油气管线无损检测技术{zx}
油气管道无损检测技术及设备浅析 高琳丽

油气管道无损检测技术及设备浅析高琳丽摘要:随着油气管道事故的频繁发生,逐渐引起社会各界的关注。
无损检测技术是应用于油气管道探测中的一项重要技术,具有非破坏性和检测全面性的特点,在预防管道设备事故发生和提高设备运行安全性中发挥重要作用。
石油天然气管道的运行安全十分重要,跟着管道运行时间的延伸,管壁也随之不断腐蚀,造成极大安全隐患。
介绍管道无损检测技术办法,对技术优缺点进行解析,优选检测办法应用到管道内检测工作中,发现并消除管道安全隐患。
关键词:管道;无损检测;管道内检测器2013年11月22日,位于山东省青岛市经济技术开发区的中石化股份有限公司管道储运分公司东黄输油管道原油走漏导致爆破事故,事故发生后,经查询发现了事故发生的原因:一方面,管道运营单位疏于对运转管道的安全查看,未能及时察觉出管道运转过程中存在的安全隐患;另一方面,也是最直接的原因,是管道长年运用,管壁腐蚀减薄,在高压力环境下决裂导致走漏爆破事故的发生。
在汲取以上经验的同时,应重视进步管道安全防范认识,采纳办法确保管道运转安全。
1无损检测管道内检测工作,即在运送介质不断输的条件下发送管道检测设备,设备前后树立压差后在介质效果下随介质一起运动,完成对管道的内检测工作。
2000年国家即公布法则,要求主干线油气管道在服役期内,每3-5年有必要对其进行检测工作,以评估、保护管道运转安全。
现在常用的检测办法包含射线检测、超声检测、磁粉检测、渗透检测、漏磁检测等,这些办法具有相同的特色,即对被测目标没有危害效果,该类办法统称为无损检测(NDT,Non-destructiveTesting)。
无损检测办法首要利用资料内部存在的缺点所引起的热、声、光、电、磁等参数的变化,凭借现代化的检测元器件,对检测目标内部或外表的缺点进行衡量,利用检测数据可分析出缺点的类型、数量、形状、方位、尺度巨细。
现在,无损检测被视为工业发展必不可少的东西,其发展情况很大程度上反映了一个国家的工业发展水平,其重要性已得到公认。
应用于油气管道的无损检测技术简介

射 线 无 损 检 测 是 指 利 用 电 磁 波 或 者 电 磁 辐 射 的
测 物 件 的 缺 陷 的情 况 , 从 而对 其进 行安 全 性评 价 , 从 而 保证设 备 能够 安全 、 高效、 可 靠 地运 行 [ 2 ] 。
能量 , 当射 线 透 过 介 质 时 会 与 介 质 发 生 相 互 作 用 , 而 这 相 互 作用 与 物质 的性 质 有 关 , 从 而 在 胶 片 上 的 感
来被普 遍 应 用 于管道 的检 测 上 面 , 及 时发 现 管 道 的 故 障 和 缺 陷 , 从 而保证 管道 系统 的安 全 可靠 , 该 对 该 技 术 进 行 了介 绍 说 明 , 并 对 其 中 的 各 个 方 法 进 行 了说 明 , 并对 油 气管道 线检 测提 出了对应 的 方法 。
优点 ; ①射线 检 测 的检测 范 围大 , 不 像 超 声 波 检 测具 有 最小 厚 度和夹 渣 局部 厚 度差 的缺 陷 ; ③ 可 以 比较 直 观 的 看 到 缺 陷的形 状 , 大小 , 数 量 以及 平 面上 的 位置 ; ④ 适用 各 种 材料 的检测 。
①在 石 油 工业 中使 用 在 钻 井岩 芯 上 ; ② 在 航 天
方 面 用 常 于 一 些 复 合 材 料 的 检 测 ;③ 可 以检 测 比 较 小 的复 杂 的缺 陷 ; ④ 对 于 各 类 电弧 焊 、 气体 保 护 焊、
电渣 焊 、 气 焊 等产生 的接头 可 以进行 检测 。
检 测 的 每一 种方 法 都 有 自己 的优 缺 点 和 适 用 范 围 , 我 们必 须根 据实 际情 况来 选择 使 用 。
1 无 损 检 测 筒 介 无 损 检 测 ( No n~ De s t r u c t i v e Te s t i n g, 简 称 NDT) 是指在 不用 破坏 性试 验 的情 况 下[ 1 ] , 对 被 检 测 件 的各个 物 性参 数 和 状 态 等 进行 测 定 的过 程 , 并且 给 出一定 的评 价 , 其 目的是 定 量 和定 性 的 了解 被检
石油管道无损检测技术的发展研究

石油管道无损检测技术的发展研究摘要:石油管道的安全运营对于石油行业至关重要。
由于长时间的使用和外界环境的影响,石油管道的损耗和腐蚀等问题不可避免。
研究和应用石油管道无损检测技术对于发现和修复管道问题至关重要。
本论文通过对现有石油管道无损检测技术的研究和分析,总结了各种无损检测技术的特点和应用情况,并对其发展趋势进行了探讨。
1. 石油管道无损检测技术的现状石油管道无损检测技术是一种通过对管道进行非破坏性检测来发现管道内部缺陷和损伤的技术。
目前,常用的石油管道无损检测技术包括超声波检测、磁粉探伤、涡流检测、X射线检测等。
这些技术各有特点,可以发现不同类型和大小的管道问题。
2. 超声波检测技术超声波检测技术是在管道表面或管道内部通过超声波传播来检测管道内部的缺陷和损伤。
该技术可以检测到管道内壁的腐蚀、裂纹和疲劳断裂等问题。
超声波检测技术具有高灵敏度、高分辨率和定位准确等特点,广泛应用于石油管道的无损检测中。
3. 磁粉探伤技术磁粉探伤技术是通过涂覆磁粉剂在管道表面,利用磁场和磁粉间的相互作用来检测管道内部的缺陷和裂纹。
该技术适用于发现管道表面的细小缺陷,具有简单、快速、经济等特点。
5. X射线检测技术X射线检测技术是通过将X射线照射到管道上,利用X射线与管道材料相互作用的原理来检测管道内部的缺陷和裂纹。
该技术适用于检测管道内部的大型缺陷,并具有高穿透力和定量分析的能力。
6. 石油管道无损检测技术的发展趋势随着石油管道运营监测的要求越来越高,石油管道无损检测技术也在不断发展和改进。
未来,石油管道无损检测技术将朝着更高的灵敏度、更高的分辨率和更快的检测速度发展。
随着数据处理和图像分析技术的发展,石油管道无损检测技术将更加智能化和自动化。
石油管道无损检测技术对于保障石油管道的安全运营具有重要意义。
本论文总结了常用的石油管道无损检测技术,并对其应用情况和发展趋势进行了探讨。
希望本论文能对石油行业相关工作者和研究人员提供参考和帮助。
油气管道在线检测诊断技术与缺陷无损检测方法探讨
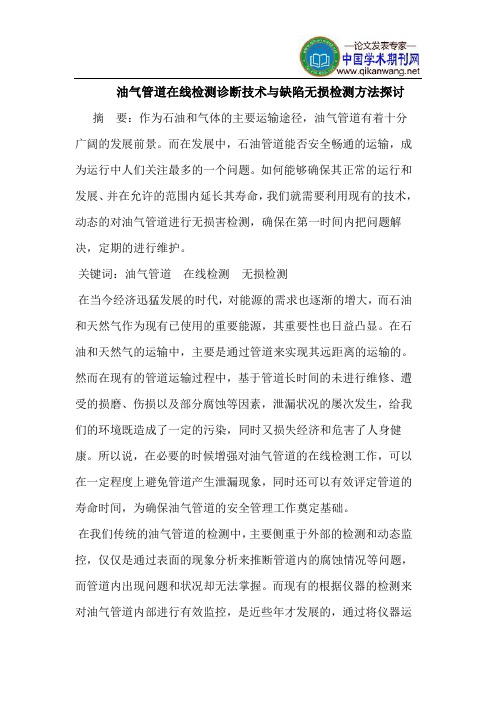
油气管道在线检测诊断技术与缺陷无损检测方法探讨摘要:作为石油和气体的主要运输途径,油气管道有着十分广阔的发展前景。
而在发展中,石油管道能否安全畅通的运输,成为运行中人们关注最多的一个问题。
如何能够确保其正常的运行和发展、并在允许的范围内延长其寿命,我们就需要利用现有的技术,动态的对油气管道进行无损害检测,确保在第一时间内把问题解决,定期的进行维护。
关键词:油气管道在线检测无损检测在当今经济迅猛发展的时代,对能源的需求也逐渐的增大,而石油和天然气作为现有已使用的重要能源,其重要性也日益凸显。
在石油和天然气的运输中,主要是通过管道来实现其远距离的运输的。
然而在现有的管道运输过程中,基于管道长时间的未进行维修、遭受的损磨、伤损以及部分腐蚀等因素,泄漏状况的屡次发生,给我们的环境既造成了一定的污染,同时又损失经济和危害了人身健康。
所以说,在必要的时候增强对油气管道的在线检测工作,可以在一定程度上避免管道产生泄漏现象,同时还可以有效评定管道的寿命时间,为确保油气管道的安全管理工作奠定基础。
在我们传统的油气管道的检测中,主要侧重于外部的检测和动态监控,仅仅是通过表面的现象分析来推断管道内的腐蚀情况等问题,而管道内出现问题和状况却无法掌握。
而现有的根据仪器的检测来对油气管道内部进行有效监控,是近些年才发展的,通过将仪器运送到管道的内部,伴随着压差的运动而随着管道里面的介质而自行运作,进而对管道内的相关信息进行有效的采集数据等信息,最终通过计算机进行系统分析然后得出数据,进而可以分析管道内的受损情况。
我们通过管道内自行检测的手段,可以收获完整的一套数据,可以准确的分析出管道内部的现有状况,进而推估出管道寿命时间,可以有针对性的进行维修,进行动态的管理。
笔者通过多年的实践经验和理论相结合,主要通过介绍油气管道内漏磁技术的充分应用,来进行相关的分析。
一、漏磁技术在油气管道中缺陷检测原理1.漏磁技术在油气管道中工作原理漏磁检测技术在进行油气管道缺陷检测的时候,装置中携带有电源,伴随着石油和天然气在管道中流动而运行,同时能够确保恒定磁场在运行过程中通过励磁设备进行加载,进而通过检测泄漏在管道内的磁通密度,然后进行数据的传送存储于设备内。
油气管道无损检测技术

油气管道无损检测技术管道作为大量输送石油、气体等能源的安全经济的运输手段,在世界各地得到了广泛应用,为了保障油气管道安全运行,延长使用寿命,应对其定期进行检测,以便发现问题,采取措施。
一、管道元件的无损检测(一)管道用钢管的检测埋地管道用管材包括无缝钢管和焊接钢管。
对于无缝钢管采用液浸法或接触法超声波检测主要来发现纵向缺陷。
液浸法使用线聚焦或点聚焦探头,接触法使用与钢管表面吻合良好的斜探头或聚焦斜探头。
所有类型的金属管材都可采用涡流方法来检测它们的表面和近表面缺陷。
对于焊接钢管,焊缝采用射线抽查或100 %检测,对于100 %检测,通常采用X射线实时成像检测技术。
(二)管道用螺栓件对于直径>50 mm的钢螺栓件需采用超声来检测螺栓杆内存在的冶金缺陷。
超声检测采用单晶直探头或双晶直探头的纵波检测方法。
二、管道施工过程中的无损检测(一)各种无损检测方法在焊管生产中的配置国外在生产中常规的主要无损检测配置如下图一中的A、B、C、E、F、G、H工序。
我国目前生产中的检测配置主要岗位如下图中的A、C、D、E、F、G、H工序。
图一大口径埋弧焊街钢管生产无损检测岗位配置(二)超声检测全自动超声检测技术目前在国外已被大量应用于长输管线的环焊缝检测,与传统手动超声检测和射线检测相比,其在检测速度、缺陷定量准确性、减少环境污染和降低作业强度等方面有着明显的优越性。
全自动相控阵超声检测系统采用区域划分方法,将焊缝分成垂直方向上的若干个区,再由电子系统控制相控阵探头对其进行分区扫查,检测结果以双门带状图的形式显示,再辅以TOFD (衍射时差法)和B扫描功能,对焊缝内部存在的缺陷进行分析和判断。
全自动超声波现场检测时情况复杂,尤其是轨道位置安放的精确度、试块的校准效果、现场扫查温度等因素会对检测结果产生强烈的影响,因此对检测结果的评判需要对多方面情况进行综合考虑,收集各种信息,才能减少失误。
(三)射线检测射线检测一般使用X射线周向曝光机或Y射线源,用管道内爬行器将射线源送入管道内部环焊缝的位置,从外部采用胶片一次曝光,但胶片处理和评价需要较长的时间,往往影响管道施工的进度,因此,近年来国内外均开发出专门用于管道环焊缝检测的X射线实时成像检测设备。
石油天然气钢质管道无损检测(最终版)
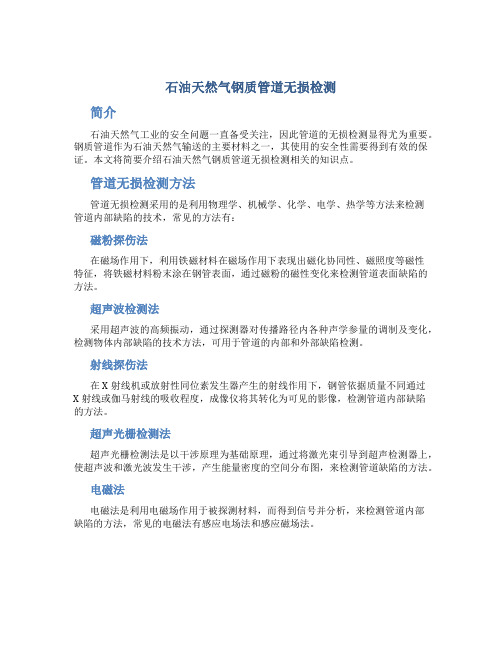
石油天然气钢质管道无损检测简介石油天然气工业的安全问题一直备受关注,因此管道的无损检测显得尤为重要。
钢质管道作为石油天然气输送的主要材料之一,其使用的安全性需要得到有效的保证。
本文将简要介绍石油天然气钢质管道无损检测相关的知识点。
管道无损检测方法管道无损检测采用的是利用物理学、机械学、化学、电学、热学等方法来检测管道内部缺陷的技术,常见的方法有:磁粉探伤法在磁场作用下,利用铁磁材料在磁场作用下表现出磁化协同性、磁照度等磁性特征,将铁磁材料粉末涂在钢管表面,通过磁粉的磁性变化来检测管道表面缺陷的方法。
超声波检测法采用超声波的高频振动,通过探测器对传播路径内各种声学参量的调制及变化,检测物体内部缺陷的技术方法,可用于管道的内部和外部缺陷检测。
射线探伤法在X射线机或放射性同位素发生器产生的射线作用下,钢管依据质量不同通过X 射线或伽马射线的吸收程度,成像仪将其转化为可见的影像,检测管道内部缺陷的方法。
超声光栅检测法超声光栅检测法是以干涉原理为基础原理,通过将激光束引导到超声检测器上,使超声波和激光波发生干涉,产生能量密度的空间分布图,来检测管道缺陷的方法。
电磁法电磁法是利用电磁场作用于被探测材料,而得到信号并分析,来检测管道内部缺陷的方法,常见的电磁法有感应电场法和感应磁场法。
管道无损检测重要性管道无损检测不仅可以发现管道内部的缺陷情况,也能提前预测管道的损耗情况,以及进行针对性的预防措施。
通过检测出管道的问题,可以采取及时有效的修复措施,保证了管道的安全运行,减少了意外事故的发生。
石油天然气工业的发展不仅需要精细的技术,也需要以人为本、保障安全的措施。
在钢质管道的制造、安装及运行过程中,因材料、设备、环境等因素,管道缺陷及其导致的事故风险无法避免。
因此,对于管道的无损检测需要时刻保持高度的重视和严肃的态度,以确保石油天然气工业的安全可靠运行。
油气管道无损检测与在线检测诊断技术

a 或 者 是 r=b。 如 果油气管道所处 的介质 属于均匀 、同性的线弹性 ,那么弹 性动力
学 的运 动 方 程 式 可 以用 下 面 的 方程 式表 示 :
2 1 T T
(k+2tx) ( ·u)+p ̄Vx(V xU)=p【 ]
.
at
(1)
式 中:u— — 位 移 矢 量 ;
中图分类号 :TE973
文献标识码 :B
文章 编号 :1004—7344(2013)18—0349—02
随着 国民经济的快速发展 ,我 国国民生产与生活对于能源 的需求量 急剧增加 ,石 油和天然气 已经成为我 国 目前最重要 的能源 ,并且 已经在 国 民 的 生产 与 生 活 中 发 挥 了 巨大 的作 用 。现 阶 段 ,我 国的 石 油 和 天 然 气 运输都 是使用 管道进行,以实现石油和 天然 气的长距离运输 。但是在石 油 和天然气运输 的过程 中,运输管道都会 因为这样那样 的原 因,发生泄 漏 的现象 ,既造成 了经济的损失 ,也污染 了环境 ,也对管道泄漏区域 的人 们 的人身健康造成 了一定程度 的威胁 ,因此 要对油气 管道进行 在线检 测 ,以有效地控 制油气管道 出现泄漏现象 的几率 ,提 高油气管道 正常运 行 的安 全 性 和 稳 定 性 。
油气管道运输 已经成为我 国石油和天 然气运输过程 中最主要 的运输 手段 。本 文首先对导波检测 技术在油气管道检 测 中的应用进行 了
概 述 ,又声发 射检测技术在 油气管道检 测中的应用进 行了阐述 ,以求能够找 出检测 结果精确性高 、经济性强的检测技 术。
关 键 词 :油 气 管 道 ;无 损 检 测 ;在 线 检 测 ;诊 断 技 术
中国石油天然气管道行业的无损检测技术发展

中国石油天然气管道行业的无损检测技术发展文章主题标签:天然气管道检测管道检测长输管道测量管道本体检测技术非开挖检测技术转载:中国石油天然气管道科学研究院白世武油气长输管道作为一种输送设备被广泛应用于石油、石化和化工等行业。
随着运行时间的增长,部分管道在设计、制造、安装及运行管理中的问题逐渐暴露,致使管道事故时有发生,对人民生命财产安全、社会稳定和工业生产构成威胁。
同时,未来二十年,我国将进入埋地管道建设和发展的高峰期。
如何发现管道缺陷,提高检测水平,在埋地管道的制造、安装和使用等不同阶段采用无损检测技术十分重要。
1管道的无损检测技术及特点埋地管道元件压力管道由各种元件安装而成,包括管子、管道、法兰、阀门、膨胀节、波纹管、密封元件及特种元件,材质分为金属和非金属两大类。
钢管埋地管道用管材包括无缝钢管和焊接钢管。
无缝钢管采用液浸法或接触法超声波检测,主要发现纵向缺陷。
液浸法使用线聚焦或点聚焦滩头,接触法使用与钢管表面吻合良好的斜探头或聚焦斜探头。
所有类型的金属管材都可采用涡流方法来检测它们的表面和近表面缺陷。
焊接管又分螺旋和直缝焊接钢管,焊缝采用100%射线检测,通常采用X射线实时成像检测技术。
锻制管件锻制管件主要包括法兰、三通、变径管、管道承插座、滩头、弯管和封头等,其制造应符合GB/T19326-2003等标准的有关规定。
通常采用超声波方法来检测锻件中的危害性冶金缺陷。
一般采用纵波直探头对加工过程中的实心锻件进行检测,采用横波斜探头对内外径之比<80%的环形或筒形锻件进行周向检测。
钢棒材钢棒材主要用于锻件和螺栓的制造。
对于直径>50mm的钢螺栓件,需要采用超声来检测螺栓杆内存在的冶金缺陷。
超声检测采用单晶或双晶直探头的纵波检测方法。
非金属附件管道附件的非金属镶装件、填料和密封垫应根据管道输送的介质,进行相应的介质耐腐蚀性和耐温等检测。
1.2埋地管道安装过程管道安装过程中的焊接施工是管道建设中最主要的环节之一。
油气管道巡线无损检测技术研究

油气管道巡线无损检测技术研究引言:随着石油和天然气行业的发展,油气管道的建设和运营变得越来越重要。
然而,油气管道的安全隐患也日益凸显,一旦发生泄露、爆炸等事故将会造成巨大的经济损失和人员伤亡。
因此,油气管道的巡线无损检测技术的研究十分重要。
本文将介绍目前主流的油气管道巡线无损检测技术,并探讨其优缺点和应用前景。
一、磁流体无损检测技术磁流体无损检测技术是一种基于磁力线漏磁信号的检测方法。
这种方法可以通过测量油气管道壁上的漏磁信号来判断管道壁的缺陷情况。
磁流体无损检测技术具有灵敏度高、检测速度快、操作简便等优点,可以对管道内部的缺陷进行有效检测。
然而,这种方法对管道表面的杂散磁场有一定的影响,仅适用于管道外表面的检测,对于管道内表面的缺陷检测效果不理想。
二、超声波无损检测技术超声波无损检测技术是一种基于声波的检测方法。
这种方法利用超声波在材料中传播时的声速和声频变化来判断材料的缺陷情况。
超声波无损检测技术具有精度高、探测范围广等优点,可以对管道内外表面的缺陷进行有效检测。
然而,这种方法需要人工操作,无法实现全自动化监测,且在一些高温高压环境中应用受到限制。
三、红外热像无损检测技术红外热像无损检测技术是一种基于红外热传导原理的检测方法。
这种方法利用红外相机拍摄管道表面的热图,通过分析热图中的温度变化来判断管道表面的缺陷情况。
红外热像无损检测技术具有高效、非接触等优点,可以对管道表面的热损伤、腐蚀等缺陷进行有效检测。
然而,这种方法对环境温度的影响较大,灵敏度较低,对一些微小缺陷的检测效果不理想。
四、电磁涡流无损检测技术电磁涡流无损检测技术是一种基于涡流感应原理的检测方法。
这种方法通过测量油气管道表面感应涡流的强度和分布情况来判断管道表面的缺陷情况。
电磁涡流无损检测技术具有高灵敏度、高分辨率等优点,可以对管道表面的微小缺陷进行有效检测。
然而,这种方法对管道材料的电导率较为敏感,无法适用于非导电材料的检测。
油气管道巡线无损检测技术研究

油气管道巡线无损检测技术研究第一章:引言近年来,随着油气资源的日益稀缺和环境保护意识的增强,油气管道的安全性和稳定运行成为全球关注的焦点。
而无损检测技术作为一种非破坏性的管道监测手段,对于管道的状况评估和安全性保障具有重要作用。
本文拟就油气管道巡线无损检测技术进行深入探讨。
第二章:油气管道巡线无损检测技术概述2.1 无损检测技术的定义和应用领域2.2 油气管道巡线无损检测技术的意义和目的2.3 已有的油气管道巡线无损检测技术综述第三章:油气管道巡线无损检测技术分类及原理3.1 X射线检测技术3.2 超声波检测技术3.3 磁粉检测技术3.4 磁谐振检测技术3.5 光学相干层析成像技术第四章:油气管道巡线无损检测技术实验与结果分析4.1 实验方法和条件的确定4.2 实验设备和仪器的选择4.3 实验结果的定量和定性分析4.4 分析结果的讨论和总结第五章:油气管道巡线无损检测技术在实际工程中的应用5.1 管道安全性评估与预防性维护5.2 故障排查与处理5.3 巡线无损检测技术与其他监测手段的结合第六章:未来发展方向6.1 油气管道巡线无损检测技术的发展趋势预测6.2 技术改进与创新6.3 人工智能在巡线无损检测技术中的应用第七章:结论通过对油气管道巡线无损检测技术的综述和实验研究,可以得出以下结论:油气管道巡线无损检测技术具有重要的应用价值,可以辅助管道的安全评估和预防性维护,提高管道运行的安全性和稳定性。
未来,随着技术的不断改进和创新,油气管道巡线无损检测技术将迎来更加广阔的应用前景。
参考文献:[1] Smith A, Johnson B. Non-destructive testing in the oil and gas industry[J]. Materials Evaluation, 2017, 75(8): 1012-1019.[2] Wang Y W, Wu Y Y, Zhang L. Basic research and application of non-destructive testing technology in oil and gas pipelines[J]. Journal of Physics: Conference Series, 2020, 1692: 012062.[3] Zhao S, Luo P, Chen Y. Real time monitoring for oil and gas pipelines using a distributed fibre optic sensor[J]. Measurement Science and Technology, 2005, 16(12): 2400-2405.[4] Shaji E , Shiva Prasad H C . Review of NDT Methods in Oil and Gas Industry[A]. 2017 International Conference on Advances in Computing, Communications and Informatics (ICACCI)[C].2017:2328-2333.[5] Abdibekov M , Anuar A , Caballero-Águila R . Overview of NDT Application in Critical Infrastructure[J]. Materials, 2020,13(7):1686.。
油气管道缺陷无损检测与在线检测诊断技术的探析

油气管道缺陷无损检测与在线检测诊断技术的探析油气管道是石油和天然气运输的重要通道,对于石油和天然气的安全和可靠运输起着至关重要的作用。
由于油气管道长期运行和外部环境的影响,管道内部可能会出现各种缺陷,例如腐蚀、裂纹、变形等问题,这些缺陷可能会导致管道泄漏、爆炸等严重事故。
对油气管道进行无损检测和在线检测诊断是保障管道安全的重要手段。
本文将对油气管道缺陷无损检测与在线检测诊断技术进行探讨,以期能够更好地了解和保护油气管道安全。
一、油气管道缺陷无损检测技术1. 超声波检测技术超声波检测技术是通过超声波穿透管道材料,对管道内部的缺陷进行检测的一种技术。
超声波可以用来检测管道壁的厚度、裂纹、腐蚀等缺陷,是目前最常用的无损检测技术之一。
该技术具有检测精度高、操作便捷等优点,但是在对复杂形状的管道进行检测时,存在一定的局限性。
2. 磁粉探伤技术磁粉探伤技术是利用磁铁或电磁铁在管道表面产生磁场,将铁磁性粉末撒在磁场下,当管道表面出现缺陷时,粉末会在缺陷处聚集,形成磁粉堆积,从而可以通过观察磁粉的分布来判断管道的缺陷情况。
该技术对于检测管道表面的缺陷效果较好,但不能用于对管道内部缺陷的检测。
射线检测技术是利用X射线或γ射线穿透管道材料,对管道内部的缺陷进行检测的一种技术。
该技术对于检测管道内部各种缺陷具有较好的效果,但是对工作环境和操作人员的辐射防护要求较高,且成本较高。
1. 金属磁记忆技术2. 声发射技术声发射技术是通过监测管道内部产生的声波信号,来判断管道是否存在缺陷的一种技术。
当管道发生变形、裂纹等缺陷时,会产生压力波或弹性波的传播,通过对这些信号进行监测和分析,可以实现对管道缺陷的在线诊断。
3. 智能传感器技术智能传感器技术是利用传感器对管道进行实时监测和数据采集,通过对采集到的数据进行分析和处理,可以实现对管道的在线检测和诊断。
该技术具有实时性强、对管道形状和缺陷类型的适应性较好等优点。
三、技术的发展趋势随着科技的不断进步,油气管道缺陷无损检测与在线检测诊断技术也在不断地得到完善和创新。
油气管道缺陷无损检测与在线检测诊断技术的探析

油气管道缺陷无损检测与在线检测诊断技术的探析油气管道是能源行业中至关重要的一环,它们承担着输送石油和天然气的重要任务。
随着管道的使用时间增长,管道内外环境的不断变化,管道存在各种安全隐患和缺陷问题。
油气管道缺陷的无损检测与在线检测诊断技术成为了保障管道安全运行的重要手段。
本文将对油气管道缺陷无损检测与在线检测诊断技术进行探讨。
一、油气管道缺陷无损检测技术1. 磁粉探伤技术磁粉探伤技术是一种常用的管道表面裂纹无损检测方法。
通过在管道表面涂覆铁粉,然后在管道上施加磁场,当磁粉表面出现裂纹时,铁粉就会集中在裂纹上,形成明显的黑色磁粉斑点,从而可以发现管道表面的裂纹缺陷。
这种方法简单方便,对管道的金属裂纹有很高的检出率和定位精度,但对于深埋在地下的管道表面缺陷无法检测。
2. 超声波检测技术超声波检测技术是一种常用的管道内部缺陷无损检测方法。
通过在管道内部发送超声波,然后接收管道内部材料的反射信号,从而可以实现对管道内部缺陷的检测。
这种方法可以检测管道内部的腐蚀、磨损等缺陷,对于管道的内部缺陷有很高的检出率和定位精度,但对于管道的外部缺陷无法检测。
3. 磁记忆检测技术1. 智能化技术的应用随着人工智能、大数据、云计算等技术的不断发展与应用,智能化技术已经开始应用于油气管道的缺陷无损检测与在线检测诊断中。
通过智能化技术,可以实现对管道缺陷的实时监测与预警,大大提高了管道安全运行的可靠性和安全性。
无人机技术已经在油气管道的巡检中得到了广泛应用,在未来,无人机技术有望应用于油气管道的缺陷检测与在线诊断中。
通过无人机技术,可以实现对管道的快速、高效的巡检,及时发现管道的问题,确保管道安全运行。
3. 多模式融合检测技术的发展未来,油气管道缺陷的无损检测与在线检测诊断技术将会向着多模式融合的方向发展。
通过融合超声检测、磁粉检测、磁记忆检测等多种检测技术,可以实现对管道缺陷的全面、多角度的检测,提高了管道缺陷检测的准确性和可靠性。
油气管道无损检测技术

油气管道无损检测技术管道作为大量输送石油、气体等能源的安全经济的运输手段,在世界各地得到了广泛应用,为了保障油气管道安全运行,延长使用寿命,应对其定期进行检测,以便发现问题,采取措施。
一、管道元件的无损检测(一)管道用钢管的检测埋地管道用管材包括无缝钢管和焊接钢管。
对于无缝钢管采用液浸法或接触法超声波检测主要来发现纵向缺陷。
液浸法使用线聚焦或点聚焦探头,接触法使用与钢管表面吻合良好的斜探头或聚焦斜探头。
所有类型的金属管材都可采用涡流方法来检测它们的表面和近表面缺陷。
对于焊接钢管,焊缝采用射线抽查或100 %检测,对于100 %检测,通常采用X射线实时成像检测技术。
(二)管道用螺栓件对于直径> 50 mm 的钢螺栓件需采用超声来检测螺栓杆内存在的冶金缺陷。
超声检测采用单晶直探头或双晶直探头的纵波检测方法。
二、管道施工过程中的无损检测(一)各种无损检测方法在焊管生产中的配置国外在生产中常规的主要无损检测配置如下图一中的A、B、C、E、F、G、H工序。
我国目前生产中的检测配置主要岗位如下图中的A、C、D、E、F、G、H工序。
图一大口径埋弧焊街钢管生产无损检测岗位配置(二)超声检测全自动超声检测技术目前在国外已被大量应用于长输管线的环焊缝检测,与传统手动超声检测和射线检测相比,其在检测速度、缺陷定量准确性、减少环境污染和降低作业强度等方面有着明显的优越性。
全自动相控阵超声检测系统采用区域划分方法,将焊缝分成垂直方向上的若干个区,再由电子系统控制相控阵探头对其进行分区扫查,检测结果以双门带状图的形式显示,再辅以TOFD (衍射时差法)和B扫描功能,对焊缝内部存在的缺陷进行分析和判断。
全自动超声波现场检测时情况复杂,尤其是轨道位置安放的精确度、试块的校准效果、现场扫查温度等因素会对检测结果产生强烈的影响,因此对检测结果的评判需要对多方面情况进行综合考虑,收集各种信息,才能减少失误。
(三)射线检测射线检测一般使用X 射线周向曝光机或γ射线源,用管道内爬行器将射线源送入管道内部环焊缝的位置,从外部采用胶片一次曝光,但胶片处理和评价需要较长的时间,往往影响管道施工的进度,因此,近年来国内外均开发出专门用于管道环焊缝检测的X 射线实时成像检测设备。
油气管道缺陷无损检测与在线检测诊断技术的探析

油气管道缺陷无损检测与在线检测诊断技术的探析随着工业化进程的不断推进,油气管道的运输需求也日益增长,并且质量和安全都成为了极其重要的问题。
在其使用过程中,管道内部可能会出现磨损、腐蚀、疲劳等缺陷问题,这些问题极大的影响了管道的使用寿命和运输安全。
因此,油气管道缺陷无损检测与在线检测诊断技术也日益成为工业界和学术界研究的热点。
油气管道的缺陷无损检测技术包括超声波检测、射线检测、涡流检测等多种类型,每种技术都有其独特的特点和应用领域。
其中,超声波检测技术是最为常用的一种,其原理是通过超声波的传播和反射来分析管道内部的缺陷情况。
超声波检测技术具有灵敏度高、准确度高、可靠性高等特点,而且可以对不同尺寸和类型的缺陷进行检测。
在石油、化工和天然气等领域,通常使用声波探头或彩色超声检测仪进行检测。
射线检测技术是另一种常用的无损检测技术,在对管道内部进行一些精细检测时表现出了巨大的优势。
射线检测技术可以通过X射线、γ射线等射线进行断层显示和检测管道内部缺陷的大小和形状。
射线检测技术的优点是可以检测到一些超声波检测难以检测的细小缺陷,并且可以通过拍照的方式对缺陷面进行直观的显示和诊断。
但是,射线检测技术有放射性污染的问题,需要进行严格的射线保护。
涡流检测技术是一种非接触式无损检测技术,主要用于检测管道表面和近表面的缺陷。
涡流检测技术通过对管道内部电磁感应信号的分析,来检测管道内部的缺陷情况。
涡流检测技术具有无损、快速、准确的特点,并且可以对钢管、不锈钢管等多种材质进行检测。
除了以上几种技术之外,线缆检测技术、磁粉检测技术等无损检测技术也被广泛应用于油气管道的缺陷检测中。
在油气管道的缺陷检测中,基于传统的无损检测技术,在线检测诊断技术可以进一步提高检测和诊断的效率和准确度。
在线检测诊断技术主要利用计算机技术和通信技术,通过实时监控和数据传输,来对管道内部情况进行分析和诊断。
现代在线检测诊断技术可以通过传感器、控制系统、数据通信等多种方式,实现对管道内部情况的实时检测和诊断。
石油天然气钢质管道无损检测 (2)

石油天然气钢质管道无损检测1. 引言石油和天然气是现代社会不可或缺的能源资源,其在工业和民用领域具有广泛的应用。
而钢质管道作为石油和天然气输送的主要通道,其安全可靠性至关重要。
为确保钢质管道运行安全,无损检测技术被广泛应用于管道的质量控制和缺陷检测。
本文将重点介绍石油天然气钢质管道无损检测技术的原理、方法和应用。
2. 无损检测原理无损检测是一种基于物理、化学和工程学原理,通过检测材料的表面或内部缺陷,不破坏被检测物体的技术。
常用的无损检测原理包括超声波检测、磁粉检测、涡流检测和X射线检测等。
2.1 超声波检测超声波检测是利用超声波在材料内部传播时的反射、透射、折射等特性来检测材料内部缺陷的一种方法。
通过发射超声波信号,接收返回的信号并分析,可以确定管道的腐蚀、裂纹、气泡等缺陷情况。
2.2 磁粉检测磁粉检测是通过涂布或撒布磁粉在被检材料上,利用磁粉在材料表面产生的磁场留下的磁粉图案来检测材料表面或近表面的缺陷的一种方法。
当材料表面存在缺陷时,磁粉会在缺陷处聚集形成磁粉图案,通过观察和记录这些磁粉图案可以判断缺陷的位置和性质。
2.3 涡流检测涡流检测是利用电磁诱导原理检测材料中导电性缺陷的一种方法。
通过将交变电源接入线圈产生交变磁场,当磁场感应到管道中的导电性缺陷时,会在缺陷处产生涡流,通过测量涡流的变化来识别和定位缺陷。
2.4 X射线检测X射线检测是利用X射线对材料进行透射、散射或吸收的特性来检测材料内部缺陷的一种方法。
通过发射X射线束,通过检测X射线的强度和能量变化,可以确定材料内部的缺陷情况,如裂纹、焊接缺陷等。
3. 无损检测方法根据石油天然气钢质管道的特点和需求,常用的无损检测方法包括超声波法、磁粉法、涡流法和X射线法。
3.1 超声波法超声波法是一种广泛应用于钢质管道无损检测的方法。
通过使用超声波传感器对管道进行扫描,可以检测到管道内部的腐蚀、裂纹等缺陷。
超声波法具有非接触、高灵敏度、高准确性等特点,适用于管道的各个部位。
石油管无损检测技术探讨

石油管无损检测技术探讨近年来,石油管道的检测技术越来越多,无损检测新技术是一种较为先进的检查技术,在检测的过程中,可以更好地进行分析和判断,检查发现石油管道内部存在的问题,进而为我们的管理人员提供技术方面的参考。
本文主要探讨了所有管道的无损检测技术,研究了技术了具体的使用方法以及原理,提出了相关的建议,供参考和借鉴。
标签:石油管道;无损检测在石油管道的无损检测过程中,检查人员首先要明确检测的具体方法,开展检查工作所要遵守的原则和流程,在检测的过程中,把握好每一个要素,才能够真正提高石油管道无损检测技术的水平。
1、石油管无损检测技术油管属于一种井下通道的钢柱管,在石油开采过程注水、筑起等环节中应用,其能够重复使用,并能够被下入和起出。
在采用过程中,油管会因为各种原因导致弯曲,如抽油管受拉伸、酸化、压裂、高温等外部环境影响,活塞效应、螺旋效应、膨胀效应等作用。
无损检测技术即为不损伤材料和成品的检测,该项技术的检测原理为材料的内部结构对光、热、点的反应,通过反应情况即可判断材料内部是否异常。
应用无损检测技术检测油管的强度,确定其是否存在缺陷,对构建所能允许的负荷和使用寿命进行评价,根据检测结构对油管进行修理。
1.1石油管缺陷检测系统的信号采集及处理方法石油管检测系统的主要组成部分为传感器、数字信号处理设备以及相对应的支撑性装置。
在石油管的实际无损检测技术应用中,在石油管中进行探测传感器的运行,从而对石油管工作中存在的缺陷信息进行有效探析。
信号处理装置主要是将在探测传感器中所检测到的相应信息进行一个放大处理,在处理操作后将其相应的信息传输到转换仪器中,并做出相关的科学处理最终在计算机内进行缺陷的分析处理。
在石油管的无损检测过程中,在石油管及相应传感器的运动过程中,均应保证石油管的整体表面状态能够被扫描头扫描到,如出现未完整扫描的情况,那么则易出现漏检状况。
因此,在对石油管进行无损检测工作时,其主要的依靠力量为扫描头的全面旋转,而扫描范围应在石油管上方呈现一种螺旋线的轨迹方向,关于探测仪器的所处位置以及相应的速度均应进行科学准确的控制。
油气管道缺陷无损检测与在线检测诊断技术的探析

油气管道缺陷无损检测与在线检测诊断技术的探析
油气管道缺陷无损检测与在线检测诊断技术是指通过使用无损检测技术和在线检测仪
器设备,对油气管道中可能存在的缺陷进行检测和诊断的方法。
这项技术的目的是为了保
障油气管道的安全运行,减少事故和损失的发生。
油气管道中可能存在的缺陷主要包括管道内壁的腐蚀、裂纹、疲劳等。
这些缺陷如果
得不到及时发现和修复,可能会导致管道破裂、泄漏等严重后果。
对于油气管道而言,进
行无损检测和在线检测诊断是非常重要的。
无损检测技术是指一种能够对物体进行检测和诊断,而不会对物体造成任何损伤或影
响的技术。
在油气管道的无损检测中,常用的技术包括超声波检测、X射线检测和磁粉检
测等。
这些技术可以通过对管道内部进行扫描和分析,发现管道壁上的腐蚀、裂纹等缺陷,并确定其严重程度和位置。
在线检测诊断技术是指通过在油气管道中安装一些特殊的检测仪器设备,可以实时监
测管道的运行状态和可能存在的问题。
这些仪器设备可以测量管道中的流体压力、温度、
流速等参数,并可以通过传感器实时监测管道壁的腐蚀、裂纹等缺陷。
通过对这些数据进
行分析和处理,可以及时发现管道的问题,并预防事故的发生。
油气管道缺陷无损检测与在线检测诊断技术的应用对于油气行业的发展和安全运行具
有重要意义。
通过这些技术的运用,可以及时发现和处理管道中的问题,保障管道的安全
运行,减少事故的发生,保护环境和人民的生命财产安全。
油气管道缺陷无损检测与在线检测诊断技术的探析
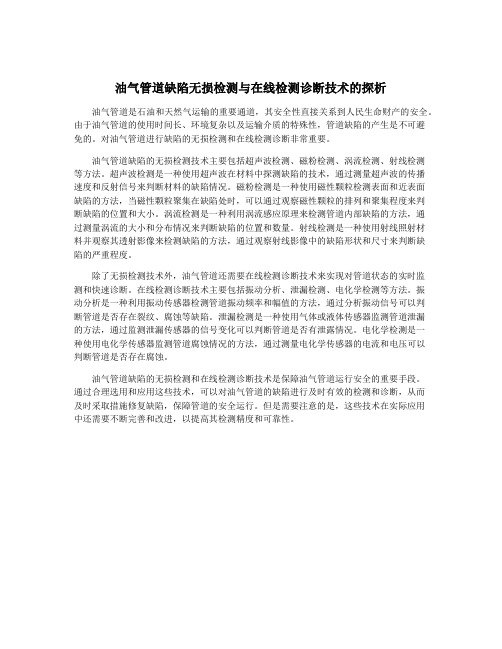
油气管道缺陷无损检测与在线检测诊断技术的探析油气管道是石油和天然气运输的重要通道,其安全性直接关系到人民生命财产的安全。
由于油气管道的使用时间长、环境复杂以及运输介质的特殊性,管道缺陷的产生是不可避免的。
对油气管道进行缺陷的无损检测和在线检测诊断非常重要。
油气管道缺陷的无损检测技术主要包括超声波检测、磁粉检测、涡流检测、射线检测等方法。
超声波检测是一种使用超声波在材料中探测缺陷的技术,通过测量超声波的传播速度和反射信号来判断材料的缺陷情况。
磁粉检测是一种使用磁性颗粒检测表面和近表面缺陷的方法,当磁性颗粒聚集在缺陷处时,可以通过观察磁性颗粒的排列和聚集程度来判断缺陷的位置和大小。
涡流检测是一种利用涡流感应原理来检测管道内部缺陷的方法,通过测量涡流的大小和分布情况来判断缺陷的位置和数量。
射线检测是一种使用射线照射材料并观察其透射影像来检测缺陷的方法,通过观察射线影像中的缺陷形状和尺寸来判断缺陷的严重程度。
除了无损检测技术外,油气管道还需要在线检测诊断技术来实现对管道状态的实时监测和快速诊断。
在线检测诊断技术主要包括振动分析、泄漏检测、电化学检测等方法。
振动分析是一种利用振动传感器检测管道振动频率和幅值的方法,通过分析振动信号可以判断管道是否存在裂纹、腐蚀等缺陷。
泄漏检测是一种使用气体或液体传感器监测管道泄漏的方法,通过监测泄漏传感器的信号变化可以判断管道是否有泄露情况。
电化学检测是一种使用电化学传感器监测管道腐蚀情况的方法,通过测量电化学传感器的电流和电压可以判断管道是否存在腐蚀。
油气管道缺陷的无损检测和在线检测诊断技术是保障油气管道运行安全的重要手段。
通过合理选用和应用这些技术,可以对油气管道的缺陷进行及时有效的检测和诊断,从而及时采取措施修复缺陷,保障管道的安全运行。
但是需要注意的是,这些技术在实际应用中还需要不断完善和改进,以提高其检测精度和可靠性。
应用于油气管道的无损检测技术简介

工业技术94 2015年44期应用于油气管道的无损检测技术简介郑树林孙霄龚则中石化长输油气管道检测有限公司,江苏徐州 221008摘要:无论是在管道制造还是在管道的运行过程中无损检测都担当了相当重要的角色,对管道的运行安全做出了相当大的贡献,对于危险因素可以利用无损检测做到了防患于未然,对于人身安全影响或是经济效益都是非常巨大的。
管道无损检测技术一直是发达国家争先发展的新技术,我们国家也是在不断的发展和进步中,相信在不久的将来我们会将无损检测技术发展的更加完整和成熟。
关键词:油气管道;无损检测;技术中图分类号:TE973.6 文献标识码:A 文章编号:1671-5810(2015)44-0094-021 导言对油气管道进行安全性的无损检测有利于提升油气管道的使用率以及提升使用效能,同时,对于油气管道的无损检测能够及时发现油气管道存在的问题,避免因油气管道破损影响正常的工作。
2 无损检测技术的发展无损检测是随着现代工业和科学技术的发展而不断发展起来的。
1906年,南非研制了第一台钢丝绳电磁无损检测装置,它对于减少当时南非的金矿由于钢丝绳断裂而引起的事故起到一定的作用。
第二次世界大战以后,无损检测技术迅速发展。
到20世纪80年代后期,随着为电子技术和计算机技术的发展,人们开始注重无损检测仪器的微计算机化和智能化,计算机模式识别技术,人工智能技术的发展为这类仪器的产生提供了坚实的理论基础,各类射线在无损检测中得到应用。
中国自20世纪50年代以后开始了无损检测技术的研究,先后开展了各种无损检测检测技术的基本原理和应用技术的研究。
在航空航天、冶金、机械、石油化工等部门,无损检测技术的应用以日益增加并日趋成熟。
3 无损检测技术常用的方法3.1 射线无损检测法射线无损检测是指利用电磁波或者电磁辐射的能量,当射线透过介质时会与介质发生相互作用,而这相互作用与物质的性质有关,从而在胶片上的感光程度也会不同,通过找出的像从而来确定缺陷,就如医院中的X光射线一般。
- 1、下载文档前请自行甄别文档内容的完整性,平台不提供额外的编辑、内容补充、找答案等附加服务。
- 2、"仅部分预览"的文档,不可在线预览部分如存在完整性等问题,可反馈申请退款(可完整预览的文档不适用该条件!)。
- 3、如文档侵犯您的权益,请联系客服反馈,我们会尽快为您处理(人工客服工作时间:9:00-18:30)。
油气管道无损检测技术管道作为大量输送石油、气体等能源的安全经济的运输手段,在世界各地得到了广泛应用,为了保障油气管道安全运行,延长使用寿命,应对其定期进行检测,以便发现问题,采取措施。
一、管道元件的无损检测(一)管道用钢管的检测埋地管道用管材包括无缝钢管和焊接钢管。
对于无缝钢管采用液浸法或接触法超声波检测主要来发现纵向缺陷。
液浸法使用线聚焦或点聚焦探头,接触法使用与钢管表面吻合良好的斜探头或聚焦斜探头。
所有类型的金属管材都可采用涡流方法来检测它们的表面和近表面缺陷。
对于焊接钢管,焊缝采用射线抽查或检测,对于检测,通常采用射线实时成像检测技术。
(二)管道用螺栓件对于直径> 的钢螺栓件需采用超声来检测螺栓杆内存在的冶金缺陷。
超声检测采用单晶直探头或双晶直探头的纵波检测方法。
二、管道项目建设周期中的无损检测(一)各种无损检测方法在焊管生产中的配置国外在生产中常规的主要无损检测配置如下图一中的、、、、、、工序。
我国目前生产中的检测配置主要岗位如下图中的、、、、、、工序。
图一大口径埋弧焊街钢管生产无损检测岗位配置(二)超声检测全自动超声检测技术目前在国外已被大量应用于长输管线的环焊缝检测,与传统手动超声检测和射线检测相比,其在检测速度、缺陷定量准确性、减少环境污染和降低作业强度等方面有着明显的优越性。
全自动相控阵超声检测系统采用区域划分方法,将焊缝分成垂直方向上的若干个区,再由电子系统控制相控阵探头对其进行分区扫查,检测结果以双门带状图的形式显示,再辅以 (衍射时差法)和扫描功能,对焊缝内部存在的缺陷进行分析和判断。
全自动超声波现场检测时情况复杂,尤其是轨道位置安放的精确度、试块的校准效果、现场扫查温度等因素会对检测结果产生强烈的影响,因此对检测结果的评判需要对多方面情况进行综合考虑,收集各种信息,才能减少失误。
(三)射线检测射线检测一般使用射线周向曝光机或γ射线源,用管道内爬行器将射线源送入管道内部环焊缝的位置,从外部采用胶片一次曝光,但胶片处理和评价需要较长的进度,往往影响管道施工的进度,因此,近年来国内外均开发出专门用于管道环焊缝检测的射线实时成像检测设备。
图二管道环焊缝自动扫描射线实时成像系统图二为美国公司生产的管道环焊缝自动扫描射线实时成像系统,该设备采用目前最先进的成像技术,用该设备完成Φ ( ) 管线连接焊缝的整周高精度扫描只需~,扫描宽度可达,该设备图像分辨率可达μ,达到和超过一般的胶片成像系统。
(四)磁粉检测磁粉检测的基础是缺陷处漏磁场与磁粉的磁相互作用。
铁磁性材料或工件被磁化后,由于不连续性的存在,使工件表面或近表面的磁力线发生局部畸变而产生漏磁场,吸附施加在工件表面的磁粉,形成在合适光照下目视可见的磁痕,从而显示出不连续性的位置、形状和大小。
国内很少对焊管坡口面进行磁粉检测。
国外使用的自动检测系统,主要采用荧光磁悬液湿法检测。
自动磁粉检测设备采用磁化线圈在钢管壁厚方向对坡口面局部磁化,同时在坡口表面喷洒荧光磁悬液,凭借在该部位装置的高分辨率摄像系统,将磁化、磁悬液喷洒区域的影像传输在旁边的监视屏上,制作人员监视屏幕,就可以及时发现磁痕影像,找出缺陷。
磁粉检测适用于检测铁磁性材料表面和近表面的缺陷,因此对于奥氏体不锈钢和有色金属等非铁磁性材料不能用磁粉检测的方法进行探伤。
由于马氏体不锈钢、沉淀硬化不锈钢具有磁性,因此可以进行磁粉检测。
磁粉检测可以发现表面和近表面的裂纹、夹杂、气孔、未熔合、未焊透等缺陷,但难以发现表面浅而宽的凹坑、埋藏较深的缺陷及与工件表面夹角极小的分层。
三、钢质管道管体无损检测技术钢质管道管体的无损检测,主要就是管体的完整性(如剩余壁厚、管道缺陷、表面腐蚀形态、腐蚀产物类型、腐蚀深度等)检测。
表一列出了目前常用的管道检测技术及其检测内容。
表一管道检测技术分类(一)弹性波检测技术弹性波检测是利用管道泄漏引起的管道内压力波的变化来进行诊断定位,一般可分为声波、负压力波和压力波三种。
其主要工作原理是利用安置好的传感器来检测管道泄漏时产生的弹性波并进行探测定位。
这种技术的关键是区分正常制作时和发生泄漏时的弹性波。
目前有两种方法,一种是利用硬件电路的延时来进行信号过滤,另一种是结合结构模式识别和神经网络来区分正常制作时和发生事故时产生的不同波形,从而更好地监测管道的运行。
(二)漏磁通检测技术漏磁式管道腐蚀检测设备的工作原理是利用自身携带的磁铁,在管壁圆周上产生一个纵向磁回路场。
如果管壁没有缺陷,则磁力线封闭于管壁之内,均匀分布。
如果管内壁或外壁有缺陷,则磁通路变窄,磁力线发生变形,部分磁力线将穿出管壁产生漏磁。
漏磁检测原理图三所示。
图三漏磁检测原理漏磁场被位于两磁极之间的紧贴管壁的探头检测到,并产生相应的感应信号。
这些信号经滤波、放大、模数转换等处理后被记录到检测器上的存储器中,检测完成后,再通过专用软件对数据进行回放处理、判断识别。
从整个检测过程来说,漏磁检测可分为图四所示的四个部分:图四漏磁检测进程安排图漏磁检测技术的优点:()易于实现自动化。
较高的检测可靠性。
()可以实现缺陷的初步量化。
()在管道检测中,厚度达到的壁厚范围内,可同时检测内外壁缺陷。
()高效,无污染,自动化的检测可以获得很高的检测效率。
漏磁检测技术的局限性:()只适用于铁磁材料。
()检测灵敏度低。
()缺陷的量化粗略。
()受被检测工件的形状限制由于采用传感器检测漏磁通,漏磁场方法不适合检测形状复杂的试件。
()漏磁探伤不适合开裂很窄的裂纹,尤其是闭合型裂纹。
()不能对缺陷的类型或者缺陷的严重程度直接作定量性的分析。
(三)超声波检测技术管道超声检测是利用现有的超声波传感器测量超声波信号往返于缺陷之间的进度差来测定缺陷和管壁之间的距离。
通过测量反射回波信号的幅值和超声波探头的发射位置来确定缺陷的大小和方位。
图五为超声波检测原理图, 图中代表管道正常壁厚, 代表超声波探头与管道内表面间的标准位移。
图五超声波检测原理图超声波检测技术的优点:()检测速度快,检测成本低。
()检测厚度大,灵敏度高。
()缺陷定位较准确。
()对细微的密闭裂纹类缺陷灵敏度高。
超声波检测的缺点:()由于受超声波波长的限制,该检测法对薄管壁的检测精度较低,只适合厚管壁,同时对管内的介质要求较高。
()当缺陷不规则时,将出现多次反射回波,从而对信号的识别和缺陷的定位提出了较高要求。
()由于超声波的传导必须依靠液体介质,且容易被蜡吸收,所以超声波检测器不适合在气管线和含蜡高的油管线上进行检测,具有一定局限性。
(四)电磁超声检测电磁超声技术()是世纪年代发展起来的无损检测新技术。
这一技术是以洛仑兹力、磁致伸缩力、电磁力为基础,用电磁感应涡流原理激发超声波。
电磁超声的发射和接收是基于电磁物理场和机械波振动场之间的相互转化,两个物理场之间通过力场相互联系。
从物理学可知,在交变的磁场中,金属导体内将产生涡流,同时该电流在磁场中会受到洛仑兹力的作用,而金属介质在交变应力的作用下将产生应力波,频率在超声波范围内的应力波即为超声波。
与之相反,该效应具有可逆性,返回声压使质点的振动在磁场作用下也会使涡流线圈两端的电压发生变化,因此可以通过接收装置进行接收并放大显示。
人们把用这种方法激发和接收的超声波称为电磁超声。
与传统压电超声换能器相比,的优点主要有:()非接触检测,不需要耦合剂。
()可产生多种模式的波,适合做表面缺陷检测。
()适合高温检测。
()对被探工件表面质量要求不高。
()在实现同样功能的前提下,探伤设备所用的通道数和探头数都少于压电超声。
()发现自然缺陷的能力强,对不同的入射角有明显的端角反射,对表面裂纹检测灵敏度较高。
的缺点:()的换能效率要比传统压电换能器低—。
()探头与试件距离应尽可能小。
()仅能应用于具有良好导电性能的材料中。
(五)涡流检测技术涡流检测技术是目前采用较为广泛的管道无损检测技术,其原理为:当一个线圈通交变电时,该线圈将产生一个垂直于电流方向(即平行于线圈轴线方向)的交变磁场,把这个线圈靠近导电体时,线圈产生的交变磁场会在导电体中感应出涡电流(简称涡流),其方向垂直于磁场并与线圈电流方向相反。
导电体中的涡流本身也要产生交变磁场,该磁场与线圈的磁场发生作用,使通过线圈的磁通发生变化,这将使线圈的阻抗发生变化,从而使线圈中的电流发生变化。
通过监测线圈中电流的变化(激励电流为恒定值),即可探知涡流的变化,从而获得有关试件材质、缺陷、几何尺寸、形状等变化的信息。
涡流检测技术可分为常规涡流检测、透射式涡流检测和远场涡流检测。
常规涡流检测受到趋肤效应的影响,只适合于检测管道表面或者亚表面缺陷,而透射式涡流检测和远场涡流检测则克服了这一缺陷,其检测信号对管内外壁具有相同的检测灵敏度。
其中远场涡流法具有检测结果便于自动化检测(电信号输出)、检测速度快、适合表面检测、适用范围广、安全方便以及消耗的物品最少等特点,在发达国家得到广泛的重视,广泛用于在用管道的检测。
涡流检测技术的优点:()检测速度高,检测成本低,制作简便。
()探头与被检工件可以不接触,不需要耦合介质。
()检测时可以同时得到电信号直接输出指示的结果,也可以实现屏幕显示。
()能实现高速自动化检测,并可实现永久性记录。
涡流检测技术的缺点:()只适用于导电材料,难以用于形状复杂的试件。
()只能检测材料或工件的表面、近表面缺陷。
()检测结果不直观,还难以判别缺陷的种类、性质以及形状、尺寸等。
()检测时受干扰影响的因素较多,易产生伪显示。
(六)激光检测技术激光检测系统主要包括激光扫描探头、运动控制和定位系统、数据采集和分析系统三个部分,利用了光学三角测量的基本原理。
与传统的涡流法和超声波法相比,激光检测(或轮廓测量)技术具有检测效率高、检测精度高、采样点密集、空间分辨力高、非接触式检测,以及可提供定量检测结果和提供被检管道任意位置横截面显示图、轴向展开图、三维立体显示图等优点。
但是激光检测方法只能检测物体表面,要全面掌握被测对象的情况,必须结合多种无损检测方法,取长补短。
(七)管道机器人检测技术管道机器人是一种可在管道内行走的机械,可以携带一种或多种传感器,在制作人员的远端控制下进行一系列的管道检测维修作业,是一种梦想的管道自动化检测装置。
一个完整的管道检测机器人应当包括移动载体、视觉系统、信号传送系统、动力系统和控制系统。
管道机器人的主要工作方式为: 在视觉、位姿等传感器系统的引导下,对管道环境进行识别,接近检测目标,利用超声波传感器、漏磁通传感器等多种检测传感器进行信息检测和识别,自动完成检测任务。
其核心组成为管道环境识别系统(视觉系统)和移动载体。
目前国外的管道机器人技术已经发展得比较成熟,它不仅能进行管道检测,还具有管道维护与维修等功能,是一个综合的管道检测维修系统。