注塑问题研究
注塑品质问题总结范文

一、前言注塑工艺在塑料制品的生产中占据着重要的地位,然而,在注塑生产过程中,品质问题时有发生,严重影响了产品的质量和企业的声誉。
为了提高注塑产品的品质,减少品质问题的发生,现将我司近期注塑品质问题进行总结分析,并提出改进措施。
二、品质问题总结1. 产品外观缺陷(1)表面有油污、划痕、气泡等。
(2)产品尺寸不稳定,存在较大公差。
2. 产品内部缺陷(1)产品内部有空洞、缩孔、熔接痕等。
(2)产品内部有冷料、飞边等杂质。
3. 材料问题(1)原材料质量不稳定,导致产品性能波动。
(2)材料配比不当,影响产品性能。
4. 设备问题(1)模具设计不合理,导致产品缺陷。
(2)设备磨损严重,影响产品质量。
5. 操作问题(1)操作人员技能水平不足,导致产品品质下降。
(2)生产过程不规范,存在安全隐患。
三、原因分析1. 原材料问题:原材料质量不稳定,供应商管理不到位。
2. 设备问题:设备维护保养不及时,模具设计不合理。
3. 操作问题:操作人员技能水平不足,生产过程不规范。
4. 管理问题:品质管理制度不完善,缺乏有效的监督机制。
四、改进措施1. 优化原材料采购流程,提高原材料质量。
2. 加强设备维护保养,确保设备正常运行。
3. 提高操作人员技能水平,规范生产过程。
4. 完善品质管理制度,加强监督机制。
5. 加强与供应商的沟通与合作,提高原材料质量。
五、总结通过本次注塑品质问题总结,我司将针对存在的问题,采取有效措施进行改进。
在今后的生产过程中,我们要高度重视注塑品质问题,不断提高产品质量,以满足客户需求,提升企业竞争力。
同时,要加强员工培训,提高整体素质,确保生产过程规范化、标准化。
相信在全体员工的共同努力下,我司的注塑品质一定会得到全面提升。
注塑车间问题点和改善对策

在注塑车间,可能会遇到各种问题,这些问题在生产过程中需要特别关注并寻求相应
的改善对策。
以下是常见的问题点以及相应的改善措施:
1. 产品质量问题:在注塑过程中,可能会出现短射、翘曲、裂纹、瑕疵等质量问题。
要改善这些问题,首先要进行原因分析,如模具设计、注塑工艺参数和原材料等。
针
对性地对问题进行调整(如调整注塑速度、压力、温度等),并进行严格的质量控制。
2. 设备故障:"机器、模具和辅助设备可能都会发生故障。
正确的维护和保养是防止故障的关键,例如定期检查润滑系统、更换磨损零件、定期清洁模具等。
3. 低生产效率:提高生产效率是提升注塑车间竞争力的关键。
改善方法包括:减少模
具更换和调试时间、采用自动化设备减少人工干预、优化生产排程和工艺参数等。
4. 浪费问题:在注塑过程中,可能会产生原材料、能源和人力等方面的浪费。
合理安
排生产计划、提高原材料利用率、节约能源(如优化加热和制冷系统)等措施,可以
降低浪费并提高整体效益。
5. 安全问题:注塑车间的生产安全非常重要,包括操作安全、消防安全、职业健康等
方面。
加强员工培训,提高安全意识和操作技能;确保车间内部的通风、照明和消防
等条件良好;合理布局生产线,以避免安全隐患。
6. 人员问题:员工流动性、技能短缺等问题可能影响注塑车间的生产效率和质量。
通
过制定合理的员工福利、培训和晋升政策,可以提高员工满意度和职业素养,从而提
高生产效果。
综上所述,在面对注塑车间的各种问题时,应想方设法地改进生产流程、提高效率和
质量、确保安全,并充分关注员工的发展及满意度。
注塑常见缺陷和原因分析
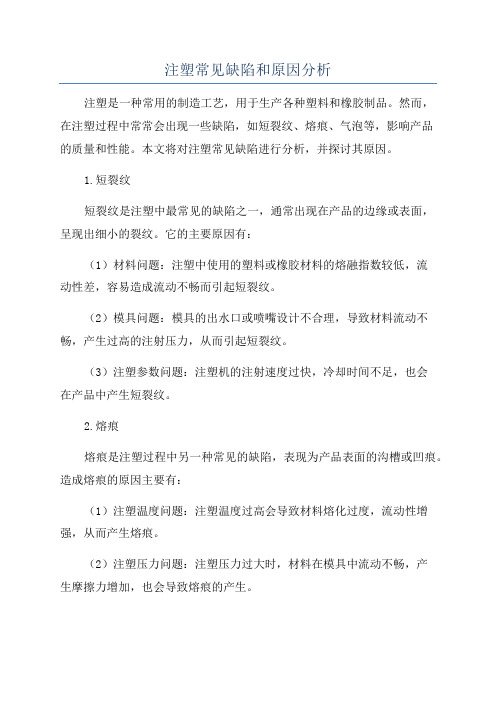
注塑常见缺陷和原因分析注塑是一种常用的制造工艺,用于生产各种塑料和橡胶制品。
然而,在注塑过程中常常会出现一些缺陷,如短裂纹、熔痕、气泡等,影响产品的质量和性能。
本文将对注塑常见缺陷进行分析,并探讨其原因。
1.短裂纹短裂纹是注塑中最常见的缺陷之一,通常出现在产品的边缘或表面,呈现出细小的裂纹。
它的主要原因有:(1)材料问题:注塑中使用的塑料或橡胶材料的熔融指数较低,流动性差,容易造成流动不畅而引起短裂纹。
(2)模具问题:模具的出水口或喷嘴设计不合理,导致材料流动不畅,产生过高的注射压力,从而引起短裂纹。
(3)注塑参数问题:注塑机的注射速度过快,冷却时间不足,也会在产品中产生短裂纹。
2.熔痕熔痕是注塑过程中另一种常见的缺陷,表现为产品表面的沟槽或凹痕。
造成熔痕的原因主要有:(1)注塑温度问题:注塑温度过高会导致材料熔化过度,流动性增强,从而产生熔痕。
(2)注塑压力问题:注塑压力过大时,材料在模具中流动不畅,产生摩擦力增加,也会导致熔痕的产生。
(3)模具设计问题:如果模具中的出水口或喷嘴设计不合理,也会在产品表面形成熔痕。
3.气泡气泡是注塑中常见的缺陷,表现为产品内部或表面的空腔。
气泡的形成原因有:(1)材料问题:注塑材料中含有过多的水分或挥发性物质,注塑过程中被加热蒸发,生成气泡。
(2)注塑温度过高:高温会导致材料熔化过度,容易产生气泡。
(3)注塑压力问题:过高的注塑压力会使材料在注塑过程中产生剧烈的振动,从而引起气泡。
(4)模具问题:模具中存在堵塞或不良的冷却系统,也会导致气泡的产生。
4.缩短问题缩短是指产品在冷却过程中出现尺寸缩小的现象。
产生缩短的主要原因有:(1)注塑温度过低:低温会使注塑材料的熔融程度不足,流动性降低,产生缩短。
(2)冷却时间不足:注塑材料冷却时间不足会导致产品未完全固化,容易产生缩短。
(3)注塑压力问题:过大的注塑压力会使产品产生内部的应力,引起尺寸缩小。
(4)模具问题:模具中存在过多的冷却系统,会导致材料过度冷却而使产品缩短。
模具注塑常见问题及解决方法

模具注塑常见问题及解决方法模具注塑是一种常见的制造工艺,广泛应用于汽车、电子、家电等行业。
然而,在注塑过程中常会遇到一些问题,例如产品质量不合格、生产效率低下等。
本文将针对这些常见问题进行分析,并提出相应的解决方法。
1. 产品尺寸不准确产品尺寸不准确是模具注塑过程中常见的问题之一。
造成尺寸不准确的原因可能有很多,例如模具设计不合理、注塑机调试不当等。
解决这个问题的方法是对模具进行优化设计,确保模具的尺寸精度和稳定性;同时,对注塑机进行精确调试,保证注塑过程的准确性。
2. 产品表面缺陷产品表面缺陷是另一个常见的问题,例如气泡、痕迹、烧焦等。
这些表面缺陷会影响产品的外观和质量。
要解决这个问题,可以从以下几个方面入手:优化模具通气系统,确保注塑过程中的气体能够顺利排出;调整注塑参数,控制注塑温度和压力,避免过高或过低造成烧焦或气泡;定期清洁模具,防止灰尘和杂质对产品表面造成影响。
3. 模具磨损严重模具在长期使用过程中会出现磨损,导致产品尺寸不准确或者产生其他问题。
要解决这个问题,可以采取以下几种措施:定期对模具进行保养和维护,及时更换磨损严重的零部件;使用高质量的模具材料,提高模具的耐磨性;注塑过程中控制好注塑温度和压力,避免过高过低造成模具磨损。
4. 注塑机故障注塑机故障是导致生产效率低下的主要原因之一。
为了避免注塑机故障,可以采取以下几个措施:定期对注塑机进行维护和保养,清洁注塑机内部的杂质和积聚物;使用高质量的注塑机零部件,避免因零部件质量差导致故障;培训操作人员,提高其对注塑机的操作技能和维修能力。
5. 塑料材料选择不当塑料材料的选择对注塑产品的质量和性能有很大影响。
如果选择的塑料材料不合适,可能会导致产品强度不足、耐热性差等问题。
因此,在进行模具注塑之前,应仔细选择合适的塑料材料,根据产品的要求和使用环境来进行选择。
6. 生产成本过高生产成本过高是许多企业关注的问题。
要降低生产成本,可以从以下几个方面入手:优化模具设计,减少材料的浪费;提高注塑机的效率,减少能耗;采用高效的生产工艺,提高生产效率。
注塑缺陷原因分析与解决方案
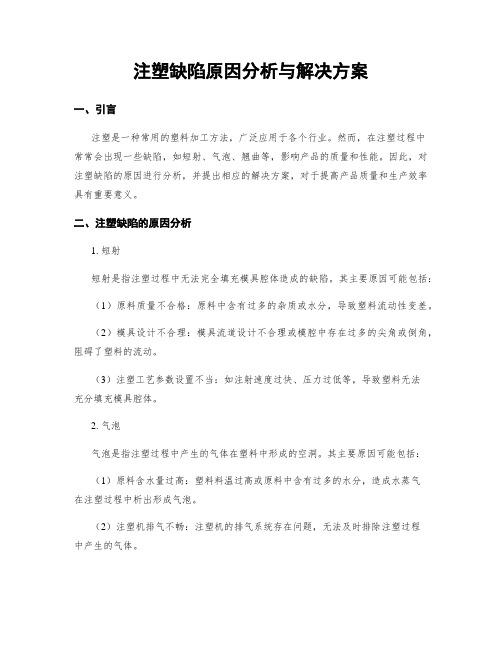
注塑缺陷原因分析与解决方案一、引言注塑是一种常用的塑料加工方法,广泛应用于各个行业。
然而,在注塑过程中常常会出现一些缺陷,如短射、气泡、翘曲等,影响产品的质量和性能。
因此,对注塑缺陷的原因进行分析,并提出相应的解决方案,对于提高产品质量和生产效率具有重要意义。
二、注塑缺陷的原因分析1. 短射短射是指注塑过程中无法完全填充模具腔体造成的缺陷。
其主要原因可能包括:(1)原料质量不合格:原料中含有过多的杂质或水分,导致塑料流动性变差。
(2)模具设计不合理:模具流道设计不合理或模腔中存在过多的尖角或倒角,阻碍了塑料的流动。
(3)注塑工艺参数设置不当:如注射速度过快、压力过低等,导致塑料无法充分填充模具腔体。
2. 气泡气泡是指注塑过程中产生的气体在塑料中形成的空洞。
其主要原因可能包括:(1)原料含水量过高:塑料料温过高或原料中含有过多的水分,造成水蒸气在注塑过程中析出形成气泡。
(2)注塑机排气不畅:注塑机的排气系统存在问题,无法及时排除注塑过程中产生的气体。
(3)注塑工艺参数设置不当:如注射速度过快、压力过高等,造成塑料内部气体无法顺利排出。
3. 翘曲翘曲是指注塑制品在冷却后出现变形的现象。
其主要原因可能包括:(1)模具温度不均匀:模具温度不均匀导致注塑制品冷却不均匀,从而引起翘曲。
(2)注塑过程中的应力积累:注塑过程中,塑料在注射后会受到冷却和收缩的影响,如果释放不及时,会导致应力积累引起翘曲。
(3)注塑工艺参数设置不当:如注射速度过快、冷却时间过短等,造成塑料冷却不充分,引起翘曲。
三、注塑缺陷的解决方案1. 短射的解决方案(1)优化原料质量:选择质量合格的原料,避免杂质和水分的存在。
(2)优化模具设计:合理设计模具流道,避免尖角和倒角的存在,保证塑料的顺畅流动。
(3)优化注塑工艺参数:合理设置注射速度和压力,确保塑料能够充分填充模具腔体。
2. 气泡的解决方案(1)控制原料含水量:确保塑料料温适宜,原料中的水分含量符合要求。
注塑过程中存在的问题及解决办法

注塑过程中存在的问题及解决办法在注塑过程中,可能会出现一些问题,影响产品的质量和生产效率。
下面列举一些常见的问题及解决办法:1. 热熔物质不充分:热熔物质的充填不充分可能会导致制品的短射或缩水等问题。
解决办法是检查喂料系统,确保熔料能够充分填充模具的所有空间,同时调整熔融温度和压力以适应具体材料和模具的要求。
2. 热熔物质的脱模性差:脱模性差可能导致产品拉伸、变形、形状不完整等问题。
解决办法是优化注塑工艺参数、或改进模具设计,增加脱模剂的使用量,确保热熔物质能顺利脱模。
3. 模具磨损严重:在长时间使用后,模具可能会出现磨损,导致制品尺寸偏差增大、质量下降。
解决办法是定期检查模具状态,必要时进行维护和修复,并妥善保养模具,延长使用寿命。
4. 模内气泡和气体线:模具填充时,可能会产生气泡或气体线,这会对产品的外观和性能造成影响。
解决办法是优化注塑压力和速度,以减少气体产生;在设计模具时,合理设置通气口和冷却系统,以排除气泡。
5. 温度控制不准确:温度是影响注塑过程和产品性能的重要因素,如果温度控制不准确,可能导致产品变形、气泡、表面瑕疵等问题。
解决办法是使用高质量的注塑机和热控系统,严格控制加热和冷却时间,确保温度分布均匀。
注塑过程中存在的问题多种多样,解决办法也需因情况而异。
因此,对于每个具体问题,需要仔细分析原因并采取相应的措施,以确保最终生产出符合要求的产品。
注塑过程中存在的问题及解决办法可以从多个方面展开,下面将深入探讨一些常见的问题,并提供相应的解决办法。
1. 模具设计问题:模具是注塑过程中至关重要的部分,如果设计不合理,就会导致一系列问题。
常见的问题包括产品尺寸偏差大、表面粗糙、开裂等。
解决办法是优化模具的进料系统和冷却系统,确保充填均匀,并增加冷却时间和加热时间。
2. 注塑机参数调节不当:注塑机的温度、压力和速度等参数设置不当,会导致产品质量问题。
例如,温度过高或过低会导致材料熔化不完全或固化不充分;压力过高或过低会影响产品的密度和强度。
注塑缺陷原因分析与解决方案

注塑缺陷原因分析与解决方案一、引言注塑是一种常用的塑料加工方法,广泛应用于各个行业。
然而,在注塑过程中,往往会浮现一些缺陷,如气泡、翘曲、短射等问题,这些缺陷会影响产品的质量和性能。
因此,进行注塑缺陷原因分析并提出相应的解决方案,对于提高产品质量和生产效率具有重要意义。
二、注塑缺陷原因分析1. 气泡问题气泡是注塑过程中常见的缺陷之一,其主要原因有:(1)塑料材料中含有水分,注入熔融塑料时水分蒸发产生气泡;(2)注塑机温度设置不当,导致塑料熔融不均匀,形成气泡;(3)模具设计不合理,存在气泡滞留区域。
2. 翘曲问题翘曲是注塑过程中常见的缺陷之一,其主要原因有:(1)注塑机注射速度过快,导致塑料流动不均匀,产生应力集中而引起翘曲;(2)模具温度不均匀,导致塑料冷却不均匀,引起翘曲;(3)模具结构设计不合理,导致翘曲。
3. 短射问题短射是注塑过程中常见的缺陷之一,其主要原因有:(1)注塑机注射压力不足,导致塑料无法充满模具腔体而产生短射;(2)模具排气不畅,导致塑料在注射过程中被挤出而产生短射;(3)模具设计不合理,导致短射。
三、解决方案1. 气泡问题解决方案(1)在塑料材料加工前,应进行充分的干燥处理,确保材料中的水分含量低于规定标准;(2)注塑机温度应根据材料的熔点和熔体流动性进行合理设置,确保塑料熔融均匀;(3)模具设计时应避免气泡滞留区域的存在,通过合理的结构设计和通气系统设置来减少气泡问题的发生。
2. 翘曲问题解决方案(1)注塑机的注射速度应根据产品的形状和尺寸进行合理设置,避免过快注射导致塑料流动不均匀;(2)模具温度应均匀分布,可以通过加热或者冷却系统来调节模具温度,确保塑料冷却均匀;(3)模具结构设计时应考虑产品的形状和尺寸,避免翘曲问题的发生。
3. 短射问题解决方案(1)注塑机注射压力应根据产品的形状和尺寸进行合理设置,确保塑料能够充满模具腔体;(2)模具排气系统应设计合理,确保塑料在注射过程中能够顺畅排气;(3)模具设计时应考虑产品的形状和尺寸,避免短射问题的发生。
注塑缺陷原因分析与解决方案

注塑缺陷原因分析与解决方案引言概述:注塑是一种常见的制造工艺,用于生产各种塑料制品。
然而,在注塑过程中,常常会出现一些缺陷,如短射、气泡、翘曲等问题,影响产品的质量和性能。
本文将分析注塑缺陷的原因,并提出相应的解决方案,以帮助企业提高产品质量和生产效率。
正文内容:1. 原材料选择不当1.1. 塑料材料质量不稳定:不同批次的塑料材料可能存在成分差异,导致注塑过程中的缺陷。
1.2. 塑料材料含水量过高:过高的含水量会导致注塑过程中产生气泡、短射等缺陷。
2. 注塑工艺参数不合理2.1. 注射速度过快:过快的注射速度容易造成短射、气泡等缺陷。
2.2. 注射压力不足:不足的注射压力会导致产品翘曲、尺寸不准确等问题。
2.3. 注射温度不当:过高或过低的注射温度都会影响产品的质量,如翘曲、缩水等缺陷。
3. 模具设计问题3.1. 模具结构不合理:模具的结构设计不合理会导致产品的翘曲、尺寸不准确等缺陷。
3.2. 模具表面处理不当:模具表面的处理不当会导致产品出现划痕、气泡等问题。
4. 注塑机设备问题4.1. 注射机压力不稳定:注射机压力的不稳定会导致产品尺寸不准确、表面不光滑等缺陷。
4.2. 注射机温度控制不准确:温度控制不准确会导致产品翘曲、缩水等问题。
5. 操作人员技术不熟练5.1. 操作不规范:不规范的操作会导致产品尺寸不准确、表面不光滑等缺陷。
5.2. 操作技术不熟练:操作人员对注塑机设备和工艺参数不熟悉,无法及时调整,导致产品质量下降。
总结:通过分析注塑缺陷的原因,我们可以得出以下解决方案:首先,选择稳定的塑料材料,并控制好含水量。
其次,合理调整注塑工艺参数,控制注射速度、压力和温度。
再次,优化模具设计,确保结构合理,表面处理良好。
同时,保证注塑机设备良好的运行状态,调整好注射机压力和温度控制。
最后,加强操作人员的培训和技术水平,确保规范操作,熟练掌握注塑机设备和工艺参数的调整。
通过以上的分析和解决方案,企业可以有效地解决注塑过程中的缺陷问题,提高产品质量和生产效率。
注塑常见不良原因和改善对策

注塑常见不良原因和改善对策注塑是一种常见的塑料制造技术,广泛应用于各个行业中。
然而,在注塑过程中,常常会出现一些不良现象,其中包括缺陷、变形、色差等问题。
本文将介绍注塑常见的不良原因,并提出相应的改善对策。
首先,缺陷是注塑过程中最常见的不良现象之一、缺陷可能是由于模具或注塑机的设计不合理导致的,也可能是由于操作人员的疏忽或技术不足造成的。
另外,材料的选择和质量也会影响缺陷的产生。
为了改善缺陷问题,我们可以采取以下对策:1.优化模具设计:对模具进行合理的设计和优化,确保注塑产品的几何尺寸、表面质量和力学性能符合要求。
另外,采用一些特殊的模具结构,如针阀模具、气动顶出模具等,可以进一步减少缺陷的产生。
2.提升操作技术:培训操作人员,提高其注塑技术水平和操作技能,确保注塑过程的稳定性和一致性。
另外,建立严格的操作规程和品质控制流程,规范操作行为,减少人为因素的影响。
3.加强材料质量控制:选择优质的注塑原料,定期对原料进行检验和筛查,确保其符合产品要求。
另外,在注塑过程中,通过控制注射速度、温度和压力等参数,有效控制材料的熔融和流动,减少缺陷的产生。
其次,变形是另一个常见的注塑不良现象。
变形可能是由于材料的热胀冷缩引起的,也可能是由于模具设计不合理或注塑工艺参数设置不当导致的。
为了减少变形问题,我们可以采取以下对策:1.优化模具设计:改善模具的冷却系统,通过增加冷却道的数量和位置,提高材料的冷却速度,减少变形的产生。
此外,采用一些特殊的模具结构,如加厚或加固构件,可以增加产品的刚度,防止变形的发生。
2.优化注塑工艺:通过调整注射速度、温度和压力等参数,控制材料的熔融和流动,减少热胀冷缩引起的变形。
另外,选择合适的注塑工艺,如预热模具或采用热流道系统等,可以进一步减少变形的产生。
最后,色差是注塑过程中常见的外观缺陷之一、色差可能是由于原料的质量问题导致的,也可能是由于注塑工艺参数设置不当或模具表面处理不良造成的。
注塑品外观缺陷原因分析及方案
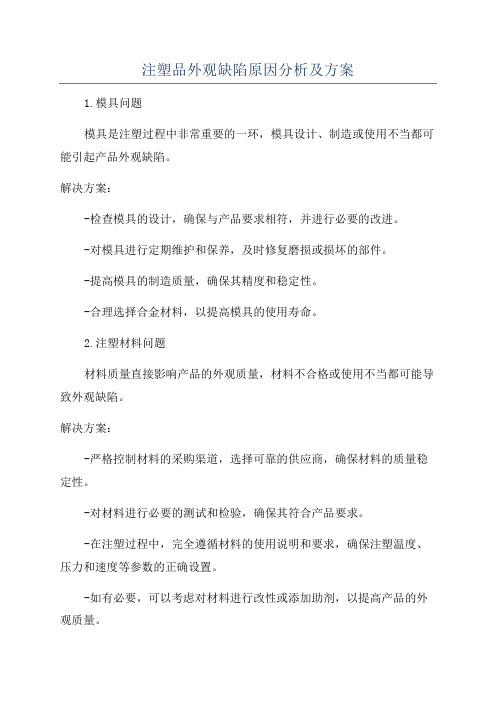
注塑品外观缺陷原因分析及方案1.模具问题模具是注塑过程中非常重要的一环,模具设计、制造或使用不当都可能引起产品外观缺陷。
解决方案:-检查模具的设计,确保与产品要求相符,并进行必要的改进。
-对模具进行定期维护和保养,及时修复磨损或损坏的部件。
-提高模具的制造质量,确保其精度和稳定性。
-合理选择合金材料,以提高模具的使用寿命。
2.注塑材料问题材料质量直接影响产品的外观质量,材料不合格或使用不当都可能导致外观缺陷。
解决方案:-严格控制材料的采购渠道,选择可靠的供应商,确保材料的质量稳定性。
-对材料进行必要的测试和检验,确保其符合产品要求。
-在注塑过程中,完全遵循材料的使用说明和要求,确保注塑温度、压力和速度等参数的正确设置。
-如有必要,可以考虑对材料进行改性或添加助剂,以提高产品的外观质量。
3.工艺参数问题注塑过程中,工艺参数的设置不合理也是导致外观缺陷的常见原因之一解决方案:-根据产品要求和材料特性,合理设置注射压力、注射速度、冷却时间等工艺参数。
-在注塑过程中,定期检查和调整工艺参数,保持其稳定性。
-使用先进的注塑设备和控制系统,提高注塑过程的自动化程度,降低人为因素对工艺参数的影响。
-针对不同的产品和外观缺陷,分析和优化工艺参数,以改善产品的外观质量。
4.操作人员问题操作人员的技术水平和经验不足,也是导致外观缺陷的一个重要原因。
解决方案:-对操作人员进行必要的培训和培养,提高其技术水平和专业知识。
-强调操作的规范性和标准化,遵守操作规程和要求。
-加强团队合作,实施相互监督和互助,减少人为失误的发生。
注塑品外观缺陷的原因分析及解决方案很多,上述只是一部分常见的原因和解决方法。
在实际应用中,还需根据具体情况来综合分析和解决问题。
同时,通过不断的优化和改进,提高注塑过程的质量和效率,减少外观缺陷的发生。
注塑缺陷原因分析与解决方案
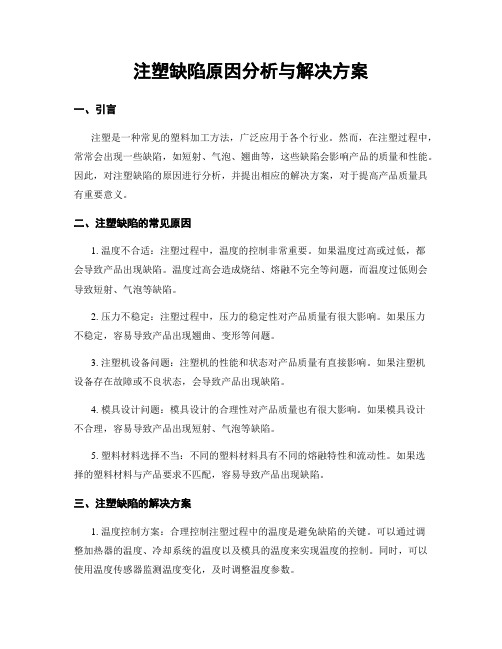
注塑缺陷原因分析与解决方案一、引言注塑是一种常见的塑料加工方法,广泛应用于各个行业。
然而,在注塑过程中,常常会出现一些缺陷,如短射、气泡、翘曲等,这些缺陷会影响产品的质量和性能。
因此,对注塑缺陷的原因进行分析,并提出相应的解决方案,对于提高产品质量具有重要意义。
二、注塑缺陷的常见原因1. 温度不合适:注塑过程中,温度的控制非常重要。
如果温度过高或过低,都会导致产品出现缺陷。
温度过高会造成烧结、熔融不完全等问题,而温度过低则会导致短射、气泡等缺陷。
2. 压力不稳定:注塑过程中,压力的稳定性对产品质量有很大影响。
如果压力不稳定,容易导致产品出现翘曲、变形等问题。
3. 注塑机设备问题:注塑机的性能和状态对产品质量有直接影响。
如果注塑机设备存在故障或不良状态,会导致产品出现缺陷。
4. 模具设计问题:模具设计的合理性对产品质量也有很大影响。
如果模具设计不合理,容易导致产品出现短射、气泡等缺陷。
5. 塑料材料选择不当:不同的塑料材料具有不同的熔融特性和流动性。
如果选择的塑料材料与产品要求不匹配,容易导致产品出现缺陷。
三、注塑缺陷的解决方案1. 温度控制方案:合理控制注塑过程中的温度是避免缺陷的关键。
可以通过调整加热器的温度、冷却系统的温度以及模具的温度来实现温度的控制。
同时,可以使用温度传感器监测温度变化,及时调整温度参数。
2. 压力控制方案:稳定的注塑压力有助于减少产品缺陷。
可以通过调整油压系统的参数、增加油泵的流量以及优化模具结构来实现压力的稳定控制。
3. 注塑机设备维护方案:定期对注塑机设备进行维护和保养,及时排除故障,确保设备处于良好状态。
同时,可以使用高精度的注塑机设备,提高产品质量。
4. 模具设计优化方案:优化模具设计,确保模具结构合理,避免出现短射、气泡等缺陷。
可以通过增加冷却系统、优化流道设计、增加排气系统等方式来改善模具设计。
5. 塑料材料选择方案:根据产品要求,选择合适的塑料材料。
可以通过对不同塑料材料的熔融特性和流动性进行测试,选择最适合的材料,避免出现缺陷。
注塑缺陷原因分析与解决方案

注塑缺陷原因分析与解决方案一、引言注塑是一种常见的塑料加工方法,广泛应用于各个行业。
然而,在注塑过程中往往会浮现一些缺陷,如短射、气泡、热缩等。
本文将对注塑缺陷的原因进行分析,并提出相应的解决方案,以匡助企业提高产品质量和生产效率。
二、注塑缺陷原因分析1. 短射短射是指注塑过程中无法将塑料彻底填充模具腔体的现象。
短射的原因可能包括以下几点:- 模具设计不合理:模具的流道设计不合理或者过小,导致塑料无法充分流动。
- 注塑参数设置不当:注塑机的注射速度、压力等参数设置不当,影响了塑料的充填性能。
- 塑料材料选择不当:选择的塑料材料流动性差,导致无法充分填充模具腔体。
2. 气泡气泡是指注塑制品中浮现的气体会萃的现象。
气泡的原因可能包括以下几点:- 塑料材料含水量高:塑料材料含水量高会在注塑过程中产生蒸汽,形成气泡。
- 注塑机排气不畅:注塑机排气系统不畅,无法及时排出注塑过程中产生的气体。
- 模具设计不合理:模具中存在死角或者过小的通气孔,导致气体无法顺利排出。
3. 热缩热缩是指注塑制品在冷却后发生尺寸变化的现象。
热缩的原因可能包括以下几点:- 注塑温度过高:注塑温度过高会导致塑料在冷却后收缩过大。
- 模具温度不均匀:模具的温度分布不均匀,导致注塑制品冷却不均匀,进而引起热缩。
- 塑料材料热性能不稳定:选择的塑料材料热性能不稳定,导致注塑制品在冷却后发生尺寸变化。
三、注塑缺陷解决方案1. 短射解决方案- 模具设计合理化:优化模具的流道设计,增加流道的截面积,确保塑料能够充分流动。
- 注塑参数优化:根据塑料材料的特性,合理设置注塑机的注射速度、压力等参数,保证塑料充填模具腔体。
- 选择合适的塑料材料:根据产品的要求,选择流动性好的塑料材料,提高充填性能。
2. 气泡解决方案- 塑料材料干燥处理:在注塑过程前,对塑料材料进行干燥处理,降低含水量,减少气泡的产生。
- 注塑机排气系统改进:优化注塑机的排气系统,增加排气孔的数量和大小,提高排气效果。
注塑产品不良原因分析及解决方案

注塑产品不良原因分析及解决方案注塑产品不良原因分析与解决方案注塑成型技术在现代制造业中无处不在,从汽车零件到家用电器,甚至医疗器械,都离不开它。
虽然这种技术已相当成熟,但问题依然层出不穷,特别是不良品的出现,真是让人感到头疼。
为了提升产品质量、降低成本、提升客户的满意度,找出问题的根源并提出有效的解决方案,显得尤为重要。
目标与范围本文的目的是要搞清楚注塑产品为何会出现不良现象,并制定具体可行的解决方案,以确保后续生产能够顺利进行。
我们将关注注塑过程中的每一个环节,从原材料的选择、模具设计、工艺流程、设备维护到质量管理,统统包括在内。
现状分析在不少企业里,注塑生产线运转频繁,效率也很高,不过,这并不意味着没有问题。
有一家汽车零部件厂家,过去一年因为不良品损失了足足50万元。
经过初步调查,发现问题主要集中在这几个方面:1. 原材料问题:一些塑料原料质量不稳定,导致成品强度不足或外观缺陷。
2. 模具设计缺陷:模具设计不合理,影响了塑料的流动,最终影响了成型质量。
3. 工艺参数设置不当:如温度、压力和注射速度等参数的控制不严,导致了产品缺陷。
4. 设备老化:一些注塑机老旧,频繁机械故障,生产效率受影响。
5. 人员素质参差不齐:操作工的技术水平参差不齐,导致操作不规范,增加了不良品的发生。
不良原因具体分析原材料问题原材料是注塑的基础,如果原料质量不过关,成品的性能和外观就会大打折扣。
不同批次的原料物性和化学成分可能差异很大,直接影响到成品的强度和韧性。
模具设计缺陷模具设计不合理会导致塑料在流动时出现不均匀现象,比如浇口设计不当可能会造成气泡或空洞,直接影响产品的密度和强度。
工艺参数设置不当每种材料都有其最佳的注塑工艺参数,未能严格遵循这些参数设置,成品就可能出现缺陷。
比如,注射温度过低可能导致塑料未能完全熔化,注射压力不足则可能导致成品填充不完全。
设备老化设备老化和维护不足会导致注塑机性能下降,常见的如注射速度不够、压力不足等,都会直接影响成品质量。
注塑件常见原因分析

注塑件常见原因分析
注塑件是制造业中常用的一种零部件,具有成本低、生产效率高、制造周期短等优点。
然而,由于注塑工艺相对复杂,注塑件在生产过程中可能会出现各种问题。
以下是注塑件常见原因分析的一些可能因素。
1.材料问题:
材料的选择对注塑件的质量有着重要的影响。
如果材料本身有缺陷或不符合要求,会导致注塑件出现问题。
例如,材料含水率过高会导致注塑件产生气泡,降低机械性能;材料中添加剂含量不准确会导致注塑件出现色差等问题。
2.模具问题:
模具是注塑件生产过程中的关键因素之一、如果模具设计不合理、加工精度不够或使用寿命较短,可能会导致注塑件尺寸不准确、表面粗糙或产生开裂等问题。
3.注塑工艺问题:
注塑工艺的参数设置直接影响注塑件的质量。
如果温度、时间、压力等参数设定不准确,可能导致注塑件缩水、变形等问题。
例如,加热温度过高会引起熔融物流动性增加、熔胶温度下降过快造成冷料温度过低,导致注塑件表面出现缺陷。
4.操作问题:
5.环境问题:
环境条件也会对注塑件的质量产生一定影响。
如果湿度过高,可能会导致注塑件表面出现气泡;如果温度过低,可能导致注塑件收缩不均匀。
6.质量管理问题:
质量管理是确保注塑件质量的重要环节。
如果企业没有严格的质量管理体系,以及缺乏相关的检测设备和人员,可能会导致注塑件的质量无法得到有效控制。
综上所述,注塑件常见问题的原因分析可以从材料问题、模具问题、注塑工艺问题、操作问题、环境问题和质量管理问题等方面进行考虑。
只有全面分析各种可能因素,并进行相应的改进和优化措施,才能提高注塑件的质量和生产效率。
十大注塑问题分析

避免模垢产生
• • • • • • 融料在机筒的滞留时间不能太长 对剪切敏感的材料用较佳的流道和浇口尺寸 足够排气,修正排气系统 定期清洗模腔 采用模腔面特殊喷涂使模垢不易粘附 钛氮表面处理可减少模垢生成
......
请参考杜邦公司提供 的设计手册和注射成 型指导,与我们联络.
请多指教!
认识不同的结果
• 空洞和针孔会降低机械性能(以缺口形式), 极大地降低断裂延伸率(%)和冲击性能 • 如果浇口太窄小,对增强聚合物来讲,纤维 会遭到破坏以致长度变短,这也进一步损害 正常的成型 • 使用较大的注射压力和较长的充填时间可以 检测浇口是否太小,比如,不同的注射速度 设定对实际注射充填影响很小
• 轴心对称件如齿轮, 碟, 转子, 用三板模圆周或多点中心入水较佳
• 中央绞链件,浇口远离绞链以消除融合线 • 杯状件浇口靠进杯底边缘,防止困气
......
Hold pressure time too short
4
保压时间太短
在保压阶段发生......
• 型腔已完成注射充填,聚合分子开始结晶, 即分子链开始互相排列,产生较大的填塞密 度 • 如保压时间太短,不能补偿体积收缩,产生 小的空洞
Effect of gate size浇口大小的影响
认识不同的结果
• 如果流道系统太小,即使延长保压时间,保 压压力足够大都不可能有效,因为体积收缩 不能得到足够的补偿,导致出现空洞和缩水 &凹陷(对未增强塑料),针孔(对增强塑料) • 此现象可以在显微镜下观察到 • 此情况下,成型后尺寸的变化较大,会出现 过多的收缩,并增加变形的机会
燥
重要的数
• • • • 空气的流量 (2.5__3.5立方米/小时*公斤) 空气的温度 露点(小于-200C) 初始湿气水平
注塑缺陷原因分析与解决方案
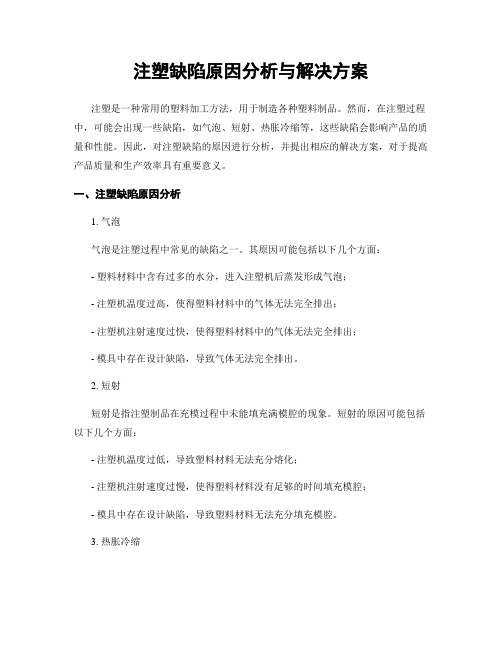
注塑缺陷原因分析与解决方案注塑是一种常用的塑料加工方法,用于制造各种塑料制品。
然而,在注塑过程中,可能会出现一些缺陷,如气泡、短射、热胀冷缩等,这些缺陷会影响产品的质量和性能。
因此,对注塑缺陷的原因进行分析,并提出相应的解决方案,对于提高产品质量和生产效率具有重要意义。
一、注塑缺陷原因分析1. 气泡气泡是注塑过程中常见的缺陷之一。
其原因可能包括以下几个方面:- 塑料材料中含有过多的水分,进入注塑机后蒸发形成气泡;- 注塑机温度过高,使得塑料材料中的气体无法完全排出;- 注塑机注射速度过快,使得塑料材料中的气体无法完全排出;- 模具中存在设计缺陷,导致气体无法完全排出。
2. 短射短射是指注塑制品在充模过程中未能填充满模腔的现象。
短射的原因可能包括以下几个方面:- 注塑机温度过低,导致塑料材料无法充分熔化;- 注塑机注射速度过慢,使得塑料材料没有足够的时间填充模腔;- 模具中存在设计缺陷,导致塑料材料无法充分填充模腔。
3. 热胀冷缩热胀冷缩是指注塑制品在冷却过程中发生尺寸变化的现象。
热胀冷缩的原因可能包括以下几个方面:- 注塑机温度控制不准确,导致塑料材料在冷却过程中温度变化不均匀;- 注塑机冷却时间过短,使得塑料材料没有足够的时间冷却固化;- 注塑机冷却压力不足,使得塑料材料在冷却过程中发生变形。
二、注塑缺陷解决方案1. 气泡解决方案- 使用干燥塑料材料,避免材料中含有过多的水分;- 控制注塑机温度,确保塑料材料中的气体能够完全排出;- 调整注塑机注射速度,使得塑料材料中的气体能够完全排出;- 设计合理的模具,确保气体能够完全排出。
2. 短射解决方案- 调整注塑机温度,确保塑料材料能够充分熔化;- 调整注塑机注射速度,使得塑料材料有足够的时间填充模腔;- 设计合理的模具,确保塑料材料能够充分填充模腔。
3. 热胀冷缩解决方案- 控制注塑机温度,确保塑料材料在冷却过程中温度变化均匀;- 增加注塑机冷却时间,使得塑料材料有足够的时间冷却固化;- 调整注塑机冷却压力,确保塑料材料在冷却过程中不发生变形。
注塑缺陷原因分析与解决方案

注塑缺陷原因分析与解决方案一、引言注塑工艺是一种常用的塑料加工方法,广泛应用于各个领域。
然而,在注塑过程中,常常会出现一些缺陷,如气泡、翘曲、短射等问题,严重影响产品的质量和性能。
因此,对注塑缺陷的原因进行分析,并提出相应的解决方案,对于提高产品质量和生产效率具有重要意义。
二、注塑缺陷的原因分析1. 模具设计不合理:模具是注塑过程中的关键因素之一,模具的设计不合理会导致产品缺陷。
例如,模具中存在过于复杂的结构、不合理的冷却系统等,都可能引起产品的翘曲、短射等问题。
2. 塑料材料选择不当:不同的塑料材料具有不同的物理性能和熔融特性,选择不当会导致产品缺陷。
例如,选择的塑料材料熔点过高或过低,都会影响产品的成型效果。
3. 注塑工艺参数设置错误:注塑工艺参数的设置对于产品质量至关重要。
例如,注射压力、注射速度、保压时间等参数的设置不当,都会导致产品的缺陷,如气泡、短射等。
4. 模具磨损和老化:长时间使用的模具会出现磨损和老化现象,导致产品的尺寸精度下降。
此外,模具的使用寿命过长也会影响产品质量。
5. 注塑设备故障:注塑设备的故障也是导致产品缺陷的原因之一。
例如,注射机的温度控制不准确、压力控制不稳定等,都会对产品的成型效果产生影响。
三、注塑缺陷的解决方案1. 模具设计优化:通过对模具的结构进行优化设计,减少复杂结构的使用,合理设计冷却系统,可以有效降低产品缺陷的发生率。
2. 塑料材料选择合理:根据产品的要求和特性选择合适的塑料材料,确保其熔融特性和物理性能与产品的要求相匹配。
3. 注塑工艺参数优化:通过合理设置注塑工艺参数,如注射压力、注射速度、保压时间等,控制好温度和压力的变化,可以提高产品的成型效果。
4. 定期维护和更换模具:定期对模具进行维护,及时更换磨损和老化的部件,可以保证模具的精度和使用寿命,提高产品的质量。
5. 定期检查和维护注塑设备:定期检查注塑设备的温度控制、压力控制等系统,确保其正常工作,减少设备故障对产品质量的影响。
注塑缺陷原因分析与解决方案

注塑缺陷原因分析与解决方案引言概述:注塑工艺是一种常见的制造工艺,广泛应用于各个行业。
然而,在注塑过程中,常常会出现一些缺陷,如短射、气泡、翘曲等问题。
本文将从原因分析和解决方案两个方面,详细介绍注塑缺陷及其解决方法。
一、短射问题1.1 原因分析:短射是指注塑制品在充模过程中未能完全填充模腔,导致制品出现不完整或缺陷。
其主要原因包括:1.1.1 注射速度过快:过快的注射速度会导致熔融塑料在进入模腔之前已经开始凝固,从而无法完全填充模腔。
1.1.2 模具温度不合适:模具温度过低会导致塑料熔融不完全,无法充分填充模腔。
1.1.3 压力不足:注塑机的射胶压力不足会导致塑料无法充分填充模腔。
1.2 解决方案:针对短射问题,可以采取以下解决方案:1.2.1 调整注射速度:根据具体情况,适当调整注射速度,以确保塑料能够完全填充模腔。
1.2.2 控制模具温度:通过调整模具温度,确保塑料能够充分熔融,提高注塑质量。
1.2.3 增加射胶压力:适当增加注塑机的射胶压力,以保证塑料能够充分填充模腔。
二、气泡问题2.1 原因分析:气泡是注塑制品中常见的缺陷之一,其主要原因包括:2.1.1 塑料中含有气体:在塑料加工过程中,如果塑料中含有气体,会在注塑过程中形成气泡。
2.1.2 注射过程中的气体:注射过程中,如果注射速度过快,会产生气泡。
2.1.3 模具温度不稳定:模具温度不稳定会导致塑料熔融不均匀,从而产生气泡。
2.2 解决方案:针对气泡问题,可以采取以下解决方案:2.2.1 塑料预处理:在注塑前对塑料进行预处理,去除其中的气体,以减少气泡的产生。
2.2.2 控制注射速度:控制注射速度,避免过快注射导致气泡产生。
2.2.3 稳定模具温度:通过控制模具温度,确保塑料能够充分熔融,减少气泡的产生。
三、翘曲问题3.1 原因分析:翘曲是指注塑制品在冷却后出现变形或弯曲的现象,其主要原因包括:3.1.1 冷却不均匀:冷却不均匀会导致注塑制品不均匀收缩,从而产生翘曲。
- 1、下载文档前请自行甄别文档内容的完整性,平台不提供额外的编辑、内容补充、找答案等附加服务。
- 2、"仅部分预览"的文档,不可在线预览部分如存在完整性等问题,可反馈申请退款(可完整预览的文档不适用该条件!)。
- 3、如文档侵犯您的权益,请联系客服反馈,我们会尽快为您处理(人工客服工作时间:9:00-18:30)。
Injection Molding Guide of Technyl 泰克尼成型指南 Abstracts摘要Engineering PlasticsCareful handling of the polyamide products 小心处理聚酰胺产品• Keep granules in their sealed bags or containers until required请保持颗粒在密封袋或容器内直到需求使用前。
• Be sure to use the polymer granules within one hour after opening its sealed packaging确保使用的颗粒在开封后1小时 内用完。
• Seal partly finished bags again to reduce any moisture absorption使用完后的余料需及时密封以减少水分的吸收。
• Dry material prior to processing in case of too high a moisture content加工前请干燥好材料以防水分含量过高。
Slide 2 / 9220 DEC, 2002XU HAI QING , ADC AsiaAuto GMTRate of water absorption by granules at 23°C 塑胶颗粒在23度时的吸水率0.6RH75湿度75%TECHNYL A 218Water content in granules (%) 颗粒含水率0.5 0.4 0.3 0.2 0.1 0 0 1 2 3 4 5 6 7RH50湿度50%RH25湿度25%Time (hours)时间Slide 3 / 9220 DEC, 2002XU HAI QING , ADC AsiaAuto GMTWater absorption of the granules after the bag is opened 包装袋打开后颗粒的吸水率TECHNYL A 218 0.4Water content in granules (%) 颗粒吸水率0.3Upper part of the bag 包装袋的表层 Middle part of the bag 包装袋的中间层 Lower part of the bag包装袋的最底层0.20.1 00246810 12 14 16 18 20 22 24Time after the bag is opened (hours) 包装袋打开后的时间Slide 4 / 9220 DEC, 2002XU HAI QING , ADC AsiaAuto GMTDrying very humid granules 干燥潮湿的颗粒TECHNYL A 218 V30 0.9Water content in granules (%) 颗粒含水率0.8 0.7 0.6 0.5 0.4 0.3 0.2 0.1 0Desiccant dryer 除湿干燥机 Temperature: 80°C温度80度 Dew point: -35°C露点-35051015202530Drying time (hours) 干燥时间Slide 5 / 9220 DEC, 2002XU HAI QING , ADC AsiaAuto GMTDifferent ways of drying不同的干燥方法0.25 TECHNYL A 218 V30 Temperature: 80°C Vacuum dryer真空干燥机 Hot air dryer热风干燥机Water content in granules (%) 颗粒含水率0.2 0.15 0.1 0.05 0 Desiccant dryer (dew point -30°C) 除湿干燥机,露点-30c02468101214Drying time (hours)干燥时间Slide 6 / 9220 DEC, 2002XU HAI QING , ADC AsiaAuto GMTDryer type & drying time干燥种类与干燥时间Dehumidifying 除湿干燥机 Dehumidifying Dryer Dryer 除湿干燥机Natural Natural and and light light color color material material自然色与轻颜色的材料 自然色与轻颜色的材料 •• Temperature ℃ 温度 70 ~ 80 ℃ Temperature = = 70 70 ~ ~ 80 80 ℃ 温度 70 ~ 80 ℃ •• Time Time = =2 2~ ~ 3hrs 3hrs (closed (closed bag) bag) 时间= 2 ~ 3 小时(密封) 时间= 2 ~ 3 小时(密封) Max. Max. 8hrs 8hrs (opened (opened bag) bag)最大 88 小时(开包) 最大 小时(开包)Hot 热风干燥机 Hot Air Air dryer dryer 热风干燥机Natural Natural and and light light color color material material自然色与轻颜色的材料 自然色与轻颜色的材料 •• Temperature ℃ Temperature = = 80 80 ~ ~ 90 90 ℃温度= 80 ℃ 温度= 80 ~ ~ 90 90 ℃ •• Time Time = =4 4~ ~ 5hrs 5hrs (closed (closed bag) bag) Max. Max. 8hrs 8hrs (opened (opened bag) bag)Black Black and and dark dark color color material material 黑色与黑暗色的材料 黑色与黑暗色的材料•• Temperature ℃ Temperature = = 80 80 ~ ~ 120 120 ℃ •• Time Time = =2 2~ ~ 3hrs 3hrs (closed (closed bag) bag) Max. Max. 12hrs 12hrs (opened (opened bag) bag)Slide 7 / 92Black Black and and dark dark color color material material 黑色与黑暗色的材料 黑色与黑暗色的材料•• Temperature ℃ Temperature = = 100 100 ~ ~ 120 120 ℃ •• Time Time = =4 4~ ~ 5hrs 5hrs (closed (closed bag) bag) Max. Max. 12hrs 12hrs (opened (opened bag) bag)Auto GMT20 DEC, 2002XU HAI QING , ADC AsiaMolding Recommendations成型建议• Set injection volumes between 30% and 60% of the maximum injection volume of the injection unit • 建议注塑容积是注塑单元的最大容积的39%~60%。
• Set granules’ temperature at 60°C at the feed hopper • 建议设定颗粒下料口处的温度为60度 • Set barrel’s temperature profile to increase along the barrel • 建议设定炮桶的温度为沿着炮筒逐步增加 • For large shot weights, set barrel’s temperature profile to decrease along the barrel对大部件,设定炮筒的温度为递减的。
Slide 8 / 9220 DEC, 2002XU HAI QING , ADC AsiaAuto GMTMolding Recommendations成型建议 Three zone screw 三段螺杆式ØdFeeding下料口处直径LF进料段长度 LC压缩段长度ØdMetering计量段直径LM计量段ØD炮桶直径P=D-Feeding Zone: LF ≥ 12D. 2 ≤ compression ratio ≤ 3 - Metering Zone: LM ≥ 4DSlide 9 / 92进料段:LF ≥ 12D 压缩段 :LC = 4D 2 ≤压缩比≤ 3 计量段:LM ≥ 4D螺棱宽度=直径- Compression Zone: LC = 4D20 DEC, 2002XU HAI QING , ADC AsiaAuto GMTInjection moulding cycle注塑成型周期Cycle time周期Closing of the mould关模时间 Injection unit forwards射台前进时间 Injection注射时间 Holding pressure保压时间 Injection unit backwards射台后退时间 Plastification塑化时间 Machine set cooling time Real cooling time固定的冷却时间 Opening / ejection 开模/顶出时间Slide 10 / 9220 DEC, 2002XU HAI QING , ADC AsiaAuto GMTMolding Recommendations 成型建议Influence of processing parameters工艺参数的影响Melt temperatureWeld line resistance Surface aspect Cycle time Packing phaseMould temperatureShrinkage Surface aspect Weld line strength Part stabilisationHolding pressure timeShrinkage Sink marks Residual stress Part qualityInjection speedWeld line strength Surface aspect Filling facilitySlide 11 / 9220 DEC, 2002XU HAI QING , ADC AsiaAuto GMTMolding Recommendations 成型建议 Molding parameters 成型参数Melt Temperature Mould Temperature (° C) (° C) Injection Speed (cm3/s) Back Pressure (bar) Peripheral Speed of Screw (mm/s)PA 66 TECHNYL AStandard viscosity Medium viscosity GF reinforced Mineral filled Flame retardant Impact modified270-290 270-290 270-300 270-300 270-280 270-290 230-250 230-250 230-260 230-260 230-240 230-25060-80 60-80 80-120 80-120 60-90 60-90 40-80 40-80 80-100 80-100 40-80 40-8050-150 50-150 120-170 120-170 80-120 80-150 50-150 50-150 120-170 120-170 80-120 80-15050-100 50-100 20-50 50-100 20-50 50-100 50-100 50-100 20-50 50-100 20-50 50-100300-600 300-600 200-300 300-400 200-300 300-600 300-600 300-600 200-300 300-400 200-300 300-600PA 6 TECHNYL CStandard viscosity Medium viscosity GF reinforced Mineral filled Flame retardant Impact modifiedSlide 12 / 9220 DEC, 2002XU HAI QING , ADC AsiaAuto GMTMoulding Recommendations成型建议Influence of regrinds 再生料的影响Variation of mechanical properties with percentage of added reground material回料的百分比和机械性能的变化Unreinforced未增强Glass fibre reinforced 玻璃纤 TECHNYL A 218 V30 维增强 15%of reground material>30%回料比例30%of reground material100%of reground materialof reground materialStress at break 断裂应力 - 3% Elongation 伸长率 < 25% Charpy impact 简支梁冲击强度 - 20%- 3% + 10% - 10%- 12% + 15% -15%- 35% + 35% - 50%All values are given at 23℃/RH0所有测量值是在23度/相对湿度0Slide 13 / 9220 DEC, 2002XU HAI QING , ADC AsiaAuto GMTDimensional stability of moulded parts成型零件的稳定性Shrinkage收缩Volumetric contraction during solidification phase (from molten state to crystalline phase在冷凝阶段的体积收缩( 从熔融阶段到结晶阶段) Further contraction of the part as full crystallisation takes place under thermal treatment在热处理时由于结晶体积 进一步缩小Post Shrinkage后收缩Moisture regain后吸湿性(exposure to a humid environment ) (暴露在潮湿的环境中)Variations in 变化发生在weight重量 dimensions 尺寸 properties性能Accelerated treatment加速后处理吸湿(in water or in air)(在水或空气中)Moistening polyamide parts to bring them to a certain humidity level使产品具有一定水分(after moulding, parts do not contain any water) (成型后,零件不含水分)Slide 14 / 9220 DEC, 2002XU HAI QING , ADC AsiaAuto GMTShrinkage收缩率Shrinkage after moulding according to ISO 294-4收缩率按 ISO 294-4 纵向收缩率 /流动方向 横向收缩率/垂 直流动方向Shrinkage Longitudinal %Shrinkage Transverse % 1.9 0.85 1 0.8PA 66 TECHNYL AUnreinforced grade GF reinforced Mineral filled Flame retardant A 216 A 216 V30 A 228 MT40 A 30H1 V30 1.9 0.6 0.9 0.6PA 6 TECHNYL CUnreinforced grade GF reinforced Mineral filled Flame retardant C 216 C 218 V25 C 228 MT40 C 30H1 V30 1.3 0.4 0.8 0.25 1.3 0.7 1.1 0.65Slide 15 / 9220 DEC, 2002XU HAI QING , ADC AsiaAuto GMTShrinkage收缩率Parameters affecting mould shrinkage影响收缩率的因素收缩By increasing... 通过增加Holding pressure 保压压力 Injection speed 注射速度 Gate size浇口尺寸The shrinkageMould temperature 模具温度 Part thickness产品胶厚Slide 16 / 9220 DEC, 2002XU HAI QING , ADC AsiaAuto GMTInfluence of the thickness of the part on the shrinkage零件壁厚对收缩率的影响Shrinkage (%) 收缩率3TECHNYL A 2162.5 21.5 1TransverseGlass Fibre reinforced TECHNYL A 216 V300.5 0 1 2 3 4Longitudinal5678Thickness of the part (mm)零件壁厚Slide 17 / 9220 DEC, 2002XU HAI QING , ADC AsiaAuto GMTInlfuence of mould temperature on shrinkage and post shrinkage 模具温度对收缩、后收缩的影响Shrinkage (%)收缩率2 1.6 1.2 0.8 0.4 0 0 20 40 60 80 Shrinkage after moulding 成型收缩Shrinkage (%)TECHNYL® PA 66TECHNYL ® PA 62 1.6 1.2 0.8Shrinkage after moulding成型收缩Post shrinkage 后收缩1100.4 0 30 50 70Post shrinkage后收缩Mould temperature (°C) 模温Mould temperature (°C) 模温90110130Plate thickness : 3.2 mm板厚 TECHNYL A 218Plate thickness : 2 mm板厚 TECHNYL C 216Slide 18 / 9220 DEC, 2002XU HAI QING , ADC AsiaAuto GMTAnnealing treatment退火处理• •Annealing treatment to accelerate post shrinkage and thus dimensional stability 退火处理加速后收缩使尺寸稳定 Treatment temperature and time 退火温度和时间 – – – – – 10 to 20°C above the maximum service temperature大于最高使用温度10 to 20°C TECHNYL® A : 175°C TECHNYL ® C : 160°C Thick parts : about 45min 壁厚的零件 : 约 45分钟 Parts less than 2mm thick : 20min 壁厚小于 2mm : 20分钟••Heating and cooling must be gradual in order to prevent thermal shocks.加热和冷却必须缓慢进行,以避免热冲击Slide 19 / 9220 DEC, 2002XU HAI QING , ADC AsiaAuto GMTPart ConditioningUse water absorption treatment for...零件的调湿处理• •Facilitated assembling 方便装配 Stabilisation of part dimensions in service conditions• 使产品在使用环境中尺寸稳定• Adjustment of impact resistance properties• 增加冲击强度Slide 20 / 9220 DEC, 2002XU HAI QING , ADC AsiaAuto GMTPart ConditioningInfluence of humidity on part dimensions 水分对产品尺寸的影响Part dimensions variations (%) 产品尺寸的变异32.5 2TECHNYL A 2161.5 10.5 0TECHNYL A 216 V30020406080100Relative humidity (%) 相对湿度Slide 21 / 9220 DEC, 2002XU HAI QING , ADC AsiaAuto GMTConditioning TECHNYL® TECHNYL®材料的调湿RH 65 - temperature 20°C 相对湿度65-温度20度含水Water content (%)PA 6PA 66Thickness in mm壁厚 1 23 46 8 104.5 4 3.5 3 2.5 2 1.5 1 0.53.5 3 2.5 2 1.5 1 0.53 510 2 weeks days5 2 months weeks5 months1 year5 yearsSlide 22 / 9220 DEC, 2002days Days3Conditioning time调湿时间/天Auto GMTXU HAI QING , ADC AsiaConditioning TECHNYL® TECHNYL®材料的调湿In water at 20°C 在 20°C 水中Water content (%)PA 6PA 66Thickness in mm产品壁厚 mm 1 2 3 46 8 108 7 9 8 7 6 5 4 3 2 1 6 5 4 3 2 13 5 days days20 DEC, 200210 2 weeks days5 25 months1 year5 yearsSlide 23 / 92XU HAI QING , ADC Asiamonths weeksConditioning time调湿时间/天Auto GMTConditioning TECHNYL® TECHNYL®材料的调湿In water at 98°C 在 98°C 水中PA 66Water content (%)8PA 6Thickness in mm产品壁厚 mm 1 2 3 468 109 8 7 6 5 4 3 27 6 5 4 3 2 1 1/4 1/2 1 hour hour hour 5 10 hours hours 1 day 5 1015 days days daysConditioning time调湿时间/小时Slide 24 / 9220 DEC, 2002XU HAI QING , ADC AsiaAuto GMTTrouble Shooting of Injection Molding注塑成型问题解答Source : Consortium of molding machine makers Maffei, (ENGEL, Kraus Maffei , etc.) 资料来源 : 注塑机生产商联盟 Maffei, (ENGEL, Kraus Maffei , 等.)Engineering PlasticsApplication Development Center AsiaSink Mark缩印Sink marks appear for example near material accumulations as depressions on the surface of the molded part, if the thermal contraction(shrinkage) cannot be compensated.缩印出现在材料肉厚部位Figure 2 : 由于热收缩没有得到补偿而在产品表面形成 Sink marks due to wall thickness 的凹痕 variation图 2 : 由于壁厚变化产生的 缩影Figure 1 : Sink marks near ribs图 1 :筋附近的缩影Slide 26 / 92Figure 3 : Sink marks on a cylindrical core whose temperature was not controlled correctly图 3 : 缩影产生在不能很好 控制温度的型芯附近20 DEC, 2002 XU HAI QING , ADC Asia Auto GMTSink Mark缩印◆ Physical cause : ● Solidification too slow ● 固化太慢 ◆原因 : ● effective holding pressure time too short ● 保压时间太短 ● not enough holding pressure transfer, because flow resistances in the mold are too high ● 由于模具内流动阻力太大,压力不能有效传递Residual melt cushion too small?剩余的垫料量是否太小?Yes⑴ Increase metering strokeNoSink marks near the gate or thick-wall areas?缩影是否在浇口附近或厚壁区域? NoSink marks away from the gate or in thin-wall areas?Yes⑵ Check non-return valve ⑵ 检查止回环 ⑴ Optimize holding pressure time ⑴ 优化保压时间 ⑵ Increase holding pressure (maybe short overpacking) ⑵ 增加保压 ⑶ Change mold temperature (-) ⑶ 改变模具温度 (-) ⑷ Change melt temperature (-) ⑷ 改变料筒温度 (-) ⑸ Change injection rate (-) ⑸ 改变注射速度 (-) ⑴ Optimize holding pressure time ⑴ 优化保压时间 ⑵ Increase holding pressure (maybe short overpacking) ⑵ 增加保压 ⑶ Change injection rate (+) ⑶ 改变注射速度 (+) ⑷ Change melt temperature (+) ⑷ 改变料筒温度 (+) ⑸ Change mold temperature (+) ⑸ 改变模具温度(+) ⑴ Check gas ventilation ⑴ 检查排气 ⑵ Check sprue and gate dimensions ⑵ 检查浇口和流道尺寸 ⑶ Check granules condition ⑶ 检查粒料状态 ⑷ Remove material accumulations⑷ 抽去肉厚部位 ⑸ Consider wall thickness/rib ratio⑸ 考虑壁厚/筋的厚度比率 ⑹ Add blowing agent ⑹ 增加吹冷装置 ⑺ Use plastic with low shrinkage⑺ 采用低收缩材料⑴ 增加料量缩影是否在远离浇口或厚壁的区域? NoSink marks directly after demolding?Yes是否脱模后立即收缩?YesNoSlide 27 / 9220 DEC, 2002⑴ Increase cooling time ⑴ 增加冷却时间 XU HAI QING , ADC Asia Auto GMTStreak (Burnt Streak)焦痕(烧焦痕)If the melt was damaged thermally by to high temperatures and/or too long residence times, gaseous decomposition products are created, which are visible on the surface as brownish or silvery discoloration如果Figure 5 : 熔体在高温下长时间停留,会分解产生气体, Burnt streaks due to 在零件表面呈现棕色或银色条纹 high shearing heat in the gate图 5 : 由于浇口处高速剪切产 生银色条纹Figure 4 : Burnt streaks due to excessive residence time in the plasticizing cylinder图 4 : 由于在料筒停留时间过 Slide 28 / 92 长产生焦料20 DEC, 2002Figure 6 : Burnt streaks due to excessive residence time in the plasticizing cylinder图 6 : 由于在料筒停留时间过 长产生焦料 XU HAI QING , ADC AsiaAuto GMTStreak(Burnt Streak)焦痕(烧焦痕)◆ Physical cause :● Temperature too high or residence time is too long during pre-drying干燥时温度过高或停 原因 : 留时间过 ● Melt temperature too high ● 料筒温度过高 ● Shearing in the plasticizing unit too high (e.g. screw speed too high)预塑时剪切过大 (如, 螺杆转速太高) ● Residence time in the plasticizing unit is too long ● 在料筒停留时间过长 ● Shearing in the mold too high (e.g. injection rate too high) ● 模具内时剪切过大 (如,注射速度太高)Melt temperature above the processing range? 料筒温度是否超过正常范围?Yes YesNoIs the melt residence time within the critical range? 停留时间是否处于临界状态?⑴ Reduce melt temperature : cylinder temp.↓, Screw Speed↓ ⑵ Reduce back pressure ⑴ 降低料筒温度 、螺杆转速⑵ 减小背压NoBurnt streaks appearing periodically or visible after Yes injecting “into the air”?是否周期性出现或对空注射后仍有?⑴ Reduce cycle Time ⑴ 缩短周期 ⑵ Increase plasticizing time delay ⑵ 增加塑化前延时时间 ⑶ Use the machine to higher capacity : increase stroke ⑶ 采用高容量机器 ⑴ Avoid dead spots flow impeding areas in the gate system and in the plasticizing unit⑴ 消除浇注系统和塑化单元流动死角 ⑵ Check the plasticizing unit for wear ⑵ 检查塑化单元磨损 ⑶ Check the granules condition and feed ⑶ 检查粒料状态和进料 ⑴ Lower injection rate (injection profile : slow → fast) ⑴ 降低速度 ⑵ Check hot runner ⑵ 检查热流道 ⑶ Avoid sharp edges in the gate system⑶ 消除浇口部位尖角 ⑴ Lower injection rate ⑴ 降低速度 ⑵ Avoid sharp edges ⑵ 消除尖角NoBurnt streaks near the gate?是否在浇口附近?YesNoSlide 29 / 9220 DEC, 2002⑶ Avoid small runner ⑶ 避免小的流道 ⑷ Check sprue and gate system ⑷ 检查浇注系统 ⑸ Check nozzle cross-section ⑸ 检查喷嘴截面 ⑹ Check functioning shut-off nozzle ⑹ 检查自锁喷嘴 ⑺ Check the pre-drying of material ⑺ 检查材料干燥 ⑻ Reduce regrind ⑻ 减少回料 ⑼Asia Use molding compound or color agent with GMT high thermal stability XU HAI QING , ADC Auto ⑼ 采用高稳定的材料或色母Streak (Moisture Streak)焦痕(银丝)Moisture streaks appear on the surface Figure 8 : of the molded part as U-shaped profile, Left: Streaks due to moist granules open against the direction of flow. The Right: due to moisture surface around the silvery streak often on the mold surface rough and porous.银丝在产品表面呈现U型 图8:左:水分含量高 ,开口对着流动方向。