KANBAN_ystem
看板与安灯物流拉动系统简介

KANBAN SYSTEM 看板物料拉动系统
线旁操作工每次从新的物流箱中取出第一个部件时,投出箱内那一张看板卡,线旁班组长根
据安东板音乐,每半小时将料架上的看板卡统
一放到车间中央邮箱,
RDC 配送三一拉动的物料到看板工程
物流工将线旁拉动的物料运
送至线旁料架上,并在每个物流工人从该工位上收集空
箱,收卡员工每半小时从车
送回空箱,整理收回看板卡
进行电脑扫描向RDC 进行物料
拉动 1 2 3 4
5
ANDON SYSTEM 安东物料拉动系统
当暗灯上用剩最后几个零件时(拇指卡物料工从协配仓库库位中取出物料,接收工将物流工沿生产线运送物料到
所需要工位,并取走空箱
暗灯上物料索取灯亮,电脑
系统并同时向供应商发出物物流工从暗灯板上取走暗灯
卡,并按动按钮向装配人员
确认物料已经发送
1 2 3 4
5 E F G
A B C
暗
灯
卡 物流工送回空的物流料架并
将暗灯卡放回暗灯按板上
6。
丰田工作法:丰田的工作哲学与方法大全_札记

《丰田工作法:丰田的工作哲学与方法大全》阅读随笔目录一、丰田工作法的核心理念与特点 (2)1. 丰田的哲学思想和工作文化 (2)1.1 精益求精,追求卓越品质 (4)1.2 团队合作,全员参与管理 (5)1.3 注重创新,适应变革环境 (6)1.4 客户至上,满足用户需求 (7)2. 丰田工作法的特点分析 (8)2.1 目标明确,计划性强 (9)2.2 注重细节,精益求精 (10)2.3 强调执行力,追求实效 (12)2.4 持续改进,不断优化 (13)二、丰田工作法的具体实践方法 (14)1. 生产流程优化与管理 (15)1.1 精益生产流程的建立与实施 (17)1.2 标准化作业与生产效率提升 (18)1.3 生产线平衡与在制品控制 (20)1.4 生产过程中的质量控制 (21)2. 人才培养与团队建设 (22)2.1 丰田式人才培养理念及方法 (24)2.2 团队建设与沟通技巧培训 (25)2.3 员工职业生涯规划与支持 (26)2.4 多元化背景下的文化融合 (27)三、丰田工作法在汽车产业中的应用实例 (28)一、丰田工作法的核心理念与特点丰田工作法,作为丰田生产方式(Toyota Production System, TPS)的精髓,其核心理念在于持续改进、尊重个性、全员参与以及精益求精。
这一工作法并非仅仅关注生产效率的提升,更强调在每一个环节中寻求最佳实践,以实现产品质量、成本控制、交货期等多方面的均衡优化。
丰田工作法的特点尤为显著,它注重个性化定制,即根据每位员工的技能和特长来分配工作任务,从而激发员工的创造力和责任感。
丰田工作法倡导全员参与,鼓励员工在工作中不断发现问题、解决问题,通过持续的改进过程提升工作效率和质量。
丰田工作法还强调对细节的极致追求,无论是生产线的布局还是设备的维护,都力求做到尽善尽美。
丰田工作法是一种以人为本、追求卓越的工作哲学和方法论。
它引导人们在工作中不断学习、创新和进步,最终实现个人和企业的共同发展。
9精益生产第二单元 工具八 看板-学员手册
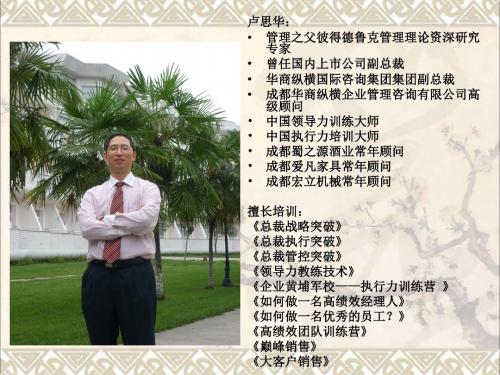
4)
5) 6)
WC-1成品移向WC-2原料的位置WC-1 FG moved to WC-2
RM position
生产看板取代成品零件 Production kanban to replace FG parts 使用WC-1的原料生产零件 RM for WC-1 used to produce
parts
from a batch of parts that will be delivered to the following process
2)
3)
将生产看板放在派工单上,作为工作中心进行生产的信号和计划
Production kanban is placed on dispatch post in order to signal and schedule production in the work center
1
至装配线 To Assembly
装配线将WC-2成品拉向装配线超市Assy pulls WC-2 FG to
Assy Supermarket
生产看板Production Kanban
取料看板Withdrawal Kanban
生产看板取代成品零件Production kanban to replace FG parts 使用WC-2的原料生产零件RM for WC-2 used to produce parts
取料看板 Withdrawal Kanban 流程间看板
Inter-Process Kanban:
发出从前面流程拿取零件的指令Delivers order for parts from a preceding process
规定定从工位A发到工位B之零件的数量和型号Specifies quantity and type of parts to
看板卡系统

当第一件工件使 用时, 用时,操作工把 看板卡拿出
Operator removes card when first part is used.
< > 主菜单 退出
取看板卡 Pickup Kanban Card
准时
Just in Time 物 料 拉 动 系 统 Kanban System Kanban System Material Pull System Material Pull System 系 统
物 料 拉 动 系 统 Kanban System Kanban System Material Pull System Material Pull System 系 统
制定标准化工作流程
Standardize Kanban process
使用临时看板卡
Temporary Kanban cards
改进包装箱结构以便于取卡
The line-side inventory depends on the quantity of Kanban linecards . Following is the main factor:
生产节拍 Actual Takt Time 使用量 Usage of per Job 标准包装数 Standard Package Quantity 运送周期 Delivery Cycle
无法适应生产批量发生变化
物 料 拉 动 系 统 Kanban System Kanban System Material Pull System Material Pull System 系 统
Batch processing adversely affects pull card loop size
定置管理、目视管理、看板管理
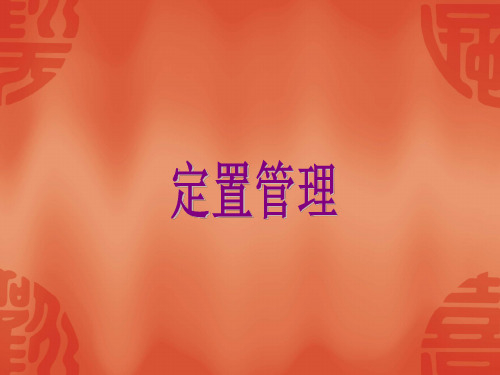
第五章 管理方法训练
目视管理的设备管理之要点: 要点1: 清楚明了地表示出应该进行维持保养的机能部位。 方 法: 颜色别加油标贴,管道、阀门的颜色别管理。 要点2: 能迅速发现发热异常。 方 法: 在马达、泵上使用温度感应标贴或温度感应油漆。 要点3: 是否正常供给、运转清楚明了。 方 法: 旁置玻璃管、小飘带、小风车。
一、目视管理的含义 目视管理是利用形象直观、色彩适宜的各种视觉感知信 息来组织现场生产活动,达到提高劳动生产率目的的一种 管理方式。它是以视觉信号为基本手段,以公开化为基本 原则,尽可能地将管理者的要求和意图让大家都看得见, 借以推动自主管理、自我控制。所以目视管理是一种以公 开化和视觉显示为特征的管理方式,也可称之为“看得见 的管理”。例如: 交通用的红绿灯,红灯停、绿灯行; 包装箱的箭头管理:有零件的箱表面箭头朝上(↑),无零 件的箱倒置箭头朝下(↓); 在排气扇上绑一根小红布条,看见布条飘起即可知到运行状 况等均为目视管理。
1.定置管理的含义 定置管理是我国工业企业20世纪80年代从日本学 习引进的一种先进管理方法。作为生产现场管理 的一个重要组成部分,定置管理的主要任务是研 究作为生产过程主要要素的人、物、场所三者的 相互关系。它通过运用调整生产现场的物品放置 位置,处理好人与物、人与场所、物与场所的关 系;通过整理,把与生产现场无关的物品消除掉; 通过整顿,把生产场所需要的物品放在规定的位 置。这种定置要科学、合理,实现生产现场的秩 序化、文明化。
(3)物与场所的关系 在生产活动中,人与物的结合状态,是 决定生产有效程度的因素。但人与物的结合都 是在一定场所进行的。因此,实现人与物的最 佳结合,必须首先处理好物与场所的关系,实 现物与场所的合理结合。研究物与场所的有效 结合,就是对生产现场、人、物进行作业分析 和动作研究,使对象物品按生产需要、工艺要 求科学地固定在某场所的特定位置上,达到物 与场所的有效结合,缩短人取物的时间,消除 人的重复动作,以促进人与物的最佳结合。
正确的流程方能产生正确结果

正确的流程方能产生正确结果正确的流程方能产生正确结果∙建立无间断的作业流程以使问题浮现∙使用「后拉式制度」以避免过度生产∙平准化:工作负荷平均(工作要像龟兔赛跑中的乌龟,而不是兔子那样)∙建立立即暂停以解决问题、一开始就重视品管的文化∙职务工作的标准化是持续改善与授权员工的基础∙使用视觉控管,使问题无从隐藏∙使用可靠的、已经经过充分测试的技术以支持人员及流程[编辑]发展员工与事业伙伴,以为组织创造价值∙栽培彻底了解并拥抱公司理念的员工成为领导者,并使他们能教导其他员工∙栽培与发展信奉公司理念的杰出人才与团队∙重视公司的事业伙伴与供货商网络,挑战它们,并帮助它们改善[编辑]持续解决根本问题是组织型学习的驱动力∙现地现物:亲临现场查看以彻底了解情况∙决策不急躁,要通过协商以共识为基础,彻底考虑所有可能选择,快速执行决策∙透过不断地省思与持续改善,以变成一个学习型组织[编辑]丰田式生产管理:不降低成本就无法提高利润成本中心型以计算或实际的成本为中心,加上预先设定好的利润而得出售价,其公式为:售价= 成本+利润在供应< 销量时,在垄断产品时可以如此定价售价中心型在供应>销量时,以售价为中心,当市场售价降低时利润随之减少,其公式为:利润= 售价-成本缺乏改善意识的企业属于此类型,市场好时有较高的利润,市场差时大幅度下降利润中心型在供应>销量时,以利润为中心,当市场售价降低时,成本也必须下降以获得的利润(目标利润) 不会减少,其公式为:成本= 售价-利润减少浪费--降低成本的主要手段什么是浪费?不增加价值的活动(如:生产过程改变零件尺寸、形状或功能,非价格) 是浪费;尽管是增加价值的活动,但所用资源超过了绝对最少的界限,也是浪费丰田式生产管理目的就是取消那些不增加产品价值的工作,即降低成本。
[编辑]丰田式生产管理哲理的理论框架丰田式生产管理哲理的理论框架包含“一个目标”、“两大支柱”和“一大基础”。
车间常用英语
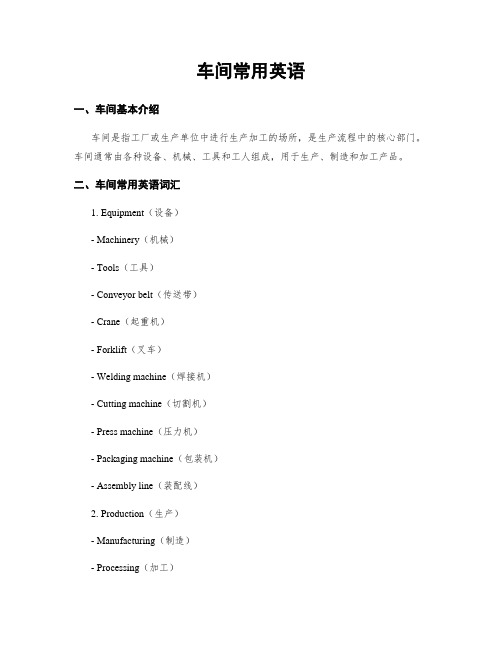
车间常用英语一、车间基本介绍车间是指工厂或生产单位中进行生产加工的场所,是生产流程中的核心部门。
车间通常由各种设备、机械、工具和工人组成,用于生产、制造和加工产品。
二、车间常用英语词汇1. Equipment(设备)- Machinery(机械)- Tools(工具)- Conveyor belt(传送带)- Crane(起重机)- Forklift(叉车)- Welding machine(焊接机)- Cutting machine(切割机)- Press machine(压力机)- Packaging machine(包装机)- Assembly line(装配线)2. Production(生产)- Manufacturing(制造)- Processing(加工)- Assembly(装配)- Inspection(检查)- Quality control(质量控制)- Efficiency(效率)- Productivity(生产率)- Output(产量)- Waste reduction(减少浪费)3. Safety(安全)- Protective equipment(防护设备)- Safety goggles(安全护目镜)- Safety helmet(安全头盔)- Safety gloves(安全手套)- Fire extinguisher(灭火器)- Emergency exit(紧急出口)- First aid kit(急救箱)- Safety training(安全培训)- Hazardous materials(危险物质)- Accident prevention(事故预防)4. Production Process(生产流程)- Raw materials(原材料)- Work in progress(生产中的产品)- Finished products(成品)- Assembly instructions(装配说明)- Production schedule(生产计划)- Quality inspection(质量检查)- Packaging and labeling(包装和标签)- Inventory management(库存管理)- Order fulfillment(订单执行)- Shipping and logistics(运输和物流)5. Job Positions(职位)- Supervisor(主管)- Operator(操作员)- Technician(技术员)- Engineer(工程师)- Quality inspector(质检员)- Maintenance staff(维修人员)- Production planner(生产计划员)- Warehouse manager(仓库经理)- Logistics coordinator(物流协调员)- Safety officer(安全员)6. Communication(沟通)- Instructions(指示)- Report(报告)- Meeting(会议)- Announcement(公告)- Memorandum(备忘录)- Email(电子邮件)- Conversation(对话)- Training session(培训会议)- Feedback(反馈)- Collaboration(合作)7. Quality(质量)- Defect(缺陷)- Non-conformance(不符合)- Standard(标准)- Specification(规格)- Quality control plan(质量控制计划)- Quality assurance(质量保证)- Continuous improvement(持续改进)- Root cause analysis(根本原因分析)- Corrective action(纠正措施)- Customer satisfaction(客户满意度)8. Maintenance(维护)- Preventive maintenance(预防性维护)- Breakdown(故障)- Repair(修理)- Lubrication(润滑)- Calibration(校准)- Replacement(更换)- Troubleshooting(故障排除)- Downtime(停机时间)- Spare parts(备件)- Equipment reliability(设备可靠性)9. Lean Manufacturing(精益生产)- Waste(浪费)- 5S methodology(5S方法论)- Value stream mapping(价值流图)- Kaizen(改善)- Just-in-time (JIT)(准时生产)- Kanban system(看板系统)- Poka-yoke(防错)- Standardized work(标准化工作)- Continuous flow(连续流)- Visual management(可视化管理)10. Performance Evaluation(绩效评估)- Key performance indicators (KPIs)(关键绩效指标)- Productivity rate(生产率)- Efficiency ratio(效率比率)- Defect rate(缺陷率)- Downtime percentage(停机时间百分比)- Cycle time(生产周期)- OEE (Overall Equipment Effectiveness)(设备综合效率)- Scrap rate(废品率)- Employee turnover rate(员工流动率)- Customer complaints(客户投诉)三、结语以上是车间常用英语的一些词汇和表达,通过学习这些常用术语,您可以更好地理解和参与车间的工作和沟通。
看板KANBAN-精益生产的高级工具

看板KANBAN-精益生产的高级工具看板KANBAN是精益工具里较为高端的一个工具,这里的看板不是指工作场地的显示和记录状况的白板,看板在这里是一种触发信号,而且尤其是指拉动方式里的触发信号。
较为复杂,却意义重大。
看板作为拉动的实施工具,作为准时生产JIT的实现方式,起的是个触发的作用。
两箱系统(two-binsystem)是很好的个入门方式。
典型应用于生产区域的小零件(比如螺丝螺帽等)的货架上,这样的小零件的缺货会影响生产区域的装配作业,而如何补货也是个棘手的问题。
两箱系统的做法是,将零件盒中间加一层隔板,前后各放一袋零件,拆前面的一袋开始用,在后面的一袋下方放一块红色的牌子,标有零件号,也就是看板。
当第一袋用完,从后面的第二袋到前方的时候,第二箱底部的红色看板即呈现,则手工将此红牌插在货架上。
因而便于补货人员在定期巡视时可以查看到什么料缺了而需要补货。
执行这个两箱系统的时候,需要对每个料号的零件的体积和最小起订量、以及单位生产使用量进行一定的计算和平衡,也对物料补给员的巡视时间进行相应的匹配(比如是每两小时巡视一次、还是每天一次)。
而这种实物看板也可以由电子看板来替代。
这种典型的看板的应用,是一种触发信号,对于在生产现场的最低库存和保证不断货的顺畅供应间的平衡下的一个补货的触发信号。
也有做法是把这样的小零件的现场货架外包给供应商,供应商每天有人来负责检查巡视缺货状况,并予以补充。
这种两箱系统的看板方法,促成了生产现场的小零件和使用方和补充方的良性互动,从而得以取得不断货和最低库存间的均衡。
对于工序间的WIP在制品、半成品、原材料的搬运中,看板也是有典型的运用。
为配合JIT的准时生产,只生产需要的量,当生产指令从生产线末端朝前方传递,同一条生产线上的内部看板为不增加额外的浪费而可以省略,因同一条生产线在拉动生产中趋向于单件流,所以每个工位只有一件WIP在制品,当完工的在制品被下一工序取走,即触发此工位的生产指令。
快速实现精益生产的九步法

快速实现精益生产的九步法,拿走不谢!
快速实现精益生产的九步法是一套经过实践验证的方案,能够帮助企业提高效率、降低成本、提升质量。
这些步骤不仅适用于制造业,也适用于其他行业。
通过实施这些步骤,企业可以发现并消除浪费,提高生产效率,提供更好的产品和服务。
具体步骤如深圳天行健精益生产咨询公司下文所述:
第一步:价值流图(Value Stream Mapping)
分析生产过程中的价值流
发现并消除浪费
第二步:单件流(Single Piece Flow)
通过减少存货和等待时间来提高效率
第三步:拉动式生产(Kanban System)
根据需求进行生产,避免过度生产第四步:持续改进(Kaizen)
不断寻找改进的机会
进行小规模的改变,持续优化
第五步:标准化(Standardization)
制定标准化的工作流程
提高效率并减少错误
第六步:5S管理
整理工作环境,使其更加清洁、有序提高工作效率和员工满意度
第七步:文化变革
培养精益生产的思维方式和价值观
全员参与,持续推动变革
第八步:员工培训和发展
提供培训机会,帮助员工掌握精益生产的知识和技能
激励员工参与改进和创新
第九步:质量管理
强调质量的重要性
实施质量管理措施,确保产品和服务的稳定性和一致性
总而言之,通过快速实现精益生产,企业可以实现持续改进和创新,提高竞争力,为客户提供更好的产品和服务。
无论企业规模大小,只要积极推动这些步骤,就能够在激烈的市场竞争中脱颖而出。
工厂中SMT制程段生产中常用英文

工厂中SMT制程段生产中常用英文In the manufacturing industry, Surface Mount Technology (SMT) is a popular method for electronic component assembly. It is widely used in factories around the world for its efficiency and accuracy. In this article, we will explore the commonly used English terms and phrases in SMT production.1. PCBA (Printed Circuit Board Assembly)PCBA refers to the process of assembling electronic components onto a printed circuit board (PCB). It includes soldering, solder paste printing, component placement, and reflow soldering.2. Solder Paste PrintingSolder paste is a mixture of solder alloy and flux. In the SMT process, solder paste is printed onto the PCB using a stencil. This is an important step to ensure proper alignment and solder joint quality.3. StencilA stencil is a metal or polymer sheet with openings that correspond to the positions of the components on the PCB. It is used to apply solder paste onto the board during the printing process.4. Pick and Place MachineA pick and place machine is used to place the electronic components onto the PCB accurately. It can handle different component sizes and shapes. This machine uses robotic arms and a vision system to ensure precise placement.5. Reflow SolderingReflow soldering is the process of melting the solder paste to create a permanent solder joint between the components and the PCB. The PCB with the components is passed through a furnace that heats it up to the soldering temperature.6. Soldering Temperature ProfileThe soldering temperature profile is a set of temperature values and durations that specify the heating and cooling process during reflow soldering. It ensures proper solder joint formation and prevents component and PCB thermal damage.7. SMD (Surface Mount Device)SMDs are electronic components that are designed to be mounted directly onto the surface of a PCB. They are small in size and have no lead wires. SMDs include resistors, capacitors, integrated circuits, and many other electronic devices.8. Moisture Sensitivity Level (MSL)MSL is a measure of how sensitive an SMD is to moisture absorption. Components with higher MSL ratings require special handling and storage conditions to avoid damage during soldering.9. InspectionInspection is an essential part of SMT production to ensure the quality of the assembly. It includes visual inspection for solder joint defects, automated optical inspection (AOI) to detect component placement errors, and X-ray inspection to check for hidden defects.10. Defect Detection and RepairIn SMT production, defects can occur during the printing, placement, or soldering processes. Defect detection systems are used to identify defective components or solder joints. Repairs are then made to correct the defects and ensure the functionality of the final product.11. ESD (Electrostatic Discharge) ProtectionESD is the sudden transfer of an electric charge between two objects. In the SMT production environment, ESD can damage sensitive electronic components. Therefore, proper ESD protection measures, such as the use of grounding straps and anti-static mats, are essential.12. Test and MeasurementAfter the PCBA is completed, it undergoes testing to ensure that it meets the required specifications. Testing may include functional testing, in-circuit testing (ICT), and boundary scan testing. Measurements are taken to verify the electrical characteristics and performance of the assembled board.In conclusion, SMT production in a factory involves various processes and techniques. This article has covered the commonly used English terms and phrases in SMT production, providing a basic understanding of the key stages and concepts. Having a good grasp of these terms will help both workers and managers communicate effectively and efficiently in an SMT production environment.SMT生产是电子制造业中常用的组装技术之一。
Withdraw Kanban Introduction领取看板卡介绍
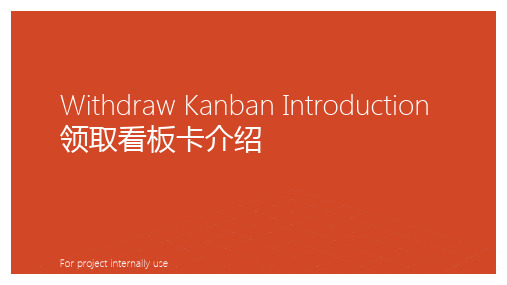
Upstream process
Source Dept. Molding Machine #: IM-P9Q2
Location:
R1K09B
Part #:
M-8532
Part description: Lower basin
Quantityery location: Sub assembly cell #2
Kanban is the acknowledgement of the failure to implement one piece flow 看板是对实现一个 流程失败的承认
看板卡的分类
临时生产/领取看板
Inter-process withdrawal Kanban制程间(领取)看板
Product information
Withdraw Kanban Introduction 领取看板卡介绍
For project internally use
目录 content
1. 看板的简介以及分类 2. 领取看板介绍 3. 领取看板运行前提 4. 领取看板运转流程 5. 领取看板运转过程 6. 领取看板运行规则及异常 7. 领取看板模拟游戏
超市/FIFO
水蜘蛛
生产线
流程/Process
领取看板流程
“See”
“board”
What is Kanban/Kanban system/ 什么是看板/看板系统
A tool of the pull system 是拉动系统的一个工具:
The actual card, container or physical signal itself 实际的卡片、容器或物理信号本身 A visual method of controlling workflow, invented in the days before IT一种控制工作流的可视 化方法,发明于IT时代之前 A signal that authorizes production or movement (withdrawal) of items是授权生产或者领取物 品的信号
公司内部英语常用缩写词汇1

➢单件工时--takt time ➢实际单件工时--actual takt time ➢周期时间—cycle time ➢瓶颈工艺--bottleneck process ➢先进先出--First In First Out ➢看板系统--KANBAN system ➢物料拉动系统--material pull System ➢缓冲区—Buffers ➢平面布置—Layout ➢暗灯--Andon
不断改进
Five Principles 五项原则
人员参与
标准化
•缩短制造周期
造入质量
➢GM-GMS通用全球制造系统 General Motors Global Manufacturing System
➢五个目标-Five Goals ➢安全—Safety ➢质量—Quality ➢响应—Response ➢成本—Cost ➢组织发展--Organization
➢开拓者--Blazer ➢S10皮卡--S10 pickup ➢内饰线--Trim line ➢底盘线--Chassis line ➢合装线--Final line ➢发动机线--engine ➢快速轨--fast track
➢TPM(全员生产性维修) TPM (Total Productive Maintenance) PM(预防性维修)--Preventive Maintenance
CKD completely knocked down SKD semi knocked down ECN engineering change notice EWO engineering work order PRR problem reslution report PAA production action authrization SSF start of systme fill PAD product assembly document UPC unit part classfication FNA functional name address KPC key product character ECO economy API annual physical inventory PPAP production part approval procedure PTR production trail run ETR engineering trail run SOP start of production OTS off tooling sample
物流Kanban System 看板系统 精益物流看板

Topics主题Section1:What is Kanban?什么是看板?Section2:Two-card Kanban Systems2张看板卡系统Section3:Kanban Calculation看板的计算Section4:Managing the Kanban System管理看板系统Section5:Kanban System Implementation看板系统的实施Jargon Buster专业术语Kanban看板Supermarket超市Production Instruction Kanban生产指示看板Withdrawal Kanban取料看板Supplier供应商Signal Kanban信号看板Safety stock安全库存Buffer stock缓冲库存Section1Topics第1章主题What is Kanban?什么是看板?A tool of the pull system拉动系统的工具A signal that authorizes production or movement(withdrawal)of items授权生产或移动物料的信号The actual card,container or physical signal itself实物卡,周转箱或者实际的信号A visual method of controlling workflow,invented in the days before IT一个目视化的控制生产流的方法,在IT之前发明The system that uses kanban这个系统使用看板Kanban is a simple and effective method for visually controlling material flow看板是一个针对目视化管理物料流的简单高效的方法The kanban system itself is full of waste such as handling,inventory and processing看板体系本身也是充满了浪费,例如物料搬运,库存及操作Kanban is the acknowledgement of the failure to implement one piece flow看板承认不能实现单件流的表现Definitions is kanban看板的定义Functions of kanban看板的功能Sets limits设定限制Kanban is like currency–you cannot buy parts without paying for them!看板就像货币—你不能在没有付钱的情况下买东西Nothing is made or moved without a kanban在没有看板的情况不生产或者移动物料Makes problems visible让问题可视化Kanban=inventory=waste看板=库存=浪费Instruct processes to produce指示工序进行生产Limits overproduction限制过量生产Instruct material handlers to move product指示物料员运送产品Withdrawal from upstream by downstream process下工序从上工序取料Forms of kanban看板的形式Classic“two card”system(uses production and withdrawal cards)经典的“2种卡”系统(使用生产及取料看板)“One card”system uses one of the following“看板”系统使用以下的方式Card卡片Triangular plates三角板Containers周转箱Carts推车Colored balls不用颜色的球Electronic signal电子信号Or anything that conveys only the necessary information.或者其他人能能够转换必要信息的工具Forms of Kanban看板的形式Forms of Kanban看板的形式Section2:Two-card Kanban Systems2张看板卡系统Types of kanban看板的类型Production instruction kanban生产指示看板Signal kanban信号看板Lot making board批量生产板Withdrawal kanban取料看板Supplier kanban供应商看板Kanban cycles看板循环Types of Kanban看板的类型Section2:Two-card Kanban Systems2张看板卡系统Types of kanban看板的类型Basic Card Design基本的卡片设计Information on a Kanban Card看板卡上的信息The action(make,move,etc.)行动(制造,移动)Part number物料名称Part description物料描述The supplier(or process)name供应商(工序)名称Quantity数量Container quantity周转箱数量The source location物料存储的地址The delivery location物料运送地址The timing of the action(kanban cycle)行动的时间(看板循环时间)Etc.等等。
KANBAN-SYSTEM-看板系统
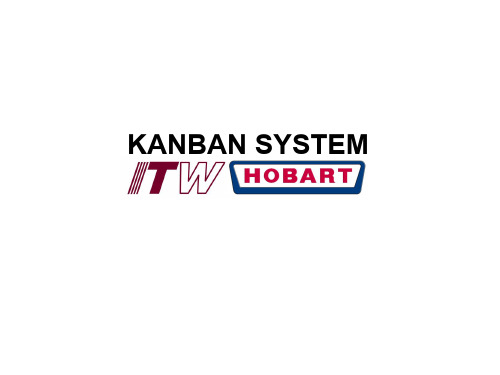
Kanban Card
物料号码: 742301 物料描述: C44B 水箱
KB方式 本卡数量
C KB 1
1
8 10
前序加工
区号: 010 工位: W
后序加工
区号: 030 工位: C2
3/10
Hobart Food Equipment Co.,Ltd
Kanban Card
物料号码: 742312
物料描述: C44B门钩焊件
F KB 1
1
2
3
供应商:
SEW T ianjin FAX:
物料送达
区号: 090 工位: WH
2/3
Hobart Food Equipment Co.,Ltd
Kanban Card
物料号码: 274232-C
物料描述: C44B穿线管
KB方式 本卡数量
C TB 30
供应商:
廊坊裕隆 FAX:
物料送达
两箱定配制:适用于低值物料。以一个 KanBan显示该物料的存储和再订购信息, 第二箱数量为固定数量。
KanBan的形式说明
以卡代料形式,适用于各种形 式的物料
以独特运载车,托盘形式,多 适用于内部加工物料。
以特殊的包装形式,多适用于 外购物料的运输。
供应商物料存储形式,多适用 于80供应商。
KB方式 本卡数量
C TB 50
前序加工
区号: 010 工位: W
后序加工
区号: 030 工位: C2
1/1
Hobart Food Equipment Co.,Ltd
Kanban Card
物料号码: 742321 物料描述: C44B门焊件
(丰田管理)丰田式管理
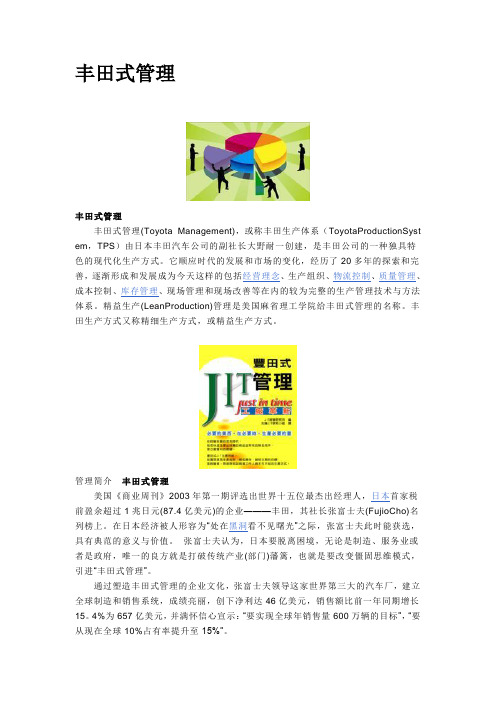
丰田式管理丰田式管理丰田式管理(Toyota Management),或称丰田生产体系(ToyotaProductionSyst em,TPS)由日本丰田汽车公司的副社长大野耐一创建,是丰田公司的一种独具特色的现代化生产方式。
它顺应时代的发展和市场的变化,经历了20多年的探索和完善,逐渐形成和发展成为今天这样的包括经营理念、生产组织、物流控制、质量管理、成本控制、库存管理、现场管理和现场改善等在内的较为完整的生产管理技术与方法体系。
精益生产(LeanProduction)管理是美国麻省理工学院给丰田式管理的名称。
丰田生产方式又称精细生产方式,或精益生产方式。
管理简介丰田式管理美国《商业周刊》2003年第一期评选出世界十五位最杰出经理人,日本首家税前盈余超过1兆日元(87.4亿美元)的企业———丰田,其社长张富士夫(FujioCho)名列榜上。
在日本经济被人形容为“处在黑洞看不见曙光”之际,张富士夫此时能获选,具有典范的意义与价值。
张富士夫认为,日本要脱离困境,无论是制造、服务业或者是政府,唯一的良方就是打破传统产业(部门)藩篱,也就是要改变僵固思维模式,引进“丰田式管理”。
通过塑造丰田式管理的企业文化,张富士夫领导这家世界第三大的汽车厂,建立全球制造和销售系统,成绩亮丽,创下净利达46亿美元,销售额比前一年同期增长15。
4%为657亿美元,并满怀信心宣示:“要实现全球年销售量600万辆的目标”,“要从现在全球10%占有率提升至15%”。
TPS的由来20世纪后半期,世界汽车工业进一个市场需求多样化的新阶段,而对质量的要求也越来越高,这就给制造业提出了这样一个新课题:只有有效地组织多品种、小批量生产,避免生产过剩所引起的设备、人员、库存、资金等一系列资源浪费,以保持企业竞争能力。
在这种历史背景下,从丰田相佐诘开始,经丰田喜一郎及大野耐一等人的共同努力,综合了单件生产和批量生产的特点和优点,创造了一种多品种、小批量混合生产条件下高质量、低消耗的生产方式。
看板系统内训大纲.pptx

•精益制造回顾 •看板定义 •何时采用看板 •看板 – 六大先决条件 •看板循环 •在价值流内确定缓冲库存的大小和区域 •物流路线和频度 •平滑工作量 •批量尺寸, 快速换产 & 看板 理解看板的四大功能 •自治神经系统 •工厂控制: 限制过量生产 •目视管理 •持续改善
ROCKET★UP
E-mail: susan@
© Copyright Rocket Corporation 2007
ROCKET★UP
罗科特企业管理咨询(深圳)有限公司
© Copyright Rocket Corporation 2007
• 1、Genius only means hard-working all one's life. (Mendeleyer, Russian Chemist) 天才只意味着终身不懈的努力。20.8.58.5.202011:0311:03:10Aug-2011:03
参加对象:
该课程设计为提供实践的精益知识和工具改进工厂运营,同时帮助你在组 织中启动精益变革。目标学员包括:
•经理,工程师,主管,变革代理人,现场作业及设备相关人员 离散型生产企业,物流中心,建筑,服务,或多重流程工业
© Copyright Rocket Corporation 2007
客户分布
电子电器
• 3、Patience is bitter, but its fruit is sweet. (Jean Jacques Rousseau , French thinker)忍耐是痛苦的,但它的果实是甜蜜的。11:038.5.202011:038.5.202011:0311:03:108.5.202011:038.5.2020
学习目标:
生产看板名词解释

生产看板名词解释生产看板是一种用于管理生产流程的工具,它提供了实时的生产信息,帮助团队成员了解工作情况、发现问题和制定决策。
以下是一些与生产看板相关的重要名词的解释:1. 生产看板(Kanban):生产看板是一个物理或电子设备,用于展示生产任务、工作进度和合作需求等信息。
它通常包括任务卡片、状态指示和问题标记等元素,以便团队成员进行可视化管理。
2. 看板系统(Kanban System):看板系统是一种基于看板原则的生产管理方法。
它通过限制在制品的数量来调控工作流程,确保团队按需求进行工作,避免过度投入资源和产生浪费。
3. 看板列(Kanban Column):看板列是指生产看板上的水平线,用于划分工作流程的不同阶段。
每个列代表一个任务状态,例如待办、进行中和已完成等。
团队成员通过将任务卡片从一列移动到另一列来表示工作的进展。
4. 任务卡片(Task Card):任务卡片是生产看板上的小卡片,用于代表一个具体的任务或工作项。
卡片上通常包括任务名称、描述、负责人和截止日期等信息。
团队成员可以通过移动和更新卡片来管理任务进程。
5. WIP限制(Work-in-Progress Limit):WIP限制是指在看板系统中设定的在制品数量上限。
通过限制工作流程中的正在进行的任务数量,团队可以降低任务堆积和任务完成时间,避免资源过度投入和工作效率下降。
6. 周期时间(Cycle Time):周期时间是指完成一个任务所需要的时间,从任务开始到任务结束的过程。
周期时间是评估工作效率和生产周期的重要指标,通过分析和改进周期时间可以提高生产效率和响应能力。
7. 拉动生产(Pull Production):拉动生产是一种生产方式,根据客户需求主动拉动生产任务,以满足需求。
在看板系统中,任务卡片的移动是由下游成员需求触发的,而不是事先推送任务。
8. 看板信号(Kanban Signal):看板信号是用于触发任务开始或移动的信号。
- 1、下载文档前请自行甄别文档内容的完整性,平台不提供额外的编辑、内容补充、找答案等附加服务。
- 2、"仅部分预览"的文档,不可在线预览部分如存在完整性等问题,可反馈申请退款(可完整预览的文档不适用该条件!)。
- 3、如文档侵犯您的权益,请联系客服反馈,我们会尽快为您处理(人工客服工作时间:9:00-18:30)。
7 wastes
No. Type of Waste Description 1. Waste of Over Production: Producing over customer requirements, producing unnecessary materials / products, or producing to soon. 2. Waste in Waiting (Time): 3. Waste in Transportation: Time delays, idle time (non value added time) Multiple handling, delay in material handling, unnecessary handling or transportation (non value added conveyance) Unnecessary processing, steps or work elements/ procedures (non value added work). Producing unnecessary inventory, holding or purchasing unnecessary inventory, RS, WIP, FG. Waste of motions, excessive handling, unnecessary steps of motion (non value added motions). Correction of errors or rework, scrap (quality problems)
A
A
X
Rack 2
A
A
The material handler comes on frequent schedules and pick up empty boxes and Delivers full boxes Empty Containers
Rack 1
Rack 3
12 1 2 3
Standardized routes delivering small containers on a frequent schedule (once per hour or less). More frequent deliveries lower material inventory at operations.
Full Full Full
Different signal can be used : -Empty box - red space on the floor
Full
Empty dolly signals replenishment.
A-108
Empty Full Empty
Operator pushes out empty dolly & container then pulls next dolly into position.
Part: Side Shield Part No: 9873214 Std. Pack: 60 Min. 2 Max. 5 • Labels affixed to rack using Velcro backed clear plastic pockets. • Labels located directly below containers on the front & back of rack. • Label content includes: Part name, Part number, Standard pack size, Minimum and Maximum Quantity. • Labels are 5 ½ x 3 ½ inches for standard flow racks and 3 x 2 inches for pipe style flow racks. • Racks identified by section and shelf levels.
inventory of each part at its point of use. • The minimum/maximum inventory level is necessary to prevent: 1) running out of parts 2) having more parts than required at the point of use. • This min/max level is set by calculating the: - Kanban loop cycle - Point of use quantity requirements (i.e. Min. 2 hours)
2 3 4 5
Parts Picking
Receiving Staging Area
Receiving Docks Receiving Docks
Blue Dolly Conveyance Route
Orange Dolly Conveyance Route
Next Delivery Cycle Staging
Empty packaging return on roller
Empty packaging
Picking area for the train Roller
Example : Courbouton
Some pictures
Empty containers Kanban
Definition : Kanban system in which a visual signal triggers part replenishment on line.
Visual signal can be : • an empty box • an empty dolly • an empty rack • an empty floor space • a collapsed box • a red mark on racks
So…what’s different?
• replenishment on demand vs. scheduled push • Every product has a specific number of designated racks. • Lot sizes are smaller – more frequent Changeovers required. • Less inventory on the line • FIFO (First-In-First Out) versus FISH (First-In-Still-Here) or FINCO ( First-In-Never-Come-Out )
Learn
See
Empty box Exchange
An empty box is a signal to the material handler for replenishment
Line Side Storage Small Lot Delivery
EMPTY RACK
EMPTY BOX
Empty Dolly Exchange
Learn See
4. Waste in Processing:
5. Waste of Inventory:
6. Waste of Motion:
7. Waste of Producing Failures:
Kanban Requirements
• Establish and maintain a minimum and maximum
3
Train station: loading Train station: unloading
4
5
Tour
Example : Courbouton
Small parts storage (new layout)
Big parts storage (new layout)
Example : Courbouton
Empty Dollies Parts Picking
CHI DET NY BOS PHI MIN
Returnable Container Sorting Area
Small Container Conveyance & Central Material Storage
Central Material Storage
Part: Adjuster Part No: 9981427 Std. Pack: 90 Min: 1 Max: 3 Stack: 3 High Part: Pan Part No: 4563273 Std. Pack: 75 Min: 1 Max: 3 Stack: 3 High
Full Route driver delivers dolly & full container based on signal. Full Full
Empty containers Kanban
Kanban with empty containers
Empty containers Kanban
Kanban takes different forms: • Cards • Empty Containers • Empty Dollies • Electronic Signals • Electronic Kanban • Production Pull (Bill Of Material) • Timed Deliveries
There must be a plan for every part!
Kanban CardDelivery Route
Central Material Storage