水泥厂三大工艺流程简介
简述水泥工艺流程图(精)

水泥粉磨是水泥制造的最后工序,也是耗电最多的工序。其主要功能在于 将水泥熟料(及胶凝剂、性能调节材料等)粉磨至适宜的粒度(以细度、比表 面积等表示),形成一定的颗粒集配,增大其水化面积,加速水化速度,满足 水泥浆体凝结、硬化要求。
7、水泥包装 水泥出厂有袋装和散装两种发运方式。
5、水泥孰料的烧成
生料在旋风预热器中完成预热和预分解后,下一道工序是进入回转窑中进 行熟料的烧成。 在 回转窑中碳酸盐进一步的迅速分解并发生一系列的固相反应,生成水泥熟料 中的等矿物。随着物料温度升高近时,等矿物会变成液相,溶解于液相中的 和 进行反应生成大量 (熟料)。熟料烧成后,温度开始降低。最后由水泥熟料冷 却机将回转窑卸出的高温熟料冷却到下游输送、储存库和水泥磨所能承受的温 度,同时回收高温熟料的显 热,提高系统的热效率和熟料质量。
1、破碎及预均化
(1)破碎水泥生产过程中,大部分原料要进行破碎,如石灰石、黏土、铁矿石 及煤等。石灰石是生产水泥用量最大的原料,开采后的粒度较大,硬度较高,因此石 灰石的破碎在水泥厂的物料破碎中占有比较重要的地位。
(2) 原料预均化 预均化技术就是在原料的存、取过程中,运用科学的堆取料 技术,实现原料的初步均化,使原料堆场同时具备贮存与均化的功能。
3、生料均化
新型干法水泥生产过程中,稳定入窖生料成分是稳定熟料烧成热工制度的前提, 生料均化系统起着源自定入窖生料成分的最后一道把关作用。
4、预热分解
把生料的预热和部分分解由预热器来完成,代替回转窑部分功能,达到缩短回窑 长度,同时使窑内以堆积状态进行气料换热过程,移到预热器内在悬浮状态下进行, 使 生料能够同窑内排出的炽热气体充分混合,增大了气料接触面积,传热速度快,热 交换效率高,达到提高窑系统生产效率、降低熟料烧成热耗的目的。
水泥生产工艺流程
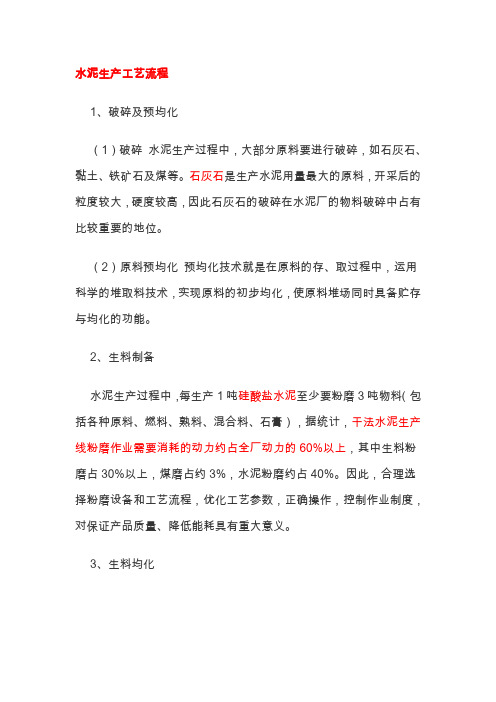
水泥生产工艺流程1、破碎及预均化(1)破碎水泥生产过程中,大部分原料要进行破碎,如石灰石、黏土、铁矿石及煤等。
石灰石是生产水泥用量最大的原料,开采后的粒度较大,硬度较高,因此石灰石的破碎在水泥厂的物料破碎中占有比较重要的地位。
(2)原料预均化预均化技术就是在原料的存、取过程中,运用科学的堆取料技术,实现原料的初步均化,使原料堆场同时具备贮存与均化的功能。
2、生料制备水泥生产过程中,每生产1吨硅酸盐水泥至少要粉磨3吨物料(包括各种原料、燃料、熟料、混合料、石膏),据统计,干法水泥生产线粉磨作业需要消耗的动力约占全厂动力的60%以上,其中生料粉磨占30%以上,煤磨占约3%,水泥粉磨约占40%。
因此,合理选择粉磨设备和工艺流程,优化工艺参数,正确操作,控制作业制度,对保证产品质量、降低能耗具有重大意义。
3、生料均化新型干法水泥生产过程中,稳定入窖生料成分是稳定熟料烧成热工制度的前提,生料均化系统起着稳定入窖生料成分的最后一道把关作用。
4、预热分解把生料的预热和部分分解由预热器来完成,代替回转窑部分功能,达到缩短回窑长度,同时使窑内以堆积状态进行气料换热过程,移到预热器内在悬浮状态下进行,使生料能够同窑内排出的炽热气体充分混合,增大了气料接触面积,传热速度快,热交换效率高,达到提高窑系统生产效率、降低熟料烧成热耗的目的。
(1)物料分散换热80%在入口管道内进行的。
喂入预热器管道中的生料,在与高速上升气流的冲击下,物料折转向上随气流运动,同时被分散。
(2)气固分离当气流携带料粉进入旋风筒后,被迫在旋风筒筒体与内筒(排气管)之间的环状空间内做旋转流动,并且一边旋转一边向下运动,由筒体到锥体,一直可以延伸到锥体的端部,然后转而向上旋转上升,由排气管排出。
(3)预分解预分解技术的出现是水泥煅烧工艺的一次技术飞跃。
它是在预热器和回转窑之间增设分解炉和利用窑尾上升烟道,设燃料喷入装置,使燃料燃烧的放热过程与生料的碳酸盐分解的吸热过程,在分解炉内以悬浮态或流化态下迅速进行,使入窑生料的分解率提高到90%以上。
水泥生产工艺流程
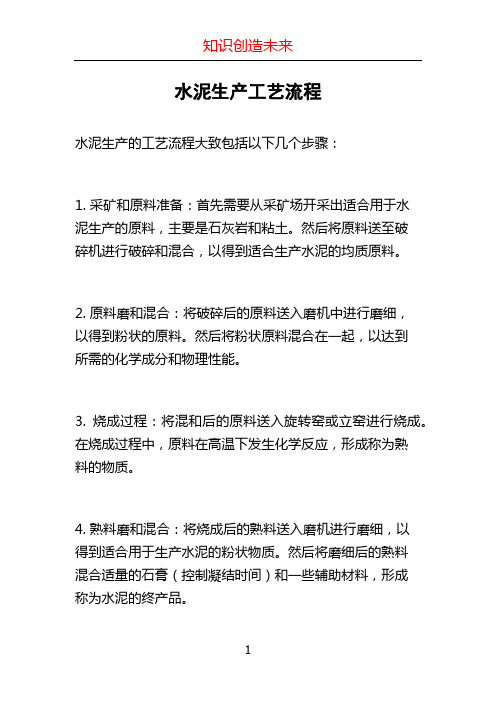
水泥生产工艺流程
水泥生产的工艺流程大致包括以下几个步骤:
1. 采矿和原料准备:首先需要从采矿场开采出适合用于水
泥生产的原料,主要是石灰岩和粘土。
然后将原料送至破
碎机进行破碎和混合,以得到适合生产水泥的均质原料。
2. 原料磨和混合:将破碎后的原料送入磨机中进行磨细,
以得到粉状的原料。
然后将粉状原料混合在一起,以达到
所需的化学成分和物理性能。
3. 烧成过程:将混和后的原料送入旋转窑或立窑进行烧成。
在烧成过程中,原料在高温下发生化学反应,形成称为熟
料的物质。
4. 熟料磨和混合:将烧成后的熟料送入磨机进行磨细,以
得到适合用于生产水泥的粉状物质。
然后将磨细后的熟料
混合适量的石膏(控制凝结时间)和一些辅助材料,形成
称为水泥的终产品。
5. 煅烧和制备:将水泥熟料送入煅烧窑中进行煅烧,将水泥熟料在高温下煅烧,使其结晶、熔融、冷却和固化,形成硅酸盐水泥。
6. 筛分和包装:将煅烧后的水泥进行筛分,去除不合格的颗粒。
然后将合格的水泥通过自动包装机进行包装,最常见的是将水泥装入袋中。
上述是水泥生产的主要工艺流程,不同的水泥生产厂家可能会有一些细微的差异。
同时,为了提高生产效率和降低能耗,还可以采用一些先进的技术和设备,如干法生产工艺、回转窑技术等。
水泥厂生产流程及设备原理
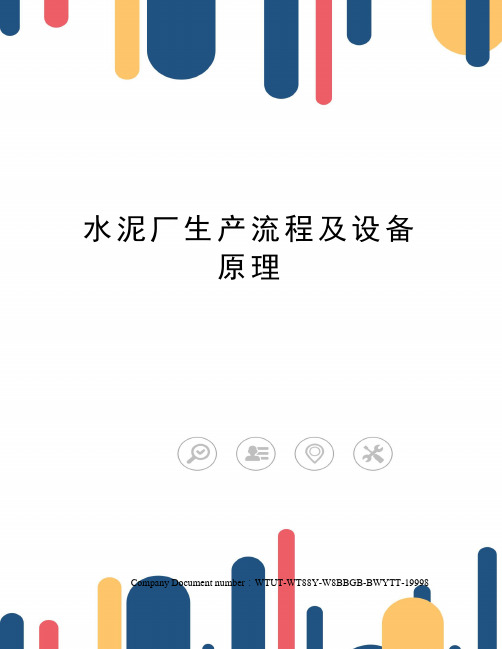
水泥厂生产流程及设备原理Company Document number:WTUT-WT88Y-W8BBGB-BWYTT-19998水泥厂生产流程及设备原理简介1、水泥厂生产流程水泥生产工艺水泥的生产工艺简单讲便是两磨一烧,即原料要经过采掘、破碎、磨细和混匀制成生料,生料经1450℃的高温烧成熟料,熟料再经破碎,与石膏或其他混合材一起磨细成为水泥。
由于生料制备有干湿之别,所以将生产方法分为湿法、半干法或半湿法、干法3种。
全场平面布置图水泥厂的工艺流程简图图立磨原理图图图全厂主机设备与存储设备表全厂主机设备与存储设备列表生料磨、回转窑、水泥磨、煤磨、冷却机、储存设备(堆料场,配料站,均化库,熟料库,水泥库)(1)PC-2018反击锤式破碎机(2)板式喂料机(3)MLS3626立式辊磨机(4)LS型螺旋输送机(5)链斗输送机(6)O-Sepa选粉机(7)罗茨鼓风机(8)水泥窑尾引风机(9)调速型液力偶合器(10)陕西压强设备厂调速机(11)离心通风机2、生料制备矿山开采的工艺流程矿山开采的工艺流程:采矿工作面的整平→布置爆孔→钻孔→装药爆破→集矿→装车原料的破碎,预均化和生料粉磨从矿山开采的矿石用卡车运到水泥厂,由板式喂料机送入单段锤式破碎机,再用皮带送到预均化堆场,采用横堆竖取的方式取料,料经皮带送到石灰石仓.再加上从铁粉仓和粘土仓及粉煤灰仓经电子皮带称定量取料混合后送入生料磨(立磨).经立磨粉磨后粗细料被选粉机分离,粗料返回立磨继续粉磨,细料送入两个锥型仓暂时储存.生料储存,均化和输送由立磨出来的细粉经气力输送管道和皮带提升机送到均化库顶部,经四嘴下料机进入均化库.均化库既有均化的作用也有储存生料的作用.水泥厂生料工段工艺流程图石灰石→板式喂料机→单段锤式破碎机→皮带→堆料机→取料机→皮带→配料站→立磨→o-sepa选粉机→气力输送管道和皮带提升机→生料均化库生料工段主要设备,设备工作原理(1) 板式喂料机板式喂料机能承受较大的料压和冲击,适应大块矿石的喂料,该机给料均衡运转可靠,但设备较重,价格高.板式喂料机分轻型,中型和重型三种.立窑水泥厂石灰石破碎的喂料机一般选用中型的占多.(2)反击锤式破碎机工作原理:物料进入锤破中受到高速回转的锤头冲击而被破碎,物料从锤头处获得动能以高速冲向打击板而被第二次破碎,粒径合格的物料通过蓖条排出,较大粒径在蓖条上再经锤头附加冲击,研磨而被破碎,直至合格后通过蓖条排出.(3) 袋收尘——脉冲袋收尘器是一种新型高效袋式收沉器,利用脉冲阀使压缩空气定时地对滤袋进行喷吹清灰,滤袋寿命长,收尘效率高.工作原理:含尘气体由进风口进入箱体,气体由滤袋外进入滤袋内,经文氏管进入上箱体,从出风口排出,粉尘能截留在滤袋外表面.为了保持收尘器的阻力在一定的范围内(一般为1176~1470Pa)必须定期清灰.清灰时由脉冲控制仪按程序开启控制阀使气沧内的压缩空气由喷嘴管的孔眼高速喷出,每个孔眼对准一个滤袋中心,通过文氏管的诱导在高速气体周围引入相当于喷嘴空气5—7倍的二次空气冲进滤袋,使滤袋急剧膨胀,引起冲击震动.同时产生由袋内向袋外的逆向气流,是黏附在滤袋外表面的积灰被吹落.此时滤布空隙中的粉尘也被吹落,吹扫下来的积灰落入灰斗经排灰系统排出.(4)堆料机和取料机堆料机是:车式悬臂胶带堆料机.(一侧两轨)取料机是:桥式刮板取料机.(两侧两轨)(5)立磨工作原理:物料由三道锁风阀门下料溜子进入磨内,堆积在磨盘中间.由于磨盘的旋转带动磨辊转动物料受离心力的作用想磨盘边缘移动,并被齿入磨辊底部而粉磨.磨辊有液力系统增压以满足粉末需要.磨盘的转速比较高,比相同直径的球蘑机要快大约80%.物料不仅在辊下被压碎,而且被推向外缘,越过挡料圈落入风环,被高速气流入分离器,在回转风叶的作用下进行分选,粗粉重新返回磨盘再粉磨.合格的成品随气流带出机外被收集作为产品,由于风环外气流速度很高因此转热速率很快,小颗粒瞬时得到干燥,大颗粒表面被烘干,再折回重新粉碎过程中得到进一步干燥.(6)O~SEPA选粉机工作原理:待选物料由上部的两个喂料管喂入选粉机,通过撒料盘缓冲板充分分散,落如选粉区,选粉气流大部分来自磨机,通过切向一次风进口.来自收尘设备的收尘风通过二次风进口进入,经导向叶片水平进入选粉区.在选粉机内由垂直叶片和水平叶片组成笼式转子,回转时使内外压差在整个高度内上下保持一定,从而使气流稳定均匀,为精确选粉创造了条件,物料自上而下为每个颗粒提供了多次重复分选的机会,而且每次分选都在精确的离心力和水平风力的平衡条件下进行.细粉从外向内克服了边壁效应的不利影响.(7)电收尘工作原理:电收尘利用高压静电场的作用,使通过的含尘气体中的尘粒荷电,在电场的作用下,使尘粒沉积于电极上,将尘粒从气体中分离出来.电收尘器具有运行可靠,维护简单,电耗低,除尘效率高等优点,在合适条件下使用,其除尘效率可达99%以上. (8)均化库工作原理:该库直径较大,生料先送至顶生料分配器,再经放射状布置的空气输送斜槽入库,库顶还设有收尘器,仓满指示器等装置,在大库的下部中心建有一圈锥型混合室,当轮流向大库的环型库底冲气时生料呈流态化并经混合室周围的8—12个进料孔流入混合库中,同时大库内的生料呈旋涡状踏落,在生料下移的过程中产生重力混合,进入混合库的生料则按扁型四分区进行激烈的空气搅拌,即进行气力均化.混合室的另一作用是靠室内所存一定数量成分均匀的生料起缓冲作用,使进入混合室时略有成分波动的生料缩小其波动.(9)气力输送斜槽以高压离心通风机为动力源,使密闭输送斜槽中的粉状物料保持流态化向斜槽的一端缓慢流动,这种斜槽的主体部分无主动部件,结构简单,输送能力大,易改变输送方向.3、熟料的煅烧生料的预热和预分解系统物料从预热器的顶端加入,从一级旋风筒依次向下再经过分解炉最后入回转窑;从窑头来的高温气体先入分解炉,然后依次向上最后进入增湿塔,一句话概括就是料往下走,气往上流.预分解系统不但合理利用了来自于窑头的废气,节约了能源,而且使物料预先进行了预热和分解,从而为物料的煅烧提供了前提,提高了熟料的质量和生产效率.生料的预热和预分解系统预热与分解系统为五级旋风预热器和分解炉,从窑头来的三次风入分解炉,分解炉上有两个喷煤管来完成煤粉的供给.煅烧设备在预分解窑系统中,回转窑具有燃烧燃料功能,热交换功能,化学反应功能,物料输送功能,降解利用废气物五大功能.回转窑中分为干燥带,预热带,分解带,固相反应带,烧成带和冷却带,在尧柏水泥厂主要是采用ф×60m的回转窑,其放置的倾斜度为4%,传动装置采用的是直流电机单传动,窑体转速为~min.在回转窑的斜度和转速不变的情况下,物料在窑内各带的化学变化和物理状态不同,使得物料以不同的速度通过窑的各带.在烧成带硅酸二钙吸收氧化钙形成硅酸三钙微吸热,只是在熟料形成过程中生成液相时需极少量的熔融净热,在分解窑内,碳酸钙分解需要吸收大量的热量.熟料冷却水泥熟料出窑温度大约为1100~1300摄氏度,充分回收熟料带走的热量以预热二次要气,对提高燃烧速度和燃料温度以及窑和冷却机的热效率,都有主要意义,冷却熟料对于改善熟料的质量和易磨性有良好的效果,冷却良好的熟料可保证设备的安全运转.熟料冷却主要有三种类型:一是:筒式(包括单筒和多筒);二是:篦式(包括震动,回转推动篦式);三是:其他形式(包括立式及"g"式)烧成工段主要设备及其工作原理回转窑(旋窑)的工作原理水泥烧成设备有竖窑、湿法回转窑(旋窑)、普通中空干法窑、立波尔窑、预热机窑(SP)以及目前普遍使用的新型干法回转窑(旋窑)。
水泥生产工艺流程

水泥生产工艺流程1、破碎及预均化(1)破碎水泥生产过程中,大部分原料要进行破碎,如石灰石、黏土、铁矿石及煤等。
石灰石是生产水泥用量最大的原料,开采后的粒度较大,硬度较高,因此石灰石的破碎在水泥厂的物料破碎中占有比较重要的地位。
(2)原料预均化预均化技术就是在原料的存、取过程中,运用科学的堆取料技术,实现原料的初步均化,使原料堆场同时具备贮存与均化的功能。
2、生料制备水泥生产过程中,每生产1吨硅酸盐水泥至少要粉磨3吨物料(包括各种原料、燃料、熟料、混合料、石膏),据统计,干法水泥生产线粉磨作业需要消耗的动力约占全厂动力的60%以上,其中生料粉磨占30%以上,煤磨占约3%,水泥粉磨约占40%。
因此,合理选择粉磨设备和工艺流程,优化工艺参数,正确操作,控制作业制度,对保证产品质量、降低能耗具有重大意义。
3、生料均化新型干法水泥生产过程中,稳定入窖生料成分是稳定熟料烧成热工制度的前提,生料均化系统起着稳定入窖生料成分的最后一道把关作用.4、预热分解把生料的预热和部分分解由预热器来完成,代替回转窑部分功能,达到缩短回窑长度,同时使窑内以堆积状态进行气料换热过程,移到预热器内在悬浮状态下进行,使生料能够同窑内排出的炽热气体充分混合,增大了气料接触面积,传热速度快,热交换效率高,达到提高窑系统生产效率、降低熟料烧成热耗的目的。
(1)物料分散换热80%在入口管道内进行的.喂入预热器管道中的生料,在与高速上升气流的冲击下,物料折转向上随气流运动,同时被分散。
(2)气固分离当气流携带料粉进入旋风筒后,被迫在旋风筒筒体与内筒(排气管)之间的环状空间内做旋转流动,并且一边旋转一边向下运动,由筒体到锥体,一直可以延伸到锥体的端部,然后转而向上旋转上升,由排气管排出.(3)预分解预分解技术的出现是水泥煅烧工艺的一次技术飞跃.它是在预热器和回转窑之间增设分解炉和利用窑尾上升烟道,设燃料喷入装置,使燃料燃烧的放热过程与生料的碳酸盐分解的吸热过程,在分解炉内以悬浮态或流化态下迅速进行,使入窑生料的分解率提高到90%以上.将原来在回转窑内进行的碳酸盐分解任务,移到分解炉内进行;燃料大部分从分解炉内加入,少部分由窑头加入,减轻了窑内煅烧带的热负荷,延长了衬料寿命,有利于生产大型化;由于燃料与生料混合均匀,燃料燃烧热及时传递给物料,使燃烧、换热及碳酸盐分解过程得到优化。
水泥厂工艺流程
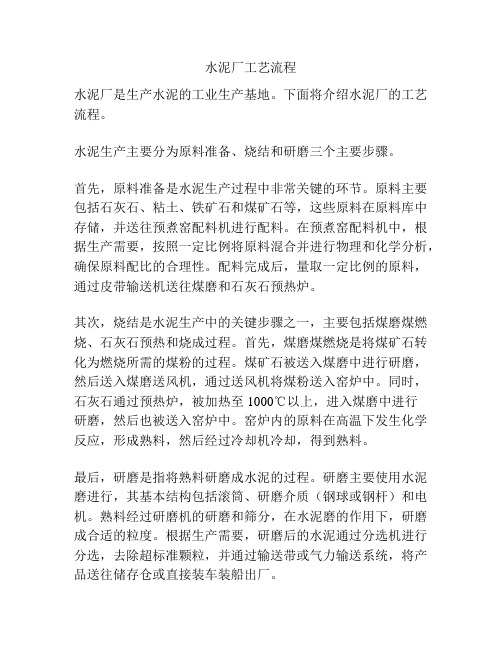
水泥厂工艺流程水泥厂是生产水泥的工业生产基地。
下面将介绍水泥厂的工艺流程。
水泥生产主要分为原料准备、烧结和研磨三个主要步骤。
首先,原料准备是水泥生产过程中非常关键的环节。
原料主要包括石灰石、粘土、铁矿石和煤矿石等,这些原料在原料库中存储,并送往预煮窑配料机进行配料。
在预煮窑配料机中,根据生产需要,按照一定比例将原料混合并进行物理和化学分析,确保原料配比的合理性。
配料完成后,量取一定比例的原料,通过皮带输送机送往煤磨和石灰石预热炉。
其次,烧结是水泥生产中的关键步骤之一,主要包括煤磨煤燃烧、石灰石预热和烧成过程。
首先,煤磨煤燃烧是将煤矿石转化为燃烧所需的煤粉的过程。
煤矿石被送入煤磨中进行研磨,然后送入煤磨送风机,通过送风机将煤粉送入窑炉中。
同时,石灰石通过预热炉,被加热至1000℃以上,进入煤磨中进行研磨,然后也被送入窑炉中。
窑炉内的原料在高温下发生化学反应,形成熟料,然后经过冷却机冷却,得到熟料。
最后,研磨是指将熟料研磨成水泥的过程。
研磨主要使用水泥磨进行,其基本结构包括滚筒、研磨介质(钢球或钢杆)和电机。
熟料经过研磨机的研磨和筛分,在水泥磨的作用下,研磨成合适的粒度。
根据生产需要,研磨后的水泥通过分选机进行分选,去除超标准颗粒,并通过输送带或气力输送系统,将产品送往储存仓或直接装车装船出厂。
总结起来,水泥厂的工艺流程主要包括原料准备、烧结和研磨三个步骤。
原料准备是将石灰石、粘土、铁矿石和煤矿石等原料进行配料和预处理的过程。
烧结是将配料后的原料在预煮窑中进行高温下的煅烧和冷却,得到熟料的过程。
研磨是将熟料研磨成合适粒度的水泥的过程。
工艺流程中的每个环节都至关重要,一环扣一环,相互关联,互为影响,只有各个环节都运行良好,才能确保水泥的质量和生产效率。
水泥厂的工艺流程

水泥厂的工艺流程
《水泥厂工艺流程》
水泥是建筑行业中不可或缺的材料之一,其生产过程需要经过许多复杂的工艺流程。
以下是一般水泥厂的工艺流程:
1. 采矿和原料处理:水泥的主要原料包括石灰石、黏土、铁矿石和石膏。
这些原料需要在采矿场或矿山中进行采集,并经过破碎、混合和磨碎等处理,使其成为适合生产水泥的颗粒状物料。
2. 熟料制备:将经过处理的原料送入回转窑或立窑中进行煅烧,煅烧过程中原料在高温下经历化学反应,形成熟料。
3. 粉磨和混合:将熟料通过磨粉机进行细磨,磨成水泥制成的粉末。
同时,根据不同种类的水泥需要,将石膏、矿渣等辅料加入,进行混合。
4. 包装和运输:将成品水泥装入袋中,并通过输送带或装车设备进行包装和运输。
以上是一般水泥厂的工艺流程,其中每个环节都需要严格控制和监测,确保水泥的质量符合标准。
同时,随着技术的发展,水泥生产的工艺流程也在不断更新和完善,以提高生产效率和减少能源消耗。
水泥生产工艺流程图

水泥生产工艺流程图水泥的生产工艺可以简述为两磨一烧,即原料要经过采掘、破碎、磨细和混匀制成生料,生料经1450℃的高温烧成熟料,熟料再经破碎,与石膏或其他混合材一起磨细成为水泥。
一、水泥生产的生料制备1破碎工艺水泥生产过程中,很大一部分原料要进行破碎,如石灰石、黏土、铁矿石及煤等。
2生料的预均化工艺原料预均化,实现原料的初步均化,。
3生料的烘干工艺烘干工艺是将生料通过烘干机加热干燥。
烘干设备有回转式和悬浮式烘干机、烘干塔等,回转式烘干机内温度约700℃,排放废气量约1300m3/t料。
4生料的粉磨工艺二、水泥生产的煅烧目前大中型水泥厂多使用回转窑,小型水泥厂多使用立窑,我国还有50﹪以上的水泥仍使用立窑生产。
1立窑煅烧立窑工艺的设备是静止的竖窑,分为普通立窑和机械化立窑,属于半干法生产。
立窑的日产量已达250~300t/d。
立窑又分普通立窑和机立窑,普通立窑采用间歇式生产,能耗热耗较高,产生的废气量约3900立米/吨熟料,粉尘浓度15g/m3。
2新型干法旋窑煅烧它是在旋窑煅烧增加预分解窑与悬浮预热工艺。
生料在预热器以内悬浮状态或沸腾状态下与热气流进行热交换,又在分解炉中加入占总燃料用量50~60%的燃料,使生料在入窑前的碳酸钙分解率达80%以上。
预热分解把生料的预热和部分分解由预热器来完成,代替回转窑部分功能。
(1)物料分散换热80%在入口管道内进行的。
喂入预热器管道中的生料,在与高速上升气流的冲击下,物料折转向上随气流运动,同时被分散。
(2)气固分离当气流携带料粉进入旋风筒后,被迫在旋风筒筒体与内筒(排气管)之间的环状空间内做旋转流动,并且一边旋转一边向下运动,由筒体到锥体,一直可以延伸到锥体的端部,然后转而向上旋转上升,由排气管排出。
(3)预分解预分解技术是在预热器和回转窑之间增设分解炉和利用窑尾上升烟道,设燃料喷入装置,使燃料燃烧的放热过程与生料的碳酸盐分解的吸热过程,在分解炉内以悬浮态或流化态下迅速进行,使入窑生料的分解率提高到90%以上。
水泥生产工艺流程

水泥生产工艺流程1、破碎及预均化(1)破碎水泥生产过程中,大部分原料要进行破碎,如石灰石、黏土、铁矿石及煤等。
石灰石是生产水泥用量最大的原料,开采后的粒度较大,硬度较高,因此石灰石的破碎在水泥厂的物料破碎中占有比较重要的地位。
(2)原料预均化预均化技术就是在原料的存、取过程中,运用科学的堆取料技术,实现原料的初步均化,使原料堆场同时具备贮存与均化的功能。
2、生料制备水泥生产过程中,每生产1吨硅酸盐水泥至少要粉磨3吨物料(包括各种原料、燃料、熟料、混合料、石膏),据统计,干法水泥生产线粉磨作业需要消耗的动力约占全厂动力的60%以上,其中生料粉磨占30%以上,煤磨占约3%,水泥粉磨约占40%。
因此,合理选择粉磨设备和工艺流程,优化工艺参数,正确操作,控制作业制度,对保证产品质量、降低能耗具有重大意义。
3、生料均化新型干法水泥生产过程中,稳定入窖生料成分是稳定熟料烧成热工制度的前提,生料均化系统起着稳定入窖生料成分的最后一道把关作用。
4、预热分解把生料的预热和部分分解由预热器来完成,代替回转窑部分功能,达到缩短回窑长度,同时使窑内以堆积状态进行气料换热过程,移到预热器内在悬浮状态下进行,使生料能够同窑内排出的炽热气体充分混合,增大了气料接触面积,传热速度快,热交换效率高,达到提高窑系统生产效率、降低熟料烧成热耗的目的。
(1)物料分散换热80%在入口管道内进行的。
喂入预热器管道中的生料,在与高速上升气流的冲击下,物料折转向上随气流运动,同时被分散。
(2)气固分离当气流携带料粉进入旋风筒后,被迫在旋风筒筒体与内筒(排气管)之间的环状空间内做旋转流动,并且一边旋转一边向下运动,由筒体到锥体,一直可以延伸到锥体的端部,然后转而向上旋转上升,由排气管排出。
(3)预分解预分解技术的出现是水泥煅烧工艺的一次技术飞跃。
它是在预热器和回转窑之间增设分解炉和利用窑尾上升烟道,设燃料喷入装置,使燃料燃烧的放热过程与生料的碳酸盐分解的吸热过程,在分解炉内以悬浮态或流化态下迅速进行,使入窑生料的分解率提高到90%以上。
水泥厂设备工艺流程图
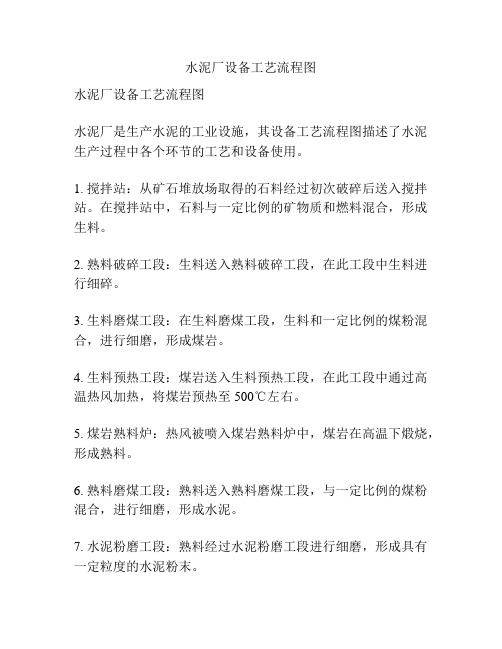
水泥厂设备工艺流程图水泥厂设备工艺流程图水泥厂是生产水泥的工业设施,其设备工艺流程图描述了水泥生产过程中各个环节的工艺和设备使用。
1. 搅拌站:从矿石堆放场取得的石料经过初次破碎后送入搅拌站。
在搅拌站中,石料与一定比例的矿物质和燃料混合,形成生料。
2. 熟料破碎工段:生料送入熟料破碎工段,在此工段中生料进行细碎。
3. 生料磨煤工段:在生料磨煤工段,生料和一定比例的煤粉混合,进行细磨,形成煤岩。
4. 生料预热工段:煤岩送入生料预热工段,在此工段中通过高温热风加热,将煤岩预热至500℃左右。
5. 煤岩熟料炉:热风被喷入煤岩熟料炉中,煤岩在高温下煅烧,形成熟料。
6. 熟料磨煤工段:熟料送入熟料磨煤工段,与一定比例的煤粉混合,进行细磨,形成水泥。
7. 水泥粉磨工段:熟料经过水泥粉磨工段进行细磨,形成具有一定粒度的水泥粉末。
8. 水泥储存工段:生产出的水泥粉末通过输送带输送到水泥的储存设备中,进行长时间的储存。
9. 水泥包装工段:从水泥储存设备中取出一定量的水泥,通过自动包装设备进行包装,形成袋装水泥或散装水泥。
10. 水泥包装堆放场:包装好的水泥袋或散装水泥在堆放场中存放待运输或销售。
整个水泥厂设备工艺流程图描述了水泥从原料破碎、混合、磨煤,到生料预热、煅烧,再经过磨煤、磨水泥等工艺步骤,最终形成水泥粉末,并进行储存和包装。
这个流程图清晰地展示了每个工艺步骤所需要的设备和操作,使人们更好地理解水泥生产的流程和步骤。
水泥是建筑化工材料中的重要组成部分,对于建筑工程的质量和耐久性至关重要。
水泥厂设备的使用和工艺流程的规范可以保证水泥的质量和生产效率,对于建筑领域的发展和水泥行业的发展具有重要意义。
水泥厂生产工艺流程

水泥厂生产工艺流程水泥厂是指采用石灰石和粘土等原材料通过机械设备进行破碎、磨细、混合等工艺过程,生产出水泥制品的工厂。
水泥是建筑施工中不可或缺的材料之一,广泛应用于各种建筑工程中。
接下来就是介绍一下水泥厂的较常见的生产工艺流程。
首先,原材料的采集和破碎是水泥生产的第一步。
一般来说,石灰石和粘土是水泥的主要原料。
石灰石通过采矿车辆运输到水泥厂,并进行破碎处理,以便达到所需的粒度。
而粘土则需要经过开采、挖掘、爆破等过程,并使用运输设备将其运送到水泥厂。
接下来是原料的预处理。
经过破碎的石灰石和粘土需要经过配料系统进行混合,以达到生产水泥所需的成分比例。
配料系统中包括料仓、给料机、输送带和称量设备等,确保原料按照一定比例准确地混合。
预处理完成后,原料进入研磨系统进行磨细。
研磨系统主要由磨机和磨辊组成,原料被送入磨机中进行磨破,以得到所需的细度。
研磨后的原料称为“生料”,它是制备水泥的基础。
接下来是生料的煅烧。
生料通过热风炉进行煅烧,炉内的高温燃烧使生料中的矿物质发生化学反应。
这个过程中,生料逐渐转化为熟料,其中包括熟料石、副石和煤膏等。
煅烧温度通常在1400℃左右,但具体温度和时间会根据不同的水泥类型进行调整。
煅烧后的熟料需要经过冷却,并与适量的石膏进行混合。
石膏是水泥生产中的一种添加剂,它能够调节水泥的凝结时间和控制其强度发展。
混合后的熟料和石膏称为熟料粉,它是生产水泥最重要的原料之一。
最后,熟料粉通过水泥磨机研磨成水泥粉,进行精制处理,以确保水泥的质量和性能。
磨机是水泥生产线中一台重要的设备,它能够将熟料粉研磨成所需细度的水泥粉。
磨粉后的水泥粉通过输送设备进入储存仓,等待出售或使用。
以上就是水泥厂常见的生产工艺流程。
每个环节都需要严格控制和检测,以确保水泥的质量和性能。
水泥生产过程中还会产生废气和废渣等副产物,对环境造成一定的影响。
因此,在水泥生产过程中,应加强环境保护措施,减少对环境的影响,实现可持续发展。
水泥厂生产流程及设备原理

水泥厂生产流程及设备原理简介1、水泥厂生产流程水泥生产工艺水泥的生产工艺简单讲便是两磨一烧,即原料要经过采掘、破碎、磨细和混匀制成生料,生料经1450℃的高温烧成熟料,熟料再经破碎,与石膏或其他混合材一起磨细成为水泥。
由于生料制备有干湿之别,所以将生产方法分为湿法、半干法或半湿法、干法3种。
全场平面布置图水泥厂的工艺流程简图图立磨原理图图图全厂主机设备与存储设备表全厂主机设备与存储设备列表生料磨、回转窑、水泥磨、煤磨、冷却机、储存设备(堆料场,配料站,均化库,熟料库,水泥库)(2)板式喂料机(3)MLS3626立式辊磨机(4)LS型螺旋输送机(5)链斗输送机(6)O-Sepa选粉机(7)罗茨鼓风机(8)水泥窑尾引风机(9)调速型液力偶合器(10)陕西压强设备厂调速机(11)离心通风机2、生料制备矿山开采的工艺流程矿山开采的工艺流程:采矿工作面的整平→布置爆孔→钻孔→装药爆破→集矿→装车原料的破碎,预均化和生料粉磨从矿山开采的矿石用卡车运到水泥厂,由板式喂料机送入单段锤式破碎机,再用皮带送到预均化堆场,采用横堆竖取的方式取料,料经皮带送到石灰石仓.再加上从铁粉仓和粘土仓及粉煤灰仓经电子皮带称定量取料混合后送入生料磨(立磨).经立磨粉磨后粗细料被选粉机分离,粗料返回立磨继续粉磨,细料送入两个锥型仓暂时储存.生料储存,均化和输送由立磨出来的细粉经气力输送管道和皮带提升机送到均化库顶部,经四嘴下料机进入均化库.均化库既有均化的作用也有储存生料的作用.水泥厂生料工段工艺流程图石灰石→板式喂料机→单段锤式破碎机→皮带→堆料机→取料机→皮带→配料站→立磨→o-sepa选粉机→气力输送管道和皮带提升机→生料均化库生料工段主要设备,设备工作原理(1) 板式喂料机板式喂料机能承受较大的料压和冲击,适应大块矿石的喂料,该机给料均衡运转可靠,但设备较重,价格高.板式喂料机分轻型,中型和重型三种.立窑水泥厂石灰石破碎的喂料机一般选用中型的占多.(2)反击锤式破碎机工作原理:物料进入锤破中受到高速回转的锤头冲击而被破碎,物料从锤头处获得动能以高速冲向打击板而被第二次破碎,粒径合格的物料通过蓖条排出,较大粒径在蓖条上再经锤头附加冲击,研磨而被破碎,直至合格后通过蓖条排出.(3) 袋收尘——脉冲袋收尘器是一种新型高效袋式收沉器,利用脉冲阀使压缩空气定时地对滤袋进行喷吹清灰,滤袋寿命长,收尘效率高.工作原理:含尘气体由进风口进入箱体,气体由滤袋外进入滤袋内,经文氏管进入上箱体,从出风口排出,粉尘能截留在滤袋外表面.为了保持收尘器的阻力在一定的范围内(一般为1176~1470Pa)必须定期清灰.清灰时由脉冲控制仪按程序开启控制阀使气沧内的压缩空气由喷嘴管的孔眼高速喷出,每个孔眼对准一个滤袋中心,通过文氏管的诱导在高速气体周围引入相当于喷嘴空气5—7倍的二次空气冲进滤袋,使滤袋急剧膨胀,引起冲击震动.同时产生由袋内向袋外的逆向气流,是黏附在滤袋外表面的积灰被吹落.此时滤布空隙中的粉尘也被吹落,吹扫下来的积灰落入灰斗经排灰系统排出.(4)堆料机和取料机堆料机是:车式悬臂胶带堆料机.(一侧两轨)取料机是:桥式刮板取料机.(两侧两轨)(5)立磨工作原理:物料由三道锁风阀门下料溜子进入磨内,堆积在磨盘中间.由于磨盘的旋转带动磨辊转动物料受离心力的作用想磨盘边缘移动,并被齿入磨辊底部而粉磨.磨辊有液力系统增压以满足粉末需要.磨盘的转速比较高,比相同直径的球蘑机要快大约80%.物料不仅在辊下被压碎,而且被推向外缘,越过挡料圈落入风环,被高速气流入分离器,在回转风叶的作用下进行分选,粗粉重新返回磨盘再粉磨.合格的成品随气流带出机外被收集作为产品,由于风环外气流速度很高因此转热速率很快,小颗粒瞬时得到干燥,大颗粒表面被烘干,再折回重新粉碎过程中得到进一步干燥.(6)O~SEPA选粉机工作原理:待选物料由上部的两个喂料管喂入选粉机,通过撒料盘缓冲板充分分散,落如选粉区,选粉气流大部分来自磨机,通过切向一次风进口.来自收尘设备的收尘风通过二次风进口进入,经导向叶片水平进入选粉区.在选粉机内由垂直叶片和水平叶片组成笼式转子,回转时使内外压差在整个高度内上下保持一定,从而使气流稳定均匀,为精确选粉创造了条件,物料自上而下为每个颗粒提供了多次重复分选的机会,而且每次分选都在精确的离心力和水平风力的平衡条件下进行.细粉从外向内克服了边壁效应的不利影响.(7)电收尘工作原理:电收尘利用高压静电场的作用,使通过的含尘气体中的尘粒荷电,在电场的作用下,使尘粒沉积于电极上,将尘粒从气体中分离出来.电收尘器具有运行可靠,维护简单,电耗低,除尘效率高等优点,在合适条件下使用,其除尘效率可达99%以上. (8)均化库工作原理:该库直径较大,生料先送至顶生料分配器,再经放射状布置的空气输送斜槽入库,库顶还设有收尘器,仓满指示器等装置,在大库的下部中心建有一圈锥型混合室,当轮流向大库的环型库底冲气时生料呈流态化并经混合室周围的8—12个进料孔流入混合库中,同时大库内的生料呈旋涡状踏落,在生料下移的过程中产生重力混合,进入混合库的生料则按扁型四分区进行激烈的空气搅拌,即进行气力均化.混合室的另一作用是靠室内所存一定数量成分均匀的生料起缓冲作用,使进入混合室时略有成分波动的生料缩小其波动.(9)气力输送斜槽以高压离心通风机为动力源,使密闭输送斜槽中的粉状物料保持流态化向斜槽的一端缓慢流动,这种斜槽的主体部分无主动部件,结构简单,输送能力大,易改变输送方向.3、熟料的煅烧生料的预热和预分解系统物料从预热器的顶端加入,从一级旋风筒依次向下再经过分解炉最后入回转窑;从窑头来的高温气体先入分解炉,然后依次向上最后进入增湿塔,一句话概括就是料往下走,气往上流.预分解系统不但合理利用了来自于窑头的废气,节约了能源,而且使物料预先进行了预热和分解,从而为物料的煅烧提供了前提,提高了熟料的质量和生产效率.生料的预热和预分解系统预热与分解系统为五级旋风预热器和分解炉,从窑头来的三次风入分解炉,分解炉上有两个喷煤管来完成煤粉的供给.煅烧设备在预分解窑系统中,回转窑具有燃烧燃料功能,热交换功能,化学反应功能,物料输送功能,降解利用废气物五大功能.回转窑中分为干燥带,预热带,分解带,固相反应带,烧成带和冷却带,在尧柏水泥厂主要是采用ф×60m的回转窑,其放置的倾斜度为4%,传动装置采用的是直流电机单传动,窑体转速为~min.在回转窑的斜度和转速不变的情况下,物料在窑内各带的化学变化和物理状态不同,使得物料以不同的速度通过窑的各带.在烧成带硅酸二钙吸收氧化钙形成硅酸三钙微吸热,只是在熟料形成过程中生成液相时需极少量的熔融净热,在分解窑内,碳酸钙分解需要吸收大量的热量.熟料冷却水泥熟料出窑温度大约为1100~1300摄氏度,充分回收熟料带走的热量以预热二次要气,对提高燃烧速度和燃料温度以及窑和冷却机的热效率,都有主要意义,冷却熟料对于改善熟料的质量和易磨性有良好的效果,冷却良好的熟料可保证设备的安全运转.熟料冷却主要有三种类型:一是:筒式(包括单筒和多筒);二是:篦式(包括震动,回转推动篦式);三是:其他形式(包括立式及"g"式)烧成工段主要设备及其工作原理回转窑(旋窑)的工作原理水泥烧成设备有竖窑、湿法回转窑(旋窑)、普通中空干法窑、立波尔窑、预热机窑(SP)以及目前普遍使用的新型干法回转窑(旋窑)。
水泥工艺流程
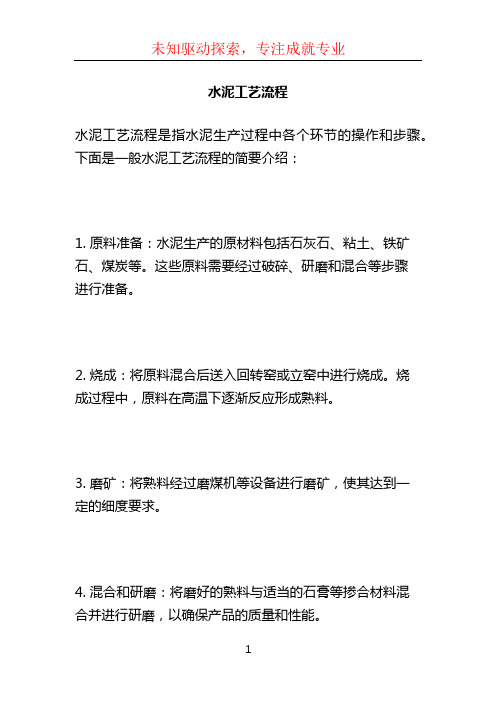
水泥工艺流程
水泥工艺流程是指水泥生产过程中各个环节的操作和步骤。
下面是一般水泥工艺流程的简要介绍:
1. 原料准备:水泥生产的原材料包括石灰石、粘土、铁矿石、煤炭等。
这些原料需要经过破碎、研磨和混合等步骤
进行准备。
2. 烧成:将原料混合后送入回转窑或立窑中进行烧成。
烧
成过程中,原料在高温下逐渐反应形成熟料。
3. 磨矿:将熟料经过磨煤机等设备进行磨矿,使其达到一
定的细度要求。
4. 混合和研磨:将磨好的熟料与适当的石膏等掺合材料混
合并进行研磨,以确保产品的质量和性能。
5. 煅烧:将混合磨制的水泥料进一步加热,使其达到特定
的温度和时间,以增加其强度和稳定性。
6. 成品仓储和包装:经过煅烧后的水泥熟料需要进行冷却,然后存放在成品仓中,最后进行包装和装车。
值得注意的是,不同的水泥生产工艺可能会有所差异,具
体操作步骤和设备配置可能会有所不同。
此外,还有一些
辅助工序和设备在水泥生产中起到重要作用,如煤磨、排尘、余热回收等。
水泥厂煤的工艺过程
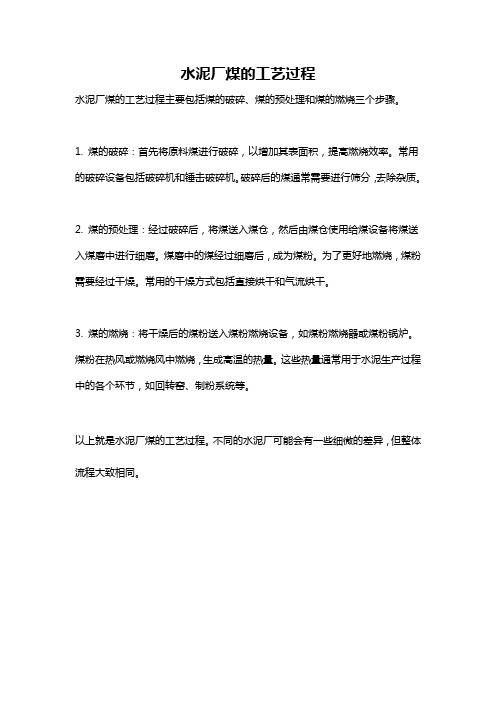
水泥厂煤的工艺过程
水泥厂煤的工艺过程主要包括煤的破碎、煤的预处理和煤的燃烧三个步骤。
1. 煤的破碎:首先将原料煤进行破碎,以增加其表面积,提高燃烧效率。
常用的破碎设备包括破碎机和锤击破碎机。
破碎后的煤通常需要进行筛分,去除杂质。
2. 煤的预处理:经过破碎后,将煤送入煤仓,然后由煤仓使用给煤设备将煤送入煤磨中进行细磨。
煤磨中的煤经过细磨后,成为煤粉。
为了更好地燃烧,煤粉需要经过干燥。
常用的干燥方式包括直接烘干和气流烘干。
3. 煤的燃烧:将干燥后的煤粉送入煤粉燃烧设备,如煤粉燃烧器或煤粉锅炉。
煤粉在热风或燃烧风中燃烧,生成高温的热量。
这些热量通常用于水泥生产过程中的各个环节,如回转窑、制粉系统等。
以上就是水泥厂煤的工艺过程。
不同的水泥厂可能会有一些细微的差异,但整体流程大致相同。
水泥厂工艺流程(配图)

一、水泥生产原燃料及配料生产硅酸盐水泥的主要原料为石灰原料和粘土质原料,有时还要根据燃料品质和水泥品种,掺加校正原料以补充某些成分的不足,还可以利用工业废渣作为水泥的原料或混合材料进行生产。
1、石灰石原料石灰质原料是指以碳酸钙为主要成分的石灰石、泥灰岩、白垩和贝壳等。
石灰石是水泥生产的主要原料,每生产一吨熟料大约需要1.3吨石灰石,生料中80%以上是石灰石。
2、黏土质原料黏土质原料主要提供水泥熟料中的、、及少量的。
天然黏土质原料有黄土、黏土、页岩、粉砂岩及河泥等。
其中黄土和黏土用得最多。
此外,还有粉煤灰、煤矸石等工业废渣。
黏土质为细分散的沉积岩,由不同矿物组成,如高岭土、蒙脱石、水云母及其它水化铝硅酸盐。
3、校正原料当石灰质原料和黏土质原料配合所得生料成分不能满足配料方案要求时(有的含量不足,有的和含量不足)必须根据所缺少的组分,掺加相应的校正原料(1)硅质校正原料含80%以上(2)铝质校正原料含30%以上(3)铁质校正原料含50%以上二、硅酸盐水泥熟料的矿物组成硅酸盐水泥熟料的矿物主要由硅酸三钙()、硅酸二钙()、铝酸三钙()和铁铝酸四钙()组成。
三、工艺流程1、破碎及预均化(1)破碎水泥生产过程中,大部分原料要进行破碎,如石灰石、黏土、铁矿石及煤等。
石灰石是生产水泥用量最大的原料,开采后的粒度较大,硬度较高,因此石灰石是生产水泥用量最大的原料,开采后的粒度较大,硬度较高,因此石灰石的破碎在水泥厂的物料破碎中占有比较重要的地位。
破碎过程要比粉磨过程经济而方便,合理选用破碎设备和和粉磨设备非常重要。
在物料进入粉磨设备之前,尽可能将大块物料破碎至细小、均匀的粒度,以减轻粉磨设备的负荷,提高黂机的产量。
物料破碎后,可减少在运输和贮存过程中不同粒度物料的分离现象,有得于制得成分均匀的生料,提高配料的准确性。
(2)原料预均化预均化技术就是在原料的存、取过程中,运用科学的堆取料技术,实现原料的初步均化,使原料堆场同时具备贮存与均化的功能。
- 1、下载文档前请自行甄别文档内容的完整性,平台不提供额外的编辑、内容补充、找答案等附加服务。
- 2、"仅部分预览"的文档,不可在线预览部分如存在完整性等问题,可反馈申请退款(可完整预览的文档不适用该条件!)。
- 3、如文档侵犯您的权益,请联系客服反馈,我们会尽快为您处理(人工客服工作时间:9:00-18:30)。
三大工艺流程简介第一,生料制备工艺流程简介石灰石预均化堆场采用φ90m圆形预均化堆场,堆料为环线连续布料,端面取料、中心卸料。
设有圆形混合预均化堆取料机(1102)一台套。
石灰石在矿山破碎后,经带式输送机送至石灰石转运站,经带式输送机(1101)转运至Φ90m圆形预均化堆场,圆形预均化堆场有效储量42000t。
经带式输送机(1101)送至预均化堆场的石灰石,由悬臂堆料皮带机(1102a)进行连续人字形堆料,由桥式刮板取料机(1102b)横切端面取料。
悬臂堆料皮带机堆料能力为1000t/h,取料机能力为500t/h。
物料由桥式刮板输送机取出进入带式输送机(1104),经带式输送机(1104)输送至Φ12m石灰石配料库内用于配料。
堆场内下部设有备用卸料坑,由棒闸(1103)控制,当堆场检修或取料机发生故障时,可由此旁路暂时卸料。
整个堆料和取料过程采用计算机全自动控制。
石灰石转运点设有单机脉冲袋除尘器对扬尘点进行收尘处理。
粒度≤400mm的砂岩、煤矸石由汽车运输进厂,先分别存放各自的露天堆场,然后分时段由铲车从露天堆场取出喂入喂料仓,经仓底板式喂料机(1301)卸入锤式破碎机(1302)破碎,破碎后物料(粒度≤25mm)由带式输送机(1309)送至辅助原料联合预均化堆场内储存,受料仓有效容积25t,破碎机生产能力为200t/h。
硫酸渣由装载机从铁粉堆场中取出卸入受料仓中(仓有效容积:45t),经仓底棒闸(1305)卸到带式输送机(1309)上并送至辅助原料联合预均化堆场中储存。
采用43×160m矩形联合预均化堆场对砂岩、煤矸石、硫酸渣进行预均化和储存。
所有辅助原料均由一台能力为250t/h的悬臂侧堆料机堆料,并共用一台能力为150t/h的侧式刮板取料机取料。
出均化堆场的砂岩、煤矸石、硫酸渣由带式输送机(1604)、电液动三通(1901)分两路,一路砂岩直接入库,另一路煤矸石、硫酸渣由正反转带式输送机(1902)分别送入各自的配料库中。
配料站仓顶设单机脉冲袋除尘器对各扬尘点进行收尘处理。
在配料站中,各种原料按设定的配比,由各自的计量调速定量给料机或转子秤(粉煤灰)计量。
石灰石从石灰石配料库底经棒闸(1903)卸出,并经计量调速定量给料机(1905)送到带式输送机(1909)上;砂岩从砂岩配料库中经仓底棒闸(1904)卸出,由定量给料机(1907)送到带式输送机(1909)上;煤矸石从煤矸石配料库中经仓底棒闸(1904)卸出,由定量给料机(1908)送到带式输送机(1909)上;硫酸渣从硫酸渣配料库中经仓底棒闸(1904)卸出,由定量给料机(1906)送到带式输送机(1909)上;参与原料配料用的干粉煤灰,由汽车直接送至粉煤灰库中,经螺旋闸门(2003)、给料机(2002)卸出,由转子秤(2004)送到带式输送机(1909)上。
由多元素荧光分析仪和微机组成的生料质量控制系统,可自动分析出磨生料成分,并根据分析结果和目标值自动调节定量给料机或转子秤(粉煤灰)转速控制各原料的下料量,确保出磨生料成分合格。
带式输送机(1909)将配合料送至生料粉磨车间,带式输送机(1909)上挂有除铁器(1910),将混入的铁件除去,同时在该皮带上装有金属探测器(1911),发现有金属后气动三通(2101)换向,将混有金属的物料卸到生料磨缓冲料仓(2105)内,以保证生料磨的安全正常。
生料粉磨采用ATOX50立磨(2103),磨机入口采用回转下料器喂料锁风。
带式输送机(1909)送来的原料通过回转下料器(2102)喂入生料磨(2103),物料在磨内被研压粉碎、烘干并被选粉机(2103c)分选,成品生料粉随出磨气体带出立磨。
入磨物料粒度为95%<100mm,综合水份一般为4.0 %,最大8.0%,产品细度为R80≤12%,水份≤0.5%,台时产量为400t/h。
采用窑尾预热器排出的废气作为立磨烘干的热源,在煤磨正常运转时,出预热器温度~320℃、流量为350000Nm3/h的窑尾废气经由窑尾高温风机(2418),分为两部分,一部分经旋风收尘器(2212)送至煤磨,大部分经增湿塔(2201)送至生料磨,与来自生料磨循环风机(2113)的循环风相混合进入生料磨。
当窑尾不能提供热风时,由与煤磨共用的热风炉(2720)提供热源。
入生料磨前的管道上设有冷风阀(2116a、2116b),可调节入磨热风的温度。
出磨的废气温度为~90℃,流量为475560 Nm3/h,含尘浓度为589g/ Nm3。
高浓度的含尘气体随后进入旋风收尘器(四筒)(2112)进行料气分离。
收下的成品经回转下料器(2112a、2112b、2112c、2112d)、空气输送斜槽(2118)卸到生料入库输送系统中的空气输送斜槽(2120),并最终进入生料均化库内。
出旋风收尘器的气体经过循环风机(2113)后,一部分废气作为循环风重新回到磨内,其余的含尘气体则进入窑、磨废气处理系统。
循环风机(2113)的进口设有调节阀(2113a),用以调节磨内通风量。
立磨(2103)入口设有电动插板阀(2115),用于生料磨停磨时,可阻止热气流进入磨机。
生料粉磨设置有物料外循环系统。
磨内不能被上升气流带起的大颗粒物料作为外循环物料通过振动输送机(2103s)、提升机(2104)、带式输送机(1909)送入外循环生料仓(2105)或直接入磨。
循环料仓内物料经带式输送机(2107)重新喂入立磨中。
带式输送机(2107)上设除铁器(2108),进行二次除铁,若还发现有意外产生的铁件,则通过气动侧三通溜子(2109)外排。
正常外循环物料量~100t/h,最大~200t/h。
外循环系统可增加磨机的产量,降低能耗。
窑、磨废气处理采用袋收尘器(2205),袋收尘器净过滤面积为13996m2,过滤风速为0.95~1.03m/min ,净化后气体含尘浓度<50mg/Nm3。
来自生料粉磨系统循环风机(2113)的废气也经过袋收尘器(2205)收尘净化后,由废气风机(2210)和烟囱排入大气。
袋收尘器(2205)收下的窑灰,由链运机(2206、2207、2208、2209)卸出,汇集到生料入库输送系统中的空气输送斜槽(2120)上,空气输送斜槽(2120)上的物料既可进入生料均化库内,又可卸到提升机(2401)上直接入窑。
增湿塔底干灰经螺旋输送机(2201a)、电动双翻板阀(2201c)、链运机(2203)汇至链运机(2214),气动插板阀(2214a)开启时,干灰经空气输送斜槽(2120)进入生料均化库提升机(2301),气动插板阀(2214a)关闭时,干灰进入窑提升机(2401),直接入窑。
增湿塔底湿灰经螺旋输送机(2201a)、电动双翻板阀(2201b)外排。
当生料磨停磨而烧成系统运转时,须关闭生料磨进口阀门(2115)。
出窑尾的高温废气经高温风机(2418)、增湿塔(2201)降温调质后,通过生料粉磨系统的循环风管,绕过生料磨,直接进入袋收尘器(2205)进行收尘处理,净化后气体由废气风机(2210)排放。
生料细度可通过选粉机转子速度调节。
生料磨入磨物料量根据磨机进出口压差调节;磨内通风量根据旋风筒出口流量调节,由磨系统风机阀门(2113a)控制;根据磨机入口负压、废气风机转速控制循环风量;根据磨机出口废气温度控制磨机喷水量。
当窑、磨同时正常运行时,来自生料磨生料通过空气输送斜槽(2120)、再由提升机(2301)经库顶斜槽(2303)、生料分配器(2305)输送入生料均化库。
生料均化库为φ22.5m IBAU库,储量16000t,库中心结构为一大圆锥,库底圆锥周围的环形区被分成向库中心倾斜的八块扇形区,在每块扇形区又分为两个充气区域,每个充气区域装有十条不同规格的充气箱,充气时两个充气区域轮流充气,生料被送至其中一条径向布置的充气箱上,再通过圆锥体下部的出料口,经充气螺旋闸门、气动流量调节阀及卸料斜槽进入库底中央的均化仓(2330)。
库底圆锥体下部至均化仓共有八套卸料系统,卸料时每次由两套卸料系统卸出,八套卸料系统循环轮流卸料。
环形区内的充气箱,由一台罗茨风机(2327)向选定的卸料区供气,该区上部物料下落形成一漏斗状料流,料流下部横断面上包含有不同时间入库的料层。
当生料从库顶达到库底时,即产生重力混合作用。
生料进入均化仓后,又依靠连续充气搅拌得到气力均化,然后从均化仓卸出。
均化仓带传感器,根据传感器信号调节出库卸料系统中电动流量控制阀开度。
均化仓均化所需空气由罗茨风机(2329)供给,另设一台罗茨风机(2328)作为环形区充气及均化仓充气备用。
出均化仓(2330)的生料经充气螺旋闸门(2331a)、气动流量调节阀(2331b)和空气输送斜槽被送至固体流量计(2344)计量,再经空气输送斜槽(2345)送入窑尾提升机(2401),均化仓(2330)另设一路备用卸料系统(2332),当固体流量计(2344)或正常卸料系统(2331)出故障时,启动备用卸料系统(2332)。
第二,熟料烧成工艺流程简介甲、乙两种原煤由汽车运输进厂,用铲车分别卸入原煤破碎的各自喂料仓中,经各自单层棒条阀门(1701)及定量给料机(1702、1703)配料后卸到皮带输送机(1704)上,经过带式永磁除铁器(1705)排除原煤中的金属异物后,喂入振动筛中。
碎煤直接落入皮带输送机(1801)上,大块煤喂入环锤破碎机(1707)内,经PCH-1010环锤式破碎机破碎后的原煤由带式输送机(1801)送入原煤预均化堆场。
废气经袋收尘器(1708)净化除尘,达到国家排放标准后,由离心风机(1709)排入大气。
原煤预均化堆场对原煤进行预均化和储存。
原煤采用一台侧式悬臂堆料机(1802)堆料,原煤堆成两个料堆,由一台桥式刮板取料机(1803)端面取料,取出的原煤进入带式输送机(1804),送至煤粉制备车间的原煤仓(2701)中。
考虑设备检修等特殊情况,在带式输送机(1804)上设置一钢仓,可用铲车将堆场内原煤铲入,经棒闸(1806)落入带式输送机(1804)送至煤粉制备车间的原煤仓(2701)中。
原煤进料带式输送机(1804) 带面上方设有一台永磁除铁器(1805), 用于排除输送物料中的金属异物以保护煤磨。
碎煤经单层棒闸(2702)、定量给料机(2704)、三道锁风阀(2705),入煤磨(2706)。
通过定量给料机(2704)可以定量地控制入磨煤量。
用于烘干原煤水分的热源来自窑尾废气,经高温风机(2418)、高效旋风收尘器(2212)、高温风机(2215)送入煤磨(2706)。
通过电动蝶阀(2723),将入磨风温控制在~260℃。
碎煤从磨机的中央落煤管落到磨盘上,旋转磨盘借助于离心力将原煤运动至磨盘滚道上,通过磨辊进行碾磨。