橡胶硫化促进剂DZ合成工艺探讨
橡胶促进剂DZ的工艺研究与工业化初探的开题报告

橡胶促进剂DZ的工艺研究与工业化初探的开题报告题目:橡胶促进剂DZ的工艺研究与工业化初探一、选题背景橡胶促进剂是一种用于促进橡胶硫化反应的化学物质,通常用于汽车轮胎、工业零件、管道等领域中的橡胶制品生产中。
其中,DZ是一种常用的橡胶促进剂,可以提高橡胶硫化速度和强度,从而提高产品的耐磨性和耐老化性能。
目前,国内外已有许多研究关于DZ的性能、结构和应用方面的文献报道,但对DZ的工艺研究和工业化应用还有待进一步深入探讨和研究。
因此,本次选题旨在对DZ进行更加系统和综合的工艺研究,并初步探讨其在工业化生产中的应用前景,为橡胶制品生产提供技术支持和理论指导。
二、研究内容与意义本次研究将从以下几个方面进行探讨:1. DZ的合成工艺研究:通过文献调研和实验室试验,确定DZ的合成方法、反应条件和优化方案,寻找最佳的合成工艺。
2. DZ结构特性研究:通过FTIR、NMR等分析方法,分析DZ分子结构和官能团的种类和分布情况,为进一步研究其性能和应用提供依据。
3. DZ与橡胶的相容性研究:通过黏度测定、玻璃化转变温度等实验方法,研究DZ与橡胶的相互作用方式和复合材料的物理化学性质。
4. DZ在工业化生产中的应用初步探讨:根据合成工艺的参数,探讨DZ在工业生产中的应用前景,分析其经济效益和市场潜力等方面的问题。
三、研究方法1. 文献调研:通过检索国内外相关期刊和数据库,查阅有关DZ的合成、结构和应用方面的文献,获取足够的理论基础和实验数据。
2. 实验室试验:基于文献调研和先前研究的基础上,设计合理的实验方案和操作流程,进行DZ的合成、结构分析和与橡胶的相容性试验等。
3. 数据分析:通过实验数据的处理和分析,评估不同工艺参数对DZ 合成效果和性能影响,为进一步优化工艺提供参考。
四、预期成果1. DZ的合成方法和工艺流程优化,为DZ的大规模生产提供技术支持和理论指导。
2. 外部物理化学性质与橡胶的相容性研究结果,为进一步掌握DZ的性能特点和工业应用提供依据。
橡胶硫化促进剂的生产工艺

橡胶硫化促进剂的生产工艺橡胶硫化促进剂是一种用于加速橡胶硫化反应的化学物质。
在橡胶工业中,橡胶硫化是一种重要的工艺过程,它能够使橡胶材料具有优良的弹性、耐热性和耐腐蚀性。
橡胶硫化促进剂的生产工艺涉及到多个步骤和关键技术,下面将详细介绍。
橡胶硫化促进剂的生产通常以化学合成的方式进行。
一般情况下,该工艺主要包括原料选择、反应条件控制和产物纯化等几个关键步骤。
原料选择是橡胶硫化促进剂生产的首要步骤。
目前常用的原料包括苯胺类、硫酰化合物和二硫化物等。
这些原料的选择应考虑到其性能、成本和环境因素等方面的因素。
在选择原料时,还需要注意其相容性和反应活性,以确保最终产品的质量和性能。
反应条件控制是橡胶硫化促进剂生产中的另一个重要环节。
在反应过程中,需要控制温度、压力和反应时间等参数,以确保反应的高效进行。
此外,还需要添加催化剂和控制pH值等因素,以促进反应的进行和产物的生成。
反应条件的选择和控制对于产品的质量和产率具有重要影响,需要进行精确的实验和工艺优化。
产物纯化是橡胶硫化促进剂生产的最后一步。
在反应结束后,产物中可能存在着未反应的原料、副产物和杂质等。
为了提高产物的纯度和质量,需要进行一系列的分离、过滤和洗涤等工艺步骤。
这些工艺步骤的目的是去除杂质和未反应的物质,以获得纯净的橡胶硫化促进剂产品。
除了上述核心步骤外,橡胶硫化促进剂的生产还需要进行质量控制和产品性能测试等工作。
质量控制主要包括原料的检测和产品的分析等环节,以确保产品符合各项标准和规定。
产品性能测试是为了评估橡胶硫化促进剂的功能和应用性能,以满足不同橡胶制品的需求。
橡胶硫化促进剂的生产工艺涉及到原料选择、反应条件控制、产物纯化、质量控制和产品性能测试等多个方面。
这些步骤的合理组合和优化设计能够提高产品的质量和产率,满足橡胶工业对于硫化促进剂的需求。
随着科技的进步和工艺的不断改进,橡胶硫化促进剂的生产工艺也将不断完善和发展,为橡胶工业的发展做出更大的贡献。
橡胶硫化配方实验报告(3篇)

第1篇一、实验目的本研究旨在通过实验,探索不同硫化配方对橡胶材料性能的影响,以优化橡胶硫化工艺,提高橡胶制品的质量和性能。
二、实验材料与设备1. 实验材料:- 天然橡胶(NR)- 硫磺(S)- 促进剂(如促进剂M、促进剂D)- 防老剂(如防老剂D、防老剂A)- 炭黑(N774)- 氧化锌(ZnO)- 硬脂酸(Stearic Acid)- 石粉- 松焦油- 氯磺化聚乙烯(CSM)- 过氧化物(如偶氮二异丁腈)2. 实验设备:- 开炼机- 密封式硫化机- 拉伸试验机- 压缩试验机- 硫化特性仪三、实验方法1. 配方设计:根据实验目的,设计不同的硫化配方,主要包括以下因素:- 硫磺用量- 促进剂用量- 防老剂用量- 炭黑用量- 其他添加剂用量2. 混炼:将橡胶、硫磺、促进剂、防老剂、炭黑等材料按照配方比例放入开炼机中,进行混炼至均匀。
3. 硫化:将混炼好的胶料放入密封式硫化机中,按照设定的温度和时间进行硫化。
4. 性能测试:对硫化后的橡胶样品进行性能测试,包括拉伸强度、撕裂强度、压缩变形、耐老化性能等。
四、实验结果与分析1. 硫磺用量对性能的影响:随着硫磺用量的增加,橡胶的拉伸强度和撕裂强度逐渐提高,但超过一定量后,性能开始下降。
这是因为硫磺用量过多会导致橡胶交联度过高,材料变硬,弹性下降。
2. 促进剂用量对性能的影响:促进剂用量的增加可以提高橡胶的硫化速度,但同时也会导致硫化胶的力学性能下降。
因此,需要选择合适的促进剂用量,以平衡硫化速度和力学性能。
3. 防老剂用量对性能的影响:防老剂用量的增加可以提高橡胶的耐老化性能,但过量的防老剂会导致硫化速度降低。
因此,需要根据实际需求选择合适的防老剂用量。
4. 炭黑用量对性能的影响:炭黑用量的增加可以提高橡胶的拉伸强度、撕裂强度和耐老化性能,但过量的炭黑会导致硫化速度降低,且会影响橡胶的加工性能。
5. 其他添加剂对性能的影响:其他添加剂如氧化锌、硬脂酸等,对橡胶的力学性能和加工性能也有一定的影响。
硫化促进剂zmbt 合成工艺 氧化锌

硫化促进剂zmbt 合成工艺氧化锌硫化促进剂ZMBT(2-mercaptobenzothiazole)是一种常用的橡胶加工助剂,可用于促进橡胶的硫化反应。
它的合成工艺以及氧化锌在其中的作用都对于橡胶工业至关重要。
本文将从深度和广度两个方面探讨这个主题,并为你提供全面的了解。
一、硫化促进剂ZMBT的合成工艺1.1 原料准备:硫化促进剂ZMBT的合成所需的原料主要包括苯甲醛、硫酸、硫化氢和苯胺。
其中,苯甲醛是合成ZMBT的关键原料,其通过芳香化合物的邻一位反应合成而成。
1.2合成步骤:(1)将苯甲醛与硫酸反应,在一定温度下进行酸化反应,得到苯酚。
(2)将苯酚与硫化氢反应,生成苯酚硫酚。
(3)苯酚硫酚与苯胺反应,生成硫化促进剂ZMBT。
通过上述合成步骤,可以得到高纯度的硫化促进剂ZMBT。
这种合成工艺的优点在于原料易得、合成条件温和,并且产率较高。
二、氧化锌在硫化促进剂ZMBT中的作用氧化锌在橡胶硫化促进剂ZMBT中起着重要的作用。
它具有以下几个方面的功能:2.1催化剂作用:氧化锌可以作为催化剂,促进硫化反应的进行。
在硫化过程中,氧化锌与硫化促进剂ZMBT共同作用,加速硫化反应的速率,提高橡胶硫化的效率。
2.2稀释作用:氧化锌可以起到稀释硫化促进剂ZMBT的作用。
由于硫化促进剂ZMBT具有较强的臭气,为了减少ZMBT的浓度,降低其毒性和刺激性,通常会加入氧化锌作为稀释剂。
2.3防老化作用:氧化锌还可以起到防老化的作用。
由于硫化促进剂ZMBT容易产生氧化反应,使用时容易导致劣化和老化。
在硫化促进剂ZMBT中加入适量的氧化锌,可以有效降低其氧化反应的可能性,延长其使用寿命。
三、个人观点和理解在我看来,硫化促进剂ZMBT的合成工艺和氧化锌在其中的作用对于橡胶工业具有重要的意义。
通过合成工艺,我们可以获得高纯度的ZMBT,为橡胶硫化过程提供良好的条件。
而氧化锌作为催化剂和稀释剂,不仅可以提高硫化促进剂ZMBT的效率和安全性,还可以延长其使用寿命,降低劣化的可能性。
硫化促进剂zmbt 合成工艺 氧化锌

硫化促进剂zmbt 合成工艺氧化锌摘要:一、硫化促进剂ZMBT简介1.硫化促进剂ZMBT的作用2.在橡胶制品中的应用二、硫化促进剂ZMBT的合成工艺1.原料准备2.反应过程3.产品收率与纯度三、氧化锌在硫化促进剂ZMBT合成工艺中的作用1.氧化锌的性质2.在反应过程中的作用3.对产品性能的影响正文:硫化促进剂ZMBT(Zinc Methyl Benzothiazole Sulfenamide)是一种重要的橡胶硫化促进剂,具有良好的热稳定性和抗氧性能,广泛应用于各种橡胶制品中,如轮胎、胶管、胶带等。
硫化促进剂ZMBT的合成工艺主要分为以下几个步骤:一、原料准备硫化促进剂ZMBT的合成主要原料为氧化锌(ZnO)和甲基苯并噻唑(MBT)。
此外,还需要一定比例的硫磺、甲硫醇和水。
二、反应过程1.将氧化锌与硫磺混合,在惰性气氛下加热至一定温度,得到硫化锌。
2.将甲基苯并噻唑与甲硫醇混合,加热至反应开始,然后加入硫化锌,继续加热反应至反应终点。
3.将反应产物进行冷却、结晶、过滤,得到硫化促进剂ZMBT产品。
三、产品收率与纯度在上述合成工艺过程中,产品收率和纯度受到多种因素影响,如反应温度、反应时间、原料比例等。
合理控制这些因素,可以提高产品收率和纯度。
氧化锌在硫化促进剂ZMBT的合成工艺中起着关键作用。
首先,氧化锌作为催化剂,可以降低反应的活化能,促进反应的进行。
其次,氧化锌可以提高产品性能,如热稳定性、抗氧性等。
因此,在合成过程中,应充分考虑氧化锌的性质和作用,合理控制其添加量。
总之,硫化促进剂ZMBT的合成工艺通过合理的原料准备和反应过程,可以得到具有优良性能的硫化促进剂ZMBT产品。
硫化促进剂zmbt 合成工艺 氧化锌
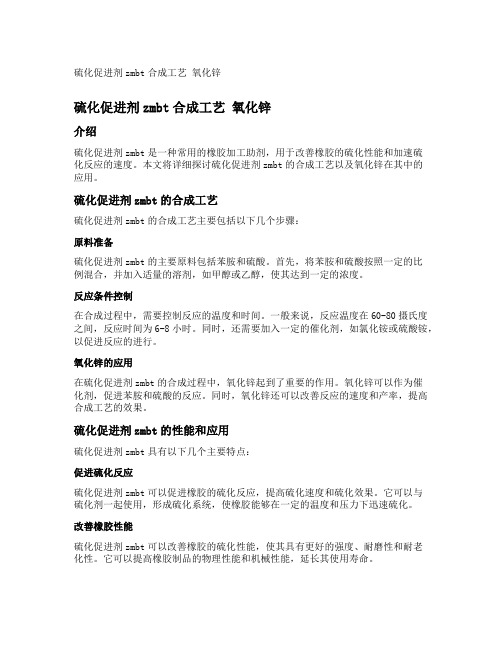
硫化促进剂zmbt合成工艺氧化锌硫化促进剂zmbt合成工艺氧化锌介绍硫化促进剂zmbt是一种常用的橡胶加工助剂,用于改善橡胶的硫化性能和加速硫化反应的速度。
本文将详细探讨硫化促进剂zmbt的合成工艺以及氧化锌在其中的应用。
硫化促进剂zmbt的合成工艺硫化促进剂zmbt的合成工艺主要包括以下几个步骤:原料准备硫化促进剂zmbt的主要原料包括苯胺和硫酸。
首先,将苯胺和硫酸按照一定的比例混合,并加入适量的溶剂,如甲醇或乙醇,使其达到一定的浓度。
反应条件控制在合成过程中,需要控制反应的温度和时间。
一般来说,反应温度在60-80摄氏度之间,反应时间为6-8小时。
同时,还需要加入一定的催化剂,如氯化铵或硫酸铵,以促进反应的进行。
氧化锌的应用在硫化促进剂zmbt的合成过程中,氧化锌起到了重要的作用。
氧化锌可以作为催化剂,促进苯胺和硫酸的反应。
同时,氧化锌还可以改善反应的速度和产率,提高合成工艺的效果。
硫化促进剂zmbt的性能和应用硫化促进剂zmbt具有以下几个主要特点:促进硫化反应硫化促进剂zmbt可以促进橡胶的硫化反应,提高硫化速度和硫化效果。
它可以与硫化剂一起使用,形成硫化系统,使橡胶能够在一定的温度和压力下迅速硫化。
改善橡胶性能硫化促进剂zmbt可以改善橡胶的硫化性能,使其具有更好的强度、耐磨性和耐老化性。
它可以提高橡胶制品的物理性能和机械性能,延长其使用寿命。
应用领域广泛硫化促进剂zmbt广泛应用于橡胶制品的生产中,如轮胎、橡胶管、橡胶鞋等。
它可以提高橡胶制品的质量和性能,满足不同领域的需求。
硫化促进剂zmbt的合成工艺优化为了进一步提高硫化促进剂zmbt的合成工艺效果,可以从以下几个方面进行优化:原料选择选择高纯度的苯胺和硫酸作为原料,以提高反应的纯度和产率。
同时,可以考虑引入其他辅助原料,如催化剂和溶剂,以进一步改善反应条件。
反应条件调控通过调节反应温度、时间和催化剂的用量,可以优化反应条件,提高反应速度和产率。
橡胶硫化促进剂DZ合成新方法研究

橡胶硫化促进剂DZ合成新方法研究
王伟;高彦鹏;刘兴康;董恩儒;岳姝雅
【期刊名称】《天津化工》
【年(卷),期】2016(30)5
【摘要】采用次氯酸钠和促进剂M浆料,同时滴加到合成好的胺的盐酸盐中,用这种方法合成了橡胶硫化促进剂DZ(N,N-二环己基-2-苯骈噻唑次磺酰胺).最佳工艺条件为n(M)∶n(二环己胺)∶n(胺的盐酸盐)=1∶1.2∶1.2,反应温度为30~60℃,以异丙醇为溶剂,持续滴加M浆料及次氯酸钠反应100~130min,此后保温5~
10min.
【总页数】2页(P38-39)
【作者】王伟;高彦鹏;刘兴康;董恩儒;岳姝雅
【作者单位】天津一化化工有限公司,天津300270;天津一化化工有限公司,天津300270;天津一化化工有限公司,天津300270;天津一化化工有限公司,天津300270;天津一化化工有限公司,天津300270
【正文语种】中文
【中图分类】TQ330.38+5
【相关文献】
1.橡胶硫化促进剂DZ合成工艺探讨 [J], 刘怡志
2.橡胶硫化促进剂DZ合成新工艺 [J], 黄友林;芮敏慧;顾浩;陈新国;芮必胜
3.钴盐催化合成橡胶硫化促进剂CBS新工艺研究 [J], 王美竹
4.橡胶硫化促进剂DZ生产废水的预处理实验研究 [J], 王亚楠;陈侠
5.用粗M合成橡胶硫化促进剂DZ [J], 张越;李小云;李建军
因版权原因,仅展示原文概要,查看原文内容请购买。
促进剂DZ加入方式对Si-69原位改性白炭黑填充NR性能的影响

促进剂DZ加入方式对Si-69原位改性白炭黑填充NR性能的影响为了解决这一问题,研究者们提出了一种新的方法——利用促进剂DZ进行原位改性,以期能够有效地提高白炭黑与橡胶基体之间的相容性,从而改善橡胶制品的性能。
本文将针对该方法进行深入研究,探讨促进剂DZ加入方式对Si-69原位改性白炭黑填充NR性能的影响。
我们需要了解白炭黑与橡胶基体之间相互作用的机理。
白炭黑由于其表面高度极性,易与橡胶分子链发生作用,但由于表面的化学惰性,这种作用力并不强。
Si-69是一种常用的硫醇型偶联剂,具有双官能团(硅烷基和硫醇基),可以有效地改善填料与橡胶基体之间的结合,提高填料的强度。
将Si-69作为原位改性剂,与白炭黑进行原位改性,可以增强白炭黑与橡胶基体之间的化学键结合,改善填料与橡胶基体的相容性。
促进剂DZ的加入方式对Si-69原位改性白炭黑填充NR性能的影响需要进行系统的研究。
促进剂DZ是一种常用的有机过硫酰胺类促进剂,可以与双官能团偶联剂进行协同作用,促进硫化反应的进行。
在本研究中,我们将通过不同方式添加促进剂DZ,如混炼法和分散法等,探讨其对Si-69原位改性白炭黑填充NR性能的影响。
通过调整促进剂DZ的加入方式,我们可以有效地控制其在橡胶混炼过程中的分散均匀性和与Si-69的协同作用效果,从而影响原位改性的效果。
我们将通过一系列实验方法来验证促进剂DZ加入方式对Si-69原位改性白炭黑填充NR 性能的影响。
通过物理性能测试、热性能测试和力学性能测试等方法,我们可以全面地评价原位改性白炭黑填充NR的性能变化情况,揭示促进剂DZ加入方式对Si-69原位改性白炭黑填充NR性能的影响规律。
促进剂DZ加入方式对Si-69原位改性白炭黑填充NR性能的影响是一个复杂而又具有重要意义的研究课题。
通过深入的研究,我们可以为橡胶制品的生产提供更为科学、合理的原位改性方法,从而更好地提高橡胶制品的性能,促进橡胶工业的发展。
希望通过本研究,能够为相关领域的研究人员提供一定的借鉴和启发,推动该领域的发展。
促进剂DZ加入方式对Si-69原位改性白炭黑填充NR性能的影响

促进剂DZ加入方式对Si-69原位改性白炭黑填充NR性能的影响本文旨在研究促进剂DZ加入方式对Si-69原位改性白炭黑填充NR(天然橡胶)性能的影响,通过一系列实验分析,探讨白炭黑改性体系中促进剂DZ的最佳加入方式,为橡胶制品的研发提供理论指导和实验依据。
一、实验材料与方法实验所用天然橡胶(NR)、白炭黑、Si-69、促进剂DZ等原材料均为工业级产品。
实验采用了常规的橡胶混炼工艺,具体操作步骤如下:首先将天然橡胶、白炭黑、Si-69和促进剂DZ按一定比例加入到橡胶研磨机中进行预混炼,然后将混炼后的胶料进行压延、硫化等后续处理,最终得到不同配方的改性橡胶样品。
随后,通过拉伸实验、硬度测试、扫描电子显微镜观察等方法对样品的物理性能、力学性能和微观结构进行了分析,以从多个角度综合评价不同配方样品的性能差异。
二、实验结果与分析1. 拉伸性能分析从实验结果来看,不同配方的改性橡胶样品的拉伸性能存在较大的差异。
促进剂DZ加入方式对样品的拉伸强度和断裂伸长率有明显影响。
促进剂DZ与Si-69同时加入可显著提高样品的拉伸强度,同时断裂伸长率也有所提高;而将促进剂DZ单独加入时,虽然拉伸强度有所提高,但断裂伸长率却出现了下降的趋势。
2. 硬度测试分析硬度是衡量橡胶材料硬软程度的重要指标。
通过硬度测试可以看出,促进剂DZ的加入方式会对橡胶样品的硬度产生一定影响。
同时加入促进剂DZ和Si-69的样品硬度略高于单独加入Si-69的样品,表明促进剂DZ的存在能够提升样品的硬度。
3. 微观结构分析通过扫描电子显微镜观察样品的微观结构,可以看出不同配方的改性橡胶样品的表面形貌存在一定差异。
在同时加入促进剂DZ和Si-69的样品中,白炭黑与橡胶之间的界面结合更加紧密,界面分散性更好;而在单独加入Si-69的样品中,白炭黑颗粒之间往往存在一定的聚集现象。
三、结论与展望通过对不同配方样品的综合性能分析可以得出,促进剂DZ的加入方式对Si-69原位改性白炭黑填充NR性能具有显著影响。
促进剂DZ加入方式对Si-69原位改性白炭黑填充NR性能的影响

促进剂DZ加入方式对Si-69原位改性白炭黑填充NR性能的影响随着汽车、轮胎、橡胶制品等行业的快速发展,对橡胶制品的性能要求也越来越高。
而白炭黑填充橡胶是一种常见的橡胶制品材料,其性能的优劣直接影响着制品的使用效果。
为了改善白炭黑填充橡胶的性能,研究者们提出了一种利用促进剂DZ对Si-69进行原位改性的方法。
本文旨在探究这种方法对白炭黑填充橡胶的性能影响,以期为橡胶制品的改性改进提供一定的参考。
我们需要了解一下白炭黑填充橡胶的性能。
白炭黑因其特殊的结构和优异的性能,在橡胶制品中具有广泛的应用。
而填充橡胶中加入白炭黑可以有效提高橡胶的机械性能、热性能和耐磨性能。
由于白炭黑的表面活性较低,与橡胶分子间的作用力不强,因此橡胶中填充白炭黑的性能仍然有待提高。
针对这一问题,研究者们提出了利用促进剂DZ对Si-69进行原位改性的方法。
我们需要了解一下促进剂DZ和Si-69的性质及其在橡胶材料中的作用。
促进剂DZ是一种常用的橡胶促进剂,它可以与橡胶分子发生化学反应,增强橡胶的加工性能和耐老化性能。
而Si-69是一种常用的硫化促进剂,它可以将填料与橡胶之间的结合力增强,提高橡胶的强度和耐磨性。
利用促进剂DZ对Si-69进行原位改性,可以有效提高Si-69在橡胶中的分散性和增强作用,从而改善白炭黑填充橡胶的性能。
接下来,我们需要讨论一下促进剂DZ加入方式对Si-69原位改性白炭黑填充橡胶性能的影响。
研究者们进行了不同加入方式下的试验研究,发现在加入方式一中,促进剂DZ可以与Si-69充分混合,形成均匀的混合体系,从而有效提高Si-69的分散性和增强作用。
白炭黑填充橡胶的机械性能、热性能和耐磨性能均得到了显著提高。
在加入方式二中,由于促进剂DZ与Si-69的混合程度较低,Si-69的分散性和增强作用均较差,使得白炭黑填充橡胶的性能改善效果不明显。
促进剂DZ加入方式对Si-69原位改性白炭黑填充橡胶性能有着显著的影响。
促进剂DZ合成工艺的改进研究的开题报告

促进剂DZ合成工艺的改进研究的开题报告一、课题背景促进剂DZ是一种常见的橡胶助剂,具有极佳的加工性能和改善橡胶物理化学性质的能力,在橡胶工业中被广泛应用。
目前,促进剂DZ的生产主要采用酰胺法,但该方法存在反应温度高、周期长、产物质量波动大等问题,限制了其在工业生产中的应用。
因此,改进促进剂DZ的合成工艺具有重要意义。
二、研究目的本研究旨在通过对促进剂DZ合成工艺的改进,提高其生产效率、降低成本、改善产品质量和稳定性,为促进剂DZ的生产提供可行性方案。
具体目的如下:1. 评估现有促进剂DZ生产工艺存在的问题和不足之处。
2. 探究促进剂DZ的替代合成方法并筛选出最佳方案。
3. 优化促进剂DZ生产的工艺参数,提升生产效率。
4. 建立稳定的促进剂DZ合成工艺,确保产品质量和稳定性。
三、研究内容与方法1. 现有促进剂DZ生产工艺的评估通过文献资料查询和深入分析现有促进剂DZ生产工艺的优点和不足,并考虑环保和节能因素,寻找切入点,确定后续改进方向。
2. 探究促进剂DZ的替代合成方法并筛选出最佳方案选择最适合的替代合成方法,并通过模拟试验和实验室小试等方式,筛选出最佳方案。
3. 优化促进剂DZ生产的工艺参数以最佳合成方案为基础,通过合理调整反应温度、反应物质量比、反应时间和溶剂种类等参数,优化整个生产过程,提高生产效率。
4. 建立稳定的促进剂DZ合成工艺通过多次试验不断调整和优化工艺参数,建立起稳定的合成工艺,确保产品质量和稳定性。
四、研究预期成果1. 建立稳定的促进剂DZ合成工艺,提高产品质量和稳定性。
2. 提高促进剂DZ生产效率,降低生产成本。
3. 探索出促进剂DZ生产的新方法,为橡胶助剂领域的研究提供新思路。
4. 对促进剂DZ生产及橡胶助剂领域的发展具有推动作用。
五、研究计划与进度安排本研究计划分为六个阶段,具体计划如下:阶段一:文献调研,总结现有促进剂DZ生产工艺存在的问题和不足之处。
阶段二:探索促进剂DZ的替代合成方法,并筛选出最佳方案。
- 1、下载文档前请自行甄别文档内容的完整性,平台不提供额外的编辑、内容补充、找答案等附加服务。
- 2、"仅部分预览"的文档,不可在线预览部分如存在完整性等问题,可反馈申请退款(可完整预览的文档不适用该条件!)。
- 3、如文档侵犯您的权益,请联系客服反馈,我们会尽快为您处理(人工客服工作时间:9:00-18:30)。
1. 合成方法的选择 DZ 的合成方法总的说来可分为两种[ 2] : 一为一步合成法, 即用次氯酸钠氧化二环己胺与 M ( 2M ercapt o benzo thiazol e) 钠盐以及有机溶剂的混合液, 该法的优点是工艺流程短, 成本低, 但产品 中 DM ( 二硫化二苯并噻唑, Dibenzot hiazyl disulf ide) 含量过高, 成品 DZ 熔程长, 产品质量达不到 要求; 另一为两步合成法, 即先用次氯酸钠将二环己胺氧化成氯代二环己胺, 再在水溶性有机介质 中让氯代二环己胺与 M 钠盐进行缩合反应而制得 DZ, 该方法的流程稍长, 但可获得质量好、收率 高的产品。因此, 选择两步法合成工艺路线, 分别使用丙酮和乙醇[ 3] 作溶剂。 2. 实验步骤 ( 1) 氯代二环己胺的制备—— 氯代 按 m olC12H23N ∶mol NaClO = 1∶1. 1 的配比将二环己胺加入带有搅拌装置的三口烧瓶中, 水浴激 烈搅拌下于 60min~80m in 内将 NaCl O 滴入到三口烧瓶内, 滴完后再继续搅拌 1. 5h, 整个过程中 控制反应温度为 35℃~40℃。该反应为轻微的放热反应, 开始时控制水浴温度为 35℃, 滴完后慢慢 升温至与反应器内相同温度, 保温完毕, 趁热将混合物倒入分液漏斗使其沉降分层, 分除下层水溶 液和中间的絮状杂质, 即可制得氯代二环己胺。 ( 2) 制 M 钠盐( C7H4N S2 N a) ——碱溶
合成化学( HECHENG HUA XUE ) 第 8 卷第 4 期( 2000)
— 367 —
橡胶硫化促进剂 DZ 合成工艺探讨*
刘怡志
[ 湖南株洲( 国家) 高新技术产业开发区创业服务中心, 株洲, 412007]
摘要 采用两步合 成法制备 橡胶硫化 促进剂 DZ ( N , N -二环己 胺-2-苯并 噻唑次 磺酰胺) , 控制 M ( 2-M er capto benzot hiazole) 钠 盐与氯代二环乙胺的 摩尔比为 1, 选择 乙醇作有机溶 剂, 将 缩合反应滴 加 M 钠 盐的温度控 制在 30℃~35℃, 即可 制得熔 点在 90℃以 上, 溶程小 于 1℃, 且 收率近 80% 的高品 质 D Z 产品。
从表 4 结果可知, 试验所得产品熔点合格、熔程短、收率近 80% , 各项消耗低于文献上报道定额, 因 此, 该工艺条件是可行的。
参考文献
[ 1] 王瑞鑫, 沈梅: “世界精细化工产品质量标准汇编”( S) , 北京, 化工部标准化研究所, 1989, 第 711 页. [ 2] 侯銮荣: “合成材料助剂手册”( M ) , 北京, 化学工业出版社, 1985, 第 723 页. [ 3] 孔德琨, 陈志武: “工业溶剂手册”( M ) , 北京, 冶金工业出版社, 1984, 第 232 页.
合成化学( HECHENG HUA XUE ) 第 8 卷第 4 期( 2000)
表 2 DZ 合成表( 以乙醇为溶剂)
实验 序号
氯代胺
乙醇 滴加 M 时间 保温时间 保温温度
DZ
(g)
( mL)
( min)
( min)
( ℃)
(g)
1
111
20 0
65
60
35
1 30
2
110
15 0
70
60
5ห้องสมุดไป่ตู้
4 50
60
30
35
26 0
75. 2
88 ~10 2
6
4 50
60
60
35
25 8
7
4 50
70
60
35
25 9
注: 氯代二环己胺均为 222g , M 均为 170g , 滴加温度均为 30℃~35℃
74. 5 74. 7
90. 5~91. 5 91. 0~92. 1
根据上述实验结果, 确定以丙酮为溶剂工艺的指标为: 促进剂 M 与氯代二环己胺的配比 molM ∶m olC12H22N Cl = 1∶1, 反应时间: 滴加 M 60min~80min, 保温时间 60min±5min, 温度: 35℃±2℃, 丙酮用量: 450mL 。
产率( % ) 79. 1 79. 0 79. 1 79. 7 79. 7
熔程( ℃) 91. 8~92. 7 92. 0~92. 9 91. 7~92. 3 91. 6~92. 5 92. 1~93. 5
— 370 —
合成化学( HECHEN G HUAXUE) 第 8 卷第 4 期( 2000)
( Jiading Distr ict Hyg iene Epidem ic Pr eventio n Office , Shang hai, 201800) ( A pplied Chemistr y, Science College, Shang hai U niv ersity, Shang hai, 201800)
Processing Technique of Rubber-Sulfidation Accelerating Agent DZ
L iu, Yi-Zhi
[ P io neer Serv ice Center , Zhuzho u( State-lev el) High -tech Industrial D evelopment Zo ne, Zhuzho u, 412007]
Abstract T he processing t echnique o f rubber-sulf idation accelerat ing ag ent DZ ( N , N dieyclohex yl -2-benzot hicazole) by t w o-st ep sy nt hesis method is discussed. Hig hqualit y pr oduct w ith melting po int o ver 90℃ and melt ing t emperat ure range w it hin 1℃ can be o bt ained in abo ut 80% yield under t he opt imum react ion condit ions as foll ow s: molC7H4NS 2Na∶mol C12H22NCl= 1∶1, t he t em perat ure fo r adding C7H5N S2 ( accelerat ing agent M ) is cont rolled w it hin 30℃~ 35℃ using Et OH as a solvent .
2 42 85 79
表中成本( 消耗) 分别根据表 1( 6) 和表 2( 4) 的最佳试验结果计算。由表 3 可以看出, 方案Ⅱ优 于方案Ⅰ, 即选用乙醇作溶剂具有操作方便、产品质量好、收率高、成本低等优点, 且乙醇毒性小, 操 作安全。
3. 根据上述确定的最佳操作条件进行了关键步骤缩合的稳定性试验, 结果见表 4。
2000 年 2 月 28 日收到。 * 作者简介: 刘怡志, 1964 年生, 湖南邵阳人, 湖南株洲( 国家) 高新技术产业开发区创业服务中心副主任, 大学本科, 工程 师, 主要从事助剂产品的研制、开发和生产管理。
— 368 —
合成化学( HECHEN G HUAXUE) 第 8 卷第 4 期( 2000)
35
1 39
3
110
18 0
70
30
35
1 34
4
110
18 0
70
60
40
136. 5
5
110
18 0
70
60
35
1 37
注: M 均为 85g , 滴加 M 温度均为 30℃~35℃
2. 两种方案的比较见表 3。
表 3 两种方案 的比较
比较项目
方案Ⅰ( 丙酮作溶剂)
每吨 DZ 耗 M ( 97% ) / kg
按 mo lM ∶mol = NaOH 1∶1. 5 的配比分别称取 167g M 和 115g 40% 的烧碱放入烧杯中, 每 1m ol M 加水 200mL , 加热至 90℃, 搅拌使之溶解。可制得 400m L pH = 9~10 的 M 钠盐。
( 3) DZ 的合成—— 缩合 这是该实验中关键的一步。在 1000mL 四口烧瓶中加入氯代二环己胺和水溶性有机溶剂, 装上 温度计、回流冷凝管及搅拌器, 置于水浴中, 在 60min~80min 内滴完 M 钠盐, 该反应是轻微的放 热反应, 控制反应温度为 30℃~35℃, 滴完后将温度进行调整, 继续保温 30min~60min, 冷却至近 10℃, 抽滤, 用 pH = 10 的稀碱水洗两次, 再用自来水洗至 pH 接近 7, 在 65℃±2℃下烘干至恒重 ( 约 6h~8h) 。
64 7
每吨 DZ 耗 二环己胺( 以 100% 计) / kg
70 5
每吨 DZ 耗 Na OH( 100% 计) / kg
52 5
每吨 DZ 耗 Cl2( 以 N aClO 90% 收率计) / kg
31 6
每吨 DZ 耗 溶剂/ kg
1 37 6
溶剂回收率/ kg/ t
51. 1
原料成本/ 元/ t
2 80 48
产品收率/ %
74. 5
— 369 —
产率 (% ) 75. 0 80. 2 77. 3 79. 0 79. 1
熔程 ( ℃) 92. 1~93. 0 88 8 9~9 2 91. 8~92. 5 92. 6~93. 5
方案Ⅱ( 乙醇作溶剂) 62 0 66 4 52 5 31 6 10 61 61
表 4 稳定性试验表
实验序号 氯代二环己胺( g)
滴加 M 时间( min)