dt!_复合材料制备技术讲义(9)-拉挤成型实例
复合材料的挤出成型
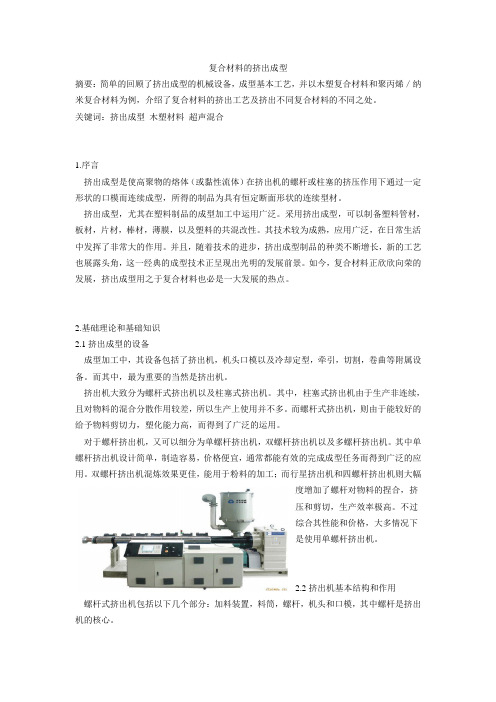
复合材料的挤出成型摘要:简单的回顾了挤出成型的机械设备,成型基本工艺,并以木塑复合材料和聚丙烯/纳米复合材料为例,介绍了复合材料的挤出工艺及挤出不同复合材料的不同之处。
关键词:挤出成型木塑材料超声混合1.序言挤出成型是使高聚物的熔体(或黏性流体)在挤出机的螺杆或柱塞的挤压作用下通过一定形状的口模而连续成型,所得的制品为具有恒定断面形状的连续型材。
挤出成型,尤其在塑料制品的成型加工中运用广泛。
采用挤出成型,可以制备塑料管材,板材,片材,棒材,薄膜,以及塑料的共混改性。
其技术较为成熟,应用广泛,在日常生活中发挥了非常大的作用。
并且,随着技术的进步,挤出成型制品的种类不断增长,新的工艺也展露头角,这一经典的成型技术正呈现出光明的发展前景。
如今,复合材料正欣欣向荣的发展,挤出成型用之于复合材料也必是一大发展的热点。
2.基础理论和基础知识2.1挤出成型的设备成型加工中,其设备包括了挤出机,机头口模以及冷却定型,牵引,切割,卷曲等附属设备。
而其中,最为重要的当然是挤出机。
挤出机大致分为螺杆式挤出机以及柱塞式挤出机。
其中,柱塞式挤出机由于生产非连续,且对物料的混合分散作用较差,所以生产上使用并不多。
而螺杆式挤出机,则由于能较好的给予物料剪切力,塑化能力高,而得到了广泛的运用。
对于螺杆挤出机,又可以细分为单螺杆挤出机,双螺杆挤出机以及多螺杆挤出机。
其中单螺杆挤出机设计简单,制造容易,价格便宜,通常都能有效的完成成型任务而得到广泛的应用。
双螺杆挤出机混炼效果更佳,能用于粉料的加工;而行星挤出机和四螺杆挤出机则大幅度增加了螺杆对物料的捏合,挤压和剪切,生产效率极高。
不过综合其性能和价格,大多情况下是使用单螺杆挤出机。
2.2挤出机基本结构和作用螺杆式挤出机包括以下几个部分:加料装置,料筒,螺杆,机头和口模,其中螺杆是挤出机的核心。
2.2.1螺杆的结构和几何参数螺杆是一根笔直的有螺纹的金属圆棒,其表面光洁,并具有很高的硬度。
拉挤成型原理及其制造工艺PPT
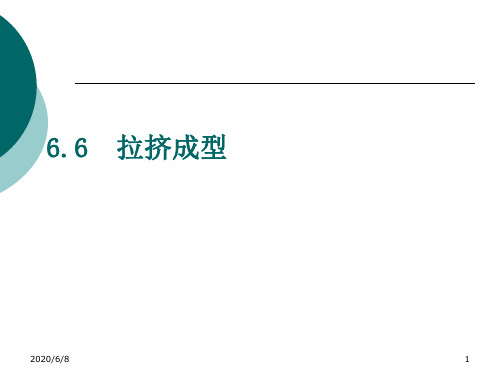
2020/6/8
4
2020/6/8
5
2020/6/8
6
(2)树脂浸渍:
是将排布整齐的增强纤维均匀浸渍上已配制 好的不饱和树脂的过程,一般是采用将纤维 通过装有树脂胶槽时进行的。一般分为:
2020/6/8
11
(1)送纱装置
作用 将无捻粗纱从安装在纱架上的纱筒中引出, 通过导纱装置进入浸胶槽浸胶。
最简单的送纱装置是纱架。 纱架结构及大小取决于产品规格及所用纱团的
数量。纱架结构根据需要可制成整体式或组合 式。纱筒在纱架上可以纵向或横向安装. 需要精确导向时,通常使用孔板导纱器或塑料管 导纱器.
2020/6/8
12
(2) 浸胶装置
浸胶装置一般包括导向辊、树脂槽、压辊、分纱栅 板、挤胶辊等。由纱架引出的玻璃纤维粗纱,在浸胶 槽中浸渍树脂,并通过挤胶辊的加紧来控制树脂含量。 胶槽长度根据浸胶时间长短和玻璃纤维运行速度而定。 胶槽中的胶液应连续不断地循环更新,以防止因胶液 中溶剂挥发造成树脂粘度加大,胶槽一般采用夹层结 构,通过调控夹套中的水温来保持胶液的温度。挤胶 辊的作用是使树脂进一步浸渍增强材料,同时起到控 制含胶量和排气的作用。分栅板的作用是将浸渍树脂 后的玻璃纤维无捻粗纱分开。确保按设计的要求合理 分布,
2020/6/8
17
2020/6/8
18
(4)固化炉
在拉挤成型中,处于一定固化度的玻璃钢型材拉出 模具后,再进入固化环境以保证制品充分固化所需 的装置。固化炉温度要严格控制并与牵引速度相适 应。固化炉的结构取决于制品形状及几何尺寸。
拉挤成型工艺及应用

展-囝1为现今的拉挤成型工艺流程示意图。
拉挤成型工艺及应用黄克均张建伟.济南250031)内容提要概述拉挤成型工艺及其应用前景,通过对拉挤成«工艺与其它复合材料加工工艺的 比较,阐述了拉挤戋型工艺的特点和这种新的复合材料加工工艺在航空、躭天、交通、电气、化工和建 筑等领域的发展潜力。
关键词拉挤成5复合杈枰树脂材料工艺应明1前言拉挤成型工艺是复合材料的主要成型工艺方法 之一。
用拉挤成型工艺可以全自动地生产不变截面 的棒、板,如c 型槽(板)、丨型梁、圆柱棒、j 型棒等。
最初的拉挤制品是钓鱼竿和电机檜楔等。
自70年代 以来,拉挤成型工艺不断完善,拉挤成型制品应用范 围已遍及航天,航空、交通、建筑、化工和电气等各个 领域,甚至用来制造桥梁结构架、汽车和轮船传动轴 等主承力结90年代初拉挤制品的世界年产量 为复合材料总年产量的3%〜5%,达9万〜15万t, 其中美国占一半左右。
拉挤制品的年增长率达到 10%〜15%,是复合材料制品中增长最快的- 种[卜2拉挤工艺过程21拉挤工艺拉挤成型工艺是指将浸溃了树脂的连续纤维粗 纱经加热模拉出形成预定截面型材的过程。
在拉挤 成型工艺的发展中,有三种同时发展起来的工艺:(1) 隧道炉拉挤工艺该工艺是把玻纤粗纱或 类似的增强材料牵引穿过树脂浴后,经过整形套管 除去包藏的空气和多余的树脂达到预定的直径,然 后牵引穿过隧道炉并悬空连续固化得到最终产品。
(2>间歜成型拉挤工艺该工艺是把增强纤维 牵引穿过树脂浸溃槽并进入对分式阴模,在脖止状 态下由模外加热固化。
通常模具的进入端要冷却以 防树脂固化.当一段增强纤维上的浸溃树脂完全固 化后,打开模具再把下一段牵引到模中。
(3)高频或微波加热拉挤工艺该工艺与上述 两种方法类似,但采用高銕或微波加热,这种方法树 脂固化速度快,在模内即可固化。
由于70年代初连续纤维毡的问世解决了拉挤 型材的横向强度问题,使拉挤成型工艺获得高速发1一纱团架>2纤维控制系统,3树脂浸溃槽;4 加热的模具,5牵引机,6切割锯 图1拉挤成型工艺流程图 通常拉挤过程包括纤维粗纱自纱团架经纤维控 制系统向前牵引,在浸溃槽中用适宜的浸溃树脂浸 润并整理,将合在一起的浸溃过树脂的纤维束穿过 成型模.使已成型的浸溃了树脂的预浸件穿过拉挤模等过程22材料拉挤成型工艺中使用的材料包括树脂、增强材料、无机填料和内脱模剂等[14〕。
拉挤成型工艺

拉挤成型工艺
拉挤成型工艺是指将目标材料拉伸并利用外力,在一定温度下让其外形、截面等特性发生变化,从而达到不同功能需求的一种成形工艺。
一、拉挤成型工艺的概述
1. 介绍
拉挤成型是针对金属、塑料等可加工的材料,利用机械加工手段,使材料在一定温度下拉伸、压缩,在外形、截面、特性上发生变化,改变材料原来的形状而达到指定目的的金属加工工艺。
2. 工艺特点
拉挤成型工艺是金属外形调整中最重要也是最基础的成形工艺之一,它具有生产效率高、工序简便、节约成本、表面状态好、后期处理少等优点,几乎可以覆盖金属外形调整的所有领域。
二、拉挤成型工艺的分类
1. 拉伸成型
拉伸成型工艺的原理是,将材料在固定的拉伸缸内,以所需要的温度和拉伸力拉伸,使其形状发生变化而达到指定成型目的。
2. 压缩成型
压缩成型工艺是一种以压力为所施加的外力,利用模具内挤压力在一定温度下,使硬物料的外形、截面或其它性能得到变化的一种工艺。
三、拉挤成型工艺的应用
1. 电子行业
在电子行业,拉挤成型工艺广泛应用于电线电缆的加工制作中,可以实现电缆以及其他电子元器件的制作、变径和改型。
2. 机械行业
拉挤成型是机械加工领域中金属零件的基本工艺,可以实现连杆、轴、活塞等机械零件的主体构建。
3. 其他行业
此外,除了电子行业和机械行业,拉挤成型工艺还可以应用于能源行业,如用于油钻管、制作锅炉、制作液压缸等;交通运输行业,可以制作法兰、轴箱、制作汽车、摩托车等等。
复合材料拉挤成型设备的生产流程优化设计

复合材料拉挤成型设备的生产流程优化设计随着科技的快速发展,复合材料在诸多领域中的应用越来越广泛。
其中,复合材料拉挤成型技术被广泛应用于航空航天、汽车、建筑和电子等领域。
为了提高生产效率和产品质量,对复合材料拉挤成型设备的生产流程进行优化设计显得尤为重要。
首先,为了确保成型产品的质量,生产流程的优化设计需要从原材料的选择和准备开始。
优质的原材料是生产出高品质产品的前提。
在选择原材料时,需要考虑其力学性能、热膨胀系数、流动性以及与挤压机的兼容性等因素。
同时,在原材料准备过程中,应确保材料的均匀性和稳定性,以避免在挤压过程中出现质量问题。
其次,挤压机的设计与调整对生产流程的优化至关重要。
挤压机是实现复合材料拉挤成型的核心设备,其结构和工作原理直接影响到产品的成型效果。
在设计挤压机时,应考虑到产品成型的要求,并尽可能实现自动化和智能化操作。
优化挤压机的结构可以提高其稳定性和可靠性,降低故障率,从而提高生产效率。
第三,确定合适的挤压工艺参数对于生产流程的优化设计非常重要。
挤压工艺参数包括挤压温度、挤压速度和挤压压力等。
通过合理地调整这些参数,可以实现成型产品的尺寸精度和表面质量的控制。
此外,在生产过程中,还需要不断监测和调整这些参数,确保产品的一致性和稳定性。
然后,设备的维护和保养也是生产流程优化设计中不可忽视的一部分。
定期对设备进行维护和保养,可以延长设备的使用寿命,减少故障和停机时间。
同时,应建立完善的设备维护记录和维修计划,及时发现和解决潜在问题,确保设备的正常运行。
最后,加强员工培训和管理,提高生产流程的效率和质量。
培训员工操作设备的正确方法和工艺流程,以提高工作效率和产品质量。
建立健全的质量控制体系,确保从原材料进厂到成品出厂的每一个环节都能得到严格把控和监管。
综上所述,复合材料拉挤成型设备的生产流程优化设计是提高生产效率和产品质量的重要手段。
通过合理选择原材料、优化挤压机设计、确定合适的挤压工艺参数、加强设备的维护和保养以及加强员工培训和管理,可以实现生产流程的优化,提高生产效率和产品质量,满足市场需求,提升企业的竞争力。
复合材料拉挤成型实例
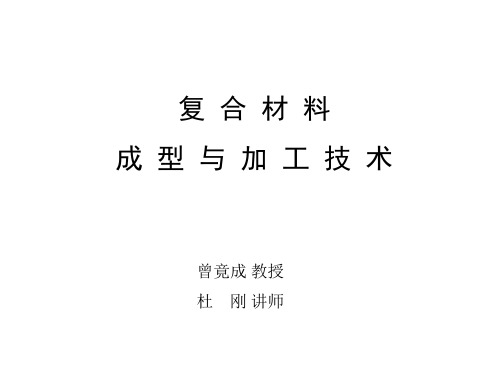
我国是建筑窗框产量最多的国家。
2. 拉挤玻璃钢窗框的工艺
材料:UP树脂+玻璃纤维+短切毡+表面毡; 温区控制:根据UP放热曲线确定; 拉挤速度; 纱量; 树脂配方。
3. 拉挤玻璃钢窗框模具
3.1模具的选材
(1)较高的强度,耐疲劳性和耐磨性; (2)较高的耐热性和较小的热变形性; (3)良好的耐腐蚀性; (4)良好的切削性和表面抛光性能; (5)受热变形小,尺寸稳定性好。
25~30 2~3
5. 成型模具加热区温度设定
加热一区
加热二区
加热三区
135 ℃
170~175 ℃
95 ℃
6. 工艺流程
选定树脂 配方体系
确定树脂体系的 固化温度区间
根据设计图纸 制备金属模具
根据模腔尺寸 计算纱用量
设计预成型模 和分纱导向板
配纱,安装模具
模具加热区 三区温度设定
观察制品表面情 况,继续或改进
复合材料 成型与加工技术
曾竟成 教授 杜 刚 讲师
第9章 拉挤制备技术(Pultrusion Process) 9.1 拉挤制备技术含义:
拉挤成型工艺是将浸渍树脂胶液的连续纤维束、带或布等,在牵 引力的作用下,通过挤压模具成型、固化,连续不断地生产长度不限的 玻璃钢型材。这种工艺最适于生产各种断面形状的型材,如棒、管、实 体型材(工字形、槽形、方形型材)和空腹型材(门窗型材、叶片等) 等。
9.9 拉挤制品常见的缺陷及改进措施
缺陷部位
现象
鸟巢
增强纤维在模具入口处相互缠绕,导致制 品在模具内破坏。
固化不稳定
在模具内粘附力突然增加,可引起制品在 模具内破坏。
复合材料-拉挤成型工艺-(综合版改)

复合材料拉挤成型工艺——纺硕1205班柴寅芳、丁倩、刘冰、刘小梅、戎佳琦、王卷1 拉挤成型定义拉挤成型是指玻璃纤维粗纱或其织物在外力牵引(外力拉拔和挤压模塑)下,经过浸胶、挤压成型、加热固化、定长切割,连续生产长度不限的玻璃钢线型制品的一种方法。
这种工艺最适于生产各种断面形状的型材,如棒、管、实体型(工字形、槽形、方形型材)和空腹型材(门窗型材、叶片)等。
2 拉挤成型的特点2.1优点:1)典型拉挤速度0.5-2m/min,效率高,适于批量生产,制造长尺寸制品;2)树脂含量可精确控制;3)主要用无捻粗纱增强,原材料成本低,多种增强材料组合使用,可调节制品力学性能;4)拉挤制品中纤维含量可高达80%,浸胶在张力下进行,能充分发挥连续纤维的力学性能,产品强度高;5)原材料利用率在95%以上,废品率低;6)制品纵、横向强度可任意调整,可以满足不同力学性能制品的使用要求。
2.2缺点:1)不能利用非连续增强材料;2)产品形状单调,只能生产线形型材(非变截面制品),横向强度不高;3)模具费用较高;4)一般限于生产恒定横截面的制品。
3 拉挤成型所需的材料拉挤成型工艺中使用的材料包括树脂、增强材料、辅助材料等。
3.1拉挤成型工艺所用树脂拉挤成型工艺要求所用的树脂黏度低,主要使用不饱和聚酯树脂和环氧树脂或改性环氧树脂。
不饱和聚酯树脂用作拉挤的基本上是邻苯和间苯型。
间苯型树脂有较好的力学性能、坚韧性、耐热性和耐腐蚀性能。
目前国内使用的较多的是邻苯型,因其价格较间苯型有优势。
环氧树脂和不饱和聚酯树脂相比,具有优良的力学性能、高介电性能、耐表面漏电、耐电弧,是优良绝缘材料。
常用拉挤工艺用树脂如表1所示,树脂生产配方如表2和表3。
表1拉挤工艺用树脂表2典型拉挤用不饱和聚酯树脂配方树脂 196 100份填料(轻质碳酸钙)脱模剂(硬脂酸锌)固化剂(过氧化物)低收缩剂(PVC树脂)颜料5~15份3~5份1~3份5~15份0.1~1份表 3环氧树脂配方环氧树脂 E-55脱模剂(硬脂酸锌)固化剂(590#)增韧剂100份3~5份15~20份10~15份适量稀释剂3.2拉挤成型工艺所用增强材料拉挤成型玻璃钢所用的纤维增强材料,主要是 E 玻璃纤维无捻粗纱居多,其优点是不产生悬垂现象,集束性好,易被树脂浸透,力学性能较高。
拉挤成型工艺及应用资料

粒径5?10 Mm。填料加入量一般为15%?40%,拉 挤工艺中常用的填料见表3。 拉挤工艺常W的脱模方法有下列4种: (1>在模具内成型料的表面放置脱模板; (2)在横具内壁涂脱模剂; (3)使用聚四氟乙烯等非粘材料制作模具; (4) 在成型料中预先加入脱模性好的内脱模糾。 实践证明方法(1)、(2)、(3)不能达到满意的脱 模效果。国外现已推出的拉挤成型工艺用脱模剂见 表4。 2. 3 模具 拉挤成型工艺使用的模具是用工具钢制成的。 为了将浸溃了树脂的增强纤维牵引通过加热的模 具,制成外观光洁美观的拉挤制品,在模具的设计与 加工中,一方面要提高加工精度,另方面要尽量提高 模腔内表面的粗糙度等级(通常采用镀铬或渗钽 法)。模腔内表面粗糙度等级高,既利于脱模又可咸 表1拉挤工艺用树脂 类型 商品牌号 生产厂家 性能与应用 聚酯 Dion 8200 Dion EP 34456 Hetron 197A Polylite 31-020 不饱和聚酯 4001A,B703 Koppers Koppers Ashland Ashland Re ic hold 日本1匕亡会社(株) 通过缓和升温引起的收缩反应,可解决热裂纹问题 在148. 9C下连续使用,用作抽油杆 反应型增韧剂与通用树脂混合使用可减缓歼温,减少 裂纹并能增加拉挤线速度 耐酸,但不耐碱和次氣酸盐 高活性间苯聚酯,可增加小直径杆与型材的拉挤速度 可提卨阻燃性,降低收缩率 溴化聚酯 Herron 613 Ashland 阻燃级树脂 乙烯基酯树脂 Hetron 922 Hetron 980 Derakane 411 — 35 ? 470-25 Ashland Af.hU nd Dow 射碱和次氣酸盐 高温F荇良好的物珲性能保持率?弔作抽油忏 阻燃剂含最低?拉挤线速賓高,苯乙烯含量低、钻度 高,用怍抽油杆,低填料量时有良好的物理性能和埘 高温性 环氧树脂 EPON 9102,9302 EPON 9310 TACTIX TETRAD-C.X ELM100,120 Shell Shell Dow 三菱瓦斯化学会社 (株) 大日本>夸化学会 社(株) 可提高拉挤速度,可用高频加热固化.粘度与收缩率 类似聚酯 推荐用于拉挤工艺 用予航天与航空结构件 可提高耐热性?用F制造飞机零部件 可提高耐磨性,用f航天航空结构件 表2拉挤成型工艺用增强材料 类型 商品 牌号 制造厂家 性能与应用 聚酯粗纱| Alhed 低模量,低性能,低成本 E —玻璃 通用品级 S-2玻 瑞463 适用于环氧树脂,可改善剪 切性能,降低成本 S-2玻 璃449 Owens 一 Corning 高性能,适甩J1军品 玻璃粗纱 425 424, 30型 常用56股和股粗纱, 低悬垂度,分散性好,工艺 性好 浸润性好,无悬垂度,常用 113股和256股粗纱;分敢 性和拉伸性能好,仅适用于 聚酯。加工条件苛刻时易断 E—玻璃 PPG 通用品级 有机纤维 Kevlar — 49 Du Pont 轻质,用于航空、航天材料 和军用材料,中等成本 石墨布带 AS Hercules 轻质,成本高于Kevlar纤 维和玻璃纤维,用于刚性要 求高的场合 T300 Union Carbide 与AS相同 表3拉挤工艺用无机填料 硅酸盐类 碳酸盐类 硫酸盐类 氧化杓类 瓷土、高岭十. 碳酸钙 硫酸钡 水合氧化铝 粘卜.、滑6粉 硫酸钙 氧化铝 珍珠岩粉. 云母粉 沉积或气相 :氧化硅 A英粉
- 1、下载文档前请自行甄别文档内容的完整性,平台不提供额外的编辑、内容补充、找答案等附加服务。
- 2、"仅部分预览"的文档,不可在线预览部分如存在完整性等问题,可反馈申请退款(可完整预览的文档不适用该条件!)。
- 3、如文档侵犯您的权益,请联系客服反馈,我们会尽快为您处理(人工客服工作时间:9:00-18:30)。
3.4模具尺寸的确定 模具尺寸的确定
目前国内模具长度一般设计为 左右。 目前国内模具长度一般设计为900mm左右。一般模具厚度为制品厚 模具长度一般设计为 左右 一般模具厚度为制品厚 度的2~ 倍 度的 ~3倍。
玻璃钢窗框型材大多是中空制品,一般芯模具的有效长度为模具长 玻璃钢窗框型材大多是中空制品,一般芯模具的有效长度为 芯模具的有效长度 度的2/3~ ,而在拉挤工艺过程中要考虑到芯棒固定及调整以及防止 芯棒固定及调整以及 度的 ~3/4,而在拉挤工艺过程中要考虑到芯棒固定及调整以及防止 偏心,此外芯棒还要考虑到配重的问题, 考虑到配重的问题 偏心,此外芯棒还要考虑到配重的问题, 对于模具长度为 左右的模具, 可设计为1200mm 对于模具长度为900mm左右的模具,芯棒的长度可设计为 模具长度为 左右的模具 芯棒的长度可设计为 左右。 左右。
浸渍区:
预成型区(preforming area) : (1)赋于概略形状,可以降低纤维束与固化模入口处的摩 擦与多余树脂。 (2)赋于纤维束、mat、或其它补强材适当的位置,以进 入固化模。
固化区:
拉挤模具 (die) :赋于工件的形状 加热装置: 电热板 电波加热 热油循环
辅助加热:在含浸纤维入模口之前先行预加热(微波加 热) 。 优点:树脂所需热传导的时间缩短,模具长度可以缩短,用 于大型工件。
建立拉挤模具温度传递模型,利用计算机辅助设计可以确定最佳的模 具温度分布及分析。 牵引速度:是平衡固化程度和生产速度的参数。在保证固化度的条件下 应尽可能提高牵引速度。 牵引力:是保证制品顺利出模的关键,牵引力的大小由制品与模具之间 的界面上的剪切应力确定。 温度参数、拉挤速度、牵引力在三个参数中,温度参数是由树脂系统的 特性确定的,是拉挤工艺中首要解决的因素。通过树脂固化体系的放热 曲线的峰值和有关条件,确定模具加热的各段温度值。拉挤速度确定的 原则是在给定的模内温度下的凝胶时间,保证制品在模具中部凝胶、固 化。牵引力与模具温度关系很大,并受拉挤速度的控制。脱模剂的影响 也是重要因素。
(1)较高的强度,耐疲劳性和耐磨性; (2)较高的耐热性和较小的热变形性; (3)良好的耐腐蚀性; (4)良好的切削性和表面抛光性能; (5)受热变形小,尺寸稳定性好。
3.2分型面的选择
在满足模具制造的前提下,尽量减少分型面,保证合缝严密。
3.3模具入口设计 模具入口设计
模具入口处周边设计1/4倒角,带有锥度(角度在 ~ ° 模具入口处周边设计 倒角,带有锥度(角度在5~8°,长度在 倒角 50~100mm) ~ )
A-模具初始温度 B-工艺过程中最佳温度
B A
模腔温度分布曲线
基于UP/复合型引发剂的固化工艺特性,将模具分为加热温度不同的三 个区段。 (1)预热段 使增强材料浸渍的树脂匀化。 (2)固化段 使树脂体系从粘稠态经凝胶态、橡胶态而迅速固化。 (3)离型段 减少温差对型材的内应力和体积收缩的影响。 由于模具长度一定,加热设备长度也一定,故制品的固化温度和时间主 要取决于树脂的引发固化体系。通用的不饱和聚酯树脂,多采用有机过 氧化物为引发剂,其固化温度一般要略高于有机过氧化物的临界温度。 若采用协同引发剂体系,则通常是通过不饱和聚酯树脂固化放热曲线来 确定。一般地,模具的温度应大于树脂的放热峰值,温度的上限是树脂 的降解温度。同时做树脂的凝胶试验,保证温度、凝主要的拉挤制品(部分制品实例及应用)
9.4 拉挤成型工艺分类
1.卧式拉挤成型工艺 (1)间歇式 牵引机构间断工作,浸胶的纤维在热模中固化定型,然后牵引出模, 下一段浸胶纤维在进入热模中固化定型后,再牵引出模。 主要特点:成型物在模具中加热固化,固化时间不受限制。生产效率低, 制品表面易出现间断分界线。 (2)连续式 牵引机构连续工作。 主要特点:牵引和模塑过程均连续,生产效率高。成型制品质量关键是 控制凝胶时间和固化程度、模具温度和牵引速度。 2.立式拉挤成型工艺 宜生产空腹型材。
9.8 拉挤成型工艺参数
工艺参数:模腔温度、树脂温度、模腔压力、树脂粘度、固化速度、 固化程度、牵引张力及速度、纱团数量等。 模腔温度:用于拉挤的树脂体系对温度敏感,模腔温度控制严格。温 度低,树脂不能固化,温度过高时,坯料一入模就固化,使成型、牵 引困难,严重时会产生废品甚至损坏设备。
300 250 200 150 100 50
复 合 材 料 成 型 与 加 工 技 术
曾竟成 教授 杜 刚 讲师
第9章 拉挤制备技术(Pultrusion Process) 9.1 拉挤制备技术含义:
拉挤成型工艺是将浸渍树脂胶液的连续纤维束、带或布等,在牵 引力的作用下,通过挤压模具成型、固化,连续不断地生产长度不限的 玻璃钢型材。这种工艺最适于生产各种断面形状的型材,如棒、管、实 体型材(工字形、槽形、方形型材)和空腹型材(门窗型材、叶片等) 等。
未完全固化
白粉
沟痕, 沟痕,不平
制品的平面部分不平整, 制品的平面部分不平整,局部有沟状痕迹
纤维含量低, 纤维含量低,局部的纤维纱过少 模具粘制品, 模具粘制品,划伤制品 纱和毡浸渍树脂不完全,毡层过厚, 纱和毡浸渍树脂不完全,毡层过厚, 或毡的本身性能不好 有杂志混入, 有杂志混入,在毡层间形成气泡 制品表面树脂层过薄 裂纹只在表层, 裂纹只在表层,树脂层过厚产生表层 裂纹; 裂纹; 树脂固化不均引起热应力集中, 树脂固化不均引起热应力集中,形成 应力开裂。 应力开裂。 纤维过多 树脂与纤维不能充分粘结 留树脂层过厚 模具内压力不够 纤维含量太少 制品固化不均,非同步, 制品固化不均,非同步,产生固化应 力 制品出模后压力降低, 制品出模后压力降低,在应力作用下 变形 制品里的材料不均匀, 制品里的材料不均匀,导致固化收缩 程度不同 出模时制品未完全固化, 出模时制品未完全固化,在牵引力作 用下产生变形。 用下产生变形。
白斑
含有表面毡,连续毡的制品表层, 含有表面毡,连续毡的制品表层,出现局 部发白或露有白纱现象
裂纹
制品表面有微小裂纹
表面起毛 表面起皮、 表面起皮、 破碎
纤维露出制品表面
制品弯曲、 制品弯曲、 扭曲变形
实例1 拉挤玻璃钢窗框模具的设计(南玻纤院) 实例 拉挤玻璃钢窗框模具的设计(南玻纤院) 1. 拉挤玻璃钢窗框的前景
履帶式拉拔机构
往覆式拉拔机构
环形拉挤成型机
往复式拉拔机构
9.6 拉挤成型模具
一般由预成型模和成型模两部分组成。 ①预成型模具:在拉挤成型过程中,增强材料浸渍树脂后(或被浸渍的 同时),在进入成型模具前,必须经过由一组导纱元件组成的预成型模 具,预成型模的作用是将浸胶后的增强材料,按照型材断面配置形式, 逐步形成近似成型模腔形状和尺寸的预成型体,然后进入成型模,这样 可以保证制品断面含纱量均匀。 ②成型模具:成型模具横截面面积与产品横截面面积之比一般应大于或 等于10,以保证模具有足够的强度和刚度,加热后热量分布均匀和稳定。 拉挤模具长度是根据成型过程中牵引速度和树脂凝胶固化速度决定,以 保证制品拉出时达到脱模固化程度。一般采用钢镀铬,模腔表面要求光 洁,耐磨,借以减少拉挤成型是的摩擦阻力和提高模具的使用寿命。 模具设计的好坏,直接影响拉挤过程中所用牵引力大小,若牵引阻力 过大,易造成机械事故。经常因某段模具被拉毛,表面不够光滑,树脂 易固化,造成牵引机履带与轮之间打滑,致使玻璃纤维都固化在模具中, 牵引机拉不动。
典型的模具长度在30~150 cm 之间; 模具材料:工具钢; 模具形式:整体式、组合式、悬垂式(空腹结构)
拉拔区:
拉拔区提供工件拉挤时所需的拉拔力与速度控制,拉拔的方式主要有两种 履带式 (caterpillar) 及往覆式 (reciprocating) ,和环型迥旋式拉拔机构(结 合了拉拔与卷曲)。
实例2 玻璃钢型材-槽钢拉挤成型制备 项目来源:株洲广缘火车线槽
纱架 导向板 拉拔机构 成型模具
集束板 浸胶槽
预成型模
成型模具按结构形式可分为整体成型模具和组合式成型模具两类。整体模具 是由整体钢材加工而成,一般适用于棒材和管材。组合成型模具有上、下模 对合而成。这种类型的模具易于加工,可生产各种类型的型材,但制品表面 有分型线痕迹。 空腹制品采用芯模。芯模一端固定,另一端悬臂伸入上、下模所形成的空间, 与上、下模一起构成产品所需的截面形状。为减少脱模时芯模产生的阻力, 芯模尾部加工成1/300~1/200的锥度,较大的芯模应考虑采用模心加热装置。
9.7 拉挤成型用增强材料
用于拉挤制品的增强材料多为玻璃纤维及其织物,如无捻粗纱、布带和 各种毡。 无捻粗纱:不产生悬垂现象,集束性好,易被树脂浸透,力学性能较高; 玻璃纤维毡:有能承受牵引力的足够强度。 拉挤制品横向增强的主要方法:玻璃纤维毡和纤维织物,纤维环向缠绕 或螺旋缠绕(过去);纤维针织物(现在)。 纤维针织物:以单束纱线连续围绕交叉的形式重叠在一起,并相互缠结 固定。针织物单重均匀,强度高,弹性好且不易悬垂,可以提高制品的 冲击强度和剪切强度,并可加工成定向或三向织物。
9.5 拉挤制备技术的流程分布 (1) 纤维区 (2) 浸渍区 (3) 预成型区 (4) 固化区 (5) 拉拔区
纤维区:
以E-glass为主,和较高性能的S-glass及carbon。 纤 维 的 形 态 主 要 有 粗 纱 ( roving ) , 短 切 毡 (mat) , 及 表 面 毡 (surfacing veil),平面织物等。
20世纪80年代初开发(加拿大); 20世纪90年代,扩展到美国、俄罗斯、德国、日本等国;
我国是建筑窗框产量最多的国家。
2. 拉挤玻璃钢窗框的工艺
材料:UP树脂+玻璃纤维+短切毡+表面毡; 温区控制:根据UP放热曲线确定; 拉挤速度; 纱量; 树脂配方。
3. 拉挤玻璃钢窗框模具 3.1模具的选材
鸟巢
增强纤维在模具入口处相互缠绕, 增强纤维在模具入口处相互缠绕,导致制 品在模具内破坏。 品在模具内破坏。