汽车线束DFMEA实例
DFMEA案例分析方法

潜在失效模式
失效后果
严重度
潜在失效原因
失效模式1 组件1(具体包括那些零件) 失效模式2 … 失效模式1 组件2(具体包括那些零件) 失效模式2 … 功能2… 重要部件 如:外壳或本体 失效模式1 …
怎么失效,后果如何? 严重度多少? … … … …
原因1 原因2 … … 原因1 原因2 … … … 原因1 原因2
DFMEA分析方法-案例(8#喷枪) 组件 功能/组件 组件1(如进水组件) 功能1(爆破压500PSI) 功能2(110LBS拉脱力测试) 功能3(20-125psi功能正常) √ √ √ √ √ 组件2(如开关组件) √ 组件3(如出水组件)
功能/组件 例如:功能1…(爆破压500PSI) (涉及的组件:)
怎么失效,后果如何? 严重度多少? … … … … … …
怎么失效,后果如何? 严重度多少?
组件3(出水组件)
组件2(开关
DFMEA范例
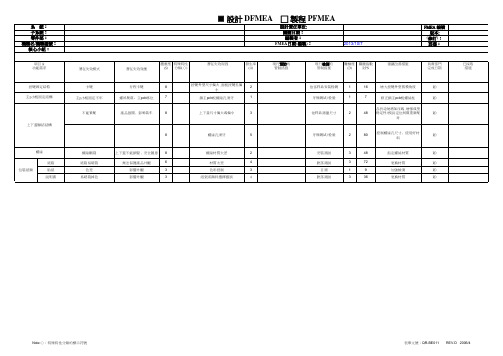
Note:◇:特殊特性分類的標示符號
表單文號:QR-BE011
REV.D 2006/4
MEA
□ 製程 PFMEA
A 1 of 1
嚴重度 發生率 難檢度 (S) (O) (D)
RPN
Note:◇:特殊特性分類的標示符號
表單文號:QR-BE011
REV.D 2006/4
潛在失效模式
潛在失效效應
現行預防的 管制措施
現行檢測的 管制措施
難檢度 (D)
關鍵指數 RPN
建議改善措施
負責部門 完成日期
已採取 措施
按键固定结构 主pcb板固定結構
卡键 主pcb板固定不牢
行程卡键 螺丝脱落,主pcb移位
8 7
按键外型尺寸偏大.面板按键孔偏 小 鎖主pcb板螺絲孔滑牙
2 1
依客样品安装检测 牙规测试/检验
1 1
16 7
增大按键外型拔模角度 修正鎖主pcb板螺絲柱 各折边处增加压线.增强成型 稳定性/模具定位间隙重新配 对
RD RD
不能紧配 上下蓋聯結結構
產品張開﹐影响装车
8
上下盖尺寸偏大或偏小
3
依样品測量尺寸
2
48
RD
8
螺絲孔滑牙絲孔尺寸﹐使用好材 料
RD
螺絲 紙箱 包裝紙類 貼紙 說明書
■ 設計 DFMEA
系 統: 子系統: 零件部: 機種名/機種編號: 核心小組:
項目 & 功能需求 嚴重度 特殊特性 (S) 分類(◇) 潛在失效原因 發生率 (O)
□ 製程 PFMEA
設計責任單位: 關鍵日期: 編製者: FMEA日期 (編製 ): 2013/10/7 FMEA 編號 版本: (修訂 ): 頁碼: A 1 of 1
汽车电器线束DFMEA范例

设计责任负责工程师修订日期关键日期确认采取行动SODRPN容许电流不足线束烧毁,不符合安规要求10电线线径选用错误5按用电器功率选用线材规格3150核对各用电器实际电流与最大电流,选用适合电线过负载测试103390短路线束烧毁,不符合安规要求10PIN定义错误,正负电有短接5绘制原理图,区分正负电回路3150实际搭配用电器验证总装测试102240低温脆化绝缘层破坏,短路9材质问题3低温试验381低温试验高温变形绝缘层破坏,短路9材质问题3高温试验381高温试验绝缘耐压不良安全隐患10胶料材质问题3高压测试390高压测试长度长度不足或过长装配后拉扯受力6尺寸定义错误4装配确认496阻燃性能不足不符合安规要求10材质问题3阻燃测试390阻燃测试阻燃测试103390非金属材料雾化超标不符合安规要求9材质问题3非金属材料雾化性试验381非金属材料雾化性试验非金属材料雾化性试验93381气味过大不符合安规要求9材质问题3气味试验381气味试验气味试验93381VOC超标不符合安规要求9材质问题3VOC检测381VOC检测VOC检测93381行动的结果项目严重性潜在缺陷原因建议措施制作核准潜在缺陷模式潜在缺陷影响设计失效模式和影响分析(DFMEA)项目FMEA 编号:责任人/完成日期功能性能材料线材核心团队发生频率预防的方法可侦测性RPN FMEA 初始日期:有害物质超标不符合安规要求9材质问题3禁限用物质检测381禁限用物质检测禁限用物质检测93381颜色装配时插错影响产品导电功能7颜色设定相近3选用对比明显的线色484容许电流不足线束烧毁,不符合安规要求8端子规格选用错误5按用电器功率选用线材规格3120核对各用电器实际电流与最大电流,选用适合端子过负载测试83372接触电阻过大接触性能不足8端子镀层选用错误2按端子规格书选型并测试电压降580按端子规格书选型并测试电压降盐雾后接触不良接触性能不足8端子镀层不良2盐雾测试580盐雾测试材料有害物质超标不符合安规要求9材质问题3禁限用物质检测381禁限用物质检测0型号与端子规格不符无法装配,无法满足电流要求7选型错误2按护套规格书选型2280绝缘耐压不良安全隐患10胶料材质问题3高压测试390高压测试阻燃性能不足不符合安规要求10材质问题3阻燃测试390阻燃测试阻燃测试103390非金属材料雾化超标不符合安规要求9材质问题3非金属材料雾化性试验381非金属材料雾化性试验非金属材料雾化性试验93381气味过大不符合安规要求9材质问题3气味试验381气味试验气味试验93381 VOC超标不符合安规要求9材质问题3VOC检测381VOC检测VOC检测93381有害物质超标不符合安规要求9材质问题3禁限用物质检测381禁限用物质检测禁限用物质检测93381端子护套导电性能材料粘性粘性不足影响产品外观与尺寸7粘胶剂粘性不足3粘性测试242试验验证0强度易断裂影响产品外观与尺寸7胶布材质问题3强度测试363阻燃性能不足不符合安规要求10材质问题3阻燃测试390阻燃测试阻燃测试103390非金属材料雾化超标不符合安规要求9材质问题3非金属材料雾化性试验381非金属材料雾化性试验非金属材料雾化性试验93381气味过大不符合安规要求9材质问题3气味试验381气味试验气味试验93381VOC超标不符合安规要求9材质问题3VOC检测381VOC检测VOC检测93381有害物质超标不符合安规要求9材质问题3禁限用物质检测381禁限用物质检测禁限用物质检测93381位置与安装位置不符影响产品固定6位置设定错误3装配确认3540强度易断裂影响产品固定6扎带材质问题3强度测试472阻燃性能不足不符合安规要求10材质问题3阻燃测试5150阻燃测试阻燃测试103390非金属材料雾化超标不符合安规要求9材质问题3非金属材料雾化性试验5135非金属材料雾化性试验非金属材料雾化性试验93381气味过大不符合安规要求9材质问题3气味试验5135气味试验气味试验93381VOC超标不符合安规要求9材质问题3VOC检测5135VOC检测VOC检测93381胶布扎带材料材料。
质量管理工具--DFMEA的案例分析

质量管理工具--DFMEA的案例分析DFMEA是一种以预防为主的可靠性设计分析技术,该技术的应用有助于企业提高产品质量,降低成本,缩短研发周期。
目前,DFMEA已在航空航天以及国外的汽车行业得到了较为广泛的应用,并显示出了巨大的威力;但在国内汽车行业并没有系统地展开,也没有发挥其应有的作用。
以DFMEA在国产汽油机节流阀体的改进设计中的实施为例,对改进后的DFMEA的实施方法和流程进行阐述。
发动机为完成其相应的功能,组成结构复杂,零部件的数量也很庞大,如不加选择地对所有的零部件和子系统都实施DFMEA,将会耗费大量人力、物力和时间,对于初次实施DFMEA的企业几乎是不可能完成的工作。
为此,需要开发一种方法,能够从发动机的子系统/零部件中选择出优先需要进行分析的对象。
发动机由曲柄连杆机构、配气机构、燃油供给系统、进气系统、冷却系统和润滑系统等组成,各机构和系统完成相应的功能。
子系统的下级部件或组件通常需要配合完成相应的功能,在描述这些部件或组件的功能时,不仅应该描述其独立完成的功能,还应描述与其他部件配合完成的功能。
组成发动机的零部件种类很多,不仅包括机械零部件还有电子元件,电子部件的故障模式已经较为规范和完整,但机械系统及其零部件的故障模式相当复杂,不仅没有完整且规范的描述,二者之间还有一定的重复,为DFMEA工作的开展带来了困难,故需要为机械系统及其零部件建立相应的故障模式库。
实施DFMEA的准备工作由于在发动机设计中实施DFMEA要遇到较多困难,故作者建议,在具体实施DFMEA之前,需要做好建立较为完善的故障模式库并确定DFMEA的详细分析对象等准备工作。
1.建立故障模式库的方法发动机的组成零部件多、结构复杂,大多数零部件在运行时还会有相互作用,导致零部件、子系统和系统的故障模式不仅复杂,各层次的故障模式还会相互重复,需要为发动机建立一个故障模式库;该模式库不仅应该包含发动机中所有子系统和零部件的故障模式,还能够反映出该故障模式究竟属于哪一个零部件或系统,其建模流程如下图所示。
DFMEA经典案例

DFMEA经典案例潜在失效模式及后果分析设计FMEA系统FMEA编号: 1234(1)子系统页码:第1页共1页(2)零组件: 01.03车身密封(2)责任部门:车身工程师(3)编制者: A。
Tate–X6412–车身工程师(4)车型年/车辆类型:199X/狮牌4门/旅行车(5) 关键日期:9X.03.01(6)FMEA日期: (编制)8X.03.22(修订)8X.07.14(7)核心小组:T.Fender–汽车产品部、C.___(___)(8)潜在失效模式:车门寿命降低,导致漆面生锈,使客户对外观不满;损害车门内附件之功能;车门内板之上方边缘保护蜡喷涂太低,蜡层厚度规定不足。
失效后果:1.降低车门寿命,导致漆面生锈,使客户对外观不满。
2.损害车门内附件之功能。
3.车门内板之上方边缘保护蜡喷涂太低,蜡层厚度规定不足。
起因/机理:1.车门内板之上方边缘保护蜡喷涂太低,蜡层厚度规定不足。
2.车门内板之上方边缘保护蜡配方不当,混入的空气阻止蜡进入边角/边缘部分。
探风险:控制整车耐久性试验T-118、T-109、T-301及整车耐久性试验-同上294.措施执行结果:增加试验室加速腐蚀试验,根据试验结果上方喷涂规定提高125mm,采取的措施增加试验室加速腐蚀试验结合试验对蜡的验证,就蜡层厚度进行设计试验分析,厚度在25%范围内变化,可以接受。
建议措施:1.提供适当的表面处理项。
2.用功能不彰的喷头进行设计辅助调查。
责任和目标完成日期:项目功能:左前车门车门内板下部。
零组件:H8HX-0000-上、下车。
失效模式:A腐蚀。
后果:保护乘员免受天气、噪声、侧碰撞的影响;车门附件,如后视镜、门铰链、门锁、及门窗升降器等的固定支撑。
物理和化学试验报告编号:1265.无。
小幅度改写:无需改写。
系统总成DFMEA分析范例

系统:H06后视镜总成设计责任:子系统:关键日期:部件:车辆项目:团队:镜面曲率半径选择错误由于车门数据的改变,造成主机厂提供的线框数据中镜面位置不正确后视镜应满足GB15084-2013规定的反射率(≥80%)镜面太暗驾驶员看后视野时不清晰7●镜面反射率选择错误后视镜应满足GB15084-2013规定的(平均SR误差≤12.5%)镜面变形驾驶员看后视野时感觉不舒服7●镜面烤弯变形要求无未预期的风噪风噪过大或难听用户感觉刺耳不舒适3外形造型不好或镜壳与背盖间隙过大后视镜应耐腐蚀后视镜内金属件锈蚀后视镜内部零件外观不良2材料选择或表面处理不当在高温作用下,后视镜零部件(如塑料件、电机等)产生变形后视镜功能减弱或丧失(如镜面移位、不可调节/折叠、抖动等)6材料选择不合理在低温作用下,后视镜零部件(如塑料件、镜面等)产生开裂、变形等后视镜功能减弱或丧失(如镜面松动、不可调节/折叠、抖动等)6材料选择不合理部件/功能后视镜应满足GB15084-2013规定的视野视野范围小于国标GB15084-2013规定整车视野不合格或视野有盲区,不能上国家目录8●设计 FMEA H06后视镜应耐高温、低温和高湿度环境潜在失效模式失效的潜在影响严重度分级失效的潜在原因/机制在高温高湿度环境下,后视镜零部件(如塑料件、镜面等)产生开裂、变形等后视镜功能减弱或丧失(如镜面松动、不可调节/折叠、抖动等)6材料选择不合理后视镜应能耐冷热冲击在高温低温交变冲击的环境下,后视镜零部件(如塑料件、镜面等)产生开裂、变形等后视镜功能减弱或丧失(如镜面松动、不可调节/折叠、抖动等)6材料选择不合理镜杆应与镜臂牢固连接镜杆和镜臂配合和设计数据不符。
1:后视野模糊 。
2:后视镜镜壳与背盖,主镜和广角镜,镜头与镜臂之间的配合间隙不能满足要求。
6镜杆和镜臂配合设计不合理后视镜镜头能可靠折叠且折叠力适中镜头折叠力过大或过小折叠力过大:有外力撞击时不易折叠;折叠力过小:行车时易抖动7●下支座定位柱弹簧工作压力过大或过小对电调总成:电调镜面的手动调节力过小行车时镜头易抖动而使后视野模糊5电机选型不当,其承载力过小镜面托板分总成拔脱力过小或感觉到横向空程镜面易脱落或抖动,无镜面或后视野模糊7托板与电机卡簧配合不合理镜头应能经受反复折叠而保持折叠功能镜头反复折叠后有空程或折叠力明显下降,行车时镜头易抖动后视镜使用一段时间后,行车时镜头易抖动视野模糊4下镜臂的凹槽与支座上的凸台直接接触,在镜头折叠时被磨损电机工作及卡止时噪声可接受电调后视镜调节噪声过大用户感觉刺耳不舒适3调节电机选型不当6数模转换误差导致数据设计失误6车身冲压件存在反弹主机厂对后视镜装配的外观效果不满意镜面能够稳定连接在镜壳中,并能进行各方向的最小8度的调节支座分总成与车身安装后外观效果应良好后视镜安装在车身上后,上下支座与车身存在断差、间隙、错位等温、低温和高湿度环境6●支座安装尺寸错误电机与基板/广角镜壳装配完好电机与基板/广角镜壳配合安装孔径不正确电机无法安装6电机安装孔径比基板/广角镜壳安装孔大基板和广角镜壳准确定位广角镜壳与镜杆相对位置偏差广角镜头与其他相配合的零件配合间隙失控6广角镜头和镜杆没有自动找正结构基板和镜杆准确定位基板与镜杆相对位置偏差主镜头与其他相配合的零件配合间隙失控6基板和镜杆没有自动找正结构镜壳与托板在调节到极限角度时有干涉电机选择不合理为镜面提供电动调节功能使用一定时间后电机调节功能失效驾驶员无法利用镜面调节开关控制镜面4电机选择不合理配的外观效果不满意主镜面调节角度在各个方向均达到8度以上主镜面分总成调节角度不够有的驾驶员看不到符合法规要求的视野5车身安装后外观效果应良好上后,上下支座与车身存在断差、间隙、错位等FMEA 号:准备人员:FMEA 日期:根据GB15084-2013规定选择曲率半径:1.主镜面/SR1200+300。
DFMEA实际案例

1
18
6
铁芯公差不合理,偏 大导致同骨架间隙过 小,移动困难
1
来料外径检查
4
24
动铁芯腐蚀,导致铁 锈碎屑堵塞动作通道
动铁芯表面做涂层处理
盐雾??或其他类 似实验去验证动铁 芯的耐腐蚀性??
动铁芯无法动 作
6
铁芯导磁性差,线圈 实际电磁感应力过小
2
不同材质铁芯在同样的线圈下的 电磁感应力测试确定选用的材料 ON-OFF启动特性测 材料使用 试(驱动电压) 使用纯铁DT4制作(导磁率...)
2
24
6
铁芯表面过粗糙,同 支架表面摩擦阻力过 大
3
1.表面涂层选择(聚四氟乙 烯),减小摩擦阻力(参考样 来料表面平整度检 品) 查 2.要求铁芯表面无毛刺,锐角采 涂层完整性检查 取倒钝处理 铁芯设计负公差,50.07/0.09mm 线圈骨架内径正公差,5 +0/0.05mm 通过二者配合防止间隙过小
表单编号:
潜在失效模式及后果分析(设计 FMEA)
FMEA编号 部件 设计责任 关键日期 多功能小组 风 险 顺 序 数 RPN 2012.1.20 第 1 页 共 页 修订 施 结 严 频 重 度 度 O S 果 探 测 度 D 风 险 顺 序 数 RPN
车型/车辆类型 核心小组 项 目 潜在失效模式 功 能 气路无法完成闭 合,怠速通道无 法开启或关闭 潜在失效后果
编 制 人 FMEA日期(编制) 措 建 措 议 施 责任及目标 完成日期
严 重 度 S
级 别
潜在失效 起因/机理
频 数 O
现行设计控制预防
现行设计 控制探测探 测 度 D采 Nhomakorabea的 措 施
动铁芯组件 由动铁芯, 平垫片,橡 胶垫片,铝 帽组成 通过动铁芯 在电磁力和 弹簧力作用 下带动橡胶 垫片对节流 阀对应空气 回路行程开 关控制 动铁芯: 由电磁力驱 动的组件, 带动相关附 着件
DFMEA-电气-发动机搭铁线束

系统电器子系统线束零部件xxx过程责任:关键日期:核心小组:系统电器潜在车型/车辆类型:跨界SUV零部件xxx过程责任:车型/车辆类型:跨界SUV关键日期:核心小组:子系统线束零部件xxx过程责任:关键日期:核心小组:系统电器潜在车型/车辆类型:跨界SUV零部件xxx过程责任:关键日期:核心小组:系统电器潜在左前门线车型/车辆类型:跨界SUV零部件xxx过程责任:关键日期:核心小组:系统电器子系统线束潜在车型/车辆类型:跨界SUV零部件xxx过程责任:关键日期:核心小组:系统电器潜在车型/车辆类型:跨界SUV子系统线束零部件xxx过程责任:车型/车辆类型:跨界SUV关键日期:核心小组:潜在失效模式及后果分析(设计FMEA)编制人:FMEA日期(编制):文件编号:潜在失效模式及后果分析(设计FMEA)编制人:FMEA日期(编制):文件编号:潜在失效模式及后果分析(设计FMEA)编制人:FMEA日期(编制):文件编号:潜在失效模式及后果分析(设计FMEA)前门线束编制人:FMEA日期(编制):文件编号:潜在失效模式及后果分析(设计FMEA)编制人:FMEA日期(编制):文件编号:潜在失效模式及后果分析(设计FMEA)编制人:FMEA日期(编制):文件编号:潜在失效模式及后果分析DFMEA编制人:FMEA日期(编制):文件编号:(修订):共7页第1页(修订):共7页第2页附件6共7页3页(修订):0附件6共7页第4页(修订):0附件6共7页第5页(修订):0附件6共7页第6页(修订):0附件6共7页第7页(修订):0。
- 1、下载文档前请自行甄别文档内容的完整性,平台不提供额外的编辑、内容补充、找答案等附加服务。
- 2、"仅部分预览"的文档,不可在线预览部分如存在完整性等问题,可反馈申请退款(可完整预览的文档不适用该条件!)。
- 3、如文档侵犯您的权益,请联系客服反馈,我们会尽快为您处理(人工客服工作时间:9:00-18:30)。
德信诚培训网
汽车线束潜在失效模式及后果分析
(设计FMEA)
FMEA编号: DF3001B 第1页,共 3页项目
功能潜在失效模式潜在失效后果
严
重
度
S
级
别
潜在失效起
因/机理
频
度
O
现行设计
控制预防
现行设计
控制探测
探
测
度
R
P
N
建议措施
责任及目标完
成日期
措施结果
采取的措施S O D
R
P
N
汽车线·传输电能·传递信号绝缘热收缩严重
高温使用条件下
热收缩过大使导
体端部裸露客户
不满意
6
绞向绞距设
计过大
3 热收缩试验
4 72 无
6
选用绝缘材
料不当
3 热收缩试验
4 72 无绝缘不耐刮磨
车辆在运行中产
生的震动摩擦使
导线绝缘损坏而
发生短路
7 ▲
选用绝缘材
料不当
2 刮磨试验 4 64 无
绝缘沾到润滑油
或燃料油时发生
溶胀
车辆运行时润滑
油和燃料油溅到
线材表面时使
PVC溶胀,绝缘
耐压不良
6
选用绝缘材
料不当
2
耐油试验
耐燃料试验
4 48 无
长时间高温后线材绝缘发生开裂运行在高温仪表
区线材发生开裂
易对金属发生放
电,使部分仪表
指示不灵敏
7
选用绝缘材
料不当
2 过热试验 4 56 无
长时间高温后线材绝缘在压力下发生变形过大运行在高温仪表
区线材变形过大
易使绝缘电阻过
低漏电流过大,
使部分仪表指示
不灵敏
7
选用绝缘材
料不当
2
绝缘和护套
高温压力试
验
4 56 无
汽车线·传输电能·传递信号长时间低温后线
材绝缘发生开裂
绝缘在冬季发生
开裂,易对金属
发生放电,使部
分仪表指示不灵
敏
7
选用绝缘材
料不当
2
低温卷绕试
验、低温冲
击试验
4 56 无绝缘电阻低
绝缘漏电流过
大,使电能衰减
严重,使部分仪
表指示不灵敏
7
绝缘层最小
厚度规定不
足
3
绝缘电阻
试验
3 63 无导体电阻过大
导线长时间运行
产生热量过多加
速绝缘老化
6
导体根数/
单根直径设
计不当,导
体截面积过
小
2
导体电阻试
验
3 36 无耐电压过低
绝缘容易被击穿
使指示仪表不灵
敏
7 ▲
选用绝缘材
料不当
2
30min工频
交流电压试
验和击穿电
压试验
3 42 无。