各种加工方法的经济精度和表面粗糙度
数控 铣工理论复习题

数控铣工技师理论复习题一、填空题(请将正确答案填入题内空白处。
每题1分)1.是规范约束从业人员职业活动的行为准则。
2.合格零件的应在两个极限尺寸所限制的尺寸范围内。
3.目前数控机床的主轴驱动系统多采用交流主轴电动机配备控制的方式。
4.分摩擦传动和啮合传动两种。
5.实际尺寸减去所得的代数差称为实际偏差.6.可分为滑动螺旋和滚动螺旋两种类型。
7.YT15属于类硬质合金刀具材料。
8.使工件与刀具产生相对运动以进行切削的最基本的运动称为。
9.平头支承钉,多用于定位。
10.对于机械进给传动系统,某些固定不变的或按确定规律变化的因素引起的定位误差属于。
11.在编制数控铣床的程序时应正确选择的位置,要避免刀具交换时碰工件或夹具。
12.是反映机床运动稳定性的一个基本指标。
13.在条件作用下,刀具切削刃硬度降低,会迅速变钝,甚至失去切削性能。
14.按照功能划分,FMS可分为加工系统、物流系统和三大部分。
15.高速切削时,加工中心的刀柄锥度以为宜。
16.在卧式铣床上,加工垂直孔系常用的方法有回转法、、角尺或定位键校正法。
17.精铣铸铁件时,为保证精铣质量,一般要求工件加工表面的硬度差HBS20。
18.是对从业人员工作态度的首要要求。
19.《中华人民共和国劳动法》是年全国人大常委会通过的。
20.步进电机对应每一个脉冲所旋转的角度称为步进电机的。
21.步进电动机采用“三相六拍”通电方式工作,“六拍”是指经过次切换绕组的通电状态为一个循环。
22.订立劳动合同的原则有、协商一致和依法订立。
23.QT400-15,其中400表示。
24.是CNC装置的核心,主要由运算器和控制器两大部分组成。
25.机件的某一部分向基本投影面投影所得的视图,称为。
26.切削是当前软金属材料最主要的精密和超精密加工方法。
27.位置公差对称度的符号为。
28.数控机床开机后,一般首先用手动或自动方式使机床各坐标轴返回,通常称回零。
29.在精密检测螺旋齿导程和螺旋角时,对导程较大而螺旋角较小的工件,应先测量出的误差,再换算成导程误差。
精密机械制造专业技术标准
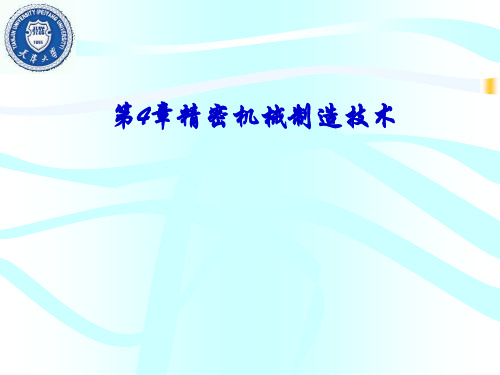
• 工序分散 设备数量多,操作工人多,生产面积大。
3.加工顺序的安排
(1)机械加工工序的安排 1)先加工基准表面,再加工其它表面
工艺路线开始安排的加工面应该是选做定位基
准的精基准面,先加工基准表面,然后以基准表面 定位,再去加工其它表面。 2)先加工主要表面,后加工次要表面
4.2.2 零件各表面加工顺序的安排
1.加工阶段的划分 (1)粗加工阶段 主要任务是切除工件表面 的大部分余量,并做出精基准。这阶段的精度 要求不高,主要是提高生产率。 (2)半精加工阶段 减小粗加工中留下的误 差,并使加工表面达到一定精度,为后续精加 工做准备。 (3)精加工阶段 使工件的尺寸、形状和位 置精度以及表面粗糙度达到或基本达到图纸规 定的要求。 (4)精密、超精密或光整加工阶段 当零件 的加工精度和表面质量要求很高时,在工艺过
与公差单位i的乘积表示: 标准公差T=等级系数a×公差单位i
公差单 i0位 .435D : 0.00D1
2.微小尺寸加工以绝对加工误差来判断加工精度, 称作绝对精度。
微小尺寸加工的绝大部分都落在了精密与超精 密加工范围内,对微小尺寸加工分为:
超 微微 细细 加加 工工 : 以:尺寸来区分 纳 微米 米工 工艺 艺( (或 或术 术 称 称) ) 以 纳 微加 米 米工 技 技精度来表
划分加工阶段的目的:
(1)满足循序渐进的原则 工件的加工是由粗到精逐步达到要求的,工件
粗加工时需要去除的余量较大。因而切削力、切削 热较大,工艺系统的受力变形、热变形及工件内应 力都较大。因而要划分若干工序,逐步消除。 (2)合理安排机床
由于粗加工主要是为了去除工件表面的大部分 余量,因而,粗加工可以选用功率大、精度低而加 工效率高的机床进行加工,而精加工阶段可以选用 与加工精度相适应的精密机床进行加工。应严禁使 用精密机床做粗加工,以保持精密机床的精度水平。
汽车典型零件制造技术
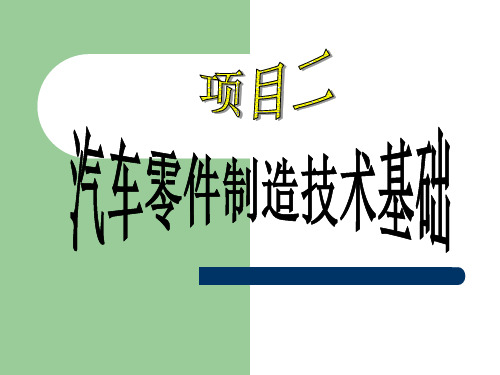
7
粗车-半精车一粗磨-精磨超精加工
IT5
0.12-0.l
主要用于 淬火钢,也 可用于未 淬火钢,但 不宜加工 有色金属
Hale Waihona Puke 主要用于8粗车-半精车-精车-精细车 (金刚石车)
IT6~7
0. 025~0.4
要求较高 的有色金
属加工
9
粗车-半精车-粗磨-精磨超精磨(或镜面磨)
IT5以上
0.006~0.025
极高精度
12.5~50
2 粗车一半精车
IT8~IT10
3 粗车一半精车—精车
4
粗车-半精车-精车-滚 压(或抛光)
IT7~IT8 IT7~IT8
3.2~6.3 0.8~1.6 0.025~0.2
适用于淬 火钢以外 的各种金
属
5 粗车一半精车-磨削
IT7~IT8 0.4~0.8
6 粗车一半精车-粗磨-精磨 IT6~IT7 0.1~0.4
工艺尺寸链的特征
尺寸链由一个自然形成的尺寸与若干个直接得到的尺寸所组成。 尺寸链一定是封闭的,且各尺寸按一定的顺序首尾相接。
尺寸链的组成
组成尺寸链的各个尺寸称为尺寸链的环
分为封闭环和组成环 封闭环 在加工(或测量)过程中最后自然形成的环称为封闭环 每个尺寸链必须有且仅能有一个封闭环。 组成环 在加工(或测量)过程中直接得到的环称为组成环。 按其对封闭环的影响,可分为增环和减环
大批大量生产的产品,可采用专用设各和工艺装备,如多刀、多轴机床或自动机 床等,将工序集中,也可将工序分散后组织流水线生产。但对一些结构简单 的产品,如轴承和刚性较差、精度较高的精密零件,则工序应适当分散。
设备与工装选择
机床的选择
图纸及工艺的理解(工艺部分)

图纸及工艺的理解(工艺部分)一工艺过程生产过程中直接改变对象的形状、尺寸、相对位置和性能的过程,称为工艺过程,可以通过不同的工艺方法来完成。
因而工艺过程又可具体分为铸造、锻造、冲压、焊接、机械加工、特种加工、热处理、表面处理、装配等工艺过程。
采用机械加工方法,直接改变加工对象的形状、尺寸和表面性能,使之成为成品的过程,称为机械加工工艺过程。
机械加工工艺过程是由若干个按一定顺序排列的工序组成。
1.工序工序是指一个或一组工人,在一个工作地对同一个或同时几个工件所连续完成的那一部分工艺过程。
划分工序的主要依据是工作地点是否改变和加工是否连续。
这里的连续,是指工序内的工作需连续完成,不能插入其它工作内容或者阶段性加工。
工序是组成工艺过程的基本单元。
工序又可细分为安装、工位、工步、走刀等组成部分。
2.安装安装是指工件(或装配单元)通过一次装夹后所完成的那一部分工序。
3.工位工位是指在一次装夹中,工件在机床上所占的每个位置上所完成那一部分工序。
4.工步工步是指在加工表面(或装配时的连续表面)不变、加工工具不变和切削用量不变的条件下,所连续完成的那部分工序。
工步是构成工序的基本单元。
5.走刀走刀是指刀具相对工件加工表面进行一次切削所完成的那部分工作。
每个工步可包括一次走刀或几次走刀。
二定位基准的选择一、基准的概念及分类零件上用以确定其它点、线、面的位置所依据的那些点、线、面称为基准。
根据其功用的不同,可分为设计基准、工艺基准两大类。
(1)设计基准在零件图上用以确定其它点、线、面的基准,称为设计基准。
(2)工艺基准零件在加工、测量、装配等工艺过程中使用的基准统称工艺基准。
工艺基准又可分为:1、装配基准在零件或部件装配时用以确定它在机器中相对位置的基准。
2、测量基准用以测量工件已加工表面所依据的基准。
例如以内孔定位用百(千)分表测量外圆表面的径向跳动,则内孔就是测量外圆表面径内跳动的测量基准。
3、工序基准在工序图中用以确定被加工表面位置所依据的基准。
车削加工

第一章车削加工概述车削加工是机械加工中最基本的一种加工方法,它所用的机床是车床,到目前为止已出现了卧式车床、立式车床、多刀车床、自动及半自动车床、仪表车床、数控车床等多种类型的车床。
所用的刀具为车刀,也可以用钻头、滚花刀、铰刀等,利用这些切削刀具与工件的一系列相对运动,可以完成多重切削。
车削加工的加工范围很广,可以加工出各种类型的带有旋转体表面的零件,如内外圆柱面、内外圆锥面、内外成形面、内外螺旋面等,其经济精度达到IT11~IT06,表面粗糙度为Ra12.5µm~0.8µm。
另外,在车床上安装上夹具和附件还可以进行镗孔、铣削、磨削、研磨、抛光等。
随着数字控制技术的发展,出现了数控车床与车削加工中心等现代化的制造设备,虽然目前所占的比例较少,但它以高柔性、高效率、高精度等传统加工所不能及的独特优点,正逐渐成为现代机械加工的重要技术装备之一,占据着越来越重要的地位。
1.1 机械类专业一、机械类专业实习纲要1、教学要求1) 基本知识①了解车削加工基本概念、设备、刀具、工、夹、量具、切削运动和切削用量适用范围及地位;②了解普通车床及其型号、结构、组成、作用、传动系统等并掌握其操作技术;③掌握车刀的组成,形状参数,材料性能及适用条件;④了解车削加工工件的安装夹持方法及所用附件,掌握三爪卡盘的应用;⑤了解车削加工工件的测量方法及量具并掌握其使用技术;⑥掌握基本车削加工方法,如车外圆、端面、锥面、钻孔、滚花、螺纹的加工工艺方法与技术;2)基本技能①熟练正确操作车床,掌握车床各手柄用途;②能独立完成车工作业件的加工;③掌握车工工具、量具的使用方法,正确测量工件;2、教学重点1)切削用量三要素的合理选择;2)车刀的几何参数;3)车床的操作;4)车削加工工艺过程;3、教学难点1)零件加工及操作;2)零件的测量准确程度;3)正确使用各类车刀;二、机械类专业实习总体安排三、机械类专业实习具体安排1、第一天1)上午 7:30~9:00 理论知识讲解(90′)车床与车削一、概述金属切削机床是用切削的方法将金属毛坯加工成机械零件的机器,是制造机器的机器,故又称为“工作母机”,一般简称机床。
机械加工工艺介绍

5.3 车削的工艺特点1.粗加工:经济精度可达到IT10,表面粗糙度在25-12.5之间;精加工:经济精度可达IT7左右,表面粗糙度Ra6.3-1.6之间。
2. 易于保证相互位置精度要求。
一次装夹可加工几个不同的表面,避免安装误差。
3. 刀具简单,制造、刃磨和安装方便,容易选用合理的几何形状和角度,有利于提高生产率。
4. 应用范围广泛,几乎所有绕定轴心旋转的内外回转体表面及端面,均可以用车削方法达到要求。
5. 可以用精细车的办法实现有色金属零件的高精度的加工(有色金属的高精度零件不适合采用磨削)6.5 铣削的工艺特点1.铣削加工的精度可达IT10-IT7,表面粗糙度可达6.3-1.6左右2.生产效率高,铣刀是多刀齿刀具,铣削时有几个刀齿同时参加切削,主运动是刀具的旋转,所以铣削的生产效率比刨削高。
3.容易产生振动,铣刀的刀齿切入和切出时产生振动,加工过程中切削面积和切削力变化较大。
4.刀齿的散热条件较好,在刀具旋转过程的不切削时间内,刀具可以得到一定的冷却。
5.与刨床相比,铣床价格高,适用于批量生产。
7.4 刨削加工的工艺特点1.加工精度通常为:精刨:IT7-IT10,粗糙度Ra为6.3-1.6之间。
2.通用性好,刨床简单、价格低、调整和操作简便,刨刀形状简单,制造、刃磨方便。
3.生产率一般比较低,主运动为往复直线运动,返回行程不参加切削。
4.适用于单件小批生产。
8.4 镗孔加工的工艺特点1.镗床主要用于加工大型工件或形状复杂工件上的孔和孔系。
例变速箱、发动机缸体等。
2.镗孔尺寸公差等级可达IT8 IT7,表面粗糙度值一般为1.6~0.8 m。
3.镗孔可以校正孔原有的轴线偏差或位置偏差。
1.镗床主要用于加工大型工件或形状复杂工件上的孔和孔系。
例变速箱、发动机缸体等。
2.镗孔尺寸公差等级可达IT8 IT7,表面粗糙度值一般为1.6~0.8 m。
3.镗孔可以校正孔原有的轴线偏差或位置偏差。
8.5 钻削的工艺特点1.钻削属于低精度(IT11-IT13)和高表面粗糙度的(Ra50-12.5)加工方法2.容易产生“引偏”,是加工过程中由于钻头弯曲产生孔径扩大、孔不圆等缺陷。
机械制造技术基础-加工方法

钻孔、扩孔、铰孔
立式钻床
通过移动工件位置 使被加工孔中心与主 轴中心对中,操作不 便,生产率不高。适 于单件小批生产中加 工中小型零件。
摇臂钻床
摇臂可绕立柱回转和升降,主轴箱可在摇臂上作水平移动。 工件固定不动,可方便地移动主轴,使主轴中心对准被加工 孔中心。适于单件小批生产中加工大而重的零件。
2. 车刀的结构形式
整体式(HSS)、焊接式、机械夹固式(重磨式、可转位式)
可转位式车刀的组成:
可转位刀片、刀垫、刀杆、夹紧机构 切削性能好,辅助时间短,生产率高
刀片夹紧方式: 1)上压式 夹紧力大,
定位可靠,阻碍流屑
2)偏心式 结构简单,
不碍流屑,夹紧力不大
3)综合式 夹紧力大,
耐冲击,结构复杂
1. CA6140型卧式车床的组成 (1)主轴箱 (2)进给箱 (3)溜板箱
(4)刀架 (5)尾架 (6)床身
2. CA6140型卧式车床的传动系统分析
为便于了解和分析机床的运动和传动情况, 常用机床的传动系统图。传动系统可分解为主 运动传动链和进给运动传动链。进给运动传动 链又可分为纵向机动和横向机动进给传动链、 螺纹进给传动链,还有刀架快速移动传动链。
车削加工
2.2.2 车床
车床占机床总数的20%~30% 车床种类:卧式、立式、转塔、仿形、自动和半自动、
专门化车床(曲轴、凸轮轴车床、铲齿车床)
CA6140 通用性好,加工范围广,能加工中小型轴类、盘
套类零件内外回转面、端面,加工米制、英制、模数制、径节制四种 标准螺纹及加大螺距、非标准螺距螺纹等。但结构复杂,自动化程度 低,适于单件小批生产及修配车间。
2.4.4 铣削方式
1)端铣和周铣 2)顺铣和逆铣 周铣有顺铣和逆铣两种方式。 顺铣切削厚度大,接触长度 短,铣刀寿命长,加工表面光 洁,但不宜加工带硬皮工件,且进给丝杠与螺母间应消除间 隙。否则,应采用逆铣。
常用加工精度对照表
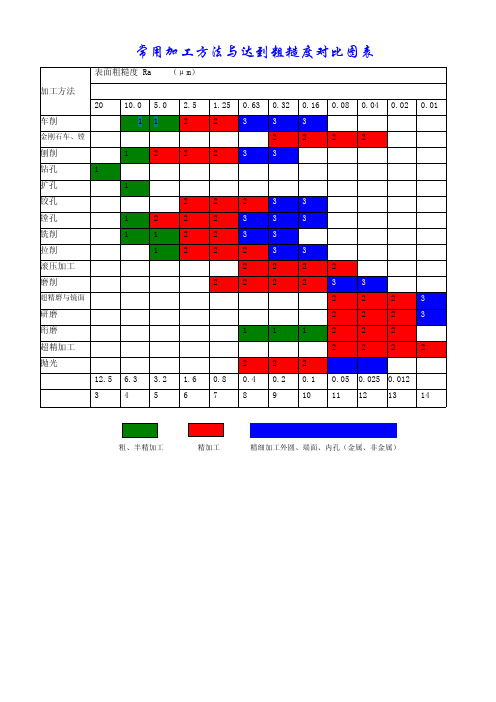
常用加工方法与达到粗糙度对比图表粗、半精加工精加工精细加工外圆、端面、内孔(金属、非金属)孔加工方案与经济公差序号加工方案经济公差等级表面粗糙度Ra(μm)适用范围1钻IT11-1320加工未淬火钢及铸铁的实心毛坯,也可用于加工有色金属(表面粗糙度稍差),孔径<(15-20)mm 2钻-铰IT8-9 5.0-2.53钻-粗铰-精铰IT7-8 2.5-1.254钻-扩IT1120-10.0同上,但孔径>(15-20)mm5钻-扩-铰IT8-9 5.0-2.56钻-扩-粗铰-精铰IT7 2.5-1.257钻-扩-机铰-手铰IT6-70.63-0.1608钻-(扩)-拉IT6-7 2.5-0.160大批大量生产(精度视)9粗镗(或扩孔)IT11-1320-10.0除淬火钢外各种材料,毛坯有铸出孔或锻出孔10粗镗(粗扩)-半精镗(精扩)IT8-9 5.0-2.511粗镗(扩)-半精镗(精扩)-精镗(铰)IT7-8 2.5-1.2512粗镗(扩)-半精镗(精扩)-精镗-浮动镗刀块精镗IT6-7 1.25-0.6313粗镗(扩)-半精镗-磨孔IT7-8 1.25-0.32主要用于加工淬火钢,也可用于不淬火钢,但不宜用于有色金属14粗镗(扩)-半精镗-粗磨-精磨IT6-70.32-0.16015粗镗-半精镗-精镗-金刚镗IT6-70.63-0.080主要用于精度要求较高的有色金属加工16钻-(扩)-粗铰-精铰-珩磨钻-(扩)-拉-珩磨粗镗-半精镗-精镗-珩磨IT6-70.32-0.040精度要求很高的孔17以研磨代替上述方案的珩磨IT6以上0.160-0.010平面加工方案与经济公差序号加工方案经济公差等级表面粗糙度Ra(μm)适用范围1粗车-半精车IT8-910-5.0端面2粗车-半精车-精车IT6-7 2.5-1.53粗车-半精车-磨削IT7-9 1.25-0.324粗刨(或粗铣)-精刨(或精铣)IT7-910.0-2.5一般不淬硬平面(端铣的表面粗糙度较好)5粗刨(或粗铣)-精刨(或精铣)-括研IT5-6 1.25-0.160精度要求较高的不淬硬平面批量较大时宜采用宽刃精刨方案6粗刨(或粗铣)-精刨(或精铣)-宽刃精刨IT6 1.25-0.327粗刨(或粗铣)-精刨(或精铣)-磨削IT6 1.25-0.32精度要求较高的淬硬平面或不淬硬平面8粗刨(或粗铣)-精刨(或精铣)-粗磨-精磨IT5-60.63-0.0409粗铣-拉IT6-9 1.25-0.32大量生产,较小的平面(精度视拉刀的精度而定)10粗铣-精铣-磨削-研磨IT5以上高精度平面外圆表面加工方案与经济公差序号加工方案经济公差等级表面粗糙度Ra(μm)适用范围1.粗车IT11-1380-20适用于淬火钢外的各种金属2.粗车-半精车IT8-910.0-5.03.粗车-半精车-精车IT6-7 2.5-1.254.粗车-半精车-精车-滚压(或抛光)IT6-70.32-0.0405.粗车-半精车-磨削IT6-7 1.25-0.63主要用于淬火钢,也可用于未淬火钢,但不宜加工有色金属6.粗车-半精车-粗磨-精磨IT5-60.63-0.1607.粗车-半精车-粗磨-精磨-超精加工(或轮式超精磨)IT50.160-0.0208.粗车-半精车-精车-金刚石车IT5-60.63-0.040主要用于要求较高的有色金属的加工9.粗车-半精车-粗磨-精磨-超精磨或镜面磨IT5以上0.040-0.010极高精度的外圆加工10.粗车-半精车-粗磨-精磨-研磨IT5以上0.160-0.010各种毛坯表面层厚度(mm)自由锻件模锻件铸件磁钢≤1.5磁钢≤1灰口铸铁1-4合金钢2-4合金钢≤0.5铸钢2-5。
各种加工方法的加工精度

各种加工方法的加工精度一:车削车削中工件旋转,形成主切削运动。
刀具沿平行旋转轴线运动时,就形成内、外园柱面。
刀具沿与轴线相交的斜线运动,就形成锥面。
仿形车床或数控车床上,可以控制刀具沿着一条曲线进给,则形成一特定的旋转曲面。
采用成型车刀,横向进给时,也可加工出旋转曲面来。
车削还可以加工螺纹面、端平面及偏心轴等。
车削加工精度一般为IT8—IT7,表面粗糙度为6.3—1.6μm。
精车时,可达IT6—IT5,粗糙度可达0.4—0.1μm。
车削的生产率较高,切削过程比较平稳,刀具较简单。
二:铣削主切削运动是刀具的旋转。
卧铣时,平面的形成是由铣刀的外园面上的刃形成的。
立铣时,平面是由铣刀的端面刃形成的。
提高铣刀的转速可以获得较高的切削速度,因此生产率较高。
但由于铣刀刀齿的切入、切出,形成冲击,切削过程容易产生振动,因而限制了表面质量的提高。
这种冲击,也加剧了刀具的磨损和破损,往往导致硬质合金刀片的碎裂。
在切离工件的一般时间内,可以得到一定冷却,因此散热条件较好。
按照铣削时主运动速度方向与工件进给方向的相同或相反,又分为顺铣和逆铣。
顺铣铣削力的水平分力与工件的进给方向相同,工件台进给丝杠与固定螺母之间一般有间隙存在,因此切削力容易引起工件和工作台一起向前窜动,使进给量突然增大,引起打刀。
在铣削铸件或锻件等表面有硬度的工件时,顺铣刀齿首先接触工件硬皮,加剧了铣刀的磨损。
逆铣可以避免顺铣时发生的窜动现象。
逆铣时,切削厚度从零开始逐渐增大,因而刀刃开始经历了一段在切削硬化的已加工表面上挤压滑行的阶段,加速了刀具的磨损。
同时,逆铣时,铣削力将工件上抬,易引起振动,这是逆铣的不利之处。
铣削的加工精度一般可达IT8—IT7,表面粗糙度为6.3—1.6μm。
普通铣削一般只能加工平面,用成形铣刀也可以加工出固定的曲面。
数控铣床可以用软件通过数控系统控制几个轴按一定关系联动,铣出复杂曲面来,这时一般采用球头铣刀。
数控铣床对加工叶轮机械的叶片、模具的模芯和型腔等形状复杂的工件,具有特别重要的意义。
数控加工培训及考证 五轴加工中心操作工理论题库判断题(100道)

1.职业道德体现的是职业对社会所负的道德责任与义务。
(√)2.企业标准比国家标准层次低,在标准要求上可稍低于国家标准。
(×)3.工作前必须戴好劳动保护物品,女工戴好工作帽,不准围围巾,禁止穿高跟鞋。
操作时不准戴手套,不准与他人闲谈,精神要集中。
(√)4.测量范围分别为0~25mm,25~50mm的两外径千分尺的示值范围相同。
(√)5.设计先进的机床夹具时,为了减少定位支承,简化夹具的结构,在满足工件加工工艺条件下,应当尽量采用完全定位。
(√)6.合格零件的实际尺寸可不在两个极限尺寸所限定的尺寸范围内。
(×)7.含碳量在0.25%~0.60%之间的碳素钢为中碳钢。
(√)8.表面热处理是仅对工件表层进行热处理以改变其组织和性能的工艺方法。
(√)9.T8中的数字8表示钢中平均含碳量为千分之8。
(√)10.工件材料的强度、硬度越高,则刀具寿命越低。
(√)11.高性能高速钢是在普通高速钢的基础上,用调整其基本化学成分和添加一些其他合金元素(如钒、钴、铅、硅、铌等)的办法,着重提高其耐热性和耐磨性而衍生出来的。
(√)12.任何切削加工方法都必须有几个主运动,可以有一个或几个进给运动。
(×)13.基准孔的最小极限尺寸等于基本尺寸。
(√)14.切削过程中,主运动的速度最高,消耗的功率最大。
(√)15.零件的各种表面所选的加工方法的经济精度和表面粗糙度应与加工表面的要求相吻合。
(√)16.数控机床伺服系统的增益系数Kv越大,进给响应越快,位置控制精度越高。
(√)17.石墨润滑脂用于外露重载的轴承,不宜用于滚动轴承。
(√)18.尺寸链计算中的反计算是已知组成环求封闭环的尺寸及公差。
(×)19.4轴联动或5轴联动加工与5个以上轴的同时加工,称为多轴加工。
(√)20.剖面图要画在视图以外,一般配置在剖切位置的延长线上,有时可以省略标注。
(×)21.H7/g6是小间隙配合,用于精密滑动零件配合部位。
各种加工方法的加工经济精度及粗糙度

8
刨
粗刨
11-13
5-20
半精刨
8-11
精刨
6-8
宽刀精刨
6
插
拉
粗拉
10-11
5-20
精拉
6-9
平磨
粗磨
8-10
半精磨
8-9
精磨
6-8
精密磨
6
刮
25x25
内点数
8-10
研磨
粗磨
6
精磨
5
精密磨
5
砂带磨
精磨
5-6
精密磨
5
滚压
7-10
精心搜集整理,只为你的需要
5-6
精珩
5
研磨
粗研
5-6
精研
5
精密研
5
挤
滚珠、滚柱扩孔器,挤压头
6-8
平面中各种加工方法的加工经济精度及表面粗糙度
加工方法
加工情况
加工经济精度(IT)
表面粗糙度Ra(um)
周铣
粗铣
11-13
5-20
半精铣
8-11
精铣
6-8
端铣
粗铣
11-13
5-20
半精铣
8-11
精铣
6-8
车
粗车
8-11
半精车
6-8扩Biblioteka 粗扩12-135-20
一次扩孔
11-13
10-40
精扩
9-11
铰
半精铰
8-9
精铰
6-7
手铰
5
拉
粗拉
9-10
一次拉孔
10-11
精拉
7-9
推
半精推
各种加工方法的加工经济精度及粗糙度

各种加工方法的加工经济精度及粗糙度加工方法是指将工件通过一定的手段和工具,经过一系列的操作和加工过程,使其达到预期的形状、尺寸和表面质量等要求的方法。
根据加工的具体要求和工件的特点不同,采用的加工方法也会有所差异。
下面将对常用的加工方法进行分析,包括加工经济、精度和粗糙度等方面。
1.切割加工切割加工是指通过切削刀具对工件进行切割和分离的加工方法,常见的有锯床、剪床、冲床等。
切割加工一般是用于中小批量生产,具有加工速度快、经济性好的特点。
但是由于切割刀具的形状和工艺的限制,其加工精度相对较低,且切割面往往存在毛刺等粗糙度问题。
2.车削加工车削加工是指利用车床上的刀具进行旋转切削的加工方法,适用于工件的外表面和内孔的现场加工。
车削加工具有加工精度高、表面质量好的特点,尤其适用于加工长度较长的工件。
但是车削加工一般速度较慢,且对车床的精度要求较高,加工成本较高。
3.铣削加工铣削加工是指通过铣床上的刀具进行切削的加工方法,适用于平面、曲面和螺纹等多种形状的加工。
铣削加工具有加工速度快、加工效率高的特点,能够实现多种加工方式,具有较高的经济性。
但是铣削加工对机床的刚性和稳定性要求较高,且铣削后的表面质量一般较差,需要进行后续处理。
4.电火花加工电火花加工(EDM)是指通过快速的电火花放电技术对工件进行加工的方法。
电火花加工具有非常高的精度和表面质量,能够加工出复杂的形状和细小的孔洞。
虽然电火花加工速度相对较慢,但是能够实现无模具、无切削力的加工方式,适用于高难度的工件加工。
然而,电火花加工一般需要进行后续的抛光处理,以达到更好的表面质量。
5.抛光加工抛光加工是指利用砂纸、磨料等工具将工件表面进行刮削和磨擦的加工方法,用于提高工件的表面光洁度和精度。
抛光加工具有较好的加工精度和表面质量,但是加工速度相对较慢,且需要一定的手工操作,劳动强度较大。
综上所述,不同的加工方法在加工经济、精度和粗糙度等方面存在不同的特点。
各种加工方法能达到的精度

非机械加工加工方法精度等级特点应用范围铸造木模手工砂型可铸出形状复杂的零件,生产率低,加工余量大。
精度低,表面有气孔、砂眼、结砂、硬皮等缺陷,废品率高,单件及小批量生产,适用于铁碳合金,有色金属及合金。
金属模机械砂型可铸出形状复杂的零件,生产率较高,加工余量小,但铸件成本高。
大批量生产,适用于铁碳合金,有色金属及合金。
金属型浇铸尺寸精度:0.1-0.5㎜Ra:6.3-12.5可铸出形状复杂的零件,铸件力学性能较好,中小型零件的大批量生产适用于铁碳合金,有色金属及合金。
离心铸造尺寸精度:IT8-IT9Ra:12.5铸件力学性能较好,材料消耗低,生产率高,但是需要专门设备大批量生成适用于铁碳合金,有色金属及合金。
融模浇铸尺寸精度:0.05-0.15㎜Ra:3.2-12.5可铸出形状复杂的小型零件,铸件精度高可直接铸出成品单件及批量适用于铸出难加工材料压铸尺寸精度:0.05-0.15㎜Ra:3.2-6.3精度高,可直接铸出成品,生产率高,但设备贵大批量生产适用于有色金属锻造自由锻造加工余量:1.5-10㎜形状简单,精度低,生产率低单件小批量生产适用于碳素钢,合金钢模锻尺寸偏差0.1-0.2㎜Ra:12.5尺寸精度高,毛坯的纤维组织好,强度高,生产率较高,需要专门的设备及锻模大批量生产适用于碳素钢,合金钢精密锻模尺寸偏差0.05-0.1㎜尺寸精度高,尺寸变形小,能节省材料和工时,生产率高,需要专门的精锻机大批量生产适用于碳素钢,合金钢冲压尺寸偏差0.05-0.5㎜Ra:0.8-1.6可冲出形状复杂的零件,可不再进行机械加工和只进行精加工,生产率高批量较大的中小尺寸的板料零件冷挤压尺寸精度:IT6-IT7Ra:0.8-1.6可挤压形状简单,尺寸较小的零件,可不经车削加工大批量生产适用于挤压碳钢,低合金钢,高速钢,轴承钢和不锈钢焊接制造简单,节约材料,重量轻,生产周期短,但变形大,抗振性差,需要时效处理.单件及批量生产碳钢及合金钢型材热轧尺寸公差:1-2.5㎜Ra:6.3-12.5圆形,方形,扁形,六角形及其他形状批量生产冷轧尺寸公差:0.05-1.5㎜Ra:1.6-3.2圆形,方形,扁形,六角形及其他形状大批量生产尺寸公差:0.02-0.05㎜一般形状较简单,设备简单,金属大批量生产,以铁基,外圆柱面加工能达到的精度及平面粗糙度加工方法尺寸精度等级表面粗糙度Ra: 备注粗车IT11以下25-100粗车--半精车IT8-10 6.3-12.5粗车--半精车--精车IT7-8 1.6-6.3粗车--半精车--磨削IT7-8 1.6-6.3细车(有色金属及合金) IT6-7 0.2-1.6粗磨--精磨IT6-7 0.2-1.6精车-滚压0.2-1.6粗车--半精车--粗磨--精磨-- 研磨IT5 0.1-0.4 超精加工抛光粗车--半精车--粗磨--精磨-- 镜面磨削IT5以上0.012-0.1 粗研磨精研磨超精加工抛光平面加工能达到的精度及平面粗糙度加工方法尺寸精度等级 表面粗糙度Ra: 备注粗刨 IT11-13Ra25-100粗铣粗刨—半精刨 IT8-11Ra3.2-12.5粗铣-半精铣车平面 拉削IT7-9 粗刨—半精刨 粗铣--半精铣宽刀精刨IT6-9Ra0.4-1.6高速精刨磨 刮研粗拉—精拉 IT6Ra0.2-0.4粗刨—半精刨 粗铣--半精铣 粗磨-精磨IT5-6粗刨—半精刨 粗铣--半精铣 粗磨-精磨-研磨-超精加工IT5 Ra0.2-0.12在钻床上加工孔(孔的长度不超过直径的5倍)孔的公差等级在实体材料上钻孔预先铸出或热冲出的孔孔径加工方法孔径加工方法IT12-13 一次钻孔用车刀或扩孔钻镗孔IT11≤10 一次钻孔≤80粗扩和精扩>10-30 钻孔及扩孔用车刀粗镗和精镗>30-80钻孔-扩钻-扩孔根据余量一次镗孔或扩孔钻孔-用扩孔刀或车刀镗孔及扩孔IT9-10≤10 钻孔及铰孔≤80扩孔(一次或两次,根据余量而定)及铰孔>10-30 钻孔-扩孔-一次铰孔>30-80钻孔-扩孔-扩钻及铰孔用车刀镗孔(一次或两次,根据余量而定)及铰孔钻孔-用扩孔刀镗孔-扩孔-铰孔IT7-8≤10 钻孔及一次或两次铰孔≤80扩孔(一次或两次,根据余量而定)及一次或两次铰孔>10-30 钻孔-扩孔--一次或两次铰孔>30-80钻孔-扩钻(或用扩孔刀镗孔)-扩孔-一次或两次铰孔用车刀镗孔(一次或两次,根据余量而定)及一次或两次铰孔注: 当孔径≤30㎜,直径余量≤4㎜,和孔径>30-80㎜, 直径余量≤4㎜时,采用一次扩孔或一次镗孔在车床或其他机床上加工孔孔的公差等级在实体材料上钻孔预先铸出或热冲出的孔孔径加工方法孔径加工方法IT12-13 一次钻孔用车刀或扩孔钻镗孔IT11≤10 用定心钻及钻头钻孔一次或二次扩孔(根据余量而定)>10-30用定心钻及钻头钻孔和用扩孔刀或车刀、扩孔钻镗孔用车刀一次或二次镗孔>30-80用定心钻及钻头钻孔-扩钻-扩孔用定心钻及钻头钻孔及用车刀镗孔IT9-10≤10 用定心钻和钻头钻孔及铰孔扩孔及铰孔>10-30用定心钻钻头钻孔-扩孔-铰孔用车刀镗孔及铰孔用定心钻钻头钻孔-用车刀扩孔或镗孔及铰孔粗镗孔、精镗孔(不铰)用定心钻和钻头钻孔-扩孔或用车刀镗孔及磨孔粗镗孔、精镗孔及磨孔用定心钻和钻头钻孔及拉孔用车刀镗孔及拉孔>30-80用定心钻和钻头钻孔-扩钻-扩孔及铰孔钻用定心钻和钻头钻孔-用车刀或扩孔刀镗孔及铰孔用定心钻和钻头钻孔-用车刀镗孔(或扩孔及磨孔)用定心钻和钻头钻孔及拉孔IT7-8≤10用定心钻和钻头钻孔、粗铰(或用扩孔刀镗孔)及精铰≤80一次或两次扩孔(,根据余量而定)、粗铰(或用扩孔刀镗孔)及精铰孔>10-30用定心钻和钻头钻孔-扩孔(或用车刀镗孔)、粗铰(或用扩孔刀镗孔)及精铰用车刀镗孔(根据余量而定)、粗铰(或用扩孔刀镗孔)及精铰用定心钻和钻头钻孔、用车刀扩孔、镗孔及磨孔粗镗-半精镗-精镗用定心钻和钻头钻孔及拉孔用车刀镗孔及拉孔粗镗-精镗-磨孔>30-80用定心钻和钻头钻孔-扩钻-扩孔-粗精铰孔>80用车刀粗镗及精镗-铰孔用定心钻和钻头钻孔、用车刀镗孔、粗铰(或用扩孔刀镗孔)及精铰粗镗-半精镗-精镗用定心钻和钻头钻孔、用车刀或扩孔钻镗孔及磨孔粗精镗及磨孔用定心钻和钻头钻孔及拉孔IT5-6 加工1级精度孔的最后工序应该是用金刚石细镗用精密调整的车刀镗细磨及精镗注: 1、用定心钻钻孔仅适用于车床、六角车床及自动车床上齿轮加工经济精度加工方法精度等级加工方法精度等级多头滚刀铣齿(m=1-20㎜) 8-10 车齿7-8单头滚刀铣齿(m=1-20㎜) 8-10磨齿成型砂轮仿形法5-6精密滚刀:精度等级:AA 7 盘形砂轮范成法4-6一般滚刀: 精度等级:A 8两个盘形砂轮范成法(马格磨齿机)3-6 精度等级:B 9 蜗杆砂轮范成法4-6 精度等级:C 10 用铸铁研磨轮研齿4-6圆盘形插齿刀插齿(m=1-20㎜) 精度等级:AA 7 直齿锥齿轮刨齿8 精度等级:A 8 弧齿锥齿轮铣齿8 精度等级:B 9 蜗轮模数滚刀滚蜗轮8圆盘形剃齿刀剃齿(m=1-20㎜) 精度等级:A 6 径向或轴向进给热轧齿形(m=2-8㎜) 8-9 精度等级:B 7 热轧后冷校准齿形(m=2-8㎜) 7-8 精度等级:C 8 冷轧齿形(m≤1.5㎜)7。
各种加工方法的经济精度和表面粗糙度
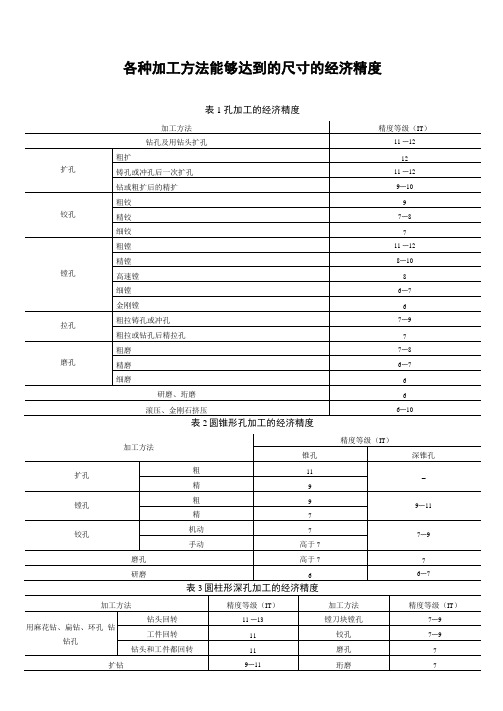
各种加工方法能够达到的尺寸的经济精度表1 孔加工的经济精度表2圆锥形孔加工的经济精度表3圆柱形深孔加工的经济精度6mm7mm91<1m2端铣刀铣削的加工精度在相同的条件下大体上比圆柱铣刀铣削高一级。
3细铣仅用于端铣刀铣削。
11各种加工方法能够达到的形状的经济精度2315各种加工方法所能够达到的相互位置的经济精度表19同轴度的经济精度表20 轴心线相互平行的孔的位置经济精度注:对于钻、卧镗及组合机床的镗孔偏差同样适用于铰孔。
表21轴心线相互垂直的孔的位置经济精度各种加工方法能够达到的零件表面粗糙度表22 各种加工方法能够达到的零件表面粗糙度各类型面的加工方案及经济精度表23外圆表面加工方案标准公差及形位公差附表1标准公差值1mm IT14IT1813 22-2-21 16:331 《金属机械加工工艺人员手册》修订本上海科学技术出版社1981年2 《机械制造工艺学》顾崇衔等编著陕西科学技术出版社1982年3 《航空机械设计手册》第三机械工业部612所编1979年4 《机械制造工艺学课程设计简明手册》华中工学院机械制造工艺教研室编1981年5 《机械工程手册》第46篇机械工业出版社1981年6 《圆柱齿轮加工》上海科学技术出版社1979年切削用量切削用量的选择原则正确地选择切削用量,对提高切削效率,保证必要的刀具耐用度和经济性,保证加工质量,具有重要的作用。
1粗加工切削用量的选择原则:粗加工时加工精度与表面求不高,毛坯余量较大。
因此,选择粗加工的切削用量时,要尽可能保证较高的单位时间金属切除量(金属切除率)和必要的刀具耐用度,以提高生产效率和降低加工成本。
金属切除率可以用下式计算:Z k vfa X1000式中Zw——单位时间内的金属切除量(mm3/s);v --- 切削速度(m/s);f --- 进给量(mm/r);a p -------- 切削深度(mm)。
提高切削速度、增大进给量和切削深度,都能提高金属切除率。
加工余量查询
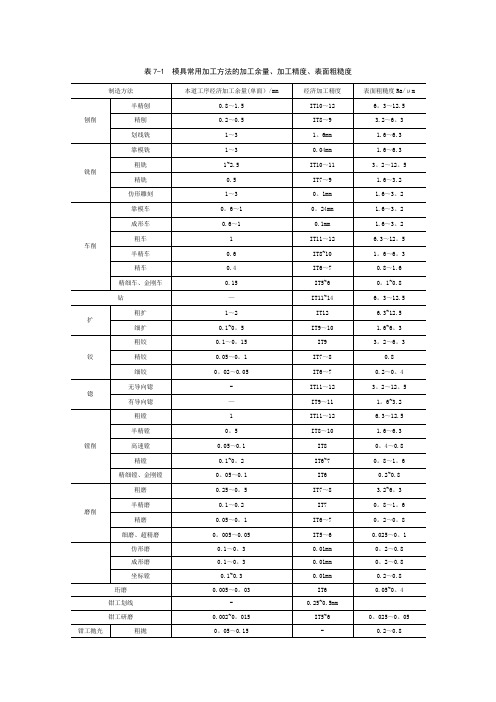
表7-1 模具常用加工方法的加工余量、加工精度、表面粗糙度细抛、镜面抛0。
005~0.01 —0.001~0.1 电火花成形加工—0.05~0。
1mm 1.25~2.5电火花线切割—0。
005~0.01mm 1.25~2.5电解成形加工—±0。
05~0。
2mm 0。
8~3.2 电解抛光0.1~0.15 —0.025~0.8电解磨削0。
1~0。
15 IT6~7 0.025~0.8照相腐蚀0.1~0.4 - 0。
1~0.8超声抛光0.02~0。
1 —0.01~0.1 磨料流动抛光0.02~0。
1 —0.01~0.1 冷挤压—IT7~8 0.08~0。
32注:经济加工余量是指本道工序的比较合理、经济的加工余量。
本道工序加工余量要视加工基本尺寸、工件材料、热处理状况、前道工序的加工结果等具体情况而定。
1。
加工总余量的确定(1)加工总余量和工序余量加工总余量(毛坯余量)—毛坯尺寸与零件图设计尺寸之差。
工序余量—相邻两工序的工序尺寸之差。
某个表面加工余量Z∑为该表面各加工工序的工序余量Zi之和,即式中n—该表面的加工工序数。
(2)影响加工余量的因素1)加工表面上的表面粗糙度和表面缺陷层深度。
2)加工前或上工序的尺寸公差。
3)加工前或上工序各表面相互位置的空间偏差。
4)本工序加工时的装夹误差.(3)查表法确定机械加工余量,总余量和半精加工、精加工工序余量可参考有关标准或工艺手册查得,并应结合实际情况加以修正。
粗加工工序余量减去半精加工和精加工工序余量而得到。
2. 工序尺寸及公差计算对于各种工序的定位基准与设计基准重合时的表面的多次加工(如外圆和内孔的加工),工序尺寸可由后续加工的工序尺寸加工上(对被包容面)或减去(对包容面)公称工序余量而求得;工序尺寸公差按所用加工方法的经济精度选定。
图4—2 表示外圆加工时加工余量、工序尺寸及其公差的分布,图中Z1、Z2、Z3为粗加工、半精加工、精加工的公称余量;To为毛坯公差.T1 、T2、T3为粗加工、半精加工、精加工的工序尺寸公差。
6.3 经济精度和经济表面粗糙度(了解)

根据统计资料证 明,任何一种加 工方法的加工误 差与加工成本之 间的关系,可用 图6-15 所示曲线 表示 。 这条曲 线可以分成三段: AB段:加工误差 小精度高,但成 本太高,不经济。
• CD 段:曲线与横坐标几乎平行,说明加工精度 很低,但加工成本不能无限制下降,它必须消 耗这种加工方法所要求的最低成本,所以,既 难以保证质量,也不经济 。
三、常用加工方法能达到的表面粗糙度
常用加工方法能达到的经济表面粗糙度 值的参考数据见表6 - 12 。
• BC段:既可达到一定的加工精度,又不会使成 本过高,所以经济。
经济精度是指每种加工方法在正常生产
条件(完好的设备、使用必要的刀具和夹具、 操作者具有熟练的技术、合理的定额工时) 下,能较经济地达到的加工精度范围 。
经济精度是由几种不同加工方法相互比
较的结果 。 如图6-16所示为车、磨外圆加 工成本的比较,可见,当零件的加工误差小于 △A时,采用磨削比较经济;而当零件的加工 误差大于ΔA时,则采用车削比较经济 。 △A 就是磨削加工经济精度的下限,同时也是车 削加工经济精度的上限 。 加工经济精度也
6.3 经济精度和经济表面粗糙度
前面已讲述了车、铣、刨 、磨、钻、镗等 加工方法,并且知道了这些加工方法所用的机 床、刀具和夹具 。 显然,不同的加工方法有各 自不同的用途,它们所能达到的加工精度和表 面粗糙度也是不同的。 即使是同一种加工方 法,使用同一台机床,由于操作者技术水平、刀 具刃磨质量、机床调整质量和切削用量的不同, 所得到的加工精度和表面粗糙度也会有很大的 差别。 例如,精车加工一般为 IT10、IT9 级精度, 若由高级技师进行精细加工也可能为 IT7 、IT6 级精度,但工件的加工工时和成本也就提高了 。
常用加工精度对照表
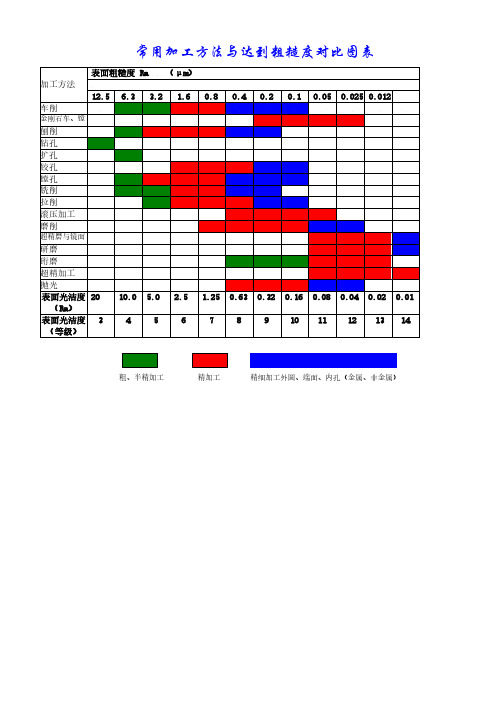
磁钢
≤1.5
合金钢
2-4
模锻件
磁钢
≤1
合金钢
≤0.5
铸件
灰口铸铁
1-4
铸钢
2-5
2
钻-铰
IT8-9
5.0-2.5 坯,也可用于加工有色金属(表面粗
3
钻-粗铰-精铰
IT7-8
2.5-1.25 糙度稍差),孔径<(15-20)mm
4
钻-扩
IT11
20-10.0
5
钻-扩-铰
6
钻-扩-粗铰-精铰
IT8-9 IT7
5.0-2.5 2.5-1.25
同上,但孔径>(15-20)mm
7
钻-扩-机铰-手铰
常用加工方法与达到粗糙度对比图表
表面粗糙度 Ra (μm)
加工方法
12.5 6.3 3.2 1.6 0.8
车削
金刚石车、镗
刨削
钻孔
扩孔
铰孔
镗孔
铣削
拉削
滚压加工
磨削
超精磨与镜面
研磨
珩磨
超精加工
抛光
表面光洁度 20 10.0 5.0 2.5 1.25
(Ra)
表面光洁度 3
4
5
6
7
(等级)
0.4
0.63 8
8. 粗车-半精车-精车-金刚石车
9.
粗车-半精车-粗磨-精磨-超精磨或 镜面磨
10. 粗车-半精车-粗磨-精磨-研磨
经济公差等 表面粗糙度
级
Ra(μm)
适用范围
IT11-13
80-20
IT8-9 IT6-7
10.0-5.0 2.5-1.25
- 1、下载文档前请自行甄别文档内容的完整性,平台不提供额外的编辑、内容补充、找答案等附加服务。
- 2、"仅部分预览"的文档,不可在线预览部分如存在完整性等问题,可反馈申请退款(可完整预览的文档不适用该条件!)。
- 3、如文档侵犯您的权益,请联系客服反馈,我们会尽快为您处理(人工客服工作时间:9:00-18:30)。
各种加工方法能够达到的尺寸的经济精度
表1 孔加工的经济精度
表2 圆锥形孔加工的经济精度
表3 圆柱形深孔加工的经济精度
表4 花键孔加工的经济精度
表5 外圆柱表面加工的经济精度
表6 端面加工的经济精度(mm)
表7 用成形铣刀加工的经济精度(mm)
注:指加工表面至基准的尺寸精度。
表8 同时加工平行表面的经刘精度(mm)
注:指两平行表面距离的尺寸精度。
表9 平面加工的经济精度
注:1 表内资料适用于尺寸<1m,结构刚性好的零件加工,用光洁的加工表面作为定位和测量基准。
2 端铣刀铣削的加工精度在相同的条件下大体上比圆柱铣刀铣削高一级。
3 细铣仅用于端铣刀铣削。
表10 公制螺纹加工的经济精度
表11 花键加工的经济精度
表12 齿形加工的经济精度
各种加工方法能够达到的形状的经济精度
表13 平面度和直线度的经济精度
表14 圆柱形表面形状精度的经济精度
注:形状精度等级的公差值见附表2、3。
表15 曲面加工的经济精度
表16 在各种机床上加工时形状的平均经济精度
各种加工方法所能够达到的相互位置的经济精度
表17 平行度的经济精度
表18 端面跳动和垂直度的经济精度
表19 同轴度的经济精度
表20 轴心线相互平行的孔的位置经济精度
注:对于钻、卧镗及组合机床的镗孔偏差同样适用于铰孔。
表21 轴心线相互垂直的孔的位置经济精度
注:在镗空间的垂直孔时,中心距误差可按上式相应的找正方法选用。
各种加工方法能够达到的零件表面粗糙度
表22 各种加工方法能够达到的零件表面粗糙度
各类型面的加工方案及经济精度
表23 外圆表面加工方案
表24 孔加工方案
表25 平面加工方案
——机械篇
标准公差及形位公差
附表1 标准公差值
注:基本尺寸小于1mm时,无IT14至IT18。
13 22-4-25 10:32
附表2 平面度、直线度公差值
附表3 圆度、圆柱度公差值
附表4 平行度、垂直度、倾斜度公差值
附表5 同轴度、对称度、圆跳动、全跳动公差值
参考文献
1 《金属机械加工工艺人员手册》修订本上海科学技术出版社1981年
2 《机械制造工艺学》顾崇衔等编著陕西科学技术出版社1982年
3 《航空机械设计手册》第三机械工业部612所编1979年
4 《机械制造工艺学课程设计简明手册》华中工学院机械制造工艺教研室编1981年
5 《机械工程手册》第46篇机械工业出版社1981年
6 《圆柱齿轮加工》上海科学技术出版社1979年
切削用量
切削用量的选择原则
正确地选择切削用量,对提高切削效率,保证必要的刀具耐用度和经济性,保证加工质量,具有重要的作用。
1 粗加工切削用量的选择原则:
粗加工时加工精度与表面求不高,毛坯余量较大。
因此,选择粗加工的切削用量时,要尽可能保证较高的单位时间金属切除量(金属切除率)和必要的刀具耐用度,以提高生产效率和降低加工成本。
金属切除率可以用下式计算:
1000⨯≈p w vfa Z
式中 Zw ——单位时间内的金属切除量(mm 3/s); v ———切削速度(m/s); f ———进给量(mm/r); a p ——切削深度(mm)。
提高切削速度、增大进给量和切削深度,都能提高金属切除率。
但是,在这三个因素中,影响刀具耐用度最大的是切削速度,其次是进给量,影响最小的是切削深度。
所以粗加工切削用量的选择原则是:首先考虑选择一个尽可能大的吃刀深度a p ,其次选择一个较大的进给量f ,最后确定一个合适的切削速度v 。
选用较大的a p 和f 以后,刀具耐用度t 显然也会下降,但要比v 对t 的影响小得多,只要稍微降低一下v 便可以使t 回升到规定的合理数值。
因此,能使v 、f 、a p 的乘积较大,从而保证较高的金属切除率。
此外,增大a p 可使走刀次数减少,增大f 又有利于断屑。
因此,根据以上原则选择粗加工切削用量对于提高生产效率,减少刀具消耗,降低加工成本是比较有利的。
切削深度的选择:
粗加工时切削深度应根据工件的加工余量和由机床、夹具、刀具、工件组成的工艺系统的刚性来确定。
在保留半精加工、精加工必要余量的前提下,应当尽量将粗加工余量一次切掉。
只有当总加工余量太大,一次切不完时,才考虑分几次走刀。
进给量的选择:
粗加工时限制进给量提高的因素主要是切削力。
因此,进给量应根据机床—夹具—刀具—工件系统的刚性和强度来确定。
选择进给量时应考虑到机床进给机构的强度、刀杆尺寸、刀片鹌鹑、工件的直径和长度等。
在工艺系统的刚性和强度好的情况下,可选用大一些的进给量;在刚性和强度较差的情况下,应适当减小进给量。
表13所示为粗车外圆和端面时的进给量,可供选用时参考。
切削速度v的选择:
粗加工时,切削速度v主要受刀具耐用度和机床功率的限制。
合理的切削速度一般不需要经过精确计算,而是根据生产实践经验和有关资料确定。
切削深度、进给量和切削速度三者决定了切削功率,在确定切削速度时必须考虑到机床的许用功率。
如超过了机床的许用功率,则应适当降低切削速度。
2 精加工时切削用量的选择原则:
精加工时加工精度和表面粗糙度要求较高,加工余量要小且较均匀。
因此,选择精加工的切削用量时应着重考虑如何保证加工质量,并在此基础上尽量提高生产效率。
切削深度的选择:
精加工时的切削深度应根据粗加工留下的余量确定。
通常希望精加工余量不要留得太大,否则,当吃刀深度a p较大时,切削力增加较显著,影响加工质量。
进给量的选择:
精加工时限制进给量提高的主要因素是表面粗糙度。
进给量f增大时,虽有利于断屑,但残留面积高度增大,切削力上升,表面质量下降。
表14所示为半精车和精车时的进给量,可供选用时参考。
切削速度v的选择:
切削速度v提高时,切削变形减小,切削力有所下降,而且不会产生积屑瘤和鳞刺。
一般选用切削性能好的刀具材料和合理的几何参数,以尽可能提高切削速度v。
只有当切削速度受到工艺条件限制而不能提高时,才选用低速,以避开积屑瘤产生范围。
由此可见,精加工时应选用较小的吃刀深度a p和进给量f,并在保证合理刀具耐用度的前提下,选取尽可能高的切削速度v,以保证加工精度和表面质量,同时满足生产率的要求。
一、车削
1 车削切削力的计算:
1) 用实验公式计算车削切削力。