AX分解炉构造介绍
分解炉
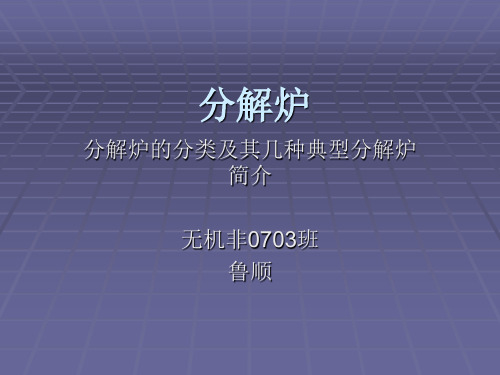
日本神户制钢与日本太平洋水泥株式会社的 DD分解炉及其三种改进型
N-MFC分解炉 N-MFC分解炉全称是:New Mitsubishi Fluidized Calciner。它由日本三菱水泥矿业 株式会社(Mitsubishi Cement Mine Inc.) 和三菱重工(MHI)联合研制开发,其窑系 统属于“流化+悬浮”。
Prepol系列分解炉与Pyroclon系列分解炉
Prepol(普列波尔)预分解窑与 Pyroclon(派洛克朗)预分解窑分别由德国 伯力休斯公司(Polysius AG)与德国洪堡 公司(KHZ)研制开发。 (1) Prepol预分解窑 Prepol预分解窑最早是德国伯力 休斯公司与德国罗尔巴赫(Rohrbach)公 司合作在多波尔(Dopol)型悬浮预热器窑 基础上,增设预分解装置而成。其全称是: Precalcining-Polysius。早期的Prepol分 解炉只有Prepol-AS(Air Separate,有单独 的三次风管)及Prepol-AT(Air Through,三 次风从窑内通过)这两种基本炉型。
下裂解、燃烧,生成H2、CO和CmHn等还 原性气体。然后在生料中的Al2O3及Fe2O3 作催化下,将空气中NOx还原为N2,使预 热器排出废气中NOx含量降低到100~ 150ppm。还原烧嘴燃烧约15%炉用燃料; 第四,三次风从Ⅱ区圆筒二侧径向入炉, 其后直接导入上喷的窑气中,所以炉内无 水平旋流,故其压损较小;第五,两个主 燃烧器在Ⅱ区的三次风管入口上部,燃料 喷入时形成涡流,这样便迅速受热着火且 在富氧条件下立即燃烧;第六,预热生料 通过Ⅲ区下部的下料管入炉,下料处有可 调式撒料箱;第七,在炉内缩口
FLS系列分解炉的三代“喷腾”型炉体结构
无极非热工设备 2.3 分解炉
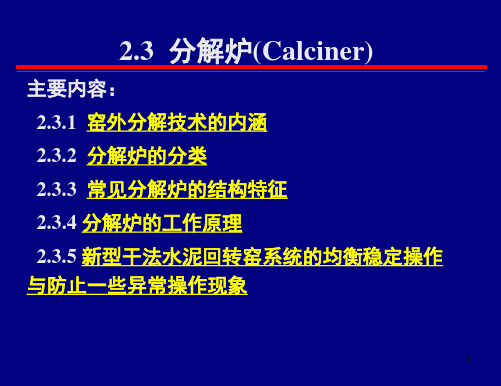
5、管道型分解炉
(1)管道式分解炉
指将窑尾与最下一级旋风 筒之间的上升烟道延长来作 为分解炉 特点:结构简单,阻力小
16
(2)洪堡公司的 Pyroclon炉型
无三次风管, 适合2500以 下、旧窑改造 窑尾气流速度
为12m/s
有三次风管, 适合带篦冷 机的SP旧窑 改造,最基 本的炉型
有三次风管, 适合旧窑改造 可以烧粗粒和 不易燃烧的燃
• 半离线式分解炉:出分解炉烟 气与窑气混合一起进入预热器
旁路防风
国外典型的分解炉结构见表2.9
国内典型的分解炉结构见表2.12
返8 回
2.3.3 常见分解炉的结构及特征简介
主要内容 1、N-SF系列分解炉 2、RSP分解炉 3、DD分解炉 4、SLC分解炉 5、管道式分解炉 6、我国自主研发的分解炉
9
1. N-SF、CSF型分解炉
(1)NSF型炉-日本石川岛公司—播磨株式会社(冀东) 结构:上部:圆柱+圆锥体—反应室
下部:旋转涡壳——涡旋室 优点:气固之间的混合得到了改善,燃料
燃烧完全,热耗低。 缺点:炉内气流容易产生偏流、短路和物
料特稀浓度区。 (2)CSF炉
10
(2) CSF炉(日本秩夫水泥厂)主要改进
② 分解炉的基本功能是什么? 在炉内进行燃料燃烧 生料分解 气流与生料间的传热
返回
4
2.3.2 分解炉的分类(表2.9)
1、按制造厂商分类 SF型(其改进型有N-SF型、C-SF型),日本石川岛公司 与秩父水泥公司研制; MFC型(改进型有N—MFC型),日本三菱公司研制 RSP型,日本小野田公司研制; KSV型(改进型有N—KSV型),日本川琦公司研制 FLS型,丹麦史密斯公司研制; DD型,日本神户制铁公司研制; 普列波尔型,德国伯力休斯公司研制; 派洛克朗型,德国洪堡—维达格公司研制; SCS型,日本住友公司研制等。
水泥工艺中分解炉的结构及原理简介

(二)、分解炉的工作原理与结构概述分解炉是把生料粉分散悬浮在气流中,使燃料燃烧和碳酸钙分解过程在很短时间(一般1.5~3秒)内发生的装置,是一种高效率的直接燃烧式固相一气相热交换装置。
在分解炉内,由于燃料的燃烧是在激烈的紊流状态下与物料的吸热反应同时进行,燃料的细小颗粒呈一面浮游,一面燃烧,使整个炉内几乎都变成了燃烧区。
所以不能形成可见辉焰,而是处于820~900℃低温无焰燃烧的状态。
水泥烧成过程大致可分为两个阶段:石灰质原料约在900℃时进行分解反应(吸热);在1200~1450℃时进行水泥化合物生成反应(放热、部分熔融)。
根据理论计算,当物料由750℃升高到850℃,分解率由原来的25%提高到85~90%时。
每千克熟料尚须1670千焦的热量。
因此,全燃料的60%左右用于分解炉的燃烧,40%用在窑内燃烧。
近几年来窑外分解技术发展很快,虽然分解炉的结构型式和工作原理不尽相同,它们各有自己的特点,但是从入窑碳酸钙分解率来看,都不相上下,一般都达到85%以上。
由此看来,分解炉的结构型式对于入窑生料碳酸钙分解率的影响是不太大的。
关键在于燃料在生料浓度很高的分解炉内能稳定、完全燃烧,炉内温度分布均匀,并使碳酸钙分解在很短时间内完成。
我国某厂烧煤分解炉的结构示意图3—18。
分解炉由预燃室和炉体两部分组成,预燃室主要起预燃和散料作用,炉体主要起燃料燃烧和碳酸钙分解作用。
在钢板壳体内壁镶砌耐火砖。
由冷却机来的二次空气分成两路进入预燃室。
三级旋风筒下来的预热料,由二次空气从预燃室柱体的中上部带入预燃室。
约四分之一的分解炉用煤粉,从预燃室顶部由少量二次空气带入并着火燃烧,约四分之三左右的煤粉在分解炉锥体的上部位置喂入,以此来提高和调整分解炉的温度,使整个炉内温度分布趋于均匀,担任分解碳酸钙的主力作用。
炉体内的煤粉颗粒,虽被大量的惰性气体CO2和N2所包围,减少了与O2接触的机会,煤粉的燃烧速度就会减慢。
但由于进入预燃室的煤粉不受生料粉的影响,而且在纯空气中燃烧,形成引燃火焰,起到火种的作用,使预燃室出口处有明火存在,对煤粉起着强制着火作用。
分解炉

早期开发的分解炉,大多主要依靠 上述“四种效应”中的一种。后来,各 种类型的分解炉在技术上相互渗透,所 以目前的分解炉大都趋向于采用以上各 种效应的“综合效应”,以力求优化分 解炉内的热量传递、质量传递、动量传 递和化学反应过程(简称“三传一反” 过程)。即遵循“以物料的高度分散为 前提,以燃料的高效与完全燃烧为关键, 以生料的有效分解为目的,以环境保护 与社会责任为己任!”的原则来改进与 完善分解炉。
DD分解炉及其窑系统的主要特点为: DD分解炉及其窑系统的主要特点为: 第一,其内分为四个区段:Ⅰ 第一,其内分为四个区段:Ⅰ区为脱氮还 原区,Ⅱ区为生料分解及燃料燃烧区,Ⅲ 原区,Ⅱ区为生料分解及燃料燃烧区,Ⅲ 区为主燃烧区,Ⅳ 区为主燃烧区,Ⅳ区为完全燃烧区;第二, 上升烟道有缩口让窑气喷入炉内,缩口喷 速为30~40m/s,以获得窑气量与三次风量 速为30~40m/s,以获得窑气量与三次风量 之间的平衡,也能阻止生料直接落入窑中, 还可加速化学反应。其简单的结构与工艺 布置有利于减少漏风和减轻炉内结皮以及 排除其他障碍物;第三, Ⅰ区侧壁装设的 数个还原烧嘴,使燃料在缺氧的情况
日本神户制钢与日本太平洋水泥株式会社的 DD分解炉及其三种改进型
N-MFC分解炉 MFC分解炉 N-MFC分解炉全称是:New Mitsubishi MFC分解炉全称是:New Fluidized Calciner。它由日本三菱水泥矿业 Calciner。它由日本三菱水泥矿业 株式会社(Mitsubishi 株式会社(Mitsubishi Cement Mine Inc.) Inc.) 和三菱重工(MHI)联合研制开发,其窑系 和三菱重工(MHI)联合研制开发,其窑系 统属于“流化+ 统属于“流化+悬浮”。 社 日 本 三 菱 分 株 解 式 炉 会 N-MFC
AX分解炉构造介绍
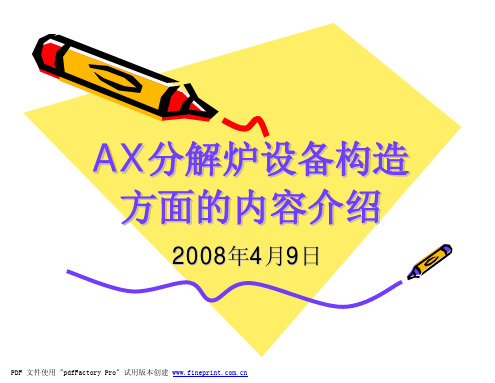
AX分解炉(氨分解装置)发生原理
工作原理:
• AX分解炉是液氨经气化后,在催化剂作用下 加热分解制得N2+H2的发生装置。其化学反 应如下: 2NH3 3H2+N2 –22千卡 它的最大特点是,不含CO和CO2,不可能有渗 碳倾向;当气氛的露点较低时,具有强还原性. 因而对含Zn、Cr等合金材料的光亮保护加 热,特别适宜。粉末冶金烧结,纯铁粉,高铬 钢、不锈钢烧结常采用氨分解气,因为煤气转 化气含有CO、H2O和CO2等成分,这些成分 能使钢中的铬氧化或碳化 。
AX分解炉的操作与维护
(1)熟悉设备原理、构造,检查气、电、水各系统是否畅通,有 无跑漏现象。并接通电源、水源。 (2)触媒(还原)活化。分解炉内装的触媒,因设备停放期间总 有水分、氧气等进入炉内,致使触媒活性下降,因此在初次开车时 需要进行触媒的活化。首先,接通电源使设备升温至350℃、,然 后打开放空阀,通入N2置换炉内空气,置换OK后,关闭N2;并 立即打开氨阀通氨气;这时,分解氨混合气阀关闭,气体不能通过 净化系统,直接放空;然后 350~500、500~650 ℃,650~800 ℃ 分段保温,进行活化,活化时间与设备的放置时间有关,待到由分解 炉出口出来得气体氨含量小于0.1%(如无化学分析设备也可以用 鼻子嗅来判断,如果嗅到得刺激性味道不大时,即可认为氨含量小 于0.1%),这时活化就可以停止。也可以从火焰得颜色判断,火 焰从黄色变成深橘红色,说明活化正常。活化初期和中期会产生大 量得水分,需要从底部排除,直至放不出水时,说明还原充分,气 体已可以使用。然后打开混合气阀,关闭放空阀,设备就可以正常 使用了。
PDF 文件使用 "pdfFactory Pro" 试用版本创建
下周学习讨论主题
第四章 窑外分解炉
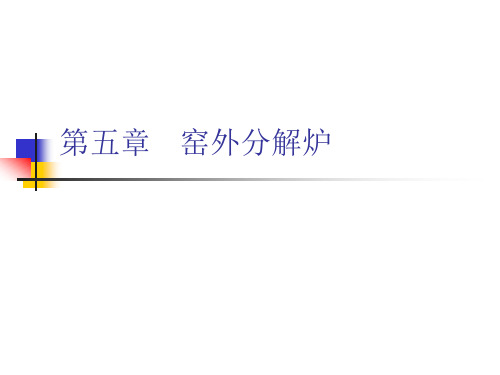
3、RSP分解炉
是日本小野田水泥公司与川畸重工业公司共同 研制 结构:由涡旋燃烧室SB、涡旋分解室SC和混合 室MC三部分组成,窑尾烟室与混合室MC之间 设有缩口以平衡窑之间的压力。 工作原理:SB室燃烧器点火,旋涡分解室是主 燃烧区和主分解室,混合室尚未分解的生料和 未燃烧完全和燃料继续完成。
天 津 院 分 解 炉
TDF
成 都 院 型 分 解 炉
CDC
6、NC分解炉系列
NC分解炉是南京水泥设计研制的分为NST-1同线 式和NST-S半离线式。 (1)、NST-1同线式,安装于窑尾烟室之上,为 涡旋、喷腾迭加式炉型;其特色是;一扩在了炉 容,并在炉出口至最下级旋风筒之间增设了“鹅 颈管道”,进一步增大了炉区空间。二是三次风 切线入炉后与窑尾高温气流混合,由于温度高, 煤、料入口装设合理,即使低挥发分煤粉入炉后 亦可迅速起火燃烧。同时在单位产10m3/(t· h) 的巨大炉容内,完全可保证煤粉的完全燃烧。
三、影响旋风、喷腾效应的因素 1、气体流动的速度 2、炉筒的直径 3、料粉质量 4、气体温度及料粉浓度
四、各种分解炉的特点
1、SF分解炉 SF分解炉是由日本石川公司开发世界上第一台分解炉。 上部是圆柱体、下部是锥形,三次风从最下部切向吹 入,同窑尾排出烟气混合,以旋流方式进入炉内,3个 喷油嘴和C3旋风筒卸出的生料喂料设在分解炉的顶部; 由于燃料燃烧时间太短,而移到下锥体部,而增加了 燃烧时间。 (1)、N-SF分解炉:喷嘴移至旋流室,下料点一部分移 至下锥体,一部分移至上升烟道内、取消烟道缩口。 (2)、C-SF分解炉:顶部改为涡室出口,在涡室下设缩 口,增加联接管道,增加生料的停留时间。
第二节,分解炉中的各种效应
氨分解炉胆设备工艺原理

氨分解炉胆设备工艺原理简介氨分解炉胆设备是一种通过氨气的分解来产生氢气的反应器。
氨气在高温下分解成氢气和氮气,反应的化学方程式为:2NH3 → 3H2 + N2利用这一反应可以产生大量的氢气,该过程广泛应用于电力、化工、能源等领域。
下面将介绍氨分解炉胆设备的工艺原理。
工艺原理氨分解炉胆设备主要由氨气供应系统、加热系统、反应器系统、冷却系统、氢气收集系统等组成。
其中反应器系统是实现反应过程的关键部位,其结构一般由炉胆、反应器内壳及隔板组成。
反应器结构炉胆炉胆是氨分解炉反应器系统内的主要部分,其结构设计主要考虑炉胆对氨分解反应的影响。
炉胆一般由炉胆壳体、炉胆盖、产氢口、储氢室、排放口等组成。
炉胆壳体一般采用钢板或合金钢管制成,壳体厚度一般在20mm以上,以满足炉胆的承压要求。
炉胆盖则通常采用活动式或半球型结构,以便于检修设备。
产氢口是连接氢气收集系统和炉胆的通道,其位置一般与炉胆盖相对应。
储氢室是用来暂存产生的氢气的,防止氢气过量溢出。
排放口则用来排放产生的副产品氮气和残余气体。
反应器内壳反应器内壳一般采用不锈钢材质制成,其目的是防止氨气对炉胆进行腐蚀,同时也可以提高反应的效率。
内壳外表面会铺设一层加热管,用来对反应器进行加热。
隔板隔板是反应器内壳的支撑部分,其间隔距离、数量和大小会影响反应器内气体的流场,进而影响反应炉的反应效率,因此选择适宜的隔板结构是重要的。
反应过程反应过程一般分为加热、分解两个阶段。
加热阶段在加热阶段,会在炉胆下方通入氨气,然后通过外部加热管对反应器进行加热,达到所需的反应温度,一般为800℃到1200℃之间。
分解阶段在达到反应温度后,氨气开始分解,产生氢气和氮气。
产生的氢气会从产氢口进入氢气收集系统中,而氮气和一部分残余气体则会从排放口排出。
结论氨分解炉胆设备利用氨气的分解产生大量的氢气,是一种重要的氢气生产方式。
通过适当的反应器结构设计和控制反应过程,可以获得更高的反应效率和产氢量。
分解炉的工作原理与结构
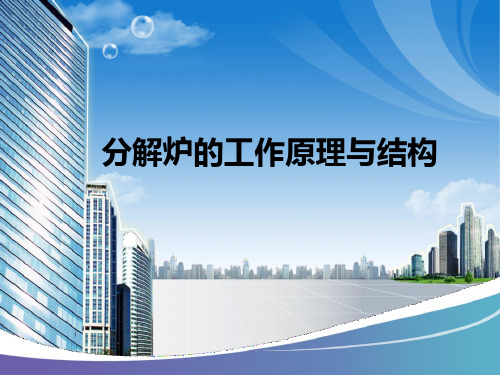
2.4带预燃室的分解炉 带预燃室的分解炉
• 为了使分解炉燃烧更加稳定,有的分解炉带有预燃室 。RSP型分解炉就是其中的一种。这种分解炉的构造较 为复杂,它是由分解炉(简称S炉)和混合室所组成。
S炉由上部旋风预热室(简称SB炉)和下 分解室(SC炉)组成,SB炉非常小。主 要是给SC炉起点火作用,并能保证SC 炉进行稳定的燃烧。SC炉是RSP型分 解炉的重要组成部分。S炉的燃料用量 为燃料总消耗量的55~60%,其中少 量燃料在SB炉内燃烧,大部分在SC炉 内燃烧,燃烧用的空气是从冷却机抽 来的700℃左右的热空气,从SC炉两 侧以切线方向送入炉内,另有一部分 空气进入SB炉中。 从第三级旋风筒来的预热生料,喂 入SC炉中,被热气流吹散,使生料呈 涡流运动,并进行分解,生料随气流 沿输送管往下运动进入混合室与出窑 废气混合并流向第四级旋风筒。 由S炉出口处的生料分解率约达40 %,在混合室遇到1000~1050℃的出 窑废气,将热量传给生料,从而进一 步提高了生料碳酸钙的分解率,入窑 生料分解率可达85~90%。
分解炉的工作原理与结构
1.分解炉 分解炉
• 分解炉是把生料粉分散悬浮在气流中,使燃料燃烧和碳酸 钙分解过程在很短时间(一般1.5~3秒)内发生的装置,是 一种高效率的直接燃烧式固相一气相热交换装置。在分解 炉内,由于燃料的燃烧是在激烈的紊流状态下与物料的吸 热反应同时进行,燃料的细小颗粒呈一面浮游,一面燃烧 ,使整个炉内几乎都变成了燃烧区。所以不能形成可见辉 焰,而是处于820~900℃低温无焰燃烧的状态。
2.1旋流式分解炉 旋流式分解炉
• 旋流式分解炉的结构比较简单.典型的旋流式分解炉其结 旋流式分解炉的结构比较简单.典型的旋流式分解炉其结 旋流式 构如图,它是由上旋流室、下旋流室和反应室所构成的。 构如图,它是由上旋流室、下旋流室和反应室所构成的。 内表面镶砌有耐火混凝土与耐火砖,反应室中部设有l 内表面镶砌有耐火混凝土与耐火砖,反应室中部设有l~3 个燃料喷嘴, 30°角向下喷射燃料。 个燃料喷嘴,成30°角向下喷射燃料。
分解炉的工作原理与结构

分解炉的工作原理与结构分解炉是一种用于处理化学物质的装置,通过在高温高压下分解原料,将其中的成分分离出来。
分解炉能够广泛应用于各种领域,如石油化工、金属冶炼、电子工业等。
本文将详细介绍分解炉的工作原理与结构。
一、工作原理分解炉的工作原理是通过提高原料的温度和压力,使得原料分子间相互碰撞,产生裂解反应分解成小分子化合物,最终将其分离出来。
一般来说,分解炉使用碳、氧气、氮气等气体作为燃料,将其加热到高温高压状态,然后通过反应管将原料送入炉内进行分解。
分解后产生的气体通过分离器进行分离,便可得到所需要的成分。
二、结构组成1. 爆炸室爆炸室位于分解炉的中部,其结构一般为圆柱形或矩形,内部有一定的燃烧空间。
爆炸室的作用是将气体和固体处理物料进行混合并提高其温度和压力。
爆炸室一般由耐火材料制成,以防止它被爆炸所摧毁。
2. 进料系统进料系统用于将处理物料送入分解炉中。
它通常包括料斗、输送机、加热炉、进气管道、反应管等。
料斗和输送机用于将原料输送到加热炉中,加热炉则用于提高物料的温度和压力,以加速裂解反应。
进气管道将气体送入爆炸室,反应管则将处理物料输送到爆炸室中进行反应。
3. 分离系统分离系统用于将分解后的气体和固体分离出来。
它通常包括冷却器、分离器和收集器。
冷却器用于将高温的气体冷却成液态,以便于分离。
分离器一般采用物理或化学方法将气体或固体的成分分离。
收集器则用于收集所需要的产品。
4. 控制系统控制系统由自动控制器、传感器和执行器组成。
自动控制器负责对分解炉的工作状态进行监测和控制,传感器则将相关数据反馈给自动控制器进行处理,执行器负责执行自动控制器下达的指令。
三、总结分解炉是一种非常重要的化工装置,其工作原理和结构与炉型密切相关。
分解炉的主要作用是将原材料分解成所需的成分,并将不需要的成分进行分离。
分解炉的结构一般由爆炸室、进料系统、分离系统和控制系统组成。
通过对分解炉的工作原理和结构的深入了解,我们可以更好地运用和管理它,使其在化工领域中扮演更加重要的角色。
分解炉
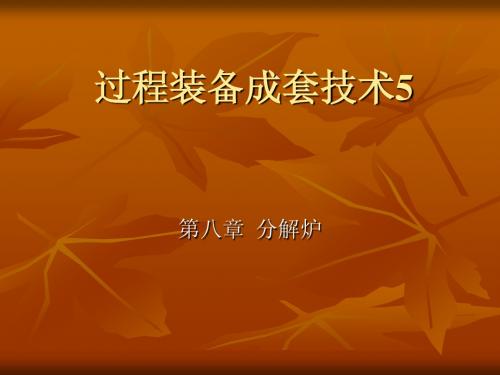
第八章 分解炉
③入窑分解率高 ④一次风——回转窑燃烧用的自然空气, 20℃。(室温) 二次风——冷却机前部的余热风,二次利 用而得名,900℃以上 三次风——冷却机中部的余热风再次利用, 650℃左右;. 2.分解炉用的空气全部通过回转窑:
第八章 分解炉
2.分解炉用的空气全部通过回转窑: ①流程简单投资少, ②适用于现有预热器窑改造, ③氧气浓度低不利于燃烧, ④窑内温度会降低,影响产量和质量, ⑤窑内风速大生料飞损严重.
第八章 分解炉
三.热量消耗图解 (曲线) 室温~850℃;物料吸收热量30%→预热阶段。 850℃~950℃;物料吸收热量50%→分解阶段。 950℃~1450℃;物料吸收热量20%→烧成阶段。 分解阶段温度仅上升了100℃,但所需热量却 达50%,这个热量是在分解炉内添加燃料来提供 的。让煤粉和生料一起在悬浮状态下,一个燃烧 放热,一个吸热分解,二者几乎同时发生。
过程装备成套技术5
第八章 分解炉
第八章 分解炉
§8—1窑外分解工艺的发展与原理 一.发展过程 1.干法旋窑生产工艺
第八章 分解炉
2.预热器பைடு நூலகம்生产工艺
第八章 分解炉
3.窑外分解生产工艺
第八章 分解炉
二.窑外分解的原理 △第一次演变:预热器窑→热量来自回转窑。 △第二次演变:预分解窑→热量来自分解炉。 在悬浮预热器和回转窑之间增设一个分解炉, 在分解炉内加入30%~60%的燃料,使燃料的放 热过程与生料的吸热过程及碳酸盐的分解过程同 时在悬浮状态下极其迅速地进行。入窑分解率可 以达到93~95%以上。
第八章 分解炉
⒋预热器窑: |_____|_____|______| 预热带 分解带 烧成带 ↓ 预热带立起来安置。 ⒌预分解窑: |_____|_____|______| 预热带 分解带 烧成带 ↓ ↓ 预热带、分解带都立起来安置。 回转窑的长度在不断地缩短,但产量、质量在不断地提高
分解炉的工作原理与结构(二)

分解炉的工作原理与结构(二)引言:分解炉作为一种常见的工业设备,在化工、石油、能源等领域具有广泛的应用。
本文将进一步介绍分解炉的工作原理与结构,以帮助读者更好地了解和应用分解炉。
正文:1. 燃料供给系统:- 燃料输送管道:用于输送燃料到燃料预处理设备。
- 燃料预处理设备:对燃料进行预处理,包括脱硫、脱氮等过程。
- 燃料喷嘴:将燃料导入燃烧室,确保燃料均匀燃烧。
2. 空气供给系统:- 空气进气管道:将空气引入燃烧室,与燃料进行充分混合。
- 空气预处理设备:对空气进行预处理,包括除尘、降温等处理。
- 风机:提供足够的风力将空气送入燃烧室。
3. 反应炉:- 燃烧室:燃料和空气混合燃烧的区域,产生高温高压的气体。
- 反应室:气体在此处进行分解反应,产生所需的产物。
- 冷却室:将分解后的气体冷却至适宜的温度,以便后续处理。
4. 热交换系统:- 冷却水系统:通过冷却水对炉体进行冷却,同时回收部分热量。
- 加热系统:通过燃料燃烧产生的热量对炉体进行加热,保持反应温度。
- 废热回收系统:对废气进行热回收,提高能源利用效率。
5. 控制系统:- 温度控制:监测和调节反应炉内的温度,确保反应过程的稳定性。
- 压力控制:监测和调节反应炉内的压力,确保操作的安全性。
- 流量控制:对燃料和空气的流量进行控制,保证燃烧和反应的平衡。
总结:通过对分解炉的工作原理与结构进行详细介绍,我们了解到燃料供给系统、空气供给系统、反应炉、热交换系统和控制系统五个大点对于分解炉的工作起到重要作用。
深入了解和熟练运用分解炉,将为化工、石油、能源等领域的生产提供更高效的工具和技术支持。
分解炉

预分解技术一.预分解技术的发展预分解窑自20世纪70年代初期诞生以来,至今已经历了四个发展阶段。
⑴第一阶段。
20世纪70年代初期到中期。
为预分解技术的诞生和发展阶段。
德国多德豪森(Dottenhausen)水泥厂于1964年用含可燃成分的油页岩作为制造水泥原料的组分。
为了避免可燃成分在低温部分过早挥发,他们在悬浮预热器的中间喂入含油页岩的生料,提高生料的入窑分解率,开创了预分解技术的先例。
但是真正使用高级燃料在分解炉内作为第二热源的预分解窑,则是从1971年开始。
因此,预分解窑的诞生,应是日本IHI公司和秩父水泥公司共同开发的第一台SF窑(Suspension Preheater-Flash Furnacel)。
第一台SF窑诞生以后,日本各种类型的预分解窑相继出现(三菱公司的MFC炉-1971年;小野田水泥公司的RSP炉-1972年;川崎与宇部水泥公司共同开发的KSV炉-1974年等等)。
分解炉都是以重油为燃料。
⑵第二阶段。
20世纪70年代中、后期,为预分解技术的完善、提高阶段。
1973年国际爆发石油危机之后,油源短缺,价格上涨,许多预分解窑以煤代油。
原来以石油为燃料的分解炉难以适应,从而通过总结、改进,各种第二代、第三代的改进型分解炉应运而生。
例如:高径比(H/D)增加的MFC炉及N-MFC炉等的出现即为典型代表。
这些改进型炉不仅增加了炉容,在结构上也有很大改进。
为了提高燃料燃尽率,延长物料在炉内的滞留时间,许多分解炉结构采用了迭加效应,改善分解炉的功效。
⑶第三阶段。
20世纪80年代至90年代中期,为悬浮预热器和预分解技术日臻成熟,全面提高阶段。
中国科研、设计和生产人员已经比较成熟熟练地掌握了新型干法水泥生产技术,对中国水泥工业地发展和科技进步发挥了巨大作用。
如:LZ日产3200t预分解系统地技术改造工程。
⑷20世纪90年代中期至今,为水泥工业向“生态环境材料型”产业迈进阶段。
五大标志:一是产品质量提高,满足高性能混凝土地耐久性要求;二是尽力降低熟料热耗及水泥综合电耗,节约一次资源和能源;三是大力采用替代性原料和燃料,提高替代率;四是实行“清洁生产”,三废自净化;五是降解利用其它工业产生地废渣、废料,生活垃圾及有毒、有害地危险废弃物,为社会造福。
分解炉

3.2.4常见分解炉特征简介
FLS系列分解炉的三代“喷腾”型炉体结构
19 19
3.2.4常见分解炉特征简介
4.DD分解炉 DD分解炉的全称是:Dual Combustion and Denitration Precalciner,简称:DD炉。它最先由原 日本水泥株式会社研制,后来该公司又与日本神户 制钢联合开发推广。分解炉属“喷腾叠加(双喷腾 )”型,在炉体下部增设还原区来将窑气中NOx有 效还原为N2,在分解炉内主燃烧区后还有后燃烧区 ,使燃料第二次燃烧,被称为:双重燃烧。
22 22
Examples of suggested formatting styles
陈越君
23
4 4
3.2.1预分解技术原理
分解炉的发展方向 适当扩大炉容,延长气流在炉内的滞留时间; 改进炉的结构,延长物料在炉内滞留时间; 保证向炉内均匀喂料,且料入炉后,尽快地分散、均布; 改进燃烧器形式与结构,合理布置,使燃料尽快点燃; 下料、下煤点及三次风之间布局的合理匹配,以有利于燃料 起火、燃烧和碳酸盐分解; 选择分解炉在预分解窑系统的最优部位、布置和流程,有利 于分解炉功能的充分发挥,提高全系统功效,降低NOx, SO3等有害成分排放量,确保环保达标。
3 3
3.2.1预分解技术原理
分解炉内气流 分解炉内的气流运动基本型式:即涡旋式、喷腾式、悬浮式 及流化床式。 功能:在这四种型式的分解炉内,生料及燃料分别依靠“涡 旋效应”、“喷腾效应”、“悬浮效应”和“流态化效应” 分散于气流之中。由于物料之间在炉内流场中产生相对运动 ,从而达到高度分散、均匀混合和分布、迅速换热、延长物 料在炉内的滞留时间,达到提高燃烧效率、换热效率和入窑 物料碳酸盐分解率的目的。
2.3分解炉

优点是保证炉内燃料在纯空气中燃烧。
半同线型
异线型
旁路放风型
(c1):窑气在分解炉后与出分解炉的炉气混合,再入预热器系统。 (c2):窑气不与出分解炉的炉气混合,各自经过一个单独的预热
(2) RSP型炉:
RSP型炉:
结构:左部:混合室(MC室) 右部:上部旋风预燃室(SB炉) 下部涡旋分解室(SC炉)
特点: 燃料:在旋风预燃室喷入,与热空气直接接触而燃烧, 燃烧效果好。 生料:从SC室喂入,被三次风分散。 气体: 窑气经上升管道喷腾进入,热空气从SC炉的内侧 以切线方向送入,两股气流一起进入混合室。
炉上行 管道
③适用各种燃料。
(8)我国自主研发的分解炉类型
(1)炉中部设有缩口,使气固 流产生二次“喷腾效应”。 (2)三次风切线进入设于炉下锥体的 上部,煤由三次风入口或侧部加入。 (3)炉的下锥体部位设有脱氮燃料 喷嘴。 (4)在炉的下部圆筒体内不同的高 度设有喂料管。 (5)炉的顶部设有气固流反弹室。
天津水泥工业设计院
N-SF和DD炉
N-MFC和DD
天津水泥工业设计院 的优化,适合 烧劣质煤
炉的优化,炉 区容积大,适
RSP和DD炉 的优化
合烧无烟煤
南京水泥工业设计院 南京水泥工业设计院
NC-SST炉
• 属于管道式分解炉
• 和ILC分解炉的基础
• 上研发。
• 结构简单炉容大 (10m3/t.h),流体 阻力小,适合低挥发份 的煤。
2.3.2分解炉的分类
旋流式——旋流效应
发展趋势
分解炉设计任务书
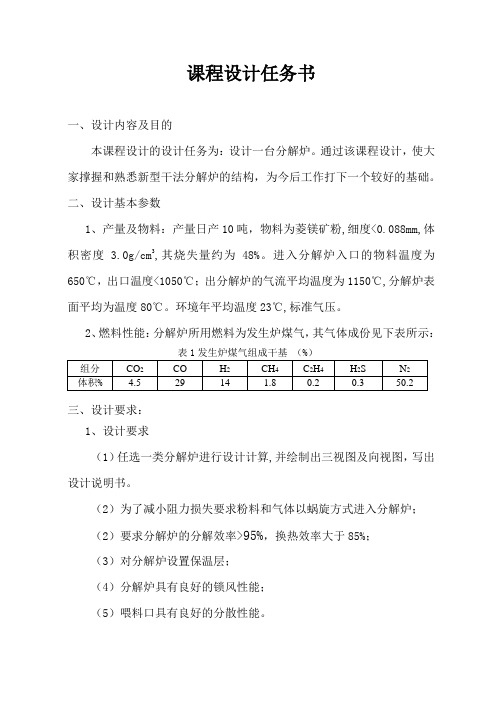
课程设计任务书一、设计内容及目的本课程设计的设计任务为:设计一台分解炉。
通过该课程设计,使大家撑握和熟悉新型干法分解炉的结构,为今后工作打下一个较好的基础。
二、设计基本参数1、产量及物料:产量日产10吨,物料为菱镁矿粉,细度<0.088mm,体积密度 3.0g/cm3,其烧失量约为48%。
进入分解炉入口的物料温度为650℃,出口温度<1050℃;出分解炉的气流平均温度为1150℃,分解炉表面平均为温度80℃。
环境年平均温度23℃,标准气压。
2、燃料性能:分解炉所用燃料为发生炉煤气,其气体成份见下表所示:表1发生炉煤气组成干基(%)组分CO2CO H2CH4C2H4H2S N2体积% 4.5 29 14 1.8 0.2 0.3 50.2三、设计要求:1、设计要求(1)任选一类分解炉进行设计计算,并绘制出三视图及向视图,写出设计说明书。
(2)为了减小阻力损失要求粉料和气体以蜗旋方式进入分解炉;(2)要求分解炉的分解效率>95%,换热效率大于85%;(3)对分解炉设置保温层;(4)分解炉具有良好的锁风性能;(5)喂料口具有良好的分散性能。
2、结构形式要求分解炉的结构形式不作特殊要求,基本要求是保证物料在分解炉中有足够的仃留时间。
3、其他计算要求:选择合适的撒料箱、连接管道、管道直径、管道间的连接法兰及锁风卸料阀。
四、计算要求1、对分解炉进行选型计算及具体尺寸的设计;2、参考有关设计资料对分解炉的主要结构进行计算确定,其中要求分解炉的入口处气流速度>18m/s;3、计算出分解炉内的压头损失;4、确定物料入分解炉的位置、入料方式,连接管道、管道直径及管道间的连接法兰、锁风卸料阀的规格型号;5、计算并确定分解炉用燃烧器的规格型号;6、确定分解炉通风量及提供风量的风机规格型号。
五、其他要求在设计计算过程中,利用excel表格进行计算并在批注中注明计算参数选择的处出。
在excel中进行的计算内容能便于大家阅读。
附录 氨分解炉操作手册

附录:AQ/FC系列液氨制氢炉/纯化装置操作指导手册1、液氨制氢炉概述氨分解总流程:液氨瓶→液氨汇流排→双回路液氨减压装置→液氨分气缸→液氨制氢炉/纯化装置→氢气分气缸→氢气氮气配比器→烧结炉高纯度的氢氮混合气是一种良好的还原性保护气体,可用于零件退火,脱碳处理及铜基、铁基粉末冶金烧结.液氨制氢炉工作原理:液氨气化后(氨气压力:<0.1MPa)在750℃—850℃情况下,经催化剂(镍催化剂)作用,分解为氢气和氮气,并吸收热量.2NH3→3H2+N2液氨制氢炉需注意的安全事项:⑴、液氨进入液氨制氢炉必须是气态的!为达到此目的,有以下3个措施:液氨储罐出口须装有减压阀,经有效减压后氨气压力小于0。
2MPa;液氨储罐和液氨制氢炉连接管路距离大于5m;液氨制氢炉设备装有汽化器,并能有效工作。
⑵、氨气是一种对人体粘膜有刺激性的化学气体,分解后的氮气是一种使人窒息的气体,氢气是一种易燃、易爆还原性极强的气体,因此,设备现场必须良好通风,5m范围内不得有明火,所有氨源处必须配置水源,作为氨泄露的应急措施.⑶、液氨制氢炉必须安全可靠接地,接地电阻<0。
5欧姆。
2、液氨制氢炉设备基本参数AQ/FC系列液氨制氢炉/纯化装置设备基本参数:工作压力:<0。
1Mpa;工作温度:800℃—850℃液氨消耗:12kg/h原料氨气:符合《液体合成氨》规定一级品要求;含水量:≤2000PPm纯化后氨分解混合气:露点:≤—10℃残氨: ≤5PPm出口压力:<0。
1Mpa;3、液氨制氢炉/纯化装置设备工作原理:AQ液氨制氢炉采用镍催化剂加热分解液氨;FC纯化装置采用专用干燥剂物理吸附混合气中水分和残氨.其工作流程如下图:AQ 液氨制氢炉为单式流程:液氨→汽化器→减压阀→热交换器→制氢炉炉胆(镍催化剂加热分解液氨)→热交换器→冷却器→分解氨其中:冷却器后设放空阀旁路,方便停炉时分解氨排放。
为实现热交换,设备配置冷却水。
水冷却流程:冷却水→冷却器进水口→冷却器→冷却器出水口→汽化器进水口→汽化器→汽化器进水口→室外(液氨瓶水池)FC纯化装置为复式流程:Ⅰ组工作,Ⅱ组再生,通过阀门操作可进行工作再生切换.FC纯化装置Ⅰ组工作流程:冷却器分解氨→Ⅰ组进工作阀→干燥器(专用干燥剂物理吸附混合气中水分和残氨)→Ⅰ组出工作阀→纯气出口阀→纯气流量计→纯化后氨分解混合气其中:纯气出口阀前设取样阀,用于检测纯化后氨分解混合气的露点及残氨含量。
- 1、下载文档前请自行甄别文档内容的完整性,平台不提供额外的编辑、内容补充、找答案等附加服务。
- 2、"仅部分预览"的文档,不可在线预览部分如存在完整性等问题,可反馈申请退款(可完整预览的文档不适用该条件!)。
- 3、如文档侵犯您的权益,请联系客服反馈,我们会尽快为您处理(人工客服工作时间:9:00-18:30)。
PDF 文件使用 "pdfFactory Pro" 试用版本创建
AX分解炉主要部件及功能
• 触煤—也称催化剂
催化剂应具有足够的强度和合适的形状 以防其在反应罐内粉化及堆实,并应提供产 气反应所需的足够表面积。催化剂应具有足 够的催化活性及较高的抗中毒能力,以加速 反应,保证正常的产气率。 触媒由泡沫氧化铝(Al2O3)作为载体, 含浸硝酸镍和硝酸镁后阴干,再经加热焙烧 而制成。氧化铝载体上沉积一定的NiO,具 有优良的耐热性和强度。
影响氨分解率的因素 • 影响氨分解率的因素主要有温度和催化 剂的活性,由于是吸热反应,温度愈 高,分解率就愈大。一般操作温度是 700~1000 ℃ 。 • 常采用催化剂有铁质催化剂和镍质催化 剂。前者一般使用温度为700 ℃左右; 后者一般使用温度为850~950 ℃ 。
PDF 文件使用 "pdfFactory Pro" 试用版本创建
分解气的特性
• 分解气中的残氨含量较高时,氨中的氮(N) 对烧结制品可能有轻微氮化作用,使零件硬化、 变脆。 • 分解氨的可燃性与爆炸危险性几乎与氢气相同。 与空气混合(当空气中含氢从4~74%时)有 爆炸的可能。分解氨遇到水银等也会因发生化 合反应引起爆炸。所以在使用氨分解气时要注 意安全。
PDF 文件使用 "pdfFactory Pro" 试用版本创建
AX分解炉主要部件及功能
• 流量计
一般多用浮子式(也称转子式)流量 计,当有气流自下而上通过时,浮子被 气流顶到一定高度,浮子的高度越高, 与玻璃管形成的环缝越大,通过的气体 量就越多。
• 减压阀
装在原料气管路上,其作用是稳定原料 气压力。
PDF 文件使用 "pdfFactory Pro" 试用版本创建
PDF 文件使用 "pdfFactory Pro" 试用版本创建
RX变成炉主要部件及功能
• 冷却器
是使反应后的高温气体 进一步冷却到40℃以下, 再进入干燥器。
PDF 文件使用 "pdfFactory Pro" 试用版本创建
PDF 文件使用 "pdfFactory Pro" 试用版本创建
下周学习讨论主题
主讲:许 时间: 月
锋 日
PDF 文件使用 "pdfFactory Pro" 试用版本创建
PDF 文件使用 "pdfFactory Pro" 试用版本创建
AX分解炉主要部件及功能
AX1#安装写真
PDF 文件使用 "pdfFactory Pro" 试用版本创建 ÿf
AX分解炉主要部件及功能
• 热交换器 液氨在汽化器内被 加热气化,经过过滤、 减压进入分解炉,在高 温和催化剂作用下,气 氨分解成H2和N2混合气。 高温的分解气,先进入 汽化器与液氨换热而被 冷却,这样既冷却了混 合气,又预热了液氨 气,混合气经冷却器进 一步冷却。
PDF 文件使用 "pdfFactory Pro" 试用版本创建
AX分解炉的操作与维护
作業標準書
NO. 内 步 容 骤 D734-0007 G 确 工 程 认 事 项
承 认 查 阅 拟 案
烧结
作成日 页 确 次 认
2003.01.13. 1 频 / 次 1
氨分解气发生装置流程图
PDF 文件使用 "pdfFactory Pro" 试用版本创建
AX分解炉的总体设计
发生装置通常由以下五部分组成:
1.汽化器(在氨站) 2.分解炉加热体和炉芯管(反应罐) 3.热交换器(AX1#、AX3#) 4.冷凝器 5.干燥器
PDF 文件使用 "pdfFactory Pro" 试用版本创建
AX分解炉设备构造 AX分解炉设备构造 方面的内容介绍
2008年4月9日
PDF 文件使用 "pdfFactory Pro" 试用版本创建X分解炉是液氨经气化后,在催化剂作用下 加热分解制得N2+H2的发生装置。其化学反 应如下: 2NH3 3H2+N2 –22千卡 它的最大特点是,不含CO和CO2,不可能有渗 碳倾向;当气氛的露点较低时,具有强还原性. 因而对含Zn、Cr等合金材料的光亮保护加 热,特别适宜。粉末冶金烧结,纯铁粉,高铬 钢、不锈钢烧结常采用氨分解气,因为煤气转 化气含有CO、H2O和CO2等成分,这些成分 能使钢中的铬氧化或碳化 。
工
程
烧结
作成日
页
2003.06.20. 1 / 1
容
AX 分 解 炉 露 点 、 残 氨 测 定 标 准
次
1.目的 保证 AX 分解炉正常运行,为烧结炉提供合格的分解气,确保产品质量。 2.适用范围 本标准适用于烧结课之 AX 分解炉。 3.露点测定的具体步骤 3.1.将露点总电源接通,进气管连接于 AX 分解气管道上。 3.2.按下露点仪电源按钮及露点记录电源按钮,调整气体流量至 6~8L/H。 3.3.露点显示稳定 2~4H 后即可读取露点值。 3.4.露点-40℃以下为正常,各分解炉露点每月校验一次。 4.残氨测定的具体步骤: 4.1.准备好真空气体采集器及氨检验管。 4.2.将氨检验管两端板断,按检验管上的箭头方向,将一端插在采集器上。 4.3.将检验管的另一端接通 AX 分解气,然后使用采集器缓慢抽气 100ml。 4.4.取下检验管, 读数变色层(淡紫色→淡黄色)末端的读数, 此即为残氨流量。 4.5.残氨 100ppm 以下为正常。各分解炉露点每月校验一次。 5.露点、残氨校验测定记录在《AX 分解炉露点、残氨测定记录》(734-0043-01) 中, 1 次/月。
1
手感温和 (10℃~45℃) 变 更 内 容 变 更 理 由 日期
03.01.13.
担当
董 强
承认
官劲松
条件变更
实际操作需求
PDF 文件使用 "pdfFactory Pro" 试用版本创建 ÿ
AX分解炉的操作与维护
作業標準書
NO.
内
承 认
查
阅
拟
案
D734-0043G
PDF 文件使用 "pdfFactory Pro" 试用版本创建
液氨分解特性(分解率理论数据)
• 氨较易分解,根据计算,氨在192℃开始 分解,但低温下分解速度很慢。有催化剂存 在时,在常压下,于600~700 ℃氨的分解 率可达99%以上。500 ℃ ,氨分解率为 99.72%,残余氨为0.14%;700 ℃ ,相应 为99.95%和0.025(250ppm);900℃ , 相应为99.99%和59ppm。
AX分解炉的操作与维护
(1)熟悉设备原理、构造,检查气、电、水各系统是否畅通,有 无跑漏现象。并接通电源、水源。 (2)触媒(还原)活化。分解炉内装的触媒,因设备停放期间总 有水分、氧气等进入炉内,致使触媒活性下降,因此在初次开车时 需要进行触媒的活化。首先,接通电源使设备升温至350℃、,然 后打开放空阀,通入N2置换炉内空气,置换OK后,关闭N2;并 立即打开氨阀通氨气;这时,分解氨混合气阀关闭,气体不能通过 净化系统,直接放空;然后 350~500、500~650 ℃,650~800 ℃ 分段保温,进行活化,活化时间与设备的放置时间有关,待到由分解 炉出口出来得气体氨含量小于0.1%(如无化学分析设备也可以用 鼻子嗅来判断,如果嗅到得刺激性味道不大时,即可认为氨含量小 于0.1%),这时活化就可以停止。也可以从火焰得颜色判断,火 焰从黄色变成深橘红色,说明活化正常。活化初期和中期会产生大 量得水分,需要从底部排除,直至放不出水时,说明还原充分,气 体已可以使用。然后打开混合气阀,关闭放空阀,设备就可以正常 使用了。
PDF 文件使用 "pdfFactory Pro" 试用版本创建
AX分解炉主要部件及功能
• 炉芯管 (反应罐)
采用耐热不锈钢管(SUS310S) 焊接,用不锈钢法兰、螺丝与 上部连接。罐内装有触媒(催 化剂),其结构有直通式、U 形和套管式等。反应罐设计原 则是:罐应有足够的长度,使 气流在催化剂床层内有足够的 反应时间;沿反应罐的径向温 差不能太大,不应使部分催化 剂过烧失效,或温度过低反应 活性不够。反应罐的设计和制 造应保证在其工作温度下具有 足够的强度,在规定的使用期 限内,不产生有碍正常工作的 变形与泄漏;
AX分解炉主要部件及功能
• 分解炉加热体
一般采用铁-铬-铝电热丝绕成的 螺管形发热体加热,提供氨分解 需要的热量。 • 外壳用普通钢板制成,外壳与反 应罐之间充填耐火棉或其他保温 材料。 • 炉体的结构根据反应罐的类型而 定。 • 分解炉的功率,以氨分解气计, 一般为1.1~1.3kw/(nm3.h)。
PDF 文件使用 "pdfFactory Pro" 试用版本创建
氨制备气氛特性理论数据如下表:
气氛组成 (%) N2 H2 25 75 露点 每100m3 (℃) 气氛氨耗 用(kg) -51 37.95 安全 性 可 燃
氨分解气
PDF 文件使用 "pdfFactory Pro" 试用版本创建
标记 变
更 内
容
变
更
理
由
日
期
担当 董 强
承认 官劲 松
1
3.3.、3.4.、4.5.
实 际 工作需要
03.06.20.
表 单 编 号 :QP.05.03-01.
扬 州 保 来 得 工 业 有 限 公 司
表单 版本:1.0-1999.
PDF 文件使用 "pdfFactory Pro" 试用版本创建 ÿ
70m 3 /Hr 分 解 炉 操 作 作 业 标 准