表面技术3 表面淬火和形变强化
第四章 表面淬火及表面形变强化技术

第四章表面淬火和表面形变强化技术第一节表面淬火技术的原理与特点一、表面淬火技术的原理与分类(一)表面淬火的原理表面淬火是通过不同的热源对工件进行快速加热,当零件表层温度达到临界点以上(此时工件心部温度处于临界点以下)时迅速予以冷却,这样工件表层得到了淬硬组织而心部仍保持原来的组织。
适用材料:中碳钢或中碳合金钢。
工艺特点:快速加热,使工件表面迅速升温至淬火温度,而工件心部仍处于A1以下,这时立即喷水冷却,使工件表面层被淬硬成为马氏体,心部仍是原来的组织,保持着良好的韧性。
经表面淬火的工件,其表面硬度、耐磨性和疲劳强度均高,而心部则保留一定的塑性和韧性。
(二)表面淬火技术的分类根据加热方法不同,表面淬火可分为感应加热(高频、中频、工频)表面淬火、火焰加热表面淬火、电接触加热表面淬火、电解液加热表面淬火、激光加热表面淬火、电子束表面淬火等。
工业上应用最多的为感应加热和火焰加热表面淬火。
(三)表面淬火与化学热处理的区别表面淬火只对工件的表面或部分表面进行热处理,所以只改变表层的组织。
而心部或其它部分的组织仍保留原来的低硬度、高塑性和高韧性的性能,这样工件截面上由于组织不同性能也就不同。
表面淬火便于实现机械化、自动化,质量稳定,变形小,热处理周期短,费用少,成本低,还可用碳钢代替一些合金钢。
化学热处理是将工件表面渗进了某些化学元素的原子,改变了表层的化学成份,使表面能得到高硬度或某些特殊的物理、化学性能。
而心部组织成份不变,仍保留原来的高塑性。
高韧性的性能,这样在工件截面上就有截然不同的化学成份与组织性能。
化学热处理生产周期长,不便于实现机械化、自动化生产,工艺复杂,质量不够稳定,辅助材料消耗多、费用大、成本高,许多情况下还需要贵重的合金钢。
化学热处理只在获得表面层的更高硬度与某些特殊性能及心部的高韧性等方面优于表面淬火。
第二节感应加热表面淬火一、感应加热表面淬火法的基本原理(一)感应加热表面淬火法定义感应加热表面淬火法是采用一定方法使工件表面产生一定频率的感应电流,将零件表面迅速加热,然后迅速淬火冷却的一种热处理操作方法。
6-表面淬火和表面强化

第一节 表面淬火技术的原理和特点 一、表面淬火技术的原理(请同学记录) 采用特定热源将钢铁材料表面快速加热到 AC3(亚共析钢)或者AC1(过共析钢)之上,然
后使其快速冷却,并发生M相变,形成表面强化
层的工艺过程。
二、表面淬火技术具体分类(请同学记录) 感应加热表面淬火技术 火焰加热表面淬火技术
三、特点 线圈形状与工件形状有关,设备成本高 淬硬深度与功率有关(请同学记录)
* 高频淬火(电流频率为200-3000 kHz):淬硬层深度为0.5-2 mm
* 中频淬火(2500-8000 Hz):2-5 mm
* 工频淬火(50 Hz):10-15 mm
对于形状复杂的零件,难以保证获得均匀的表面淬火层 尖角效应:感应加热容易使零件的尖角棱边处过热
喷水冷却 马氏体 较深
>107 <10-7 <0.2
自淬火 大量晶体 缺陷
10-100 10-100 10-15
喷水冷却 马氏体 深 水冷 马氏体 深
操作方便, 适合野外 作业
<1 0.1-1.2
自淬火 隐针马氏 体 很浅
<0.01 <0.35
自动淬火 马氏体 较浅 原位淬火
0.1-0.5
自淬火 隐针马氏 体 最浅 工件变形 小
受控喷丸技术以强化工件表面为目的 清理喷丸是利用冲击力和摩擦力清理材 料表面,如:毛刺、氧化皮、熔渣等。
2.表面形貌和亚结构(请同学记录) • 外形变化:变形层
• 组织结构:强化层内形成了密度极高(>10¹²/厘米²)的位错,并且
在随后的交变应力或温度(或二者)的作用下,位错逐渐排列规则, 形成多边形化,由此强化层内逐渐形成更加微小的亚晶粒(亚结构)。
Re 第四章 表面淬火和表面形变强化

激光焊接
四、电子束淬火
电子束淬火技术是以高能电子束作为能 源进行表面相变硬化的热处理工艺。原 理与激光淬火类似,不需要介质,工件 对于电子束的吸收率比激光大得多,淬 硬层深度也高于激光淬火。 限制:在真空环境下进行。限制使用范 围,在工业中已经被激光淬火取代。
应用:
广泛用于: 弹簧、齿轮、链条、轴等零部件。 某大汽车公司对喷丸处理的齿轮箱 传动轴和齿轮进行疲劳实验(材料 40CrMo,HRC58-62).疲劳寿命提 高三倍以上。
二、表面滚压技术 表面滚压技术就是用辊轮、辊轴对零件表面进行滚压 或者挤压,通过塑性变形,形成强化层。对于圆角、 沟槽等皆可通过滚压获得表层形变强化,并引入残余 压应力,深度能达5mm. 缺点是:只能强化一些形状简单的平板类零件、轴类 零件和沟槽类零件。复杂零件无法应用。
感应加热表面淬火分类
(1)高频淬火: 20万-30万Hz, 0.5-2.5mm, 小模数齿轮、中小 型轴类零件。 (2) 中频淬火: 2500-8000Hz,3-6mm,直径较大轴类零件、 模数较大齿轮。 (3) 工频淬火: 50Hz,10-15mm, 火车车轮,轧辊。
2.特点 (1)加热速度快,时间短,奥氏体不易长 大,淬火后得到非常细小 的隐晶马氏体, 比普通淬火硬度高HRC2-3. (2)感应加热淬火后,工件表层疲劳强度 高。因为马氏体转变体积膨胀,在工件表 层产生残余压应力,提高疲劳强度。 (3)加热速度快,无保温时间,钢件表面 不易氧化、脱碳,心部未加 热,钢件变形 小。 (4)生产效率高。 缺点:设备昂贵,不适合单件生产,形状 复杂的零件感应器不好制备。
金属表面处理工艺及技术
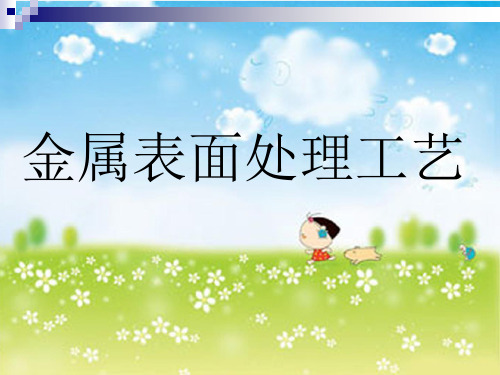
四 喷涂的涂层厚度为几十微米至数毫米.
二.热喷涂的特点
一 工艺灵活,适用范围广.热喷涂施工对象可大可小,小的可 到一0mm内孔[线爆喷涂],大的可到桥梁、铁塔[火焰线材喷 涂或电孤喷涂],可在室内喷涂,也可在野外现场作业;可 整体喷涂,也可以局部喷涂.
低碳钢渗碳缓冷后的组织
五渗碳后的热处理 淬火+低温回火, 回火温度为一六0-一八0℃.淬火方法有: ⑴ 预冷淬火法 渗碳后预冷到略高于Ar一温度直接淬火.
渗碳后的热处理示意图
⑵一次淬火法:即渗碳缓冷后重新加热淬火. ⑶ 二次淬火法: 即渗碳缓冷后第一次加热为心部Ac三+三0-五0℃,细化心部;
金属表面处理工艺
一、表面热处理
一、表面淬火 表面淬火是指在不改变钢的化学成分及心部组织情
况下,利用快速加热将表层奥氏体化后进行淬火以强 化零件表面的热处理方法.
火焰加热 感
应 加 热
表面淬火目的: 一 使表面具有高的硬度、耐磨性和疲劳极限; 二 心部在保持一定的强度、硬度的条件下,具有足够的塑
碳钢. 常用钢号为三八CrMoAl. ⑵氮化温度为五00-五七0℃ 氮化层厚度不超过0.六-0.七
mm.
井式气体氮化炉
⑶常用氮化方法 气体氮化法与离子氮化法. 气体氮化法与气体渗碳法类似,
渗剂为氨. 离子氮化法是在电场作用下,
使电离的氮离子高速冲击作为 阴极的工件.与气体氮化相比, 氮化时间短,氮化层脆性小.
第二次加热为Ac一+三0-五0℃,细化表层.
渗碳后的热处理示意图
常用方法是渗碳缓冷后,重新加热到Ac一+三0-五0℃淬火+低 温回火.此时组织为:
4章:表面淬火和表面形变强化技术

• 受控喷丸对材料表面 形貌与性能的影响: 形貌与性能的影响: 1)对硬度的影响 弹丸强度或动能越大, 弹丸强度或动能越大, 则变形层深度越大; 则变形层深度越大; 弹丸硬度越高, 弹丸硬度越高,喷丸 层深度越深; 层深度越深; 被喷零件的硬度越高, 被喷零件的硬度越高, 则喷丸强化层越浅。 则喷丸强化层越浅。
第五节 高能密束表面淬火技术
• 高能密束(>103W/cm2)离子束、激光束、 高能密束( 离子束、激光束、 电子束( 电子束(108~9W/cm2) • 特点: 特点: • 能量作用集中,能量利用率高,具选择性; 能量作用集中,能量利用率高,具选择性; • 加热速度快,温度梯度大,自冷淬火,晶 加热速度快,温度梯度大,自冷淬火, 粒细化和超细化; 粒细化和超细化; • 非接触加热,无机械力,热应力小; 非接触加热,无机械力,热应力小;
第一节 表面淬火技术的原理和特点
三、表面淬火层的组织与性能 1.组织 1.组织 • 一般可分为淬火区、 一般可分为淬火区、 • 过渡区、 过渡区、 • 及心部组织; 及心部组织; 2.性能 2.性能 • 大于普淬2~5HRC, 大于普淬2 主要是因为晶粒和精细结构的细化, 主要是因为晶粒和精细结构的细化,以及冷却 快等原因。此外, 快等原因。此外,表面压应力有效抑制裂纹 的萌生与扩展过程,因此可提高疲劳强度。 的萌生与扩展过程,因此可提高疲劳强度。
第二节 感应加热淬火技术
一、基本原理 • 高频磁场→感应电流→集肤效应→电流密度 高频磁场→感应电流→集肤效应→ 电阻)→加热→ )→加热 (电阻)→加热→使受热区快速 升温至Ac3,Acm之上。 Ac3,Acm之上 升温至Ac3,Acm之上。 • 感应加热的工艺参数选择: 感应加热的工艺参数选择: 线圈形状与工件形状有关; 线圈形状与工件形状有关; 功率与淬硬深度有关; 功率与淬硬深度有关;
常用金属表面处理工艺及技术

③ 工件应力变形小。基体可保持较低的温度,工件产生的应力 变形很小。
n ⑶ 激光热处理: 利用高能量密度的 激光对工件表面进行加热的方法。 效率高,质量好。
火焰加热表面淬火
激光表面热处理
火焰加热表面淬火示意图
二、化学表面热处理
n 化学热处理是将工件置于特定介质中加热保温,使 介质中活性原子 渗入工件表层从 而改变工件表层 化学成分和组织, 进而改变其性能 的热处理工艺。
n 将工件放入密封炉内,在高 温渗碳气氛中渗碳。
n 渗剂为气体 (煤气、液化气 等)或有机液体(煤油、甲醇 等)。
n 优点: 质量好, 效率高; n 缺点: 渗层成分与深度不易
控制
气体渗碳 法示意图
n ⑵ 固体渗碳法 n 将工件埋入渗剂中,装箱密封后在高温下加热渗碳。 n 渗剂为木炭。 n 优点:操作简单; n 缺点:渗速慢,劳动条件差。
离子氮化炉
n ⑷氮化的特点及应用 n 氮化件表面硬度高(69~72HRC),耐磨性高。 n 疲劳强度高。由于表面存在压应力。
氮 化 层 组 织
38CrMoAl氮化层硬度
n ⑶工件变形小。原因是氮化温度低,氮化后不需进行热处理。 n ⑷ 耐蚀性好。因为表层形成的氮化物化学稳定性高。 n 氮化的缺点:工艺复杂,成本高,氮化层薄。 n 用于耐磨性、精度要求高的零件及耐热、耐磨及耐蚀件。如
无数个小锤锤击金属表面,使零件表层和次表层发生一定的 塑性变形而实现强化的一种技术。 n 应用:形状较复杂的零件 n 在磨削、电镀等工序后进行
2、滚压处理 n 利用自由旋转的淬火钢滚子对钢件的已加工表面进行滚压,
使之产生塑性变形,压平钢件表面的粗糙凸峰,形成有利的 残余压应力,从而提高工件的耐磨性和抗疲劳能力。 n 应用:圆柱面、锥面、平面等形状比较简单的零件
表面处理办法第五讲表面淬火与表面形变强化

0.5mm的零件表层在极短的时间内加热,然后靠自身迅速冷却, 达到淬火目的。
特点:变形量较小,不必回火。主要用于小、薄的零件,可 明显提高质量,降低成本。
表面处理办法第五讲表面淬火与表 面形变强化
第四章 表面淬火和表面形变强化
表面处理办法第五讲表面淬火与表 面形变强化
热处理知识(复习)
➢ 热处理的本质:通过改变 组织达到改善金属的机械性能。
➢ 热处理的4个工艺参数:加 热速度、加热温度、保温时间、 冷却速度。
➢ 热处理的4种工艺:退火、 正火、淬火、回火。
表面处理办法第五讲表面淬火与表 面形变强化
Die Hardening
表面处理办法第五讲表面淬火与表 面形变强化
第三节 火焰表面加热淬火技术 (flame surface hardening)
用火焰将工件表面快速 加热到Ac3或Acm以上,然后 用水快速冷却,以在表层获 得马氏体组织。
表面处理办法第五讲表面淬火与表 面形变强化
1 火焰加热的特点
燃料名称 发热值
火焰温度 ℃ 氧与燃料 空气与燃料
kcal/m3 氧助燃 空气助燃 气体积比 气体体积比
乙炔
12754
天然气(甲烷) 8900
丙烷
2435
城市煤气 2670 ~ 8010
煤油
*
3100 2700 2640 2540 2300
2320 1875 1925 1985
—
1.0 1.75 4.0
45钢的淬硬区组织为马氏体;过 渡区组织为马氏体+铁素体;心部 组织为珠光体+铁素体。 表面处理办法第五讲表面淬火与表
表面技术3 表面淬火和形变强化

45的过渡区在相同温度下 大于T8的过渡区宽度。
过渡区的宽窄对钢的残 余应力分布有重要影响, 其宽窄程度主要取决于 温度梯度。
预备热处理为表面淬火作准备,以获得最终的心部组织。方法有 调质或正火等。
③ 表面淬火后的组织
表层组织为回火马氏体,心部组织为回火索氏体(调质)或铁素 体加索氏体(正火)。
7. 特点
② 升温速度快,保温时间极短。奥氏体形核多又不易长大,因此淬 火后得到细小的隐晶马氏体,故表面硬度比一般淬火的高2~3HRC。 ③ 工件表层强度高。由于马氏体转变产生体积膨胀,在工件表面产 生很大的残余压应力,因此可以显著提高疲劳强度并降低缺口敏感性。 ④ 工件的耐磨性比普通淬火高。这与奥氏体晶粒细化、表面硬度高 以及表面压应力状态等因素有关。 ⑤ 由于加热速度快,无保温时间,工件一般不产生氧化和脱碳问题, 又因工件内部未被加热,故工件淬火变形小。 ⑥ 生产率高,便于实现机械化和自动化;淬火层深度易于控制,适 于批量生产形状简单的机器零件,因此得到广泛的应用。 缺点:设备费用昂贵,不适用于单件生产。
1.原理
利用高能量的激光扫描工件表面,使工件表面快速加热.工件基体仍处
于冷态。由于热传导的作用,表面热量迅速传到工件其它部位,在瞬间
进行自冷淬火,实现工件表面相变硬化。
2. 组织
淬硬区、过渡区、心部组织(基材) 单道硬化区域小 硬度大幅度提高、硬度分布不均匀
淬硬区
过渡区
基材
3. 工艺
影响淬硬层性能的主要因素 (1)材料成分
表面淬火和表面形变强化技术

特点: 工件对电子束的吸收率高 淬硬层深度更高,无氧化、无污染 必须在真空环境下进行
电子束淬火技术逐步被激光淬火技术所取 代,工业应用较少。
第二十六页,共39页。
电子束与激光束的特点(tèdiǎn)比较:
可大幅度提高材料表面硬度、耐磨性
和疲劳强度。
(缺点)设备成本较高;
尖角效应;
一般只适合形状简单的零件。
第十一页,共39页。
三、感应(gǎnyìng)加热淬火工艺流程
回火(huí huǒ) 温度较低
自回火(huí huǒ)
第十二页,共39页。
4.3 火焰(huǒyàn)加热表面淬火技术
火焰加热(jiā rè)表面淬火技术是应用历史最长的表面淬火技术之一。
工件表面吸收高速运动弹丸的动能后产生塑性流变和加工硬化(位 错与孪晶),同时使工件表面保留残余压应力。
第三十二页,共39页。
曲 轴 曲轴
(( qq ūū
z
h
曲轴喷丸强化机
ó
u
工艺(设备)种类:
)) 喷 喷
叶轮式(抛丸式)
丸 丸
压缩空气式(干喷式和湿喷式)
强 强 化 化
机 机
弹丸种类:
铸铁(zhùtiě)丸、铸钢丸、不锈
第二十八页,共39页。
电接触(jiēchù)加热表面淬火原理图
电解液加热表面淬火原理图
特点: (优点(yōudiǎn))工艺简单,设备费用低,工件变形小。 (缺点)淬硬层薄,对形状复杂(电阻接触加热法)、尺寸很大(电解液加 热法)的工件不适用。
第二十九页,共39页。
金属的表面强化工艺
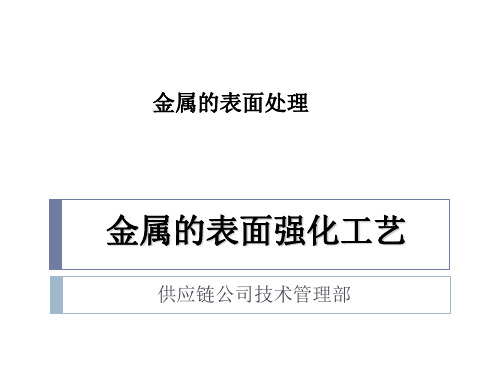
• 其标识为: 电镀层GB/T 9799-Fe/SR(200)3/Zn25/ER(190)8/D/T2
镀铜特点
铜镀层
BRIGHT
光亮 好的
EASILY BUFFED
GOOD ELONGATION GOOD MICROTHROW
容易抛光
好的延展性 好的微观均镀性
GOOD LEVELING 填平 DUCTILE
表面覆层强化是通过物理或化学的方法在金属表面
涂覆一层或多层其他金属或非金属的表面强化工艺。
目的:提高钢件的耐磨性、耐蚀性、耐热性或进行
表面装饰。
1、金属喷涂技术
将金属粉末加热至熔化或半熔化状态,用高压气流使其雾
化并喷射于工件表面形成涂层的工艺称为热喷涂。
利用热喷涂技术可改善材料 的耐磨性、耐蚀性、耐热性
塑性变形而实现强化的一种技术。
应用:形状较复杂的零件 在磨削、电镀等工序后进行
2、液压处理
利用自由旋转的淬火钢滚子对钢件的已加工表面进行滚压,
使之产生塑性变形,压平钢件表面的粗糙凸峰,形成有利的
残余压应力,从而提高工件的耐磨性和抗疲劳能力。
应用:圆柱面、锥面、平面等形状比较简单的零件
三、表面覆层
硬度低,不耐磨
锌离子对人体有
害 钝化处理可提高
镀层保护性能
40
电镀锌应用
镀锌桥架
富士康热浸镀锌机箱
广泛用于钢铁零部件和结构件的防护镀层。近年来,使 用热浸镀锌表面对防腐能力非常强,但其价格相对很高。
41
锌镀层钝化铬酸盐转化膜的类型,外观和表面密度
类型 代号 A 名称 光亮膜 典型外观 透明,透明至浅蓝色
- 1、下载文档前请自行甄别文档内容的完整性,平台不提供额外的编辑、内容补充、找答案等附加服务。
- 2、"仅部分预览"的文档,不可在线预览部分如存在完整性等问题,可反馈申请退款(可完整预览的文档不适用该条件!)。
- 3、如文档侵犯您的权益,请联系客服反馈,我们会尽快为您处理(人工客服工作时间:9:00-18:30)。
6. 感应加热表面淬火工艺
①一般用于中碳钢和中碳合金钢,用以制造机床、汽车及拖拉 机齿轮、轴等。也可以采用碳素工具钢和低合金工具钢,用以 制造量具、模具、锉刀等。 ②表面淬火前的预备热处理
第三节
1. 原理
将高温火焰或燃烧着的炽热气 体喷向工件表面,使其迅速加 热到淬火温度,然后在一定淬 火介质中冷却。
火焰淬火
应用历史最长的表面淬火技术之一
2. 特点
优点:设备简单,成本低,可对大型零件局部实现表面淬火。 缺点:加热温度不易控制,噪音大,劳动条件差,混合气体 不够安全,不易获得薄的表面淬火层。
(1)优点 淬火硬度高,能量密度高,加热速度快,不需要淬火介质,工件变 形小,加热层深度和加热轨迹易于控制(淬火部位可控),无氧化、 无污染,易于实现自动化。 (2)缺点
硬度分布不均匀,单道激光淬火区域小,大面积淬火时容易产生回 火软带。设备成本高、生产成本较高(能量转换效率低)。
5. 应用
20世纪70年代欧美等国在汽车行 业中最先应用激光淬火。1974年 GE公司使汽车转向器壳体内腔(可 锻铸铁)的耐磨性提高10倍。
硬化层深度:硬化层深度总小于感应电流透入深度
2. 感应加热温度和方式的选择
淬火加热温度:一般高频加热淬火温度可比普通加热淬火温 度高30-200℃。加热速度较快的,采用较高的温度。淬火前 的原始组织也不同,也可适当地调整淬火加热温度。调质处 理的组织比正火的均匀,可采用较低的温度。 感应加热方式:一种称同时加热法,即对工件需淬火表面同 时加热,一般在设备功率足够、生产批量比较大的情况下采 用;另一种称连续加热法,即对工件需淬火部位逐渐加热, 通过感应器与工件之间的相对位移速度来实现。
3)对疲劳寿命与抗应力腐蚀的影响
可大幅度提高材料的疲劳寿命和抗应力腐蚀能 力。例如,焊缝。
5. 喷丸应用
主要应用于那些需要改善疲劳强度和抗应力腐蚀能 力零件上。如弹簧、齿轮、链条、轴、叶片、火车 轮等。
钢板弹簧(疲劳寿命提高5倍)
渗碳齿轮(疲劳寿命提高4倍)
第九节 滚压强化
1.定义
3. 应用
主要用于单件、小批量及大型零件(如大型齿轮、轴、轧辊 等)的表面淬火。
近年来,7CrSiMnMoV专用火焰淬火模具钢的研制使其在汽车 覆盖件制造中占据主导地位(节省工时,保证模具精度)。
第四节 接触电阻加热淬火
1. 定义
2. 原理
变压器二次侧线圈供给低电 压大电流,在电极(铜滚轮 或碳棒)与工件表面接触处 产生局部电阻加热。当电流 足够大时,产生的热能足以 使此部分工件表面温度达到 淬火临界温度以上,然后靠大
类,喷丸机又有干喷和湿喷之分。 干喷式工作条件差,湿喷式是将弹
丸混合在液体中成悬浮状后喷丸,
工作条件有所改善。
喷是以压缩空气作为动力 将砂料或丸料喷到材料表 面;抛是将丸料以高速旋 转时产生的离心力的方法, 冲击材料表面,达到清除 和一定的粗糙度。 叶轮式喷丸机
第七节 电子束淬火
采用高能密度电子束对材料表面进行相变硬化的热 处理工艺。
原理
动能→热能
工件对电子束的吸收率比激光束大得多, 淬硬层深度也高于激光束淬火。
特点
缺点
必须是真空环境,限制了其使用范围。
第八节 表面形变强化
其理论基础是加工硬化,即通过机械手段(喷丸、滚压等)在 金属表面产生塑性变形,使表面形成加工硬化层,其深度可 达0.5~1.5 mm。 结果:亚晶粒极大细化,位错密度增加,晶格畸变增大;形 成高残余压应力。 常用方法——喷丸、滚压等,而尤以喷丸应用最广。
表面热处理:仅对钢的表面加热、冷却而不改 变其成分的热处理工艺,也叫表面淬火。
第一节 表面淬火技术的原理和特点
1. 表面淬火技术的原理与方法
用特定热源将钢铁材料表面快速加热到Ac3(对亚共析钢)或者
Ac1(对过共析钢)之上(奥氏体化),然后使其快速冷却并发生
马氏体相变,形成表面强化层的工艺过程。
种类:感应加热淬火、火焰淬火、激光淬火、电子束淬火等。 适用对象:中碳钢、球墨铸铁(C含量:0.35-1.20wt%)
利用触头和工件间的接触电阻使工件表面加热,并 借助本身未加热部分的热传导来实现淬火冷却。
3. 特点和应用
1. 设备简单、操作方便、工件变形小
2. 淬火后表面硬度可达50~55HRC 3. 淬火后不需回火 4. 淬硬层薄(0.15-0.30mm),金相组织及硬度 均匀性差。 应用:机床铸铁导轨、汽缸套、曲轴、工具、 模具等
3. 冷却方式和冷却介质的选择
最常用的冷却方式是喷射冷却法和漫液冷却法
喷射冷却法即当感应加热终了时把工件置于喷射器之中,向 工件喷射淬火介质进行淬火冷却。其冷却速度可以通过调节 液体压力、温度及喷射时间来控制。 漫液淬火法即当工件加热终了时,浸入淬火介质中进行冷却。 对细、薄工件或合金钢齿轮,为减少变形、开裂、可将感应 器与工件同时放入油槽中加热,断电后冷却。
提高加热速度,可增大 温度梯度,显著减少过 渡区宽度。
第二节 感应淬火
应用最广泛的表面淬火技术。
1. 原理
图 感应加热表面淬火原理图
当感应圈中通过一定频率交流电时,在其内外将产生与电流变 化频率相同的交变磁场。将工件放入感应圈内,在交变磁场作 用下,工件内就会产生与感应圈频率相同而方向相反的感应电 流。感应电流沿工件表面形成封闭回路,通常称之为涡流。
第五节 电解液加热淬火
将工件淬火部位浸入电解液,工件接阴极,电解槽接阳极;通电 后,在阴极上生成氢气,形成氢气膜,电流流经电阻大的氢气膜 时产生大量的热量,迅速将工件表层加热到淬火温度;断电后氢 气膜消失,电解液变为冷却介质,使工件表层淬火。
设备简单,淬火变形小,适用于形状简单小件的批量生产
第六节 激光淬火
4. 回火工艺
感应加热淬火后一般只进行低温回火。其目的是为了降低残 余应力和脆性,而又不致降低硬度。一般采用炉中回火、自 回火和感应加热回火。
5. 感应加热表面淬火设备
15000 250000 f x2 x2 60000 最理想的情况是当 热=2x,f= 2 x
① 高频感应加热
电流频率范围250~300kHz,淬硬层深度x为 0.5~2.0mm,适用于中小模数的齿轮及中小 尺寸的轴类零件。
此涡流能将电能变成热能,使工件加热。涡流在被加热工件中 的分布由表面至心部呈指数规律衰减。因此涡流主要分布在工 件表面,工件内部几乎没有电流通过。这种现象叫做表面效应 或集肤效应。 感应加热就是利用集肤效应,依靠电流热效应把工件表面迅速 加热到淬火温度的。当工件表面在感应圈内加热到相变温度时, 立即喷水或浸水冷却,实现表面淬火工艺。
1.原理
利用高能量的激光扫描工件表面,使工件表面快速加热.工件基体仍处
于冷态。由于热传导的作用,表面热量迅速传到工件其它部位,在瞬间
进行自冷淬火,实现工件表面相变硬化。
2. 组织
淬硬区、过渡区、心部组织(基材) 单道硬化区域小 硬度大幅度提高、硬度分布不均匀
淬硬区
过渡区
基材
3. 工艺
影响淬硬层性能的主要因素 (1)材料成分
前
言
表面和心部性能要求不同的零件实例
工作条件:磨损、冲击载荷 性能要求:高耐磨性+高疲劳强度(表)、高冲击韧性(心)
在这种情况下,单从材料选择入手或采用普通热 处理方法,都不能满足其要求。
解决这一问题的方法是表 面热处理和化学热处理
低碳钢 :可满足心部要求, 表面要求不能满足; 高碳钢: 可满足表面要求, 心部要求不能满足;
淬硬性、淬透性 影响淬硬层深度 和硬度
②工艺参数
淬火层宽度取决于光斑直径D 淬硬深度h:激光功率P、D和 扫描速度V共同决定,主要关 系:hP/(DV)
③表面预处理
a. 表面组织准备:较细的表面组织(细片状珠光体、回 火马氏体或奥氏体) 。
b. 表面“黑化”处理:磷化法、碳素法、氧化物涂层
4.特点
预备热处理为表面淬火作准备,以获得最终的心部组织。方法有 调质或正火等。
③ 表面淬火后的组织
表层组织为回火马氏体,心部组织为回火索氏体(调质)或铁素 体加索氏体(正火)。
7. 特点
② 升温速度快,保温时间极短。奥氏体形核多又不易长大,因此淬 火后得到细小的隐晶马氏体,故表面硬度比一般淬火的高2~3HRC。 ③ 工件表层强度高。由于马氏体转变产生体积膨胀,在工件表面产 生很大的残余压应力,因此可以显著提高疲劳强度并降低缺口敏感性。 ④ 工件的耐磨性比普通淬火高。这与奥氏体晶粒细化、表面硬度高 以及表面压应力状态等因素有关。 ⑤ 由于加热速度快,无保温时间,工件一般不产生氧化和脱碳问题, 又因工件内部未被加热,故工件淬火变形小。 ⑥ 生产率高,便于实现机械化和自动化;淬火层深度易于控制,适 于批量生产形状简单的机器零件,因此得到广泛的应用。 缺点:设备费用昂贵,不适用于单件生产。
2. 表面淬火技术与常规淬火技术的区别
表面淬火加热、冷却速度很快,与普淬在相变及特征 存在区别:
1) 快热使Ac3,Acm,但使Ac1有限;快热使A晶 粒细化,加热很快甚至使钢产生无扩散A相变;
冷速比普淬也快,所以,硬度 比普淬要高,与方法有关。
2) 快热使渗C体难充分溶解,形成A成分相当不均 匀,包括未溶C化物,高C偏聚区(原P)和贫C 区(原F) 促使A分解,缩短A的孕育期, 随 后淬火形成低C马氏体和高C马氏体区域,造成 显微硬度不均匀。 因此,表面淬火前,需预先热处理(调质 或正火),使碳化物或自由铁素体均匀、 细小分布,以便有利于快速加热时奥氏体 的均匀化。