常见冲压质量问题及解决—产生冲压件质量缺陷的分析-完整版
常见冲压质量问题及解决—产生冲压件质量缺陷的分析 ppt课件
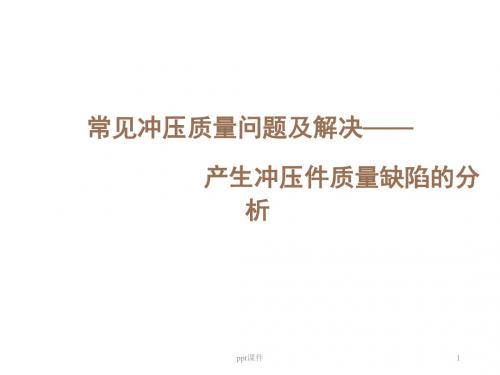
ppt课件
3
1.1 间隙 冲裁间隙过大、过小或不均匀均可产生毛刺。影响间隙过大、过小或不均匀的 有如下因素: a 模具制造误差-冲模零件加工不符合图纸、底板平行度不好等; b 模具装配误差-导向部分间隙大、凸凹模装配不同心等; c 压力机精度差—如压力机导轨间隙过大,滑块底面与工作台表面的平行度不 好 ,或是滑块行程与压力机台面的垂直度不好,工作台刚性差,在冲裁时 产生挠度,均能引起间隙的变化;
1.2可靠的定位方法
毛坯的定位形式主要有以外形为基准和以孔为基准两种。外形定位操作 方便,但定位准确性较差 。孔定位方式操作不大方便,使用范围较窄,但 定位准确可靠。在特定的条件下,有时用外形初定位,大致使毛坯控制在一 定范围内,最后以孔位最后定位,吸取两者的优点,使之定位即准确又操作 方便。
ppt课件
2.2.2 压料面的进料阻力太小,进料过多而起皱。这时可调节外滑块压力或改 变拉深毛坯局部形状,增加压料面积来消除,或局部增加拉深筋来增大进料 阻力。 2.2.3 压料面接触不好,严重时形成里松外紧。材料通过外紧区域后压料圈就 失去压料作用,造成进料过多,产生皱纹。这时要重新研磨压料面,保证全 面接触,允许稍有里紧外松。 2.2.4涂油润滑过多。
ppt课件 6
小结: 毛刺的产生,不仅使冲裁以后的变形工序由于产生应力集中 而容易开裂,同时也给后续工序毛坯的分层带来困难。大的毛刺 容易把手划伤;焊接时两张钢板接合不好,易焊穿,焊不牢;铆 接时则易产生铆接间隙或引起铆裂。 因此,出现允许范围以外的毛刺是极其有害的。对已经产生 的毛刺可用锉削、滚光、电解、化学处理等方法来消除。
ppt课件
7
孔变形,凸焊螺 母后不易取出
孔毛刺,凸焊 螺母困难
ppt课件
常见冲压质量问题及解决之冲裁件的常见缺陷及原因分析
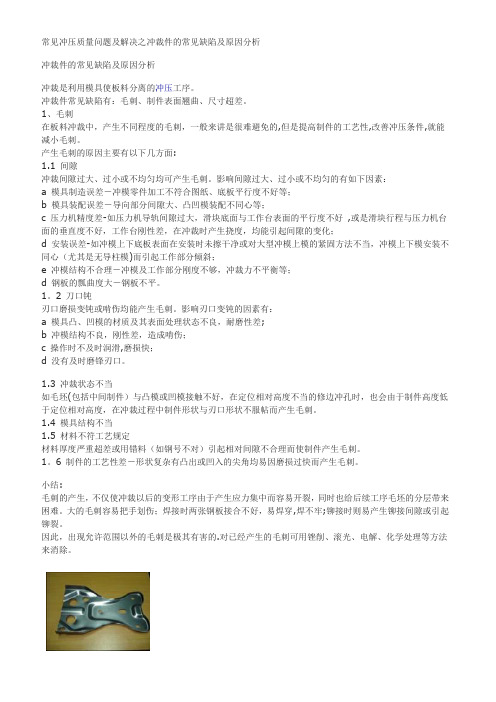
常见冲压质量问题及解决之冲裁件的常见缺陷及原因分析冲裁件的常见缺陷及原因分析冲裁是利用模具使板料分离的冲压工序。
冲裁件常见缺陷有:毛刺、制件表面翘曲、尺寸超差。
1、毛刺在板料冲裁中,产生不同程度的毛刺,一般来讲是很难避免的,但是提高制件的工艺性,改善冲压条件,就能减小毛刺。
产生毛刺的原因主要有以下几方面:1.1 间隙冲裁间隙过大、过小或不均匀均可产生毛刺。
影响间隙过大、过小或不均匀的有如下因素:a 模具制造误差-冲模零件加工不符合图纸、底板平行度不好等;b 模具装配误差-导向部分间隙大、凸凹模装配不同心等;c 压力机精度差-如压力机导轨间隙过大,滑块底面与工作台表面的平行度不好,或是滑块行程与压力机台面的垂直度不好,工作台刚性差,在冲裁时产生挠度,均能引起间隙的变化;d 安装误差-如冲模上下底板表面在安装时未擦干净或对大型冲模上模的紧固方法不当,冲模上下模安装不同心(尤其是无导柱模)而引起工作部分倾斜;e 冲模结构不合理-冲模及工作部分刚度不够,冲裁力不平衡等;d 钢板的瓢曲度大-钢板不平。
1。
2 刀口钝刃口磨损变钝或啃伤均能产生毛刺。
影响刃口变钝的因素有:a 模具凸、凹模的材质及其表面处理状态不良,耐磨性差;b 冲模结构不良,刚性差,造成啃伤;c 操作时不及时润滑,磨损快;d 没有及时磨锋刃口。
1.3 冲裁状态不当如毛坯(包括中间制件)与凸模或凹模接触不好,在定位相对高度不当的修边冲孔时,也会由于制件高度低于定位相对高度,在冲裁过程中制件形状与刃口形状不服帖而产生毛刺。
1.4 模具结构不当1.5 材料不符工艺规定材料厚度严重超差或用错料(如钢号不对)引起相对间隙不合理而使制件产生毛刺。
1。
6 制件的工艺性差-形状复杂有凸出或凹入的尖角均易因磨损过快而产生毛刺。
小结:毛刺的产生,不仅使冲裁以后的变形工序由于产生应力集中而容易开裂,同时也给后续工序毛坯的分层带来困难。
大的毛刺容易把手划伤;焊接时两张钢板接合不好,易焊穿,焊不牢;铆接时则易产生铆接间隙或引起铆裂。
常见冲压质量问题及解决—产生冲压件质量缺陷的分析 ppt课件
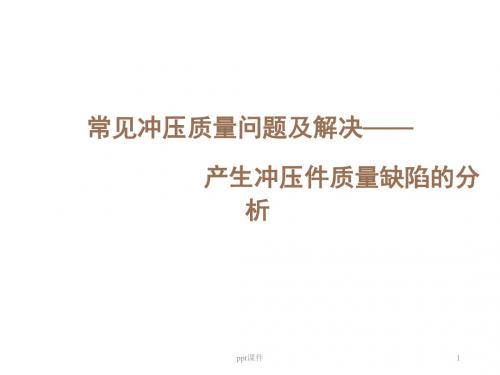
1.2可靠的定位方法
毛坯的定位形式主要有以外形为基准和以孔为基准两种。外形定位操作 方便,但定位准确性较差 。孔定位方式操作不大方便,使用范围较窄,但 定位准确可靠。在特定的条件下,有时用外形初定位,大致使毛坯控制在一 定范围内,最后以孔位最后定位,吸取两者的优点,使之定位即准确又操作 方便。
ppt课件
ppt课件 6
小结: 毛刺的产生,不仅使冲裁以后的变形工序由于产生应力集中 而容易开裂,同时也给后续工序毛坯的分层带来困难。大的毛刺 容易把手划伤;焊接时两张钢板接合不好,易焊穿,焊不牢;铆 接时则易产生铆接间隙或引起铆裂。 因此,出现允许范围以外的毛刺是极其有害的。对已经产生 的毛刺可用锉削、滚光、电解、化学处理等方法来消除。
2.2.2 压料面的进料阻力太小,进料过多而起皱。这时可调节外滑块压力或改 变拉深毛坯局部形状,增加压料面积来消除,或局部增加拉深筋来增大进料 阻力。 2.2.3 压料面接触不好,严重时形成里松外紧。材料通过外紧区域后压料圈就 失去压料作用,造成进料过多,产生皱纹。这时要重新研磨压料面,保证全 面接触,允许稍有里紧外松。 2.2.4涂油润滑过多。
ppt课件 12
二、弯曲件的常见缺陷及原因分析
弯曲件常见缺陷有:形状与尺寸不 符、弯裂、表面擦伤、挠度和扭曲 取措施以减少回弹 外,提高毛坯定位的可靠性也是很 重要的,通常采用以下两种措施;
ppt课件
13
1.1压紧毛坯 采用气垫、橡皮或弹簧产生压紧力,在弯曲开始前就把板料压紧。为达 到此目的,压料板或压料杆的顶出高度应做得比凹模平面稍高一些。
ppt课件
11
3、尺寸精度超差 3.1 模具刃口尺寸制造超差 3.2 冲裁过程中的回弹、上道工序的制件形状与下道工序模具工 作部分的支承面形状不一致,使制件在冲裁过程中发生变形,冲 裁完毕后产生弹性回复,因而影响尺寸精度。 3.3 板形不好。 3.4 多工序的制件由于上道工序调整不当或圆角磨损,破坏了变 形时体积均等的原则,引起了冲裁后尺寸的变化。 3.5 由于操作时定位不好,或者定位机构设计得不 好,冲裁过 程中毛坯发生了窜动。或者由于剪切件的缺陷(棱形度、缺边等 )而引起定位的不准,均能引起尺寸超差。 3.6 冲裁顺序不对。
常见冲压质量问题及解决之冲裁件的常见缺陷及原因分析

常见冲压质量问题及解决之冲裁件的常见缺陷及原因分析冲裁件的常见缺陷及原因分析冲裁是利用模具使板料分离的冲压工序。
冲裁件常见缺陷有:毛刺、制件表面翘曲、尺寸超差。
1、毛刺在板料冲裁中,产生不同程度的毛刺,一般来讲是很难避免的,但是提高制件的工艺性,改善冲压条件,就能减小毛刺。
产生毛刺的原因主要有以下几方面:1.1 间隙冲裁间隙过大、过小或不均匀均可产生毛刺。
影响间隙过大、过小或不均匀的有如下因素:a 模具制造误差-冲模零件加工不符合图纸、底板平行度不好等;b 模具装配误差-导向部分间隙大、凸凹模装配不同心等;c 压力机精度差—如压力机导轨间隙过大,滑块底面与工作台表面的平行度不好,或是滑块行程与压力机台面的垂直度不好,工作台刚性差,在冲裁时产生挠度,均能引起间隙的变化;d 安装误差—如冲模上下底板表面在安装时未擦干净或对大型冲模上模的紧固方法不当,冲模上下模安装不同心(尤其是无导柱模)而引起工作部分倾斜;e 冲模结构不合理-冲模及工作部分刚度不够,冲裁力不平衡等;d 钢板的瓢曲度大-钢板不平。
1.2 刀口钝刃口磨损变钝或啃伤均能产生毛刺。
影响刃口变钝的因素有:a 模具凸、凹模的材质及其表面处理状态不良,耐磨性差;b 冲模结构不良,刚性差,造成啃伤;c 操作时不及时润滑,磨损快;d 没有及时磨锋刃口。
1.3 冲裁状态不当如毛坯(包括中间制件)与凸模或凹模接触不好,在定位相对高度不当的修边冲孔时,也会由于制件高度低于定位相对高度,在冲裁过程中制件形状与刃口形状不服帖而产生毛刺。
1.4 模具结构不当1.5 材料不符工艺规定材料厚度严重超差或用错料(如钢号不对)引起相对间隙不合理而使制件产生毛刺。
1.6 制件的工艺性差-形状复杂有凸出或凹入的尖角均易因磨损过快而产生毛刺。
小结:毛刺的产生,不仅使冲裁以后的变形工序由于产生应力集中而容易开裂,同时也给后续工序毛坯的分层带来困难。
大的毛刺容易把手划伤;焊接时两张钢板接合不好,易焊穿,焊不牢;铆接时则易产生铆接间隙或引起铆裂。
冲压件常见质量缺陷及原因分析整改对策
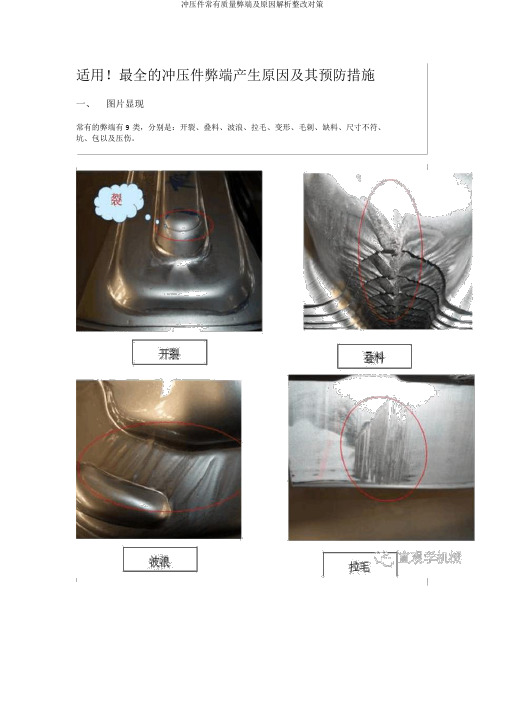
适用!最全的冲压件弊端产生原因及其预防措施一、图片显现常有的弊端有 9 类,分别是:开裂、叠料、波浪、拉毛、变形、毛刺、缺料、尺寸不符、坑、包以及压伤。
二、冲压件弊端原因及预防1.冲压废品1〕原因:原资料质量低质;冲模的安装调整、使用不当;操作者没有把条料正确的沿着定位送料也许没有保证条料按必然的缝隙送料;冲模由于长远使用,发生缝隙变化或自己工作零件及导向零件磨损;冲模由于受冲击振动时间过长紧固零件松动使冲模各安装地址发生相对变化;操作者的马虎,没有按操作规程进行操作。
2〕对策:原资料必定与规定的技术条件相吻合 (严格检查原资料的规格与牌号,在有条件的情况下对尺寸精度和表面质量要求高的工件进行化验检查。
);对于工艺规程中所规定的各个环节应全面的严格的遵守;所使用的压力机和冲模等工装设备,应保证在正常的工作状态下工作;生产过程中建立起严格的检验制度,冲压件首件必然要全面检查,检查合格后才能投入生产,同时加强巡检,当发买卖外时要及时办理; >前沿数控技术微信不错,记得关注。
坚持文明生产制度,如工件和坯件的传达必然要用适合的工位器具,否那么会压伤和擦伤工件表面影响到工件的表面质量;在冲压过程中要保证模具腔内的干净,工作场所要整理的有条理加工后的工件要摆放整齐。
2.冲裁件毛刺1〕原因:冲裁缝隙太大、太小或不均匀;冲模工作局部刃口变钝;凸模和凹模由于长远的受振动冲击而中心线发生变化,轴线不重合,产生单面毛刺。
2〕对策:保证凸凹模的加工精度和装置质量,保证凸模的垂直度和承受侧压力及整个冲模要有足够的刚性;在安装凸模时必然要保证凸凹模的正确缝隙并使凸凹模在模具固定板上安装牢固,上下模的端面要与压力机的工作台面保持相互平行;要求压力机的刚性要好,弹性变形小,道轨的精度以及垫板与滑块的平行度等要求要高;要求压力机要有足够的冲裁力;冲裁件剪裂断面赞同毛刺的高度冲裁板材厚度 >0.3>0.3-0.5>0.5-1.0>1.0-1.5>1.5-2.0新试模毛刺高度≤0.015≤0.02≤0.03≤0.04≤0.05生产时赞同的毛刺高度≤0.05≤0.08≤0.10≤0.13≤0.153.冲裁件产生翘曲变形1〕原因:有缝隙作用力和反作用力不在一条线上产生力矩。
常见冲压质量问题及解决—产生冲压件质量缺陷的分析

9
孔不同心原因: 1.弯曲高度不够 2.毛坯发生滑动 3.回弹 4.弯曲平面上出现起伏现象 弯曲线和两孔中心线不平行弯曲高度小于最小弯曲高度的 部位在弯曲后呈现出向外张口形状。
◆确保左右弯曲高度正确。 ◆修正磨损后的定位销和定位板, ◆减少回弹保证两弯曲面的平行度和平面度。 ◆改变工艺路线,先弯曲校正后进行冲孔。
冲压件的缺陷及其预防措施
序号 缺陷 1 废品 原因 1.原材料质量低劣; 2.冲模的安装调整、使用不当; 3.操作者没有把条料正确的沿着定位送料或者没有保证条 料按一定的间隙送料; 4.冲模由于长期使用,发生间隙变化或本身工作零件及导 向零件磨损; 5.冲模由于受冲击振动时间过长紧固零件松动使冲模各安 装位臵发生相对变化; 6.操作者的疏忽,没有按操作规程进行操作。 措施 ◆原材料必须与规定的技术条件相符合(严格检查原材料的规格与牌号,在有 条件的情况下对尺寸精度和表面质量要求高的工件进行化验检查。) ◆对于工艺规程中所规定的各个环节应全面的严格的遵守; ◆所使用的压力机和冲模等工装设备,应保证在正常的工作状态下工作; ◆生产过程中建立起严格的检验制度,冲压件首件一定要全面检查,检查合 格后才能投入生产,同时加强巡检,当发生意外时要及时处理; ◆坚持文明生产制度,如工件和坯件的传送一定要用合适的工位器具,否则 会压伤和擦伤工件表面影响到工件的表面质量; ◆在冲压过程中要保证模具腔内的清洁,工作场所要整理的有条理加工后的 工件要摆放整齐。
冲压件的缺陷及其预防措施 弯曲件弯曲部位 产生裂纹(弯曲 序号 变形区的内应力 缺陷 原因 措施 超过材料的强度 2.弯曲工件时最好使弯曲方向和材料的纤维方向(辗轧方 极限) 向)垂直。 3.弯曲半径不能太小,在质量允许的情况下尽量使圆角半 径加大。 4.弯曲坯件表面要光洁,无明显的凸起及疤痕。 5.弯曲时采用中间退火工序,使其消除内应力,经软化后 的弯曲很少产生裂纹。 6.弯曲时对于大型弯曲件一定要涂以润滑剂,以减少弯曲 过程中的摩擦。 7 弯曲件在弯曲过 在弯曲过程中坯件沿着凹模表面滑动时,会受到摩擦阻 ◆形状不对称的弯曲件,采用对称弯曲成形(单面弯曲件采用两件对称弯曲后 程中的偏移 力,若坯料两侧的摩擦阻力相差较大时,坯件会向摩擦阻 再切开) 力较大的一侧偏移。 ◆在弯曲模上增加弹性压料装臵,以便在弯曲时能全胬压住坯料防止移动。 ◆采用内孔及外形定位形式使其定位准确
常见冲压质量问题及解决产生冲压件质量缺陷的分析

3.3 板形不好。
3.4 多工序的制件由于上道工序调整不当或圆角磨损,破坏了变 形时体积均等的原则,引起了冲裁后尺寸的变化。
3.5 由于操作时定位不好,或者定位机构设计得不 好,冲裁过 程中毛坯发生了窜动。或者由于剪切件的缺陷(棱形度、缺边等 )而引起定位的不准,均能引起尺寸超差。
2.1材料塑性差。 2.2弯曲线与板料轧纹方向夹角不符合规定
排样时,单向V形弯曲时,弯曲线应垂直于轧纹方向;双向弯曲 时,弯曲线与轧纹方向最好成45度。 2.3弯曲半径过小。 2.4毛坯剪切和冲裁断面质量差——毛刺、裂纹。 2.5凸凹模圆角半径磨损或间隙过小——进料阻力增大。 2.6润滑不够——摩擦力较大 2.7料厚尺寸严重超差——进料困难 2.8酸洗质量差
b 模具装配误差-导向部分间隙大、凸凹模装配不同心等;
c 压力机精度差—如压力机导轨间隙过大,滑块底面与工作台表 面的平行度不好 ,或是滑块行程与压力机台面的垂直度不好 ,工作台刚性差,在冲裁时产生挠度,均能引起间隙的变化;
d 安装误差—如冲模上下底板表面在安装时未擦干净或对大型冲 模上模的紧固方法不当,冲模上下模安装不同心(尤其是无导 柱模)而引起工作部分倾斜;
在板料冲裁中,产生不同程度的毛刺 ,一般来讲是很难避免的,但是提高制件 的工艺性,改善冲压条件,就能减小毛刺 。..
产生毛刺的原因主要有以下几方面:
1.1 间隙
冲裁间隙过大、过小或不均匀均可产生毛刺。影响间隙过大、过 小或不均匀的有如下因素:
a 模具制造误差-冲模零件加工不符合图纸、底板平行度不好等 ;
常见冲压质量问题及解决-产生冲压件质量缺陷的分析

产生的原因可能是材料质量差、成型工艺不当、热处理不当等。解决方法包括加强原材料的质量控制、优化成型 工艺、选择合适的热处理工艺等。
02 冲压件质量缺陷分析
材料问题
总结词
材料问题是导致冲压件质量缺陷的重要因素之一。
详细描述
如果使用的材料质量不佳,如厚度不均、表面粗糙、内部组织不均匀等,会导致冲压件出现裂纹、变 形、翘曲等质量缺陷。因此,选择合适的材料,确保其厚度、表面质量和内部组织均匀是避免冲压件 质量问题的关键。
细心是避免冲压件质量问题的关键。
03 提高冲压件质量的措施
选用高质量的材料
总结词
选用高质量的材料是提高冲压件质量的 关键措施之一。
VS
详细描述
在选择材料时,应考虑材料的机械性能、 化学成分、表面质量等因素,以确保材料 具有足够的强度、塑性和韧性,以及良好 的表面光洁度,从而减少冲压过程中的开 裂、起皱、拉裂等问题。
THANKS FOR WATCHING
感谢您的观看
优化工艺参数是提高冲压件质量的有效措施之一。
详细描述
工艺参数的优化包括冲压力、行程、速度、时间等方 面的调整。通过对这些参数的合理设置,可以减小冲 压过程中的冲击和振动,避免材料过度变形和热量积 累,从而提高冲压件的尺寸精度和表面质量。
加强操作人员的培训和考核
总结词
加强操作人员的培训和考核是提高冲压件质量的必要措 施之一。
形状变形
总结词
形状变形是指冲压件在成型过程中出 现的扭曲、翘曲、波浪形等不规则形 状变化,影响产品的形状精度和稳定 性。
详细描述
产生的原因可能是模具设计不合理、 压力不均匀、材料厚度不均等。解决 方法包括优化模具设计、调整压力分 布、选择合适的材料等。
常见冲压质量问题及解决之冲裁件的常见缺陷及原因分析

常见冲压质量问题及解决之冲裁件的常见缺陷及原因分析冲裁件的常见缺陷及原因分析冲裁是利用模具使板料分离的冲压工序。
冲裁件常见缺陷有:毛刺、制件表面翘曲、尺寸超差。
1、毛刺在板料冲裁中,产生不同程度的毛刺,一般来讲是很难避免的,但是提高制件的工艺性,改善冲压条件,就能减小毛刺。
产生毛刺的原因主要有以下几方面:1.1 间隙冲裁间隙过大、过小或不均匀均可产生毛刺。
影响间隙过大、过小或不均匀的有如下因素:a 模具制造误差-冲模零件加工不符合图纸、底板平行度不好等;b 模具装配误差-导向部分间隙大、凸凹模装配不同心等;c 压力机精度差—如压力机导轨间隙过大,滑块底面与工作台表面的平行度不好,或是滑块行程与压力机台面的垂直度不好,工作台刚性差,在冲裁时产生挠度,均能引起间隙的变化;d 安装误差—如冲模上下底板表面在安装时未擦干净或对大型冲模上模的紧固方法不当,冲模上下模安装不同心(尤其是无导柱模)而引起工作部分倾斜;e 冲模结构不合理-冲模及工作部分刚度不够,冲裁力不平衡等;d 钢板的瓢曲度大-钢板不平。
1.2 刀口钝刃口磨损变钝或啃伤均能产生毛刺。
影响刃口变钝的因素有:a 模具凸、凹模的材质及其表面处理状态不良,耐磨性差;b 冲模结构不良,刚性差,造成啃伤;c 操作时不及时润滑,磨损快;d 没有及时磨锋刃口。
1.3 冲裁状态不当如毛坯(包括中间制件)与凸模或凹模接触不好,在定位相对高度不当的修边冲孔时,也会由于制件高度低于定位相对高度,在冲裁过程中制件形状与刃口形状不服帖而产生毛刺。
1.4 模具结构不当1.5 材料不符工艺规定材料厚度严重超差或用错料(如钢号不对)引起相对间隙不合理而使制件产生毛刺。
1.6 制件的工艺性差-形状复杂有凸出或凹入的尖角均易因磨损过快而产生毛刺。
小结:毛刺的产生,不仅使冲裁以后的变形工序由于产生应力集中而容易开裂,同时也给后续工序毛坯的分层带来困难。
大的毛刺容易把手划伤;焊接时两张钢板接合不好,易焊穿,焊不牢;铆接时则易产生铆接间隙或引起铆裂。