降低溶剂消耗量的方法
回流提取法
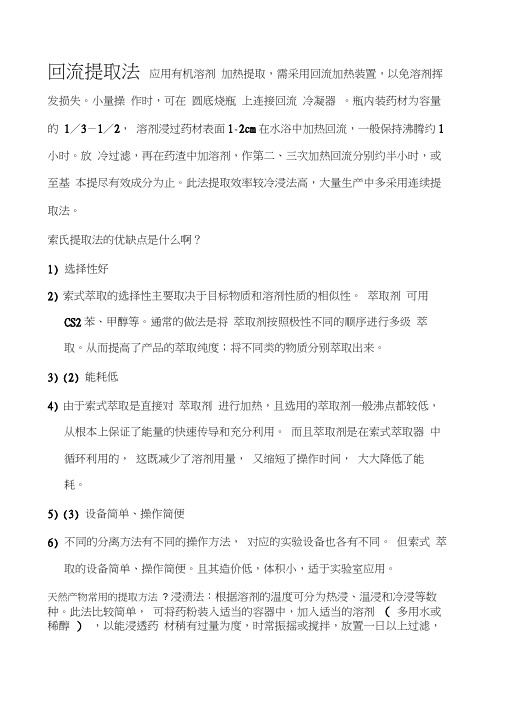
回流提取法应用有机溶剂加热提取,需采用回流加热装置,以免溶剂挥发损失。
小量操作时,可在圆底烧瓶上连接回流冷凝器。
瓶内装药材为容量的1/3-1/2,溶剂浸过药材表面1-2cm在水浴中加热回流,一般保持沸腾约1小时。
放冷过滤,再在药渣中加溶剂,作第二、三次加热回流分别约半小时,或至基本提尽有效成分为止。
此法提取效率较冷浸法高,大量生产中多采用连续提取法。
索氏提取法的优缺点是什么啊?1) 选择性好2)索式萃取的选择性主要取决于目标物质和溶剂性质的相似性。
萃取剂可用CS2苯、甲醇等。
通常的做法是将萃取剂按照极性不同的顺序进行多级萃取。
从而提高了产品的萃取纯度;将不同类的物质分别萃取出来。
3)(2) 能耗低4)由于索式萃取是直接对萃取剂进行加热,且选用的萃取剂一般沸点都较低,从根本上保证了能量的快速传导和充分利用。
而且萃取剂是在索式萃取器中循环利用的,这既减少了溶剂用量,又缩短了操作时间,大大降低了能耗。
5)(3) 设备简单、操作简便6) 不同的分离方法有不同的操作方法,对应的实验设备也各有不同。
但索式萃取的设备简单、操作简便。
且其造价低,体积小,适于实验室应用。
天然产物常用的提取方法? 浸渍法:根据溶剂的温度可分为热浸、温浸和冷浸等数种。
此法比较简单,可将药粉装入适当的容器中,加入适当的溶剂(多用水或稀醇),以能浸透药材稍有过量为度,时常振摇或搅拌,放置一日以上过滤,药渣另加新溶剂。
如此再提2〜3次。
第2、3次浸渍时间可缩短。
合并提取液,浓缩后可得提取物。
本法不需加热(必要时温热),适用于有效成分遇热易破坏以及含多量淀粉、树胶、果胶、粘液质的天然药物的提取。
但本法提取时间长,效率不高,特别用水浸渍时,水提取液易发霉变质,必要时应加适量的甲苯等防腐剂。
渗漉法:将中药粗粉装入渗漉筒中,用适当的溶剂润湿膨胀24h〜48h,然后不断地添加新溶剂。
使其自上而下渗透过药材,自渗漉筒的下口收集提取液。
当溶剂渗进药粉溶出成分比重加大而向下移动时,上层的溶液或稀浸液便置换其位置,造成良好的浓度差,使扩散能较好地进行,提取的过程是一种动态的过程,故浸出效果优于浸渍法。
溶剂残留限量标准的应对措施

溶剂残留限量标准的应对措施引言随着现代化工生产和生活用品的普及,溶剂在工业生产过程中的应用越来越广泛,而残留的溶剂也越来越成为社会关注的焦点。
因此,建立并完善溶剂残留限量标准已成为各国控制有害物质残留的必要途径之一。
本文将从溶剂残留的现状、溶剂残留限量标准及其制定以及应对措施三个方面进行探讨。
溶剂残留的现状溶剂残留是指在生产过程中,生产物料经过处理后,有些溶剂不能与生产物料完全分离,而残留在最终产品中的某一种化学物质的量。
这些残留的化学物质对人体及环境产生危害。
近年来,溶剂残留已成为工商业和消费者关注的焦点。
据统计,在制药、化妆品、食品、餐饮等领域,大量溶剂残留已严重影响到消费者的健康,因此制定相应的溶剂残留限量标准显得尤为必要。
溶剂残留限量标准的制定目前,溶剂残留限量标准由各国政府制定或指定国家相关机构制定,标准的制定依据和执行内容也不尽相同。
以中国为例,我国通过实施生产许可证制度、合格供应商认证采购体系等措施来控制产品的溶剂含量。
同时,国家卫生计生委、国家食品药品监管总局等部门还发布了多个涉及溶剂残留限量标准的标准规定,如《食品添加剂使用标准》、《化妆品卫生标准》等。
应对溶剂残留的措施在面对溶剂残留问题时,各行业都在积极采取措施,以降低残留溶剂的含量,如以下几方面:1. 优化生产工艺合理规划生产工艺,通过调节参数和配置设备等方式,降低溶剂残留量;2. 使用低溶剂或无溶剂工艺利用低致癌、低挥发性、低毒性的溶剂,并优化工艺流程,可有效降低溶剂残留量;3. 加强安全措施强化安全管理,防范化学品泄漏、溢出等事故,尽量减少各种溶剂的流失;4. 合规使用溶剂使用符合国家标准的溶剂,遵循安全文明生产原则,提高使用效率,减少溶剂的消耗以及可能产生的溶剂残留量;5. 建立追踪和监督制度在生产过程中建立严格的监测和追踪机制,对可能存在溶剂残留物质的产品进行抽检,以便及时发现和解决问题。
结束语由于溶剂是生产过程中必不可少的化学品,控制其残留量对于产品质量和消费者健康都至关重要。
降低浸出油厂溶剂消耗的措施

降低浸出油厂溶剂消耗的措施
1减少溶剂消耗的方法
溶剂浸出油厂是一种很耗费溶剂的工艺过程,溶剂消耗非常大,需要控制在最低限度上。
那么,要想降低溶剂消耗,应该采取哪些措施?
1.1改进工艺
改进浸出油厂的生产工艺,减少溶剂流量,是减少溶剂消耗的最有效的方法。
通过改进提取条件,降低液体固比,增强液体推动力,提高液体吸收能力,采用低温、低流速的方格提取,以及通过改进系统水的分离质量,可以有效地减少溶剂消耗。
1.2改善设备操作
设备操作对溶剂消耗有直接影响。
应根据设备构造,合理调整设备运行参数,如溶液压力、流速和温度等,将溶剂利用率提高到最高。
同时,应增强对设备操作的培训,保证操作人员对设备参数的控制,以降低溶剂消耗。
1.3采用先进技术
采用先进的技术,以节省溶剂消耗,比如表面活性剂的应用,人工智能技术,分子筛技术,多层激浆气流选择技术等。
这些新技术的应用将有助于节约投入的投入资源流,减少溶剂的消耗量。
总的来说,要想有效降低溶剂消耗,应综合考虑改进工艺、改善设备操作以及采用先进技术等多方面因素,这样才能够取得良好的降低溶剂消耗的效果。
加工国储大豆如何降低溶剂消耗——左青

)"
P Q R J ST R U AS J HV S @ A((((((((((((((!"#C W 3 0 X $) J 3 X $
粉末度高在膨化机内要多加几倍的直接蒸汽很难 膨化到浸出器内 物料结团结块 导致溶剂很难渗 #* / 5 具体时 透浸出效果差 所以需要延长 #" = 间取决于浸出器的形式 才能达到浸出提油的生 产指标 同 样 原 浸 出 器 的 沥 干 段 时 间 设 计 均 为 #" / 5应该延长料层高度在 ": E" = #: "* 沥干 / 5 料层高度 !: * 沥干时间应延 时间应延长 ! / 5 湿粕 膨化料 含溶达到 !*< 长* 浸出器要单独配置 # 台独立冷凝器 保持浸出 器内稳定的微负压 !: !(湿粕脱溶机 H @ 根据 ! 家 油 脂 行 业 成 套 设 备 供 应 商 的 C """ F > GH @做相关介绍 @ 设计气体温度 E! = E* I 直接蒸汽 皇冠的 H J !: *= $: "孔间隙小在同样量的直接喷 孔径 H 6 > ?6 用进 汽量下更均匀地汽提设计豆粕残溶 !*" 6 > ?6 特点 口大豆生产 豆粕残溶小于等于 !"" 是直接蒸汽孔径小孔间隙小对密度大的油料汽提 脱溶有益 @ 直接蒸汽孔径 H J C: * 孔间 迪斯美的 H E! I设计豆 隙大开孔率大于 $"<气体温度 E" = 6 > ?6 用进口大豆生产 残溶 粕残溶小于等于 !'" 6 > ?6 特点是气体温度低而开孔率 小于等于 !"" 大因此不易结团 我们发现加工国储大豆局部大豆存在升温含 水低豆粕蛋白溶解度低 坯片松而含粉的缺点 在 @内的蒸汽压降和气体 加工国储大豆时为了保持 H @的顶部是帽子头不能是直筒 H @的整体 温度H @体积大 #: $ 倍 容积要比正常 H 我公司镇江 东莞两个油厂加工国储大豆低于 ! - 采取矿物油吸收尾气含溶在 #* 6
液体萃取中的溶剂选择与用量优化
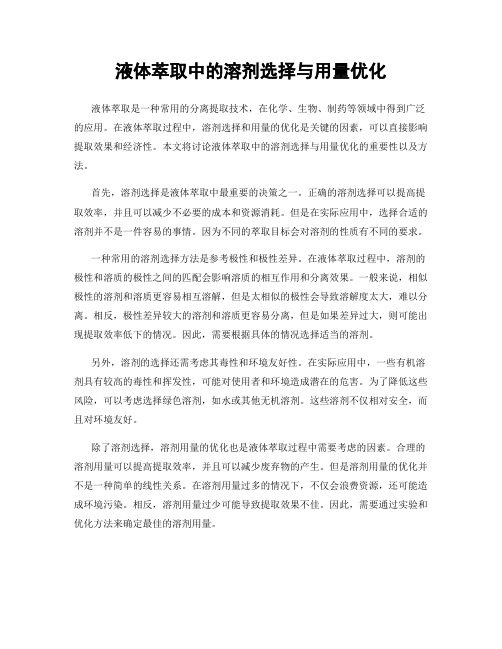
液体萃取中的溶剂选择与用量优化液体萃取是一种常用的分离提取技术,在化学、生物、制药等领域中得到广泛的应用。
在液体萃取过程中,溶剂选择和用量的优化是关键的因素,可以直接影响提取效果和经济性。
本文将讨论液体萃取中的溶剂选择与用量优化的重要性以及方法。
首先,溶剂选择是液体萃取中最重要的决策之一。
正确的溶剂选择可以提高提取效率,并且可以减少不必要的成本和资源消耗。
但是在实际应用中,选择合适的溶剂并不是一件容易的事情。
因为不同的萃取目标会对溶剂的性质有不同的要求。
一种常用的溶剂选择方法是参考极性和极性差异。
在液体萃取过程中,溶剂的极性和溶质的极性之间的匹配会影响溶质的相互作用和分离效果。
一般来说,相似极性的溶剂和溶质更容易相互溶解,但是太相似的极性会导致溶解度太大,难以分离。
相反,极性差异较大的溶剂和溶质更容易分离,但是如果差异过大,则可能出现提取效率低下的情况。
因此,需要根据具体的情况选择适当的溶剂。
另外,溶剂的选择还需考虑其毒性和环境友好性。
在实际应用中,一些有机溶剂具有较高的毒性和挥发性,可能对使用者和环境造成潜在的危害。
为了降低这些风险,可以考虑选择绿色溶剂,如水或其他无机溶剂。
这些溶剂不仅相对安全,而且对环境友好。
除了溶剂选择,溶剂用量的优化也是液体萃取过程中需要考虑的因素。
合理的溶剂用量可以提高提取效率,并且可以减少废弃物的产生。
但是溶剂用量的优化并不是一种简单的线性关系。
在溶剂用量过多的情况下,不仅会浪费资源,还可能造成环境污染。
相反,溶剂用量过少可能导致提取效果不佳。
因此,需要通过实验和优化方法来确定最佳的溶剂用量。
一种常用的溶剂用量优化方法是响应面分析。
通过设计一系列实验,探索不同溶剂用量对提取效果的影响,并通过统计分析得出最佳的溶剂用量范围。
这种方法可以有效地减少试验次数和实验成本,并且可以在一定程度上对实验误差进行补偿。
另外,还可以考虑在液体萃取过程中引入其他辅助技术来进一步优化溶剂用量。
化工工艺中常见的节能降耗技术措施

化工工艺中常见的节能降耗技术措施1. 废热回收利用:通过采用热交换器、蒸汽再压缩装置等设备,将工艺过程中产生的废热进行回收利用,用于加热介质或蒸汽发生器,减少能源消耗。
2. 低温余热利用:利用低温余热发电,采用有机废热发电技术,将废热转换为电能,提高能源利用效率。
3. 薄膜分离技术:通过采用薄膜分离技术,如膜渗透、膜蒸馏等,实现分离过程的能耗降低,减少工艺流程中的能量损失。
4. 质量热法:通过调整工艺参数,如温度、压力等,改变反应速率和产物选择性,实现能耗降低和产物质量的提高。
5. 溶剂替代与回收:通过选择更加环保的溶剂替代有机溶剂,减少溶剂使用量;采用溶剂回收技术,对废溶剂进行回收再利用,实现能源和原料的节约。
6. 设备能耗优化:对化工设备进行技术改造,如采用节能设备、降低过程能耗等,减少能源消耗。
7. 生产工艺优化:通过对生产工艺流程进行优化,如缩短反应时间、改进催化剂、改变传质方式等,实现能耗降低和产物质量的提高。
8. 生物技术应用:在某些化工生产过程中,可以引入生物技术,如微生物发酵、酶催化等,利用生物催化剂替代传统化学催化剂,实现能耗降低和反应选择性的提高。
9. 智能化控制系统:采用智能化控制系统,对化工工艺过程进行精确控制和优化调节,减少能耗和废品产生,提高生产效率。
10. 能源管理与优化:建立完善的能源管理体系,监测和分析能源消耗情况,并进行能源使用的优化调整,提高能源利用效率。
通过采取以上节能降耗技术措施,可以在化工工艺中减少能源消耗、降低生产成本,提高资源利用效率和环境友好性。
这些技术措施的应用可以帮助化工企业实现可持续发展,并推动绿色化工产业的发展。
dmf做反应溶剂的后处理方法

dmf做反应溶剂的后处理方法以DMF做反应溶剂的后处理方法DMF(N,N-二甲基甲酰胺)是一种常用的有机溶剂,广泛应用于化学反应中。
然而,在许多情况下,使用DMF作为反应溶剂后,需要对其进行后处理,以确保反应产物的纯度和安全性。
本文将介绍几种常见的DMF后处理方法。
DMF的后处理主要包括溶剂去除、溶剂回收、废弃物处理等步骤。
首先,我们将重点介绍DMF的溶剂去除方法。
1. 挥发法:DMF具有较低的沸点(153°C),因此可以通过加热溶液使DMF挥发而去除。
这种方法适用于DMF溶液中含有较少固体残留物的情况。
通常可以在搅拌下用加热设备对溶液进行蒸发,以去除DMF。
然而,需要注意的是,DMF是易燃易爆的溶剂,在操作中需注意安全。
2. 蒸馏法:DMF可以通过蒸馏纯化,去除其中的杂质和固体残留物。
蒸馏过程中,通过控制温度和压力,使DMF汽化并在冷凝器中重新凝结,从而实现纯化。
蒸馏法适用于DMF溶液中含有较多固体残留物的情况。
3. 搅拌沉淀法:DMF溶液可以通过添加适量的反溶剂(如水、醇类)或其他沉淀剂,使DMF与反溶剂发生相分离,从而实现DMF的去除。
这种方法适用于DMF与反溶剂之间存在较大的互溶性差异的情况。
在搅拌过程中,DMF会与反溶剂分离出来,形成两相体系,通过分离器将DMF层与反溶剂层分离,从而去除DMF。
除了溶剂去除方法外,还有一些常用的DMF后处理方法,如溶剂回收和废弃物处理。
溶剂回收是指将用过的DMF进行回收利用。
常见的溶剂回收方法包括蒸馏回收法和萃取回收法。
蒸馏回收法是通过将用过的DMF进行蒸馏,将DMF分离出来并回收利用。
而萃取回收法则是通过添加适量的萃取剂,将用过的DMF与萃取剂发生反应,从而将DMF从溶液中提取出来,再进行回收利用。
溶剂回收可以减少DMF的消耗,降低生产成本,对环境也更加友好。
废弃物处理是指对用过的DMF溶液进行处理,以确保其对环境的影响最小化。
常见的废弃物处理方法包括焚烧、催化氧化和生物降解等。
溶剂挥发影响因素

溶剂挥发影响因素
溶剂挥发的影响因素主要包括溶质浓度、溶剂性质、外界条件等。
具体如下:
1. 溶质浓度:溶质浓度较低时,溶剂分子间相互作用较小,挥发性较高,沸点较低。
相反,溶质浓度较高时,分子间相互作用增强,挥发性降低,沸点升高。
2. 溶剂性质:溶剂的挥发性本质上取决于其在特定温度下的蒸汽压,分子量和蒸发潜热。
一般来说,沸点较低的溶剂挥发速度快。
例如,醋酸乙酯和乙醇虽然沸点相近,但醋酸乙酯的挥发速度几乎是乙醇的两倍。
此外,极性溶剂通常会提高溶质的挥发性和沸点,而非极性溶剂则相对较低。
3. 外界条件:温度和压力是影响溶剂挥发的重要外界条件。
提高温度或降低压力会增加分子的动力学能量,使溶液中的分子更容易逸出,从而提高挥发性并降低沸点。
在干式复合过程中,烘箱的温度梯度和通风效果也是影响溶剂残留的主要因素。
良好的通风和适宜的温度梯度有助于降低溶剂残留量。
此外,气流、表面积与体积比以及环境湿度等因素也会影响溶剂的挥发速度。
例如,增加气流可以加快挥发速度,而较大的表面积与体积比提供了更多的表面供溶剂分子逸出。
综上所述,溶剂挥发是一个复杂的过程,受到多种因素的影响。
在实际应用中,理解和控制这些因素对于优化溶剂的使用和减少环境污染至关重要。
化学工程的溶剂回收资料
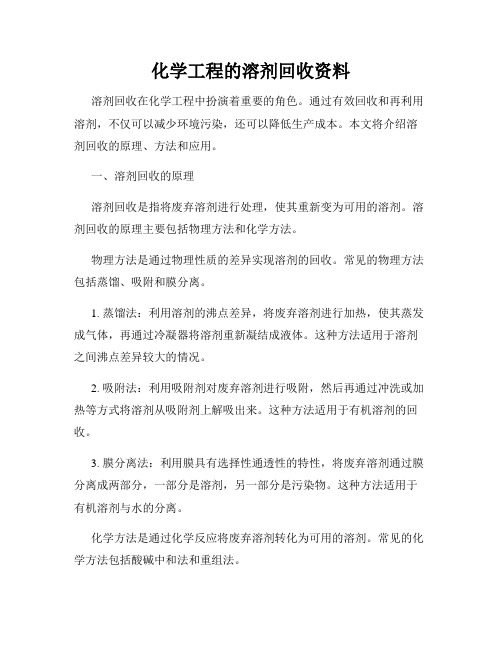
化学工程的溶剂回收资料溶剂回收在化学工程中扮演着重要的角色。
通过有效回收和再利用溶剂,不仅可以减少环境污染,还可以降低生产成本。
本文将介绍溶剂回收的原理、方法和应用。
一、溶剂回收的原理溶剂回收是指将废弃溶剂进行处理,使其重新变为可用的溶剂。
溶剂回收的原理主要包括物理方法和化学方法。
物理方法是通过物理性质的差异实现溶剂的回收。
常见的物理方法包括蒸馏、吸附和膜分离。
1. 蒸馏法:利用溶剂的沸点差异,将废弃溶剂进行加热,使其蒸发成气体,再通过冷凝器将溶剂重新凝结成液体。
这种方法适用于溶剂之间沸点差异较大的情况。
2. 吸附法:利用吸附剂对废弃溶剂进行吸附,然后再通过冲洗或加热等方式将溶剂从吸附剂上解吸出来。
这种方法适用于有机溶剂的回收。
3. 膜分离法:利用膜具有选择性通透性的特性,将废弃溶剂通过膜分离成两部分,一部分是溶剂,另一部分是污染物。
这种方法适用于有机溶剂与水的分离。
化学方法是通过化学反应将废弃溶剂转化为可用的溶剂。
常见的化学方法包括酸碱中和法和重组法。
1. 酸碱中和法:利用酸碱中和反应将废弃溶剂中的酸碱物质与中和剂反应,生成相应的盐和水,从而达到回收溶剂的目的。
2. 重组法:将废弃溶剂利用化学反应进行转化,得到与原溶剂性质相似的物质,然后再通过分离方法将溶剂从产物中回收。
二、溶剂回收的方法溶剂回收的方法多种多样,具体的选择取决于废弃溶剂的种类、废弃溶剂中污染物的性质以及回收效果的要求。
1. 蒸馏法:适用于有机溶剂之间沸点差异较大的情况。
通过加热回收溶剂,可将溶剂回收效率提高到90%以上。
2. 吸附法:适用于有机溶剂的回收。
吸附剂可以选择活性炭等材料,通过吸附达到回收溶剂的目的。
3. 膜分离法:适用于有机溶剂与水的分离。
根据溶剂和水的物理性质差异选择合适的膜材料,并通过膜分离技术实现溶剂的回收。
4. 酸碱中和法:适用于废弃溶剂中含有酸碱物质的情况。
根据酸碱物质的性质选择合适的中和剂进行回收。
5. 重组法:根据废弃溶剂的种类选择合适的化学反应方法,将废弃溶剂转化为可用的溶剂,并通过分离方法回收。
降低顺酐溶剂吸收工艺溶剂消耗因素分析与控制

提 干燥形成品质较 高的新鲜溶剂 实现循环 利用。 溶 剂在循 环利用过程 中消耗偏 高 , 甚 至 出现 消耗异常上升 的状
况, 本 文从 溶 剂 循 环 各 输 出端 口分 析 溶 剂 消 耗 影 响 因素 , 并 提 出能 控 制 溶 剂 消 耗 的措 施 , 为 降低 溶 剂 消 耗 工 作
Ab s t r a c t : Ma l e i c a n h y d i r d e s o l v e n t a b s o r p t i o n p r o c e s s i s w i d e l y u s e d i n f o r e i g n c o u n t i r e s , a n d i s a l s o t h e ma i n me t h o d o f ma le i c a n h y d i r d e a b s o po r t i o n . T h e ma le i e a n h y d id r e u n i t i n o u r p l a n t t a k e s d i b u t y l p h t h a l a t e a s s o l v e n t t o a b s o p r ma le i c a n h y d r i d e a n d f o r m i r c h s o l v e n t , t h e t a i l g a s a t f e r s e p e r a t i o n i s s e n t t o b o i l e r t o s e t o n i f r e . Ri c h s o l v e n t i s s e n t t o t h e v a c u u m a n a l y t i c a l c o l u mn nd a ma le i c nh a y d i r d e i s r e s o l v e d u n d e r v a c u u m. S o l v e n t a f t e r p a me d i s c a r r i e d o u t f u t r h e r v a c u u m l f a s h t o r e d u c e t h e ma l e i c a n h y d i r d e c o n t e n t .
溶剂残留超标可能的原因及处理措施

溶剂残留超标可能的原因及处理措施
引言:溶剂残留超标是一种常见的问题,可能会对环境和人体健康造成潜在风险。
了解溶剂残留超标的原因和采取相应的处理措施,对于确保产品质量和环境安全至关重要。
一、原因分析
1.质量控制不当:在生产过程中,未严格控制溶剂使用量、溶剂类型和溶剂挥发速率,导致残留超标。
2.不合理的设备和工艺:使用老旧设备或不合适的工艺流程,容易造成溶剂残留超标。
3.操作不规范:操作人员未按照标准操作程序进行操作,如未戴手套、未佩戴防护口罩等,容易导致溶剂残留超标。
4.溶剂回收不彻底:未对废水、废气中的溶剂进行有效回收处理,导致残留超标。
二、处理措施
1.加强质量控制:在生产过程中,严格控制溶剂使用量、选择合适的溶剂和控制溶剂挥发速率,确保质量符合标准。
2.更新设备和工艺:使用新型设备和改进的工艺流程,降低溶剂残留的风险。
3.规范操作程序:培训操作人员,确保其按照标准操作程序进行操作,提高操作规范性。
4.加强溶剂回收:建立完善的废水处理和废气处理系统,对废水、
废气中的溶剂进行高效回收和处理,减少溶剂残留的可能性。
结论:溶剂残留超标可能的原因包括质量控制不当、不合理的设备和工艺、操作不规范和溶剂回收不彻底等。
为了解决这一问题,应加强质量控制、更新设备和工艺、规范操作程序以及加强溶剂回收。
通过采取这些处理措施,可以降低溶剂残留超标的风险,保障产品质量和环境安全。
残留溶剂的指导原则
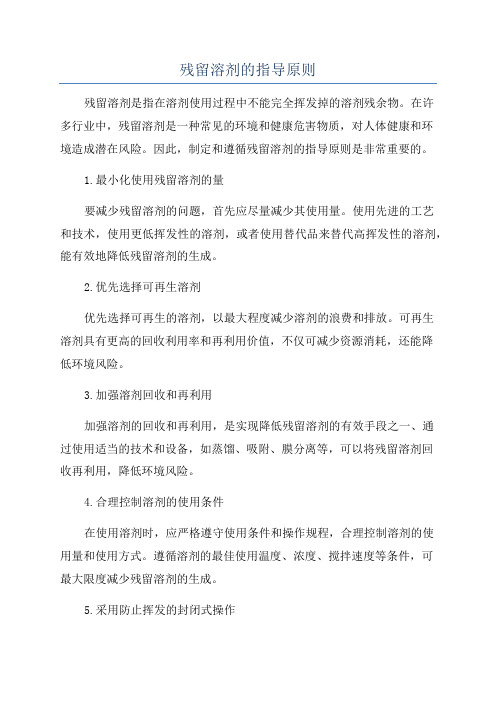
残留溶剂的指导原则残留溶剂是指在溶剂使用过程中不能完全挥发掉的溶剂残余物。
在许多行业中,残留溶剂是一种常见的环境和健康危害物质,对人体健康和环境造成潜在风险。
因此,制定和遵循残留溶剂的指导原则是非常重要的。
1.最小化使用残留溶剂的量要减少残留溶剂的问题,首先应尽量减少其使用量。
使用先进的工艺和技术,使用更低挥发性的溶剂,或者使用替代品来替代高挥发性的溶剂,能有效地降低残留溶剂的生成。
2.优先选择可再生溶剂优先选择可再生的溶剂,以最大程度减少溶剂的浪费和排放。
可再生溶剂具有更高的回收利用率和再利用价值,不仅可减少资源消耗,还能降低环境风险。
3.加强溶剂回收和再利用加强溶剂的回收和再利用,是实现降低残留溶剂的有效手段之一、通过使用适当的技术和设备,如蒸馏、吸附、膜分离等,可以将残留溶剂回收再利用,降低环境风险。
4.合理控制溶剂的使用条件在使用溶剂时,应严格遵守使用条件和操作规程,合理控制溶剂的使用量和使用方式。
遵循溶剂的最佳使用温度、浓度、搅拌速度等条件,可最大限度减少残留溶剂的生成。
5.采用防止挥发的封闭式操作在工业生产过程中,应尽可能采用封闭式设备和操作工艺,以防止溶剂的挥发和扩散。
通过密封设备、负压操作、局部排风等措施,可有效减少残留溶剂对环境和人体的危害。
6.严格遵守相关法律法规和标准制定和遵循残留溶剂管理的指导原则,既要在国家和地方层面上遵守相关的法律法规和标准,也要在企业内部建立相应的规章制度和管理体系。
通过加强监督和管理,确保残留溶剂的处理和处置符合法律法规和环保要求。
7.开展溶剂的危险性评估和监测对使用的溶剂进行危险性评估和监测,了解其挥发性、毒性、可燃性等性质和特点,及时采取相应的控制措施和防护措施。
通过定期检测和监测,及时发现和处理残留溶剂的问题,减少环境和健康风险。
总之,制定和遵循残留溶剂的指导原则是保护环境和人体健康的重要措施。
通过最小化使用残留溶剂的量、优先选择可再生溶剂、加强回收和再利用、控制使用条件、采用封闭式操作、遵守法律法规和标准、进行危险性评估和监测等措施,可以有效减少残留溶剂对环境和健康的危害。
萃取剂的选择
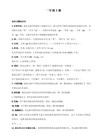
5.其它指标 如萃取剂的价格、来源、毒性、以及是否易燃、易爆等等,均为选择萃取剂时需要考虑的问题。
萃取剂的选择范围一般很宽,但若要求选用的溶剂具备以上各种期望的特性,往往也是难以达到的,最后的选择仍应按经济效果进行权衡,以定取舍。
工业生产中常用的萃取剂可分为三大类:①有机酸或它们的盐,如脂肪族的一元羧酸、磺酸、苯酚等。②有机碱的盐,如伯胺盐、仲胺盐、叔胺盐、季胺盐等。③中性溶剂,如水、醇类、酯、醛、酮等。
界面张力 萃取物系的界面张力较大时,细小的液滴比较容易聚结,有利于两相的分离,但界面张力过大,液体不易分散,难以使两相混合良好,需要较多的外加能量。界面张力小,液体易分散,但易产生乳化现象使两相难分离,因此应从界面张力对两液相混合与分层的影响综合考虑,选择适当的界面张力,一般说不宜选用张力过小的萃取剂。常用体系界面张力数值可在文献中找到。有人建议,将溶剂和料液加入分液漏斗中,经充分剧烈摇动后,两液相最多在5min以内要能分层,以此作为溶剂界面张力σ适当与否的大致判别标准。
1.萃取剂的选择性 萃取时所采用的萃取剂,必须对原溶液中欲萃取出来的溶质有显著的溶解能力,而对其它组分(稀释剂)应不溶或少溶,即萃取剂应有较好的选择性。
2.萃取剂的物理性质 萃取剂的某些物理性质也对萃取操作产生一定的影响。
密度 萃取剂必须在操作条件下能使萃取相与萃余相之间保持一定的密度差,以利于两液相在萃取器中能以较快的相对速度逆流后分层,从而可以提高萃取设备的生产能力。
粘度 萃取剂的粘度低,有利于两相的混合与分层,也有利于流动与传质,因而粘度小对萃取有利。有的萃取剂粘度大,往往需加入其他溶剂来调节其粘度。
3.萃取剂的化学性质 萃取剂需有良好的化学稳定性,不易分解、聚合,并应有足够的热稳定性和抗氧化稳定性。对设备的腐蚀性要小。
回流提取法

回流提取法应用有机溶剂加热提取,需采用回流加热装置,以免溶剂挥发损失。
小量操作时,可在圆底烧瓶上连接回流冷凝器。
瓶内装药材为容量的1/3-1/2,溶剂浸过药材表面1-2cm。
在水浴中加热回流,一般保持沸腾约1小时。
放冷过滤,再在药渣中加溶剂,作第二、三次加热回流分别约半小时,或至基本提尽有效成分为止。
此法提取效率较冷浸法高,大量生产中多采用连续提取法。
索氏提取法的优缺点是什么啊?1)选择性好索式萃取的选择性主要取决于目标物质和溶剂性质的相似性。
萃取剂可用CS2、苯、甲醇等。
通常的做法是将萃取剂按照极性不同的顺序进行多级萃取。
从而提高了产品的萃取纯度;将不同类的物质分别萃取出来。
(2)能耗低由于索式萃取是直接对萃取剂进行加热,且选用的萃取剂一般沸点都较低,从根本上保证了能量的快速传导和充分利用。
而且萃取剂是在索式萃取器中循环利用的,这既减少了溶剂用量,又缩短了操作时间,大大降低了能耗。
(3)设备简单、操作简便不同的分离方法有不同的操作方法,对应的实验设备也各有不同。
但索式萃取的设备简单、操作简便。
且其造价低,体积小,适于实验室应用。
天然产物常用的提取方法?浸渍法:根据溶剂的温度可分为热浸、温浸和冷浸等数种。
此法比较简单,可将药粉装入适当的容器中,加入适当的溶剂(多用水或稀醇),以能浸透药材稍有过量为度,时常振摇或搅拌,放置一日以上过滤,药渣另加新溶剂。
如此再提2~3次。
第2、3次浸渍时间可缩短。
合并提取液,浓缩后可得提取物。
本法不需加热(必要时温热),适用于有效成分遇热易破坏以及含多量淀粉、树胶、果胶、粘液质的天然药物的提取。
但本法提取时间长,效率不高,特别用水浸渍时,水提取液易发霉变质,必要时应加适量的甲苯等防腐剂。
渗漉法:将中药粗粉装入渗漉筒中,用适当的溶剂润湿膨胀24h~48h,然后不断地添加新溶剂。
使其自上而下渗透过药材,自渗漉筒的下口收集提取液。
当溶剂渗进药粉溶出成分比重加大而向下移动时,上层的溶液或稀浸液便置换其位置,造成良好的浓度差,使扩散能较好地进行,提取的过程是一种动态的过程,故浸出效果优于浸渍法。
高负荷下溶剂DMF消耗高的原因浅析
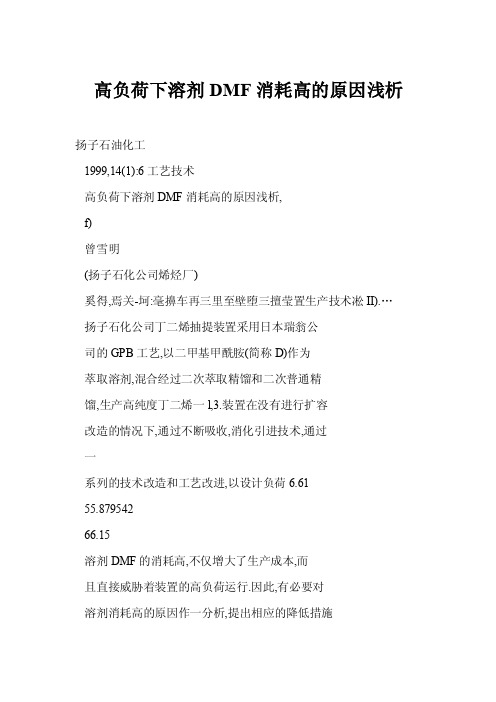
高负荷下溶剂DMF消耗高的原因浅析扬子石油化工1999,14(1):6工艺技术高负荷下溶剂DMF消耗高的原因浅析,f)曾雪明(扬子石化公司烯烃厂)奚得,焉关-坷:毫擤车再三里至壁堕三擅莹置生产技术凇II).…扬子石化公司丁二烯抽提装置采用日本瑞翁公司的GPB工艺,以二甲基甲酰胺(简称D)作为萃取溶剂,混合经过二次萃取精馏和二次普通精馏,生产高纯度丁二烯一l,3.装置在没有进行扩容改造的情况下,通过不断吸收,消化引进技术,通过一系列的技术改造和工艺改进,以设计负荷6.6155.87954266.15溶剂DMF的消耗高,不仅增大了生产成本,而且直接威胁着装置的高负荷运行.因此,有必要对溶剂消耗高的原因作一分析,提出相应的降低措施和建议.1原因分析1.1操作原因1.1.1气相负荷增高1.1.1.1第2汽提塔DA一105负荷增加DA一105塔的主要作用是把从丁二烯回收塔(DA一104)来的富溶剂(含烃类1.14%~5%)中的烃类完全脱除出去,以保证干净的循环溶剂.随着装置运行负荷的增加,DA一105(第2汽提塔)塔的进料量相应增加.同时,由于DA一104(丁二烯回收塔)塔釜温度偏低(135℃以下),使DA一105塔顶尾气中BD—l,3的含量从l1.84%上升至65%,导致尾气排放量从166.21【g/h(设计值)上升至3201【g/h左右,超过设计值近l倍.扬子石化公司研究院利用ASPENPLUS软件对DA一105塔进行模拟计算也表明,当装置负荷13t/h时,其最大泛点率已达65%,所以当负荷达到16.5t/h时,其最大泛点率已超过80%,DA一105塔的处理能力已难以满足实际生产的需要. DA一105塔进料负荷的增加,增大了该塔的气相负荷,气液平衡难以维持,塔顶压力上升,因而操作难度增大.在实际操作中,该塔已出现了塔顶,釜温度升高,回流不稳,压力不稳,DA一105塔操作难于控制的现象,从而引起DMF随塔顶尾气排放而夹带损失.1996年3~4月,因这方面原因,DA一105塔夹带DMF损失达60t左右.1.1.1.2溶剂精制塔DA一108处理量增加DA—lO8(溶剂精制塔)主要用脱除两个汽提塔顶溶剂中富集的水和二聚物.高负荷情况下,萃取系统所加萃取溶剂量相应增加,以保证萃取精馏塔的分离效果.因而有更多的溶剂需要精制,确保循环溶剂水值控制在60o×l0一以下.DA一108塔设计处理量为5801,g/h,当装置负收蒋日期:1998—01一u.作者筒介:曾雪明.萝.工程师.1985年毕业于南京化工学校基本有机合成专业,同年分配翻插子石化公司婿烃厂,现在丁二母车间从事工艺技术管理工作.1999年第14卷第1期曾雪明.高负荷下溶剂DMF消耗高的原因浅析7荷为l6.5t/h时,其处理量通常在800l【g/h以上,比设计负荷增大了37%,使得塔操作十分困难,时常出现压力升高,顶温波动等现象,引起塔顶,塔釜质量的不合格,更直观地表现在塔顶排放水中所舍DMF的升高,使得DMF消耗出现大幅度的升高. 表2为DA-108塔釜,塔顶质量的一些数据.裹21996年DA一1(18塔运行情况从表2可看出,由于DA一108塔的操作不稳定从而使塔顶水中DMF含量高达4%~5%,比设计值1.0%高出4~5倍.因而DMF随塔顶水排放的损失很大.1.1.2尾气系统压力升高系统的尾气排放设置了一条76.2ram(6)的尾气总管,各系统中尾气先排放至尾气总管,再经尾气处理系统回收夹带液体后排放至火炬总管或外送至乙烯装置作燃料.在高负荷运行时,由于尾气排放量的大幅度增加,从465kg/h增加到6O0l【g/h以上,引起尾气压力的升高,使得排放气中部分溶剂和其它较重组分(如阻聚剂,焦状物等)易于积液沉降,引起尾气排放不畅.与之相连的各系统的操作压力都会受到不同程度的影响.特别是DA一1o5,DA一1o8塔都是在常压下操作,所以尾气系统压力的小幅波动都会引起两塔操作压力的大幅度波动,破坏塔内的气液平衡,引起DA—lo5和DA一108塔操作紊乱,导致DA一108塔顶DMF含量严重超标而损耗以及DA一1o5塔顶DMF随尾气夹带而大量损耗.1.2排放气中夹带DMF增加随着装置高负荷的运行,DA一1o5,DA一108塔顶气液负荷均增加,尾气的排放量随之大幅度增加,馏出物从塔顶冷却器进入回流罐(FA—l08,FA一1o7),其流速大大增加.由于两台回流罐未作增容处理,馏出物中的气体与液体来不及分离而夹带液体(包括DMF及二聚物和水)进入尾气管线.随着气液流速的增加,即两塔处理量的增加越大,夹带溶剂量也就越大.1.2.1溶剂精制回流罐带液高负荷运行必然要求DA一108塔的处理量加大.在进料增加,尤其是进料中水,Q,二聚物含量超高时,也就更增大了塔顶气液流速.在系统加快脱水的同时,因为脱除Q烃类而造成DMF夹带损失增多.从l996年下半年的实际生产来看,FA一107(溶剂精制回流罐)罐顶气体排放量大时,往往导致FA一119(燃料气吸人罐)罐凝液异常增加,达到平均1个星期FA一119罐中的积液就会满罐而排放掉.实际操作中,经常通过开启塔顶冷却器EA一121放空阀门来调节该塔操作压力.如此操作,虽然可以迅速降低压力,但未经充分冷却的气体直接排放到尾气管线,其夹带的溶剂损失量将更多.1.2.2第2汽提塔回流罐带液DA—lo5塔回流罐FA—lo8(第2汽提回流罐)罐顶气体排放是一直敞开的,在解析大量的Q 时,因塔顶冷却器换热面积小且回流罐FA一108为卧式小罐(稍加rr1II1×2000rr1II1),馏出物中的液体与气体(DMF含量为41%)进入该罐时,来不及充分分离,随着乙烯基乙炔等气体的排放而被夹带至尾气中去.13水解量增加溶剂DMF易发生水解反应:NH2CO(CH3)2+H2O—一H(3OOH+NH(CH3)2其水解速度与溶剂中水含量及温度有关.含水量越大,则永解程度越大,即DMF分解增大;温度越高水解越严重.在DA一1o5塔的上部及DA—l08塔的中部,由于操作温度比较高(高于100℃),而且这些部位的水含量相对较高(达到5.35%),水解程度比较严重.同时由于高负荷因素,使得DA一1o5及DA—lo8塔内气液平衡失调,影响塔的能量平衡.在两塔内部,因为轻组分含量升高,水等组分在塔中的分布下移.这样,水含量上升,温度升高更利于溶剂的分解,因而水解而造成的DMF损失增加.2降低措施爰建议21降低第1萃取精馏塔的溶剂比由前可知,DA一108塔进料量增加及进料中轻组分的增加,使该塔顶排放水及尾气中夹带的溶剂损失大大增加.如果能够降低溶剂使用量,也就可扬子石油化工1999年第l4卷第1期以相对减少DA一108塔的处理量,使之在合适的范围内操作,进而减少溶剂的消耗.扬子石化公司研究院对高负荷(16.5t/h)下,DA一101塔最佳溶剂比进行了计算.裹3量佳溶剂比模拟计算由表3可以看出,当抽余油中的丁二烯一1,3含量控制在0.3%时,溶剂比5.1:1,产品丁二烯一1,3的纯度就可以达到99.3%(优级品标准).但模拟计算时,没有考虑原料中顺,反丁烯含量对溶剂比选择的影响.根据实际生产’隋况,G原料中反丁烯一般在5%.顺丁烯4%左右,因此,我们把实际溶剂比确定在7.4-7.5.溶剂比优化后,DA一101塔的质量仍在控制范围内(顺丁烯≤0.1%,反丁烯≤4.0%),产品丁二烯的纯度也在99.5%以上.这样,降低了DA一101塔的操作负荷,且降低了D芦L一108塔的处理量. 22调整第2革取系统工艺DA一104塔釜温度偏低,不但使丁二烯一1,3损失增大,而且也增加了DA一105塔顶放空量,引起塔顶DMF夹带损失.l996年l2月扬子石化公司研究院在对装置进行标定(标定负荷为16.5t/h)时,对最佳丁二烯回收率下DA一104塔釜温度进行的模拟计算,其结果如表4.裹4模拟计算结果注:循环量即为DA-104塔顶丁二烯回收量.由表4可以看出,随DA一104塔釜温度的升高,对最终产品的纯度几乎无影响,但DA一105塔顶排放量明显减少.因而,可以尽可能地提高DA一104塔釜温度(140”C以上).实际操作中的温度控制在143℃左右,DA一105塔顶排放气中乙烯基乙炔(V A)浓度在40%以下(因为V A浓度大于50%时,易引起爆炸).为保证乙烯基乙炔浓度在安全范围内,可以通过增加BBR(抽余油)量稀释的办法.我们对原有稀释管线进行了改造:将DA一101塔顶原有放空管线接至稀释量调节阀FIC一127处,且管线加粗.这样既利于DA一101压力的控制,又保证了DA一105塔的安稳运行.2.3DA一108塔操作指标的优化DA一108塔的处理量从580/h提高至800kg/h以上,使原有一些操作指标难以满足实际操作的需要.因此,在现有条件下,只有对一些操作指标进行优化调整,才能使塔的操作处在一个比较合理的状态下.在实际操作过程中,我们对一些操作指标进行了的优化选择,确定了工艺指标,见表5.裹5nA一108塔工艺指标优化℃工艺指标优化后,DA一108塔塔顶,塔釜的质量有了明显的好转,1997年DA一108塔运行情况见表6.但由于受塔处理能力的限制,在保证塔釜的水值在600×10-6条件下,塔顶DMF的损失量要大些.裹6DA一108塔操作数据1999年第14卷第1期曾雪明高负荷下落剂DMF消耗高的原因浅析?9?24尾气系统的改造2+4.1取消废Q,脱除器废cd,蒸发器(EA一127)作用是把第2精馏塔(DA一107)塔釜液蒸发掉部分q,后将浓缩的阻聚剂(TBC)重新返回系统使用或进至燃料油罐FA—ll8.由于EA一127A/B操作的不稳定性.时常出现超温,满罐现象,极易将凝固点很低的TBC(凝固点为52℃)及渣质夹带至尾气系统,引起尾气总管堵塞.因此取消了EA一127A/B系统,把DA一107塔釜液直接送至液化罐,避免H妃及渣质进人尾气系统.2+4.2FA一119的扩容改造原设计的FA一119罐体积小,各系统排放出的气体在FA一119的停留时间极短,气液很难在罐内得到充分分离后,就排放人火炬系统.因此,随气体夹带出来的DMF得不到很好地回收.在高负荷下(16.5t/h),尾气排放量更大,达到6001,g/h(设计值为4651,g/h),DMF夹带损失更为严重.为此,对FA一119进行了扩容改造:a.把FA一119从qr0600 mm×1400mm扩容至l200mmX2500rm’n;b.改原来的直线进料为侧面切线进料.FA一119经过扩容改造后,提高了尾气在罐中的停留时间,促使气液得到充分分离.回收来的DMF排至FA一112,精制后循环使用,从而较大幅度地减少了尾气夹带DMF的损失2.4.3FA一105罐尾气排放线的改造为降低尾气压力,减少因压力高而造成的尾气管线积液增加现象,将原FA一105罐顶排放至尾气总管改为直接进人火炬总管.2.5DA一105塔回流罐(FA一108)的扩容改造由于装置高负荷(16.5t/h)运行,DA一105塔顶尾气排放量很大,在DA一105塔未作扩容改造的情况下,难以避免塔顶尾气夹带DMF损耗的现象. 为此,我们对回流罐进行扩容改造,以增加气液在罐中的滞留时间,提高分离效果,达到减少夹带DMF 的目的.a.将原罐鹋00rain×2000mm扩容至l200mx3000mm,增大液体的容留体积,增加气液在罐中的分离时间.b.将原罐卧式安装改为立式安装,增加净空高度,减少气液夹带.c.改罐顶进料为侧面切线进料,有利气液在罐中的分离.d.采用低液位控制,增大气液分离空间,进一步减少气液夹带.FA一108扩容改造后,采用了立式,侧面切线进料等措施,有利于气液分离,将很大程度上减少气液夹带.从而降低DMF消耗.26改变DA-105塔的控制方式由于受进料组成,物性因素,尾气压力等影响,在DA一105塔釜加热蒸气量恒定的情况下,第l2 块灵敏板温度很难保持在允许变化范围内,波动很大,从而引起塔顶DMF的夹带损耗.为此,建议把塔釜蒸气加热与灵敏板温度串级起来,通过灵敏板的温度来调节加热汽量.此种控制方式,能使塔顶气体夹带DMF损失得到一定程度的控制.抚顺石油化工公司引进的l5万t/a丁二烯装置就是采用了这种控制方式,效果良好.2.7溶剂消耗比较1996年下半年溶剂消耗情况见表7.裹71996年下半年溶剂消耗情况月份/月单耗曙?tI1月份/月单耗曙?t7669102.6786.611l240954212251从表7可看出,通过技术改造和工艺改进,溶剂消耗有了一定程度的下降,溶剂的单耗由3季度的6.3l【g/t下降到4季度的2.5kg/t,但与达标值1.0k/h还有一定的差距.随着FA一108和FA一119扩容改造项目的投用,溶剂单耗有望达到设计值.3结语在高负荷下,装置设计能力的不足,是造成溶剂DMF消耗难于达到设计值(1.0kg/t)的主要原因.随着装置负荷的不断提高,这一问题将更为突出.有必要对DA一105,DA一108塔进行扩容改造.可采用浮阀塔盘改为导向浮阀塔盘方法或TP4型错排条形浮阎塔盘来提高塔的处理能力.尽快对闲置的,设计中存在缺陷的DA一108B塔进行技术改造, 一方面弥补DA一108A处理能力的不足,另一方面可用来处理洗涤水和回收废液,回收DMF.(审稿编委:徐培仕高级工程师)。
化学技术中的反应条件优化与工艺放大实例

化学技术中的反应条件优化与工艺放大实例化学反应是现代工业生产中非常重要的一环,如何优化反应条件及放大工艺成为了提高生产效率和降低生产成本的关键。
在本文中,将以几个实际案例来探讨化学技术中的反应条件优化与工艺放大的重要性和实施方法。
案例一:催化剂的优化选择催化剂在化学反应中起着举足轻重的作用,它能够加速反应速率,改变反应路径,并降低反应温度和能量要求。
在某化学工艺中,使用的催化剂被发现在工业生产中效果不佳,导致产品质量不稳定。
为了解决这个问题,需要对催化剂进行优化选择。
首先,通过理论计算和实验测试,确定催化剂在特定反应条件下的活性和稳定性。
同时,考虑到成本和可持续性,选择合适的催化剂基于其活性、选择性、廉价性和环境友好性。
其次,采用适当的方法改善催化剂的性能。
例如,可以通过改变催化剂的物理和化学性质来提高其活性和稳定性。
此外,使用载体材料、调整催化剂的物理形态和表面性质等也可以增强其催化性能。
最后,在实际生产中,需要对催化剂进行合理的控制和监测,以保证反应条件和催化剂的使用寿命。
通过定期的清洗、再生或更换,可以最大限度地利用催化剂的性能,实现反应条件的优化和生产工艺的放大。
案例二:溶剂的选择和反应条件优化溶剂在化学反应中扮演着重要的角色,它可以影响反应速率、选择性和产率。
在某化学合成反应中,使用的溶剂对环境友好性要求较高,但目前的反应条件下,溶剂的利用率低且产生大量有机废弃物。
为了优化反应条件和提高溶剂利用率,需要对溶剂的选择和反应条件进行优化。
首先,选择具有较高溶解能力和选择性的溶剂。
能够通过理论计算和实验测试来确定溶剂对于特定反应的影响。
同时,需考虑溶剂的成本、易购买性以及对环境的潜在影响,选择符合工业生产要求的合适溶剂。
其次,优化反应条件以提高溶剂利用率。
通过调整反应温度、压力和反应物浓度等条件,可以降低溶剂在反应中的消耗量,提高反应产率和选择性。
最后,在实际生产中,需采用恰当的分离和回收技术,以最大限度地回收和再利用溶剂。
MDEA溶剂的热降解与净化
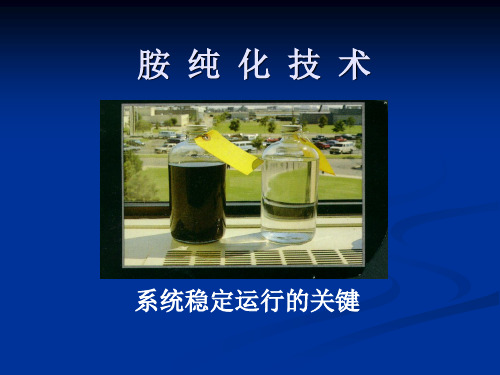
MPR
.
杂质2 - 降解产物
主要的降解产物是氨基酸类的酸性物质 影 响
1、破坏系统的保护层FeS(S) ,系统中降解产物量增加会加大腐蚀速率, 胺的供应商推荐 <250 ppm
增加系统的不安定性
2、运行中增加胺的损耗及减少有效胺的量 系统中降解产物的增加,导致胺的起泡高度/破裂参数上升,增 加了吸附塔和再生塔中胺的夹带量,造成胺的损耗;另外有效胺 的量也会下降。 3、增加热损失 降解产物在热交换器上沉积会导致热交换效率下降。
MPR
.
♂溶解及降解损失 :溶解损失是胺在液态烃中
的溶解损失;降解损失是胺溶剂的热降解及
与杂质生成 HSS-(热稳定盐)的损失。
♂夹带损失:传质设备缺陷及内件损坏、操作条件
变化所造成的过饱和损失。
♂发泡损失 :系统存在溶剂发泡诱因(如重烃、
固体颗粒、其它有机物等)所带来的溶剂大量跑损
夹带损失及发泡损失约占溶剂损失的80%
300
200
Incursion of Chlorides
100
0
MPR
.
MPR的产品
Performance of Gylcolex TM Unit at a Gulf Coast Aromatics Extraction Plant- Solvent TEG
700
600
500
Chlorides in System PPM
胺 纯 化 技 术
系统稳定运行的关键
MPR
.
胺法气体脱硫
天然气、炼厂气脱硫应用最广泛、最成熟的脱硫工艺。
MPR
.
胺的工作目的及原理
目的:
从气体或者液体中去除酸性气体(H2S/CO2) 从酸性气体中回收硫 原理: 自由胺 + 酸气 束缚胺阳离子 + 酸阴离子 束缚胺阳离子 + 热 自由胺 + 酸气 “ 束缚胺”是不能吸附酸性气体的
- 1、下载文档前请自行甄别文档内容的完整性,平台不提供额外的编辑、内容补充、找答案等附加服务。
- 2、"仅部分预览"的文档,不可在线预览部分如存在完整性等问题,可反馈申请退款(可完整预览的文档不适用该条件!)。
- 3、如文档侵犯您的权益,请联系客服反馈,我们会尽快为您处理(人工客服工作时间:9:00-18:30)。
降低溶剂消耗量的方法-节省乙腈溶剂的对策-岛津制作所在HPLC的UV检测中,HPLC用乙腈由于在短波长一侧的干扰较少等,而得到广泛应用,但最近一段时间,乙腈短缺,价格攀升。
乙腈是生产丙烯腈时的副产物,由于以丙烯腈为主原料的ABS树脂(用途:汽车零部件等)的减产,乙腈的生产量以及库存都在减少。
本文就如何节省乙腈溶剂进行了说明,从日常可做到的少量节约,到有效利用已有LC 系统大幅降低溶剂使用量。
由于分析上的制约以及样品的不同,最佳方法也不尽相同,但为了降低分析业务成本、保护环境,您不妨进行一下以下尝试。
1日常可做到的节约 (3)1-1) 将色谱柱清洗溶剂变更为甲醇1-2) 降低调整、分析结束后停机时消耗的溶剂量1-3) 在等度洗脱条件下进行流动相2液混合 (已有梯度洗脱系统时)2使用已有LC系统时的方法 (5)2-1) 流动相从乙腈变更为甲醇2-2) 使用高性能短色谱柱3变更已有LC系统的配置 (9)3-1) 色谱柱内径的尺寸减小(半微量化)・・分离得以保留不变,降低流动相流量 3-2) 快速化 ・・使用分离性能出色的小尺寸色谱柱,缩短分析时间3-3) 溶剂再循环・・未检测到峰时,将从检测器出口排出的洗脱液返回到流动相储液瓶中,以节约溶剂4介绍省溶剂实施方案 (18)・・将已有LC系统升级为省溶剂型LC系统1日常可做到的节约首先,完善乙腈的库存管理,最为重要的是在流动相储液瓶上记载使用者的姓名、流动相组成/配制日期(避免因内容不明而废弃流动相)。
并且,重新审视日常的分析业务,通过实行以下措施,可以减少溶剂的浪费。
(1)将色谱柱清洗溶剂变更为甲醇(2)降低在分析前的调整以及分析结束后停机时消耗的溶剂量(3)在等度洗脱条件下进行流动相2液混合 (已有梯度洗脱系统时)1-1) 将色谱柱清洗溶剂变更为甲醇您是否因为分析流动相使用的是乙腈,所以在色谱柱清洗中也在使用着乙腈呢?为了将用于分析的乙腈变更为甲醇,需要考虑分离模式的变化,但在多数的场合下,可以使用甲醇进行清洗。
有时甲醇的清洗效果高于乙腈。
但是,甲醇/水系的压力高于乙腈/水系,因此,在开始清洗时,请以较小的流量(分析时流量的一半左右),边观察压力的变化边送液。
(在使用甲醇之前,请阅读色谱柱说明书确认是否可以使用甲醇。
) 并且,甲醇的比例设定要高于现在所用清洗液的乙腈比例。
(比如,清洗液的乙腈比例为50%时,设定甲醇的比例为80%等。
) 特别是含碱性化合物时,如果使用混合0.1%左右磷酸水的清洗液则可提高清洗效果。
分析结束后卸下色谱柱,有时出于流路清洗或长期保管的目的,使用不同于流动相的溶剂置换流路,同样,也可使用甲醇代替乙腈。
1-2)降低调整、分析结束后停机时消耗的溶剂量在分析前进行流动相送液直到基线稳定以实施调整,或在分析后停机时进行送液直到色谱柱温度降低,您是否曾经在这些时候离开装置而造成了过度送液?如果利用LC工作站(LCsolution等)、系统控制器的自动化功能,可在一定时间之后开始分析或停止泵的送液。
使用这样便利的功能,可以抑制非实际测定时的无谓的流动相消耗量 。
1-3)在等度洗脱条件下进行流动相2液混合(已有梯度洗脱系统时)在等度洗脱分析时,一般预先将水系和有机溶剂系溶剂混合后使用,但是,有没有发生过在分析结束后还剩有混合溶剂而造成浪费的情况呢?即使在等度洗脱分析时也可以与高压梯度洗脱一样利用2台送液单元进行混合,或者使用低压梯度洗脱单元进行混合。
在等度洗脱分析中,为了避免在分析中流动相用尽而多准备一些流动相,往往在最后废弃多余的部分(短时期内尚可保存,但有可能因蒸发而组成发生变化)。
并且,在探讨分析条件中,继续以其他的分析条件进行尝试时,如果流动相预先混合好,则就只好废弃掉未用完的流动相,造成无谓的溶剂消耗。
在梯度洗脱系统中,有机溶剂是由独立的流动相储液瓶供给,即使在不同的流动相条件下,有机溶剂仍然可以再利用。
虽然在要求微妙分离的分析中,需要与使用预先混合的流动相时的分离状况进行比较讨论,但在大部分的事例中,不需要大幅变更分析条件等,可实现节省溶剂。
2使用已有LC系统时的方法2-1)流动相从乙腈变更为甲醇如有可能,还可以考虑将用于流动相的乙腈置换为甲醇。
但由于洗脱选择性的差异等原因,分离或分析条件有可能发生变化。
置换为甲醇时必须注意以下事项。
1)吸光度在UV低波长侧,甲醇的吸收大于乙腈,因此,根据检测波长,有可能基线难以稳定或者噪声变大。
梯度洗脱分析时,与使用乙腈时相比,鬼峰变大。
2)洗脱力乙腈与甲醇的洗脱力不同,与水系的混合系时,乙腈的洗脱力大。
如果将使用乙腈时的条件置换为甲醇时,请尝试提高有机溶剂的比率。
另一方面,有机溶剂极接近或为100%时,溶剂的性质(极性)全面显现,甲醇的洗脱力变大。
甲醇25%乙腈10%3)分离(洗脱)的选择性乙腈与甲醇的分离选择性不同,有时分离度或洗脱顺序发生变化。
这可认为是由有机溶剂分子的化学性质(甲醇:质子性,乙腈:非质子性)的差异所造成的。
方法变更时,需要注意是否对分离产生了影响,但也有时能够分离以水/乙腈系不能分离的成分。
甲醇4)压力甲醇粘性高于乙腈,因此,水/甲醇系时色谱柱压力高于水/乙腈系。
将水/乙腈系的流动相条件置换为甲醇时,先通入较小的流量,边观察送液压力边确定分析流量。
(请您在使用甲醇之前,阅读色谱柱说明书,确认是否可以使用。
)由于较水/乙腈系提高了有机溶剂比率,所以,在甲醇比率为40~60%时,应特别注意。
2-2)使用高性能短色谱柱■概论灵活应用已有LC系统方便地实现省溶剂化的方法之一是变更为内径相同的短色谱柱。
比如,如下例所示,将色谱柱长度缩短至1/2时,分析时间也缩短到1/2。
如果只是简单地更换为同一种填料的短色谱柱,则会发生分离恶化,但将填料粒径从5μm 缩小到2.2μm,就可维持分离。
【色谱柱更换例】现在的色谱柱:150 mm L.×4.6 mmI.D.(Shim-pack VP-ODS; 粒径5μm)新选用的色谱柱:75 mm L.× 4.6 mmI.D.(Shim-pack XR-ODS; 粒径2.2μm)分析条件:梯度洗脱分析时,将时间程序的设定时间全部缩短到1/2。
送液泵的流速、样品的注入量不变更。
梯度洗脱混合器:梯度洗脱分析的时,变更为约一半左右容量的混合器。
(岛津LC时,如果连接的是1.7mL的混合器的话,那么变更连接为0.5mL的混合器)■注意点但是,不能适用于所有的峰。
洗脱比较快的峰或峰数较多时,常规LC与短色谱柱的组合,因配管、检测池产生的色谱柱外扩散的影响,造成理论塔板数降低、分离恶化。
在确定分析条件时,如果使用方法移植程序,则可以判断是否是恰当的移植。
填料的种类与现在使用中的色谱柱不同时,有时因保留特性的差异,分离模式发生变化。
如果认为溶剂消耗量减半仍然未实现省溶剂化时,根据「3-2) 快速化」的说明,如果变更已有LC系统则可以缩短分析时间。
3变更已有LC系统的配置3-1) 色谱柱内径的尺寸减小(半微量化)■原理如果使用填料相同但色谱柱内径小的色谱柱,则流动相消耗量相应于色谱柱的(内径)2而减少。
假设将同质量的样品注入了内径2mm、长度150mm的半微量色谱柱和内径4.6mm、同一长度的常规色谱柱中,如果使流动相线速度相等 (下图中1.0mL/min和0.2mL/min),因为色谱柱的长度相同,所以成分洗脱位置 (保留时间)相同,那么,流动相消耗量减少至原有的1/5。
这被称为半微量LC。
■优点最近,使用同一填料的4.6mmI.D.色谱柱和2mmI.D.色谱柱,大多都已产品系列化。
分离选择性基本上处于同等程度(因充填方法不同多少有些差异,所以,有时分离模式有差异),因此,获得同样的色谱图的可能性高,这是半微量化的特长。
■注意点但是,为使半微量LC可以获得与常规色谱柱相同的分析结果,有需留意的事项。
如果固定相填料相同,那么在同一色谱柱长度时,样品在流动相流速方向上的扩散也在同等程度,所以,在色谱柱洗脱部上的成分谱带宽度(上图的a和b)相同。
b的截面积是a 的1/5,因此,通过检测池部的样品成分的浓度,对应于两色谱柱的流动相流量比,b为a 的5倍,即b响应为a的5倍。
这称为质量灵敏度,色谱柱内径越小,其越大。
但是,这种效果是假设可忽视样品注入容量为前提,实际上,有注入容量的影响,因此,单纯为了获得相同的色谱图,注入容量也需要相应于色谱柱截面积而减少。
在图例 (A和C)中,注入样品容量为1/5,结局响应相等。
这称为浓度灵敏度,与色谱柱内径无关,是一定值。
在半微量LC中,如下面要说明的那样,为了相应于色谱柱截面积抑制色谱柱外扩散,流路使用小内径的配管。
UV检测器的流通池也是小内径的适合,但光路长变短或光路截面积变小时,因光量减少,吸收响应变小。
通常噪声水平变化不大,因此,灵敏度有可能变低。
■制约事项另一方面,抑制配管等造成的色谱柱外扩散的影响是比较重要的。
下图是分别使用半微量LC系统/常规LC系统 (也包括UV检测器检测池)与半微量色谱柱组合,分析p-羟基苯甲酸烷基酯4成分的例子。
可知常规LC系统时,与色谱柱尺寸相比,色谱柱外容量过大,理论塔板数显著降低。
n-丁基对羟基苯甲酸乙酯n-丁基对羟基苯甲酸乙酯使用半微量色谱柱时,为了抑制色谱柱外扩散,配合色谱柱的内径,使用小尺寸的流路配管、检测器检测池。
并且,配合流路整体尺寸的减小,也使用小的梯度洗脱混合器。
自动进样器也要考虑样品通过部分的配管内径(SIL-20A系列,SIL-10ADvp,SIL-HT的配管内径为0.13mm)。
配管内径0.3mmI.D.⇒0.13mmI.D.梯度洗脱混合器 0.5mL (标准最小)⇒100μL(半微量混合器)检测器检测池8μL⇒2.5μL(半微量检测池)另外,与常规LC相比,要求送液单元在低流量域具有流量准确性、精密性等送液稳定性,要求自动进样器具有微量注入时的注入重现性。
Prominence系列可满足这样的基本性能。
交叉污染的影响相对变大,因此,最好使用像SIL-20A那样的采取了降低交叉污染措施(直接注入方式,针表面材质,针清洗,阀材质等)的自动进样器。
已有LC系统可以对应低流量送液、微量样品注入时,半微量化可期待获得大的省溶剂效果。
需要半微量色谱柱时,请向岛津技迩公司问询。
3-2) 快速化超快速分析,实现省溶剂化,降低分析成本在UV检测之中,由于乙腈在短波长侧的干扰少等原因而被普遍使用。
最近乙腈短缺成为人们议论的话题。
在此介绍与之前的方法相比能够大幅降低溶剂消耗量、缩短分析时间的「分析的快速化」方法。
● 通过分析的快速化缩短分析时间分析快速化可以达到什么程度呢?比如,12种头孢类抗生素成分的分析,如果使用常规LC则需要27.5分钟,但使用超快速HPLC UFLC则只需4分钟即可完成。