基于ANSYS的推力滚针轴承垫圈应力分析
基于ANSYS的轴承座的有限元分析

基于ANSYS的轴承座的有限元分析摘要:本文利用ANSYS14.0对轴承座的强度进行有限元分析。
通过三维实体建模,设置单元类型,设置材料参数,网格划分控制,施加载荷约束建立轴承座的有限元模型,然后对轴承座进行求解,得出应力,位移分布图和变形图,继而对其进行强度分析,找出结构最易破坏的地方。
最后的计算结果表明该轴承座符合强度设计要求。
关键词:有限元分析、轴承座1.引言轴承座可以为轴提供支撑,并且承受轴传递的各种载荷。
一个可靠的轴承座对于减轻轴的偏心振动,保证设备的正常性能具有重要作用。
但由于轴承座形状复杂,传统的解析法无法较为精确地计算其性能。
所以使用有限元分析软件ANSYS,对汽车上的某轴承座的承载特性进行有限元分析。
2.建立有限元模型该轴承座采用普通碳钢Q235,弹性模量E=2.01E11,泊松比u=0.3。
沉孔上受到径向推力为1000psi(6.89MPa),安装安装轴瓦的下表面受到向下作用力5000psi(34.45MPa)。
Q235的屈服极限为34808psi(240MPa)。
2.1在ANSYS14.0中建立三维实体模型在ANSYS中建立实体模型时,主要有自底向上和自顶向下两种方法。
根据该轴承的结构特点,采用自顶向下的建模方法,并且综合运用工作平面的平移、旋转,布尔运算,镜像等方法生成轴承座的实体模型。
模型的创建过程大致分为以下三步。
第一步进行基座的创建,如图1所示。
图1 轴承座基座第二步进行支撑部分的创建,如图2所示。
图2 轴承座支撑部分第三步进行肋板的创建,并且通过镜像完成轴承座三维实体的创建,见图3。
图3 轴承座三维模型2.2网格划分2.2.1设置单元类型在有限元分析过程中,对于不同的问题,需要应用不同的特性单元,所以选择合适的单元对于有限元分析非常重要。
在此我们选择Solid187单元,它是三维10节点四面体结构实体单元,每个四面体边的中点也是节点,其中每个节点具有3个自由度,具有空间的任意方向。
基于ANSYS的轴承座结构分析
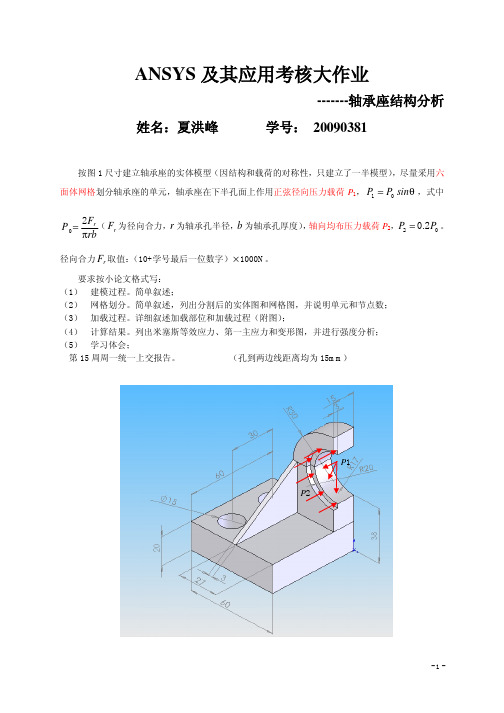
ANSYS 及其应用考核大作业-------轴承座结构分析姓名:夏洪峰 学号: 20090381按图1尺寸建立轴承座的实体模型(因结构和载荷的对称性,只建立了一半模型),尽量采用六面体网格划分轴承座的单元,轴承座在下半孔面上作用正弦径向压力载荷P 1,θsin P P 01=,式中rbF P rπ20=(r F 为径向合力,r 为轴承孔半径,b 为轴承孔厚度),轴向均布压力载荷P 2,200.2P P =。
径向合力r F 取值:(10+学号最后一位数字)×1000N 。
要求按小论文格式写: (1) 建模过程。
简单叙述;(2) 网格划分。
简单叙述,列出分割后的实体图和网格图,并说明单元和节点数; (3) 加载过程。
详细叙述加载部位和加载过程(附图);(4) 计算结果。
列出米塞斯等效应力、第一主应力和变形图,并进行强度分析; (5) 学习体会;第15周周一统一上交报告。
(孔到两边线距离均为15mm )P 1P 2一、有限元单元法与ANSYS简介有限元法是将连续体或结构先人为地分割成许多单元,并认为单元与单元之间只通过节点联结,力也只通过节点作用。
在此基础上,根据分片近似的思想,假定单元位移函数,利用力学原理推导建立每个单元的平衡方程组,再将所有单元的方程组,组织集成表示整个结构力学特性的代数方程组,并引入边界条件求解。
应用有限元法求解弹塑性问题的分析过程包括结构离散化、单元分析、整体分析和弓}入边界条件、求解方程四个步骤:ANSYS软件是由美国的John Swanson博士和Swanson分析系统公司(SASI)开发出的,一个功能强大灵活的、集设计分析及优化功能于一体的大型通用有限元软件包,它将有限元分析.计算机图学、可靠性技术和优化技术相结合,是融结构、热、流体、电磁、声学于一体,可广泛用于机械制造、航空航天、铁道、轻工,生物医学等的科学研究的大型通用商业软件。
ANSYS软件具有很强的硬件平台适应性,可以在PC机到巨型机的所有硬件平台上运行。
基于ANSYS WORKBENCH轴承的模态分析

基于ANSYS WORKBENCH轴承的模态分析1有限元模型的建立利用proe软件进行建模,可以从原件库里面直接调用,也可以重新建模,建模无需建立装配模型,只需要在单体零件中直接建立轴承内外圈和球体,选择不合并实体,从而形成多实体的单体零件。
轴承元件之间的间隙可以消除。
•三维模型的建立三维模型的建立是数值模拟分析中重要、关键的环节。
UG软件能够方便地建立复杂的三维模型,企业提供的初始的轴承三维模型主体钢结构是由不同厚度的钢板焊接而成,模型钢板之间存在较多的焊缝,导致模型存在不同大小的间隙,给后继有限元分析带来困难,而且模型结构复杂,且为三维实体,建立有限元模型的过程中,要在符合结构力学特性的前提下建立模型,有必要对结构做合理的简化。
其主要简化说明如下:(1).忽略零件中一些微小特征。
螺栓孔、倒圆角等一些微小的结构对结果准确性的影响很小,所以建模时不考虑这些微小几何图元;(2).所有焊接位置不允许出现裂缝、虚焊等工艺缺陷,认为在焊接位置材料是连续的,直接填充间隙;(3).轴承模型附件品种繁多,形状复杂,且对机架的刚度和强度影响不大,在计算模型中只要考虑其自重即可,例如料斗、辊子、走台、链板等其它辅助设备。
•材料属性结构用钢均采用Q235碳素结构钢材,Q235的弹性模量E=2.1e11N/m2,密度7830kg/m3,剪切模量为81000MPa,泊松比为0.3,模型材料为各向同性。
表1 材料Q235许用应力一览表: MPa (N/mm2)Tab.1 List of Material Q235 Allowable stress: MPa (N/mm2)40<t≤100215 143 83 162 93 179 103•网格划分有限元网格数目过少,容易产生畸变,并影响计算精度;而数目过大,不仅对提高精度作用不大,反而大大增加了计算工作量[2]。
因此网格划分前对模型进行了体切割与粘接布尔用算,再采用自由划分方式,以满足计算精度与控制计算量的要求。
基于ANSYS的滚针轴承的有限元分析
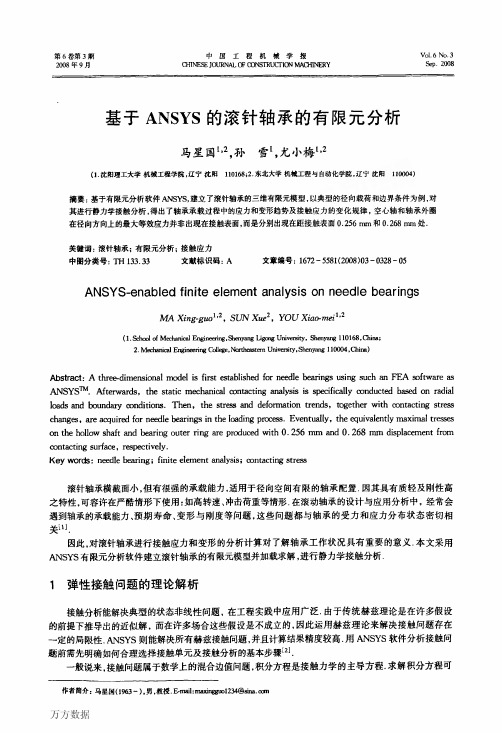
算,本文只考虑滚针与外圈和空心轴的接触情况。忽略滚针之间的互相接触,所以在柱坐标下将滚针进行
了,z方向的位移砜,以约束.
万方数据
中国工程机械学报
第6卷
2.3加载滚针轴承只承受径来自载荷,对空心轴的内表面加载,实际的
载荷是1个变化的值,底部最大,到边缘逐渐减小,基本满足如
下函数关系:Qi=Q1×sinO[6】,其中Q1为最大载荷,①为夹
受载荷,因此只建立下半圈模型进行分析.
选择的单元类型为Solid8node45,轴承材料的弹性模量E=206 GPa,泊松比/2=0.3,将接触区域的
网格细化,共有188 249个单元,398 765个节点.
、
2.2施加边界条件【5】5
将轴承外圈的外表面施加全约束,截面对称约束,对空心轴的端面z向的自由度进行约束.为简化计
3 8 2
罡
:
、
6●5
R
9
目
4
8
2
∞"弱强如”∞M毖%侉引限筋孙∞"船n盯纪瓶 7
7
2
9石2
9
罡
乏
6
\
2
R
翅
9
5
2
9
聊暑:Ⅲ捌琊硎粥拗蟒旧7●Ⅲ6●}眦置弘t 5
图10空心轴径向等效应力分布图
豫.10 Von Mises stress of the hollow shaft
图11外圈径向等效应力分布圈
outer她 rig.11 V抽Mises stress of the
3结论
(1)由计算可知最大的接触应力值为644 MPa,而材料的屈服极限是1 175 MPa,材料满足强度要求. (2)最大接触应力出现在滚针与空心轴的接触面上.滚针在接触面中心的接触应力最大,沿着远离接 触中心的方向,接触应力值逐渐减小到零,整个应力分布曲线呈抛物线状,这与赫兹弹性体接触理论的应 力分布规律是相同的. (3)滚针与空心轴接触时,在滚针的端部出现了“边缘效应”的现象,设计时应该设置减载槽,以消除 “边缘效应”.2端以外应力值分布相对比较均匀.滚针与外圈接触时,因有减载槽,没有在两端出现应力集 中的现象,相反应力值衰减为零. (4)空心轴和外圈在径向方向上的最大等效应力并非出现在接触表面,而是在距接触表面0.256 mm 和O.268 ITIITI处,
基于ANSYS的推力永磁轴承磁力特性研究

案 值为 0. 001 m。而相对磁环来说,空气和远场作为 E n 包络场,其对网格所要求的精度不高,故对其进行 A .c 自由网格划分,并设置面单元边长为 0. 002 m。
2. 3 加载求解
C g 在研究推力永磁轴承内部的磁场分布时,暂 r 不考虑其向外的漏磁,因此在模型最外层加上磁
凯 o 面重合时能产生较大的轴向力,而径向方向上的
不稳定力 较 小,适 合 做 斥 力 型 轴 向 轴 承。 故 文 中
e 以此类型永磁轴承单元作为基本结构组成一种推 O 力永磁轴承,其结构如图 2 所示,该轴承主要用于 CAwMwEw.cam 承受轴向载荷。
环对动磁环的磁力 Fz1 ( 方向向上) 相应增大,而动 磁环与上定 磁 环 间 的 气 隙 变 大,上 定 磁 环 对 动 磁
值。空气的相对磁导率设置为 1,磁环的材料则通
过设置 Hc 和 μr 来完成。由于磁环材料采用 N35
型 NdFeB,根据 实 验 室 所 定 制 的 磁 环 测 得: Hc =
922 880 A / m,Br = 1. 210 6 T。由 于 真 空 磁 导 率
μ0 = 4π × 10 - 7 H / m,故磁环的相对磁导率 μr = Br /
ISSN1000 - 3762 轴承 2014 年4 期 CN41 - 1148 / TH Bearing 2014 ,No. 4
5 -9
基于 ANSYS 的推力永磁轴承磁力特性研究
张坚,孙玉卓,张海龙,孟庆涛,张钢
( 上海大学 机电工程与自动化学院,上海 200072)
摘要: 对一种推力永磁轴承进行了力学特性分析,由于其只产生轴向位移且具有轴对称结构,故将其简化成轴
基于ANSYS的圆柱滚子轴承有限元应力分析

% % 在滚动轴承的设计与应用分析中, 经常会遇 到轴承的 承 载 能 力、 预 期 寿 命、 变形与刚度等问 题, 这些问题都与轴承的受力和应力分布状态密 切相关。 因此, 对滚动轴承的内外圈和滚动体进行应 力分析具有十分重要 的 意 义。本 文 采 用 !"#$# 有限元分析软件建立滚动轴承的有限元模型并加 载求解, 进行应力场分析, 得出应力场分布, 对生 产实际有一定的指导作用。
基于 !"#$# 的圆柱滚子轴承有限元应力分析
刘% 宁,张% 钢 ,高% 刚 ,赵志峰
( 上海大学% 机电工程与自动化学院, 上海% &’’’(& ) 将在 )* 中完成建模并装配好的轧机滚动轴承导入 摘要: 利用 )* 软件与 !"#$# 软件之间良好的数据接口, !"#$# 中, 对其进行接触应力分析, 得出内圈与轴过盈配合时应力的分布情况和内圈与滚子之间接触应力的分 布情况, 并与传统的理论分析所得结论进行比较, 证明有限元应力分析的正确性。 关键词: 圆柱滚子轴承; 有限元分析; 应力 中图分类号: +,-../ .. ; 0&1&/ &-% % % 文献标识码: 2% % % 文章编号: -’’’ 3 .(4& ( &’’4 ) -& 3 ’’’5 3 ’.
由分析结果可以看出, 在外载作用下, 234 569 787 应力等值线沿接触点的载荷作用线呈对称分 布, 最大 234 56787 应力在载荷作用线上。图 -$ 和图 -- 为基于理论公式, 利用 5:;<:= 编写程序计 算所得的受载最大的滚动 体 与 内 圈 接 触 表 面 下 234 56787 应力分布情况, 显然 ./010 分析结果与 理论计算结果是吻合的。根据位错能失效理论, 此时最大 234 56787 应力没有超过屈服极限, 轴承 是安全的。由此可见, 利用 ./010 软件分析代替 传统的理论分析是可行的。
安世亚太:基于ANSYS WB平台的滑动轴承分析工具(一)
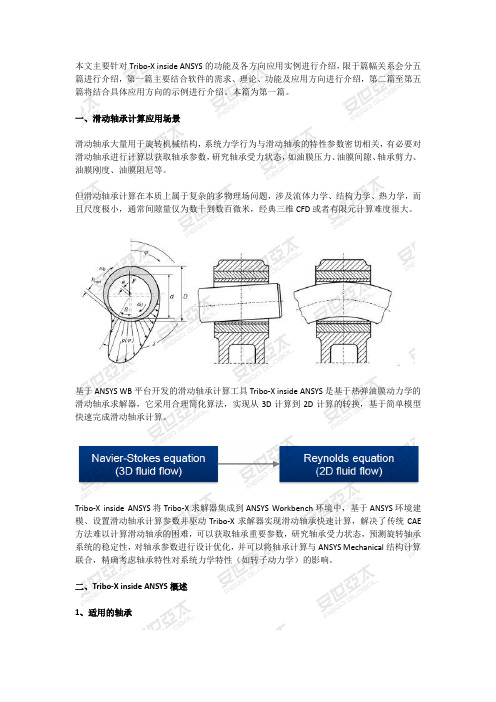
本文主要针对Tribo-X inside ANSYS的功能及各方向应用实例进行介绍,限于篇幅关系会分五篇进行介绍,第一篇主要结合软件的需求、理论、功能及应用方向进行介绍,第二篇至第五篇将结合具体应用方向的示例进行介绍。
本篇为第一篇。
一、滑动轴承计算应用场景滑动轴承大量用于旋转机械结构,系统力学行为与滑动轴承的特性参数密切相关,有必要对滑动轴承进行计算以获取轴承参数,研究轴承受力状态,如油膜压力、油膜间隙、轴承剪力、油膜刚度、油膜阻尼等。
但滑动轴承计算在本质上属于复杂的多物理场问题,涉及流体力学、结构力学、热力学,而且尺度极小,通常间隙量仅为数十到数百微米,经典三维CFD或者有限元计算难度很大。
基于ANSYS WB平台开发的滑动轴承计算工具Tribo-X inside ANSYS是基于热弹油膜动力学的滑动轴承求解器,它采用合理简化算法,实现从3D计算到2D计算的转换,基于简单模型快速完成滑动轴承计算。
Tribo-X inside ANSYS将Tribo-X求解器集成到ANSYS Workbench环境中,基于ANSYS环境建模、设置滑动轴承计算参数并驱动Tribo-X求解器实现滑动轴承快速计算,解决了传统CAE 方法难以计算滑动轴承的困难,可以获取轴承重要参数,研究轴承受力状态,预测旋转轴承系统的稳定性,对轴承参数进行设计优化,并可以将轴承计算与ANSYS Mechanical结构计算联合,精确考虑轴承特性对系统力学特性(如转子动力学)的影响。
二、Tribo-X inside ANSYS概述1、适用的轴承目前版本功能支持的滑动轴承类型如图所示:图-适用于TriboX-inside ANSYS进行分析的轴承(红线框内)2、合理假定油膜间隙远小于轴承尺寸厚度方向压力不变3、理论公式TriboX-inside ANSYS基于TEHD(热弹油膜动力学)的油膜轴承求解器,图-润滑方程图-三维NS方程(CFD)与二维雷诺方程(Tribo-X)计算结果对比●RDE与CFD计算结果存在微小偏差●RDE计算时间明显低于CFD的计算时间4、应用方向Tribo-X求解器集成在ANSYS Workbench环境中,二者优势互补。
基于ANSYS的推力滚针轴承垫圈应力分析
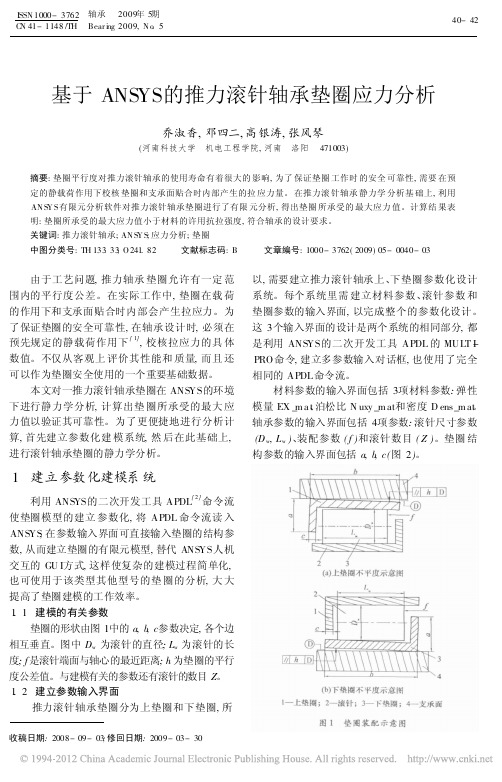
基于ANSYS的推力滚针轴承垫圈应力分析乔淑香,邓四二,高银涛,张风琴(河南科技大学机电工程学院,河南洛阳471003)摘要:垫圈平行度对推力滚针轴承的使用寿命有着很大的影响,为了保证垫圈工作时的安全可靠性,需要在预定的静载荷作用下校核垫圈和支承面贴合时内部产生的拉应力量。
在推力滚针轴承静力学分析基础上,利用AN S Y S有限元分析软件对推力滚针轴承垫圈进行了有限元分析,得出垫圈所承受的最大应力值。
计算结果表明:垫圈所承受的最大应力值小于材料的许用抗拉强度,符合轴承的设计要求。
关键词:推力滚针轴承;AN S Y S;应力分析;垫圈中图分类号:TH133.33;O241.82文献标志码:B文章编号:1000-3762(2009)05-0040-03由于工艺问题,推力轴承垫圈允许有一定范围内的平行度公差。
在实际工作中,垫圈在载荷的作用下和支承面贴合时内部会产生拉应力。
为了保证垫圈的安全可靠性,在轴承设计时,必须在预先规定的静载荷作用下[1],校核拉应力的具体数值。
不仅从客观上评价其性能和质量,而且还可以作为垫圈安全使用的一个重要基础数据。
本文对一推力滚针轴承垫圈在ANSYS的环境下进行静力学分析,计算出垫圈所承受的最大应力值以验证其可靠性。
为了更便捷地进行分析计算,首先建立参数化建模系统,然后在此基础上,进行滚针轴承垫圈的静力学分析。
1建立参数化建模系统利用ANSYS的二次开发工具APDL[2]命令流使垫圈模型的建立参数化,将APDL命令流读入ANSYS,在参数输入界面可直接输入垫圈的结构参数,从而建立垫圈的有限元模型,替代ANSYS人机交互的GU I方式,这样使复杂的建模过程简单化,也可使用于该类型其他型号的垫圈的分析,大大提高了垫圈建模的工作效率。
1.1建模的有关参数垫圈的形状由图1中的a,b,c参数决定,各个边相互垂直。
图中D w为滚针的直径;L w为滚针的长度;f是滚针端面与轴心的最近距离;h为垫圈的平行度公差值。
利用ANSYS软件分析滚动轴承接触问题_韦春翔
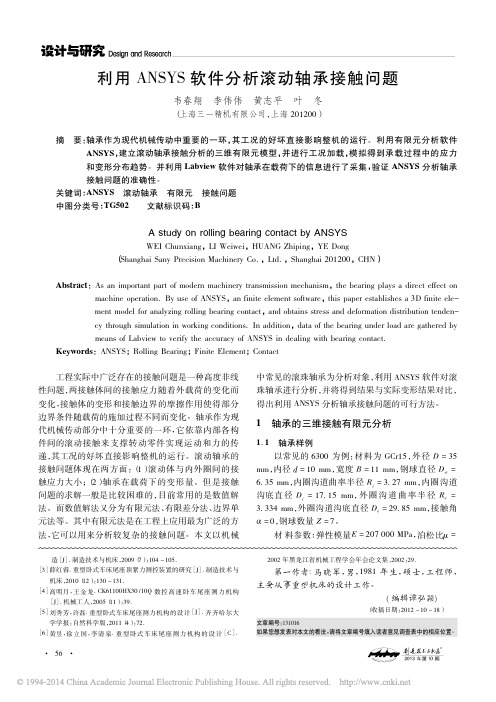
( 上海三一精机有限公司, 上海 201200 ) 摘 要: 轴承作为现代机械传动中重要的一环, 其工况的好坏直接影响整机的运行。 利用有限元分析软件 ANSYS, 建立滚动轴承接触分析的三维有限元模型 , 并进行工况加载, 模拟得到承载过程中的应力 和变形分布趋势。并利用 Labview 软件对轴承在载荷下的信息进行了采集 , 验证 ANSYS 分析轴承 接触问题的准确性。 关键词: ANSYS 滚动轴承 有限元 接触问题 文献标识码: B 中图分类号: TG502
施加在内部表面的轴向线的节点上 。 1. 6 有限元分析结果 ( 1 ) 显示结果 通过 ANSYS 后处理分析, 得到最大载荷作用下钢 球同内外圈的接触结果。 图 4 、 图 5 所示的分别是钢 球同内外圈的等效应力和模型的总变形 。模型的接触 应力如图 6 所示。 ( 2 ) 结果分析 从上面 ANSYS 进行有限元分析所得的结果可以 看出, 应力最大的地方发生在钢球与内圈接触处 , 这与 理论计算中预期的初始接触点一致 。从图 4 可以很清 楚地看出, 两个相同材料接触体内部的接触应力是不 同的, 外圈最大接触应力在与钢球接触的位置 , 最大应 力为 3 350. 8 MPa。而内圈最大应力发生在内圈滚道 边缘, 最大应力 P = 3 882. 6 MPa。 从图 5 得知, 内圈的接触变形为长轴 a = 1. 854 mm, 短轴 b = 0. 158 mm; 外圈的接触变形为 a = 1. 452 b = 0. 254 mm。 mm,
A study on rolling bearing contact by ANSYS
WEI Chunxiang,LI Weiwei,HUANG Zhiping,YE Dong ( Shanghai Sany Precision Machinery Co. ,Ltd. ,Shanghai 201200 ,CHN) Abstract: As an important part of modern machinery transmission mechanism,the bearing plays a direct effect on machine operation. By use of ANSYS,an finite element software,this paper establishes a 3D finite element model for analyzing rolling bearing contact,and obtains stress and deformation distribution tendency through simulation in working conditions. In addition,data of the bearing under load are gathered by means of Labview to verify the accuracy of ANSYS in dealing with bearing contact. Keywords: ANSYS; Rolling Bearing; Finite Element; Contact 工程实际中广泛存在的接触问题是一种高度非线 性问题, 两接触体间的接触应力随着外载荷的变化而 变化, 接触体的变形和接触边界的摩擦作用使得部分 边界条件随载荷的施加过程不同而变化 。轴承作为现 它依靠内部各构 代机械传动部分中十分重要的一环, 件间的滚动接触来支撑转动零件实现运动和力的传 递, 其工况的好坏直接影响整机的运行。 滚动轴承的 接触问题体现在两方面: ( 1 ) 滚动体与内外圈间的接 触应力大小; ( 2 ) 轴承在载荷下的变形量。 但是接触 问题的求解一般是比较困难的, 目前常用的是数值解 法。而数值解法又分为有限元法、 有限差分法、 边界单 元法等。其中有限元法是在工程上应用最为广泛的方 法, 它可以用来分析较复杂的接触问题。 本文以机械
ANSYS轴承分析

轴承座实体建模及静力学分析姓名:张健,学号:200901042033,班级:机设09-3班一:主要参数:图2中镗孔上的推力Pa和座孔向下的作用力Ps为Pa=1000+33=1033pa,Ps=5000+033=5033pa图1 轴承座实体结构图2 轴承座受载及约束情况二:关键操作步骤:1.实体建模:(1)建立长方体Main Menu>Preprocessor>Create>Block>By Dimensions输入x1=0,x2=3,y1=0,y2=1,z1=0,z2=3(2)平移旋转工作平面Utility Menu>WorkPlane>Offset WP by IncrementsX,Y,Z Offsets 输入2.25,1.25,.75 >ApplyXY,YZ,ZX Angles输入0,-90 >OK。
(3)创建圆柱体Main Menu>Preprocessor>Create>Cylinder> Solid Cylinder在Radius里输入0.375, Depth输入-1.5>OK。
然后生成另一个圆柱体Main Menu>Preprocessor>Copy>Volume拾取圆柱体>Apply, DZ输入1.5>OK (4)从长方体减去这两个圆柱体Main Menu >Preprocessor>Operate>Subtract Volumes先拾取被减的长方体,单击Apply,然后拾取减去的两个圆柱体>OK,再将工作平面与笛卡尔坐标系保持一致,Utility Menu>WorkPlane>Align WP with> Global Cartesian(5)创建支撑部分Main Menu>Preprocessor >Modeling>Create>Volumes-Block> By 2 corners & Z>输入数值:WP X = 0,WP Y = 1,Width = 1.5,Height = 1.75,Depth = 0.75>OK (6)再偏移工作平面Utility Menu> WorkPlane > Offset WP to > Keypoints + >拾取实体块的左上角作为关键点>OK(7)创建支架的上部Main Menu> Preprocessor > Modeling-Create > Volumes>Cylinder > Partial Cylinder+>输入参数:WP X = 0,WP Y = 0,Rad-1 = 0,Theta-1 = 0,Rad-2 = 1.5,Theta-2 = 90,Depth = -0.75>OK(8)在轴口位置建立圆柱体Main Menu:Preprocessor >Modeling>Create>Volume>Cylinder>Solid Cylinder +>输入参数:WP X = 0,WP Y = 0,Radius = 1,Depth = -0.1875>Apply再输入参数:WP X = 0,WP Y = 0,Radius = 0.85,Depth = -2>OK(9)去掉圆柱体形成轴孔.Main Menu: Preprocessor -> Modeling-Operate ->Subtract -> Volumes +>拾取构成支架的两个体>Apply>拾取大圆柱>Apply>拾取(8)中的两个体>Apply>拾取小圆柱体>OK>合并重合的关键点>Main Menu > Preprocessor > Numbering Ctrls > Merge Items >将Label 设置为Keypoints>OK(10)在底座的上部边缘线的中点建立关键点:Main Menu>Preprocessor > Modeling>Create > Keypoints > KP between KPs +>拾取两个关键点>OK>RATI = 0.5>OKMain Menu > Preprocessor > Modeling>Create >Areas>Arbitrary>Through KPs +>拾取孔座和基座的交点,拾取轴承孔上下两个体的交点,拾取基座中间的关键点>OK完成了三角形侧面,沿面的法向拖拉三角面形成一个三棱柱。
基于ANSYS的轴承座分析详解
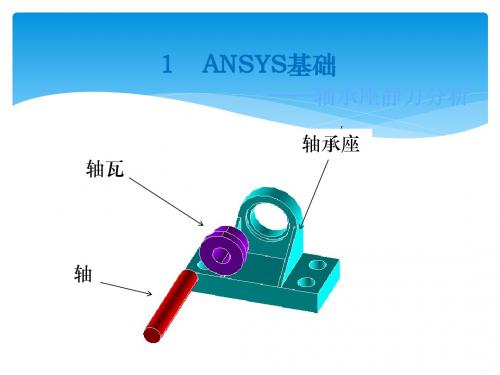
32
二、施加载荷并求解 1.定义单元类型
定义单元类型1为10-节点四面体实体结构单元 (SOLID92) Main Menu: Preprocessor > Element Type > Add/Edit/Delete ... (1)Add (2)选择 Structural-Solid, 并下拉菜单选择 “Tet 10Node 92”单击OK (3)Close
3
2 4
2
1
1
24
继续 Main Menu: Preprocessor>Modeling>Operate>Booleans>Subtr act >Volumes首先拾取1和2,点击Apply,然后拾取4 ,点击Apply。
25
(10)合并重合的关键点 Main Menu > Preprocessor > Numbering Ctrls>Merge Items 将Label 项 设置为 “Keypoints”, 单击 [OK]
39
7. 在轴承孔的下半部分施加径向压力载荷,这 个载荷是由于受重载的轴承受到支撑作用而产生 的。
Main Menu: Solution > Define Loads>Apply > Structural>Pressure >On Areas (1)拾取宽度为.1875” 的下面两个圆柱面 (2)OK (3)输入压力60e6 (4)OK Toolbar: SAVE_DB
1
ANSYS基础
——轴承座静力分析
轴承座
轴瓦
轴
1
静力分析 —主要用来分析由于稳态外载荷所 引起的系统或零部件的位移、应力、应变和 作用力。
基于ANSYS_LS_DYNA的滚动轴承仿真与分析

到。
( 2 ) 保持架的最大应力变化程度最大 , 说明保持架的应力
为了考虑摩擦的影响 , 将轴承实际的摩擦因数 、 润滑油和 挡边等模型综合考虑 , 建立了现有的摩擦因数 [ 4 ] , 相应数值的 设置见表 3。
表 3 接触模型中摩擦参数的取值 目标面 接触面 内圈外表面
fS = 0. 1 fD = 0. 05
2. 3 接触模型与载荷
由滚动轴承工作特点可知 , 在运动过程中 , 滚动轴承各部 件之间存在 3种接触 , 即滚动体与内圈外表面之间的接触 、 滚动 体与外圈内表面之间的接触及滚动体与保持架兜孔之间的接 触。 接触类型选择为普通的“ 面 -面” 接触 。 AN SYS/L S - D YNA 的接触摩擦基于库仑公式 , 摩擦因数 μ C 由式 ( 5 ) 给定 :
64 3. 2. 1 同一转速 、 不同外载荷接触应力分析
机 械 设 计
第 24 卷第 9 期
DYNA 下考虑摩擦条件的接触问题 , 成功实现了基于显式动力
由于后期实验装置能够施加的外力载荷大小有限 ,实例计 算中的外力取值主要考虑配合实验的情况 , 以便进行对比和验 证 。因此 ,外载荷分别取为 0. 5 kN , 1. 5 kN 和 2. 5 kN ,转速取为 4 000 r/m in。 在载荷施加过程中 ,外力载荷简化为轴承外圈的均布力形 式 ,按照程序要求施加以后 ,程序自动分解到有限元的节点上 , 通过接触的定义和计算传递到滚珠上 , 因此 , 没有以解析的方 式给出外力与单个滚珠受力的关系 。 如图 4 所示 ,等效应力值的分布情况用 3 种线型表示 ,横坐 标为等效应力值 , 纵坐标为出现的频率 。当载荷增加时 , 应力 分布曲线向右偏移且最大值随载荷的增大而增大 。说明随着 载荷的增加 ,滚动体在非承载区及承载区内的应力水平整体增 加。
基于ANSYS的轴承座有限元分析
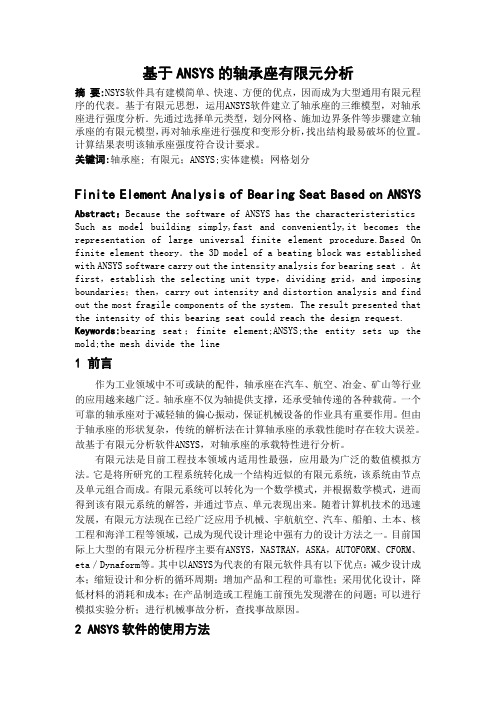
基于ANSYS的轴承座有限元分析摘要:NSYS软件具有建模简单、快速、方便的优点,因而成为大型通用有限元程序的代表。
基于有限元思想,运用ANSYS软件建立了轴承座的三维模型,对轴承座进行强度分析.先通过选择单元类型,划分网格、施加边界条件等步骤建立轴承座的有限元模型,再对轴承座进行强度和变形分析,找出结构最易破坏的位置。
计算结果表明该轴承座强度符合设计要求。
关键词:轴承座; 有限元;ANSYS;实体建模;网格划分Finite Element Analysis of Bearing Seat Based on ANSYSAbstract:Because the software of ANSYS has the characteristeristics Such as model building simply,fast and conveniently,it becomes the representation of large universal finite element procedure.Based On finite element theory.the 3D model of a beating block was established with ANSYS software carry out the intensity analysis for bearing seat .At first,establish the selecting unit type,dividing grid,and imposing boundaries;then,carry out intensity and distortion analysis and find out the most fragile components of the system.The result presented that the intensity of this bearing seat could reach the design request. Keywords:bearing seat;finite element;ANSYS;the entity sets up the mold;the mesh divide the line1 前言作为工业领域中不可或缺的配件,轴承座在汽车、航空、冶金、矿山等行业的应用越来越广泛。
基于ansys的轴承座强度分析
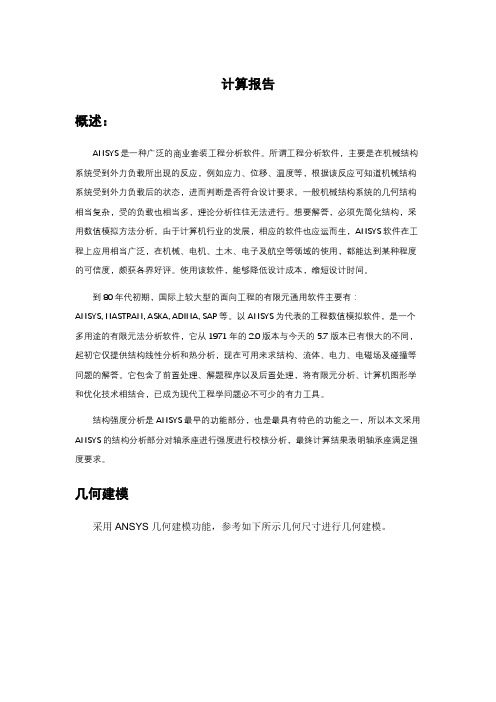
计算报告概述:ANSYS是一种广泛的商业套装工程分析软件。
所谓工程分析软件,主要是在机械结构系统受到外力负载所出现的反应,例如应力、位移、温度等,根据该反应可知道机械结构系统受到外力负载后的状态,进而判断是否符合设计要求。
一般机械结构系统的几何结构相当复杂,受的负载也相当多,理论分析往往无法进行。
想要解答,必须先简化结构,采用数值模拟方法分析。
由于计算机行业的发展,相应的软件也应运而生,ANSYS软件在工程上应用相当广泛,在机械、电机、土木、电子及航空等领域的使用,都能达到某种程度的可信度,颇获各界好评。
使用该软件,能够降低设计成本,缩短设计时间。
到80年代初期,国际上较大型的面向工程的有限元通用软件主要有:ANSYS, NASTRAN, ASKA, ADINA, SAP等。
以ANSYS为代表的工程数值模拟软件,是一个多用途的有限元法分析软件,它从1971年的2.0版本与今天的5.7版本已有很大的不同,起初它仅提供结构线性分析和热分析,现在可用来求结构、流体、电力、电磁场及碰撞等问题的解答。
它包含了前置处理、解题程序以及后置处理,将有限元分析、计算机图形学和优化技术相结合,已成为现代工程学问题必不可少的有力工具。
结构强度分析是ANSYS最早的功能部分,也是最具有特色的功能之一,所以本文采用ANSYS的结构分析部分对轴承座进行强度进行校核分析,最终计算结果表明轴承座满足强度要求。
几何建模采用ANSYS几何建模功能,参考如下所示几何尺寸进行几何建模。
图1 轴承座几何尺寸根据几何建模规则,首先建立轴承座初始模型,如图所示,首先在ANSYS 中建立轴承底座的长方体部分,同时在轴承地板上建立加强筋和轴承孔凸台。
图2 初始几何模型然后在上述模型的基础上进行孔和沉孔的建模,通过布尔运算中的Divide功能进行螺栓孔切割,和沉孔的切割,最终如下所示。
图3 添加螺栓孔和沉孔后几何模型在进行轴承座下法兰的模型建立,可以通过轴承座下底的面进行拉伸得到。
基于ANSYS WORKBENCH轴承的模态分析

基于ANSYS WORKBENCH轴承的模态分析1有限元模型的建立利用proe软件进行建模,可以从原件库里面直接调用,也可以重新建模,建模无需建立装配模型,只需要在单体零件中直接建立轴承内外圈和球体,选择不合并实体,从而形成多实体的单体零件。
轴承元件之间的间隙可以消除。
•三维模型的建立三维模型的建立是数值模拟分析中重要、关键的环节。
UG软件能够方便地建立复杂的三维模型,企业提供的初始的轴承三维模型主体钢结构是由不同厚度的钢板焊接而成,模型钢板之间存在较多的焊缝,导致模型存在不同大小的间隙,给后继有限元分析带来困难,而且模型结构复杂,且为三维实体,建立有限元模型的过程中,要在符合结构力学特性的前提下建立模型,有必要对结构做合理的简化。
其主要简化说明如下:(1).忽略零件中一些微小特征。
螺栓孔、倒圆角等一些微小的结构对结果准确性的影响很小,所以建模时不考虑这些微小几何图元;(2).所有焊接位置不允许出现裂缝、虚焊等工艺缺陷,认为在焊接位置材料是连续的,直接填充间隙;(3).轴承模型附件品种繁多,形状复杂,且对机架的刚度和强度影响不大,在计算模型中只要考虑其自重即可,例如料斗、辊子、走台、链板等其它辅助设备。
•材料属性结构用钢均采用Q235碳素结构钢材,Q235的弹性模量E=2.1e11N/m2,密度7830kg/m3,剪切模量为81000MPa,泊松比为0.3,模型材料为各向同性。
表1 材料Q235许用应力一览表: MPa (N/mm2)Tab.1 List of Material Q235 Allowable stress: MPa (N/mm2)40<t≤100215 143 83 162 93 179 103•网格划分有限元网格数目过少,容易产生畸变,并影响计算精度;而数目过大,不仅对提高精度作用不大,反而大大增加了计算工作量[2]。
因此网格划分前对模型进行了体切割与粘接布尔用算,再采用自由划分方式,以满足计算精度与控制计算量的要求。
ansys在轴承设计中的应用
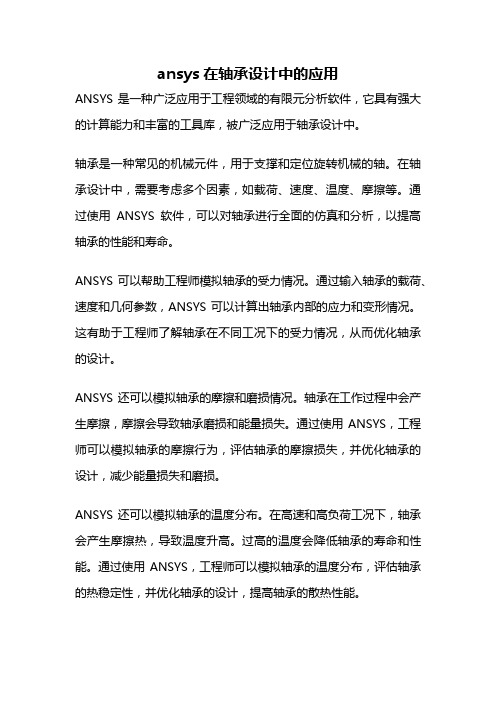
ansys在轴承设计中的应用ANSYS是一种广泛应用于工程领域的有限元分析软件,它具有强大的计算能力和丰富的工具库,被广泛应用于轴承设计中。
轴承是一种常见的机械元件,用于支撑和定位旋转机械的轴。
在轴承设计中,需要考虑多个因素,如载荷、速度、温度、摩擦等。
通过使用ANSYS软件,可以对轴承进行全面的仿真和分析,以提高轴承的性能和寿命。
ANSYS可以帮助工程师模拟轴承的受力情况。
通过输入轴承的载荷、速度和几何参数,ANSYS可以计算出轴承内部的应力和变形情况。
这有助于工程师了解轴承在不同工况下的受力情况,从而优化轴承的设计。
ANSYS还可以模拟轴承的摩擦和磨损情况。
轴承在工作过程中会产生摩擦,摩擦会导致轴承磨损和能量损失。
通过使用ANSYS,工程师可以模拟轴承的摩擦行为,评估轴承的摩擦损失,并优化轴承的设计,减少能量损失和磨损。
ANSYS还可以模拟轴承的温度分布。
在高速和高负荷工况下,轴承会产生摩擦热,导致温度升高。
过高的温度会降低轴承的寿命和性能。
通过使用ANSYS,工程师可以模拟轴承的温度分布,评估轴承的热稳定性,并优化轴承的设计,提高轴承的散热性能。
ANSYS还可以模拟轴承的动态响应。
在高速旋转和不平衡载荷的情况下,轴承会产生振动和噪声。
通过使用ANSYS,工程师可以模拟轴承的动态响应,评估轴承的振动和噪声水平,并优化轴承的设计,减少振动和噪声。
ANSYS在轴承设计中的应用非常广泛。
通过使用ANSYS,工程师可以对轴承进行全面的仿真和分析,以提高轴承的性能和寿命。
在未来,随着ANSYS软件功能的不断更新和完善,轴承设计也将进一步发展和创新。
基于ANSYS的推力滚子轴承接触分析
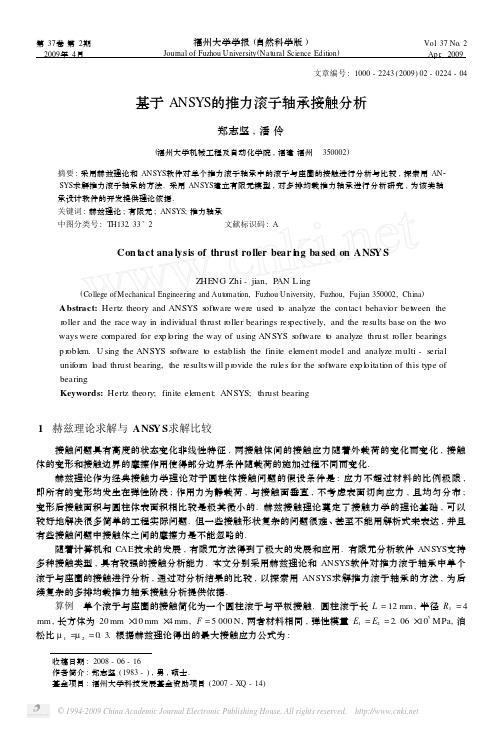
第37卷第2期2009年4月福州大学学报(自然科学版)Journal of Fuzhou University(Natural Science Editi on)Vol.37No.2Ap r.2009文章编号:1000-2243(2009)02-0224-04基于ANSYS的推力滚子轴承接触分析郑志坚,潘伶(福州大学机械工程及自动化学院,福建福州 350002)摘要:采用赫兹理论和ANSYS软件对单个推力滚子轴承中的滚子与座圈的接触进行分析与比较,探索用AN2SYS求解推力滚子轴承的方法.采用ANSYS建立有限元模型,对多排均载推力轴承进行分析研究,为该类轴承设计软件的开发提供理论依据.关键词:赫兹理论;有限元;ANSYS;推力轴承中图分类号:TH132.33+2 文献标识码:ACon t act ana lysis of thrust roller bear i n g ba sed on ANS Y SZ HE NG Zhi-jian,P AN L ing(College ofM echanical Engineering and Aut omati on,Fuzhou University,Fuzhou,Fujian350002,China) Abstract:Hertz theory and ANSYS s oft w are were used t o analyze the contact behavi or bet w een ther oller and the race way in individual thrust r oller bearings res pectively,and the results base on the t w oways were co mpared f or exp l oring the way of using ANSYS s oft w are t o analyze thrust r oller bearingsp r oble m.U sing the ANSYS s oft w are t o establish the finite ele ment model and analyze multi-serialunif or m l oad thrust bearing,the results will p r ovide the rules f or the s oft w are exp l oitati on of this type ofbearing.Keywords:Hertz theory;finite ele ment;ANSYS;thrust bearing1 赫兹理论求解与ANS Y S求解比较接触问题具有高度的状态变化非线性特征,两接触体间的接触应力随着外载荷的变化而变化,接触体的变形和接触边界的摩擦作用使得部分边界条件随载荷的施加过程不同而变化.赫兹理论作为经典接触力学理论对于圆柱体接触问题的假设条件是:应力不超过材料的比例极限,即所有的变形均发生在弹性阶段;作用力为静载荷,与接触面垂直,不考虑表面切向应力,且均匀分布;变形后接触面积与圆柱体表面积相比较是极其微小的.赫兹接触理论奠定了接触力学的理论基础,可以较好地解决很多简单的工程实际问题.但一些接触形状复杂的问题很难、甚至不能用解析式来表达,并且有些接触问题中接触体之间的摩擦力是不能忽略的.随着计算机和CAE技术的发展,有限元方法得到了极大的发展和应用.有限元分析软件ANSYS支持多种接触类型,具有较强的接触分析能力.本文分别采用赫兹理论和ANSYS软件对推力滚子轴承中单个滚子与座圈的接触进行分析,通过对分析结果的比较,以探索用ANSYS求解推力滚子轴承的方法,为后续复杂的多排均载推力轴承接触分析提供依据.算例 单个滚子与座圈的接触简化为一个圆柱滚子与平板接触.圆柱滚子长L=12mm,半径R1=4 mm,长方体为20mm×10mm×4mm,F=5000N,两者材料相同,弹性模量E1=E2=2.06×105MPa,泊松比μ1=μ2=0.3.根据赫兹理论得出的最大接触应力公式为:收稿日期:2008-06-16作者简介:郑志坚(1983-),男,硕士.基金项目:福州大学科技发展基金资助项目(2007-XQ-14)第2期郑志坚,等:基于ANSYS 的推力滚子轴承接触分析σH max =F πL 1/ρred 1-μ21E 1+1-μ22E 2其中:1ρred =1ρ1+1ρ2,ρ1、ρ2分别是两接触体的曲率半径,ρ1=R 1=4mm ,ρ2=∞,L 是接触长度,代入数据计算得σH max =1.923×103M Pa .采用ANSYS 分析时,有限元模型如图1.网格划分单元的选择是很重要的,ANSYS 提供了190多种不同的单元类型[1].选择S OL I D 45单元用于构造三维实体结构,单元通过8个节点来定义,每个节点有3个沿着x 、y 、z 方向平移的自由度,单元具有塑性、蠕变、膨胀、应力强化、大变形和大应变能力.选择CONT A174作为接触单元,对应选择T ARGE170作为目标单元,CONT A174单元具有8个节点,每个节点有沿x 、y 、z 方向平移的自由度,该单元与实体单元S OL I D 45具有相同的几何特征,位于其下的实体单元具有中间节点,因S OL I D 45没有中间节点,求解时放弃其中间节点.有限元网格划分质量和密度对有限元的计算精度影响较大,通常网格越细,单元形状越能够适应实体模型,所得出的计算结果精确度越高.但到一定程度后,网格的细化程度对精确度贡献比较低,而且计算成本高、计算时间长.所以在保证精确度的情况下,只对接触区进行局部网格细化,如图2.在平板的底面施加垂直方向的位移约束,并在圆柱滚子最上面母线上施加均布载荷.ANSYS 有限元接触分析结果表明最大接触应力为1.95×103MPa,与赫兹理论计算结果相比较,两者相对误差仅为1.4%,因此采用ANSYS 对该类轴承进行接触分析是符合工程实际的、可行的.2 推力滚子轴承ANSY S 求解多排均载推力滚子轴承是塑料双螺杆挤出机螺杆轴端专用推力轴承组件,其整体结构图及均载机理见参考文献[2].该类轴承的设计目标是在较小的径向空间内采用多排轴承来均匀分担巨大的轴向推力.由于受到当时计算机技术和制造水平等的限制,轴承各元件之间的接触、滚子形状、优化设计和软件开发等问题还有待进一步深入研究.以下是4排均载推力轴承的设计计算,其内径为22mm ,外径为32mm ,承受最大径向载荷为160kN.2.1 模型的建立和网格划分这类轴承组建模时,考虑到整个轴承组结构的循环对称性,每排轴承有13个滚子,为了节约计算时间,只需取整个结构实体的1/26进行分析,略去保持架[2].选择S OL I D 45单元对实体进行映射网格划分,并进行局部细化,总共划分成103360个网格单元,生成118332个节点,如图3.选择CONT A174和T ARGE170建立接触对,圆柱滚子与轴圈和座圈接触的地方都需设置接触对,内外垫圈与轴圈或座圈接触的地方也需设置接触对.・522・福州大学学报(自然科学版)第37卷2.2 载荷施加对轴承结构和装配特点进行分析[2],不计轴承组的自重,轴承系统内侧和外侧不加任何约束,在轴承最底下座圈施加轴向位移约束,并在各个对称截面上施加对称约束.各结构件之间动摩擦系数可在接触对的关键字里设置.所受载荷为轴向均布载荷,并施加在第一轴圈的上表面.2.3 求解和结果分析ANSYS 后处理功能非常强大,通过后处理可以得到各种数据和云图.经过ANSYS 分析计算,得到轴承应变图(图4).从图4可以看出,应变最大值出现在滚子和轴圈、座圈接触区域.图5是各排滚子的等效应力云图,第一~四排滚子的最大Von .M ises 应力分别是:1553、1764、1388、2236MPa .从图中可以看出,应力最大值都是出现在接触区域,第一、二、三排滚子与轴圈接触处等效应力分布比较均匀,第四排滚子的等效应力分布却是由里向外逐渐缩小.第一、二、三排滚子与座圈接触处等效应力分布区域基本相同,都是由里向外逐渐扩大,第四排却相反.图5 各排滚子的Von .M ises 等效应力云图Fig .5 Cont our chart of Von .M ises stress of every r oller各排滚子与轴圈、座圈接触应力值分别如图6、7所示,第一~第四排滚子的最大接触应力分别是:1835、2076、1678、2600MPa .与前文所得出的最大Von .M ises 应力相比较,可知最大接触应力大20%左右.从两图中可以看出,滚子与轴圈的接触在刚开始地方接触应力比其他地方明显偏高,第一、二、三排滚子与座圈在端部也出现了相同的情况,因为这里存在边界应力集中,即“边缘效应”.由图6可以看出,滚子与轴圈之间最大接触应力都出现在最里面,第一、二、三排滚子与轴圈的接触应力沿接触线分布比较均匀,而第四排下降趋势比较明显.从图7中可以看出,第一、二、三排滚子与座圈接触应力沿接触线逐渐增大,在端部达到最大,而第四排情况相反.这是由于第四轴圈比其他轴圈少了内垫圈支撑,受载后变形较大,缩短了接触线.从图中看出滚子与座圈接触应力变化较大,适当改变轴、座圈倾斜角度及合理设计滚子的形状和结构等,可以减小偏载,改善滚子受载状态,提高均载率.在ANSYS 后处理中,用户可以通过表面操作模块,映射节点结果数据到用户定义的表面上,然后可以对表面结果进行数学运算而获得集中力、横截面的平均应力、流体速率、通过任意界面的热流等.因此,通过表面操作,获取通过各内外垫圈的平均应力,进一步得出各排滚子所受载荷.通过不断的微调各内外垫圈的厚度,使得各排轴承所受载荷趋于相等.考虑轴承的加工和装配精度及薄壁垫圈的稳定性[2-3],当均载率大于95%时就可以停止.轴承受载情况如表1,均载率为95.68%,可以满足工程实际的要求.・622・第2期郑志坚,等:基于ANSYS的推力滚子轴承接触分析表1 各排轴承所受载荷与均载率Tab .1 The under load of each bear i n g and the ra te of the un i for m load排次F /N 占总载荷的比例/%均载率/%第一排4060325.38第二排3906224.41第三排3954624.72第四排4078925.4995.683 结语1)通过与赫兹理论计算结果比较,采用ANSYS 对推力滚子轴承进行接触分析是行之有效的.建立正确的有限元模型描述多排推力圆柱滚子轴承中各接触体之间力的传递以及接触状态的变化,可较好地模拟各接触面间的摩擦.2)用ANSYS 有限元法对多排推力轴承进行数值计算,得出的接触应力都比Von .M ises 应力大20%左右,表明轴承的失效主要是由接触应力过大造成,这与实际工程中滚动轴承失效情况一致.为以滚子接触应力均匀分布为目标对各轴圈、座圈、垫圈及滚子的结构进行优化设计提供必要的理论基础.3)各垫圈作为弹性支承,其尺寸对多排推力轴承均载率的影响非常敏感,通过调整各垫圈厚度可有效地提高轴承均载率,但工作量相当大.因此,开发多排推力轴承专用软件以简便、快速地设计不同尺寸、不同排数的轴承,方便一般工程技术人员使用是非常必要的.参考文献:[1]刘相新,孟宪颐.ANSYS 基础与应用教程[M ].北京:科学出版社,2006.[2]潘伶.多排均载推力轴承设计研究[J ].福州大学学报:自然科学版,1999,27(5):40-44.[3]潘伶.多排均载推力轴承中薄壁圆筒稳定性计算[J ].福州大学学报:自然科学版,2001,29(1):52-55.(责任编辑:杨青)・722・。
基于ANSYSWorkbench的轴承座分析计算

基于ANSYSWorkbench的轴承座分析计算
基于ANSYS Workbench的轴承座分析计算
杨天玲1 王想连2 姜土根2
【摘要】摘要轴承座是重要的轴承连接元件,利用ANSYS Workbench仿真平台,在设计基础上对轴承座结构进行有限元分析,验证模型结构设计的合理性及安全性。
【期刊名称】能源与环境
【年(卷),期】2013(000)002
【总页数】1
【关键词】关键词轴承座有限元安全
Workbench是ANSYS公司提出的协同仿真环境,解决企业产品研发过程中CAE软件的异构问题。
ANSYS仿真协同环境的目标是通过对产品研发流程中仿真环境的开发与实施,搭建一个具有自主知识产权的、集成多学科异构CAE 技术的仿真系统。
以产品数据管理PDM 为核心,组建一个基于网络的产品研制虚拟仿真团队,基于产品数字虚拟样机,实现产品研制的并行仿真和异地仿真。
所有与仿真工作相关的人、技术、数据在这个统一环境中协同工作,各类数据之间的交流、通讯和共享皆可在这个环境中完成。
在Workbench开发的应用程序中设置计算参数,如设计尺寸、工程材料或运行工况等,然后提交给求解器求解。
若用户对当前的设计方案不满意,可重新设置参数,再求解,直到对当前的设计方案满意为止。
本文针对主驱动轴承的轴承座结构,在设计基础上进行了有限元分析,验证了模型结构设计的合理性及安全性。
1 轴承座有限元模型的建立及材料确定。
- 1、下载文档前请自行甄别文档内容的完整性,平台不提供额外的编辑、内容补充、找答案等附加服务。
- 2、"仅部分预览"的文档,不可在线预览部分如存在完整性等问题,可反馈申请退款(可完整预览的文档不适用该条件!)。
- 3、如文档侵犯您的权益,请联系客服反馈,我们会尽快为您处理(人工客服工作时间:9:00-18:30)。
基于ANSYS的推力滚针轴承垫圈应力分析
乔淑香,邓四二,高银涛,张风琴
(河南科技大学机电工程学院,河南洛阳471003)
摘要:垫圈平行度对推力滚针轴承的使用寿命有着很大的影响,为了保证垫圈工作时的安全可靠性,需要在预定的静载荷作用下校核垫圈和支承面贴合时内部产生的拉应力量。
在推力滚针轴承静力学分析基础上,利用AN S Y S有限元分析软件对推力滚针轴承垫圈进行了有限元分析,得出垫圈所承受的最大应力值。
计算结果表明:垫圈所承受的最大应力值小于材料的许用抗拉强度,符合轴承的设计要求。
关键词:推力滚针轴承;AN S Y S;应力分析;垫圈
中图分类号:TH133.33;O241.82文献标志码:B文章编号:1000-3762(2009)05-0040-03
由于工艺问题,推力轴承垫圈允许有一定范围内的平行度公差。
在实际工作中,垫圈在载荷的作用下和支承面贴合时内部会产生拉应力。
为了保证垫圈的安全可靠性,在轴承设计时,必须在预先规定的静载荷作用下[1],校核拉应力的具体数值。
不仅从客观上评价其性能和质量,而且还可以作为垫圈安全使用的一个重要基础数据。
本文对一推力滚针轴承垫圈在ANSYS的环境下进行静力学分析,计算出垫圈所承受的最大应力值以验证其可靠性。
为了更便捷地进行分析计算,首先建立参数化建模系统,然后在此基础上,进行滚针轴承垫圈的静力学分析。
1建立参数化建模系统
利用ANSYS的二次开发工具APDL[2]命令流使垫圈模型的建立参数化,将APDL命令流读入ANSYS,在参数输入界面可直接输入垫圈的结构参数,从而建立垫圈的有限元模型,替代ANSYS人机交互的GU I方式,这样使复杂的建模过程简单化,也可使用于该类型其他型号的垫圈的分析,大大提高了垫圈建模的工作效率。
1.1建模的有关参数
垫圈的形状由图1中的a,b,c参数决定,各个边相互垂直。
图中D w为滚针的直径;L w为滚针的长度;f是滚针端面与轴心的最近距离;h为垫圈的平行度公差值。
与建模有关的参数还有滚针的数目Z。
1.2建立参数输入界面
推力滚针轴承垫圈分为上垫圈和下垫圈,所收稿日期:2008-09-03;修回日期:2009-03-30以,需要建立推力滚针轴承上、下垫圈参数化设计系统。
每个系统里需建立材料参数、滚针参数和垫圈参数的输入界面,以完成整个的参数化设计。
这3个输入界面的设计是两个系统的相同部分,都是利用ANSYS的二次开发工具APDL的MULT I-PRO命令,建立多参数输入对话框,也使用了完全相同的APDL命令流。
材料参数的输入界面包括3项材料参数:弹性模量EX_m a t、泊松比N uxy_m at和密度D ens_m at。
轴承参数的输入界面包括4项参数:滚针尺寸参数(D w,L w)、装配参数(f)和滚针数目(Z)。
垫圈结构参数的输入界面包括a,b,c(图2)。
ISSN1000-3762 C N41-1148/TH 轴承2009年5期
Bear i ng2009,N o.5
40-42
图2垫圈结构参数输入界面
1.3用APDL建立有限元模型
根据上面输入的各个参数,在ANSYS环境的工作平面上建立垫圈的实体模型。
定义轴承的径向(某滚针的中心线)为x轴,轴向为z轴,在AP-DL命令流里通过数学表达式计算垫圈上各个关键点的坐标值。
两个系统里的命令流从坐标值的计算开始不同,通过计算各关键点的坐标,建立垫圈的截面模型。
垫圈的结构符合周期对称的特点,在建立模型和求解时,只对一个基本扇区(整个模型的1/n, n为滚针数目)建模和分析,在后处理中再进行扩展,得到整个结构的结果。
因此,本系统设计中,用VROTAT命令将垫圈的截面模型绕z轴分别旋转180b/n和-180b/n,即得到一个基本扇区[3]的垫圈模型。
再通过VS W EEP对每个扇区进行网格划分。
2利用AN S Y S验证垫圈强度
本文所研究的推力滚针轴承的参数为:滚针直径D w为2.205mm;滚针的长度L w为4mm;滚针端面与轴心的最近距离f为17.6mm;滚针数目Z为24;承受的最大轴向载荷为2250N;垫圈材料为65M n,经830e淬火后,该材料的屈服极限为784M Pa,抗拉强度为980M Pa。
通过上述的参数化设计系统建立垫圈的有限元模型,并通过静力学分析验证该垫圈设计的强度可靠性[4]。
2.1建立垫圈的有限元模型
本文分析的垫圈形状尺寸如下:a为2.3mm, b为6.3mm,c为1mm。
推力垫圈材料65M n (65M n的弹性模量为200GPa、泊松比为0.3,密度为7810kg/c m3,淬硬处理,硬度为58~61HRC,热处理后不进行磨加工,抛光后直接作为成品。
由于工艺问题,轴承垫圈对其支承面允许有0.05 mm的平行度公差。
打开ANSYS用户界面,导入APDL命令流文件,在先后弹出的3个参数输入界面里分别输入材料参数、滚针参数和垫圈参数。
得到上、下垫圈的1/24有限元模型,如图3
所示。
图3垫圈模型
使用ANSYS前处理器里A rchive M odel的W rite及R ead功能,将上、下垫圈和滚针组合在一起,图4
是没有添加保持架的垫圈和滚针的模型。
图4组合模型
2.2施加边界条件
在上垫圈模型里,选择面A21,A25,A29及后
#
41
#
乔淑香等:基于AN S Y S的推力滚针轴承垫圈应力分析
侧面部分的A 8,A 12,A 16,用Define LOADS 里面的Sy mm e try B .C .定义对称边界条件。
然后定义端面A 7,A 9,A 20和A 22的所有位移约束。
下垫圈的边界约束方法与上垫圈相同。
在模型里建立垫圈与滚针之间的接触对,垫圈的接触面是目标表面,滚针的接触面是接触表面,图5
所示为垫圈与滚针的接触对。
图5 接触对
2.3 施加载荷、求解并查看结果
施加2250/24N 的载荷。
通过加载得到一个扇区的应力图,如图6所示。
建立局部柱坐标系Cy li n drica l 1,绕z 轴扩展,得到上垫圈和下垫圈整个结构的结果,如图7所示。
由图4、图5可知,上垫圈的最大应力值为457M Pa ,下垫圈的最大应力值为539MPa ,均小于65M n 材料的抗拉强度980MPa。
图6 垫圈1/24
模型的应力图
图7 垫圈整体模型的应力图
3 结论
(1)利用ANSYS 的二次开发工具APDL 的
MULTI PRO 命令,使垫圈模型的建立参数化。
将APDL 命令流读入ANSYS ,在参数输入界面可直接输入垫圈的结构参数,从而建立垫圈的有限元模型,替代ANSYS 人机交互的GU I 方式,大大提高了垫圈建模的工作效率。
(2)推力轴承垫圈允许有一定的平行度公差,在实际工作时,当垫圈在载荷的作用下和支承面贴合会在垫圈内部产生应力。
本文利用ANSYS 有限元分析软件,在预先规定的静载荷2250N 的作用下,计算出上垫圈最大拉应力为457M Pa ,下垫圈最大拉应力为539MPa ,均小于材料的抗拉强度980M Pa ,为垫圈的设计提供了一个重要基础数据。
参考文献:
[1] 马俊华.输油管线泵轴承用的蝶形垫圈的静载荷变
形试验[J].沈阳:水泵技术,2000(1):44-45.[2] 博弈创作室.APDL 参数化有限元分析技术及其应用
实例[M ].北京:中国水利水电出版社,2004.[3] 王庆五,左昉,胡人喜,等.AN S Y S10.0机械设计高
级应用实例[M ].北京:机械工业出版社,2006.[4] 刘宁,张钢,高刚,等.基于AN S Y S 的圆柱滚子轴承
有限元应力分析[J].轴承,2006(12):8-10.
(编辑:赵金库)
#42#5轴承62009.l .5。