作业排程知识概述
生产计划与管理-作业排程

生产计划与管理-作业排程在现代工业生产中,生产计划与管理是至关重要的环节。
作业排程作为生产计划与管理的一部分,扮演着关键的角色。
本文将介绍生产计划与管理中的作业排程,并讨论其重要性及应用。
一、作业排程的定义作业排程是指根据生产计划,对各项作业进行时间和资源的安排,以满足生产需求。
它是在充分考虑资源利用率和工期要求的前提下,合理分配生产任务,使生产过程高效运行的过程。
二、作业排程的重要性1. 实现顺畅生产:作业排程的主要目标是保证生产过程的连续性和顺畅性。
通过合理安排作业顺序和时间,可以减少生产中的等待时间和瓶颈,提高生产效率。
2. 最大限度利用资源:作业排程能够帮助企业合理分配资源,避免资源的浪费和闲置。
通过充分利用设备、人力和原材料,可以降低单位产品成本,提高企业竞争力。
3. 提高客户满意度:作业排程的合理安排能够保证按时交付产品,提高客户满意度。
及时交付产品意味着企业可以更好地满足市场需求,增强客户忠诚度。
三、作业排程的应用1. 传统制造业:在传统制造业中,作业排程被广泛应用于生产车间的运作。
通过合理安排生产任务的先后顺序、时间和资源的利用,可以提高生产效率,减少工艺各环节的等待和停滞。
2. 服务业:作业排程不仅适用于制造业,也可以在服务业中应用。
比如,医院可以利用作业排程来安排手术、检查和病房的使用,提高医疗资源的利用率,缩短患者等待时间。
3. 项目管理:在项目管理中,作业排程被用于确定项目任务的时间、资源和人员分配等方面。
通过合理的作业排程,可以提高项目进度控制的精确性,降低项目风险。
四、作业排程的方法1. 先来先服务法(FIFO):按照作业提交的顺序进行排程,先提交的作业先执行。
这种方法简单易行,但对于优先级较高的紧急任务,可能无法及时响应。
2. 最短作业优先法(SJF):选择执行时间最短的作业先执行。
这种方法能够最大限度地减少等待时间,提高生产效率,但容易忽略其他因素如资源限制和工期要求。
作业排序是什么意思?作业排序的优先规则?

作业排序是什么意思?作业排序的优先规则?1)作业排序的概念作业排序(Sequencing)是指为每台设备、每位员工详细确定每天的工作任务和工作挨次的过程。
也就是说,作业排序要解决不同工件在同一设备上的加工挨次问题、不同工件在整个生产过程中的加工挨次问题,以及设备和员工等资源的安排问题。
作业排序与作业方案(Scheduling)是有区分的。
一般来说,作业排序只是确定工件在机器设备上的加工挨次,而作业方案则不仅要确定工件的加工挨次,还要确定机器设备加工每个工件的开头时间和完成时间。
因此,在实际生产中,指导工人的生产活动的是作业方案。
但由于作业方案的主要问题在于确定工件在各工作地的加工挨次,一般状况下,作业方案都是以最早可能开工时间和完工时间来编制的,因此,一旦工件的作业排序确定之后,作业方案自然也就确定了。
所以,在大多数生产与运营管理教科书中,一般对“排序”和“作业方案”是不加以严格区分的。
作业排序需要解决“设备”与“工作”之间的关系,归纳起来,也就是“服务者”与“服务对象”之间的关系。
作业排序对于提高整个加工过程或服务过程的效率,缩短工件或客户的等待时间是至关重要的。
不同的作业排序,可能会导致差别很大的结果。
生产排程的效益和作用有以下4点:①经由排程可以明确取得各待产料品的用料数量和需求日期,选购部门可以轻松且更经济(可汇合各待产料品的需求量,以大批量来压低选购价格)地支配选购事宜。
②经由排程可以明确取得各待产料品、各制程的开工时间,如需委外产制,将有充裕的时间接洽支配委外产制事宜。
③排程之后可执行生产方案排程和分析产能利用率,了解产能的供需状况,先期发觉产能瓶颈并筹谋对策;另可供应业务接单时交期和价格的明确参考,使公司获得最大收益。
④排程之后可参考生产方案/排程和分析/甘特图(制程)、甘特图(制站)的分析数据预先妥当支配人力需求。
2)作业排序的优先规章(1)作业排序规章在生产过程中经常可能会消失两种状况:工件等待和机器空闲。
车间作业计划与作业排程

车间作业计划与作业排程1. 背景介绍随着生产规模的扩大和生产流程的复杂化,现代制造业中的车间作业计划和作业排程变得越来越重要。
车间作业计划是根据订单需求和生产资源的可用性,制定车间内每一道工序的计划,确保生产按时交付。
作业排程则是根据车间内工序之间的关系,合理安排各个工序的进行顺序,以最小化生产时间和成本。
本文将介绍车间作业计划和作业排程的基本概念、常见方法和实施步骤,帮助读者了解如何有效管理和优化生产过程。
2. 车间作业计划车间作业计划是根据订单需求和生产资源的情况,制定车间内每一道工序的计划,以达到按时交付产品的目标。
车间作业计划需要考虑以下几个因素:2.1 订单需求首先,根据销售订单和客户需求,确定需要生产的产品种类、数量和交付日期。
这是车间作业计划的基础。
2.2 生产资源接下来,评估车间可利用的生产资源,包括设备、人力和原材料。
了解资源的可用性和瓶颈将有助于合理安排生产计划。
必要时,可以通过增加生产能力或调整生产工艺来满足订单需求。
2.3 工序流程针对每个产品,确定其需要经过的工序流程。
这包括制定每道工序的工时和工艺要求,以及确定各工序之间的依赖关系。
2.4 任务分配根据订单需求和生产资源情况,将任务分配给不同的工人和设备。
任务分配应考虑每个工人和设备的熟练程度、产能和可用性。
2.5 交付日期和实时调整确定最终的交付日期,并建立相应的计划和时间表。
同时,需要灵活调整计划,以应对生产过程中的变化和突发情况。
3. 作业排程作业排程是根据车间内工序之间的关系,合理安排各个工序的进行顺序,以最小化生产时间和成本。
3.1 工序间关系首先,通过分析工序之间的制约关系,确定各个工序之间的先后顺序。
例如,某些工序必须在其他工序完成后才能开始,而其他工序可以并行进行。
3.2 排程算法根据车间内工序的数量和复杂性,选择合适的排程算法。
常见的排程算法包括作业车间调度规则、遗传算法和模拟退火算法等,这些算法可以根据不同的情况进行组合使用。
生产计划与管理之作业排程

多任务优先级问题及解决方法
常见问题:多个任务同时进行,无法确定优先级,导致任务延误或资源浪 费
解决方法:根据任务的紧急程度、重要性、资源需求等因素,制定合理的 优先级排序,确保关键任务优先完成
实施步骤:明确任务目标、评估任务优先级、制定任务计划、监控任务进 度、调整任务优先级
注意事项:避免过度分配资源,确保任务之间的协调与平衡,及时调整计 划以适应变化
个性化定制需求:满足客户的个性化定制 需求,提高生产计划的柔性和精细化程度, 提高生产效率和产品质量
供应链协同管理:加强与供应商、分销 商等合作伙伴的协同管理,实现信息共 享和资源优化配置,提高供应链的响应 速度和灵活性
培训员工:通过培训提高员工对作业排程 计划实施流程的认识和技能水平,促进员 工积极参与和改进工作。
资源冲突问题及解决方法
资源冲突问题:不 同工序同时使用同 一资源,导致资源 分配不均
解决方法:采用优 先级规则、设置等 待时间、使用缓冲 区等措施进行优化
考虑因素:生产节 拍、设备利用率、 生产成本等
作业排程定义及 重要性
作业排程计划制 定流程
作业排程常见问 题及解决方法
作业排程基本原 则和目标
作业排程计划实 施步骤
作业排程未来发 展趋势和挑战
作业排程定义
添加标题 添加标题
定义:作业排程是将生产计划中的任务按照交货期、优先级、资源等因素进行合理安排,以确 保生产顺利进行的过程。
重要性:作业排程是生产计划与管理的核心环节,它直接影响到生产效率、交货期和产品质量。 通过合理的作业排程,可以降低生产成本、提高生产效率,并确保按时交付产品。
监控和调整计划
监控计划实施过程
及时发现偏差
分析原因并采取措施
生产作业计划与作业排序概论

生产作业计划与作业排序概论生产作业计划和作业排序是生产管理中非常重要的环节,通过合理的计划和排序,可以提高生产效率,降低生产成本,保证产品质量,确保生产进度的顺利进行。
在现代化的生产管理中,生产作业计划和作业排序已经成为不可或缺的一部分。
本文将介绍生产作业计划和作业排序的概念、意义和方法。
生产作业计划的概念和意义生产作业计划是根据生产需求和资源情况,合理安排生产活动的时间、顺序、数量和方法的过程。
通过制定生产计划,可以有效地安排生产活动,使生产过程有序、高效。
生产作业计划的主要目的是保证生产进度的准时、产品质量的稳定和生产成本的最低化。
生产作业计划的意义在于:1.提高生产效率:通过合理的计划,可以提高生产效率,减少空转时间和不必要的等待时间,充分利用生产资源。
2.降低生产成本:通过合理的计划,可以避免资源浪费和重复投入,降低生产成本,提高企业的竞争力。
3.保证产品质量:通过合理的计划,可以确保生产过程中每个环节都按照要求进行,从而保证产品质量稳定。
4.确保生产进度:通过合理的计划,可以提前安排生产活动,确保生产进度的顺利进行,避免延误和返工。
生产作业排序的概念和意义生产作业排序是根据生产作业的性质、优先级和资源限制等因素,合理安排生产作业的顺序和时间的过程。
通过作业排序,可以使生产作业有序、高效地进行,保证生产计划的顺利执行。
生产作业排序的主要目的是提高生产效率、缩短生产周期、降低生产成本。
生产作业排序的意义在于:1.提高生产效率:通过合理的排序,可以减少作业之间的等待时间和传送时间,提高生产效率。
2.缩短生产周期:通过合理的排序,可以优化生产流程,减少生产周期,提高产品的市场竞争力。
3.降低生产成本:通过合理的排序,可以减少不必要的资源浪费和生产停顿,降低生产成本。
4.提高生产计划执行的准确性:通过合理的排序,可以保证生产计划的准时、准确执行,确保产品的交付周期。
生产作业计划和作业排序的方法生产作业计划和作业排序的方法有很多种,根据不同的生产环境和要求,可以采用不同的方法。
车间作业计划与作业排程

车间作业计划与作业排程引言在车间生产中,合理的作业计划和作业排程是保证生产效率和产品质量的关键。
良好的作业计划能够帮助车间合理安排生产任务,有效利用资源,减少生产返工和浪费。
作业排程则能够合理安排生产顺序,确保生产任务按时完成。
本文将介绍车间作业计划和作业排程的概念、重要性以及常用的方法和工具。
一、车间作业计划的概念车间作业计划是根据客户需求和生产资源的状况,合理安排生产任务的过程。
作业计划的目标是通过合理的任务安排,提高生产效率、降低成本、保证产品质量,以满足客户需求。
二、车间作业计划的重要性1.提高生产效率:作业计划可以合理安排生产任务的先后顺序,减少生产中的等待时间,提高生产效率。
2.优化资源利用:作业计划可以根据生产资源的实际情况,合理安排任务,最大程度地利用资源,减少浪费。
3.提前预警:通过作业计划,可以提前了解生产任务的需求和准备工作,及时做好准备,避免生产延误和产能瓶颈。
4.降低返工率:合理的作业计划可以避免生产任务的冲突和交叉干扰,减少因错误操作导致的返工率。
三、车间作业计划的方法和工具1.生产任务单:生产任务单是车间作业计划中常用的工具,它包括任务名称、任务描述、任务负责人、任务开始和结束时间等信息,帮助车间明确任务目标和任务执行情况。
2.Gantt图:Gantt图是一种常用的作业计划工具,它以时间为横轴,显示任务的开始和结束时间,通过条形图的长度和位置展示任务进度和关系,方便车间进行任务安排和跟踪。
3.生产计划软件:一些专门的生产计划软件,如SAP、Oracle等,可以根据生产规则和资源约束,自动生成合理的作业计划,并实时跟踪任务的执行情况。
4.人工经验:车间管理人员可以根据自己的经验和对生产过程的了解,制定合理的作业计划。
四、车间作业排程的概念车间作业排程是指根据作业计划和生产需求,按照一定的规则和约束条件,合理安排生产任务的顺序和时间。
作业排程的目标是最大化生产效率,保证生产任务按时完成。
怎样做好生产作业排程

评估人员能力:评估 员工技能和生产能力
评估物料供应:评估 物料库存和供应能力
评估生产环境:评估 生产环境和安全条件
评估生产成本:评估 生产成本和利润空间
制定排程计划
确定生产目标:明确生产任务、产量、质量等要求 收集生产信息:了解生产设备、原材料、人力资源等状况 制定排程方案:根据生产信息制定合理的排程计划 优化排程方案:根据实际情况对排程方案进行调整和优化 实施排程计划:按照排程计划进行生产作业,确保生产顺利进行
生产调度:根据生产计划进行 生产调度,包括生产任务分配、
生产进度监控等
信息化管理:利用计算机技 术进行生产作业排程的管理
生产监控:对生产过程进行监 控,包括生产进度、生产质量、
生产成本等
生产作业排程的未来发展趋势
智能化:利用AI技术进行生产排程 优化,提高生产效率
柔性化:适应市场需求变化,快速 调整生产计划和排程
优先级策略
紧急程度:根据任 务的紧急程度进行 排序
重要程度:根据任 务的重要程度进行 排序
资源分配:根据资 源的分配情况进行 排序
时间限制:根据任 务的时间限制进行 排序
负荷平衡策略
目的:确保生产线的负荷平衡,避免过度负荷或闲置 方法:根据订单数量、生产周期、设备能力等因素,合理安排生产任务 优势:提高生产效率,减少浪费,降低成本 注意事项:需要实时监控生产线的负荷情况,及时调整生产计划
生产作业排程
目录
生产作业排程的基本概念 生产作业排程的流程 生产作业排程的策略 生产作业排程的优化方法 生产作业排程的实践应用
生产作业排程的定义
生产作业排程是指在生产过程中,根据生产计划、物料供应、设备状况等因素,合理 安排生产作业的顺序和时间,以实现生产效率最大化。
生产计划与管理-作业排程

前言 作业排程的基本概念 作业排程的特征与限制 单机排程问题 平行机台排程问题 流线型生产之排程问题 零工型生产之排程问题 前推与后推排程问题 人员排程问题 结语
前言
系统安装设置(installation)专案 半导体制造工厂 汽车组装生产线
汽车租赁保留(reservation)系统 医院中的护士排班问题
工作i
1 2 3 4 5 6 7 8 9 10
作业时间
5 6 3 8 7 2 3 5 4 2
交期
8 9 14 12 11 5 8 10 15 7
機台3
1
5
機台2 10
2
機台1 6
7
8
9 4 3
2 4 6 8 10 12 14 16 18
7-23
降低延迟工件数目
在探讨单机排程时,我们发现Hodgson方法可 使延迟件数最小,现在依此方法应用到平行机 台排程上。
决定工作之处理顺序(sequencing)
7-3
作业排程的基本概念1/2
负荷安排
将各项工作分配至各工作站,它决定各工作站该负责 之工作,让管理者将制令单安排至各工作站,同时兼 顾各工作站间目前的产能负荷情况以及生产线平衡问 题,但并未排定各工作站内的工作次序。
工作的处理优先级
又称派工(Dispatching),透过派工法则来决定在线执 行顺序。排程可定义成一种短期计划,此计划关系着 制造现场的制令单或拟作业之工作的作业顺序和时间 配置,此定义说明排程是一序列的排序步骤。
(Sequencing rule)
步骤1 利用方法7.5.3指派所有工作。
步骤2 步骤3
针对每部机台,找出第一个延迟工作,假设 发现在机台j的第i个顺位。
生产计划与管理之作业排程
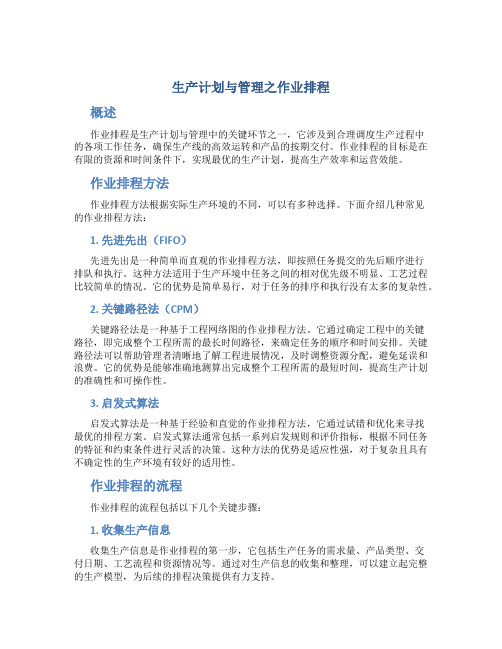
生产计划与管理之作业排程概述作业排程是生产计划与管理中的关键环节之一,它涉及到合理调度生产过程中的各项工作任务,确保生产线的高效运转和产品的按期交付。
作业排程的目标是在有限的资源和时间条件下,实现最优的生产计划,提高生产效率和运营效能。
作业排程方法作业排程方法根据实际生产环境的不同,可以有多种选择。
下面介绍几种常见的作业排程方法:1. 先进先出(FIFO)先进先出是一种简单而直观的作业排程方法,即按照任务提交的先后顺序进行排队和执行。
这种方法适用于生产环境中任务之间的相对优先级不明显、工艺过程比较简单的情况。
它的优势是简单易行,对于任务的排序和执行没有太多的复杂性。
2. 关键路径法(CPM)关键路径法是一种基于工程网络图的作业排程方法。
它通过确定工程中的关键路径,即完成整个工程所需的最长时间路径,来确定任务的顺序和时间安排。
关键路径法可以帮助管理者清晰地了解工程进展情况,及时调整资源分配,避免延误和浪费。
它的优势是能够准确地测算出完成整个工程所需的最短时间,提高生产计划的准确性和可操作性。
3. 启发式算法启发式算法是一种基于经验和直觉的作业排程方法,它通过试错和优化来寻找最优的排程方案。
启发式算法通常包括一系列启发规则和评价指标,根据不同任务的特征和约束条件进行灵活的决策。
这种方法的优势是适应性强,对于复杂且具有不确定性的生产环境有较好的适用性。
作业排程的流程作业排程的流程包括以下几个关键步骤:1. 收集生产信息收集生产信息是作业排程的第一步,它包括生产任务的需求量、产品类型、交付日期、工艺流程和资源情况等。
通过对生产信息的收集和整理,可以建立起完整的生产模型,为后续的排程决策提供有力支持。
2. 任务分析和排序任务分析是根据任务的特征和约束条件,对任务进行详细的分析和分类。
任务排序是根据任务的优先级,确定任务的先后次序。
任务分析和排序是作业排程的关键步骤,它直接影响到后续任务的安排和执行。
3. 资源分配和调度资源分配和调度是作业排程的核心内容,它要根据任务的需求量和资源的有效利用率,合理安排各项工作任务的时间和地点。
怎样做好生产作业排程
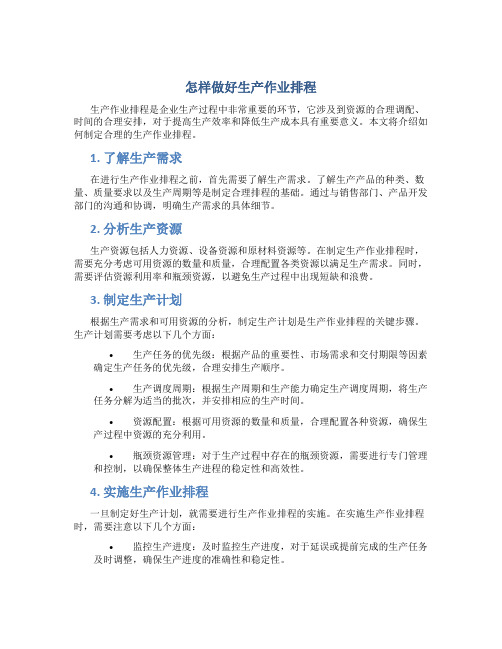
怎样做好生产作业排程生产作业排程是企业生产过程中非常重要的环节,它涉及到资源的合理调配、时间的合理安排,对于提高生产效率和降低生产成本具有重要意义。
本文将介绍如何制定合理的生产作业排程。
1. 了解生产需求在进行生产作业排程之前,首先需要了解生产需求。
了解生产产品的种类、数量、质量要求以及生产周期等是制定合理排程的基础。
通过与销售部门、产品开发部门的沟通和协调,明确生产需求的具体细节。
2. 分析生产资源生产资源包括人力资源、设备资源和原材料资源等。
在制定生产作业排程时,需要充分考虑可用资源的数量和质量,合理配置各类资源以满足生产需求。
同时,需要评估资源利用率和瓶颈资源,以避免生产过程中出现短缺和浪费。
3. 制定生产计划根据生产需求和可用资源的分析,制定生产计划是生产作业排程的关键步骤。
生产计划需要考虑以下几个方面:•生产任务的优先级:根据产品的重要性、市场需求和交付期限等因素确定生产任务的优先级,合理安排生产顺序。
•生产调度周期:根据生产周期和生产能力确定生产调度周期,将生产任务分解为适当的批次,并安排相应的生产时间。
•资源配置:根据可用资源的数量和质量,合理配置各种资源,确保生产过程中资源的充分利用。
•瓶颈资源管理:对于生产过程中存在的瓶颈资源,需要进行专门管理和控制,以确保整体生产进程的稳定性和高效性。
4. 实施生产作业排程一旦制定好生产计划,就需要进行生产作业排程的实施。
在实施生产作业排程时,需要注意以下几个方面:•监控生产进度:及时监控生产进度,对于延误或提前完成的生产任务及时调整,确保生产进度的准确性和稳定性。
•沟通与协调:与相关部门、生产人员保持良好的沟通和协调,及时解决生产过程中的问题和难题。
•质量控制:严格按照产品质量标准进行生产,确保产品质量的一致性和稳定性。
5. 监控和改进生产作业排程并不是一次性的任务,而是需要不断进行监控和改进的过程。
通过对生产作业排程过程的监控,可以及时发现和解决问题,提高生产效率和优化资源配置。
作业排程

生產計畫與管理 Chapter 7 作業排程
7-3
作業排程的基本概念
排程是一種資源分配的決策活動。 排程是一種資源分配的決策活動 。 作業排程 (Operations Scheduling)為廣義排程中的一種 , 為廣義排程中的一種, 為廣義排程中的一種 若在製造業中特別是指製造現場機台與工件間 的安排,以下簡稱排程。 的安排,以下簡稱排程。 在一般工廠內常見的排程問題中, 在一般工廠內常見的排程問題中,處理步驟主 要可分為兩部份。 要可分為兩部份。
在集合中從頭至尾找出第一個延遲作業,假設為k Step2 在集合中從頭至尾找出第一個延遲作業,假設為 包含第個), 包含第個 Step3 檢視前個工作 (包含第個 ,將最長作業時間之工作 開始為空集合), 移至另一集合中 (開始為空集合 ,其中。 開始為空集合 其中。 重新計算集合中所有工作的完工時間。 Step4 重新計算集合中所有工作的完工時間。若集合中沒 有延遲作業,則停止,集合的延遲個數即為最小解。 有延遲作業,則停止,集合的延遲個數即為最小解。 否則回到步驟2。 否則回到步驟 。
流程時間 ti 3 3+4 3+4+5 3+4+5+6 3+4+5+6+7 3+4+5+6+7+8 3+4+5+6+7+8+10 3+4+5+6+7+8+10+12
7-14
範例 7.1 3/3
所以平均流程時間 1 Fs = [ (8 × 3) + (7 × 4) + (6 × 5) + (5 × 6) + (4 × 7) + (3 × 8) + (2 × 10) + (1 × 12)] = 24.5
第十一章 作业排序
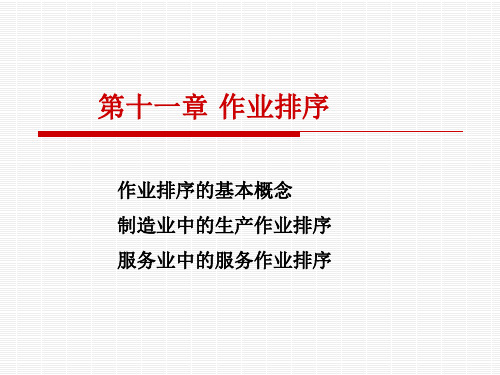
22
44
22
总数
115
118
3
36
平均数
23.0
0.6 7.2
平均在制品库存=115/44=2.61个
平均总库存=118/44=2.68个
假设:顾客不会提前取货,如果加工延迟,顾客将在加工完成后马上去走。
平均在制品库存=各工件流程时间之和/全部完工时间 平均总库存=全部在制品库存+完成品库存(等待顾客取货) 各工件的实际取货时间=等待加工时间+加工时间+等待取货时间 平均总库存=各工件实际取货时间之和/全部完工时间 排序结果比较 SPT规则排序,平均流程时间更短,在制品库存更少。 EDD规则排序,为顾客提供更好的服务,总库存水平低。
五、局部与整体优先规则及其事例
优先调度规则可以分为局部优先规则和整体优先规则两类,局 部优先规则决定工作的优先分配顺序仅以在单个工作地队列中的工 作所代表的信息为依据。例如,EDD,FCFS和SPT都是局部优先规则。 相比之下,整体优先规则决定工作地优先分配顺序不仅根据正在排 序的工作地,而且还要考虑到其他工作地的信息。SCR、MWKR、LWKR 以及MOPNR都是整体优先规则。整体优先规则可以看作是更好的选择, 但由于需要较多的信息,而信息的获取也是要付出成本的,因此在 某些情况下不一定能够提供足够的优势。
第十一章 作业排序
作业排序的基本概念 制造业中的生产作业排序 服务业中的服务作业排序
第一节 作业排序的基本概念
一、作业计划与排序
排序:只是确定工件在机器上的加工顺序。 作业计划:不仅包括确定工件的加工顺序,还包括确定机器加工每个 工件的开始时间和完成时间 工件等待:一个工件的某道工序完成之后,执行它下一道工序的机器 还在加工其他工件,这时,工件要等待一段时间才能开始加工。 机器空闲:一台机器已经完成对某个工件的加工,但随后要加工的工 件还未到达。 提供服务者:指“工作地”、“机器”、“人员”等。 接受服务者:指“工作”、“工件”、“顾客”等。 排程难点:按时间来分配特定的工作,但许多工作同时为同一资源而 竞争。
生产计划与管理作业排程

生产计划与管理作业排程引言生产计划和作业排程是制造业中至关重要的环节,它们对于企业的生产效率和客户满意度具有重要影响。
生产计划是根据销售预测、库存状况和生产能力等因素,制定产品生产数量和时间安排的活动。
作业排程则是在生产计划的基础上,根据工序的要求和资源的可用性,决定具体的生产顺序和时间安排。
本文将详细介绍生产计划和管理作业排程的过程和方法。
生产计划1. 生产计划的定义生产计划是制定在一定时间范围内,在满足客户需求的前提下,通过合理安排生产资源和控制生产流程,实现产品按时生产的活动。
一个有效的生产计划应考虑以下几个方面。
2. 生产计划的目标生产计划的主要目标是确保产品按时交付,并最大程度地提高生产效率和资源利用率。
为了实现这些目标,生产计划需要考虑以下因素。
3. 生产计划的制定过程生产计划的制定过程包括以下几个步骤。
作业排程1. 作业排程的定义作业排程是根据生产计划和资源的可用性,确定具体的生产顺序和时间安排的活动。
作业排程的目标是合理安排生产任务,使得资源利用率最大化,并确保生产过程的连续性和顺畅性。
2. 作业排程的方法作业排程的方法有多种,常见的包括先来先服务(FCFS)、最短作业优先(SJF)、最早截止期优先(EDD)等。
不同的方法适用于不同的生产环境和要求。
在选择作业排程方法时,需要考虑以下几个因素。
3. 作业排程的实施步骤作业排程的实施步骤包括以下几个方面。
生产计划与作业排程的关系生产计划和作业排程是制造业中不可分割的两个环节,它们之间存在着密切的关系。
生产计划提供了作业排程的依据和目标,而作业排程则根据生产计划和资源情况,决定具体的生产顺序和时间安排。
两者的协同作用可以提高生产效率和资源利用率,并确保产品按时交付。
结论生产计划和作业排程是制造业中至关重要的环节,它们对于企业的生产效率和客户满意度具有重要影响。
本文介绍了生产计划和作业排程的定义、目标、方法和实施步骤,并强调了两者的密切关系。
排程及车间作业管理

排程及车间作业管理引言排程及车间作业管理是生产过程中非常关键的一环,它涉及到对生产任务的合理安排和车间资源的有效管理。
通过合理的排程及车间作业管理,企业可以提高生产效率,降低生产成本,提高产品质量,增强市场竞争力。
本文将介绍排程及车间作业管理的基本概念、方法和常用工具。
一、排程管理1.1 排程的定义排程是指对生产任务的时间和资源进行安排的过程。
其主要目的是合理规划和安排生产任务的先后顺序,确保产品能够按时交付,并最大程度地利用车间资源,提高生产效率。
1.2 排程的重要性排程对于车间的生产效率和质量控制具有重要意义。
合理的排程可以避免生产任务的冲突和延误,提高生产效率,降低生产成本。
同时,排程还可以有效地控制生产过程中的质量风险,保证产品的质量。
1.3 排程的方法排程有多种方法,常用的包括任务编排法、资源约束法和进度优化法。
1.3.1 任务编排法任务编排法是一种常用的排程方法,它将生产任务按照其工艺流程和优先级进行排列,确定任务的先后顺序。
通过任务编排可以合理规划生产任务的流程,避免任务之间的冲突和延误。
1.3.2 资源约束法资源约束法是一种以车间资源为基础的排程方法,它主要关注车间资源的可用性和合理利用。
在资源约束法中,排程的关键是确定车间资源的容量和利用率,确保车间资源能够满足生产任务的需求。
1.3.3 进度优化法进度优化法是一种以时间为基础的排程方法,它通过优化任务的开始和结束时间,使得整个生产过程的时间最短。
进度优化法通常使用数学模型和算法进行计算,能够得到最优的排程方案。
1.4 排程工具排程工具是辅助排程的软件工具,它可以帮助企业实现自动化排程,提高排程的准确性和效率。
常用的排程工具有Microsoft Project、Oracle Primavera等。
二、车间作业管理2.1 车间作业的定义车间作业是指在车间内进行的各种生产活动和任务,包括物料配送、加工、装配等。
良好的车间作业管理可以有效地控制车间生产过程,提高生产效率。
第十一章-作业排序讲解

2023/5/24
16
生
产
与 运 作
约翰逊-贝尔曼规则
管
理
例:4项作业在两台设备上进行加工,其加工顺
序相同,作业时间如下表所示:
1
作业 机床
A
B
C
D2
5
t1 3 6 5 7
t2 2 8 6 4
C DA
6
7
3
6
8
T
42
2023/5/24
T = 2+4+8+6+5 = 25
17
生
产 与 运
五、3台机器上N项作业的排
则 ci=ri+ti+wi
2023/5/24
7
生
产
与 运 作
计算公式(续)
管
理
第i项作业任务在机床组的流程时间为:
Fi=ci-ri=ti+wi 如果作业任务i的完成时刻ci已超过要求完
成时刻di,则形成交货延期,延期量Di为: Di= ci-di=Fi+ri-di
如果ci未超过di ,则延期量Di为0。
作业
加工时间(天) 预定日期(天)
A
2
7
B
8
16
C
4
4
D1017E Nhomakorabea5
15
F
12
18
2023/5/24
11
生
产
与 运 作
按FCFS规则排序
管
理
排序的结果是A-B-C-D-E-F。
顺序 加工时间 流程时间 预定交货期
A
2
2
7
B
8
10
作业排程与车间作业计划
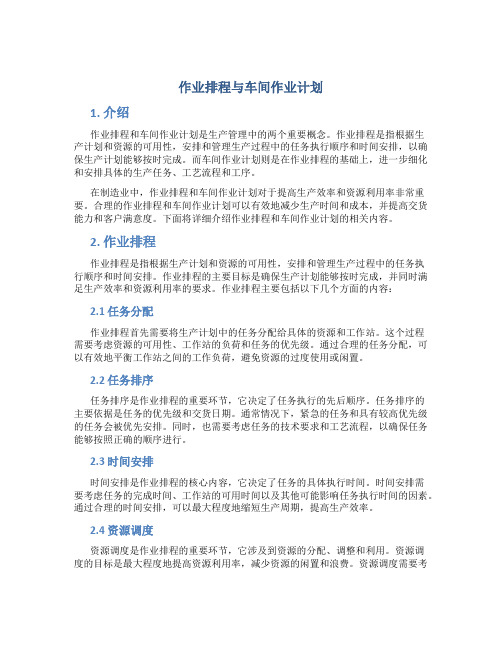
作业排程与车间作业计划1. 介绍作业排程和车间作业计划是生产管理中的两个重要概念。
作业排程是指根据生产计划和资源的可用性,安排和管理生产过程中的任务执行顺序和时间安排,以确保生产计划能够按时完成。
而车间作业计划则是在作业排程的基础上,进一步细化和安排具体的生产任务、工艺流程和工序。
在制造业中,作业排程和车间作业计划对于提高生产效率和资源利用率非常重要。
合理的作业排程和车间作业计划可以有效地减少生产时间和成本,并提高交货能力和客户满意度。
下面将详细介绍作业排程和车间作业计划的相关内容。
2. 作业排程作业排程是指根据生产计划和资源的可用性,安排和管理生产过程中的任务执行顺序和时间安排。
作业排程的主要目标是确保生产计划能够按时完成,并同时满足生产效率和资源利用率的要求。
作业排程主要包括以下几个方面的内容:2.1 任务分配作业排程首先需要将生产计划中的任务分配给具体的资源和工作站。
这个过程需要考虑资源的可用性、工作站的负荷和任务的优先级。
通过合理的任务分配,可以有效地平衡工作站之间的工作负荷,避免资源的过度使用或闲置。
2.2 任务排序任务排序是作业排程的重要环节,它决定了任务执行的先后顺序。
任务排序的主要依据是任务的优先级和交货日期。
通常情况下,紧急的任务和具有较高优先级的任务会被优先安排。
同时,也需要考虑任务的技术要求和工艺流程,以确保任务能够按照正确的顺序进行。
2.3 时间安排时间安排是作业排程的核心内容,它决定了任务的具体执行时间。
时间安排需要考虑任务的完成时间、工作站的可用时间以及其他可能影响任务执行时间的因素。
通过合理的时间安排,可以最大程度地缩短生产周期,提高生产效率。
2.4 资源调度资源调度是作业排程的重要环节,它涉及到资源的分配、调整和利用。
资源调度的目标是最大程度地提高资源利用率,减少资源的闲置和浪费。
资源调度需要考虑资源的可用性、工作站的需求以及任务的优先级。
通过合理的资源调度,可以提高生产效率和降低生产成本。
作业排程与车间作业计划概论

作业排程与车间作业计划概论引言作业排程和车间作业计划是生产管理中的重要环节,它们的目标是优化生产资源的利用,合理安排生产计划,提高生产效率和产品质量。
本文将介绍作业排程与车间作业计划的概念、作用以及相关的方法和工具。
作业排程的概念和作用作业排程是指根据产品的生产需求和生产资源的可用情况,合理安排和调度各项生产活动的时间、顺序和资源分配,以达到生产目标的管理过程。
作业排程的主要作用包括:1.提高生产效率:通过合理安排生产活动的时间和顺序,避免生产瓶颈和资源浪费,提高生产效率。
2.降低生产成本:通过优化资源利用和减少产品的等待时间,降低生产成本。
3.缩短交货期:通过优化生产计划和及时调整作业优先级,缩短产品的交货期,提高客户满意度。
4.提高产品质量:通过合理安排生产活动和控制生产过程,提高产品质量,减少次品率。
车间作业计划的概念和作用车间作业计划是指根据生产排程,将作业任务分配给具体的工作组和机器设备,制定详细的生产计划和作业流程,指导车间操作的管理过程。
车间作业计划的主要作用包括:1.明确作业任务和流程:通过详细制定作业计划,明确作业任务和操作流程,确保每个环节按照规定的程序进行。
2.提高生产效率:通过合理安排作业任务和资源分配,避免资源浪费和生产滞后,提高生产效率。
3.降低生产风险:通过合理安排作业任务和指导生产操作,减少因操作失误导致的生产风险,提高生产安全性。
4.改善生产环境:通过合理安排作业任务和资源利用,改善生产环境,提高员工劳动条件和工作效率。
作业排程与车间作业计划的方法和工具作业排程和车间作业计划涉及到复杂的生产资源调度和作业任务分配问题,需要借助一些方法和工具进行支持和优化,常用的方法和工具包括:1.作业流程图:通过绘制作业流程图,明确作业任务之间的依赖关系和顺序,为作业排程和车间作业计划提供可视化参考。
2.作业调度算法:根据具体的生产需求和资源情况,采用不同的作业调度算法,如先来先服务(FCFS)、最短作业优先(SJF)、最早截止期优先(EDD)等,进行作业排程和车间作业计划的优化。
- 1、下载文档前请自行甄别文档内容的完整性,平台不提供额外的编辑、内容补充、找答案等附加服务。
- 2、"仅部分预览"的文档,不可在线预览部分如存在完整性等问题,可反馈申请退款(可完整预览的文档不适用该条件!)。
- 3、如文档侵犯您的权益,请联系客服反馈,我们会尽快为您处理(人工客服工作时间:9:00-18:30)。
–第二位作業員在未被圈選的正整數中
•(剩餘的五天都沒有被圓圈圈住)都減去1
•步驟重覆使用於第二位、第三位工作 者等等
•
一致是强有力的,而纷争易于被征服 。。20. 8.1220. 8.12We dnesda y, August 12, 2020
•
勤奋是登上知识高峰的一条捷径,不 怕吃苦 才能在 知识的 海洋里 自由遨 游。。1 0:49:19 10:49:1 910:49 8/12/20 20 10:49:19 AM
平均流程時間 (天)
10 7 .2 7 .8 9 .2 1 0 .6 8 .6
平均延誤 (天)
4 .6 2 .4 2 .4 4 .0 5 .4 3 .2
2機對n項作業之排程
• n/2流程工作站 • 作業必須以相同的順序經過2部機器 • Johnson法則 • 讓第一項工作的開始至最後一項工作
的結束為止之間的流程時間最小化
I
13020
II
10411
III 2 2 0 1 3
IV 4 0 1 0 1
V
04103
工作站現場控制
• Shop Floor Control的主要功能
–指定每項工作站訂單之分派優先順序 –維持在製品數量之資訊 –傳送工作站訂單之現況資訊至辦公室 –提供確實產出之資料以利產能控制 –提供在製品庫存及會計所需之數量資料 –提供人力及機器的生產力等衡量指標
•反向排程 (Backward Scheduling)
–以未來的某特定日期(可能是交期) –開始反向往前排定各作業的時間 –可得知最晚開始時刻
•MRP系統是物料無限負荷、反向排程
•機器導向排程
–機器是最重要的資源,故排定機器的時間
•人員導向排程
–人員是最重要的資源,故排定人員的時間
常用的排程與控制功能
•
衷心感谢社会各界对电建事业的明白 关心和 支持。2 0.8.121 0:49:19 10:49A ug-201 2-Aug-2 0
A
3
B
6
C
5
D
7
在 機 器 # 2上 之 作 業 時 間 2 8 6 4
步驟2和3:選擇最短的作業時間並將其分派
工作A在機器2上之作業時間最短, 所以應 優先被分派與
最後被執行。 (刪除工作A)
步驟4:重覆步驟2和3,直到排程結束 剩餘的工作中選擇最短的作業時間, 工作D在機器2上之作業時間是第二短, 所以它被排在倒數第二個執行
•分配訂單、設備和人員至工作中心
–短期的產能規劃
•決定訂單執行的順序 •派工 (dispatching)
–啟動排程工作之執行
•現場管制
–控制訂單之進度 –已延誤與緊急訂單之跟催
電腦
等候之訂單
領班
生產控制
等候之訂單
工作站排程的目的
•滿足交期 •使前置時間最小化 •使設置時間或設置成本最小化 •使在製品庫存最小化 •使設備利用率最大化
新的訂單
未分派 訂單
生產管制 投入速率
生產之 前置時間
在製品 (負荷)
產能
產出/完成訂單
資料完整性
•工作站現場控制系統電腦化
–使用條碼及光學掃描器
•加速報告處理速度與減少資料輸入錯誤
•資料不精確會造成整個控制系統回饋 之資料是錯誤的
–工作站紀律 (shop discipline)
•盤點錯誤 •零件加工路徑之改變
工作A和D已被安排或已被刪除, 在剩餘之工作中, 工作C在機器1上有最短的作業時間, 故工作C被安排在第一個執行
現在僅剩下工作B, 而且其在機器1上的作業時間最短
執行順序的答案是C→B→D→A,流程時間為25天
機器 機器
1作 業
作C 業
2閒 置 作 業
B作 業 作 D 業
A閒 其
置 他
但 作
可 業
工作依到達之順序
A B C D E
處理時間 (天)
3 4 2 6 1
交期 (從現在起之天數)
5 6 7 9 2
所有的訂單都需要使用僅有的彩色影印機, Morales必須決定這五個訂單的處理順序, 評估準則是使流程時間最小化
FCFS法則導出下列之流程時間:
工作
處理天數
交期
(天)
(從 現 在 起 之 天 數 )
考慮SOT法則。給予加工時間最短之訂單第一優先處理, 導出之流程時間:
工作
處理天數(天)
交 期 (從 現 在 起 之 天 數 )
流程時間(天)
E
1
2
0+1=1
C
2
7
1+2=3
A
3
5
3+3=6
B
4
6
6+4=10
D
6
9
10+ 6= 16
流程時間合計=1+3+6+10+16=36天 平均流程時間=36/5=7.2天 只有工作E和C在交期前完成,工作A僅遲了一天 平均工作延誤(0+0+1+4+7)/5=2.4天
•滿足客戶交期或下游生產的需求 •使流程時間最小化 •使在製品最小化 •使機器與工作人員之閒置時間最小化
排程法則與技術
單機對n項工作之排程
例16.1 n項工作在單機上作業 Mike Morales是法律影印快遞公司的主管, 這家公司為洛杉磯市中心區的 法律事務所提供影印服務, 有五個客戶在本週的剛開始時, 提出他們的訂單,排程資料詳列於下:
處理天數 (天)
1 3 4 6 2
交期 (從 現 在 起 之 天 數 )
2 5 6 9 7
流程時間 (天)
0+1=1 1+3=4 4+4=8 8+6=14 14+2=16
法則
FC FS SO T D D a te LC FS R andom STR
流程時間合計 (天)
50 36 39 46 53 43
使用DDATE (交期) 法則,則排程之結果是:
工作
處理天數
交期
流程時間
(天)
(從 現 在 起 之 天 數 )
(天)
E
1
2
0+1=1
A
3
5
1+3=4
B
4
6
4+4=8
C
2
7
8+2=10
D
6
9
10+ 6= 16
流程時間合計=1+4+8+10+16=39天 平均流程時間=39/5=7.8天 工作B、C、D之交期將延誤 平均一項工作將延誤(0+0+2+3+7)/5=2.4天
0+1=1 1+6=7 7+2=9 9+4=13 13+3=16
9
0+6=6
7
6+2=8
5
8+3=11
2
11+1=12
6
12+4=16
剩餘寬裕時間 (STR; slack time remaining)
工作
STR排 程 E A B D C
流 程 時 間 合 計 = 43天 平 均 流 程 時 間 = 8 .6 天 平 均 延 誤 = 3 .2 天
A
3
5
B
4
6
C
2
7
D
6
9
E
1
2
流程時間 (天)
0+3=3 3+4=7 7+2=9 9+6=15 15+1=16
流程時間合計=3+7+9+15+16=50天 平均流程時間=50/5=10天 僅有工作A將能準時交貨 工作B、C、D、E則將分別延誤1、2、6、14天, 平均一項工作將延誤(0+1+2+6+14)/5=4.6天
可按部就班的完成 •一個已經開始作業的工作訂單不應該
被中斷
•藉由集中注意力在瓶頸之工作中心和 工作訂單上,最能有效的達成流量的 速度
•每天重新排程
•每天取得每個工作中心未完工之工作 訂單的資訊回饋
•使工作中心之投入資訊與工作者確實 能做的相配合
•當尋求產出的改善時,查看工程設計 與執行處理間之不一致
0
II
2
0
5
4
1
III
2
1
0
3
2
IV
5
0
2
3
1
V
0
3
1
2
2
步驟 2:欄之減法 每欄各數減去該欄最小之數
機
器
工作
A
B
C
D
E
Ⅰ
2
3
1
3
0
II
2
0
5
2
1
III
2
1
0
1
2
IV
5
0
2
1
1
V
0
3
1
0
2
步驟 3:利用直線驗證
以最少直線劃過所有的0 , 計算直線數是4, 因需五條直線,故繼續步驟四
機
器
工作
A
B
C
做
C作 業
B作 業 作 D 業
A
0
5
11
19
23
2 5累 積 天 數
機器數與工作數相同之排程
•指派方法 (assignment method) •線性規劃運輸模式 (Transportation) •目的是使衡量績效最小化或最大化
–最小成本、流程時間,最大利潤
• 適用條件
–有n項「東西」被分派至n個「目的地」 –每項東西必須被分派至一個,而且僅有一