铸铁冒口设计手册
冒口设计参考
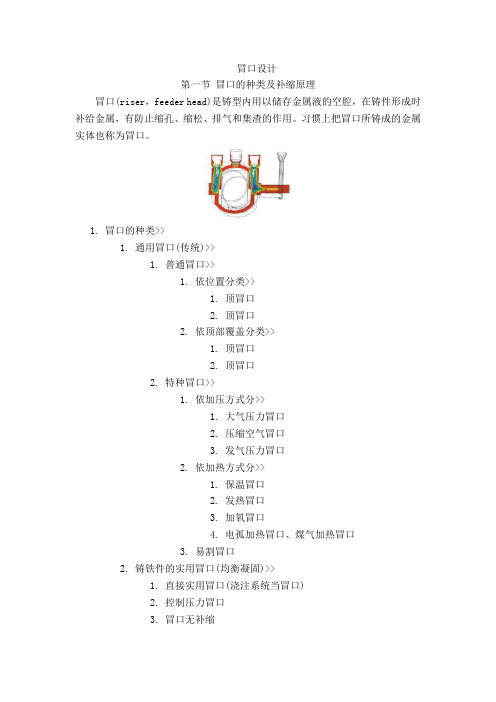
冒口设计第一节冒口的种类及补缩原理冒口(riser,feeder head)是铸型内用以储存金属液的空腔,在铸件形成时补给金属,有防止缩孔、缩松、排气和集渣的作用。
习惯上把冒口所铸成的金属实体也称为冒口。
1.冒口的种类>>1.通用冒口(传统)>>1.普通冒口>>1.依位置分类>>1.顶冒口2.顶冒口2.依顶部覆盖分类>>1.顶冒口2.顶冒口2.特种冒口>>1.依加压方式分>>1.大气压力冒口2.压缩空气冒口3.发气压力冒口2.依加热方式分>>1.保温冒口2.发热冒口3.加氧冒口4.电孤加热冒口、煤气加热冒口3.易割冒口2.铸铁件的实用冒口(均衡凝固)>>1.直接实用冒口(浇注系统当冒口)2.控制压力冒口3.冒口无补缩2.冒口形状冒口的形状有圆柱形、球顶圆柱形、长(腰)圆柱形、球形及扁球形等多种3.通用冒口补缩原理>>1.基本条件>>1.冒口凝固时间大于或等于铸件(被补缩部分)的凝固时间2.有足够的金属液补充铸件的液态收缩和凝固收缩,补偿浇注后型腔扩大的体积3.在凝固期间,冒口和被补缩部位之间存在补缩通道,扩张角向着冒口2.选择冒口位置的原则>>1.冒口应就近设在铸件热节(hotspot)的上方或侧旁2.冒口应尽量设在铸件最高、最厚的部位。
对低处的热节增设补贴或使用冷铁,造成补缩的有利条件3.冒口不应设在铸件重要的、受力大的部位,以防组织粗大降低强度4.冒口位置不要选在铸造应力集中处,应注意减轻对铸件的收缩阻碍,以免引起裂纹5.尽量用一个冒口同时补缩几个热节或铸件6.冒口布置在加工面上,可节约铸件精整工时,零件外观好7.不同高度上的冒口,应用冷铁使各个冒口的补缩范围隔开3.冒口有效补缩距离的确定>>冒口的有效补缩距离为冒口作用区与末端区长度之和,它是确定冒口数目的依据,与铸件结构、合金成分及凝固特性、冷却条件、对铸件质量要求的高低等多种因素有关,简称为冒口补缩距离1.铸钢件冒口的补缩距离有色合金的冒口补缩距离外冷铁的影响补贴(padding)的应用第二节铸钢件冒口的设计与计算铸钢件冒口属于通用冒口,其计算原理适用于实行顺序凝固的一切合金铸件。
可锻铸铁件冒口设计

可锻铸铁件冒口设计铸铁是一种常用的材料,广泛应用于制造行业。
在铸铁制品的生产中,冒口设计是至关重要的,它直接影响到产品质量和加工成本。
正确的冒口设计可以有效地避免缺陷的产生,提高产品的成形质量,同时也可以降低后续加工的难度和成本。
本文将介绍可锻铸铁件冒口设计的相关知识,并提出一种合理的冒口设计方案。
一、可锻铸铁件的特点可锻铸铁是一种含碳量较高的铸铁材料,其强度和硬度较高,具有较好的可锻性,适用于锻造和精密加工。
可锻铸铁件通常用于制造汽车零部件、机械零件等需要高强度和耐磨性的工件。
由于可锻铸铁的成分和性能特点,其在铸造过程中对冒口设计有着特殊的要求。
二、冒口设计原则1.冒口位置:冒口应设置在可锻铸铁件的最高点,以便将浮渣和气泡排除。
通常情况下,冒口位置应位于铸件的上部,离毛口处一定距离。
2.冒口形状:冒口应设计成易于开启和清理的形状,避免产生断口和裂纹。
常见的冒口形状有圆形、方形和椭圆形等,根据铸件的形状和结构来选择合适的冒口形状。
3.冒口尺寸:冒口的尺寸应根据铸件的大小和结构来确定,通常情况下,冒口的面积越大,排气和排渣效果越好。
但是也要避免过大的冒口导致浪费材料和增加加工成本。
4.冒口数量:根据可锻铸铁件的结构和复杂程度,确定冒口的数量和位置。
通常情况下,大型和复杂结构的铸件需要设置多个冒口,以确保浇注材料充分进入铸型腔。
5.冒口连接:冒口应与铸件的毛口连接,以确保铸注产物的完整性和一致性。
冒口的连接处应设计成光滑和密封的结构,避免产生漏料和漏底等问题。
三、可锻铸铁件冒口设计方案针对可锻铸铁件的特点和冒口设计原则,提出一种合理的冒口设计方案:1. 冒口位置:冒口设置在铸件的最高点,离毛口处约5-10mm,以便排气和排渣。
冒口位置应经过精确计算和模拟,确保冒口的位置准确无误。
2.冒口形状:冒口设计为圆形或椭圆形,便于开启和清理。
冒口的形状应光滑和密封,减少产生断口和裂纹的可能性。
3.冒口尺寸:根据铸件的大小和结构确定冒口的尺寸,通常情况下,冒口的直径或长宽比应为1:3-1:5、冒口尺寸的选择应考虑到浇注材料的流动性和铸件的充实度。
铸铁件冒口设计手册

铸铁件冒口设计手册诸葛胜福士科铸造材料(中国)有限公司铸铁冒口设计手册一、概述冒口是一个个储存金属液的空腔。
其主要作用是在铸件成形过程中提供由于体积变化所需要补偿的金属液,以防止在铸件中出现的收缩类型缺陷(如图1和图2所示),而这些需要补偿的体积变化可能有:图1 各种缩孔图2 缩孔生产图a)和冒口的补缩图b)1—一次缩孔 2—二次缩孔 3—缩松 1—缩孔 2—型腔胀大 3—铸件(虚线以内) 4—显微缩松 5—缩陷(缩凹,外缩孔)(1)铸型的胀大(2)金属的液态收缩(3)金属的凝固收缩补偿这些体积变化所需要的金属液量随着铸型和金属种类的不同而异。
此外,冒口还有排气及浮渣和非金属夹杂物的作用。
铸件制成后,冒口部分(残留在铸件上的凸块)将从铸件上除去。
由此,在保证铸件质量要求的前提下,冒口应尽可能的小些,以节省金属液,提高铸件成品率。
由此冒口的补缩效率越高,冒口将越小,铸件成品率越高、越经济。
FOSECO公司的发热保温冒口具有高达35%的补缩效率;因而,具有极高的成品率和极其优越的经济性。
在金属炉料价格飞涨的情况下,其优越性显得尤其突出。
另外,高品质发热保温冒口,及其稳定可靠的产品质量是获得高品质铸件的重要手段和可靠的质量保证。
二、铸铁的特点铸钢和铸铁都是铁碳合金,它们在凝固收缩过程中有共同之处)如凝固前期均析出初生奥氏体树枝晶,都存在着液态、凝固态和固态下的收缩),但也有不同的特点。
其根本不同之处是铸铁在凝固后期有“奥氏体+石墨”的共晶转变,析出石墨而发生体积膨胀,从而可部分地或全部抵消凝固前期所发生的体积收缩,即,具备有“自补缩的能力”。
因此在铸型刚性足够大时,铸铁件可以不设冒口或采用较小的冒口进行补缩。
灰铸铁在共晶转变过程中析出石墨,并在与枝晶间的液体直接接触的尖端优先长大,其石墨长大时所产生的体积膨胀直接作用在晶间液体上,进行“自补缩”。
对于一般低牌号的灰铁铸件,因碳硅含量高,石墨化比较完全,其体积膨胀量足以补偿凝固时的体收缩,故不需要设置冒口,只放排气口。
铸铁件冒口设计.

5 冒口个数(均衡段的个数)
均衡段 冒口位置
均衡段
6 无冒口铸造工艺
无冒口铸造的本质是浇口当冒口
7 浇口当冒口补缩工艺
(1)补缩模型
(2)浇注系统流通效应:金属液流
过、通过直浇道、横浇道、内浇道 时,周围的型砂被加热,凝固时间 延长的热效应。为此,小的浇注系 统模数可以有长的凝固时间。流通 效应系数推荐为: f直浇道流通效应系数=0.70~0.80 f横浇道流通效应系数=0.75~0.85 f内浇道流通效应系数=0.35~0.40
10 铸铁件冒口系列
1989年国家科委成都均衡凝固推广班
谢 谢!
铸造技术杂志社祝会议圆满成功
提高铸造企业工艺水平和铸件品质
提高中国铸件在国际市场上的竞争力
Qm=
G Mc3
(2)球铁件收缩时间分数
Pc=
1.0 e
(0.65Mc+0.01Qm)
3 冒口体模数MR MR=f1f2f3Mc
f1 ——冒口平衡系数 取f1=1.2
f2 ——收缩模数系数 f2=√Pc f3 ——冒口压力系数 f3=1.1~1.3
4 冒口颈模数MN
MN=fp.f2.f4 Mc
(3)直浇道模数 MZ MZ=f直.f1f2f3Mc
f1 ——冒口平衡系数 取f1=1.2
f2 ——收缩模数系数 f3 ——冒口压力系数 f3=1.1-1.3 f直浇道流通效应系数=0.70-0.80
(4)横浇道模数 Mh
Mh=f横.f2.Mc
f2 ——收缩模数系数 f横浇道流通效应系数=0.75~0.85
(5)内浇道模数Mn Mn=f内f2.f4Mc
板类铸铁件的冒口设计
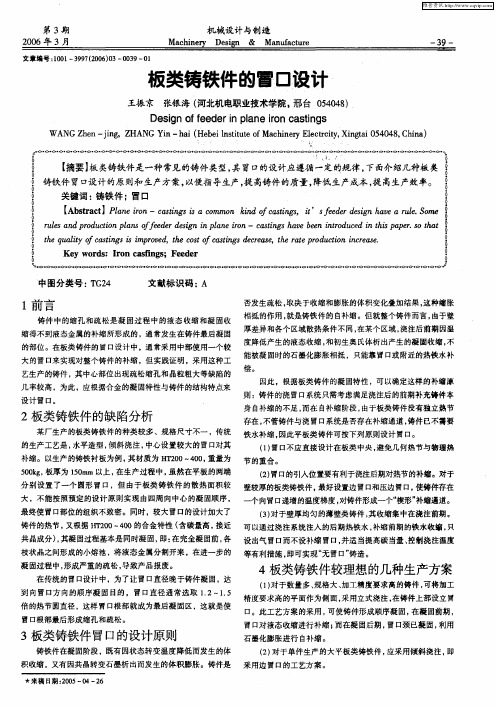
缩得不 到液态金属的补缩所形成 的,通 常发生 在铸件最后凝固 的部位 。在板类铸件的冒E设计 中,通 常采用 中部使用一个较 l 大的冒 口来实现对整个铸件 的补缩 ,但实践证 明 ,采用这种工 艺生产 的铸件 ,其中心部位 出现疏松缩孔 和晶粒粗大等缺陷的 几率较高 ,为此 ,应根据合金 的凝 固特性与铸件 的结构特点来
-‘ ・‘ ・‘ ・ ・ ・ ・ - ・ ・ ・‘ ・ ・ ・ ・ ・ ・ ・‘ - - ‘ ‘ ‘ ‘ ‘ ‘ ‘ ‘ ‘ ‘ - ‘ ‘ ‘ -
1 前言
铸件 中的缩孔和疏 松是凝 固过程 中的液态 收缩和凝 固收
否发生疏松 , 取决 于收缩和膨胀 的体积变化叠加结果 , 这种缩胀 相抵的作用 , 就是铸铁 件的 自补 缩。但就整个铸件而言 , 由于壁 厚差异 和各个 区域散热条件不 同, 某个 区域 , 在 浇注后前期 因温 度降低 产生 的液态收缩 , 和初生奥氏体析 出产生的凝固收缩 , 不 能被凝 固时的石 墨化膨胀相抵 ,只能靠 冒 E或 附近的热铁水补 l
板类铸铁件的冒口设计
王振京 张银海 ( 河北机电职业技术学院, 台 04 4 ) 邢 50 8
De inQ e d ri pa ei nc sig sg f e e ln o a t s f n r n WA GZ e j g H N i hi H bintue f cieyEet i, ig i 50 8C ia N hn-i ,Z A GYn— a ( eeIstto hnr lc cyXnt 44 , hn ) n i Ma rt a0
.‘ .. -. .. .。 . .。 .。 .。 .。 . 。 . 。 。 . ‘ . . . . .
中图分 类号 : G 4 T 2
铸造工艺学冒口设计方案

保温作用:冒口可 以减缓铸件凝固速 度,提高铸件质量
冒口的设计原则
保证补缩量:根据铸件的结 构、尺寸、壁厚等确定冒口 的补缩量
便于操作:冒口的位置应便 于操作,以便于浇注和清理
减少金属消耗:在保证补缩 量的前提下,尽量减少冒口 的金属消耗
避免形成热节:冒口的设计 应避免形成热节,以防止铸 件产生缩孔和缩松等缺陷
计算法
冒口体积计算 冒口直径计算 冒口高度计算 冒口材料选择
实验法
实验目的:确定最 佳冒口尺寸和位置
实验步骤:设计多 种方案,进行实际 铸造实验
实验结果:观察铸 件质量,分析实验 数据
结论:根据实验结 果,确定最佳冒口 设计方案
05 冒口的设计优化
减小冒口体积
优化冒口结构: 采用合理的冒 口结构,如分 片式、组合式 等,以减
冒口的设计原则: 根据铸件的结构、 尺寸、材质等因 素进行设计
冒口的设计方法: 根据铸造工艺学 原理,采用合适 的冒口尺寸、形 状和位置
冒口设计的实际 应用:在铸铁件 生产中,根据实 际情况选择合适 的冒口设计方案, 提高铸件质量和 生产效率
铝合金铸件的冒口设计
口体积
降低冒口高度: 通过减小冒口 高度,减少冒 口体积,同时 保证补缩效果
减小冒口直径: 采用较小的冒 口直径,以减 小冒口体积, 同时保证补缩
效果
改进冒口材料: 采用轻质、高 强度、低热膨 胀系数的材料 制作冒口,以 减小冒口体积
提高冒口补缩效率
确定冒口的位置和数量 选择合适的冒口类型 优化冒口尺寸和形状 控制冒口补缩时间
铸造工艺学冒口设计 方案
,a click to unlimited possibilities
汇报人:
铸造工艺学冒口设计
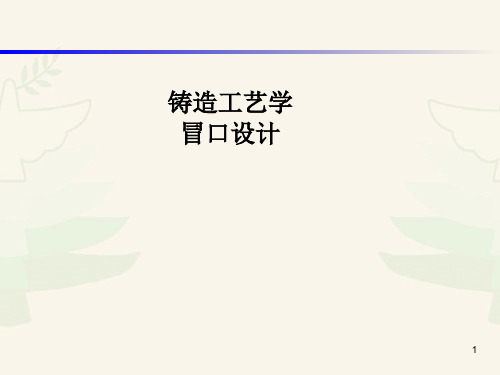
(2)按比例确定轮缘冒口 尺寸
1)冒口补贴按下列经验 比例关系确定:
d1=(1.3-1.5)dy; 42 42
R1=R件+dy+(1-3)mm;R2=(0.5-1)dy;δ=5-15mm 2)冒口尺寸用下述比例关系计算: 暗冒口宽:B=(2.2-2.5)dy 明冒口宽:B=(1.8-2.0)dy 冒口长:A=(1.5-1.8) B 3)计算冒口补缩距离,L=4dy。当两冒口距离超过此值时,应放置冷
① 在热节的上方或侧旁;
② 尽量在铸件最高、最厚部位, 低处热结设补贴或冷铁;
③不应设在铸件最重要、受力 大的部位;
④ 不要选在铸造应力集中处,
应减轻对铸件的收缩阻碍,避免 裂纹;
⑤ 尽量用一个冒口同时补缩几 个热节或铸件;
⑥ 冒口布置在加工面上,可节 约铸件精整工时,外观好;
⑦ 不同高度的冒口,用冷铁使
22
22
补贴种类: 金属补贴 加热(耐火隔片)补贴 发热(保温)补贴 补贴的位置: 水平补贴:最大长度为 冒口模数的4.7倍,其它尺 寸如图。 垂直补贴:试验条件和 关系曲线如图,生产条件变 化时补贴厚度乘以补偿系数。
23
23
24
24
局部热节的补贴尺寸:采用A·Heuvers氏滚圆法。重要部 位的热节可用扩大滚圆法。
铁或设水平补贴。
(3)轮毂冒口尺寸
1)轮毂补贴按下列关系确定
D1=(1.1-1.3)dy
2)当轮毂较小时用一个冒口,冒口尺寸为:
冒口直径:D=Φ2-(15-20)mm,Φ2是轮毂直径
冒口高度:H=(2-2.5)d1+r r的值待d1确定后按图作出。当轮毂较
3.4.3及3.4.4 铸钢及铸铁件冒口设计

3.4.3 铸钢件冒口设计与计算
四、铸件模数的计算
1. 正立方体
2. 圆柱体
3. 具有“无限大”尺寸的物
体 4. 圆筒壁 5. 交接立方体
3.4.3 铸钢件冒口设计与计算
四、铸件模数的计算
4. 圆筒壁
5. 交接立方体
6. 冒口颈的模数(riser neck)
铸钢件:Mn>Mc 铸铁件:Mn<Mc
选择圆柱形冒口,由标准冒口表查得冒口尺寸:
D=160mm,H=24mm 校核冒口个数: 估计冒口个数1000/(D+4.5a×2)≈1.6 ≈2 按两个冒口校核长度方向 4.5×50+4×50+4.5×50+2×160=970<1000
增加一个冒口,按三个冒口校核 970+160+4×50=1330>1000 宽度方向校核
4.5×50×2+160=610 >600
校核冒口最大补缩能力:
εv(Vr+Vc)=5%(100×60×5+π(16/2)2 ×24×3)
=2223(cm3)
Vrη=15 %π(16/2)2 ×24×3=2170 (cm3)
增大冒口尺寸,D=180mm
εv(Vr+Vc) = 2415 cm3 <Vrη=2746 cm3
有先有后,相互交错重叠,而铁水是相通的,这时膨胀、 收缩就可以叠加相抵,铸件表现出来的收缩实质上是胀缩 相抵的剩余量。然而就某一点而言,是收缩在前,膨胀在 后,二者是不能相抵的。
3.4.4 铸铁件实用冒口设计
图3-3-24 铸铁件凝固时收缩和膨胀的叠加 曲边三角形ABC—铸件的总收缩 曲边三角形ADC —铸件总膨胀 曲边三角形AB‘P—铸件的表观收缩 AC—铸件凝固时间 AP—铸件表观收缩时间 (冒口作用时间) P—均衡点(收缩量等于膨胀量的时间)
铸钢件冒口的设计规范.
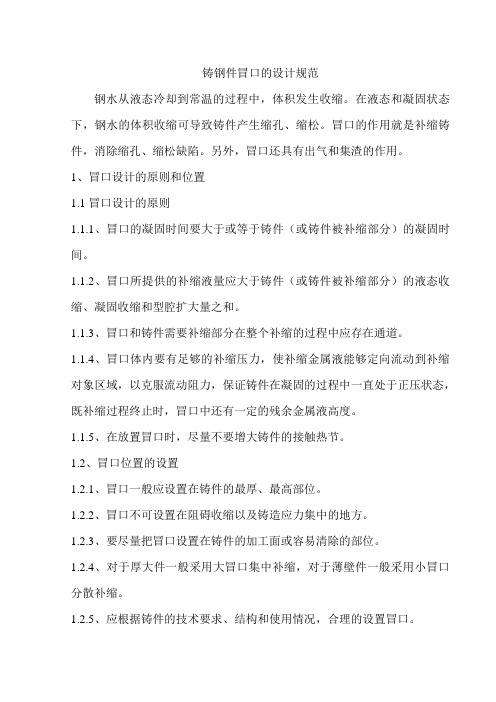
铸钢件冒口的设计规范钢水从液态冷却到常温的过程中,体积发生收缩。
在液态和凝固状态下,钢水的体积收缩可导致铸件产生缩孔、缩松。
冒口的作用就是补缩铸件,消除缩孔、缩松缺陷。
另外,冒口还具有出气和集渣的作用。
1、冒口设计的原则和位置1.1冒口设计的原则1.1.1、冒口的凝固时间要大于或等于铸件(或铸件被补缩部分)的凝固时间。
1.1.2、冒口所提供的补缩液量应大于铸件(或铸件被补缩部分)的液态收缩、凝固收缩和型腔扩大量之和。
1.1.3、冒口和铸件需要补缩部分在整个补缩的过程中应存在通道。
1.1.4、冒口体内要有足够的补缩压力,使补缩金属液能够定向流动到补缩对象区域,以克服流动阻力,保证铸件在凝固的过程中一直处于正压状态,既补缩过程终止时,冒口中还有一定的残余金属液高度。
1.1.5、在放置冒口时,尽量不要增大铸件的接触热节。
1.2、冒口位置的设置1.2.1、冒口一般应设置在铸件的最厚、最高部位。
1.2.2、冒口不可设置在阻碍收缩以及铸造应力集中的地方。
1.2.3、要尽量把冒口设置在铸件的加工面或容易清除的部位。
1.2.4、对于厚大件一般采用大冒口集中补缩,对于薄壁件一般采用小冒口分散补缩。
1.2.5、应根据铸件的技术要求、结构和使用情况,合理的设置冒口。
1.2.6、对于清理冒口困难的钢种,如高锰钢、耐热钢铸件的冒口,要少放或不放,非放不可的,也尽量采用易割冒口或缩脖型冒口。
2、设置冒口的步骤与方法冒口的大小、位置及数量对于铸钢件的质量至关重要。
对于大型铸钢件来说,必须把握技术标准及使用情况,充分了解设计意图,分清主次部位,集中解决关键部位的补缩。
以模数法为例,冒口设计的步骤如下:2.1、对于大、中型铸钢件,分型面确定之后,首先要根据铸件的结构划分补缩范围,并计算铸件的模数(或铸件被补缩部分的模数)M铸。
2.2、根据铸件(或铸件被补缩部分)的模数M铸,确定冒口模数M冒。
2.3、计算铸件的体收缩ε。
2.4、确定冒口的具体形状和尺寸。
铸铁件收缩模数法冒口设计
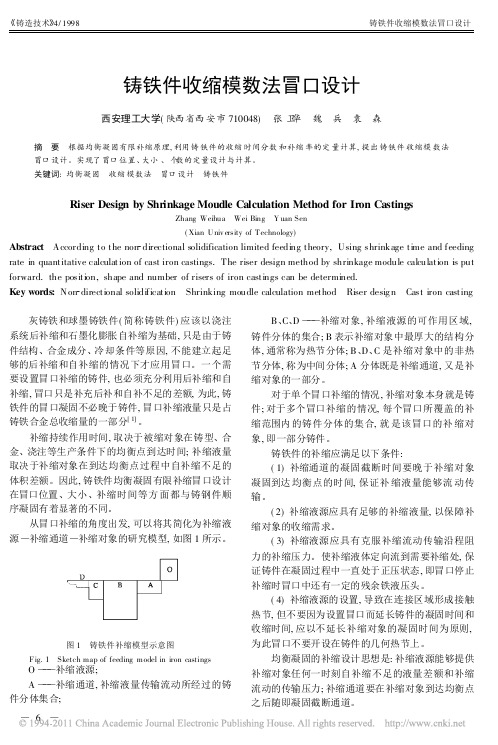
合金的收缩时间、收缩率不同, 铸铁合金的收缩时间、 收缩率是在一定的工艺条件下, 用规定的试样( 一种
特定的铸件) 测定的收缩、补缩特性参数。铸铁件的
补缩持续作用时间与补缩液量与浇注条件、浇冒口设
置位置、铸型冷却特性、铸型硬度等工艺条件及铸件
本身的结构有关, 具有动态特性。
这种动态特性, 按照补缩液源 补缩通道 补
灰铸铁件: P c =
1 e( 0. 5Mc+ 0. 01 qm )
( 4)
Fc =
0. 06
e( 0. 2M + 0. 01q )
c
m
( 5)
球 铁 件: Pc =
1
e( 0. 65M + 0. 01q )
c
m
( 6)
Fc =
0. 08
e( 0. 5M + 0. 01q )
c
m
( 7)
2 收缩模数法补缩设计原理
均衡凝固的补缩设计思想是: 补缩液源能够提供 补缩对象任何一时刻自补缩不足的液量差额和补缩
流动的传输压力; 补缩通道要在补缩对象到达均衡点 之后随即凝固截断通道。
铸造技术 4/ 1998
铸铁件收缩模数法冒口设计
1 铸铁件收缩时间和补缩率动态特性的数学描述
铸铁件的补缩持续作用时间与补缩液量, 与铸铁
f3
Ms
式中 M r Ar Vf Vp
= f 1 f 2 f 3 Mc
( 9)
冒口模数, cm ;
冒口散热表面积, cm2;
补缩液量, cm3;
形成补缩压力的安全液量, cm3;
f 1 补缩液量平衡系数;
f 3 补缩压力系数。
2 4 冒口颈大小的确定 冒口颈作为连接补缩液源 铸件的过渡通道,
铸铁件冒口设计
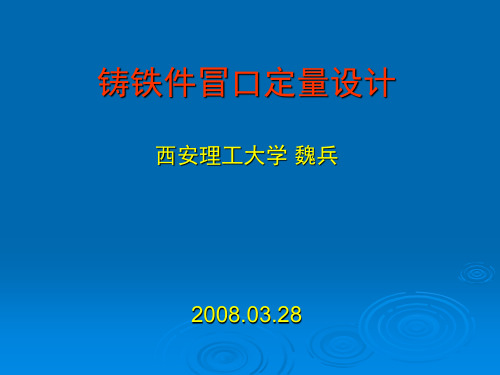
Qm=
G Mc3
(2)球铁件收缩时间分数
Pc=
1.0 e
(0.65Mc+0.01Qm)
3 冒口体模数MR MR=f1f2f3Mc
f1 ——冒口平衡系数 取f1=1.2
f2 ——收缩模数系数 f2=√Pc f3 ——冒口压力系数 f3=1.1~1.3
4 冒口颈模数MN
MN=fp.f2.f4 Mc
(3)直浇道模数 MZ MZ=f直.f1f2f3Mc
f1 ——冒口平衡系数 取f1=1.2
f2 ——收缩模数系数 f3 ——冒口压力系数 f3=1.1-1.3 f直浇道流通效应系数=0.70-0.80
(4)横浇道模数 Mh
Mh=f横.f2.Mc
f2 ——收缩模数系数 f横浇道流通效应系数=0.75~0.85
⑸冒口的压力使铸件凝固过程处于正压 状态; ⑹冒口颈 短、 薄、 宽。
可见,铸铁件均衡凝固有限补缩 设计的冒口位置、冒口大小、冒口补缩 时间等与顺序凝固有显著不同。
2 铸铁件收缩时间分数
(1)灰铸铁件收缩时间分数 PC=
PC=
AP AC
1.0
e (0.5Mc+0.01Qm)
e=2.7
Mc ——铸件模数 Qm ——质量周界商
fp ——流通效应系数 fp=0.45-0.55 f4 ——冒口颈长度系数 f4=0.8~1.0
5 冒口个数(均衡段的个数)
均衡段 冒口位置
均衡段
6 无冒口铸造工艺
无冒口铸造的本质是浇口当冒口
7 浇口当冒口补缩工艺
(1)补缩模型
(2)浇注系统流通效应:金属液流
过、通过直浇道、横浇道、内浇道 时,周围的型砂被加热,凝固时间 延长的热效应。为此,小的浇注系 统模数可以有长的凝固时间。流通 效应系数推荐为: f直浇道流通效应系数=0.70~0.80 f横浇道流通效应系数=0.75~0.85 f内浇道流通效应系数=0.35~0.40
估算法设计球墨铸铁冒口ppt实用资料
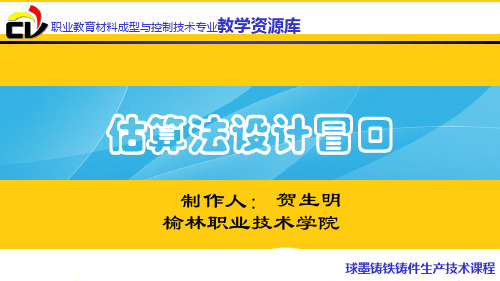
图3的条件是冒口颈与铸件的连接要有一定的水平段,一般要大于50mm,可认为之间无热交换。
尺寸: 图2 铸铁2分钟内靠近石英砂型壁处固态壳的厚度
图3 ( )件,浇注温度与( )颈的关系
冒口颈的具体计算步骤如下:
冒口颈的具体计算步骤如下:
按图2查出凝固层厚度δ。
图2 铸铁2分钟内靠近石英砂型壁处固态壳的厚度式中,d-冒口直径;
职业教育材料成型与控制技术专业教学资源库
图3的条件是冒口颈与铸件的连接要有一定的水平段, 一般要大于50mm,可认为之间无热交换。用这种方法能 难确估计冒口颈的凝固时间。如果值口颈与铸件垂直连接, 冒口颈要当减小,影响因素太复杂,难于准确估计。
卡赛法能抓住冒口补缩主要任务进行设计与计算,但稍 复杂,适用浇注温度较高,铸型刚度较大的铸件。
球墨铸铁铸件生产技术课程
职业教育材料成型与控制技术专业教学资源库
职业教育材料成型与控制技术专业教学资源库
制作人: 榆林职业技术学院
球墨铸球铁墨铸铸铁件铸生件产生产技技术术课课程程
职业教育材料成型与控制技术专业教学资源库
职业教育材料成型与控制技术专业教学资源库
制作人: 榆林职业技术学院
球墨铸球铁墨铸铸铁件铸生件产生产技技术术课课程程
(2)由浇注温度和()件查图4得到()颈。
d 4V 2 δ-铸件液态收缩期形成的冒口凝固壳厚度。 H
V-铸件和冒口需补充的金属收缩体积; H-冒口高度;
δ-铸件液态收缩期形成的冒口凝固壳厚度。
球墨铸铁铸件生产技术课程
ቤተ መጻሕፍቲ ባይዱ
职业教育材料成型与控制技术专业教学资源库
职业教育材料成型与控制技术专业教学资源库
职业教育材料成型与控制技术专业教学资源库
第九章 冒口冷铁的设计

(一) 比例法
(二) 公式计算法
(三) 模数法
(一) 与浇注系统和冒口配合控制铸件的凝固次序
(二) 加速铸件的凝固速度,细化晶粒组织,提高铸件的力学性能
(三) 划分冒口的补缩区域,控制和扩大冒口的补缩范围,提高冒口的补缩效率。
可以制作冷铁的材料很多,凡是比砂型材料的热导率、蓄 热系数大的金属和非金属材料均可选用。生产中常用的冷铁材 料有铸铁、铝合金、石墨和铜合金等,各种冷铁材料的热物理 系数见表9-5。
1.冒口有什么作用?设计冒口应遵循哪些基本原则? 2.冒口分为哪几类?各有什么特点? 3.选择冒口形状时应主要考虑哪些内容? 4.如何确定冒口的位置?应注意哪些问题? 5.如何用比例法来确定冒口的尺寸? 6.如何评定冒口的有效补缩作用? 7.如何提高冒口的补缩效率? 8.冷铁在铸件凝固过程中起什么作用?如何根据不同的 目的来确定冷铁的放置位置及尺寸大小? 9.如何选择冷铁材料?8
(1) 补偿铸件凝固时的收缩。
(2) 调整铸件凝固时的温度分布,控制铸件的凝固顺序。 (3) 排气、集渣。 (4) 利用明冒口观察型腔内金属液的充型情况。
在铸件凝固过程中,要使 冒口中的金属液能够不断地补 偿铸件的体收缩,冒口与铸件 被补缩部位之间应始终保持着 畅通的补缩通道。
(1)侧冒口应就近设在铸件热节的上方或侧旁。 (2)冒口应尽量设在铸件最高、最厚的部位。 (3)对低处的热节增设补贴或使用冷铁、造成补缩的有利条件。 (4)通常把铸件划分成几个区域,在每一个区域内设置若干个合适的冒口。 (5)根据冒口的有效补缩距离来确定冒口的位置和个数。
(1) 要求冷铁所起作用的分析
(2) 铸件结构的分析
(3) 与冒口配合使用
(4) 浇注系统及引入位置的影响
第八章冒口设计

6)冒口最好布置在需进行机械加工的表面,以减少精整 工件的工时。 7)为加强铸件的顺序凝固,应尽可能使内浇道靠近或 通过冒口,以造成对冒口有利的温度分布。 8)应避免在重要部位放置冒口,因冷却缓慢,晶粒粗大, 造成性能下降。
第十八页,编辑于星期五:二十二点 二十二分。
最厚的部位,以便利用金属液
的自重力补缩。
第十五页,编辑于星期五:二十二点 二十二分。
3、冒口的位置
3)在铸件不同高度上有热节需要补缩时,可按不同水平面放 置冒口,并配合使用冷铁。
第十六页,编辑于星期五:二十二点 二十二分。
4)冒口应尽可能不阻碍铸件的收缩,不应放在应力集中处, 以免引起裂纹;
5)力求用一个冒口同时补缩一个铸件的几个热节或几 个铸件的热节。
第三页,编辑于星期五:二十二点 二十二分。
要达到补缩的目的,冒口必须满足以下基本条 件: (1)冒口的凝固时间必须大于或至少等于铸件 (或铸件被补缩部分)的凝固时间。 (2)冒口中必须储存足够的金属液补充铸件 (或铸件被补缩的部分)的收缩。 (3)冒口与铸件被补缩的部位之间必须存在良 好的补缩通道。
第二十四页,编辑于星期五:二十二点 二十二 分。
(2)冷铁对冒口有效距离的影响
根据在板形和杆形件上应用冷铁的实验结果表明:对板
形件冷铁放在末端时,冷铁的厚度应等于该板的厚度是适宜 的,当冷铁放在两冒口之间时,冷铁约需板厚的二倍。
冷铁使铸件末端的冷却
速度增大,从而使板形铸
件致密的末端区长度增加
约50mm,此数值与板厚无关。 对杆形铸件来说,冷
第八页,编辑于星期五:二十二点 二十二分。
二 、冒口的Hale Waihona Puke 类及位置整体冒口:整个铸件
铸铁冒口设计手册

铸铁件冒口设计手册诸葛胜福士科铸造材料(中国)有限公司铸铁冒口设计手册一、概述冒口是一个个储存金属液的空腔。
其主要作用是在铸件成形过程中提供由于体积变化所需要补偿的金属液,以防止在铸件中出现的收缩类型缺陷(如图1和图2所示),而这些需要补偿的体积变化可能有:图1 各种缩孔图2 缩孔生产图a)和冒口的补缩图b)1—一次缩孔 2—二次缩孔 3—缩松 1—缩孔 2—型腔胀大 3—铸件(虚线以内) 4—显微缩松 5—缩陷(缩凹,外缩孔)(1)铸型的胀大(2)金属的液态收缩(3)金属的凝固收缩补偿这些体积变化所需要的金属液量随着铸型和金属种类的不同而异。
此外,冒口还有排气及浮渣和非金属夹杂物的作用。
铸件制成后,冒口部分(残留在铸件上的凸块)将从铸件上除去。
由此,在保证铸件质量要求的前提下,冒口应尽可能的小些,以节省金属液,提高铸件成品率。
由此冒口的补缩效率越高,冒口将越小,铸件成品率越高、越经济。
FOSECO公司的发热保温冒口具有高达35%的补缩效率;因而,具有极高的成品率和极其优越的经济性。
在金属炉料价格飞涨的情况下,其优越性显得尤其突出。
另外,高品质发热保温冒口,及其稳定可靠的产品质量是获得高品质铸件的重要手段和可靠的质量保证。
二、铸铁的特点铸钢和铸铁都是铁碳合金,它们在凝固收缩过程中有共同之处)如凝固前期均析出初生奥氏体树枝晶,都存在着液态、凝固态和固态下的收缩),但也有不同的特点。
其根本不同之处是铸铁在凝固后期有“奥氏体+石墨”的共晶转变,析出石墨而发生体积膨胀,从而可部分地或全部抵消凝固前期所发生的体积收缩,即,具备有“自补缩的能力”。
因此在铸型刚性足够大时,铸铁件可以不设冒口或采用较小的冒口进行补缩。
灰铸铁在共晶转变过程中析出石墨,并在与枝晶间的液体直接接触的尖端优先长大,其石墨长大时所产生的体积膨胀直接作用在晶间液体上,进行“自补缩”。
对于一般低牌号的灰铁铸件,因碳硅含量高,石墨化比较完全,其体积膨胀量足以补偿凝固时的体收缩,故不需要设置冒口,只放排气口。
完整版铸钢件冒口的设计与计算
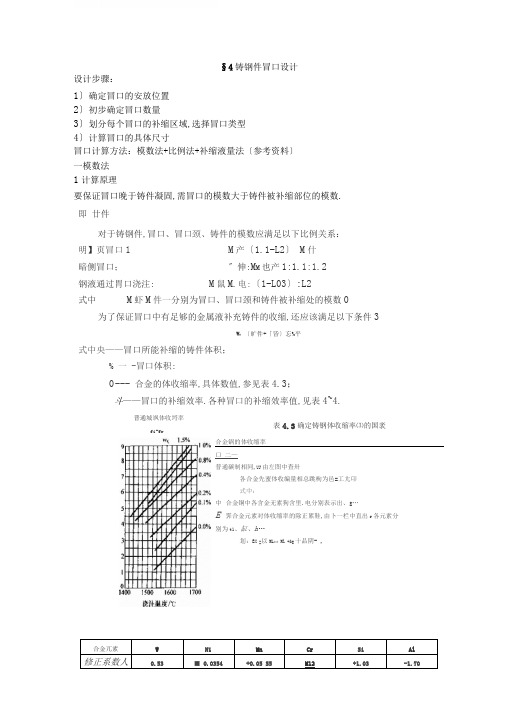
§4铸钢件冒口设计设计步骤:1〕确定冒口的安放位置2〕初步确定冒口数量3〕划分每个冒口的补缩区域,选择冒口类型4〕计算冒口的具体尺寸冒口计算方法:模数法+比例法+补缩液量法〔参考资料〕一模数法1计算原理要保证冒口晚于铸件凝固,需冒口的模数大于铸件被补缩部位的模数.即 廿件对于铸钢件,冒口、冒口颈、铸件的模数应满足以下比例关系:明】页冒口1M 产〔1.1-L2〕 M 什 暗侧冒口;〞伸:M M 也产1:1.1:1.2 钢液通过胃口浇注:M 鼠M.电:〔1-L03〕:L2 式中 M 虾M 件一分别为冒口、冒口颈和铸件被补缩处的模数0为了保证冒口中有足够的金属液补充铸件的收缩,还应该满足以下条件3W V 〔旷件+「皆〕忘%平式中央——冒口所能补缩的铸件体积;% 一 -冒口体积:0 --- 合金的体收缩率,具体数值,参见表4.3;斗——冒口的补缩效率.各种冒口的补缩效率值,见表4~4.表4.3确定铸钢体收缩率⑶的国袤 合金锅的体收缩率 口 二—普通碳制相同,UJ 由左图中查卅各合金先蜜体收编量相总跳枸为邑=工尢卬式中:中 合金铜中各含金无素狗含里.电分别表示出、g …E 霁合金元素对体收缩率的除正累鞋,由卜一栏中直出r 各元素分别为t1、缸、h …划:EX =以ML** Ml +&g 十品阴- ,合金兀素W Ni Mn Cr Si Al 修正系数人0.53 ■ 0.0354 +0.05 S5 M12 +1.03 -1.70 普通城飒体收埒率fi-fr总结:M冒=1.2M件P127式4-5,左边为总收缩量,右边为由冒口补充量2计算步骤1〕计算铸件模数根据铸件需补缩部位,划分补缩区,分别计算铸件的模数.计算方法:公式计算+图表计算—表4-5 〔p128-130〕.2〕计算冒口及胃口颈模数.根据热节的位置,确定胃口的类型,再根据式〔4-2〕或式〔4-3〕、式〔4-4〕. 即可计算出国口及冒口颈模数计算举例;铸钢件在下部法上处放置暗冒口补缩. 如图4-3三所示.求吩和利用表4・5中上形体计算公式,法兰处o=200mm, b—lOOnun*非散热面可得:“*0x20 …M 社=—j ---- ——cm = 3.636cm件2〔10 + 20〕-5因浇口通过冒口,故:1.05Mr = 374 cm 加冒=L2A/件=436 cmS 中左边的冒口颈…W R=〔22X 10X2〔22+10〕]四4一箝补缩铸钢件法兰的目口颈cm- 3.43cm,小于3.74cm,不能满足补缩要求,在铸件热节处将出现缩松口采用右边的冒口颈,必=Q0X 12V[2QO+I2〕]crti=3.75cm,满足了要求.计算M件用L形体计算公式,为什么不用法兰体公式去套呢?〔法兰体高度b无法确定〕图4-33B-B剖面图中200应改为220,因计算M B时用的数值是220;另外, 冒口直径为〔|〕220,其冒口颈宽也应为220.〔A-A剖面图中200改否.〕采用右边的A-A剖面冒口颈满足了要求,A-A剖面冒口颈尺寸怎么得来的呢?不要瞎懵,可列式M仝^=3.74=20X/[2 〔20+X〕],求出X=12.生产中可根据M冒数值查出标准侧冒口,得冒口尺寸〔直径、高等〕,冒口颈尺寸,冒口体积、重量,能补缩的铸件体积及重量〔 M冒结合一查〕.3〕确定铸钢件体收缩率由表4-3求出.例如,ZG270-500的平均W C=0.35%,假设浇注温度为1560℃,可从表4-3 查出=4.7%〔碳钢e V= e C〕.£V如何查出的呢?浇注温度为1560 C; W C=0.40%, ev=5%; W C=0.20%,&V=3.8%;据此列式〔5-3.8〕 / 〔0.4-0.2〕 = 〔5-X〕 / 〔0.4-0.35〕,解出X=4.7 〔插入法,比例法〕4〕确定冒口形状和尺寸查相关表格.5〕确定冒口数目6〕校核冒口的最大补缩水平.二比例法〔热节圆法〕使冒口根部直径大于铸件被补缩处热节圆直径或壁厚, 再以冒口根部直径来确定其他尺寸.D=cd式中D ……冒口根部直径;c ••…比例系数,参见表4-6;〔查表步骤〕d ……铸件被补缩热节处内切圆直径.可用作图法画出图4-34热节圆直件a 〕壁厚均匀b 〕壁面和交查表步骤:1〕选取比例系数c 〔先按铸件结构选择冒口类型,再选比例系数〕2〕确定冒口高度〔根据直径 D 确定〕;3〕确定每个冒口长度或冒口个数〔根据冒口延伸度确定〕.三铸件工艺出品率的校核表4-7说明校核方法.采用普通冒口时,冒口尺寸 可根据表中数值进行验算 和调整,即将冒口重量代入 计算后,假设工艺出品率低于 表中数值,那么冒口尺寸偏 大,可适当减小冒口高度; 假设高于表中数值,那么应加大 冒口尺寸或增加冒口个数.四冒口计算举例 见p133例题.图535 ZG35SiMn 铸钢齿轮铸件1模数法工艺出品率= 铸件重量铸件重量+浇铸系统重 量+冒口重量轮缘与轮辐的交接处为热节,其直径d按作图法得50〔大于轮缘厚40〕;按作图法且考虑热节增大,见P126图4-31,dy=d+〔10~30〕,取d=60 〔见P134比例法〕.轮缘热节处按表4-5应为板与杆的相交体,由图4-35可得a=d=60mm, b=180mm,c=24mm.2比例法〔热节圆法〕作业:如下列图铸钢齿圈坯件ZG25,为一圆环,中径〔|〕920,厚80,高240, 有三种补缩方案:3个6190冒口, 3个6190冒口和3个冷铁,尺寸为:宽100X厚50X高240, 6个6190冒口.按有效补缩距离检验,冒口数目是否足够?。
第五章 冒口设计
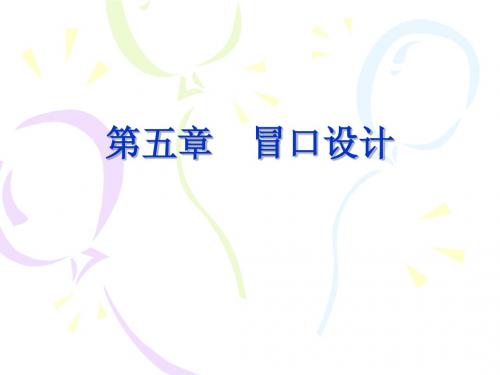
I-I端面
垂直补贴的尺寸可依照图3-5-13确定。 该图是对板型碳钢铸件进行顶注、立浇试验,后经过X光透 视检查而总结出来的关系曲线—补贴厚度a和铸件壁高H, 厚度T之间的关系曲线。(断面板型件—宽厚比>5:1)
K (0.9~1.26) 10
3米 / 秒1 / 2
(或K 0.75~ 0.98厘米 / 分1 / 2 )
2. 基本原理
遵守顺序凝固的基本条件。首先,冒口的凝固时间τr 应大于于铸件被补缩部位年凝固时间τc。运用Chvorinov 公式τ =(Mr/Kr)2和τc=(Mc/Kc)2 ,于是得:
6. 冒口布置在加工面上,可节约铸件精整工时,零件外观 好。 7. 不同高度上的冒口,应用冷铁使各个冒口的补缩范围隔 开 (图3-5-4)。
(三)冒口有效补缩距离的确定
冒口有效补缩距离=冒口作用区与末端区长度之 和。 它是确定冒口数目的依据。
有效补缩距离与铸件结构、合金成分、凝固特性、冷 却条件、对铸件质量要求的高低等多种因素有关,简称为 冒口补缩距离。
<200 25 250 30 300 33 400 35 500~1000 40 >1000 45
3. 冒口设计步骤
1)把铸件划分为几个补缩区,计算各区的铸件模数Mc。 2)计算冒口及颈的模数。 3)确定冒口形状和尺寸(应尽量采用标准系列冒口尺寸) 4)检验顺序凝固条件,如补缩距离是否足够,补缩通道是 否畅通。 5)校核冒口补缩能力。
第五章
冒口设计
第一节 冒口的种类及补缩原理
- 1、下载文档前请自行甄别文档内容的完整性,平台不提供额外的编辑、内容补充、找答案等附加服务。
- 2、"仅部分预览"的文档,不可在线预览部分如存在完整性等问题,可反馈申请退款(可完整预览的文档不适用该条件!)。
- 3、如文档侵犯您的权益,请联系客服反馈,我们会尽快为您处理(人工客服工作时间:9:00-18:30)。
诸葛胜铸铁冒口设计手册一、概述冒口是一个个储存金属液的空腔。
其主要作用是在铸件成形过程中提供由于体积变化所需要补偿的金属液,以防止在铸件中出现的收缩类型缺陷(如图1和图2所示),而这些需要补偿的体积变化可能有:图1 各种缩孔图2 缩孔生产图a)和冒口的补缩图b)1—一次缩孔 2—二次缩孔 3—缩松 1—缩孔 2—型腔胀大 3—铸件(虚线以内) 4—显微缩松 5—缩陷(缩凹,外缩孔)(1)铸型的胀大(2)金属的液态收缩(3)金属的凝固收缩补偿这些体积变化所需要的金属液量随着铸型和金属种类的不同而异。
此外,冒口还有排气及浮渣和非金属夹杂物的作用。
铸件制成后,冒口部分(残留在铸件上的凸块)将从铸件上除去。
由此,在保证铸件质量要求的前提下,冒口应尽可能的小些,以节省金属液,提高铸件成品率。
由此冒口的补缩效率越高,冒口将越小,铸件成品率越高、越经济。
FOSECO公司的发热保温冒口具有高达35%的补缩效率;因而,具有极高的成品率和极其优越的经济性。
在金属炉料价格飞涨的情况下,其优越性显得尤其突出。
另外,高品质发热保温冒口,及其稳定可靠的产品质量是获得高品质铸件的重要手段和可靠的质量保证。
二、铸铁的特点铸钢和铸铁都是铁碳合金,它们在凝固收缩过程中有共同之处)如凝固前期均析出初生奥氏体树枝晶,都存在着液态、凝固态和固态下的收缩),但也有不同的特点。
其根本不同之处是铸铁在凝固后期有“奥氏体+石墨”的共晶转变,析出石墨而发生体积膨胀,从而可部分地或全部抵消凝固前期所发生的体积收缩,即,具备有“自补缩的能力”。
因此在铸型刚性足够大时,铸铁件可以不设冒口或采用较小的冒口进行补缩。
灰铸铁在共晶转变过程中析出石墨,并在与枝晶间的液体直接接触的尖端优先长大,其石墨长大时所产生的体积膨胀直接作用在晶间液体上,进行“自补缩”。
对于一般低牌号的灰铁铸件,因碳硅含量高,石墨化比较完全,其体积膨胀量足以补偿凝固时的体收缩,故不需要设置冒口,只放排气口。
但对高牌号的灰铸铁件,因碳、硅含量较低,石墨化不完全,其产生的体积膨胀量不足以补偿铸件的液态和凝固体收缩,此时必须要设置冒口。
球墨铸铁在共晶转变时石墨的析出同样会产生体积膨胀,但是它产生缩松的倾向性却比灰铸铁大得多。
因为球墨铸铁共晶团的石墨核心是在奥氏体包围下长大的,石墨球长大时所产生的体积膨胀要通过奥氏体的膨胀来发生作用,这个膨胀只有一小部分被传递到枝晶间的液体上,而大部分却是作用在相邻的共晶团或初生奥氏体骨架上,正因为如此,导致了球墨铸铁产生缩前膨胀的倾向比灰铸铁大得多。
另外,球墨铸铁呈“糊状凝固”,在整个凝固期间它的外壳的坚实程度远远比不上灰铸铁,如果铸型刚性不够,会使石墨化产生的体积膨胀的大部了分消耗于外壳膨胀,结果枝晶间或共晶团之间的内部液体的液态收缩和凝固收缩得不到补偿;同时由于球墨铸铁凝固时析出的石墨共晶团细而多,即使使用冒田进行补缩,当冒口效率不高,保持液态时间不够长或压力不够大时,效果常不理想。
因此设计球墨铸铁件冒口比灰铸铁件更具有重要的意义。
三、模数计算:(一)模数的概念在铸件材质、铸型性质和浇注条件确定之后,铸件的凝固时间主要决定于铸件的结构形状和尺寸。
而千差万别的铸件形体,对凝固时间的影响主要表现在铸件的体积和表面积的关系上。
铸件体积愈大,则金属液愈多,它所包含的热量也愈多,凝固时间就长。
铸件体积相等,液体金属的重量及所含的热量就相等,如果铸件的结构不一样,则散热表面积就不相等。
显然,表面积愈大,散热就愈快,凝固时间愈短;反之,表面积愈小,凝固时间就愈长。
为了反映铸件体积和表面积对凝固时间的影响,引用了模数的概念,其数学表达式为:)((厘米冷却表面积体积模数)A ()V ()M = (1) 用各种形状、重量和用途不相同的铸钢件进行试验发现,不管铸件形状如何,只要它们的模数相等,其凝固时间就相等或相近。
铸件的模数和凝固时间τ之间的关系服从平方根定律2kM =τ (2)式中 k ——凝固系数,与铸件金属、铸型的热物理性能、铸件形状、浇注温度等有关。
(二)模数法计算冒口的原理为了实现补缩,冒口与铸件上被补缩部位之间必须存在补缩通道,同时它必须满足下面两个基本条件:1.冒口凝固时间应大于,至少等于铸件(或铸件被补缩部分)的凝固时间。
即 τ冒≥τ件或22件件冒冒M k M k ≥式中 τ冒、τ件——分别为冒口和铸件(或铸件被补缩部分)的凝固时间M 冒、M 件——分别为冒口和铸件(或铸件被补缩部分)的模数K 冒、K 件——分别为冒口和铸件的凝固系数,当用普通冒口时,k 冒≈k 件 由此得 M 冒≥M 件 (3)实际上计算冒口时并不需要计算冒口和铸件的绝对凝固时间,而只要求出它们的模数,就可知相对凝固时间的长短。
当满足 M 冒≥M 件时,冒口就比铸件凝固晚。
(三)铸件模数的计算任何复杂的铸件,均可看成是由许多简单的几何体(板、杆、圆柱体等)组合而成。
只要掌握一些简单几何体、组合体的模数计算公式,就不必用繁琐的公式去计算铸件的体积和表面积。
简单几何体的模数计算公式如下图所示:(四)模数放大系数采用中福的保温发热冒口套的目的是减慢冒口表面的散热速度,甚至是加热冒口套内的金属液。
这样,通过改善冒口的散热条件,提高冒口的补缩效率,减小冒口的尺寸。
如前所述,冒口的凝固时间可表示为:2F F kM =τ (4)式中,常数k 可分成两部分:围住整个冒口的铸型材料的热学性能;冒口内金属的性能。
因此,k 可还原为其两个组成单元的物理性能参数的乘积,即:2cf k = (5)图 3 基本几何体的模数计算式中 C ——常数,取决于所铸造金属的性能;f 2——常数,取决于铸型材料性能。
常数f 2表示为平方形式,仅仅是为了数学上的方便。
因此式(4)可改写成:(2f f fM C =τ) (6) 式(6)中fM f 称为视在模数,f 称为围住冒口全部表面积的铸型材料的模数扩大系数MEF 。
MEF 提供了评价和比较不同冒口套的手段,冒口套应设计成具有最大的MEF ,并且要具有获得合格铸件所需的其它一切要求。
铸造工作者通常并不关心这个系数的绝对值,而是将砂型冒口的值设定为1,把它作为评价各种冒口套材料的基础。
FOSECO 的Kalminex 系列的冒口套的MEF 高达1.4以上,也就是说FOSECO 的保温发热冒口套与其它冒口相比较有相当长的凝固时间,能保证冒口迟于铸件凝固,充分发挥冒口之补缩功能。
比其它种类的冒口更有利于获得致密铸件。
(五)冒口模数的计算一般来说,铸造工作者确定冒口尺寸的目的,并不是想要计算冒口和铸件的绝对凝固时间,而只是希望冒口的凝固时间比铸件的凝固时间长出很长的一段时间,因此在计算得到铸件截面的模数后,相应冒口模数应比铸件截面模数放大一定倍数,通常对于各种合金材料,此放大倍数为1.2 倍,即: c f M M 2.1=但对于铸铁,由于在凝固期间存在着石墨相的膨胀,所以可显著减少安全系数。
但不不同成分的铸铁、不同的浇注温度下,石墨的膨胀量是不同的,因此对冒口模数的放大系数也存在着差别。
在这类合金的凝固过程中发生的石墨膨胀,意味着灰铸铁和球墨铸铁件在存在有液体金属的全过程中并不是始终处于收缩的。
收缩时间(ST ) 仅占全部凝固时间的一部分。
这部分时间表示成总凝固时间的百分数,可由如下VDG 图的中图和左图确定。
该图的使用方法如下:用已知的含碳量,沿平行于碳线的方向移动到与相应的(Si+P )含量相交的点A ;画一条铅垂线使之与铸件模数线相交于点B ;由B 点向左引一条水平线,与表示铸铁在型中估计温度的线相交于D ;读出收缩时间(ST )占总凝固时间的百分数。
图4 VDG 数据表有效冒口模数由下式确定:100/2.1ST M M c f ×=由上式确定冒口的模数,然后查中福保温发热冒口样本选定冒口。
四、补缩液量校核上述计算所获得的冒口尺寸符合冒口模数的要求,但它并不总是能满足对铸件截面总的补缩金属量的需要。
对此要自始至终进行验算,如果发现冒口所含的补缩金属量不足,则必须加大冒口的尺寸。
一般情况下,同时增大冒口直径和高度。
在考虑冒口的补缩液量时,下列数据是必须要考虑的:(1)满足模数要求的冒口所能提供的补缩金属的百分数(η%),即补缩效率。
一般情况下,其值为:中福冒口套:33~35%普通砂冒口:6~8%(2)被铸合金的收缩率,由上图中的右图确定,由B 点画一条水平线与型内金属温度线相交(该温度须由浇注温度来估算,通常低于浇注温度50℃)。
大水平轴上读出表示成百分率的膨胀率或收缩率(ζ)。
由此应用下面公式,可以计算出补缩该截面铸件所需的冒口重量。
1−=ςηcf W W其中:W f :冒口重量W c :所需补缩区域的铸件重量η:冒口补缩效率(中福冒口取33%)ζ:金属液的体收缩率如果实际选用冒口重量大于所需值,则补缩液量足够,否则,需要进一步放大冒口。
五、有效补缩距离1、灰铸铁件的有效补缩距离铸铁的共晶度不同,其凝固方式也不同。
一般亚共晶灰铸铁属于中间凝固方式,而共晶灰铸铁则接近于层状凝固方式。
灰铸铁凝固时石墨化膨胀可以抵消一部分或全部凝固时的体收缩,因此,冒口要用来补给液态收缩。
2、球墨铸铁件冒口的有效补缩距离球墨铸铁一般呈“糊状凝固”,冒口的补缩通道会较早地受到析出的共晶团或共晶集团的阻碍,这不利于铸件的补缩,容易出现缩松。
因而,球墨铸铁冒口的有效补缩距离较灰铸铁小。
对于冒口的有效补缩距离,我们通常将冒口的补缩区域分为冒口区FD,末端区EZ,冷铁影响区C,对于不同的板件或杆件,可表示为如下形式:板件:杆件:这有效补缩距离FOSECO国际公司使用成分为:C.E.=4.3%,在砂型B型硬度为90度的粘土砂型中进行测定:灰铸件杆件 (宽度 = 厚度)厚度t (cm) FD+ EZ FD+ EZ+ C1 FD FD+ C224271 27 3047532 53 7671633 71 80794 79 906781675 81 9671896 89 106831037 103 123119968 119 1411331079 133 15912014910 149 17716313111 163 19417712 177 211143板件(宽度=5倍厚度)厚度t (cm) FD+ EZ FD+ EZ+ C1 FD FD+ C21 27 30 24 272 44 50 39 443 49 57 40 494 59 70 47 595 74 89 60 746 89 106 71 897 103 123 83 1038 119 141 96 1191339 133 159 10714910 149 177 12016311 163 194 13117712 177 211 143如果碳当量降低至3.0~3.2,建议将冒口区FD减小30%。