Overview of SCM
供应商资料英文

供应商资料英文IntroductionIn this document, you will find a summary of the information and details related to our suppliers. This document aims to provide an overview of the suppliers and their important details in English.Supplier InformationSupplier NameThe supplier name refers to the name of the company or individual that supplies the products or services to our organization.LocationThe location of the supplier is an important detail that identifies the physical address or addresses where the supplier conducts its business operations.Contact InformationThe contact information includes various details through which we can get in touch with the supplier. This typically includes the following:•Phone number: The telephone number that can be used to contact the supplier.•Email address: The email address of the supplier for communication purposes.•Website: The website of the supplier, if applicable.Products/Services ProvidedThis section provides an overview of the products or services offered by the supplier. It includes the following information:•Products: A list of the products supplied by the supplier, along with their brief descriptions.•Services: If the supplier offers services, a description of the services provided.Quality Control MeasuresThis section outlines the quality control measures implemented by the supplier to ensure the products or services meet the required standards. It includes information such as:•Certifications: Any relevant certifications or standards that the supplier adheres to.•Inspection Procedures: Details of the inspection procedures followed by the supplier to ensure the quality of the products or services.•Quality Testing: Information on any specific quality testing processes carried out by the supplier.Pricing and Payment TermsThis section provides details on the pricing and payment terms agreed upon with the supplier. It includes information such as:•Pricing Structure: An overview of the pricing structure followed by the supplier, including any discounts or bulk pricing options available.•Payment Terms: The agreed-upon terms and conditions related to payment, such as payment methods, due dates, and any late payment penalties.Delivery TermsThe delivery terms refer to the conditions under which the products or services are delivered by the supplier. This section includes information such as: •Shipping Methods: The methods used for shipping the products, including any specific shipping providers or options available.•Delivery Timeframe: The estimated timeframe for the delivery of the products or services.•Return Policy: Information on the supplier’s policy regarding product returns or exchanges.Supplier Performance EvaluationThis section provides details on the evaluation of the supplier’s performance based on various parameters. It includes information such as:•On-Time Delivery: Evaluation of the supplier’s ability to deliver products or services on time.•Quality of Products/Services: Assessment of the quality of the supplied products or services.•Communi cation and Responsiveness: Evaluation of the supplier’s communication and responsiveness.ConclusionThis document serves as a comprehensive summary of the supplier information in English. It covers various aspects such as supplier details, products/services offered, quality control measures, pricing/payment terms, delivery terms, and supplier performance evaluation. By having this information documented, we can effectively manage our relationship with suppliers and ensure the smooth operation of our business.。
scm供应链管理-供应链管理Chap1 精品

– Raw materials manufacturers – Intermediate products manufacturers – End product manufacturers – Wholesalers and distributors and – Retailers
The total integration of the overall business process creates value
Table 1.1 Integrative Management Value Proposition
Question
• P20 • 2. Compare and contrast economic, market, and
• Consumer Customizer: Using mass customization to build and maintain close relationships with end-consumers through direct sales. • Logistics Optimizer: Emphasizing a balance of supply chain efficiency and effectiveness. • Trade Focused: Prioritizing "low price, best value" for the consumer (as with the logistics optimizer strategy but focusing less on brand than on dedicated service to trade customers).
SCM 供应链管理
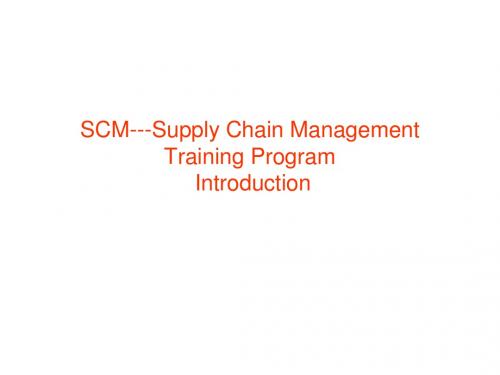
1. Introduction
Definition
Supply Chain is: – A sequence of suppliers that contribute to the creation and delivery of a good or service to end customers.
1. Introduction
Strategic SCM Activities
– – – – – – – Forecasting demand Selecting suppliers Ordering material Managing inventory Scheduling production Shipping and delivery Organizing information exchange
Direct Data Flow: Messaging is the direct exchange of data directly ―system to system‖, bypassing manual data entry to go directly to ESD systems and data stores
Inventory level
1. Introduction
Logistics Process
1. Accepting a customer order – receive and enter – credit clearance / authorize – delivery commitment 2. Supplier ordering 3. Forecasting demand 4. Scheduling manufacturing 5. Inventory management 6. Delivery to customer
scm供应链管理-DS供应链管理 精品

All partners have real time information about status and performance of each element in the supply chain from customers to suppliers.
• Optimization
• Collaborative Supply Planning CSUP • Collaborative Production Planning • Capable to Promise CTP • e-Procurement (auctioning, bidding) • Internet-based Tendering • Internet-based Kanban • e-Fulfillment
Material/Service Supplier Integration
• Fusion • Financial Linkage • Strategic Alignment • Operational Supplier Relationship Management
High Achievers:
10:00 - 11:00 - e-Procurement Overview
11:00 - 11:15 -
Break
11:15 - 12:00 - c-Manufacturing
12:00 - 1:00 -
Lunch
1:00 - 2:30 - Workshop
2:30 - 3:00 - Implementation Considerations, Case Studies
– Develop interlocking programs and activities – Commit to shared responsibility with suppliers – Place employees at customer/supplier business facilities – Enter into long-term agreements – Include suppliers’ suppliers in planning
SAP SCM教程:供应链管理模块说明书
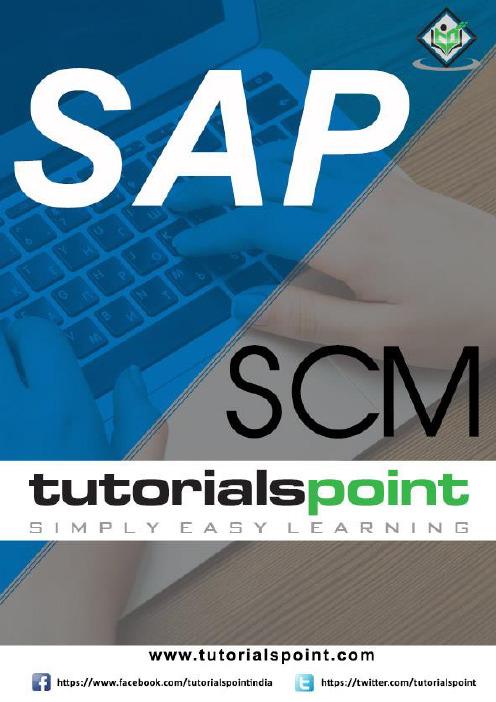
About the T utorialSAP Supply Chain Management is one of the key modules in SAP ERP and controls Production Planning, business forecasting and demand planning. It helps the organization to manage their supply chain process in a dynamic environment. SAP SCM is a complete software to cover key processes such as supply chain networking, supply chain planning and coordination, and supply chain execution.AudienceThis tutorial is meant for Project leaders, project team members, SAP consultants, sales consultant, and those related to the departments of planning and material management. PrerequisitesBefore you start proceeding with this tutorial, we are assuming you have familiarity, prior experience, and knowledge of the domain of supply chain management. However, it is sufficient if you are aware of the basics of computer applications and SAP tools. Copyright & DisclaimerCopyright 2018 by Tutorials Point (I) Pvt. Ltd.All the content and graphics published in this e-book are the property of Tutorials Point (I) Pvt. Ltd. The user of this e-book is prohibited to reuse, retain, copy, distribute, or republish any contents or a part of contents of this e-book in any manner without written consent of the publisher.We strive to update the contents of our website and tutorials as timely and as precisely as possible, however, the contents may contain inaccuracies or errors. Tutorials Point (I) Pvt. Ltd. provides no guarantee regarding the accuracy, timeliness or completeness of our website or its contents including this tutorial. If you discover any errors on our website or inthistutorial,******************************************T able of ContentsAbout the Tutorial (i)Audience (i)Prerequisites (i)Copyright & Disclaimer (i)Table of Contents (ii)1.SAP SCM – Overview (1)2.SAP SCM – Components (2)3.SAP SCM – Benefits (4)4.SAP SCM – Demand Management (5)Planning Strategies (5)5.SAP SCM – Creating PIR (7)Change and Delete PIR (8)6.SAP SCM – Material Requirement Planning (10)MRP Parameters (10)Running MRP for all Products (11)MRP Evaluation – Stock / Requirement List (15)SAP PP – MRP List (16)7.SAP SCM – Planned Order Creation (17)8.SAP SCM – Production Order Creation (22)9.SAP SCM – Goods Issue (25)Goods Issue Reversal (26)10.SAP SCM – Production Order Confirmation (28)11.SAP SCM – Production Order Cancellation (30)12.SAP SCM – Integration (31)13.SAP SCM – Integration Models (32)Activation and Deactivation of Integration Model (34)14.SAP SCM – Master Data (37)Bills of Material (BOM) (37)Material Master (38)Work Center (39)Routing (40)15.SAP SCM – Resources (42)Resource Types (42)Create and Change Resources (43)16.SAP SCM – Production Data Structures (44)Production Data Structure in SAP APO (45)Production Data Structure in ERP (46)17.SAP SCM – Transfer Changed Master Data (49)18.SAP SCM – Transfer Changed BOMs (51)19.SAP SCM – Model and Versions (53)Creating Model (54)Delete Model/Planning Version (57)20.SAP SCM – Applications (60)21.SAP SCM – Advanced Planning and Optimization APO (61)Supply Chain Monitoring (61)22.SAP SCM – Extended Warehouse (63)Communication Method (63)SAP EWM – Menu Structure (64)23.SAP SCM – Transportation Management (67)Custom Settings in APO (69)24.SAP SCM – Supply Network Collaboration (71)25.SAP SCM – Forecasting & Replenishment (73)SAP F&R Administration (73)26.SAP SCM – Consultant Responsibilities (75)1.SAP SCMSAP Supply Chain Management is one of the key modules in SAP ERP and controls Production Planning, business forecasting and demand planning.The key features of SAP SCM are-∙It helps the organization to manage their supply chain process in a dynamic environment.∙SAP SCM process helps suppliers, customers, manufacturers, business partners and retailers connect with each other to manage supply chain process effectively and efficiently.∙It helps organizations to accelerate and optimize end-to-end procure-to-pay process.∙SCM products from SAP allows an organization to integrate their processes and enforce contract compliance for supply-side and supplier-side requirements throughout using supply chain processes in distributed environment.∙SAP SCM is a complete software to cover the key processes- Supply Chain networking, supply chain planning and coordination, and supply chain execution.∙It includes different planning applications related to Advanced Planning and Optimization APO, and for the integration with other SAP execution applications.∙The primary applications are SAP General Areas, SAP Supply Network Collaboration SNC, SAP Extended Warehouse Management EWM, Advanced Planning and Optimization (APO), Forecasting and Replenishment FRE and SAP Transportation Management TM.In the image shown below, you can see SAP Supply Chain Management and its integration with other R/3 modules to manage supply chain process.2.SAP SCMSAP Supply Chain Management allows organizations to perform effective planning and execution of logistics within supply network and to perform workflow management.You can see the key steps in managing Supply network in an organization. Each step consists of defined set of activities and hence helping customers, suppliers, and retailers connect with each other to provide an effective supply-chain-management solution.SAP SCM consists of the following components-∙SC Collaboration: This is used to help in making collaborative forecasts and agreements.∙SC Planning: This is used to generate the operational plans as per current and relevant data in the system.∙SC coordination: This component in Supply Chain is used to coordinate the exchange of data and information between different business units.∙SC Execution: This is used to ensure that you execute the supply chain plans in the best possible manner to get the desired result.As per functionality, you can divide SCM/APO into three parts-∙Forecasting: To perform demand planning and forecasting, you can link to Customer Relationship Management CRM to get data related to customer campaigns, etc.∙Supply Network Planning (SNP): To view organization as a network of locations and to check stock projections and stock keeping criteria. Calculations in SNP drive dependent requirements down to supplying locations production and receiving stores.∙Production Planning and Detailed Scheduling: This is to check the dependent requirements from locations within the supply network, passed down from SNP.SAP SCM This is linked with Material Requirement Planning (MRP) in Production Planning, which determines the inbound material required to complete a production order.3.SAP SCMUsing Supply Chain Management in SAP, an organization can achieve the following benefits in a distributed environment-∙Reduce accounts receivable collections with better visibility into the AR process, aging, and extension of credit and consequently, help to reduce the day’s sales outstanding.∙Effectively manage forecasting and handling sudden changes in demand and supply process.∙Effectively use Net Fixed assets NFA like plants and equipment.∙To meet customer demands, you can smartly plan and manage Supply Chain Management process in an organization.∙Proper inventory optimization, order fulfillment, and shipping of the goods.∙Distribution of the key information to all the stakeholders spread across the network.∙Improve communication and collaboration between different business lines to manage demand and supply process in an organization.∙Improve production efficiency and reduction in production quality issues and hence reduce cost of goods sold.∙To reduce transportation duties and taxes, and increase rebates and incentives. It also helps to reduce transportation errors.4.SAP SCMDemand management is used to forecast, manage, and plan the demands of goods and has defined set of processes and capabilities to produce goods.The key features of Demand Management are-∙This component is used to improve the demand planning by utilizing promotions.∙Based on historical sales data, you can handle demand for every store, product from different customers and hence you can see customer responses as per change in pricing policies, and profit for a particular product in the organization.∙You use demand models to predict consumers’ reaction with price change. As per organization goals like- increase profit, revenue, etc. you can define selling strategies for the products.In SAP PP system, demand management is performed by Planned Independent requirement PIR. Planned Independent Requirement provides input for production planning. A PIR contains one planned quantity of product and one date for material or a Planned quantity is split over a span of time period.To set your PIR version active use value 00 to specify requirement would be considered in material requirement planning. To maintain number of versions of planned independent requirement, you can set some numbers to active and others to inactive.PIRs define the planning strategy in material master, which determines planning methods- make to order and make to stock.In Make-to-Stock environment, PIRs are used where stock is built based on the forecast and not on sales order.Planning StrategiesPlanning strategies are divided into two categories-Make to Stock Planning strategy (MTS)This is planning strategy where stock is produced without sales order. It is used to meet the customer demands in future.When you use Planning strategy 10, only PIR quantity is considered for MRP run and sales order are completely ignored. In this PIR requirement type LSF is reduced when you deliver stock to customer.When you use Planning strategy 40, for MRP run maximum of 2 PIR and Sales order can be considered and PIR is reduced when enter the Sales order. PIR requirement type is VSF in this case.SAP SCMMake to Order Planning strategy (MTO)In this planning strategy, finished products are not produced until you receive sales order from a customer. For MRP run, you only consider Sales order.In MTO strategy, you only produce sales order stock and products are delivered as per sales orders from specific customer.You use Planning strategy 20 for make to order MTO process and planning strategy 25 is used to produce product variants when there is request for variant products from customer.5.SAP SCMIn this chapter, we will learn how to create, change, or delete PIRs.To create PIR, follow the given steps-Step 1: Use T-code MD61 or go to Logistics -> Production -> Production Planning-> Demand Management -> Planned Independent Requirements -> CreateStep 2: In the next window, enter the following details-∙Enter the single material for which demand needs to be created.∙Enter MRP area and Plant Code.∙Enter version as 00, which shows the active version and requirements would be considered in MRP run.∙Enter the Planning horizon dates for which demand needs to be created.∙Enter planning period as month M and click the tick mark given above.Step 3: Enter Version 00. By default, active check box is flagged. It shows it is an active requirement and would be considered in the MRP run. Enter the requirement quantity in monthly buckets.Click the save icon to save the PIR.Change and Delete PIRTo delete a PIR, select the row in above screen and click the Delete button.Step 1: To change PIR, use T-code: MD62 or go to Logistics -> Production -> Production Planning -> Demand Management -> Planned Independent Requirements -> ChangeStep 2: Enter the following details-∙Enter parent material for which PIR needs to be changed.∙Enter Plant Code.∙Enter version as 00.∙Input the planning horizon dates with planning period as month M.In the next window make changes to the requirement quantity and click the Save button to enter the changes.End of ebook previewIf you liked what you saw…Buy it from our store @ https://。
gjb软件配置管理计划范文
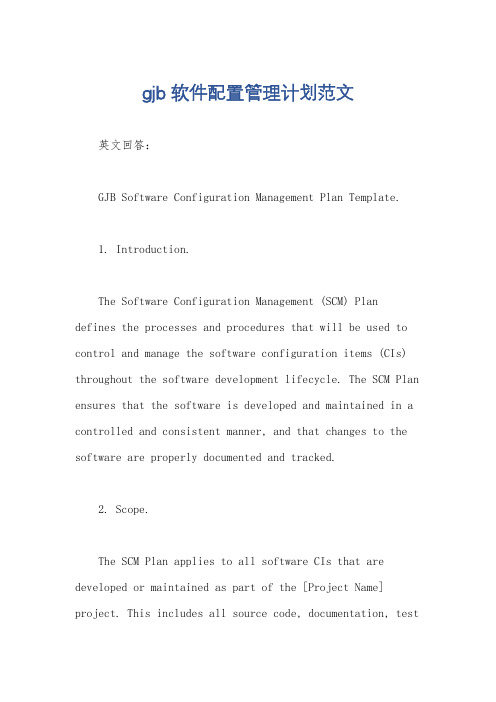
gjb软件配置管理计划范文英文回答:GJB Software Configuration Management Plan Template.1. Introduction.The Software Configuration Management (SCM) Plan defines the processes and procedures that will be used to control and manage the software configuration items (CIs) throughout the software development lifecycle. The SCM Plan ensures that the software is developed and maintained in a controlled and consistent manner, and that changes to the software are properly documented and tracked.2. Scope.The SCM Plan applies to all software CIs that are developed or maintained as part of the [Project Name] project. This includes all source code, documentation, testcases, and other artifacts that are necessary to build, test, and deploy the software.3. Roles and Responsibilities.The following roles and responsibilities are defined in the SCM Plan:Configuration Manager: The Configuration Manager is responsible for overall management of the SCM process.Development Team: The Development Team is responsible for creating and maintaining the software CIs.Testing Team: The Testing Team is responsible for testing the software CIs.Release Team: The Release Team is responsible for releasing the software CIs to production.4. Processes and Procedures.The following processes and procedures are defined in the SCM Plan:Version Control: The software CIs will be stored in a version control system.Change Management: Changes to the software CIs will be managed through a change management process.Release Management: Releases of the software CIs will be managed through a release management process.5. Tools and Techniques.The following tools and techniques will be used to implement the SCM Plan:Version Control Tool: [Tool Name] will be used as the version control tool.Issue Tracking Tool: [Tool Name] will be used as the issue tracking tool.6. Training and Education.The following training and education will be provided to the project team:SCM Overview: All project team members will receive an overview of SCM concepts and processes.Version Control Tool Training: All project team members who will be using the version control tool will receive training on how to use the tool.Change Management Training: All project team members who will be involved in the change management process will receive training on how to use the change management process.7. Audit and Review.The SCM Plan will be audited and reviewed on a regular basis to ensure that it is being followed and that it iseffective.中文回答:GJB软件配置管理计划范文。
scm供应链管理-Philips供应链概况 精品
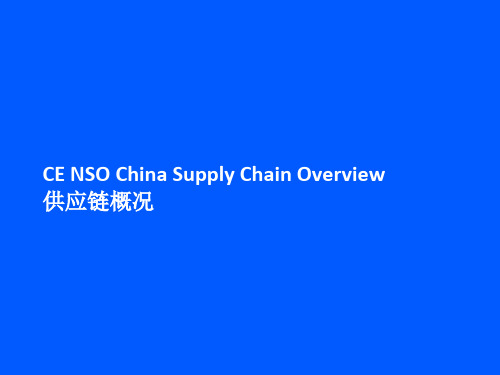
TCL Planning
将完成的滚动三个月销售预测 发到PHILIPS商务部
详细说明:1)飞利浦商务部在每月第一个周五前更新滚动三个月的销售预测格式(见附件),并在第一个周五前将更新的销售预测表格发到TCL计划部 2) TCL在每月月结日前第二个周三将完成的滚动预测发回给飞利浦商务部。(附飞利浦日历)
双方经讨论,确定并调整本月的月供应总量
Last week最后一周
M
T
W
T
F
每天更新日供应量,并于每天上 午10:00前将此通知发到TCL
详细说明:
1)飞利浦供应链管理部计划经理于每月第一个周三将对应TCL的本月各个型号的供货总量发到TCL计划部门;供货总量的确定主要参照TCL的滚动预测, 同时根据TCL最近两个月的销售记录及工厂供货量做调整;
部门:财务部 责任:信用检查及销售发票处理
Division, Content owner, Date(in numbers), ISO No
部门:仓库 职能:进行货物发货处理
部门:运输 职能:负责货物运输
17
PHILIPS &TCL PSI Process
SUPPLY CHAIN MANAGEMENT Jul. 2002
<<=or +/- %
➢ 当前月的产量通常可根据实际需求作调整,但对于当月增加量较大的型号需由 生产部门和采购部门确认是否可行。通常从第二个月起的生产量可按销售计划 调整。
➢ 当前月的产量确定后,商务如需要增产或减产,在工厂检查材料供应状况及平 衡库存水准后给予确认。
➢ 当月生产总量确定后,商务若要求提前某一批次的生产,则必须在要求的生产 日前七个工作日通知生产计划部,在有材料的前提下,工厂可按需求提前生产 。
全球物流及供应链概览 Overview of Global Logistics & SCM
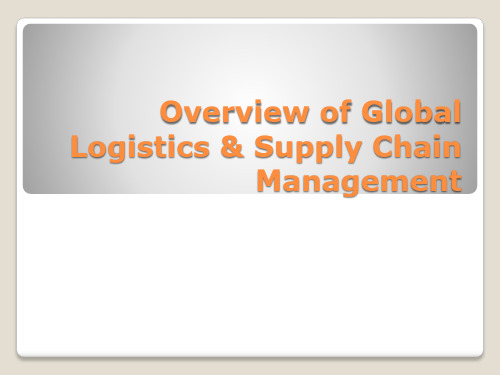
Global Supply Chain
Suppliers
Order processi ng
Corporation
Customers
Order placement
transp ortati on storag e
Materials manageme nt Inventory manution
transportat ion Physical distribution
Storage
Inventory manageme nt
Forward and reverse flows of information, products and funds
Two major areas of Global Logistics are i. Global sourcing and ii. Global distribution
1.
Major concepts in Global Logistics
The activities involved in Supply chain are i. Purchasing ii. Manufacturing iii. Logistics iv. Distribution v. Transportation and vi. Marketing
The International Supply Chain/Global Supply Chain
Supply chain as a cross-functional entity 2. Supply chain as the integrator and coordinator of production and logistics activities
SCM-物流与供应链管理
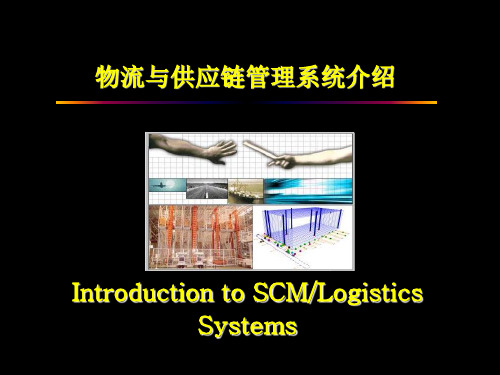
SCM
Integration of key business processes from end user through original suppli ers that provides products, services, and information that add value for cust omers and other stakeholders - global Optimum
Demand Collaboration
Supplier
DesignColla源自oration Collaboration
• Benefit of Collaboration
• Greatly improved demand and supply visibility for both parties
To survive, Enterprises need
to extend processes to
create efficient and effective Values
Why SCM? - Issues
Enterprise Functional Silos with Conflicting Goals
Supply Network Planning
Demand Planning/ Collaborative Planning
Collaborative Production Planning/ Scheduling Detailed Scheduling Deployment
VMI / CPFR Global ATP
SCP SCM SCE
Questionnaire_2011

对咨询的反馈质量 日常工作中的态度与合作 业务操作流程复杂度
Organizational complexity (e.g. if can find right person quickly) 组织复杂度 (是否方便迅速找到正确的联系人) Professional Behavior专业行为方式 专业行为方式 Understanding of Schaeffler business and the market requirements 对舍弗勒业务及市场需求的了解
-
1 1
2. Evaluation on Schaeffler Greater China SCM Service Level
Please rate your satisfaction with our performance in the below areas, as well as these areas' importance to your department: 请评价您对我们在以下方面的表现的满意度,以及这些方面对您的重要性: Importance 对您的重要度 very unimportant 非常不重要 unimportant 不重要 very important 非常重要 very unsatisfied 非常不满意 important 重要 average 中等 Our service level 满意度 unsatisfied 不满意 satisfied 满意 very satisfied 非常满意 0 2 2.1.2 2.1.3 2.1.4 2.1.5 2.2 2.2.1 Problem solving efficency Problem solving effectiveness Complaint handling efficency Complaint handling effectieness 解决问题效率 解决问题效果 投诉处理的效率 投诉处理的效果 0 0
偏向于SCM方面的SAP学习路径

偏向于SCM⽅⾯的SAP学习路径偏向于SCM⽅⾯的SAP学习路径——感谢我的好友、⽼师Ok Daddy ⼀、Solution OverviewSAP01 SAP OverviewSAPTEC Fundamentals of SAP Web AS⼆、SAP Supply Chain Management - ProcurementSAPSCM Overview of the mySAP SCM solutionSCM500 Processes in ProcurementSCM510 Inventory Management and Physical InventorySCM520 PurchasingSCM525 Consumption-Based Planning and ForecastingSCM540 Procurement of ServicesSCM515 Invoice VerificationSCM521 Pricing in Purchasing SAP R/3SCM550 Cross-Functional Customizing in MM三、SAP Supply Chain Management - Planning (Production Planning)SCM100 Business Processes in Planning (SAP ERP)SCM200 Business Processes in Planning (SCM)SCM210 Core Interface APOSCM215 Integrated Master data in SAP SCMSCM240 Production Planning (ERP)SCM220 Demand PlanningSCM250 Production Planning and DetailedScheduling (SAP APO-PP/DS)SCM260 Capacity Planning (APO)SCM240 Production Planning (ERP)SCM230 Supply Network Planning (SNP)SCM360 Capacity Planning (ERP)SCM240 Production Planning (ERP)SCM230 Supply Network Planning (SNP)SCM250 Production Planning and DetailedScheduling (SAP APO-PP/DS)SCM225 Advanced Demand PlanningSCM220 Demand PlanningSCM220 Demand Planning四、SAP Supply Chain Management - Manufacturing (Manufacturing Planning)SCM300 Overview ManufacturingSCM310 Production OrdersSCM130 Planning & Manufacturing OverviewSCM340 Process ManufacturingSCM344 Process ManagementSCM310 Production OrdersSCM320 Repetitive ManufacturingSCM340 Process ManufacturingSCM344 Process ManagementSCM350 Lean Processes using KANBAN五、SAP Supply Chain Management - Order Fulfillment (Sales Order Management) SCM600 Business Processes in Sales Order ManagementSCM601 Processes in Logistics ExecutionSCM620 Pricing in SDSCM605 SalesSCM611 TransportationSCM680 Cross-Application Business ProcessesSCM660 Handling Unit ManagementSCM600 Business Processes in Sales Order ManagementSCM615 BillingSCM650 Cross-Functional Customizing in Sales and DistributionSCM605 SalesSCM645 Credit and Receivables Risk ManagementSCM611 TransportationSCM680 Cross-Application Business ProcessesSCM635 Task Resource ManagementSCM640 Foreign TradeSCM615 BillingSCM650 Cross-Functional Customizing in Sales DistributionSCM620 Pricing in SDSCM610 Delivery ProcessesSCM670 Global Available to PromiseSCM601 Processes in Logistics Execution六、SAP Supply Chain Management - Logistic Execution (Warehouse Management) SCM601 Processes in Logistics ExecutionSCM630 Warehouse ManagementSCM631 Additional Topics in Warehouse ManagementSCM660 Handling Unit Management七、SAP PLM - Life-Cycle Data Management (Life-Cycle Data Management) SAPPLM mySAP PLM Solution OverviewPLM100 Life-Cycle Data Management OverviewPLM130 ClassificationPLM115 Basic Data for Process ManufacturingPLM110 Basic Data Part 1PLM140 Variant Configuration Part 1PLM120 Document Management SystemPLM111 Basic Data Part 2 (Discrete Manufacturing)PLM114 Basic Data for Manufacturing and Product ManagementPLM112 Customizing Basic Data⼋、SAP PLM-Asset Life-Cycle Management - Plant MaintenancePLM300 Plant MaintenancePLM305 Structuring and Managing Technical ObjectsPLM310 Preventive Maintenance and ServicePLM318 Analytics in Enterprise Asset Management九、SAP PLM - Program and Project ManagementPLM200 Project ManagementPLM210 Project Management - StructuresPLM220 Project Management – LogisticsPLM230 Project Management – Network Controlledand Customer-Driven Project AccountingPLM235 Project Management – WBS controlled Project Accounting⼗、SAP Product Lifecycle Management - Quality Management(我的重点QM)PLM400 Business Processes in Quality ManagementPLM405 Quality InspectionsPLM410 Quality NotificationsPLM412 Quality Planning and InspectionPLM415 QM in ProcurementPLM420 QM in Discrete Manufacturing⼗⼀、SAP PLM-Asset Life-Cycle Management - Customer Service PLM301 Customer ServicePLM335 Service Processing⼗⼆、Plant MaintenancePLM300 Business Processes in Plant MaintenancePLM305 Managing Technical ObjectsPLM310 Maintenance and Service Processing: PreventativePLM315 Maintenance Processing: Operational FunctionsPLM335 Service ProcessingPLM316 Maintenance Processing: Controlling and Reporting Functions PLM318 Analytics in Enterprise Asset ManagementPLM301 Customer ServicePLM316 Maintenance Processing: Controlling and Reporting Functions ⼗三、Master Data ManagementMDM100 Master Data Management 5.5 SP04MDM300 MDM 5.5 SP04 Print PublishingMDM400 SAP NW 2004s Data Modeling in MDM。
企业物流与供应链管理英文
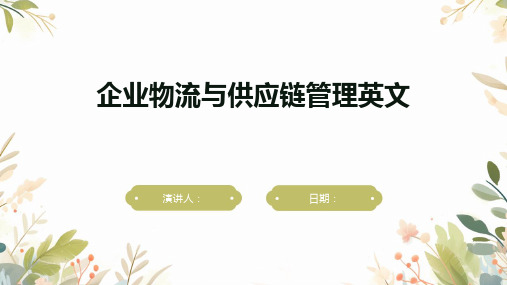
Integration can be achieved through the use of technology, such as enterprise resource planning (ERP) systems, and through collaboration and partnership among supply chain members
Secure packaging of goods to ensure safe delivery, and coordination with transportation providers for timely shipment
03
Returns and Exchanges
Management of customer returns and exchanges, including inspection of returned goods and processing of credit or replacement orders
Inventory Control
Management of stock levels to ensure availability of products while minimizing excess inventory and associated costs
Technology and Automation
Warehouse and Inventory Management
scm供应链管理-Mckency供应链管理 精品

Communication
Measuring progress towards goals through
interactive communication and
education
There is no one “right” answer
This document’s an initial step in the right direction.
• NAPM (US):
Purchasing.
• Kaiser Associates:
Benchmark Specialist Consultant.
• US University Research: New global initiative (investigating entry opportunities—Bob Ackerman).
We used a generic supply chain framework as a basis for our analysis . . .
– High level benchmarking framework for supply chain performance (H .Cook): • Shop Study (March 1997) accessing information from available experts and past projects.
• The Supply Chain CoE’s objective is to define a benchmarking framework capable of:
– Comparing generic metric performances for use on projects. – Capturing further benchmarking data in a consistent format.
供应链管理和高级计划的趋势和综述(英文)
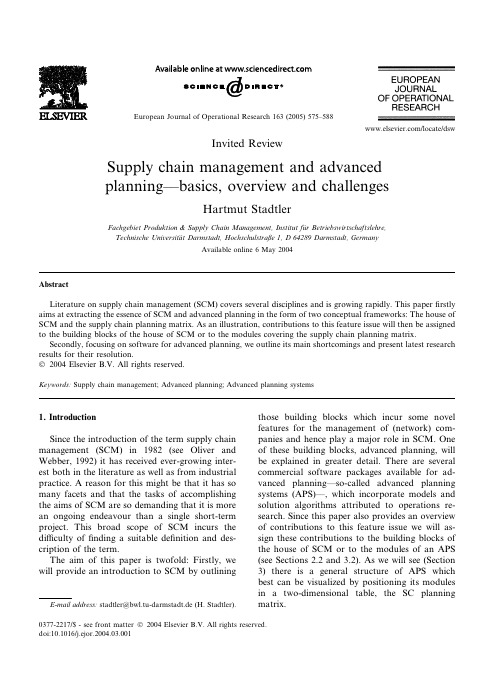
Invited ReviewSupply chain management and advanced planning––basics,overview and challengesHartmut StadtlerFachgebiet Produktion &Supply Chain Management,Institut f €ur Betriebswirtschaftslehre,Technische Universit €a t Darmstadt,Hochschulstraße 1,D 64289Darmstadt,GermanyAvailable online 6May 2004AbstractLiterature on supply chain management (SCM)covers several disciplines and is growing rapidly.This paper firstly aims at extracting the essence of SCM and advanced planning in the form of two conceptual frameworks:The house of SCM and the supply chain planning matrix.As an illustration,contributions to this feature issue will then be assigned to the building blocks of the house of SCM or to the modules covering the supply chain planning matrix.Secondly,focusing on software for advanced planning,we outline its main shortcomings and present latest research results for their resolution.Ó2004Elsevier B.V.All rights reserved.Keywords:Supply chain management;Advanced planning;Advanced planning systems1.IntroductionSince the introduction of the term supply chain management (SCM)in 1982(see Oliver and Webber,1992)it has received ever-growing inter-est both in the literature as well as from industrial practice.A reason for this might be that it has so many facets and that the tasks of accomplishing the aims of SCM are so demanding that it is more an ongoing endeavour than a single short-term project.This broad scope of SCM incurs the difficulty of finding a suitable definition and des-cription of the term.The aim of this paper is twofold:Firstly,we will provide an introduction to SCM by outliningthose building blocks which incur some novelfeatures for the management of (network)com-panies and hence play a major role in SCM.One of these building blocks,advanced planning,will be explained in greater detail.There are several commercial software packages available for ad-vanced planning––so-called advanced planning systems (APS)––,which incorporate models and solution algorithms attributed to operations re-search.Since this paper also provides an overview of contributions to this feature issue we will as-sign these contributions to the building blocks of the house of SCM or to the modules of an APS (see Sections 2.2and 3.2).As we will see (Section 3)there is a general structure of APS which best can be visualized by positioning its modules in a two-dimensional table,the SC planning matrix.E-mail address:stadtler@bwl.tu-darmstadt.de (H.Stadtler).0377-2217/$-see front matter Ó2004Elsevier B.V.All rights reserved.doi:10.1016/j.ejor.2004.03.001European Journal of Operational Research 163(2005)575–588/locate/dswSecondly we are concerned with the future of APS.Therefore,we will highlight deficiencies of APS,which may give rise to future research.Three areas for improvements are proposed:Improve-ments which are possible within the modules of today’s APS,issues which challenge the premises of today’s APS,and last but not least two business functions are identified which should be better integrated with APS.The structure of the paper is as follows.In Section2the term SCM is defined and its building blocks are described.Section3intro-duces the architecture and modules of today’s APS.Issues and challenges of APS are presented in Section4.A few comments conclude this paper (Section5).2.Essence and scope of supply chain management 2.1.The house of supply chain managementFollowing the proposal of Christopher(1998,p.15)a supply chain(SC)‘...is a network of orga-nizations that are involved,through upstream and downstream linkages in the different processes and activities that produce value in the form of prod-ucts and services in the hand of the ultimate con-sumer.’This definition stresses that all the activities along a SC should be designed according to the needs of the customers to be served.Con-sequently,the(ultimate)consumer is at best an integral part of a SC.The main focus is on the order fulfilment process(es)and corresponding material,financial and informationflows.In case the organizational units belong to one single enterprise an intra-organizational SC is gi-ven.Here,hierarchical coordination is possible and prevailing.While hierarchical coordination in globally operating enterprises is already a demanding task,the real challenge arises in an inter-organizational SC where hierarchical coor-dination is no longer possible.Although there is a coherent view of what a SC represents,there are numerous definitions of the term SCM(see Otto and Kotzab,1999).The def-inition proposed here is not totally new but tries to extract the essence of existing proposals:Supply chain management(SCM)is the task of integrat-ing organizational units along a SC and coordi-nating materials,information andfinancialflows in order to fulfil(ultimate)customer demands with the aim of improving competitiveness of the SC as a whole.This definition is best visualized bytheFig.1.House of SCM(Stadtler,2002a,p.10).576H.Stadtler/European Journal of Operational Research163(2005)575–588house of SCM(Fig.1)and will be described in greater detail below.petitiveness and customer serviceThe roof of the house of SCM depicts the ulti-mate aim of SCM,namely improving competi-tiveness of a SC as a whole.This is achieved by directing the SC in a sustainable,strategic position compared to its competitors(this is in line with the ideas of Porter(1998,p.55)for a single company). An important means to achieve this aim is cus-tomer satisfaction(see Christopher(1998,p.35) for a detailed description).Excellent examples of how to focus SC processes on customers are given by two case studies(Berry et al.,1999;Childer-house et al.,2002),which––based on the work of Skinner(1974)––show how to analyse the strengths and weaknesses of a SC in a competitive market.Concentrating on order qualifiers and order winners,a methodology is proposed for market segmentation followed by the re-engineer-ing of a specific order fulfilment process for each market segment.The roof of the house of SCM rests on two pillars,‘integration of organizational units’and ‘coordination offlows’.Of the many facets of SCM we will outline three building blocks in each ‘pillar’,which we believe play an important and innovative role in SCM.2.1.2.Choice of partnersStarting with the integration of organizational units we have to design the SCfirst,i.e.find those partners with the bestfit to the existing SC and the needs of the customers to be served.At the very beginning the SC may consist of a single company taking the initiative.Due to the large efforts necessary to form a working SC usually only a small subset of all companies involved in the creation of a product or service for the ulti-mate consumer form a SC.Obviously geogra-phical aspects will play an important role,the capabilities of potential partners––like product and process know how––as well as thefinancial position to name only a few.Thefit might also be tested in the form of a due diligence(Berens and Strauch,1999).This concept originates from public accounting and being used in mergers and acquisitions extensively advocates a thorough analysis of potential partners along several dimensions.These dimensions comprise the core competencies,trust,culture,strategy,organiza-tional structure andfinancial situation(for a complete checklist see Ries,2001,p.337).In contrast to a‘virtual company’,which is often formed for just fulfilling a single customer order,a SC partnership is created in the medium-term,e.g.the lifetime of a product.This allows greater investments in close partnerships across the SC.The cooperation between partners in a SC should be such that each partner benefits––at least on a medium-term(so-called win–win situation). From afinancial perspective this requires to adapt transfer prices negotiated within the SC and potentially to render compensation to partners, if asked to give up locally optimal decisions in favour of the SC as a whole.2.1.work of organizationsA SC can be regarded as a network of organi-zations with some common goals.The challenge in controlling such a network stems from the nature of relationships between SC partners.They are neither part of a single hierarchy nor loosely cou-pled by market relations.Hence,control mecha-nisms for a hybrid between market and hierarchy are looked for(e.g.Sydow,1999).Also,a SC partnership always runs the risk of either sepa-rating(establishing e.g.market relations,if there are greater opportunities in short-term contracts) or being integrated into a hierarchy as a result of a take over.The latter may occur in case the SC runs the risk of losing a crucial partner.Based on a literature review Spekman et al.(1998)argue that the misfit of goals and strategies are frequent causes for the disintegration of networks(see also Skjøtt-Larsen,1999).A partnership between organizational units rests on daily decisions by employees and man-agement.Although this statement is easy to make it is rather difficult to accomplish,considering that partners formerly may have experienced market relationships with information hiding,mistrust and perhaps even cheating.This is where the social sciences come into play, e.g.by analyzing how bonds can be created between interactingH.Stadtler/European Journal of Operational Research163(2005)575–588577employees.These can be social,administrative or legal bonds to name only a few(see H akansson and Johanson,1990).2.1.4.LeadershipThe third building block concerns leadership within the SC.We only point out two extremes in the following,namely,focal and polycentric SCs (Wildemann,1997).A focal SC is characterized by the presence of a partner who is the‘natural’lea-der,e.g.due to hisfinancial power or exceptional knowledge of products and processes.Leadership then is similar to a hierarchy even if SC partners are legally separated(e.g.in the European auto-motive industry).In the other extreme,a poly-centric network,all partners are regarded equal (e.g.in consumer goods manufacturing and retailing).Here,a steering committee might be appropriate for aligning decisions of partners,e.g. stipulating transfer prices and compensations.The steering committee might also have access to a SC-wide data and make use of SC-wide planning models(e.g.master planning),which are discussed in the following.In practice often intermediate states of leadership between the two extremes will prevail.rmation and communication technologyBuilding blocks enabling improved coordina-tion of material,information andfinancialflows across the SC represent the second pillar of the house of SCM.New opportunities of today’s information and communication technology enable information exchange between partners within instants by means of the Internet and related services.Thus, sales data,forecasts,orders and any kind of mes-sages can be exchanged across the SC immediately at low costs.Since information transmission con-stitutes a part of an order’s lead-time,its reduction may also restrain the bullwhip effect(Lee et al., 1997).Furthermore,one has to mention the availability of Data Warehouses,which enable decision makers anywhere in the SC to store and retrieve historical mass data at a level of detail and in dimensions(e.g.time interval,geographical re-gion and product type)most suitable for decision making.2.1.6.Process orientationProcess orientation,the second building block of the coordination pillar,not only aims at tearing down barriers between business functions in order to accelerate the execution of processes and asso-ciated activities but also between organizations.In contrast to the original work of Hammer and Champy(1993)who propose a radical redesign of processes for gaining competitive advantage, incremental improvements are also looked for in SCs.Nonetheless,one should not stop with linking existing activities more effectively but also consider a redesign of processes,by eliminating duplicate or unnecessary activities.As Hammer(2001,p.84) puts it‘streamlining cross-company processes is the next great frontier for reducing costs,enhanc-ing quality,and speeding operations.’2.1.7.Advanced planningIt is well-known that the strength of transac-tional enterprise resource planning(ERP)systems is not in the area of planning.Hence,APS have been developed tofill this gap.APS are based on the principles of hierarchical planning(Anthony, 1965;Hax and Meal,1975)and make extensive use of solution approaches known as mathematical programming and meta-heuristics.More details about APS will be given in the next section.In summary SCM is not a novel management paradigm as such.Instead it represents a new focus on how to link organizational units to best serve customer needs and to improve the competitive-ness of a SC as a whole.In this endeavour SCM has drawn knowledge and approaches from a number of disciplines like computer science, logistics,marketing,operations research,organi-zational theory and many more.To extract,adapt and combine those approaches which best suit a specific SC is the challenge of managing a SC successfully(Simchi-Levi et al.,2003).The importance of the building blocks of SCM presented above is supported by empirical studies, pointing out that these represent major success factors in today’s business(e.g.Fawcett and Myers,2001;Pfohl and Mayer,1999;Ramdas and Spekman,2000).The only exception is‘advanced planning’which has not been addressed in the empirical studies.Instead the role of its predeces-578H.Stadtler/European Journal of Operational Research163(2005)575–588sor––enterprise resource planning(ERP)––has been investigated.Next,we will assign the contributions of this feature issue to the house of SCM wherever pos-sible.2.2.Assigning contributions of this feature issueto the house of SCMIt has been argued that customer service has several dimensions.Traditionally,inventory the-ory considers one dimension,namely performance measures related to the customer demand that can be fulfilled instantaneously(from stock).Accord-ingly,Nielsen and Larsen(2005)deal with joint replenishments of several retailers from a single warehouse analytically by means of a Q(s,S)pol-icy.They show that the Q(s,S)policy is at least as good as other policies proposed for this decision problem.Service considerations also play an important role in a spare part distribution network including repair shops where a target system availability has to be achieved.Here,Sleptchenko et al.(2005)extend the well-known VAR-MET-RIC method.The structure of SCs as well as decision prob-lems in specific lines of business are addressed by Persson and G€o the-Lundgren(2005)(oil industry) as well as Carlsson and R€o nnqvist(2005)(forest industry).Inter-organizational collaboration is the con-cern of two papers:Dudek and Stadtler(2005)devise a negotiation scheme for aligning master plans between a buyer and a supplier based on the assumption of a fair exchange of(order)infor-mation without cheating.Corbett et al.(2005) analyse purchase contracts for indirect materials in a situation of double moral hazard and propose an incentive scheme(shared savings)that lead to a greater efficiency for the SC(buyer and seller)as a whole.While traditional SCM focuses on the order fulfilment process in primary markets the paper by Robotis et al.(2005)extends it to remanufacturing and secondary markets(e.g.for used mobile phones).They address issues like the cut-offqual-ity level of a product to be remanufactured instead of being disposed.In the following we will further explore one building block,advanced planning.Contributions to this building block are indicated in Section3.2.3.Architecture of APS3.1.The supply chain planning matrixAlthough developed independently by different software vendors APS exhibit a common architec-ture based on the principles of hierarchical plan-ning.The main focus is on supporting the material flow across a supply chain and related business functions:procurement,production,transport and distribution as well as sales(see Fig.2,x-axis). Fig.2.Software modules covering the SC planning matrix(Meyr et al.,2002,p.99).H.Stadtler/European Journal of Operational Research163(2005)575–588579The associated planning tasks can be considered at different levels of aggregation and planning inter-vals ranging from‘aggregated long-term’to‘de-tailed short-term’planning(see Fig.2,y-axis). These two axes form the SC planning matrix.Its contents are planning tasks,which also correspond to software modules constituting an APS.These planning tasks and associated function-ality of software modules will now be described briefly.3.1.1.Demand planningSince SCM is driven by demand,the starting point of planning are available and planned cus-tomer orders.The longer the planning horizon the greater the portion of forecasted demand.Apart from well-known methods for univariate time series––like Winters exponential smoothing for seasonal and trend demand(Silver et al.,1998)––there are also multivariate methods and life cycle models.The step from pure demand forecasting to demand planning is made by adding to the formal demand forecasts those exceptional influences ex-pected to happen in the future and their impact on sales.These events may either be controlled by members of the SC itself(like promotions)or to be subject to competitor actions(like the introduction of a new product)or by neutral parties(like a football world cup).Expected demands are input to several modules in various aggregations and forecast intervals.3.1.2.Strategic network planningA planning interval of several years can be as-sumed when designing the structure of a SC.Here the location of production sites,warehouses,geo-graphical customer areas to serve are laid out. Also,the capacity of these facilities as well as the transportation means(ships,trucks,railway,etc.) to use are decided upon.3.1.3.Master planningGiven the structure of the SC,master planning looks for the most efficient way to fulfil demand forecasts over a medium-term planning interval, which often covers a full seasonal cycle.Master planning not only balances demand forecasts with available capacities but also assigns demands (production amounts)to sites in order to avoid bottlenecks.Due to the medium-term planning horizon it is often possible to adjust available capacities to a certain extent(e.g.by overtime).As regards procurement,some purchased items may become a bottleneck too,which then have to be considered as a restriction to master planning. However,in the majority of cases,the amounts to be procured can be derived ex-post from master planning and may result in special arrangements with suppliers(e.g.standing orders).Whether lot-sizing has to be incorporated explicitly into master planning largely depends on the relation of an item’s expected time between orders(TBO)and the length of a period in master planning.If the TBO is larger than a period,lot-sizing has to be taken into account,because otherwise the time between lot-size productions(orders)of an item proposed by master planning may be reduced to a single period.3.1.4.Production planning and detailed schedulingWhile master planning coordinatesflows be-tween sites,production planning and detailed scheduling is run within each site,or even each production department based upon directives of master planning.In production planning the level of detail are shifts,machine groups orflow lines which may become a bottleneck and operations to be performed on these potential bottlenecks.In case the loading of machine groups––including lot-size decisions––is strongly affected by the sequence of jobs both production planning and detailed scheduling should be performed simultaneously (which often applies to the process industry).3.1.5.Purchasing and material requirements planningMaster planning as well as short-term produc-tion planning and detailed scheduling provide directives for calculating procurement quantities to be planned within the module purchasing and material requirements planning.After disaggre-gating product types or product families into items a bill of materials(BOM)explosion is applied to derive required quantities of procured items.Furthermore,this module is needed in the short term for planning of non-bottleneck oper-580H.Stadtler/European Journal of Operational Research163(2005)575–588ations because only potential bottleneck opera-tions are planned for in production planning and detailed scheduling.In order tofind out which operations have to be performed at which points in time also a simple BOM explosion is executed. Here,planned production amounts of potential bottleneck operations arefixed and build the starting point of the BOM explosion.Capacity considerations may be omitted by definition of a non-bottleneck operation.Hence,a given lead-time offset should suffice.3.1.6.Distribution planningSo far we have mainly concentrated on pro-duction operations.Now theflow of goods be-tween sites as well as in the distribution network comes into play.Seasonal stock levels at different stocking points in the SC have already been planned for in master planning.Here,we have to take care of transports of goods to customers (directly)as well as via warehouses and cross docking.This now happens at a greater detail than in master planning.In case production amounts do not exactly match a current period’s demand,rules and procedures are applied to guide theflow of goods within the SC(e.g.in the case of scarcity transport of goods will be such that target inventories of an item at different distribution centres arefilled at an equal per-centage).3.1.7.Transport planningBased on production orders to be completed the next day(or shift)truckloads for different desti-nations have to be formed(so-called vehicle loading).This also requires detailed knowledge of outstanding orders from warehouses and custom-ers.Also,the specific needs of customers(like time windows for delivery)and legal restriction for drivers have to be obeyed.Sequencing customer locations on a vehicle’s trip is accomplished in (models of)vehicle routing.However,there is a trend in Europe towards utilizing a third party logistics provider(3PL)for transportation.Often a 3PL can consolidate orders from different SCs, thus the above planning tasks are executed by the 3PL himself with the help of special purpose software.3.1.8.Demand fulfilment and available-to-promiseLast but not least there is the interface to the customers via the demand fulfilment and avail-able-to-promise module.One task is to track cus-tomer orders from order entry,via order execution to order delivery.Furthermore,order promising, due date setting and shortage planning are con-sidered here.Order promising starts with matching available inventory and expected supplies––as known from master planning––with already committed cus-tomer orders.Remaining quantities are the available-to-promise(ATP)quantities which can be used for promising due dates for(new) incoming orders.If ATP quantities are insuffi-cient,orders can be promised on the basis of capable-to-promise(CTP)quantities,indicating the slack capacity remaining after matching available capacity with already committed cus-tomer orders.In case of unforeseen events,like a breakdown of machines,shortage planning comes into play,specifying which(committed) customer orders will not be served in time.Only simple rules are implemented in standard soft-ware so far(Fischer,2001;Kilger and Schnee-weiss,2002).It should be noted that despite the general description,software vendors also offer additional modules for the specific needs of industrial sectors, like a car sequencing module to be used for con-trollingfinal assembly lines in the automobile industry.Advanced planning is not an isolated building block of SCM;instead it should be used for deci-sion support within other building blocks:e.g.the choice of partners in different geographical regions can be evaluated by strategic network planning. Different proposals from partners for the best utilization of available resources within the SC can be compared as alternative master plans and contrasted with globally optimal plans.These master plans may be generated for discussions in a steering committee(see leadership building block). Hence,there should be no surprise,that some contributions to this feature issue will be listed both in Section 2.2and in the next subsection where we assign them to the modules covering the SC planning matrix.H.Stadtler/European Journal of Operational Research163(2005)575–5885813.2.Assigning contributions of this feature issueto the SC planning matrixSpitter et al.(2005)present a novel approach for modelling lead times within master planning, where an operation can be executed at any time within itsfixed lead time offset.This greaterflexi-bility can lead to a much better utilization of re-sources(machines).Dudek and Stadtler(2005) consider an inter-organizational SC where master planning is performed decentrally.A negotiation-based procedure is presented for one buyer and one supplier,which results in a near optimal master plan for the SC as a whole.The joint replenishment inventory control pol-icy analysed by Nielsen and Larsen(2005)can be attributed to a central purchasing function. Dellaert and Jeunet(2005)demonstrate how stockout situations may arise in a deterministic, multi-level,rolling schedule environment and de-vise a procedure to overcome this problem(see material requirements planning).Some researchers consider specific SCs,which are not adequately represented in the general architecture of today’s APS.The paper of Arbib and Marinelli(2005)is concerned with a line of business where cutting operations are a key issue.A hierarchical production planning system is proposed covering master planning and produc-tion planning and detailed scheduling.The inte-gration of production scheduling and shipment planning at oil refineries is the concern of Persson and G€o the-Lundgren(2005).Here,a column generation approach is used for solving the resul-tant model.4.The future of advanced planning––issues and challengesIn the following we would like to point out some drawbacks and deficiencies of today’s APS and indicate research results and opportunities for their resolution.The issues and challenges of today’s APS will be discussed in three main categories.Firstly, research results are available as well as imple-mentations are under way for improving modules of an APS.The aim is to achieve an even betterfit between modules,planning tasks and decision making.Secondly,one may challenge the premises of today’s APS,like bucket oriented planning,the consideration of uncertainty by rolling planning and(single-stage)safety stocks or even the appli-cability of the principles of hierarchical planning for an inter-organizational SC.Thirdly,today’s APS are recommended for the seamless integration of business functions.We will argue that there are still missing links between APS and real-time control of the shopfloor as well as cost accounting systems.4.1.ModulesWe will start the discussion by looking at ways to improve existing APS modules4.1.1.Demand planningAccurate demand forecasts are an important input to decision models used in APS.Forecast errors are directly related to required safety stocks, while frequent adjustments of demand forecasts can lead to dramatic changes in plans(i.e.ner-vousness).Hence,great emphasis has to be put on choosing correct forecasting models.So far sophisticated models are very rare in demand planning.For example consider the behaviour of customers responding to price promotions.Here, the impact of varying sales prices between pack-ages of the same good has to be taken into account when estimating sales(Huchzermeier et al.,2002).4.1.2.Master planningMaster planning has to coordinate activities and processes along a SC and thus has to capture decisions in procurement,transport,production and distribution adequately.The integration of transport and production decisions within SCs has been the concern of several papers(e.g.Simpson and Ereng€u c,2001;Z€a pfel and Wasner,2000; Haehling von Lanzenauer and Pilz-Glombik, 2000).However,these proposals lead to an in-creased complexity due to additional integer vari-ables for discrete transport amounts.So far master planning has been devised largely for make-and assemble-to-stock industries while582H.Stadtler/European Journal of Operational Research163(2005)575–588。
SCM-物流与供应链管理

Why SCM? - Issues
• Customer’s Uncertainty
• Information Distortion • Propagated Uncertainty
• Supplier’s Uncertainty
• Delivery, MFG Lead Time • Quality, Transportation, Labor Unions
Collaboration has extending to c-Commerce
Visibility
.com Begins Internet Web
e-Commerce Peaks
Publicized E-Failures
Business Disillusionment
Demand
Demand Collaboration
AGENDA
PART I. SCM Introduction
Definition of SCM & Logistics SCM Processes Why SCM? SCM Trends SCM Architecture SCM Strategy Value of SCM
Retailer
• Simple Network • Dependency Relationship • Vertical & Sequential
Supplie r
Supplie r
MFG
MFG
Distributo
Retaile
r
r
•
Distributo r
Retailer
• Customer •
by Council of Logistics Management
- 1、下载文档前请自行甄别文档内容的完整性,平台不提供额外的编辑、内容补充、找答案等附加服务。
- 2、"仅部分预览"的文档,不可在线预览部分如存在完整性等问题,可反馈申请退款(可完整预览的文档不适用该条件!)。
- 3、如文档侵犯您的权益,请联系客服反馈,我们会尽快为您处理(人工客服工作时间:9:00-18:30)。
Supply Chain Management – (C: Ordering)
Two business processes in a company
A cross company supply chain process
A cross company supply chain process
Two forecasts are generated independently and then compared A difference engine highlights where forecasts differ beyond a given tolerance Trading partners work together to resolve exceptions and agree on a single number
From traditional company towards supply chain management
A traditionally organized company
Different objectives in different departments
Marketing High service levels Short lead times Big order quantities Long lead times Small inventories
Source: Bowersox, D. Et al.; 21st century logistics: Market supply chain integration a reality, Council of logistics management.
Supply chain management in practice
CustomerCustomer-managed ordering
Customer enters order in suppliers system
The customer has access to and can enter orders directly into the suppliers order entry system. Entered orders are checked by the supplier and acknowledged.
Supply chain management
“Supply chain management is a collaborativecollaborativebased strategy to link-organizational business linkoperations to achieve a shared market opportunity” opportunity”
Getting a shared forecast: Reference forecast process
One single reference forecast is generated in the customers system The supplier has visibility and rights to comment and demand updates on the forecast Trading partners work out and analyses exceptions based on the reference forecast, e.g. forecast Vs actual
Manufacturing
Finance
Different forecasts in different departments
Traditional focus when improving operation efficiency
Each company optimize their own internal management based on the boundary of financial relation Regard related company such as suppliers & retailers as opponent
Increased number of transactions due to outsourcing
Supply Chain Management – (A: Concept)
A supply chain network
The supply chain management concept
Basic supply chain
Three entities Supplier Producer Retailer
Basic supply chain
Four flows Physical materials and services Cash Information Reverse flow for repair, recycling or disposal
Parallel communication
Unidirectional dialogue
To a more bidirectional dialogue
Different forecasts in various companies
Getting a shared forecasts: dual forecast process
An enable strategy
Integration through customer managed ordering
CustomerCustomer-managed ordering
Customer enters order in own system
The customer enters orders in his own system. The orders are transferred to the suppliers system by EDI and automatically loaded as requested orders. Entered orders are checked by the supplier and acknowledged.
CustomerCustomer-managed ordering
Customer finalizes order in suppliers system
The customer has access to and can enter orders directly into the suppliers order entry system. Entered orders are finalized by the customer and not acknowledged by the supplier.
A new focus when improving efficiency
Optimize the whole supply chain to reduce the cost, smooth the demand and supply Regard related company such as suppliers & retailers as stakeholder
Driving forces towards supply chain management
Increasing supplier value adding
Towards value creation in networks of companies
Driving forces towards supply chain management
Inventories when implementing JIT-deliveries JIT-
Inventories when implementing JIT-deliveries JIT-
Solving my own problem type of attitudes
Survey of manufacturing companies in the US: “Does JIT imply a shift in inventory from customer to supplier” supplier” 100% of the respondents answered yes Source: Bartholomew, D. The vendor-customer relationship today. Production and vendorInventory Management, 2nd Qtr, 1994. Survey of European suppliers in the automotive industry: “JIT only transfers inventory from customer to suppliers” suppliers” 49% of the respondents agreed to this statement Source: Mclvor, R. _ Humphreys, P._ McAleer, W. European car makers and their suppliers, European business review, No 2, page 87-99, 1998. 87“If you are smart enough to transfer ownership to your vendors, your raw materials and WIP inventory comes off your balance sheet” sheet” Ron Barris, Global leader of supply chain management, Ernst & Young Source: Emigh, J. Vendor-managed inventory, Computerworld, August 1999. Vendor-