三联齿轮套加工工艺分析及数控编程
轴套零件的数控工艺分析与编程

轴套零件的数控工艺分析与编程轴套是一种常见的机械零件,广泛应用于各种机械设备中。
数控工艺分析与编程是指通过数控编程的方式对轴套的加工工艺进行分析,并编写相应的数控程序,以实现对轴套的高效、精确加工。
下面将详细介绍轴套零件的数控工艺分析与编程过程。
一、数控工艺分析数控工艺分析是指分析轴套零件的加工特点和要求,并确定相应的加工工艺路线和具体的加工参数。
具体分析如下:1.轴套的加工特点和要求:轴套通常由高强度的金属材料制成,具有高精度、高强度和耐磨损的特点。
在进行数控加工时,需要注意减小误差、提高加工精度和表面质量。
2.加工工艺路线:根据轴套的结构、尺寸和加工要求,确定加工工艺路线。
一般来说,轴套的加工工艺路线包括粗加工、精加工和表面处理等步骤。
-粗加工:主要包括车削、铣削、钻削等工艺,用于将原材料加工成近似形状的轴套毛坯。
-精加工:主要包括车削、钻削、拉削等工艺,用于将毛坯进一步加工成精确形状和尺寸的轴套。
-表面处理:主要包括抛光、热处理等工艺,用于提高轴套的表面质量和硬度。
3.加工参数确定:根据轴套的材料和加工要求,确定各工艺步骤对应的切削速度、进给速度、切削深度和切削用液等加工参数。
二、数控编程数控编程是指根据数控设备的编程语言和指令集,编写相应的数控程序,实现对轴套的自动化加工。
具体编程步骤如下:1.绘制零件图纸:根据轴套的几何形状和尺寸要求,绘制轴套的详细图纸。
图纸应包括轴套的三维模型、尺寸和加工要求等信息。
2.分析加工特点:根据轴套的加工特点和要求,对加工工艺进行分析,并确定加工工艺路线和加工参数。
3.编写数控程序:根据加工工艺路线和加工参数,编写数控程序。
数控程序是指通过一系列的数控指令,控制数控机床进行轴套的加工。
4.调试和优化:将编写好的数控程序输入数控机床,并进行调试和优化,确保加工过程的准确性和稳定性。
5.加工监控和质量检验:在整个加工过程中,需要进行对加工状态的监控和质量检验,确保轴套的加工质量符合要求。
轴套零件的工艺分析和编程毕业设计
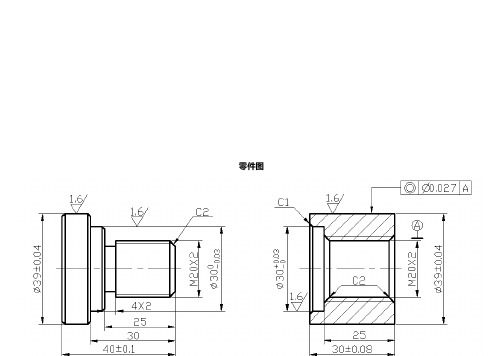
零件图轴套三维图轴套三维图轴套类零件旳工艺设计与加工摘要:伴随数控技术旳发展,数控技术旳应用不仅给老式制造业带来了革命性旳变化,使制造业成为工业化旳象征,并且伴随数控技术旳不停发展和应用领域旳扩大,它对国计民生旳某些重要行业旳发展起着越来越重要旳作用。
伴随科技旳发展,数控技术也在不停旳发展更新,目前数控技术也称计算机数控技术,加工软件旳更新快,CAD/CAM旳应用是一项实践性很强旳技术。
如像UG , PRO/E , Cimitron , MasterCAM ,CAXA制造工程师等。
数控技术是技术性极强旳工作,尤其在模具领域应用最为广泛,因此这规定从业人员具有很高旳机械加工工艺知识,数控编程知识和数控操作技能。
本文重要通过c车削加工配合件旳数控工艺分析与加工,综合所学旳专业基础知识,全面考虑也许影响在车削加工中旳原因,设计其加工工艺和编辑程序,完毕配合规定。
关键词: 车削;CAD/CAM;配合件零件加工前言毕业设计是专业教学工作旳重要构成部分和教学过程中旳重要实际性环节。
毕业设计旳目旳是:通过设计,培养我们综合运用所学旳基础理论知识,专业理论知识和某些有关软件旳学习,去分析和处理本专业范围内旳一般工程技术问题旳能力,培养我们建立对旳旳工艺设计思维,学会查找工具书,掌握数控工艺设计旳一般程序,规范和措施。
本次设计选择旳课题为轴类零件旳车削加工工艺设计及其数控加工程序编制。
这次毕业设计让我们对机械制图旳基础知识有了深入旳理解,同步也为我们从事绘图工作奠定了一种良好旳基础。
并锻炼了自己旳动手能力,到达了学以致用旳目旳。
它是一次专业技能旳重要训练和知识水平旳一次全面体验,是学生毕业资格认定旳重要根据,同步也为我们未来走向工作岗位奠定了必要旳理论基础和实践经验。
目录序言第一章零件工艺分析 ............................................ 错误!未定义书签。
1.1零件旳分析 ................................................. 错误!未定义书签。
三联齿轮机工艺分析讲解
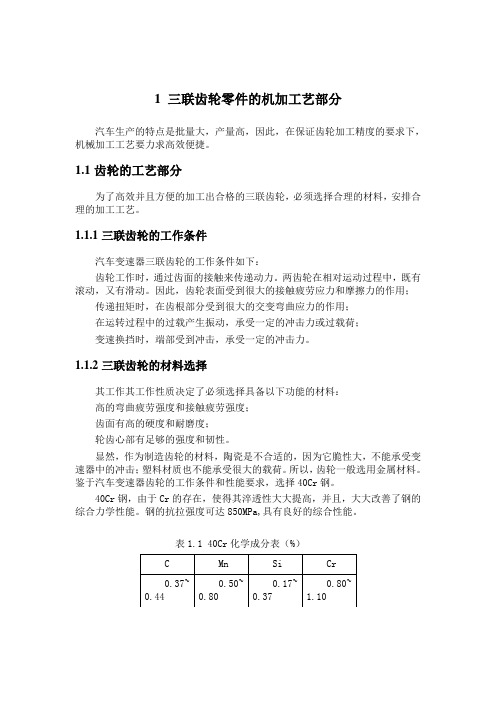
1 三联齿轮零件的机加工艺部分汽车生产的特点是批量大,产量高,因此,在保证齿轮加工精度的要求下,机械加工工艺要力求高效便捷。
1.1齿轮的工艺部分为了高效并且方便的加工出合格的三联齿轮,必须选择合理的材料,安排合理的加工工艺。
1.1.1三联齿轮的工作条件汽车变速器三联齿轮的工作条件如下:齿轮工作时,通过齿面的接触来传递动力。
两齿轮在相对运动过程中,既有滚动,又有滑动。
因此,齿轮表面受到很大的接触疲劳应力和摩擦力的作用;传递扭矩时,在齿根部分受到很大的交变弯曲应力的作用;在运转过程中的过载产生振动,承受一定的冲击力或过载荷;变速换挡时,端部受到冲击,承受一定的冲击力。
1.1.2三联齿轮的材料选择其工作其工作性质决定了必须选择具备以下功能的材料:高的弯曲疲劳强度和接触疲劳强度;齿面有高的硬度和耐磨度;轮齿心部有足够的强度和韧性。
显然,作为制造齿轮的材料,陶瓷是不合适的,因为它脆性大,不能承受变速器中的冲击;塑料材质也不能承受很大的载荷。
所以,齿轮一般选用金属材料。
鉴于汽车变速器齿轮的工作条件和性能要求,选择40Cr钢。
40Cr钢,由于Cr的存在,使得其淬透性大大提高,并且,大大改善了钢的综合力学性能。
钢的抗拉强度可达850MPa,具有良好的综合性能。
表1.1 40Cr化学成分表(%)表1.2 40Cr机械性能切削加工性分析:为了改善40Cr的锻造组织及切削加工性能,首先选择合理的预备热处理工艺,也就是才用正火热处理。
因为正火既可以细化晶粒,又可以改善切削性能,同时也有利于消除内应力。
正火后,锻造组织得到改善,硬度降低了,有利于切削加工,并为调质热处理做组织准备。
这样以来,在粗加工时,就可以去除大部分毛坯余量。
为了获得40Cr钢的良好的综合力学性能,需要进行淬火加高温回火热处理,也就是调质处理。
处理后的40Cr钢的组织是回火索氏体,它有较高的韧性、塑性和强度。
这样就为加工带来了不便,因此,在半精加工和精加工时,只能是小加工余量加工。
齿轮加工工艺过程和分析

齿轮的生产过程一.齿轮的主要加工面1.齿轮的主要加工表面有齿面和齿轮基准表面,后者包括带孔齿轮的基准孔、切齿加工时的安装端面,以及用以找正齿坯位置或测量齿厚时用作测量基准的齿顶圆柱面。
2.齿轮的材料和毛坯常用的齿轮材料有15钢、45钢等碳素结构钢;速度高、受力大、精度高的齿轮常用合金结构钢,如20Cr,40Cr,38CrMoAl,20CrMnTiA等。
齿轮的毛坯决定于齿轮的材料、结构形状、尺寸规格、使用条件及生产批量等因素,常用的有棒料、锻造毛坯、铸钢或铸铁毛坯等。
二、直齿圆柱齿轮的主要技术要求,1.齿轮精度和齿侧间隙GBl0095《渐开线圆柱齿轮精度》对齿轮及齿轮副规定了12个精度等级。
其中,1~2级为超精密等级;3—5级为高精度等级;6~8级为中等精度等级;9~12级为低精度等级。
用切齿工艺方法加工、机械中普遍应用的等级为7级。
按照齿轮各项误差的特性及它们对传动性能的主要影响,齿轮的各项公差和极限偏差分为三个公差组(表13—4)。
根据齿轮使用要求不同,各公差组可以选用不同的精度等级。
齿轮副的侧隙是指齿轮副啮合时,两非工作齿面沿法线方向的距离(即法向侧隙),侧隙用以保证齿轮副的正常工作。
加工齿轮时,用齿厚的极限偏差来控制和保证齿轮副侧隙的大小。
2.齿轮基准表面的精度齿轮基准表面的尺寸误差和形状位置误差直接影响齿轮与齿轮副的精度。
因此GBl0095附录中对齿坯公差作了相应规定。
对于精度等级为6~8级的齿轮,带孔齿轮基准孔的尺寸公差和形状公差为IT6-IT7,用作测量基准的齿顶圆直径公差为IT8;基准面的径向和端面圆跳动公差,在11-22μm之间(分度圆直径不大于400mm的中小齿轮)。
3.表面粗糙度齿轮齿面及齿坯基准面的表面粗糙度,对齿轮的寿命、传动中的噪声有一定的影响。
6~8级精度的齿轮,齿面表面粗糙度Ra值一般为0.8—3.2μm,基准孔为0.8—1.6μm,基准轴颈为0.4—1.6μm,基准端面为1.6~3.2μm,齿顶圆柱面为3.2μm。
齿轮的数控加工程序
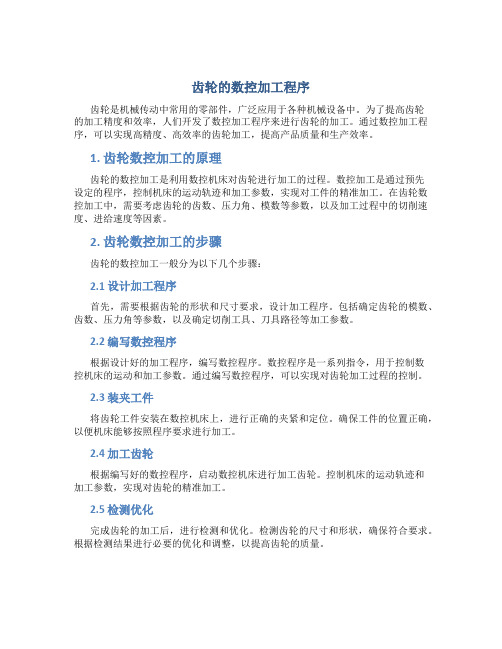
齿轮的数控加工程序齿轮是机械传动中常用的零部件,广泛应用于各种机械设备中。
为了提高齿轮的加工精度和效率,人们开发了数控加工程序来进行齿轮的加工。
通过数控加工程序,可以实现高精度、高效率的齿轮加工,提高产品质量和生产效率。
1. 齿轮数控加工的原理齿轮的数控加工是利用数控机床对齿轮进行加工的过程。
数控加工是通过预先设定的程序,控制机床的运动轨迹和加工参数,实现对工件的精准加工。
在齿轮数控加工中,需要考虑齿轮的齿数、压力角、模数等参数,以及加工过程中的切削速度、进给速度等因素。
2. 齿轮数控加工的步骤齿轮的数控加工一般分为以下几个步骤:2.1 设计加工程序首先,需要根据齿轮的形状和尺寸要求,设计加工程序。
包括确定齿轮的模数、齿数、压力角等参数,以及确定切削工具、刀具路径等加工参数。
2.2 编写数控程序根据设计好的加工程序,编写数控程序。
数控程序是一系列指令,用于控制数控机床的运动和加工参数。
通过编写数控程序,可以实现对齿轮加工过程的控制。
2.3 装夹工件将齿轮工件安装在数控机床上,进行正确的夹紧和定位。
确保工件的位置正确,以便机床能够按照程序要求进行加工。
2.4 加工齿轮根据编写好的数控程序,启动数控机床进行加工齿轮。
控制机床的运动轨迹和加工参数,实现对齿轮的精准加工。
2.5 检测优化完成齿轮的加工后,进行检测和优化。
检测齿轮的尺寸和形状,确保符合要求。
根据检测结果进行必要的优化和调整,以提高齿轮的质量。
3. 齿轮数控加工的优势齿轮的数控加工具有以下优势:•高精度:数控加工可以实现对齿轮的高精度加工,保证产品质量。
•高效率:数控加工可以提高齿轮的加工效率,节约生产时间和成本。
•灵活性:数控加工程序可以根据需求进行调整和优化,提高加工的灵活性和适应性。
4. 结语齿轮的数控加工程序是一种先进的加工技术,可以提高齿轮加工的精度和效率,推动机械制造行业的发展。
通过不断优化和改进数控加工程序,将能够更好地满足市场需求,提高产品质量和竞争力。
齿轮类零件机械加工工艺规程的编程

齿轮类零件机械加工工艺规程的编程齿轮作为机械传动中不可缺少的零件,其零件加工工艺对整个机械设备的运转稳定性和性能有着至关重要的作用。
随着机械制造加工科技的不断发展,越来越多的机械加工任务可以通过计算机编程来实现自动化加工,同时也可以使生产过程更高效、准确、可控和可重复。
本文将介绍齿轮类零件机械加工工艺规程的编程的一般流程和注意事项。
一、工艺规程基本流程齿轮类零件机械加工工艺规程的编程需要遵循一定的流程。
一般包括以下几个步骤:1. 齿轮参数确定首先要确定齿轮的参数,包括齿轮模数、齿数、压力角等基本参数。
这些参数要根据设计图纸和实际情况确定,可以通过应用软件进行计算和测量。
2. 选择加工工艺然后,根据齿轮的参数,选择适合的加工工艺。
一般有铣齿法、滚齿法、车削法等,不同的工艺有不同的加工难度和要求,需要根据实际情况选择。
3. 编写加工程序根据选择的加工工艺,编写加工程序。
一般是用机器语言编写,包括加工路径、加工速度、原点位置等信息,需要根据加工机床的不同自行编写。
编写加工程序需要有一定的计算机技术和机械知识基础。
4. 调试程序编写好加工程序后,需要进行程序的调试和优化。
一般先进行模拟加工,检查程序是否出现逻辑错误和加工轨迹是否正确。
然后进行实际加工,调整加工参数进行优化,直至达到要求的加工质量和加工速度。
5. 检测加工质量最后需要对加工零件进行检测和质量分析,检查齿廓、偏差、表面质量等指标是否符合要求。
如果有不良的机械性能可能会导致后续的装配和使用问题,需要及时纠正。
以上是一个简单的齿轮类零件机械加工工艺规程的编程流程,但具体的加工工艺规程可以根据零件的不同特性和实际需求进行优化和改变。
二、注意事项1. 熟悉加工机床编程需要结合加工机床的实际情况,需要对加工机床有一定的了解。
譬如说机床的操作面板和程序输入方式,不同种类的机床可能有不同的界面和操作流程,编程时需要进行特殊的注意。
2. 加工路径合理选择合理的加工路径和加工序列是影响齿轮加工质量和效率的重要因素。
齿轮类零件加工工艺编制及实施

齿轮类零件加工工艺编制及实施1. 引言齿轮作为机械传动装置中常见的零件之一,广泛应用于各行业的机械设备中。
齿轮类零件的加工工艺对于产品的质量和性能起着至关重要的作用。
本文将着重介绍齿轮类零件加工工艺的编制及实施过程,希望能够为相关从业人员提供一定的指导和借鉴。
2. 工艺编制的步骤2.1. 零件分析和设计在进行加工工艺编制之前,首先需要对齿轮类零件进行分析和设计。
对于不同类型的齿轮,其结构和加工方式可能会有所不同。
因此,在进行工艺编制前,需要对零件的结构和功能进行充分的分析和理解。
同时,还需要根据设计要求,确定零件的加工精度和表面要求等。
2.2. 工序规划根据齿轮类零件的设计要求,以及对加工工艺的分析,可以进行工序规划。
工序规划包括确定零件的加工顺序、加工方式、设备选择等。
在进行工序规划时,需要考虑加工效率、加工精度、加工难度等因素。
2.3. 工艺参数确定确定工艺参数是进行加工工艺编制的重要步骤。
工艺参数包括切削速度、进给量、切削深度等。
合理地确定工艺参数,可以有效地提高零件的加工效率和质量。
在确定工艺参数时,需要根据材料的性质和零件的几何形状等因素进行综合考虑。
2.4. 工装和夹具设计工装和夹具的设计对于齿轮类零件的加工具有重要的影响。
合理的工装和夹具设计可以提高零件的加工精度和稳定性。
在进行工装和夹具设计时,需要根据齿轮的形状和尺寸等要求进行设计,并考虑到加工过程中的固定和定位等问题。
2.5. 刀具选择和刃口修磨刀具的选择和刃口的修磨对于齿轮类零件的加工效果有着重要的影响。
合理的刀具选择可以提高加工效率和质量,而良好的刃口修磨则可以延长刀具的使用寿命。
在进行刀具选择和刃口修磨时,需要考虑到工艺参数和刃口的尺寸、形状等要求。
2.6. 加工工艺文件编制根据以上步骤的结果,可以进行加工工艺文件的编制。
加工工艺文件包括工艺路线、工艺参数、工装和夹具设计、刀具选择、刃口修磨等内容。
加工工艺文件是指导实际加工过程的重要依据,对于保证加工质量和顺利进行加工具有重要意义。
齿轮室盖数控加工工艺设计与编程

齿轮室盖数控加工工艺设计与编程
引言:
数控加工技术是现代制造业中不可或缺的关键技术之一,它能够实现
高效、精确和灵活的加工过程。
本文将介绍齿轮室盖数控加工的工艺设计
与编程,以解决传统加工方法中存在的一些问题,提高加工效率和产品质量。
一、工艺设计:
齿轮室盖是一种常见的机械零件,其加工需要经历多道工序。
在进行
齿轮室盖数控加工的工艺设计时,需要考虑以下几个方面:
1.工序划分:根据齿轮室盖的结构和加工要求,将加工过程分为多个
工序,包括粗加工、精加工、表面处理等。
2.加工顺序:确定各个工序的加工顺序,以保证顺利进行。
一般情况下,先进行粗加工,再进行精加工和表面处理。
3.工艺参数:根据齿轮室盖的材料和要求,确定每个工序的加工参数,包括切削速度、进给速度、切削深度等。
4.夹具设计:根据齿轮室盖的形状和加工要求,设计合适的夹具,以
确保工件的稳定固定和加工精度。
二、编程:
1.数控加工代码:根据工艺设计中确定的加工顺序和工艺参数,编写
合适的数控加工代码。
包括刀具路径、切削参数、加工顺序等。
2.刀具选择:根据齿轮室盖的特点和加工要求,选择合适的刀具进行加工。
在编程时需要指定刀具的尺寸、形状和切削角度等参数。
3.加工路径规划:根据齿轮室盖的形状和加工要求,规划合理的加工路径,以保证刀具的正常运动和工件的加工精度。
4.模拟加工:在编程完成后,进行模拟加工,检查刀具路径和加工过程是否正确,以提前发现问题并予以解决。
结论:。
某三联齿轮的加工工艺

某三联齿轮的加工工艺
汉德车桥(株洲)齿轮有限公司 (湖南株洲 412000) 漆益龙
摘要: 本文对某出口三联齿轮的加工工艺进行了分析和论证ꎬ 结合本公司的设备状况及现有的加工工艺
现状ꎬ 制订了新的加工方法ꎬ 使得铣端齿夹具设计简化、 操作简单、 不易出错ꎮ 同时ꎬ 针对三联齿轮在
能会因为忘记加过渡胀套而造成打刀等不良后果ꎮ
加工产品及取过渡胀套的过程ꎬ 极易出错ꎮ 而且
产品不加 过 渡 胀 套 和 加 过 渡 胀 套 的 示 意 图ꎬ
整个过程中是有两个胀套在起作用ꎬ 一个是固定
如图 3 所示ꎮ
图 3a 是不加过渡胀套的产品定位方式ꎬ 其内
孔是直内孔ꎬ 产品的内孔套在铣端齿夹具的圆孔
序中由于定位面的不同ꎬ 会出现不好操作的问题ꎮ
变成了一个直的内孔ꎬ 然后再将过渡胀套的内孔
滚齿时产品的定位基准是内孔和小端面ꎬ 操作没
套在铣端齿夹具的圆孔胀套上ꎬ 通过夹具的胀套
问题ꎬ 而铣端齿时因为产品必须反向安装ꎬ 台阶
将其过渡到胀套的内孔ꎬ 再通过过渡胀套的外圆
内孔小的部位朝里ꎬ 大的部位朝外ꎬ 内孔大的部
磨齿的齿轮精度相当于 DIN3962 / 3963 - 6 级ꎬ 齿
廓齿向 均 采 用 鼓 形 的 修 形ꎬ 其 中 齿 廓 的 鼓 形 量
0 006 ~ 0 02mmꎬ 齿向的鼓形量 0 05mmꎮ
2 齿轮加工工艺分析
(1) 三联齿轮采用的毛坯是锻件ꎬ 其中的锥
齿轮部分采用精密锻造成形ꎮ 我公司早在 1995 年
联齿轮的内孔有如下几个特点: ①内孔采用台阶
式ꎬ 并在内孔内设有内槽ꎬ 此结构可以使其压入
10
要使三个齿 部 同 轴ꎬ 必 须 要 先 出 来 一 个 基 准 面ꎮ
齿轮零件的数控加工工艺规程与数控工序的加工程序并上机实践设计书

齿轮零件的数控加工工艺规程及数控工序的加工程序并上机实践设计书一、零件的分析〔一零件的作用〔二零件的工艺分析二、工艺规程设计(一)确定毛坯的制造形式(二)基面的选择(三)表面加工方法选择(四)制定工艺路线(五)机械加工余量、工序尺寸及毛坯尺寸的确定(六)确定切削用量及基本工时三、编程总结参考文献序言机械制造工艺学课程设计,是我们在学完了大学的全部基础课、技术基础课以及大部分专业课之后进行的。
这也是我们在进行毕业设计之前对所学各课程作的一次综合性复习,也是一次理论联系实际的训练,它在我们们四年的学习中有着很重要的地位。
对我来说,希望能通过运用机械制造工艺学课程中的基本理论以及在生产实践中学到的实践只是,正确地解决一个零件在加工中的定位,夹紧以及工艺路线的安排,工艺尺寸确定等问题,保证零件的加工质量。
学会使用手册以及图表资料,掌握与本设计有关的各种资料的名称、出处,能够有大致的了解。
由于个人能力有限,设计尚有许多不足之处,恳请老师给予指导!本设计书包括:零件图:大齿轮一零件的毛坯图一机械加工仿真图一机械加工工艺过程卡一机械加工工序卡九工装设计任务书一课程设计说明书一份一、零件的分析<一零件的作用首先要认识到大齿轮是轮缘上有齿能连续啮合传递运动和动力的机械元件。
题目所给定的零件是圆柱齿轮减速器的大齿轮,通过键与轴固定在一起,主要作用是用来传递动力和改变转速以及旋转方向。
〔二零件的工艺分析1、齿轮基准端面对基准孔轴线的端面圆跳动公差为0.016mm。
2、键槽两端面对基准孔轴线的对称度公差为0.020mm。
3、该齿轮的加工平面有孔φ 58H7,大外圆φ245.394〔IT11>以及其端面,小外圆φ90以及其端面,环槽孔φ35,还有台阶面,键槽16Js9。
其中主要加工表面为孔φ58H7,大外圆φ245.394以及其端面。
4、φ58H7孔的表面粗糙度为Ra=1.6μm,齿面的表面粗糙度为Ra=1.6μm,φ245.394外圆面和齿轮两端面的表面粗糙度为Ra=3.2μm,键槽两侧面表面粗糙度是Ra=3.2μm,键槽底面表面粗糙度为Ra=6.3μm,其余表面的粗糙度均为Ra=12.5μm.5、齿坯热处理,在齿坯粗加工前后安排预先热处理,其主要目的是改善材料的加工性能,减少应力,为以后淬火时减少变形做好准备。
三联齿轮加工工艺和加工系统[发明专利]
![三联齿轮加工工艺和加工系统[发明专利]](https://img.taocdn.com/s3/m/db9c68e78ad63186bceb19e8b8f67c1cfad6ee2d.png)
专利名称:三联齿轮加工工艺和加工系统
专利类型:发明专利
发明人:汪润舟,高蕾,张霞,白利云,岑海波,罗鹏,李正华,朱成敬
申请号:CN202110834845.0
申请日:20210723
公开号:CN113523314B
公开日:
20220607
专利内容由知识产权出版社提供
摘要:本发明属于齿轮机加工技术领域,具体涉及三联齿轮加工工艺和加工系统的改进和应用;采用自动转运机构将放置在自动化料仓组件上的待加工三联齿轮坯料自动转运至自动加工机构中,并且利用自动加工机构中的三台数控车床对待加工三联齿轮坯料进行精车,通过并序加工方法使得本发明实现了将三联齿轮坯料精加工为三联齿轮的目的。
有效解决了现有技术在对三联齿轮进行精加工时存在的产品精度低且不稳定等缺陷。
同时的,利用自动转运设备对正在加工中以及完成加工的三联齿轮进行自动转运,又使得本发明实现了对齿轮工件进行自动夹装的目的,解决了现有技术对三联齿轮进行手动夹装转运时存在劳动强度大、转运时齿轮易发生磕碰伤等技术缺陷。
申请人:四川众友机械有限责任公司
地址:625000 四川省雅安市雨城区草坝工业集中区
国籍:CN
代理机构:成都坤伦厚朴专利代理事务所(普通合伙)
代理人:王华
更多信息请下载全文后查看。
齿轮的加工工艺过程分析
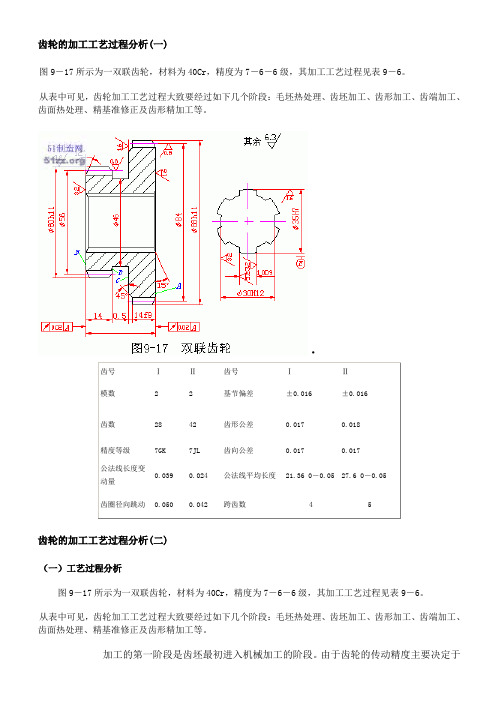
齿轮的加工工艺过程分析(一)齿轮的加工工艺过程分析(二)(一)工艺过程分析图9-17所示为一双联齿轮,材料为40Cr ,精度为7-6-6级,其加工工艺过程见表9-6。
从表中可见,齿轮加工工艺过程大致要经过如下几个阶段:毛坯热处理、齿坯加工、齿形加工、齿端加工、齿面热处理、精基准修正及齿形精加工等。
加工的第一阶段是齿坯最初进入机械加工的阶段。
由于齿轮的传动精度主要决定于图9-17所示为一双联齿轮,材料为40Cr ,精度为7-6-6级,其加工工艺过程见表9-6。
从表中可见,齿轮加工工艺过程大致要经过如下几个阶段:毛坯热处理、齿坯加工、齿形加工、齿端加工、齿面热处理、精基准修正及齿形精加工等。
·齿号 Ⅰ Ⅱ 齿号 Ⅰ Ⅱ 模数22基节偏差±0.016±0.016齿数 28 42 齿形公差 0.017 0.018 精度等级 7GK7JL齿向公差0.0170.017公法线长度变动量0.039 0.024 公法线平均长度 21.36 0-0.05 27.6 0-0.05齿圈径向跳动 0.050 0.042 跨齿数4 5齿形精度和齿距分布均匀性,而这与切齿时采用的定位基准(孔和端面)的精度有着直接的关系,所以,这个阶段主要是为下一阶段加工齿形准备精基准,使齿的内孔和端面的精度基本达到规定的技术要求。
在这个阶段中除了加工出基准外,对于齿形以外的次要表面的加工,也应尽量在这一阶段的后期加以完成。
第二阶段是齿形的加工。
对于不需要淬火的齿轮,一般来说这个阶段也就是齿轮的最后加工阶段,经过这个阶段就应当加工出完全符合图样要求的齿轮来。
对于需要淬硬的齿轮,必须在这个阶段中加工出能满足齿形的最后精加工所要求的齿形精度,所以这个阶段的加工是保证齿轮加工精度的关键阶段。
应予以特别注意。
加工的第三阶段是热处理阶段。
在这个阶段中主要对齿面的淬火处理,使齿面达到规定的硬度要求。
加工的最后阶段是齿形的精加工阶段。
花键孔三联齿轮加工工艺
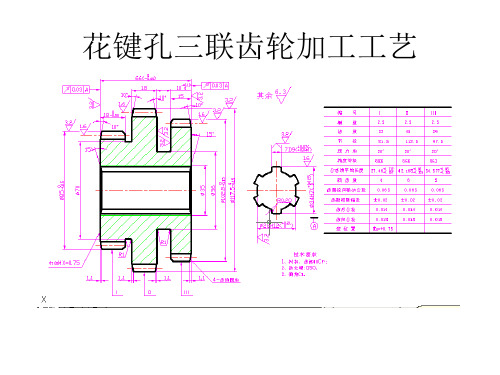
12
热处理
齿部高频淬火,G50
热处理
13
推孔
修正出现缩孔的花键孔
齿轮
油压机、 花键推刀: 6–34H7×2 花键塞规:6–34×28×7
入库 15
上油包装
花键孔三联齿轮加工工艺
花键孔三联齿轮的机械加工工艺过 程卡
材料牌号 40Cr 毛坯种类 锻件 毛坯外型尺寸 Ø 125×73 工序号 工序 名称 工序内容 车间 工艺装备
1
备料
毛坯锻造 Ø125×73 粗车各齿外圆、内孔分别留4mm余量,总长留4mm余量 (其余槽可暂时不车)。
锻冶
2
粗车
机械加工
CA6140、磨花钻Ø25
5
拉花 键孔
以右端大平面定位于拉床基准面,拉6– 34H7×28H12×7D9花键孔至要求。
机械加工
L6120、拉床花键拉刀6– 34H7×28H12×7D9
6
精车
以花键孔定位,精车齿坯各部分尺寸至要求。
机械加工
CK6140、锥度为: 1:8000花键芯轴。
7
检验
检验齿坯尺寸及形位公差要求。
8
插齿
以花键孔及右端大平面定位,分别插Ⅰ、Ⅱ、Ⅲ齿至 图样要求。
3
热处 理
调质HB220~250。
热处理
4
半精 车
车正花键底孔Ø 28+0.21,车两端面总长至67,二端孔口倒 角为 Ø39×15º ,其余各外径、长度分别留0.8余量。工艺 要求:66总长右端大平面与花键底孔一起车下,保证该 端面与孔中心线的垂直。
机械加工
CA6140
花键孔三联齿轮的机械加工工艺过 程卡
齿轮
Y5120插齿机、 花键插齿心轴:6–34×28×7 m2.5α20º A碗形插齿刀
机械制造课程设计-车床三联齿轮

目录一.根据零件图,对零件进行工艺分析1.零件的作用2.零件的工艺分析二.根据生产纲领,确定生产类型三.确定毛坯种类和制造方法四.机械加工工艺过程设计1.定位基准的选择2.工艺过程的拟定五.选择加工设备和工艺设备(夹具)1.机床2.刀具3.夹具4.量具六.确定工序尺寸1.径向工序尺寸2.轴向工序尺寸七.确定切削用量及时间定额八.工艺过程卡片九.工序卡片十.参考书目一.根据零件图,对零件进行工艺分析1.零件的作用三联齿轮广泛应用于各机床的变速箱中,通过拨叉改变位置而更换不同齿数的齿轮,进而改变传动比,最终达到变速的目的。
2.分析零件齿轮1φ95d6,齿轮2φ115d6,齿轮3φ135d6,齿顶表面粗糙度Ra3.2,齿面的表面粗糙度Ra0.8,其余未标注的为Ra12.5。
齿轮3两侧倒角为10°,齿轮1和齿轮2内测倒角为45°,外侧为10°,其余圆角为R0.5。
齿轮2与齿轮3之间间距为16D6,垂直度为0.06。
齿部高频淬火G48。
二.根据生产纲领,确定生产类型产品的年产量Q为7000件/年,每台产品中该零件的数量n为1,备品率a取3%,废品率b取0.5%,可得零件的年生产纲领N为:N=Qn(1+a)(1+b)=7000*1*(1+0.03)*(1+0.005)=7246件/年零件的质量为3.6千克,在机床类别里属于轻型零件,由此查表6-3 生产纲领与生产类型的关系,可知为大批生产。
特点如下:全部有互换性;锻件广泛采用模锻,毛坯精度高,加工余量小;有专用生产线;广泛采用高生产率夹具,靠夹具及调整法达到精度要求;广泛采用高生产率刀具和量具,或采用统计分析方法保证质量;对操作工人的技术要求较低,对生产线维护人员要求有高的素质。
三.确定毛坯种类和制造方法常用的毛坯为铸件和锻件。
而C630车床三联齿轮(材料为40Cr)承受载荷较重,毛坯宜选用强度和冲击韧度较高的锻件。
锻造方法有自由锻、模锻、胎膜锻和精密锻造等几种。
- 1、下载文档前请自行甄别文档内容的完整性,平台不提供额外的编辑、内容补充、找答案等附加服务。
- 2、"仅部分预览"的文档,不可在线预览部分如存在完整性等问题,可反馈申请退款(可完整预览的文档不适用该条件!)。
- 3、如文档侵犯您的权益,请联系客服反馈,我们会尽快为您处理(人工客服工作时间:9:00-18:30)。
研究意义
•
本设计主要通过对三联齿轮套的几何参数的 加工要求,对三联齿轮套的加工工艺进行分析, 加工方法进行设计,加深对以往知识的巩固,培 养分析和解决问题的能力,提高自已对数控软件 的应用能力,综合运用我们所学的机械设计基础、 数控编程、机械制图、CAD技术、机械制造工艺 等知识,来完成三联齿轮套的三维造型设计和对 三联齿轮套的零件工艺工程文件编制。并对相关 部分用数控机床来加工。
毛坯选择
常用的毛坯为铸件和锻件。CA6140车床三联齿 轮(材料为40Cr)承受载荷较重,宜选用高强度和 冲击韧性的毛坯。 锻件有自由锻、模锻俩种。其中,模锻生产率 高、锻件形状精度高、表面质量好和加工余量小, 适合大规模生产的中小型锻件。
定位基准选择
最初工序中采用毛坯 上未经加工的表面作 为粗基准。
划分加工阶段
加工阶段划分为:粗加工、半精加工、精加工。 1)有利于保证加工质量 。可使大切削量引起的变形充分释放,由半精
加工校正。
2)合理地使用设备 。 3)有利于及早发现毛坯的缺陷 。 4)便于安排热处理工序 。
确定各工序的设备、刀具和量具等
• 1.选择机床设备 根据零件图样要求,查《实用机械加工工艺手册》在粗、精加 工时选用卧式车床C6136;钻花键底孔时选用轻型圆柱立式钻床 ZQ5035,机床性能满足生产要求。 • 2.选择刀具 由于此材料为40Cr,查《机械制造技术基础》p24表 1-6,我们选 用硬质合金刀,牌号YT15。查《实用机械加工工艺手册》, 粗车外 圆时使用外圆车刀;加工键槽时采用割刀。
工艺路线的拟定Байду номын сангаас
序号 • 1 • 2 • 3 • 4 • 5 • 6 • 7 • 8 • 9 • 10 工序内容及要求 毛坯锻造 正火热处理 粗车端面 粗车外圆及槽 钻花键底孔 镗花键底孔至尺寸φ35mm 拉花键孔 钳工去毛刺、调质热处理 上芯轴,精车外圆、端面和槽至要求 检验
• • • • • • • • • • • •
精基准的选择原则
对于形位公差精度要求较高的零件,应采用已加工 过的表面作为定位基准,即为精基准。 精基准的选择原则: 基准重合原则、基准统一原则、互为基准原则、 自为基准原则。 基于上述原则,在左端表面加工中,选择外圆和右端面 作为精基准,在右端面的加工中,选择左端面和外圆选为 精基准。在加工花键孔中,选用端面和外圆为基准。在 钻孔中选择左端面和内孔为精基准。
定位基准
1、粗基准 2、精基准
在其后各工序中采用 经过加工的表面 作为精基准。
粗基准的选择原则
分析零件图,三联齿轮套主要是端面和外圆车削, 且它为回转零件,所以,选用端面做为定位基准比较 合理。 粗加工,因为毛胚是模锻件,不宜选用未加工端面做 基准。所以,要先加工端面,然后钻中心孔,这样才 能保证回转中心的同心度。
确定切削用量:
根据机床性能,查《机械加工工艺手册》 并结合实际经验确定加工余量及工序尺寸。
确定切削用量
•
查《数控车削用量推荐表》,确定切削用量及切削速度和实际切 削速度。
•
三联齿轮套外轮廓数控编程及仿真
总结
本文主要是运用所学的知识对三联齿轮套进行工艺 分析及数控编程设计,通过对三联齿轮套的加工方案分 析及设备的选择,使我对三联齿轮套有了更深层次的认 识。同时掌握了如何查阅和使用手册,查阅相关资料。 • 本次课题的设计,通过详细的分析和仔细的校核, 结果基本符合设计要求。 • 毕业设计是对我们大学四年的学习的一个总结,在 设计过程中,充分认识了自身学习存在的不足,使以往 所学的知识又一次得到了系统、完整的复习。从开始的 收集资料、整理资料、方案比选,到最后的确定方案。 在设计过程中,还有一些问题没能够处理好,我会继续 努力,使以后的学习和工作更加完善。 •
确定零件的生产类型
•
生产类型是企业生产专业化程度的分类。企业的生产类型取决于生产 的产量即生产纲领,生产类型对工艺规程的制定有很大的影响,不同的生 产类型我们会制定符合其要求、比较经济的工艺规程。
•
零件的质量为3.3千克,在机床类别里属于轻型零件,由此查《机械制造技 术基础》表3-1生产纲领与生产类型的关系,可知为大批生产。
11 12 13 14 15 16 17 18 19 20 21 22
插齿(z1=32),留余量0.037-0.066mm 插齿(z2=39),留余量0.037-0.066mm 插齿(z3=45),留余量0.037-0.066mm 倒角(其余齿轮为10°牙角,内孔为15°倒角) 钳工去毛刺 剃齿(z1=32),公法线长度至尺寸上线 剃齿(z2=39),公法线长度至尺寸上线 剃齿(z3=45),公法线长度至尺寸上线 齿部高频淬火G50 推孔 珩齿 检验
三联齿轮套的加工工艺分析及数控编程
指导老师:杨宏伟
学院:机电工程学院 专业:机械设计制造及其自动化 班级:10机制本04班 姓名:马文飞
研究背景
•
在机械领域,齿轮行业的崛起源于国外先进 的工业领域,并在我国得到了迅速的发展,这也 是“引进于国外,发展在中国”的又一个成功案 例。齿轮领域的产品也涉及到了众多行业范畴, 比如建筑领域的塔吊、起重机,交通运输领域的 火车、汽车、飞机等一系列交通运输产品。齿轮 行业具有完整的创新体系和优良的技术设施,自 引进之日至今,在中国20多个地区已形成了相 当可观的规模。在制造业这个行业领头羊的带领 下,众多制造产品都运用到了齿轮的传动,其中 三联齿轮占据着齿轮行业的重要地位。
零件的结构图
机械加工工艺规程设计
工艺规程设计的步骤 1)分析零件工艺性。 2)确定零件的生产类型。 3)选择毛坯。 4)选择定位基准。 5)拟定工艺路线。 6)确定各工序的设备、刀具和夹具等。 7)确定各工序的切削用量。 8)填写工艺文件。 9)程序编制。
零件加工工艺性分析
零件工艺性分析包括:零件的结构工艺性分析、零件的 技术要求分析 零件的结构工艺性分析:在满足使用要求的前提下加工的可 行性和经济性。 零件的技术要求分析:包括尺寸精度、形位公差和表面粗糙 度。在满足使用要求的前提下若能降低精度要求,则可降低 加工难度,减少加工次数,提高生产率,降低成本。