论高炉容积的选择
高炉的规格

高炉的规格可以根据具体项目和需求而有所不同,以下是一些常见的高炉规格参数:
1.容积:高炉容积是指高炉内部可容纳冶炼物料的体积大小,通常以立方米(m³)为单位进行表示。
高炉的容积大小直接关系到其生产能力和冶炼效率。
2.高度:高炉的高度是指从高炉顶部到高炉底部的垂直距离,通常以米(m)为单位进行表示。
高度直接影响高炉内部的气体流动和冶炼物料的下降速度。
3.内径:高炉的内径是指高炉内部炉身的直径,通常以米(m)为单位进行表示。
内径直接关系到高炉内部冶炼物料的堆积状况和煤气在高炉内的流动速度。
4.排气温度:高炉的排气温度是指高炉顶部排出的煤气温度,通常以摄氏度(℃)为单位进行表示。
排气温度直接影响高炉冶炼过程中的热能损失和冶炼效率。
5.炉龄:高炉的炉龄是指高炉建成至今的运行时间,通常以年为单位进行表示。
炉龄直接关系到高炉的使用寿命和维护保养情况。
需要注意的是,高炉的规格参数会根据不同的冶炼过程和技术要求而有所差异,例如煤气发生量、燃料种类、冶炼产量等因素都会对高炉的规格造成影响。
因此,在具体项目中,需要根据冶炼工艺设计和工程要求进行详细的规格确定。
高炉常用计算公式
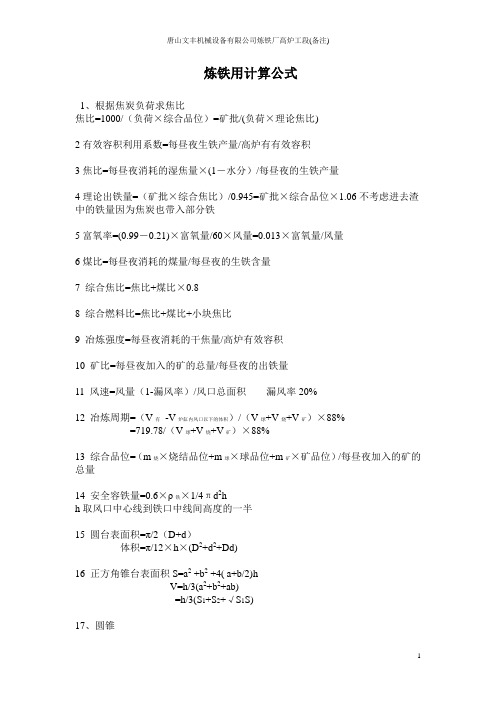
炼铁用计算公式1、根据焦炭负荷求焦比焦比=1000/(负荷×综合品位)=矿批/(负荷×理论焦比)2有效容积利用系数=每昼夜生铁产量/高炉有有效容积3焦比=每昼夜消耗的湿焦量×(1-水分)/每昼夜的生铁产量4理论出铁量=(矿批×综合焦比)/0.945=矿批×综合品位×1.06不考虑进去渣中的铁量因为焦炭也带入部分铁5富氧率=(0.99-0.21)×富氧量/60×风量=0.013×富氧量/风量6煤比=每昼夜消耗的煤量/每昼夜的生铁含量7 综合焦比=焦比+煤比×0.88 综合燃料比=焦比+煤比+小块焦比9 冶炼强度=每昼夜消耗的干焦量/高炉有效容积10 矿比=每昼夜加入的矿的总量/每昼夜的出铁量11 风速=风量(1-漏风率)/风口总面积漏风率20%12 冶炼周期=(V有-V炉缸内风口以下的体积)/(V球+V烧+V矿)×88%=719.78/(V球+V烧+V矿)×88%13 综合品位=(m烧×烧结品位+m球×球品位+m矿×矿品位)/每昼夜加入的矿的总量14 安全容铁量=0.6×ρ铁×1/4πd2hh取风口中心线到铁口中线间高度的一半15 圆台表面积=π/2(D+d)体积=π/12×h×(D2+d2+Dd)16 正方角锥台表面积S=a2 +b2 +4( a+b/2)hV=h/3(a2+b2+ab)=h/3(S1+S2+√S1S)17、圆锥侧面积M=πrl=πr√r2+h2体积V=1/3πr2h18、球S=4πr2=πd2V=4/3πr3=π/6d319、风口前燃烧1kg碳素所需风量(不富氧时)V风=22.4/24×1/(0.21+0.29f) f为鼓风湿度20、吨焦耗风量V风=0.933/(0.21+0.29f)×1000×85%f为鼓风湿度85%为焦炭含碳量21、鼓风动能(1)E=(764I2-3010I+3350)dE-鼓风动能I-冶炼强度(2)E=1/2mv2=1/2×Q×r风/(60gn)v风实2Q-风量r风-风的密度g=9.8 n-风口数目22、石灰的有效容剂性CaO有效=CaO熔-SiO2×R23、洗炉墙时,渣中CaF2含量控制在2%-3%,洗炉缸时可掌控在5%左右,一般控制在4.5%每批料萤石加入量X=P矿×TFe×Q×(CaF2)/([Fe]×N)P矿-矿批重TFe-综合品位[Fe]-生铁中含铁量Q-吨铁渣量(CaF2)-渣中CaF2含量N-萤石中CaF2含量24、风口前燃烧1kg碳素的炉缸煤气量V煤气=(1.21+0.79f)/(0.21+0.29f)×0.933×C风C风-风口前燃烧的碳素量,kg25、理论出渣量渣量批=QCaO批/CaO渣渣量批-每批炉料的理论渣量,tQCaO批-每批料带入的CaO量,tCaO渣-炉渣中CaO的含量,%25、喷吹煤粉热滞后时间t=V总/(V批×n)V总-H2参加反应区起点处平面(炉身温度1100℃~1200℃处)至风口平面间的容积,m³V批-每批料的体积,m³n-平均每小时的下料批数,批/h26、高炉某部位需要由冷却水带走的热量称为热负荷,单位表面积炉衬或炉壳的热负荷称为冷却强度Q=CM(t-t0)×103Q-热负荷kJ/hM-冷却水消耗量,t/hC-水的比热容,kJ/(kg.℃)t-冷却水出水温度℃t0-冷水进水温度,℃。
高炉炉型设计

4、炉腹高度h2 ;炉腰直径D;炉腹角α
• 选取炉腹角α : 一般取值79o~83o h2 =
1 2 ( D d ) tg
选取 D/d 炉型 D/d 小型高炉 1.25~1.5 中型高炉 1.15~1.25 大型高炉 1.09~1.15
5、选取炉身角β; 炉身高度 h4 ; 炉喉直径 d1
世界高炉之王——沙钢5860立方米炼铁高炉
日本第二大钢铁集团——日本JFE钢铁福山厂 。
(左起)第2高炉、第3高炉、第4高炉、第5高炉,4号高炉 2006年5月扩容到5000立方米,5号高炉扩容到5500立方米
全世界共有9座5500m³ 以上特大型炼铁高炉
• 1、沙钢的5860m³ 高炉;
• 2、日本新日铁大分厂1号、2号高炉(容积均为5775m³ ) • 3、俄罗斯北方钢铁切列波维茨厂5号高炉(容积5580m³ ) 4、日本新日铁君津厂4号高炉(容积5555m³ ) • 5、德国蒂森钢铁斯韦尔根厂2号高炉(容积5513m³ ), • 6、日本JFE福山厂5号高炉(容积5500m³ ) • 7、韩国浦项光阳钢厂4号高炉(容积5500m³ )
h z 1 . 27
0 . 45
bP ' Nc d 铁
2
hf
hz k
― 渣口高度与风口高度之比
k = 0.5~0.6 ; k
炉缸高度: h =h + a ; 1 f
a―风口结构尺寸,一般取值0.35~0.5m
hz― 渣口与铁口中心线的距离称为渣口高度 P ― 生铁日产量,t b ― 生铁产量波动系数,一般取值1.2 N ― 昼夜出铁次数,8~12次/d (大高炉取大值)
• 通过对高炉炉型的大量研究和探索,人们 逐步认识了高炉炉型与原燃料和鼓风制度 的适应关系,即炉型与炉料运动和煤气流 运动规律的适应性。炉型是随着原燃料条 件的改善,操作技术水平的提高,科学技 术的进步而不断发展变化的,逐步形成了 现代的五段式高炉炉型。
炉况判断小技巧
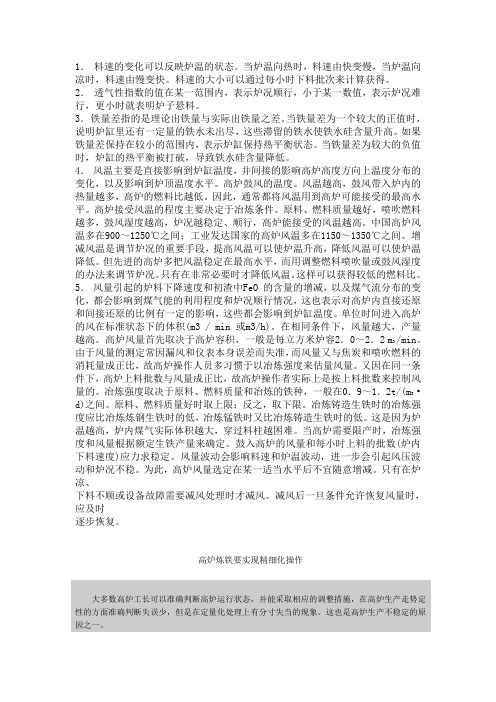
1.料速的变化可以反映炉温的状态。
当炉温向热时,料速由快变慢,当炉温向凉时,料速由慢变快。
料速的大小可以通过每小时下料批次来计算获得。
2.透气性指数的值在某一范围内,表示炉况顺行,小于某一数值,表示炉况难行,更小时就表明炉子悬料。
3.铁量差指的是理论出铁量与实际出铁量之差。
当铁量差为一个较大的正值时,说明炉缸里还有一定量的铁水未出尽,这些滞留的铁水使铁水硅含量升高。
如果铁量差保持在较小的范围内,表示炉缸保持热平衡状态。
当铁量差为较大的负值时,炉缸的热平衡被打破,导致铁水硅含量降低。
4.风温主要是直接影响到炉缸温度,并间接的影响高炉高度方向上温度分布的变化,以及影响到炉顶温度水平。
高炉鼓风的温度。
风温越高,鼓风带入炉内的热量越多,高炉的燃料比越低。
因此,通常都将风温用到高炉可能接受的最高水平。
高炉接受风温的程度主要决定于冶炼条件。
原料、燃料质量越好,喷吹燃料越多,鼓风湿度越高,炉况越稳定、顺行,高炉能接受的风温越高。
中国高炉风温多在900~1250℃之间;工业发达国家的高炉风温多在1150~1350℃之间。
增减风温是调节炉况的重要手段,提高风温可以使炉温升高,降低风温可以使炉温降低。
但先进的高炉多把风温稳定在最高水平,而用调整燃料喷吹量或鼓风湿度的办法来调节炉况。
只有在非常必要时才降低风温。
这样可以获得较低的燃料比。
5.风量引起的炉料下降速度和初渣中FeO 的含量的增减,以及煤气流分布的变化,都会影响到煤气能的利用程度和炉况顺行情况,这也表示对高炉内直接还原和间接还原的比例有一定的影响,这些都会影响到炉缸温度。
单位时间进入高炉的风在标准状态下的体积(m3 / min 或m3/h)。
在相同条件下,风量越大,产量越高。
高炉风量首先取决于高炉容积,一般是每立方米炉容2.0~2.2 m3 /min。
由于风量的测定常因漏风和仪表本身误差而失准,而风量又与焦炭和喷吹燃料的消耗量成正比,故高炉操作人员多习惯于以冶炼强度来估量风量。
高炉常用计算公式

炼铁用计算公式1、根据焦炭负荷求焦比焦比=1000/(负荷×综合品位)=矿批/(负荷×理论焦比)2有效容积利用系数=每昼夜生铁产量/高炉有有效容积3焦比=每昼夜消耗的湿焦量×(1-水分)/每昼夜的生铁产量4理论出铁量=(矿批×综合焦比)/=矿批×综合品位×不考虑进去渣中的铁量因为焦炭也带入部分铁5富氧率=-×富氧量/60×风量=×富氧量/风量6煤比=每昼夜消耗的煤量/每昼夜的生铁含量7 综合焦比=焦比+煤比×8 综合燃料比=焦比+煤比+小块焦比9 冶炼强度=每昼夜消耗的干焦量/高炉有效容积10 矿比=每昼夜加入的矿的总量/每昼夜的出铁量11 风速=风量(1-漏风率)/风口总面积漏风率20%12 冶炼周期=(V有 -V炉缸内风口以下的体积)/(V球+V烧+V矿)×88%=(V球+V烧+V矿)×88%13 综合品位=(m烧×烧结品位+m球×球品位+m矿×矿品位)/每昼夜加入的矿的总量14 安全容铁量=×ρ铁×1/4πd2hh取风口中心线到铁口中线间高度的一半15 圆台表面积=π/2(D+d)体积=π/12×h×(D2+d2+Dd)16 正方角锥台表面积S=a2 +b2 +4( a+b/2)h V=h/3(a2+b2+ab)=h/3(S1+S2+√S1S)17、圆锥侧面积M=πrl=πr√r2+h2体积V=1/3πr2h18、球S=4πr2=πd2V=4/3πr3=π/6d319、风口前燃烧1kg碳素所需风量(不富氧时)V风=24×1/+ f为鼓风湿度20、吨焦耗风量V风=(+)×1000×85%f为鼓风湿度 85%为焦炭含碳量21、鼓风动能(1)E=(764I2-3010I+3350)dE-鼓风动能 I-冶炼强度(2)E=1/2mv2=1/2×Q×r风/(60gn)v风实2Q-风量 r 风-风的密度 g= n-风口数目22、石灰的有效容剂性 CaO 有效=CaO 熔-SiO 2×R23、洗炉墙时,渣中CaF 2含量控制在2%-3%,洗炉缸时可掌控在5%左右,一般控制在%每批料萤石加入量X=P 矿×TFe ×Q ×(CaF 2)/([Fe]×N) P 矿-矿批重 TFe-综合品位 [Fe]-生铁中含铁量 Q-吨铁渣量 (CaF 2)-渣中CaF 2含量 N-萤石中CaF 2含量24、风口前燃烧1kg 碳素的炉缸煤气量 V 煤气=(+)/(+)××C 风 C 风-风口前燃烧的碳素量,kg25、理论出渣量 渣量批=QCaO 批/CaO 渣渣量批-每批炉料的理论渣量,t QCaO 批-每批料带入的CaO 量,t CaO 渣-炉渣中CaO 的含量,%25、喷吹煤粉热滞后时间 t=V 总/(V 批×n )V 总-H 2参加反应区起点处平面(炉身温度1100℃~1200℃处)至风口平面间的容积,m ³V 批-每批料的体积,m ³ n-平均每小时的下料批数,批/h26、高炉某部位需要由冷却水带走的热量称为热负荷,单位表面积炉衬或炉壳的热负荷称为冷却强度Q=CM(t-t)×103Q-热负荷 kJ/hM-冷却水消耗量,t/hC-水的比热容,kJ/(kg.℃) t-冷却水出水温度℃-冷水进水温度,℃t。
高炉炉型计算

高炉炉型计算高炉炉型是指高炉内部耐火材料构成的几何空间,近代高炉炉型由炉缸、炉腹、炉腰、炉身和炉喉五部分组成。
炉型的设计要适应原燃料条件,保证冶炼过程的顺行。
高炉炉型设计的依据是单座高炉的生铁产量,由产量确定高炉有效容积,以高炉有效容积为基础,计算其它尺寸。
一、确定容积1、确定年工作日高炉的工作日是指高炉一代寿命中,扣除大、中、小修时间后,平均每年的实际生产时间。
根据国内经验,不分炉容大小,年工作日均可定为355天。
2、确定高炉日出铁量年工作日年产量高炉日出铁量=t/d3、确定高炉的有效容积V uUu PV η高炉有效容积利用系数高炉日出铁量=二、高炉缸尺寸1、炉缸直径d炉缸直径的计算可参考下述经验公式:大型高炉 45.032.0u V d =3620m 以下高炉 37.0564.0u V d = 计算后取整2、炉缸高度'hA 渣口高度h 渣 m 式中:b ——生铁产量波动函数,一般取值1.2 N ——昼夜出铁次数,取9铁γ——铁水密度,取值7.1t/m3C ——渣口以下炉缸容积利用系数,取值055一般小高炉设一个渣口,大中型高炉设两个渣口,高低渣口标高差一般为100~200mm ,2000m 3以上高炉渣口数目应和铁口数目一起考虑,如有两个铁口,可以设二个渣口。
B 、风口高度h 风k ——渣口高度与风口高度的比,一般k 二0.5~0.6(渣量大取低值)。
C 、炉缸高度h 1h 1=h 风+a式中a ——风口结构尺寸,一般a=0.35~0.5m ,中小高炉取下限,大高炉取上限。
227.1d c N bp h 铁渣γ⋅=kh h 渣风=三、死铁层厚度h 0死铁层的作用在于防止炉底炉渣,煤气侵蚀和冲刷,使炉底温度均匀稳定。
通常死铁层厚度为450~600mm ,新设计的大型高炉多在1000mm 左右或更高。
四、炉腰直径D 1、炉腰直径D大型高炉D/d=1.10~1.15 中型高炉D/d=1.15~1.25 小型高炉D/d=1.25~1.5 2、炉腹角α炉腹角α一般为79°~82°。
高炉炉型选择以及炉容计算
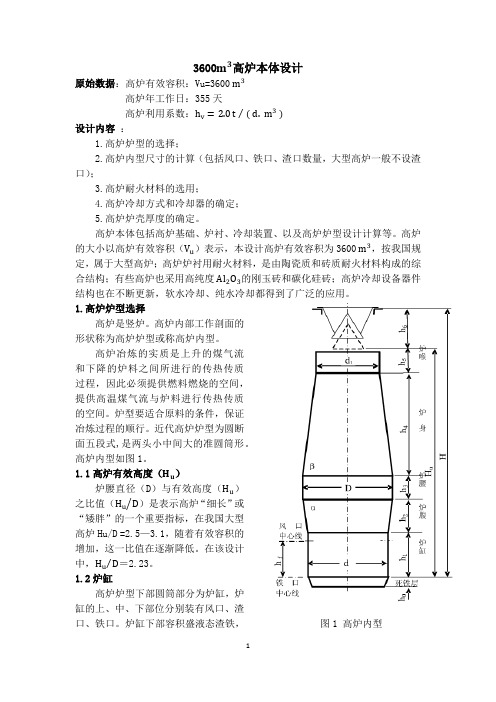
3600m3高炉本体设计原始数据:高炉有效容积:Vu=3600 m3高炉年工作日:355天⁄ )高炉利用系数:h v=2.0t ( d. m3设计内容:1.高炉炉型的选择;2.高炉内型尺寸的计算(包括风口、铁口、渣口数量,大型高炉一般不设渣口);3.高炉耐火材料的选用;4.高炉冷却方式和冷却器的确定;5.高炉炉壳厚度的确定。
高炉本体包括高炉基础、炉衬、冷却装置、以及高炉炉型设计计算等。
高炉的大小以高炉有效容积(V u)表示,本设计高炉有效容积为3600 m3,按我国规定,属于大型高炉;高炉炉衬用耐火材料,是由陶瓷质和砖质耐火材料构成的综合结构;有些高炉也采用高纯度 Al2O3的刚玉砖和碳化硅砖;高炉冷却设备器件结构也在不断更新,软水冷却、纯水冷却都得到了广泛的应用。
1.高炉炉型选择高炉是竖炉。
高炉内部工作剖面的形状称为高炉炉型或称高炉内型。
高炉冶炼的实质是上升的煤气流和下降的炉料之间所进行的传热传质过程,因此必须提供燃料燃烧的空间,提供高温煤气流与炉料进行传热传质的空间。
炉型要适合原料的条件,保证冶炼过程的顺行。
近代高炉炉型为圆断面五段式,是两头小中间大的准圆筒形。
高炉内型如图1。
1.1高炉有效高度(H u)炉腰直径(D)与有效高度(H u)⁄是表示高炉“细长”或之比值(H u D)“矮胖”的一个重要指标,在我国大型高炉Hu/D =2.5—3.1,随着有效容积的增加,这一比值在逐渐降低。
在该设计⁄ 2.23。
中,H u D=1.2炉缸高炉炉型下部圆筒部分为炉缸,炉缸的上、中、下部位分别装有风口、渣口、铁口。
炉缸下部容积盛液态渣铁,图1 高炉内型上部空间为风口燃烧带。
铁口位于炉缸下水平面,铁口数目依炉容或产量而定,对于3000m3以上的高炉,设置3—4个铁口,以每个铁口日出铁量1500—3000t设置铁口数目。
在该设计中,设置4个铁口。
渣口与铁口中心线的距离称为渣口高度(H Z),它取决于原料条件,即渣量的大小。
高炉主要技术经济指标及有关计算

6、冶炼周期:
24V ' t nV (1 c)
V' N V (1 c)
或
式中 t —冶炼周期,h;N —由料线到风口中 心线的料批数,批; V ' —由料线到风口中心线的 容积,m3; n —每天料批数,批; V —每批料 体积,m3/批; c —炉料在高炉内压缩率,一般 为12~15%。
各牌号生铁折合炼钢生铁系数(A)
生铁种类 炼钢生铁 铁号 各号 铸14 铸18 铸造生铁 铸22 铸26 铸30 折算系数 1.00 1.14 1.18 1.22 1.26 1.30
铸34
球10 球墨铸铁用生铁 球13 球18 球20 含钒生铁 w(V)>0.2%各号 w(V)>0.2%、 w(Ti)>0.1%各号
(3)计算每批料中量:
SiO2 料 SiO2 矿 SiO2 焦 SiO2 煤 SiO2 熔
式中 SiO2 料—每批料中 SiO2量,kg; SiO2 矿 —矿石 带入 SiO2 量,kg;SiO2 焦 —焦炭带入 SiO2量,一 般按焦炭灰分的45%计算,kg; SiO2 煤 —煤粉带 入 SiO2 量,一般按煤粉灰分的45%计算, SiO2 量,kg。 kg; SiO2 熔—其他熔剂带入 (4)计算炉料中还原成 [ Si] 消耗的 SiO2 :
3 2 1 1 Q ( t 273 ) 2 E mV实 0.412 2 2 n F ( p p0 ) 2
m=1.29*Q /n/60
式中 E —鼓风动能,J/s; t—风温,℃; Q — 风量,m3/min; F —风口送风总面积,m2; n — 风口个数,个; p —热风压力,Pa; p0 —标准 大气压,等于101325Pa。 5、富氧率:(不考虑鼓风湿度,氧气流量经过流 量孔板) Q氧 f O (a 0.21) 100% Q风 式中 f O —富氧率,%;Q氧 —富氧量, m3/min; Q风—风量(冷风流量孔板显示值), m3/min; a —氧气中含氧率,%。
高炉工艺参数

高炉工艺参数炼铁厂高炉内型尺寸 m³1280m³三、1800m³高炉内型尺寸工长常用调剂参数原燃料质量要求一、焦炭质量要求二、烧结矿化学成份:球团矿质量要求块矿质量要求喷吹煤粉质量要求看水工艺参数一、450m³高炉1、450m³要求2、各部位冷却器水温差规定:四、1280 m³高炉和1800 m³高炉冷却系统参数规定煤气工艺参数一、煤气系统指标1、煤气净化指标:净煤气含尘量≤5mg/m3温度:100℃≤T≤280℃2、煤气压力控制:450m³、1280m³净煤气支管压力不小于3KPa,1800m³净煤气支管压力不小于4KPa3、热风炉部分二、1280 m³高炉热风炉1、各部分工艺设计参数2、1280m³操作参数3、1280m³换热器设计参数三、1800m³高炉1、1800m³煤气系统控制要求2、1800m³煤气系统设计参数3、1800m³煤气系统操作参数上料系统一、450m3上料二、1280m3高炉三、1800m3高炉上料操作参数炉前操作参数规定1、铁口深度参数2、打泥量的规定3、液压参数的规定4、耐材浇注规定水泵房操作参数一、高炉对软水要求二、、密闭系统运行控制指标风机房一、450高炉二、汽拖风机正常运行指标三、汽拖风机报警值一、空压机工艺参数及报警、停机参数表:TRT 一、1280m³高炉TRT工艺参数二、1280m³高炉TRT润滑系统各调整项目与联锁报警##。
高炉炉体内型参数表
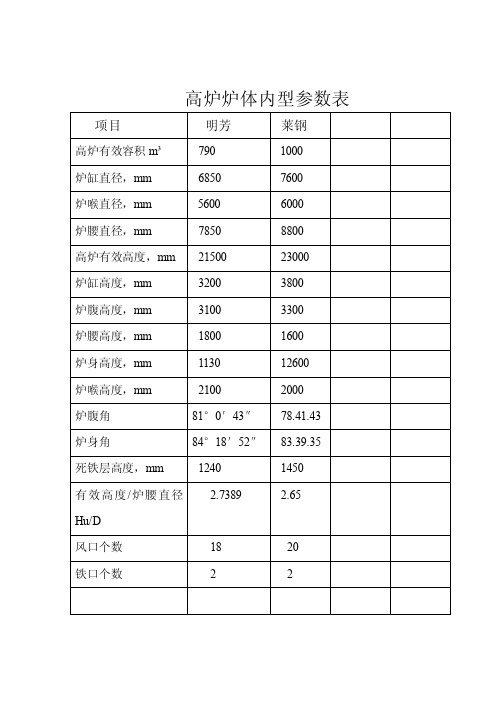
高炉炉体内型参数表高炉各部分的热流强度设计取值表w/m²热风炉主要性能参数热风炉耐火球堆比重(t/m³)热风炉使用球的数值热风炉主要性能参数柳钢6号高炉球式热风炉设计参数青钢500m³高炉卡鲁顶燃式热风炉设计参数烘炉操作及改进1 烘炉准备工作青钢两座500m³高炉采用卡鲁金顶燃式热风炉均采用天津热能设备厂专用内燃式烘炉器进行烘炉。
烘烤器安装在热风炉顶部燃烧器的下部点火孔上。
改设备用柴油作燃料,产生的热气体,经配风系统调节送风温度。
送风系统出口风速达到80m/s,产生很大的动能,搅动燃烧产物循环使炉内温度均匀,提高了烘炉质量。
烘炉前需要做好如下工作:1)热风炉的修建和检修工作全部完成,并达到质量要求。
2)热风炉系统各阀门必须进行全部联合、联锁试车,各机电设备运转正常。
3)热风炉冷却水通水正常。
4)各仪表必须正常运转,保证准确可靠,特别是炉顶温度,废气温度、煤气压力表必须保证好用。
5)各热风炉试漏合格。
6)烟囪烘好,具有抽力。
7)如烘炉期间,高炉内常有人施工,热风炉与高炉必须彻底隔断。
8)一切烘炉设备安装完毕,提供三相380v动力电源,24h不间断,供三台18.5kw助燃风机、油泵及现场照明使用。
9)准备好可装10吨柴油的油罐。
10)提供不间断压缩空气源,压力>0.60MPa。
11)烘炉报表台账等数据记录及材料器具准备完毕。
烘炉曲线的制订青钢5、6号高炉热风炉在炉顶和上部高温区均采用了硅砖砌筑。
烘炉曲线由俄方提供,计划烘炉30天,如图中I所示。
烘炉时严格按烘炉曲线升温,温度误差±2°C。
在烘炉过程中实验了两种烘炉曲线,5号高炉的热风炉实际烘炉时间为30天,6号高炉的热风炉为23天。
这两座高炉热风炉计划和实际烘炉曲线如图2所示。
图3为霍戈文(Hoogov-ens)供鞍钢新一号高炉(3200m³)硅砖热风炉的烘炉曲线。
图2 改进前后卡鲁金顶燃式硅砖热风炉烘炉曲线I—改进前(青钢5号高炉热风炉烘炉曲线);Ⅱ--改进后(青钢6号高炉热风炉烘炉曲线硅砖热风炉的烘炉曲线是最复杂的一种。
高炉操作02高炉操作基本内容

表料,以便调整煤气流达到合理分布。表 2-5 中, A,B 分别代表不同的装料顺序,m,n 则分别代表批数,加重边缘的程度取决于 m/(m+n)的比值,比值增大则加重边缘,反之则疏松边缘。随着正装比例的增 加,煤气利用得到改善,综合煤气 CO2 含量会进一步提高。
选定各种合理操作制度的根据。 2.2 热制度的选择 2.2.1 表示热制度的参数 高炉生产操作者特别重视炉缸的热状态,因为决定高炉热量需求和燃料比的
是高炉下部,所以常用说明炉缸热状态的一些参数作为热制度的指标。 (1)铁水温度。1350~1500℃,以铁水温度表示,又称为物理热。 (2)铁水[Si]含量。[Si]又叫化学热,[Si]高表示温度高。 2.2.2 热制度的选择 确定高炉热制度时,一般要考虑以下诸因素与相应的条件: (1)冶炼生铁的品种 (2)本厂的原料条件 (3)高炉本体与设备状态 (4)技术与管理水平 (5)高炉容积的大小 2.2.3 影响热制度的因素 影响炉缸热制度的因素有:
冶金答案

第一讲概述、化学原理填空题:1、炼铁的还原剂主要有三种,即 C 、 H 和 CO 。
2、铁矿石在高炉中冶炼要三个基本作用:还原作用、造渣作用、渗碳作用。
3、间接还原:用 CO、H2为还原剂还原铁的氧化物,产物无 CO2、 H2O的还原反应。
4、直接还原:用 C作为还原剂,最终气体产物为CO的还原反应。
5、高炉内非铁元素的还原,主要包括 Si 、 Mn 、 P 等的还原。
6、高炉炼铁是用还原剂在高温下将铁矿石或含铁原料还原成液态生铁的过程。
7、高炉解剖研究证明,按炉料物理状态的不同,高炉大致分为五个区域,分别为块状带、软熔带、滴落带、风口带、渣铁带。
8、高炉料中铁的氧化物有多种,但最后都是经 FeO 的形态还原成金属铁。
9、根据温度不同,高炉内还原过程划分为三个区,低于800℃的块状带是间接还原区;800~1100℃的是间接还原与直接还原共存区;高于1100℃的是直接还原区。
10、滴落带是指渣铁全部熔化,穿过__焦炭层___下到炉缸的区域。
选择题:1. 高炉冶炼过程中,P的去向有( D )。
A.大部分进入生铁B.大部分进入炉渣C.一部分进入生铁,一部分进入炉渣D.全部进入生铁2. 高炉煤气和部分焦炭夺取铁矿石中的氧,这一过程称作( D )。
A.氧化过程 B.物理反应 C.相互作用 D.还原过程3. 高炉冶炼中焦炭在风口区燃烧产生的温度高达( D )℃。
A.1400~1600 B.1600~1800 C.1700~1900 D.1800~21004.高炉解体调研查明,炉料在炉内基本上是按装料顺序( C )分布的。
A.矿石超越焦炭 B.逐步混合 C.呈层状下降 D. 杂乱无章5、铁氧化物中难以还原的是( C )。
A、Fe2O3B、Fe3O4C、FeO6、炉内低于800℃区域是哪种还原为主( B )。
A.直接还原 B.间接还原 C.二种还原均在7、高炉冶炼条件下,下列氧化物最易还原的是(C )。
A.CaO B.SiO2C.FeO8、高炉内铁氧化物的还原顺序是(B)。
高炉炉体系统设计
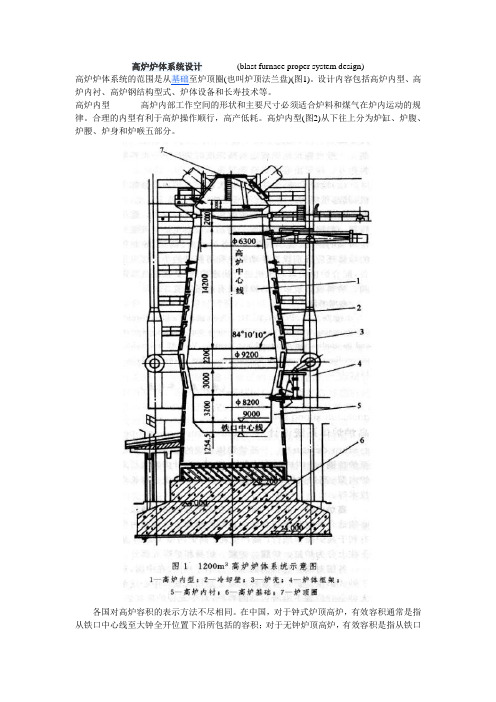
高炉炉体系统设计(blast furnace proper system design)高炉炉体系统的范围是从基础至炉顶圈(也叫炉顶法兰盘)(图1)。
设计内容包括高炉内型、高炉内衬、高炉钢结构型式、炉体设备和长寿技术等。
高炉内型高炉内部工作空间的形状和主要尺寸必须适合炉料和煤气在炉内运动的规律。
合理的内型有利于高炉操作顺行,高产低耗。
高炉内型(图2)从下往上分为炉缸、炉腹、炉腰、炉身和炉喉五部分。
各国对高炉容积的表示方法不尽相同。
在中国,对于钟式炉顶高炉,有效容积通常是指从铁口中心线至大钟全开位置下沿所包括的容积;对于无钟炉顶高炉,有效容积是指从铁口中心线至炉喉上沿之间的容积。
欧美诸国把从风口中心线至料线之间的容积称为工作容积。
日本把从铁口底端至料线之间的容积称为内容积。
料线位置,日本定在大钟全开位置底面以下一米的水平面上,美国一般定在炉喉高度的一半处。
对于高炉内型各部尺寸的合理比例及算法,是雷得布尔(A.jejeyp)在他1878年出版的著作里首次提出的。
巴甫洛夫(M.A.ПaBJoB)提出用下式表示全高(H)与有效容积(V u)的关系:H= n (V u )1/3。
式中n是大于2.85的数字,并且H:D的比值愈高,n的数值愈大。
有效容积按要求的生铁日产量和利用系数求出后,用上式可求出全高H。
炉腰直径D可按公式D =(V u/0.54H) 1/2求出,然后再决定内型其它尺寸。
巴氏建议选择炉缸直径应以燃烧强度(每小时每m2炉缸面积燃烧的焦炭量,用kg表示)为出发点。
美国莱斯(Owen Rice)在计算燃烧强度时所指的炉缸面积是从风口前端起6f t 环状带的面积。
拉姆(A.H.Pamm)内型每个尺寸都是与有效容积成一定方次的函数,建议用经验公式x=cV n u 计算内型各部分尺寸x,式中n和c对内型各部分尺寸是固定的系数。
高炉内型主要与原、燃料条件和操作制度有关。
合适的内型来源于生产实践,实际上高炉内型的设计大都是根据冶炼条件类似的同级高炉的生产实践进行分析和比较确定。
315万吨高炉有效容积利用系数

315万吨高炉有效容积利用系数引言高炉是冶金行业重要的炼铁设备之一,其有效容积利用系数是衡量高炉运行效率的重要指标之一。
本文将深入探讨315万吨高炉的有效容积利用系数及其影响因素,并提出相应的优化建议。
什么是315万吨高炉有效容积利用系数?有效容积利用系数是指高炉在一定时间内实际生产能力与理论生产能力之间的比值。
315万吨高炉有效容积利用系数即该规模高炉在一定时间内实际生产的铁水量与理论最大生产铁水量之间的比值。
该系数是评估高炉运行效率和生产能力利用程度的重要指标。
影响315万吨高炉有效容积利用系数的因素1.原料配比原料配比是决定高炉生产能力的关键因素之一。
合理的原料配比可以提高高炉的产量和效率。
合适的焦比、矿石粒度和燃料质量等都会对高炉的有效容积利用系数产生重要影响。
2.炉渣特性炉渣是高炉冶炼过程中生成的一种副产品,其特性直接关系到高炉运行的顺畅程度和效率。
合理的炉渣特性可以提高高炉内的热传导和气体流动,从而提高高炉的有效容积利用系数。
3.铁口形状和温度铁口是高炉排出铁水的出口,其形状和温度对铁水的排出速度和铁液流动的平稳程度有着重要影响。
合理设计和控制铁口形状和温度可以提高高炉的出铁效率和有效容积利用系数。
4.高炉内部结构高炉内部结构对高炉的煤气流动和热传导等过程有着重要影响。
合理设计高炉内部结构,如风口和炉壁冷却设备等,可以提高高炉的流程运行稳定性和生产能力。
优化315万吨高炉有效容积利用系数的建议1.优化原料配比分析不同原料的化学成分和物理特性,合理调整原料配比,以实现更高的炼铁生产能力和高炉效率。
2.控制炉渣特性通过调整炉渣成分和炉渣形态,控制炉渣脱渣速度和流动性,提高高炉内部的热传导和气体流动,从而提高高炉的有效容积利用系数。
3.定期维护和清理铁口定期检查和清理铁口,确保其畅通无阻,控制铁口温度,避免铁水倒灌和冷凝现象,提高高炉的出铁效率和容积利用系数。
4.优化高炉内部结构设计根据高炉的规模和运行情况,优化高炉内部结构设计,如增加风口数量和布置,改善炉壁冷却设备等,以提高高炉的流程运行稳定性和产能利用效率。
高炉容积利用系数
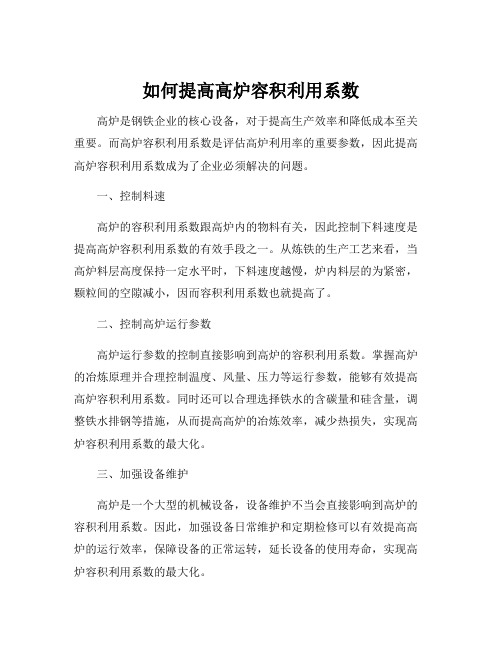
如何提高高炉容积利用系数高炉是钢铁企业的核心设备,对于提高生产效率和降低成本至关重要。
而高炉容积利用系数是评估高炉利用率的重要参数,因此提高高炉容积利用系数成为了企业必须解决的问题。
一、控制料速
高炉的容积利用系数跟高炉内的物料有关,因此控制下料速度是提高高炉容积利用系数的有效手段之一。
从炼铁的生产工艺来看,当高炉料层高度保持一定水平时,下料速度越慢,炉内料层的为紧密,颗粒间的空隙减小,因而容积利用系数也就提高了。
二、控制高炉运行参数
高炉运行参数的控制直接影响到高炉的容积利用系数。
掌握高炉的冶炼原理并合理控制温度、风量、压力等运行参数,能够有效提高高炉容积利用系数。
同时还可以合理选择铁水的含碳量和硅含量,调整铁水排钢等措施,从而提高高炉的冶炼效率,减少热损失,实现高炉容积利用系数的最大化。
三、加强设备维护
高炉是一个大型的机械设备,设备维护不当会直接影响到高炉的容积利用系数。
因此,加强设备日常维护和定期检修可以有效提高高炉的运行效率,保障设备的正常运转,延长设备的使用寿命,实现高炉容积利用系数的最大化。
综上所述,提高高炉容积利用系数需要从控制料速、控制高炉运
行参数以及加强设备维护等多方面入手,以实现高炉利用率的最大化,提高生产效益。
高炉工作容积
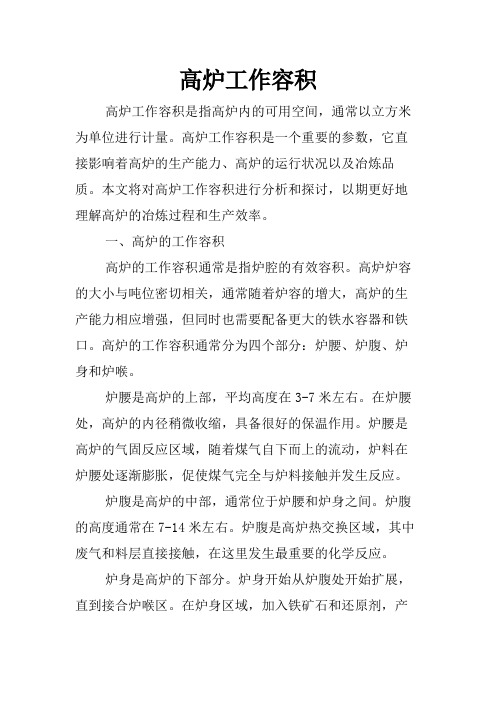
高炉工作容积高炉工作容积是指高炉内的可用空间,通常以立方米为单位进行计量。
高炉工作容积是一个重要的参数,它直接影响着高炉的生产能力、高炉的运行状况以及冶炼品质。
本文将对高炉工作容积进行分析和探讨,以期更好地理解高炉的冶炼过程和生产效率。
一、高炉的工作容积高炉的工作容积通常是指炉腔的有效容积。
高炉炉容的大小与吨位密切相关,通常随着炉容的增大,高炉的生产能力相应增强,但同时也需要配备更大的铁水容器和铁口。
高炉的工作容积通常分为四个部分:炉腰、炉腹、炉身和炉喉。
炉腰是高炉的上部,平均高度在3-7米左右。
在炉腰处,高炉的内径稍微收缩,具备很好的保温作用。
炉腰是高炉的气固反应区域,随着煤气自下而上的流动,炉料在炉腰处逐渐膨胀,促使煤气完全与炉料接触并发生反应。
炉腹是高炉的中部,通常位于炉腰和炉身之间。
炉腹的高度通常在7-14米左右。
炉腹是高炉热交换区域,其中废气和料层直接接触,在这里发生最重要的化学反应。
炉身是高炉的下部分。
炉身开始从炉腹处开始扩展,直到接合炉喉区。
在炉身区域,加入铁矿石和还原剂,产生铁液和副产物。
炉身是铁液产生的主体区域。
炉身对炉料的均衡派生具有举足轻重的作用。
炉喉通常位于炉身的下方,是高炉底部到炉腔下部的过渡区域。
炉喉的宽度通常比炉身的直径小一些,最终汇入高炉的铁口。
二、高炉的炉容在高炉的冶炼过程中,高炉的炉容也是非常关键的参数。
高炉的炉容是指高炉的总体积。
炉容的大小直接决定高炉的生产能力,炉容越大,高炉产量也就越大。
高炉的炉容主要由炉身和炉腰两部分组成,其中,炉身部分是高炉的主体结构,炉腰部分则是高炉的加热区域。
高炉的炉容随着炉身直径的增大而增加。
高炉炉容的大小还会受到工作条件、生产目标等因素的影响。
三、高炉的工作容积与炉料质量高炉内的工作容积直接影响着炉料的质量和产量。
炉腰、炉腹、炉身和炉喉共同构成了高炉的内部结构,也是气固两相流的操作空间。
高炉的内部结构对炉料分级有着显著的影响。
高炉本体尺寸设计
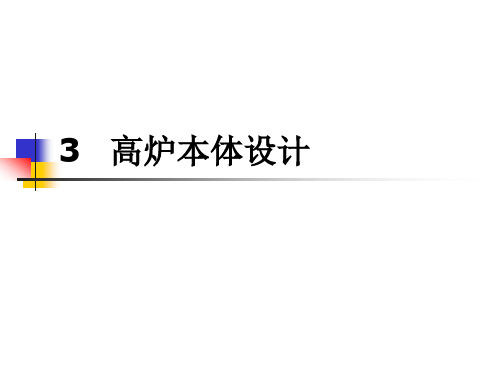
2. 计算法:
计算法即经验数据的统计法。 计算时可选定某一关系式,算出某一主
要尺寸,再根据炉型中各部位尺寸间的关系 式作炉型计算,最后校核炉容,修定后确定 设计炉型。
经验公式 :
大型高炉:
Hu 6.44Vu0.2
d 0.32Vu 0.45
适应于我国50~70年代1000~2000m3高 炉的基本情况,炉型为瘦长型。
风口数目:
n 2(d 2) 2 (9.8 2) 23.6
取 n 24个
风口结构尺寸: 选取: a=0.5m 则炉缸高度:
h1 hf a 3.0 0.5 3.5(m)
(4)死铁层厚度
选取: h0 1.5m
(5)炉腰直径、炉腹角、炉腹高度
选取:
D d 1.13
铁口中心线到炉底砌砖表面之间的 距离称为死铁层厚度。
作用:
(1)残留的铁水可隔绝铁水和煤气对炉底 的冲刷侵蚀,保护炉底; (2)热容量可使炉底温度均匀稳定,消除 热应力的影响; (3)稳定渣铁温度。
死铁层厚度: 新设计高炉的死铁层厚度h0=0.2d。
3.1.3 炉型设计与计算
名词概念:
(1)设计炉型:按照设计尺寸砌筑的炉型; (2)操作炉型:指高炉投产后,工作一段时 间,炉衬被侵蚀,高炉内型发生变化后的炉型;
2. 炉缸
高炉炉型下部的圆筒部分为炉缸, 炉缸的上、中、下部位分别设有风口、 渣口与铁口。
(1)炉缸直径
炉缸截面燃烧强度:指每小时每平方 米炉缸截面积所燃烧的焦炭的数量, 一般为1.0~1.25t/m2·h。
d 0.23 I Vu i燃
式中: I——冶炼強度, t/m3·d
i 燃——燃烧強度,t/m2·h
高炉容积利用系数
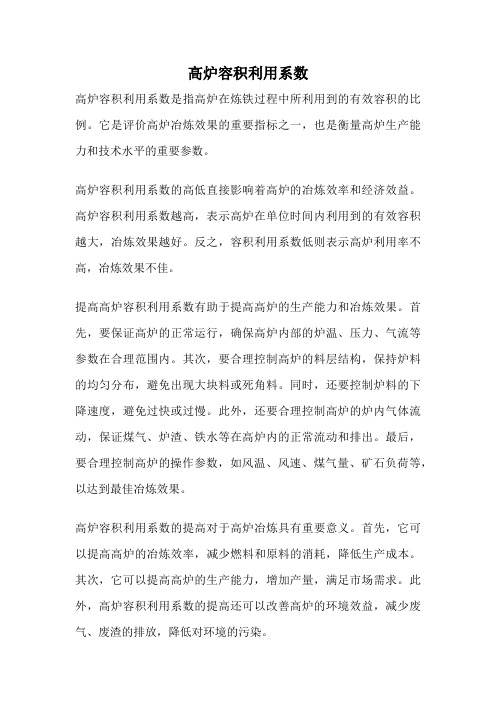
高炉容积利用系数高炉容积利用系数是指高炉在炼铁过程中所利用到的有效容积的比例。
它是评价高炉冶炼效果的重要指标之一,也是衡量高炉生产能力和技术水平的重要参数。
高炉容积利用系数的高低直接影响着高炉的冶炼效率和经济效益。
高炉容积利用系数越高,表示高炉在单位时间内利用到的有效容积越大,冶炼效果越好。
反之,容积利用系数低则表示高炉利用率不高,冶炼效果不佳。
提高高炉容积利用系数有助于提高高炉的生产能力和冶炼效果。
首先,要保证高炉的正常运行,确保高炉内部的炉温、压力、气流等参数在合理范围内。
其次,要合理控制高炉的料层结构,保持炉料的均匀分布,避免出现大块料或死角料。
同时,还要控制炉料的下降速度,避免过快或过慢。
此外,还要合理控制高炉的炉内气体流动,保证煤气、炉渣、铁水等在高炉内的正常流动和排出。
最后,要合理控制高炉的操作参数,如风温、风速、煤气量、矿石负荷等,以达到最佳冶炼效果。
高炉容积利用系数的提高对于高炉冶炼具有重要意义。
首先,它可以提高高炉的冶炼效率,减少燃料和原料的消耗,降低生产成本。
其次,它可以提高高炉的生产能力,增加产量,满足市场需求。
此外,高炉容积利用系数的提高还可以改善高炉的环境效益,减少废气、废渣的排放,降低对环境的污染。
然而,提高高炉容积利用系数也面临一些挑战。
首先,高炉冶炼是一个复杂的过程,涉及到多个因素的综合作用,因此要全面考虑各种因素的影响。
其次,高炉冶炼是一个动态过程,需要根据实际情况进行调整和优化。
最后,高炉冶炼是一个高温、高压的工艺过程,对设备和操作人员的要求较高,需要保证安全生产。
高炉容积利用系数是评价高炉冶炼效果的重要指标,提高容积利用系数对于提高高炉的生产能力和冶炼效果具有重要意义。
要实现高炉容积利用系数的提高,需要从多个方面进行优化和调整,包括高炉的正常运行、料层结构的控制、炉内气体流动的调整以及操作参数的控制等。
同时,还需要克服一些挑战,全面考虑各种因素的影响,根据实际情况进行调整和优化,确保高炉的安全生产。
高炉有效容积的定义

高炉有效容积的定义高炉是冶金行业中常用的设备,用于将铁矿石还原为铁。
而高炉有效容积是衡量高炉生产能力的一个重要指标。
本文将对高炉有效容积进行定义和解析。
高炉有效容积是指高炉在一定条件下能够容纳的炉料的体积。
它是高炉设计和运行的重要参数之一,直接影响高炉的生产能力和经济效益。
高炉有效容积与高炉的内部结构有关。
通常,高炉由上部、中部和下部组成。
上部主要包括炉缸、炉喉和炉身。
中部是高炉的主要部分,包括炉腹、炉腰和炉腿。
下部是高炉的底部,包括炉底和铁口。
在高炉运行过程中,铁矿石、焦炭和石灰石等炉料通过高炉顶部的料斗进入高炉炉缸,然后通过炉喉进入炉身。
在炉身内,炉料逐渐下降,并在高温下发生化学反应,最终得到铁和炉渣。
铁通过铁口排出,炉渣则通过炉底的渣口排出。
高炉有效容积是指炉料在高炉内部能够自由下降的空间。
它与高炉的内部尺寸、形状以及炉料的物理性质有关。
高炉的设计和改造需要根据高炉有效容积来确定合适的尺寸和形状,以确保炉料能够充分下降,并保证高炉的正常运行。
高炉有效容积的大小直接影响高炉的生产能力。
如果高炉有效容积较小,炉料下降的空间有限,会导致炉料堆积在炉顶或炉中部,影响高炉正常生产。
因此,高炉有效容积的大小需要根据高炉的设计和运行要求进行合理确定。
高炉有效容积的计算通常采用几何法或数值模拟方法。
几何法是通过高炉内部的尺寸和形状参数来计算高炉有效容积。
数值模拟方法则是利用计算机模拟高炉内部流动和化学反应等过程,从而得到高炉有效容积。
高炉有效容积的确定需要考虑多个因素。
首先是炉料的物理性质,包括炉料的粒度、密度和流动性等。
不同的炉料在高炉内部的下降速度和堆积特性有所不同,因此需要根据具体情况来确定高炉有效容积。
其次是高炉的内部结构和操作参数,包括炉身直径、炉腹和炉腰的形状以及炉温、风量和炉压等。
这些参数对高炉的炉料下降和流动有着重要影响,需要进行综合考虑。
最后是高炉的生产要求,包括产量、炉渣排出和铁口操作等。
- 1、下载文档前请自行甄别文档内容的完整性,平台不提供额外的编辑、内容补充、找答案等附加服务。
- 2、"仅部分预览"的文档,不可在线预览部分如存在完整性等问题,可反馈申请退款(可完整预览的文档不适用该条件!)。
- 3、如文档侵犯您的权益,请联系客服反馈,我们会尽快为您处理(人工客服工作时间:9:00-18:30)。
论高炉容积的选择刘琦钢铁联合企业中高炉容积的选择,与企业生产规模、产品结构、高炉座数、投资能力、资源状况、所选高炉的生产效率以及日常组织生产是否顺畅等诸多因素密切相关。
必须综合考虑才能作出科学、合理的选择。
由于这种选择对企业未来的生产运行、经营状况、经济效益和进一步的发展有重要影响,在市场经济条件下企业应经过全面思考,科学论证后,慎重决策。
在此拟就采用传统流程(高炉-转炉)的钢铁联合企业如何科学地选择高炉炉容的问题,谈一些意见,供决策者参考。
一、由企业规模和产品结构考虑钢铁联合企业的规模以年产粗钢能力为代表,以吨钢耗铁水0.9-0.95吨计算,就可得出生铁的生产规模。
再根据各类炉容的高炉能够达到的利用系数(每昼夜、每立方米炉容产铁量),即可计算出总炉容。
由生产组织顺畅出发,现代钢铁企业的高炉座数以2-4座为好,而以3-4座为最佳。
单高炉生产因煤气系统处理复杂,为钢铁生产之大忌。
两座高炉虽无煤气之忧,但高炉检修时,对后部工序生产影响太大。
而3-4座就好得多。
但超过4座,会带来如原料供应、铁水运输等诸多生产组织方面的困难,也不可取。
当然,到底选几座还与场地大小有关。
生产规模和高炉座数决定后,就可据此决定每座高炉容积的大小了。
企业适宜的规模,最主要是由产品结构决定的。
如果企业的产品主要是棒、线材、窄带等建筑用材,因其附加值低,轧机规模小,产品销售半径不大,所以100万吨/年左右就可以形成经济规模,一般不应超过300万吨/年。
这类企业可以选择较小容积的高炉。
这一点,对于产品结构中建筑用钢材占很大比例的中国现阶段而言,与以板管和大型材为主的发达国家有所不同。
根据当前我国各类高炉所达到的利用系数水平,100-150万吨/年钢的企业,可以建设2-3座380-420m3的高炉;200万吨/年钢的企业,可建设420-500m3的高炉3-4座;250万吨/年钢的企业可建设500m3的高炉4座或750m3的高炉3座;300万吨/年钢的企业可建设750m3级的高炉3-4座。
也可建1200m3高炉3座。
如果企业的产品以热连轧板卷为主,因轧机规模大,并且必须用大吨位的转炉与之匹配,要求企业规模相对较大。
其经济规模的下限是300万吨/年钢,上限在七八十年代国际上曾认为是850万吨/年钢。
近二、三十年因高炉容积和转炉吨位加大,特别是>4000m3高炉和≥300吨转炉的出现,被放大到1200-1500万吨/年钢。
年产钢的规模与高炉容积的配套可以是:350-500万吨钢配2000m3×2或1750-2000m3×3;也可以1200m3×4;500-650万吨/年钢配2000-2500m3×3;550-800万吨/年钢配3200m3×2-3;800-1500万吨/年钢配3200m3×3-4或4000-4500m3×3-4。
国内在高炉容积和产钢能力配套上曾出现误区。
一是拥有大高炉、大转炉,钢的能力达到800万吨以上,而最终产品只是棒线材,白白浪费了炼铁、炼钢功能,如同用尼子大衣的衣料做了许多短裤。
并且大转炉配小方坯连铸出钢温度拉得很高,极不合理。
而且因产品销售半径小,造成销售困难。
二是钢产量已超过300-400万吨,而高炉容积仍是300-400m3,座数高达6-7座或更多,造成生产组织上的困难,劳动生产率也低。
由以上论述可知,选择高炉容积应遵循钢铁工业内在的技术经济规律。
既不能因容积较小的高炉投资省而普遍建设中小型高炉,也不能盲目追求大型化而普遍建设大型高炉。
二、从高炉指标考虑因为容积较小的高炉容积与炉缸截面积的比值比大型高炉小,所以,相同冶炼强度下中小型高炉(在本文中指<1000m3高炉)单位炉缸面积上产生的煤气量小。
也就是说,中小型高炉更容易强化。
虽然在高炉设计上大型高炉(在本文中指>1000m3高炉)采用了较高的炉顶压力,但在实际生产中,中小型高炉还是达到了比大型高炉高得多的冶炼强度,从而取得了高得多的利用系数。
因此,不同容积的高炉,每1m3容积在产品数量上的贡献是不同的。
国内目前正在生产和建设(或拟建)中的高炉容积系列大致是4000m3、3200m3、2500m3、2000m3、1200m3、1000m3、750m3、620m3、380m3。
此处讨论中,将与上述炉容接近的合并列入上述系列。
低于300m3的高炉不作讨论。
我将2002和2003年参加炼铁情报网统计的149座和188座高炉的利用系数和燃料比(焦比+煤比)按炉容级别分类统计。
因只有1-2座3200m3高炉生产,故指标统计在2500m3一级中。
另外,攀钢4座1200m3级高炉,因冶炼特殊矿,品位偏低,燃料比高,在统计该级别燃料消耗时扣除。
容积较小的高炉,利用系数高。
特别是300-500m3的高炉,虽然这一级别的高炉座数较多,生产水平参差不齐,但在2002年高炉利用系数还是比1000m3、1200m3和2000m3三个级别分别高51.2%、50.2%、53.3%;比2500m3级和4000m3级高47.4%和40%,2003年也极为相近。
4000m3和2500m3级的大型特大型高炉,一般都拥有优越的装备、精良的原料和一流的操作水平,因此能达到较高的利用系数。
而1000m3、1200m3和2000m3的高炉,装备和精料水平多数不如上边两档,因此,这三个级别高炉的系数普遍比以上两组偏低。
而750m3、620m3和380m3三个级别,近几年由于精料和设备操作水平的提高,容易强化的特点得到充分发挥,达到很高的利用系数,成为中国高炉技术的亮点。
随着高炉容积的缩小,燃料消耗上升。
这是大型高炉无可争议的优势,也是符合高炉基本理论的。
因为随着高炉容积缩小,料柱变短、煤气在上升过程中与矿石接触的机会减少。
但是,从表1也可看出,这种差距比前些年小了许多。
这是因为近些年来,中小高炉的精料水平明显提高,有些甚至赶上或超过了大型高炉。
因而出现虽然中小高炉冶炼强度很高但燃料消耗却不致过高的局面。
高炉的业绩,代表了我国当代的炼铁水平。
而且这种优秀的高炉不是个别的,各类高炉中都有一批达到或接近此等水平。
特别是容积较小的高炉,达到高水平的更为普遍。
2003年≤500m3的高炉中,利用系数≥3.3吨/m3?日的就有40座,其中21座>3.50吨/m3?日。
以产量而论,许多中小高炉的日均产量超过比他们容积大得多的高炉。
如杭钢450m3与青岛500m3高炉的日均产量就赶上甚至超过好几座1000m3级的高炉。
而莱钢750m3高炉2004年前几个月的日均产量不仅超过(除湘钢1#以外)所有1000m3级高炉,并且超过了5座1200-1513m3的高炉。
笔者在这里不是主张不要建设1000-1200m3高炉,而去普遍推广500-750m3的高炉,只是想说明在评价或建设高炉时,不要仅着眼于容积,更应注意其实际产铁能力。
三、由投资考虑钢铁工业是投资密集型产业,特别是高炉建设更是需要投入大量的资金。
因此,钢铁行业的投资者,应根据筹资能力量力而行。
表3列出的是近几年各种炉容级别一座高炉的投资量。
在具体高炉建设中,因征地价格、包含范围、装备水平及原有公用设施的利用等的差异,实际投资与表3数据可能略有不同,但大致范围是不差的。
按理,设备越是大型化,单位容积的投资应该越少。
但这一规律在国内高炉建设上并不明显。
特别自2000m3以下,倒是容积越小,单位容积投资越省。
这主要是因为,炉容越大,装备越复杂,档次越高,特别是所需造价高得多的进口设备越多的缘故。
按表3,2000m3以上的高炉,单位容积投资比450m3高炉要增加25.4%-34.5%。
特别要指出的是,在国内的实践中,较小的高炉,利用系数要高得多。
因此,若按年产1吨生铁的投资量考虑,投资随炉容的减少而下降的幅度,比按容积计算要大得多。
尤其是各级别高炉都按先进的利用系数水平(各级别高炉中少数高炉达到的年或月平均先进水平)计算时,这种差距就更为明显,450m3高炉的吨铁投资要比3200m3和4000m3高炉节省一倍还多。
既然容积较小的高炉单位容积和单位产量的投资省,我以为,在现阶段,应该允许因生产建筑钢材或周边市场较小而产钢规模不大的企业(如≤300万吨);或是筹资能力不够大的企业,根据他们的需要和可能,建设相应容积的高炉。
这也是市场经济体制下,企业自主决策应该有的权利。
特别是对于正在崛起的民营企业和西部地区,应该允许他们有一个从小到大的发展过程。
当然,为了避免过度竞争和形成恶性循环,对于过度的能力扩张和重复建设,特别是针对近两年钢铁投资过热的局面,政府还是应该从政策上加以抑制,而当前最有效的办法是控制建设用地和投资贷款。
我国现有的中小型高炉(这里主要指300-1000m3高炉),仍占据着我国生铁总产量的半壁江山以上。
根据今明两年新建和改造扩容的计划,到2005年上述比例将有所改变。
2003年的2亿吨生铁,有61.8%是中小高炉生产的。
其中<500m3的占49.7%。
随着我国钢铁工业的发展和结构调整的需要,近两年高炉大型化取得可喜进展,新建了一批大型高炉,另有一批大型高炉正在建设中。
特别是原来只有中小型高炉的企业,纷纷建起了大型高炉。
今后几年高炉容积结构将发生变化。
但是,目前中小高炉存量太多,而且还有一批中小高炉在建设中,所以,预计到2005年中小高炉的产量比仍将高达56.5%。
今后几年,随着国家对钢铁投资过热的控制,这一进程可能会加快,但是仍然可以肯定,我国高炉大型化的道路会是相当漫长的。
中小高炉在相当长的时间内,仍将在我国国民经济的运行和发展中起着重要的支撑作用;同时也是钢铁工业取得经济效益和赖以生存和未来发展(如为大型化积累资金)的重要基石。
在重点关照大高炉和实行大型化的同时,对于存量中小高炉要理智地对待,使其有生存和适当发展的空间。
四、从生铁成本考虑降低产品成本,追求利润最佳化,永远是企业生产经营活动的核心目标。
国内钢铁企业的生铁成本,主要取决于原燃料资源的占有和取得。
特别是近来由于铁矿石和煤炭资源供应全面紧张,价格猛涨,这一特点更加突出。
凡是自有矿石比例大;靠近矿山和煤炭产地;沿江(长江)沿海水运费用低,便于使用进口矿;与国外供矿商和海运公司签有长期供矿运输合同;自身炼焦能力强,不用或少用外购焦炭的企业,生铁成本就低。
这一点与高炉容积大小无关。
笔者在几年前进行的生铁成本调查中发现,由于大型高炉对原燃料要求严格,原燃料加工费较高,生铁成本往往比中小型高炉高。
特别是在同一个企业内出现这种现象,很能说明问题。
大型高炉在成本上的优势主要在于燃料和动力消耗较低。
中小型高炉由于利用系数高,建设投资低,折旧和其他固定费用要比大高炉低。
两相抵消,大高炉在成本上基本没有优势可言。