环氧树脂固化的三个阶段
环氧树脂和酚醛树脂固化温度
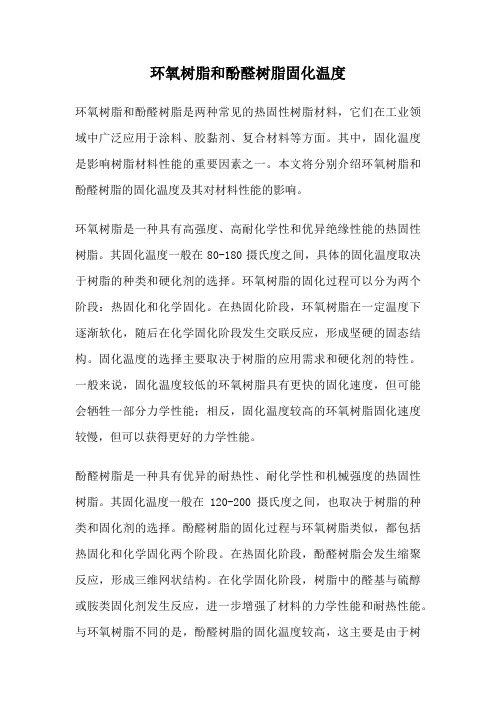
环氧树脂和酚醛树脂固化温度环氧树脂和酚醛树脂是两种常见的热固性树脂材料,它们在工业领域中广泛应用于涂料、胶黏剂、复合材料等方面。
其中,固化温度是影响树脂材料性能的重要因素之一。
本文将分别介绍环氧树脂和酚醛树脂的固化温度及其对材料性能的影响。
环氧树脂是一种具有高强度、高耐化学性和优异绝缘性能的热固性树脂。
其固化温度一般在80-180摄氏度之间,具体的固化温度取决于树脂的种类和硬化剂的选择。
环氧树脂的固化过程可以分为两个阶段:热固化和化学固化。
在热固化阶段,环氧树脂在一定温度下逐渐软化,随后在化学固化阶段发生交联反应,形成坚硬的固态结构。
固化温度的选择主要取决于树脂的应用需求和硬化剂的特性。
一般来说,固化温度较低的环氧树脂具有更快的固化速度,但可能会牺牲一部分力学性能;相反,固化温度较高的环氧树脂固化速度较慢,但可以获得更好的力学性能。
酚醛树脂是一种具有优异的耐热性、耐化学性和机械强度的热固性树脂。
其固化温度一般在120-200摄氏度之间,也取决于树脂的种类和固化剂的选择。
酚醛树脂的固化过程与环氧树脂类似,都包括热固化和化学固化两个阶段。
在热固化阶段,酚醛树脂会发生缩聚反应,形成三维网状结构。
在化学固化阶段,树脂中的醛基与硫醇或胺类固化剂发生反应,进一步增强了材料的力学性能和耐热性能。
与环氧树脂不同的是,酚醛树脂的固化温度较高,这主要是由于树脂分子中醛基团的反应活性较低所致。
固化温度对环氧树脂和酚醛树脂的性能有着重要影响。
在固化温度较低的情况下,树脂分子的固化速度较快,但可能会导致材料内部存在未固化的区域,从而影响材料的力学性能和耐热性能。
相反,在固化温度较高的情况下,树脂分子的固化速度较慢,但可以获得更好的力学性能和耐热性能。
因此,在实际应用中,需要根据具体需求选择合适的固化温度,以平衡材料的性能要求和生产效率。
环氧树脂和酚醛树脂是两种常见的热固性树脂材料,其固化温度的选择对材料的性能具有重要影响。
环氧树脂与固化剂反应:深度解析与应用

环氧树脂与固化剂反应:深度解析与应用一、环氧树脂与固化剂反应概述环氧树脂是一种高分子聚合物,因其优异的物理性能和化学性能而被广泛应用于各个领域。
然而,环氧树脂本身并不稳定,需要在特定的条件下进行固化,这一过程就需要用到固化剂。
环氧树脂与固化剂的反应是一种重要的化学反应,涉及到多种复杂的化学机制。
二、环氧树脂与固化剂反应的化学机制环氧树脂的固化过程可以大致分为三个阶段:凝胶阶段、硬化阶段和熟化阶段。
在这个过程中,固化剂起着至关重要的作用。
固化剂的种类繁多,根据其化学组成和用途可以分为胺类、酸酐类、聚合物类等。
这些固化剂通过与环氧树脂中的环氧基团发生反应,将环氧树脂的线性分子交联成为网状结构,从而使其固化。
三、环氧树脂与固化剂反应的影响因素环氧树脂与固化剂的反应受到多种因素的影响,如温度、压力、固化剂的种类和用量、促进剂的种类和用量等。
在实际应用中,需要根据具体的条件和要求选择合适的固化剂和促进剂,以获得最佳的固化效果。
此外,环氧树脂的纯度、杂质含量、分子量等也会对固化效果产生影响。
四、环氧树脂与固化剂反应的应用由于环氧树脂与固化剂反应具有优异的物理性能和化学性能,因此被广泛应用于建筑、电子、航空航天、汽车制造等领域。
例如,在建筑领域中,环氧树脂可以用于制备防水材料、防腐涂料等;在电子领域中,环氧树脂可以用于制备电路板、电子元件的封装材料等;在航空航天领域中,环氧树脂可以用于制备结构材料、绝缘材料等;在汽车制造领域中,环氧树脂可以用于制备汽车零部件、刹车片材料等。
五、结论环氧树脂与固化剂反应是一种重要的化学反应,涉及到多种复杂的化学机制。
在实际应用中,需要根据具体的条件和要求选择合适的固化剂和促进剂,以获得最佳的固化效果。
未来随着科学技术的不断发展和进步,相信环氧树脂与固化剂反应的应用前景将更加广阔。
环氧树脂-百度百科

环氧树脂百科名片环氧树脂是泛指分子中含有两个或两个以上环氧基团的有机高分子化合物,除个别外,它们的相对分子质量都不高。
环氧树脂的分子结构是以分子链中含有活泼的环氧基团为其特征,环氧基团可以位于分子链的末端、中间或成环状结构。
由于分子结构中含有活泼的环氧基团,使它们可与多种类型的固化剂发生交联反应而形成不溶、不熔的具有三向网状结构的高聚物。
简介英文术语:epoxy Resin凡分子结构中含有环氧基团的高分子化合物统称为环氧树脂。
固化后的环氧树脂具有良好的物理化学性能,它对金属和非金属材料的表面具有优异的粘接强度,介电性能良好,变定收缩率小,制品尺寸稳定性好,硬度高,柔韧性较好,对碱及大部分溶剂稳定,因而广泛应用于国防、国民经济各部门,作浇注、浸渍、层压料、粘接剂、涂料等用途。
我国自1958年开始对环氧树脂进行了研究,并以很快的速度投入了工业生产,至今已在全国各地蓬勃发展,除生产普通的双酚A-环氧氯丙烷型环氧树脂外,也生产各种类型的新型环氧树脂,以满足国防建设及国家经济各部门的急需。
环氧树脂是泛指分子中含有两个或两个以上环氧基团的有机高分子化合物,除个别外,它们的相对分子质量都不高。
环氧树脂的分子结构是以分子链中含有活泼的环氧基团为其特征,环氧基团可以位于分子链的末端、中间或成环状结构。
由于分子结构中含有活泼的环氧基团,使它们可与多种类型的固化剂发生交联反应而形成不溶、不熔的具有三向网状结构的高聚物。
类型1、活性氢化物与环氧氯丙烷反应;2、以过氧化氢或过酸(例过醋酸)将双键进行液相氧化;3、双键化合物的空气氧化;4、其它。
由于它的性能并不是十分完美的,同时应用环氧树脂的对象也不是千遍一律的,根据使用的对象不同,对环氧树脂的性能也有所要求,例如有的要求低温快干,有的要求绝缘性能优良。
因而要有的放矢对环氧树脂加以改性。
改性的方法1、选择固化剂;2、添加反应性稀释剂;3、添加填充剂;4、添加别种热固性或热塑性树脂;5、改良环氧树脂本身。
环氧树脂的固化过程

环氧树脂的固化过程同学们!今天咱们来一起探索一下环氧树脂的固化过程,这可有趣啦!环氧树脂啊,一开始是一种液态的物质,就像是水一样可以流动。
但是当我们加入一些特定的东西之后,它就会慢慢变得坚硬起来,这个过程就是固化。
那环氧树脂是怎么固化的呢?这得从它的化学变化说起。
我们会往环氧树脂里面加入一种叫做固化剂的东西。
固化剂就像是环氧树脂的“小伙伴”,它们一相遇,就会发生一系列的化学反应。
当固化剂和环氧树脂混合在一起时,分子之间就开始相互作用。
就好像是小朋友们手拉手一样,环氧树脂的分子和固化剂的分子逐渐连接起来,形成一个巨大的网络结构。
在这个过程中,环氧树脂会从液态逐渐变得黏稠。
一开始,它还能流动,但是随着反应的进行,它会变得越来越稠,就像是蜂蜜一样。
环氧树脂会继续发生变化,开始变硬。
这个时候,它就不再是能流动的液体了,而是慢慢具有了一定的形状和硬度。
整个固化过程的速度会受到很多因素的影响。
比如说温度,如果温度比较高,固化的速度就会加快;相反,如果温度低,固化就会变得慢一些。
再比如说固化剂的用量。
如果固化剂加得多,反应就会进行得更快;加得少,固化就会慢一些。
咱们来举个例子。
假如我们在夏天做环氧树脂的固化实验,因为夏天温度高,可能只需要几个小时环氧树脂就能固化好。
但是如果在冬天,温度低,可能就需要一天甚至更长的时间才能固化完成。
如果我们在调配环氧树脂和固化剂的时候,比例没有掌握好,固化的效果也会不一样。
要是固化剂加少了,环氧树脂可能一直都没法完全固化,还是软软的;要是加多了,可能固化得太快,还没来得及操作就已经变硬了。
在环氧树脂固化的过程中,我们还可以通过一些方法来控制它的性能。
比如调整固化剂的种类和用量,可以让固化后的环氧树脂具有不同的硬度、强度和韧性。
环氧树脂的固化过程是一个神奇的化学变化,通过控制各种条件,我们可以让它变成我们想要的样子,在很多领域发挥重要的作用。
同学们,现在你们是不是对环氧树脂的固化过程有更清楚的认识啦?。
环氧树脂固化过程中的收缩和内应力

环氧树脂固化过程中的收缩和内应力【导言】在化学领域中,环氧树脂是一种重要的聚合物材料。
它具有极高的稳定性和耐用性,因此在各个领域都有广泛的应用。
然而,由于环氧树脂的固化过程中存在收缩和产生内应力的问题,这给其应用带来了一定的挑战。
本文将对环氧树脂固化过程中的收缩和内应力进行全面评估和探讨,并分享个人观点和理解。
【正文】一、环氧树脂的固化过程环氧树脂的固化是指在特定温度和时间条件下,其单体之间发生化学反应,形成交联网络结构的过程。
固化过程可以分为两个主要阶段:缓慢固化阶段和快速固化阶段。
1. 缓慢固化阶段在环氧树脂的缓慢固化阶段,环氧树脂单体与固化剂之间的反应速率较慢。
此时,环氧树脂处于液态,分子之间通过弱的物理作用力相互结合。
在这个阶段,环氧树脂的体积不会发生明显变化,因此不会产生显著的收缩和内应力。
2. 快速固化阶段当固化反应进入快速固化阶段时,反应速率急剧增加,环氧树脂开始形成交联网络结构。
在这个阶段,由于分子间化学键的形成导致分子体积减小,环氧树脂开始发生收缩现象。
与此固化过程中产生的内应力也会逐渐积累。
二、收缩的原因及影响环氧树脂固化过程中的收缩主要有两个原因:分子结构的改变和反应体积变化。
1. 分子结构的改变当环氧树脂单体与固化剂发生反应时,分子结构会发生改变。
在快速固化阶段,分子间的化学键的形成会导致分子体积减小,从而引起收缩现象。
这种分子结构的改变既是环氧树脂能够形成强大网络结构的原因,也是引起收缩和内应力的根本原因之一。
2. 反应体积变化除了分子结构的改变外,固化过程中反应体积的变化也是导致环氧树脂收缩的原因之一。
在快速固化阶段,固化剂与环氧树脂单体之间的反应会释放出大量的热量,导致温度升高。
热胀冷缩效应会导致环氧树脂在固化过程中发生体积收缩,从而引起收缩和内应力。
环氧树脂固化过程中的收缩和内应力对其应用产生了一定的影响。
收缩会导致制品尺寸变化,可能会引起零件变形、变形甚至破裂。
环氧树脂合成原理

环氧树脂合成原理环氧树脂是一种重要的高分子材料,具有优异的性能和广泛的应用领域。
环氧树脂的合成原理是指通过特定的化学反应将环氧基团与含有活泼氢的化合物发生开环反应,形成环氧树脂分子链的过程。
环氧树脂的合成原理主要包括环氧化、缩合和固化三个阶段。
首先,环氧树脂的合成通常是从环氧化合物开始的。
环氧化合物是一类分子中含有两个或多个环氧基团的化合物,常见的环氧化合物有环氧乙烷、环氧丙烷等。
在合成环氧树脂的过程中,环氧化合物首先与含有活泼氢的化合物发生环氧化反应,活泼氢可以来自于酚类、醛类、酮类等化合物。
环氧化反应是环氧树脂合成的起始阶段,也是决定环氧树脂性能的重要环节。
其次,环氧树脂的合成还包括缩合反应。
在环氧化合物发生环氧化反应后,得到的产物往往是含有羟基的化合物。
这些含有羟基的化合物会在一定的条件下发生缩合反应,形成环氧树脂的前体物。
缩合反应是环氧树脂合成过程中的关键步骤,它决定了环氧树脂分子链的长度和结构,直接影响到环氧树脂的性能和用途。
最后,环氧树脂的合成还需要进行固化处理。
在环氧树脂的应用中,为了使其具有良好的力学性能和化学稳定性,通常需要将其与固化剂进行反应,形成三维网络结构。
固化反应是环氧树脂合成的最后一个阶段,通过固化反应可以使环氧树脂分子之间形成交联结构,从而提高环氧树脂的硬度、强度和耐热性能。
总的来说,环氧树脂的合成原理是一个复杂的化学过程,需要精确控制反应条件和原料配比,才能得到具有良好性能的环氧树脂产品。
通过对环氧化、缩合和固化三个阶段反应的深入研究,可以进一步优化环氧树脂的合成方法,提高环氧树脂的品质和性能,拓展其在各个领域的应用范围。
环氧树脂作为一种重要的高分子材料,其合成原理的研究和应用具有重要的科学意义和工程价值。
环氧树脂胶固化条件
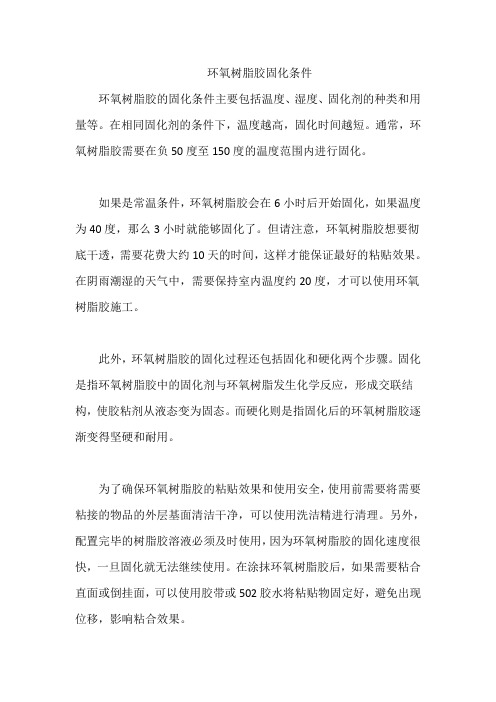
环氧树脂胶固化条件
环氧树脂胶的固化条件主要包括温度、湿度、固化剂的种类和用量等。
在相同固化剂的条件下,温度越高,固化时间越短。
通常,环氧树脂胶需要在负50度至150度的温度范围内进行固化。
如果是常温条件,环氧树脂胶会在6小时后开始固化,如果温度为40度,那么3小时就能够固化了。
但请注意,环氧树脂胶想要彻底干透,需要花费大约10天的时间,这样才能保证最好的粘贴效果。
在阴雨潮湿的天气中,需要保持室内温度约20度,才可以使用环氧树脂胶施工。
此外,环氧树脂胶的固化过程还包括固化和硬化两个步骤。
固化是指环氧树脂胶中的固化剂与环氧树脂发生化学反应,形成交联结构,使胶粘剂从液态变为固态。
而硬化则是指固化后的环氧树脂胶逐渐变得坚硬和耐用。
为了确保环氧树脂胶的粘贴效果和使用安全,使用前需要将需要粘接的物品的外层基面清洁干净,可以使用洗洁精进行清理。
另外,配置完毕的树脂胶溶液必须及时使用,因为环氧树脂胶的固化速度很快,一旦固化就无法继续使用。
在涂抹环氧树脂胶后,如果需要粘合直面或倒挂面,可以使用胶带或502胶水将粘贴物固定好,避免出现位移,影响粘合效果。
环氧树脂固化方法
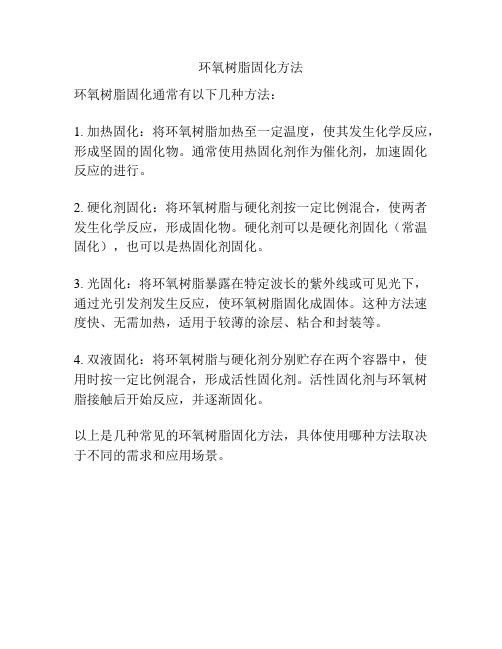
环氧树脂固化方法
环氧树脂固化通常有以下几种方法:
1. 加热固化:将环氧树脂加热至一定温度,使其发生化学反应,形成坚固的固化物。
通常使用热固化剂作为催化剂,加速固化反应的进行。
2. 硬化剂固化:将环氧树脂与硬化剂按一定比例混合,使两者发生化学反应,形成固化物。
硬化剂可以是硬化剂固化(常温固化),也可以是热固化剂固化。
3. 光固化:将环氧树脂暴露在特定波长的紫外线或可见光下,通过光引发剂发生反应,使环氧树脂固化成固体。
这种方法速度快、无需加热,适用于较薄的涂层、粘合和封装等。
4. 双液固化:将环氧树脂与硬化剂分别贮存在两个容器中,使用时按一定比例混合,形成活性固化剂。
活性固化剂与环氧树脂接触后开始反应,并逐渐固化。
以上是几种常见的环氧树脂固化方法,具体使用哪种方法取决于不同的需求和应用场景。
环氧树脂固化原理
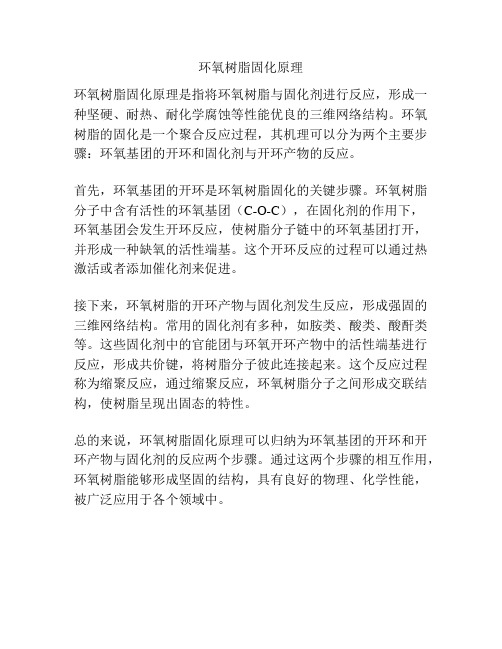
环氧树脂固化原理
环氧树脂固化原理是指将环氧树脂与固化剂进行反应,形成一种坚硬、耐热、耐化学腐蚀等性能优良的三维网络结构。
环氧树脂的固化是一个聚合反应过程,其机理可以分为两个主要步骤:环氧基团的开环和固化剂与开环产物的反应。
首先,环氧基团的开环是环氧树脂固化的关键步骤。
环氧树脂分子中含有活性的环氧基团(C-O-C),在固化剂的作用下,
环氧基团会发生开环反应,使树脂分子链中的环氧基团打开,并形成一种缺氧的活性端基。
这个开环反应的过程可以通过热激活或者添加催化剂来促进。
接下来,环氧树脂的开环产物与固化剂发生反应,形成强固的三维网络结构。
常用的固化剂有多种,如胺类、酸类、酸酐类等。
这些固化剂中的官能团与环氧开环产物中的活性端基进行反应,形成共价键,将树脂分子彼此连接起来。
这个反应过程称为缩聚反应,通过缩聚反应,环氧树脂分子之间形成交联结构,使树脂呈现出固态的特性。
总的来说,环氧树脂固化原理可以归纳为环氧基团的开环和开环产物与固化剂的反应两个步骤。
通过这两个步骤的相互作用,环氧树脂能够形成坚固的结构,具有良好的物理、化学性能,被广泛应用于各个领域中。
uv 环氧树脂 固化过程

uv 环氧树脂固化过程
环氧树脂是一种两部分混合物,由环氧树脂和固化剂组成。
当两者混合后,开始固化过程。
环氧树脂的固化过程可以分为以下几个阶段:
1. 混合:将环氧树脂和固化剂按照一定比例混合均匀,通常是根据厂家提供的配比进行混合。
2. 反应:混合后的环氧树脂和固化剂开始发生化学反应,形成交联结构。
这个阶段的时间可以根据使用的固化剂不同而有所差异。
3. 凝胶:在反应过程中,环氧树脂会逐渐变稠并形成凝胶状态。
在这个阶段,环氧树脂的流动性会逐渐减小。
4. 硬化:凝胶状态的环氧树脂最终会达到完全硬化的状态。
硬化的时间取决于环境温度和使用的固化剂类型。
5. 完全固化:经过一段时间,固化的环氧树脂会完全固化并变得坚硬。
此时,环氧树脂的性能会达到最佳状态。
需要注意的是,环氧树脂的固化过程中温度对固化速度会有影响。
通常,较高的温度可以加快固化速度,但过高的温度可能会导致环氧树脂变黄或产生气泡等问题。
因此,在固化过程中需控制好温度。
环氧树脂完全固化时间

环氧树脂完全固化时间1. 哎呀,说到环氧树脂的完全固化时间,那可真是个有意思的话题!这就像是等待一块糖果慢慢变硬的过程,不过可比糖果复杂多啦!2. 要说环氧树脂完全固化,那得分好几个阶段呢!刚开始的时候,它就像果冻一样,摸起来有点黏黏的,这时候可千万别着急,这才刚刚开始呢!3. 在常温下,也就是咱们平常说的室温环境,环氧树脂要完全固化通常需要7天左右。
你说这时间也太磨人了吧?就像守株待兔一样,得有足够的耐心!4. 温度可是个调皮的小家伙,它对固化时间的影响可大啦!要是温度高一点,比如在25到30度之间,固化速度就会快一些,就像是给树脂打了兴奋剂似的。
5. 要是温度低于15度,这固化过程就慢得像蜗牛爬步,可能得等上10天甚至更久。
所以冬天用环氧树脂,那可真是要考验人的耐心!6. 湿度这个小捣蛋鬼也会来凑热闹,要是湿度太大,固化时间就会被拖长,就像是给树脂穿了一件湿漉漉的衣服,怎么都干不了。
7. 有的小伙伴会问:为啥不能用吹风机加热让它快点固化呢?嘿嘿,这可不行!突然的高温会让树脂内部产生气泡,就像是煮沸的开水一样咕嘟咕嘟的,这可不是我们想要的效果。
8. 树脂厚度也是个关键因素,薄薄的一层可能3-5天就能完全固化,厚厚的一块可能得等上两周。
这就像是晒衣服,薄衣服干得快,厚棉袄就得多晒会儿。
9. 要想知道是不是完全固化了,可以用指甲轻轻按压表面。
要是一点印子都不留,硬得跟石头似的,那就说明大功告成啦!10. 有的朋友总想着偷懒,觉得摸着不黏手就行了。
可这样不行啊!表面固化不等于完全固化,就像煎饼表面金黄,里面还是生的一样。
11. 专业人士都建议,就算感觉已经固化了,也最好再多等个一两天。
这就像是煮饭,火关了之后还得焖一会儿才更香嘛!12. 总的来说啊,环氧树脂完全固化这事儿,真是考验人的耐心。
但只要你按照正确方法来,给足时间,就一定能得到理想的效果。
这可真像是在等待一个美丽的蝴蝶破茧而出,值得等待!。
单组分环氧树脂固化时间

单组分环氧树脂固化时间1. 简介单组分环氧树脂是一种常用的固化材料,广泛应用于涂料、粘合剂、复合材料等领域。
其固化时间是指从涂覆或混合后开始,到达所需强度或硬度的时间。
本文将详细介绍单组分环氧树脂固化时间的相关知识。
2. 固化过程单组分环氧树脂在固化过程中经历了几个阶段:流动期、凝胶期和硬化期。
2.1 流动期在涂覆或混合后,单组分环氧树脂首先进入流动期。
在这个阶段,树脂具有较低的粘度,可以自由地流动和填充空隙。
流动期的时间取决于环境温度、树脂种类和添加剂等因素。
2.2 凝胶期当单组分环氧树脂开始固化时,它逐渐从流动状态转变为凝胶状态。
在凝胶期,树脂的粘度大幅增加,开始形成网络结构。
凝胶期的时间也受到温度和树脂配方的影响。
2.3 硬化期硬化期是指单组分环氧树脂完全固化并达到所需强度或硬度的阶段。
在这个阶段,树脂网络结构进一步增强,形成坚固的材料。
硬化期的时间取决于环境温度、树脂配方、添加剂和所需强度等因素。
3. 影响因素单组分环氧树脂固化时间受到多种因素的影响,包括温度、湿度、添加剂和树脂配方等。
3.1 温度温度是影响单组分环氧树脂固化时间最重要的因素之一。
一般来说,较高的温度会加快固化过程,而较低的温度会延长固化时间。
这是因为高温可以提供更多能量,促进分子间反应和交联。
然而,过高的温度可能导致过快的固化速率,使操作变得困难。
3.2 湿度湿度对于某些单组分环氧树脂也具有一定影响。
某些树脂在高湿度环境下会吸湿,导致固化时间延长。
在湿度较高的环境中使用单组分环氧树脂时,需要注意调整配方或采取其他措施。
3.3 添加剂添加剂可以对单组分环氧树脂的固化时间产生显著影响。
催化剂可以加速固化过程,而抑制剂则可以延缓固化时间。
通过调整添加剂的种类和比例,可以灵活地控制固化时间以满足特定需求。
3.4 树脂配方不同的单组分环氧树脂配方也会对固化时间产生影响。
不同的材料比例和配方可以导致不同的反应速率和网络结构形成。
在选择树脂配方时,需要考虑所需的固化时间以及其他性能要求。
乙二胺交联固化环氧树脂的方程式
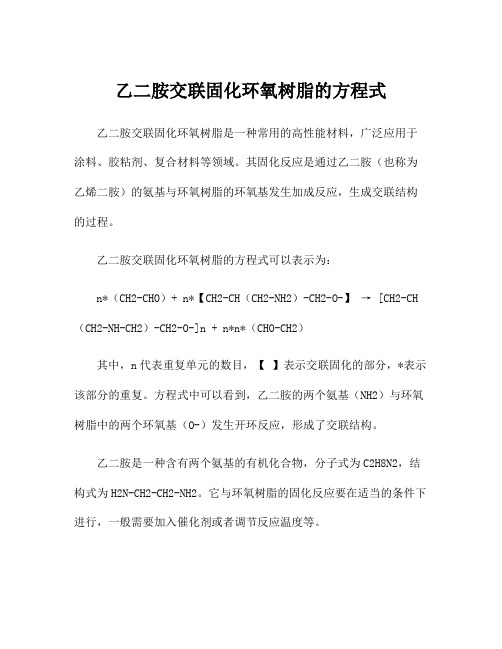
乙二胺交联固化环氧树脂的方程式乙二胺交联固化环氧树脂是一种常用的高性能材料,广泛应用于涂料、胶粘剂、复合材料等领域。
其固化反应是通过乙二胺(也称为乙烯二胺)的氨基与环氧树脂的环氧基发生加成反应,生成交联结构的过程。
乙二胺交联固化环氧树脂的方程式可以表示为:n*(CH2-CHO)+ n*【CH2-CH(CH2-NH2)-CH2-O-】→ [CH2-CH (CH2-NH-CH2)-CH2-O-]n + n*n*(CHO-CH2)其中,n代表重复单元的数目,【】表示交联固化的部分,*表示该部分的重复。
方程式中可以看到,乙二胺的两个氨基(NH2)与环氧树脂中的两个环氧基(O-)发生开环反应,形成了交联结构。
乙二胺是一种含有两个氨基的有机化合物,分子式为C2H8N2,结构式为H2N-CH2-CH2-NH2。
它与环氧树脂的固化反应要在适当的条件下进行,一般需要加入催化剂或者调节反应温度等。
乙二胺交联固化环氧树脂的反应过程可以分为三个阶段。
首先是乙二胺的两个氨基与环氧树脂的环氧基发生加成反应,生成一个氨基和一个醇基的中间产物。
这个中间产物会继续进行反应,通过两个醇基的缩聚作用,生成一个环氧的骨架结构。
最后,在适当的条件下,环氧骨架中的环氧基会与其他环氧骨架或乙二胺的氨基交联,形成交联结构。
乙二胺交联固化环氧树脂具有优异的性能。
交联结构赋予了其良好的热稳定性、化学稳定性和物理性能。
它具有较高的玻璃化转变温度、强度、刚度和耐候性,可以用于制备高性能复合材料,如航空航天领域的复合材料结构件。
此外,乙二胺交联固化环氧树脂还具有良好的粘附性能,可以作为胶粘剂,用于粘接各种材料。
总之,乙二胺交联固化环氧树脂的方程式描述了其固化反应过程,它是一种重要的高性能材料。
研究和应用乙二胺交联固化环氧树脂的性能和工艺条件,对于推动材料科学和工业技术的发展具有重要意义。
碳纤维环氧树脂固化
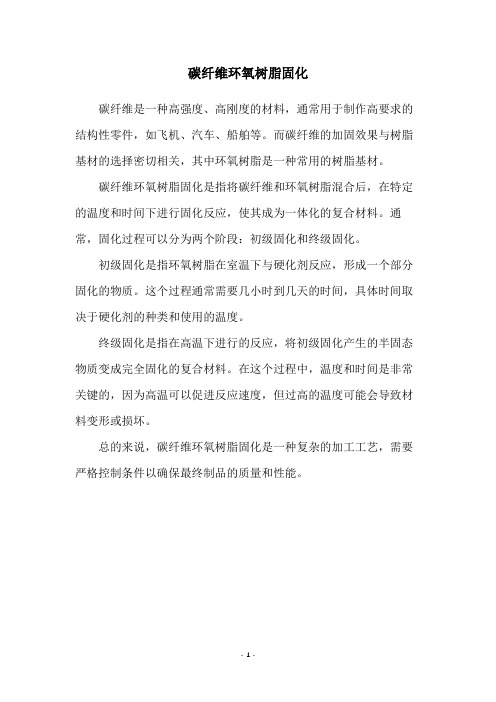
碳纤维环氧树脂固化
碳纤维是一种高强度、高刚度的材料,通常用于制作高要求的结构性零件,如飞机、汽车、船舶等。
而碳纤维的加固效果与树脂基材的选择密切相关,其中环氧树脂是一种常用的树脂基材。
碳纤维环氧树脂固化是指将碳纤维和环氧树脂混合后,在特定的温度和时间下进行固化反应,使其成为一体化的复合材料。
通常,固化过程可以分为两个阶段:初级固化和终级固化。
初级固化是指环氧树脂在室温下与硬化剂反应,形成一个部分固化的物质。
这个过程通常需要几小时到几天的时间,具体时间取决于硬化剂的种类和使用的温度。
终级固化是指在高温下进行的反应,将初级固化产生的半固态物质变成完全固化的复合材料。
在这个过程中,温度和时间是非常关键的,因为高温可以促进反应速度,但过高的温度可能会导致材料变形或损坏。
总的来说,碳纤维环氧树脂固化是一种复杂的加工工艺,需要严格控制条件以确保最终制品的质量和性能。
- 1 -。
环氧树脂固化两个放热峰
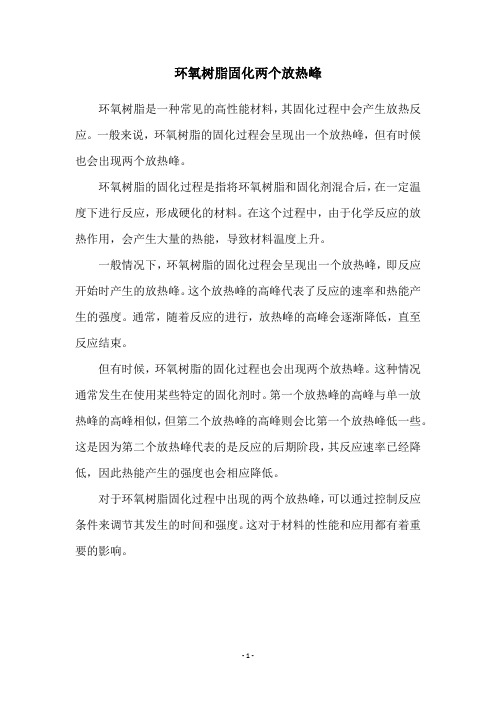
环氧树脂固化两个放热峰
环氧树脂是一种常见的高性能材料,其固化过程中会产生放热反应。
一般来说,环氧树脂的固化过程会呈现出一个放热峰,但有时候也会出现两个放热峰。
环氧树脂的固化过程是指将环氧树脂和固化剂混合后,在一定温度下进行反应,形成硬化的材料。
在这个过程中,由于化学反应的放热作用,会产生大量的热能,导致材料温度上升。
一般情况下,环氧树脂的固化过程会呈现出一个放热峰,即反应开始时产生的放热峰。
这个放热峰的高峰代表了反应的速率和热能产生的强度。
通常,随着反应的进行,放热峰的高峰会逐渐降低,直至反应结束。
但有时候,环氧树脂的固化过程也会出现两个放热峰。
这种情况通常发生在使用某些特定的固化剂时。
第一个放热峰的高峰与单一放热峰的高峰相似,但第二个放热峰的高峰则会比第一个放热峰低一些。
这是因为第二个放热峰代表的是反应的后期阶段,其反应速率已经降低,因此热能产生的强度也会相应降低。
对于环氧树脂固化过程中出现的两个放热峰,可以通过控制反应条件来调节其发生的时间和强度。
这对于材料的性能和应用都有着重要的影响。
- 1 -。
环氧树脂光固化机理

环氧树脂的光固化机理
环氧树脂的光固化机理主要基于其分子结构中不饱和双键对光引发剂吸收紫外光或可见光后产生的活性自由基的反应。
以下是具体的步骤:
1. 光引发剂吸收光能:
光固化过程中,首先需要添加特定的光引发剂,这类物质可以吸收紫外光或特定波长的可见光能量,从而被激发到激发态。
2. 光引发剂分解:
吸收了光能的光引发剂分子发生内部化学变化,从激发态跃迁回到基态时释放出足够的能量,使自身发生断裂,生成具有高活性的自由基或阳离子。
3. 链引发:
这些由光引发剂产生的自由基或阳离子与环氧树脂中的环氧基团(环氧基—O—C==C—R)进行反应,打开环氧环,形成一个新的碳中心自由基或阳离子,启动聚合链的增长过程。
4. 链增长:
新生成的碳中心自由基或阳离子能够迅速与树脂体系中未反应的
环氧基团结合,继续打开环氧环,并且不断重复这一过程,形成一个较长的聚合物链。
5. 链终止:
当两个带相反电荷的活性末端相遇时(对于阳离子聚合,可能是阴离子与阳离子;对于自由基聚合,则是自由基与自由基),会发生偶合或转移反应,从而终止链的增长。
或者,当自由基或阳离子捕获稳定剂(如氢原子、醇类等)时,也会导致链终止。
6. 交联网络形成:
通过上述链增长和链终止的过程,大量的环氧树脂分子彼此之间通过化学键连接起来,形成了三维立体的交联网络结构,实现材料的固化。
总的来说,环氧树脂光固化是一个由光引发剂在光的作用下产生自由基或阳离子引发环氧树脂交联固化成固体的过程。
这种固化方式速度快,效率高,无溶剂排放,环保性较好,广泛应用于涂料、胶粘剂、电子封装材料等领域。
环氧树脂粘合剂固化时间
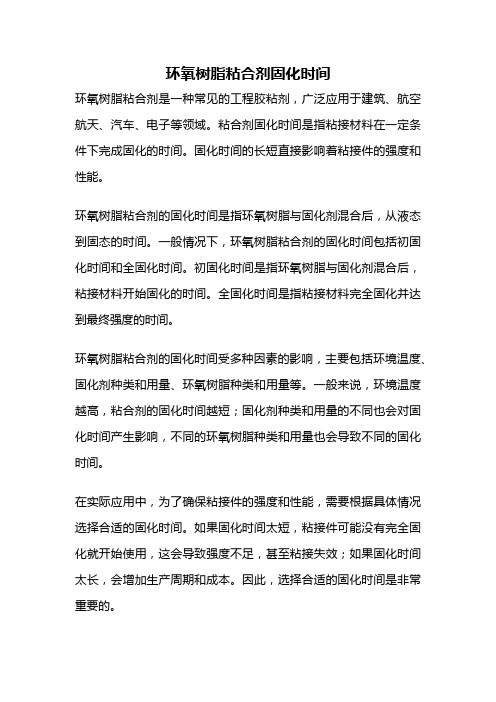
环氧树脂粘合剂固化时间环氧树脂粘合剂是一种常见的工程胶粘剂,广泛应用于建筑、航空航天、汽车、电子等领域。
粘合剂固化时间是指粘接材料在一定条件下完成固化的时间。
固化时间的长短直接影响着粘接件的强度和性能。
环氧树脂粘合剂的固化时间是指环氧树脂与固化剂混合后,从液态到固态的时间。
一般情况下,环氧树脂粘合剂的固化时间包括初固化时间和全固化时间。
初固化时间是指环氧树脂与固化剂混合后,粘接材料开始固化的时间。
全固化时间是指粘接材料完全固化并达到最终强度的时间。
环氧树脂粘合剂的固化时间受多种因素的影响,主要包括环境温度、固化剂种类和用量、环氧树脂种类和用量等。
一般来说,环境温度越高,粘合剂的固化时间越短;固化剂种类和用量的不同也会对固化时间产生影响,不同的环氧树脂种类和用量也会导致不同的固化时间。
在实际应用中,为了确保粘接件的强度和性能,需要根据具体情况选择合适的固化时间。
如果固化时间太短,粘接件可能没有完全固化就开始使用,这会导致强度不足,甚至粘接失效;如果固化时间太长,会增加生产周期和成本。
因此,选择合适的固化时间是非常重要的。
为了准确测量环氧树脂粘合剂的固化时间,可以使用各种测试方法,如差示扫描量热法(DSC)、动态机械分析法(DMA)等。
这些测试方法可以通过测量粘合剂样品的热性能和机械性能变化来确定固化时间。
为了加快环氧树脂粘合剂的固化时间,可以采取一些措施。
例如,可以通过增加固化剂的用量来加速固化反应;可以提高环境温度或者采用热固化的方式来加快固化速度。
当然,在进行这些操作时,需要根据具体情况进行调整,以确保固化反应的安全性和粘接件的质量。
环氧树脂粘合剂的固化时间是一个重要的参数,直接影响着粘接件的强度和性能。
通过选择合适的固化时间和采取相应的措施,可以确保粘接件具有良好的粘接效果和使用寿命。
同时,对于生产和工程应用中的环氧树脂粘合剂,对固化时间的准确测量和控制也是至关重要的,可以通过合适的测试方法和操作来实现。
环氧树脂固化的温度-黏度-时间的关系

环氧树脂固化的温度-黏度-时间的关系
环氧树脂体系的流变性质随时间发生改变具有一定的规律,对于浇注成型来说,这个规律相当重要。
经过试验证明,要想得到良好的混合和低压填充,环氧树脂体系的初始黏度应尽可能小,必须在固化点之前而黏度又不大的某一时间完成填充。
环氧树脂体系固化过程中动态黏度的变化规律为:当温度升高至100~ 120℃时,树脂的黏度逐渐减小,静置1小时左右的时间,其黏度可低于10-1pa·s,呈液态,(水的黏度1*10-3pa·s),随着温度增加到固化温度(125℃)以及反应时间的增加,体系的黏度也逐渐增加,趋于固化。
基于环氧树脂的上述特性,特将浇注体的固化曲线确定为。
- 1、下载文档前请自行甄别文档内容的完整性,平台不提供额外的编辑、内容补充、找答案等附加服务。
- 2、"仅部分预览"的文档,不可在线预览部分如存在完整性等问题,可反馈申请退款(可完整预览的文档不适用该条件!)。
- 3、如文档侵犯您的权益,请联系客服反馈,我们会尽快为您处理(人工客服工作时间:9:00-18:30)。
环氧树脂固化的三个阶段
液体-操作时间
操作时间(也是工作时间或使用期)是固化时间的一部份,混合之后,树脂/固化剂混合物仍然是液体和可以工作及适合应用。为了保证可靠的粘接,全部施工和定位工作应该在固化操作时间内做好。
凝胶-进入固化
混合物开始进入固化相(也称作熟化阶段),这时它开始凝胶或“突变”。这时的环氧没有时间的工作可能,也将失去粘性。在这个阶段不能对其进行任何干扰。它将变成硬橡胶似的软凝胶物,你用大拇指将能压得动它。
因为这时混合物只是局部固化,新使用的环氧树脂仍然能与它化学链接,因此该未处理的表面仍然可以进行粘接或反应。无论如何,接近固化的混合物这些能力在减小。深圳市鑫华良科技有限公司
固体-最终固化
环氧混合物达到固化变成固体阶段,这时能砂磨及整型。这时你用大拇指已压不动它,在这时环氧树脂约有90%的最终反应强度,因此可以除去固定夹件,将它放在室温下维持若干天使它继续固化。