材料特性对热障涂层合理压入深度的影响
YSZ热障涂层的微观结构及其影响

YSZ热障涂层的微观结构及其影响YSZ热障涂层的微观结构及其影响热障涂层(YSZ)是一种常用于陶瓷热障涂层的材料,具有良好的耐热性能和绝缘性能。
它由陶瓷氧化物氧化锆稳定剂(YSZ)组成,经过特殊工艺制备而成。
YSZ热障涂层的微观结构对其性能具有重要影响。
本文将从微观结构的角度来探讨YSZ热障涂层的影响。
首先,YSZ热障涂层的微观结构主要由YSZ颗粒和粘结相组成。
YSZ颗粒是热障涂层的主要耐热组分,具有高熔点和优异的绝缘性能。
它们通常具有多孔结构,这有助于提高热稳定性和减少热传导。
粘结相则起到连接YSZ颗粒的作用,以增强涂层的结构稳定性。
其次,YSZ热障涂层的YSZ颗粒尺寸和分布对其性能具有重要影响。
较小的YSZ颗粒尺寸可以提高涂层的密实性和耐热性能。
这是因为小颗粒能更紧密地填充涂层中的空隙,减少热传导通道,并提供更多的界面反射。
此外,YSZ颗粒的均匀分布有助于提高涂层的力学性能和耐久性。
此外,YSZ热障涂层中粘结相的类型和含量也会影响其性能。
通常使用的粘结相包括玻璃和陶瓷粘结剂。
玻璃粘结剂可以提供较好的粘结性能和耐化学腐蚀性能,但在高温下容易软化。
陶瓷粘结剂则具有较高的耐热性能,但可能会影响涂层的机械性能。
因此,合理选择粘结相的类型和含量是提高YSZ热障涂层性能的关键。
最后,除了上述微观结构因素外,YSZ热障涂层的制备工艺也会对其微观结构和性能产生重要影响。
例如,涂层的喷涂工艺和热处理条件会影响YSZ颗粒的熔融和结晶行为,从而影响涂层的微观结构和性能。
综上所述,YSZ热障涂层的微观结构对其性能具有重要影响。
合理调控YSZ颗粒尺寸和分布、粘结相的类型和含量,以及优化制备工艺,可以提高热障涂层的耐热性能、绝缘性能和耐久性,从而满足高温应用的要求。
热障涂层材料的制备与性能研究

热障涂层材料的制备与性能研究随着现代工业的不断发展,高温工况下材料的热稳定性成为了一个重要的研究方向。
热障涂层材料由于其良好的绝缘性和高温稳定性,成为了一种非常有前景的防护材料。
本文将就热障涂层材料的制备方法和性能研究展开讨论。
一、热障涂层材料的制备热障涂层材料的制备方法多种多样,常见的有物理气相沉积法和化学气相沉积法。
1. 物理气相沉积法物理气相沉积法是一种通过高温下蒸发材料并将其沉积到基材表面的方法。
它可以得到具有较高结晶度和粒界结构的热障涂层材料。
在这种方法中,常用的气相源材料有氧化铝和氧化锆等。
通过将气相源材料加热蒸发,并通过气流将其输送至基材表面,可以实现热障涂层材料的沉积。
2. 化学气相沉积法化学气相沉积法是一种将气体中的化学原料转化为沉积物的方法。
该方法可以控制沉积层的成分和结构,从而实现所需的性能。
在这种方法中,常用的气相源材料有氯化铝和氧化铝等。
通过将气体中的化学原料引入反应室,使其在高温下发生化学反应,并在基材表面形成所需的热障涂层材料。
二、热障涂层材料的性能研究热障涂层材料的性能研究主要包括热稳定性、热导率和界面附着力等方面。
1. 热稳定性热稳定性是评价热障涂层材料性能的重要指标。
在高温工况下,热障涂层材料需要能够有效阻挡热量传递,并保护基材不受热应力的影响。
研究人员通过热循环试验和热冲击试验等方法来评估热障涂层材料的热稳定性能。
2. 热导率热导率是指材料传导热量的能力,对于热障涂层材料来说,较低的热导率可以降低热量传递,提高防护效果。
研究人员通过热导率测试仪来测定热障涂层材料的热导率,以评估其防护性能。
3. 界面附着力界面附着力是指热障涂层材料与基材之间的结合强度。
良好的界面附着力可以确保涂层在高温工况下不易剥落。
研究人员通过剪切试验和界面剥离试验等方法来评估热障涂层材料的界面附着力。
结语热障涂层材料的制备和性能研究对于提高材料的热稳定性具有重要意义。
通过物理气相沉积法和化学气相沉积法可以制备具有不同性能的热障涂层材料。
热障涂层的研究与应用
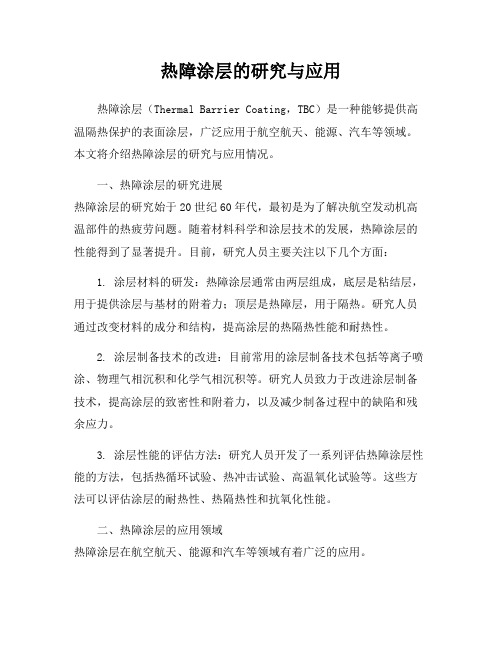
热障涂层的研究与应用热障涂层(Thermal Barrier Coating,TBC)是一种能够提供高温隔热保护的表面涂层,广泛应用于航空航天、能源、汽车等领域。
本文将介绍热障涂层的研究与应用情况。
一、热障涂层的研究进展热障涂层的研究始于20世纪60年代,最初是为了解决航空发动机高温部件的热疲劳问题。
随着材料科学和涂层技术的发展,热障涂层的性能得到了显著提升。
目前,研究人员主要关注以下几个方面:1. 涂层材料的研发:热障涂层通常由两层组成,底层是粘结层,用于提供涂层与基材的附着力;顶层是热障层,用于隔热。
研究人员通过改变材料的成分和结构,提高涂层的热隔热性能和耐热性。
2. 涂层制备技术的改进:目前常用的涂层制备技术包括等离子喷涂、物理气相沉积和化学气相沉积等。
研究人员致力于改进涂层制备技术,提高涂层的致密性和附着力,以及减少制备过程中的缺陷和残余应力。
3. 涂层性能的评估方法:研究人员开发了一系列评估热障涂层性能的方法,包括热循环试验、热冲击试验、高温氧化试验等。
这些方法可以评估涂层的耐热性、热隔热性和抗氧化性能。
二、热障涂层的应用领域热障涂层在航空航天、能源和汽车等领域有着广泛的应用。
1. 航空航天领域:热障涂层被广泛应用于航空发动机的涡轮叶片、燃烧室和燃气涡轮等高温部件。
它可以提供高温隔热保护,延长部件的使用寿命,提高发动机的性能和可靠性。
2. 能源领域:热障涂层被应用于燃气轮机、燃煤锅炉和核电站等能源设备中。
它可以减少能源设备的热损失,提高能源利用效率,降低能源消耗。
3. 汽车领域:热障涂层被应用于汽车发动机的活塞、气缸盖和排气系统等部件。
它可以降低发动机的燃油消耗,提高汽车的动力性能和经济性。
三、热障涂层的未来发展趋势热障涂层的研究和应用仍然面临一些挑战,如涂层的耐热性、热隔热性和抗氧化性能的进一步提高,涂层制备技术的改进,以及涂层与基材之间的附着力等。
未来的发展趋势包括:1. 新材料的研发:研究人员将继续开发新的材料,如陶瓷基复合材料和金属基复合材料,以提高涂层的性能。
热障涂层的作用机理

热障涂层的作用机理全文共四篇示例,供读者参考第一篇示例:热障涂层是一种常用于航空航天领域的高技术涂层,它具有良好的隔热和耐高温性能,能够有效保护机体材料不受高温气流的侵蚀。
那么,热障涂层是如何实现这一功能的呢?下面我们就来详细探讨一下热障涂层的作用机理。
热障涂层主要包括两个组成部分:热障层和粘结层。
热障层通常由氧化铝、氧化锆等陶瓷材料构成,其主要作用是隔绝高温气流,减少热量传导到机体内部。
而粘结层则用于将热障层牢固地粘贴在机体表面,防止其脱落。
两者协同作用,构成了热障涂层的基本结构。
热障涂层的隔热性能主要依赖于热障层的结构和材料特性。
一般来说,热障层的密度低、孔隙率高,能够有效反射和散射高温气流的热辐射,减少热传导。
热障层材料具有耐高温性能,能够抵御高温气流的腐蚀作用。
由于热障层具有吸热、反射和散射等多种隔热机制,因此能够显著降低机体表面的温度,保护机体材料不受高温气流的侵蚀。
热障涂层还具有良好的抗热疲劳性能。
由于航空航天领域的飞行器在高速飞行过程中会受到高温气流的剧烈冲击,导致机体材料产生热膨胀和热收缩,容易产生裂纹和脱落。
而热障涂层的弹性和粘结性能可以有效缓解这种热应力,避免热疲劳破坏,从而延长机体的使用寿命。
热障涂层还可以提高飞行器的整体性能。
由于热障涂层能够有效降低机体表面的温度,减少空气阻力,提高飞行效率。
热障涂层还能减轻飞行器的自重,提高燃油利用率。
热障涂层不仅可以保护机体材料,还可以提高飞行器的性能指标,具有广泛的应用前景。
热障涂层的作用机理包括隔热、耐高温、抗热疲劳和提高整体性能等方面。
通过研究热障涂层的结构特点和材料性能,我们可以更好地理解热障涂层的作用机理,并进一步提高其性能,满足航空航天领域对高温材料的需求。
【文章结束】.第二篇示例:热障涂层是一种应用于航空航天等高温工作环境中的涂层技术,其作用是提高材料的耐高温性能,以保护基材不受高温气流的侵蚀和损坏。
热障涂层的作用机理主要包括热障效应、氧化保护和陶瓷保护。
热障涂层 制备

热障涂层制备热障涂层是一种应用广泛的高科技材料,它可以在高温环境下保护机械设备和航空航天器的表面不受热损伤。
热障涂层的制备是一项复杂的工艺,需要经过多道工序才能完成。
本文将介绍热障涂层的制备过程和应用领域。
一、热障涂层的制备过程1.基材表面处理在制备热障涂层之前,需要对基材进行表面处理。
表面处理的目的是去除基材表面的氧化物和杂质,使基材表面变得光滑、干净,便于涂层的附着和生长。
表面处理的方法包括机械处理、化学处理和电化学处理等。
2.涂层材料的选择热障涂层的材料通常是氧化铝、氧化锆、氧化钇等陶瓷材料。
这些材料具有高熔点、高硬度、高耐热性和良好的隔热性能,可以有效地保护基材表面不受高温热损伤。
涂层材料的选择要根据具体的应用环境和要求来确定。
3.涂层工艺涂层工艺是热障涂层制备的关键环节。
涂层工艺包括喷涂、热处理、烧结等多个步骤。
其中,喷涂是最关键的一步,它决定了涂层的质量和性能。
喷涂方法包括等离子喷涂、火焰喷涂、电弧喷涂等。
不同的喷涂方法有不同的优缺点,需要根据具体情况选择。
4.涂层性能测试涂层制备完成后,需要对涂层的性能进行测试。
涂层性能测试包括耐热性、隔热性、耐腐蚀性、机械性能等多个方面。
测试结果可以反映涂层的质量和性能,为涂层的应用提供依据。
二、热障涂层的应用领域热障涂层的应用领域非常广泛,主要包括以下几个方面:1.航空航天领域热障涂层在航空航天领域中得到了广泛应用。
它可以保护飞机发动机、火箭发动机等高温部件不受热损伤,提高了飞行器的可靠性和安全性。
2.能源领域热障涂层在能源领域中也有着广泛的应用。
它可以保护燃气轮机、燃煤锅炉等高温设备的表面不受热损伤,提高了设备的使用寿命和效率。
3.汽车工业热障涂层在汽车工业中也有着应用。
它可以保护汽车发动机的高温部件不受热损伤,提高了发动机的性能和寿命。
4.电子领域热障涂层在电子领域中也有着应用。
它可以保护电子元器件的表面不受高温热损伤,提高了元器件的可靠性和稳定性。
热障涂层材料

热障涂层材料热障涂层材料是一种应用广泛的高温材料,它具有优异的隔热性能和耐高温性能,被广泛应用于航空航天、能源、汽车等领域。
热障涂层的主要作用是在高温环境下保护基础材料不受热损伤,延长材料的使用寿命。
本文将对热障涂层材料的种类、特性和应用进行介绍。
热障涂层材料主要分为陶瓷涂层和金属涂层两大类。
陶瓷涂层是指将陶瓷颗粒或陶瓷材料溶液喷涂在基础材料表面形成的涂层,具有优异的耐高温性能和隔热性能。
常见的陶瓷涂层材料包括氧化铝、氧化锆、氧化硅等。
金属涂层则是将金属材料喷涂在基础材料表面形成的涂层,具有良好的导热性能和耐腐蚀性能。
常见的金属涂层材料包括镍基合金、钛合金、铬合金等。
热障涂层材料具有良好的隔热性能,能够有效减少基础材料受热损伤,延长材料的使用寿命。
同时,热障涂层材料还具有良好的耐腐蚀性能,能够在恶劣环境下保护基础材料不受腐蚀。
此外,热障涂层材料还具有良好的耐磨性能,能够有效减少基础材料的磨损,提高材料的使用寿命。
热障涂层材料在航空航天、能源、汽车等领域有着广泛的应用。
在航空航天领域,热障涂层材料被应用于航空发动机、涡轮机等部件,能够有效提高部件的耐高温性能和耐腐蚀性能,保障飞行安全。
在能源领域,热障涂层材料被应用于燃气轮机、燃烧器等部件,能够有效提高部件的使用寿命和热效率。
在汽车领域,热障涂层材料被应用于发动机缸体、排气管等部件,能够有效提高部件的耐高温性能和耐磨性能,提高汽车的性能和可靠性。
总之,热障涂层材料是一种具有广泛应用前景的高温材料,具有优异的隔热性能、耐高温性能、耐腐蚀性能和耐磨性能。
它在航空航天、能源、汽车等领域有着广泛的应用,能够有效保护基础材料不受热损伤,延长材料的使用寿命,提高部件的性能和可靠性。
随着科技的不断进步,相信热障涂层材料将会有更广阔的发展空间,为各行业的发展做出更大的贡献。
新型热障涂层材料的研发与性能优化

新型热障涂层材料的研发与性能优化随着航空、航天、能源等领域的不断发展,热障涂层材料越来越重要。
它们是一种用于减少高温环境下材料热损失的涂层,广泛应用于航空发动机叶片、燃烧室内衬、热交换器和燃气轮机叶片等部件上。
但是,随着现代工业和科技的不断进步,对热障涂层材料的性能要求也越来越高。
因此,新型热障涂层材料的研发和性能优化变得尤为重要。
第一,研发新型热障涂层材料的需求热障涂层材料在航空、航天、能源等领域中,有着不可替代的重要作用。
但随着现代科技的不断发展,更高的性能要求也在不断提出,例如高温抗氧化性、高温低热传递、高韧性、高耐磨性等等。
而传统的热障涂层材料已经无法满足这些要求,因此需要研发新型热障涂层材料。
第二,新型热障涂层材料的分类新型热障涂层材料包括光子晶体、纳米材料、复合材料、金属基材料、氧化物材料等。
这些材料都具有较高的性能,但它们的应用和实践还需要与传统材料进行比较和研究,以确定其性能和适用性。
第三,对新型热障涂层材料的性能优化针对新型热障涂层材料的缺点和优点,可以通过以下方式进行性能优化:1. 不断进行材料的研究和测试,以保证热障涂层材料的稳定性、热慢变性等性能。
2. 提高材料的抗氧化性和耐热性能,以保证热障涂层材料的长期使用寿命。
3. 研究和发展新的热障涂层材料的生产、制备和加工工艺,以降低成本、提高热障涂层材料的质量和性能。
4. 增强热障涂层材料的损伤诊断和评估技术,以预测和评估热障涂层材料的损伤和寿命,提升使用可靠性。
第四,新型热障涂层材料的应用新型热障涂层材料不仅能够应用于航空发动机叶片、燃烧室内衬、热交换器和燃气轮机叶片等部件上,还能应用于其他领域,例如石油化工、电力设备、医疗和船舶等领域。
这些材料可在高温和极端环境下发挥重要的作用,使机械设备能够更加可靠和稳定地运行,从而提高生产效率和使用安全性。
总结新型热障涂层材料的研发和性能优化是一个重要的课题,需要不断地进行材料的研究、测试和开发。
热障涂层研究现状的综述
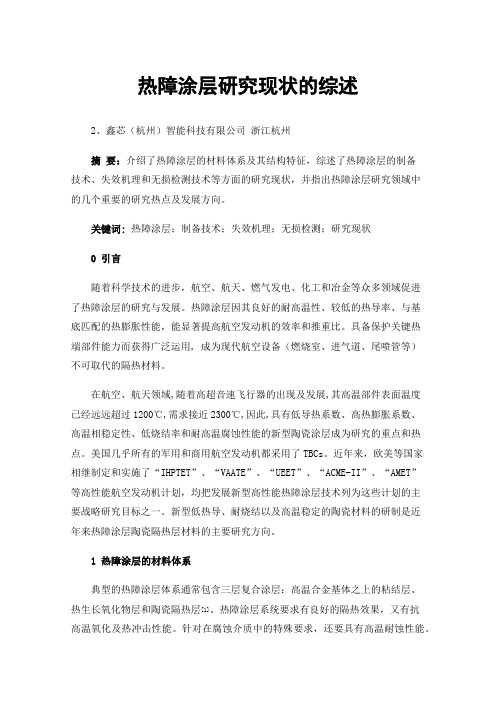
热障涂层研究现状的综述2、鑫芯(杭州)智能科技有限公司浙江杭州摘要:介绍了热障涂层的材料体系及其结构特征,综述了热障涂层的制备技术、失效机理和无损检测技术等方面的研究现状,并指出热障涂层研究领域中的几个重要的研究热点及发展方向。
关键词:热障涂层;制备技术;失效机理;无损检测;研究现状0引言随着科学技术的进步,航空、航天、燃气发电、化工和冶金等众多领域促进了热障涂层的研究与发展。
热障涂层因其良好的耐高温性、较低的热导率、与基底匹配的热膨胀性能,能显著提高航空发动机的效率和推重比。
具备保护关键热端部件能力而获得广泛运用, 成为现代航空设备(燃烧室、进气道、尾喷管等)不可取代的隔热材料。
在航空、航天领域,随着高超音速飞行器的出现及发展,其高温部件表面温度已经远远超过1200℃,需求接近2300℃,因此,具有低导热系数、高热膨胀系数、高温相稳定性、低烧结率和耐高温腐蚀性能的新型陶瓷涂层成为研究的重点和热点。
美国几乎所有的军用和商用航空发动机都采用了TBCs。
近年来,欧美等国家相继制定和实施了“IHPTET”、“VAATE”、“UEET”、“ACME-II”、“AMET”等高性能航空发动机计划,均把发展新型高性能热障涂层技术列为这些计划的主要战略研究目标之一。
新型低热导、耐烧结以及高温稳定的陶瓷材料的研制是近年来热障涂层陶瓷隔热层材料的主要研究方向。
1热障涂层的材料体系典型的热障涂层体系通常包含三层复合涂层:高温合金基体之上的粘结层、热生长氧化物层和陶瓷隔热层[1]。
热障涂层系统要求有良好的隔热效果,又有抗高温氧化及热冲击性能。
针对在腐蚀介质中的特殊要求,还要具有高温耐蚀性能。
因此,新型低热导、耐烧结以及高温稳定的陶瓷材料的研制是近年来热障涂层陶瓷隔热层材料的主要研究方向。
YSZ因其较低的热导率和较高的热膨胀系数成为当前应用最为广泛的热障涂层材料。
YSZ 材料发展至今,已经通过理论计算和实验合成等对其材料性能进行了较为全面的研究。
先进热障涂层的综述

关于先进热障涂层的综述摘要:在过去的几十年中,许多陶瓷材料都被作为新型的热障涂层材料,其中很大一部分都是氧化物。
由于它独特的性能,这些新型化合物很难与最先进的热障涂层材料YSZ相媲美。
另一方面,由于YSZ有一些缺点,尤其是在1200℃以上时它有限的高温性能使得在先进的燃气轮机中YSZ被其他材料所取代。
本篇文献是对不同新型涂层材料的综述,尤其是参杂氧化锆、烧绿石、钙钛矿和氯酸盐等材料。
文献的结果还有由我们的研究调查得出的结果都将同我们的要求相比较。
最终,我们将讨论双层结构这个概念。
它是一种克服新型热障涂层材料冲击韧性的方法关键词:热障涂层、氧化锆、烧绿石、钙钛矿、氯酸盐、热导率一、简介TBC系统是典型的双层式结构,它包括金属粘结层和陶瓷顶层。
粘结层是保护基层氧化和腐蚀的并有改善陶瓷层和基层之间结合强度的作用。
陶瓷顶层相比金属机体而言拥有很低的热传导率,通过内冷发陶瓷层可以实现一个很大的温差度(几百K)。
因此,它既可以降低金属基体的温度以提高部件的使用寿命又可以提高涡轮发动机的点火温度来提高它的工作效率。
自19世纪50年代第一个军用发动机搪瓷涂层的制造起热障涂层开始了工业化发展。
在19世纪60年代,第一个带有NiAl粘结层的火焰喷涂陶瓷涂层应用于商业航空发动机上。
接下来的几十年中,热障涂层材料和喷涂技术持续的发展。
19世纪80年代热障涂层迅猛发展。
在这十年中,氧化钇稳定的氧化锆(YSZ)被认为是一种特殊的陶瓷顶层材料,因为它作为一个近30年来的标准而被确立。
根据沉积工艺的不同,已经确立了两种不同的方法。
一种是电子束物理气相沉积(EB-PVD),另一种是大气等离子喷涂(APS)。
电子束物理气相沉积法制备的涂层拥有柱状显微结构并被广泛应用于航空发动机的高热机械载荷叶片中。
同电子束物理气相沉积法相比,大气等离子喷涂以它的操作粗放度及经济可行性为傲,因此现在更多的TBC 采用这种方法。
典型静态部件,像燃烧器罐和叶片平台都是用APS进行喷涂。
材料特性对热障涂层合理压入深度的影响

第28卷 第5期2008年10月 航 空 材 料 学 报JOURNAL OF AERONAUTI CA L MATER I ALSVol 128,No 15 Oct obe r 2008材料特性对热障涂层合理压入深度的影响钱秀清, 张建宇, 费斌军(北京航空航天大学航空科学与工程学院,北京100083)摘要:基于有限元计算方法和量纲分析原理提出了热障涂层合理压入深度的确定方法,并研究了涂层及基体材料特性对合理压入深度的影响。
首先,根据量纲分析原理提出了合理压入深度的无量纲表达式;其次基于锥形压头识别理想弹塑性材料的材料特性的方法,提出合理压入深度的确定方法;最后研究了各无量纲因素对合理压入深度的影响。
研究发现基体的弹性模量对合理压入深度的影响最大,粘结层材料特性的影响较大,热氧化生成层的材料特性及基体的屈服极限对合理压入深度的影响不大。
关键词:热障涂层;材料特性;压入深度;量纲分析;有限元法中图分类号:O34313 文献标识码:A 文章编号:100525053(2008)0520045205收稿日期22;修订日期226作者简介钱秀清(—),女,博士后,(2)q xq@。
近年来,随着航空发动机向高流量比、高推重比、高进口温度的方向发展,热障涂层(TBC )作为一种有效的热防护技术,已在国内外先进发动机涡轮部件得到广泛的使用[1-2],其材料特性是衡量热端部件性能的重要参数。
测量涂层力学性能的方法有许多,其中压入法通过连续记录压入过程中位移和载荷变化的数值,大大提高了材料参数的测试精度[3]。
用纳米压入法提取涂层的材料特性时,压头的压入响应与涂层和基体的应力与应变场有关。
当压入深度超过某一值后,随着压入深度的增加,基体材料特性的对涂层材料特性提取的影响增加,使得涂层材料特性的测量不准确甚至错误。
通常情况下,认为压入深度取涂层厚度的十分之一可以避免基体塑性变形的影响[4],但是这种理论在涂层材料特性的提取中并没有得到验证[5]。
高性能热障涂层材料的设计与研发

高性能热障涂层材料的设计与研发在现代工业领域中,高温环境的应用日益广泛,涂层材料的设计与研发对于保护高温工件表面、提高工件的耐热性能具有重要意义。
其中,高性能热障涂层材料的设计与研发是一个备受关注和研究的课题。
本文将讨论高性能热障涂层材料的设计原则、制备方法和应用前景等方面的问题。
首先,高性能热障涂层材料的设计需要考虑材料的热导率、热膨胀系数和化学稳定性等因素。
由于高温工作环境对材料性能的严苛要求,热障涂层应具有低热导率,以减少热能传导,提高工作温度下的稳定性。
同时,热膨胀系数与基体材料接近,可以避免因温度变化引起的应力集中,提高涂层的耐久性。
此外,热障涂层材料还应具有良好的化学稳定性,以应对高温下的氧化和腐蚀等问题。
其次,在高性能热障涂层材料的制备方法方面,热喷涂技术是目前应用最广泛的方法。
热喷涂技术包括等离子喷涂、高速喷涂和火焰喷涂等多种方法。
其中,等离子喷涂是一种常用的制备方法,通过等离子态的材料颗粒在高速气流中熔融并沉积在基体表面,形成热障涂层。
高速喷涂则采用超音速喷涂枪将材料颗粒喷射到基体上,可实现更快的涂层制备速度和更高的材料熔融状态。
火焰喷涂则利用火焰燃烧产生的高温气体和气流将材料颗粒喷射到基体表面。
这些制备方法各有优劣,需要根据具体要求选择适合的方法。
此外,高性能热障涂层材料的研发还需要考虑应用领域和需求。
目前,热障涂层在航空航天、能源、石化等行业中得到广泛应用,如航空发动机叶片、燃烧器、涡轮叶片等。
在航空发动机中,高性能热障涂层材料可以提高发动机的工作温度,降低燃烧温度,提高燃烧效率和节约燃料。
而在能源领域,热障涂层材料的应用可提高燃料电池、燃气轮机等设备的效率和寿命。
未来,高性能热障涂层材料的研发还有很大的发展空间和挑战。
随着科技的进步,研究人员可以利用纳米材料、复合材料等先进技术来提高涂层的性能。
例如,使用纳米颗粒来修饰热障涂层的表面,可以增强涂层的耐热性和降低热传导率,从而提高涂层的性能和寿命。
热障涂层表面出现的失效

热障涂层表面出现的失效
热障涂层表面可能出现的失效问题包括:
1. 热障涂层剥落:涂层与基底金属之间的粘附力不足,导致涂层脱落。
主要原因可能是涂层制备不良,或者在使用过程中受到过大的温度变化和热应力。
2. 燃素击穿:在高温和高速气流的作用下,涂层表面可能出现溶解和侵蚀现象,导致涂层的燃素(主要成分为氧化锆)被冲刷掉,从而失去热隔离功能。
3. 裂纹和剥离:热障涂层表面可能出现裂纹,特别是在高温和热应力作用下。
这些裂纹可能导致涂层剥离或开裂,进一步加剧涂层的失效。
4. 腐蚀和氧化:在高温和气体环境中,热障涂层表面可能受到腐蚀和氧化的影响,特别是在存在湿气和腐蚀性物质的环境中。
这些问题可能导致涂层表面的局部失效或全面失效。
5. 热障涂层粒子熔化:在高温环境下,热障涂层表面的颗粒可能遭受熔化,导致涂层表面变得粗糙或失去原有的结构和功能。
这些失效问题可能会降低热障涂层的热隔离性能,从而影响涂层所保护的基底材料和工件的使用寿命和性能。
因此,为了确保热障涂层的有效性和稳定性,需要进行严格的涂层制备、材料选择和应用环境控制等措施。
热喷涂条件对热障涂层性能的影响

热喷涂条件对热障涂层性能的影响热喷涂技术是一种将金属或陶瓷粉末喷涂到基材表面的表面涂层技术。
热障涂层是一种常用的热喷涂涂层,具有优异的耐热性能和隔热性能,在航空航天、能源领域等重要领域得到广泛应用。
然而,热喷涂条件对热障涂层性能有重要影响,本文将从成分、微观结构和性能三个方面探讨热喷涂条件对热障涂层性能的影响。
首先,热障涂层的成分是影响其性能的关键因素之一、热喷涂技术一般通过火焰等单一热源使粉末熔化,并通过气流喷射到基体表面。
在热喷涂过程中,影响成分的主要因素包括喷涂粉末的化学成分和其间杂质的含量。
喷涂粉末的化学成分决定了热障涂层的基本性质,如化学稳定性、热膨胀系数等。
当喷涂粉末的化学成分与基材相似时,喷涂粉末更容易与基材形成结合,提高涂层的附着力。
此外,喷涂粉末中的杂质含量较高时,容易导致涂层中存在氧化物等结构缺陷,降低涂层的抗氧化性能。
其次,热喷涂条件对热障涂层的微观结构产生重要影响。
在热喷涂过程中,粉末被加热至熔化,并通过气流喷射到基体表面,形成涂层。
喷射速度、压力、温度等喷涂条件与涂层的微观结构之间存在一定的关系。
例如,较高的喷射速度和压力能产生更好的涂层附着力,同时也能导致涂层更致密,晶粒更细小。
而温度对于涂层中晶体的生长速率有重要影响。
在合适的温度范围内,晶体生长速度较快,晶粒相对较大;而在过高的温度下,晶体生长速度过快,晶粒易出现过大的情况。
因此,恰当的热喷涂条件可以调控涂层的微观结构,从而影响其性能。
最后,热喷涂条件对热障涂层的性能产生直接影响。
热喷涂技术制备的热障涂层通常具有较高的孔隙率和粗糙度,这些因素可以直接影响其导热性能和氧化性能。
消除涂层的孔隙和提高其致密性是提高热障涂层性能的关键。
合适的喷涂条件和方法可以减少喷涂过程中的气体和杂质的含量,降低涂层中的孔隙率。
此外,增加喷涂粉末的熔融性能和降低喷枪与基体之间的距离也有助于改善涂层的性能。
通过调整喷涂条件,可以优化涂层的孔隙率、粗糙度和致密性,从而获得具有优异性能的热障涂层。
航空发动机热障涂层结构的低速冲击性能研究

航空发动机热障涂层结构的低速冲击性能研究随着现代航空运输的不断发展和进步,越来越多的研究致力于新型航空发动机的研制。
其热障涂层是航空发动机的关键部件之一。
热障涂层能够保护发动机表面不受高温及高速气流的侵蚀,同时增强发动机的耐久性和稳定性。
然而,航空发动机在起飞、着陆、飞行等过程中可能会遭受到多种不同类型的冲击,这些冲击会对涂层产生一定的损伤和破坏。
因此,对热障涂层的低速冲击性能进行深入研究,对于提高航空发动机的安全性和性能具有一定的重要意义。
热障涂层主要分为陶瓷涂层、氧化铝涂层、氧化硅涂层等几种。
其中,氧化铝涂层的使用较为广泛,其具有高耐磨性、耐高温性、抵抗腐蚀等优点。
同时,热障涂层的冲击性能主要受到热障涂层微观结构和材料性质的影响。
研究表明,热障涂层的组织结构、厚度及材料的机械性能对其冲击性能有着重要的影响。
低速冲击性能是指在低速冲击载荷下,热障涂层宏观损伤的能力。
通常采用冲击试验来考察热障涂层的低速冲击性能。
在冲击试验中,球形或柱状冲击头以一定速度冲击涂层表面,通过对冲击头与涂层之间的相互作用来评估热障涂层的冲击性能。
在热障涂层的冲击试验中,常采用冲击头直径、冲击速度、冲击质量、冲击次数等参数来记录热障涂层的低速冲击性能。
同时,还需要掌握热障涂层在冲击过程中宏观损伤的特征以及微观损伤机理等方面的信息。
目前,国内外对热障涂层低速冲击性能的研究取得了一定的进展。
各种不同类型的冲击试验方法和试验设备被设计和应用。
然而,对于热障涂层冲击载荷下的真实效应和力学响应还需要深入研究。
因此,未来研究方向应包括但不限于以下几个方面:1.构建模型以掌握冲击载荷下的微观力学信息热障涂层组织结构和材料性质等因素对其低速冲击性能有着非常重要的影响。
在未来的研究中,应建立尽可能准确的模型来了解其在冲击载荷下受到的力学作用,并从中掌握涂层材料的响应过程。
草图和有限元分析可以为模型的建立和分析提供很大的帮助。
2.多样化的冲击实验方法热障涂层的低速冲击性能的评估应该结合现实中的不同载荷环境,并应小心接受不同方法(例如角度冲击,冲击轨迹等)在其表现中的帮助。
热障涂层在900℃混盐中的抗热腐蚀性能
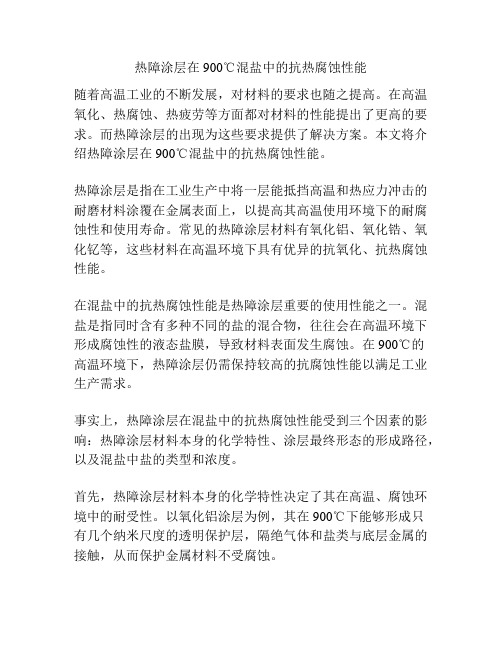
热障涂层在900℃混盐中的抗热腐蚀性能随着高温工业的不断发展,对材料的要求也随之提高。
在高温氧化、热腐蚀、热疲劳等方面都对材料的性能提出了更高的要求。
而热障涂层的出现为这些要求提供了解决方案。
本文将介绍热障涂层在900℃混盐中的抗热腐蚀性能。
热障涂层是指在工业生产中将一层能抵挡高温和热应力冲击的耐磨材料涂覆在金属表面上,以提高其高温使用环境下的耐腐蚀性和使用寿命。
常见的热障涂层材料有氧化铝、氧化锆、氧化钇等,这些材料在高温环境下具有优异的抗氧化、抗热腐蚀性能。
在混盐中的抗热腐蚀性能是热障涂层重要的使用性能之一。
混盐是指同时含有多种不同的盐的混合物,往往会在高温环境下形成腐蚀性的液态盐膜,导致材料表面发生腐蚀。
在900℃的高温环境下,热障涂层仍需保持较高的抗腐蚀性能以满足工业生产需求。
事实上,热障涂层在混盐中的抗热腐蚀性能受到三个因素的影响:热障涂层材料本身的化学特性、涂层最终形态的形成路径,以及混盐中盐的类型和浓度。
首先,热障涂层材料本身的化学特性决定了其在高温、腐蚀环境中的耐受性。
以氧化铝涂层为例,其在900℃下能够形成只有几个纳米尺度的透明保护层,隔绝气体和盐类与底层金属的接触,从而保护金属材料不受腐蚀。
其次,涂层最终形态的形成路径对于其在混盐中的抗腐蚀性能也起着至关重要的作用。
例如,对于一些过厚的热障涂层,其表面将形成多孔状的表面形貌,表面的微观孔洞等缺陷都将成为盐的渗透道,从而降低了涂层的抗腐蚀性。
最后,与混盐中盐的类型和浓度有关。
一般来说,氯化物、硫酸盐、硝酸盐等高浓度的盐类会更加容易造成材料表面的损伤。
这时候,热障涂层材料需要选择更高级别的材料,以增加其抵御盐危害的能力。
总之,热障涂层在900℃混盐中的抗热腐蚀性能受到多因素的影响,而含氧化铝、氧化锆、氧化钇等材料的热障涂层能够提供比较优秀的抗腐蚀性能。
对于混盐中较高浓度的盐类,热障涂层需使用更高级别的材料以提升其抵御盐危害的能力。
热障涂层的不断发展将会进一步提升材料的高温使用环境下的耐腐蚀性和使用寿命,为高温工业的发展提供坚实的支撑。
新型热障涂层材料的设计制备及其应用研究
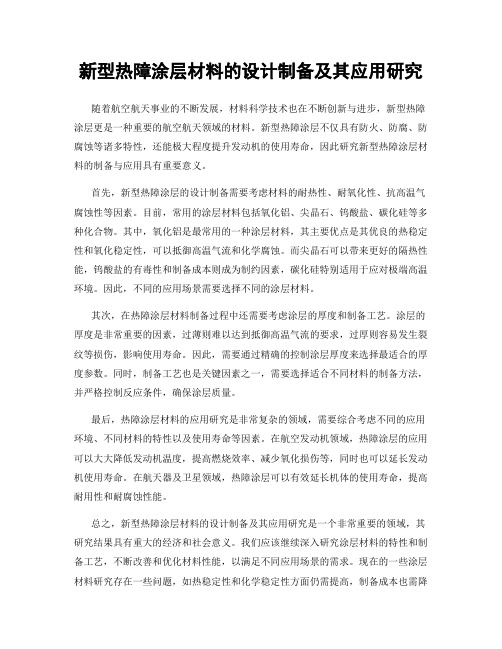
新型热障涂层材料的设计制备及其应用研究随着航空航天事业的不断发展,材料科学技术也在不断创新与进步,新型热障涂层更是一种重要的航空航天领域的材料。
新型热障涂层不仅具有防火、防腐、防腐蚀等诸多特性,还能极大程度提升发动机的使用寿命,因此研究新型热障涂层材料的制备与应用具有重要意义。
首先,新型热障涂层的设计制备需要考虑材料的耐热性、耐氧化性、抗高温气腐蚀性等因素。
目前,常用的涂层材料包括氧化铝、尖晶石、钨酸盐、碳化硅等多种化合物。
其中,氧化铝是最常用的一种涂层材料,其主要优点是其优良的热稳定性和氧化稳定性,可以抵御高温气流和化学腐蚀。
而尖晶石可以带来更好的隔热性能,钨酸盐的有毒性和制备成本则成为制约因素,碳化硅特别适用于应对极端高温环境。
因此,不同的应用场景需要选择不同的涂层材料。
其次,在热障涂层材料制备过程中还需要考虑涂层的厚度和制备工艺。
涂层的厚度是非常重要的因素,过薄则难以达到抵御高温气流的要求,过厚则容易发生裂纹等损伤,影响使用寿命。
因此,需要通过精确的控制涂层厚度来选择最适合的厚度参数。
同时,制备工艺也是关键因素之一,需要选择适合不同材料的制备方法,并严格控制反应条件,确保涂层质量。
最后,热障涂层材料的应用研究是非常复杂的领域,需要综合考虑不同的应用环境、不同材料的特性以及使用寿命等因素。
在航空发动机领域,热障涂层的应用可以大大降低发动机温度,提高燃烧效率、减少氧化损伤等,同时也可以延长发动机使用寿命。
在航天器及卫星领域,热障涂层可以有效延长机体的使用寿命,提高耐用性和耐腐蚀性能。
总之,新型热障涂层材料的设计制备及其应用研究是一个非常重要的领域,其研究结果具有重大的经济和社会意义。
我们应该继续深入研究涂层材料的特性和制备工艺,不断改善和优化材料性能,以满足不同应用场景的需求。
现在的一些涂层材料研究存在一些问题,如热稳定性和化学稳定性方面仍需提高,制备成本也需降低等。
未来,随着材料科学技术的不断进步,新型热障涂层材料的性能一定会越来越优化,应用范围也会越来越广泛,这为航空航天事业的发展提供了有力的支持。
热障涂层的研究进展

热障涂层的研究进展随着现代工业的发展,高温材料的应用越来越广泛,如航空发动机、燃气涡轮等。
然而,高温环境下的材料容易发生氧化、腐蚀等问题,降低了材料的使用寿命和可靠性。
为了解决这一问题,人们引入了热障涂层技术,使其在高温工作环境中具有更优异的性能。
热障涂层是一种在金属表面涂覆陶瓷材料的技术,通过降低热通量的方式实现保护材料的目的。
它的特性包括良好的隔热性、抗氧化性、抗腐蚀性、抗磨损性等,使其广泛应用于航空航天、石油、化工、冶金等行业。
近年来,研究人员对热障涂层的性能进行了深入的研究和探讨,取得了不俗的成果。
热障涂层材料的研究热障涂层材料的性能主要取决于表面涂层的结构和材料的选择。
目前,常见的热障涂层材料包括氧化铝、氧化锆、氧化镁、二氧化硅等,其中以氧化铝涂层应用最为广泛。
研究人员通过对涂层材料的组织结构、化学成分等方面的研究,不断优化和提升热障涂层的性能。
例如,一些研究人员通过改变涂层中氧化铝和氧化锆的组成比例,制备了一种新型热障涂层材料。
实验结果表明,该涂层具有更好的耐热性能和耐磨性能,可以有效地提升高温材料的使用寿命。
另外,一些研究人员通过改变热障涂层中陶瓷颗粒的尺寸、形状等参数,探讨了不同参数对涂层性能的影响。
研究结果发现,涂层颗粒尺寸越大,涂层的热阻值越大;而颗粒形状则会对涂层磨损、断裂等性能产生影响。
热障涂层加工技术的研究由于热障涂层是一种高技术含量的涂层技术,其加工过程也十分关键。
研究人员对热障涂层加工技术进行了系统研究,探讨不同加工方法对涂层性能的影响,并提出了相应的改进方案。
例如,一些研究人员对热障涂层的喷涂工艺进行了优化,采用了高速火焰喷涂技术,实现了高效、节能的喷涂过程,同时提高了涂层质量和性能。
另外,研究人员还在热障涂层加工过程中引入了纳米材料,提高了涂层的性能和稳定性。
纳米材料具有较高的比表面积和活性,可以增加涂层的强度、硬度和耐磨性。
热障涂层应用领域的研究热障涂层技术的应用领域越来越广泛,涉及到航空、航天、汽车、船舶、石油、化工、冶金等多个领域。
CMAS对热障涂层影响的研究的开题报告

CMAS对热障涂层影响的研究的开题报告
热障涂层是一种用于保护高温部件(如航空发动机、燃气轮机等)
的涂层。
但是,随着使用时间的增长和高温环境下的运行,热障涂层会
出现磨损、剥落等问题,影响其保护作用。
为了解决这一问题,不断研
究热障涂层的耐久性和稳定性显得尤为重要。
CMAS(钙镁铝硅酸盐)是一种高温灰渣,通常由燃料中的杂质和燃烧产物组成。
CMAS在高温环境下与热障涂层发生反应,会导致热障涂层的撕裂、瓦解和降解等问题。
因此,研究CMAS对热障涂层的影响至关
重要。
本论文旨在研究CMAS对热障涂层的影响,具体包括以下内容:
1. 热障涂层的类型和工作原理;
2. CMAS在高温环境下与热障涂层发生反应的机理;
3. 研究方法:选择有代表性的热障涂层材料,并以CMAS的形式进
行侵蚀实验,分析侵蚀前后热障涂层的结构和性能变化;
4. 结果分析:通过分析实验结果,探究CMAS对热障涂层的影响,
以及影响的程度和范围;
5. 结论和展望:总结实验结果,探讨研究的局限和未来的发展方向。
本论文的研究结果可以为热障涂层在高温环境下的应用提供一定的
理论和实践参考,具有一定的科学意义和实用价值。
Al2O3含量对YSZ热障涂层性能的影响

Al2O3含量对YSZ热障涂层性能的影响李宇杰;于月光;冀晓鹃;侯伟骜;贾芳【摘要】Al2O3等氧化物对YSZ热障涂层的高温使用性能有一定的影响.本文用HVOF喷涂NiCoCrAlY合金粘结层,APS喷涂YSZ陶瓷面层,制备了Al2O3含量为0.01~0.64wt%的YSZ涂层.比较了不同Al2O3含量的YSZ涂层在1100℃下的热震性能和抗烧结性能,并探讨Al2O3对涂层的影响机理.结果表明相较于高纯YSZ 涂层,随着涂层中Al2O3含量升高,涂层的抗热震性能降低,且Al2O3促进YSZ涂层的烧结.Al2O3含量在小于0.01wt%-0.12wt%区间内时,对涂层抗热震和抗烧结性能有显著影响,含量继续增加至0.64%时,对性能影响减缓.显微组织观察与EDS检测结果表明涂层中Al2O3并未在熔融颗粒界面处偏聚,但在颗粒内部有局部偏析.由此推测,含Al2O3的YSZ涂层热震失效的原因可能是Al2O3在YSZ颗粒内部偏析,并影响涂层的烧结性能,导致裂纹容易萌生和扩展.【期刊名称】《热喷涂技术》【年(卷),期】2018(010)001【总页数】7页(P62-68)【关键词】热障涂层;抗热震性能;抗烧结性能;Al2O3;偏析【作者】李宇杰;于月光;冀晓鹃;侯伟骜;贾芳【作者单位】北京矿冶研究总院,北京100160;北京市工业部件表面强化与修复工程技术研究中心,北京102206;北京矿冶科技集团有限公司,北京100160;北京市工业部件表面强化与修复工程技术研究中心,北京102206;北京矿冶科技集团有限公司,北京100160;北京市工业部件表面强化与修复工程技术研究中心,北京102206;北京矿冶科技集团有限公司,北京100160;北京市工业部件表面强化与修复工程技术研究中心,北京102206;北京矿冶科技集团有限公司,北京100160;北京市工业部件表面强化与修复工程技术研究中心,北京102206【正文语种】中文【中图分类】TG174.40 引言随着航空航天技术的快速发展,航空发动机涡轮前进口温度不断提高,使得发动机结构材料的工作环境恶化,从而对高温结构材料提出更高的性能要求[1,2]。
金属粘结层对PS-PVD热障涂层的影响及机理研究

金属粘结层对PS-PVD热障涂层的影响及机理研究随着我国航空事业的不断发展,发动机的推重比不断升高,使得发动机叶片所承受的温度也越来越高,需要结合热障涂层技术使叶片所承受的温度降低。
等离子喷涂-物理气相沉积(PS-PVD)技术是基于低压等离子喷涂发展起来的一种新型多功能薄膜及涂层制备技术,由于其独特的等离子射流特征可实现气液固多相涂层沉积,同时还可进行非视线沉积,有望成为下一代新型热障涂层制备技术。
粘结层作为热障涂层体系中一个必要组成部分,提供抗氧化、抗腐蚀和调节热膨胀系数的作用,同时影响到热障涂层的抗剥落等性能,有着至关重要的研究意义本文以DZ40M合金为基体,在其上制备NiCrAlY与CoCrAlSiY两种粘结层,探究粘结层/基体Al元素扩散情况;采用PS-PVD技术在粘结层上制备YSZ涂层,研究了两种不同粘结层体系热障涂层的结合强度、热震性能及抗氧化性能的差异,主要得出以下结论。
(1)在DZ40M高温合金基体上分别制备NiCrAlY与CoCrAlSiY两种的粘结层,对两种试样进行25h、50h、100h的真空扩散处理,并对扩散后粘结层/基体界面位置处Al元素的含量进行测量,发现试验后粘结层中而对Al元素向机体内发生了明显的扩散现象,随着扩散距离的增加Al元素含量不断减小,并且相同位置处扩散时间越长Al元素含量越高。
同时计算了两种试样不同位置处Al元素的扩散系数,发现随着扩散距离的增加,Al元素扩散系数逐渐下降。
(2)NiCrAlY/YSZ和CoCrAlSiY/YSZ两种热障涂层的结合强度分别为66.7MPa和59.0MPa,由于两种涂层的断裂位置的区别造成了结合强度的差异。
两种涂层经过150次水淬试验后,NiCrAlY/YSZ涂层在TGO 层与陶瓷之间的界面处出现了连续的裂纹,而CoCrAlSiY/YSZ涂层的裂纹主要位于陶瓷层中间部位。
通过纳米压痕试验分析了两种涂层水淬后粘结层中的残余应力,结果显示两种涂层水淬后粘结层中都产生了残余拉应力,CoCrAlSiY粘结层中的残余拉应力更大,导致CoCrAlSiY/YSZ涂层中裂纹的尺寸及数量也更大。
- 1、下载文档前请自行甄别文档内容的完整性,平台不提供额外的编辑、内容补充、找答案等附加服务。
- 2、"仅部分预览"的文档,不可在线预览部分如存在完整性等问题,可反馈申请退款(可完整预览的文档不适用该条件!)。
- 3、如文档侵犯您的权益,请联系客服反馈,我们会尽快为您处理(人工客服工作时间:9:00-18:30)。
第28卷 第5期2008年10月航 空 材 料 学 报J OURNAL OF A ERONAUT ICAL MAT ER I A LSV o l 28,N o 5 O ctober 2008材料特性对热障涂层合理压入深度的影响钱秀清, 张建宇, 费斌军(北京航空航天大学航空科学与工程学院,北京100083)摘要:基于有限元计算方法和量纲分析原理提出了热障涂层合理压入深度的确定方法,并研究了涂层及基体材料特性对合理压入深度的影响。
首先,根据量纲分析原理提出了合理压入深度的无量纲表达式;其次基于锥形压头识别理想弹塑性材料的材料特性的方法,提出合理压入深度的确定方法;最后研究了各无量纲因素对合理压入深度的影响。
研究发现基体的弹性模量对合理压入深度的影响最大,粘结层材料特性的影响较大,热氧化生成层的材料特性及基体的屈服极限对合理压入深度的影响不大。
关键词:热障涂层;材料特性;压入深度;量纲分析;有限元法中图分类号:O 343 3 文献标识码:A 文章编号:1005-5053(2008)05-0045-05收稿日期:2007-09-07;修订日期:2008-01-16作者简介:钱秀清(1971 ),女,博士后,(E -m ail )q i anxq @buaa .edu .cn 。
近年来,随着航空发动机向高流量比、高推重比、高进口温度的方向发展,热障涂层(TBC)作为一种有效的热防护技术,已在国内外先进发动机涡轮部件得到广泛的使用[1-2],其材料特性是衡量热端部件性能的重要参数。
测量涂层力学性能的方法有许多,其中压入法通过连续记录压入过程中位移和载荷变化的数值,大大提高了材料参数的测试精度[3]。
用纳米压入法提取涂层的材料特性时,压头的压入响应与涂层和基体的应力与应变场有关。
当压入深度超过某一值后,随着压入深度的增加,基体材料特性的对涂层材料特性提取的影响增加,使得涂层材料特性的测量不准确甚至错误。
通常情况下,认为压入深度取涂层厚度的十分之一可以避免基体塑性变形的影响[4],但是这种理论在涂层材料特性的提取中并没有得到验证[5]。
本工作主要针对热障涂层,对多层涂层结构的合理压入深度进行研究。
1 材料模型和量纲分析用于发动机的典型的热障涂层是一个多层结构,包括合金基体、金属粘结层、热氧化生成层和陶瓷涂层[2,6,7],如图1所示。
其中,陶瓷涂层的厚度约为100~200 m ,热氧化生成层是热障涂层在加工和受热过程中产生的,层厚随时用时间而增加,在0~8 m 之间变化,粘结层的厚度约为50~100 m。
图1 热障涂层结构示意图F ig 1 S tructure ske tch of the r ma l ba rr ier coa tings1 1 材料模型考虑半锥角为70 3 的刚性压头压入弹塑性涂层的情况。
根据G a m onpilas 和Busso [5]的研究,材料的应变硬化指数对合理压入深度的影响不大,因此本文仅考虑理想弹塑性材料,材料模型为: =E ( y )(1)=E y = y ( > y )(2)其中,E 为材料的弹性模量, , 分别为应力和应变, y , y 分别为屈服应力和屈服应变。
1 2 量纲分析对于弹塑性材料的锥形压头压入,在压入过程中,合理压入深度h l 是下列独立参数的函数:涂层的弹性模量E c 、泊松比v c 、屈服强度 yc 、厚度h c ;热氧化生成层的弹性模量E o 、泊松比v o 、屈服强度 yo 、厚度h o ;粘结层的弹性模量E b 、泊松比v b 、屈服强度 yb 、厚度h b ;基体的弹性模量E s 、泊松比v s 、屈服强度 ys ,刚性压头的半锥角 ,即h l =f h (E c , yc ,v c ,h c ,E o , yo ,v o ,h o ,E b , yb ,航 空 材 料 学 报第28卷v b ,h b ,E s , ys ,v s , )(3)利用复合模量的概念[8],令1E *i=1-v 2i E i (4)则(3)式可写为h l =f h (E *c , yc ,h c ,E *o , yo ,h o ,E *b , yb ,h b ,E *s, ys , )(5)根据 定理,可以将一个包括k 个变量的有物理意义的方程等效地写成包括k -m 个无量纲参数的方程,其中m 是所用基本量纲的数目。
即使方程的形式未知,也可以根据已知的变量计算这些无量纲参数。
因此,(5)式可写为 h lh c= h (E *c E *s ,E *o E *s ,E *b E *s, yc E *s , yo E *s , yb E *s , ys E *s ,h o h c ,h bh c, )(6)2 有限元计算采用AB AQUS 软件进行有限元模拟计算,取20020个四节点双线性轴对称单元,单元在接触区域网格划分较细,见图2;基体厚度取得足够大,使得边界条件对计算结果没有影响;边界条件选取外表面无面力,下表面节点固定z 向位移和转动;材料假设为各向同性幂强化材料,屈服准则选取M ises 准则,包含大变形;假设压头为刚体, 取70 3 ;压头与涂层之间的摩擦系数取0 15。
图2 有限元网格F i g 2 M esh o f the fi n ite ele m ent用于发动机的热障涂层多为含Y 2O 3稳定的Zr O 2陶瓷涂层,由于受涂层加工过程的影响,材料特性测量数值变化较大[10]。
热氧化生成层成分基本为AL 2O 3。
粘结层的材料多为MC r A LY 。
基体多为耐热合金[3,6,9,10]。
考虑到热障涂层的特点,为了简化计算,本文不研究涂层中各层厚度及泊松比变化对合理压入深度的影响,取h o /h c =1/25,h b /h c =1/2;各层材料的泊松比为[7]:涂层取为0 1,热氧化生成层0 23,粘结层0 3,基体0 33。
材料参数取值范围如下[3,7,10~12]:E *c /E *s =0 09~4 5,E *o /E *s =0 94~9 4,E *b /E *s =0 245~9 8, yc /E *s =0 00223~0 0668, yo /E *s =0 00022~0 045, yb /E *s =0 0022~0 0066, ys /E *s =0 0011~0 0066。
为方便计算,假设基体的材料特性不变,取为E s =200GPa 。
3 合理压入深度的确定3 1 材料参数识别方法 根据Cao 等[13]利用球形压头识别的材料弹性模量的方法,对于理想弹塑性材料,采用半锥角为70 3 的刚性锥形压头,选择比较宽的材料参数范围:4<E / y <6667,通过有限元计算得到压入的载荷位移曲线,求得w ,经研究发现压入曲线的斜率C 与复合弹性模量E *的比值C /E *与压入曲线弹性功与总功的比值w 之间存在一一对应的关系,如图3所示。
图3 C /E *与w 之间的关系F i g 3 R elationsh i p of C /E *and w用下列函数拟合上述关系得到:C E*=4 5409w -7 8750w 2+19 5358w 3- 32 3246w 4+26 4483w 5-8 3919w 6(7)其中:w =W e /W t。
同样,对于理想弹塑性材料,当锥形压头压入时,屈服应力与压入曲线的斜率C 之比值 y /C 与w 之间也存在一一对应的关系,如图4所示。
用指数函数拟合上述关系得到:yC=7 1812e w0 04856-25 3284+0 00022ew0 17805+0 03421w 0 93185-0 02575(8)由压入实验得到的载荷位移曲线直接测量得到w 和C 后,就可识别出材料的复合弹性模量E *和屈46第5期材料特性对热障涂层合理压入深度的影响图4 y /C 与w 之间的关系F i g 4 R e l a ti ons h i p o f y /C and w服极限 y ,从而得到E 和 y 。
3 2 合理压入深度的确定方法保持涂层与基体各参数不变,不断改变压头的压入深度,通过大量的有限元模拟计算发现:涂层弹性模量的识别误差随着压入深度的增加而呈线形增大,如图5所示,因此涂层材料参数的识别精度与压入深度有很大关系。
可取识别材料弹性模量和屈服极限的最大误差在 (本文取5%)以内的压入深度为合理压入深度。
例如根据上述计算,当h /h c <5%时,弹性模量的识别误差小于5%,屈服极限的识别误差小于1%,因此,合理压入深度可取h l /h c =5%。
4 影响合理压入深度的因素分析4 1 yo /E *s 及E *o /E *s 的影响取E *c /E *s =0 225,E *b /E *s =0 98, ys /E *s =0 022, yb /E *s = ys /E *s =0 0044时,研究参数 yo /E *s 和E *o /E *s 对合理压入深度的影响。
经计算发现,当E*o/E *s 从0 94变到9 4时, yo /E *s从图5 识别材料参数的误差随压入深度的变化F i g 5 V ar i a tion o f the i dentified errors of m ater i a lsproperti es w ith the indenta ti on dep t h0 00022变到0 044时,合理压入深度均为涂层厚度的5 4%变化到5 3%,变化很小,如图6a 所示。
取E *c /E *s =0 9,其他参数不变,研究参数 yo /E *s 和E *o /E *s 对合理压入深度的影响。
经计算发现,合理压入深度在涂层厚度的18%~23%之间,变化也不大,如图6b 所示。
分析涂层系统各层厚度可知,由于这两个参数都与热氧化生成层有关,而该层的厚度仅为涂层厚度的1/25,因此其材料特性对合理压入深度的影响不大。
4 2 E *b /E *s 及 yb /E *s 的影响取E *c /E *s =0 225,E *o /E *s =1 88, yc /E *s =0 022, yo /E *s =0 022, ys /E *s =0 0044时,研究E *b /E *s 及 yb /E *s 对合理压入深度的影响。
研究结果显示粘结层的弹性模量对合理压入深度有较大的影响,而屈服极限对于合理压入深度没有影响,因为当h /h c 7 6%时,热氧化生成层、粘结层和基体都没有屈服,因此屈服极限对于合理压入深度没有影响。
如果参数E *c /E *s 取为0 9,则情况如图7b所图6 yo /E *s 及E *o /E *s 对合理压入深度的影响F i g 6 E ffec ts o f yo /E *s and E *o /E *s on the reasonab l e i ndenta tion depth(a)E *c /E *s =0 225;(b)E *c /E *s =0 947航 空 材 料 学 报第28卷图7 E *b /E *s 及 y b /E *s 对合理压入深度的影响F i g 7 E ffects of E *b /E *s and yb /E *s on the reasonab l e indenta ti on dept h(a)E *c /E *s =0 225;(b)E *c /E *s =0 9示。