6.28粉浆PH值00:00样5.01的事故报告
粉末涂装作业事故中存在的隐患与对策参考文本
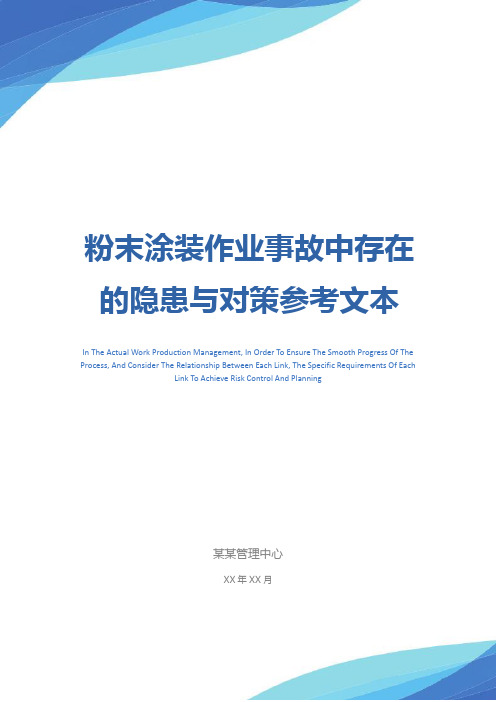
粉末涂装作业事故中存在的隐患与对策参考文本In The Actual Work Production Management, In Order To Ensure The Smooth Progress Of The Process, And Consider The Relationship Between Each Link, The Specific Requirements Of EachLink To Achieve Risk Control And Planning某某管理中心XX年XX月粉末涂装作业事故中存在的隐患与对策参考文本使用指引:此安全管理资料应用在实际工作生产管理中为了保障过程顺利推进,同时考虑各个环节之间的关系,每个环节实现的具体要求而进行的风险控制与规划,并将危害降低到最小,文档经过下载可进行自定义修改,请根据实际需求进行调整与使用。
常用的静电粉末喷涂工艺流程:作业中事故最为严重的是粉末喷涂引起的燃烧和爆炸,发生的原因有:(1)粉末涂料为可燃物质,粒径在350μm以下,其中大部分是75 μm以下,处于这个范围的有机粉尘具有燃烧爆炸的可能性,以环氧粉为例,它的着火温度是530 ℃,最小点火能量是0.35 mJ;(2)正常喷涂时,静电高压为6~9×104 V,如果喷涂器电极与工件(或其他物体)的间距不当,就有可能发生放电打火现象,如果恒流源控制失效,这一打火的能量就可能超过悬浮粉末燃爆的最小点火能量;(3)喷粉舱内粉末与空气的混合,若回收风量不足以将粉末与空气混合浓度降低到允许浓度(10 g/m3)下,则容易达到爆炸浓度下限,若静电打火能量超过粉末最小点火能量,就很有可能引发爆炸事故。
事故发生频率最高的要数因抽吸风量不匹配而引起喷粉舱跑粉(逸粉),这也直接影响作业人员的健康。
此外,跑粉现象还可能在燃爆事故发生时酿成二次事故。
第3种事故是电气故障,其发生点较多,其中喷室、喷枪装置、电热炉、烘道等设备发生率都较高。
修改后的-双氧水车间事故案例统计分析

双氧水车间事故案例统计分析1、1997年7月萃取塔底部视镜坏,影响生产造成停车。
岗位:一楼岗位原因:萃取塔底部视镜安装变形紧固不均匀,温差变化大,在开车过程中造成视镜破裂。
现象:双氧水从底部视镜断裂处流出造成大量浪费。
安全处理措施:将萃取塔内双氧水全部放至视镜以下用不锈钢盲板代替视镜将视镜处盲死。
教训:两系统开车升温时一定要缓慢,尽量避免温度大起大落。
2、1997年10月萃取塔严重积料最低流量降至30立方/每小时难以维持生产。
岗位:原因:由于空气压力波动导致2#氧化液气液分离器出料不稳,氧化液中溶解少量的空气带入萃取塔,使萃取塔内产生大量气泡造成液泛致使积料的产生。
现象:萃取塔内有机层增厚,淹没降液管致使工作液在塔内积聚,纯水加不进造成大量带水。
安全处理措施:在氧化液2#气液分离器后加设氧化液槽和氧化液泵,使溶解的气体在槽内得到释放,增设氧化液泵后增加了工作液的上浮动力,使积料问题得到有效解决。
教训:3、1997年11月后处理出料不畅,影响系统流量。
岗位:一楼岗位原因:后处理白土床更换氧化铝时,没有彻底清理底部瓷球及杂物,使瓷球及杂物堵塞管道造成工作液流动不畅。
现象:工作液计量槽液位不好降,流量加不上,白土床出料不畅。
安全处理措施:及时清除堵塞物恢复正常生产。
教训:加强更换氧化铝时清理工作的检查,在扒氧化铝重新装填新氧化铝时一定要将瓷球及杂物清理干净并用纯水冲洗干净后再装填。
4、1998年4月触媒再生后效果不好,主要表现在氢化效率不好提。
岗位:主控岗位原因:触媒再生后没有将水分吹干,使触媒中水分超标,致使活性提不起来。
现象:氢化效率低安全处理措施:改用热氮气吹干触媒。
教训:再生后一定要用热氮气吹干,只有这样才能将触媒中的水分吹出,才能恢复触媒的活性。
5、1998年7月氢化液过滤器垫片损坏,造成跑料停车。
岗位:二楼岗位原因:氢化液过滤器垫片是石棉板,再加上过滤器进口压力超标,使垫片浸渍后变形承受不了压力造成垫片损坏造成跑料。
玻璃防霉粉事故报告范文
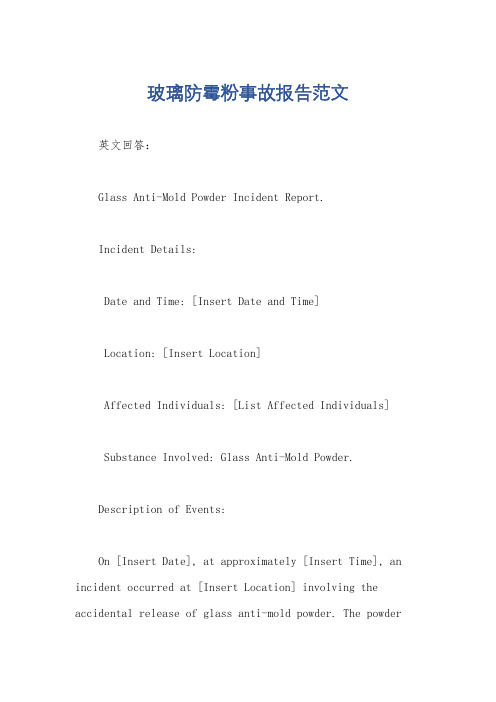
玻璃防霉粉事故报告范文英文回答:Glass Anti-Mold Powder Incident Report.Incident Details:Date and Time: [Insert Date and Time]Location: [Insert Location]Affected Individuals: [List Affected Individuals] Substance Involved: Glass Anti-Mold Powder.Description of Events:On [Insert Date], at approximately [Insert Time], an incident occurred at [Insert Location] involving the accidental release of glass anti-mold powder. The powderwas being used to combat mold growth in a storage area when a container containing the powder was knocked over,spilling its contents onto the floor.Several individuals present in the area at the time of the spill inhaled or came into contact with the powder. The affected individuals reported experiencing a variety of symptoms, including respiratory irritation, skin irritation, and eye irritation.Immediate Actions Taken:The affected area was immediately evacuated and access was restricted.The individuals affected by the spill were instructedto remove any contaminated clothing and thoroughly washtheir skin and eyes with water.The area was ventilated to disperse the powder and reduce exposure levels.Medical assistance was provided to the affected individuals as needed.Investigation and Analysis:An investigation was conducted to determine the cause of the incident and identify any potential contributing factors. The investigation revealed that:The container containing the glass anti-mold powder was not properly secured and was knocked over due to a lack of caution.The individuals affected by the spill were not wearing appropriate personal protective equipment (PPE) at the time of the incident.The ventilation in the storage area was inadequate to prevent the accumulation of the powder in the air.Control Measures Implemented:To prevent similar incidents from occurring in the future, the following control measures were implemented:All containers of glass anti-mold powder must be securely stored and labeled.All individuals handling the powder must wear appropriate PPE, including respirators, gloves, and eye protection.The storage area where the powder is used must be adequately ventilated to prevent the accumulation of airborne powder.Recommendations:Regular safety training should be provided to all individuals who may handle glass anti-mold powder.The storage and handling procedures for the powder should be reviewed and revised as necessary.The ventilation system in the storage area should be upgraded to ensure adequate air exchange.Conclusion:The accidental release of glass anti-mold powder at [Insert Location] on [Insert Date] resulted in several individuals experiencing respiratory, skin, and eye irritation. The incident was caused by a lack of proper storage, use of PPE, and ventilation. The implementation of the recommended control measures will help prevent similar incidents from occurring in the future.中文回答:玻璃防霉粉事故报告。
科迈化工公司“6.19”粉尘爆炸事故调查报告

2016年6月19日18时38分左右,位于古林街工业园区的科迈化工股份公司(以下简称科迈公司)DZ造粒车间发生一起其他爆炸事故,事故造成1人死亡,2人受伤,直接经济损失292万元。
事故发生后,该公司未按规定报告事故,根据群众举报,经查证属实。
依据《中华人民共和国安全生产法》(以下简称安全生产法)和《生产安全事故报告和调查处理条例》(国务院令第493号)等有关法律法规,经区政府批准,成立了由区安全监管局、区监察局、区总工会、古林街道办等部门组成的科迈公司“6·19”其他爆炸事故调查组(以下简称事故调查组),并邀请区大港人民检察院派员及相关专家参加,开展事故调查工作。
事故调查组按照“四不放过”和“科学严谨、依法依规、实事求是、注重实效”的原则,通过现场勘察、调查取证及综合分析,查明了事故发生的经过、原因、人员伤亡、事故瞒报过程和直接经济损失情况,认定了事故性质和责任,提出了对有关责任人和责任单位的处理建议,并针对事故原因及暴露出的突出问题,提出了事故防范措施建议。
现将有关情况报告如下:一、基本情况(一)事故单位情况科迈化工股份有限公司(以下简称科迈公司)。
科迈公司成立于2002年7月,为股份企业。
注册资本:一亿壹仟壹佰壹拾万元人民币;法定代表人:王XX;注册地址:天津市滨海新区大港古林工业区海欣路72号;从业人员:687人;经营范围:防老剂RD、促进剂:CZ、DZ、医药中间体MBT、MBTS、防水油、抗氧化剂KL、橡胶粘合剂KTR、增塑剂A、硫酸钡、碳酸锶及碳酸钡等生产经营。
具有工业产品生产许可证和安全生产许可证,证书编号分别为(津)XK13-008-00034和(津)WH安许证字〔2006〕DG0004;具有危险化学品登记证,证书编号为120912034。
(二)事故涉及的DZ产品情况事故涉及产品为:N-环已基-2-苯噻唑次磺酰胺(又名:促进剂DCBS、简称DZ)。
化学分子式:C19H26N2S2;分子量:378.5519(264.4);相对密度1.27;成品熔点:不低于96℃;产品外观与性状:白色或灰白色颗粒,不溶于水。
关于2012年7月28日水泥凝结时间异常的分析报告YYYY 2

关于2012年7月28日出厂P.O42.5级散装水泥凝结时间异常的报告佳木斯市松江水泥有限公司化验室二O一二年八月一日关于2012年7月28日P.O42.5级散装水泥凝结时间异常的事故分析报告一、事故经过2012年7月28日上午7:30左右化验室物检组在检测出厂水泥过程中,发现散装P.O42.5级水泥标准稠度用水量突然增大,需水量比平时增加10ml左右,凝结时间异常,在45min以内凝结硬化(试验过程中并没有发现剧烈放热,可以排除水泥急凝现象,同时水泥浆体在短时间内彻底失去可塑性,也可以排除水泥假凝现象),化验员郭爱华发现问题后立即将信息反馈给林英库、段崇国,并通知销售科许艳艳查明该批量水泥发出多少、流向何方,为确保产品质量、维护公司利益,建议销售科全部追回。
销售科查明,该批量水泥发出两车,佳东某建筑工地一车已追回,平洋商砼一车已打入水泥筒库且已经检验出凝结时间异常并向销售科反应,许艳艳通知平洋商砼暂停使用。
二、事故处理事故发生后,公司化验室坚持“质量第一,客户第一”的基本原则,尽可能的降低公司损失,按以下情况处理:1. 生产报表显示该批量水泥出磨水泥163吨,外加矿粉21.8吨,合计184.8吨,全部打入2#库,发现质量异常后,根据水泥量库情况,立即通知车间2#库水泥暂停发放散装,同时通知包装车间按以下比例搭配包装P.O42.5袋装水泥,1# 2# 3#1000r/min 500r/min 500r/min以确保出厂水泥质量;2. 追回的一车散装水泥通过¢3.2m×13m磨机打入P.C32.5水泥贮库4#库,并通知包装车间4#限量搭配使用,确保32.5级水泥质量合格。
3.化验室联系销售科安排散装罐车自2#库放水泥半车,取样检测,凝结时间异常,此半车水泥自外上熟料提升机打入熟料库。
4. 为确保散装42.5水泥正常发货,¢3.2m×13m开车后粉磨P.O42.5水泥,化验室取样检测凝结时间正常后直接打入3#库,同时将2#库放料闸板适当开启,少量搭配2#库水泥,化验室取样检测凝结时间正常后放行。
6.28液化DE值00:00样12.70的事故报告

6.28液化DE值不合格事故报告
一事故经过
2010年6月28日,00:00化验室测得液化DE值为12.70,超出指标控制范围。
二原因分析
1、18:00车间将粉浆干物质浓度调整至28.5—30.5,液化总糖也将会随之下降,所以调节还原糖,把加酶量下调。
2、加酶量截止18:00多加2KG,截止28日00:00少加0.5KG,加酶量不稳。
3、液化时间2.1小时,超出范围2.5—3小时
4、现场人员跟踪测样不及时。
三责任划分
1 液化主控褚雪霞液化酶加入量不稳定未对数据做出正确分析,合理调节加酶量。
2 班长祝大朋对组织人员对还原糖数据跟踪不及时,未对中控没有正确指导
3 值班长刘忠伟、宋安安对数据缺乏分析,未对现场及控制人员做出正确的指导。
四处罚结果
1液化主控褚雪霞罚款50元。
2 液化发酵班长洪景亮罚款30元。
3 酒精值班长刘忠伟、宋安安各罚款30元。
五预防措施
1 监控好投料量,稳定液化酶加入量。
2 组织人员对控制指标及时跟踪测样。
3 保证液化时间,严格遵守工艺纪律。
4增强数据分析能力,提前做出预判。
5、组织学习此次事故加深印象。
酒精车间
二〇一〇年六月十八日。
脱硫浆液品质劣化技术分析报告11.01.13(1)

脱硫浆液品质劣化技术分析报告一、事件经过:1.2010年12月3日—12月7日,石膏化验结果显示含水率达30%,而后采取了一般性的调整,石膏旋流器压力、向事故浆液箱倒浆、脱水机检查、增启浆液循环泵(共3台运行)、增启氧化风机达3台运行,降低pH 值至4.0等一系列调整,但浆液品质还是进一步恶化,石膏含水达45%以上。
2.12月8日—12月17日,向事故浆液箱倒浆液、并排浆,降低吸收塔液位后,并投加50吨石膏晶种,浆液有好转迹象,脱水石膏含水降到34%以内,由于事故浆液箱搅拌器故障,被迫将事故浆液箱400m3浆液倒回吸收塔,期间也进行过多次调整,均无明显效果,也对设备进行全面检查,并发现B、C氧化风管不进气,判断是风管堵,进行过处理,均未能使吸收塔浆液品质转好。
3.12月17日— 12月31日,将吸收塔浆液倒至事故浆液箱,吸收塔液位降至3.06m,并向吸收塔投加脱硫添加0.85吨,浆液密度降至1180kg/m³,脱水也是开始几天有好转迹象, 23日后石膏含水升至37%,26日升至40%以上,浆液品质没有得到解决。
期间又将余下的0.15吨脱硫添加投用,对A脱水进行大修,更换了滤布和密封件。
4.2011年1月1日—1月4日脱硫退出进行检修,对A、D氧化风管断, A、I、S除雾器冲洗水管断、pH表进口阀坏进修复,对除雾器进行清理。
打开人孔,发现吸收塔四周(除搅拌器1米范围内)石膏沉积严重,A、B浆液循环泵进口滤网有损坏。
5.经空塔检修和投加石膏晶种50吨,1月4日脱硫投入运行,吸收塔进口含硫较稳定,平均4000 mg/Nm3左右,5日将脱水投入运行,石膏含水率在13%,运行正常。
6日-7日浆液亚硫酸钙含量达15—27%之间,后投入三台氧化风机、吸收塔液位保持6.7-6.8m、浆液pH控制在4.9-5.2之间处理,浆液亚硫酸钙降至5%以下,石膏含水在13%左右,至此吸收塔浆液品质恢复正常。
二、原因分析:1.在2010年11月以来吸收塔进口含硫一直都较高,4000—7000mg/Nm3范围内波动,而且煤质发热量较低,同样负荷燃煤量增加,进入吸收塔含硫量增大,超过了吸收塔设计容量,吸收塔内生成小晶体的石膏量也增大,导致吸收塔浆液密度升高,起初密度在1150—1190的范围内偏高,也促使了石膏晶体的长大。
7月5日粉浆PH值超标的事故报告

7月5日粉浆PH值超标的事故报告
一、事故经过
2010年7月5日甲班当班,经中心化验室取样分析发现液化工段18:00粉浆PH5.80,20:00粉浆PH5.06,超出了车间的正常控制范围。
二、原因分析
1、接班活化B正在更新载体浸泡水,浸泡水打入工艺
水罐给粉浆拌料,其浸泡水PH值为2.5,工艺水罐PH
值为7.0—8.0,直至20:50活化B罐水打空,期间粉
浆一直加碱。
2、主控对活化B罐浸泡水打入工艺水罐拌料情况重视
程度不够,调整不及时,现场送样不及时。
三、责任认定
1、主控对PH变化不够重视,调整不及时,没有经验,
是造成此次事故的直接原因;
2、现场人员清罐,对物料PH变化跟踪不到位,是造
成此次事故的间原因;
四、处理意见
1、对液化、发酵主控陈茹罚款50元;
2、对当班值长刘忠伟罚款20元。
五、整改措施
1、提高操作人员的岗位操作技能;
2、严格执行工艺纪律;
3、提高对异常数据变化的敏感度,准确、及时地作出
调整;
4、增强员工的责任感,对工作要认真负责。
5、各岗位加强沟通,保证生产工艺稳定运行。
酒精车间
二〇一〇年七月5日。
事故分析报告格式

蛋白液事故报告
一、事故简要经过
2018年5月23日,发货配料蛋白液批次2018年5月15日中有一箱5月10日的批次
二、事故原因分析
1、直接原因(导致事故发生的直观原因)
1)冷藏一库故障,移库后,员工粗心大意,将5月10日的批次压在5月15日的批次下面
2、间接原因(剔除直观原因以外的因素)
1)未按先进先出摆放
2)批次收货后,多批次物资未做明显标识区分
3、主要原因
1)员工粗心大意,监管不到位
三、整改防范措施(针对以上各个要因提出对策措施)
1)增加每日巡查,必须保证所有蛋液外箱批次明显区分
2)增加仓管员日常盘点,每日盘点一次蛋液,确保摆放先进先出没问题
3)加强员工培训,日常会议宣导,增加员工责任心意识
四、事故处理结果
直接仓管员:李振风罚款100 间接仓管员: 叶如操罚款50 仓管主管:罚款100。
水泥粉磨站危险源

皮带事故开关不符合标准 其他伤害 6 割或撬皮带破口不停机 运转时进非通道侧 未挂好安全链开动磨机 巡检时越过警示线 球磨机防护网缺陷 倒球时安全措施不当 机械伤害 6 机械伤害 3 机械伤害 6 机械伤害 1 机械伤害 6 物体打击 3
未停电,进行磨内作业, 其他伤害 3 环境不良 现场作业环境噪声超标 噪声 3
1 18
2
生产班 安全防护设施不齐全,未 机械伤害 3 前检查 及时恢复 地面环境不好 跨越转动设备 对使用安全带,不符合要 求 未进行安全教育 未确认是否有酒后上岗 其他伤害 1 机械伤害 1 其他伤害 3 其他伤害 6 其他伤害 3 其他伤害 3 其他伤害 6 其他伤害 3
轻微风险 一般风险, 7 21 需注意 一般风险, 3 54 需注意 1 6
6
进入库内清除库壁结料作 业清理料仓(库)未系好 安全带、安全绳,未确认 掩埋 6 爬梯牢固可靠,没有保持 足够照明,安全绳未固定 点 进入库内清除库壁结料作 业清理料仓(库)监护人 掩埋 3 员脱离岗位,库内情况外 部人员不掌握。 设备运转部位加油、清扫 机械伤害 3 、紧固 未走安全通道 未停机更换托辊,挡轮 清理滚筒积料时未停机 机械伤害 6 机械伤害 6 机械伤害 6
13
检查袋收尘时未系安全带 其他伤害 6 袋收尘 器检修 检修气缸阀时措施不当 机械伤害 3 在收尘器顶部作业站位不 其他伤害 6 当 检修风机措施不当 其他伤害 6
8 球磨机
8
筒体螺栓紧固安全措施不 高处坠落 3 球磨机 当 磨内搬运衬板超重 加钢球时多人作业,配合 不当 打大锤、确认不够 机械伤害 3 物体打击 3
2 1 2
3 18 7 21 3 18
轻微风险 一般风险, 需注意 轻微风险
搅拌站生产安全事故调查报告
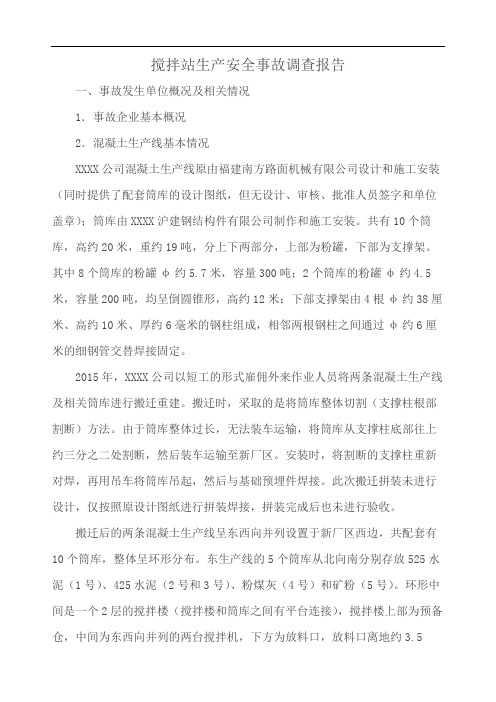
搅拌站生产安全事故调查报告一、事故发生单位概况及相关情况1.事故企业基本概况2.混凝土生产线基本情况XXXX公司混凝土生产线原由福建南方路面机械有限公司设计和施工安装(同时提供了配套筒库的设计图纸,但无设计、审核、批准人员签字和单位盖章);筒库由XXXX沪建钢结构件有限公司制作和施工安装。
共有10个筒库,高约20米,重约19吨,分上下两部分,上部为粉罐,下部为支撑架。
其中8个筒库的粉罐φ约5.7米,容量300吨;2个筒库的粉罐φ约4.5米,容量200吨,均呈倒圆锥形,高约12米;下部支撑架由4根φ约38厘米、高约10米、厚约6毫米的钢柱组成,相邻两根钢柱之间通过φ约6厘米的细钢管交替焊接固定。
2015年,XXXX公司以短工的形式雇佣外来作业人员将两条混凝土生产线及相关筒库进行搬迁重建。
搬迁时,采取的是将筒库整体切割(支撑柱根部割断)方法。
由于筒库整体过长,无法装车运输,将筒库从支撑柱底部往上约三分之二处割断,然后装车运输至新厂区。
安装时,将割断的支撑柱重新对焊,再用吊车将筒库吊起,然后与基础预埋件焊接。
此次搬迁拼装未进行设计,仅按照原设计图纸进行拼装焊接,拼装完成后也未进行验收。
搬迁后的两条混凝土生产线呈东西向并列设置于新厂区西边,共配套有10个筒库,整体呈环形分布。
东生产线的5个筒库从北向南分别存放525水泥(1号)、425水泥(2号和3号)、粉煤灰(4号)和矿粉(5号)。
环形中间是一个2层的搅拌楼(搅拌楼和筒库之间有平台连接),搅拌楼上部为预备仓,中间为东西向并列的两台搅拌机,下方为放料口,放料口离地约3.5米,两个放料中控室分别位于两台搅拌机两侧;搅拌楼北面为两条并列的输送带,分别为两个搅拌机输送黄沙和石子的混合物;搅拌楼南面为两个混凝土搅拌车的接料进口,每个进口宽度近4米。
发生坍塌的为东生产线3号(下称“东3号”)筒库。
事发时,该筒库存量约280吨。
搅拌楼位于东3号筒库西偏北20°处,东3号筒库以西偏北50°向西北方向倾倒压塌搅拌楼,并压住一辆停放在东放料口的混凝土搅拌车尾部,倒塌的3号筒库粉罐与地面约呈20°,支撑架东侧两根钢柱中部已弯曲折断;西侧两根钢柱中部已严重压屈断裂。
粉浆
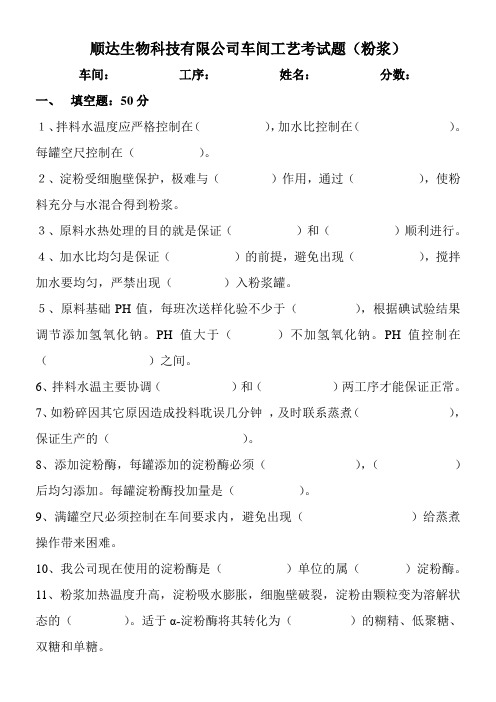
顺达生物科技有限公司车间工艺考试题(粉浆)
车间:工序:姓名:分数:
一、填空题:50分
1、拌料水温度应严格控制在(),加水比控制在()。
每罐空尺控制在()。
2、淀粉受细胞壁保护,极难与()作用,通过(),使粉料充分与水混合得到粉浆。
3、原料水热处理的目的就是保证()和()顺利进行。
4、加水比均匀是保证()的前提,避免出现(),搅拌加水要均匀,严禁出现()入粉浆罐。
5、原料基础PH值,每班次送样化验不少于(),根据碘试验结果调节添加氢氧化钠。
PH值大于()不加氢氧化钠。
PH值控制在()之间。
6、拌料水温主要协调()和()两工序才能保证正常。
7、如粉碎因其它原因造成投料耽误几分钟,及时联系蒸煮(),保证生产的()。
8、添加淀粉酶,每罐添加的淀粉酶必须(),()后均匀添加。
每罐淀粉酶投加量是()。
9、满罐空尺必须控制在车间要求内,避免出现()给蒸煮操作带来困难。
10、我公司现在使用的淀粉酶是()单位的属()淀粉酶。
11、粉浆加热温度升高,淀粉吸水膨胀,细胞壁破裂,淀粉由颗粒变为溶解状态的()。
适于α-淀粉酶将其转化为()的糊精、低聚糖、双糖和单糖。
二、问答题:50分
1、粉浆工序的安全操作要求有哪些?
2、闭风器堵塞的原因是什么?应怎样避免?
3、自开产以来粉浆发生了哪些生产工艺事故?是什么原因造成的?
4、水膜除尘器循环水罐里的水每班次放、填几次?为什么?
5、添加氢氧化钠有哪些注意事项?。
博汇及鲁西双氧水装置事故原因评析

3
☆ 距爆炸现场30m左右的氯气储罐管线断裂,造成氯气泄漏;
1.博汇 “8.25”双氧水爆炸事故简介(续)
山东国金化工厂位于淄博市桓台县经济开发区化学产业园, 原为山东桓台博汇社会福利化工厂,始建于2000年9月,由山东 博汇集团有限公司投资管理。事故发生时的主要产品生产能力 为:液碱12万吨/年、液氯10万吨/年、双氧水4万吨/年。 发生事故的双氧水生产装置由中国天辰化学工程公司设计, 2006年5月份投入生产; 2010年10月因市场原因停车;
23
(4)开车(试运行)运行准备工作不到位。
1)装置开车的管理组织设置不合理,技术、管理人员配置不够、 力量薄弱。
2)开、停车方案不完善,未对生产系统中可能产生杂质、粉末 的因素进行彻底排除。 3)氮气中氧含量超标、氮气压力值不合格,导致装置紧急停车 后不能及时开车,造成双氧水分解放出的热量积聚,局部温度升高 导致双氧水分解地更剧烈。同时给事故应急带来隐患。 4)上岗前教育培训不到位,人员综合素质较差。 开车前未对操作人员进行转岗前的二、三级安全教育,车间技 术员、操作工等对工艺过程、操作参数、控制指标、常见异常现象、 紧急处理措施等知之甚少,人员安全意识、应急处置能力差。 24
2
前言:博汇及鲁西双氧水事故简介
1.博汇“8.25”双氧水爆炸事故简介
2012年8月25日18时46分许,博汇集团山东国金化工厂4万吨/ 年双氧水生产装置在停车过程中发生爆炸事故,造成3人死亡,7 人受伤,伤亡损失惨重,社会影响较大。 ☆ 距爆炸事故80m范围内的所有玻璃全部震碎; ☆ 爆炸物将500m以外的液氨球罐顶部阀门砸坏,罐内液氨全 部泄漏,持续泄漏长达36小时左右。
扬州市邗江杨庙污水泵站“5·29”硫化氢中毒较大事故调查报告
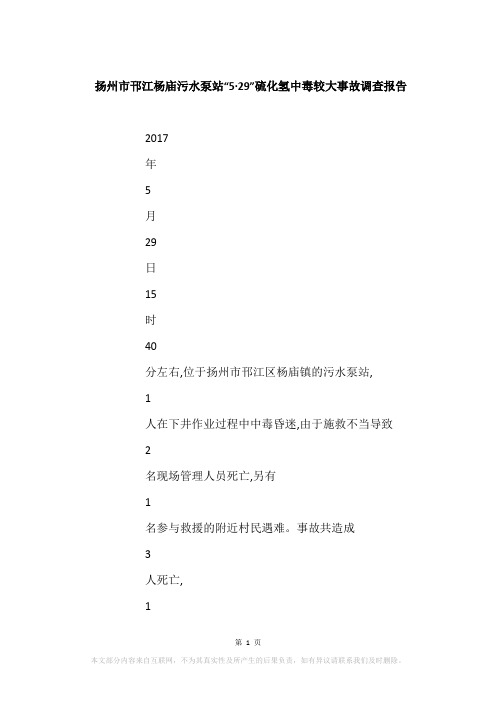
扬州市邗江杨庙污水泵站“5·29”硫化氢中毒较大事故调查报告2017年5月29日15时40分左右,位于扬州市邗江区杨庙镇的污水泵站,1人在下井作业过程中中毒昏迷,由于施救不当导致2名现场管理人员死亡,另有1名参与救援的附近村民遇难。
事故共造成3人死亡,1人受伤。
依据《中华人民共和国安全生产法》、《生产安全事故报告和调查处理条例》(国务院令第493号)的规定,5月30日市政府成立“5·29”事故调查组,事故调查组由市安监局牵头,市建设局、市监察局、市公安局、市总工会、市卫计委、邗江区安监局等单位参加。
同时,邀请市人民检察院派员参加。
事故调查组按照“四不放过”和“科学严谨、依法依规、实事求是、注重实效”的原则,从技术和管理两个层面分组,通过现场勘验、查阅资料、调查取证、检测鉴定,查明了事故发生的经过、原因、人员伤亡等情况,认定了事故性质和责任,提出了对有关责任人员和责任单位的处理建议,并针对事故暴露出的问题,提出了防范整改措施。
现将有关情况报告如下:一、基本情况(一)工程基本情况位于扬州市邗江区杨庙镇的环保产业园污水泵站工程(以下简称“杨庙泵站工程”),地上建筑128.71平方米,由泵房、配电控制室及值班房组成。
地下泵房泵池深度8.65米,平面面积72.2平方米。
其功能是解决环保产业园污水排放,完善城市污水收集系统。
该泵站工程是环保产业园及杨庙镇污水雨水主管网工程中四项工程中的一项。
市政府明确“市城乡建设局为该工程的牵头责任单位,负责工程总体布局、规划设计、雨水管网、污水泵站建设施工等各项工作,城控集团负责污水管网施工,相关单位(部门)积极配合”。
2013年10月22日,市城乡建设局《关于杨庙环保产业园及杨庙镇雨污水主管网等相关工程建设问题协调的专题会议纪要》明确,“考虑到雨污水管道交叉施工难度、污水提升泵站建成后的移交管理及工期要求等相关问题,为确保能按时完成,雨水管道和污水提升泵站工程由市城乡建设局与城控公司签订委托代建协议,委托城控公司统一负责实施及相关手续的办理”。
涂料工厂安全事故调查报告
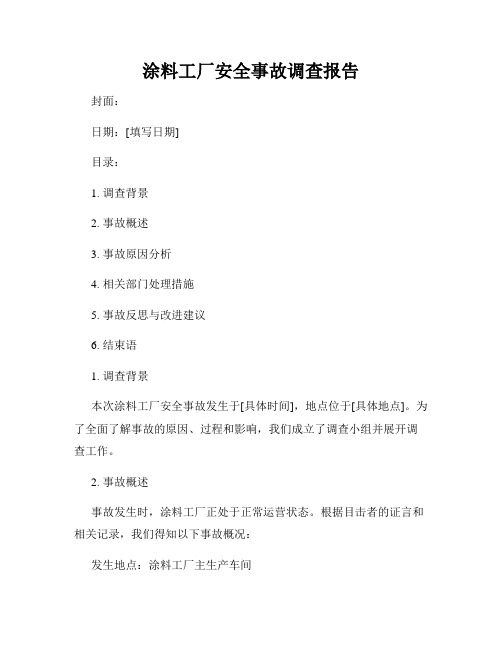
涂料工厂安全事故调查报告封面:日期:[填写日期]目录:1. 调查背景2. 事故概述3. 事故原因分析4. 相关部门处理措施5. 事故反思与改进建议6. 结束语1. 调查背景本次涂料工厂安全事故发生于[具体时间],地点位于[具体地点]。
为了全面了解事故的原因、过程和影响,我们成立了调查小组并展开调查工作。
2. 事故概述事故发生时,涂料工厂正处于正常运营状态。
根据目击者的证言和相关记录,我们得知以下事故概况:发生地点:涂料工厂主生产车间事故时间:[具体时间]事故类型:化学品泄漏引起的爆炸事故事故影响:造成3名工人受伤,车间设备严重损坏,生产线停工我们立即对现场进行了勘察,并与相关人员进行了深入交流,以了解事故的具体原因。
3. 事故原因分析经过对涂料工厂安全事故的深入调查和分析,我们确定了以下可能的事故原因:3.1 人为因素a) 工人安全意识不强:在事故现场的交流中发现,部分工人对涂料工厂的安全操作规程和风险防范知识了解不足,缺乏紧急情况的应对能力。
b) 不当操作行为:事故发生前,一名工人在操作过程中未正确关闭涂料罐盖,导致涂料泄漏。
同时,该工人未及时上报泄漏情况,延误了事故的处理时间窗口。
3.2 设备原因a) 设备老化:经过对现场设备进行检查,我们发现部分设备已超过其设计寿命周期,存在一定的老化现象。
老化设备的运行状态不稳定,容易造成诸如泄漏或故障等安全隐患。
b) 质量问题:根据我们的调查,部分设备存在质量问题,例如阀门无法完全关闭,从而导致涂料泄漏的发生。
4. 相关部门处理措施涂料工厂事故发生后,立即启动了应急预案,采取了以下措施:a) 伤员救治:工厂紧急联系医院,将受伤工人送往医院接受治疗,并为其安排了必要的休息和康复。
b) 现场封控:针对事故现场,工厂安排专业人员进行封控,防止事故扩大化和二次发生。
c) 调查启动:工厂成立了事故调查小组,对事故原因展开深入调查,并与相关部门协调合作。
d) 设备维修和更换:工厂针对老化设备和质量问题设备,立即启动了维修和更换计划,确保设备运行的可靠性和安全性。
一起糖厂制炼车间澄清工段急性硫化氢中毒事故的调查

一起糖厂制炼车间澄清工段急性硫化氢中毒事故的调查发表时间:2012-11-08T10:17:15.810Z 来源:《中外健康文摘》2012年第25期供稿作者:宋宁生[导读] 了解急性硫化氢中毒事故发生的原因, 为采取相应卫生防护措施提供依据。
宋宁生 (广西柳城县疾病预防控制中心广西柳城 545200)【中图分类号】R595.4【文献标识码】A【文章编号】1672-5085(2012)25-0100-02【摘要】目的了解急性硫化氢中毒事故发生的原因, 为采取相应卫生防护措施提供依据。
方法用快速检气管对事故现场硫化氢浓度进行检测, 对中毒事故发生的原因进行调查分析。
结果 2名沉淀池工人因缺乏防护意识和抢救知识发生了急性硫化氢中毒。
结论对从事接触有毒有害气体作业的劳动者普及自我保护知识和施救技巧是预防有毒有害气体急性中毒的关键。
【关键词】糖厂硫化氢急性中毒调查硫化氢为无色、剌激性和窒息性气体,具有强烈的臭鸡蛋气味,可迅速引起嗅觉疲劳,是强烈的神经毒物,对粘膜有强烈的剌激作用,高浓度时可猝死。
分子式为H2S,相对分子量34.08,相对密度1.19,略重于空气,易溶于水,因此,易积聚在低洼积水处如水井、下水道、潜涵、隧道、清理垃圾、阴沟、粪池、菜窖等有机物腐败及通风不良的地方。
短时间吸入高浓度硫化氢可以引起中枢神经系统、眼和呼吸系统损害为主的急性中毒,轻者出现头痛、头晕、乏力、恶心、眼胀痛、畏光、眼结膜充血、咽干、咳嗽等症状。
较重者上述症状加重,并出现胸闷、心悸等症状,视力模糊、眼结膜水肿及角膜糜烂、肺部有干、湿性啰音,神志出现轻度障碍。
重症者则神志不清、昏迷、出现脑水肿,肺水肿,呼吸循环衰竭[1]。
急性硫化氢中毒如能及时抢救治疗,尤其现场急救进行心肺复苏术,一般可获救。
长期以来,职业性急性硫化氢中毒事故频发。
2011年6月, 广西柳城县某糖厂发生1起制炼车间澄清工段沉淀池岗位2人急性硫化氢中毒事故。
本文旨在探讨该急性中毒发生的原因, 总结经验, 为采取相应的职业卫生防护措施提供依据。
泥浆不合格的原因

泥浆不合格的原因泥浆作为一种常用的钻井液,在石油勘探和开采过程中起到了重要的作用。
然而,有时会出现泥浆不合格的情况,给钻井作业带来一系列问题和隐患。
泥浆不合格的原因有很多,下面将进行详细阐述。
泥浆不合格可能是由于成分配比不当导致的。
泥浆的成分配比应当根据具体的地质条件和钻井目的进行合理调整,包括添加适量的黏土、胶体、分散剂、增稠剂等。
如果配比不当,比如添加过多的黏土或增稠剂,会导致泥浆黏稠度过高,无法正常循环,甚至堵塞井眼,造成作业困难和安全隐患。
泥浆不合格的原因还可能是由于泥浆中含有过多的杂质。
杂质可能来自于钻井过程中的井底碎屑、钢材颗粒、油污等。
如果这些杂质没有得到及时有效的处理,会导致泥浆的性能下降,造成泥浆的污染和不稳定。
同时,杂质还会对井壁形成不良的膜状结构,影响钻井液的附着性能,增加了钻井事故的风险。
泥浆不合格还可能与泥浆的pH值有关。
泥浆的pH值过高或过低都会对泥浆的性能产生不利影响。
如果pH值过高,会导致泥浆中的黏土颗粒胶结,减少其分散性能。
而如果pH值过低,会导致泥浆中的胶体颗粒变得容易沉淀,降低整个泥浆的性能。
因此,合理调节泥浆的pH值是保证泥浆合格的重要因素之一。
泥浆不合格还可能与泥浆的密度有关。
泥浆的密度应当根据井深、井壁稳定性、地层压力等因素进行合理调整。
如果泥浆的密度过低,会导致井壁不稳定,易发生井壁塌陷等问题。
而如果泥浆的密度过高,会增加井眼压力,导致泥浆泄漏、井喷等灾害事故的发生。
因此,合理控制泥浆的密度是保证泥浆合格的关键之一。
泥浆不合格还可能与泥浆的循环和处理方式有关。
泥浆在钻井过程中需要进行循环和处理,以保证其性能的稳定和持久。
如果循环方式不当,比如循环速度过慢、循环时间过长等,会导致泥浆中的固相物无法及时排除,降低泥浆的性能。
同时,泥浆的处理方式也需要科学合理,比如通过离心机、过滤器等设备进行泥浆的固液分离,以去除杂质和固相颗粒。
泥浆不合格的原因有很多,包括成分配比不当、泥浆中含有过多的杂质、pH值不合适、密度调节不当以及循环和处理方式不当等。
- 1、下载文档前请自行甄别文档内容的完整性,平台不提供额外的编辑、内容补充、找答案等附加服务。
- 2、"仅部分预览"的文档,不可在线预览部分如存在完整性等问题,可反馈申请退款(可完整预览的文档不适用该条件!)。
- 3、如文档侵犯您的权益,请联系客服反馈,我们会尽快为您处理(人工客服工作时间:9:00-18:30)。
6.28粉浆PH值00:00样5.01的事故报告
一事故经过
2010年6月28日,00:30化验室测得粉浆PH值为5.01。
二原因分析
1、物料可能产酸,近期粉浆调节PH值主要以加碱调整。
2、活化罐B罐浸泡水按工艺要求打入工艺水罐,給粉浆拌料,其浸泡水PH值2.5。
3、粉浆加碱量未补加及时。
三责任划分
1 液化主控褚雪霞未对数据做出正确分析,活化罐B罐浸泡水打入工艺水罐的因素未考虑分析清楚,未合理调节加碱量。
2 班长祝大朋、主操何平对原料变化不明感,未对中控没有正确指导
3 值班长刘忠伟、宋安安对原料、临时数据缺乏分析,未对现场及控制人员做出正确的指导。
四处罚结果
1液化主控褚雪霞罚款50元。
2 液化发酵班长洪景亮罚款30元。
3 酒精值班长刘忠伟、宋安安各罚款30元。
五预防措施
1 稳定操作,对不同物料要认真分析,合理调节加碱量
2 监控好投料比例
3 加强现场人员对物料的观测和分析能力
4 增强数据分析能力,提前做出预判
酒精车间
二〇一〇年六月十八日。