全断面钻井钻头结构的优化
钻井优化数学建模
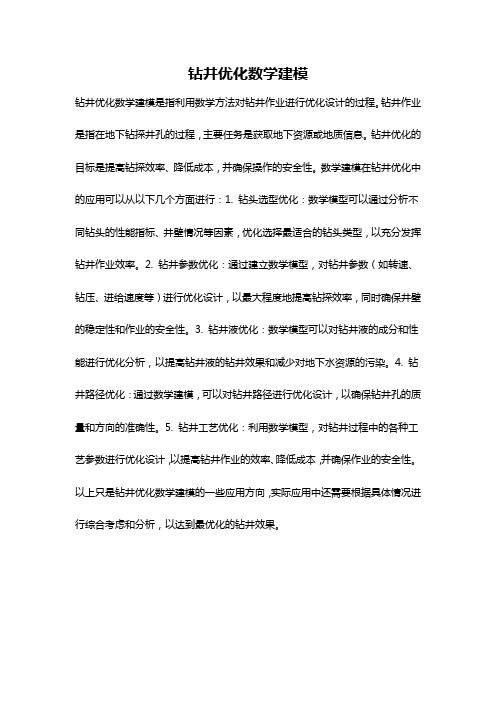
钻井优化数学建模
钻井优化数学建模是指利用数学方法对钻井作业进行优化设计的过程。
钻井作业是指在地下钻探井孔的过程,主要任务是获取地下资源或地质信息。
钻井优化的目标是提高钻探效率、降低成本,并确保操作的安全性。
数学建模在钻井优化中的应用可以从以下几个方面进行:1. 钻头选型优化:数学模型可以通过分析不同钻头的性能指标、井壁情况等因素,优化选择最适合的钻头类型,以充分发挥钻井作业效率。
2. 钻井参数优化:通过建立数学模型,对钻井参数(如转速、钻压、进给速度等)进行优化设计,以最大程度地提高钻探效率,同时确保井壁的稳定性和作业的安全性。
3. 钻井液优化:数学模型可以对钻井液的成分和性能进行优化分析,以提高钻井液的钻井效果和减少对地下水资源的污染。
4. 钻井路径优化:通过数学建模,可以对钻井路径进行优化设计,以确保钻井孔的质量和方向的准确性。
5. 钻井工艺优化:利用数学模型,对钻井过程中的各种工艺参数进行优化设计,以提高钻井作业的效率、降低成本,并确保作业的安全性。
以上只是钻井优化数学建模的一些应用方向,实际应用中还需要根据具体情况进行综合考虑和分析,以达到最优化的钻井效果。
PDC钻头设计与优选技术
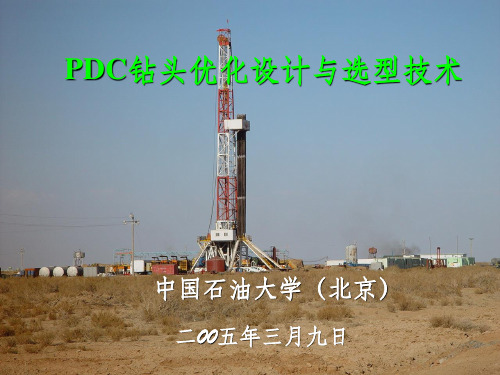
迪那、塔东等地区一批典型高效井。钻头技术基本满足了
探区复杂井的需要,钻井成本得到了有效控制:探井、评
价井平均机速由1999年的2.21米/小时提高到2003年的3.89
米/小时,四年提高了76%,平均每年提高15%以上。
精选课件
3
二、钻头优化设计
一)PDC钻头结构设计的基本参数
钻头结构设计参数
切削结构
精选课件
15
平衡力设计的方法
• ①改变切削齿的空间角度消除不平衡力; • ②采用不对称刀翼设计消除不平衡力; • ③采用低摩擦保径设计抵消不平衡力。 • ④采用轨道式布齿形成的沟槽限制钻头
的涡动。
精选课件
16
图2 钻头切削的井底 A—常规 B—涡动
精选课件
17
改变切削齿的角 度及位置
不对称刀翼设计
精选课件
水力结构
4
精选课件
5
1、切削结构设计的基本参数
切削结构
冠部形状
刀翼的数量及结构
切削齿的分布
切削齿的空间结构
保径结构
精选课件
6
2、水力结构设计的基本参数
水力结构
流道的结构
喷嘴的分布及空间结构
精选课件
7
二)钻头设计理论的研究
1、传统的PDC钻头设计理论
等切削体积原则; 等功率原则; 等磨损原则。
宏观结构是理想的PDC钻头结构形式,钻
头的设计应当以这种结构形式为基础。那
么,如何解决现有钻头切削齿偏磨的问题,
进一步提高钻头的质量呢?
精选课件
32
局部强化设计理论的构思
对于刮刀式PDC钻头,冠部形状、刮 刀数确定,钻头局部布齿的有效长度确 定,局部布齿的数量也即确定。
优化钻井

5优化钻井技术5.1 优化钻井的基本概念优化钻井是科学钻井的重要标志之一,它是应用最优化理论和技术寻求使钻井速度最快,钻井成本最低的钻井参数和技术措施。
对一口井全过程进行最优化处理,称为全局最优化。
对一口井的某一过程进行最优化处理,称为局部最优化。
对钻井过程的某些参数进行最优化处理,称为优选参数钻井。
优选参数钻井是应用优化理论分析影响钻井速度的因素,建立钻速方程,钻头磨损方程,钻井成本方程(目标函数)。
在此基础上确定相应的约束条件,用最优化方法确定达到最优化目标的解向量,即最优化钻井参数和技术措施。
5.2优化钻井的发展优化钻井是在喷射钻井和平衡钻井的基础上发展起来的。
(1)50年代以前,国外就有人研究钻压、转速、水力因素、泥浆性能等对钻速的影响。
当时采用高钻压、低转速、大排量钻进,未取得明显效果;(2)50-70年代,优化钻进技术发展很快,出现了各种钻进模式。
包括Sper和Moore的数学模型,古宁汉和Woods的钻头磨损方程,Woods和Gall的二元钻速方程,Young模式方程,Bourgyne 的多元钻速方程等。
(1)我国起步较晚,”6.5“期间进行了科技攻关。
油科院与辽河油田合作用阿莫柯模式进行了研究和试验,石油大学与中原油田合作,用扬格模式进行试验研究,西南石油学院与胜利油田合作,用修正的多元钻速方程进行了研究和试验,取得了一定成效5.3 影响钻井速度的因素及钻井模式方程影响钻井速度的主要因素有: 钻压、 转速、 水力因素、泥浆性能、井底压差、钻头型号、喷嘴组合、地层可钻性、地层埋藏深度、设备条件和操作水平。
上述因素又可分为相互独立和相互关联因素。
水力因素、泥浆性能、井底压差、喷嘴组合、操作水平是相互独立因素,不进入钻速方程。
而钻压、转速、地层特性、钻头类型是相互关联因素,这些因素要进入钻速方程。
5.3.1 相对独立因素对钻速的影响(1)泥浆性能对钻速的影响泥浆性能主要是泥浆密度、塑性粘度、固含、固相颗粒分散度及剪切稀释作用对钻速的影响。
深海钻井中钻头受力分析与优化设计

深海钻井中钻头受力分析与优化设计深海钻井是一项复杂而又具有挑战性的工程,需要克服许多困难和技术难题。
其中一个关键问题是钻头的受力分析与优化设计。
钻头是深海钻井中最重要的工具之一,其性能直接影响到钻井的效率和成本。
钻头在深海钻井中承受着巨大的受力。
首先,钻头需要克服地层的抗力,将钻头钻入地下。
同时,钻头还要承受来自钻井液的压力,以及钻井过程中产生的振动和冲击力。
这些受力会导致钻头的磨损和破损,降低钻井效率,甚至造成钻头的丢失。
为了更好地理解钻头的受力情况,我们可以进行受力分析。
首先,钻头在钻井过程中受到的主要受力有三个方向:径向、切向和轴向。
径向力是指钻头在钻井过程中受到的来自地层的抗力,它决定了钻头的钻进速度。
切向力是指钻头在旋转过程中受到的摩擦力,它对钻头的磨损和破损起着重要作用。
轴向力是指钻头在钻井过程中受到的来自钻井液的压力,它决定了钻头的稳定性和钻井速度。
在深海钻井中,由于水深较大,钻头还需要承受更大的水压力。
这就需要对钻头的材料和结构进行优化设计。
首先,钻头的材料需要具有良好的抗压和耐磨性能,以承受来自地层和钻井液的压力和摩擦力。
其次,钻头的结构需要具有良好的稳定性和切削性能,以保证钻头的钻进速度和钻井效率。
为了优化钻头的设计,我们可以采用一些先进的技术和方法。
首先,可以利用计算机模拟和数值分析的方法,对钻头的受力情况进行模拟和分析。
通过优化设计,可以减小钻头的受力和磨损,提高钻井效率。
其次,可以利用先进的材料和加工工艺,提高钻头的强度和耐磨性能。
例如,可以采用高强度合金材料和先进的热处理工艺,提高钻头的抗压和耐磨性能。
同时,可以采用先进的涂层技术,提高钻头的切削性能和耐磨性能。
此外,还可以采用智能化技术和装备,提高钻头的性能和效率。
例如,可以利用传感器和控制系统,实时监测和控制钻头的受力和运动状态。
通过智能化控制,可以减小钻头的受力和磨损,提高钻井效率和安全性。
综上所述,深海钻井中钻头的受力分析与优化设计是一项重要而又具有挑战性的工作。
钻井布局方案最优化方法

钻井布局方案最优化方法钻井是一项复杂的地质工程,需要考虑许多因素,比如地质条件、钻探设备、工人技能、工期成本等等。
为了提高钻井效率和质量,需要利用先进的优化方法,来选择最优的钻井布局方案。
钻井布局方案优化的局限性钻井布局方案优化是一项多因素决策问题,不同的权衡和限制因素会影响到钻井方案的选择和设计。
因此,优化目标和优化方法一定要考虑到以下几个因素:•地质条件:包括地形、地质构造、地层状况、地下水位等因素;•钻探设备:包括钻机类型、钻头规格、钻杆长度等工具设备因素;•工人技能:包括工人的技能水平、工作经验、技术素质等个人因素;•工期成本:包括项目周期、人工费用、材料费用、能源费用等项目成本。
钻井布局方案的优化目标往往是复合型的,不同的优化组合和方案可能会导致不同的优化结果和效果。
因此,钻井布局方案的优化方法必须考虑到这些因素的限制和局限性。
钻井布局方案优化的方法与原理在钻井布局方案的优化中,常见的优化方法有两种,一种是基于规则的优化方法,另一种是基于模型的优化方法。
基于规则的优化方法基于规则的优化方法是一种常见的方法,它借助手工创造的规则和经验来处理钻井布局方案的优化问题。
这种方法往往需要依赖于专家和经验和规则,因此会受制于规则显示缺陷、专家经验不足、数据资料不全等因素。
基于模型的优化方法基于模型的优化方法是一种常见的优化技术,它通常利用计算机化模型来对钻井布局方案进行数据分析和计算处理。
在这种方法中,模型会结合不同的优化算法和策略,对多种指标进行分析,以确定最优的钻井布局方案。
这种方法的优点在于可更新、可测量、可重复复现等多重优势。
基于模型的优化方法中,常见的优化算法包括:遗传算法、模拟退火算法、蚁群算法、粒子群算法等。
这些算法均具有进化和搜索的特点,适合处理多因素决策问题下的优化方案。
钻井布局方案优化的案例下面以某工程集团某钻探项目为例,介绍如何利用上述方法对钻井布局方案进行优化。
该工程集团的钻井项目地理位置特殊,周边地质条件复杂,需要考虑到地形起伏、地下水位、气候和环境影响等因素。
钻井技术的发展趋势及优化策略

钻井技术的发展趋势及优化策略近年来,随着能源需求的增加,钻探技术也随之不断发展。
钻井是石油和天然气行业的核心业务之一,作为一种高风险、高投入的技术,钻探需要不断提高效率、优化流程,以降低成本并提高产量。
在此背景下,本文将探讨钻井技术的发展趋势及优化策略。
一.钻井技术的发展趋势1. 数字化技术的应用随着数字化技术的快速发展,越来越多的钻探公司开始将自动化、无人化技术引入钻井过程中。
例如,自动化钻探系统可以自动调整钻头的位置和转速,以适应井眼变化,减少人工干预的错误率。
无人机可以利用更高效的方式检查设备,并将数据上传到云端,以进行后续分析和处理。
应用这些数字化技术不仅能够提高钻探过程的效率,还能提高安全性和可持续性,降低成本。
2. 新材料的应用高强度、高耐磨、高耐腐蚀的新材料的出现,得以满足更苛刻的钻井需求。
例如,钻头的使用寿命和效率已经显著提高,因为采用了新材料,比如纳米陶瓷和纳米涂层材料,提高了磨损性能和耐腐蚀性能。
新材料的使用还可以减少设备维护次数,节省成本。
3. 绿色、环保技术的应用严格的环保政策和更高的环保要求已经推动了行业转型升级。
钻井公司需要采用更环保的技术,以应对对环境的影响。
例如,利用再生能源,减少对化石燃料的依赖,增加光伏发电、风力发电等能源占比,以减少二氧化碳排放和其他污染物的排放。
二.钻井优化策略1. 优化钻探软件和设备通过合理调整钻探设备和软件,可以提高钻井过程的效率和准确性。
例如,通过升级设备,改善数据收集和传输的质量,以改善数据分析和处理速度。
优化钻井软件和算法,实现新的动态调整参数,以充分利用设备提供的资源和数据,从而优化井下操作。
2. 加强培训和技术管理行业技术更新速度非常快,要想利用最新技术和技巧,在设备和操作方面保持最优状态,必须不断进行技术培训和管理。
推行“带学生、带工,学会的教,会的传,懂的指”的培训方式,提高技术人员的素质和操作能力,搭建技术人员之间相互学习和交流思想的平台,以不断提高钻井过程的效率和效果。
钻井优化新技术提高如何钻井效率
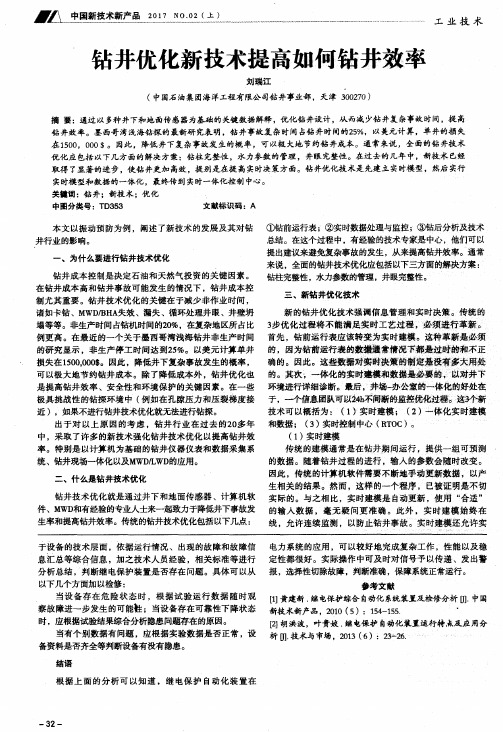
察故障进一步发生的可能1 I E ;当设备存在可靠性下降状态 新技术新产品 , 2 0 1 0( 5 ):1 5 4 - 1 5 5 . ’ 时, 应根据试验结果综合分析隐患问题存在的原因。 [ 2 】 胡洪波,叶贵姣 . 继 电保护 自 动化装置运行特 点及 应用分
当有个 别数 据有 问题 ,应根 据实验 数据 是否 正常 ,设 析 Ⅱ 】 . 技术与市场 ,2 0 1 3( 6 ):2 3  ̄ 2 6 : 备资料是否齐全等判断设备有没有隐患。
中 ,采取 了许 多的新 技术强 化钻井技 术优 化 以提高钻 井效 率 。特别 是 以计 算机 为基础 的钻井 仪器 仪表和 数据采 集系 统 、钻井现场一体化 以及M WD / L WD 的应用。 二、什么是钻井技术优化
( 1 )实时建模 传统 的建模 通 常是在 钻井期 间运 行 ,提供一 组可 预测 的数据。随着钻井过程的进行 ,输人的参数会随时改变。
本文 以振动 预 防为例 ,阐述 了新技 术 的发 展及 其对钻 ①钻前运行表 ;②实时数据处理与监控 ;③钻后分析及技术 井行业 的影 响。 总结 。在这个过程 中,有经验的技术专家是 中心 ,他们可 以 提出建议来避免复杂事故的发生,从来提高钻井效率。通常 为什么要进行钻井技术优化 来说,全面的钻井技术优化应包括以下三方面的解决方案 : 钻井 成本 控制是 决定 石油 和天然气 投 资的关键 因素 。 钻柱完整性 ,水力参数 的管理 ,井眼完整性 。 在钻井 成本 高和钻 井事故 可能 发生 的情况下 ,钻 井成本 控 三、新钻井优化技术 制尤其 重要 。钻井 技术优 化 的关键在 于减少 非作 业时 间 , 新 的钻 井优 化技 术强调 信息 管理 和实时 决策 。传统 的 诸如卡钻 、MWD / B HA 失效 、漏失 、循环处理井 眼 、井壁坍
钻井参数优化
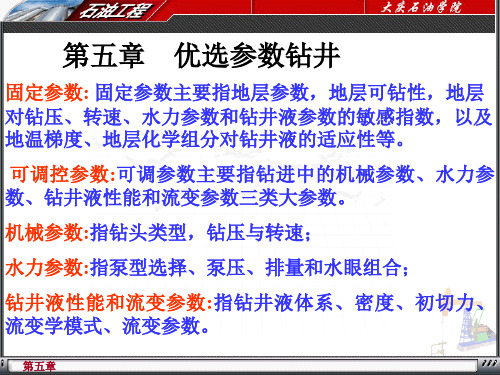
2. 钻压、转速对钻头磨损的影响
(1) 钻压、转速对牙齿磨损速度的影响
第五章
第一节
钻井参数作用机理
Q1,Q2——由钻头类型决定的系数; D1,D2——钻压影响系数,其值与牙轮 钻头尺寸有关; C1——牙齿磨损系数; Af——地层研磨性系数,其含义是当钻 压、转速和牙齿的磨损状况一定时,牙 轮钻头牙齿的磨损速度与地层的研磨性 成正比。
(1)在射流中心,由于受淹没钻井液和返回钻井液影响 较小,速度最高。在射流任一截面上,轴线上速度最高, 自中心向外速度很快降低,到射流边界上速度为零。 (2)射流出口后有一段长度,这段长度内的中心部分始 终保持刚出口时的速度VO 。这段射流的中心部分称为射 流的等速核。等速核长度以LO表示。这段射流称为射流 的初始段。超过初始段以后称为射流的基本段。
1. 射流水力参数
喷射速度
射流水力参数包括:
射流冲击力 Wj=ρdQ2/Ant 射流水功率 Pj
vj=Q/Ant
d Q
2A
3
2 nt
第五章
第二节
水力参数的优选
2. 钻头水力参数
钻头压力降
钻头水力参数包括 钻头水功率 (1)钻头压降
第五章
第二节
水力参数的优选
所以 为能量转换系数
令:
(2)钻头水功率
Pi 2 f 2 A 2 A
0 .2 pv
Lv 2
di (3.2) (3.2)
2 A
0.2 pv
(3.2 d i v )
0.2
Lv 2
di
0 .2
0 .8
Lv1.8 d 1.2 i LQ 1.2 1 2 1. 8 d i ( d i ) 4
定向井钻井工艺技术优化措施解析

定向井钻井工艺技术优化措施解析定向井钻井工艺技术是指在油气勘探中,通过控制钻具的方向和位置,使井眼能够沿着预定的路径向目标层段穿越。
定向井钻井的主要优化措施有以下几点:一、井斜测量和传感技术的优化井斜测量和传感技术是实现定向井钻井的关键技术之一。
通过优化井斜测量和传感技术,可以提高钻具的定向性能,减少井斜测量的误差,提高地面数据的准确性。
目前,常用的井斜测量和传感技术包括陀螺仪、电子罗盘和惯性测量单元等。
优化井斜测量和传感技术可以提高定向井的钻进效率和钻进质量。
二、钻头设计和选择的优化钻头是定向井钻井中最重要的钻具之一,其设计和选择直接影响了钻井的效果和成本。
为了提高钻井的效率和质量,需要优化钻头的设计和选择。
需要根据井眼的尺寸、地质条件和钻井目标,选择合适的钻头类型和尺寸。
需要根据地层的特点和钻井参数,设计合理的钻头结构和刀具配置,以提高钻进效率和降低钻头的磨损。
三、钻井液系统的优化钻井液系统是定向井钻井中不可忽视的一环,其优化可以改善井壁稳定性、控制井斜和方位、减少钻井事故。
钻井液系统的优化主要包括钻井液性能的优化和钻井液循环系统的优化。
钻井液的性能优化包括密度控制、粘度控制、润滑性能和抗腐蚀性能等。
钻井液循环系统的优化包括泥浆循环系统的设计和泥浆废弃物处理系统的优化。
钻具系统是定向井钻井中的核心装备,其优化可以提高钻具的传递能力、降低钻井事故风险。
钻具系统的优化主要包括钻杆的选择和设计、钢丝绳和液压扩散器的优化等。
钻杆的选择和设计主要考虑钻杆的强度和刚度,以及钻杆与井眼之间的摩擦力等。
钢丝绳和液压扩散器的优化主要考虑它们的传递能力和使用寿命。
钻井参数的优化可以提高钻井的效率和质量。
钻井参数的优化主要包括钻速、钻压和钻紧力的优化。
钻速的优化需要根据地质条件和钻具性能,选择合适的钻速范围。
钻压的优化需要根据井壁稳定性和钻杆的受力情况,避免钻压过大或过小。
钻紧力的优化需要根据井眼的尺寸和井斜的目标,选择合理的钻紧力范围,以保证钻具的传递能力和钻井的效果。
多功能深井钻机的钻头选择与优化方法研究
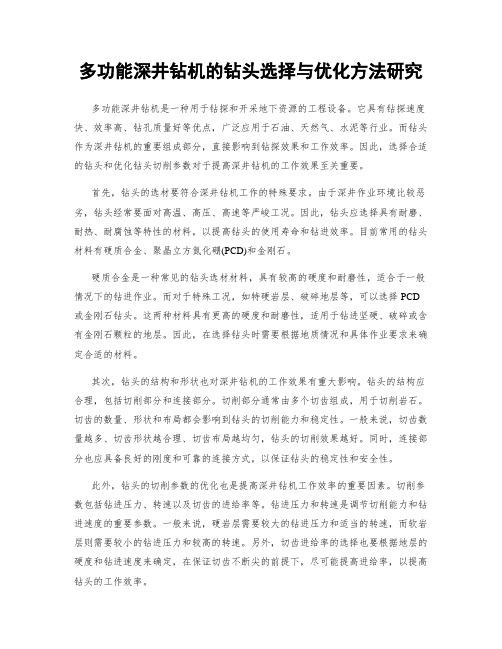
多功能深井钻机的钻头选择与优化方法研究多功能深井钻机是一种用于钻探和开采地下资源的工程设备。
它具有钻探速度快、效率高、钻孔质量好等优点,广泛应用于石油、天然气、水泥等行业。
而钻头作为深井钻机的重要组成部分,直接影响到钻探效果和工作效率。
因此,选择合适的钻头和优化钻头切削参数对于提高深井钻机的工作效果至关重要。
首先,钻头的选材要符合深井钻机工作的特殊要求。
由于深井作业环境比较恶劣,钻头经常要面对高温、高压、高速等严峻工况。
因此,钻头应选择具有耐磨、耐热、耐腐蚀等特性的材料,以提高钻头的使用寿命和钻进效率。
目前常用的钻头材料有硬质合金、聚晶立方氮化硼(PCD)和金刚石。
硬质合金是一种常见的钻头选材材料,具有较高的硬度和耐磨性,适合于一般情况下的钻进作业。
而对于特殊工况,如特硬岩层、破碎地层等,可以选择PCD 或金刚石钻头。
这两种材料具有更高的硬度和耐磨性,适用于钻进坚硬、破碎或含有金刚石颗粒的地层。
因此,在选择钻头时需要根据地质情况和具体作业要求来确定合适的材料。
其次,钻头的结构和形状也对深井钻机的工作效果有重大影响。
钻头的结构应合理,包括切削部分和连接部分。
切削部分通常由多个切齿组成,用于切削岩石。
切齿的数量、形状和布局都会影响到钻头的切削能力和稳定性。
一般来说,切齿数量越多、切齿形状越合理、切齿布局越均匀,钻头的切削效果越好。
同时,连接部分也应具备良好的刚度和可靠的连接方式,以保证钻头的稳定性和安全性。
此外,钻头的切削参数的优化也是提高深井钻机工作效率的重要因素。
切削参数包括钻进压力、转速以及切齿的进给率等。
钻进压力和转速是调节切削能力和钻进速度的重要参数。
一般来说,硬岩层需要较大的钻进压力和适当的转速,而软岩层则需要较小的钻进压力和较高的转速。
另外,切齿进给率的选择也要根据地层的硬度和钻进速度来确定,在保证切齿不断尖的前提下,尽可能提高进给率,以提高钻头的工作效率。
最后,钻头的维护与保养也是保证深井钻机工作效果的关键。
钻井液钻头设计中的优化算法研究
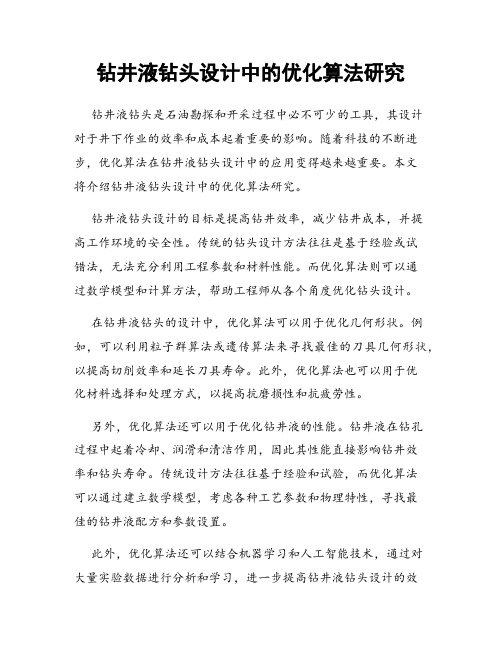
钻井液钻头设计中的优化算法研究钻井液钻头是石油勘探和开采过程中必不可少的工具,其设计对于井下作业的效率和成本起着重要的影响。
随着科技的不断进步,优化算法在钻井液钻头设计中的应用变得越来越重要。
本文将介绍钻井液钻头设计中的优化算法研究。
钻井液钻头设计的目标是提高钻井效率,减少钻井成本,并提高工作环境的安全性。
传统的钻头设计方法往往是基于经验或试错法,无法充分利用工程参数和材料性能。
而优化算法则可以通过数学模型和计算方法,帮助工程师从各个角度优化钻头设计。
在钻井液钻头的设计中,优化算法可以用于优化几何形状。
例如,可以利用粒子群算法或遗传算法来寻找最佳的刀具几何形状,以提高切削效率和延长刀具寿命。
此外,优化算法也可以用于优化材料选择和处理方式,以提高抗磨损性和抗疲劳性。
另外,优化算法还可以用于优化钻井液的性能。
钻井液在钻孔过程中起着冷却、润滑和清洁作用,因此其性能直接影响钻井效率和钻头寿命。
传统设计方法往往基于经验和试验,而优化算法可以通过建立数学模型,考虑各种工艺参数和物理特性,寻找最佳的钻井液配方和参数设置。
此外,优化算法还可以结合机器学习和人工智能技术,通过对大量实验数据进行分析和学习,进一步提高钻井液钻头设计的效果。
例如,可以利用神经网络来预测钻井液的性能和钻头的寿命,以辅助钻头设计的决策。
优化算法在钻井液钻头设计中的研究还面临一些挑战。
首先,钻井液钻头设计是一个多变量优化问题,涉及多个设计变量和多个目标函数。
如何选择合适的优化算法和建立适当的数学模型是一个难题。
其次,钻井液钻头设计中的数据收集和实验验证比较困难和昂贵。
如何充分利用有限的数据和保证模型的准确性也是一个挑战。
总结起来,钻井液钻头设计中的优化算法研究是一个重要的课题。
通过运用优化算法,可以提高钻井液钻头的效率和寿命,减少钻井成本,提高工作环境的安全性。
然而,优化算法研究在这一领域还面临挑战,包括多变量优化问题和数据收集难题。
未来的研究应该继续探索更高效的优化算法和更准确的数学模型,以推动钻井液钻头设计的发展和进步。
浅谈强化钻井作业及修井技术措施
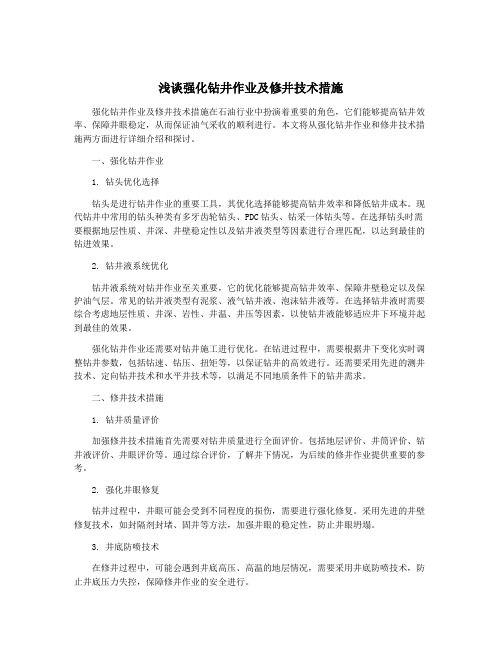
浅谈强化钻井作业及修井技术措施强化钻井作业及修井技术措施在石油行业中扮演着重要的角色,它们能够提高钻井效率、保障井眼稳定,从而保证油气采收的顺利进行。
本文将从强化钻井作业和修井技术措施两方面进行详细介绍和探讨。
一、强化钻井作业1. 钻头优化选择钻头是进行钻井作业的重要工具,其优化选择能够提高钻井效率和降低钻井成本。
现代钻井中常用的钻头种类有多牙齿轮钻头、PDC钻头、钻采一体钻头等。
在选择钻头时需要根据地层性质、井深、井壁稳定性以及钻井液类型等因素进行合理匹配,以达到最佳的钻进效果。
2. 钻井液系统优化钻井液系统对钻井作业至关重要,它的优化能够提高钻井效率、保障井壁稳定以及保护油气层。
常见的钻井液类型有泥浆、液气钻井液、泡沫钻井液等。
在选择钻井液时需要综合考虑地层性质、井深、岩性、井温、井压等因素,以使钻井液能够适应井下环境并起到最佳的效果。
强化钻井作业还需要对钻井施工进行优化。
在钻进过程中,需要根据井下变化实时调整钻井参数,包括钻速、钻压、扭矩等,以保证钻井的高效进行。
还需要采用先进的测井技术、定向钻井技术和水平井技术等,以满足不同地质条件下的钻井需求。
二、修井技术措施1. 钻井质量评价加强修井技术措施首先需要对钻井质量进行全面评价。
包括地层评价、井筒评价、钻井液评价、井眼评价等。
通过综合评价,了解井下情况,为后续的修井作业提供重要的参考。
2. 强化井眼修复钻井过程中,井眼可能会受到不同程度的损伤,需要进行强化修复。
采用先进的井壁修复技术,如封隔剂封堵、固井等方法,加强井眼的稳定性,防止井眼坍塌。
3. 井底防喷技术在修井过程中,可能会遇到井底高压、高温的地层情况,需要采用井底防喷技术,防止井底压力失控,保障修井作业的安全进行。
环空修井是一种钻井井眼受损时进行修复的技术手段,采用封隔、固井等方法对井眼进行修复,使井眼恢复原有稳定状态。
强化钻井作业及修井技术措施对于石油行业的发展至关重要。
通过对钻头、钻井液系统、钻井施工等方面的优化,能够提高钻井效率,降低钻井成本,保障井眼稳定。
现河油田快速钻井优化技术
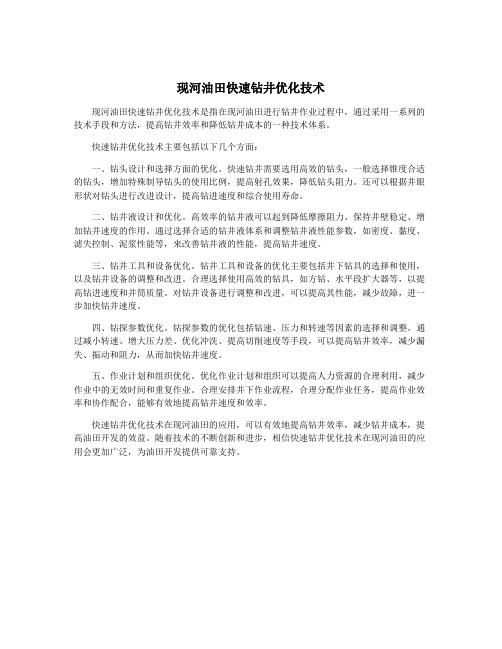
现河油田快速钻井优化技术现河油田快速钻井优化技术是指在现河油田进行钻井作业过程中,通过采用一系列的技术手段和方法,提高钻井效率和降低钻井成本的一种技术体系。
快速钻井优化技术主要包括以下几个方面:一、钻头设计和选择方面的优化。
快速钻井需要选用高效的钻头,一般选择锥度合适的钻头,增加特殊制导钻头的使用比例,提高射孔效果,降低钻头阻力。
还可以根据井眼形状对钻头进行改进设计,提高钻进速度和综合使用寿命。
二、钻井液设计和优化。
高效率的钻井液可以起到降低摩擦阻力、保持井壁稳定、增加钻井速度的作用。
通过选择合适的钻井液体系和调整钻井液性能参数,如密度、黏度、滤失控制、泥浆性能等,来改善钻井液的性能,提高钻井速度。
三、钻井工具和设备优化。
钻井工具和设备的优化主要包括井下钻具的选择和使用,以及钻井设备的调整和改进。
合理选择使用高效的钻具,如方钻、水平段扩大器等,以提高钻进速度和井筒质量。
对钻井设备进行调整和改进,可以提高其性能,减少故障,进一步加快钻井速度。
四、钻探参数优化。
钻探参数的优化包括钻速、压力和转速等因素的选择和调整。
通过减小转速、增大压力差、优化冲洗、提高切削速度等手段,可以提高钻井效率,减少漏失、振动和阻力,从而加快钻井速度。
五、作业计划和组织优化。
优化作业计划和组织可以提高人力资源的合理利用,减少作业中的无效时间和重复作业。
合理安排井下作业流程,合理分配作业任务,提高作业效率和协作配合,能够有效地提高钻井速度和效率。
快速钻井优化技术在现河油田的应用,可以有效地提高钻井效率,减少钻井成本,提高油田开发的效益。
随着技术的不断创新和进步,相信快速钻井优化技术在现河油田的应用会更加广泛,为油田开发提供可靠支持。
如何提高钻具组合和钻头水眼组合及优化钻井参数的探究
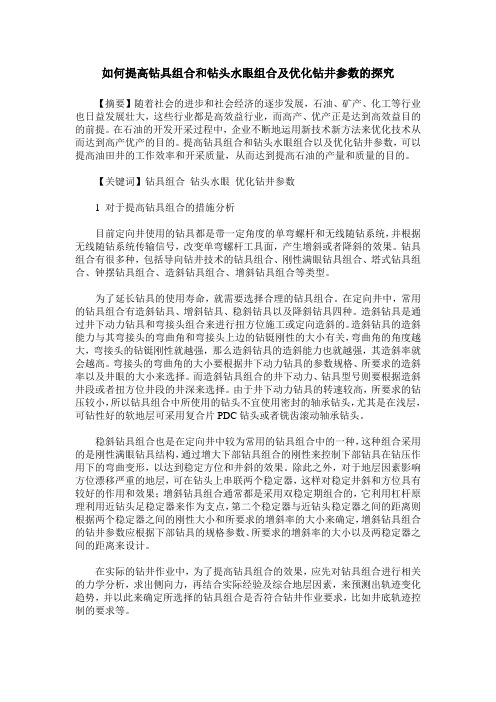
如何提高钻具组合和钻头水眼组合及优化钻井参数的探究【摘要】随着社会的进步和社会经济的逐步发展,石油、矿产、化工等行业也日益发展壮大,这些行业都是高效益行业,而高产、优产正是达到高效益目的的前提。
在石油的开发开采过程中,企业不断地运用新技术新方法来优化技术从而达到高产优产的目的。
提高钻具组合和钻头水眼组合以及优化钻井参数,可以提高油田井的工作效率和开采质量,从而达到提高石油的产量和质量的目的。
【关键词】钻具组合钻头水眼优化钻井参数1 对于提高钻具组合的措施分析目前定向井使用的钻具都是带一定角度的单弯螺杆和无线随钻系统,并根据无线随钻系统传输信号,改变单弯螺杆工具面,产生增斜或者降斜的效果。
钻具组合有很多种,包括导向钻井技术的钻具组合、刚性满眼钻具组合、塔式钻具组合、钟摆钻具组合、造斜钻具组合、增斜钻具组合等类型。
为了延长钻具的使用寿命,就需要选择合理的钻具组合。
在定向井中,常用的钻具组合有造斜钻具、增斜钻具、稳斜钻具以及降斜钻具四种。
造斜钻具是通过井下动力钻具和弯接头组合来进行扭方位施工或定向造斜的。
造斜钻具的造斜能力与其弯接头的弯曲角和弯接头上边的钻铤刚性的大小有关,弯曲角的角度越大,弯接头的钻铤刚性就越强,那么造斜钻具的造斜能力也就越强,其造斜率就会越高。
弯接头的弯曲角的大小要根据井下动力钻具的参数规格、所要求的造斜率以及井眼的大小来选择。
而造斜钻具组合的井下动力、钻具型号则要根据造斜井段或者扭方位井段的井深来选择。
由于井下动力钻具的转速较高,所要求的钻压较小,所以钻具组合中所使用的钻头不宜使用密封的轴承钻头,尤其是在浅层,可钻性好的软地层可采用复合片PDC钻头或者铣齿滚动轴承钻头。
稳斜钻具组合也是在定向井中较为常用的钻具组合中的一种,这种组合采用的是刚性满眼钻具结构,通过增大下部钻具组合的刚性来控制下部钻具在钻压作用下的弯曲变形,以达到稳定方位和井斜的效果。
除此之外,对于地层因素影响方位漂移严重的地层,可在钻头上串联两个稳定器,这样对稳定井斜和方位具有较好的作用和效果;增斜钻具组合通常都是采用双稳定期组合的,它利用杠杆原理利用近钻头足稳定器来作为支点,第二个稳定器与近钻头稳定器之间的距离则根据两个稳定器之间的刚性大小和所要求的增斜率的大小来确定,增斜钻具组合的钻井参数应根据下部钻具的规格参数、所要求的增斜率的大小以及两稳定器之间的距离来设计。
论如何对钻修井施工设计进行必要的优化及处理
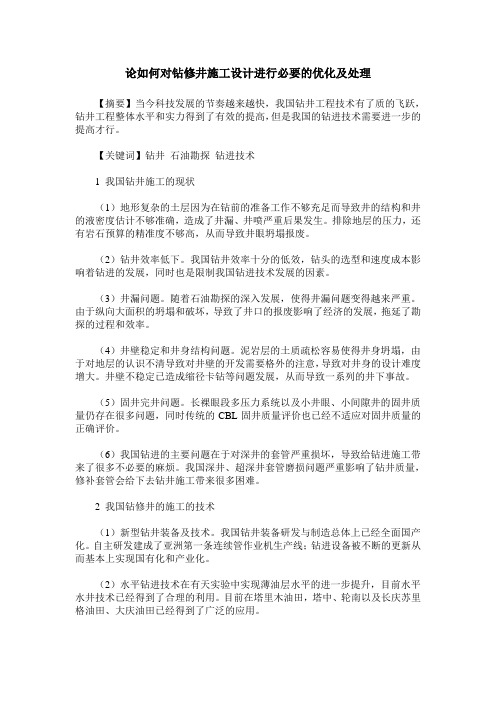
论如何对钻修井施工设计进行必要的优化及处理【摘要】当今科技发展的节奏越来越快,我国钻井工程技术有了质的飞跃,钻井工程整体水平和实力得到了有效的提高,但是我国的钻进技术需要进一步的提高才行。
【关键词】钻井石油勘探钻进技术1 我国钻井施工的现状(1)地形复杂的土层因为在钻前的准备工作不够充足而导致井的结构和井的液密度估计不够准确,造成了井漏、井喷严重后果发生。
排除地层的压力,还有岩石预算的精准度不够高,从而导致井眼坍塌报废。
(2)钻井效率低下。
我国钻井效率十分的低效,钻头的选型和速度成本影响着钻进的发展,同时也是限制我国钻进技术发展的因素。
(3)井漏问题。
随着石油勘探的深入发展,使得井漏问题变得越来严重。
由于纵向大面积的坍塌和破坏,导致了井口的报废影响了经济的发展,拖延了勘探的过程和效率。
(4)井壁稳定和井身结构问题。
泥岩层的土质疏松容易使得井身坍塌,由于对地层的认识不清导致对井壁的开发需要格外的注意,导致对井身的设计难度增大。
井壁不稳定已造成缩径卡钻等问题发展,从而导致一系列的井下事故。
(5)固井完井问题。
长裸眼段多压力系统以及小井眼、小间隙井的固井质量仍存在很多问题,同时传统的CBL固井质量评价也已经不适应对固井质量的正确评价。
(6)我国钻进的主要问题在于对深井的套管严重损坏,导致给钻进施工带来了很多不必要的麻烦。
我国深井、超深井套管磨损问题严重影响了钻井质量,修补套管会给下去钻井施工带来很多困难。
2 我国钻修井的施工的技术(1)新型钻井装备及技术。
我国钻井装备研发与制造总体上已经全面国产化。
自主研发建成了亚洲第一条连续管作业机生产线;钻进设备被不断的更新从而基本上实现国有化和产业化。
(2)水平钻进技术在有天实验中实现薄油层水平的进一步提升,目前水平水井技术已经得到了合理的利用。
目前在塔里木油田,塔中、轮南以及长庆苏里格油田、大庆油田已经得到了广泛的应用。
(3)平衡钻井和气体钻井的技术的迅猛发展。
全井段钻头序列的优化方法
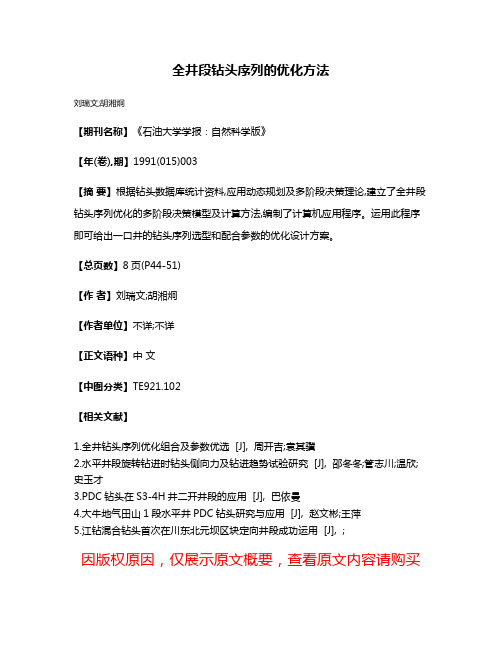
全井段钻头序列的优化方法
刘瑞文;胡湘炯
【期刊名称】《石油大学学报:自然科学版》
【年(卷),期】1991(015)003
【摘要】根据钻头数据库统计资料,应用动态规划及多阶段决策理论,建立了全井段钻头序列优化的多阶段决策模型及计算方法,编制了计算机应用程序。
运用此程序即可给出一口井的钻头序列选型和配合参数的优化设计方案。
【总页数】8页(P44-51)
【作者】刘瑞文;胡湘炯
【作者单位】不详;不详
【正文语种】中文
【中图分类】TE921.102
【相关文献】
1.全井钻头序列优化组合及参数优选 [J], 周开吉;袁其骥
2.水平井段旋转钻进时钻头侧向力及钻进趋势试验研究 [J], 邵冬冬;管志川;温欣;史玉才
3.PDC钻头在S3-4H井二开井段的应用 [J], 巴依曼
4.大牛地气田山1段水平井PDC钻头研究与应用 [J], 赵文彬;王萍
5.江钻混合钻头首次在川东北元坝区块定向井段成功运用 [J], ;
因版权原因,仅展示原文概要,查看原文内容请购买。
怎样改进PDC钻头结构以提高定向效率
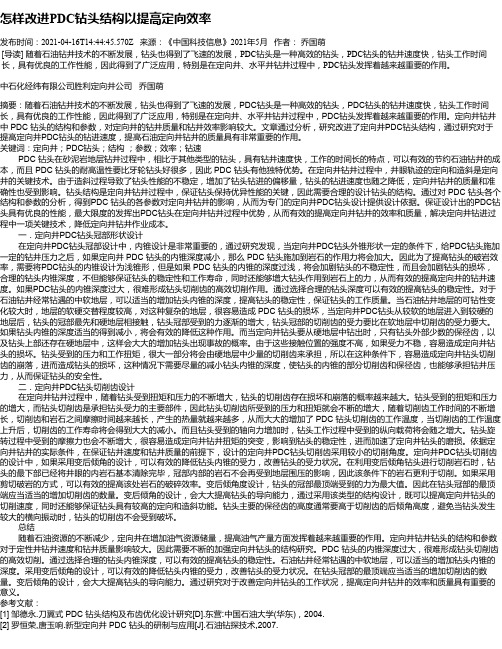
怎样改进PDC钻头结构以提高定向效率发布时间:2021-04-16T14:44:45.570Z 来源:《中国科技信息》2021年5月作者:乔国萌[导读] 随着石油钻井技术的不断发展,钻头也得到了飞速的发展,PDC钻头是一种高效的钻头,PDC钻头的钻井速度快,钻头工作时间长,具有优良的工作性能,因此得到了广泛应用,特别是在定向井、水平井钻井过程中,PDC钻头发挥着越来越重要的作用。
中石化经纬有限公司胜利定向井公司乔国萌摘要:随着石油钻井技术的不断发展,钻头也得到了飞速的发展,PDC钻头是一种高效的钻头,PDC钻头的钻井速度快,钻头工作时间长,具有优良的工作性能,因此得到了广泛应用,特别是在定向井、水平井钻井过程中,PDC钻头发挥着越来越重要的作用。
定向井钻井中 PDC 钻头的结构和参数,对定向井的钻井质量和钻井效率影响较大。
文章通过分析,研究改进了定向井PDC钻头结构,通过研究对于提高定向井PDC钻头的钻进速度,提高石油定向井钻井的质量具有非常重要的作用。
关键词:定向井;PDC钻头;结构;参数;效率;钻速PDC 钻头在砂泥岩地层钻井过程中,相比于其他类型的钻头,具有钻井速度快,工作的时间长的特点,可以有效的节约石油钻井的成本,而且 PDC 钻头的耐高温性要比牙轮钻头好很多,因此 PDC 钻头有他独特优势。
在定向井钻井过程中,井眼轨迹的定向和造斜是定向井的关键技术。
由于造斜过程导致了钻头性能的不稳定,增加了钻头钻进的偏移量,钻头的钻进速度也随之降低,定向井钻井的质量和准确性也受到影响。
钻头结构是定向井钻井过程中,保证钻头保持优异性能的关键,因此需要合理的设计钻头的结构。
通过对 PDC 钻头各个结构和参数的分析,得到PDC 钻头的各参数对定向井钻井的影响,从而为专门的定向井PDC钻头设计提供设计依据。
保证设计出的PDC钻头具有优良的性能,最大限度的发挥出PDC钻头在定向井钻井过程中优势,从而有效的提高定向井钻井的效率和质量,解决定向井钻进过程中一项关键技术,降低定向井钻井作业成本。
通用钻头的持续优化和发展
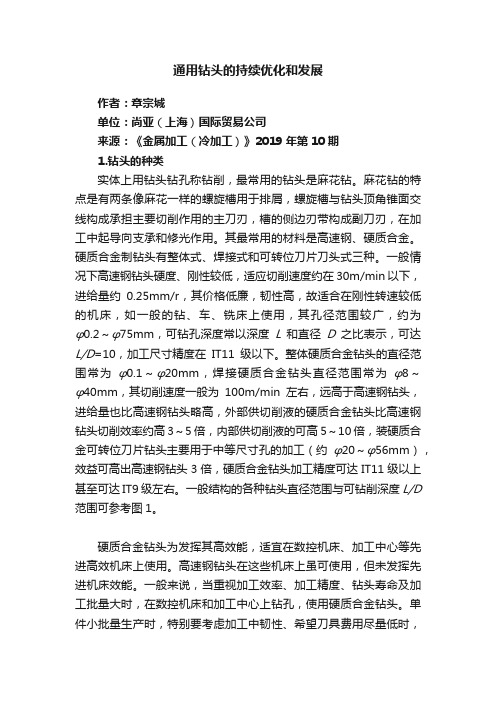
通用钻头的持续优化和发展作者:章宗城单位:尚亚(上海)国际贸易公司来源:《金属加工(冷加工)》2019年第10期1.钻头的种类实体上用钻头钻孔称钻削,最常用的钻头是麻花钻。
麻花钻的特点是有两条像麻花一样的螺旋槽用于排屑,螺旋槽与钻头顶角锥面交线构成承担主要切削作用的主刀刃,槽的侧边刃带构成副刀刃,在加工中起导向支承和修光作用。
其最常用的材料是高速钢、硬质合金。
硬质合金制钻头有整体式、焊接式和可转位刀片刀头式三种。
一般情况下高速钢钻头硬度、刚性较低,适应切削速度约在30m/min以下,进给量约0.25mm/r,其价格低廉,韧性高,故适合在刚性转速较低的机床,如一般的钻、车、铣床上使用,其孔径范围较广,约为φ0.2~φ75mm,可钻孔深度常以深度L和直径D之比表示,可达L/D=10,加工尺寸精度在IT11级以下。
整体硬质合金钻头的直径范围常为φ0.1~φ20mm,焊接硬质合金钻头直径范围常为φ8~φ40mm,其切削速度一般为100m/min左右,远高于高速钢钻头,进给量也比高速钢钻头略高,外部供切削液的硬质合金钻头比高速钢钻头切削效率约高3~5倍,内部供切削液的可高5~10倍,装硬质合金可转位刀片钻头主要用于中等尺寸孔的加工(约φ20~φ56mm),效益可高出高速钢钻头3倍,硬质合金钻头加工精度可达IT11级以上甚至可达IT9级左右。
一般结构的各种钻头直径范围与可钻削深度L/D 范围可参考图1。
硬质合金钻头为发挥其高效能,适宜在数控机床、加工中心等先进高效机床上使用。
高速钢钻头在这些机床上虽可使用,但未发挥先进机床效能。
一般来说,当重视加工效率、加工精度、钻头寿命及加工批量大时,在数控机床和加工中心上钻孔,使用硬质合金钻头。
单件小批量生产时,特别要考虑加工中韧性、希望刀具费用尽量低时,可使用高速钢钻头。
以上这几种钻头,如可以钻削大部分工件材料如碳钢、铸铁、不锈钢、有色金属及合金钢等,则称为通用钻头。
- 1、下载文档前请自行甄别文档内容的完整性,平台不提供额外的编辑、内容补充、找答案等附加服务。
- 2、"仅部分预览"的文档,不可在线预览部分如存在完整性等问题,可反馈申请退款(可完整预览的文档不适用该条件!)。
- 3、如文档侵犯您的权益,请联系客服反馈,我们会尽快为您处理(人工客服工作时间:9:00-18:30)。
tew oesci t cueo rl gbt pi ztn po oe o t n rs l r et sces l xein e h hl etns u tr f d ln io t ai , rp sdsl i sf i a poc s uc s u p r c . o r a ii mi o u o o mir j f e e 【 yw r s Fl fc; r l oeBt t cue Ke o d ul ae A di l;isr tr l — lh u
\
B旰 程
泥 流j 历 三 阶 藁 j 的 个段 l } 经
图1
首 先 我 们 采 用 减 刀 法调 整 了 刀具 的间 隔 。 谓 减 刀 法 就 是 将 斜 面 所 处 两 条 渐 开 线 上 刀 具 相 对 密集 、 距 较 小 的 刀具 间 隔 拆 除 , 保 证 切 间 在
i lme tto ewh l e to mp e n ain o t oes cin a f h Uigmeho .I r cia p iain i rl n fiin y i o g n t d n p a t la pl to t dil g e ce c sn t h.T i r ce a aye h e sns n c c s i hi hsat l n zster ao ,o i l
1 袁 店 一 矿 回 风 井 钻进 施工 中遇 到 的 问 题
割 带 完 整 和 钻 头 稳 定 的 情 况 下 , 求 刀 间距 最 大 。 在第 一 条 渐 开 线 上 力 袁 店 一 矿 南 风 井 位 于 淮 北 市 濉 溪 县 五 沟 镇 境 内 ,井 筒 设 计 净 径 拆除第 n圈刀 , 第 1圈刀必须在第二条 渐开线上拆除 , 则 每圈刀只 52 .m, 设 计 钻 井 直 径 71 . m, 钻 井 深 度 3 1 0 m, 其 中 粘 土 层 总 厚 度 拆除一把刀 , 保留刀座。通过调整后 , 在粘 土层 和钙质粘 土层 中钻进 , 158 m, 质 粘 土 层 总厚 度 2 .5 泥 岩 总 厚 度 3 .h , 它 地 层 总 钻头泥包 的程度和次数 略有 降低 , 6 .9 钙 59 m, 87 n 其 泥包 的面积大大下降 , 泥包 的位置 厚度 7 .5 04 m。设 计 采 用 全 断 面 一 次 钻 进 方 案施 工 , 井 施 工 选 用 的主 发生 在 平 底 部 位 。 钻 要设 备 有 : 型 A 3 ,o 0型动 力 头竖 井 钻 机 一 台套 ,55螺 杆 空 压 新 D1O1o L. 其 次 ,在 第 一 种 处 理 方 法 的 基 础上 我 们 又 改 变 了 吸 收 1的 位 置 , 3 机 5台 , 中 两 台 正 常 使 用 , 台 备 用 。 71 钻 头 由 中55 钻 头 改 将侧 吸收 口改为 中心吸 收 口, 其 三 .m .m 同时拆 除中心 刀一把 , 以加大 泥浆冲洗 制而成 , 钻头 为圆 台形 , 布置滚 刀 5 共 O把 , 中边 刀 6把 . 其 中心 刀 2 量 。 过 调 整 后 , 粘 土 层 和 钙 质 粘 土 层 中 钻进 , 头 平 底 部 位 泥 包 的 通 在 钻 把, 刀4 正 2把 , 面 处 按 渐 开 线 对 称 布 置 ; 底 部 分 滚 刀 的 布 置 力 求 程度 有 所 缓 解 。 斜 平 刀具 间距 最 大 , 时考 虑 到钻 头 的 稳 定 性 , 可 能使 刀 具 均 匀 分 布 。 同 尽 在 在 风化泥岩段钻进 时 . 我们仍采 用中心吸收 口循环泥浆 , 但中心 斜 面位 置 和平 底 中心 位 置 各 设 吸 收 口一 个 。就 71 钻 头而 言 . .m 随着 刀的数量不 同。采用一把 中心刀钻进时 , 平均进尺 01m/ 采用两把 .l h; 切割半径的缩小, 刀具 的密 集 度 越 来 越 高 , 具 间 的 间 距 也 逐 渐 变 小 , 中心 刀钻 进 时 , 均 进 尺 00 5 l 刀 平 .7m/。 l 在 切 割 半 径 21 至 1 m 处 的渐 开 线 上 , .m . 5 刀具 相 对 密集 。 实 践证 明 , 粘 土 层 和 钙 质 粘 土 层 钻 进 时 , 尽 可 能 使 刀 具 问 距 在 应
பைடு நூலகம்
( h n o l n n tu t n Gr u o p r t n Hu e An u ,3 0 4 h n ) C i a C a Mi eCo sr ci o p C r o a o ,  ̄b i h i 5 4 ,C ia o i 2
【 btatAt r facuto r et rl gp g m o d ln n t ai o l , n o e t i p v ed l ge i ec f e A s c]f r b e con f e n d l r r f rl go eb s f a i r r o m r et rl fc ny o t r ea i c i i o a i i n h s w d o h ii n i h
0 引 言
随 着 矿 井 建设 技 术 的发 展 , 井 法 凿 井 的新 技 术 、 工 艺 、 设 备 钻 新 新 也 不 断 出 现 。 型 A 3 /0 0型竖 井 钻 机 的研 制 成 功 , 志 着 大 扭 矩 新 DI010 标
\ \ \
钻机的诞生 , 它将 减少 钻进分级级数 , 实现并级钻进 , 同时也 为提 高钻 井 速 度 , 短 钻 井 工期 奠定 了坚 实 的基 础 。 型 A 3 /0 0型 竖 井 钻 缩 新 D10 10 机 研 制 成 功 以 前 ,我 国 引 进 和 自行 设 计 制 造 的 大 型 竖 井 钻 机 主要 有 L O10 、Z 97 0 、 S 95 o和 A 1/0 4 /0 0 S 一 /0 A 一 ,o S 280型 四种 类 型 。采 用 以 上 钻 机施工钻井直 径为 71 的井筒 时, . m 受钻 机扭矩 限制 , 一般至少 需要 分 二 级 钻 进 才 能 完 成 ,而采 用 新 型 A 3 /0 0型 钻机 施 工 则 只 需 一 D1010 级钻进便可完成 , 实现一钻成井 。但 采用全断面钻进方案施工 71 .m 井筒时 , 因切割带宽度大 , 破岩面积大, 钻进效率受钻 头结 构形式和泥 浆 冲洗量的影响较大 。 如何提高钻进效率 , 发挥新 型钻机 的优势 . 就必 须从优化钻头的结构人手。
率 并 不 高 , 文 就 其 原 因进 行 分 析 , 全 断 面一 次 钻 进 钻 头 结 构 进行 优 化 , 出 了解 决 方 案 , 类 似 工 程施 工提 供 了成 功 的 经 验 。 本 对 提 为
【 关键词】 全断面 ; 钻井; 钻头结构
FulFa ea Drlig Bi tmia in o h r cur l c il tOp i z to ft eStu t e n ZHENG - e Lifng
21 年 01
第5 期
SIN E E H O O YIF R TO CE C &T C N L G O MA IN N
O矿业论坛O
科技信息
全断面钻井钻头结构的优化
郑立 锋 ( 中煤 矿 山建设集 团有 限责 任公 司 安徽
淮北
2 54 3 0 4)
【 摘 要I 在扼要介 绍了近年 来钻井法 凿井方案的基础上, 为了提 高钻进效率 , 研究 实施 了全断面一次钻进 的方法。 在实际应用中其钻进效