物理气相沉积技术的研究进展与应用
物理气相沉积技术的发展与应用
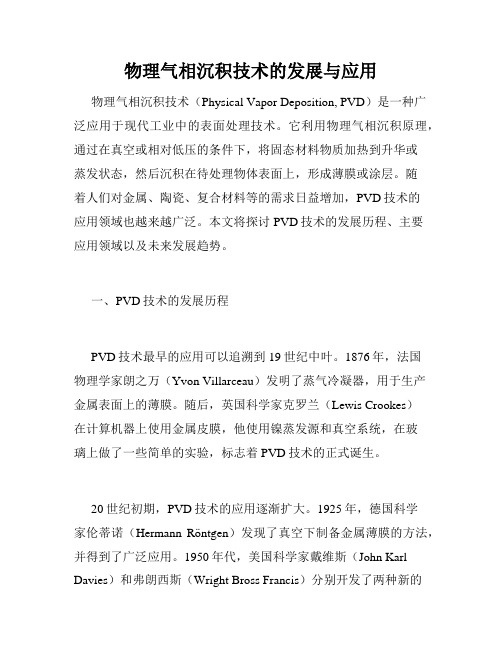
物理气相沉积技术的发展与应用物理气相沉积技术(Physical Vapor Deposition, PVD)是一种广泛应用于现代工业中的表面处理技术。
它利用物理气相沉积原理,通过在真空或相对低压的条件下,将固态材料物质加热到升华或蒸发状态,然后沉积在待处理物体表面上,形成薄膜或涂层。
随着人们对金属、陶瓷、复合材料等的需求日益增加,PVD技术的应用领域也越来越广泛。
本文将探讨PVD技术的发展历程、主要应用领域以及未来发展趋势。
一、PVD技术的发展历程PVD技术最早的应用可以追溯到19世纪中叶。
1876年,法国物理学家朗之万(Yvon Villarceau)发明了蒸气冷凝器,用于生产金属表面上的薄膜。
随后,英国科学家克罗兰(Lewis Crookes)在计算机器上使用金属皮膜,他使用镍蒸发源和真空系统,在玻璃上做了一些简单的实验,标志着PVD技术的正式诞生。
20世纪初期,PVD技术的应用逐渐扩大。
1925年,德国科学家伦蒂诺(Hermann Röntgen)发现了真空下制备金属薄膜的方法,并得到了广泛应用。
1950年代,美国科学家戴维斯(John Karl Davies)和弗朗西斯(Wright Bross Francis)分别开发了两种新的物理气相沉积技术,即电弧放电和磁控溅射。
60年代,PVD技术开始用于半导体和太阳能电池等领域。
70年代和80年代,随着微电子技术、薄膜电子技术、光学涂层技术等的快速发展,PVD技术逐渐成为了各种先进材料获得薄膜的最主要的手段。
二、PVD技术的主要应用领域1、半导体在半导体行业中,PVD技术被广泛应用于制造各种薄膜,如金属、氧化物、硅等。
这些薄膜被用于半导体器件制造的不同步骤,如金属接触、深度磨槽、浅孔孔板、薄膜电容器、光学涂层等。
利用PVD技术在薄膜中添加或掺杂一些特殊的元素,可以提高半导体器件的性能和稳定性。
2、工具涂层PVD技术在工具涂层方面的应用也比较广泛。
气相沉积技术

温度对化学反应的速率和程度有重要影响 ,同时也影响固态薄膜的结晶度和结构。
反应气体流量
基材温度
反应气体流量对化学反应的速率和产物有 直接影响,适当调整气体流量可以提高薄 膜的质量和性能。
基材温度对固态薄膜的附着力和结晶度有 重要影响,适当提高基材温度可以提高薄 膜的附着力和致密性。
03
气相沉积技术分类
化学气相沉积(CVD)是一种利用化学反应将气态物质转化为固体薄膜的工艺。
CVD技术通过将反应气体在一定温度和压力下进行化学反应,生成固态薄膜沉积在 基材表面。
CVD技术适用于制备各种高性能材料,如金刚石、类金刚石碳、碳化硅和氮化硅等。
物理化学气相沉积
物理化学气相沉积(PCVD)结合了物理气相沉积和 化学气相沉积的原理,通过物理和化学两种方式共同
未来应用前景与挑战
应用前景
气相沉积技术在许多领域都有广泛的应用前景,如半导体、新能源、生物医疗、环保等。随着技术的不断进步和 应用领域的拓展,气相沉积技术有望在未来发挥更加重要的作用。
挑战
尽管气相沉积技术具有广泛的应用前景,但仍然面临一些挑战,如设备成本、技术成熟度、生产效率和环保问题 等。因此,在未来的发展中,需要加强技术研发和产业合作,推动气相沉积技术的广泛应用和可持续发展。
复合材料
通过气相沉积技术将两种或多种材料复合在一起, 形成具有优异性能的复合材料。
光学薄膜制备
高反射膜
利用气相沉积技术制备高反射膜,用于反射激光、增强光学器件的 反射率。
增透膜
通过气相沉积技术制备增透膜,减少光学器件表面的反射,提高光 的透过率。
滤光片
气相沉积技术可制备各种光学滤光片,用于光谱分析、激光控制等领 域。
气相沉积技术
PVD技术研究报告
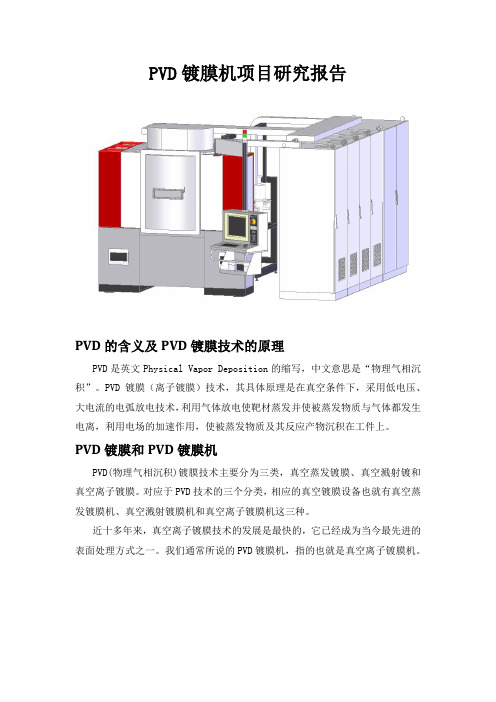
PVD镀膜机项目研究报告PVD的含义及PVD镀膜技术的原理PVD是英文Physical Vapor Deposition的缩写,中文意思是“物理气相沉积”。
PVD镀膜(离子镀膜)技术,其具体原理是在真空条件下,采用低电压、大电流的电弧放电技术,利用气体放电使靶材蒸发并使被蒸发物质与气体都发生电离,利用电场的加速作用,使被蒸发物质及其反应产物沉积在工件上。
PVD镀膜和PVD镀膜机PVD(物理气相沉积)镀膜技术主要分为三类,真空蒸发镀膜、真空溅射镀和真空离子镀膜。
对应于PVD技术的三个分类,相应的真空镀膜设备也就有真空蒸发镀膜机、真空溅射镀膜机和真空离子镀膜机这三种。
近十多年来,真空离子镀膜技术的发展是最快的,它已经成为当今最先进的表面处理方式之一。
我们通常所说的PVD镀膜机,指的也就是真空离子镀膜机。
PVD镀膜机结构构成PVD镀膜与传统化学电镀(水电镀)的异同PVD镀膜与传统的化学电镀的相同点是,两者都属于表面处理的范畴,都是通过一定的方式使一种材料覆盖在另一种材料的表面。
两者的不同点是:PVD镀膜膜层与工件表面的结合力更大,膜层的硬度更高,耐磨性和耐腐蚀性更好,膜层的性能也更稳定; PVD镀膜技术是一种能够真正获得微米级镀层(厚度较薄,一般为0.3μm ~5μm,其中装饰镀膜膜层的厚度一般为0.3μm ~1μm ,因此可以在几乎不影响工件原来尺寸的情况下提高工件表面的各种物理性能和化学性能,镀后不须再加工)且无污染的环保型表面处理方法,它能够制备各种单一金属膜(如铝、钛、锆、铬等),氮化物膜(TiN、ZrN、CrN、TiAlN)和碳化物膜(TiC、TiCN),以及氧化物膜(如TiO等)。
PVD镀膜技术目前主要应用的行业PVD镀膜技术的应用主要分为两大类:装饰镀膜和工具镀膜。
装饰镀的目的主要是为了改善工件的外观装饰性能和色泽同时使工件更耐磨耐腐蚀延长其使用寿命;这方面主要应用五金行业的各个领域,如门窗五金、锁具、卫浴五金等行业。
物理气相沉积技术

物理气相沉积技术1简介物理气相沉积(Physical Vapor Deposition,PVD)是一种表面处理技术,它基于原子、分子或离子在真空条件下从固体源“蒸发”或“剥离”,并在另外一个表面生成薄膜或涂层的过程。
PVD技术广泛应用于半导体、电子、机械、医疗等领域,可以改善材料表面的性能、延长使用寿命,也可以改变物体的颜色和外观。
2工艺流程PVD技术是在真空下完成的,因此主要工具是真空室,其次是沉积源,对于不同的应用场景,沉积源也会有所不同。
例如,如果是进行金属沉积,则沉积源可以是纯净金属,或者是通过将金属块或箔片加热,使其蒸发或溅射而得到的。
如果需要沉积金属氧化物,则需要放置源材料和氧气在沉积室中进行反应。
在PVD过程中,首先需要将材料放入真空室中,制备必要的工艺条件,使得沉积源的物质能够蒸发、溅射并扩散到目标基板上。
其中一个关键参数是真空度,PVD通常在10^-4~10^-8torr的高真空条件下进行。
另一个参数是沉积源与基板的距离,过近会导致过度热量和膜的不均匀厚度,过远影响膜的成形。
3分类根据真空沉积源材料的不同,PVD可分为四种类型:蒸发、离子镀、磁控溅射和分子束外延。
其中,蒸发和离子镀常常被用于制备功能性和装饰性薄膜涂层,磁控溅射则常被用于制备金属、半导体和陶瓷等薄膜,而分子束外延则适用于高质量、高洁净度的材料制备。
4应用PVD技术的应用涵盖了许多领域。
其中,电子和半导体产业是其中的重要应用领域之一。
在芯片制造过程中,PVD技术用于制备镀膜、金属连线等的处理;在随着显示技术的发展,PVD技术也被广泛应用于液晶显示器、有机EL显示器、柔性显示器等各种显示器领域。
此外,在航空航天、汽车、医疗、光学等领域都有PVD技术的应用。
5结论总的来说,PVD技术是一种成熟、广泛应用的表面处理技术。
它可以对各种材料表面进行处理,使其具有功能性和装饰性,可以改善产品的表面性能。
然而,由于技术的复杂性和设备的昂贵性,PVD技术在应用过程中也存在一定的限制性。
物理气相沉积技术

物理气相沉积技术
物理气相沉积技术(PVD)是一种表面处理技术,它利用原子或分子沉积在物体表面上以改变其性质和外观。
PVD技术包括磁控溅射、电弧放电、激光蒸发和离子束沉积等方法。
其中最常用的是磁控溅射。
磁控溅射利用磁场和电场控制离子在靶材表面的碰撞,使表面原子或分子被溅射并沉积到基底上。
这种技术可以制备多种材料,如金属、合金、陶瓷、半导体、光学薄膜等,并具有优异的物理和化学性质。
PVD技术广泛应用于电子、光电、机械、航空航天、医疗和环保等领域。
PVD技术具有以下优点:1)沉积过程中无需添加化学物质,无毒无害,环保安全;2)可以控制沉积速率、成膜厚度和成膜均匀性;3)沉积后的薄膜具有高硬度、高耐磨性、高抗腐蚀性、高温稳定性等优点;4)可以在复杂形状的物体表面进行沉积,如3D打印件表面的涂层,具有重要应用价值。
但是,PVD技术也存在一些限制:1)成本高,设备和操作费用较高;2)沉积速率较慢,不利于大规模生产;3)对于某些材料如聚合物,PVD技术难以应用。
综上所述,PVD技术是一种重要的表面处理技术,具有广泛应用前景。
随着技术的不断发展,PVD技术将继续在各个领域发挥重要作用。
- 1 -。
物理气相沉积技术的研究进展与应用_吴笛

CrN-CrAlN 多层沉积层等。 3 物理气相沉积技术的应用 3.1 在刀具、模具中的应用[19,20]
物理气相沉积技术最早应用于模具和刀具中。通 过沉积 TiC 镀层,可以有效延长模具的寿命;在高速 钢刀具中沉积镀膜,可提高刀具的抗磨损性、抗粘屑 性和刀具的切削速度,同时经镀膜的刀具还具有高硬 度、高化学稳定性、高韧性、低摩擦系数等特点。目 前 超 硬 沉 积 材 料 如 (TiAl)N、 TiCrN, 多 镀 层 如 TiC/Ti(C,N)/TiN 已经应用于生产。 3.2 在建筑装饰中的应用
2011 年第 4 期
吴笛:物理气相沉积技术的研究进展与应用
·215·
积表面。其主要特点是:沉积过程中的冷却速度比传统 喷射沉积要高,冷却效果较好;可制备大尺寸工件,且 冷却速度不受影响;工艺操作简单,易于制备尺寸精度 较高、表面均匀平整的工件;液滴沉积率高;材料显微 组织均匀细小,无明显界面反应,材料性能较好。但是 该技术还处于研究、开发和完善阶段,因此对其沉积到 工件表面的轨迹的规律性研究还缺少理论依据。 2 物理气相沉积技术的新进展及其特点
1.2 电火花沉积技术(ESD) 电火花沉积技术是将电源存储的高能量电能,在
气相法沉积

气相法沉积气相法沉积是一种在高温高压下将气体转化为固体的方法,被广泛应用于材料科学领域,特别是在制备薄膜材料方面。
本文将介绍气相法沉积的基本原理、分类、应用以及一些相关研究进展。
气相法沉积基本原理是通过将气体在特定条件下转化为固体沉积在基底上。
这种方法类似于水蒸气在凝结为液态水或冰时的现象,只不过在气相法沉积中,气体通常是由化学反应产生的。
这些气体可以是单一元素的化合物,也可以是多元素化合物。
通过控制气体的流量、温度和压力等参数,可以实现对沉积薄膜的厚度、成分和结构的控制。
气相法沉积根据其基本原理和工艺条件的不同,可以分为几种不同的类型。
其中最常见的是化学气相沉积(CVD)和物理气相沉积(PVD)。
化学气相沉积是通过化学反应将气体转化为固体沉积物,常用的方法有热分解法、气相氧化法等。
物理气相沉积则是通过物理手段将气体转化为固体沉积物,常用的方法有蒸发法、溅射法等。
气相法沉积在材料科学领域有着广泛的应用。
其中最重要的应用之一是制备薄膜材料。
气相法沉积可以制备各种类型的薄膜,包括金属薄膜、半导体薄膜和功能薄膜等。
这些薄膜广泛应用于电子器件、光电子器件和能源材料等领域。
此外,气相法沉积还可以制备纳米颗粒和纳米线材料等,这些材料对于纳米科学和纳米技术的研究也具有重要的意义。
近年来,气相法沉积的研究取得了一些进展。
一方面,研究人员通过改变气相法沉积的条件,例如温度、压力和气体流量等,来控制薄膜的成分、结构和性能。
另一方面,一些新的气相法沉积技术也被开发出来,例如原子层沉积(ALD)和电化学沉积等。
这些新技术进一步提高了气相法沉积的精度和可控性,为材料研究和应用提供了更多的可能性。
综上所述,气相法沉积是一种重要的材料制备方法,其原理是将气体转化为固体沉积物。
这种方法可以用于制备薄膜材料、纳米颗粒和纳米线材料等,并在电子器件、光电子器件和能源材料等领域得到广泛应用。
随着研究的深入,气相法沉积的技术和应用也在不断发展,为材料科学的研究和应用提供了更多的可能性。
物理气相沉积技术及其在纳米材料制备中的应用
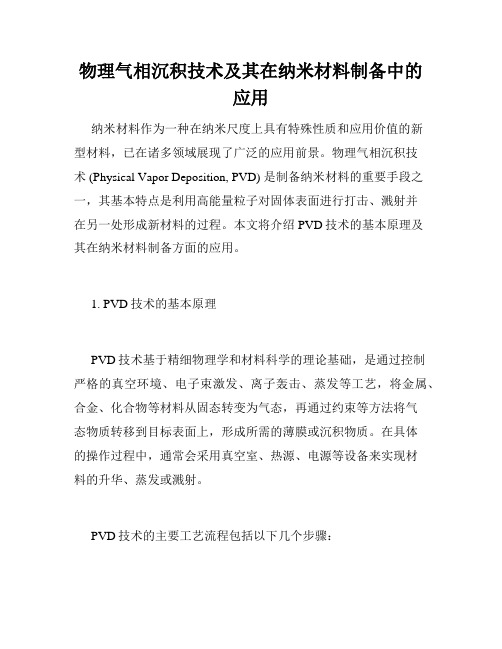
物理气相沉积技术及其在纳米材料制备中的应用纳米材料作为一种在纳米尺度上具有特殊性质和应用价值的新型材料,已在诸多领域展现了广泛的应用前景。
物理气相沉积技术 (Physical Vapor Deposition, PVD) 是制备纳米材料的重要手段之一,其基本特点是利用高能量粒子对固体表面进行打击、溅射并在另一处形成新材料的过程。
本文将介绍PVD技术的基本原理及其在纳米材料制备方面的应用。
1. PVD技术的基本原理PVD技术基于精细物理学和材料科学的理论基础,是通过控制严格的真空环境、电子束激发、离子轰击、蒸发等工艺,将金属、合金、化合物等材料从固态转变为气态,再通过约束等方法将气态物质转移到目标表面上,形成所需的薄膜或沉积物质。
在具体的操作过程中,通常会采用真空室、热源、电源等设备来实现材料的升华、蒸发或溅射。
PVD技术的主要工艺流程包括以下几个步骤:(1) 材料的升华或蒸发:采用熔融的方式或其他方式,将原始材料升华或蒸发,形成气态物质。
(2) 维持真空环境:将制备环境维持在高度真空状态,以防止气态物质在空气中与水分或氧气等的反应。
(3) 气态物质的传输:使用约束方法将气态物质传输到制备物质的表面。
(4) 沉积过程:将气态物质在制备物质的表面沉积,形成薄膜或其他制备物质。
2. PVD技术在纳米材料制备中的应用PVD技术广泛应用于纳米材料的制备中,特别是在金属、半导体、薄膜等领域有着重要的应用,如下所示:(1) 金属纳米材料的制备通过PVD技术可以制备各种金属的纳米材料,如Au、Ag、Cu、Ni和Pt等,这些纳米材料具有比其它形态的同种金属粒子更优异的物理、化学和生物学特性,例如更小的粒径、更可控的表面活性和更好的生物相容性等。
同时,PVD技术还可以制备多种形态的金属纳米材料,如球形、立方体、多面体等,具备良好的结构性能和表面活性,应用于催化、表面增强拉曼光谱、电子器件等方面。
(2) 半导体纳米材料的制备PVD技术可用于制备半导体陶瓷纳米材料,如TiO2、ZnO、Al2O3等材料。
物理气相沉积技术在薄膜制备中的应用研究

物理气相沉积技术在薄膜制备中的应用研究一、引言物理气相沉积技术是一种重要的薄膜制备技术,广泛应用于微电子、光电子、材料科学和工程等领域。
近年来,随着薄膜制备在各个领域中的广泛应用,物理气相沉积技术的发展也越来越受到关注。
本文将对物理气相沉积技术在薄膜制备中的应用展开深入研究。
二、物理气相沉积技术介绍1. 物理气相沉积技术的基本原理物理气相沉积技术又称为物理气相沉积法,是指将气体束注入真空腔中,在基板表面产生反应生成薄膜的一种方法。
常见的物理气相沉积技术包括热蒸发法、离子束辅助蒸发法、磁控溅射法、激光剥蚀法等。
2. 物理气相沉积技术的特点物理气相沉积技术具有以下特点:(1)制备过程中的反应物和中间体不需要直接接触基板表面,避免掺杂和氧化等问题。
(2)基板表面受到的热和化学影响较小,适用于对材料表面特性有要求的应用。
(3)制备的薄膜具有厚度均匀、晶体质量高、精确控制等特点,适用于微电子、光电子等应用。
三、物理气相沉积技术在薄膜制备中的应用1. 磁控溅射法制备金属薄膜磁控溅射法是物理气相沉积技术中应用最广泛的一种方法。
它基于磁控效应和靶材的原子表面扩散,利用高能粒子撞击靶材表面,将靶材原子蒸发到真空室内,最终在基板表面形成薄膜。
该技术制备的金属薄膜厚度均匀、结晶度高,广泛应用于微电子、太阳能电池、传感器等领域。
2. 离子束辅助蒸发法制备光学薄膜离子束辅助蒸发法是一种高纯度光学薄膜制备方法。
它利用电子轰击源将靶材产生蒸气,离子束通过高能粒子的撞击,使薄膜形成过程中的缺陷得到修复,从而制备出晶粒细小、透光率高、表面平整的光学薄膜。
3. 热蒸发法制备有机薄膜热蒸发法是将有机蒸发物蒸发到真空室中,通过它被表面吸附、扩散等作用,最终在基板表面形成薄膜的方法。
热蒸发法能够有效地制备出高纯度、高质量的有机薄膜,广泛应用于薄膜电容器、固态电池等领域。
四、总结与展望物理气相沉积技术作为一种有效的薄膜制备方法,已经在各个领域中得到了广泛应用。
物理气相沉积技术的开发与应用

物理气相沉积技术的开发与应用近几十年来,物理气相沉积技术(PVD)在各个领域的应用越来越广泛。
这种技术能够在几乎所有材料的表面上形成高质量的薄膜,并能够在微米和纳米尺度下控制。
因此,PVD已成为制备各种电子、光电、机械、生物和化学材料的重要手段。
一、 PVD技术分类1.打靶式物理气相沉积技术打靶式PVD是一种常见的物理气相沉积技术,它如同采用火器一样,使靶材上的原子或离子被“轰击”。
常用的打靶式PVD包括磁控溅射、电子束蒸发和离子束蒸发。
2.化学气相沉积技术除了物理气相沉积技术外,还有一种专门用于化学物质沉积的技术--化学气相沉积技术(CVD)。
其原理是将一种气体或气体混合物在反应器中加热至一定温度,将气态混合物转变为气态中间体/反应物质在固体表面上反应,从而沉积形成纯无杂质的薄膜。
CVD技术在太阳能电池、纳米材料等领域应用广泛。
二、 PVD技术的应用1. 电子器件磁控溅射技术被广泛应用在电子器件制造中,例如通过在硅晶体上沉积一层铝或铜,可以制造集成电路。
此外,离子束技术也可用于制造探测器、光电二极管和激光二极管等器件。
2. 光学材料激光器和LED灯的生产利用了物理气相沉积技术的靶材磁控溅射,PVD技术还可用于制造反射镜、选择性光谱吸收膜等光学材料。
3. 医学材料PVD技术可用于制造人工晶体、人造关节、生物隔膜、药物载体和防走船材料等医学材料。
4. 工业材料物理气相沉积技术在工业领域的应用已相当广泛,例如石墨涂层生产、电火花加工、车削刀具附属、大型机械部件等。
三、开发趋势1.纳米PVD技术随着纳米技术的不断发展,PVD技术也出现了纳米级别的磁控溅射和离子束蒸发。
这些技术提供了对纳米型材料性质和半导体器件等各种应用形态的控制,推动了PVD技术的发展。
2.多功能PVD技术利用PVD技术可同时在同一基底上沉积多种材料。
这种方法不仅可开发新型金属配合物,其在微纳制造和新型材料制备方面之需求,也符合现代制造需求,这是PVD技术的一个值得重视的发展方向。
半导体制造中的物理气相沉积技术研究

半导体制造中的物理气相沉积技术研究一、引言半导体芯片是现代社会最为重要的电子元件之一,它的制造是一项非常复杂而精细的科技活动。
其中涉及到很多制造工艺,其中物理气相沉积技术(Physical Vapor Deposition,PVD)是一种应用十分广泛的半导体制造技术。
本文将对物理气相沉积技术在半导体制造中的作用进行详细介绍。
二、物理气相沉积技术的概念物理气相沉积技术是一种制造半导体薄膜的技术,它利用真空系统将精制金属或合金材料制成真空蒸气,再沉积在基底表面上,从而形成一层非常薄的半导体薄膜。
物理气相沉积技术的制造原理主要是利用高温真空下金属材料的蒸发和汽化,将金属气体或离子沉积到基底表面,形成薄膜结构。
三、物理气相沉积技术的分类根据不同的沉积过程,物理气相沉积技术可以分为电子束物理气相沉积(Electron Beam Physical Vapor Deposition,EB-PVD)、磁控溅射沉积(Magnetron Sputtering Deposition,MSD)和电弧放电物理气相沉积(Arc-PVD)。
1、电子束物理气相沉积电子束物理气相沉积是指利用极高的真空度下,利用电子束将来源材料(电子束加热的材料)蒸发形成蒸气,再让蒸气沉积在基板表面上,形成一层薄膜的制备技术。
其特点是能够制备高密度、低氢、少缺陷、高纯度、高附着力的金属和陶瓷薄膜。
2、磁控溅射沉积利用磁场的作用,将金属粉末或者合金材料转化成离子,再通过电场作用,将其束缚在基底表面上,形成一层非常薄的膜。
其特点是可制备高均匀度、较厚、制备速度较快的薄膜。
3、电弧放电物理气相沉积电弧放电物理气相沉积是指将金属或者合金材料电弧加热至高温,形成金属蒸气,再将蒸气通过电场作用沉积于基底表面,形成一层薄膜。
其特点是沉积速度快,沉积的薄膜具有高硬度、高纯度和高致密度。
四、物理气相沉积技术的应用物理气相沉积技术在半导体制造中广泛应用,可以制备出高质量的薄膜和微结构。
气相沉积技术在智能制造中的应用与发展

气相沉积技术在智能制造中的应用与发展随着智能制造技术的不断发展,气相沉积技术在智能制造中的应用也变得越来越广泛。
气相沉积技术具有高效、精密、可重复性等优点,能够更好地满足现代智能制造的需求,成为智能制造技术中不可或缺的一部分。
一、气相沉积技术概述气相沉积技术是指通过将基底材料暴露在高温、高压、不同气氛下的反应气氛中,使气态物质沉积在基底表面上,形成具有特定性质的涂层。
气相沉积技术主要有热蒸发、物理气相沉积、化学气相沉积等多种类型。
其中,热蒸发技术具有简单、易操作的优点,但是成膜速度慢,难以用于大面积涂覆;物理气相沉积技术具有高成膜速率、高纯度的优点,但是设备复杂,制备过程受到温度、压力等因素影响较大;化学气相沉积技术则具有高速、高效、高质量、低温成膜等诸多优点,可以广泛用于各种材料的制备。
二、气相沉积技术在智能制造中的应用(一)建筑领域气相沉积技术可以用于建筑领域中的防护涂料和功能涂层的制备,可以提高建筑领域的防风、防水、防腐、隔热、隔音等特性,提高建筑的使用寿命。
(二)汽车制造领域气相沉积技术可以用于汽车制造领域中的车身涂料和引擎涂料的制备,可以提高汽车的表面硬度、耐腐蚀性、防刮擦性、耐高温性等特性,保护汽车表面和引擎不受外界环境的影响,提高汽车的使用寿命。
(三)电子元器件领域气相沉积技术可以用于电子元器件领域中的薄膜材料的制备,可以在晶体管、显示屏等电子元器件表面形成非常薄的涂层,提高元器件的稳定性和性能,延长元器件的使用寿命。
(四)新能源领域气相沉积技术可以用于新能源领域中太阳能电池和燃料电池的制备,可以提高太阳能电池的转换效率,提高燃料电池的稳定性和寿命,为新能源的开发和应用做出贡献。
三、气相沉积技术在智能制造中的发展趋势(一)多功能化智能制造中,气相沉积技术不仅需要满足部件的涂层质量要求,还需要具备导电、导热、抗磨损、抗高温、防辐射等多种功能,因此气相沉积技术的发展趋势是多功能化。
(二)智能化随着人工智能技术的发展,气相沉积技术也正在智能化方向上迈进。
ALD技术的发展与应用
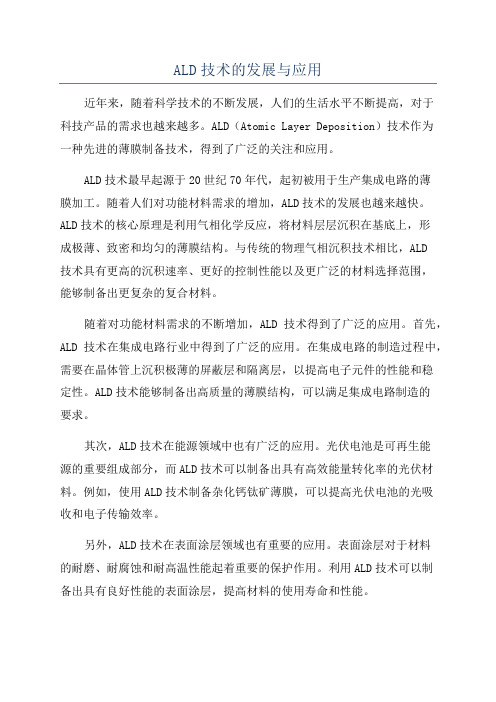
ALD技术的发展与应用近年来,随着科学技术的不断发展,人们的生活水平不断提高,对于科技产品的需求也越来越多。
ALD(Atomic Layer Deposition)技术作为一种先进的薄膜制备技术,得到了广泛的关注和应用。
ALD技术最早起源于20世纪70年代,起初被用于生产集成电路的薄膜加工。
随着人们对功能材料需求的增加,ALD技术的发展也越来越快。
ALD技术的核心原理是利用气相化学反应,将材料层层沉积在基底上,形成极薄、致密和均匀的薄膜结构。
与传统的物理气相沉积技术相比,ALD技术具有更高的沉积速率、更好的控制性能以及更广泛的材料选择范围,能够制备出更复杂的复合材料。
随着对功能材料需求的不断增加,ALD技术得到了广泛的应用。
首先,ALD技术在集成电路行业中得到了广泛的应用。
在集成电路的制造过程中,需要在晶体管上沉积极薄的屏蔽层和隔离层,以提高电子元件的性能和稳定性。
ALD技术能够制备出高质量的薄膜结构,可以满足集成电路制造的要求。
其次,ALD技术在能源领域中也有广泛的应用。
光伏电池是可再生能源的重要组成部分,而ALD技术可以制备出具有高效能量转化率的光伏材料。
例如,使用ALD技术制备杂化钙钛矿薄膜,可以提高光伏电池的光吸收和电子传输效率。
另外,ALD技术在表面涂层领域也有重要的应用。
表面涂层对于材料的耐磨、耐腐蚀和耐高温性能起着重要的保护作用。
利用ALD技术可以制备出具有良好性能的表面涂层,提高材料的使用寿命和性能。
此外,ALD技术在纳米材料的制备中也有潜力应用。
纳米材料具有独特的物理和化学性质,对于光电、磁电、催化和传感等领域有着广泛的应用前景。
ALD技术能够精确控制材料的形貌和尺寸,制备出具有特定功能的纳米材料。
虽然ALD技术发展迅速且应用广泛,但也面临着一些挑战。
首先,ALD技术的生产成本相对较高,这限制了其在大规模生产中的应用。
其次,ALD技术目前还存在一些技术难题,如反应速率慢、沉积速度低等问题,需要进一步研究和改进。
气相沉积的原理及应用

气相沉积的原理及应用1. 气相沉积的概述气相沉积(Gas Phase Deposition,简称GPD)是一种将气体原料转化为薄膜或纳米结构的技术。
它通过在真空或气氛控制环境中将气体原料分解并沉积在基底表面上,使得薄膜形成。
气相沉积技术具有高生长速率、均匀性好、可对复杂形状的基底进行沉积等优点,因此在材料科学、能源领域、纳米技术等多个领域得到广泛应用。
2. 气相沉积的原理气相沉积技术包括化学气相沉积(Chemical Vapor Deposition,简称CVD)和物理气相沉积(Physical Vapor Deposition,简称PVD)两种主要类型。
2.1 化学气相沉积(CVD)化学气相沉积技术是通过将气体原料传送到沉积区域,其在表面反应而形成固态产物。
主要包括以下几个步骤: - 气体原料的传送:气体原料从气源经过传送管道进入沉积区域。
- 表面反应:气体原料在沉积区域与基底表面发生反应,形成沉积产物。
- 官能团组装:沉积产物会通过表面反应与其他气体原料中的官能团进行反应,形成更加复杂和完整的结构。
2.2 物理气相沉积(PVD)物理气相沉积技术是通过将气体原料通过物理手段转化为固态产物。
主要包括以下几种类型: - 热蒸发:将固体材料加热至其蒸发温度,产生的蒸汽在基底表面沉积。
- 电子束蒸发:利用高能电子束蒸发固体材料,生成蒸汽在基底表面沉积。
- 磁控溅射:通过在真空环境中使用磁场控制离子运动轨迹,溅射固体材料,使其在基底表面沉积。
3. 气相沉积的应用气相沉积技术在许多领域都有广泛的应用。
3.1 薄膜制备气相沉积可以制备许多不同类型的薄膜,如金属薄膜、氧化物薄膜、氮化物薄膜等。
这些薄膜在电子器件、光学器件、防护涂层等方面具有重要的应用。
3.2 光学镀膜气相沉积技术可以制备出具有特殊光学性质的薄膜,用于制备光学器件,如反射镜、透明电极等。
这些器件在太阳能电池、液晶显示器等领域有着广泛的应用。
物理气相沉积技术的研究及其应用

物理气相沉积技术的研究及其应用物理气相沉积技术,简称PVD(Physical Vapor Deposition),是一种广泛应用于材料制备领域的重要技术。
其基本原理是通过一定外界条件下的金属或合金材料气相化,通过真空/惰性气体等载体将其转变为蒸汽态,再在基板表面沉积形成薄膜。
PVD技术具有制备过程简单、制备质量优良、反应物飞行距离短、控制涂层厚度和成分等优点。
因此,PVD技术得到了广泛的应用,如在半导体、光电、化学、机械和制造等领域,成功的制备出了各种形态和用途的功能材料。
一、PVD技术中的多种形式在PVD技术中,通常分为物理气相沉积和化学气相沉积两大类。
在物理气相沉积中,又可以分为蒸发法、电子束法和磁控溅射法等不同类型。
蒸发法是最简单的一种PVD技术,其制备过程主要是利用电加热或电子束辐照等方法将原材料蒸发成小分子蒸汽,然后沉积在基板上形成薄膜。
电子束法是来自一个热电子束的能量来转变反应物为蒸汽,其优势表现在具有狭缝束来合理地调节和控制沉积速度和成分组成。
在磁控溅射法中,利用离子轰击金属靶,使其中金属粒子获得足够能量而将原材料强制离子化,并通过惰性气体或真空将其转变为蒸汽态颗粒沉积在基板表面上。
二、PVD技术中的应用在现代科技领域,PVD技术已经广泛应用于半导体、光电、化学、机械和制造等领域。
其中,半导体和光电是PVD技术的特别典型应用。
在半导体领域,PVD技术已经成功应用于铝箔、镀锌钢铁、钼片等材料表面的氢化、硝化处理及半导体材料掺杂,而在光电领域,PVD技术成功制备了光敏电致变色材料及生物材料磁光材料等新型光电材料。
在化学领域,PVD技术成功制备了一系列清洁和安全的新型化学淀积物,如钛纠铝和氧化铝等纳米电泳材料,以及铝箔膜、氧化磷蒸发源等高级涂层材料。
因此,PVD技术在如今的科技界中已是不可或缺的技术之一。
三、PVD技术中存在的问题尽管PVD技术有着广泛的应用,但也存在着几个主要问题,防止大规模的应用。
关于物理气相沉积工艺及原理调研报告

关于物理气相沉积工艺及原理调研报告一、PVD技术简介:1、PVD是英文Physical Vapor Deposition(物理气相沉积)的缩写,是指在真空条件下,采用低电压、大电流的电弧放电技术,利用气体放电使靶材蒸发并使被蒸发物质与气体都发生电离,利用电场的加速作用,使被蒸发物质及其反应产物沉积在工件上。
PVD技术出现于二十世纪七十年代末,制备的薄膜具有高硬度、低摩擦系数、很好的耐磨性和化学稳定性等优点。
最初在高速钢刀具领域的成功应用引起了世界各国制造业的高度重视,人们在开发高性能、高可靠性涂层设备的同时,也在硬质合金、陶瓷类刀具中进行了更加深入的涂层应用研究。
与CVD工艺相比,PVD工艺处理温度低,在600℃以下时对刀具材料的抗弯强度无影响;薄膜内部应力状态为压应力,更适于对硬质合金精密复杂刀具的涂层;PVD工艺对环境无不利影响,符合现代绿色制造的发展方向。
二、PVD工艺的特点:物理气相沉积具有金属汽化的特点,与不同的气体发应形成一种薄膜涂层。
今天所使用的大多数PVD 方法是电弧和溅射沉积涂层。
这两种过程需要在高度真空条件下进行。
Ionbond 阴极电弧PVD 涂层技术在20 世纪70 年代后期由前苏联发明,如今,绝大多数的刀模具涂层使用电弧沉积技术。
典型的PVD 涂层加工温度在250 ℃—450 ℃之间,但在有些情况下依据应用领域和涂层的质量,PVD 涂层温度可低于70 ℃或高于600 ℃进行涂层,适合多种材质,涂层多样化,减少工艺时间,提高生产率;较低的涂层温度,零件尺寸变形小;对工艺环境无污染。
当前物理气相沉积分为三类,射频直流溅射、PLD、ion beam。
缺点,由于不同粒子溅射速率不同,所以物理气相沉积薄膜组分控制比较困难。
三、PVD技术的发展:目前国内PVD技术的发展更具多元性及创新性,归纳起来有以下几种类型:①阴极电弧法(Cathode Arc Deposition )国内已由小圆型阴极电弧技术发展到大面积阴极电弧技术及柱型靶阴极电弧技术,主要用于TiAlN等薄膜的制备。
物理气相沉积的应用

物理气相沉积的应用物理气相沉积技术表示在真空亲件下,采用物理方法,将材料源一一固体或液体表面气化成气态原子、分子或部分电离成离子,并通过低压气体(或等离子体)过程,在基体表面沉积具有某种特殊功能的薄膜的技术.物理气相沉积的主要方蒸镀、溅射镀膜电弧等离子体镀、离子镀膜,及分子束外延等.发展到目前,物理气相沉积技术不仅可沉积金属膜、合金膜、还可以沉积化合物、陶瓷、半导体、聚合物膜等.真空蒸镀基本原则是在真空条件下,使金属、金属合金或化合物蒸发,然后沉积在基体面上,蒸发的方法常用电阻加热,高频感应加热,电子柬、激光束、离子束高能轰击镀料,使蒸发成气相,然后沉积在基体表面,历史上,真空蒸镀是PVD法中使用最早的技术.溅射镀膜基本原理是充氩(Ar)气的真空条件下,使氩气进行辉光放电,这时氩(Ar)原子电离成氩离子离子在电场力的作用下,加速轰击以镀料制作的阴极靶材,靶木被溅射出来而沉积到工件表面.如果采用直流辉光放电,称直流(Qc)溅射,射频(RF)辉光放电引起的称射频溅射.磁控(M)辉光放电引起的称磁控溅射.电弧等离子体镀膜基本原理是在真空条件下,用引弧针引弧,使真空金壁(阳极)和镀材(阴极)之间进行弧光放电,阴极表面快速移动着多个阴极弧斑,不断迅速蒸发甚至"异华"镀料,使之电离成以镀料为主要成的电弧等离子体,并能迅速将镀料沉积于基体.因为有多弧斑,所以也称多弧蒸发离化过程.离子镀基本原理是在真空亲件下,采用某种等离子体电离技术,使镀料原子部分电离成离子,同时产生许多高能量的中性原子,在被镀基体上加负偏压.这样在深度负偏压的作用下,离子沉积于基体表面形成薄膜.物理气相沉积技术基本原理可分三个工艺步骤:(1)镀料的气化:即使镀料蒸发,异华或被溅射,也就是通过镀料的气化源.(2)镀料原子或离子的迁移:由气化源供出原子、分子或离子经过碰撞后,产生多种反应.(3)镀料原子、分子或离子在基体上沉积.物理气相沉积技术工艺过程简单,对环境改善,无污染,耗材少,成膜均匀致密,与基体的结合力强.该技术广泛应用于航空航天、电子、光学、机械、建筑、轻工、冶金、材料等领域,可制备具有耐磨、耐腐饰、装饰、导电、绝缘、光导、压电、磁性、润滑、超导等特性的膜层.随着高科技及新兴工业发展,物理气相沉积技术出现了不少新的先进的亮点,如多弧离子镀与磁控溅射兼容技术,大型矩形长弧靶和溅射靶,非平衡磁控溅射靶,孪生靶技术,带状泡沫多弧沉积卷绕镀层技术,条状纤维织物卷绕镀层技术等,使用的镀层成套设备,向计算机全自动,大型化工业规模方向发展.。
物理气相沉积x

,
汇报人:
目录 /目录
01
点击此处添加 目录标题
04
物理气相沉积 技术的优缺点
02
物理气相沉积 技术概述
05
物理气相沉积 技术的发展趋 势
03
物理气相沉积 技术的应用领 域
06
物理气相沉积 技术的前景展 望
01 添加章节标题
02 物理气相沉积技术概述
物理气相沉积技术的定义
物理气相沉积技术 是一种利用物理方 法将气态物质转化 为固态薄膜的技术。
增强与其他表面处理技术的结合应用如电镀、化学镀等以提高沉积效率和 质量。
开发新型物理气相沉积技术如脉冲电弧放电、激光诱导等离子体等以满足 更广泛的应用需求。
深入研究物理气相沉积的机理和过程控制提高沉积层的均匀性和致密性。
加强与其他表面处理技术的结合应用如电镀、化学镀等以提高沉积效率和 质量。
06
物理气相沉积技术的前 景展望
新能源领域
太阳能电池: 物理气相沉积 技术用于制备 高效太阳能电 池提高光电转
换效率。
锂离子电池: 通过物理气相 沉积技术制备 电极材料提高 锂离子电池的 能量密度和循
环寿命。
燃料电池:利 用物理气相沉 积技术制备质 子交换膜和催 化剂降低燃料 电池的成本和
提高性能。
储能技术:物 理气相沉积技 术在储能领域 也有广泛应用 如超级电容器 和电池储能系
拓展应用领域和提高应用水平
拓展应用领域:随着技术的不断发展物理气相沉积技术的应用领域正在不断拓展例如在新能源、生物医学、 航空航天等领域的应用。
提高应用水平:通过不断的技术创新和改进物理气相沉积技术的应用水平也在不断提高例如在薄膜的均匀性、 附着力、耐久性等方面的提升。
物理气相沉积及其在薄膜制备中的应用

物理气相沉积及其在薄膜制备中的应用物理气相沉积(Physical Vapor Deposition, PVD)是一种广泛应用于薄膜制备领域的表面处理方法。
在PVD制备过程中,原料材料以固体或液体的形式添加到真空室中,然后被加热和蒸发至其气态。
这些气态分子蒸发出来后,会沉积在需要处理的表面上,形成一个均匀的薄膜。
PVD技术可以分为多种方法,其中包括热蒸发沉积、磁控溅射沉积和电弧溅射沉积等。
在这些方法中,热蒸发沉积是最古老的PVD技术。
将固体材料放入真空腔体中并施加热量,从而使原料氧化或转移为气态物质。
然后,气态物质穿过真空室并Form一个稳定的薄膜沉积在待处理物体表面上。
磁控溅射沉积是一种使用磁场将原料转移到待处理表面的技术。
在磁控溅射沉积过程中,原料被打碎和离子化,然后被引入一个磁场中。
在磁场的作用下,电离原料可以沉积在待处理物体表面上,最终形成一个薄膜。
电弧溅射沉积是一种高能量的PVD技术,通过将电弧加热金属原料,使其氧化并形成气态原料,然后在真空室内通过电场进行沉积。
与其他PVD技术相比,电弧溅射利用了高能量的优势,可以形成高质量的薄膜。
PVD技术及其应用在制备平整、致密和均匀的薄膜方面具有非常重要的作用。
物理气相沉积可以应用于生产各种对表面特性有特殊要求的设备和零件,包括线路板、光学元件以及高频电子设备等。
在半导体工业中,PVD技术被广泛应用于微电子器件的制备。
通过控制气压和温度等条件,可制备出各种形状、厚度和化学特性的薄膜。
其制备出来的薄膜可用于制备各种高精度微电子器件,如存储器、传感器、LED显示屏和光纤通信器件等。
同时,在纳米技术领域,PVD技术可以制备出极薄的纳米材料薄膜。
由于这些薄膜厚度只有纳米级别,因此在制备纳米光电设备方面具有很大的应用前景。
例如,PVD技术制备出的具有不同光响应波段的多层纳米结构可以形成多色的光电器件,而这种器件已广泛应用于基于光子学的新型显示器件和光纤通信中。
- 1、下载文档前请自行甄别文档内容的完整性,平台不提供额外的编辑、内容补充、找答案等附加服务。
- 2、"仅部分预览"的文档,不可在线预览部分如存在完整性等问题,可反馈申请退款(可完整预览的文档不适用该条件!)。
- 3、如文档侵犯您的权益,请联系客服反馈,我们会尽快为您处理(人工客服工作时间:9:00-18:30)。
成 分宏 观偏 析 以及 组织 粗 大等诸 多弊端 ,可实现 大尺 寸快速 凝 固材料 的一 次成 型 , 目前 多应 用 于颗粒 增强
为提 高硬 度 ,后 来 逐渐 转 向立 方 氮 化硼 (B ) 金 刚 CN 和
第 4期 ( 第 17期 ) 总 6
21 0 1年 8月
机 械 工 程 与 自 动 化
M E CH A N I CA L EN G I EER I N NG & AU T0 M A TI N O
No. 4 Aug.
文 章 编 号 :6 2 6 1 2 1 17 — 4 3( 0 1)0 — 24 0 40 1— 3
冷 却速 度 不受影 响 ; 工艺 操作 简单 , 于制备 尺 寸精度 易
较 高 、 面 均匀 平整 的工 件 ; 滴沉 积率 高 ; 表 液 材料 显 微
组织均 匀 细小 , 明显界面 反应 , 料性 能较 好 。但 是 无 材 该技术 还 处于研 究 、 开发和 完 善阶段 , 因此对其 沉积 到 工件表 面 的轨迹 的规律性 研究 还缺 少理论依 据 。 2 物理 气相沉 积技 术的 新进展及 其特 点 物 理气 相沉 积技术 作 为高新 技术 在先 进制造 技 术
I C ) T N已经应 用于 生产 。 a r ( ,N , I 4 /
32 在 建筑装饰 中的应 用 .
因物 理气 相沉 积技 术具有 沉积 过程 易于操 作 ,膜 层 的成分 易 于控 制 , 存在 废 水 、 气 、 渣 的污 染 等 不 废 废
由原来较 单 一 的 H S S 、硬 质合 金 等材 料 不 断 向中低 合
中图分 类 号 : G1 4 4 4 T . 4 7 文献 标 识 码 : A
1 物理气相沉积 技术的种类
物 理 气 相 沉 积 (h s c l a o D p st o , P y ia V p r e o i in P D 是制备硬质 镀层 ( V) 薄膜) 的常用 技术 ,按 照沉积 时
k/ g h的蒸 发速率 ) 、涂 层致密 、化 学成 分 易于精确 控 制 、可 得 到柱 状 晶组 织 、无 污 染 以及 热 效 率 高等 优 点 。该技 术 的缺点 是设 备 昂贵 ,加工 成本 高 。 目前 ,
该技术 已经 成为各 国研 究的热点 ∞ 。 “ 14 多层喷射 沉积技 术 (L D . M S) 与传 统的喷射 沉积技 术相 比,多层 喷射 沉积 的一
1 3 电子束 物理气相 沉积技 术 (B P D . E-V) 电子束 物理气相 沉积 技术是 以高能密度 的 电子束
直接 加热蒸发 材料 ,蒸发材料 在较低 温度下沉 积在基
体表 面 的技术 。该 技术具 有沉 积速 率高 (0 k /  ̄1 1 g h 5
入 的优 点外 ,还可在较 低 的轰 击能量 下连续 生长任意 厚度 的膜层 ,并能在室温 或近 室温下合 成具有 理想化
学配 比的化合物 膜层 ( 括 常温 常 压 无法 获得 的新 型 包
膜层 ) 。该技 术具 有工 艺温 度低 ( 0 ℃) <2 0 ,对所 有
衬底 结合力强 ,可在 室温得 到 高温 相 、亚稳相及 非晶 态 合金 ,化 学组成便 于控制 ,方便控 制生 长过程等优 点 。主要缺 点是离子 束具有直 射性 ,因此处 理形状复
化。 ‘
(l c r n S a k D p s t o ) 电子 束 物 理 气相 沉 E e t o p r e o i in 、 积 技 术 (l c r n B a - V ) 多 层 喷 射 沉 积 技 术 E e t o e m P D 和
(u i l y r S r y D p s t o e h iu ) ~。 M t— a e p a e o i i n T c n q e 等n
石 、类 金 刚石 (D a o d lk C r o ,D C 膜 。 同 (i m n — e a b n L ) i
时 ,还 出现 了一些 功 能薄膜 ,例如 具有 光催 化作用 的
m  ̄P
,
和技 术进步 中占有重 要 的地位 ,工 业应 用 的要求 也越
来越 高 ,在 工 艺、材 料 、装各 改进 的 同时 ,物 理气 相
沉积 技术 的研 究 也有 了新 的进 展 ,具有 了新 的特 点 。 ()应 用 范 围不 断扩 大 : 目前 ,P D处 理 的对 象 I V
物理 气相 沉积技术 的研 究进展 与应用
天 , 吴 笛 由
( 兰州 石化 职业技术 学院 机械 工程 系 ,甘肃 兰州 70 6 ) 3 00
摘要 : 绍 了物理 气相沉积技术 的新工 艺、新进展及其特 点,总结 了物理 气相沉积技术的一些新应用。指 介
出特殊功能复合膜 的制备 、复合膜 的研究与应用 以及 超硬膜制备将是物理 气相沉积技术今后研 究的重点。 关键词 : 物理气相沉积 ;沉积;薄膜
1 1 离子束增强沉积技 术 (B D . IE)
离子束增强沉 积技术 是一种将 离子 注入与薄膜 沉 积融为 一体的材料 表面 改性新技术 。它 是指在气相 沉 积 镀 膜 的 同 时 ,采 用 一 定 能量 的离 子 束进 行 轰 击 混
合 ,从而形 成单质或 化合物膜 层 。它除 了保 留离子注
1 m 0 r 0 n  ̄4 i 金 属 膜 ,膜 料 通 常 为金 属 C 、T 、 m的 r i N 及 其 合 金 ,该层 也是 利 用溅 射 沉 积 技术 制 得 。对 i
于 建筑 瓷砖及 镜面 不锈 钢薄 板 的镀 膜来 说 ,通 常制 备
的膜 系 为金 黄色 的 T N i ,这 种仿 金色 彩 在装 璜业 上特
l 2 电火花 沉积技 术 (S ) 。 E D
电火 花沉积 技术是将 电源存储 的高能量 电能 ,在 金 属 电极 ( 阳极) 与金 属母 材 ( 阴极) 问瞬 时高频 释放 , 通过 电极材料 与母材 间的 空气 电离 ,形 成通道 ,使母 材表 面产生瞬 时高温 、高压微 区 ;同时离子态 的电极 材料在 微 电场 的作用下 融渗到母 材基体 ,形成冶金 结
物 理机制 的差别 ,物 理气 相沉 积一般 分为 真空蒸发镀
膜 技 术 (a o v p r t o ) 真 空溅 射 镀 膜 (a o V p r E a o a in 、 Vpr
Sutrn ) p t e i g 、离子 镀膜 (o l t n ) 分子束 外延 InPa g和 i (o e u a em E i a y 等 。近年 来 ,薄膜技 术和 M lc lr B a p t x ) 薄膜 材 料 的发 展 突 飞猛 进 ,成 果 显 著 ,在 原有 基 础 上 , 相 继 出 现 了 离 子 束 增 强 沉 积 技 术
别 受青 睐 。
国 内的研 究和生产 中已得 到应 用 。 () 薄膜材 料越 来越 丰 富[~] 3 1 i:早 期 发展 的材 料 3s
为 T C年 N类 型 ,女 1 、T N r 、 ( i N等 。 i 日T 口A N i 、C N T M)
33 在特殊薄膜材料制备中的应用 . 雾化沉 积 技 术可 以显 著地 扩 大合 金 元素 固溶度 , 获 得细 小均 匀 的等 轴 晶组织 ,减 小合金 元素 的宏观 偏
个重 要特 点是 可 调节接 收器 系统 和 坩埚 系统 的运 动 , 使沉 积过程 为匀速且 轨迹不 重复 ,从 而得到 平整 的沉
杂 的表面 比较 困难 。
收 稿 日期 :2 1— 2 2 ;修 回 日期 :2 1 - 3 2 0 lo — 1 0 l0 — 1
作 者 简 介 :吴 笛 (9 8 ) 男 , 肃 庆 阳人 , 师 , 士 , 17一 , 甘 讲 硕 主要 从 事 金 属材 料 表 面 改性 技可达 1 5 0 H ~2 0 0 H ,性 能 0 V 0 V 远 高于 电镀 c r和氮 化 。
()沉积 的基体温 度 越来越 低 [ :为保证 P D 2 1 ] V 表
面 处理后 被 处理件 整 体材 料 的性 能不 下 降 ,降低 P D V 处 理温度 ,在较 低 的温 度 下 获得 性 能优 良的沉 积 层 , 是 P D技 术的一 个主 要技 术 问题 。国外相 继 出现 了在 V 3 0 ℃下采 用磁 控溅 射对 高速 工具钢 和滚 珠轴 承沉积 5 T N层 ; 在 2 0 ℃ 用 非 平 衡 磁 控 溅 射 沉 积 多 层 i 0 T N C A N和 C N C A N复 合 涂 层 等 新 技 术 。 目前 , i— r 1 r —r I 利 用磁控 溅射沉 积 的方法 降低 沉积 基体 温度 的技 术在
过沉 积 T C镀层 ,可 以有 效延长 模具 的寿命 ;在 高速 i 钢 刀 具 中沉 积镀 膜 ,可 提 高刀具 的抗 磨损性 、抗 粘屑
性 和 刀具 的切 削速度 , 同时经镀 膜 的刀具还 具有 高硬
度 、 高化学 稳定 性 、高韧性 、低 摩擦 系数等特 点 。 目
前 超 硬 沉 积 材 料 如 (i N T CN 多 镀 层 如 TM) 、 ir ,
性 好 、耐 腐 蚀 性 能 强 等 诸 多优 点 ; 中 间层 是 厚 度 为
金 结 构钢 、模 具钢 乃 至 有 色 金 属 等 其 他 材 料类 型 拓 宽。 出现 了在压 模上 使用 电弧蒸发 镀沉积 具 有高 附着 力 和耐磨 性 能的 CN涂层 的 PD法 ;在活塞 环 等零 件 r V 表 面采 用 离 子镀 法 镀 覆具 有 CN或 C2 r rN成分 、附着
特 点, 目前 , 一技 术 在建 筑 装饰 中得 到广 泛 应用 [。 这 2