电机定、转子片冲压工艺及模具设计讲解
y160l-6电机定、转子冲片设计

y160l-6电机定、转子冲片设计Y160L-6电机定子和转子冲片设计是电机制造中重要的部分,对电机的性能起着至关重要的作用。
定子和转子冲片的设计需要遵循一定的原则和规范,以保证电机能够正常运行。
一、定子设计定子是电机中静止不动的部分,它负责产生旋转磁场。
定子包括一定数量的定子线圈,通过交变电流供电。
定子线圈的数量、截面积、匝数等参数是定子设计中需要考虑的关键因素。
首先,定子线圈的数量应该与电机的规格相适应,以达到最佳功率和效率。
若定子线圈数量不足,则电机的功率将会受损,效率也会降低。
其次,定子线圈的截面积应该满足电机工作时所需的电流,以保证产生足够的磁场来驱动转子。
匝数的选取也需要满足电机工作条件下的电流和磁场强度。
最后,定子线圈的设计应该充分考虑绕制工艺和材料要求。
定子线圈通常采用铜线绕制而成,应保证导体与绝缘层之间的电性能和热性能,以较低的绕制成本和较高的电机效率来实现优秀的性能。
二、转子冲片设计转子是电机中旋转的部分,它负责产生电磁感应并驱动负载。
转子通常由磁体、转轴和冲片共同构成。
冲片是转子最重要的组成部分之一,通过与定子磁场交互作用来完成电机的转动。
冲片的设计需要确保磁场运动的规律和转子的稳定性。
冲片的数量和形状应该与定子的设计相匹配,以保证磁场的连续性和充分的旋转力矩。
冲片的宽度和厚度应该由冲片和直流电机工作条件来确定,以保证电机产生较大的扭矩。
在冲片的材料选择方面,通常采用硅钢或其他磁性材料。
硅钢具有低的磁滞和铁损,这可以减少电机的能量损耗和发热。
其他磁性材料的选择应考虑材料的磁导率和饱和磁场强度,以满足电机工作条件下的磁场要求。
总的来说,定子和转子冲片的设计是电机性能成功的关键之一。
在设计时,应该遵循一定的原则和规范,以保证电机的可靠性、高效性和经济性。
定子片转子冲压工艺及其模具设计论文
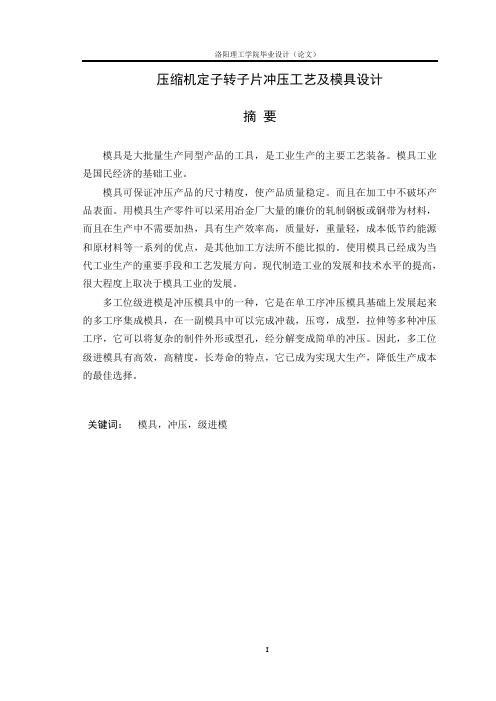
压缩机定子转子片冲压工艺及模具设计摘要模具是大批量生产同型产品的工具,是工业生产的主要工艺装备。
模具工业是国民经济的基础工业。
模具可保证冲压产品的尺寸精度,使产品质量稳定。
而且在加工中不破坏产品表面。
用模具生产零件可以采用冶金厂大量的廉价的轧制钢板或钢带为材料,而且在生产中不需要加热,具有生产效率高,质量好,重量轻,成本低节约能源和原材料等一系列的优点,是其他加工方法所不能比拟的。
使用模具已经成为当代工业生产的重要手段和工艺发展方向。
现代制造工业的发展和技术水平的提高,很大程度上取决于模具工业的发展。
多工位级进模是冲压模具中的一种,它是在单工序冲压模具基础上发展起来的多工序集成模具,在一副模具中可以完成冲裁,压弯,成型,拉伸等多种冲压工序,它可以将复杂的制件外形或型孔,经分解变成简单的冲压。
因此,多工位级进模具有高效,高精度,长寿命的特点,它已成为实现大生产,降低生产成本的最佳选择。
关键词:模具,冲压,级进模The Stamping Process And Mold Design Of Stator And RotorPiece Of CompressorABSTRACTMolds to form a mass production of industrial production facilities, is the main techniques and equipment。
Mold industry is the foundation of the national economy industry。
Tool to ensure accuracy of the ram of the product sizes, and make products quality。
And the process of the surface of the product。
Die in the production of parts of the metallurgical factory of rolled steel plates or with a material,And in production don't need, with high efficiency, quality, light weight and low cost to save energy and raw materials for a range of advantages,is Other process could compare with。
定转子冲片生产工艺的改进与模具设计
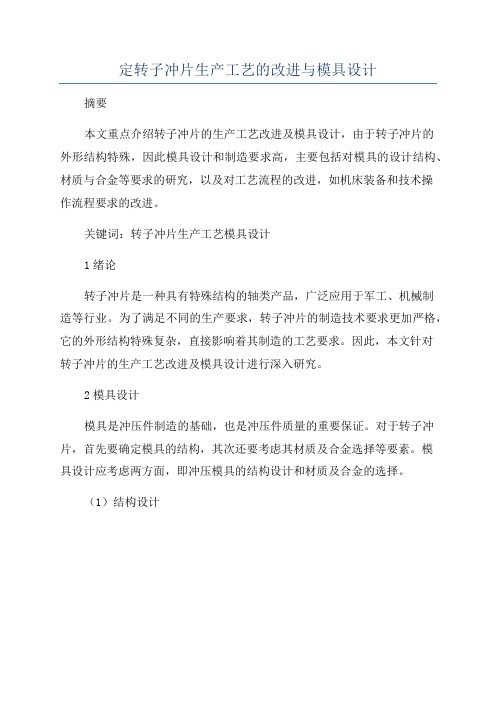
定转子冲片生产工艺的改进与模具设计摘要
本文重点介绍转子冲片的生产工艺改进及模具设计,由于转子冲片的
外形结构特殊,因此模具设计和制造要求高,主要包括对模具的设计结构、材质与合金等要求的研究,以及对工艺流程的改进,如机床装备和技术操
作流程要求的改进。
关键词:转子冲片生产工艺模具设计
1绪论
转子冲片是一种具有特殊结构的轴类产品,广泛应用于军工、机械制
造等行业。
为了满足不同的生产要求,转子冲片的制造技术要求更加严格,它的外形结构特殊复杂,直接影响着其制造的工艺要求。
因此,本文针对
转子冲片的生产工艺改进及模具设计进行深入研究。
2模具设计
模具是冲压件制造的基础,也是冲压件质量的重要保证。
对于转子冲片,首先要确定模具的结构,其次还要考虑其材质及合金选择等要素。
模
具设计应考虑两方面,即冲压模具的结构设计和材质及合金的选择。
(1)结构设计。
电机定转子片冲压工艺及模具设计讲解
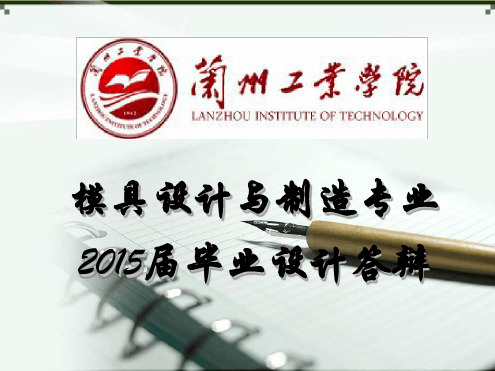
三、模具设计及主要的尺寸计算
1—下模座; 2、15—销钉; 3—凹模; 4—套;5—导柱; 6—导套; 7—上模座; 8—卸料 板9—橡胶; 10—凸模固定板; 11 —垫板; 12—卸料螺钉; 13—凸模; 14—模柄; 16、 17—螺钉
冲裁模典型结构与模具总体设计尺寸关系图
1.模具类型的选择
复合冲压是在压力机滑块的一次 行程中,在同一位置上,使材料顺 序完成几个冲压工序的方法,如落 料—冲孔、落料—拉深、落料—拉 深—冲孔、冲孔—翻边等复合工序, 该类模具称为复合模。生产现场应 用较多的有落料—冲孔复合模、落 料—拉深复合模和落料—拉深—冲 孔复合模等。
1)复合冲裁模的结构形式 复合冲裁模有倒装、顺装两种
结构形式。 倒装式复合模结构简单,使用
方便,应用较为广泛。 2)落料—拉深复合模
落料—拉深—冲孔复合模 3)带浮动模柄的落料—冲孔复合模
4)翻边复合冲模
2.工作部分的结构和尺寸的确定
工件的外形落料凹模采用整体 结构,直刃口形式。这种刃口强度 较好,孔口尺寸不随刃口的刃磨而 增大,适于形状复杂、精度高的工 件向上顶出的要求。
电机定、转子冲片工艺方案的种类
在冲裁工艺分析和技术经济分 析的基础上根据冲裁件的特点确定 冲裁工艺方案。冲裁工艺方案可分 为单工序冲裁、复合冲裁、级进冲 裁。
单工序冲裁是在压力机一次行 程,在模具单一的工位中完成单一 工序的冲压;复合冲裁是在压力机
一次行程中,在模具的同一工作位 置同时完成两个或两个以上的冲压 工序;级进冲裁是把冲裁件的若干 个冲压工序,排列成一定的顺序, 在压力机一次行程中条料在冲模的 不同工序位置上,分别完成工件所 要求的工序,在完成所有要求的工 序后,以后每次冲程都可以得到一 个完善的冲裁件,组合的冲裁工序 比单工序冲裁生产效率高,获得的
定子片、转子片级进模设计

摘要本次设计生产的是电动机定子片和转子片,精度要求较高,形状比较复杂,生产批量大,通过工艺性分析,工序均为落料和冲孔。
采用级进模制造,能很好的解决这些问题,并且能同时完成两个工件的冲裁,提高材料利用率。
原料选用硅钢片卷料,采用自动送料器和自动送料装置送料。
模架采用四导柱滚珠导向钢板模架和弹性卸料板,并在卸料板和固定板之间设置辅助导向机构——小导柱和小导套,保证卸料板有足够的运动精度。
关键字:定子片、转子片、落料、冲孔、级进模、卸料板1.工件名称:微型电动机定子片、转子片2.生产批量:大批大量3.材料:电工硅钢片4.料厚:0.35mm第一章绪论 31.1 冲压加工与模具设计简介 31.2 冷冲压与模具技术现状 41.3 冲压加工自动化与柔性化 41.4 冲模CAD/CAM 4第二章冲裁工艺设计 52.1冲裁件工艺性分析 52.1.1 分析工件的技术要求 52.1.2 零件材料的选用 62.1.3 零件的结构工艺性分析 82.2 冲裁工艺方案的确定 92.2.1.冲裁工序的组合 92.2.2.冲裁顺序的安排 11第三章排样图设计 133.1 材料利用率初算 133.2 排样方法 143.3 搭边值的选用和条料的选用及步距的确定 16 3.3.1 搭边值的选用 163.3.2 条料宽度的确定 163.3.3 步距的确定 173.4 材料利用率确定 183.5 排样图确定 18第四章主要设计计算 204.1 冲压力的计算 204.1.1 计算冲裁力 204.1.2 卸料力及推件力计算 224.2 压力中心的计算 234.3 压力机选择 244.3.1.冲压设备类型的选择 244.3.2 确定压力机设备的规格 25第五章冲裁模工作部分设计计算 265.1.冲裁间隙 265.1.1 间隙的影响 265.1.2.合理间隙的选用 295.2 模具刃口尺寸的计算 305.2.1 计算原则 305.2.2 计算方法 315.2.3 级进模的各个工位凸、凹模刃口尺寸计算 32 第六章模具总体设计 386.1 确定送料方式 386.2 定位方式选择和定位装置 386.3 卸料方式的选择 386.4 模架选择 386.5 卸料板及其配套设施选择 406.6 导料装置 416.7 模具材料的选用处理 41第七章模具主要零、部件设计 437.1 工作零件设计 437.1.1.线槽冲模设计 447.1.2 校正模设计 457.1.3 小凸模设计 457.1.4 转子片落料凸模设计 457.1.5 异形孔冲模设计 467.1.6 切废料模设计 467.1.7 切断模设计 467.2 垫板、凸模固定板设计 477.3 模具闭合高度的确定 47第八章绘制模具装配图、及零件图及编写设计说明书 48 第九章总结 50参考文献 51致谢 52附录 53文献综述 58。
定转子冲片生产工艺的改进与模具设计
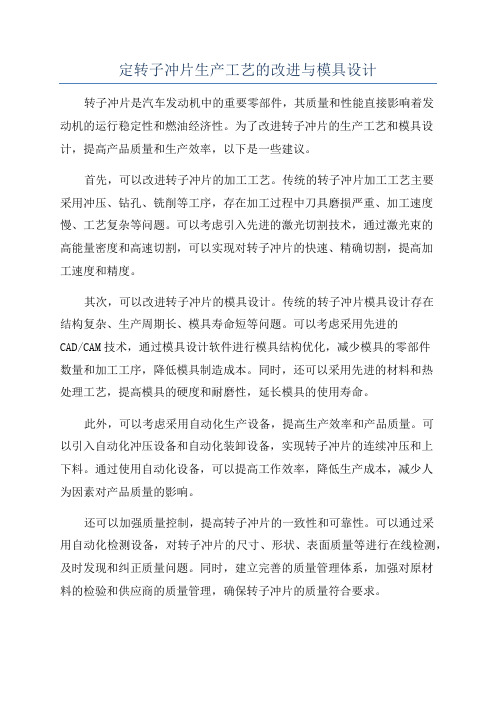
定转子冲片生产工艺的改进与模具设计转子冲片是汽车发动机中的重要零部件,其质量和性能直接影响着发动机的运行稳定性和燃油经济性。
为了改进转子冲片的生产工艺和模具设计,提高产品质量和生产效率,以下是一些建议。
首先,可以改进转子冲片的加工工艺。
传统的转子冲片加工工艺主要采用冲压、钻孔、铣削等工序,存在加工过程中刀具磨损严重、加工速度慢、工艺复杂等问题。
可以考虑引入先进的激光切割技术,通过激光束的高能量密度和高速切割,可以实现对转子冲片的快速、精确切割,提高加工速度和精度。
其次,可以改进转子冲片的模具设计。
传统的转子冲片模具设计存在结构复杂、生产周期长、模具寿命短等问题。
可以考虑采用先进的CAD/CAM技术,通过模具设计软件进行模具结构优化,减少模具的零部件数量和加工工序,降低模具制造成本。
同时,还可以采用先进的材料和热处理工艺,提高模具的硬度和耐磨性,延长模具的使用寿命。
此外,可以考虑采用自动化生产设备,提高生产效率和产品质量。
可以引入自动化冲压设备和自动化装卸设备,实现转子冲片的连续冲压和上下料。
通过使用自动化设备,可以提高工作效率,降低生产成本,减少人为因素对产品质量的影响。
还可以加强质量控制,提高转子冲片的一致性和可靠性。
可以通过采用自动化检测设备,对转子冲片的尺寸、形状、表面质量等进行在线检测,及时发现和纠正质量问题。
同时,建立完善的质量管理体系,加强对原材料的检验和供应商的质量管理,确保转子冲片的质量符合要求。
总结起来,改进转子冲片的生产工艺和模具设计,需要综合考虑加工工艺、模具设计、自动化设备和质量控制等方面的因素。
通过引入先进的加工技术和设备,优化模具设计,加强质量控制,可以提高转子冲片的加工效率、产品质量和生产效益,满足市场需求。
发电机定子与转子冲片模具优化设计

发电机定子与转子冲片模具优化设计摘要:发电机中的定子与转子冲片的质量对于发电机的工作效率有着尤为重要的作用。
研究定子与转子冲片模具优化设计方案能够为各个领域提供强劲的动力。
本文所研究的定子与转子复合模具优化设计方案是将传统的开放式环形改为上半部封闭的结构,并采用整圆刃块形式的凸凹模结构,减少模具所需加工成本,提高质量,延长使用寿命。
关键词:发电机定子与转子冲片优化设计半封闭凸凹模一、发电机定子与转子冲片模具简介随着我国科技水平的不断提高,发电机的核心技术也在不断提升。
在生活中应用最广的是为汽车提供电能的直流无刷发电机。
直流无刷发电机是汽车行车取力系统的一个重要组件,该发电机能够在汽车的行驶过程中借助汽车机动组中的传动装置,将汽车底盘中柴油机为汽车提供的动能,转化为汽车在运行过程中所需要的电能,为汽车中的用电设备提供源源不断的电力,为车主提供舒适的车内环境。
由此可以看出,直流无刷发电机的应用具有重要的意义。
由于定转子冲片模具是整个发电机的专用模具重要的组成部分,能够直接影响发电机的性能,定子冲片冲模和定转子冲片复合模不仅是定转子冲片冲模设计的关键步骤,也是整个发电机模具设计工作的重点。
在定、转子冲片的成型过程中,一般采用的方案是先成型定子冲片的外形结构,然后再进行转子冲片与定子冲片的落料分离方案。
并且在模具的制造过程中需要考虑制作的成本以及成型模具的生产效率与质量等相关因素。
发点集中的定子冲片冲模应当尽可能的采用单槽冲孔成型的方式,延长发电机使用的寿命和提高发电机的发电效率。
发电机对我国的各个领域来说均有着重要的应用,是推进我国生产力进步的重要构件。
因此设计工作人员需要保证发电机成型的质量,进一步优化电机专用模具的设计方案,在传统设计方案的基础上取其精华,去其糟粕,积极引入先进的技术来节约材料的使用以及提升发电机的工作效率。
二、发电机定子与转子冲片模具的具体方案2.1定、转子冲片的成型方案定、转子冲片的成型应当采用以下方案,主要分三个部分进行。
电机铁心定转子片复合冲压工艺及模具设计
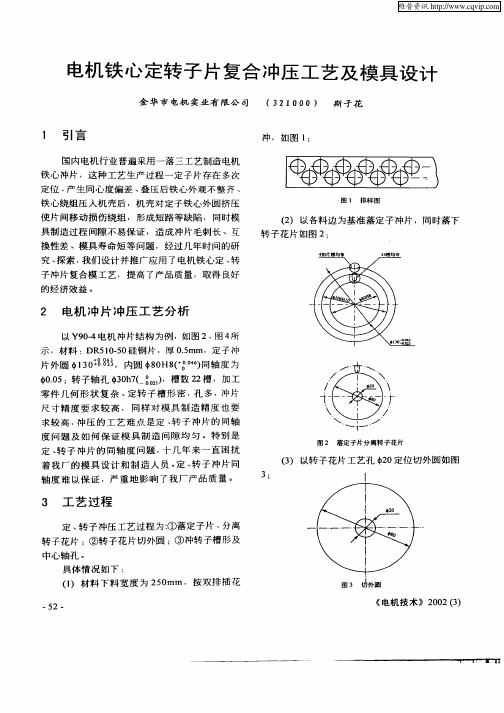
冲 ,如 图 1
铁 心 绕 组 压 入 机 壳 后 ,机 壳 对 定 子 铁 心 外 圆 挤 压 使 片 间 移 动 损 伤 绕 组 ,形 成 短 路 等 缺 陷 ,同 时 模 具 制 造 过 程 间隙 不 易 保 证 ,造 成 冲 片毛 刺 长 、互
出 ) 冲 裁 过 程 定 子 片 由弹 脱 料 装 置 采用 上 出料 方 ,
5 凸 凹模 l J 6 橡 胶 7 脱 料 板 8 定 子 脱 料 板 1 9 脱 料 板 1 凸 凹 摸 I 0 2J 1 下模 座 1
式 ,而 转 子 花 片 则 采 用 刚 性 打 料 在 冲床 上 行 时 通 过料杆 1 、打 料 板 2、脱 料 板 7打 落 ,并 由安 装在
中心轴孔 。 具体情况 如下 : () 材 料 下 料 宽 度 为 2 0 1 5 mm ,按 双 排 插 花
.
图 3
外 圆
52 .
《 电机 技 术 》2 0 3 0 2()
维普资讯
() 以转 子 片 工 艺 孔 定 位 冲 槽 形 及 中心 轴 孔 4
。
巾 . ;转子轴孔  ̄0 7一 ∞) 05 0 3h( : . ,槽数 2 槽 ,加工 2
零 件 几何 形状 复 杂 、 定转 子槽 形 密 , 多 , 片 孔 冲
尺 寸 精 度 要 求 较 高 , 同 样 对 模 具 制 造 精 度 也 要 求 较 高 , 压 的 工 艺 难 点 是 定 、 子 冲 片 的 同 轴 冲 转 度 问 题 及 如 何 保 证 模 具 制 造 间 隙 均 匀 。特 别 是 定 、 子 冲 片 的 同 轴 度 问 题 , 几 年 来 一 直 困 扰 转 十 着 我 厂 的 模 具 设 计 和 制 造 人 员 。 、 子 冲 片 同 定 转 轴 度 难 以 保 证 ,严 重 地 影 响 了 我 厂 产 品 质 量 。
4.设计实例:定子冲片冲压工艺及模具设计
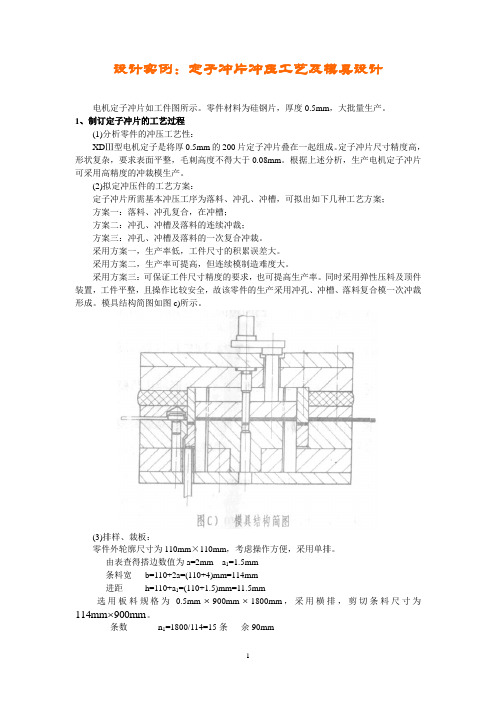
设计实例:定子冲片冲压工艺及模具设计电机定子冲片如工件图所示。
零件材料为硅钢片,厚度0.5mm,大批量生产。
1、制订定子冲片的工艺过程(1)分析零件的冲压工艺性:XDⅢ型电机定子是将厚0.5mm的200片定子冲片叠在一起组成。
定子冲片尺寸精度高,形状复杂,要求表面平整,毛刺高度不得大于0.08mm。
根据上述分析,生产电机定子冲片可采用高精度的冲裁模生产。
(2)拟定冲压件的工艺方案:定子冲片所需基本冲压工序为落料、冲孔、冲槽,可拟出如下几种工艺方案;方案一:落料、冲孔复合,在冲槽;方案二:冲孔、冲槽及落料的连续冲裁;方案三:冲孔、冲槽及落料的一次复合冲裁。
采用方案一,生产率低,工件尺寸的积累误差大。
采用方案二,生产率可提高,但连续模制造难度大。
采用方案三:可保证工件尺寸精度的要求,也可提高生产率。
同时采用弹性压料及顶件装置,工件平整,且操作比较安全,故该零件的生产采用冲孔、冲槽、落料复合模一次冲裁形成。
模具结构简图如图c)所示。
(3)排样、裁板:零件外轮廓尺寸为110mm×110mm,考虑操作方便,采用单排。
由表查得搭边数值为a=2mm a1=1.5mm条料宽b=110+2a=(110+4)mm=114mm进距h=110+a1=(110+1.5)mm=11.5mm选用板料规格为0.5mm⨯900mm⨯1800mm,采用横排,剪切条料尺寸为900m m114m m⨯。
条数n1=1800/114=15条余90mm每条个数 n 2=(900-1.5)/111.5=8个 余6.5mm每板个数 n 3=n 1×n 2=15×8=120个冲片面积 S= ∏(58.52-352)-12×7×24=6903mm 2材料利用率 51% 100%)1800900/6903120(=⨯⨯⨯=η(4)计算工序压力,选择压力机:已知:工件材料:硅钢片材料厚度:0.5mm模具结构简图如图c)所示。
一种电机定转子的冲片冲压加工工艺 -回复

一种电机定转子的冲片冲压加工工艺-回复电机定子的冲片冲压加工工艺,是电机制造中非常关键的一个环节。
冲片冲压加工是通过模具将薄板材料冲剪成所需形状,然后再通过装配等工艺流程将其固定在电机定子上。
本文将分步介绍电机定子冲片冲压加工工艺的具体步骤和相关要点。
第一步:材料准备冲片的材料一般是电工硅钢片,因其具有优异的磁导性能和低铁损耗,适用于电机的磁路部件制造。
在冲片冲压加工之前,需要确保所选材料符合相关的技术要求,包括材料的化学成分、表面状态、硬度等。
此外,材料还需进行定尺寸的切割,以适应不同型号的电机定子需要。
第二步:模具设计与制造冲片冲压加工依赖于模具来实现,因此模具的设计和制造至关重要。
首先,根据电机定子的尺寸要求,设计出合适的模具结构,并制定出相应的加工工艺。
模具的制造需要考虑到材料的可加工性和长时间使用的耐用性,通常采用优质的合金钢材料,并通过精密加工技术制造出具有高度精度和稳定性能的模具。
第三步:定模与调试将制好的模具安装在冲床上,并进行相关的调试工作。
此过程中,需要保证模具的平稳运行、工作间隙的控制以及冲床的工作稳定性,以确保冲压过程的顺利进行。
调试过程中还需检查冲片尺寸的准确性和加工质量,若有偏差或问题,需要及时调整和修正。
第四步:冲片冲压加工材料经过切割和准备后,将放置在冲床上,准备进行冲片冲压加工。
冲片冲压的过程是通过上下冲头的移动和施加压力,将材料冲剪成所需的形状。
在此过程中,需要控制好冲床参数,如冲击力、速度、行程等,以及冲床和模具的配合精度,以保证冲压加工的质量和稳定性。
第五步:清洁和表面处理冲片冲压加工完成后,需要对冲出的片料进行清洁和表面处理。
清洁工作主要是去除冲床加工中产生的油污、金属屑等杂质,保持冲片的干净与光滑。
表面处理可以采用镀锌、喷涂等方法,以增强冲片的耐腐蚀能力和美观度。
第六步:冲片装配经过冲片冲压加工得到的冲片,需要进行装配工作。
装配过程是将冲片固定在电机定子上,通常采用铆接、焊接等方法进行。
电机转子冲片冲压工艺分析与级进模设计

电机转子冲片冲压工艺分析与级进模设计摘要:本文针对电机转子冲片的冲压工艺分析与级进模设计进行研究。
首先对电机转子冲片的冲片工艺进行概述,包括材料选择和工艺流程。
然后介绍了质量控制与检测方法,包括冲片尺寸测量、表面质量检验和冲片硬度测试。
接着探讨了级进模的设计,包括模具结构设计、材料选择和热处理,以及模具加工工艺和装配调试。
最后,总结了工艺分析与级进模设计的重要性和影响。
关键词:电机转子;冲片;冲压工艺引言:电机转子冲片的冲压工艺分析与级进模设计在电机制造领域中具有重要的应用价值。
冲片工艺的合理分析和设计能够有效提高冲片的制造质量和生产效率。
而级进模作为冲压工艺中的关键设备,对于保证冲片的尺寸精度和表面质量具有至关重要的作用。
因此,深入研究电机转子冲片的冲压工艺分析与级进模设计,对于提升电机转子冲压制造的技术水平具有重要意义[1]。
一、电机转子冲片冲压工艺分析与级进模设计的重要性通过深入分析和优化冲片工艺,可以有效控制冲片的尺寸精度、几何形状和表面质量,从而提高冲片的制造质量。
合理的冲片工艺能够减少材料的变形、裂纹和缺陷,确保冲片的稳定性和可靠性。
冲片工艺的优化和设计能够减少制造过程中的工序和周期,提高生产效率。
通过合理的冲片布局和工艺流程,可以实现高速冲裁和连续生产,降低生产成本并提高产能。
冲片工艺分析与级进模设计能够确保不同批次或不同型号的电机转子冲片具有一致的质量和性能。
通过设计合适的级进模和优化的工艺参数,可以实现冲片的精准制造,确保产品的一致性和互换性。
通过对冲片工艺进行分析和优化,可以减少材料的浪费和能源消耗,降低生产成本。
合理设计的级进模能够减少材料的切削量和损耗,提高材料利用率,从而节约生产成本[2]。
二、电机转子冲片冲压工艺分析(一)冲片工艺概述设计模具:冲片工艺的第一步是设计和制造适用于冲片加工的模具。
模具的设计需要考虑冲片的几何形状、尺寸和数量,并确保模具的强度和稳定性。
材料选择:合适的材料选择对于冲片的制造非常重要。
一种电机定转子的冲片冲压加工工艺

一种电机定转子的冲片冲压加工工艺1. 概述- 介绍电机定转子的冲片冲压加工工艺是电机制造过程中的重要环节之一,其质量和效率直接影响到电机的性能和生产成本。
- 本文将从工艺流程、设备要求、工艺参数等方面对电机定转子的冲片冲压加工工艺进行详细阐述。
2. 工艺流程- 首先,对冲片原材料进行切割,获得符合尺寸要求的冲片毛坯。
- 然后,将冲片毛坯放置在冲床上,通过冲压模具进行冲压成型,得到定转子的冲片。
- 最后,对冲压成型后的冲片进行清洗、除毛刺和表面处理,使其达到工艺要求。
3. 设备要求- 冲床:需要具备较大的冲床工作台面积和冲床冲击力,以适应定转子冲片的大尺寸和复杂形状。
- 冲模:冲模的设计和制造需要考虑到冲片的形状和尺寸要求,保证冲压成型的精度和稳定性。
- 其他辅助设备:清洗设备、除毛刺设备和表面处理设备等,用于对冲片进行后续加工处理。
4. 工艺参数- 冲压速度:冲片的材料和厚度不同,冲压速度也会有所变化,需要根据具体情况进行调整。
- 冲模温度:冲模的温度对冲压成型的质量有着重要影响,需要控制在适当的范围内。
- 冲床压力:冲床的冲击力需要根据冲片的材料和形状进行调整,以保证冲压成型的质量和效率。
5. 质量控制- 对冲片的尺寸、形状和表面质量进行严格的检测和控制,确保冲片符合设计要求。
- 对冲压过程中的各项工艺参数进行监控和调整,及时发现和解决问题,保证冲片的一致性和稳定性。
6. 总结- 电机定转子的冲片冲压加工工艺是一个复杂的制造过程,需要综合考虑材料、设备、工艺参数和质量控制等方面的因素。
- 合理优化工艺流程、精心选择和设计设备、严格控制工艺参数和加强质量控制是保证冲片加工质量和效率的关键。
定子与转子片的冲压模具设计与制造

定子与转子片的冲压模具设计与制造定子与转子片的冲压模具是一种广泛应用于电机、发电机、风力机、电动工具等领域的模具。
冲压模具的设计和制造对产品的质量和成本有着至关重要的影响。
在本文中,将详细介绍定子和转子片的冲压模具的设计流程、制造工艺和注意事项。
一、冲压模具设计冲压模具的设计是整个制造过程中最关键的部分,它直接影响到后续的模具制造和产品加工质量。
在定子和转子片的冲压模具设计中,主要包括以下几个步骤:1.产品分析产品分析是冲压模具设计的第一步。
要根据定子或转子片的形状、尺寸和工艺要求绘制三维图形。
一般来说,定子和转子片的轮廓都是曲线型,需要借助CAD等设计软件进行绘制。
同时还需要确定工艺要求,包括模具的结构形式、材料选用、凸台数量和位置、裁冲顺序等。
2.冲压模具结构设计在产品分析的基础上,需要设计冲压模具的结构。
冲压模具包括模板、凸台、挡料、弹簧、导柱等组成部分。
其中,凸台是冲压过程中起关键作用的部分。
凸台数量和位置、材料和硬度以及凸台高度都需要根据产品的特点来进行合理的设计。
3.模具结构成型设计模具的结构成型设计是模具制造的重点。
主要包括模具组合方式、各零部件之间连接方式、螺栓的数量、位置和规格等。
这一步需要考虑到模具的可靠性、稳定性和快捷性,同时要考虑材料的节约和使用寿命。
4.模具细节设计模具细节设计主要包括凸模、凹模、挡料、导柱、弹簧等零部件的设计。
在这一步中,需要考虑以下几个方面:(1)凸模和凹模的配合度,包括毛坯的设计、修边和刀模的选用等。
(2)挡料的精度和调节方式,挡料是保证冲裁品质的重要部分。
(3)导柱的固定和调节方式,导柱主要起定位和锁定作用。
(4)弹簧的选用和布置方式,弹簧的作用是将模具保持稳定,并减小冲击力。
在弹簧的选择和布置过程中,需要考虑到模具重量、冲压力和工作环境等因素。
二、冲压模具制造完成冲压模具设计之后,就需要进行制造。
在制造过程中,需要根据设计要求进行材料选取、图纸制作和加工等工作。
一种电机定转子的冲片冲压加工工艺

一种电机定转子的冲片冲压加工工艺随着现代工业的发展,电机在各个领域得到了广泛的应用。
而电机的核心部件之一就是转子,而转子的制造过程中,冲片冲压加工工艺被广泛采用。
本文将介绍电机定转子的冲片冲压加工工艺的相关内容。
一、冲片冲压加工工艺概述冲片冲压加工是利用冲压设备,通过模具对金属材料进行冲击,使其在受力作用下发生塑性变形,以获得所需形状的制造工艺。
在电机转子的制造中,冲片冲压加工工艺被广泛应用于定子和转子的制造过程中。
二、冲片冲压加工的步骤1. 材料准备:首先需要准备好符合要求的金属材料,通常使用的材料有硅钢片、铝合金等。
2. 模具设计和制造:根据转子的形状和尺寸要求,设计并制造出相应的冲压模具。
3. 材料切割:将准备好的金属材料进行切割,得到与模具形状相对应的片状材料。
4. 材料上料:将切割好的金属材料放入冲压机的送料装置中,进行上料操作。
5. 冲压加工:通过冲压机将材料放入冲压模具中,施加适当的压力,使材料发生塑性变形,并得到所需形状的转子。
6. 去毛刺和清洗:冲压加工后的转子表面可能会残留毛刺,需要进行去毛刺处理,并进行清洗,以保证转子的质量。
7. 检验和质量控制:对冲压加工后的转子进行检验,检查其形状、尺寸等是否符合要求,确保转子的质量。
三、冲片冲压加工的优势1. 生产效率高:冲片冲压加工工艺可以实现对大批量转子的快速制造,生产效率高。
2. 节约材料:冲片冲压加工可以使金属材料发生塑性变形,有效利用材料,减少浪费。
3. 产品质量稳定:冲压模具的使用可以保证转子的形状和尺寸精度,从而保证产品质量的稳定性。
四、冲片冲压加工的应用范围冲片冲压加工工艺在电机制造中的应用范围广泛,不仅可以用于制造定子和转子,还可以用于制造电机的其他部件,如电机壳体、风扇叶片等。
五、冲片冲压加工的发展趋势随着科技的进步,冲片冲压加工工艺也在不断发展。
未来,冲片冲压加工工艺将更加注重绿色环保、高效节能,同时也将注重提高产品的精度和质量稳定性。
小型电机定、转子冲压工艺及模具设计
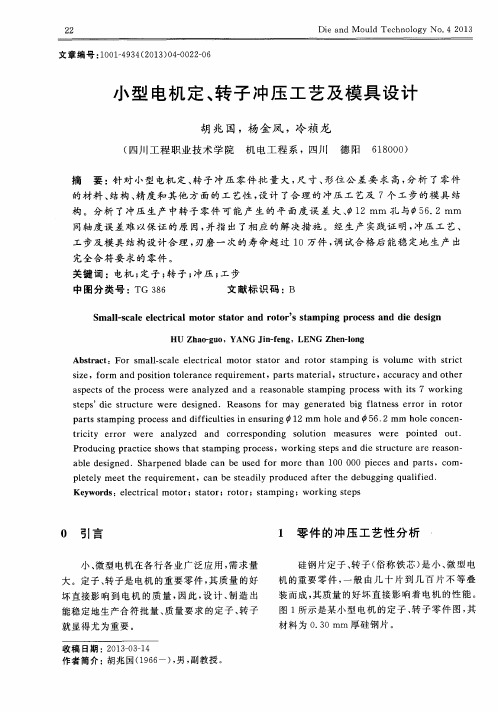
0
引言
小、 微型电机在各 行各业广泛 应用 , 需求 量
1 零 件 的 冲压 工 艺性 分 析
硅 钢 片定 子 、 转子 ( 俗称铁 芯) 是小 、 微 型 电 机 的 重要 零 件 , 一 般 由几 十 片 到 几 百 片 不 等 叠 装而成 , 其 质 量 的好 坏 直 接 影 响 着 电机 的 性 能 。 图 1所 示 是某 小 型 电 机 的 定 子 、 转子零 件 图 , 其
胡 兆 国 ,杨 金 凤 ,冷 祯 龙
( 四川 工程 职业 技 术 学 院 机 电工 程 系 ,四J I I 德 阳 6 1 8 0 0 0 ) 摘 要 : 针 对 小型 电机 定 、 转子 冲压零件 批 量大 , 尺寸、 形 位 公 差要 求 高 , 分 析 了零 件 的材 料 、 结构 、 精 度 和 其 他 方 面 的 工 艺性 , 设 计 了合 理 的 冲 压 工 艺及 7个 工 步 的模 具 结 构 。分 析 了冲 压 生 产 中转 子 零 件 可 能 产 生 的 平 面 度 误 差 大 、 妒1 2 mm 孔 与驴5 6 . 2 mm 同轴度 误 差 难 以保 证 的 原 因 , 并 指 出 了相 应 的 解 决措 施 。经 生 产 实践 证 明 , 冲压 工 艺 、
a bl e d e s i g ne d.Sha r pe ne d bl a de c an b e us ed f o r m or e t han 1 0 0 00 0 pi e c e s and pa r t s,c om 。 pl et e l y me e t t he r e qui r eme nt,c an be s t e adi l y pr oduc e d a f t e r t he d eb ug gi ng qu a l i f i ed. Ke y wor d s:el e c t r i c al m ot or;s t a t or ;r ot or;s t a m pi ng;wo r ki ng s t e ps
电机定转子片冲压工艺及模具设计

电机定转子片冲压工艺及模具设计电机定子和转子片的冲压工艺及模具设计是电机制造过程中非常重要的环节。
下面将对这两个环节进行分别介绍。
电机定子是电机的重要部件之一,它负责传递电能到转子,并通过相互作用转化为动力。
电机定子的冲压工艺设计主要包括:冲压工艺流程设计、工件材料选择、模具设计等。
1.冲压工艺流程设计:冲压工艺流程设计是指根据电机定子的结构和要求,确定冲压过程中的各个步骤和工序。
其中包括切割、冲孔、冲凹、成形等工序。
在设计过程中,要考虑到定子的材料的特性和加工工艺的可行性,使得冲压效果更加稳定和高效。
2.工件材料选择:电机定子的材料一般选择导电性好、磁性强、机械强度高的硅钢板。
在确定材料时,要综合考虑材料的特性和成本因素,确保产品的性能和经济性。
3.模具设计:模具是冲压过程中的重要设备,它的设计直接影响到冲压的准确度和效果。
在模具设计过程中,要考虑到定子的结构和尺寸,确定冲孔、冲凹的位置和尺寸。
同时,还要考虑到材料的屈服强度和导热性能,确定模具的材料和结构,以确保模具在冲压过程中的稳定性和耐用性。
电机转子片是电机的核心部件之一,它通过旋转产生动力。
电机转子片的冲压工艺设计主要包括:冲压工艺流程设计、工件材料选择、模具设计等。
1.冲压工艺流程设计:冲压工艺流程设计是指根据转子片的结构和要求,确定冲压过程中的各个步骤和工序。
其中包括切割、冲孔、冲凸、成形等工序。
在设计过程中,要考虑到转子片的材料特性和形状复杂性,同时还要考虑到冲压过程中的变形和残余应力等因素,确保冲压效果和转子片的性能。
2.工件材料选择:电机转子片的材料一般选择具有稳定性和导电性的钢材。
在确定材料时,要综合考虑材料的特性和成本因素,确保产品的性能和经济性。
3.模具设计:模具是冲压过程中的核心设备,它的设计直接影响到冲压的准确度和效果。
在模具设计过程中,要考虑到转子片的结构和尺寸,确定冲孔、冲凸的位置和尺寸。
同时,还要考虑到材料的屈服强度和导热性能,确定模具的材料和结构,以确保模具在冲压过程中的稳定性和耐用性。
电机定、转子片冲压工艺及模具设计讲解共70页

56、死去何所道,托体同山阿。 57、春秋多佳日,登高赋新诗。 58、种豆南山下,草盛豆苗稀。晨兴 理荒秽 ,带月 荷锄归 。道狭 草木长 ,夕露 沾我衣 。衣沾 不足惜 ,但使 愿无违 。 59、相见无杂言,但道桑麻长。 60、迢迢新秋夕,亭亭月将圆。
61、奢侈是舒适的,否则就不是奢侈 。——CocoCha nel 62、少而好学,如日出之阳;壮而好学 ,如日 中之光 ;志而 好学, 如炳烛 之光。 ——刘 向 63、三军可夺帅也,匹夫不可夺志也。 ——孔 丘 64、人生就是学校。在那里,与其说好 的教师 是幸福 ,不如 说好的 教师是 不幸。 ——海 贝尔 65、接受挑战,就可以享受胜利的喜悦 。——杰纳勒 尔·乔治·S·巴顿
Байду номын сангаас
谢谢!
电机定子转子片套冲级进冲压模设计设计
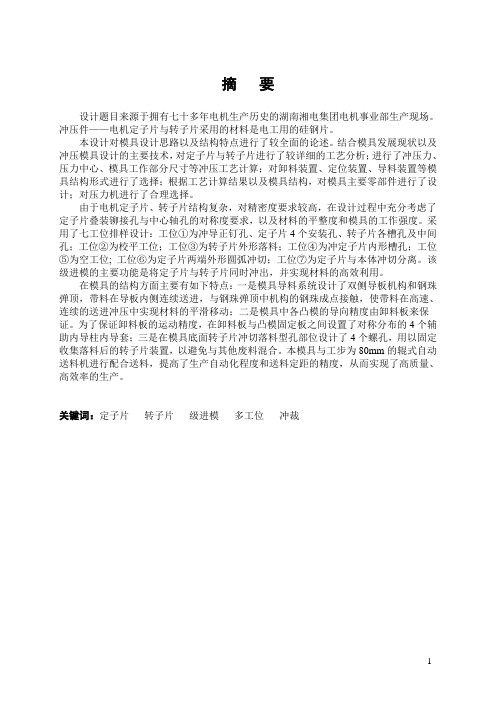
摘要设计题目来源于拥有七十多年电机生产历史的湖南湘电集团电机事业部生产现场。
冲压件——电机定子片与转子片采用的材料是电工用的硅钢片。
本设计对模具设计思路以及结构特点进行了较全面的论述。
结合模具发展现状以及冲压模具设计的主要技术,对定子片与转子片进行了较详细的工艺分析;进行了冲压力、压力中心、模具工作部分尺寸等冲压工艺计算;对卸料装置、定位装置、导料装置等模具结构形式进行了选择;根据工艺计算结果以及模具结构,对模具主要零部件进行了设计;对压力机进行了合理选择。
由于电机定子片、转子片结构复杂,对精密度要求较高,在设计过程中充分考虑了定子片叠装铆接孔与中心轴孔的对称度要求,以及材料的平整度和模具的工作强度。
采用了七工位排样设计:工位①为冲导正钉孔、定子片4个安装孔、转子片各槽孔及中间孔;工位②为校平工位;工位③为转子片外形落料;工位④为冲定子片内形槽孔;工位⑤为空工位; 工位⑥为定子片两端外形圆弧冲切;工位⑦为定子片与本体冲切分离。
该级进模的主要功能是将定子片与转子片同时冲出,并实现材料的高效利用。
在模具的结构方面主要有如下特点:一是模具导料系统设计了双侧导板机构和钢珠弹顶,带料在导板内侧连续送进,与钢珠弹顶中机构的钢珠成点接触,使带料在高速、连续的送进冲压中实现材料的平滑移动;二是模具中各凸模的导向精度由卸料板来保证。
为了保证卸料板的运动精度,在卸料板与凸模固定板之间设置了对称分布的4个辅助内导柱内导套;三是在模具底面转子片冲切落料型孔部位设计了4个螺孔,用以固定收集落料后的转子片装置,以避免与其他废料混合。
本模具与工步为80mm的辊式自动送料机进行配合送料,提高了生产自动化程度和送料定距的精度,从而实现了高质量、高效率的生产。
关键词:定子片转子片级进模多工位冲裁ABSTRACTThe design topic mainly originates from the production frontline in Generator Manufacturing Group of Xiangtan Electric Company, which has 70 years in the line of generator manufacturing. The material the stator and rotor plate use is electrical silicon steel sheet.The full text is to express the design idea and structural characteristics in detail;Here are the main context: Though Combining the current development situation of stamping die ,with the main technical of stamping die design; we focus on the motor stator and rotor plate to do the process analysis; doing the stamping process calculation, including the punching pressure, pressure center and so on; analyzing the reason of selecting the unloading device, positioning device, a material guide device of die structure and so on; describing the process of choose the right and reasonable press machine.Because of the stator and rotor plate are high complex and precise parts in the motor, so after careful and full consideration of the requirements of the place relationship between the stator lamination riveting hole and the hole of center axis, material flatness and die work intensity, we draw a seven station layout: Station 1—piercing pilot hole, 4 stator mounting holes, and the middle hole; Station 2—shool ping station; Station 3—rotor shape blanking station; Station 4—punching a stator inner slotted hole;Station 5—the air station ;Station 6—the outside shape arc of the stator cutting;Station 7—separation of stator plate and body. The main function of the progressive model is getting the motor stator and rotor plate out at one time,reaching the goal of the utter use of material.The main characters of the progressive mold structure:1.In the material guide system , bilateral plate mechanism and steel ball are included , with material in the plate medial continuous feeding, and the steel balls body point contacting with material, so that the strip can continuous to achieve smooth movement at high speed in the high punching stamping mold.2.The accuracy of each punching die in the mold can ensured by the stripper plate.In order to ensure the stripper plate motion accuracy , 4 auxiliary guide pillar and guide sleeve are distributed between the stripper plate and punching die fixing board .3.There are 4 screw holes in the bottom surface of the mold rotor punching blanking hole site , and the screw holes are used for fixing the collection after the blanking rotor device, in order to avoid mixing with other waste.The motor should be equipped with roller type automatic feeding machine in order to increase the automation level and feeding distance accuracy, realizing high quality, high efficient production.Keywords: stator plate rotor plate progressive punching die multi-station punching毕业设计(论文)原创性声明和使用授权说明原创性声明本人郑重承诺:所呈交的毕业设计(论文),是我个人在指导教师的指导下进行的研究工作及取得的成果。