dcs和sis工作原理
DCS工作原理及组成

DCS工作原理及组成DCS(Distributed Control System)是分布式控制系统的缩写,是一种用于工业过程控制的自动化系统。
DCS系统通过将多个控制单元分布在不同的物理位置,通过网络进行通信,从而实现对工业过程的监控、控制和优化。
下面将对DCS的工作原理及组成进行详细介绍。
一、DCS的工作原理DCS系统由多个控制单元组成,这些控制单元分布在不同的物理位置,通过网络进行连接和通信。
每个控制单元都有自己的CPU、内存、输入输出接口等硬件设备,同时还包括控制算法、执行逻辑等软件。
DCS系统的工作过程可以分为三个阶段:数据采集、数据处理和控制执行。
在数据采集阶段,DCS系统通过传感器、仪表等设备采集工业过程的各项参数和信号,并将这些数据传输给控制单元。
在数据处理阶段,控制单元会根据预设的控制算法和逻辑进行数据处理和分析,生成相应的控制指令。
最后,在控制执行阶段,控制单元将生成的控制指令发送给执行器、调节器等设备,通过改变设备的工作状态来实现对工业过程的控制。
DCS系统的工作原理基于分布式控制的概念,即将控制功能和硬件设备进行分散化处理,每个控制单元负责一部分控制任务,并通过网络进行协作和通信。
这种分布式的架构使得DCS系统能够适应复杂的控制任务和多变的工业环境,具有较高的可靠性和灵活性。
二、DCS的组成DCS系统由多个组件组成,包括硬件设备、软件系统和人机界面等。
下面将对DCS系统的主要组成部分进行介绍。
1.控制单元:DCS系统由多个控制单元组成,每个控制单元都包括自己的CPU、内存、输入输出接口等硬件设备,同时还包括控制算法、执行逻辑等软件。
控制单元负责对工业过程的监控、控制和优化。
2.网络:DCS系统通过网络将各个控制单元连接在一起。
网络可以是局域网(LAN)、广域网(WAN)等不同范围的网络,用于实现控制单元之间的数据传输和通信。
3.数据采集系统:DCS系统通过传感器、仪表等设备采集工业过程的各项参数和信号。
SIS与ESD、DCS、PLC之间的区别

SIS与ESD、DCS、PLC之间的区别1、SIS系统(Safety Instrumented System 安全仪表系统)属于企业生产过程自动化范畴,用于保障安全生产的一套系统,安全等级高于DCS的自动化控制系统,当自动化生产系统出现异常时,SIS会进行干预,降低事故发生的可能性。
2、DCS集散控制系统是以微处理器为基础,采用控制功能分散、显示操作集中、兼顾分而自治和综合协调的设计原则的新一代仪表控制系统。
集散控制系统简称DCS,也可直译为“分散控制系统”或“分布式计算机控制系统”。
SIS与DCS在石油、石化生产过程中分别起着不同的作用,如下图所示:生产装置从安全角度来讲,可分为3个层次:第一层为生产过程层,第二层为过程控制层,第三层为安全仪表系统停车保护层。
SIS与ESD之间的区别SIS是系统化的概念,更关注整体性的概念,从命名就可以看出来,SIS关注回路,关注系统整体。
安全型的现场检测器件(变送器,仪表,传感器)-> 安全型 A -》安全型控制器-安全型的DO -》安全型的现场执行器件(安全关断阀,泄压阀,保护器等)。
而ESD通常是指,安全控制系统厂家生产的,安全型控制器,(CPU),IO,等纯控制系统的概念。
从本质上来讲,SIS 的硬件系统不光包括,SIS控制器及IO(例如Triconex,HIMA,西门子400FH)。
还应包括所有跟控制器接口的其他输入部件,例如获得TUV SIL认证的传感器,变送器,检测装置;还应该包括所有输出部件,如获得TUV SIL认证的执行器(液压安全执行器,气动安全执行器,电动型安全执行器),还应该有获得认证的现场设备。
要求严格的现场,阀门本体也必须是有TUV 证书的。
例如核电厂的安全阀不光是锅炉与压力容器质检合格,还应该有核检证书,还应该有TUV 的安规证书,明确标明是SIL几等级。
ESD是生产厂家的安全性控制器用在不同的场合,根据不同的用途,有着这些不同的叫法,从理论上说,只有ESD,“未必” 会是个完整的SIS控制系统。
dcs工作原理

dcs工作原理DCS(分布式控制系统)是一种广泛应用于工业控制领域的自动化系统,它通过将控制功能分布在多个位置,实现了对生产过程的高效监控和控制。
DCS系统的工作原理是通过将各个控制单元连接在一起,实现数据的实时传输和处理,从而实现对整个生产过程的集中监控和控制。
本文将从硬件架构、软件系统和通讯协议三个方面,对DCS系统的工作原理进行详细介绍。
首先,从硬件架构来看,DCS系统通常由控制器、输入/输出模块、网络通信模块和人机界面组成。
控制器是整个系统的核心,负责接收和处理各个输入信号,并根据预设的控制策略生成相应的输出信号。
输入/输出模块用于连接各种传感器和执行器,将现场设备的状态信息传输给控制器,并接收控制器的指令进行操作。
网络通信模块则负责将各个控制单元连接在一起,实现数据的实时传输和共享。
人机界面则提供了操作员与系统交互的界面,通过显示当前生产过程的状态信息,以及提供操作控制的功能。
其次,从软件系统来看,DCS系统的软件通常包括操作系统、控制逻辑、人机界面和数据库等部分。
操作系统是整个系统的基础,负责管理硬件资源和提供运行环境。
控制逻辑是系统的核心,包括了各种控制算法和策略,用于实现对生产过程的监控和控制。
人机界面则提供了操作员与系统交互的界面,通过显示当前生产过程的状态信息,以及提供操作控制的功能。
数据库则用于存储系统的配置信息、历史数据和报警信息等。
最后,从通讯协议来看,DCS系统通常采用现场总线和以太网等通讯协议,实现各个控制单元之间的数据传输和共享。
现场总线通常用于连接控制器、输入/输出模块和人机界面等设备,实现实时数据的传输和共享。
以太网则用于连接各个控制单元,实现远程监控和控制。
综上所述,DCS系统的工作原理是通过将控制功能分布在多个位置,实现了对生产过程的高效监控和控制。
它通过硬件架构、软件系统和通讯协议等多个方面的协同工作,实现了对生产过程的集中监控和控制。
希望本文能够对读者对DCS系统的工作原理有所帮助。
SIS MIS与DCS的关系

1 引言在科技飞速发展的今天,自动化控制也广泛的应用于电厂中,其中最主要的有分散控制系统DCS,信息管理系统MIS和厂级信息监控系统SIS 。
在企业面对趋激烈的市场竞争条件下,他们在保证生产过程的安全稳定,提高工艺系统的经济效益,实现全厂范围内的优化运行,并且在管理层的决策支持方面发挥着越来越重要的作用。
在电厂运行中,SIS、MIS和DCS互相独立,又互相联系,下面我们就来研究一下他们的关系。
2 DCS、SIS和 MIS的定义及功能2.1 DCS集散控制系统 (Distributed Control system DCS) 是以微处理器为基础的集中分散型控制系统。
自70年代中期第一套集散控制系统问世以来,集散控制系统已经在工业控制领域得到了广泛应用。
集散控制系统的主要特性是它的集中管理和分散控制。
而且,随着计算机技术的发展,网络技术已经使集散控制系统不仅主要用于分散控制,而且向着集成管理的方向发展。
系统的开放不仅使不同制造厂商的集散控制系统产品可以互相连接,而且使得它们可以方便地进行数据的交换,系统的开放也使第三方的软件可以方便地在现有的集散控制系统上应用。
在我国石化行业已运行着许多套不同型号的集散和控制系统,它们在过程控制中发挥着非常重要的作用。
DCS主要完成机组级的实时监控。
2.2 SIS火电厂厂级监控信息系统 ( Supervisory Informntion System SIS )是集过程实时监测、优化控制及生产过程管理为一体的厂级自动化信息系统。
该系统通过对火电厂生产过程的实时监测和分析,实现对全厂生产过程的优化控制和负荷经济分配,在整个电厂范围内充分发挥主辅机设备的潜力,达到整个电厂生产系统运行在最佳工况的目的;同时该系统提供全厂完整的生产过程历史/实时数据信息,可作为电力集团公司信息网络化的可靠生产信息资源,使集团公司管理人员能够实时掌握各发电企业生产信息及辅助决策信息,充分利用和共享信息资源,提高决策科学性[ 5 ] 。
Dos与SIS 系统 区别及关系

Dos与SIS系统区别及关系
DCS通常采用分级递阶结构,每一级由若干子系统组成,每一个子系统实现若干特定的有限目标,形成金字塔结构。
目前DCS在电力、冶金、石化等各行各业都获得了极其广泛的应用。
DCS --distribution control system 分散式控制系统,工厂控制级系统,常规数据采集,设备控制都由此系统完成。
SIS--safty instruments system 安全仪表系统,联锁系统的一种,一般做工厂过程设备的安全保护控制,有时也包含机组安全保护控制。
DCS为了控制,SIS为了保护。
实现功能:DCS用于过程连续测量、常规控制(连续、顺序、间歇等)操作控制管理使生产过程在正常情况下运行至最佳工况;而SIS是超越极限安全即将工艺、设备转至安全状态。
dcs为了实现分散控制、集中操作。
dcs是分散控制系统、sis是厂级实时监控系统
sis为了实现管控一体化。
电力里面SIS是指厂级监控信息系统,DCS主要侧重于设备监控,SIS主要侧重于全厂数据实时监测和性能计算及分析等数据挖掘工作,并不参与控制。
SIS 的数据来源基于DCS、PLC等其他控制系统、单有SIS是没有数据的。
化工里面SIS是指安全仪表系统,与DCS一样用于设备监控,但SIS系统的故障安全措施及等级要远高于DCS。
化工项目工程设计阶段会做危险与可操作性分析,分析结果要求安全度等级SIL2及以上的设备需要用SIS控制,SIL2以下的可以用DCS、PLC等控制(有的要求更严,SIL1及以上均要用SIS)。
SIS系统为什么要和DCS单独设置

SIS系统为什么要和DCS单独设置生产多年的装置,也加装了自动化控制系统,DCS也平稳运行了这么多年,为什么要加SIS?加了SIS以后费用不少,给企业带来了资金的压力。
安全仪表系统SIS包括了安全型控制逻辑器PES、现场仪表、执行机构等,行业内对安全型控制逻辑器以SIS代称,并不完全合理,从直观上不如10年前说的紧急停车系统ESD更容易理解。
事实如此,所以标题是SIS为什么要和DCS独立设置,其中的SIS指的是安全型控制逻辑器PES,但下文依旧以SIS开笔。
一、标准规范的角度目前石化行业和SIS相关的标准主要如下:(1)GB/T50770-2013石油化工安全仪表系统设计规范;(2)HG/T20511-2014信号报警、安全联锁系统设计规范;(3)SH-T3018-2003石油化工安全仪表系统设计规范,因这个标准相比于GB50770太老了,所以不参考此规范。
在HG/T20511里面给DCS的定义如下:基本过程控制系统(basic process control system),对来自过程的、与该系统相关设备的以及操作员的输入信号进行响应,并产生输出信号使过程及与该系统相关设备按要求方式运行的系统。
该系统不应执行安全完整性等级大于或等于1的仪表安全功能。
而SIS是由多个SIF回路组成的,SIF回路的SIL等级为1-3级,根据上述DCS的定义,DCS去执行SIF回路的功能不合适。
所以DCS与SIS是独立设置的。
在GB50770-2013里面,则对LOPA分析的洋葱图,如下所示。
从上图可以看出,DCS作为基本过程控制系统和SIS隶属于不同的保护层,如果他们公用的话,则起不到独立的作用,也没法避免与DCS的共因失效问题。
二、安监文件的角度规范是推荐的,安监文件是规范的。
安监文件和SIS相关的主要是《2014-116号文-国家安全监管总局关于加强化工安全仪表系统管理的指导意见》,节选内容如下。
从2018年1月1日起,所有新建涉及两重点一重大的化工装置和危险化学品储存设施要设计符合要求的安全仪表系统。
DCS、SIS和MIS三者之间的区别

DCS、SIS和MIS三者之间的区别一、DCS、SIS和 MIS定义和分工1、DCS集散控制系统(Distributed Control system)是以微处理器为基础的集中分散型控制系统。
自70年代中期第一套集散控制系统问世以来,集散控制系统已经在工业控制领域得到了广泛应用。
集散控制系统的主要特性是通过实时监控达到集中管理和分散控制。
2、SIS厂级监控信息系统(Supervisory Informntion System )是集过程实时监测、优化控制及生产过程管理为一体的厂级自动化信息系统。
SIS的目标是通过大规模的数据搜集处理,实现生产实时信息与管理信息的共享,在此基础上,通过计算、分析、统计、优化、数据挖掘手段,实现化工厂生产过程监视、工艺设备性能及经济指标分析和运行指导。
主要特性体现再系统决策支持上。
3、MIS管理信息系统(Management Information System),是一个由人、计算机等组成的能进行信息的收集、传送、储存、维护和使用的系统,能够实测企业的各种运行情况,并利用过去的历史数据预测未来,从企业全局的角度出发辅助企业进行决策,利用信息控制企业的行为,帮助企业实现其规划目标。
这里给出的定义强调了管理信息系统的功能和性质,也强调了管理信息系统中的计算机对企业管理而言只是一种工具。
二、DCS、SIS和 MIS关系DCS系统重在实时监控和精确控制,以设备安全、稳定运行为目的。
SIS是建立在DCS基础上的,通过对监测数据的实时分析对全厂生产运行实时指挥调度,以保证生产整个系统的运行质量和经济性为目的。
而MIS是管理信息系统,主要任务是信息处理、任务流转和工作协同等,为全厂的生产经营和行政管理人员提供所需的信息,强调生产、辅助、财务等关系协调,主要完成设备和维修管理直至生产经营管理、财务管理以及办公自动化。
因此,SIS系统、MIS系统、DCS系统是面向不同层次、不同目标,具有不同功能的三种系统,既有相互联系,又有重大区别。
DCS工作原理讲义及组成
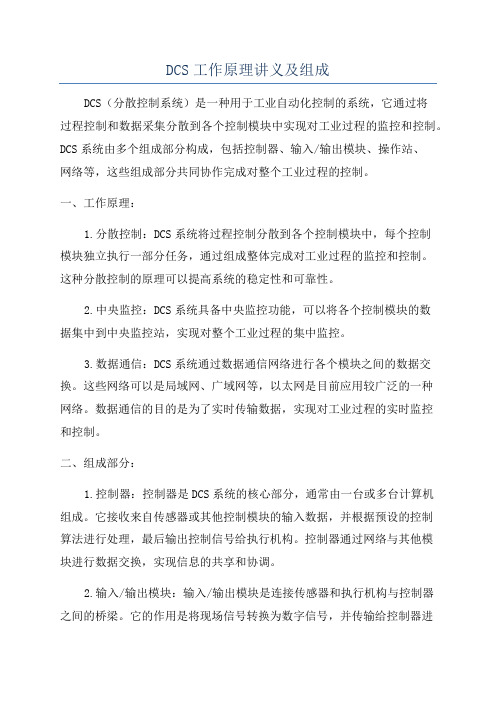
DCS工作原理讲义及组成DCS(分散控制系统)是一种用于工业自动化控制的系统,它通过将过程控制和数据采集分散到各个控制模块中实现对工业过程的监控和控制。
DCS系统由多个组成部分构成,包括控制器、输入/输出模块、操作站、网络等,这些组成部分共同协作完成对整个工业过程的控制。
一、工作原理:1.分散控制:DCS系统将过程控制分散到各个控制模块中,每个控制模块独立执行一部分任务,通过组成整体完成对工业过程的监控和控制。
这种分散控制的原理可以提高系统的稳定性和可靠性。
2.中央监控:DCS系统具备中央监控功能,可以将各个控制模块的数据集中到中央监控站,实现对整个工业过程的集中监控。
3.数据通信:DCS系统通过数据通信网络进行各个模块之间的数据交换。
这些网络可以是局域网、广域网等,以太网是目前应用较广泛的一种网络。
数据通信的目的是为了实时传输数据,实现对工业过程的实时监控和控制。
二、组成部分:1.控制器:控制器是DCS系统的核心部分,通常由一台或多台计算机组成。
它接收来自传感器或其他控制模块的输入数据,并根据预设的控制算法进行处理,最后输出控制信号给执行机构。
控制器通过网络与其他模块进行数据交换,实现信息的共享和协调。
2.输入/输出模块:输入/输出模块是连接传感器和执行机构与控制器之间的桥梁。
它的作用是将现场信号转换为数字信号,并传输给控制器进行处理,或者将控制信号传输给执行机构。
输入/输出模块具有多种类型,如模拟输入模块、数字输入模块、模拟输出模块、数字输出模块等。
3.操作站:操作站是用于人机交互的界面,操作员通过操作站与DCS系统进行交互。
操作站通常由工业计算机和触摸屏组成,可以实时监控工业过程的状态,并进行参数设置、报警处理等操作。
4.数据通信网络:数据通信网络是DCS系统的基础设施,它连接各个控制模块和操作站,实现数据的实时传输和共享。
数据通信网络可以采用不同的协议和通信方式,如以太网、现场总线等。
5.软件系统:软件系统是DCS系统的核心控制软件,它负责控制算法的运行、数据的处理和通信协议的实现等功能。
化工企业DCS与SIS一体化分析与探讨
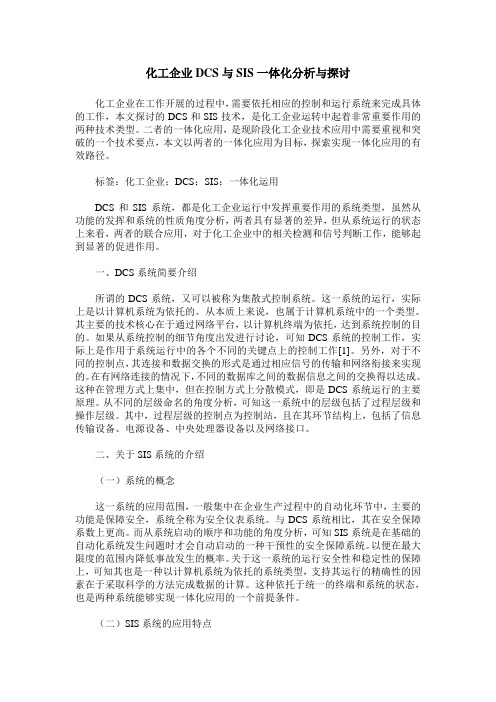
化工企业DCS与SIS一体化分析与探讨化工企业在工作开展的过程中,需要依托相应的控制和运行系统来完成具体的工作,本文探讨的DCS和SIS技术,是化工企业运转中起着非常重要作用的两种技术类型。
二者的一体化应用,是现阶段化工企业技术应用中需要重视和突破的一个技术要点,本文以两者的一体化应用为目标,探索实现一体化应用的有效路径。
标签:化工企业;DCS;SIS;一体化运用DCS和SIS系统,都是化工企业运行中发挥重要作用的系统类型,虽然从功能的发挥和系统的性质角度分析,两者具有显著的差异,但从系统运行的状态上来看,两者的联合应用,对于化工企业中的相关检测和信号判断工作,能够起到显著的促进作用。
一、DCS系统简要介绍所谓的DCS系统,又可以被称为集散式控制系统。
这一系统的运行,实际上是以计算机系统为依托的。
从本质上来说,也属于计算机系统中的一个类型。
其主要的技术核心在于通过网络平台,以计算机终端为依托,达到系统控制的目的。
如果从系统控制的细节角度出发进行讨论,可知DCS系统的控制工作,实际上是作用于系统运行中的各个不同的关键点上的控制工作[1]。
另外,对于不同的控制点,其连接和数据交换的形式是通过相应信号的传输和网络衔接来实现的。
在有网络连接的情况下,不同的数据库之间的数据信息之间的交换得以达成。
这种在管理方式上集中,但在控制方式上分散模式,即是DCS系统运行的主要原理。
从不同的层级命名的角度分析,可知这一系统中的层级包括了过程层级和操作层级。
其中,过程层级的控制点为控制站,且在其环节结构上,包括了信息传输设备、电源设备、中央处理器设备以及网络接口。
二、关于SIS系统的介绍(一)系统的概念这一系统的应用范围,一般集中在企业生产过程中的自动化环节中,主要的功能是保障安全,系统全称为安全仪表系统。
与DCS系统相比,其在安全保障系数上更高。
而从系统启动的顺序和功能的角度分析,可知SIS系统是在基础的自动化系统发生问题时才会自动启动的一种干预性的安全保障系统。
SIS与ESD、DCS、PLC之间的区别

SIS与ESD、DCS、PLC之间的区别1、SIS系统(Safety Instrumented System 安全仪表系统)属于企业生产过程自动化范畴,用于保障安全生产的一套系统,安全等级高于DCS的自动化控制系统,当自动化生产系统出现异常时,SIS会进行干预,降低事故发生的可能性。
2、DCS集散控制系统是以微处理器为基础,采用控制功能分散、显示操作集中、兼顾分而自治和综合协调的设计原则的新一代仪表控制系统。
集散控制系统简称DCS,也可直译为“分散控制系统”或“分布式计算机控制系统”。
SIS与DCS在石油、石化生产过程中分别起着不同的作用,如下图所示:生产装置从安全角度来讲,可分为3个层次:第一层为生产过程层,第二层为过程控制层,第三层为安全仪表系统停车保护层。
SIS与ESD之间的区别SIS是系统化的概念,更关注整体性的概念,从命名就可以看出来,SIS关注回路,关注系统整体。
安全型的现场检测器件(变送器,仪表,传感器)-> 安全型 A -》安全型控制器-安全型的DO -》安全型的现场执行器件(安全关断阀,泄压阀,保护器等)。
而ESD通常是指,安全控制系统厂家生产的,安全型控制器,(CPU),IO,等纯控制系统的概念。
从本质上来讲,SIS 的硬件系统不光包括,SIS控制器及IO(例如Triconex,HIMA,西门子400FH)。
还应包括所有跟控制器接口的其他输入部件,例如获得TUV SIL认证的传感器,变送器,检测装置;还应该包括所有输出部件,如获得TUV SIL认证的执行器(液压安全执行器,气动安全执行器,电动型安全执行器),还应该有获得认证的现场设备。
要求严格的现场,阀门本体也必须是有TUV 证书的。
例如核电厂的安全阀不光是锅炉与压力容器质检合格,还应该有核检证书,还应该有TUV 的安规证书,明确标明是SIL几等级。
ESD是生产厂家的安全性控制器用在不同的场合,根据不同的用途,有着这些不同的叫法,从理论上说,只有ESD,“未必” 会是个完整的SIS控制系统。
为什么装置在有了DCS后还要上SIS?(DCS和SIS的区别和优缺点)

为什么装置在有了DCS后还要上SIS?(DCS和SIS的区别和优缺点)安全仪表系统SIS是由传感单元、逻辑控制单元、执行机构组成的能够行使一项或多项安全仪表功能(SIF)的仪表系统。
人们常认为安装了SIS就能达到安全要求,却忽略了SIS在结构设置、仪表选型及软件等方面的问题。
主要的问题是有些企业联锁回路设置在DCS中,未设置独立的SIS。
由于DCS没有认证要求,因而在进行SIS的功能安全评估时,缺少验证数据,而无法进行系统评估。
案例分析以某甲醇低温甲醇洗装置的联锁设置情况进行说明,低温甲醇洗是一种新型的煤化工技术,是酸性气脱除技术的首选技术,作为目前国内先进的煤气净化工艺,它对酸性气体有较高的吸收选择性,并且净化程度高。
甲醇为有毒液体,并且易燃,装置中工艺气中含有氢气、一氧化碳、硫化氢等易燃易爆气体,一旦泄漏将有可能引起火灾、爆炸事故,对环境造成无法挽回的损坏。
采用保护层分析(LOPA)方法对装置23条联锁回路逐条进行定级分析,分析步骤如下图所示。
联锁回路统计见下表所列。
SIS的独立性要求我们在LOPA分析过程中,以上分析结果均基于保护层的独立性原则,根据IEC61511-1关于基本过程控制系统(BPCS)作为独立保护层时有以下规定:当触发条件是BPCS保护层防控的触发源为BPCS本身时,应确保触发源与BPCS保护层之间的隔离和独立,如下图所示。
实践中,很难达到上图中所示的独立性要求,因为DCS中的冗余CPU通常采用“热备用”机制,不具备图中控制器1和控制器2之间的独立性,除非配置2套DCS。
因此,当同一危险场景下,如果DCS控制故障,则设置在DCS中的相应联锁就会失效。
GB/T50770-2013《石油化工安全仪表系统设计规范》中规定了SIS设计的基本原则:SIS独立于过程控制系统,独立完成安全保护功能。
如果用DCS来承担SIS的任务,则相应的要求水平较常规的过程控制系统更高、花费也更大,因而都建议将SIS与DCS硬件独立设置。
最全DCS、SIS和 MIS的区别

最全DCS、SIS和 MIS的区别一、DCS、SIS和 MIS定义和分工1.DCS集散控制系统 (Distributed Control system)是以微处理器为基础的集中分散型控制系统。
自70年代中期第一套集散控制系统问世以来,集散控制系统已经在工业控制领域得到了广泛应用。
集散控制系统的主要特性是通过实时监控达到集中管理和分散控制。
2.SIS厂级监控信息系统(Supervisory Informntion System )是集过程实时监测、优化控制及生产过程管理为一体的厂级自动化信息系统。
SIS的目标是通过大规模的数据搜集处理,实现生产实时信息与管理信息的共享,在此基础上,通过计算、分析、统计、优化、数据挖掘手段,实现化工厂生产过程监视、工艺设备性能及经济指标分析和运行指导。
主要特性体现再系统决策支持上。
3. MIS管理信息系统 ( Management Information System) ,是一个由人、计算机等组成的能进行信息的收集、传送、储存、维护和使用的系统,能够实测企业的各种运行情况,并利用过去的历史数据预测未来,从企业全局的角度出发辅助企业进行决策,利用信息控制企业的行为,帮助企业实现其规划目标。
这里给出的定义强调了管理信息系统的功能和性质,也强调了管理信息系统中的计算机对企业管理而言只是一种工具。
二、DCS、SIS和 MIS关系DCS系统重在实时监控和精确控制,以设备安全、稳定运行为目的。
SIS是建立在DCS基础上的,通过对监测数据的实时分析对全厂生产运行实时指挥调度,以保证生产整个系统的运行质量和经济性为目的。
而MIS是管理信息系统,主要任务是信息处理、任务流转和工作协同等,为全厂的生产经营和行政管理人员提供所需的信息,强调生产、辅助、财务等关系协调,主要完成设备和维修管理直至生产经营管理、财务管理以及办公自动化。
因此,SIS系统、MIS系统、DCS系统是面向不同层次、不同目标,具有不同功能的三种系统,既有相互联系,又有重大区别。
DCS系统和SIS安全仪表系统的区别

DCS系统和SIS安全仪表系统的区别一、DCS系统和SIS安全仪表系统的重要性化工产业是我国经济和社会发展中重要的行业之一,极大地推动了我国经济的发展。
由于化工产业环境的特殊性、安全性以及生产效率问题,工业自动化DCS 系统控制和安全仪表系统sis控制程度一直受到较大的关注。
通过化工生产控制自动化系统的应用、操作人员技能的提升以及仪表的有效表现,将在一定程度上提高化工装置的可靠性、安全性和生产效率,从而推动我国化工产业的继续向前发展。
因此DCS系统和SIS安全仪表系统在化工行业尤为重要。
二、DCS和SIS的概念DCS系统是Distributed Control System分散控制系统简称。
DCS系统是过程控制系统,是动态的,需要人工频繁的干预,这有可能引起人为误动作;而SIS(ESD)是静态的,不需要人为干预,这样设置可以避免人为误动作。
PLC通常作为成套设备的控制方案,比如说真空、废水、集装、压缩机等等自成一个体系的系统。
他们的特点往往是不要求很多的模拟量控制,对数字量控制极为有效、方便、可靠、经济。
通常做为DCS的子站点,便于监视。
SIS系统是Safety Interlocking System(Safety Instrument System)安全联锁系统/安全仪表系统简称。
SIS包括现场仪表、逻辑解决器、执行机构三部分,这三个部分都要是安全设计的,常规的ESD系统只是SIS的逻辑解决器这部分,当然也要是安全设计的。
特点依然是PID控制,借助其强大的通讯功能,是整合工厂所有自动化设备的系统,SIS比DCS 在可靠性、可用性上要求更严格,IEC61508、IEC61511等标准中,要求SIS与DCS硬件独立设置。
这类系统往往用于石化等高危行业,一旦动作就是全厂停车,是牺牲生产效益,保障安全的防线。
SIS认证,石化行业通常等级为3.生产装置从安全角度来讲,可分为三个层次:第一层为生产过程层,第二层为过程控制层,第三层为安全仪表系统停车保护层。
【热控知识】DCS、SIS和MIS分别是什么作用?有什么区别?

【热控知识】DCS、SIS和MIS分别是什么作用?有什么区别?一、DCS、SIS和 MIS定义和分工1.DCS集散控制系统 (Distributed Control system) 是以微处理器为基础的集中分散型控制系统。
自70年代中期第一套集散控制系统问世以来,集散控制系统已经在工业控制领域得到了广泛应用。
集散控制系统的主要特性是通过实时监控达到集中管理和分散控制。
2.SIS厂级监控信息系统 ( Supervisory Informntion System )是集过程实时监测、优化控制及生产过程管理为一体的厂级自动化信息系统。
SIS的目标是通过大规模的数据搜集处理,实现生产实时信息与管理信息的共享,在此基础上,通过计算、分析、统计、优化、数据挖掘手段,实现化工厂生产过程监视、工艺设备性能及经济指标分析和运行指导。
主要特性体现再系统决策支持上3. MIS管理信息系统 ( Management Information System) ,是一个由人、计算机等组成的能进行信息的收集、传送、储存、维护和使用的系统,能够实测企业的各种运行情况,并利用过去的历史数据预测未来,从企业全局的角度出发辅助企业进行决策,利用信息控制企业的行为,帮助企业实现其规划目标。
这里给出的定义强调了管理信息系统的功能和性质,也强调了管理信息系统中的计算机对企业管理而言只是一种工具。
二、DCS、SIS和 MIS关系DCS系统重在实时监控和精确控制,以设备安全、稳定运行为目的。
SIS是建立在DCS基础上的,通过对监测数据的实时分析对全厂生产运行实时指挥调度,以保证生产整个系统的运行质量和经济性为目的。
而MIS是管理信息系统,主要任务是信息处理、任务流转和工作协同等,为全厂的生产经营和行政管理人员提供所需的信息,强调生产、辅助、财务等关系协调,主要完成设备和维修管理直至生产经营管理、财务管理以及办公自动化。
因此,SIS系统、MIS系统、DCS 系统是面向不同层次、不同目标,具有不同功能的三种系统,既有相互联系,又有重大区别。
电厂SIS系统简介

电厂SIS系统简介电厂SIS系统指的是电厂的安全仪表系统,它是电厂的安全保障系统之一。
SIS 系统负责在电厂发生危险事故时,自动或手动切断电路,避免危险事件加剧,保障设备和人员的安全。
SIS系统的作用SIS是Safety Instrumented Systems的缩写,翻译为“安全仪表系统”,它的任务是在安全控制系统失效时,确保设备、产品和人员的安全。
SIS具有以下重要作用:1.防止传染性故障扩大:当设备故障时,会导致压力和温度等物理参数变化,如果没有SIS系统隔离故障,问题将变得更加严重,可能导致原本可以控制的故障快速扩大,然后危害到其他设备和人员的安全。
2.防止过程故障:如果操作员没有正确地运行电厂设备,将会导致过程问题。
SIS系统会迅速介入,帮助操作员纠正问题,避免产生更严重的后果。
3.防止内部矛盾:电厂的设备系统非常复杂,需要由多个供应商生产,而这些供应商可能在不同的时期分别提供设备的不同部分。
SIS的作用是使各个部分顺利协作,协调一个完整的系统。
SIS系统的工作原理电厂SIS系统的工作原理可以分为以下三个步骤:1.监视与诊断:SIS系统会不断监视电厂设备运行的状态,一旦发现某些参数超出了设定的范围,就会警告操作员或自动切断电路。
然后,SIS系统会自动进行诊断和监测,以确认是否发生了一种特定的故障。
2.切断电路:如果SIS系统发现设备正在发生故障,它会给出切断电路的指令,避免进一步的危险事件的发生。
该指令可以由自动控制逻辑控制,也可以由操作员手动控制。
3.恢复:在SIS系统切断电路之后,电厂必须进行故障诊断和维修。
在重建电厂设备后,SIS系统可以再次启动,确保设备可以正常运行。
SIS系统的部分设计要素电厂SIS系统的设计需要考虑以下几个方面的要素:1.安全仪表阶段:SIS系统要保证处于最高安全级别,它保证在出现故障时,自动切断电路。
SIS系统的安全级别须要符合电厂的安全保障要求,因此SIS系统的设计必须经过认真的审查,并且要符合国家、地区的安全标准,保证每个阶段都进行了设计、测试、部署和验证。
【学习】一文读懂:SIS、SIL、DCS技术不再是难题

【学习】一文读懂:SIS、SIL、DCS技术不再是难题文章导读近年来随着技术的发展,化工项目和炼油项目的规模越来越大,其配套的罐区也越来越大,储存的介质也越来越复杂。
而不同于一般的油库,其操作比较频繁,误操作可能性较大,而误操作引起的后果也比较严重,给企业造成经济损失、对环境造成破坏。
因此罐区设计中对于可燃、毒害介质的安全控制要尤其重视。
本文主要介绍了某大型化工项目配套罐区,根据可燃、毒害介质的特性和储存量进行重大危险源的辨识,综合考虑安全和投资,采用独立的安全仪表系统(SIS)进行安全控制。
0 引言一直以来,化工项目的罐区一般根据石油库设计规范进行设计,而此规范,并没有要求设置安全仪表系统。
但是化工项目的罐区不同于一般的石油库或者储备库,它的特点是:单罐罐容小、介质种类复杂、毒害介质多。
由于储罐容量一般较小,储罐的仪表设置都比较简单,介质本身的危险性往往被忽视。
本项目设计中,充分考虑了介质的危险性并兼顾投资要求,对于属于重大危险源介质的储罐设置了独立的安全仪表系统(SIS),用于防冒罐的高高液位联锁控制。
1 设置SIS 系统的必要性化工项目罐区的介质种类复杂,可燃毒害介质多,发生事故后危害巨大。
罐区一旦发生事故,将会对上下游的工艺都产生影响,连带着相关装置都需要停产,损失不小。
减少罐区的安全事故可以更好的保证工厂的正常生产,提高效益。
不因节省初次投入而增大事故风险。
现行化工项目配套的罐区大多采用分散控制系统(DCS)进行操作控制及连锁。
DCS 系统具有控制功能完善多样、易操作、易扩展及维护方便等特点,但是并不适用于安全控制。
对于化工项目罐区要比一般油库操作更加频繁,误操作的概率就更大。
这时采用一套安全性更高的、容错能力强、具有故障自诊断功能、顺序事件记录功能(SOE)的安全仪表系统(SIS)就十分必要了。
2011 年8 月5 日,国家安全生产监督管理总局发布第40 号令,要求“涉及毒性气体、液化气体、剧毒液体的一级或者二级重大危险源,配备独立的安全仪表系统(SIS)”。
sis仪表控制系统的原理

sis仪表控制系统的原理
SIS仪表控制系统是指安全仪器系统,它是为了监控工业过程中的险情而设计的一种系统。
SIS系统跟一般的自动控制系统相比,主要作用就是保护人员和现场设备安全,同时通常应用于高危、高温、高压等危
险环境下。
SIS系统的原理是在多种工艺控制系统和主控制系统失效时,可以及时接管控制系统并采取应急措施以保障设备和人员的安全。
SIS系统包含了传感器、逻辑电路、风险估计、处理器、执行器等基本组件。
在正
常工作状态下,SIS系统的各个模块会一直工作并监控设备,以便快速检测并正确响应设备失效或存在危险的情况。
SIS系统的交互方式包括数字以及模拟信号,在风险参数到达预设值时,系统会根据其自身的策略采取相应的应急措施,如关闭阀门、卸载压
力等等。
对于 SAS 型 SIS 系统而言,其自主的应急控制系统包含了多个退避层级,这样就可以在前几层不包含应急情况时保证自身的稳定性。
如果任何一个层级的信号存在失效情况,继续到第n层将进入应
急操作阶段,越高的层级所采取的动作呈加强趋势。
SIS系统的设计通常根据国际标准EuroNorm-61508,该标准是一种
适用于电气、电子和电子信号传递系统安全的标准,并强调系统的各
个组成部分(例如传感器、逻辑评估器和控制器)需要具有高可靠性和安全性。
此外,SIS系统还必须经过严格的工厂测试,以确保其在实际应用场景中能够正确响应所有风险事件。
总的来说,SIS系统应用广泛,它可以在工业生产中保障设备和人员的安全。
SIS系统的原理和设计在全球范围内得到了广泛的认可,它是一种虽然不被人们经常提及,但是在关键一刻却可为人类保驾护航的安全措施。
SIS的联锁和DCS的联锁动作的区别

SIS的联锁和DCS的联锁动作的区别导读SIS系统和DCS系统处于生产装置的不同安全层级,DCS的联锁属于生产过程中经常使用的开关连锁或设备启动停止联锁,属于正常操作;SIS的联锁大多与人员及设备的安全联锁有关(尤其是停车联锁),属于SIL级别确定严格的故障及事故联锁。
两者性质和配置都不相同。
安全仪表系统(SIS)与分散控制系统(DCS)在工业生产过程中分别起着不同的作用.生产装置从安全角度来讲,可分为三个层次,第一层为生产过程层;第二层为过程控制层;第三层为安全仪表系统停车保护层。
生产装置在最初的工程设计、设备选型及安装阶段,都对过程和设备的安全性进行了考虑,因此装置本身就构成了安全的第一道防线。
采用用控制系统对过程进行连续动态控制,使装置在设定值下平稳运行,不但生产出各种合格产品,而且将装置的风险又降低了一个等级,是安全的第二道防线。
在过程之上要设置一套安全仪表系统,对过程进行监测和保护,把发生恶性事故的可能性降到最低,最大限度地保护生产装置和人身安全,避免恶性事故的发生,构成了生产装置最稳固、最关键的最后一道防线。
因此SIS与DCS在生产过程中所起的作用是截然不同的。
DC S系统①DCS用于过程连续测量、常规控制(连续、顺序、间歇等)、操作控制管理,保证生产装置平稳运行;②DCS是“动态”系统,它始终对过程变量连续进行监测、运算和控制,对生产过程动态控制,确保产品质量和产量;③DCS可以进行故障自动显示;DCS对维修时间的长短和要求不算苛刻;DCS 可进行自动/手动切换;④DCS系统只作一般联锁、电机的开停、顺序等控制,安全级别要求不像SIS 那么高;⑤DCS系统一般是由人机界面操作站、通信总线及现场控制站组成,DCS不含检测执行部分;⑥为了实现生产过程自动化,操作人员会经常改变DCS系统的一些输出动作。
SIS系统①SIS用于监测生产设置的运行状况,对出现异常工况迅速进行处理,使故障发生的可能性降到最低,使人和装置处于安全状态;②SIS是静态系统,在正常工况下,它始终监视装置的运行,系统输出不变,对生产过程不产生影响,在异常工况下,它将按着预先设计的策略进行逻辑运算,使生产装置安全停车;③SIS必须测试潜在故障;SIS维修时间非常关键,严重的会造成装置全线停车;SIS系统永远不允许离线运行,否则生产装置将失去安全保护屏障;④SIS与DCS相比,在可靠性、可用性上要求更严格,IEC 6150811,ISA S84.01强烈推荐SIS与DCS硬件独立设置;⑤SIS系统是由传感器、逻辑解算器和最终单元三部分组成;⑥SIS系统日常是静默的不会发出动作,只有联锁触发才会动作。
为何SIS系统和DCS系统联合应用又要相对独立
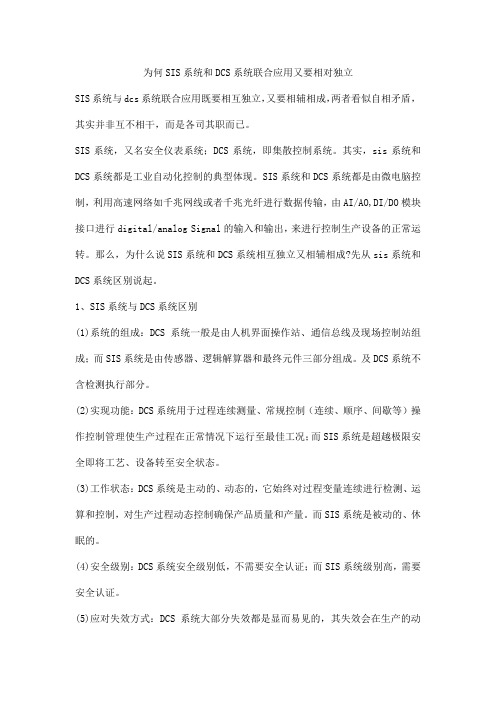
为何SIS系统和DCS系统联合应用又要相对独立SIS系统与dcs系统联合应用既要相互独立,又要相辅相成,两者看似自相矛盾,其实并非互不相干,而是各司其职而已。
SIS系统,又名安全仪表系统;DCS系统,即集散控制系统。
其实,sis系统和DCS系统都是工业自动化控制的典型体现。
SIS系统和DCS系统都是由微电脑控制,利用高速网络如千兆网线或者千兆光纤进行数据传输,由AI/AO,DI/DO模块接口进行digital/analog Signal的输入和输出,来进行控制生产设备的正常运转。
那么,为什么说SIS系统和DCS系统相互独立又相辅相成?先从sis系统和DCS系统区别说起。
1、SIS系统与DCS系统区别(1)系统的组成:DCS系统一般是由人机界面操作站、通信总线及现场控制站组成;而SIS系统是由传感器、逻辑解算器和最终元件三部分组成。
及DCS系统不含检测执行部分。
(2)实现功能:DCS系统用于过程连续测量、常规控制(连续、顺序、间歇等)操作控制管理使生产过程在正常情况下运行至最佳工况;而SIS系统是超越极限安全即将工艺、设备转至安全状态。
(3)工作状态:DCS系统是主动的、动态的,它始终对过程变量连续进行检测、运算和控制,对生产过程动态控制确保产品质量和产量。
而SIS系统是被动的、休眠的。
(4)安全级别:DCS系统安全级别低,不需要安全认证;而SIS系统级别高,需要安全认证。
(5)应对失效方式:DCS系统大部分失效都是显而易见的,其失效会在生产的动态过程中自行显现,很少存在隐性失效;SIS系统失效就没那么明显了,因此确定这种休眠系统是否还能正常工作的唯一方法,就是对该系统进行周期性的诊断或测试。
因此安全仪表系统需要人为的进行周期性的离线或在线检验测试,而有些安全系统则带有内部自诊断。
2、SIS系统与DCS系统独立安全仪表系统/SIS系统为何要独立于DCS系统?因为安全仪表系统遵照安全独立原则,独立于集散控制系统,并且其安全级别高于DCS系统,如上图所示。
- 1、下载文档前请自行甄别文档内容的完整性,平台不提供额外的编辑、内容补充、找答案等附加服务。
- 2、"仅部分预览"的文档,不可在线预览部分如存在完整性等问题,可反馈申请退款(可完整预览的文档不适用该条件!)。
- 3、如文档侵犯您的权益,请联系客服反馈,我们会尽快为您处理(人工客服工作时间:9:00-18:30)。
dcs和sis工作原理
一、概述
DCS(DistributedControlSystem)和SIS(SafetyInstrumentedSystems)是工业自动化领域中的两种重要系统,分别用于过程控制和安全联锁监控。
本文将介绍DCS和SIS的工作原理,包括其基本概念、组成、工作流程及常见应用场景。
二、DCS工作原理
DCS是一种分布式控制系统,它将复杂的控制系统分布到多个控制器上,实现分散控制、集中操作的管理模式。
其工作原理如下:
1.数据采集:DCS通过传感器、变送器等设备采集生产过程中的各类数据,如温度、压力、流量等。
这些数据被送入DCS的各个控制器进行运算和处理。
2.控制器运算:控制器根据采集的数据和预设的控制算法,对生产过程进行实时调整和控制。
3.输出控制:控制器将运算结果输出到执行器,如调节阀、电磁阀等,实现对生产设备的控制。
4.系统维护:DCS还配备有监控和报警功能,以便于工作人员实时掌握系统的运行状况,及时发现和处理故障。
SIS是一种安全联锁监控系统,用于在危险性较大的生产环境中,实现对关键设备的监控和保护。
其工作原理如下:
1.传感器监测:SIS通过各类传感器监测生产环境中的危险参数,如可燃气体浓度、压力等。
一旦检测到异常情况,SIS会立即报警并采取相应的安全措施。
2.逻辑运算:SIS内部包含一系列的逻辑运算和控制单元,能够对检测到的数据进行处理和分析,判断是否触发紧急停车(ESD)等安全措施。
3.紧急停车:当SIS判断危险情况已经发生或即将发生时,会触发紧急停车,停止危险区域内所有设备,从而确保人员和设备的安全。
4.反馈调节:SIS在处理紧急停车后,会对系统的运行状况进行评估和调整,以确保生产环境的稳定和安全。
四、应用场景
DCS和SIS广泛应用于各种工业生产环境中,包括但不限于以下场景:
1.化工、石化、炼油等危险性较大的生产领域。
2.电力、钢铁、煤矿等大型工厂的自动化控制。
3.食品、制药等对生产过程有严格要求的行业。
五、总结
DCS和SIS作为工业自动化领域的两种重要系统,分别用于过程控制和安全联锁监控。
其工作原理包括数据采集、控制器运算、输出控制、系统维护等多个环节。
在实际应用中,这两种系统能够有效提高生产过程的稳定性和安全性,降低事故发生的概率。
随着工业自动化技术的不断发展,DCS和SIS的应用场景也将不断扩大,为工业生产带来更多便利和安全保障。