工艺检查记录表
印刷工艺检验记录表

印刷工艺检验记录表
1. 检验记录概要
本检验记录表用于记录印刷工艺的检验结果和评估,以确保印刷品的质量和符合要求。
以下是对每个检验项的详细记录。
2. 检验项一:色彩准确性
目标:
确保印刷品的色彩与原始设计一致
检验方法:
1. 与原始设计进行对比,检查印刷品的颜色是否准确。
2. 使用色彩校准仪器对印刷品进行测试,并与标准色彩进行比较。
结果:
- 印刷品的颜色与原始设计一致。
- 色彩校准仪器显示印刷品的色彩与标准色彩相符合。
3. 检验项二:印刷质量
目标:
评估印刷品的质量,包括清晰度、锐度和细节等方面。
检验方法:
1. 检查印刷品的清晰度和锐度,确保文字和图像清晰可辨认。
2. 检查印刷品的细节,包括线条和阴影等。
结果:
- 印刷品的清晰度和锐度良好,文字和图像清晰可辨认。
- 印刷品的细节处理仔细,线条和阴影处理得当。
4. 检验项三:印刷材料
目标:
检查印刷材料的质量和适用性。
检验方法:
1. 检查印刷材料的耐用性和耐久性。
2. 检查印刷材料的适用性,包括纸张质量、墨水和覆膜等。
结果:
- 印刷材料具有良好的耐用性和耐久性。
- 印刷材料的适用性符合要求,纸张质量、墨水和覆膜等均符
合标准要求。
5. 总结
以上为印刷工艺检验记录表的检验项和结果。
本表旨在保证印
刷品的质量和符合要求。
根据本次检验结果,印刷品的色彩准确性、印刷质量和印刷材料均符合要求,可投入使用。
拉丝工序工艺纪律检查记录表

5
产品外观工艺要求.
1、线盘外观排线不平整扣2分
2、压丝扣2分
3、碰伤扣1分
4、有毛刺扣2分
5、氧化不符合要求扣2分。
6
操作记录是否齐全
操作记录一项不全扣2分来自操作人员:合计得分:检查人员: 陪同人员:
拉丝工序工艺纪律检查记录表
检查日期: 生产机台: 生产人: 产品型号规格:
序号
工艺纪律检查内容
检查扣分标准
检查情况记录
单项扣分
1
现场工艺卡的要求
1、工艺卡随意涂改扣2分
2、使用无效工艺卡扣2分。
2
模具配比
1、不按要求配模扣1分
3
拉丝后工艺要求。
1、外径不在工艺内扣1分
2、外观不符合工艺要求扣2分
4
单丝接头工艺要求。
工艺质量检查记录表

工艺指令执行是否按要求落实
岗位操作记录是否按规定填写
交接班是否满足公司文件要求
看板管理是否及时更新
清洁生产是否满足文件要求
产
品
质
量
质量指标是否满足文件要求
产品包装及标识是否满足要求
产品重量是否满足文件要求
产品防护是否满足文件要求
产品存放是否满足文件要求
取样是否满足文件要求
检查人:
车间工艺质量检查记录表
岗位: 时间:
项目
检查内容
是
否
异常情况
整改措施及落实
原
料
原料是否充足
原料指标是否满足文件要求
包装、标识、重量是否满足要求
原料储存是否满足文件要求
生
产
过
程
岗位是否存放有效的作业文件
公用工程是否满足文件要求
设备状况是否满足文件要求
岗位员工是否按Leabharlann 件操作操作参数控制是否满足文件要求
工艺指标控制是否满足文件要求
工艺文件检查记录表
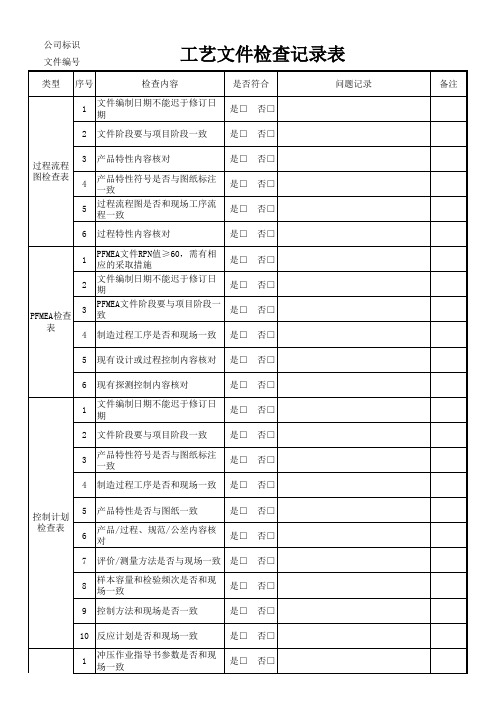
是□ 否□
2 文件阶段要与项目阶段一致 是□ 否□
3
产品特性符号是否与图纸标注 一致
是□ 否□
4 制造过程工序是否和现场一致 是□ 否□
控制计划 检查表
5 产品特性是否与图纸一致
6
产品/过程、规范/公差内容核 对
是□ 否□ 是□ 否□
7 评价/测量方法是否与现场一致 是□ 否□
8
样本容量和检验频次是否和现 场一致
11 控制要点是否对应控制计划 是□ 否□
12 特性是否和标注并和图纸一致 是□ 否□
四大文件 一致性检
查表
13
检测方法、检验频次、反应计 划是否和现场一致
1
重要特性和关键特性是否标注 并一致
2
控制计划和作业指导书过程参 数是否一致
3 工序号是否一致
4
检测方法、检验频次、反应计 划是否一致
5
控制计划与作业指导书产品特 性和过程特性内容是否一致
是□ 否□
9 控制方法和现场是否一致
是□ 否□
10 反应计划是否和现场一致
是□ 否□
1
冲压作业指导书参数是否和现 场一致
是□ 否□
备注
类型 序号
检查内容
是否符合
2
焊接作业指导书参数是否和现 场一致
3
装配作业指导书参数是否和现 场一致
4
涂装作业指导书参数是否和 场一致
5
操作内容、顺序是否与现场一 致
是□ 否□
1
PFMEA文件RPN值≥60,需有相 应的采取措施
是□ 否□
2
文件编制日期不能迟于修订日 期
是□ 否□
PFMEA检查
3
PFMEA文件阶段要与项目阶段一 致
工艺纪律检查记录表

冲压工艺纪律检查记录表检查时间检查时间 : 检查人:检查人: 序号序号考核项目考核项目分值分值 被检查者被检查者 得分得分 备注备注1 产品图样、工艺文件不齐全完好,作业指导书未悬挂现场2 2操作者不熟悉技术标准,不知道自已所在岗位、工序作业指导书的技术要求、检验要求等内容技术要求、检验要求等内容 33原始记录原始记录: :51. 记录填写不符合规定要求记录填写不符合规定要求,,漏项漏项2. 记录数据不真实记录数据不真实3. 字迹不清楚正确字迹不清楚正确4. 记录保存不完好记录保存不完好5. 无模具使用记录无模具使用记录4 是否严格按照设备维护保养规定进行设备的保养维护工作并如实填写记录填写记录35 是否严格按照工艺规定的检验频次进行检验并记录3 6 模具安装前未按规定对模具上、下模板及工作台面进行清理;压件前及压件过程中未按规程对模具进行检查清理和润滑;前及压件过程中未按规程对模具进行检查清理和润滑;压件后模具压件后模具清理不彻底,润滑不良,末件丢失。
2 7 野蛮操作,不注意保护冲件及模具,造成冲压件变形、磕碰划伤、脏污,模具部件损伤脏污,模具部件损伤5 8 在模具使用过程中出现的模具损坏情况,生产线没有事故记录,不及时将损坏情况上报及时将损坏情况上报3 9 模具出现严重磨损、定位不准、工件误差,带病运转,不及时上报 3 10 工位器具未定置摆放,产品件摆放超出,地面有产品件等不良情况 2 11 板材、毛坯料、冲压件有锈蚀、磕碰、脏、划伤、坑包或其它缺陷未修复转下序未修复转下序3 12 不认真执行首件、末件检验,未按有关程序交检。
2 13 首件首件//末件放置是否合适并有标识末件放置是否合适并有标识2 14 检验员对首件质量判定不及时有错检/错判错判//误判的情况误判的情况3 15 每批生产工序结束后操作者是否主动交检验员检查产品件 3 16 巡检员对转序件进行确认合格后是否在《产品追溯记录卡》上加盖自己的检验章,自己的检验章,2 17 压件时双料叠压,二次冲压,模具内压入异物等情况发生 5 18 检验过程中的抽检比例,检验方法是否符合要求5 19 生产过程发现质量异常应是否立即处理,并填写《产品异常通知单》,追查原因,并矫正及作成记录防止再发。
工艺检查记录表

检查结果:(主要问题点及整改)
内容 部门
问题描述
问题点 图片
1.熔铸车间配料 生产记录在做 假,记录全部是 A356的重量,实 际废轮也在加
2.5#熔炼炉气 氛温度要求500 ~1000℃,实际 46℃,铝水温度 仪表显示284 ℃,热电偶处陶 瓷已坏需更换
3.灭火器4月份 没有点检
责任人
完成日期
复查情况及 时间
扣款
已完成
4.打磨后清洗设 备点检卡记录不 及时,有些班都 很长时间没有记 录了
《设备操作 规程》的要
求
5.热水洗温度超 出工艺范围,要 求50~60℃,实 际显示76℃
《前处理作 业指导书》 操作内容第5
点前处理
1.以上检查不符合项各责任部门在5月2日前完成整改计划,并提交。 2.以上通报,希各相关部门引以为戒,踏踏实实做好每项工作,问题点及时整改。
工艺纪律检查通报
不符合 条款
《记录控制 程序》
纠正措施
责任人
完成日期
复查情况及 时间
扣款
没有整改
《投料配比 作业指导书 》操作内容 第4点温度控
制
已完成
《消防安全 规定》
已完成
第 1 页,共 5 页
内容 部门
问题描述
4.23#机生产的 5460 5#模没有 工艺卡和设备点 检卡
5.5#熔化炉打 印温度处合格证 已过期,需更换
检测 《X光检查作 业指导书》 操作内容第8 点产品叠放
(最高 1.7m)
第 2 页,共 5 页
没有整改
没有整改
水位是到了 ,但水需更
换太混了
已完成
内容 部门
问题描述
9.5#熔炼炉温 度记录打印纸4 月25日已打印 完,需更换
生产线工艺记录检查表
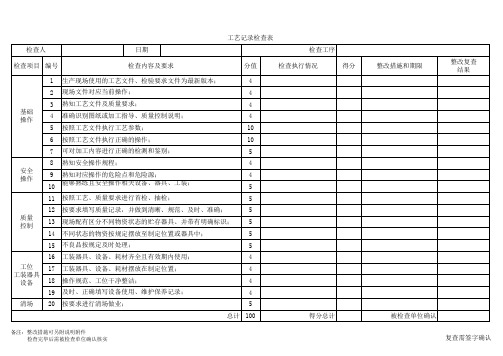
备注:整改措施可另附说明附件 检查完毕后需被检查单位确认核实
检查工序 检查执行情况 得分 整改措施和期限 整改复查 结果
得分总计
被检查单位确认 复查需签字
工艺纪律检查记录表

工程名称:XX项目
工序:作业(工艺)控制年月日
序号
检查项目及内容
检查记录
检查结果
备注
1
关键工序过程控制中吊装就位
1、锅炉基础检查、划线和垫铁安装工艺规程
2、钢架结构安装工艺规程
柱和梁吊装设备、吊装人员、指挥人员、安全措施等符合钢架结构安装工艺规程的要求
(现场吊装钢结构照片)
锅炉基础检查、划线和垫铁安装工艺规程的要求
(ห้องสมุดไป่ตู้场检查锅炉基础图片)
(锅炉基础划线图片)
2
关键工序过程控制中的焊接控
制之柱和梁的焊接
1、焊工管理,查焊工唐辉、朱继业、何平等
现场焊接的焊工已取得焊工项目,项目满足施得要求。
2、焊接材料控制
现场使用的焊条和焊丝已按焊材管理制度进行了验收、复验、保管、发放,现场使用前按要求进行
了烘烤;
(焊条保温桶使用时照片)
3、查现场的焊条烘箱、焊接设备、焊接工艺卡014SB-AZ-03钢结构焊接
现场使用的焊机状态正常,焊机上面的电流表、电压表经过检定合格,在有效使用期内;现场焊接钢梁使用的焊条及焊接参数符合焊接工艺卡的要求。
(现场焊机正常使用照片)
被检查班组责任人签字:检查人:
班组日常工艺检查表完整优秀版

班组日常工艺检查表完整优秀版1. 检查对象- 班组:(填写班组名称)- 日期:(填写检查日期)2. 工艺检查内容2.1 设备运行状况- 检查设备是否正常运行,并记录异常情况。
- 检查设备的润滑情况,是否需要进行维护保养。
- 检查设备的使用环境是否符合安全要求。
2.2 工艺参数检查- 检查关键工艺参数是否符合要求,如温度、压力、速度等。
- 检查参数调整记录,确认是否在规定范围内。
- 如有异常情况,记录并及时采取措施进行调整。
2.3 产品质量检查- 抽查产品进行质量检验,记录检验结果。
- 检查产品外观,是否存在缺陷、损坏等问题。
- 检查产品尺寸、重量等指标,确保符合标准要求。
2.4 作业场所安全- 检查作业场所的安全设施是否完善,如防护栏、警示标识等。
- 检查操作流程是否安全规范,是否存在安全隐患。
- 检查工作人员是否佩戴必要的安全装备。
3. 检查结果记录- 根据检查情况,记录每一项检查内容的结果,包括正常、异常等。
- 对于异常情况,需要详细描述,并提出改进意见和处理措施。
- 签字确认:检查人员、班组负责人。
4. 改进措施执行情况- 对于之前发现的异常情况,记录改进措施的执行情况。
- 若改进措施已执行并取得满意结果,进行确认并记录。
- 若改进措施未能有效执行,请说明原因并提出调整建议。
5. 检查表评审和修改记录- 评审人:(填写评审人姓名)- 日期:(填写评审日期)- 修改记录:(描述对检查表的修改内容及原因,若无修改可不填写)以上为班组日常工艺检查表的完整优秀版,用于检查和记录工艺过程中的关键要点和结果。
完成检查后,根据实际情况进行改进和调整,以提高工艺的稳定性和产品质量。
施工工艺检查记录表
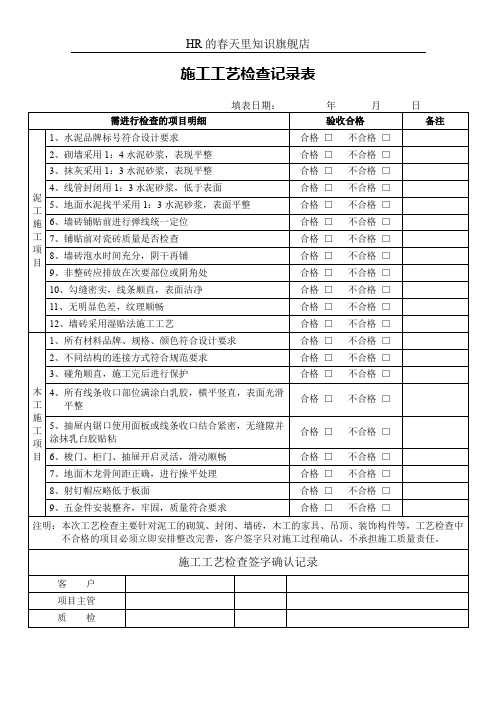
6、墙砖铺贴前进行弹线统一定位
合格□ 不合格 □
7、铺贴前对瓷砖质量是否检查
合格□ 不合格 □
8、墙砖泡水时间充分,阴干再铺
合格□ 不合格 □
9、非整砖应排放在次要部位或阴角处
合格□ 不合格 □
10、勾缝密实,线条顺直,表面洁净
合格□ 不合格 □
11、无明显色差,纹理顺畅
合格□ 不合格 □
12、墙砖采用湿贴法施工工艺
合格□ 不合格 □
木工施工项目
1、所有材料品牌、规格、颜色符合设计要求
合格□ 不合格 □
2、不同结构的连接方式符合规范要求
合格□ 不合格 □3、Fra bibliotek角顺直,施工完后进行保护
合格□ 不合格 □
4、所有线条收口部位满涂白乳胶,横平竖直,表面光滑
平整
合格□ 不合格 □
5、抽屉内锯口使用面板或线条收口结合紧密,无缝隙并涂抹乳白胶贴粘
合格□ 不合格 □
6、梭门、柜门、抽屉开启灵活,滑动顺畅
合格□ 不合格 □
7、地面木龙骨间距正确,进行操平处理
合格□ 不合格 □
8、射钉帽应略低于板面
合格□ 不合格 □
9、五金件安装整齐,牢固,质量符合要求
合格□ 不合格 □
注明:本次工艺检查主要针对泥工的砌筑、封闭、墙砖,木工的家具、吊顶、装饰构件等,工艺检查中
施工工艺检查记录
填表日期:年月日
需进行检查的项目明细
验收合格
备注
泥工施工项目
1、水泥品牌标号符合设计要求
合格□ 不合格 □
2、砌墙采用1:4水泥砂浆,表现平整
合格□ 不合格 □
3、抹灰采用1:3水泥砂浆,表现平整
工艺纪律检查记录表

涂装工艺纪律检查记录表
注:1、每工艺组每周与车间联查两次,要求车间联查人员确认签字。
2、每次检查前工艺组要先做好计划(包括检查工序及内容)。
3、要求检查考核项目中50%以上的项目,重点检查A、B类问题及生产中经常发生的问题。
4、要求车间对发现的问题填写纠正措施进行整改,并反馈工艺科,工艺组对上次改进问题进行审查验证,记录交综合组存档。
5、检查结果及时返给综合组归档,综合组针对四工艺组和四车间联查情况督促进行工艺考核,月底向人力资源部反馈工艺考核情况。
总装工艺纪律检查记录表
注:1、每工艺组每周与车间联查两次,要求车间联查人员确认签字。
2、每次检查前工艺组要先做好计划(包括检查工序及内容)。
3、要求检查考核项目中50%以上的项目,重点检查A、B类问题及生产中经常发生的问题。
4、要求车间对发现的问题填写纠正措施进行整改,并反馈工艺科,工艺组对上次改进问题进行审查验证,记录交综合组存档。
5、检查结果及时返给综合组归档,综合组针对四工艺组和四车间联查情况督促进行工艺考核,月底向人力资源部反馈工艺考核情况。
工艺检查记录表
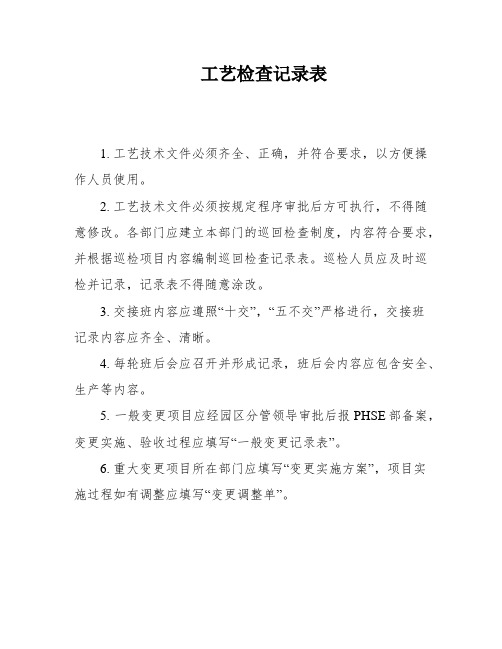
工艺检查记录表
1. 工艺技术文件必须齐全、正确,并符合要求,以方便操作人员使用。
2. 工艺技术文件必须按规定程序审批后方可执行,不得随意修改。
各部门应建立本部门的巡回检查制度,内容符合要求,并根据巡检项目内容编制巡回检查记录表。
巡检人员应及时巡检并记录,记录表不得随意涂改。
3. 交接班内容应遵照“十交”,“五不交”严格进行,交接班
记录内容应齐全、清晰。
4. 每轮班后会应召开并形成记录,班后会内容应包含安全、生产等内容。
5. 一般变更项目应经园区分管领导审批后报PHSE部备案,变更实施、验收过程应填写“一般变更记录表”。
6. 重大变更项目所在部门应填写“变更实施方案”,项目实施过程如有调整应填写“变更调整单”。
工艺执行情况检查记录表

Q-R-TD-048
④其它 巡查员
④其它
(聂艳云)
(聂艳云)
(皱硕)
焊接三
(聂艳云)
说明:违反项目打X,未违反打√,未生产打“-”,违反情况填写处理审批单,由违反者或班线长以上人员签名确认。 工艺巡查人员,一个礼拜须随机安排3天进行现场工艺监察(1天1次);
检查确认
③作业手法/工装使用
日期____________________ 巡查员 班组 工序 七轴机1 七轴机2 七轴机3 七轴机4 七轴机5 七轴机6 七轴机7 七轴机8 七轴机9 七轴机10 七轴机11 七轴机12 七轴机13 七轴机14 七轴机15 七轴机16 三维折角机1 三维折角机2 三维折角机3 三维折角机4 三维折角机5 双弯机 蛇簧生产线 手工成型 包装及其它 气动成型 ①工艺参数 ②点检自检
班组项目工序工艺参数点检自检作业手法工装使用其它巡查员班组工序工艺参数点检自检作业手法工装使用其它巡查员co2焊接七轴机1双工位点焊七轴机2手工焊接七轴机3专机点焊七轴机4分选校正七轴机5双工位点焊七轴机6分选校正七轴机7双工位点焊七轴机8co2焊接七轴机9分选校正七轴机10三轴点焊七轴机11分选校正七轴机12co2焊接工位1七轴机13co2焊接工位2七轴机14分选校正七轴机15co2焊接七轴机16分选校正三维折角机1co2焊接三维折角机2分选校正三维折角机3co2焊接三维折角机4分选校正三维折角机5co2焊接双弯机分选校正蛇簧生产线钣金件焊接手工成型13专机包装及其它23专机气动成型手工点焊分选校正缩管机co2焊接双弯机1分选涂油双弯机2三轴点焊单弯机分选校正80t冲床机器人点焊65t冲床分选校正40t冲床机器人点焊110t冲床分选校正200t冲床机器人点焊300t冲床小总成co2焊接300t油压总成co2焊接产品分选分选校正其它co2焊接七轴机17三轴点焊七轴机18分选校正七轴机19手工点焊七轴机20分选校正七轴机21co2焊接回火分选校正分选三轴点焊尼龙处理分选校正分选包装七轴点焊手工点焊分选校正co2焊接分选校正t3说明
涂装工艺检查记录表

6、硝基漆、聚酯色漆漆膜光滑、色泽一致
合格□ ቤተ መጻሕፍቲ ባይዱ合格 □
7、涂刷油漆不得对其他装饰物造成污染
合格□ 不合格 □
乳胶漆项目
1、乳胶漆材料必须符合设计要求
合格□ 不合格 □
2、基层平整,无污染,清理干净
合格□ 不合格 □
3、乳胶漆材料必须符合预算需要
合格□ 不合格 □
4、乳胶漆兑水量应符合产品说明书要求
涂装工艺检查记录
需进行检查的项目明细
验收合格
油漆项目
1、所有油漆材料必须符合预算需求
合格□ 不合格 □
2、钉眼、嵌缝应平整无凹陷或凸起、基本无色差
合格□ 不合格 □
3、每遍油漆后必须打磨平整,清理洁净
合格□ 不合格 □
4、不得有漏刷、流坠、疙瘩等缺陷
合格□ 不合格 □
5、清漆应均匀,漆膜光滑、丰满、无刷痕
合格□ 不合格 □
2、裱糊前应用专用材料封闭底面基层
合格□ 不合格 □
3、阳角处包角压实,阴角处允许顺光搭接
合格□ 不合格 □
4、拼图案花纹应吻合一致,阴阳角顺直
合格□ 不合格 □
5、墙纸与装饰线、线盒交接严密,中间无缝隙
合格□ 不合格 □
6、墙纸应粘贴牢固,表面平整,无气泡、裂缝、皱折、翘
合格□ 不合格 □
合格□ 不合格 □
5、每遍乳胶漆后必须打磨平整,清理洁净
合格□ 不合格 □
6、刷纹应通顺,分色线应通直
合格□ 不合格 □
7、表面不得有掉粉、起皮、透底、漏刷、泛碱、流坠、疙瘩等缺陷
合格□ 不合格 □
8、墙面应侧光或行灯检查应无明显波浪起伏
合格□ 不合格 □
工艺纪律检查记录表

序号
检查内容
1 工艺文件、生产图纸是否正确、完整,能有效指导生产
2
工艺文件是否按有关技术通知及时进行了更改、内容正确、手续齐全, 符合规定要求,版本是否受控。
3
工艺文件是否确定重要工序、特殊工序,其参数是否按要求进行了监控, 是否进行了质量记录。
4 工艺文件中质量要求、工艺参数、设备、工装等是否齐全。
11 工装满足工艺文件规定要求,保证精度和良好的状态。
12 生产用的计量测量器具测量能力适宜,状态良好,按规定使用、送检。
13 对工艺上有特殊要求的作用环境,应满足工艺文件要求,并做好监控记录。
14 是否建立原材料、外购件检验标准,是否按要求进行了检验并记录。
15 生产现场原材料、外购件、在产品存放、防护标示管理符合规定要求。
备注(整改日期)
5 是否按工艺文件要求进行操作,查工艺文件执行情况。
6 操作人员进行岗位培训,满足上岗要求,满足工艺文件要求。
7 特殊关键工序人员提供相关资格证明,持证上岗。
8 操作人员熟悉工艺文件内容,严格按照图纸执行。
9 操作人员按规定进行自检、互检工作,记录规精度和良好的性能,确保正常运行、安全、可靠,并有 日常维护、保养、检查记录,生产人员熟悉设备安全操作规程。
16 产品采用的代用材料是否符合审批手续。
17
新工艺、新技术、新材料和新装备必须经过验证合格后纳入工艺文件 方可正式使用。
18 操作人员发现不合格品、不稳定状态及时汇报。
19 生产现场做好定置管理,产品区域及状态标示符合规定,生产现场整洁有序。
检查人员:
检查记录
检查时间: 站 别:
责任部门/责任 人
不锈钢工艺检查表

切段
1、长度L0 -0.5。
2、 宽度B0 -0.5。
3、 切口平直、无毛刺。
符合要求
冲孔
1、 中心距L±0.1。
2、 孔直径D+0. 1 0。
3、零件摆放整齐。
4、 表面无缺口、无硌伤。
5、 毛刺高度小于0.06。
C03、H01、H11
切弧
1、 中心距C±0.5。
2、长度L0 -0.5。
3、 宽度B 0 -0.5。
Z01
芯子组装
1、 涂止焊剂成薄膜状 (浓度40%) 。
2、 按顺序叠件。
3、 夹紧力0.8- 1.0Mpa气压。
4、 中心距L±0.4。
符合要求
B01(续三)
(碳钢件) 焊前处理
1、除油液浓度3-5%、温度90- 100℃ 、 时间5-8分钟
2、 冲洗时间5-8分钟。
3、 酸洗液浓度盐酸10%、硫酸15%、时间5-8分钟。
2、除底片外,大小片一律使用冲孔焊料。
压边300中间起凸芯片没有用冲孔焊料
B03
45°合口
1、周边扳边均匀,无小片外露。
200芯片有2片小片外漏
B04
合口
1、 压边产品周边厚度≤1.25(大片焊料拉深) , ≤
2、 油压机油压17-20Mpa,保压5- 10秒。
3、 芯片厚度3.8±0. 1,但必须保证均匀度±0.05。
符合要求
总结人
日期:
期
3、平面度≤0.40。
4、 无硌伤、压伤、小片外露。
符合要求
P06、P15、P35、P42、P46
起凸
1、 中心距L±0.2。
2、 底圆直径D±0.5。
3、 顶圆直径D+0.5 0。