S方程模拟液体流动●模具表面粗糙度●气体计算有限差分法控制体积法上图中,使用相同的网格数量划分同一薄壁压铸件,如果采用不同的方法,结果截然不同。
采用有限差分法,由于网格数量太少,导致几何完全失真。
使用控制体积法即使网格数量较少,但仍然能够通过体积分数来精确表达。
控制体积法网格图中是采用控制体积法划分网格的截面图中可以看出,青色部分为铸件金属液部分,薄壁处网格数量即使不足一层单元,仍然能够满足计算要求。
计算效率对比NOVACAST早期版本同大多数铸造仿真软件一样使用的是有限差分法,通过NFS团队不断的研究探索,重新开发软件后核心技术改用控制体积法,新的算法不但精度高,而且计算效率相对于有限差分法提高了5~10倍以上,大大缩短了工艺人员计算机试模的时间。
因此,如论是从模拟精度还是计算效率上,NOVACAST为实现又细又长的排气孔模拟验证工作提供可靠的仿真工具。
对于铸件和排气孔模拟问题,需要以下详细的信息:⏹哪些模具需要添加排气系统;⏹排气孔的位置⏹排气孔的尺寸⏹排气孔位置的冷却⏹冷铁的材料带冷铁块的排气系统深入研究后得到的模拟结果如下:⏹冷铁块的冷却影响⏹金属液流入排气孔和空气排出⏹几何背压⏹气体背压⏹通过薄壁截面时的金属液填充和流动⏹活塞在充填结束时由于填充面积减少而减速案例一:某铝合金高压铸件浇铸系统如上图所示,需要验证其排气系统设计。
模拟设置及工艺参数如下:●网格数量:120万●铸件材料:EN AC 46000(浇铸温度680℃)●模具材料:奥瓦儿(瑞典)产模具钢(预热温度220℃)●冷铁:铍铜(初始温度100℃)●压射速率:第一阶段=0.4米每秒;第二阶段=2.5米每秒●计算时间:完整的金属液充填流动和热平衡过程共花费40分钟●计算机:四核8G内存台式机●软件信息:NovaFlow & Solid CV 4.3r6(截至2017年底最新版本为6.3r3)模拟结果如下图所示金属液充填过程的速率场,为了方便研究压铸模具结构的排气系统,主要观察金属液充满型腔的后半段。
ProCAST 熔模铸造过程数值模拟
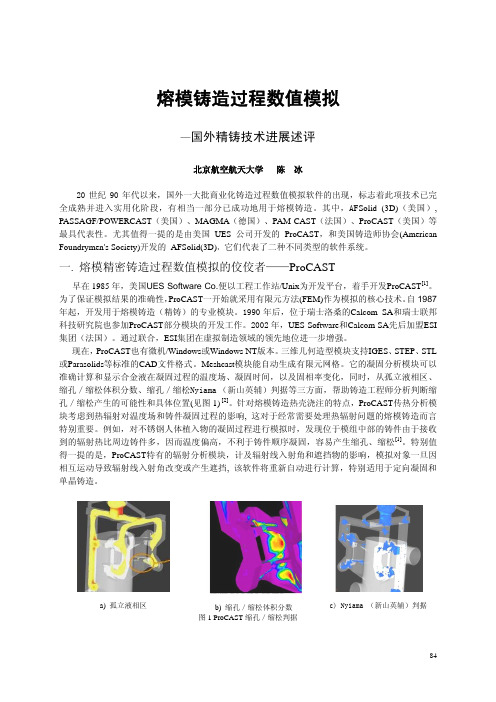
熔模铸造过程数值模拟—国外精铸技术进展述评北京航空航天大学陈冰20世纪90年代以来,国外一大批商业化铸造过程数值模拟软件的出现,标志着此项技术已完全成熟并进入实用化阶段,有相当一部分已成功地用于熔模铸造。
其中,A FSolid (3D)(美国), PASSAGF/POWERCAST(美国)、MAGMA(德国)、PAM-CAST(法国)、ProCAST(美国)等最具代表性。
尤其值得一提的是由美国UES公司开发的ProCAST,和美国铸造师协会(American Foundrymen's Society)开发的 AFSolid(3D),它们代表了二种不同类型的软件系统。
一. 熔模精密铸造过程数值模拟的佼佼者——ProCAST早在1985年,美国UES Software Co.便以工程工作站/Unix为开发平台,着手开发ProCAST[1]。
为了保证模拟结果的准确性,ProCAST一开始就采用有限元方法(FEM)作为模拟的核心技术。
自1987年起,开发用于熔模铸造(精铸)的专业模块。
1990年后,位于瑞士洛桑的Calcom SA和瑞士联邦科技研究院也参加ProCAST部分模块的开发工作。
2002年,UES Software和Calcom SA先后加盟ESI 集团(法国)。
通过联合,ESI集团在虚拟制造领域的领先地位进一步增强。
现在,ProCAST也有微机/Windows或Windows NT版本。
三维几何造型模块支持IGES、STEP、STL 或Parasolids等标准的CAD文件格式。
Meshcast模块能自动生成有限元网格。
它的凝固分析模块可以准确计算和显示合金液在凝固过程的温度场、凝固时间,以及固相率变化,同时,从孤立液相区、缩孔/缩松体积分数、缩孔/缩松Nyiama (新山英辅)判据等三方面,帮助铸造工程师分析判断缩孔/缩松产生的可能性和具体位置(见图1) [2]。
针对熔模铸造热壳浇注的特点,ProCAST传热分析模块考虑到热辐射对温度场和铸件凝固过程的影响, 这对于经常需要处理热辐射问题的熔模铸造而言特别重要。