胶料配方及工艺要求
橡胶加工工艺及配方
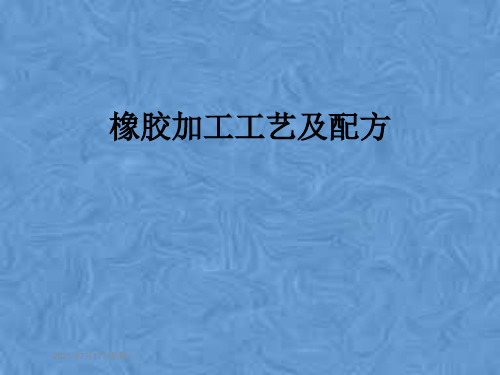
链缠结 链扣
修正后的理想橡胶弹性方程(矛盾平衡)
ρRT
1ห้องสมุดไป่ตู้
2Mc
F=
(λ- )(1- )
Mc
λ2
M
比例于无 用的游离 末端数
热弹力(RT):热弹力与绝对温度成正比,弹力由长链分子的热 运动产生
ρ 网状结构: (1- 2Mc ) 说明弹力与有效分子
Mc
M
链数有关,与交联程度有关
1
变形(λ-
橡胶加工工艺及配方
2021年7月17日星期六
第一章 橡胶配方设计原理 第二章 特种橡胶制品 第三章 配方设计中的数学方法
第一章 橡胶配方设计原理
第一节 第二节 第三节 第四节 第五节
橡胶配方设计基本概念 橡胶配方设计的原则与程序 橡胶配方设计的组成与表示方法 配方设计与硫化胶物机性能关系 配方设计与胶料工艺性能间的关系
撕裂强度(KN/m):试样单位厚度承 受的负荷。
分为起始型撕裂和延续型撕裂。
起始型撕裂:指在一定拉伸速度下, 试样直角部位被撕裂时的强度。
延续型撕裂:预先割好口的试样,被 撕裂时的强度。
有效弹性(E´) :在拉力试验机上,将 试样拉伸到一定长度测定试样收缩时 恢复的功同伸长时所消耗的功之比。
老化性能:包括大气老化,臭氧老化, 热、光老化和湿热老化等。
一般是用老化后前物理机械性能变化 的比值来表征。如:
扯断强度老化系数是老化后与前的扯 断强度之比。扯断伸长率老化系数是 老化后与前的扯断伸长率之比。
第四节 配方设计与硫化胶物 机性能关系
一、定伸强度与硬度
测试给定伸 长的强度
哑铃型试片
品种,用量与含胶率有关。 2)确定硫化体系。根据生胶的类型和品种,硫化工艺及产品
橡胶配方大全
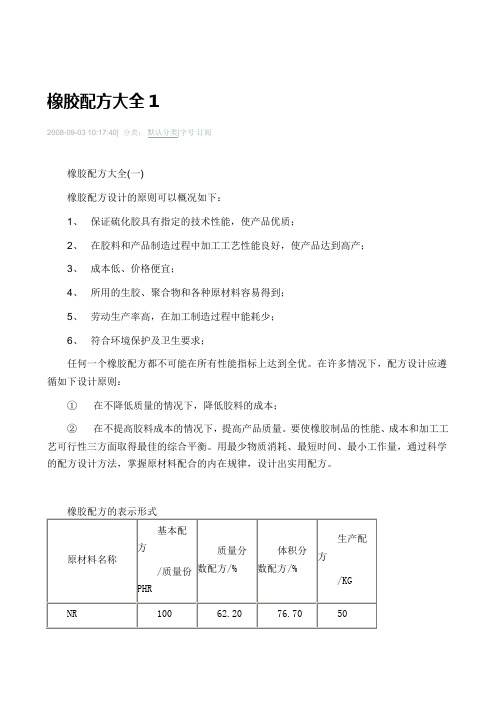
70
25
0.5
0.7
0.5
100
40
2
0.4
0.4
5
5
30
0.6
3.5
100
10
5
60
10
5
1
1
0.5
1
1.5
合计
175.4
183.25
196.5
202.7
186.9
195.0
子午线轮胎胎面胶配方
原材料
载重子午线轮胎胎面胶
轿车子午线轮胎胎面胶
NR
NR/SBR
NR/BR
NR/BR/SBR
NR
NR/BR/SBR
—
—
—
10
0.3
0.1
注:硫化时间为150℃×30min,40min,50min
丙烯酸酯橡胶(ACM)基础配方
原材料名称
质量份
原材料名称
质量份
ACM
快压出炭黑FEF
硬脂酸钾
100
60
0.75
防老剂RD
硬脂酸纳
硫磺
1
1.75
0.25
注:硫化条件为一段166℃×10min;二段硫化180℃×8h。
混炼型聚氨酯橡胶(PUR)基础配方
氯磺化聚乙烯(CSM)基础配方
原材料名称
黑色配方
白色配方
CSM
SRF
一氧化铅
活性氧化锌
促进剂DM
促进剂DPTT
二氧化钛
碳酸钙
季戊四醇
100
40
25
—
0.5
2
—
—
—
100
—
—
丙烯酸酯橡胶(ACM)的配方及工艺

丙烯酸酯橡胶(ACM)的配方及工艺丙烯酸酯橡胶(ACM)具有优异的耐油、耐热、耐臭氧、抗紫外线等性能,从20世纪60年代末开始,随着高速汽车的发展而在美国、日本等工业先进国家获得较为广泛的应用。
近年,随着我国汽车工业、摩托车工业、电力工业的快速发展以及进口车辆、机具的增多,对ACM的需求已越来越大。
据国家机械工业局规划发展司介绍,国产汽车中采用ACM的车种为12种,2000年汽车装车和维修需要ACM5000t。
电力行业现在也已经逐步使用ACM代替NBR制造变压器的密封件,以提高使用寿命。
特别是现在国内的电网改造给ACM提供了较大的市场,使ACM的应用快速增长。
很多行业已逐步采用ACM替代NBR以提高制品的性能,或替代价格昂贵的氟橡胶以降低成本,或与氟橡胶并用以改善加工性能。
为了满足国内市场对ACM的需求,国家有关部门已将ACM 列入了积极发展的品种之列,一些科研院所和大专院校等都加入到这一领域进行研究和技术开发,研究成果报道增多,给ACM 的应用打下了一定的理论基础。
从80年代末开始,国内先后建立了几套ACM工业化生产装置,部分满足了国内市场的需求。
ACM的配合和加工具有特殊性,各厂家生产的ACM具有不同的配合和加工要求,给ACM的推广应用造成一定难度。
我国的橡胶制品企业多为中小型企业,技术力量薄弱,也影响了ACM的推广应用。
为了使ACM在我国尽快得到推广应用,解决好配合加工中的技术问题成为当前一项迫切任务。
为此,我们将所了解的用户在实际应用中遇到的配合技术问题进行了分析探讨,现介绍如下。
1ACM配合中的常见问题及产生原因在ACM胶料的配合中,比较常见的技术问题主要有:①胶料性能不稳定;②拉伸强度太低;③压缩永久变形和扯断永久变形大;④回弹性差,有的胶料硫化后近似于硬质塑料;⑤耐磨性差;⑥耐高温老化性差;⑦浅色胶料难以配合和硫化,彩色制品在硫化时变色。
出现上述问题的原因是多方面的,主要影响因素有以下几点:(1)生胶质量低或不稳定生胶质量低或不稳定是影响胶料性能的最重要原因。
橡胶工业手册第三册配方与基本工艺

上篇配方设计第一章配方设计第一节概述天然橡胶和合成橡胶的纯胶性能都比较差,无法满足制品的使用要求,加入多种配合剂后才能获得改善。
橡胶、配合剂及其配比的方案,即为橡胶配方。
根据制品各种性能要求,制定橡胶配方,通过试验、调整和验证,最后确定胶料的各种组分及其配比的过程,即称谓橡胶配方设计。
橡胶性能配方,主要研究配方组分与硫化胶及混炼胶性能之间的关系,探求组分对橡胶各种性能的影响和贡献。
橡胶制品配方则主要研究硫化橡胶物理机械性能和化学性能与橡胶只怕你实际使用性能之间的关系,探求硫化橡胶性能对制品使用性能的影响和贡献。
这两类配方所研究的对象和内容虽然不同,但又互相联系,不可分割,由此形成橡胶配方设计体系。
一、配方设计的变迁和发展一、配方组成的多样化现代配合组分可分为五个体系:1.主体材料:生胶、再生胶2.硫化体系:硫化机、促进剂、活性剂、防焦剂。
3.操作体系:增塑剂(化学增塑剂、物理增塑剂)。
4.性能体系:补强剂、防老剂、着色剂、发泡剂、芳香剂、增硬剂。
5.成本体系:填充剂、增容剂。
一个具有实际意义的配方通常含有不同体系二、配合剂品种的专用化适合氯丁橡胶的硫脲类促进剂不适合于其他类型的橡胶。
适合天然橡胶的植物系物理增塑剂并不适合合成橡胶。
三、配合效果的提高四、配方设计过程的简化科学的数理方法用于配方设计:等高线法、实验设计法、三角坐标法及电子计算机法等。
用计算机进行配方试验的数据处理、优选配方,可以通过少量试验获得大量有用的信息,使配方设计发生了根本性变化。
二、配方设计的基本要求和配方分类为获取最佳的共和平衡性能,三个目的1.改善橡胶使用性能。
2.改进橡胶的工艺性能。
配以操作助剂。
3.不影响或少影响性能的前提下,配入填充材料,降低成本。
橡胶配方按其作用分为:试验(或检验)配方、性能配方和制品配方。
试验(或检验)配方。
通用橡胶基础配方:三、橡胶配合中出现的反常现象1.实验室得到的配方,在生产中不一定有满意结果。
熬胶的正确方法与配方

熬胶的正确方法与配方
熬胶是一种将动物骨骼、皮肉或鱼鳞制成的胶原蛋白浓缩液体,常用于烹饪和烘焙中增加食物的口感和营养价值。
下面是一种常见的熬胶方法和配方:
材料:
- 1kg 动物骨头、鱼头或鱼鳞
- 3L 水
- 1个洋葱(切块)
- 2根胡萝卜(切块)
- 2根芹菜(切块)
- 2瓣大蒜(切碎)
- 2片姜(拍扁)
- 2片香叶(可选)
- 1茶匙粗盐
步骤:
1. 将动物骨头或鱼头清洗干净,用刀剁碎成小块,鱼鳞用刀背刮取。
2. 在一个大锅中,加入足够的水,将骨头、鱼头或鱼鳞放入锅中。
3. 将锅放在中小火上,慢慢加热,待水开始变热但未煮沸时,搅拌杂质浮于水面。
4. 将锅上火大火煮沸,煮沸后立即转小火。
同时加入洋葱、胡萝卜、芹菜、大蒜、姜和香叶。
5. 缓慢熬煮3-4小时,定期搅拌并去除浮沫。
如果熬的时间太短,胶原蛋白可能无法完全释放。
6. 在煮熟后,用滤网或纱布过滤掉食材渣滓,将胶浆留下。
7. 长时间熬胶可能会使液体减少,如果需要,可以加入适量的水来调整浓度。
8. 筛选后的胶浆留至室温后,放入冰箱冷却凝固。
熬胶配方可以根据个人口味和需求进行调整,也可以根据不同的食材进行变化。
例如,您可以添加一些香料如胡椒粒、丁香或五香粉等。
请根据自己的喜好和需求来调整配方和熬胶时间。
密炼作业指导书

目录胶料的制备一、胶料代号二、各胶料配方及混炼规程三、设备特征四、原材料输送称量及配合五、工艺条件六、混炼操作要点七、胶料管理第二部分胶料的制备一、胶料的代号外胎1.ALT 胎体钢丝帘线复胶及带束层复胶2.ALN 胎里过渡层胶3.ATG 胎圈钢丝复胶4.BASF 胎冠胶(XY100)5.BRAM 胎冠胶(XY300)6.ESD 胎侧胶7.GQC 胎圈缠绕包布胶8.LIB 无内胎内衬层胶9.LIA 有内胎内衬层胶10.TEVB 耐磨胶条胶<子口护胶>11.THC 胎肩垫胶12.TMD 钢圈上填充胶PA 胎圈下填充胶14.TOGO 无内胎轮胎三角胶芯胶15.OTA 工程胎胎冠胶16.OTE 工程胎型胶17.OTS 工程胎胎侧胶18.OTF 工程胎子口胶19.OTM 工程胎气密层胶20.SGF 胶浆胶21.COP 成型胶囊(反包胶囊)胶22.104-B 加强层设备特征1.生产母胶的设备:1.1密炼机上辅机及微机控制系统1.1.1设备组成:主要由碳黑、油料和生胶或母胶输送、称量和投料系统,以及动力、控制系统所组成。
1.1.2设备参数炭黑气力输送能力, Tph 6-15 炭黑气力输送距离, m 约100炭黑气力输送管道直径 DN150/175炭黑气力输送速度, mps 5-10炭黑最大破碎率, % 10炭黑秤称量范围,㎏1-100炭黑种类 6油料秤称量范围,㎏1-50油料种类 2胶料秤皮带尺寸,㎜L4000×W800 胶料秤皮带速度, mps 0.5秤配料周期, S ≤90秤的静态精度, % ≤±0.1满量程系统动态精度, % ≤±0.2动力蒸汽压力, Mpa 0.3-0.4动力蒸汽耗量, tph 0.5压缩空气压力, Mpa 0.6-0.8压缩空气耗量, m3pm 16电源 380VAC220V50Hz40KW3ph4线微机控制室要求温度, ℃ 20-251.2 F-270×20×30×40×60密炼机(液压)1.2.1设备组成:主要由转子、混炼室及密封装置、加料及加压机构、排料装置、传动装置、液压系统、温控系统、润滑系统、电控系统等组成。
胶条生产工艺
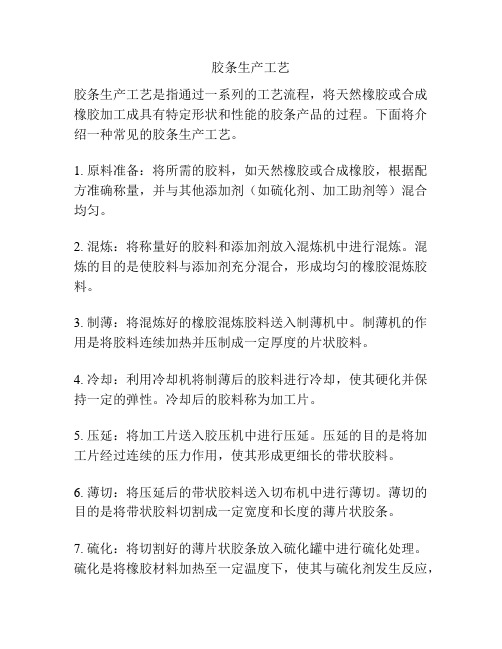
胶条生产工艺胶条生产工艺是指通过一系列的工艺流程,将天然橡胶或合成橡胶加工成具有特定形状和性能的胶条产品的过程。
下面将介绍一种常见的胶条生产工艺。
1. 原料准备:将所需的胶料,如天然橡胶或合成橡胶,根据配方准确称量,并与其他添加剂(如硫化剂、加工助剂等)混合均匀。
2. 混炼:将称量好的胶料和添加剂放入混炼机中进行混炼。
混炼的目的是使胶料与添加剂充分混合,形成均匀的橡胶混炼胶料。
3. 制薄:将混炼好的橡胶混炼胶料送入制薄机中。
制薄机的作用是将胶料连续加热并压制成一定厚度的片状胶料。
4. 冷却:利用冷却机将制薄后的胶料进行冷却,使其硬化并保持一定的弹性。
冷却后的胶料称为加工片。
5. 压延:将加工片送入胶压机中进行压延。
压延的目的是将加工片经过连续的压力作用,使其形成更细长的带状胶料。
6. 薄切:将压延后的带状胶料送入切布机中进行薄切。
薄切的目的是将带状胶料切割成一定宽度和长度的薄片状胶条。
7. 硫化:将切割好的薄片状胶条放入硫化罐中进行硫化处理。
硫化是将橡胶材料加热至一定温度下,使其与硫化剂发生反应,形成交联结构,从而使胶条具有一定的强度和弹性。
8. 洗净:将硫化后的胶条经过洗净机清洗,去除表面的油污和其他杂质。
9. 干燥:将洗净的胶条放入干燥机中进行烘干处理,使其表面水分蒸发,达到一定干燥程度。
10. 包装:将干燥的胶条进行包装,包装成一定长度和重量的胶条产品。
以上是一种常见的胶条生产工艺,不同的胶条产品可能会有所不同的生产工艺过程。
此外,胶条生产工艺还会受到工艺参数、生产设备和产品要求等因素的影响。
橡胶制品是如何生产制作的?配方、工艺、设备基础介绍

橡胶制品是如何生产制作的?配方、工艺、设备基础介绍一、概论1.橡胶分子链几何形状大致分为三类:线型橡胶分子,支链型橡胶分子,网状橡胶分子。
2.胶料的组成可概括为五个体系,即生胶,硫化体系,增塑及软化体系,补强与填充体系,仿护体系。
3.橡胶制品生产的基本工艺过程包括塑炼、混炼、压延、压出、成型、硫化六个基本工序。
★橡胶的流动性是整个加工过程中最重要的工艺特性。
★分子量较高且分布窄的橡胶,物理机械性能较好,但加工性较差。
★生胶分子量越低,生胶的可塑度越大.★生胶分子量分布越宽,在开炼机上混炼时包辊性越好。
二、橡胶配方设计(一)、生胶1.SBR是丁苯橡胶,BR是顺丁橡胶,EPDM是三元乙丙橡胶,CR是氯丁橡胶。
★合成丁苯橡胶的单体是丁二烯和苯乙烯,合成乙丙橡胶的单体是乙烯和丙烯丁腈橡胶和氟橡胶----------耐油性最好丁基橡胶----------------------气密性最好氟橡胶----------最佳耐热耐化学药品性三元乙丙橡胶---------------耐候性最好丁腈橡胶的耐油性、耐热性及机械强度随丙烯腈含量的增加而提高,而弹性和耐寒性却有所下降。
三元乙丙橡胶大分子主链不含双键,双键在侧链上。
主链为稳定的碳碳饱和键,受到老化因素的影响时,主链不易短链,因此三元乙丙橡胶具有优良的耐老化性能。
二元乙丙橡胶主链和侧链都不含双键,用过氧化物硫化后,形成稳定的碳碳饱和键,因此二元乙丙橡胶的耐老化性能比三元乙丙橡胶还好。
(二)、配合剂补强与填充剂1.炭黑的混炼性主要取决于炭黑的结构,粒径和表面化学性质。
★炭黑粒径减小,硫化胶硬度升高。
★炭黑结构越高,炭黑在胶料中的分散越容易。
增塑剂2.增塑剂应与橡胶具有良好的相溶性。
3.促进剂M可作天然胶的化学增塑剂(塑解剂)。
硫化与促进剂、活性剂4.在橡胶硫化中,凡能加快橡胶与硫化剂的交联作用,使硫化时间缩短的物质,都叫硫化促进剂。
5.按促进剂的活性可将其分为以下四类超促进剂,中超促进剂,中等促进剂,弱促进剂。
再生胶配方

再生胶配方再生胶配方是制造再生胶产品的关键。
再生胶是指由废旧橡胶制成的一种材料,可以再次使用和生产各种橡胶制品。
再生胶被广泛应用于橡胶工业,例如橡胶底板、汽车胎和橡胶管等。
本文将介绍一种常见的再生胶配方,包括原料及其比例、加工过程和产品特性等。
1. 原料及其比例再生胶的原料主要包括废橡胶和添加剂。
废橡胶通常来自废旧轮胎、橡胶制品或橡胶加工废料等。
添加剂是为了提高再生胶的物理性能和加工性能而加入的,常见的添加剂包括硫化剂、防老剂和增塑剂等。
以下是一种常见的再生胶配方示例:- 废橡胶:60%- 硫化剂:3%- 防老剂:1%- 增塑剂:2%- 其他添加剂:4%- 橡胶粉:30%上述比例仅供参考,实际配方可能因产品用途、性能要求和生产工艺的不同而有所变化。
2. 加工过程再生胶的生产过程分为四个主要阶段:破碎、造粒、混合和硫化。
首先,废橡胶经过破碎处理,将废旧橡胶制品或废料破碎成小颗粒状。
然后,将破碎后的橡胶颗粒进行造粒,即通过高温和高压将颗粒进行加热和挤压,使其形成固体颗粒。
接下来,将造粒后的再生橡胶与添加剂进行混合。
混合的过程需要借助橡胶混炼机,将再生橡胶和添加剂均匀混合,确保添加剂充分分散在再生橡胶中。
最后,混合后的胶料经过硫化处理,即在一定的温度和时间条件下进行硫化反应。
硫化剂起到交联橡胶分子的作用,使其形成弹性体。
3. 产品特性再生胶的性能取决于原料的质量和配方的比例。
再生胶的主要特性和性能包括以下几个方面:- 耐磨性:再生胶具有较高的耐磨性,适用于制造汽车胎和工业橡胶制品等高磨损性的产品。
- 弹性:再生胶具有良好的弹性,可以有效地吸收震动和减少噪音。
- 耐候性:再生胶具有较好的耐候性,能够抵抗日晒、雨淋等外部环境的影响。
- 加工性能:再生胶易于加工成型,可以通过挤出、压延、模压等工艺制造不同形状和规格的产品。
然而,与原料橡胶相比,再生胶在某些性能方面可能存在一定的差异。
例如,再生胶的耐热性、抗拉强度和耐油性等性能通常较原料橡胶略差。
安全鞋用胶料配方

的化 学性 质可提 供更 宽广 的加工 范围 ; 3 当用 超 细胶 粉 替代 原 料 聚合 物 时 , 对硫 ) 应
化体 系作适 当的调整 。
参考文献: 1 C r D Mc e 等 , R b e rd V 12 7 No 6 2 0 ) 3 al . Afe 《 u br Wo l ) o. 3 , . ( O 8 , 1
1 、0份 及 3 的配 合量 替代原 料聚合 物 , O份 2 O份 保 持相似 的动 态 性 能 。建 议 对 硫 化体 系 加 以调 整 ,
从 而保 持相应 胶料 的硫 化速率 和硫化 程度 。 另 外 , 径较 小 的超 细 胶 粉可 产 生 更 强 的聚 粒
动态性 能 , 全可 以 由最 终用 户定 制 。 完
3 8
橡 胶 参 考 资 料
2 1 年 00
察 这些 数据后 似乎 可 以看 出 , 未调 整硫化体 系时 , 大 部分情 况下 tn 在相 同范 围 内 。另 外 , 果 a艿值 如
对硫 化体 系优 化后 , 预计 这些值 都会 相 同。而且 ,
最 终配方 以及 由此 获得 的物 理性 能 、 工 性 能 和 加
硫 化条件 :5 1 5℃ ×5mi。 n 硫 化胶 物性 : 度 ( I — A) 6 ; 伸 强 度 硬 JS 5拉
( a 2 6 伸 长 率 ( ) 4 0 撕 裂 强 度 ( N/ MP ) 2 ; 0; k
m) 型 5 B 6。
耐 溶剂 优 良的氟 橡 胶 ( IE - 0 ) DA - L G 9 2
4 结 语
关 于本文 所研 究 的两大应 用领 域可得 出如 下
结论:
首先 , 细胶粉 配合 量 在 4 ~6 范 围的 超 O 0 各种橡 胶/ 料 共 混 物 , 聚 合 物 粘 度 与 常 规 的 塑 其 T O 材料 接 近 。这 就表 明超 细 橡 胶 粒 子 可 以成 P 功地用 于 聚丙烯 的抗 冲击改 性 。设 计实 验结果 显 示 , 小的粒子可以产生更为理想的物理性能。 较 建 议 对更 小 的粒 径 ( 近 目前 3 5目即 4 / 的 接 2 4m  ̄ 极 限 ) 进一 步 的研究 。 作
橡胶配方设计基础-2+3+4+5+6+7+8
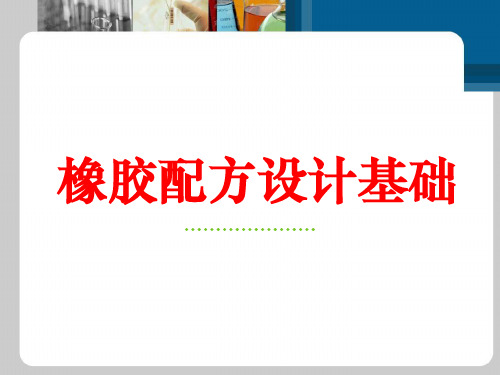
Vi% = Vi /∑Vi ×100%
2. 配方的表示形式
4. 生产配方(Mi ):
取胶料的总质量等于炼胶机的装胶量
Q,各组分以实际用量表示。
M i = Q× m i / ∑ m i
配方换算
①质量分数配方计算:mi=mi/∑mi ②体积分数配方计算:
Vi=mi/ρi[∑(mi/ρi)]
③生产配方计算:Mi=Qi×(m/∑mi)
胶的粘度,改善加工工艺性能。
硫化:
“硫化”因最初的天然橡胶制品用 硫磺作交联剂进行交联而得名,随 着橡胶工业的发展,现在可以用多
种非硫磺交联剂进行交联。
硫化:
因此硫化的更科学的意义应是“交
联”或“架桥”,即线性高分子通
过交联作用而形成的网状高分子的
工艺过程。
硫化过程:分为四个阶段:
硫化过程:
橡胶配方设计基础
1、概 述
橡胶配方设计:根据橡胶产品的
性能要求和工艺条件,合理地选用
原材料,并确定各种原材料的用量 配比关系,使得胶料的物性、工艺
性和成本三者取得最佳平衡。
橡胶配方:生胶和多种配合剂按照
一定比例的一种组合。
五大体系:
生胶体系 ( 高聚物单用或并用 ) :母
体材料或基体材料
橡胶配方的表示形式
原材料名称, (g/cm3) NR 0.92 硫磺 2.05 促进剂M 1.42 ZnO 5.57 St 0.92 C.B. 1.80 合计 基本配 体积分 质量分数 生产配 方,质量 数配方 配方/% 方,kg 份 /% 100 62.20 76.70 50.0 3 1.86 1.03 1.5 1 0.60 0.50 0.5 5 3.10 0.63 2.5 2 1.24 1.54 1.0 50 31.00 19.60 25.0 161 100 100 80.5
常见生胶与混炼胶的加工工艺
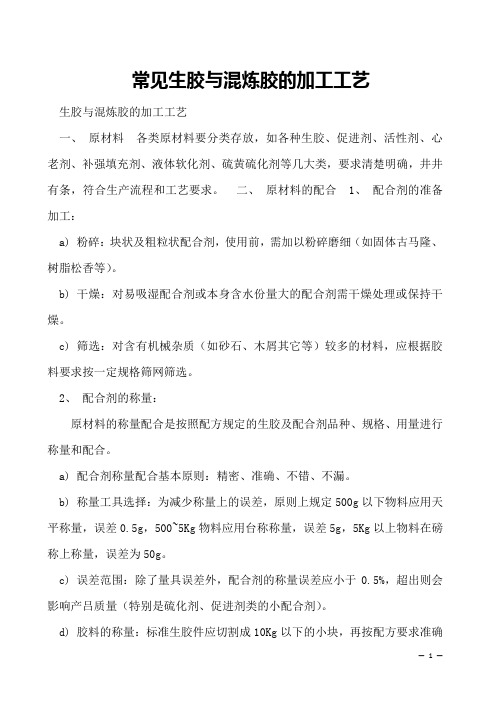
常见生胶与混炼胶的加工工艺生胶与混炼胶的加工工艺一、原材料各类原材料要分类存放,如各种生胶、促进剂、活性剂、心老剂、补强填充剂、液体软化剂、硫黄硫化剂等几大类,要求清楚明确,井井有条,符合生产流程和工艺要求。
二、原材料的配合 1、配合剂的准备加工:a) 粉碎:块状及粗粒状配合剂,使用前,需加以粉碎磨细(如固体古马隆、树脂松香等)。
b) 干燥:对易吸湿配合剂或本身含水份量大的配合剂需干燥处理或保持干燥。
c) 筛选:对含有机械杂质(如砂石、木屑其它等)较多的材料,应根据胶料要求按一定规格筛网筛选。
2、配合剂的称量:原材料的称量配合是按照配方规定的生胶及配合剂品种、规格、用量进行称量和配合。
a) 配合剂称量配合基本原则:精密、准确、不错、不漏。
b) 称量工具选择:为减少称量上的误差,原则上规定500g以下物料应用天平称量,误差0.5g,500~5Kg物料应用台称称量,误差5g,5Kg以上物料在磅称上称量,误差为50g。
c) 误差范围:除了量具误差外,配合剂的称量误差应小于0.5%,超出则会影响产吕质量(特别是硫化剂、促进剂类的小配合剂)。
d) 胶料的称量:标准生胶件应切割成10Kg以下的小块,再按配方要求准确称量后,备于投料使用,误凑巧不超过0.5%。
e) 操作:生胶配合剂的称量配合,应严格按照每日生产计划及配方要求进行,保正精度,避免药品的漏用和错用,称好的配合剂合理装载,做好标识,按一定的规则顺序放置备用,混炼时按一定的工艺要求顺序投料。
f) 质量控制:对具体胶料及所用的配合剂应有明确的文字标识,并设质量跟踪卡,以便质量检查及生产管理。
三、混炼工艺 1、生胶的塑炼:a) 投料:开炼机塑炼及混炼时,所有生胶、母胶、并用胶,须在靠炼胶机大齿轮一则加入。
b) 根据各种不同的生胶性能,应采用不同的塑炼方法,具体如下: 1) 天然胶:一段塑炼:以0.5~1mm辊距将生胶破开,薄通落盘,如此重复过机到规定时间或次数。
经典橡胶配方大全
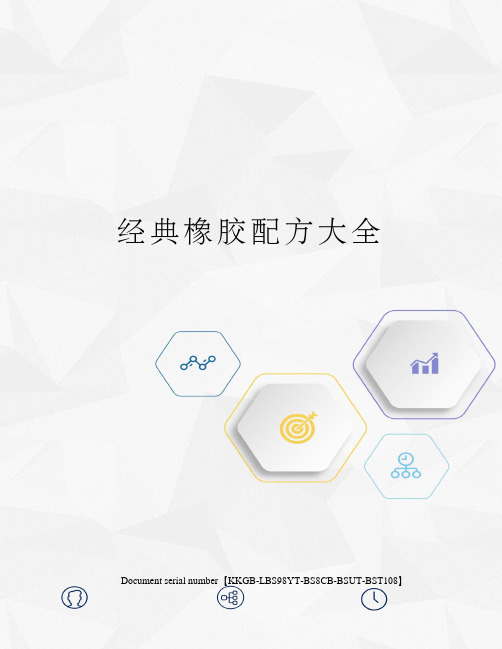
经典橡胶配方大全 Document serial number【KKGB-LBS98YT-BS8CB-BSUT-BST108】橡胶配方设计的原则橡胶配方设计的原则可以概况如下:1、保证硫化胶具有指定的技术性能,使产品优质;2、在胶料和产品制造过程中加工工艺性能良好,使产品达到高产;3、成本低、价格便宜;4、所用的生胶、聚合物和各种原材料容易得到;5、劳动生产率高,在加工制造过程中能耗少;6、符合环境保护及卫生要求;任何一个橡胶配方都不可能在所有性能指标上达到全优。
在许多情况下,配方设计应遵循如下设计原则:① 在不降低质量的情况下,降低胶料的成本;② 在不提高胶料成本的情况下,提高产品质量。
要使橡胶制品的性能、成本和加工工艺可行性三方面取得最佳的综合平衡。
用最少物质消耗、最短时间、最小工作量,通过科学的配方设计方法,掌握原材料配合的内在规律,设计出实用配方。
橡胶配方的表示形式天然橡胶(NR)基础配方注:硫化时间为140℃×10min,20min,40min,80min。
NBS为美国国家标准局编写丁苯橡胶(SBR)基础配方Phr指每百质量份橡胶的分量数注:硫化时间为145℃×25min,35min,50min氯丁橡胶(CR)基础配方注:硫化时间为150℃×15min,30min,60min丁基橡胶(IIR)基础配方注:硫化时间为150℃×20min,40min,80min;150℃×25min,50min,100min 丁腈橡胶(NBR)基础配方注:硫化时间为150℃×10min,20min,80min顺丁橡胶(BR)基础配方注:硫化时间为145℃×25min,35min ,50min 异戊橡胶(IR )基础配方注:硫化时间为15℃×20min,30min ,40min ,60min 。
纯胶配方采用天然橡胶基础配方。
三元乙丙橡胶(EPDM )基础配方注:硫化条件在第三单体为DCDP 时为160℃×30min,40min ,第三单体为ENB 时为160℃×10min,20min氯磺化聚乙烯(CSM )基础配方注:硫化时间为153℃×30min,40min ,50min氯化丁基橡胶(CIIR )基础配方注:硫化时间为153℃×30min,40min,50min聚硫橡胶(PSR)基础配方注:硫化时间为150℃×30min,40min,50min丙烯酸酯橡胶(ACM)基础配方注:硫化条件为一段166℃×10min; 二段硫化180℃×8h。
经典橡胶配方大全
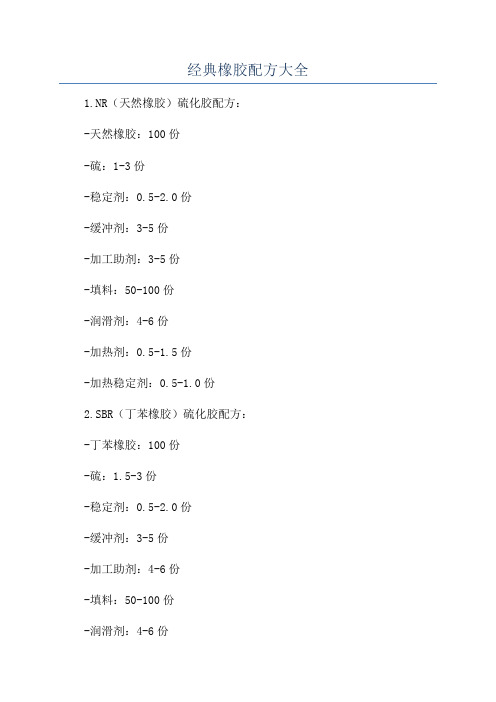
经典橡胶配方大全1.NR(天然橡胶)硫化胶配方:-天然橡胶:100份-硫:1-3份-稳定剂:0.5-2.0份-缓冲剂:3-5份-加工助剂:3-5份-填料:50-100份-润滑剂:4-6份-加热剂:0.5-1.5份-加热稳定剂:0.5-1.0份2.SBR(丁苯橡胶)硫化胶配方:-丁苯橡胶:100份-硫:1.5-3份-稳定剂:0.5-2.0份-缓冲剂:3-5份-加工助剂:4-6份-填料:50-100份-润滑剂:4-6份-加热剂:0.5-1.5份-加热稳定剂:0.5-1.0份3.NBR(丁腈橡胶)硫化胶配方:-丁腈橡胶:100份-硫:2-4份-稳定剂:0.5-2.0份-缓冲剂:3-5份-加工助剂:4-6份-填料:50-100份-润滑剂:4-6份-加热剂:0.5-1.5份-加热稳定剂:0.5-1.0份4.EPDM(乙丙橡胶)硫化胶配方:-乙丙橡胶:100份-硫:2-3份-稳定剂:0.5-2.0份-缓冲剂:3-5份-加工助剂:3-5份-填料:50-100份-润滑剂:4-6份-加热剂:0.5-1.5份-加热稳定剂:0.5-1.0份5.CR(氯丁橡胶)硫化胶配方:-氯丁橡胶:100份-硫:2-3份-稳定剂:0.5-2.0份-缓冲剂:3-5份-加工助剂:3-5份-填料:50-100份-润滑剂:4-6份-加热剂:0.5-1.5份-加热稳定剂:0.5-1.0份以上是几种常见橡胶材料的硫化胶配方,不同的橡胶材料所需的添加剂比例和类型可能有所不同,具体的配方还需要根据实际需求和应用环境进行调整。
配方中的添加剂包括稳定剂、缓冲剂、加工助剂、填料、润滑剂、加热剂和加热稳定剂等,这些添加剂的作用包括提高橡胶的耐热性、耐候性、机械性能等。
在配方制备时,需要根据橡胶材料的性质和要制备的橡胶制品的具体要求来选择和调整添加剂的种类和用量。
O形橡胶密封圈胶料配方设计

O形橡胶密封圈胶料配方设计O型橡胶密封圈是一种常用的密封材料,广泛应用于机械设备、汽车、航空航天等领域。
其主要功能是防止液体或气体的泄漏,并具有良好的耐磨、耐油、耐气候等性能。
O型橡胶密封圈的胶料配方设计需要考虑多个因素,包括胶料的物理力学性能、耐热性、耐化学性等。
下面将介绍一种常用的O型橡胶密封圈胶料配方设计。
1.胶料选用一般选择丁苯橡胶(BR)作为O型橡胶密封圈的主要胶料,丁苯橡胶具有良好的耐磨、耐油、耐气候性能,能够满足密封圈的使用要求。
2.加入剂为了改善橡胶的特性,可以添加一些加入剂,如填充剂、增塑剂、抗氧剂等。
(1) 填充剂:可以选择炭黑作为填充剂,炭黑能够增强橡胶材料的耐磨性和抗拉伸性能。
一般添加量为30-50 phr。
(2)增塑剂:可以选择加入邻苯二甲酸酯类增塑剂,如二异丁基酯(DBP)。
增塑剂能够提高橡胶材料的柔软度和延展性。
(3)抗氧剂:可以选择加入苯链氨类抗氧剂,如二羟基联苯醚(AO-80)。
抗氧剂能够有效延缓橡胶老化过程,提高密封圈的使用寿命。
3.硫化系统硫化系统是橡胶材料固化的关键,一般选择硫磺和过氧化硫为硫化剂。
硫磺的添加量一般为3-5 phr,过氧化硫的添加量一般为1-3 phr。
4.加工助剂为了提高橡胶材料的加工性能,可以加入一些加工助剂,如活性剂、分散剂等。
(1)活性剂:可以选择二硫化苯(MBTS)作为活性剂。
活性剂能够提高硫化速度和硫化效果。
(2)分散剂:可以选择双苯基二氮唑(DBD)作为分散剂。
分散剂能够提高填充剂和硫磺与橡胶的分散性,提高胶料的强度和耐热性。
通过以上配方设计,可以得到一种具有良好性能的O型橡胶密封圈胶料配方。
但需要指出的是,具体的配方设计需要根据具体的应用场景和要求来确定,因此在实际生产过程中,还需要进行相关实验和测试来进一步优化配方。
epdm密炼工艺配方

EPDM(三元乙丙橡胶)的密炼工艺配方通常涉及多个方面,包括生胶的选择、硫化体系、填充增强剂、软化增塑剂以及其他配合剂等。
以下是一些关键点:
1. 生胶选择:生胶是EPDM配方的基础,其选择至关重要。
主要考虑因素包括第三单体类型(如ENB或DCPD)、丙烯含量、门尼粘度和充油量。
这些特性决定了EPDM的硫化速度、压缩变形等性能。
2. 硫化体系:EPDM可以使用硫黄硫化或过氧化物硫化体系。
硫黄硫化工艺加工性能较好,物理性能好,成本低。
过氧化物硫化则可以提供更好的耐热性和耐候性。
3. 填充增强剂:常用的填充剂包括炭黑和白色填料,如钛白粉、滑石粉、碳酸钙等。
这些填充剂可以改善胶料的机械性能和加工性能。
4. 软化增塑剂:增塑剂可以改善EPDM的加工性能和柔韧性,但需适量使用以避免影响胶料的物理机械性能。
5. 其他配合剂:例如硬脂酸可以提高胶料的加工性能和表面光洁度;氧化钙作为吸湿剂,有助于保持胶料的稳定性。
6. 粘合力提升:为了提高EPDM与其他材料的粘合力,可以添加增粘剂或使用特殊的粘合体系。
7. 混炼工艺控制:在密炼机中进行混炼时,需要注意控制加入硫磺、促进剂的初始温度,排料温度以及混炼时间,以防止焦烧现象的发生。
8. 压延和压出:在压延和压出过程中,需要控制适当的速度和温度,以确保产品的表面质量和尺寸稳定性。
综上所述,EPDM的密炼工艺配方是一个复杂的过程,需要根据最终产品的性能要求和加工工艺的特点来综合考虑各种因素。
在实际操作中,可能还需要根据生产设备的实际情况和原材料的特性进行相应的调整。
轮胎胶料配方设计

轮胎胶料配方设计
设计轮胎胶料配方需要考虑以下几个方面:
1. 耐磨性:轮胎胶料需要具备较高的耐磨性,以满足长时间高速行驶的要求。
可添加磨损抗剥离剂和碳黑等填充材料来提高耐磨性。
2. 抗老化性:轮胎胶料需要具备良好的抗氧化和抗紫外线老化性能,以延长使用寿命。
可添加抗氧剂和紫外线吸收剂等添加剂来提高抗老化性。
3. 激活剂:轮胎胶料需要通过添加活化剂来促进交联反应,提高胶料的强度和耐久性。
4. 弹性和耐撕裂性:轮胎胶料需要具备较好的弹性和耐撕裂性,以确保在各种路况下的安全性能。
可添加交联剂、增韧剂和增强剂等来提高弹性和耐撕裂性。
5. 粘附性:轮胎胶料需要能够与胎面和胎体良好的粘接,以确保稳定和安全的使用。
可添加粘合剂和胶黏剂等来提高粘附性。
以上只是一些常见的考虑因素,具体的轮胎胶料配方设计还需要根据具体的应用和要求来确定,可以通过实验和测试来优化和调整配方。
10个密封胶配方,10个密封胶制作方法

一、水性密封胶配方1.原材料及用量:水泥100kg无机胶粉30kg小苏打4kg石灰2.5kg水60kg。
2.制作过程:(1)将水、小苏打和石灰混合,内加少量消泡剂,调成浆糊;(2)将100kg水泥倒入搅拌机中搅拌,再加入步骤(1)中的浆糊和无机胶粉,搅拌至均匀;(3)将搅拌好的密封胶放入容器中,搅拌10-15分钟至黏性均匀,即可供装修使用。
二、硅酸铝铸铁密封胶1. 原材料及用量:硅酸铝200克无机胶粉50克铸铁粉15克改性乳化油30毫升二氧化硅6克水性木器漆4毫升。
(1)将硅酸铝和改性乳化油,放入搅拌机,搅拌至溶解;(2)将50克无机胶粉和15克铸铁粉,一起添加到第一步的溶解液中,继续搅拌至均匀;(3)将4毫升水性木器漆和6克二氧化硅放入搅拌机内搅拌,最后将均匀的密封胶装入容器中,完成密封胶制作。
三、聚氨酯密封胶聚氨酯树脂200克醇酐20克改性剂20克催化剂3克正碳酸钠5克抗氧剂2克抗黄变剂2克。
(1)将聚氨酯树脂、醇酐和改性剂加入搅拌机,搅拌至均匀;(2)将催化剂、正碳酸钠、抗氧剂和抗黄变剂,全部加入到第一步搅拌的液体中,继续搅拌至均匀;(3)将均匀的密封胶放入容器中,搅拌10-15分钟至黏性均匀,即可供装修使用。
四、石棉纤维增强水泥基复合密封胶水泥200克石棉纤维40克无机胶粉30克表面活性剂1克正碳酸钠3克抗氧剂0.3克抗黄变剂0.2克水100克。
(1)将水泥和正碳酸钠混合搅拌均匀,加入表面活性剂搅拌均匀,放入搅拌机搅拌;(2)将石棉纤维和无机胶粉放入搅拌机中加入搅拌,同时加入水,搅拌至均匀;(3)将抗氧剂和抗黄变剂加入搅拌机中,继续搅拌,最后将搅拌好的密封胶装入容器中,即可供使用。
五、石墨烯增强水泥基复合密封胶水泥200克,石墨烯20克,无机胶粉20克,小苏打2克,石灰1克,水120克。
(2)将200克水泥倒入搅拌机中搅拌,再加入步骤(1)中的浆糊和20克无机胶粉,同时加入20克石墨烯,搅拌至均匀;(3)将搅拌好的密封胶放入容器中,搅拌10-15分钟,待胶凝定;(4)将2克小苏打和1克石灰加入120克水中,搅拌成糊状;(5)将步骤(4)中的混合液浆加入步骤(3)中的密封胶搅拌均匀,最后得到石墨烯增强水泥基复合密封胶。
- 1、下载文档前请自行甄别文档内容的完整性,平台不提供额外的编辑、内容补充、找答案等附加服务。
- 2、"仅部分预览"的文档,不可在线预览部分如存在完整性等问题,可反馈申请退款(可完整预览的文档不适用该条件!)。
- 3、如文档侵犯您的权益,请联系客服反馈,我们会尽快为您处理(人工客服工作时间:9:00-18:30)。
6
3
15
3
2
辊温
前辊60-65℃
共计
后辊50-55℃
29分钟
备注:1、下片前打三角包3次
3、下片后及时冷却
外胶配方及工艺要求
胶号
外-01
加药顺序
加药时间(分)
配
方
成
分
及
数
量
1、氯丁胶5kg
2、丁腈胶5kg
3、氧化锌500g
4、硬脂酸200g
5、防老剂4010200g
6半补强炭黑6kg
3、下片后清水冷却
衡水永利胶管有限公司
胶料配方及工艺要求
2006年8月5日
内胶配方及工艺要求
胶号
内-01
加药顺序
加药时间(分)
配
方
成
分
及
数
量
1、丁腈2610kg
2、硬脂酸100g
3、氧化锌500g
4、330黑4kg
5、660黑6kg
6、轻钙3kg
7、二丁酯1.5kg
8、聚脂增塑剂1kg
9、促进剂CE200g
10、促进剂TMTD150g
胶号
中-01
加药顺序
加药时间(分)
配
方
成
分
及
数
量
1、丁腈2610kg
2、氧化锌1kg
3、硬脂酸200g
4、氧化钙80g
5、古马龙1kg
6、二丁酯1kg
7、白炭黑1.5kg
8、660黑3.5kg
9、促进剂CE250g
10、硫磺200g
1、生胶压合
2、氧化锌、硬脂酸
3、古马龙、白炭黑、660黑、二丁酯
4、促进剂CE、硫磺
11、硫磺50g
1、胶料压合
2、硬脂酸氧化锌
3、轻钙、330、660、二丁酯交叉加入
4、增塑剂
5、CE、TMTD、硫磺
6、下片5-6mm
6
3
15
2
3
2
辊温
前辊60-65℃
共计
后辊50-55℃
31分钟
备注:1、促进剂CE、TMTD、硫磺混炼胶过滤后加入
2、下片前打三角包3次
3、下片后及时冷却
中胶配方及工艺要MTD50g
10、硫磺100g
11、二丁酯1.5kg
1、两种胶料压合
2、4010、炭黑、轻钙、二丁酯交叉加入
3、氧化锌、硬脂酸
4、促进剂CE、TMTD、硫磺
5、下片5-6mm
6
14
3
4
2
辊温
前辊60-65℃
共计
后辊50-55℃
29分钟
备注:1、下片前打三角包3次