表面粗糙度
表面粗糙度
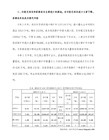
48.表面粗糙度Ra为0.1μm时,表面形状什么特征,如何应用?
答:表面形状特征为暗光泽面,应用于精密机床主轴箱与套筒配合的孔,仪器在使用中要承受摩擦的表面,如导轨、槽面等,液压传动用的孔的表面,阀的工作面,汽缸内表面,活塞销的表面等。一般机械设计界限值。磨削加工很不经济。
配合性质相同,零件尺寸越小,其表面粗糙度值应越小。同一精度等级,小尺寸比大尺寸、轴比孔的表面粗糙度值要小。
对于配合表面,其尺寸公差、形状公差、表面粗糙度应当协凋,一般情况下有一定的对应关系。
39.表面粗糙度Ra为50-100μm时,表面形状什么特征,如何应用?
答:表面形状特征为明显可见刀痕,应用于粗造的加工面,一般很少采用。铸、锻、气割毛坯可达此要求。
42.表面粗糙度Ra为6.3μm时,表面形状什么特征,如何应用?
答:表面形状特征为可见加工痕迹,应用于半粗加工面,支架、箱体、离合器、皮带轮侧面、凸轮侧面等非接触的自由表面,与螺栓头和铆钉头相接触的表面,所有轴和孔的退刀槽,一般遮板的结合面等。
43.表面粗糙度Ra为3.2μm时,表面形状什么特征,如何应用?
表面粗糙度100个问与答
1. 什么称为表面粗糙度?
答:表面粗糙度是指零件加工表面上具有的由较小间距和峰谷所组成的微观几何形状特征。它是一种微观几何形状误差。
2. 表面粗糙度如何产生?
答:零件经切削加工或其他方法所形成的表面,由于加工中的材料塑性变形、机械振动、摩擦等原因,总是存在着几何形状误差。
7. 什么称为评定长度?
表面粗糙度参数
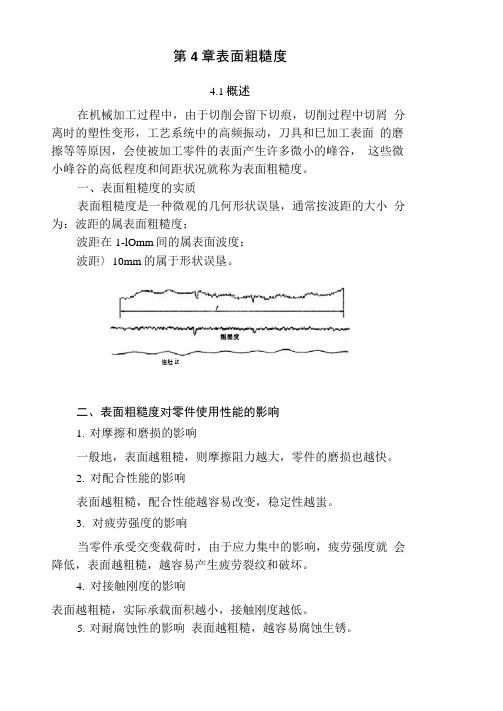
第4章表面粗糙度4.1概述在机械加工过程中,由于切削会留下切痕,切削过程中切屑分离时的塑性变形,工艺系统中的高频振动,刀具和巳加工表面的磨擦等等原因,会使被加工零件的表面产生许多微小的峰谷,这些微小峰谷的高低程度和间距状况就称为表面粗糙度。
一、表面粗糙度的实质表面粗糙度是一种微观的几何形状误垦,通常按波距的大小分为:波距的属表面粗糙度;波距在1-lOmm间的属表面波度;波距〉10mm的属于形状误垦。
住肚it二、表面粗糙度对零件使用性能的影响1.对摩擦和磨损的影响一般地,表面越粗糙,则摩擦阻力越大,零件的磨损也越快。
2.对配合性能的影响表面越粗糙,配合性能越容易改变,稳定性越蚩。
3.对疲劳强度的影响当零件承受交变载荷时,由于应力集中的影响,疲劳强度就会降低,表面越粗糙,越容易产生疲劳裂纹和破坏。
4.对接触刚度的影响表面越粗糙,实际承载面积越小,接触刚度越低。
5.对耐腐蚀性的影响表面越粗糙,越容易腐蚀生锈。
此外,表面粗糙度还影响结合的密封性,产品的外观,表面涂层的质量,表面的反射能力等等,所以要给予充分的重视。
4.2表面粗糙度的评定一•基本术语1•轮廓滤波器把轮廓分成长波和短波成分的滤波器。
2.M虑波器确定粗糙度与波纹度成分之间相交界限的滤波器。
3•取样长度用以判别具有表面粗糙度特征的一段基准线长度。
规定和选取取样长度的目的是为了限制和削弱表面波纹度对表面粗糙度测量结果的影响。
推荐的取样长度值见表41。
在取样长度内一般应包含五个以上的轮廓峰和轮廓谷。
4.评定长度评定表面粗糙度时所必须的一段基准线长度。
为了充分合理地反映表面的特性,一般取1口=51。
5.轮廓中线m 用以评定表面粗糙度值的基准线。
(1)轮廓的最小二乘中线具有几何轮廓形状并划分轮廓的基准线。
在取样长度范围内,使被测轮廓线上的各点至该线的偏距的平方和为最小。
即:(,r Z2J(> " dx = min(2)轮廓的算术平均中线在取样长度内,将实际轮廓划分为上、下两部分,并使上、下两部分的面积相等的基准线。
5 表面粗糙度

(5)对接触刚度的影响
接触刚度影响零件的工作精度 和抗振性。这是由于表面粗糙度使 表面间只有一部分面积接触。一般 情况下,实际接触面积只有公称接 触面积的百分之几。因此,表面越 粗糙受力后局部变形越大,接触刚 度也越低。
3.2
C×45
12
.5
3.2
12
.5
30°
3.2
3.
2
0.4
1.6
12.5
3.2
1.
3.2
12.5
30° 12
.5
3.2
12
.5
3.2
表面粗糙度符号、代号一般注在可见轮廓线、尺寸界线、引出线或它 们的延长线上。符号的尖端必须从材料外指向表面
12.5
6
3.
2
12.5
其余
2 锪平
6.3
3.
2
3.2
取样长度2.5mm
加工方法(铣削)
总加工余量(5mm)
附加标注示例
表面加工纹理方向
部分加工纹理方向符号
说明
(1)当允许在表面粗糙度参数的所有实测值中超过规定值的个数少于总 数的16%时,应在图样上标注表面粗糙度参数的上限值或下限值;
(2)当要求在表面粗糙度参数的所有实测值中不得超过规定值时,应在图样 上标注表面粗糙度参数的最大值或最小值;
二、表面粗糙度与零件使用性能的关系
表面粗糙度与零件使用性能有密切的关系主要表现在以下几 方面:
1.影响摩擦、磨损 2.影响配合性质 3.影响抗腐蚀性 4.影响抗疲劳强度
5.影响接触刚度 6.影响结合密封性
表面粗糙度定义

表面粗糙度的国家标准主要术语及定义(1)表面粗糙度取样长度l取样长度是用于判断和测量表面粗糙度时所规定的一段基准线长度,它在轮廓总的走向上取样。
(2)表面粗糙度评定长度Ln由于加工表面有着不同程度的不均匀性,为了充分合理地反映某一表面的粗糙度特性,规定在评定时所必须的一段表面长度,它包括一个或数个取样长度,称为评定长度Ln。
(3)表面粗糙度轮廓中线m轮廓中线m是评定表面粗糙度数值的基准线。
评定参数及数值国家规定表面粗糙度的参数由高度参数、间距参数和综合参数组成。
表面粗糙度高度参数共有三个:(1)轮廓算术平均偏差Ra在取样长度l内,轮廓偏距绝对值的算术平均值。
(2)微观不平度十点高度Rz在取样长度内最大的轮廓峰高的平均值与五个最大的轮廓谷深的平均值之和。
(3)轮廓最大高度Ry在取样长度内,轮廓峰顶线和轮廓谷底线之间的距离。
表面粗糙度间距参数共有两个:(4)轮廓单峰平均间距S两相邻轮廓单峰的最高点在中线上的投影长度Si,称为轮廓单峰间距,在取样长度内,轮廓单峰间距的平均值,就是轮廓单峰平均间距。
(5)轮廓微观不平度的平均间距Sm含有一个轮廓峰和相邻轮廓谷的一段中线长度Sm i,称轮廓微观不平间距。
表面粗糙度综合参数(6)轮廓支承长度率t p轮廓支承长度率就是轮廓支承长度n p与取样长度l之比。
工件表面粗糙度是数字越小表面越光滑吗?数字的单位是um,看下面的参数可以知道数值越小工件表面越光滑表面粗糙度参数共有3个分别是Ra Rz RyRa 在取样长度内,轮廓偏距绝对值的算术平均值Rz 在取样长度内最大的轮廓峰高的平均值与五个最大的轮廓谷深的平均值之和Ry 在取样长度内,轮廓峰顶线和轮廓谷底线之间的距离顺便说一下表面粗糙度的表示方法:如果粗糙度表示符号是一个对号,里面加小短横,意思是通过加工的方法获得的表面粗糙度如果粗糙度表示符号是一个对号,里面加小圆圈,意思是非加工表面的粗糙度如果粗糙度表示符号是一个对号,里面什么也没有,意思是表面粗糙度无论用什么办法获得都可以如果图面没标注粗糙度选用Ra 还是Rz 还是Ry 的情况下应选用Ra.旧标准是级数越高越光洁,新标准是标注数字越小越光洁.(RMS)微粗糙度表面粗糙度是影响表面的物理和化学性能的重要因素。
表面粗糙度

表面粗糙度
1、表面粗糙度的概念:
零件加工后形成的微观表面状况叫表面粗糙度。
2、表面粗糙度的符号:
基本符号,单独使用这个符号没有意义。
基本符号上加一端线,表示表面粗糙度是用去除材料的方法获得,例如:车、铣、钻、磨、剪切、抛光、腐蚀、电火花加工等。
基本符号上加一圆圈,表示表面粗糙度是用不去除材料的方法获得,例如:铸、锻、冲压、热轧、冷轧、粉末冶金等。
3、表面粗糙度R a值:
R a值越大,表面越粗糙,R a值一般有50、12.5、6.3、3.2、1.6、0.8、0.4 ……0.006微米。
4、表面粗糙度R a值的标注方法:
○1:表面粗糙度标注的一般要求:在同一图样中,每一表面一般只标注一次符号,要标注在可见轮廓线、尺寸界线或延长线上,符号的等边三角形如同刀尖指向并指与被加工的表面。
○2:当零件全部表面的特征要求均相同时,其符号可以在图样的右上角同一标注。
5、表面粗糙度R a值的表面特征如下:
○1:R50 (明显可见刀痕)○2:R25 (微见刀痕)○3:R12.5(可见加工痕迹)○4:R6.3(微见加工痕迹)○5:R3.2(看不见加工痕迹)○6:R3.2(可见加工痕迹的方向)○7:R1.6(微见加工痕迹的方向)○8:R0.8(微辩加工痕迹的方向)○9:R0.4(不可微辩加工痕迹的方向)○10:R0.2 (暗光泽面)○11:R0.1 (亮光泽面)○12:R0.05 (镜状光泽面)○13:R0.025 (雾状光泽面)○14:R0.012 (镜面)。
表面粗糙度
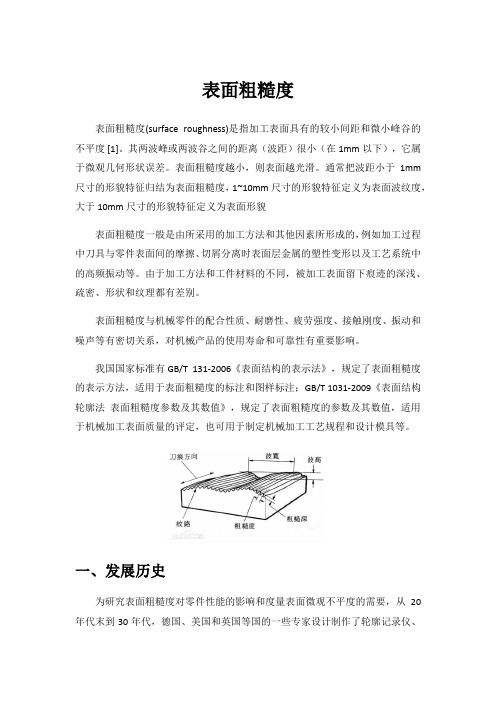
表面粗糙度表面粗糙度(surface roughness)是指加工表面具有的较小间距和微小峰谷的不平度 [1]。
其两波峰或两波谷之间的距离(波距)很小(在1mm以下),它属于微观几何形状误差。
表面粗糙度越小,则表面越光滑。
通常把波距小于1mm 尺寸的形貌特征归结为表面粗糙度,1~10mm尺寸的形貌特征定义为表面波纹度,大于10mm尺寸的形貌特征定义为表面形貌表面粗糙度一般是由所采用的加工方法和其他因素所形成的,例如加工过程中刀具与零件表面间的摩擦、切屑分离时表面层金属的塑性变形以及工艺系统中的高频振动等。
由于加工方法和工件材料的不同,被加工表面留下痕迹的深浅、疏密、形状和纹理都有差别。
表面粗糙度与机械零件的配合性质、耐磨性、疲劳强度、接触刚度、振动和噪声等有密切关系,对机械产品的使用寿命和可靠性有重要影响。
我国国家标准有GB/T 131-2006《表面结构的表示法》,规定了表面粗糙度的表示方法,适用于表面粗糙度的标注和图样标注;GB/T 1031-2009《表面结构轮廓法表面粗糙度参数及其数值》,规定了表面粗糙度的参数及其数值,适用于机械加工表面质量的评定,也可用于制定机械加工工艺规程和设计模具等。
一、发展历史为研究表面粗糙度对零件性能的影响和度量表面微观不平度的需要,从20年代末到30年代,德国、美国和英国等国的一些专家设计制作了轮廓记录仪、轮廓仪,同时也产生出了光切式显微镜和干涉显微镜等用光学方法来测量表面微观不平度的仪器,给从数值上定量评定表面粗糙度创造了条件。
从30年代起,已对表面粗糙度定量评定参数进行了研究,如美国Abbott就提出了用距表面轮廓峰顶的深度和支承长度率曲线来表征表面粗糙度。
1936年出版了Schmaltz论述表面粗糙度的专著,对表面粗糙度的评定参数和数值的标准化提出了建议。
但粗糙度评定参数及其数值的使用,真正成为一个被广泛接受的标准还是从40年代各国相应的国家标准发布以后开始的。
表面粗糙度的基本概念汇总

表面粗糙度的基本概念表面粗糙度的基本概念表面粗糙度的定义(本站相关粗糙度仪的产品介绍:粗糙度仪)表面粗糙度(Surface roughness)是指加工表面上具有的较小间距和峰谷所组成的微观几何形状特性性它是一种微观几何形状误差,也称为微观不平度。
表面粗糙度应与形状误差(宏观几何形状误差)和表面波度区别开。
通常,波距小于 1mm 的属于表面粗糙度,波距在 1~10mm 的属于表面波度,波距大于 10mm 的属于形状误差。
表面粗糙度对机械零件使用性能的影响表面粗糙度的大小对零件的使用性能和使用寿命有很大影响。
1. 影响零件的耐磨性表面越粗糙,摩擦系数就越大,相对运动的表面磨损得越快。
然而,表面过于光滑,由于润滑油被挤出或分子间的吸附作用等原因,也会使摩擦阻力增大和加速磨损。
2. 影响配合性质的稳定性零件表面的粗糙度对各类配合均有较大的影响。
对于间隙配合,两个表面粗糙的零件在相对运动时会迅速磨损,造成间隙增大,影响配合性质;对于过盈配合,在装配时表面上微观凸峰极易被挤平,产生塑性变形,使装配后的实际有效过盈减小,降低联接强度;对于过渡配合,因多用压力及锤敲装配,表面粗糙度也会使配合变松。
3. 影响疲劳强度承受交变载荷作用的零件的失效多数是由于表面产生疲劳裂纹造成的。
疲劳裂纹主要是由于表面微观峰谷的波谷所造成的应力集中引起的。
零件表面越粗糙,波谷越深,应力集中就越严重。
因此,表面粗糙度影响零件的抗疲劳强度。
4. 影响抗腐蚀性粗糙表面的微观凹谷处易存积腐蚀性物质,久而久之,这些腐蚀性物质就会渗入到金属内层,造成表面锈蚀。
此外,表面粗糙度对接触刚度、密封性、产品外观、表面光学性能、导电导热性能以及表面结合的胶合强度等都有很大影响。
所以,在设计零件的几何参数精度时,必须对其提出合理的表面粗糙度要求,以保证机械零件的使用性能。
公差等级与粗糙度的关系表面粗糙度是反映零件表面微观几何形状误差的一个重要技术指标,是验证零件表面质量的主要依据;它选择的合理与否,直接关系到产品的质量,使用寿命和生产成本。
表面粗糙度及加工符号

轮廓算术平均偏差(Ra)是目前生产中评定表面粗糙度用的最多的参数,Ra 值越小,表面质量就越高。
§9-4 表面粗糙度的符号、代号及其标注
不同表面粗糙度的外观情况,加工方法和应用举例:
Ra(μm) 表面外观情况
主要加工方法
需要表示镀 (涂)覆或 其它表面处 理后的表面 粗糙度值时
需要表示镀 (涂)覆前 的表面粗糙 度值时,应 另加说明
若同时要求 表示镀(涂) 覆前及镀 (涂)覆后 的表面粗糙 度值时
§9-4 表面粗糙度的符号、代号及其标注
~
~
零件局部热处理或局部镀(涂)覆时,应 用粗点画线画出其范围,并标注相应的尺 寸,也可将其要求注写在表面粗糙度符号 长边的横线上
数字与字母的高度h
2.5 3.5 5 7 10 14 20
符号的线宽d’ 数字与字母的笔画宽度d 0.25 0.35 0.5 0.7 1 1.4 2
高度H1
3.5 5 7 10 14 20 28
高度H2
8 11 15 21 30 42 60
§9-4 表面粗糙度的符号、代号及其标注
三、表面粗糙度、镀(涂)覆及热处理在图样上的标注方法
表面、齿轮轮齿的工作表面等
0.10 暗光泽面 0.05 亮光泽面
研磨、抛光、超级精细研磨 精密量具的表面、极重要零件的摩擦
等
面,如气缸的内表面、精密机床的主
轴颈、坐标镗床的主轴颈等
0.025 镜状光泽面
0.012 雾状镜面
0.006 镜面
二、表面粗糙度的符号和代号 1、表面粗糙度符号
符号
§9-4 表面粗糙度的符号、代号及其标注
表面粗糙度定义

表面粗糙度(表面光洁度)的定义及说明一,表面粗糙度/表面光洁度定义国家标准主要术语及定义本资料给出的参数符合GB/T 3505-2000《产品几何技术规范表面结构轮廓法表面结构的述语、定义及参数》。
图一:放大n倍后的工件截面/表面粗糙度及轮廓:图二:各种加工方法能得到的表面光度:表面粗糙度关键技术术语:(1)表面粗糙度:取样长度L: 取样长度是用于判断和测量表面粗糙度时所规定的一段基准线长度,它在轮廓总的走向上取样。
(2)表面粗糙度:评定长度Ln:由于加工表面有着不同程度的不均匀性,为了充分合理地反映某一表面的粗糙度特性,规定在评定时所必须的一段表面长度,它包括一个或数个取样长度,称为评定长度Ln。
(3)表面粗糙度:轮廓中线(也有叫曲线平均线)M轮廓中线M是评定表面粗糙度数值的基准线。
评定参数及数值:国家规定表面粗糙度的参数由高度参数、间距参数和综合参数组成。
表面粗糙度高度参数共有三个:(1)轮廓算术平均偏差Ra :在取样长度l内,轮廓偏距绝对值的算术平均值。
(2)微观不平度十点高度Rz在取样长度内最大的轮廓峰高的平均值与五个最大的轮廓谷深的平均值之和。
(3)轮廓最大高度Ry在取样长度内,轮廓峰顶线和轮廓谷底线之间的距离。
表面粗糙度间距参数共有两个:(4)轮廓单峰平均间距S 两相邻轮廓单峰的最高点在中线上的投影长度Si,称为轮廓单峰间距,在取样长度内,轮廓单峰间距的平均值,就是轮廓单峰平均间距。
(5)轮廓微观不平度的平均间距Sm,含有一个轮廓峰和相邻轮廓谷的一段中线长度Smi,称轮廓微观不平间距。
表面粗糙度综合参数:(6)轮廓支承长度率tp 轮廓支承长度率就是轮廓支承长度np与取样长度L之比。
另附:表面光洁度与粗糙度Ra、Rz数值换算表(单位:μm)表面粗糙度符号表面粗糙度surface roughness加工表面上具有的较小间距和峰谷所组成的微观几何形状特性。
它是互换性研究的问题之一。
表面粗糙度一般是由所采用的加工方法和其他因素所形成的,例如加工过程中刀具与零件表面间的摩擦、切屑分离时表面层金属的塑性变形以及工艺系统中的高频振动等。
详解表面粗糙度
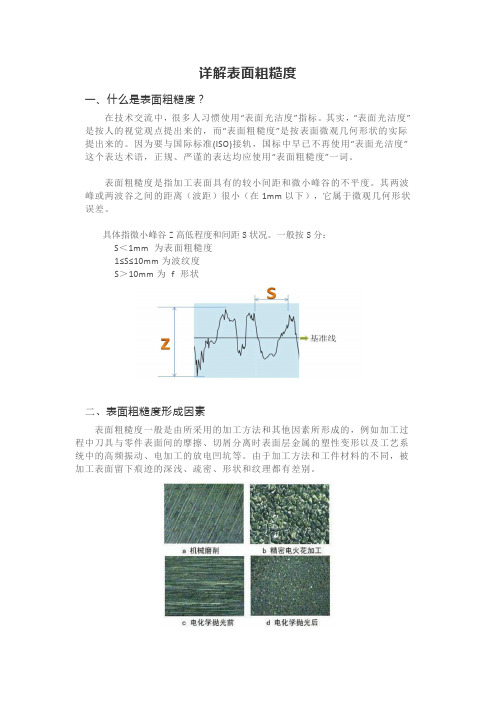
详解表面粗糙度一、什么是表面粗糙度?在技术交流中,很多人习惯使用“表面光洁度”指标。
其实,“表面光洁度”是按人的视觉观点提出来的,而“表面粗糙度”是按表面微观几何形状的实际提出来的。
因为要与国际标准(ISO)接轨,国标中早已不再使用“表面光洁度”这个表达术语,正规、严谨的表达均应使用“表面粗糙度”一词。
表面粗糙度是指加工表面具有的较小间距和微小峰谷的不平度。
其两波峰或两波谷之间的距离(波距)很小(在1mm以下),它属于微观几何形状误差。
具体指微小峰谷Z高低程度和间距S状况。
一般按S分:S<1mm为表面粗糙度1≤S≤10mm为波纹度S>10mm为f形状二、表面粗糙度形成因素表面粗糙度一般是由所采用的加工方法和其他因素所形成的,例如加工过程中刀具与零件表面间的摩擦、切屑分离时表面层金属的塑性变形以及工艺系统中的高频振动、电加工的放电凹坑等。
由于加工方法和工件材料的不同,被加工表面留下痕迹的深浅、疏密、形状和纹理都有差别。
三、表面粗糙度评定依据1)取样长度各参数的单位长度,取样长度是评价表面粗糙度规定一段基准线的长度。
在ISO1997标准下一般使用0.08mm、0.25mm、0.8mm、2.5mm、8mm为基准长度。
Ra、Rz、Ry的取样长度L与评定长度Ln选用值2)评定长度由N个基准长度所构成。
零部件表面各部分的表面粗糙度,在一个基准长度上无法真实地体现出粗糙度真实参数,而是需要取N个取样长度来评定表面粗糙度。
在ISO1997标准下评定长度一般为N等于5。
3)基准线基准线是用以评定表面粗糙度参数的轮廓中线。
四、表面粗糙度评定参数1)高度特征参数Ra轮廓算术平均偏差:在取样长度(lr)内轮廓偏距绝对值的算术平均值。
在实际测量中,测量点的数目越多,Ra越准确。
Rz轮廓最大高度:轮廓峰顶线和谷底线之间的距离。
在幅度参数常用范围内优先选用Ra。
在2006年以前国家标准中还有一个评定参数为“微观不平度十点高度”用Rz表示,轮廓最大高度用Ry表示,在2006年以后国家标准中取消了微观不平度十点高度,采用Rz表示轮廓最大高度。
表面粗糙度的评定标准及方法

表面粗糙度的评定标准及方法当钢材表面经喷射清理后,就会获得一定的表面粗糙度或表面轮廓。
表面粗糙度可以用形状和大小来进行定性。
经过喷射清理,钢板表面积会明显增加很多,同时获得了很多的对于涂层系统有利的锚固点。
当然,并不是粗糙度越大越好,因为涂料必须能够覆盖住这些粗糙度的波峰。
太大的粗糙度要求更多的涂料消耗量。
一般的涂料系统要求的粗糙度通常为 Rz40~75微米.1.粗糙度的定义对表面粗糙度的定义有以下几种:hy:在取样长度内,波峰到波谷的最大高度, ISO8503—3(显微镜调焦法)Ry:在取样长度内,波峰到波谷的最大高度,ISO8503—4(触针法)Ra:波峰和波谷到虚构的中心线的平均距离, ISO 3274Ry5:在取样长度内,五个波峰到波谷最大高度的算术平均值,ISO8503—4(触针法)有关 Rz的表述与 Ry5其实是相同的,Rz的表述来自于德国标准 DIN 4768-1.Ra和 Rz 之间的关系是 Rz相当于 Ra 的 4~6倍。
2. 表面粗糙度的评定标准为了测定钢板表面粗糙度,不同的标准规定了相应的仪器可以使用,测量值以微米(µm)为单位。
国际标准分 ISO 8503 成五个部分在来说明表面粗糙度:ISO8503—1:1995表面粗糙度比较样块的技术要求和定义ISO8503-2:1995喷射清理后钢材表面粗糙度分级―样板比较法ISO8503-3:1995 ISO基准样块的校验和表面粗糙度的测定方法―显微镜调焦法ISO8503—4:1995 ISO基准样块的校验和表面粗糙度的测定方法,触针法ISO8503-5:2004表面轮廓的复制胶带测定法我国的国家标准 GB/T 13288-91《涂装前钢材表面粗糙度等级的评定(比较板块法)》,参照 ISO8503所制订。
3。
比较样块法评定表面粗糙度在涂装现场较为常用的粗糙度评定方法是比较样块法。
常用的粗糙度比较块有英国易高elcometer125,荷兰TQC LD2040、LD2050以及英国PTE R2006、R2007等。
表面粗糙度的基本知识
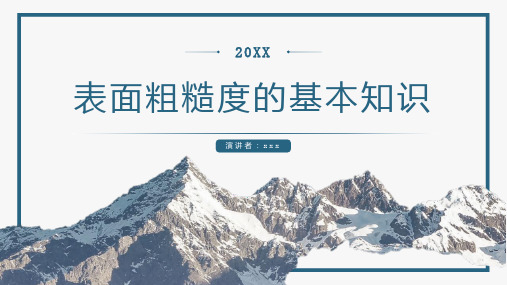
Rz则表示在取样长度内 ,五个最大的轮廓峰高 的平均值和五个最大的 轮廓谷深的平均值之和
Part 4
表面粗糙度对机械 零件性能的影响
表面粗糙度对机械零件性能的影响
1
表面粗糙度对机械零件的性能和寿命 具有重要影响
例如,对于需要承受摩擦和磨损的零 件,表面粗糙度会直接影响其耐磨性
和疲劳强度
2
3
此外,表面粗糙度还会影响零件的配 合性能、密封性能和外观质量等
未来发展趋势
➢ 总之,表面粗糙度是机械 制造领域中一个非常重要 的概念和技术参数。了解 和掌握表面粗糙度的基本 知识对于提高产品质量、 延长零件寿命以及提高制 造水平都具有重要意义。 同时,随着科技的不断进 步和创新,未来对于表面 粗糙度的研究和发展将更 加深入和广泛
-
XXX
感谢各位观看
xxxxxxxxx
Part 5
表面粗糙度的测 量方法
表面粗糙度的测量方法
1
表面粗糙 度的测量 2
方法
3
表面粗糙度的测量方法有多种,包括触针法、干涉法、 光干涉法等
其中,触针法是最常用的测量方法之一,通过在表面 上放置一个微小的触针,使其沿着表面移动,记录触 针在垂直方向上的位移变化来计算表面粗糙度
干涉法则是利用光的干涉原理来测量表面粗糙度,通 过将表面反射的光与标准反射镜反射的光进行干涉, 从而获得表面的微观几何形状信息
演讲人:XXX 时间:20XX年XX月XX日
表面粗糙度概念
Part 2
表面粗糙度的形 成原因
表面粗糙度的形成原因
Part 3
表面粗糙度的评 定参数
表面粗糙度的评定参数
表面粗糙度的评定参数 包括轮廓算术平均偏差 (Ra)、微观不平度十点 平均高度(Rz)等
表面粗糙度及其评定标准

二、表面粗糙度对零件使用性能的影响
5. 对结合面密封性的影响
粗糙的表面结合时,两表面只在局部点上接触,中间有缝隙,影响密封性。 6. 表面接触刚度
粗糙的表面在表面间的实际接触面积越小,单位面积受力越大,会使峰顶 处的局部塑性变形加剧,接触刚度降低,影响机器的工作精度和抗振性。
此外,表面粗糙度对零件的外观、测量精度、表面光学性能、导电导热性能和 胶合强度等也有着不同程度的影响。因此,在零件设计过程中必须合理选择表 面粗糙度。
一、表面粗糙度的定义
在放大镜下,可以观察出零件表面具有高低不平的峰谷,这种由较小 间距和峰谷所组成的微观几何形状误差,称为表面粗糙度。
一、表面粗糙度的定义
通常按照零件表面相邻波峰或相邻波谷之间的距离来划分零件表面的 几何形状误差
(1)表面粗糙度:零件表 面峰谷波距λ <1mm,属微 观误差,图5-2(b) (2)表面波纹度:零件表 面峰谷波距λ在1~10mm之 间,图5-2(c) (3)形状公差:零件表面 峰谷波距λ >10mm,属宏 观误差,图5-2(d)
(8)评定长度ln 评定长度是指用于评定被评定轮廓的X轴方向上的长度。评定长度包含一个 或几个取样长度,通常取ln=5lr。
三、表面粗糙度的评定标准
2. 几何参数术语
(1)R参数、P参数、W参数 在粗糙度轮廓上计算所得的参数称为R参数。而在原始轮廓和波纹度轮廓上 计算所得的参数分别称为P参数和W参数。
3. 表面轮廓参数定义 (1)幅度参数(峰和谷) ④轮廓单元的平均高度Rc 是指在一个取样长度内轮廓单元高度Zt的平均值
三、表面粗糙度的评定标准
3. 表面轮廓参数定义
(2)幅度参数(纵坐标平均值)
①评定轮廓的算术平均偏差Ra 是指在一个取样长度lr内纵坐标值Z(x)绝对值的算术平均值
- 1、下载文档前请自行甄别文档内容的完整性,平台不提供额外的编辑、内容补充、找答案等附加服务。
- 2、"仅部分预览"的文档,不可在线预览部分如存在完整性等问题,可反馈申请退款(可完整预览的文档不适用该条件!)。
- 3、如文档侵犯您的权益,请联系客服反馈,我们会尽快为您处理(人工客服工作时间:9:00-18:30)。
• 表面粗糙度是指工件表面上具有的较小间距的微小峰谷组 成的微观几何形状特性。表面缺陷应从中排除,且不考虑 表面其他物理特性诸因素;为避免与光亮,清洁的概念混 淆并与国际间称呼一致,不采用“表面光洁度”这一术语, 而称作表面粗糙度。表面粗糙度是在机械加工过程中,由 于刀痕,材料的塑性变形,工艺系统的高频振动,刀具与 被加工表面的摩擦等原因引起的。它对零件的配合性能, 耐磨性,抗腐蚀性,接触刚度,抗疲劳强度,密封性和外 观等都有影响。为了提高产品质量,促进互换性生产,必 须对表面粗糙度的评定方法,测量手段等提出科学的规定 和要求。表面粗糙度是工件表面上的微观几何特性。形状 误差是工件表面上的宏观几何特性。而表面波纹度是工件 表面上介于微观和宏观几何特性之间的特性。形状误差, 波纹度,粗糙度常于一个表面轮廓叠加出现,这中结构即 为所有表面几何误差的总和。表面波纹度是间距比粗糙度 大得多,随机的或接近周期形式的成分构成的表面不平度。
• 2表面粗糙度的评定参数: 表面粗糙度的常用评定参 数有5个即: • 轮廓的算术平均偏差Ra • 轮廓单元的平均线高度Rc • 轮廓的最大高度Rz • 轮廓单元的平均宽度RSm • 轮廓的支承长度率Rmr(c) • 与高度特性有关的参数为Ra,Rc,Rz,它们是基本评定参数。 • 与间距特性有关的参数为RSm. • 与形状特性有关的参数为Rmr(c)。
• • • • • • • • •
加工纹理方向的符号有下列几种: ⑴ =:纹理方向平行于注有符号的视图投影面。 ⑵ ⊥:纹理方向垂直于注有符号的视图投影面。 ⑶ X:纹理对注有符号的视图投影面是两个相交的方相。 ⑷ M:纹理呈多方向。 ⑸ C:纹理对于注有符号表面的中心来说是近似同心圆。 ⑹ R:纹理对于注有符号表面的中心来说近似放射形。 ⑺ P:纹理无方向或呈凸起的细粒状。 表面粗糙度在图样的标注示例,如图所示。
磨削加工表面的粗糙度
• 磨削加工表面粗糙度的形成是磨料颗粒在工件表面的划痕 和材料的塑性变形来决定的,若工件表面划痕越细越密越 均匀,则表面粗糙度数值就越小,若工件表面塑性变形越 小,则划痕两侧翻起越小,则表面粗糙度数值越小。 • ⑴几何因素的影响: a砂轮粒度,粒度号越大,即砂 粒越细,工件表面的划痕就越多越细,表面粗糙度数值就 越小。但磨粒过细,则易发生砂轮堵塞,破坏表面粗糙度。 所以一般粗磨、精磨、铣磨时使用砂轮粒度号应逐步增大。
• b砂轮硬度,砂轮过软,砂粒容易脱落,砂轮工作表面不 易保持,其等高性被破坏,造成粗糙度数值增大。若砂轮 太硬,砂粒钝化后不易脱落,造成塑性变 • 形增大,粗糙度数值增大。砂轮硬度既是几何因素又是物 理因素之一。一般磨削硬度高的工件砂轮采用软一些,磨 削硬度低的工件砂轮可采用硬一性。 • C砂轮的修整 对于要求粗糙度数值小的工件,修整砂 轮的要求就要严格,即砂轮工作表面砂粒的微刃性和等高 性要求就高。为此砂轮修整时要求金刚石修整笔尖锋锐, 背吃刀量小,进给量小且均匀。工件表面粗糙度数值越小, 这些要求就越高。
• ⑸轮廓的支承长度率Rmr(c) 它是指在给定水平位置C 上轮廓的实体材料长度ML(c)与评定长度Ln的比率。 • 即 • • 轮廓峰顶线和平行于它并与轮廓相交的截线之间的距离称 为水平位置C.C值可用微米或Rz的百分数表示。选用轮廓 支承长度率参数时必须同时给出水平位置C值。 目前 只有少数仪器可以直接测量Rmr(c).它是评定零件表面耐 磨性能比较合理的指标。具有相同间距和相同高度的轮廓, 因形状特性不相同,其表面耐磨性也会不同。
切削加工表面粗糙度:
• 影响切削加工表面粗糙度的因素有几何因素,物理因素和 振动。 • ⑴几何因素:是指刀具几何形状的复映,尖刀和圆弧刀车 削时的残留高度H,圆弧刀的H值明显小于尖刀的H值所以 就降低了工件表面的粗糙度数值。适当增大刀具的前角和 到刃的刃磨质量(如刃口无缺陷,前后刀面的粗糙度数值 小)也是有效的减小工件表面粗糙度数值的措施。 • ⑵物理因素: ①工件材料:材料切削加工中塑性变形 大,则粗糙度就差。中、低碳钢工件其韧性好,加工中塑 性变形大,表面粗糙度数值就达,因此这些材料常安排调 质或正火处理,提高切削性能,使其塑性变形减小,可减 表面粗糙度数值。脆性材料切削时由于切削的崩碎产生麻 点,影响表面粗糙度,可以采用适当的热处理来细化金相 组织的晶粒大小,也可采用磨削的加工方法来提高表面粗 糙度。
• ⑵评定长度Ln 为了充分反映微观几何形状误差不均匀 的程度,测量评定粗糙度轮廓所必须的一段长度。一般情 况,评定长度取为取样长度的5倍,并以5个取样长度内的 粗糙度数值的平均值作为评定长度内的粗糙度的可靠值。 均匀性较差的粗糙度轮廓可选用大于5L的评定长度值,均 匀性较好的粗糙度轮廓可选用小于5L的评定长度值。 • ⑶轮廓中线m 是具有几何轮廓形状并划分轮廓的基准 线,是在取样长度内,按最小二乘法拟合所确定的轮廓线。
表面粗糙度的标注方法:
• 表面粗糙度新国家标准取消了按Ra系列值划分为▽1~ ▽14等级的规定,而是按选定的评定参数及其所允许的数 值表示。表面粗糙度的标注符号为与被注轮廓线倾斜成 60°的左右两条不同长度的直线,长线约为短线的二倍, • ① • 限值为3.2a 表示用任何方法获得的表面粗糙度,Ra的上
• ⑵物理因素: 指工件材料、磨削用量、冷却液等方面 的影响。 • a铜、铝及和金材料工件,一般采用精切方法来或得粗糙 度数值小的表面,若采用磨削加工,普通砂轮很容易堵塞, 破坏表面粗糙度,必须采用金刚石砂轮。硬脆材料的工件, 如花岗岩,硬质合金,淬火钢等可选用金刚石砂轮。CBN 砂轮和橡胶结合剂的砂轮。耐热钢磨削时还会发生磨削烧 伤,影响工件的表面质量。所以,根据工件材料选用合适 材质的砂轮,以便满足工件粗糙度的要求。
• ⑴轮廓的算术平均偏差Ra 它是指在一个取样长度内, 被测轮廓上各点至轮廓中线偏距绝对值的算术平均值
• 即 此参数反映表面轮廓信息较全面, 概念直观,用于测量的电子仪器的电路设计比较简单,用 触针式电动轮廓仪测量时,可以直接读出Ra的数值。 • ⑵轮廓单元的平均线高度Rc 它是指在一个取样长度内, 轮廓峰和轮廓谷组合的轮廓单元高度Zt的平均值。即
• 3表面粗糙度参数及其允许值的确定:Ra,Rc,Rz三个高度 参数中,Ra是主参数,可选其中一个或Ra和Rz,Rc和Rz 的组合。对于大多数表面来说,一般只给出一个高度参数。 在长用参数范围内(Ra为0.025~6.3位米,Rc为0.1~25 微米)推荐优先选用Ra。当仅用高度参数不能满足功能 要求时,可选用附加评定参数RSm或Rmr(c)。当Ra< 0.025微米或者Ra>6.3微米且没有标准样块或者对于触针 可能引起变形的软材料表面,为了提高测量精度可选用参 数Rc.Ra,Rc,Rz高度参数的允许值标准数值系列可见下表。 Ra与Rc的数值从理论上讲无严格的对应关系,但要求不 高时,可按下式近似换算; • 当Ra≥2.0微米时;Ra:Rc=1:4,当Ra<2.0微米时, Ra:Rc=1:5。此比例式仅供参考。
• 此参数概念直观。对于此参数需要辨别高度和间距。除非 另有要求,省略标注的高度分辨力应按Rz的10%选取。省 略标注的间距分辨力应按取样长度的1%选取。上述两个 条件都应满足。
• ⑶轮廓的最大高度Rz它是指在一个取样长度内,最大轮廓 峰高Zp和最大轮廓谷深Zv之和的高度即 Rz=Zp+Zv 这个参数测量比较简单,对不允许有较深加工痕迹的 表面有实用意义。 • ⑷轮廓单元的平均宽度RSm它是指在一个取样长度内,轮 廓峰和轮廓谷组合的轮廓单元宽度Xs的平均值。即 • 一般情况下,高度分辨力按Rz的10%选取, 间距分辨力按取样长度Lr的1%选取。对于Rc参数也适用。 RSm参数可按制造加工痕迹的细密程度,对密封性,接触 刚度等有一定影响,概念比较直观,可用性能比较完善的 触针式电动轮廓仪测量。
• ⑴同一零件上,工作表面的粗糙度允许值应小于非工作面 的表面粗糙度允许值; • ⑵受循环载荷的表面及易引起应力集中的表面(如圆角, 沟槽)粗糙度允许值要小; • ⑶配合性质相同时,零件尺寸小的比尺寸大的表面粗糙度 允许值要小;同一公差等级,轴比孔的表面粗糙度允许值 要小; • ⑷运动速度高,单位压力大的摩擦表面比运动速度低,单 位压力小的摩擦表面粗糙度允许值小; • ⑸一般来讲,表面形状精度要求高的表面,表面粗糙度允 许值也小; • ⑹不同的表面粗糙度允许值,其加工方法是不同的,因此, 经济效果也是不同的,在选择表面粗糙度允许值时必须予 以考虑。表-各种制造方法可能达到的Ra界限值。表中, 从左向右斜升的范围,表示要采用特别措施才能达到所给 出的粗糙度数值;从左向右斜降的范围,表示粗糙度数值 是由于制造特别粗糙所引起的变化。当选用较小的Ra的 允许值时要慎重,否则成本将急剧增加。
Ra、Rc、Rz的数值系列
• 注:1*为优先数值。 • 2Rc和Rz系列中,400以上的数值还有500,630,1000, 1250,1600*。 • 3()中符号,为旧国家标准中,近似对应的等级符号。 高度参数允许数值的选用,总的原则是在满足功能要求的 前提下,尽量选用较大的优先数值(表中带*号者)。具体选 用时,可参考表-机件功能与许用的Rc数值范围,表-各 种制值(单位为 );参数为Ra 时,参数值前不注符号Ra;参数为Rc或Rz时,参数值前 必须注出相应的参数符号。 • b:加工方法,镀涂或其他表面处理。 • c:取样长度(单位为mm,符合规定时可以省略不注)或 波纹度参数和数值(单位为 )。 • d:加工纹理方向符号。 • e:加工余量(单位为mm)。 • f:粗糙度间距参数RSm的参数与数值(单位为mm)或者 支承长度率Rmr(c)与C的参数与数值。图中加一小圆圈, 则表示所有表面具有相同的表面粗糙度要求。
• ②
Ra的上限值为3.2。。
• ③ 表示用去除材料的方法获得的表面粗糙度,Ra 的上限值为3.2,Ra的下限值为1.6。
• ④ 表示用去除材料的方法获得的表面粗糙度,Ra 的最大值为3.2。
• ⑤ 表示不用去除材料的方法获得的表面粗糙度, Ra的上限值为a。