CLB-50KLB传感器参数
奔驰盲点辅助系统介绍

H4/61A7/3B29/7B29/10B29/6(5)转向柱模块控制单元:读取电子方向盘和转向角速度信号,B29/2B29/3图1 前雷达传感器图2 后雷达传感器图3 警告灯M21/1e2A1仪表盘 N49方向盘传感器A7/3牵引液压控制单元 N62/9雷达传感器控制单元B24/15横摆率,横向和纵向加速度传感器 N69/1左前车门控制单元B29前部远距离雷达传感器 N69/2右前车门控制单元B29/2左前保险杠雷达传感器 N73电子点火开关B29/3右前保险杠雷达传感器 N80转向柱模块B29/6左后保险杠雷达传感器 N88轮胎压力监控器控制单元B29/7右后保险杠雷达传感器 N127传动系统控制单元H4/61仪表盘扬声器 S4组合开关图7 雷达传感器的探测范围图8 警告信息1 装配主动式盲点辅助系统的车辆2 处于盲点中的车辆3 左后探测范围(近距离)4 右后探测范围(近距离)5 左前探测范围(近距离)6 右前探测范围(近距离)7 前部探测范围(远距离)(4)制动系统主动干预:如果雷达传感器控制单元检测到即将与盲区域内的车辆有发生侧面碰撞的危险,尤其是在变道期间时,则会3457621t4t3t2t1A 车道,超车期间存在处于盲点中的车辆。
B 车道和装配盲点辅助系统的车辆。
t1 车辆进入盲点区域。
就绪显示从30km起为绿色(系统启用)A1仪表盘 N49方向盘传感器A7/3牵引液压控制单元 N62/9雷达传感器控制单元B24/15横摆率,横向和纵向加速度传感器 N69/1左前车门控制单元B29前部远距离雷达传感器 N69/2右前车门控制单元B29/2左前保险杠雷达传感器 N73电子点火开关B29/3右前保险杠雷达传感器 N80转向柱模块B29/6左后保险杠雷达传感器 N88轮胎压力监控器控制单元B29/7右后保险杠雷达传感器 N127传动系统控制单元H4/61仪表盘扬声器 S4组合开关M21/1左侧车外后视镜 Y3/8n4集成式变速箱控制系统单元M21/1e2左侧盲点辅助系统警告灯 CAN B车内控制器区域网络(CAN)M21/2右侧车外后视镜 M21/2e2右侧盲点辅助系统警告灯 B29/2B29/3B24/15A7/3N49N80N30/4N127N73A1N88Y3/8n4N69/1N69/2N28/1H4/61M21/1e2M21/1M21/2e2M21/2N3/9N3/10S4B29/6B29/7B29N62/1广 告Copyright©博看网. All Rights Reserved.。
贝利尼维加吕斯3300 XL 50mm接近传感器系统产品数据手册说明书

3300 XL 50mm Proximity Transducer System Product DatasheetBently Nevada* Asset Condition MonitoringDescriptionThe 3300 XL 50 mm Transducer System consists of a separate 50mm probe, an extension cable, and a 3300 XL 50 mm Proximitor*Sensor. The large diameter coil gives this system a maximum linearrange of 27.9 mm (1100 mils), the longest linear range of our eddycurrent transducer line. This linear range makes the 3300 XL 50mmTransducer System ideal for measuring the differential expansion(DE) or rotor expansion (RX) of large steam turbine generators thatresults from the difference in growth rates between the turbinerotor and the machine stator (casing).Measuring Differential ExpansionThe Differential Expansion measurement is made by using twoproximity transducers that observe a collar or ramp some distancefrom the thrust bearing. Typical transducer mounting arrangementsthat require the 3300 XL 50 mm Transducer’s long linear rangeinclude:•Two transducers observing the same side of a collar.•Two complementary input transducers observing oppositesides of a collar, effectively doubling the measurable DErange.The criteria for selecting a mounting method are the size of theavailable target, the expected amount of rotor axial movement, andthe type of DE target that exists in the machine. If the collar height issufficient and the required total measurement range is less than27.9 mm (1.1 inches), the preferred configuration for redundantmeasurements is to use two transducers observing the same side ofa collar. When 28 mm to 56 mm (1.1 to 2.2 inches) of total range arerequired, install the transducers in a complementary fashion onopposite sides of the differential expansion collar or other targetmaterial.System CompatibilityThe 3300 XL 50 mm probe comes in three case & threadconfigurations to physically replace all standard 7200 50 mmsystems (including side and rear exit probes). The standard 7200style mounting brackets are still available as accessories. Inaddition, a new bracket to adapt the probe to the 50mm DE Integraltransducer sliding mount base is also available. The ProximitorSensor has a 0.394 V/mm (10 mV/mil) output that is identical to thatof the 7200 and 50 mm DE Integral systems, which allows customersto upgrade without requiring any changes in the monitorconfiguration. When upgrading from previous systems, everytransducer system component (probe, extension cable, andPart Number: 174014Rev: FProximitor Sensor) must be replaced with 3300 XL 50 mm components.Proximity Probe and Extension CableThe 3300 XL 50 mm probe is designed to survive the harshest steam turbine DE environments. It can continually operate and maintain its accuracy in high temperatures up to 200 ︒C (392 ︒F), and can withstand intermittent high temperatures up to 250 ︒C (482 ︒F). The 50 mm probe has both a front and rear seal which, combined with the High Temperature FluidLoc* cable (standard on all 50 mm probes), prevent moisture from entering the probe tip. Special high-temperature ClickLoc* connectors are also standard on the probe and extension cable. Each probe and cable comes with connector protectors and a disposable connector protector installation tool to ensure that the connectors remain free of contamination. The ClickLoc connector on the probe lead features a removable collar that facilitates routing the cable through tight clearances.The 3300 XL 50 mm probe is available in straight exit case styles with ½-20 English threads or M14x1.5 metric threads, including a locknut with predrilled safety wire holes. The side exit probe has two ¼-20 mounting holes in the rear of the probe case. For both straight exit and side exit probes the overall case diameter is 1.99 inches.Proximitor SensorThe 3300 XL 50 mm Proximitor Sensor1 has the same advanced features as all 3300 XL Proximitor Sensors. Its thin design allows it to be mounted in either a high-density DIN-rail installation or a more traditional panel mount configuration. Improved RFI/EMI immunity allows the 3300 XL Proximitor Sensor to achieve European CE mark approvals without any special mounting considerations. This RFI immunity prevents the transducer system from being adversely affected by nearby high frequency radio signals. SpringLoc terminal strips on the Proximitor Sensor require no special installation tools and facilitate faster, highly robust field wiring connections.Notes:Proximitor Sensors are supplied by default from the factory calibrated to AISI 4140 steel. Calibration to other target materials is available upon request. Mounting AccessoriesThe correct operation of the transducer system must be initially verified during installation and periodically thereafter. This is done by physically moving the transducer to simulate the motion of the shaft collar. This requires a mounting bracket that allows the transducer system to slide relative to the shaft rotor and collar.An optional Sliding Bracket can be ordered for the 3300 XL 50 mm Transducer for both single transducer and complementary input applications. This mounting bracket allows you to verify the transducer system and gap the probes by sliding the transducer system through its linear range. The base plate of the sliding bracket is installed on the inner surface of the turbine case near the differential expansion collar. Probes are installed in the probe clamp that attaches to the sliding carriage. The sliding carriage slides onto and is secured to the base plate with bolts and safety wire. To verify and install the transducer, loosen the bolts securing the sliding carriage to the base plate and move the sliding carriage and probes. A verification kit with spindle micrometer can be temporarily secured to the base plate to provide a reference for axial verification measurements. The spindle micrometer measures the movement of the transducer system relative to the collar during these verification tests. SpecificationsUnless otherwise noted, the following specifications are for a 3300 XL 50 mm Proximitor Sensor, extension cable and probe between 0︒C and +45︒C (+32︒F to +113︒F), with a -24 Vdc power supply, a 10 kΩ load, a Bently Nevada supplied AISI 4140 steel target that is 102 mm (4.0 in) diameter or larger. The system accuracy and interchangeability specifications do not apply when using a transducer system calibrated to any target other than a Bently Nevada AISI 4140 steel target.ElectricalProximitorSensor InputAccepts one non-contacting 3300XL 50 mm Proximity Probe andExtension Cable.PowerRequires -17.5 Vdc to -26 Vdcwithout barriers at 12 mAmaximum consumption, -23 Vdcto -26 Vdc with barriers.Operation at a more positivevoltage than -23.5 Vdc can resultin reduced linear range.Outputresistance50Extension cablecapacitance:69.9 pF/m (21.3 pF/ft) typical Field wiring:0.2 to 1.5 mm2(16 to 24 AWG)Recommend using three-conductor shielded triad cable. Linear Range:27.9 mm (1100 mils). Linear rangebegins at approximately 1.3 mm(50 mils) from target and is from1.3 to 29.2 mm (50 to 1150 mils)(approximately –1.5 to –12.5 Vdc). Average ScaleFactor (ASF)394 mV/mm (10 mV/mil) nominal Deviation frombest fit straightline (DSL)Less than ±0.74 mm (±29 mils) Systemperformanceover extendedtemperatures:Over a probe temperature rangeof -35°C to +120°C (-31°F to+248°F) with the ProximitorSensor and extension cablebetween 0°C to +45°C (+32°F to+113°F), the DSL remains within±2.03 mm (±80 mils).Over a Proximitor Sensor andextension cable temperaturerange of -35°C to +65°C (-31°F to+149°F) with the probe between0°C to +45°C (+32°F to +113°F),the DSL remains within ±2.03 mm(±80 mils). RecommendedMinimumTarget Size:102 mm (4.0 in) diameter (flattarget)Compliance and Certifications Note: This device complies with part 15 of the FCC Rules. Operation is subject to the following two conditions: (1) This device may not cause harmful interference, and (2) This device must accept any interference received, including interference that may cause undesired operation.EMCEuropean Community Directives:EMC Directive 2014/30/EUStandards:EN61000-6-2EN61000-6-4RoHSEuropean Community Directives:RoHS Directive 2011/65/EU MaritimeABS 2009 Steel Vessels Rules1-1-4/7.7, 4-8-3/1.11.1, 4-9-7/13Hazardous Area ApprovalsFor the detailed listing of country and product specific approvals, refer to the Approvals Quick Reference Guide , document 108M1756, at .CSA/NRTL/C3300 XL Proximitor Sensor ia:Class I, Zone 0: AEx/Ex ia IIC T4/T5 Ga; Class I, Groups A, B, C, and D,Class II, Groups E, F and G, Class III;When installed with intrinsically safe zener barriers per drawing 141092 or when installed with galvanic isolators.nA, ec:Class I, Zone 2: AEx/Ex nA IIC T4/T5 Gc; Class I, Division 2, Groups A, B, C, and D;Class I, Zone 2: AEx/Ex ec llC T4/T5 Gc; Class I, Division 2, Groups A, B, C, and D; When installed without barriers per drawing 140979. T5 @ Ta= -55 ˚C to +85 ˚C.T4 @ Ta= -55 ˚C to +100˚C.3300 XL Probe ia:Class I, Zone 0: AEx/Ex ia IIC T5…T1 Ga; Class I, Groups A, B, C, and D,Class II, Groups E, F and G,Class III;When installed with intrinsically safezener barriers per drawing 141092 orwhen installed with galvanic isolators. (see Table 1: Temperature Schedule)nA, ec:Class I, Zone 2: AEx/Ex nA IIC T5…T1 Gc; Class I, Division 2, Groups A, B, C, and D;Class I , Zone 2: AEx/Ex ec llC T5…T1 Gc; Class I, Division 2, Groups A, B, C, and D;When installed without barriers per drawing 140979. (see Table 1: Temperature Schedule)ATEX/IECEx3300 XL Proximitor Sensor ia:II 1 GEx ia IIC T4/T5 Ga Ui= -28V Uo= -28V Ii= 140mA Io= 140mA Pi= 0.91W Po= 0.742W Ci- 47nF Co= 1.5nF Li= 1460µH Lo= 610µH nA,ec: II 3 GEx nA IIC T4/T5 GcEx ec llC T4/T5 Gc Ui= -28V li= 140 mAT5 @ Ta= -55˚ C to +85 ˚C T4 @ Ta= -55 ˚C to +100 ˚C 3300 XL ProbeNote: Probe entity parameters are met when used with BN extension cables and connected to BN Prox.ia: II 1 GEx ia IIC T5…T1 Ga, (see Table 1: Temperature Schedule) Ui = -28V Ci = 1.5 nF Ii = 140 mA Li =610 µHPi = 0.91 WnA, ec:II 3 GEx nA IIC T5…T1 Gc,Ex ec llC T5…T1 Gc,(see Table 1: Temperature Schedule).Ui = -28V li= 140 mA Table 1: Temperature ScheduleTemperature Classification Ambient Temperature (Probe Only)T1 -55ºC to +232ºCT2 -55ºC to +177ºCT3 -55ºC to +120ºCT4 -55ºC to +80ºCT5 -55ºC to +40ºC Hazardous Area Conditions of Safe Use: CSA/NRTL/C:ia:Install per Bently Nevada drawing 141092.nA, ec:Install per Bently Nevada drawing 140979. ATEX/IECEx:ia:Install per Bently Nevada drawing 141092.nA, ec :The Prox must be installed so IBas to providethe terminals with a degree of protection ofat least IP54.MechanicalProbe TipMaterial:Polyphenylene Sulfide (PPS). Probe CaseMaterial:AISI 304 stainless steel (SST). Probe CableSpecifications:75 Ω triaxial,perfluoroalkoxyethylene (PFA)insulated FluidLoc probe cable inthe following total probe lengths:1, 5 or 9 metres.Extension CableMaterial:75 Ω triaxial,perfluoroalkoxyethylene (PFA)insulated FluidLoc cable. ProximitorSensorMaterial:A380 aluminumSliding BracketMaterial:Anodized aluminum and stainlesssteelSystem Length:5 or 9 metres including extensioncableProbe andExtension CableArmor(optional):Flexible SST with PFA outer jacket. TensileStrength(maximumrated):330 N (75 pounds) probe case toprobe lead. 270 N (60 pounds) atprobe lead to extension cableconnectors.Connector material:Gold-plated brass and gold-platedberyllium copperTorque SpecificationsConnector-to-connector torque Recommendedtorque:Finger tightMaximumtorque:0.565 N•m (5 in•lb)Minimum BendRadius (with orwithout sstarmor):25.4 mm (1.0 in) Environmental LimitsProbe Temperature RangeOperatingand StorageTemperature:-35°C to +200°C (-31°F to +392°F) Short-termOperatingand StorageTemperature:+250°C (+482°F) for less than 24hours.Extension Cable TemperatureRangeOperatingand StorageTemperature:-51°C to +200°C (-31°F to +392°F) Proximitor Sensor TemperatureRangeOperatingTemperature:-51°C to +100°C (-60°F to +212°F) StorageTemperature:-51°C to +105°C (-60°F to +221°F) Sliding Bracket TemperatureRangeOperatingand StorageTemperature:-35°C to +200°C (-31°F to +392°F) RelativeHumidity:Less than a 3% change in AverageScale Factor (ASF) when tested inaccordance with IEC standard 68-2-66.Probe Pressure:3300 XL probes are designed toseal differential pressure betweenthe probe tip and case. The probeis sealed with Viton® O-rings.Probes are not pressure testedprior to shipment. Contact ourcustom design department if yourequire a test of the pressure sealfor your applicationNote: It is the responsibility of thecustomer or user to ensure that all liquidsand gases are contained and safelycontrolled should leakage occur from aproximity probe. In addition, solutionswith high or low pH values may erode thetip assembly of the probe causing medialeakage into surrounding areas. BentlyNevada will not be held responsible for anydamages resulting from leaking 3300 XLproximity probes. In addition, 3300 XLproximity probes will not be replacedunder the service plan due to probeleakage.Patents:5,685,8846,293,0056,643,9097,239,133Components or procedures described in these patents apply to this product.Ordering InformationFor the detailed listing of country and product specific approvals, refer to the Approvals Quick Reference Guide, document 108M1756, at3300 XL 50 mm Proximity Probe: 330876-AXX-BXX-CXX-DXXA:Probe Case Type Option0 1 ½-20 Thread - Straight Exit0 2 M14x1.5 Thread - Straight Exit0 3Smooth 1.99 in dia - Side ExitB:Total Length Option1 0 1.0 metre (3.3 feet)5 0 5.0 metres (16.4 feet)9 0 9.0 metres (29.5 feet)Note: Five meter probes are designed for use with thefive meter Proximitor Sensor only..C: Armor Option0 0High Temperature FluidLoc Cable0 1High Temperature FluidLoc Cablewith ArmorD: Agency Approval Option0 0 No Approvals0 5Multiple Approvals3300 XL 50 mm Proximitor Sensor 330878-AXX-BXXA:Total Length and Mounting Option5 0 5.0 metres (16.4 feet) system length,panel mount5 1 5.0 metres (16.4 feet) system length,DIN mount9 09.0 metres (29.5 feet) system length,panel mount9 19.0 metres (29.5 feet) system length,DIN mountB:Agency Approval Option0 0 No Approvals0 5Multiple Approvals3300 XL 50 mm Extension Cable 330877-AXXX-BXX-CXXNote: Make sure that the extension cable length andthe probe length, when added together, equal theProximitor Sensor total length.A:Cable Length Option0 4 0 4.0 metres (13.1 feet)0 8 08.0 metres (26.2 feet) B:Armor and Cable Option3 6FluidLoc ext cable3 7FluidLoc ext. cable w/ armorC:Agency Approval Option0 0 No Approvals0 5 Multiple ApprovalsMounting BracketsEach Sliding Mounting Bracket comes with•One sliding plate•One base plate•Sliding plate securing bolts withsafety wire holes•Lock washersThe material used for the mounting bracketsis T6061-T6 aluminum. Base platesecuring bolts are not provided;recommended bolt size is 3/8in or M8socket head bolts.3300 XL 50 mm Sliding Probe Bracket and Clamp:330879-AXX-BXXA: Probe Clamp Style0 1 Left Exit0 2 Right Exit0 3 Two clamps (used for CIDEapplications)1B: DE Mounting Bracket0 0 No Mounting Bracket; Clamp Only0 1 Single DE Mounting Bracket20 2 Short CIDE Mounting Bracket30 3 Long CIDE Mounting Bracket3This bracket is recommended for most installations. While any probe may be used, the smooth side exit probe is most often used with this bracket.1.When ordering two clamps, one right exit andone left exit clamp will be provided so that thecables exit from the same side of the CIDEbracket.2.The B01 probe mounting bracket option is onlyavailable with the A01 or A02 probe clamp styleoptions.3.The B02 and B03 probe mounting bracket optionsare only available with the A03 probe clamp styleoptions.4.When replacing 50mm DE 130713, part number330879-AA-00 should be ordered. Ordering withBB=00 will prevent unnecessary parts from beingordered with the clamp.Sliding Mounting Brackets without clamps 131071-01Single TransducerMounting Bracket 131030-01Short ComplementaryInput DifferentialExpansion (CIDE) MountingBracket131031-01Long Complementary InputDifferential Expansion(CIDE) Mounting BracketNon-sliding Mounting Brackets167285Kit, 50 mm Clamp Mount(used with smooth-caseside exit or threadedstraight exit probes). 167286Kit, 50 mm Bolt Mount(used only with smooth-case side exit probes).Verification KitsEach verification kit comes with:• a verification kit bracket• a spindle micrometer with either 0 to 2 in or0 to 50 mm range•two set screws• a bracket securing boltThe material used for the verification kit bracket isT6061-T6 aluminum.131036-01Verification Kit, SpindleMicrometer with EnglishUnits131036-02Verification Kit, SpindleMicrometer with MetricUnits Accessories173959Manual148722-013300 XL Test Plug. The 3300 XLTest Plug has three self-containedtest pins attached to three color-coded wires 1 metre in length,each terminated in a banana plug.The three-pin adapter plugs intothe test pin holes on 3300 XL-style Proximitor Sensors. It is usedto check the performance of theProximitor Sensor from the testpin holes in the terminal stripwithout requiring the removal ofthe field wiring.Extended Range Micrometer KitThe extended range micrometer kit contains a precision micrometer and a 100 mm (4 inch) AISI 4140 target and is intended for acceptance testing of Bently Nevada extended range transducers. Bracket options are available to hold 8mm – 50mm probes as well as the 50 mm Integral DE transducer.330187-AXX-BXXA:Probe options0 1 8 mm to 50 mm probe threaded orsmooth cases0 38 mm to 50 mm probe threaded orsmooth cases and an adapter for 50mm Integral DE probesB:Micrometer Option0 1 Standard English 0-2 inch micrometer0 2Standard metric 0-50 mmmicrometer02120015Bulk field wire. 1.0 mm2 (18 AWG),3 conductor, twisted, shieldedcable with drain wire. Specifylength in feet.02173009Bulk field wire. 1.0 mm2 (18 AWG),3 conductor, twisted, shieldedcable. Specify length in feet.138492-01Replacement panel-mountmounting pad138493-01Replacement DIN-mountmounting pad043103103300 XL Proximitor SensorPanel-mount Screws. Packageincludes four 6-32 UNC threadforming mounting screws(Supplied standard with 3300 XLProximitor Housings [3300 XLoption]).03200006Silicone self-fusing tape. A 9.1metre (10 yard) roll of siliconetape to protect connectors. It iseasy to install and providesexcellent electrical isolation andprotection from the environment.It is not recommended for useinside the casing of the machine. 40180-02Connector Protectors. Packagecontains 10 pairs of connectorprotectors.03839410Male Connector Protector.Placed on the extension cable toconnect to the female connectorprotector on the probe andprovide environmental protectionof connectors.03839420Female Connector Protector.Placed on the probe lead toconnect to the male connectorprotector on the extension cableand provide environmentalprotection of connectors. Alsoplaced on the extension cable toslide over the Proximitor Sensorconnection and protect it fromthe environment.330153-103300 XL 50 mm Connector Kit.Used on 3300 XL 50 mm probesand extension cables. Containsone male (removable nut) andfemale ClickLoc connectors, color-coded sleeves and two pieces slitPFA tubing.163356Connector Crimp Tool Kit.Includes one set of multi-connector inserts and connectorinstallation instructions. Suppliedwith carrying case.173873High Temperature Cable Zip-Ties. PEEK cable tie is rated foruse up to 200 C continuoustemperature. Available in bags of50 zip ties.174804-01Side Exit Probe Adapter Kit.Used to adapt side exit probes forthe 330187 Extended RangeVerification Kit.Graphs and Dimensional Drawings…Note: All dimensions on figures are in millimeters (inches) unless otherwise specified.Figure 1: Typical 3300 XL 50 mm 5 m System Over Ambient Testing RangeFigure 2: Typical 3300 XL 50 mm 9 m System Over Ambient Testing RangeFigure 3: Typical 3300 XL 50 mm Probe + 1m Cable @ Low Temperature (Proximitor Sensor+ 8m of Extension Cable @ 25 C)Figure 4: Typical 3300 XL 50 mm Probe + 1m Cable @ High Temperature (Proximitor Sensor+ 8m of Extension Cable @ 25 C)Figure 5: Typical 3300 XL 50 mm 5 m Proximitor Sensor with 4 m of Extension Cable @ ColdTemperature (Probe is at 25 C)Figure 6: Typical 3300 XL 50 mm 5 m Proximitor Sensor with 4 m Extension Cable @ HighTemperature (Probe is at 25 C)Figure 7: Typical 3300 XL 50 mm 9 m Proximitor Sensor with 8 m of Extension Cable @ LowTemperature (Probe is at 25 C)Figure 8: Typical 3300 XL 50 mm 9 m Proximitor with 8 m of Extension Cable @ HighTemperature (Probe is at 25 C.)(1) Shaft to side of probe distance.(2) Collar Height.Figure 9: Recommended Probe Position Based on Collar Height1.62.2 mm (2.45 in) maximum diameter2.3/4-in or 21 mm diameter jam nut with safety wire holes3.Case thread4.FluidLoc coaxial cable with PFA Jacket, 3.94 mm (0.155 in) maximum diameter.5.Miniature male coaxial connector, 8.0 mm (0.32 in) maximum diameter.6.Optional Stainless steel armor with PFA jacket, 9.58 mm (0.377 in) maximum diameter; 12.7 mm (0.50 in)maximum diameter of armored ferrule.Figure 10: 330876, 3300 XL 50 mm Proximity Probe, Straight Exit1.50.5 mm (1.99 in) diameter2.FluidLoc coaxial cable with PFA Jacket,3.94 mm (0.155 in) maximum diameter.3.Miniature male coaxial connector, 8.0 mm (0.32 in) maximum diameter.Figure 11: 330876, 3300 XL 50 mm Proximity Probe, Smooth 1.99 Inch Dia. Side Exit Case1.Cable length +20%, -0%2.Miniature male coaxial connector, 7.2 mm (0.29 in) maximum diameter3.Customer shrink tubing, 84 mm (3.3 in), 2 places4.Optional stainless steel armor with PFA jacket, 7.65 mm (0.301 in) maximum diameter; 10.12 mm (0.0400in) maximum diameter of armored ferrule.5.FluidLoc coaxial cable with PFA Jacket, 3.94 mm (0.155 in) maximum diameter6.Miniature female coaxial connector,7.24 mm (0.285 in) maximum diameter7.Armor Length = Cable Length – 300 mm (11.8 in)Figure 12: 330877, 3300 XL 50 mm Extension Cable5.1(0.20)Mounting Option “A” –50 or -90Figure 13: 330878 Panel Mount 3300 XL 50 mm Proximitor Sensor1.Mounting option “A” –51 or –912.35mm DIN rail (not included)3.89.4 mm (3.52 in) (additional 3.05 mm (0.120 in) required to remove DIN rail) Figure 14: 330878 DIN Mount 3300 XL 50 mm Proximitor Sensor1.10(0.40) diameter through, 15 (0.61) counterbore typicalFigure 15: 131071-01 Single Transducer Mounting Bracket1.10(0.40) diameter through, 15 (0.61) counterbore typicalFigure 16: 131030-01 Short Complementary Input Differential Expansion (CIDE) MountingBracket1. 10 (0.40) diameter through, 15 (0.61) counterbore typicalFigure 17: 131031-01 Long Complementary Input Differential Expansion (CIDE) MountingBracket1.12.7 (0.5) diameter, 2 places2.9.5 (0.37) diameterFigure 18: 131036-01 and 131036-02 Verification Kit Spindle Micrometer1.Vertical adjustments in ¼” incrementsFigure 19: 330879 Probe Clamp (330879-01 Shown)NOTE: All dimensions are in millimeters (inches) unless otherwise specified.Copyright 2006-2018 Baker Hughes, a GE c ompany, LLC (“BHGE”) A ll rights reserved.* Denotes a trademark of Bently Nevada, LLC, a wholly owned subsidiary of Baker Hughes, a GE company.All product and company names are trademarks of their respective holders.Use of the trademarks does not imply any affiliation with or endorsement by the respective owners.The information contained in this document is subject to change without prior notice.1631 Bently Parkway South, Minden, Nevada USA 89423Phone: 1-775.782.3611 。
电动汽车交流充电桩使用说明书

目 录第一章 安全说明 (2)1.1 常用符号说明 (2)1.2 禁止事项 (2)1.3 安全注意事项 (2)第二章 产品简介 (3)2.1 产品简介 (3)2.2 遵循标准 (3)2.3 型号说明 (4)2.4 技术指标 (4)2.5 外形结构 (5)第三章 安装说明 (6)3.1 搬运或移动 (6)3.2 开箱检验 (6)3.3 安装..... . (6)第四章 操作使用说明 (8)4.1 主界面.............................................................................................................. . (8)4.2 充电界面 (8)4.3 充电桩设置界面 (10)第五章 日常维护及故障处理 (14)5.1 通用故障处理流程 (14)5.2 常见故障分析和处理方法 (15)‐1‐-2-第一章 安全说明1.1 常用符号说明下面一些符号可能在本说明书中用到,也可能在您应用过程中出现。
因此,请各位用户熟悉它们,并知道其含义。
符号含义提示注意高压危险保护接地 交流直流重复循环1.2 禁止事项充电设备内部有高压,非本公司或本公司授权的技术人员,请勿擅自打开机箱盖,否则会有触电的危险,同时失去保修资格。
1.3 安全注意事项设备开通之前,请务必确认设备是否接地良好,以避免触电造成人员伤亡; 在任何情况下切勿自行改装、加装和变更任何部件;设备通电前请务必确认输入电压、频率及其他条件都已符合产品要求;为了确保本设备的使用寿命和运行稳定,本设备不得在有挥发性气体或者易燃环境下使用。
第二章产品简介2.1 产品简介EVAC系列交流充电桩是为现代电动汽车设计的符合市场需求的电动汽车充电产品,并提供友好的人机操作界面,具有相应的控制、计费和通信等功能,属于电动汽车专用交流供电装置。
广泛应用于各类家用电动汽车充电,也可应用于各种充电站、停车场、小区车库以及公共电动汽车充电场所。
CLS2容电水位传感器安装和操作指南说明书

Series CLS2 Capacitive Level SwitchSpecifications - Installation and Operating InstructionsBulletin L-26The CLS2 Capacitive Level Switch was designed to sense material level in a wide range of applications and environments using the dielectric properties of the sensed material. State of the art sensing technology in the CLS2, using impulse RF admittance measurement combined with an active guard, provides excellent level measurement and stability while being insensitive to material buildup. This technology also provides immunity to external RF sources like walkie-talkies and cell phones as well as minimal interference with radio communication or other electronic systems.The product features automatic calibration and 8 selectable sensitivity levels. Calibration may be initiated with either the internal switch or using the external calibration magnet allowing calibration without removing the cover. A selectable failsafe mode allows the relay to be active either normally open or normally closed. The unit also features an active guard mechanism that effectively eliminates the effects of material buildup on the probe. A selectable delay is provided to ensure false detection due to splashing or other tank disturbances will not cause nuisance triggering. A high brightness LED indicator is provided externally so that the level status can be easily seen even in bright sunlight. Three multicolored LEDs are provided internally for maintenance anddiagnostic use.OPERATING PRINCIPLECapacitance and DielectricsCapacitance is the property of two or more conductors to store a charge when there is a voltage difference between the conductors. In other words, capacitance relates the voltage between two conductors and the amount of charge that can be held on the conductors (i.e., the number of electrons). Capacitance is measured in Farads, but since a Farad of capacitance represents a very large charge storage capacity, most capacitance encountered is generally measured in micro Farads (µF, 10-6) or pico Farads (pF, 10-12). Capacitances encountered in level sensing applications are generally in the pico Farad range.The material between the conductors also affects the capacitance. Insulating materials do not allow free movement of electrons, however, in an electric field the molecules of these materials will tend to align with the field, thus storing energy. This is called the dielectric effect and these materials are often referred to as dielectrics. When placed between two conductors the energy storage capability of these dielectrics will allow more charge to be stored on the conductors for a given voltage difference thus increasing the capacitance between the conductors. The ratio of capacitance change caused by these dielectrics is referred to as the dielectric constant. Different materials have differing dielectric constants and will consequently change the capacitance between two conductors more or less depending on the value of this constant. This value ranges from 1.0 for a vacuum to over 100 for certain materials. The dielectric constant for air is very close to 1.0 and usually assumed to be exactly 1.0.Capacitive level sensors determine the level of material by changes in probe capacitance resulting from the movement of dielectric materials between the probe and the reference ground such as a tank wall. Since measuring very small capacitance changes (less than 1 pF) can be problematic in industrial environments, capacitance level sensing tends to be most effective for materials with a dielectric constant greater than about 1.2. Since the difference in capacitance is being measured, it is also possible to detect the level of two immiscible liquids that have different dielectricconstants such as oil and water.Level DetectionThe CLS2 uses the capacitance difference between the uncovered sensor and covered sensor to sense level such as the probe in air verses the probe in oil. This would allow, for instance, detection when the level in a tank is below a threshold and a pump must be started or when the level is above a threshold where the pump must be turned off.The CLS2 can be used in applications were the probe gets coated or covered with sticky, dusty, or clingy materials. The CLS2 has an active guard near the top that compensates for material that coats the probe preventing false alarms.When detecting level, two critical items must be established: a reference capacitance and the sensitivity. The reference capacitance is set through an automatic calibration process. The sensitivity is selected using an internal DIP switch which provides 8 sensitivity levels to accommodate differing material dielectric constants. See the calibration section for specific calibration instructions.The level detection is available to external systems through a double pole double throw (2-form C) relay. In any alarm or control system some consideration must be made for a power failure in one or more elements of the system. The CLS2 provides a fail-safe selection that allows the relay to operate in either a normally open or a normally closed state when the probe is uncovered.INSTALLATION UnpackingRemove the CLS2 from the shipping carton and inspect for damage. If damage is found, notify the carrier immediately.Mounting LocationThe CLS2 is designed to be mounted in a tank and is rated for industrial environments with few restrictions, however certain considerations must be made to ensure optimal sensing and extended operational life.• The process temperature and ambient temperature must be within the specified limits for the instrument.• Avoid locating the unit near or in high mechanical shock or vibration areas. • The probe must be located away from tank inlets or chutes where material may fall on the probe during filling or emptying.• Avoid mounting the probe close to tank structures as conductive product bridging between the guard and tank structure can cause false alarms. • In nonmetallic tanks a ground reference must generally be provided. If the probe is near the wall of the tank an adhesive backed metallic sheet may be applied to the outside of the tank wall nearest to the probe. Other metallic objects may be used also if they are in close proximity to the tank wall. If the probe is located further than 10 inches from the wall, an internal conductor must be providedparallel to and within 10 inches of the probe. These conductors must be connected to the case ground of the sensor. An external ground clamp is provided for this ifother grounding is not available.Note: Installation must be made in accordance with National Electric Code and local codes and regulations. When fishing wire through the conduit connection do not allow the wire to touch or press on components on the boards. Damage to the circuitry may result.The unit is to be wired to a switch or circuit breaker in close proximity to the unit. The switch or circuit breaker shall be marked as the disconnections device for the unit.The CLS2 has a 1/2˝ female NPT conduit connection. The conduit connection must be made such that condensation is not allowed to enter the housing.Grounding: The case of the CLS2 must be wired to a protective earth ground. This may be done by using a metal conduit or by wiring to one of the protective earth groundscrews in Figure 1 or Figure 2.The terminal block may be removed for easier connection. To remove, place a small screwdriver between the terminal block and the connector base and pry the terminal block forward. This will unlatch the block from the base allowing it to be removed. When installing the block, tip it forward on the connector base to snap it in the forward locking tab then rock the connector back onto the contacts until it snaps in place. Make sure the terminal block is securely in place.Strip 0.25˝ of insulation from the wires. Connect the power wires to terminals 1 and 2. If powered by DC, the polarity is not critical and either terminal may be selected for positive or negative. Connect control lines to the relay contact terminals (see Figure 1 for terminals). Torque terminals to 5 in-lb.Controls and Indicators (See Figure 2 and 3)Calibrate Switch —Pressing this switch twice initiates the automatic calibration process.Time Delay Potentiometer—This control selects a delay time from 0 to 60 seconds from the detection of a level change to the output.Dip Switch —This four section switch selects the sensitivity level and failsafe mode.Sensor LED —Yellow. This LED is illuminated immediately when the probe capacitance exceeds the setpoint threshold.Output LED —Red. This LED is illuminated when the relay is powered. It is affected by the failsafe setting and the delay.Power LED —Green. This LED is illuminated when the unit is powered and indicates that power is being supplied to the sensing circuitry.External LED—Red. The external LED indicator operates in conjunction with the internal Output LED.External Calibration Magnet —An external magnet is provided on the end of a chain to initiate calibration without having to open the case. Calibration is started by touching the magnet to the label target twice.Always install or service this device with the power off and whererequired install a disconnect lockout.For power line connections use NEC Class 1 wiring rated 75°C. Use 12 to 20 AWG copper only for line and load connections.Torque terminals to 5 in-lb. Strip the wires 0.25˝.Protective earthL1Figure 1: TerminalsExternal LED(YELLOW)Power LED (GREEN)(RED)Calibrate Time delay External calibration magnetProtective earthground screwFigure 2: Swiches and LED’sPrinted in U.S.A. 10/20FR# 443401-00 Rev. 9©Copyright 2020 Dwyer Instruments, Inc.Setup and Calibration1. Fail Safe Mode Selection: The relay will always be off when the power fails. In this case the contacts identified as normally open will be open. The fail safe switch selects whether the normally open contacts are open or closed when the probe is uncovered. There are two options for the failsafe condition that are selected by DIP switch S4 (see Figure 2). Selecting normally open (NO) will force the relay contacts to be open when the probe is uncovered and the output status LED to be off.Selecting normally closed (NC) will energize the relay when the probe is uncovered and light the output status LED.2. Sensitivity Selection: The sensitivity must be selected to match the dielectric constant of the material and its density. Eight sensitivity levels are provided by positioning DIP switches S1, S2, and S3 (see Figure 2). A high sensitivity setting is a low pF, and a low sensitivity setting would be a high pF. High sensitivity is used for materials such as plastic pellets, light powders, and dry grain. Mediumsensitivity is used for materials such as cement, petroleum products, and flour. Low sensitivity is used for products such as aqueous solutions. The switchpositions are summarized in Table 1. For best operation use the minimal sensitivity required for reliable operation.3. Calibration: Calibrate with the probe uncovered and the material at least 5 inches below the probe.To start the automatic calibration process press the calibrate switch twice (see Figure 2) or press the external magnet up to the housing at the marked location on the housing twice (see Figure 3). The external magnet is attached to the housing by a chain. The output status LEDs will begin to blink slowly, about once per second, when the calibration process has started. The automatic calibration will take approximately 10 to 15 seconds, and the output status LEDs will stop flashing at the end of the calibration process. If during the calibration process the tank level changes or a sensor failure has occurred, the calibration process may fail. The output status LEDs will begin to flash rapidly (about 4 times per second). Makesure the probe is uncovered and retry the calibration step.Table 1: Switch position for sensitivityFigure 3: Magnent location4. Time Delay Selection: The time delay is the programmed time between when the probe senses the material and when the relay changes state from the sensed material. A time delay of 3 seconds or greater is required to meet CE requirements. Choose a delay setting appropriate for the specific application. Adjust the delay potentiometer to the desired delay (see Figure 2). The delay can be set anywhere from 0 to 60 seconds and a scale is printed on the sensor board. For verification of delay programming the yellow sensor LED will come on when material is sensed and the red output LED will come on with the relay after the programmed time delay.5. Verify Operation: Make sure the probe is uncovered, material at least 5 inches below the probe, and that the yellow sensor LED is off. Fill the tank until thematerial is at the desired threshold level and verify that the sensor LED is illuminated. If the sensor LED turns on before the material reaches the probe, reduce the sensitivity as needed. If when the probe is covered the sensor LED is notilluminated, increase the sensitivity. Water or other conductive liquids will activate the sensor when they just contact the probe. Low density and dielectric constantmaterial may require more of the probe to be covered.Note: Default values as the product ships from the factory is a follows: S1:off, S2:off, S3:on, S4:on, and time delay off.MAINTENANCEOther than the controls mentioned in this manual there are no user maintenance adjustments or routine servicing required for this product. Very heavy buildup on the probe may ultimately reduce sensitivity. Moderate buildup is compensated for by the active guard.The Series CLS2 Capacitive Level Switch is not field serviceable and should be returned if repair is needed (field repair should not be attempted and may void warranty). Be sure to include a brief description of the problem plus any relevant application notes. Contact customer service to receive a return goods authorization (RGA) number before shipping.When the CLS2 with a Sanitary Process Connection is to be used in a sanitary or hygienic application, the unit must be cleaned and/or sanitized in accordance with appropriate guidelines prior to installation. The CLS2 with a Sanitary ProcessConnection is suitable for “Clean In Place” methods.Explanation of Symbols:。
康明斯伟力柴油发电机组操作与保养手册
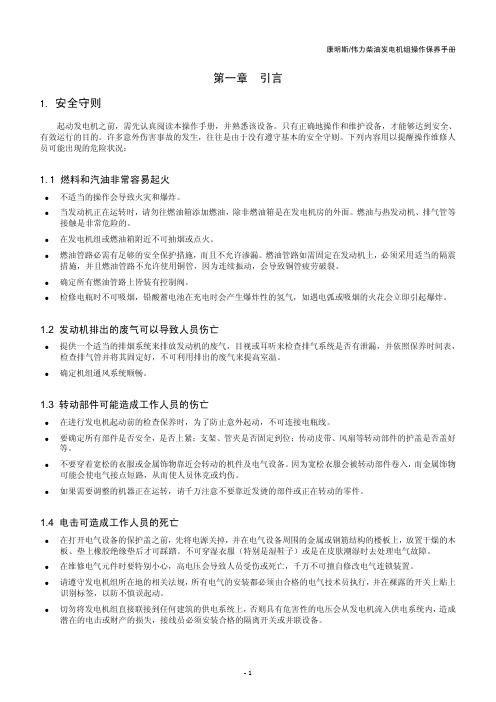
康明斯/伟力柴油发电机组操作保养手册
图标
定义 停机/复位 Stop/Reset 自动/Auto
手动/Manual
说明 停止发电机组运转;对任何警告进行复位。 当远程起动信号有效时,自动起动发电机组。 用手动方式控制发电机组的起动。
公共报警/Common Alarm
模拟主电源失效(测试) Mains Failure Simulation (Test) 警报消音/Alarm Mute
措施,并且燃油管路不允许使用铜管,因为连续振动,会导致铜管疲劳破裂。 z 确定所有燃油管路上皆装有控制阀。 z 检修电瓶时不可吸烟,铅酸蓄电池在充电时会产生爆炸性的氢气,如遇电弧或吸烟的火花会立即引起爆炸。
1.2 发动机排出的废气可以导致人员伤亡
z 提供一个适当的排烟系统来排放发动机的废气,目视或耳听来检查排气系统是否有泄漏,并依照保养时间表, 检查排气管并将其固定好,不可利用排出的废气来提高室温。
检测到任何一个故障信号 (警告 = 稳定, 停机 = 闪烁) 对于自动电源失效控制器来说,用于模拟市电失效状态(带 载测试)。
消除报警系统发声装置
试验灯光/Lamp Test
发动机仪表 Engine Instruments
发电机仪表 Generator Instruments
市电仪表 Mains Instruments
z 在维修电气元件时要特别小心,高电压会导致人员受伤或死亡,千万不可擅自修改电气连锁装置。 z 请遵守发电机组所在地的相关法规,所有电气的安装都必须由合格的电气技术员执行,并在裸露的开关上贴上
识别标签,以防不慎误起动。 z 切勿将发电机组直接联接到任何建筑的供电系统上,否则具有危害性的电压会从发电机流入供电系统内,造成
总线防盗报警控制器-大华

使用,但是却会导致系统自动的转发相应端口的数据,从而导致本应该受限的数据被他人窃 取。 如果已在路由器上手工打开了 HTTP 和 TCP 端口映射,我们强烈建议您关闭此功能。在实际 的使用场景中,我们强烈建议您不开启此功能。
电源要求
请务必按照要求使用电池,否则可能导致电池起火、爆炸或燃烧的危险! 更换电池时只能使用同样类型的电池! 产品必须使用本地区推荐使用的电线组件(电源线),并在其额定规格内使用。 请使用满足 SELV(安全超低电压)要求的电源,并按照 IEC60950-1 符合 Limited Power
部分老版本的 IP 摄像机固件,系统的主密码更改后,ONVIF 密码不会自动跟着更改。你需要更 新摄像机的固件或者手动更新 ONVIF 密码。 6. 只转发必须使用的端口 只转发必须使用的网络端口。避免转发一段很长的端口区。不要把设备的 IP 地址设置成 DMZ。 如果摄像机是连接到本地的 NVR,你不需要为每一台摄像机转发端口,只有 NVR 的端口需
在适用法律未明令禁止的程度下,对于因使用或无法使用本产品或服务而引起的任何利润、 收入、销售损失、数据丢失或采购替代商品或服务的成本、财产损害、人身伤害、业务中断、 商业信息损失,或者任何特殊的、直接的、间接的、附带的、经济性、覆盖性、惩罚性、特 殊或从属损害,无论是基于何种责任理论(合同、侵权、过失或其他),本公司及其员工、 许可方或附属公司都不承担赔偿责任,即使其已被告知存在此种损害的可能性也是如此。某 些司法管辖区不允许对人身伤害、附带或从属损害等进行责任限制,则此限制可能不适用于 您。
要被转发。 7. 关闭 SmartPSS 的自动登录功能 如果你使用 SmartPSS 来监控你的系统而你的电脑是有多个用户,请必须把自动登录功能关闭。 增加一道防线来防止未经授权的人访问系统。 8. 在 SmartPSS 上使用不同于其他设备的用户名和密码 万一你的社交媒体账户,银行,电邮等账户信息被泄漏,获得这些账户信息的人也无法入侵你的 视频监控系统。 9. 限制普通账户的权限 如果你的系统是为多个用户服务的,请确保每一个用户只获得它的作业中必须的权限。
低压开关柜技术规范.

80×8
630KVA 变压器
4
2500
2×(100×10)
100×10
800KVA 变压器
注:1.铜母排横截面应为直角矩形。
2.表中铜母线规格为建议值,供货厂家如选用以上规格或选用其它规格替代,应提供相关型式试验报
告。
13)母线相色参见表 3。 表 3 电工成套装置中的母线相色
标准参数值共用参数主要电气参数额定工作电压400v额定绝缘电压660v额定耐受电压2500v1min工频水平母线额定电流项目单位提供母线3lnpe标准参数值额定短时耐受电流65ka1s额定峰值耐受电流供货方提供防护等级ip31进线柜断路器型式框架断路器3p额定工作电压660v额定电流项目单位提供额定极限分断能力65ka框架断路器额定运行分断能力65ka框架断路器额定绝缘电压1000v框架断路器额定冲击耐受电压12kv框架断路器机械寿命免维护10000进线柜断路器电气寿命6000电流互感器精度05项目单位提供多功能数显表有功10无功20通信接口rs485标准接口通信规约dlt6451997尺寸宽度mm800深度mm1000高度mm2200浪涌保护器保护类型iec类别400v最大持续工作电压供货方提供标称放电电流820us100ka电压保护水平kv供货方提供进线方式侧进线母线上进线供货前与项目单位确认分段柜断路器型式框架断路器3p额定工作电压660v额定电流800a1250aa2500a额定极限分断能力65ka框架断路器额定运行分断能力65ka框架断路器额定绝缘电压1000v框架断路器额定冲击耐受电压12kv框架断路器标准参数值机械寿命免维护10000电气寿命6000电流互感器精度05项目单位提供多功能数显表有功10无功20通信接口rs485标准接口通信规约dlt6451997双电源切换装置ats4p额定电流63a分段柜熔断器3p额定电流100a微型断路器3p额定电流16a63a尺寸宽度mm800深度mm1000高度mm2200出线方式侧出线母线上出线供货前与项目单位确认馈线柜垂直母线额定电流1000a额定短时耐受电流50ka1s额定峰值耐受电流供货方提供断路器出线配置项目单位提供型式塑壳断路器电子脱扣3p额定工作电压400v塑壳断路器额定电流项目单位提供额定极限分断能力50ka塑壳断路器额定运行分断能力50ka塑壳断路器额定绝缘电压660v塑壳断路器额定冲击耐受电压8kv塑壳断路器机械寿命免维护10000电气寿命7000塑壳断路器是否带失压脱扣器电流互感器精度05标准参数值电流表三相数显式柜体尺寸宽度mm600深度mm1000高度mm2200使用环境条件表使用环境条件见表5
印度马克CLS50 CLS50D电磁导电度传感器说明书
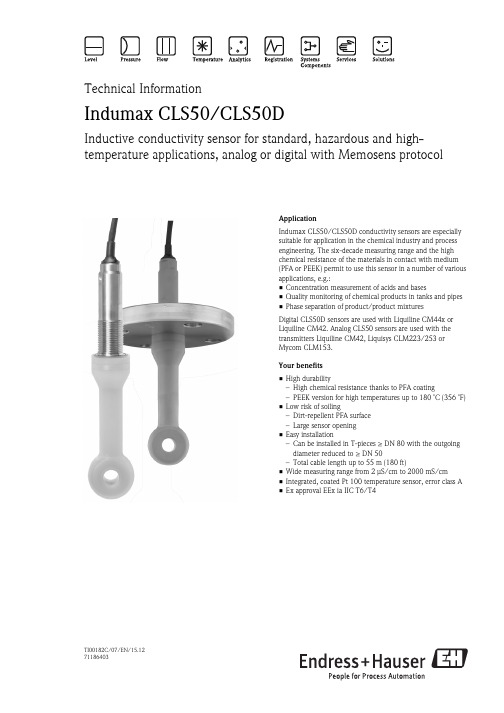
TI00182C/07/EN/15.1271186403Technical InformationIndumax CLS50/CLS50DInductive conductivity sensor for standard, hazardous and high-temperature applications, analog or digital with Memosens protocolApplicationIndumax CLS50/CLS50D conductivity sensors are especially suitable for application in the chemical industry and process engineering. The six-decade measuring range and the high chemical resistance of the materials in contact with medium (PFA or PEEK) permit to use this sensor in a number of various applications, e.g.:•Concentration measurement of acids and bases•Quality monitoring of chemical products in tanks and pipes •Phase separation of product/product mixturesDigital CLS50D sensors are used with Liquiline CM44x or Liquiline CM42. Analog CLS50 sensors are used with the transmitters Liquiline CM42, Liquisys CLM223/253 or Mycom CLM153.Your benefits•High durability–High chemical resistance thanks to PFA coating–PEEK version for high temperatures up to 180˚C (356˚F)•Low risk of soiling–Dirt-repellent PFA surface –Large sensor opening •Easy installation–Can be installed in T-pieces ≥DN 80 with the outgoing diameter reduced to ≥DN 50–Total cable length up to 55m (180ft)•Wide measuring range from 2 μS/cm to 2000mS/cm •Integrated, coated Pt 100 temperature sensor, error class A •Ex approval EEx ia IIC T6/T4Indumax CLS50/CLS50D2Endress+HauserFunction and system designMeasuring principleInductive conductivity measurementA generator (1) generates an alternating magnetic field in the primary coil (2) which induces a current in the medium (3). The strength of the induced current depends on the conductivity and thus the ion concentration of the medium. The current flow in the medium generates another magnetic field in the secondary coil (4). The resulting current induced in the coil is measured by the receiver (5) and processed to determine the conductivity.Important properties•Wide measuring rangeThe sensor’s measuring range comprises six decades, from 2 μS/cm to 2000 mS/cm.•DurabilityThe materials in contact with medium (PEEK, PFA) feature a very high chemical resistance. In addition, the PEEK version is suitable for application at high temperatures (CLS50 up to 180˚C (356 ˚F) and CLS50D up to 125 ˚C (260 ˚F)).•Low risk of soilingThanks to its large opening, the sensor is not susceptible to soiling. The PFA version requires even less cleaning thanks to its dirt-repellent surface.Advantages of digital sensors with Memosens protocol (CLS50D only)Digital sensors are able to store the following system data in the sensor:•Manufacturing data –Serial number –Order code–Date of manufacture •Calibration data –Calibration date –Cell constant–Change in cell constant –Number of calibrations–Serial number of the transmitter used for the last calibration •Application data–Temperature application range –Conductivity application range –Date of first commissioning –Maximum temperature value–Operating hours at high temperaturesInductive conductivity measurement 12345Generator Primary coilCurrent flow in the medium Secondary coil ReceiverBenefits of inductive conductivity measurement •No electrodes, therefore no polarization•Accurate measurement in media or solutions with a high soiling degree and a tendency to deposition •Complete galvanic separation of measurement and mediumIndumax CLS50/CLS50DMeasuring system CLS50DA complete measuring system comprises:•a CLS50D conductivity sensor with fixed cable•a transmitter, e.g. Liquiline CM44xOptional:•Weather protection cover for the field installation of the transmitter•Assembly for sensor installation in tanks or in pipework, e.g. CLA111Example of a measuring system1Transmitter Liquiline CM44x2Weather protection cover3Pipe socket for flange DN50 PN/64Sensor CLS50D, flange version DN50 PN/6, fixed cable with M12 plugEndress+Hauser3Indumax CLS50/CLS50D4Endress+HauserCLS50A complete measuring system comprises:•a CLS50 conductivity sensor with fixed cable •a transmitter, e.g. Liquiline CM42Optional:•Weather protection cover for the field installation of the transmitter •Assembly for sensor installation in tanks or in pipework, e.g. CLA111Example of a measuring system 1Indumax CLS502Liquiline CM42 transmitter 3Weather protection cover 4Pipework 5Pipe socketInputMeasured variable•Conductivity •Temperature Cell constant k = 1.98 cm –1Measuring frequency 2 kHzMeasuring rangeTemperature measurementCLS50DPt 1000 (class A acc. to IEC 60751)CLS50Pt 100 (class A acc. to IEC 60751)Conductivity: 2 μS/cm to 2000 mS/cm (uncompensated)Temperature:–20 to +180 ˚C (-4 to +350 ˚F)Indumax CLS50/CLS50DEndress+Hauser 5WiringCable specificationThe sensor is supplied with a fixed cable. The connection to the transmitter can be extended using the CYK81 (CLS50D) or the CLK5 (CLS50) special measuring cable.Please note that the residual coupling increases when the cable is extended.Performance characteristicsMaximum measured error•-20 to 100 ˚C (-4 to 212 ˚F):±(5 μS/cm + 0.5 % of the measured value)•> 100 ˚C (212˚F):±(10 μS/cm + 0.5 % of the measured value)Temperature response time•PEEK versions:approx. 7 min •PFA versions:approx. 11minInstallation conditionsInstallation positionInstall the sensor in such a way that the sensor opening is oriented in the flow direction of the medium. The sensor head must be completely immersed in the medium.a0007035Installation position of the sensor 1Flow direction of medium2Minimum water level in the pipe aSensor distance from the pipe wallCYK81 for cable extension for CLS50D –max. total cable length: 100 m (330 ft)CLK5 for cable extension for CLS50–max. total cable length: 55 m (180 ft)Indumax CLS50/CLS50D6Endress+HauserInstallation factorIn narrow installation conditions, the conductivity measurement is affected by the pipe walls. This effect is compensated by the so-called installation factor. The transmitter corrects the cell constant by multiplication with the installation factor.The value of the installation factor depends on the diameter and the conductivity of the pipe as well as the sensor’s distance from the wall.If the distance from the wall is sufficient (a > 15mm (0.59"), from DN 80), it is not necessary to consider the installation factor (f = 1.00).If the distance from the wall is smaller, the installation factor increases in case of electrically insulating pipes (f >1) and decreases in case of electrically conductive pipes (f <1).The installation factor can be measured using calibration solutions or it can be approximately determined from the following diagram.a0005441Relationship between installation factor f and distance from wall a1Electrically conductive pipe wall 2Insulating pipe wallAir setCLS50To compensate residual coupling in the cable and between the two sensor coils, you must perform a zero calibration in air ("air set") before installing the sensor.For further information, refer to the Operating Instructions of your transmitter.CLS50DThe digital sensor is already adjusted at the factory, an on-side compensation is not necessary.Indumax CLS50/CLS50DEndress+Hauser 7Installation of sensors with flangeThe sensor is suitable for installation in T-pieces ≥DN 80 with the outgoing diameter reduced to ≥DN 50.WARNING!LeakagesDanger of injuries by leaking medium►Tighten the nut with a torque of 20 Nm.►To avoid leakages, regularly check the tightness of the nut.Flange, not in contact with mediumFlange, in contact with mediumFixed flange, not in contact with medium (order option "process connection": 5, 6, 7)123Flange (stainless steel)NutSealing disk (GYLON)45O-ring SensorFixed flange, in contact with medium (order option "process connection": 3, 4)12Flange (stainless steel)Nut 34O-ring SensorIndumax CLS50/CLS50D8Endress+HauserLap-joint flange, not in contact with mediumInstallation of sensor assemblyEnvironmentAmbient temperature rangeCLS50D–10 to +60 ˚C (+10 to +140 ˚F)CLS50–10 to +70 ˚C (+10 to +160 ˚F)Storage temperature –20 to +80 ˚C (-4 to +180 ˚F)Ingress protectionIP 68 / NEMA 6 (installed with original sealing)Lap-joint flange, not in contact with medium (order option "process connection": A, B, C)123Lap-joint flange (PP-GF)Nut (stainless steel)Flange (PVDF)45O-ring SensorInstallation of sensor with assembly12CLA111 with suspension bracket CLA111 with flange connection 34CLA140 with flange connection CYA611Indumax CLS50/CLS50DEndress+Hauser 9ProcessProcess temperatureCLS50DCLS50Process pressure max. 20 bar (290 psi), acc. to the sensor version, see pressure-temperature diagramPressure-temperature diagramWithout flangeDN50, ANSI 2"JIS PVDF lap-joint flange Sensor CLS50D-*1/2CLS50D-*3/4/5/6/8CLS50D-*7CLS50D-*A/B/C PEEK –20 to 125 °C (-4 to 260 °F)–20 to 125 °C (-4 to 260 °F)–20 to 125 °C (-4 to 260 °F)–20 to 125 °C (-4 to 260 °F)PFA–20 to 110 °C (-4 to 230 °F)–20 to 125 °C (-4 to 260 °F)–20 to 125 °C (-4 to 260 °F)–20 to 125 °C (-4 to 260 °F)Without flangeDN50, ANSI 2"JIS PVDF lap-joint flange Sensor CLS50-*1/2CLS50-*3/4/5/6/8CLS50-*7CLS50-*A/B/C PEEK –20 to 180 °C (-4 to 360 °F)–20 to 180 °C (-4 to 360 °F)–20 to 180 °C (-4 to 360 °F)–20 to 125 °C (-4 to 260 °F)PFA–20 to 125 °C (-4 to 260 °F)–20 to 125 °C (-4 to 260 °F)–20 to 125 °C (-4 to 260 °F)–20 to 125 °C (-4 to 260 °F)Pressure-temperature-diagram of CLS50D 1PEEK sensor, without flange2PFA sensor, without flange (blue line)3PEEK or PFA sensor, with DN50/ANSI 2" flange (red line)4PEEK or PFA sensor, with JIS flange5PEEK or PFA sensor, with lap-joint flange PVDF (green line)Indumax CLS50/CLS50D10Endress+HauserMechanical constructionSensor dimensionsPressure-temperature-diagram of CLS501PEEK sensor, without flange2PFA sensor, without flange or with DN50/ANSI 2" flange (blue line)3PEEK sensor, with DN50/ANSI 2" flange (red line)4PFA sensor, with JIS flange (black line)5PEEK or PFA sensor, with lap-joint flange PVDF (green line)6PEEK sensor, with JIS flange (grey line)Dimensions of sensor version with G ¾ thread *Dimensions of PEEK versionDimensions of sensor version with NPT 1" threadIndumax CLS50/CLS50DEndress+Hauser 11Flange dimensionsFlange dimensions 1Lap-joint flange (PP-GF)2Fixed flange (stainless steel)Weight approx. 650 g (1.43 lbs)MaterialLap-joint flange PP-GF DN50 PN10ANSI 2" 150 lbs JIS 10K 50A D 165165152Ø k 125121120d 2 4 x 188 x 19 4 x 19b 181818a 787878ScrewsM16M16M16Fixed flange SS 316 L DN50 PN16ANSI 2" 300 lbs JIS 10K 50A D 165165.1155Ø k 125127120d 2 4 x 188 x 19 4 x 19b 1822.216a 272727ScrewsM16M16M16Sensor:PEEK, PFA (depending on ordered version)Sensor seal:VITON, CHEMRAZ (depending on ordered version)Process connections:G ¾:CLS50-**A: stainless steel 1.4571 (AISI 316Ti)CLS50-**B/C: PEEK GF30CLS50D-**D: stainless steel 1.4571 (AISI 316Ti)CLS50D-**B/C: PEEK GF30NPT 1":PEEK Fixed flange:stainless steel 1.4404 (AISI 316 L)Sealing disk:GYLON (ceramic-filled PTFE)Lap-joint flange:PP-GF Flange combined with lap-joint flange:PVDFIndumax CLS50/CLS50D12Endress+HauserChemical durabilityNo responsibility is taken for the correctness of this information.Ordering informationProduct pageYou can create a complete and valid order code by using the configurator on the internet product page.Enter the following address to access the product page://cls50dOnline configurator1.2.Click "Configure this product".3.The configurator opens in a separate window. You can now configure your device and receive the complete order code that applies for the device.4.Afterwards, export the order code as a PDF or Excel file. To do so, click the appropriate button at the top of the page.Medium Concentration PEEK PFA CHEMRAZ VITONSodium hydroxide solution NaOH0 to 50%20 to 100 ˚C (68to 212 ˚F)not suitable 0 to 150 ˚C (32to 302˚F)not suitable Nitric acid HNO 30 to 10 %20 to 100 ˚C (68to 212 ˚F)20 to 80 ˚C (68to 176 ˚F)0 to 150 ˚C (32to 302˚F)0 to 120˚C (32to 248˚F)0 to 40 %20 ˚C (68 ˚F)20 to 60 ˚C (68to 140 ˚F)0 to 150 ˚C (32to 302˚F)0 to 120˚C (32to 248˚F)Phosphoric acid H 3PO 40 to 80 %20 to 100 ˚C (68to 212 ˚F)20 to 60 ˚C (68to 140 ˚F)0 to 150 ˚C (32to 302˚F)0 to 120˚C (32to 248˚F)Sulphuric acid H 2SO 40 to 2.5 %20 to 80 ˚C (68to 176 ˚F)20 to 100 ˚C (68to 212 ˚F)0 to 150 ˚C (32to 302˚F)0 to 120˚C (32to 248˚F)0 to 30 %20 ˚C (68 ˚F)20 to 100 ˚C (68to 212 ˚F)0 to 150 ˚C (32to 302˚F)0 to 120˚C (32to 248˚F)Hydrochloric acid HCl0 to 5 %20 to 100 ˚C (68to 212 ˚F)20 to 80 ˚C (68to 176 ˚F)0 to 150 ˚C (32to 302˚F)0 to 120˚C (32to 248˚F)0 to 10 %20 to 100 ˚C (68to 212 ˚F)20 to 80 ˚C (68to 176 ˚F)0 to 150 ˚C (32to 302˚F)0 to 120˚C (32to 248˚F)Indumax CLS50/CLS50DEndress+Hauser 13Product structureThe following product structure represents the status of printing. You can create a complete and valid order code on the Internet using the configurator tool.CLS50DApprovalAA Non-hazardous areaBA ATEX II 1G Ex ia IIC T3/T4/T6BV ATEX II 3G Ex nL IIC T4/T6 + NEPSI Ex nL IIC T4/T6C2CSA IS NI Cl . I, II, III, Div. 1&2, Group A-G FB FM IS NI Cl . I, II, III, Div. 1&2, Group A-G NANEPSI Ex ia IIC T4/T6Process connectionA Lap joint flange DN 50 PN 10, PP-GFB Lap joint flange ANSI 2" 150 lbs, PP-GFC Lap joint flange JIS 10 K 50 A, PP-GF 1Thread G ¾2Thread NPT 1", PEEK3Flange DN 50 PN 16, stainless steel 1.4404 (AISI 316 L)4Flange ANSI 2" 300 lbs, stainless steel 1.4404 (AISI 316 L)5Flange DN 50 PN 16, stainless steel 1.4404 (AISI 316 L), PTFE sealing disk 6Flange ANSI 2" 300 lbs, stainless steel 1.4404 (AISI 316 L), PTFE sealing disk 7Flange JIS 10 K 50 A, stainless steel 1.4404 (AISI 316 L), PTFE sealing disk8Flange DN 50 PN 16, stainless steel 1.4404 (AISI 316 L), welded PFA sealing plate sensorMaterial: sensor , seal, adapterB PEEK, VITON, PEEKC PEEK , CHEMZRAZ, PEEKDPFA, CHEMRAZ, stainless steel 1.4571 (AISI 316 Ti)Cable length1 3 m (9.84 ft)27 m (23 ft) 315 m (49 ft)7... m fixed cable, max. 50 m 8... ft fixed cable, max. 164 ftCable connection1Fixed cable, terminated cable cores 2Fixed cable, M12 plug CLS50D-order codeCalibration (single choice only)F1Cell constantDienstleistung (multiple choice possible)HCLABS free (LABS = paint-wetting impairment substances)TAG (multiple choice possible)1TAG, see additional specification 2Feldbus TAGIndumax CLS50/CLS50DCLS50ApprovalA Non-hazardous areaG ATEX II 1G Ex ia IIC T4/T6 GaH NEPSI Ex ia IIC T4/T6L Non-hazardous area, PWIS freeO FM IS NI Cl . I, II, III, Div. 1&2, Group A-GS CSA IS NI Cl . I, II, III, Div. 1&2, Group A-GT TIISV ATEX II 3G Ex nL IIC T4/T6 + NEPSI Ex nL IIC T4/T6Process connectionA Lap joint flange DN 50 PN 10, PVDFB Lap joint flange ANSI 2" 150 lbs, PVDFC Lap joint flange JIS 10 K 50 A, PVDF1Thread G¾2Thread NPT 1", PEEK3Flange DN 50 PN 16, stainless steel 1.4404 (AISI 316 L)4Flange ANSI 2" 300 lbs, stainless steel 1.4404 (AISI 316 L)5Flange DN 50 PN 16, stainless steel 1.4404 (AISI 316 L), PTFE sealing disk6Flange ANSI 2" 300 lbs, stainless steel 1.4404 (AISI 316 L), PTFE sealing disk7Flange JIS 10 K 50 A, stainless steel 1.4404 (AISI 316 L), PTFE sealing disk8Flange DN 50 PN 16, stainless steel 1.4404 (AISI 316 L), welded PFA sealing plate sensorMaterial: sensor, seal, adapterA PFA, CHEMRAZ, stainless steel 1.4571 (AISI 316 Ti)B PEEK, VITON, PEEKC PEEK , CHEMZRAZ, PEEKCable length and temperature range1 5 m (16 ft) fixed cable, max. 125 ˚C (257 ˚F)210 m (32 ft) fixed cable, max. 125 ˚C (257 ˚F)320 m (65 ft) fixed cable, max. 125 ˚C (257 ˚F)4fixed cable of specific length, max. 55 m (180 ft), max. 125 ˚C (257 ˚F)5 5 m (16 ft) fixed cable, max. 180 ˚C (356 ˚F) (PEEK only, version for non-hazardous areas only)610 m (32 ft) fixed cable, max. 180 ˚C (356 ˚F) (PEEK only, version for non-hazardous areas only)CLS50-complete order codeCertificates and approvalsEx approvals CLS50D•ATEX II 1G Ex ia IIC T4/T6 GaCLS50•ATEX II 1G Ex ia IIC T4/T6 Ga•ATEX II 3G Ex nL IIC T4/T6 + NEPSI Ex nL IIC T4/T6•FM/CSA IS NI Cl. I, II, III, Div. 1 & 2; Group A - G in connection with a Liquiline CM42 or MycomCLM153 transmitter•NEPSI Ex ia IIC T4/T614Endress+HauserIndumax CLS50/CLS50DAccessoriesMeasuring cables For CLS50DCYK11 Memosens data cable•Extension cable for digital sensors with Memosens protocol•Ordering as per product structure (--> Online configurator, /cyk11)For CLS50Extension cable CLK6•For inductive conductivity sensors, for extension via the VBM junction box, sold by the meter•Order no.: 71183688Junction box VBM•For cable extension•10 terminals•Cable entries: 2 x Pg 13.5 or 2 x NPT ½"•Material: aluminum•Ingress protection: IP 65 (i NEMA 4X)•Order numbers:–cable entries Pg 13.5: 50003987–cable entries NPT ½": 51500177Assemblies Dipfit CLA111•Immersion assembly for open and closed tanks with flange DN 100•Ordering acc. to product structure, --> online configurator: /cla111•Technical Information TI00135C/07/ENDipfit CLA140•For the inductive sensors CLS50/CLS50D•Immersion assembly with flange connection for highly demanding processes•Ordering acc. to product structure, --> online configurator: /cla140•Technical Information TI00196C/07/ENImmersion assembly Dipfit CYA611•For sensor immersion in basins, open channels and tanks, PVC•Ordering acc. to product structure, --> online configurator: /cya611•Technical Information TI00166C/07/ENCalibration solutions Precision solutions, traceable to SRM (standard reference material) by NIST, for qualified calibration ofconductivity measurement systems according to ISO 9000, with temperature table•CLY11-B149.6 μS/cm (reference temperature 25 ˚C / 77 ˚F), 500 ml / 16.9 fl.ozOrder no. 50081903•CLY11-C1.406 mS/cm (reference temperature 25 ˚C / 77 ˚F), 500 ml / 16.9 fl.ozOrder no. 50081904•CLY11-D12.64 mS/cm (reference temperature 25 ˚C/ 77 ˚F), 500 ml / 16.9 fl.ozOrder no. 50081905•CLY11-E107.0 mS/cm (reference temperature 25 ˚C / 77 ˚F), 500 ml / 16.9 fl.ozOrder no. 50081906Endress+Hauser15TI00182C/07/EN/15.12 71186403FM9。
星光机 V-1用户手册说明书

星光机目录1前言 (1)1.1包装内容 (1)1.2包装开拆 (1)1.3标识符号 (1)1.4免责声明 (1)1.5安全须知 (1)1.5.1个人安全 (2)1.5.2安装和装配 (2)1.5.3电源和接线 (2)1.5.4操作 (2)2产品介绍 (3)2.1产品描述 (3)2.2产品特点 (3)2.3外观概述 (3)2.4机器尺寸 (4)3技术参数 (4)4设定安装 (5)4.1交流电源 (5)4.2交流插头 (5)4.3复位过载保护器 (5)4.4DMX连接 (6)4.5安装 (6)4.5.1方位 (6)4.5.2装配 (6)5操作机器 (6)5.1准备工作 (6)5.2机身控制面板 (6)5.3机身控制模式及操作 (6)5.3.1操作指导 (6)5.3.2菜单页面 (7)5.4DMX控制模式及操作 (8)5.4.1起始地址 (8)5.4.2DMX模式菜单页面 (8)5.4.3DMX通道设置和数值 (9)5.5喷花高度与喷花密度的关系 (9)5.6运行时间 (9)5.6.1查询运行时间 (9)5.6.2运行时间耗尽 (10)5.7高级设定页面 (10)5.7.1进入和退出高级设定页面 (10)5.7.2高级设定菜单页面 (10)6星光粉 (10)6.1识别和激活星光粉 (10)6.2添加星光粉 (11)6.3星光粉注意事项 (11)7技术信息 (11)7.1机器维护 (11)7.2储存 (11)7.2.1机器储存 (11)7.2.2星光粉储存和回收 (11)7.3一般故障 (12)7.3.1故障描述 (12)7.3.2故障菜单页面 (12)11前言1.1包装内容1.2 包装开拆收到机器后,请小心拆开包装箱,检查所有内容,以确保所有零配件都齐全并处于良好的状态。
如果外包装及任何部件因运输过程出现损坏或缺少,请立即联络承运商或经销商,并以原包装退回。
1.3标识符号符号含义注意关于安装,配置或操作的关键信息。
海利尔C7130A,B墙面挂载空气温度传感器说明书

® U.S. Registered TrademarkCopyright © 2000 Honeywell • All Rights Reserved INSTALLATION INSTRUCTIONS63-2044-2C7130A,B Wall-MountAir Temperature SensorsAPPLICATIONThe C7130A,B Wall-Mount Air Temperature Sensors provide the input required by the R7380J,L, W7100,W7600, W7620, and Excel 500 Control Systems to sense air temperature in indoor spaces. SPECIFICATIONSIMPORTANT:The specifications given in this publication donot include normal manufacturing tolerances.Therefore, this unit may not exactly match thelisted specifications. Also, this product is testedand calibrated under closely controlledconditions and some minor differences inperformance can be expected if thoseconditions are changed.Models:C7130A Wall-mount Temperature Sensor: Intended for use as an indoor air sensor with the R7380J,LIndicating Controller, the W7100 Discharge Controller, the W7600 Direct Digital Controller, and the W7620 Direct Digital Controller.C7130B Wall-mount Temperature Sensor: Intended for use as an indoor air sensor with the Excel 500Controller.Dimensions: See Fig. 1.Mounting Arrangement: Two holes provided in base of device for mounting onto wall or horizontal 2 in. by4in. [51 by 102 mm] junction box.Sensing Element:C7130A: Platinum thick film element on a ceramic base. C7130B: Platinum thin film element on a ceramic base.Resistance/Temperature:C7130A:Nominal Resistance: 3484 ohms at 77° F [25° C].Nominal Sensitivity: 4.8 ohms per degree F[8.6 ohms per degree C].C7130B:Nominal Resistance: 1097 ohms at 77° F [25° C].Nominal Sensitivity: 2.1 ohms per degree F[3.9 ohms per degree C].Maximum Ambient Temperature: 150°F [66°C]. Operating Temperature Range:-40° F to 100° F [-40° C to +38° C].Cable Length: Maximum 300 ft [91 m].Accessories:Shielded Cable: Optional for wiring to the controller at distances greater than 50 ft [15 m] to prevent possible electrical noise from causing erratic sensing.4074CAV: 50 ft [15 m].4074CAW: 100 ft [30.4 m].4074CAY: 200 ft [61 m].Fig. 1. C7130A,B Wall-Mount TemperatureSensor dimensions in in. [mm].M178502-13/16(71)1-3/8(35)5/8 (17)5/8 (17)4-5/8(118)1-3/8(35)C7130A,B WALL-MOUNT AIR TEMPERATURE SENSORS63-2044—22INSTALLATIONWhen Installing this Product...1.Read these instructions carefully. Failure to follow them could damage the product or cause a hazardous condition.2.Check the ratings given in the instructions and on the product to make sure the product is suitable for your application.3.Installer must be a trained, experienced service technician.4.After installation is complete, check out product operation as provided in these instructions.IMPORTANTAll wiring must agree with applicable codes, ordinances and regulations.CAUTIONElectrical Shock or Equipment Damage Hazard.Can shock individuals or short equipment circuitry.Disconnect power supply before installation.Mounting And LocationMount the C7130 Wall-mount Temperature Sensor where the thermostat setting will not be subjected to tampering:1.Choose a location for the sensor on an insidewall about 5 ft [1.5 m] above the floor. A horizontally mounted standard 2 in. by 4 in. [51 mm by 102 mm] junction box may also be used at the selected location for the C7130.2.Place the sensor 300 ft [91 m] or less from thecontroller.3.Make sure that there is good air circulation ataverage temperature at the chosen location. Avoid the following locations because they can introduce errors in sensor measurements (see Fig. 2):—Hot areas caused by:Concealed pipes or ducts.Drafts from fireplaces or other heat sources.Convection or radiant heat from the sun or electrical equipment.—Cold areas caused by:Concealed pipes or ducts.Drafts from windows and doors.Unheated areas on the other side of the wall location.—Dead air areas:Behind doors, furniture, and curtains.In corners and alcoves.4.Mark the area on the wall where the C7130 Sensoror junction box will be mounted.Fig. 2. C7130 mounting location.WiringCAUTIONErratic System Operation Hazard.Failure to follow proper wiring practices can introduce disruptive electrical interference (noise).Keep wiring at least one foot away from large inductive loads such as motors line starters, lighting ballasts, and large power distribution panels.Shielded cable is required in installations where these guidelines cannot be met.Ground shield only to grounded controller case.IMPORTANT1.All wiring must agree with applicable codes, ordinances and regulations.2.Do not mount sensor in incorrect environment.3.Wire according to the applicable controller instructions.4.Avoid poor wiring connections.5.Avoid intermittent or missing building earth ground.Disconnect the power supply before connecting thewiring to prevent electrical shock or equipment damage. Wiring must comply with applicable codes, ordinances and regulations.Wire the C7130 Sensor to the temperature controller using the procedure in the controller instructions. For an example of general wiring of the C7130, see Fig. 3.Mount the C7130 to the wall or to the junction box.M9175C7130A,B WALL-MOUNT AIR TEMPERATURE SENSORS363-2044—2Fig. 3. General wiring hookup for C7130A sensor to R7380 Controller.CABLE SHIELD( 2-WIRE SHIELDED RECOMMENDED FOR RUNS OVER 50 FT . (15M)R7380CONTROLLER SENSOR24V POWER GROUNDGREENBLACK BLACKEARTH GROUNDDO NOT CONNECT SHIELD AT C7130A24 VAC2211BACKSIDE OF C7130A SENSOR24 VAC SUPPLY. DO NOT GROUND ANY 24 VAC LEADS.GROUND SHIELD OF SENSOR WIRING AT EARTH GROUND AT THE CONTROL ONLY. DO NOT GROUND AT SENSOR.M1098463-2044—2 B.B. Rev. 12-00 Printed in U.S.A. on recycled paper containing at least 10% post-consumer paper fibers.Home and Building Control Home and Building ControlHoneywellHoneywell Limited-Honeywell Limitée 1985 Douglas Drive North 35 Dynamic Drive Golden Valley, MN 55422Scarborough, Ontario M1V 4Z9OPERATION AND CHECKOUTOperationThe C7130 Wall-mount Temperature Sensor converts room temperature to a resistance that the controller can interpret. The C7130 Wall-mount Temperature Sensor has a positive temperature coefficient (PTC), whichmeans that the resistance increases as the temperature increases. Fig. 4 shows how sensor resistance (for the C7130A) increases by 4.8 ohms per degree Fahrenheit [8.6 ohms per degree Celsius]. Since the curve shown in Fig. 4 is the same as the curve used by the C7100A and C7170A Sensors, these sensors are interchangeable.Fig. 5 shows how sensor resistance varies withtemperature for the C7130B by 2.1 ohms per degree Fahrenheit [3.85 ohms per degree Celsius].CheckoutAllow the C7130 Wall-mount Temperature Sensor to soak in the air moving through the room for a minimum of five minutes before taking a resistance measurement.With an accurate thermometer (± 1° F [0.5° C]) measure the temperature at the sensor location, allowing time for the thermometer to stabilize before reading. Use an ohmmeter to measure the resistance across the sensor wires. Then verify sensor accuracy with the temperature/resistance curve of Fig. 4 or Fig. 5 as applicable.Fig. 4. C7130A Sensor resistance vs. temperatureperformance characteristics.Fig. 5. C7130B resistance vs. temperatureperformance characteristics.RESISTANCE (OHMS)4200400038003600340020020406080100120140160180200220-7102030405060708090100F C3484 ± 6.5 OHMS AT 77°F (25°C)M2829TEMPERATURE (DEGREES)RESISTANCE (OHMS)1400131712311145105997320406080100120140160180200220-7102030405060708090100F C1097 ± 0.08 OHMS AT 77 F [25 C]M2824TEMPERATURE (DEGREES)By using this Honeywell literature, you agree that Honeywell will have no liability for any damages arising out of your use or modification to, the literature. You will defend and indemnify Honeywell, its affiliates and subsidiaries, from and against any liability, cost, or damages, including attorneys’ fees, arising out of, or resulting from, any modification to the literature by you.。
航盛维修手册统一版

上海航盛实业有限公司售后服务部
上海航盛维修指导手册
所有权声明
该文档及其所含信息是 HSAE(上海航盛实业有限公司)的财产。该文档及其所含信息的复制、使用及披露必须 得到 HSAE(上海航盛实业有限公司)的书面授权。
www. hangsheng- sh. com
售后服务部 赵强
2013-10-18
上海航盛实业有限公司售后服务部
Firetrol Mark IIXG型电动消防泵控制器使用手册说明书

安装和操作说明书Fire Pump Controllers General InformationCalifornia Proposition 65WarningWARNING : This product can expose you to chemicals including DINP, which is known to the State of California to cause cancer, and DIDP which is known to the State of California to cause birth defects or other reproductive harm.WARNING : This product can expose you to chemicals including lead and lead compounds, which are know to the State of California to cause cancer and birth defects or other reproductive harm.For more information go to: 3412 Apex Peakway Apex, North Carolina 27502P +1 919 460 5200F +1 919 460 目 录介绍 (1)安装控制器 (2)墙式安装 (2)地板/基座式安装 ....................................................................................................................2-3电气连接 ................................................................................................................................3-4系统压力连接管 . (4)一般预启动操作 (4)一般启动操作 (4)相位旋转 (5)电机旋转方向FTA750、1000、1500、1800、2000、2400控制器 (5)FTA1250 控制器 (5)FTA1300、1350 控制器..............................................................................................5-6 FTA1930 控制器 . (6)FTA900、975电源转换开关 (6)FTA950、976电源转换开关 (6)初始启动操作 (7)手动启动 (7)应急运行启动 (7)简单启动顺序FTA750, 1000, 2000, 2400 (7)FTA1250 .....................................................................................................................7-8 FTA1300, 1350 (8)FTA1500 (8)FTA1800 (8)FTA1930 (8)型IIXG程序设置用户界面和显示器 (9)用户菜单结构 (10)程序设置说明 (11)菜单设置系统设置显示亮度 (12)对比度 (12)反向 (12)键盘 (12)语言和单元语言 (12)压力单位 (12)密码1级 (12)2级 (12)日期和时间时间 (12)日期 (12)日期格式 (12)日光节约 (13)定时器延时开机 (13)最短运行/关机延迟 (13)加速 (13)子系统旁路 (13)压力压力单位 (14)启动 (14)停止 (14)禁用自动停机 (14)过压报警 (14)记录 -德耳塔 (14)传感器 (14)校正 (14)恢复默认设置 (14)电机和电源电压 (14)相序 (15)频率 (15)全负荷安培数 (15)CT 比值 (15)过负荷 (15)数字软启动电机 FLA (15)初始化电流 (15)最大电流 (15)斜坡加速时间 (15)UTS定时器 (15)减速开始水平 (15)减速中止水平 (15)减速中止时间 (15)减速结束水平 (15)斜坡减速时间 (15)相位旋转 (15)启用超时 (15)超时 (15)全负荷电流 (16)CT比值 (16)TX (16)RX (16)误差 (16)微调电压 (16)报警极限过压报警 (16)最小电压 (16)最大电压 (16)最小频率 (16)最大频率 (16)不平衡 (16)过负荷 (16)功能设置互锁报警 (17)低压力声音报警 (17)低吸入压力 (17)泵运行报警 (17)用户输入 (17)每周测试 ..........................................................................................................17-18选项设置 .. (18)主菜单- 事件日志 (18)主菜单-数据历史 (18)主菜单 USB储存到 USB (18)移出驱动器 (19)工厂配置序列号 (19)型号 (19)马力 (19)电压 (19)全负荷电流 (19)CT 比值 (19)频率 (19)相序 (19)压力传感器 (19)自动启动 NC (19)用户输入数字 (19)低吸入压力 (19)配置 - 选项 (20)配置 – 模数转换器 校正 (20)诊断原始输入:模拟 (20)原始输入:独立部件 (20)原始输入:键 (20)原始输出:独立部件 (20)IIXG型启动 (20)指示灯测试 (20)声音报警测试 (20)USB 测试 (20)相位失锁 (20)相序逆转 (20)并联跳闸装置1 (21)并联跳闸装置2 (21)标志 (21)工具清除数据历史 (21)清除事件日志 (21)恢复出厂设置 (21)固件更新 (21)关于......................................... (21)警告在设备通电期间,禁止安装或维护设备!接触通电设备可能造成死亡、人身伤害或大量财产损失。
球机安装方法

上电模式
掉电恢复 水平扫描俯仰范围 水平扫描速度 巡视组数量 预置位数量 预置位运行速度 预置位停留时间 两点扫描速度 两点扫描位置 两点扫描停留时间 看守模式 看守等待时间 看守位 隐私遮蔽 球机菜单 支持一体机 聚焦 光圈 电子变倍 视频冻结 背光补偿 数据复位 防水 防雷
断电恢复/两点扫描/水平扫描/看守位/ 巡视组1~3/无动作 记忆坐标与指令 0°~ 90°可定位 01 ~ 64级 3组(8个/组) 128个 01 ~ 64级可调 02 ~ 60秒可调 01 ~ 64级可调 任意设置 5 ~ 60秒可调 看守位/两点扫描/水平扫描/巡航组1~3 01 ~ 60分钟可调 任意设置 支持 支持多国语言(P/N制自定义) 10倍机芯/CCD板 手动/自动 手动/自动 支持 支持 支持 恢复出厂值/清除预置位/像机数据复位 IP50 瞬间3000V
技术指标21技术参数产品类型室内红外迷你中速球供电电源dc12v5环境温度4060环境湿度95无结露现象功率消耗10w通信方式rs485总线通信协议自动识别pelcod通信波特率软波特率1200bps2400bps4800bps9600bps球机地址软地址1250水平旋转速度50s水平旋转范围360垂直旋转速度30s垂直控制2级控制180翻转比例变速支持红外有效距离50m红外控制自动手动键控红外驱动pwm功率调置红外检测时间215秒环境光照度检测050级红外开启照度115级红外输出功率4级控制红外待机功率4级控制红外待机时间1530秒上电模式断电恢复两点扫描水平扫描看守位巡视组13无动作掉电恢复记忆坐标与指令水平扫描俯仰范围90可定位水平扫描速度0164级巡视组数量预置位数量128个预置位运行速度0164级可调预置位停留时间0260秒可调两点扫描速度0164级可调两点扫描位置任意设置两点扫描停留时间60秒可调看守模式看守位两点扫描水平扫描巡航组13看守等待时间0160分钟可调看守位任意设置隐私遮蔽支持球机菜单支持多国语言pn制自定义支持一体机10倍机芯ccd板聚焦手动自动光圈手动自动电子变倍支持视频冻结支持背光补偿支持数据复位恢复出厂值清除预置位像机数据复位防水ip50防雷瞬间3000v22外观尺寸23安装板尺寸产品安装31基本要求所有的电气工作都必须遵守使用最新的电气法规防火法规以及有关法规
Leuze ODSL 96B M L-2000-S12 光学距离传感器说明书

W e r e s e r v e t h e r i g h t t o m a k e c h a n g e s • D S _O D S L 96B M L 2000_e n _50118550.f m●Reflection-independent distance information●IO-Link/OLED display and key pad for configuration●Measurement value is indicated in mm on OLED display●Measurement range and mode adjustable ●Teachable switching output and analogue output150…2000mm18 - 30 VDCAccessories:(available separately)●Mounting systems●Cable with M12 connector (K-D …)●IO-Link master set MD12-US2-IOL1(50112085) andK-DS M12A-M12A-4P-2m-PVC cable(50110126)Dimensioned drawingA Green indicator diodeB Indicator diode yellowC TransmitterD ReceiverE Optical axisF Device plug M12x1G Countersinking for SK nut M5, 4.2mm deep H OLED display and key padIReference edge for the measurement (cover glass)Electrical connectionODSL 96B M/L-2000-S12ODSL 96B Optical laser distance sensorse n 01-2012/0350118550SpecificationsOptical dataMeasurement range 1)1)Luminosity coefficient 6%…90%, complete measurement range, at 20°C, medium range of U B , measurement object ≥50x50mm²150…2000mm Resolution 2)2)Minimum and maximum value depend on measurement distance1…3mm Light source laserWavelength 655nm (visible red light)Light spotdivergent, 2x6mm² at 2m Max. output power 1.2mW Pulse duration22ms Error limits (relative to measurement distance)Absolute measurement accuracy 1)±1.5%Repeatability 3)3)Same object, identical environmental conditions, measurement object ≥50x50mm²±0.5%B/W detection thresh. (6…90% rem.)≤1%Temperature compensation yes 4)4)Typ. ± 0.02 %/KTimingMeasurement time 5)5)internal measurement time distance sensor1…51)ms Response time 1)≤15ms Delay before start-up≤300msElectrical dataOperating voltage U B 18…30V (incl. residual ripple)Residual ripple≤15% of U B Open-circuit current ≤150mASensor operating modeIO-LinkCOM2 (38.4kBaud), Frame 2.2, Vers. 1.0, min. cycle time 2.2ms SIOnot supportedIndicatorsGreen LED continuous lightreadyoffno voltageYellow LED continuous lightobject within measurement range offno object within measurement rangeMechanical datametal housingHousing diecast zinc Optics cover glassWeight 380g Connection type M12 connector Environmental dataAmbient temp. (operation/storage)-20°C …+50°C / -30°C …+70°C Protective circuit 6)6)1=transient protection, 2=polarity reversal protection, 3=short circuit protection for all outputs 1, 2, 3VDE safety class 7)7)Rating voltage 250VAC, with cover closedII, all-insulated Protection class IP 67, IP 69K 8)8)IP 69K test in accordance with DIN 40050 part 9 simulated, high pressure cleaning conditions without the use of additives. Acids and bases are not part of the testLaser class2 (acc. to EN 60825-1)Standards appliedIEC 60947-5-2Order guideDesignationPart no.IO-Link interfaceODSL 96B M/L-2000-S1250111164TablesDiagramsODSL 96BRemarksApproved purpose :This product may only be used by qualified person-nel and must only be used for the approved purpose. This sensor is not a safety sensor and is not to be used for the protection of persons.IO-Link process dataOutput data device16 bit measurement value:distance 1 bit output resolution:1mm Signal too weak:65535Laser error:65533Data bitA15A14A13A12A11A10A9A8A7A6A5A4A3A2A1A0M S B16 bit measurement valueL S BODSL 96BOptical laser distance sensorsIO-Link service dataSensors with IO-Link interface can be configured and diagnosed via the service data.ParametersMeasure modeA measurement mode for adapting to the application task can be activated with this parameter.There is a selection of four measurement modes (standard, precision, speed und light suppression). By selecting the mode, the following results are achieved:●Standard : standard setting●Precision : high accuracy, approx. 95% slower ●Speed : fast measurement, approx. 30% faster●Light suppression : higher immunity against external light interferenceThe following table provides an overview of the effects of the individual parameters on the measurement function.Measurement filterA measurement filter for adapting to the application task can be activated with this parameter.There is a selection of three options (off, averaging, center value). By selecting the filter, the following results are achieved:●Off :no filtering of the measurement values.●Averaging :a moving average from the last 2…99 measurement values (setting of the number with measurem.count ) is calculated and output. If the measurement value changes abruptly, the output value moves linearly over n measurements from the old to the new measurement value. The time until the measurement value is updated is therefore not affected by the number of measurements; the response time for distance changes slows down.●Center value :filtering out of extreme values - the average is calculated from 10…50 individual measurements. Thenumber of individual measurements used for this purpose is selected via measurem. count (10, 20, 30, 40 or 50). The setting under filter depth specifies whether only the most extreme (coarse ), the middle (medium ) or the lowest deviations (fine ) should be filtered out.The following table provides an overview of the effects of the individual parameters on the measurement function.Number of measurement values (averaging)This parameter defines the number of individual measurements which are used for filtering.Number of measurement values (center value)This parameter defines the number of individual measurements which are used for filtering.Filter depth (center value)This parameter defines the filter gauge (medium, coarse, fine).DisplayThis parameter determines the display setting on the sensor (on, off, auto).Button lockThis parameter determines whether the key pad on the sensor is locked or activated.Measure mode Accuracy Measurement time /update Ambient lightVarying diffuse reflectionStandard ++++Precision ++--++Speed-++++Light suppression+--++oUpdating measurement timeResponse time for smallchange in distanceResponse time for large change in distanceFiltering of individual faulty measurementsFiltering of cumulative faulty measurementsOff+++----Averaging +--o -Center value----+++ODSL 96BSystem commands:Laser transmitter activationThis system command switches on the laser ser transmitter deactivationThis system command switches off the laser transmitter.If the sensor is deactivated, the last measurement value detected is frozen. The state of the laser can be seen from the sensor status.Setting to factory settingThis system command restores the factory settings of the sensor.Diagnostics (observation)Signal too weak [process value 65535] or laser failure [process value 65533]Reception signal is not sufficient: either no object is in the measurement range or the signal from the object is too weak for detec-tion. A displayed laser failure signalizes interference of the laser light source.Signal warningLow reception signal: the object is not detected reliably, e.g. because the signal from the object is very weak. Laser activationStatus information on whether the laser transmitter is activated or deactivated.Measurement range sensorStatus information on whether an object is located in the measurement range of the sensor.Notice!If parameters are changed on the device via the display and keyboard, the master is not signaled. In the event the master sends an explicit request, however, the changed value is available.Notice!Detailed information about the IO-Link service data and the IODD can be found at .ODSL 96BOptical laser distance sensorsWorking safelyAttention Laser Radiation!The optical distance sensors ODSL 96B operate with a red light laser of class 2 acc. to EN 60825-1. If you look into the beam path over a longer time period, the retina of your eye may be damaged!Never look directly into the beam path! Do not point the laser beam of the ODSL 96B at persons!When mounting and aligning the ODSL 96B take care to avoid reflections of the laser beam off reflective sur-faces!The use of operating and adjusting devices other than those specified in the technical description, carrying out of differing procedures, or improper use of the optical laser distance sensor may lead to dangerous exposure to radiation!The use of optical instruments or devices in combination with the device increases the danger of eye damage!Adhere to the applicable legal and local regulations regarding protection from laser beams acc. to EN 60825-1 in its latest version.The ODSL 96B uses a laser diode with low power in the visible red light range with an emitted wavelength of about 655nm.The glass optics cover is the only opening through which the laser radiation can escape from the device. The housing of the ODSL 96B is sealed and has no parts that need to be adjusted or maintained by the user. The device must not be tampered with and must not be changed in any way! The destruction of the seal voids the warranty!Notice!It is important to attach the stick-on labels delivered with the device (notice signs)! If the signs could be covered due to the installation location of the ODSL 96B, attach them close to the ODSL 96B so that it is not possible tolook into the laser beam when reading the notices!ODSL 96B。
ckd w2000参数
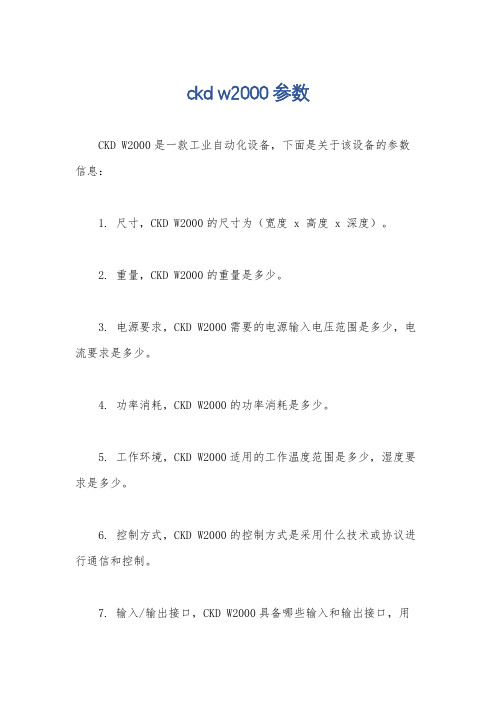
ckd w2000参数
CKD W2000是一款工业自动化设备,下面是关于该设备的参数信息:
1. 尺寸,CKD W2000的尺寸为(宽度 x 高度 x 深度)。
2. 重量,CKD W2000的重量是多少。
3. 电源要求,CKD W2000需要的电源输入电压范围是多少,电流要求是多少。
4. 功率消耗,CKD W2000的功率消耗是多少。
5. 工作环境,CKD W2000适用的工作温度范围是多少,湿度要求是多少。
6. 控制方式,CKD W2000的控制方式是采用什么技术或协议进行通信和控制。
7. 输入/输出接口,CKD W2000具备哪些输入和输出接口,用
于连接其他设备或传感器。
8. 运动控制能力,CKD W2000能够实现哪些运动控制功能,例如位置控制、速度控制等。
9. 通信接口,CKD W2000支持哪些通信接口,例如以太网、串口等,用于与其他设备进行数据交换。
10. 可编程性,CKD W2000是否支持编程,如果支持,使用的编程语言是什么,是否具备相关开发工具。
11. 安全性,CKD W2000是否具备安全保护功能,例如密码保护、权限管理等。
12. 可靠性,CKD W2000的可靠性如何,是否具备故障诊断和报警功能。
13. 维护保养,CKD W2000的维护保养要求是什么,是否需要定期进行保养和维修。
14. 应用领域,CKD W2000适用于哪些工业领域,例如自动化生产线、机械加工等。
以上是关于CKD W2000的一些参数信息,具体的参数可能需要参考该设备的官方文档或联系制造商以获取更详细的信息。
CA12CLC08BPRT商品说明书

CA12CLC08BPRTSpecifications are subject to change without notice (15.06.2017)1Housing diameter Rated operating distance Ordering no. Ordering no.(S n )Cable Plug M 12 8 mmCA12CLC08BP R T CA12CLC08BPM1R TProduct DescriptionProximity Sensors Capacitive Thermoplastic Polyester Housing Types CA, M12, DC, Teach-in• Featuring TRIPLESHIELD ™ Sensor Protection• Sensing distance: 0.5 - 8 mm• Teach-in of sensing distance via push-button or wire • Automatic detection of NPN or PNP load• Selectable make or break switching by means of the Teach-in function• Protection: short-circuit, transients and reverse polarity • Humidity compensation • Alarm outputType SelectionCapacitive proximity switch-es with a sensing distance of either 4 mm flush mount-ed in metal or 8 mm non-flush mounted.The switching points can be altered by means of theteach-in function. 3-wire DC output with selectable make (NO) or break (NC) switching and NPN Alarm. Grey poly-ester housing with 2 m PVC cable or M12 plug.TR I P L ES HI E L D ™Specifications2Specifications are subject to change without notice (15.06.2017)CA, M12, DC, Teach-inThe environments in which capacitive sensors are in s tall e d can often be un s table as regards to tem-perature, humi d ity , object dis-tance and industrial (noise) inter f erence. Because of this, Carlo Ga v azzi offers as standard features in all TRIP L ESHIELD ™ capaci-tive sensors a user-friendly sensitivity adjustment instead of a fixed sensing range. Likewise, these sensors provide an extend e d sen-sing range to accommodatemechanically de m and i ng are-as and tem p erature stability to en s ure high immunity to elec t ro m agnetic interference (EMI) and a minimum need for adjusting sensitivity if the temperature varies.Note:Sensors are factory set (default) to nominal sensing range S n .Adjustment GuideWiring DiagramSpecifications (cont.)Detection DiagramSpecifications are subject to change without notice (15.06.2017)3Installation HintsCapacitive sensors have a unique ability to detect al m ost any material in li q uid or solid form. Capa-ci t ive sensors are able to detect me t allic as well as non-metallic ob j ects. How-ever, their traditional use is for non-metallic materials such as:• Plastics Industry Resins, regrinds or mould-ed products.• Chemical Industry Cleansers, fertilizers, liquid soaps, corrosives and pe t r o c hemicals.• Wood Industry Saw dust, paper products, door and window frames.• Ceramics & Glass I ndustry Raw materials, clay or finish e d products, bottles.• Packaging Industry Package inspection for level or con-tents, dry goods, fruits and vegetables, dairy products.Materials are detected due to their dielectric constant.The bigger the size of anobject, the higher the density of ma t erial, the better or eas-ier it is to detect the object. The nominal sensing di s tan-ce for a capacitive sensor is refe r r ed to a grounded me t al plate (ST37). For addi-tional information regarding di e lec t ric ratings of materi-als please re f er to Technical Information.DimensionsRelief of cable strainProtection of the sensing faceSwitch mounted on mobile carrierTo avoid interference from inductive voltage/current peaks, separate the prox. switch power cables from any other power cables, e.g. motor, contactor or solenoid cablesNot correctCorrectThe cable should not be pulledA proximity switch should not serve as mechanical stopAny repetitive flexing of the cable should be avoidedDelivery Contents• Capacitive switch: CA12CLC08BP..• Installation & Adjustment Guide • 2 x M12 nuts• Packaging: Cardboard boxAccessories• Connector type CONB14NF.. -series.CA, M12, DC, Teach-in4Specifications are subject to change without notice (15.06.2017)Teach functionsNormal operation, optimized switching point 1. Mount the sensor in the application without the target present. Yellow LED is not important and green LED is O N.2. Press the button for 3 seconds until both LEDs are flashing simultaneously. (The background is stored)3. Place the target in the detection zone.4. Press the button once and the sensor is ready to operate (green LED ON, yellow LED ON) (The second switch point is stored). If the target is too close to the background, the sensor will perceive both background and object as background and the LEDs will alternate 3 times.For maximum sensing distance (default setting)1. Mount the sensor in the application without the target present. Yellow LED is not important and green LED is ON.2. Press the button for 3 seconds until both LEDs are flashing simultaneously. (The background information is stored)3. Press the button a second time and the sensor is ready to operate (green LED ON, yellow LED ON) (The sensor is set up with the maximum sensing distance that is not influenced by the background).For dynamic set-up (running process)1. Line up the sensor at the target. Green LED is ON, status on the yellow LED is not important.2. Press the button for 3 seconds until both LEDs are flashing simultaneously.3. Press and hold the button a second time for at least one second (both LEDs are flashing simultaneously and fast) and keep the button pressed for at least one process cycle. Release the button and the sensor is ready to operate (the switch point is stored into the sensor and is optimized respecting both background and target information). A more precise setting is possible if several process cycles are analysed.For make or break set-up (N.O. or N.C.)1. Press the button for 10 seconds, until the green LED flashes.2. While the green LED flashes, the output is inverted each time the button is pressed. Yellow LED indicates N.O. function selected. If the button is not pressed within the next 16 seconds, the current output is stored.Factory settingsPress the button for 16 sec.1243 sec.Push once3133 sec.Push once2133 sec.One cycle2210 sec.Push once1CA, M12, DC, Teach-inCA12CLC08BPRT。
AWM 2000 系列微桥质量气流传感器说明书
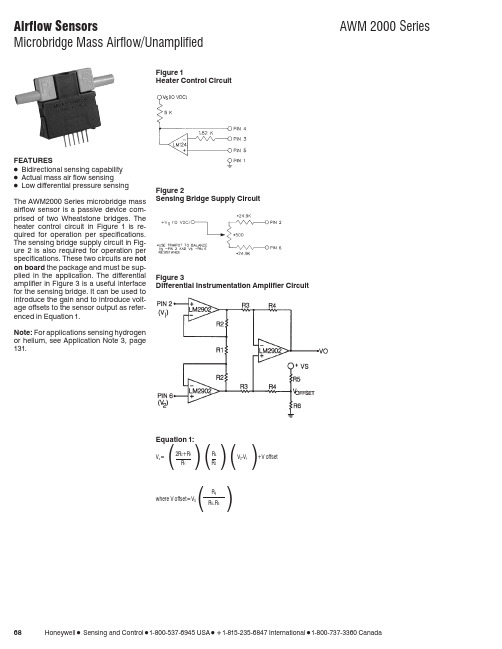
681-800-537-6945 USA 1-815-235-6847 International1-800-737-3360 CanadaFEATURESɀBidirectional sensing capability ɀActual mass air flow sensingɀLow differential pressure sensing The AWM2000 Series microbridge mass airflow sensor is a passive device com-prised of two Wheatstone bridges. The heater control circuit in Figure 1is re-quired for operation per specifications.The sensing bridge supply circuit in Fig-ure 2 is also required for operation per specifications. These two circuits are not on board the package and must be sup-plied in the application. The differential amplifier in Figure 3 is a useful interface for the sensing bridge. It can be used to introduce the gain and to introduce volt-age offsets to the sensor output as refer-enced in Equation 1.Note: For applications sensing hydrogen or helium, see Application Note 3, page 131.Figure 1Heater Control CircuitFigure 2Sensing Bridge Supply CircuitFigure 3Differential Instrumentation Amplifier CircuitEquation 1:V o ⍧2R 2+R 1R 4V 2-V 1+V offset()()()R 1R 3where V offset ⍧V S()R 6R 6+R 51-800-537-6945 USA 1-815-235-6847 International 1-800-737-3360 Canada 691. Output Voltage is ratiometric to supply voltage.2. Temperature shifts when sensing differential pressure correlates to the density change of the gas over temperature.See Application Note 1.3. Maximum allowable rate of flow change to prevent damage: 5.0 SLPM/1.0 sec.MOUNTING DIMENSIONS (for reference only)Airflow701-800-537-6945 USA 1-815-235-6847 International 1-800-737-3360 CanadaOUTPUT FLOW VS INTERCHANGEABILITY (Note 1)Performance Characteristics @10.0 ±0.01VDC, 25°C AWM2100V AWM2150VAWM2200V(Note 2)AWM2300V Press.Flow Nom.Tol.Press.Flow Nom.Tol.Flow Press.Nom.Tol.Press.Flow Nom.Tol.mBar sccm mV±mVȖBar sccm mV±mVsccm ⍯H 2O mV±mVmBar sccm mV±mV0.4920044.50 4.25533014.0 2.5120 4.0031.75 3.50 3.4100055.50 3.700.3515038.75 3.0036209.5 1.590 3.0026.75 2.50 2.480052.90 3.500.2110030.00 1.501710 5.0 1.560 2.0020.00 1.20 1.865050.00 2.500.095016.50 2.509.85 2.5 1.030 1.0011.20 1.800.8340042.50 3.000.000.00 1.007.44 2.0 1.000.000.001.000.3120029.20 3.20−0.09−50−16.50 4.50 6.23 1.5 1.0−30−1.00−11.20 3.0000.00 1.00−0.21−100−30.00 5.0052 1.0 1.0−60−2.00−20.00 3.30−0.31−200−28.9015.00−0.35−150−38.807.65 2.510.50.8−90−3.00−26.75 5.30−0.83−400−41.2026.00−0.49−200−44.509.75000.00.6−120−4.00−31.757.00−1.6−600−48.2029.50−9.8−5−2.5 2.0−2.4−800−52.2032.50−53−30−14.05.0−3.4−1000−55.0036.00Notes:1.Numbers in BOLD type indicate calibration type, mass flow or differential pressure.Tolerance values apply to calibration type only.2.Differential pressure calibrated devices are not recommended for flow e flow calibrated devices for flow measurement.OUTPUT CURVES。
海康威尔自动汽车引擎油箱保养指南说明书
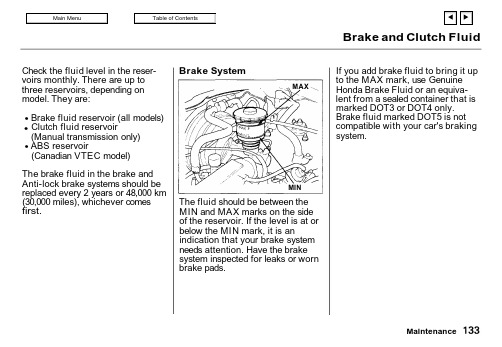
Brake and Clutch FluidCheck the fluid level in the reser-voirs monthly. There are up to three reservoirs, depending on model. They are:Brake fluid reservoir (all models)Clutch fluid reservoir(Manual transmission only)ABS reservoir(Canadian VTEC model)The brake fluid in the brake and Anti-lock brake systems should be replaced every 2 years or 48,000 km (30,000 miles), whichever comes first.Brake SystemThe fluid should be between the MIN and MAX marks on the side of the reservoir. If the level is at or below the MIN mark, it is anindication that your brake system needs attention. Have the brake system inspected for leaks or worn brake pads.If you add brake fluid to bring it up to the MAX mark, use Genuine Honda Brake Fluid or an equiva-lent from a sealed container that is marked DOT3 or DOT4 only.Brake fluid marked DOT5 is not compatible with your car's braking system.MAXMINBrake and Clutch FluidAnti-lock Brake SystemThe fluid should be between the MIN and MAX marks on the side of the reservoir. If it is at or below the MIN mark, it may indicate a problem in the braking system.Have the dealer inspect your car.If the fluid level is half an inch or more above the MAX mark, it may indicate a problem in the ABS.Have your dealer inspect the system as soon as possible.If you add brake fluid to bring it up to the MAX mark, use the same DOT3 or DOT4 brake fluid from a sealed container specified for the brake system.Clutch SystemThe fluid should be between the MIN and MAX marks on the side of the reservoir. If it is not, add brake fluid to bring it up to that level. Use the same DOT3 or DOT4brake fluid from a sealed container specified for the brake system.Low fluid level can indicate a leak in the clutch system. Have this system inspected as soon as possible.MAXMINPower SteeringYou should check the fluid level in the power steering reservoirmonthly. Check the level when the engine is cold. Look at the side of the reservoir. The fluid should be between the UPPER LEVEL and LOWER LEVEL. If it is below the LOWER LEVEL, add power steering fluid to the UPPER LEVEL.Using automatic transmission fluid or another brand of power steering fluid will damage the system. Use only GENUINE HONDA Power Steering Fluid-V.A low power steering fluid level can indicate a leak in the system.Check the fluid level frequently and have the system inspected as soon as possible.NOTICEUPPER LEVELLOWERLEVEL。