【EP3561428A1】HEATPIPEWITHCAPILLARYPUMPINGWITHIMPRO
Peerless ELS垂直湍流水泵说明书

Enclosed Line Shaft Threaded ColumnSpecificationsCapacities: ..............Up to 100,000 gpm (2,273 m 3/hr)Head: ........................Up to 2,300 feet (760 meters)Pressure: .................Fit to the applicationHorsepower: .........Up to 5,000 hp (3,730 kW)Temperature: .........Up to 180 °F (82 °C)Drives: .......................Vertical electric motors, engines with right angle gears,combination gear drives, or vertical motors with variable speed drives Liquids: .....................Water or abrasive liquidsMaterials: .................Cast iron/bronze-fitted standard; alternate materials available to suit the application.Peerless PumpThe Peerless Pump ELS vertical turbinepump provides a wide range of hydraulic and mechanical coverage. Peerless Pump offers many different material and design configurations; these numerous configuration options allow for custom-engineered construction tailored to suit your requirements. Maximum value, high efficiency and economical long-term pump performance are assured in each application.ApplicationsELS pumps can be lubricated either with oil or a clean water flush. Corrosion-resistant materials are available for many industrial uses. Applications vary from small, single pump commercial applications to large, multi-pump municipal water supply systems . ELS pumps are appropriate for both raw water transfer and finished water projects. They are also widely used in mining and agriculture . In addition, Peerless ELS vertical lineshaft pumps are the best choice for deep-set wells (up to 1500 feet).FeaturesPeerless Pump’s standard cast iron discharge head can handle pressures up to 400 psi . Discharge heads are standardized to accommodate the maximum number of NEMA motor sizes, and a variety of options such as fabricated steel construction or underground discharge are available.Enclosed-type bronze impellers are standard. Peerless impellers cover a wide range of flow and head conditions. Each impeller is balanced for smooth operation .Peerless standard ELS bowls are cast with integral vanes to guide the flow to the next stage with minimum losses and maximum efficiency . Bypass ports cast in the top bowl equalize the internal tube pressure and prevent the pumped liquid from entering the lubrication line and bearings. In addition, all bowls are porcelain-lined for protection and efficiency.Peerless Pump pioneered and patented the “double seal” feature in bowls. The two sealing surfaces prevent efficiency-robbing recirculation within the bowl. Minimal radial clearances between the impeller skirt and the bowl create a dynamic sealing surface. The static sealing surface is the lateral ring, installed into the bowl below the impeller skirt. This lateral ring is constructed of a rigid metallic core surrounded by heavy-duty resilient rubber. Lateral rings protect bowl surfaces, provide protection for the impellers in case of catastrophic failures, and enable prolonged pumping efficiency.Threaded column is available for pumps up to 16 inches in diameter. Straight-threaded column is an economical yet durable choice, particularly in the municipal market.Quality EngineeringPeerless Pump designs tough, versatile products to meet your pumping needs. Peerless vertical turbine pumps deliver variety, durability, standardized options and configurations unequalled in the industry. Please contact your local Peerless Pump sales office to find outmore about vertical turbine pump options and prices.Vertical Lineshaft Turbine PumpsThe content of this brochure is subject to change without notice. Copyright 2003 by Peerless Pump Company. Printed in U.S.A. 4/03. Brochure B-103Peerless Pump Company P .O. Box 7026Indianapolis, IN 46207-7026(317)925-9661, Fax: (317)924-7388ELS Vertical Turbine Range Chart - 1180 RPMH E A D (F e e t )FLOW (M 3/HR)FLOW (GPM)H E A D (M e t e r s )H E A D (F e e t )FLOW (GPM)H E A D (M e t e r s )FLOW (M 3/HR)ELS Vertical Turbine Range Chart - 1750 RPMAdjusting NutShaft Supportsupport.ush connectionLineshaftprotectionavailablenishedTop Bowloptimal support。
约克离心机配件中英文对照
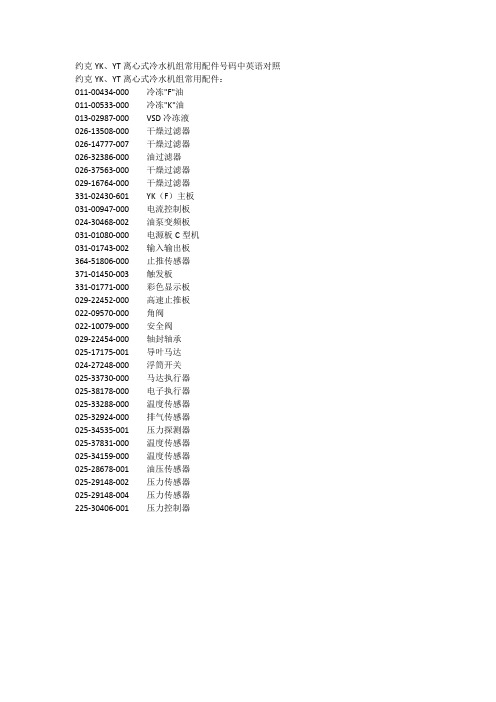
约克YK、YT离心式冷水机组常用配件号码中英语对照约克YK、YT离心式冷水机组常用配件:011-00434-000 冷冻"F"油011-00533-000 冷冻"K"油013-02987-000 VSD冷冻液026-13508-000 干燥过滤器026-14777-007 干燥过滤器026-32386-000 油过滤器026-37563-000 干燥过滤器029-16764-000 干燥过滤器331-02430-601 YK(F)主板031-00947-000 电流控制板024-30468-002 油泵变频板031-01080-000 电源板C型机031-01743-002 输入输出板364-51806-000 止推传感器371-01450-003 触发板331-01771-000 彩色显示板029-22452-000 高速止推板022-09570-000 角阀022-10079-000 安全阀029-22454-000 轴封轴承025-17175-001 导叶马达024-27248-000 浮筒开关025-33730-000 马达执行器025-38178-000 电子执行器025-33288-000 温度传感器025-32924-000 排气传感器025-34535-001 压力探测器025-37831-000 温度传感器025-34159-000 温度传感器025-28678-001 油压传感器025-29148-002 压力传感器025-29148-004 压力传感器225-30406-001 压力控制器York YK、YT centrifugal chillers commonly used accessories: 011-00434-000 Frozen"F"Oil011-00533-000 Frozen"K"Oil013-02987-000 VSD chilled liquid026-13508-000 Dry Filter026-14777-007 Dry Filter026-32386-000 oil filter026-37563-000 Dry Filter029-16764-000 Dry Filter331-02430-601 YK(F)Motherboard031-00947-000 current control panel024-30468-002 pump inverter board031-01080-000 Power Plate C-Machine031-01743-002 input and output boards364-51806-000 Thrust Sensor371-01450-003 Trigger Board331-01771-000 color display panel029-22452-000 high-speed thrust plate022-09570-000 angle valve022-10079-000 safety valve029-22454-000 Seal Bearing025-17175-001 guide vane motor024-27248-000 float switch025-33730-000 Motor Actuator025-38178-000 E-actuators025-33288-000 Temperature Sensor025-32924-000 exhaust sensor025-34535-001 Pressure Detector025-37831-000 Temperature Sensor025-34159-000 Temperature Sensor025-28678-001 oil pressure sensor025-29148-002 Pressure Sensor025-29148-004 Pressure Sensor225-30406-001 Pressure Co ntroller。
阿尔法拉夫双扁平泵介绍说明书

pulse-free, the pump provides smooth and gentle operation,making it an excellent choice for handling sensitive products.Two-in-one operation provides easy handling of process media of varying viscosities as well as CIP fluids. This simplifies piping and pump control, cutting costs and minimizing contamination risks.Superior suction performance with excellent lift capability and low NPSHr provides installation flexibility and increases product recovery.The Alfa Laval Twin Screw Pump is available in twelve models based on four frame sizes. Each frame size is available with three different screw profiles for varying pressure, flow and solids-handling capabilities.Benefits•Greater process flexibility.•Ease of service, increased process uptime.•Robust reliable design, reducing cost of ownership andincreasing process uptime.•Improved product quality.•Exceptional hygiene and cleanability.Standard designAll media contacting steel components, like pump casing, front cover and feed screws are in W. 1.4404 (AISI 316L). Furthermore, the pump casing is diffusion hardened. A stainless steel gearbox, end cover and foot ensure increased life and assist in washdown.The gearbox is designed with the timing gears located between the bearing sets, rather than external to them. This allows the bearing location to be optimized in order to provide maximum support to the shaft assembly, thereby providing a robust rigid design. The internal gearcase design optimizes oil circulation to both sets of bearings and the timing gears with an oil sump design. This improves the lubrication effect on both bearings and timing gears, minimizing the energy produced due to friction and thereby reducing heat generation within the pump gearbox.The front-loading, self-setting cartridge design makes it easy to replace the shaft seal while the pump is in place. Single, single flush and double mechanical cartridge seals are available. All options are fully front-loading and interchangeable.The Alfa Laval Twin Screw Pump can be supplied either as a bare shaft pump or mounted on a base plate complete with coupling, guard, shroud and a direct coupled motor or a gear motor for easy, plug-and-play installation.Working principleThe Alfa Laval Twin Screw Pump is a positive displacement pump. As the pump rotates, the intermeshing of the two contra-rotating screws, along with the pump casing, form volumetric chambers. These chambers fill with the pumped fluid and move the fluid axially from the suction side of the pump to the higher pressure discharge side.TECHNICAL DATAScrews, front cover, seal housing:W. 1.4404 (316L)Inside surface finish:Mech Ra ≤ 0.8Gear box:Stainless steel Base plate:Stainless steel Coupling guard:Stainless steel Product wetted elastomers:EPDM Other elastomers:FPMShaft seal:Single flush Rotary seal face:Silicon Carbide Stationary seal face:Silicon CarbideMax. flush pressure, single flush:0.5 bar Max. flush pressure, double mechanical:16 bar (max. 6 bar over product pressure)Water consumption, single flush and double mechanical:0.5 l/min.Flush connections, OS12-36:G 1/4" or NPT 1/4"Flush connections, OS42-46:G 1/2" or NPT 1/2"Max. discharge pressure:16 barMax. CIP/SIP temperature:150ºCOperating dataOS1410.4122800330011OS1616.082800330017OS2218.2162500330012OS2424.3122500330016OS2636.582500330024OS3234.8162200300016OS3446.6122200300021OS3669.982200300032OS4266.8161800280021OS4489.5121800280029OS46134.381800280043Dimension (mm)PUMP SHOWN WITH TRI-CLAMP, SUCTION AND DISCHARGE CONNECTIONSØA170180718509040640510110125101451551359188,528OS14401½OS16502OS22401½222,522092054,511240650512,5117,516512,51902001751121633OS24502OS26652½OS32652½280260113062132408625151452001523024021013262,543OS34OS36803OS428033603501545871807014790201802502029032028017,534658OS44OS4610041Dimension 'V'is with flush plugs installed - NPT adaptors will increase this dimension by ~10mmOS145027877.2576.7576.8OS1665 2.58683.1583.183.15OS225029089.388.7588.8OS2465 2.59895.1595.1095.15OS26803105.5101.45101.45101.5OS32803111.5107.45107.45107.5OS34OS361004121119.8119.7119.8OS421004148.5147.3147.2147.3OS44OS461506173.5-171.93-Options •Single mechanical shaft seal.•Double mechanical shaft seal.•Silicon Carbide/Carbon seal faces•Product wetted elastomers in FPM or FFPM.•Diffusion hardened screws.•Heating jacket.•Rectangular inlet.•Hydrostatic testing with certificate.•Reversed flow.•Bottom inlet or outlet.•Stainless steel shroud covering coupling and motor.•Baseplate fitted with adjustable stainless steel ball feet.•ATEX approval.Pump sizingIn order to correctly size a twin screw pump some essential information is required. Provision of this information listed below enables our Technical Support personnel to obtain the optimum pump selection. Specific CIP data are important as well. Product/Fluid Data:•Fluid to be pumped.•Viscosity.•Pumping temperature, minimum, normal and maximum.•Cleaning in Place temperature(s), minimum, normal and maximum.Performance Data:•Flow rate, minimum, normal and maximum.•Discharge head/pressure (closest to pump outlet).•Suction condition.Note!For further details, see also 100000817.This product has EHEDG certificate.This document and its contents are subject to copyrights and other intellectual property rights owned by Alfa Laval Corporate AB. No part of this document may be copied, re-produced or transmitted in any form or by any means, or for any purpose, without Alfa Laval Corporate AB’s prior express written permission. Information and services provided in this document are made as a benefit and service to the user, and no representations or warranties are made about the accuracy or suitability of this information and these services for any purpose. All rights are reserved.200006106-1-EN-GB© Alfa Laval Corporate AB How to contact Alfa LavalUp-to-date Alfa Laval contact details for all countries are always availableon our website at 。
船厂和船舶修理需要使用的密封件Microsoft Word 文档

船厂和船舶修理需要使用的密封件油污水排放监控系统碳钢-热镀锌聚四氟乙烯OIL DISCHARGE MONITORING SYSTEM 不锈钢-酸洗焚烧炉管系原理图酸洗非石棉INCINERATOR PIPING DIAGRAM燃油日用管系原理图酸洗非石棉F.O. SERVICE PIPING DIAGRAM燃油驳运管系原理图酸洗非石棉F.O. TRANSFER PIPING DIAGRAM燃油净油管系原理图酸洗非石棉F.O. PURIFYING PIPING DIAGRAM燃油泄放管系原理图酸洗非石棉L.O. SERVICE PIPING DIAGRAM滑油日用管系原理图酸洗非石棉L.O. SERVICE PIPING DIAGRAM滑油驳运与净油管系原理图酸洗非石棉L.O. TRANS & PURIF. PIPING DIAGRAM滑油泄放管系原理图酸洗非石棉L.O. DRAIN PIPING DIAGRAM艉管滑油管系原理图酸洗非石棉L.O. PIPING DIAGRAM OF STERN TUBE海水冷却管系原理图热镀锌丁腈橡胶SEA WATER COOLING PIPING DIAGRAM低温淡水冷却管系原理图酸洗磷化丁腈橡胶L.T. F.W. COOLING PIPING DIAGRAM高温淡水冷却管系原理图酸洗磷化丁腈橡胶H.T.F.W. COOLING PIPING DIAGRAM制淡装置管系原理图热镀锌无毒硅橡胶FRESH-WATER GENERATOR PIPING DIAGRAM排气管系原理图外涂耐热漆石墨复合EXHAUST GAS PIPING DIAGRAM压缩空气管系原理图酸洗磷化聚四氟乙烯COMPRESSED AIR PIPING DIAGRAM控制空气管系原理图酸洗磷化聚四氟乙烯CONTROL AIR PIPING DIAGRAM应急操纵空气管系图酸洗磷化聚四氟乙烯EMERGENCY OPERATION AIR SYSTEM锅炉给水管系原理图酸洗石墨缠绕BOILER FEED WATER PIPING DIAGRAM全船蒸汽管系原理图油舱外:石墨缠绕STEAM PIPING DIAGRAM 外涂耐热漆机舱蒸汽管系原理图油舱外:石墨缠绕E/R STEAM PIPING DIAGRAM 外涂耐热漆凝水管系原理图外涂耐热漆石墨缠绕CONDENSATE WATER PIPING DIAGRAM机舱舱底和消防管系原理图热镀锌丁腈橡胶E/R BILGE & FIRE. FIGHTING PIPING DIAGRAM甲板疏排水管系统图热镀锌丁腈橡胶DECK SCUPPER & DRAIN SYSTEM全船舱底压载系统图热镀锌丁腈橡胶GENERAL BILGE & BALLAST SYSTEM全船水消防管系图热镀锌丁腈橡胶WATER FIRE FIGHTING SYSTEMCO2灭火系统图热镀锌非石棉CO2 FIRE FIGHTING SYSTEM机舱局部水雾系统热镀锌丁腈橡胶E/R LOCAL WATER MIST SYSTEM机舱供水系统原理图清洗无毒硅橡胶E/RDOMESTIC WATER SUPPLY SYSTEM全船供水系统图清洗无毒硅橡胶DOMESTIC WATER SERVICE SYSTEM污水处理系统图热镀锌非石棉SEWAGE TREATMENT SYSTEM全船舱室疏排水管系图黑水热镀锌非石棉货油舱透气及蒸气回收管系原理图内涂酚醛环氧聚四氟乙烯CARGO TANK VENTING & VAPOUR RETURN PIPING DIAGRAM全船空气,测量及注入系统图油舱:酸洗耐油橡胶SHIP'S VENT, SOUNDING & FILLING PIPING SYSTEM 水舱:热镀锌机舱空气,测量及注入系统图油舱:酸洗耐油橡胶E/R VENT, SOUNDING & FILLING PIPING SYSTEM 水舱:热镀锌全船压缩空气管系图热镀锌聚四氟乙烯GENERAL COMPRESSED AIR SYSTEM货油输送管系原理图酸洗钝化聚四氟乙烯CARGO OIL TRANSFER PIPING DIAGRAM货油泄放管系原理图酸洗钝化聚四氟乙烯CARGO OIL DRAIN PIPING DIAGRAM压载水系统热镀锌丁腈橡胶BALLAST WATER SYSTEM货油舱清洗系统热镀锌聚四氟乙烯CARGO TANK CLEAING SYSTEM货油加热管系原理图酸洗石墨缠绕CARGO HEATING PIPING DIAGRAM惰性气体系统内涂焦油环氧柔性石墨INERT GAS SYSTEM。
卡梅伦液压数据手册(第 20 版)说明书
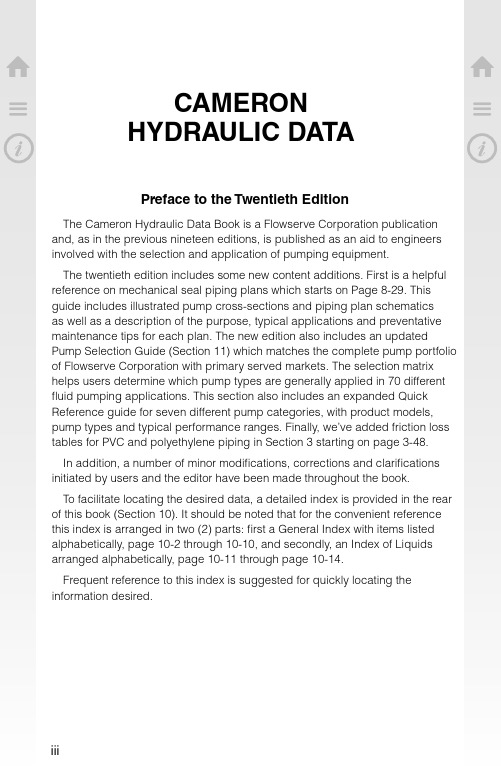
iv
⌂
CONTENTS OF SECTION 1
☰ Hydraulics
⌂ Cameron Hydraulic Data ☰
Introduction. . . . . . . . . . . . . ................................................................ 1-3 Liquids. . . . . . . . . . . . . . . . . . . ...................................... .......................... 1-3
4
Viscosity etc.
Steam data....................................................................................................................................................................................... 6
1 Liquid Flow.............................................................................. 1-4
Viscosity. . . . . . . . . . . . . . . . . ...................................... .......................... 1-5 Pumping. . . . . . . . . . . . . . . . . ...................................... .......................... 1-6 Volume-System Head Calculations-Suction Head. ........................... 1-6, 1-7 Suction Lift-Total Discharge Head-Velocity Head............................. 1-7, 1-8 Total Sys. Head-Pump Head-Pressure-Spec. Gravity. ...................... 1-9, 1-10 Net Positive Suction Head. .......................................................... 1-11 NPSH-Suction Head-Life; Examples:....................... ............... 1-11 to 1-16 NPSH-Hydrocarbon Corrections.................................................... 1-16 NPSH-Reciprocating Pumps. ....................................................... 1-17 Acceleration Head-Reciprocating Pumps. ........................................ 1-18 Entrance Losses-Specific Speed. .................................................. 1-19 Specific Speed-Impeller. .................................... ........................ 1-19 Specific Speed-Suction...................................... ................. 1-20, 1-21 Submergence.. . . . . . . . . ....................................... ................. 1-21, 1-22 Intake Design-Vertical Wet Pit Pumps....................................... 1-22, 1-27 Work Performed in Pumping. ............................... ........................ 1-27 Temperature Rise. . . . . . . ...................................... ........................ 1-28 Characteristic Curves. . ...................................... ........................ 1-29 Affinity Laws-Stepping Curves. ..................................................... 1-30 System Curves.. . . . . . . . ....................................... ........................ 1-31 Parallel and Series Operation. .............................. ................. 1-32, 1-33 Water Hammer. . . . . . . . . . ...................................... ........................ 1-34 Reciprocating Pumps-Performance. ............................................... 1-35 Recip. Pumps-Pulsation Analysis & System Piping...................... 1-36 to 1-45 Pump Drivers-Speed Torque Curves. ....................................... 1-45, 1-46 Engine Drivers-Impeller Profiles. ................................................... 1-47 Hydraulic Institute Charts.................................... ............... 1-48 to 1-52 Bibliography.. . . . . . . . . . . . ...................................... ........................ 1-53
(完整word版)三管轮轮机英语听力与会话问答要点参考
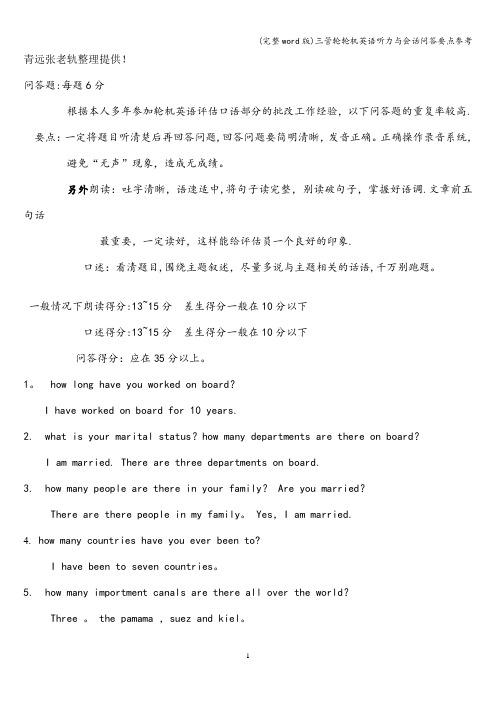
青远张老轨整理提供!问答题:每题6分根据本人多年参加轮机英语评估口语部分的批改工作经验,以下问答题的重复率较高.要点:一定将题目听清楚后再回答问题,回答问题要简明清晰,发音正确。
正确操作录音系统,避免“无声”现象,造成无成绩。
另外朗读:吐字清晰,语速适中,将句子读完整,别读破句子,掌握好语调.文章前五句话最重要,一定读好,这样能给评估员一个良好的印象.口述:看清题目,围绕主题叙述,尽量多说与主题相关的话语,千万别跑题。
一般情况下朗读得分:13~15分差生得分一般在10分以下口述得分:13~15分差生得分一般在10分以下问答得分:应在35分以上。
1。
how long have you worked on board?I have worked on board for 10 years.2. what is your marital status?how many departments are there on board?I am married. There are three departments on board.3. how many people are there in your family? Are you married?There are there people in my family。
Yes,I am married.4.how many countries have you ever been to?I have been to seven countries。
5. how many importment canals are there all over the world?Three 。
the pamama ,suez and kiel。
6.can you tell me what is the most important thing for a seafarer。
热泵精馏在气分装置丙烯塔中的应用
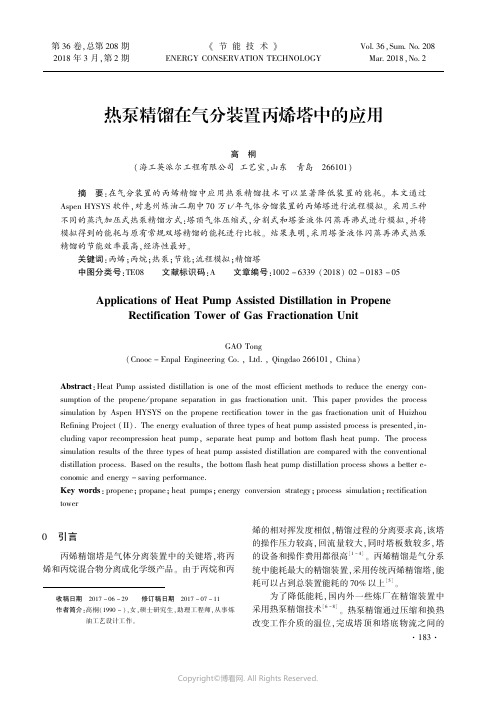
第36卷,总第208期2018年3月,第2期《节能技术》ENERGY CONSERVATION TECHNOLOGY Vol.36,Sum.No.208Mar.2018,No.2热泵精馏在气分装置丙烯塔中的应用高 桐(海工英派尔工程有限公司工艺室,山东 青岛 266101)摘 要:在气分装置的丙烯精馏中应用热泵精馏技术可以显著降低装置的能耗。
本文通过Aspen HYSYS 软件,对惠州炼油二期中70万t /年气体分馏装置的丙烯塔进行流程模拟。
采用三种不同的蒸汽加压式热泵精馏方式:塔顶气体压缩式,分割式和塔釜液体闪蒸再沸式进行模拟,并将模拟得到的能耗与原有常规双塔精馏的能耗进行比较。
结果表明,采用塔釜液体闪蒸再沸式热泵精馏的节能效率最高,经济性最好。
关键词:丙烯;丙烷;热泵;节能;流程模拟;精馏塔中图分类号:TE08 文献标识码:A 文章编号:1002-6339(2018)02-0183-05Applications of Heat Pump Assisted Distillation in PropeneRectification Tower of Gas Fractionation UnitGAO Tong(Cnooc -Enpal Engineering Co.,Ltd.,Qingdao 266101,China)Abstract :Heat Pump assisted distillation is one of the most efficient methods to reduce the energy con⁃sumption of the propene /propane separation in gas fractionation unit.This paper provides the process simulation by Aspen HYSYS on the propene rectification tower in the gas fractionation unit of Huizhou Refining Project (II).The energy evaluation of three types of heat pump assisted process is presented,in⁃cluding vapor recompression heat pump,separate heat pump and bottom flash heat pump.The process simulation results of the three types of heat pump assisted distillation are compared with the conventional distillation process.Based on the results,the bottom flash heat pump distillation process shows a better e⁃conomic and energy -saving performance.Key words :propene;propane;heat pumps;energy conversion strategy;process simulation;rectificationtower收稿日期 2017-06-29 修订稿日期 2017-07-11作者简介院高桐(1990~),女,硕士研究生,助理工程师,从事炼油工艺设计工作。
Armstrong 术语中英对照

―fail safe‖ to cold water―Feature Code‖ References―out of range‖ system failure―U‖ stampsa complete failurea differential pressure diaphragm actuated mixing unita power failurea pumped recirculationa significant pressure reductiona single-temperature locking seta thermal-shutdown featurea top outleta unique feed forward designa water seala wide range of sizesAbbott reported many Watson-McDaniel trap failures detected by AIM. They are currently replacing with Armstrong IB traps. Additionally, Abbott plans to monitor all (650) traps in facility, purchasing (75 - 100) AIM ST5700 devices over next 5 years.ability to purge systemabsolute pressureaccessories optionsaccessoryaccumulateAccumulation Chamberaccuracy and to provide redundancy in case of individual thermostatAccurate control of blended water drawn from the systemaccurate water temperaturesActivated in error modeactual gravityActuateactuatoractuator stemADAM (Armstrong Digital Account Management)Adaptable to High Ambient Temperatureadjustable maximum temperature limitAdjustable Single Temperature lockoutadjusting the mix of steam and wateradjustment keyAdministratorsAFHAFTaftercoolerAII – T.R.AIMair and CO2 venting at steam temperatureair changeAir CompressorAir Dryerair filter regulatorsair flowAir Handler Unitair handling systemair lineair loadAir LossAir MainAir Motiveair movementair must be introduced into the systemair or inert gasAir Pressureair separatorair streamair supply pressureair systemAir Temperatureair to closeair to openAir valveAir Velocityair ventairstreamAll dimensions and weights are approximate. Use certified print for exact dimensions. Design and materials are subject to change without notice.allen boltAllowable Pressureallowing no condensate backupAlternate ChoiceAluminum Flataluminum KeyfinAmbient Sensing Isolation Valveambient temperatureAmerican Chemical SocietyAmerican Gas AssociationAmerican National Standards InstituteAmerican Petroleum InstituteANCAncillaryanimationANTI-NOISE TRIMAntI-theft devicesapplicable lawaquastatArmey SteamstrongArmstrong Brand PromiseArmstrong coilsArmstrong Condensate Management GroupArmstrong core valuesArmstrong Flo-Rite-Temp Instantaneous Steam/Water Heater pre-piped packages Armstrong Flo-Rite-Temp® Instantaneous SteamArmstrong Global HoldingsArmstrong Heat Transfer GroupArmstrong hot and cold water hose stationsArmstrong Hot Water Equipment Trade (Shanghai) Co., Ltd.Armstrong Hot Water GroupArmstrong Humidification GroupArmstrong HumidiPackArmstrong Intelligent MonitoringArmstrong InternationalArmstrong International - S.E. AsiaArmstrong International Italiana S.r.l.Armstrong International Korea Co., Ltd.Armstrong International Mexico S de RL de CVArmstrong International Mexico S de RL de CVArmstrong International Private LimitedArmstrong International S.A.Armstrong inverted bucket trapArmstrong Machinery (China) Co. LtdArmstrong Machinery (China) Co.,Ltd.Armstrong ModelArmstrong Pressure/Temperature Control GroupArmstrong PromiseArmstrong provides intelligent system solutions that improve utility performance, lower energy consumption, and reduce environment emissions while providing an "enjoyable experience." Armstrong representativeArmstrong SeriesArmstrong ServiceArmstrong Service France SAArmstrong Single Temperature Hose Stations Armstrong Smart Services GroupArmstrong SolutionArmstrong Steam and Condensate GroupArmstrong Sustainability BrochureArmstrong Unfired Steam GeneratorArmstrong‘s engineered condensate trap/pump packages Armstrong‘s engineered condensate pump trap packages Armstrong‘s engineered XXXArmstrong-Cool Fog SystemAsbestos-freeASIASME pumps and receiversASME Sec.ASSEassembled on a compact common base-plateassure maximum efficiencyASTM A216 WCBASTM A351 Gr.ASTM A48 classatmospheric pressureatomize wateraudible alarmAutomatic air ventingAutomatic Differential Condensate ControllerAutomatic shutoff of hot water flowautomatic water softenerAutomation Research CorporationAvailable in a wide range of sizesavailable upon requestback pressureBaked Enamelbalance valveBALANCED TRIMBalancing Valveball float drain trapball valveball valves cross-linked by a stainless steelBall-Type Flow Indicatorsbare pipe heatingbargBASBDbe compliant with ASSE Standardbe supplied pre-plumbed and pressure testedbe supplied pre-wiredbellowsbellows sealBellows sealedBellows Sealed Globe ValvesBENCH SETbimetallicbimetallic elementbimetallic mechanismBimetallic Steam TrapBimetallic Trapbleedblendblended waterblind flangesblowdownblowdown connectionblowdown rateblowdown valveblowerbodyBody and Capbody fits in tight spacesBody Materialbody materialboilerBoiler Blowdown Heat RecoveryBoiler Blowdown Recoveryboiler efficiencyboiler feedBoiler Forced Draft Fansboiler headerBoiler HouseBoiler side recirculating pumpBoiler side recirculating pump to supply the heat exchanger Boiler water conductivityBoiler Water to Water Instantaneous Water Heaters boiling pointboltBolt Assemblybonnetboronizedboth peakBottom Inletbottom outletBottom to C InletBranch LineBranch Welding Fittingbreak a vacuumBronze Gauge Glass AssemblyBtu‘s are captured and returned to the system bucketbucket ventBucket Vent Scrubbing WireBuilding Automation SystembuildupbulletinBulletin 110 - IS-4 LiteratureBulletin No. 200buoyancyburnerBushingbuttweldBuy Onlineby-passby-pass valveC Outlet to C InletCabinet constructionCabinet has a polished stainless steel piano-hinged Cabinet outer flangeCAGECanadian Standards AssociationcapCap BlockCap Gal.Capable of close temperature controlCapacity Conversion Factors for Other Fill Heads capacity linecapacity tableCapital Repaircapsulecarbon dioxideCarbon Steelcarbon steel anglecarbon steel pipecarbonic acidcarryoverCast ironCast Stainless Steelcast steelcatalogcautioncavitationCentifeed CoilCentral Recirculation System Control certified drawingchaplaincheck valveChemical-Free Steamchrome-plated DZR brassCIP connection portcirculating pumpclean steamClosed Loopclosed loop means no motive or flash closed-loopCLOSURE MEMBERCO2 EmissionCO2 emissions will be reduced with Cold Hose Stationscold trapcold water capacityCold Water Hose Stationscold water inlet supplycold water inlet supply failureCold Water Start-Up Capacities combination inlet isolation combining a pump within a steam trap combustionCOMMUNITY COVENANTcompact designcompensatecomplete shutdown of outlet flow Complete Thermal Exchange compress aircompressed air system Compressed Gas Association compression fittingcompressorComputrol, Inc.Condensate Collection Assembly condensate controllercondensate controllerscondensate coolercondensate drainagecondensate loadcondensate must be lifted condensate pumpcondensate recoveryCondensate Recovery Equipment condensate recovery requirements condensate recovery systemCondensate RemovalCondensate Removal and Recovery System condensate returncondensate return linescondensate return systemcondensate supply and returncondensecondensercondensing rateConnection Sizeconnection typeconnectorconnector styleConnector with Integral StrainerConserve Energyconstant low pressure steamConstant PressureCONSTANT PRESSURE DROPconstant steam pressureConsult Armstrong or your local Representative Consult Factorycontaminantscontinuous air venting at steam temperature continuous automatic air and CO2 venting Continuous Discharge Capacities in kgs control chambercontrol loopcontrol modulecontrol panelControl panel UL and CSA approvedcontrol signalcontrol systemcontrol valveControlled Disc TrapCool Fog systemcore valuesCorn Refiners Associationcorrosion resistantcorrosivecost-effective solutioncross-contaminatedcross-linked by a stainless steel bridge pieceCuring PressCuring Press Condensate RemovalCustomer E-BlastsCustomer LocationCv valuecycling wear and tearcylindricalDC Series Automatic Differential Condensate Controllers DCSdeaerationdeareatorde-ionized waterdeliver precise mixed water temperature demineralizedDescriptionDesign and materials are subject to changedesign conditionDESIGN CONDITIONSDesign Pressuredesign specificationdetecting transmitterdew pointdial screwdiaphragm actuatordifferential condensate controllerDifferential Pressuredifferential purging actionDifferntial PressureDigital Control SystemDigital Cycle CounterDigital Mixing CenterDigital Mixing ValveDigital Recirculating Valvedigital recirculation valveDigital Water Temperature Control SolutionsDignitydimensional informationDimensions and WeightDirect Actingdirect acting valveDirect Area DischargeDirect Steam Injection Humidifierdirect-actingDIRECT-ACTING VALVEdirtdirt are held in suspension until dischargeddirt can collect on the orificeDirt PocketDisc SpringsDisc TrapDischarge OrificeDischarge Pressuredischarge valvedispersion tubedissolveDistributed Control SystemDistribution Manifolddistribution systemdistributordiverse flow ratesDomestic Manufactureddoor heaterdouble actingDouble offset butterfly valveDouble-Duty Seriesdownstreamdown-streamdownstream solenoid valve relayDrain Connectiondrain cycledrain linedrain liquiddrain pandrain separatorDrain Trapdrain valvedrainagedrainerdraw off pointsdraw-off requirementdripdrip legdropletsdry airDryerdryer coilsdrying chamberdual gravitydual gravityDual gravity drain trapdual scale top mount Thermometer and Inlet Dual thermostatic elementsdual thermostatsDuct Air TemperatureDuct Heightduct systemductile irondurabledurableduring no-demand periodsDYNAMIC UNBALANCEDZR brass constructionEconomical non-electric operationEducationefficient operationelectric condensate pumpelectric controlelectric humidifierElectric ModulatingElectric motorElectric Steam Humidifierelectricity consumptionElectricity Distributionelectro pneumatic positionerelectrocutionelectrodeElectronic control boxElectronic Mixing Centerelectronic temperature controllerElement Assyelevateelevatedeliminate the requirement for a fitted aquastatEmergency Fixtureemergency fixtureenameled steel frame terminating in five standard union connections enclosureEnd CapEnd connectionend coverend of lifeend-userenergy conservationenergy conservation measureEnergy Conservation Measure (ECM)energy consumptionEnergy ConsumptionEnergy costenergy efficiencyEnergy Efficiencyenergy lossenergy managerEnergy Optimization SystemEnergy SavingsEnergy SeminarEnergy Servicesenergy-efficiency methodologyEnjoyable experienceEnjoyable ExperiencesenthalpyEnvironmentEPCEPC (engineering, procurement, construction) EQUAL PERCENTAGEEquipment Being Drainedequipped with removable temperature adjustment key Error RelayEstimated Investment and Paybackethicsevaporative coolingevaporatorevaporator or condenser of an air conditioner Everlasting Valve, Inc.exhaust headExpect many enjoyable experiences!Exposed areaExpressPackexternal check valvesexternal corrosionExternal PilotExternal StrainerExternally removableF condensatefabricateFabricated StrainersFace to FaceFace-to-FaceFactory settingsFail Closefailure safeFairnessFaith in God, Family, Job (in this order)Fan LocationFan PackageFearlessfeature codefeatures a unique integral thermostatic return limiter feed back/modulating steam control valvefeed headFeed WaterFeed-Forwardfeet of ―safety yellow‖ washdownfield-adjustable maximum limitFigure CGFigure LDfill headFill ValveFin CoilFin Materialfin pitchfin typeFinned pipe tank heatersfitted aquastatFive PillarFixed Pivotfixtureflangeflangeflanged and socketweld connectionsFlanged ConnectionsFlanged lbflanges available in Class 600 and 900flash steamflash tankFloat & Thermostatic Steam Trapsfloat and thermostatic steam trapFloat and Thermostatic TrapFloat Drain Trapfloat steam trap valvefloat type drain trapFloat weightFloat-Fixed Pivotflooded pitsFlo-Rite-Temp® instantaneous steamFlo-Rite-Temp® instantaneous water heaterFlo-Rite-Temp® Pre-Pipedflow applicationsflow capacityflow characteristic curvesflow coefficient CvFlow Controlflow directionflow indicatorflow rateflow timeFlue GasFlue Gas TemperatureFlue Stack TemperatureFluid Catalytic CrackingFluid Controls InstituteFLUID DATAFLUID NAMEFMC RadaFMC-BTfog chamberFog SystemFogger Headfogger manifold barFood ProcessorsfootprintForced Draft (FD)Forged Chrome-moly Steelforged steelFree FloatFree Floating Guided Lever Drain Trap Free Floating Guided Lever Drain Trap free floating lever Air Ventfree-floating stainless steel mechanism freeze protectionfreeze-protection drainfresh steam lossfriction lossfurnishedfuzzy adaptive tuning (FAT)G.P.Mgalvanic corrosiongalvanized steelGas Ventgas-fired humidifiersgasketGatewaygaugegaugegauge glassgauge glassgauge pressureGeneral Services Administration gland packingGlobe ValveGradualgrains of moistureGranbygravity draingreen buildingGreen TeamgrooveGroups of Fixturesguide bushguidelinesHAFThand hinged doorhand leverhandbookHandwheelHard WorkingHardened chrome steel17 hardened stainless steel hazardheaderheat exchangeHeat Exchangerheat lossheat of vaporizationHeat Recoveryheat transferheat transfer equipmentheat valueheaterHeating and Cooling Coils Heating ChamberHeating Coilheating elementheating mediumheating systemheavy dutyheavy duty industrial chrome heavy gaugeheavy oilHeavy-duty springshelp deskhemispherical valveHexhigh back pressureHigh Capacityhigh fireHigh Heat ValueHigh Limit HumidistatHigh Pressurehigh pressure dropHigh temperature safety shut-offhigh washdown temperatureshigh-limit controllerHLARHLAR AVHLAR Maximum Operating Pressures HLS LDHonestyhorizontal flash tanksHorizontal Installationhosehose lengthshose rackhose reelHose StationHose Station Less Hosehot and cold portshot water applicationsHot Water SolutionsHot Water System Solutionshot water temperature control units how to trap jacketed kettlesHPI/CPIHumidiCleanhumidificationHumidification Loadhumidification systemHumidifierhumidifier controlhumidifier locationHumidifier ManifoldHumidity Controlhumidity levelHydro TestHydrocarbonhydronichygroscopic materialhysteresisIB (Trap)IBLVICI ChemicalsIdentifying an occurrence/liftimpellerIMPORTANT NOTEimprove utility performancein the event of a diaphragm failureInconel XIndividual Bathindividual thermostat failureindustrial nickel platingindustrial process critical heat transferIndustry-Specific E-blastsIndustry-Specific Sales LiteratureINHERENT DIAPHRAGM PRESSURE:inlet and outlet connectionsinlet combination ball valve strainersInlet ConnectionInlet PipeInlet Pressureinlet sizeinlet strainerinlet supply temperatureInlet Swing Check Valveinlet union connectionsinlet vane after the fanIn-Linein-lineIn-line Check ValvesIn-line Connectionin-line repairableInstallation and Maintenanceinstalled as the primary temperature controller within a pumped recirculation InstitutionalInstitutional Hot Waterinstitutional low-pressure steam heatinginstruction manualinsulateinsulation jacketIntegral check valveintegral combination inlet check valveIntegral inlet check valves and strainersintegral inlet spring loaded check valvesintegral inlet supply risersintegral mounting flangeIntegral slight flow indicatorintegral strainerintegral strainer connectorIntegral thermometerintegral thermostatic return limiter Integral vacuum breakerintegrated circuit board technology intelligent system solutions interchangingintercoolerintermittentinternal operating componentsInternal pilotInternational Electrotechnical Commission Internet Service ProviderIntrinsically safe digital cycle counters Inverted BucketInverted Bucket Drain Trapinverted bucket large ventInverted Bucket Steam Trapinverted bucket trapIonic Bed TechnologyIonic Bed TechnologyIsolation valvejacketed kettlejobberKey Performance Indicatorskeyed cylinder lockkilojouleKindnessknow-howKnowledge not shared is energy wasted Kyoto ProtocolL finlabor costlag timeslatent heatlavatoryleakageleaking sealsLeaking valves on critical process Legionella risk reductionLevel Controlleverlever mechanismsLeverage Systemlidlifted from the drain pointlight liquidlight loadlightweightLi-ionlimit switchlinear distancelinkageLiquid CoilLiquid Drainerliquid levelLiquid LoadList of MaterialsLIST OF MATERIALSLiteratureLiterature Order Formlive male swivellive steamlive steam lossLoad AirLocal Area Networklock nutlockshield for single temperaturelower energy consumptionLow-maintenance operationLow-profile bodyLoyalistLoyaltylubricationmagnitude of dischargemain housingMain ValveMaintain a consistent systemMaintains mixed water temperaturesmaintains recirculating water temperatures within the circuit maintenanceMaintenance Costmaintenance costsMake Up WaterMake-up Watermanagement programmanifoldmanifold barmanifold lengthManifold Lengths and Duct WidthsManifold Modelmanual throttling devicematerials and weightMaterials of ConstructionMax Allowable PressureMax Allowable TemperatureMax. Operating TemperatureMaximum Allowable PressureMaximum allowable pressuremaximum capacitymaximum efficiency while maintaining minimum motor horsepower Maximum flash loadmaximum inlet pressureMaximum Operating ConditionsMaximum Operating Pressuremaximum pressure dropmaximum protection against freezing and water hammermaximum temperature limiting and single temperature locking feature maximum working pressureMeasured Blend TemperatureMechanical Designmechanical failuremechanical roommechanism assemblyMetering ValveMini Pump Trapminimal fill headminimize stressMixed Airmixed return and return to heat source check valvesmixed return flow indicatormixed return inlet with thermostatic return limitermixed return sight flow indicatormixed water outlet and mixed return inlet with thermostatic return mixing STEAM and WATER for washdownMixing Unitsmixing valveMODEL NUMBER INDEXmodulated controlmodulated outputmodulating steam control valvemodulating steam pressuremoisture contentmotive pressureMotive Steam PressureMotor circuit protectormotor powermount Thermometer and Inlet Check Valvesmount Thermometer and Stainless Steel inlet Checkmounting bracketmoving partsmultiple effectMultiple orientationsmulti-tube steam dispersion panelName of PartNAME OF PARTname plateNational Sanitation Foundationnational sanitation foundation (NSF)Natural Gas PipelinenegligenceNEMAnet positive suction headnew construction and retrofit installationnickel platenitrous oxideNoiseless HeaternominalNon modulating constant steam pressurenon-asbestosnon-condensable gasesNon-Electric Steamnon-helical straight internal tube bundleNon-intrusiveNon-intrusive to the valve, pipe or system; no shutdown required to install. Non-Recirculating Hot Water SystemNon-recirculating hot water systemsNon-Shocknon-wetting distancenozzleNPS Sch.NPSH issuesNPT inlets and outletnutOD TubesOEMoffset from centre of seatoffset from centre of valveolder style dual-globe valve mixing ―YOpen Systemopen the valve against systemopening angleoperating conditionOperating Costoperating historyOperating PressureOperating PrincipleOperation & Maintenanceoperation and maintenanceoperation costoperation of pumpingOperational SpecificationsOperational water pressureoperator programmableoperator typeOperators and Maintenance personnel Optional double-wall platesOptional External Network Adapterorificeorifice sizeOrifice Steam Pressureoriginal flow setting in hot failure modeO-Ringoutdoor airOutdoor EnclosureOutdoor Temperatureoutdoors low ambient temperature trapping outlet ball valveOutlet Connectionoutlet dial thermometeroutlet pressureoutlet stop valve and thermometeroutlet temperatureoutlet temperatureoutlet thermometer and inlet supplyoutlet trapsOutline StrategyOutside Airpackaged solutionPacking sealedPainting Strategypasteurization temperaturepasteurizerPatentPeace of mindperforatedPerformance ContractPetrochempetroleumpharmaceutical manufacturingPhysical Datapiano-hinged door with a keyed cylinder lock pilot valvePipe ConnPipe Connectionspipe sizePiping and Insulationpiping configurationsPiping welded by Section IX welders Piping—Schedule 40, Schedule 80pistonpiston actuatorPiston ValvePlate and frame heat exchangerPlate heat exchangerplate-fin heat exchangerplug & stem assemblyplumbing codes or safety requirements pneumaticpneumatic angel valvepneumatic controlpneumatic control valvePneumatic Modulatingpneumatic operatorpneumatic valve positionersPoint of Usepolymer constructionpolysulfoneportable water supplyPORT-GUIDEDposition feed back transmitterspositionerPower Managementpower supplyPre-Assembledprecise controlpreheatpreheat coilPre-Pipedpre-piped packagespre-piped single temperaturePre-Piped Tempered Waterpre-set outlet temperaturePressure and Temperature Controlpressure differentialPressure DripPressure DropPressure Gaugepressure ratingPressure Reducing Valves PTCpressure temperature ratingpressure waterpressure-testedprevent over-temperature selectionPreventive Set in Order proceduresPrice SheetPrimary Humidificationprimary humidifierProbe Connectionproduct and serviceProduct DescriptionProduct Literatureprogrammable logic controller (PLC)Programmable rangeProgrammable set point rangeproper trapprovide the most efficient and cost-effective solution to your condensate recovery requirements. PRV stationPSIG steampsychrometricpulling the valve off the seatPump Cappump capacityPump Combination PackagesPump CREPump DischargePump TrapPump Trap CapacitiesPump Trap MaterialsPump Trap PackagesPump Trap Physical Datapumped recirculation systemPure FogpurgePurgerPUSH-DOWN-TO-CLOSEPUSH-DOWN-TO-OPENRadaRada Thermostatic Mixing ValveradiatorRadiator TrapRadiator Valveradio frequencyrangeabilityratingratingsrecess flangere-circulated hot water systems Recirculating Hot Waterre-circulating hot water system Recirculating Single Temperature Systems Recirculation Systems Recommendation Chartrecovered flash steamRecovered Liquidreduce cycling wear and tearreduce energyreduce environmental emissionsreduce heat transferredundancyredundantRe-engineeredrefineryrefinery processes.refrigerantregistered trademarkregulatorrelative humidityRelay outputRelief Valve ChallengesRemarksRemote SensorRemovable Insulation Jacketremovable keyremoveremoving the mechanism assemblyrepreplaceable seatsReplacement Coilreplacing gland packingrepresentativeRequired Design PressureRequired Design TRequired Operation PressureRequired Operation Trequired valve fittings and isolation valves reservoirReservoir for Curing Pressresist high back pressureResistance to Hydraulic Shockresistant to water hammerresonatorRespectretrofitreturn airreturn bendreturn check valvereturn headerreturn limiterreturn linereturn on investmentreturn systemreverse acting positionerreverse osmosisReverse Osmosis (RO) plantreverse osmosis waterReverse-ActingREVERSE-ACTING VALVEreversed anglerisky consequencesrivetruggedRugged construction materialrunoutSafetysafety drainsafety factorSaintsame size and specificationSample Specificationssanitarysanitary usesaturated steamsaturated steamsaturated steam temperaturesaturated temperaturescale top mount Thermometerscreen materialsScreen RetainerScrewed NPT and BSPTScrewed or SWscrewed, socketweld or flangedScrivenscrub wireseamlessSeamless Steelseat centre lineseat leakageseat leakage testSeat Nutseat retainerSEAT RINGsectionalSee-Thruself-containedself-operated pressure reducing valves sell trap management services semiconductorSensible heatseparatorseparator chamberserial connection data portSeries CapacitySeries Inverted Bucket Steam Trap Series Low Profile Pump TrapSeries SS TrapSeries Stainless Steel Trap Valve Station Series TrapService flush cycleService flush waiting periodService LifeSet and lock to a single temperatureSet PointSetpoint SelectionSharing Knowledge. Saving Energy. shell and tube heat exchangershine assignmentsShipping Weightshut off pressureshut-offside connectionsignboardSimplestsimplexsingle actingsingle effect。
新型三维脉动热管的性能
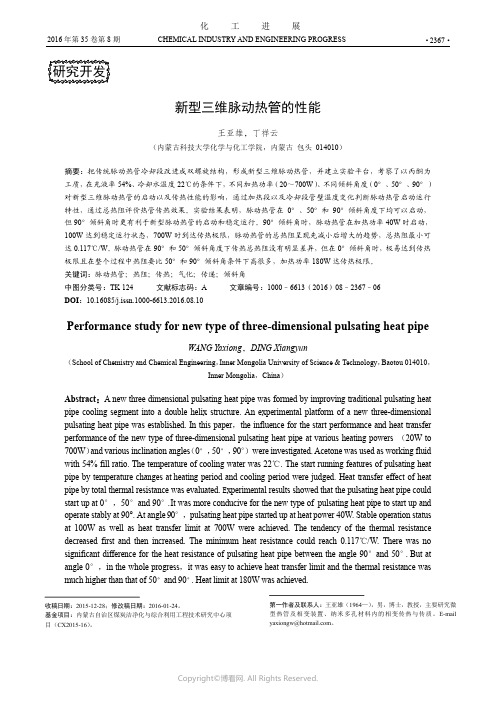
2016年第35卷第8期 CHEMICAL INDUSTRY AND ENGINEERING PROGRESS·2367·化 工 进 展新型三维脉动热管的性能王亚雄,丁祥云(内蒙古科技大学化学与化工学院,内蒙古 包头 014010)摘要:把传统脉动热管冷却段改进成双螺旋结构,形成新型三维脉动热管,并建立实验平台,考察了以丙酮为工质,在充液率54%、冷却水温度22℃的条件下,不同加热功率(20~700W )、不同倾斜角度(0°、50°、90°)对新型三维脉动热管的启动以及传热性能的影响,通过加热段以及冷却段管壁温度变化判断脉动热管启动运行特性,通过总热阻评价热管传热效果。
实验结果表明,脉动热管在0°、50°和90°倾斜角度下均可以启动,但90°倾斜角时更有利于新型脉动热管的启动和稳定运行。
90°倾斜角时,脉动热管在加热功率40W 时启动,100W 达到稳定运行状态,700W 时到达传热极限,脉动热管的总热阻呈现先减小后增大的趋势,总热阻最小可达0.117℃/W 。
脉动热管在90°和50°倾斜角度下传热总热阻没有明显差异,但在0°倾斜角时,极易达到传热极限且在整个过程中热阻要比50°和90°倾斜角条件下高很多,加热功率180W 达传热极限。
关键词:脉动热管;热阻;传热;气化;传递;倾斜角中图分类号:TK 124 文献标志码:A 文章编号:1000–6613(2016)08–2367–06 DOI :10.16085/j.issn.1000-6613.2016.08.10Performance study for new type of three-dimensional pulsating heat pipeWANG Yaxiong ,DING Xiangyun(School of Chemistry and Chemical Engineering ,Inner Mongolia University of Science & Technology ,Baotou 014010,Inner Mongolia ,China )Abstract :A new three dimensional pulsating heat pipe was formed by improving traditional pulsating heatpipe cooling segment into a double helix structure. An experimental platform of a new three-dimensional pulsating heat pipe was established. In this paper ,the influence for the start performance and heat transfer performance of the new type of three-dimensional pulsating heat pipe at various heating powers (20W to700W )and various inclination angles (0°,50°,90°) were investigated. Acetone was used as working fluid with 54% fill ratio. The temperature of cooling water was 22℃. The start running features of pulsating heat pipe by temperature changes at heating period and cooling period were judged. Heat transfer effect of heat pipe by total thermal resistance was evaluated. E xperimental results showed that the pulsating heat pipe could start up at 0°,50°and 90°. It was more conducive for the new type of pulsating heat pipe to start up and operate stably at 90°. At angle 90°,pulsating heat pipe started up at heat power 40W. Stable operation status at 100W as well as heat transfer limit at 700W were achieved. The tendency of the thermal resistance decreased first and then increased. The minimum heat resistance could reach 0.117℃/W. There was no significant difference for the heat resistance of pulsating heat pipe between the angle 90°and 50°. B ut at angle 0°,in the whole progress ,it was easy to achieve heat transfer limit and the thermal resistance wasmuch higher than that of 50°and 90°. Heat limit at 180W was achieved.第一作者及联系人:王亚雄(1964—),男,博士,教授,主要研究微型热管及相变装置、纳米多孔材料内的相变传热与传质。
Design of a high temperature production heat pump system using

high temperature generation heat pump replacing a combustion boiler to the plant can be a good upgrade.
ARTICLE IN PRESS
Current Applied Physics xxx (2009) xxx–xxx
Contents lists aபைடு நூலகம்ailable at ScienceDirect
Current Applied Physics
journal homepage: /locate/cap
1567-1739/$ - see front matter Ó 2009 Elsevier B.V. All rights reserved. doi:10.1016/j.cap.2009.11.015
Please cite this article in press as: M. Kim et al., Design of a high temperature production heat pump system using geothermal water at moderate temperature, Curr. Appl. Phys. (2009), doi:10.1016/j.cap.2009.11.015
For this purpose, advanced heat pump cycles including compression/absorption heat pump are under development in Korea. The compression/absorption heat pump is also called as a hybrid heat pump, since it has conceptual background of the combination of vapor compression and absorption cycle. Baik et al. (2004) investigated compression/absorption cycle with single-stage solution circuit, the simplest form of compression/absorption heat pumps, by simulation method as an attempt to apply it to dyeing process [2]. The authors brought the former concept of Åhlby et al. (1991) to observe the system performance by cooling water temperature gradient in the absorber, DTabs, in the simulation [3]. The simulation results showed that the performance can be up to 80% higher compared to the conventional pure refrigerant heat pump for 90 °C process hot water production.
heatpipe

Heat pipes for electronics coolingapplicationsScott D. Garner, PE., Thermacore IncFigure 1: Heat pipe operationIntroductionAll electronic components, from microprocessors to high end power converters, generate heat and rejection of this heat is necessary for their optimum and reliable operation. As electronic design allows higher throughput in smaller packages, dissipating the heat load becomes a critical design factor. Many of today's electronic devices require cooling beyond the capability of standard metallic heat sinks. The heat pipe is meeting this need and is rapidly becoming a main stream thermal management tool.Heat pipes have been commercially available since the mid 1960's. Only in the past few years, however, has the electronics industry embraced heat pipes as reliable, cost-effective solutions for high end cooling applications. The purpose of this article is to explain basic heat pipe operation, review key heat pipe design issues, and to discuss current heat pipe electronic cooling applications.Heat Pipe OperationA heat pipe is essentially a passive heat transfer device with an extremely high effective thermal conductivity. The two-phase heat transfer mechanism results in heat transfer capabilities from one hundred to several thousand times that of an equivalent piece of copper.As shown in Figure 1, the heat pipe in its simplest configuration is a closed, evacuated cylindrical vessel with the internal walls lined with a capillary structure or wick that is saturated with a working fluid. Since the heat pipe is evacuated and then charged with the working fluid prior to being sealed, the internal pressure is set by the vapor pressure of the fluid.As heat is input at the evaporator, fluid is vaporized, creating a pressure gradient in the pipe. This pressure gradient forces the vapor to flow along the pipe to a cooler section where it condenses giving up its latent heat of vaporization. The working fluid is then returned to the evaporator by the capillary forces developed in the wick structure.Heat pipes can be designed to operate over a very broad range of temperatures from cryogenic (< -243°C) applications utilizing titanium alloy/nitrogen heat pipes, to high temperature applications (>2000°C) using tungsten/silver heat pipes. In electronic cooling applications where it is desirable to maintain junction temperatures below 125-150°C, copper/water heat pipes are typically used. Copper/methanol heat pipes are usedif the application requires heat pipe operation below 0°C.Heat Pipe DesignThere are many factors to consider when designing a heat pipe: compatibility of materials, operating temperature range, diameter, power limitations, thermal resistances, and operating orientation. However, the design issues are reduced to two major considerations by limiting the selection to copper/water heat pipes for cooling electronics. These considerations are the amount of power the heat pipe is capable of carrying and its effective thermal resistance. These two major heat pipe design criteria are discussed below.Limits To Heat TransportThe most important heat pipe design consideration is the amount of power the heat pipeis capable of transferring. Heat pipes can be designed to carry a few watts or several kilowatts, depending on the application. Heat pipes can transfer much higher powers for a given temperature gradient than even the best metallic conductors. If driven beyond its capacity, however, the effective thermal conductivity of the heat pipe will be significantly reduced. Therefore, it is important to assure that the heat pipe is designed to safely transport the required heat load.The maximum heat transport capability of the heat pipe is governed by several limiting factors which must be addressed when designing a heat pipe. There are five primary heat pipe heat transport limitations. These heat transport limits, which are a function of the heat pipe operating temperature, include: viscous, sonic, capillary pumping, entrainment or flooding, and boiling. Figures 2 and 3 show graphs of the axial heat transport limits asa function of operating temperature for typical powder metal and screen wicked heat pipes. Each heat transport limitation is summarized in Table 1.Heat Transport Limit Description Cause Potential SolutionViscousViscous forces preventvapor flow in the heat pipeHeat pipe operating belowrecommended operatingtemperatureIncrease heat pipeoperating temperature orfind alternative workingfluidSonicVapor flow reaches sonicvelocity when exiting heatpipe evaporator resulting ina constant heat pipetransport power and largetemperature gradientsPower/temperaturecombination, too muchpower at low operatingtemperatureThis is typically only aproblem at start-up. Theheat pipe will carry a setpower and the large ^Twill self correct as theheat pipe warms upEntrainment/Flooding High velocity vapor flowprevents condensate fromreturning to evaporatorHeat pipe operating abovedesigned power input or attoo low an operatingtemperatureIncrease vapor spacediameter or operatingtemperatureCapillary Sum of gravitational, liquidand vapor flow pressuredrops exceed the capillarypumping head of the heatpipe wick structureHeat pipe input powerexceeds the design heattransport capacity of theheat pipeModify heat pipe wickstructure design or reducepower inputBoilingFilm boiling in heat pipeevaporator typically initiatesat 5-10 W/cm2 for screenwicks and 20-30 W/cm2 forpowder metal wicksHigh radial heat flux causesfilm boiling resulting inheat pipe dryout and largethermal resistancesUse a wick with a higherheat flux capacity orspread out the heat load Table 1: Heat pipe heat transport limitationsFigure 2: Predicted heat pipe limitationsAs shown in Figures 2 and 3, the capillary limit is usually the limiting factor in a heat pipe design.Figure 3: Predicted heat pipe limitsThe capillary limit is set by the pumping capacity of the wick structure. As shown in Figure 4, the capillary limit is a strong function of the operating orientation and the type of wick structure.Figure 4: Capillary limits vs. operating angleThe two most important properties of a wick are the pore radius and the permeability. The pore radius determines the pumping pressure the wick can develop. The permeability determines the frictional losses of the fluid as it flows through the wick. There are several types of wick structures available including: grooves, screen, cables/fibers, and sintered powder metal. Figure 5 shows several heat pipe wick structures.It is important to select the proper wick structure for your application. The above list is in order of decreasing permeability and decreasing pore radius.Grooved wicks have a large pore radius and a high permeability, as a result the pressure losses are low but the pumping head is also low. Grooved wicks can transfer high heat loads in a horizontal or gravity aided position, but cannot transfer large loads against gravity. The powder metal wicks on the opposite end of the list have small pore radii and relatively low permeability. Powder metal wicks are limited by pressure drops in the horizontal position but can transfer large loads against gravity.Effective Heat Pipe Thermal ResistanceThe other primary heat pipe design consideration is the effective heat pipe thermal resistance or overall heat pipe T at a given design power. As the heat pipe is a two-phase heat transfer device, a constant effective thermal resistance value cannot be assigned. The effective thermal resistance is not constant but a function of a large number of variables, such as heat pipe geometry, evaporator length, condenser length, wick structure, and working fluid.Figure 5: Wick structuresThe total thermal resistance of a heat pipe is the sum of the resistances due to conduction through the wall, conduction through the wick, evaporation or boiling, axial vapor flow, condensation, and conduction losses back through the condenser section wick and wall.Figure 6 shows a power versus T curve for a typical copper/water heat pipe.Figure 6: Predicted heat pipe Delta-TTThe detailed thermal analysis of heat pipes is rather complex. There are, however, a few rules of thumb that can be used for first pass design considerations. A rough guide for a copper/water heat pipe with a powder metal wick structure is to use 0.2°C/W/cm2 for thermal resistance at the evaporator and condenser, and 0.02°C/W/cm2 for axial resistance.The evaporator and condenser resistances are based on the outer surface area of the heat pipe. The axial resistance is based on the cross-sectional area of the vapor space. This design guide is only useful for powers at or below the design power for the given heat pipe.For example, to calculate the effective thermal resistance for a 1.27 cm diametercopper/water heat pipe 30.5 cm long with a 1 cm diameter vapor space, the following assumptions are made. Assume the heat pipe is dissipating 75 watts with a 5 cm evaporator and a 5 cm condenser length. The evaporator heat flux (q) equals the power divided by the heat input area (q = Q/A evap; q = 3.8 W/cm2). The axial heat flux equals the power divided by the cross sectional area of the vapor space (q=Q/A vapor; q = 95.5W/cm2).The temperature gradient equals the heat flux times the thermal resistance.T = q evap * R evap + q axial * R axial + q cond * R condT = 3.8 W/cm2 * 0.2°C/W/cm2 + 95.5 W/cm2 * 0.02°C/W/cm2+ 3.8 W/cm2 * 0.2°C/W/cm2T = 3.4°CIt is important to note that the equations given above for thermal performance are only rule of thumb guidelines. These guidelines should only be used to help determine if heat pipes will meet your cooling requirements, not as final design criteria. More detailed information on power limitations and predicted heat pipe thermal resistances are given in the heat pipe design books listed in the reference section.Heat Pipe Electronic Cooling Applications:Perhaps the best way to demonstrate the heat pipes application to electronics cooling is to present a few of the more common examples. Currently, one of the highest volume applications for heat pipes is cooling the Pentium processors in notebook computers. Due to the limited space and power available in notebook computers, heat pipes are ideally suited for cooling the high power chips.Fan assisted heat sinks require electrical power and reduce battery life. Standard metallic heat sinks capable of dissipating the heat load are too large to be incorporated into the notebook package. Heat pipes, on the other hand, offer a high efficiency, passive, compact heat transfer solution. Three or four millimeter diameter heat pipes can effectively remove the high flux heat from the processor. The heat pipe spreads the heat load over a relatively large area heat sink, where the heat flux is so low that it can be effectively dissipated through the notebook case to ambient air. The heat sink can be the existing components of the notebook, from Electro-Magnetic Interference (EMI) shielding under the key pad to metal structural components. Various configurations of notebook heat pipe heat sinks are shown in Figure 7.Figure 7: Typical notebook heat pipe heat sinkTypical thermal resistances for these applications at six to eight watt heat loads are 4 - 6°C/watt. High power mainframe, mini-mainframe, server and workstation chips may also employ heat pipe heat sinks. High end chips dissipating up to 100 watts are outside the capabilities of conventional heat sinks. Heat pipes are used to transfer heat from the chip to a fin stack large enough to convect the heat to the supplied air stream. The heatpipe isothermalizes the fins eliminating the large conductive losses associated with standard sinks. The heat pipe heat sinks, shown in Figure 8, dissipate loads in the 75 to 100 watt range with resistances from 0.2 to 0.4°C/watt, depending on the available air flow.Figure 8: High end CPU heat pipe heat sinkIn addition, other high power electronics including Silicon Controlled Rectifiers (SCR's), Insulated Gate Bipolar Transistors (IGBT's) and Thyristors, often utilize heat pipe heat sinks. Heat pipe heat sinks similar to the one shown in Figure 9, are capable of cooling several devices with total heat loads up to 5 kW. These heat sinks are also available in an electrically isolated versions where the fin stack can be at ground potential with the evaporator operating at the device potentials of up to 10 kV. Typical thermal resistances for the high power heat sinks range from 0.05 to 0.1°C/watt. Again, the resistance is predominately controlled by the available fin volume and air flow.Figure 9: High power IGBT heat pipe heat sink。
加温呼吸管路 独立证书

加温呼吸管路独立证书The problem at hand is the need for a heated breathing circuit independent certification. This requirement arises in the context of medical devices, particularly those used in respiratory therapy. A breathing circuit is a vital component of such devices, responsible for delivering oxygen and removing carbon dioxide from a patient's lungs. The use of a heated breathing circuit is especially important in certain cases, such as when treating patients with respiratory conditions or those undergoing anesthesia.The first perspective to consider is the patient's comfort and safety. A heated breathing circuit can provide a more comfortable experience for patients by ensuring that the air they breathe is warm and humidified. This is particularly beneficial for patients with respiratory conditions, as it can help alleviate symptoms such as dryness and irritation in the airways. Additionally, a heated breathing circuit can also reduce the risk of complications, such as the formation of mucus plugs ordamage to the airways due to cold and dry air.From a healthcare professional's standpoint, the independent certification of a heated breathing circuit is crucial. Certification ensures that the device meets the necessary safety and performance standards, providing healthcare professionals with the confidence to use it in clinical settings. It also helps in selecting the most suitable device for specific patient needs, as certified products have been thoroughly evaluated and proven to be effective. Moreover, independent certification adds credibility to the manufacturer's claims about the device's performance and safety, enabling healthcare professionals to make informed decisions.For manufacturers, independent certification of a heated breathing circuit is essential for market competitiveness. Certification not only demonstrates the quality and reliability of their product but also differentiates it from non-certified alternatives. It serves as a powerful marketing tool, showcasing the manufacturer's commitment to meeting the highest industrystandards and ensuring customer satisfaction. Furthermore, certification can open doors to new markets and collaborations, as it provides assurance to potential partners and clients that the device has undergone rigorous testing and evaluation.Regulatory bodies and policymakers also have a vested interest in the independent certification of heated breathing circuits. Certification ensures that these devices comply with regulatory requirements and safety standards, protecting the public from potential harm. By setting clear guidelines and standards, regulators can promote the development of safe and effective medical devices, fostering innovation while safeguarding patient well-being. Furthermore, certification helps regulators in monitoring and enforcing compliance, ensuring that manufacturers adhere to the established standards throughout the lifecycle of the product.Lastly, the independent certification of heated breathing circuits contributes to the overall advancement of respiratory therapy. By establishing standardizedcriteria for performance and safety, certification encourages research and development in this field. This, in turn, can lead to the introduction of more advanced and efficient devices, benefiting both patients and healthcare professionals. Additionally, certification can facilitate the exchange of knowledge and best practices among manufacturers, healthcare professionals, and researchers, fostering collaboration and driving continuous improvement in respiratory therapy.In conclusion, the independent certification of heated breathing circuits is crucial from various perspectives. It ensures patient comfort and safety, provides healthcare professionals with confidence in device performance, enhances market competitiveness for manufacturers, supports regulatory compliance, and promotes the advancement of respiratory therapy. By addressing these requirements, the certification process contributes to the overall quality and effectiveness of medical devices used in respiratory therapy, ultimately benefiting patients and the healthcare community as a whole.。
Heat pump with capillary tube-type expansion devic

专利名称:Heat pump with capillary tube-typeexpansion device发明人:Hama, Hiroaki,Imanishi, Masami,Tanaka,Naoki申请号:EP85303661申请日:19850523公开号:EP0162720A3公开日:19860723专利内容由知识产权出版社提供专利附图:摘要:A heat pump employing a capillary tube as an expansion device. The mainthrottle portion of the heat pump comprises a main capillary tube 312 and a by-pass 311through which a portion of the refrigerant flows and cools the refrigerant flowing through the main capillarytube. A solenoid valve 360 for controlling the flow of refrigerant through the main capillary tube is connected to the intake of the main capillary tube, and an electrical expansion valve 350 is connected to the intake of the by-pass for controlling the flow therethrough. An auxiliary capillary tube 400 for cooling and an auxiliary capillary tube 500 for heating are connected in parallel with the main throttle portion, both capillary tubes having a higher resistance to flow than the main capillary tube. The auxiliary capillary tubes increase the range over which control of the flow of refngerant can be achieved, allowing both a smaller flow of refrigerant during under minimum cooling or heating load as well as a larger flow of refrigerant under maximum cooling or heating load.申请人:MITSUBISHI DENKI KABUSHIKI KAISHA更多信息请下载全文后查看。
超临界机组锅炉汽水流程英语

超临界机组锅炉汽水流程英语Supercritical Power Plant Boiler Drum Water Cycle.In a supercritical power plant, the boiler drum water cycle is a crucial process for generating high-pressure steam to drive the turbine and electricity generator. The subcritical system operates at pressures below the critical pressure of water (22.064 MPa), while the supercritical system operates at a pressure greater than this critical value, often around 24-25 MPa.Water Cycle in a Supercritical Power Plant Boiler.The water cycle in a supercritical power plant boiler typically involves the following steps:1. Feedwater Preheating:Feedwater from the condensate pump is preheated in a series of heat exchangers, such as the economizer andpreheater, using heat from the flue gases leaving the boiler.This preheating raises the feedwater temperature to near the saturation temperature of the boiler pressure.2. Evaporation and Steam Generation:The preheated feedwater enters the boiler drum, where it mixes with the saturated water in the drum.Heat from the combustion process in the furnace causes part of the water in the drum to evaporate, generating saturated steam.3. Steam Separation:The saturated steam-water mixture rises into the steam separator, located at the top of the boiler drum.The steam separator removes most of the entrained water droplets from the steam, producing dry saturatedsteam.4. Superheating:The dry saturated steam leaving the steam separator is further heated in the superheater, which is located in the path of the flue gases.This additional heat raises the steam temperature above its saturation temperature, creating superheated steam.5. Reheating (Optional):In some supercritical power plants, the superheated steam may be expanded in a high-pressure turbine and then reheated in a reheater before entering a low-pressure turbine.Reheating improves the overall efficiency of the cycle by reducing the moisture content of the steam entering the low-pressure turbine.6. Steam Turbine and Generator:The superheated steam (or reheated steam) flows to the steam turbine, where it expands and loses pressure.The expansion of the steam drives the blades of the turbine, which is connected to the electricity generator.7. Condensation and Return:After passing through the turbine, the steam enters the condenser, where it is cooled and condensed back into water.The condensate is then pumped back to the feedwater preheater, completing the cycle.Advantages of Supercritical Power Plants:Supercritical power plants offer several advantages over conventional subcritical power plants:Higher Thermal Efficiency: Operating at supercritical pressures allows for higher steam temperatures and pressures, resulting in improved thermal efficiency and reduced fuel consumption.Reduced Emissions: Supercritical power plants can achieve lower nitrogen oxide (NOx) and sulfur dioxide (SO2) emissions due to the higher combustion efficiency.Compact Design: Supercritical boilers are more compact than subcritical boilers, as they operate at higher pressures and require less heat transfer area.Increased Flexibility: Supercritical power plants can ramp up and down more quickly than subcritical plants, making them more responsive to changes in demand.Challenges:Despite these advantages, supercritical power plants come with some challenges:High Material Stress: Operating at supercritical pressures poses significant challenges for materials, as they must withstand high temperatures and pressures without failure.Water Chemistry Control: Supercritical water is more corrosive and requires strict water chemistry control to prevent damage to boiler components.Equipment Costs: Supercritical boilers and turbines are typically more expensive than subcritical components due to the need for specialized materials and designs.Overall, supercritical power plants play a key role in the generation of efficient and reliable electricity from fossil fuels. As technology continues to advance and materials improve, supercritical power plants are expected to become even more prevalent in the future.。
美国标准2-22-1773-02 1.5-5吨热泡机 冷气机冷凝管说明书

Cased and UncasedHeat Pump / Cooling Coils 1 1/2 - 5 TonPUB. NO. 22-1773-02Heat Pump/Cooling CoilNomenclature2T X C B036A C3H C A ARefrigerant Type2 - R224 - R410AProduct FamilyT-Premium (Heat Pump or Convertible Coil)C - Standard (Cooling Only)Coil DesignX - Direct Expansion Evaporator CoilProduct FamilyC - Cased A CoilA - Uncased A CoilF - Cased Horizontal Flat CoilCoil Width (Cased/Uncased)A - 14.5" / 13.3"B - 17.5" / 16.3"C - 21.0" / 19.8"D - 24.5" / 23.3"H - 10.5"Refrigerant Line Coupling0 - BrazedNominal Capacity in 000's of BTU'sMajor Design ChangeEfficiencyC - StandardS - Hi EfficiencyRefrigerant Control3 - TXV - Non-BleedCoil CircuitryH - Heat PumpC - Cooling OnlyAirflow ConfigurationA - Upflow OnlyU - Upflow / DownflowH - Horizontal OnlyC - Convertible - Upflow, Downflow, Left AirflowM - Convertible - Upflow, Downflow, Left or Right AirflowMinor Design ChangeUnit Parts Identifier2Pub. No. 22-1773-02© 2006 American Standard Inc. All rights reserved3Pub. No. 22-1773-02General DataOptional Accessories13 SEER Coil EnclosuresModel Number Coil Cooling or Heat PumpUsed With Furnaces Flush on Both Sides Dimensions (in.)H x W x DBAYCLE14A1422A2/4CXAA018AC3CUA 2/4CXAA024AC3CUA TXA018C4TXA024C4TXA030C414-1/2" Wide Furnaces22-1/2 x 14-1/2 x 21-1/2BAYCLE17A1722A 2/4CXAB025AC3CUA 2/4CXAB031AC3CUA 2/4CXAB036AC3CUA 2/4CXAB042AC3CUA 2/4CXAB048AC3CUA TXA025C4TXA031C4TXA035C4TXA036C4TXA042C4TXA048C417-1/2" Wide Furnaces 22-5/8 x 17-1/2 x 21-1/2BAYCLE21A2130A 2/4CXAC037AC3CUA 2/4CXAC043AC3CUA 2/4CXAC049AC3CUA 2/4CXAC060AC3CUATXA037C4TXA043C4TXA049C4TXA060C5RXA060S321" Wide Furnaces 30 x 21 x 21-1/2BAYCLE24A2430A2/4CXAD050AC3CUA 2/4CXAD061AC3CUA TXA061C5RXA061S324-1/2" Wide Furnaces 30 x 24-1/2 x 21-1/2GeneralDataNON-BLEED TXV KITS13 SEER Coils R410A R222/4TXC,CXC,CXA - 0184AYTXVH3D1831A2AYTXVH3C1818A2/4TXC,CXC,CXA - 0244AYTXVH3D1831A2AYTXVH3C2425A2/4TXC,CXC,CXA - 0254AYTXVH3D1831A2AYTXVH3C2425A2/4TXC,CXC,CXA - 0304AYTXVH3D1831A2AYTXVH3C3031A2/4TXC,CXC,CXA - 0314AYTXVH3D1831A2AYTXVH3C3031A2/4TXC,CXC,CXA - 0364AYTXVH3D3343A2AYTXVH3C3337A2/4TXC,CXC,CXA - 0374AYTXVH3D3343A2AYTXVH3C3337A2/4TXC,CXC,CXA - 0424AYTXVH3D3343A2AYTXVH3C4243A2/4TXC,CXC,CXA - 0434AYTXVH3D3343A2AYTXVH3C4243A2/4TXC,CXC,CXA - 0484AYTXVH3D4863A2AYTXVH3C4850A2/4TXC,CXC,CXA - 0494AYTXVH3D4863A2AYTXVH3C4850A2/4TXC,CXC,CXA - 0504AYTXVH3D4863A2AYTXVH3C4850A2/4TXC,CXC,CXA - 0604AYTXVH3D4863A2AYTXVH3C5463A2/4TXC,CXC,CXA - 0614AYTXVH3D4863A2AYTXVH3C5463A4Pub. No. 22-1773-025Pub. No. 22-1773-02General DataPRODUCT SPECIFICATIONS [1] --- 2/4 CXC COOLING ONLYUPFLOW / DOWNFLOW CASED COILS* Reducer supplied with R-410A model[1]These indoor coils are A.R.I. certified with various split system air conditioners and heat pumps (A.R.I. Standard 210/240).Refer to the split system product data guides for performance data.2/4CXCA018AC3CU A2/4CXCA024AC3CUA2/4CXCB025AC3CUA2/4CXCB031AC3CUA2/4CXCB036AC3CUAINDOOR COIL--Type Rows / F .P .I.Face Area (sq.ft.)T ube Size (in.)Refrigerant Control (No internal check valve)Drain Conn. Size (in.)Duct Connections PLA TE FIN 2 / 183.503/8Non-Bleed TXV3/4 NPT PLA TE FIN 2 / 184.003/8Non-Bleed TXV3/4 NPT PLA TE FIN 3 / 143.503/8Non-Bleed TXV 3/4 NPT- See Outline Drawings -PLA TE FIN 3 / 143.503/8Non-Bleed TXV3/4 NPT PLA TE FIN 3 / 145.003/8Non-Bleed TXV3/4 NPT REFRIGERANT CONNECTIONS Line Size (Gas) (in.Line Size (Liquid) (in.)R-22 R-410A BRAZED BRAZED 5/8 1/2*1/4 1/4R-22 R-410A BRAZED BRAZED 3/4 5/8*5/16 5/16R-22 R-410A BRAZED BRAZED 3/4 5/8*5/16 5/16R-22 R-410A BRAZED BRAZED 3/4 3/4 5/16 5/16R-22 R-410A BRAZED BRAZED 7/8 3/4*3/8 3/8DIMENSIONS (In.)Crated (H x W x D)Uncrated (H x W x D)H x W x D 19 X 16-3/4 X 26H x W x D 19 X 16-3/4 X 26H x W x D 19 X 19-3/4 X 26- See Outline Drawings-H x W x D 19 X 19-3/4 X 26H x W x D 24 X 19-3/4 X 26WEIGHT (lbs.)Shipping -- Net17 / 1520 / 1822 / 2025 / 2326 / 242/4CXCC037AC3CUA2/4CXCB042AC3CUA2/4CXCC043AC3CUA2/4CXCB048AC3CUA2/4CXCC049AC3CUAINDOOR COIL--Type Rows / F .P .I.Face Area (sq.ft.)T ube Size (in.)Refrigerant Control (No internal check valve)Drain Conn. Size (in.)Duct Connections PLA TE FIN 3 / 145.003/8Non-Bleed TXV3/4 NPT PLA TE FIN 3 / 145.003/8Non-Bleed TXV3/4 NPT PLA TE FIN 3 / 145.003/8Non-Bleed TXV 3/4 NPT- See Outline Drawings -PLA TE FIN 3 / 146.003/8Non-Bleed TXV3/4 NPT PLA TE FIN 3 / 146.003/8Non-Bleed TXV3/4 NPT REFRIGERANT CONNECTIONS Line Size (Gas) (in.Line Size (Liquid) (in.)R-22 R-410A BRAZED BRAZED 7/8 3/4*3/8 3/8R-22 R-410A BRAZED BRAZED 7/8 3/4*3/8 3/8R-22 R-410A BRAZED BRAZED 7/8 3/4*3/8 3/8R-22 R-410A BRAZED BRAZED 1-1/8 7/8*3/8 3/8R-22 R-410A BRAZED BRAZED 1-1/8 7/8*3/8 3/8DIMENSIONS (In.)Crated (H x W x D)Uncrated (H x W x D)H x W x D 24 x 23-1/4 x 26H x W x D 24 x 19-3/4 x 26H x W x D 24 x 23-1/4 x 26- See Outline Drawings -H x W x D 28-1/4 x 19-3/4 x 26H x W x D 28-1/4 x 23-1/4 x 26WEIGHT (lbs.)Shipping -- Net17 / 1520 / 1822 / 2025 / 2326 / 242/4CXCD050AC3CUA2/4CXCC060AC3CUA2/4CXCD061AC3CUAINDOOR COIL--Type Rows / F .P .I.Face Area (sq.ft.)Tube Size (in.)Refrigerant Control (No internal check valve)Drain Conn. Size (in.)Duct Connections PLA TE FIN3 / 146.003/8Non-Bleed TXV3/4 NPT PLA TE FIN 3 / 147.003/8Non-Bleed TXV 3/4 NPT- See Outline Drawings -PLA TE FIN 3 / 147.003/8Non-Bleed TXV3/4 NPT REFRIGERANT CONNECTIONS Line Size (Gas) (in.Line Size (Liquid) (in.)R-22 R-410A BRAZED BRAZED 1-1/8 7/8*3/8 3/8R-22 R-410A BRAZED BRAZED 1-1/8 7/8*3/8 3/8R-22 R-410A BRAZED BRAZED 1-1/8 7/8*3/8 3/8DIMENSIONS (In.)Crated (H x W x D)Uncrated (H x W x D)H x W x D 28-1/4 x 26-3/4 x 26H x W x D 31-1/2 x 23-1/4 x 26- See Outline Drawings -H x W x D 31-1/2 x 26-3/4 x 26WEIGHT (lbs.)Shipping -- Net17 / 1520 / 1822 / 206Pub. No. 22-1773-022/4CXAB042AC3CUA 2/4CXAB048AC3CUA 2/4CXAC037AC3CUA 2/4CXAC043AC3CUA 2/4CXAC049AC3CUAINDOOR COIL -- Type Rows / F .P .I.Face Area (sq.ft.)T ube SizeRefrigerant Control (No internal check valve)Drain Conn. Size (in.)Duct Connections PLA TE FIN 3 / 145.003/8Non-Bleed TXV3/4 NPT PLA TE FIN 3 / 146.003/8Non-Bleed TXV3/4 NPT PLA TE FIN 3 / 145.003/8Non-Bleed TXV 3/4 NPT-See Outline Drawings-PLA TE FIN 3 / 145.003/8Non-Bleed TXV3/4 NPT PLA TE FIN 3 / 146.003/8Non-Bleed TXV3/4 NPT REFRIGERANT CONNECTIONS Line Size -- Gas (in.)Line Size -- Liquid (in.)R-22 R-410A BRAZED BRAZED 7/8 3/4*3/8 3/8R-22 R-410A BRAZED BRAZED 1-1/8 7/8*3/8 3/8R-22 R-410A BRAZED BRAZED 7/8 3/4*3/8 3/8R-22 R-410A BRAZED BRAZED 7/8 3/4*3/8 3/8R-22 R-410A BRAZED BRAZED 1-1/8 7/8*3/8 3/8DIMENSIONS (in.)Crated (H x W x D)Uncrated H X W X D 22-3/4x 24 x 26-1/2H X W X D 28-1/4x20-1/2x26-1/2H X W X D 22-3/4x24x26-1/2-See Outline Drawings-H X W X D 22-3/4x 24 x 26-1/2H X W X D 28-1/4x24x26-1/2WEIGHT (lbs)Shipping -- Net44 / 4246 / 4334 / 3237 / 3542 / 392/4CXAC060AC3CUA 2/4CXAD050AC3CUA 2/4CXAD061AC3CUAINDOOR COIL -- Type Rows / F .P .I.Face Area (sq.ft.)Tube SizeRefrigerant Control (No internal check valve)Drain Conn. Size (in.)Duct Connections PLATE FIN 3 / 147.003/8Non-Bleed TXV3/4 NPT PLA TE FIN 3 / 146.003/8Non-Bleed TXV3/4 NPT PLA TE FIN 3 / 147.003/8Non-Bleed TXV 3/4 NPT-See Outline Drawings-REFRIGERANT CONNECTIONS Line Size -- Gas (in.)Line Size -- Liquid (in.)R-22 R-410A BRAZED BRAZED 1-1/8 7/8*3/8 3/8R-22 R-410A BRAZED BRAZED 1-1/8 7/8*3/8 3/8R-22 R-410A BRAZED BRAZED 1-1/8 7/8*3/8 3/8DIMENSIONS (in.)Crated (H x W x D)Uncrated H X W X D 31-1/2x27-1/2x26-1/2H X W X D 28-1/4x27-1/2x26-1/2H X W X D 31-1/2x27-1/2x26-1/2-See Outline Drawings-WEIGHT (lbs)Shipping -- Net44 / 4246 / 4334 / 32PRODUCT SPECIFICATIONS [1] 2/4 CXA UNCASED UPFLOW / DOWNFLOW* Reducer supplied with R-410A models[1]These indoor coils are A.R.I. certified with various split system air conditioners and heat pumps (A.R.I. Standard 210/240).Refer to the split system product data guides for performance data.General Data2/4CXAA018AC3CUA2/4CXAA024AC3CUA2/4CXAB025AC3CUA2/4CXAB031AC3CUA2/4CXAB036AC3CUAINDOOR COIL--Type Rows / F .P .I.Face Area (sq.ft.)Tube Size (in.)Refrigerant Control (No internal check valve)Drain Conn. Size (in.)Duct Connections PLATE FIN 2 / 183.503/8Non-Bleed TXV3/4 NPT PLATE FIN 2 / 184.003/8Non-Bleed TXV3/4 NPT PLATE FIN 3 / 143.503/8Non-Bleed TXV 3/4 NPT-See Outline Drawings-PLATE FIN 3 / 143.503/8Non-Bleed TXV3/4 NPT PLATE FIN 3 / 145.003/8Non-Bleed TXV3/4 NPT REFRIGERANT CONNECTIONS Line Size (Gas) (in.Line Size (Liquid) (in.)R-22 R-410A BRAZED BRAZED 5/8 1/2*1/4 1/4R-22 R-410A BRAZED BRAZED 3/4 5/8*5/16 5/16R-22 R-410A BRAZED BRAZED 3/4 5/8*5/16 5/16R-22 R-410A BRAZED BRAZED 3/4 3/43/8 3/8R-22 R-410A BRAZED BRAZED 7/8 3/4*3/8 3/8DIMENSIONS (In.)Crated (H x W x D)Uncrated (H x W x D)H x W x D 15-1/2x17-1/2x26-1/2H x W x D 18-1/2x17-1/2x26-1/2H X W X D 16-1/2x20-1/2x 26-1/2-See Outline Drawings-H X W X D 16-1/2x20-1/2 x26-1/2H X W X D 22-3/4x20-1/2x26-1/2WEIGHT (lbs.)Shipping -- Net25 / 2326 / 2434 / 3237 / 3542 / 397Pub. No. 22-1773-02PRODUCT SPECIFICA TIONS [1] -- 2/4 TXC - SPLIT SYSTEM HEA T PUMP / COOLING COMFORT™ COILSCASED UPFLOW / DOWNFLOW / HORIZONTAL* Reducer supplied with R-410A models[1]These indoor coils are A.R.I. certified with various split system air conditioners and heat pumps (A.R.I. Standard 210/240).Refer to the split system product data guides for performance data.General Data2/4TXCA018AC3HCA2/4TXCA024AC3HCA2/4TXCB025AC3HCA 2/4TXCB031AC3HCA 2/4TXCB036AC3HCAINDOOR COIL -- Type Rows / F .P .I.Face Area (sq.ft.)Tube SizeRefrigerant Control (No internal check valve)Drain Conn. Size (in.)Duct Connections PLATE FIN 2 / 183.503/8Non-Bleed TXV3/4 NPT PLATE FIN 2 / 184.003/8Non-Bleed TXV 3/4 NPT-See Outline Drawings-PLATE FIN 3 / 143.503/8Non-Bleed TXV3/4 NPT PLATE FIN 3 / 1243.503/8Non-Bleed TXV3/4 NPT PLATE FIN3 / 15.003/8Non-Bleed TXV3/4 NPT REFRIGERANT CONNECTIONS Line Size -- Gas (in.)Line Size -- Liquid (in.)R-22 R-410A BRAZED BRAZED 5/8 1/2*1/4 1/4R-22 R-410A BRAZED BRAZED 3/4 5/8*5/16 5/16R-22 R-410A BRAZED BRAZED 3/4 5/8*5/16 5/16R-22 R-410A BRAZED BRAZED 3/4 3/45/16 5/16R-22 R-410A BRAZED BRAZED 7/8 3/4*3/8 3/8DIMENSIONS (in.)Crated (H x W x D)Uncrated H X W X D 15-1/2x17-1/2x26-1/2H X W X D 18-1/2x17-1/2x26-1/2-See Outline Drawings-H X W X D 16-1/2x20-1/2x26-1/2H X W X D 16-1/2x20-1/2x26-1/2H X W X D 22-3/4x20-1/2x26-1/2WEIGHT (lbs)Shipping -- Net47 / 3450 / 3754 / 4267 / 5480 / 672/4TXCC037AC3HCA 2/4TXCB042AC3HCA2/4TXCC043AC3HCA 2/4TXCB048AC3HCA 2/4TXCC049AC3HCA INDOOR COIL -- Type Rows / F .P .I.Face Area (sq.ft.)T ube SizeRefrigerant Control (No internal check valve)Drain Conn. Size (in.)Duct Connections PLA TE FIN 3 / 145.003/8Non-Bleed TXV3/4 NPT PLA TE FIN 3 / 145.003/8Non-Bleed TXV 3/4 NPT-See Outline Drawings-PLA TE FIN 3 / 145.003/8Non-Bleed TXV3/4 NPT PLA TE FIN 3 / 146.003/8Non-Bleed TXV3/4 NPT PLA TE FIN 3 / 146.003/8Non-Bleed TXV3/4 NPT REFRIGERANT CONNECTIONS Line Size -- Gas (in.)Line Size -- Liquid (in.)R-22 R-410A BRAZED BRAZED 7/8 3/4*3/8 3/8R-22 R-410A BRAZED BRAZED 7/8 3/4*3/8 3/8R-22 R-410A BRAZED BRAZED 7/8 3/4*3/8 3/8R-22 R-410A BRAZED BRAZED 1-1/8 7/8*3/8 3/8R-22 R-410A BRAZED BRAZED 1-1/8 7/8*3/8 3/8DIMENSIONS (in.)Crated (H x W x D)Uncrated H X W X D 22-3/4x24x26-1/2H X W X D 22-3/4x20-1/2x26-1/2-See Outline Drawings-H X W X D 22-3/4x24x26-1/2H X W X D 28-1/4x20-1/2x26-1/2H X W X D 28-1/4x24x26-1/2WEIGHT (lbs)Shipping -- Net83 / 7072 / 5969 / 5684 / 7180 / 672/4TXCD050AC3HCA2/4TXCC060AC3HCA2/4TXCD061AC3HCA INDOOR COIL -- Type Rows / F .P .I.Face Area (sq.ft.)Tube SizeRefrigerant Control (No internal check valve)Drain Conn. Size (in.)Duct Connections PLA TE FIN 3 / 146.003/8Non-Bleed TXV3/4 NPT PLA TE FIN 3 / 147.003/8Non-Bleed TXV 3/4 NPT-See Outline Drawings-PLA TE FIN 3 / 147.003/8Non-Bleed TXV3/4 NPT REFRIGERANT CONNECTIONS Line Size -- Gas (in.)Line Size -- Liquid (in.)R-22 R-410A BRAZED BRAZED 1-1/8 7/8*3/8 3/8R-22 R-410A BRAZED BRAZED 1-1/8 7/8*3/8 3/8R-22 R-410A BRAZED BRAZED 1-1/8 7/8*3/8 3/8DIMENSIONS (in.)Crated (H x W x D)Uncrated H X W X D 28-1/4x27-1/2x26-1/2H X W X D 31-1/2x24x26-1/2-See Outline Drawings-H X W X D 31-1/2x27-1/2x26-1/2WEIGHT (lbs)Shipping -- Net90 / 7787 / 7490 / 778Pub. No. 22-1773-022/4TXFH018AS3HHA 2/4TXFH033AS3HHA2/4TXFH041AS3HHA2/4TXFH054AS3HHA 2/4TXFH063AS3HHAINDOOR COIL -- TypeRows / F.P .I.Face Area (sq.ft.)Tube SizeRefrigerant Control (No internalcheck valve)Drain Conn. Size (in.)Duct ConnectionsPLATE FIN 2/163.333/8Non-Bleed TXV 3/4 NPT PLATE FIN 3/143.333/8Non-Bleed TXV 3/4 NPT PLATE FIN 3/144.613/8Non-Bleed TXV 3/4 NPT -See Outline Drawings-PLATE FIN 4/144.613/8Non-Bleed TXV 3/4 NPT PLATE FIN 4/165.993/8Non-Bleed TXV 3/4 NPT REFRIGERANTCONNECTIONS Line Size -- Gas (in.)Line Size -- Liquid (in.)R-22 R-410A BRAZED BRAZED 5/8 1/21/4 1/4R-22 R-410A BRAZED BRAZED 3/4 3/45/16 5/16R-22 R-410A BRAZED BRAZED 7/8 3/43/8 3/8R-22 R-410A BRAZED BRAZED 1-1/8 7/83/8 3/8R-22 R-410A BRAZED BRAZED1-1/8 7/83/8 3/8DIMENSIONS (in.)Crated (H x W x D)Uncrated H X W X D 23 x 13-1/2 x 32-1/2See Outline Drawings H X W X D 23 x 13-1/2 x 32-1/2See Outline Drawings H X W X D 23 x 13-1/2 x 41-1/2See Outline Drawings H X W X D 23 x 13-1/2 x 41-1/2See Outline Drawings H X W X D 29 x 13-1/2 x 41-1/2See Outline Drawings WEIGHT (lbs)Shipping -- Net40 / 3546 /4156 / 3964 / 5779 / 70General DataPRODUCT SPECIFICATIONS [1] - 2/4 TXFH -- SPLIT SYSTEM HEAT PUMP / COOLINGCOMFORT™ COILS CASED HORIZONTAL[1]These indoor coils are A.R.I. certified with various split system air conditioners and heat pumps (A.R.I. Standard 210/240).Refer to the split system product data guides for performance data.9Pub. No. 22-1773-02Performance DataPRESSURE DROP CHARACTERISTICS FOR COOLING AND HEAT PUMP COILSAIRFLOW (CFM) VS. PRESSURE DROP ACROSS WET COILPRESSURE DROP (INCHES OF WATER COLUMN)MODEL.050.10.150.20.250.30.350.42/4CXCA018AC3CUA 2/4CXAA018AC3CUA 2/4TXCA018AC3HCA 4306157608809851080117512552/4TXFH018AS3HHA 3505758001050----2/4CXCA024AC3CUA 2/4CXAA024AC3CUA 2/4TXCA024AC3HCA 3605456908209301040113512302/4CXCB025AC3CUA 2/4CXCB031AC3CUA 2/4CXAB025AC3CUA 2/4CXAB031AC3CUA 2/4TXCB025AC3HCA 2/4TXCB031AC3HCA 31051570086510201170131014502/4TXFH033AS3HHA 5257501000115013251500--2/4CXCB036AC3CUA 2/4CXCB042AC3CUA 2/4CXAB036AC3CUA 2/4CXAB042AC3CUA 2/4TXCB036AC3HCA 2/4TXCB042AC3HCA 480690860100511301250136014602/4TXFH041AS3HHA 8001075132515751900---2/4CXCB048AC3CUA 2/4CXAB048AC3CUA 2/4TXCB048AC3HCA 47068084098011101220133014252/4CXCC037AC3CUA 2/4CXCC043AC3CUA 2/4CXAC037AC3CUA 2/4CXAC043AC3CUA 2/4TXCC037AC3HCA 2/4TXCC043AC3HCA 6309001105128014401520171018302/4CXCC049AC3CUA 2/4CXAC049AC3CUA 2/4TXCC049AC3HCA 6759701200139015601715186020002/4CXCC060AC3CUA 2/4CXAC060AC3CUA 2/4TXCC060AC3HCA 6809651190137515401685182019502/4CXCD050AC3CUA 2/4CXAD050AC3CUA 2/4TXCD050AC3HCA 81011401390160017901950211022502/4TXFH054AS3HHA 6008251050130015001700185220752/4CXCD061AC3CUA 2/4CXAD061AC3CUA 2/4TXCD061AC3HCA 82011551410162018101980213022802/4TXFH063AS3HHA80011501450175020002225--F r o m D w g . D 342478 R e v 1F r o m D w g . D 342479 R e v 1Pub. No. 22-1773-02F r o m D w g . D 342475 R e v 1Pub. No. 22-1773-02F r o m D w g . D 342476 R e v 114Pub. No. 22-1773-02F r o m D w g . D 342477 R e v 115Pub. No. 22-1773-02F r o m D w g . C 341655 R e v4Since American Standard has a policy of continuous product improvement, it reserves the right to change design and specifications without notice.Literature Order Number P.I.File Number22-1773-02Supersedes22-1773-01Stocking LocationPI Louisville & Inland-LaCrosseAmerican Standard Inc.6200 Troup Highway Tyler, TX 75707For more information contact your local dealer (distributor)。
板式换热器端口过滤器说明书

IntroductionThis manual provides information needed to install, operate and carry outmaintenance of the port filter used for gasketed plate heat exchanger with portsize 200 mm or larger.Intended useThe intended use of this equipment is to prevent foreign objects from enteringand causing clogging in gasketed plate heat exchangers.All other use is prohibited. Alfa Laval will not be held responsible for injury ordamage if the equipment is used for any other purpose than the intended usedescribed above.Environmental complianceAlfa Laval endeavours to perform its own operations as cleanly and efficientlyas possible, and to take environmental aspects into consideration whendeveloping, designing, manufacturing, servicing and marketing its products.Waste managementSeparate, recycle, or dispose of all material and components in a safe, andenvironmentally responsible way, or according to national legislation or localregulations. If there is any uncertainty regarding what material a component ismade of, contact the local Alfa Laval sales company. Use a certified (ISO14001 or similar) scrapping or waste handling company.UnpackingPacking material consists of wood, plastics, cardboard boxes and, in somecases, metal straps.•Wood and cardboard boxes can be reused, recycled or used for energyrecovery.•Plastics should be recycled or burnt at a licensed waste incineration plant.•Metal straps should be sent for material recycling.200001927-2-EN-GBThis document and its contents are subject to copyrights and other intellectual property rights owned by Alfa Laval Corporate AB. No part of this document may be copied, re-produced or transmitted in any form or by any means, or for any purpose, without Alfa Laval Corporate AB’s prior express written permission. Information and services provided in this document are made as a benefit and service to the user, and no representations or warranties are made about the accuracy or suitability of this information and these services for any purpose. All rights are reserved.© Alfa Laval Corporate ABMaintenance•All metal parts should be sent for material recycling.•Oil and all non-metal wear parts must be taken care of in accordance with local regulations.ScrappingAt end of use, the equipment shall be recycled according to relevant, local regulations. Besides the equipment itself, any hazardous residues from the process liquid must be considered and dealt with in a proper manner. When in doubt, or in the absence of local regulations, please contact the local Alfa Laval sales company.SafetySafety considerationsThe port filters shall be used and maintained in accordance with Alfa Laval’s instructions in this manual. Incorrect handling of the port filters may result in serious consequences with injuries to persons and/or property damage. Alfa Laval will not accept responsibility for any damage or injury resulting from not following the instructions in this manual.The port filters shall be used in accordance with the specified configuration of material, media types, temperatures and pressure for the specific plate heat exchanger were the port filter are used.Definitions of expressionsPersonal protective equipmentProtective shoesA shoe with a reinforced toe cap to minimize foot injuries caused by dropped articles.Protective helmetAny helmet designed to protect the head from accidental injury.Protective gogglesA pair of tight-fitting eyeglasses worn to protect the eyes from hazards.Protective glovesGloves that protects the hand from hazards.Working at heightIf the installation requires working at a height of two meters or higher, safety arrangements must be taken in consideration.DescriptionComponentsThe port filter consists of a cylindrical meshed tube with a flange in one end. The length of the filter tube is adapted for the total length of the plate pack including the thickness of the frame and pressure plate. The conical guide ring is inserted at the opposite port and keep the filter tube centered after installation. The welded rings in both ports provide a flat surface for flange gasket sealing against pipework and inspection cover.Following parts are required to install port filter.1.Port filter2.Conical guide ring3.Flange gasket (4 pieces per port filter)FunctionThe port filter is used to ensure high thermal efficiency of the plate heat exchanger by preventing foreign objects from entering and causing clogging of the plate pack. The port filter is designed to operate in conditions involving sea water, process water, cooling tower water or any kind of liquid containing particles with potential risk of disrupting the performance of the system.InstallationUnpackingFollow the instruction below to unpack the components of the port filter1Prepare an area with required space forunpacking.2Open the transport enclosure.3Check your shipment immediately uponarrival and make sure that the port filterreceived is in accordance with the orderspecification. In the event of damage, defectsor deficiency, immediately report the problemto the transport company and Alfa Laval.4Remove all additional components such asconical guide ring or other delivered partsfrom the transport enclosur.5Lift the port filter from the transport enclosure.Use lifting equipment with straps attachedaccording to picture or by hand for smallerport filters.Before installationPreparation of the plate heat exchanger before installation of the port filter. 1.Prepare the installation area around the plate heat exchanger and ensurethat required space is available.2.Installing port filter into an existing plate heat exchanger requirepreparation to ensure that correct port arrangement is in place for theinstallation. Consult Alfa Laval representative if any hesitation.3.Shut down, isolate and drain the plate heat exchanger by following theinstruction in section Shut-down4.Install port filter according to the section Installation of port filterShut-down1Slowly close the valve controlling the flowrate of the pump you are about to stop.2When the valve is closed, stop the pump.3Repeat the two steps for the other side for the second media.4If the plate heat exchanger is shut down forseveral days or longer, it should be drained.Draining should also be done if the process isshut down and the ambient temperature isbelow the freezing temperature of the media.Depending on the media processed, it is alsorecommended to rinse and dry the plate heatexchanger plates and connections.Installation of port filterInstallation of the port filter can be done when all preparation has been performed with shut-down and isolating the plates heat exchanger.1.Pressure plate 2.Frame plate 3.Inspection cover 4.Port filter 5.Conical guide ring 6.Flange gasket1Remove the connection flange pipe on the frame plate by loosening all nuts.2Attach one flange gasket at the port in the frame plate if not already in place.3Insert the conical guide ring into the port of the inlet flow (frame plate).4Attach one flange gasket to the outside of the conical guide ring flange.5Remove the inspection cover from the pressure plate by loosening all nuts. Uselifting equipment with straps attachedaccording to picture.6pressure plate if not already in place.7Insert the port filter into the port in the pressure plate.a)For large port filter use lifting equipment.b)Installation in lower port: Arrange strapsand chain pulley according to picture forinstallation in ports. Protect the threads ofthe tightening bolts by sliding a metal tubeover the tightening bolt.and chain pulley according to picture forinstallation in ports. Protect the threads ofthe tightening bolts by sliding a metal tubeover the tightening bolt.8Thread the port filter tube over the cone atthe opposite port by pushing the lower part of flange against the port and pull the upper part to guide the tube over the cone. Then pushthe port filter until the flange reach the liningof the port.9Attach the flange gasket to the outside of the port filter flange if not already in place.10Put the inspection cover back in place and fasten the nuts. Use lifting equipment withstraps arranged in the same way as in thestep of removing the inspection cover earlierin this instruction.11Attach the flange connection and fasten the nuts.OperationStart-upDuring the start-up, check that there are no visible leakages from the plate pack, valves or piping system.Centrifugal pumps must be started with valves closed and the valves must be operated as smoothly as possible.Do not run pumps temporarily empty on the suction side.1Check that the valve is closed between thepump and the unit controlling the system flowrate to avoid pressure surge.2If there is a vent valve installed at the exit,make sure it is fully open.3Increase the flow rate slowly.4Open the air vent and start the pump.5Open the valve slowly.6When all the air is expelled, close the airvent.7Repeat the procedure for the second media.MaintenanceTo keep a high performance of the plate heat exchanger the port filter needs to be cleaned at regular intervals. The frequency depends on volume of clogging or impurities in the media.Indicators of clogging filters can be pressure drop over the plate heat exchanger or difficulties to reach design temperature.Cleaning of port filters can be done by manual cleaning of port filter, see instruction Manual cleaning of the port filterManual cleaning of the port filter1Shut-down the plate heat exchangeraccording to the instruction Shut-down.2Close the valves and isolate the plate heat exchanger from the rest of the system.3Remove the inspection cover on the pressure plate by loosening all nuts. Use liftingequipment and arrange it according toinstruction in Installation of port filter.4Remove flange gasket5Grip around the port filter flange and pull out the port filter. If stuck, use a sharp tool toloosen it from the gasket. Use liftingequipment and arrange it according toinstruction in Installation of port filter.6Flush the port filter with water and brush to remove all clogging.7If clogging is present in the plate pack follow instruction in the Instruction Manual for theplate heat exchanger.8Re-insert the port filter, follow instruction in Installation of port filter.。
Wakefield-Vette 热管选择指南说明书

Heat pipes are used to transport heat over a distance with verylow thermal resistance. This is very helpful when small or distantheat sources need to be dissipated over a larger area or moved toa remote heat exchanger. Heat pipes are a Fluid Phase Changeapplication, often referred to as “re-circulating,” because they usea closed loop to transfer heat quickly through evaporation andcondensation within the heat pipe.Heat pipes do not actually dissipate the heat to the environment, butserve to move heat efficiently within a thermal system. A heat pipe isa copper tube with an internal wick structure that is sealed on bothends with a small amount of water inside. As heat is applied to thepipe, the water will boil and turn to a gas, which then travels to thecolder section of the heat pipe where it condenses back to a liquid.It is the evaporating and condensing of the water that form apumping action to move the water (and thus the heat) from end toend of the pipe.There are many types of wick structure that can be used within the heat pipeand they are generally classified into grooved, mesh, powder and hybrid. Agrooved heat pipe is a copper tube with a series of shallow grooves around theinternal perimeter of the heat pipe. While the water is a liquid, it travels in thegrooves and while it is a vapor it travels in the open space of the pipe. Groovedpipes can be used in horizontal orientations, but are very limited inperformance if used above 15°out of horizontal. A mesh heat pipe is a smoothwall copper tube with a woven copper mesh installed along the interior of thepipe. The mesh is designed to remain in contact with the walls of the pipe inareas where the pipe may be bent or flattened. Mesh pipes can be used inhorizontal and orientations up to 30°out of horizontal. A powder wick heatpipe can also be known as a sintered heat pipe.Grooved Heat PipeMesh Heat PipeDuring the manufacturing process a mandrel isinstalled in the center of the pipe and copperpowder is poured into the pipe around the mandrel.After the powder is sufficiently packed, the parts areplaced into a sintering oven. Once at temperature,the copper powder will stick to the pipe and toitself, forming numerous internal pockets like asponge. Because of the small pocket sizes, sinteredpipes can efficiently move the water and can beused horizontally, vertically and all points inbetween including upside down. Wakefield-Vetteprimarily sells sintered, or powder, style heat pipesdue to their higher performance and the best heatpipe for your application.Powder Wick Heat PipeHeat Pipe IntroductionMany thermal systems benefit from the addition of heat pipes, especially when heat sources are dense and/or remote to the final heat exchanger. Computer applications, such as processors, graphics cards and other chip-sets, have high thermally dissipated power in a small area. Fan heat sink combinations used in these applications can offer high-performance dissipation to the ambient, but much of the battle is to bring the heat to the heat exchanger with as little temperature change as possible. Heat pipes excel at this and can transport large heat loads from small areas with very little temperature difference.Why Use Heat Pipes?Key Features•Material:Copper•Wick Structure:Powder Sintered Copper •Light Weight•Versatile with high thermal performanceHeat pipes are used in many harsh environments such as:•Telecommunications •Aerospace•Transportation•Computers and DatacentersHeat pipes have proven to be robust and reliable over many years in these types of applications. The next section will give more technical detail on the performance of heat pipes depending on diameter, length, and angle of use.How Heat Pipes Operate1.Working fluid absorbs heat while evaporating to vapor2.Vapor transfers along the cavity to the lower temperature area3.Vapor condenses back to fluid, discharging heat4.Fluid is absorbed by the sintered/powdered wick structure5.Fluid returns to high temperature end via capillary force in the wick structure6.Natural or forced convection air flow dissipates excess heat to ambientHeat SourceHeat Pipe BasicsHeat Pipe Basics•Picking the correct pipe•Transport•General parameters•Bending•FlatteningWhen selecting the diameter and length of heat pipe it isimportant to consider the orientation with respect to gravityand overall heat load for the thermal system. The transportof vapor within the heat pipe is responsible for the thermalconduction from one end to the other. A larger diameterheat pipe can transport more vapor, translating into a largerheat carrying capacity. Also, the orientation of the pipe withrespect to gravity plays a role in the thermal capacity of aheat pipe.When selecting the diameter and length of heat pipe it is important to consider the orientation with respect to The thermal capacity is increased when the heat source is lower than the condenser (or ambient heat exchanger) because gravity assists the return of condensed water back to the heat source. The opposite is also true as the thermal capacity is reduced when the condensed water must move by capillary forces back to the heat source against gravity. This effect is exaggerated with longer heat pipes and testing has shown that the gravity effect can nearly the double the thermal capacity in the advantageous direction and cut the capacity in half in the deleterious direction from the heat pipe in the horizontal orientation. In the short heat pipe extreme (3”-4” length), this effect is nearly zero, so please consult with Wakefield-Vette engineers to find the right solution for your application.Flattening Heat PipesFlattening is another aspect of heat pipes that effect their performance.Often it is necessary to flatten a heat pipe to fit into a desired shape orgap or to increase the contact area of the pipe with the heat. Sinceflattening reduces the effective cross-sectional area of the round pipe,the thermal capacity is reduced, just as if a smaller diameter pipe wasbeing used. The larger diameter of the starting heat pipe, the largerreduction of thermal capacity is seen when flattening. Also, the largerdiameter pipes cannot be flattened to the same ultimate dimension asthe smaller pipes without disrupting heat flow altogether. This is alsotrue for bending of pipes. The radius of bending is usually 3-5x thediameter of the heat pipe depending on the pipe diameter and theprocess of bending the pipe. The potential danger is to collapse thepipe, effectively cutting off vapor and thermal transport.Bending radius for heatpipes of differentdiameters depending onthe method of bending.Bending•By Hand:•4mm: 4 x diameter•6mm: 4 x diameter•8mm: 5 x diameter•Tooling:•4mm: 3 x diameter•6mm: 3 x diameter•8mm: 4 x diameterHeat Pipe AssembliesInterfacing heat pipes with plates and heat exchangers ispredominately about maximizing contact area while adhering to theflattening and bending guidelines mentioned above. In most cases,the heat pipes are slotted into channels/grooves in the plate tomaximize contact. The heat pipe can be secured into the grooveusing solder or thermal epoxy, which also augments the contact areaof the heat pipe. The heat pipe can also be clamped between twoplates with matching channels/grooves which are fastened together.In the clamped configuration, thermal grease can be used to increasethe contact of the heat pipe to the plates to reduce the thermalresistance of the contact interface, just as the thermal epoxy andsolder did in the prior example.Wakefield-Vette offers individual Heat Pipes through distribution. These most common offerings are a great option for testing, sampling, and validating your heat pipe solution into eventual production.When building or testing your heat sink assembly please feel free to contact one of Wakefield Vette’s authorized distributors to purchase. Always remember to contact us for free consultation on assembly design or parameter questions.Wakefield Vette Standard Heat PipesWKV PARTNUMBER DESCRIPTION Type Length(mm)Diameter(mm)qMax124641Heat Pipe Straight Sintered 3X70MM Round7035W 124642Heat Pipe Straight Sintered 3X100MM Round10038W 124643Heat Pipe Straight Sintered 3X150MM Round150310W 124644Heat Pipe Straight Sintered 3X200MM Round20035W 121686_rev1Straight Sintered 4mmx70mm Round7047W 121687_rev1Straight Sintered 4mmx100mm Round100415W 121688_rev1Straight Sintered 4mmx150mm Round150410W 124646Heat Pipe Straight Sintered 4X200MM Round200410W 124647Heat Pipe Straight Sintered 4X250MM Round25048W 124645Heat Pipe Straight Sintered 4X300MM Round30045W 124650Heat Pipe Straight Sintered 5X70MM Round70520W 124651Heat Pipe Straight Sintered 5X100MM Round100532W 124652Heat Pipe Straight Sintered 5X150MM Round150535W 124653Heat Pipe Straight Sintered 5X200MM Round200530W 124654Heat Pipe Straight Sintered 5X250MM Round250525W 124648Heat Pipe Straight Sintered 5X300MM Round300515W 124649Heat Pipe Straight Sintered 5X350MM Round350510W 124657Heat Pipe Straight Sintered 6X70MM Round70635W 110578_rev1Heat Pipe Straight Sintered 6x0.3x100mm Round100635W 110579_rev1Heat Pipe Straight Sintered 6x0.3x150mm Round150660W 110580_rev1Heat Pipe Straight Sintered 6x0.3x200mm Round200650W 110581_rev1Heat Pipe Straight Sintered 6x0.3x250mm Round250640W 110582_rev1Heat Pipe Straight Sintered 6x0.3x300mm Round300640W 124655Heat Pipe Straight Sintered 6X350MM Round350625W 124656Heat Pipe Straight Sintered 6X400MM Round400618W 124682Heat Pipe Straight Sintered 8X70MM Round70845W 124662Heat Pipe Straight Sintered 8X150MM Round150870W 110583_rev1Heat Pipe Straight Sintered 8x0.3x200mm Round200850W 110584_rev1Heat Pipe Straight Sintered 8x0.3x250mm Round250840W 110585_rev1Heat Pipe Straight Sintered 8x0.3x300mm Round300855W 124658Heat Pipe Straight Sintered 8X350MM Round350835W 124659Heat Pipe Straight Sintered 8X400MM Round400825W 214660Heat Pipe Straight Sintered 8X450MM Round450820W 124661Heat Pipe Straight Sintered 8X500MM Round500815W 121689_rev1Straight Sintered 10mmx100mm Round1001080W 124669Heat Pipe Straight Sintered 10X150MM Round15010120W 121690_rev1Straight Sintered 10mmx200mm Round2001070W 121691_rev1Straight Sintered 10mmx250mm Round2501065W 121692_rev1Straight Sintered 10mmx300mm Round3001050W 124663Heat Pipe Straight Sintered 10X350MM Round3501060W 124664Heat Pipe Straight Sintered 10X400MM Round4001052W 124665Heat Pipe Straight Sintered 10X450MM Round4501045W 124666Heat Pipe Straight Sintered 10X500MM Round5001040W 124667Heat Pipe Straight Sintered 10X550MM Round5501035W 124668Heat Pipe Straight Sintered 10X600MM Round6001025W 124670Heat Pipe Straight Sintered 12x70MM Round701250W 124671Heat Pipe Straight Sintered 12x100MM Round10012130W 124672Heat Pipe Straight Sintered 12x150MM Round15012150W 124673Heat Pipe Straight Sintered 12x200MM Round20012130W 124674Heat Pipe Straight Sintered 12x250MM Round25012115W 124675Heat Pipe Straight Sintered 12x300MM Round30012100W 214676Heat Pipe Straight Sintered 12x350MM Round3501275W 124677Heat Pipe Straight Sintered 12x400MM Round4001265W 124678Heat Pipe Straight Sintered 12x450MM Round4501255W 124679Heat Pipe Straight Sintered 12x500MM Round5001250W 124680Heat Pipe Straight Sintered 12x550MM Round5501242W 124681Heat Pipe Straight Sintered 12x600MM Round6001230W 120229Straight Ultra thin 5mm dia x 100mm length; Flattened thickness 1.0mmm Flat100112W 120231Straight Ultra thin 6mm dia x 100mm length; Flattened thickness 1.5mm Flat100 1.525W 121716_rev1Flat Heat Pipe 2.5 X 100mm Flat100 2.535W 121717_rev1Flat Heat Pipe 2.5 X 150mm Flat150 2.530W 121718_rev1Flat Heat Pipe 2.5 X 200mm Flat200 2.525W 121719_rev1Flat Heat Pipe 2.5 X 250mm Flat250 2.515W 121720_rev1Flat Heat Pipe 3.0 X 100mm Flat100345W 121721_rev1Flat Heat Pipe 3.0 X 1500mm Flat150340W 121722_rev1Flat Heat Pipe 3.0 X 200mm Flat200335W 121723_rev1Flat Heat Pipe 3.0 X 250mm Flat250330W 121724_rev1Flat Heat Pipe 3.0 X 300mm Flat300325W 121725_rev1Flat Heat Pipe 4.5 X 100mm Flat100 4.555W 121726_rev1Flat Heat Pipe 4.5 X 150mm Flat150 4.555W。
特立尼Modular空气冷却机(热泵)CXAJ CGAJ系列产品说明书

CXAJ/CGAJModular Air-Cooled Chiller (Heat Pump) Unit 65KW/130KWHigh efficiency model • Standard modelTrane CXAJ/CGAJ Modular Air-cooled Chiller (Heat Pump) UnitT heUniform appearance of different modules (65kW and 130kW) guarantees orderly installation on site. Up to 25 modules, with capacity of 3,250kW and applicable floor space of 30,000 m 2.Module installation allows easy transportation as well as system expansion and staged investment.Up to 25 modules in single modular system, easier to expand system capacityLight-weight unit reduces the foundation loadTrane's new CXAJ/CGAJ modular chiller adopts Y-shape design, which is granted with appearance patent.The design achieves seamless connection at length directionn, saving the service space between modules. More than 30% floor space is reduced comparing with conventional design.The design simplifies water piping, saves installation space, and effectively reduces system pressure drop, which further reduces pump consumption.Y-shape design achieves seamless module connection, saving more installation spaceFloor space: 2.145 m 2Length * width:2,145mm x 1,000mmFloor space: 2.17 m 2Length * width:2,170mm x 1,000mmProduct featuresNew Y-shape unit:For example, the three-module unit saves 30% of floor space.Previous typeThanks to the shell-tube heat exchanger design, the pressure drop inside is lower, and thesystem energy consumption and risks of filth or ice blockage will thus be reduced.Efficient shell-tube heat exchangerThe tandem scroll compressor (high efficient model) greatly improves the efficiency under partial loads.The compressor is standard with heating belt on crank case, keeping the lubricating oil effective in cold winter.Efficient scroll compressorFeaturing high accuracy of adjustment and rapidmovement, the electronic expansion valve can adapt to any sudden change of the refrigerant flow, especially at low temperature. Comparing with the thermal expansion valve, it may better react to superheat conditions for accurate and rapid adjustment.Electronic expansion valveIt stores extra refrigerant based on the demands of different conditions needs to keep stable operation of the system.AccumulatorIt avoids liquid shock caused by liquid refrigerant into compressor.SeparatorIt avoids filth or ice blockage caused by impurities or moisture in the refrigerating circuit.Dry filterMulti protectionPower protectionLow water flow protectionFan overloading protectionHigh exhausting temperature protectionLow suction pressure protection High delivery water temperature protectionHigh exhausting pressure protection Low delivery water temperature protectionCompressor overloading protectionFailureKeep runningSingle CXAJ/CGAJ module contains more than two compressors and refrigerating circuits. In case of failure of one compressor, other compressors will switch to emergency operation.Back-up operation will be activated in case of failureWith automatic failure alarm, the fault code will be indicated on the screen of the controller in case of any failure, enabling operators to conduct trouble shooting timely.Automatic failure alarmCXAJ/CGAJ system can monitor compressors status in each module timely via modular controller and adjust each compressor running time to balance and allocate compressors intelligently, thus prolonging service life.Balanced compressor operation190-hour operation180-hour operation200-hour operationFailureUnit failureController shows the fault code.Keep running Single moduleReliable support for stable operationContinuous heating and defrosting with non-stop running in winterUnder heating mode in winter, the air-cooled heat pump will encounter frost due to the moisture in the air at a low temperature. Trane's intelligent defrosting function can select the appropriate defrosting time automatically as per the operating conditions to guarantee continuous indoor heating effect.When modular connected, the master controller willcalculate and balance the defrosting time of each module automatically. The defrosting operations in any modules will not impact the normal working of the others, so as to guarantee the continuous heating in winter.C ir cu l ar t e mp er a t u r e p r e s s ur es t e mt em p e r at u r e..Intelligent defrostingSingle moduleModule combinationY-shaped design with seamless module connection cankeep air circulation on a smaller floor space. 610mm spaceat the bottom conduces to the smooth maintenance.It is suggested to put the unit at a place with good heat dissipation andat least 1.2m away from the wall.Installation spaceUp to 8 units in single module.Only reversed return connection is allowed.Multi modules (Reversed return connection)Note: For multi modules, up to 8 units in single module. Direct return connection is not allowed.Single module: Can connect up to 8 unitsReversed return connectionAir inletAir inletExhaustfrom the topNote: The maximum units in direct return connection is 4.Water outletWater inletWater inlet Up to 8 unitsThe special design of the frame and cover keeps the major parts and control panel, inside, which can protect thedamage arising from external environment and reduce the operation noise. Meanwhile, the maintenance of theunit is also very simple and convenient.Easy maintenanceService cover ofelectrical partsService cover ofrefrigerating partsPlease refer to the installation manual if the unit needs toThe unit can be connected to the building management (System BMS) by the standard Mod Bus communica-tion protocol, which can support up to 375 units.Modular controller50x100mm LCD display and 15buttons,convenient operation interface.RS485 port provides standard Mod Bus communication protocol to control system in buildings.FunctionsFeaturesRapid query (Automatic browsing and manual query)Software monitoringKeyboard locking to avoid mis-operation Display of unit failureTrane's modular controller is applicable to single unit or multi-modules combination for centralized control.A centralized control of up to 25 units can be achieved.Up to 25 units can be centrally controlled by one modular controller1. The cooling capacity is measured at the condition of water inlet at 12°C, water outlet at 7°C and air inlet at 35°C of ambient temperature.2. The heating capacity is measured at the condition of water inlet at 40°C, water outlet at 45°C and air inlet at 7°C of dry-bulb temperature and 6°C of wet-bulb temperature.3. Executive standard: CXAJ/CGAJ 065/ 130unit GB/T18430.1 – 2007Unit parametersControl and unit parameters。
- 1、下载文档前请自行甄别文档内容的完整性,平台不提供额外的编辑、内容补充、找答案等附加服务。
- 2、"仅部分预览"的文档,不可在线预览部分如存在完整性等问题,可反馈申请退款(可完整预览的文档不适用该条件!)。
- 3、如文档侵犯您的权益,请联系客服反馈,我们会尽快为您处理(人工客服工作时间:9:00-18:30)。
(51) Int Cl.: F28D 15/02 (2006.01)
F28D 15/04 (2006.01)
(84) Etats contractants désignés: AL AT BE BG CH CY CZ DE DK EE ES FI FR GB GR HR HU IE IS IT LI LT LU LV MC MK MT NL NO PL PT RO RS SE SI SK SM TR Etats d’extension désignés: BA ME Etats de validation désignés: KH MA MD TN
ouverture dont les bords délimitent en partie un canal (8). Les ouvertures d’au moins trois plaques intercalaires (14, 16) sont dimensionnées de sorte qu’elles délimitent des rainures (10) s’étendant entre la première extrémité et la deuxième extrémité du caloduc, les rainures (10) présentant une largeur dans une direction de l’empilement est inférieure à la profondeur dans la direction du plan des plaques (14, 16).
de sous forme vapeur et de part et d’autre de ces zones
[0002] L’invention appartient au domaine des disposi-
des zones poreuses de circulation du liquide, ces zones
(19)
*EP003561428A1*
(11)
Hale Waihona Puke EP 3 561 428 A1
(12)
DEMANDE DE BREVET EUROPEEN
(43) Date de publication: 30.10.2019 Bulletin 2019/44
(21) Numéro de dépôt: 19168582.5
(30) Priorité: 11.04.2018 FR 1853173
(71) Demandeur: Commissariat à l’énergie atomique et aux énergies alternatives 75015 Paris (FR)
(72) Inventeurs: • GRUSS, Jean-Antoine 38170 SEYSSINET (FR) • MARIOTTO, Mathieu 38054 GRENOBLE CEDEX 09 (FR)
DOMAINE TECHNIQUE ET ÉTAT DE LA TECHNIQUE
fondeur sur largeur important. En outre, les coins du fond
ANTÉRIEURE
des rainures sont arrondis.
5 [0012] Le document US 7 051793 décrit un caloduc
(74) Mandataire: Brevalex 95, rue d’Amsterdam 75378 Paris Cedex 8 (FR)
(54) CALODUC A POMPAGE CAPILLAIRE A FONCTIONNEMENT AMELIORE
(57) Caloduc à pompage capillaire comprenant une première extrémité destinée à être échauffée et une deuxième extrémité destinée à être refroidie, et une enceinte étanche s’étendant entre la première extrémité et la deuxième extrémité, l’enceinte comprenant un empilement de plaques (12, 14, 16), ledit empilement comportant deux plaques de fermeture (12), et des plaques intercalaires (14, 16) entre les plaques de fermeture (12), chaque plaque intercalaire (14, 16) comportant une
tifs d’échange thermique, en particulier des caloducs,
capillaires s’étendant sur tout le caloduc.
EP 3 561 428 A1
Printed by Jouve, 75001 PARIS (FR)
1
EP 3 561 428 A1
2
Description
[0011] Une autre technique utilise la gravure chimique.
Mais elle ne permet pas non plus d’avoir un rapport pro-
[0001] La présente invention se rapporte à un caloduc
comportant une ou plusieurs zones de circulation du flui-
à pompage capillaire à fonctionnement amélioré.