某车型副车架防转支架失效原因分析
某款车型橡胶衬套与副车架连接失效原因分析

车号 行驶里程
螺栓连接剖视图
衬套内管端面与副车架板啮合
失效案例
故障车 1
故障车 2
故障车 3
1780
9300
12000
故障现象 起步、刹车、转弯 起步、刹车、转弯时 起步、刹车、转弯
时有咔哒声
有较明显的咔哒声 时有咔哒声
二、失效原因分析
整车 Z 向视图(侧向力、制动力、牵引力、及不平路面的上下冲击力) 故障车辆拆解后,发现螺栓的力矩存在明显的衰减,副车架板与衬
— 281 —
套内管端面接触的区域有明显磨损。经过对新下线车辆的初步检测,发 现新车在试车场路试 2 小时后,对力矩进行检测,亦有一定程度的减小 (15N.m 以上)。因此可以初步判断力矩衰减是故障产生的原因。
发生衰减是具备外部原因的。以下是衬套在汽车的基本运动时存 在的力及力矩,实际上,由于汽车本身是一个高度耦合的运动及传力力 系统,衬套真实的受力更加复杂。
三、外观质量控制中其他几点相关事项 1、表面施工滞留物的清除及孔眼的封堵、修补 对施工过程中可能滞留于混凝土中而无法拔出的拉杆、撑件等必 须予以割除,后与孔眼一起进行封堵、修补;同时,为减小色差,建议在 进行连接层处理后,用原施工配合比及各类组料拌制混凝土修补。 2、混凝土成型构件的维护 构件成型后,必须进行维护。拆模过程中,应将模板沿接缝逐一取 出,避免硬敲引起成型构件碰损、掉角;拆模后的结构物,不得作为物品 的集放处及其他构件的架模支撑点,不得让油渍、砂浆等杂物飞溅、挂
溢其上。混凝土拆模后必须及时浇水养护,每天早、中、晚一次,养护时 间两至三周。同样,应做好工程运行管理阶段的维护工作。
3、钢筋保护层的控制 保护层过大,钢筋达不到设计受力状态,温度筋远离层面,表面易 开裂;过小,则耐久性下降,常常在工程投入运行后的一定时间内,引起 内部钢筋失钝锈蚀而膨胀,导致表层混凝土沿钢筋方向的爆裂、松脱。 保护层控制不当,有时还会形成露筋,严重影响构件受力及外观。因此 钢筋保护层厚度应控制在 5CM 左右。 四、结束语 随着经济的不断发展,许多经济较发达的城镇,特别是珠三角和长 三角地区,对水利工程的功能要求不断加大和完善,因此对外观质量也 更加注重。水利工程外观质量只有在设计单位、建设单位、监理单位、施 工单位及政府职能监督单位等相关人员的共同努力下,设计独具匠心、 管理监督到位、精心施工,才能打造出具有一方特色的外观质量一流的 优良工程,使其成为形象性建筑、标志性建筑、景点性建筑,为当地创造 更多的经济效益。
某车型后副车架安装点开裂问题分析及解决
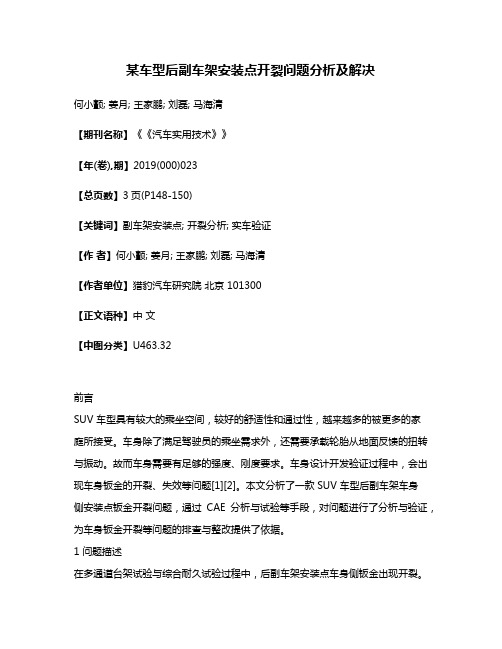
某车型后副车架安装点开裂问题分析及解决何小颤; 姜月; 王家鹏; 刘磊; 马海清【期刊名称】《《汽车实用技术》》【年(卷),期】2019(000)023【总页数】3页(P148-150)【关键词】副车架安装点; 开裂分析; 实车验证【作者】何小颤; 姜月; 王家鹏; 刘磊; 马海清【作者单位】猎豹汽车研究院北京 101300【正文语种】中文【中图分类】U463.32前言SUV 车型具有较大的乘坐空间,较好的舒适性和通过性,越来越多的被更多的家庭所接受。
车身除了满足驾驶员的乘坐需求外,还需要承载轮胎从地面反馈的扭转与振动。
故而车身需要有足够的强度、刚度要求。
车身设计开发验证过程中,会出现车身钣金的开裂、失效等问题[1][2]。
本文分析了一款SUV 车型后副车架车身侧安装点钣金开裂问题,通过CAE 分析与试验等手段,对问题进行了分析与验证,为车身钣金开裂等问题的排查与整改提供了依据。
1 问题描述在多通道台架试验与综合耐久试验过程中,后副车架安装点车身侧钣金出现开裂。
开裂详细情况如表1和图1所示:图1 副车架车身侧安装点实车开裂图表1 后副车架安装点钣金开裂情况记录表?2 原因分析根据疲劳破坏的过程可知,零件在交变载荷作用下,在结构有缺陷部位或者应力集中部位,结构形成塑性变形结晶,继而在晶粒界面之间滑移形成微裂纹,然后发展成宏观裂纹,裂纹扩展到一定程度导致截面再度削弱到截面应力达到强度极限,导致疲劳破坏[3]。
试验中开裂部位的断面图,如图2所示。
从疲劳破坏与结构组成分析,零件的材质性能、冲压方式、使用条件、焊接方式、安装方式、试验条件等诸多方面均与开裂问题相关。
试图找到问题的根本原因,并制定相关措施,现从以上几方面着手进行原因分析。
图2 后副车架安装点断面图2.1 安装点载荷的影响分析由道路试验采集的道路载荷谱,按照综合耐久规范对台架试验路面组合与用时进行分析,台架上下跳动条件下,车身侧存在最大应力。
某车型后副车架主减速器安装支架开裂问题及解决方案
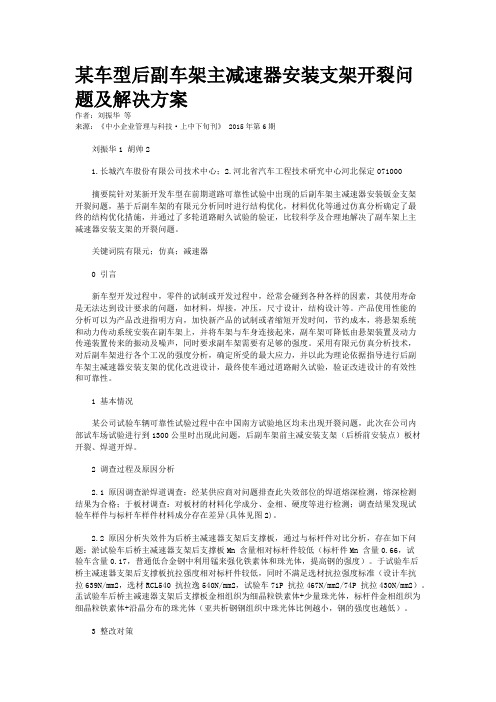
某车型后副车架主减速器安装支架开裂问题及解决方案作者:刘振华等来源:《中小企业管理与科技·上中下旬刊》 2015年第6期刘振华1 胡帅21.长城汽车股份有限公司技术中心;2.河北省汽车工程技术研究中心河北保定071000摘要院针对某新开发车型在前期道路可靠性试验中出现的后副车架主减速器安装钣金支架开裂问题,基于后副车架的有限元分析同时进行结构优化,材料优化等通过仿真分析确定了最终的结构优化措施,并通过了多轮道路耐久试验的验证,比较科学及合理地解决了副车架上主减速器安装支架的开裂问题。
关键词院有限元;仿真;减速器0 引言新车型开发过程中,零件的试制或开发过程中,经常会碰到各种各样的因素,其使用寿命是无法达到设计要求的问题,如材料,焊接,冲压,尺寸设计,结构设计等。
产品使用性能的分析可以为产品改进指明方向,加快新产品的试制或者缩短开发时间,节约成本,将悬架系统和动力传动系统安装在副车架上,并将车架与车身连接起来,副车架可降低由悬架装置及动力传递装置传来的振动及噪声,同时要求副车架需要有足够的强度。
采用有限元仿真分析技术,对后副车架进行各个工况的强度分析,确定所受的最大应力,并以此为理论依据指导进行后副车架主减速器安装支架的优化改进设计,最终使车通过道路耐久试验,验证改进设计的有效性和可靠性。
1 基本情况某公司试验车辆可靠性试验过程中在中国南方试验地区均未出现开裂问题,此次在公司内部试车场试验进行到1300公里时出现此问题,后副车架前主减安装支架(后桥前安装点)板材开裂、焊道开焊。
2 调查过程及原因分析2.1 原因调查淤焊道调查:经某供应商对问题排查此失效部位的焊道熔深检测,熔深检测结果为合格;于板材调查:对板材的材料化学成分、金相、硬度等进行检测;调查结果发现试验车样件与标杆车样件材料成分存在差异(具体见图2)。
2.2 原因分析失效件为后桥主减速器支架后支撑板,通过与标杆件对比分析,存在如下问题:淤试验车后桥主减速器支架后支撑板Mn 含量相对标杆件较低(标杆件Mn 含量0.66,试验车含量0.17,普通低合金钢中利用锰来强化铁素体和珠光体,提高钢的强度)。
发动机支架失效分析及改进
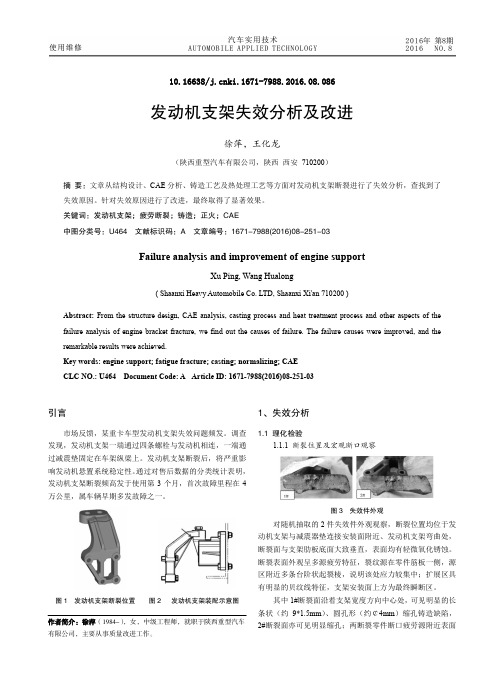
10.16638/ki.1671-7988.2016.08.086发动机支架失效分析及改进徐萍,王化龙(陕西重型汽车有限公司,陕西西安710200)摘要:文章从结构设计、CAE分析、铸造工艺及热处理工艺等方面对发动机支架断裂进行了失效分析,查找到了失效原因。
针对失效原因进行了改进,最终取得了显著效果。
关键词:发动机支架;疲劳断裂;铸造;正火;CAE中图分类号:U464 文献标识码:A 文章编号:1671-7988(2016)08-251-03Failure analysis and improvement of engine supportXu Ping, Wang Hualong( Shaanxi Heavy Automobile Co. LTD, Shaanxi Xi'an 710200 )Abstract: From the structure design, CAE analysis, casting process and heat treatment process and other aspects of the failure analysis of engine bracket fracture, we find out the causes of failure. The failure causes were improved, and the remarkable results were achieved.Key words: engine support; fatigue fracture; casting; normalizing; CAECLC NO.: U464 Document Code: A Article ID: 1671-7988(2016)08-251-03引言市场反馈,某重卡车型发动机支架失效问题频发。
调查发现,发动机支架一端通过四条螺栓与发动机相连,一端通过减震垫固定在车架纵梁上。
某汽车副车架NVH性能分析
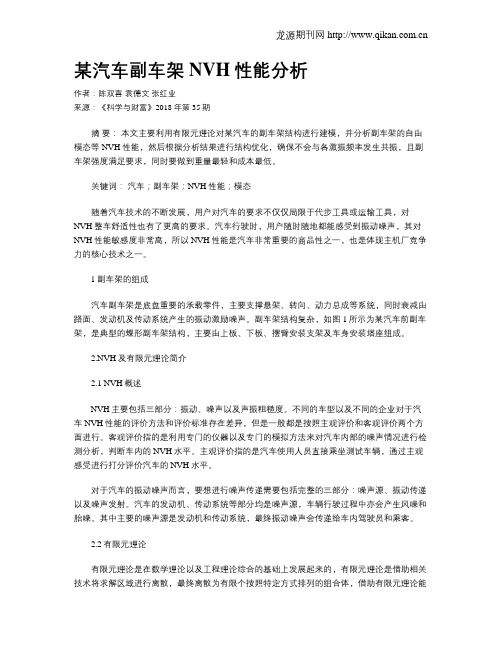
某汽车副车架NVH性能分析作者:陈双喜袁德文张红业来源:《科学与财富》2018年第35期摘要:本文主要利用有限元理论对某汽车的副车架结构进行建模,并分析副车架的自由模态等NVH性能,然后根据分析结果进行结构优化,确保不会与各激振频率发生共振,且副车架强度满足要求,同时要做到重量最轻和成本最低。
关键词:汽车;副车架;NVH性能;模态随着汽车技术的不断发展,用户对汽车的要求不仅仅局限于代步工具或运输工具,对NVH整车舒适性也有了更高的要求。
汽车行驶时,用户随时随地都能感受到振动噪声,其对NVH性能敏感度非常高,所以NVH性能是汽车非常重要的商品性之一,也是体现主机厂竞争力的核心技术之一。
1副车架的组成汽车副车架是底盘重要的承载零件,主要支撑悬架、转向、动力总成等系统,同时衰减由路面、发动机及传动系统产生的振动激励噪声。
副车架结构复杂,如图1所示为某汽车前副车架,是典型的蝶形副车架结构,主要由上板、下板、摆臂安装支架及车身安装塔座组成。
2.NVH及有限元理论简介2.1 NVH概述NVH主要包括三部分:振动、噪声以及声振粗糙度。
不同的车型以及不同的企业对于汽车NVH性能的评价方法和评价标准存在差异,但是一般都是按照主观评价和客观评价两个方面进行。
客观评价指的是利用专门的仪器以及专门的模拟方法来对汽车内部的噪声情况进行检测分析,判断车内的NVH水平。
主观评价指的是汽车使用人员直接乘坐测试车辆,通过主观感受进行打分评价汽车的NVH水平。
对于汽车的振动噪声而言,要想进行噪声传递需要包括完整的三部分:噪声源、振动传递以及噪声发射。
汽车的发动机、传动系统等部分均是噪声源,车辆行驶过程中亦会产生风噪和胎噪。
其中主要的噪声源是发动机和传动系统,最终振动噪声会传递给车内驾驶员和乘客。
2.2有限元理论有限元理论是在数学理论以及工程理论综合的基础上发展起来的,有限元理论是借助相关技术将求解区域进行离散,最终离散为有限个按照特定方式排列的组合体,借助有限元理论能够构造几何性质复杂的模型。
汽车副车架力矩衰减问题解析张旭 贾磊

汽车副车架力矩衰减问题解析张旭贾磊摘要:副车架与车身之间采用螺栓连接,在经各种复合路况后,由于受横向冲击及轴向力作用,连接标准件多少会出现不同层度的松动、扭矩衰减,严重时产生异响,影响客户使用。
本文通过对标准件扭矩衰减的机理研究,提供有效的解决措施,为后续车型设计提供参考。
关键词:副车架;扭矩衰减;异响前言:副车架多采用螺栓与车身进行连接,其主要是利用内外螺纹旋合所构成的螺旋副的自锁特性形成连接关系,为确保螺纹连接的刚性、防松功能以及受拉螺栓的疲劳强度,往往会赋予连接螺栓一定的预紧力。
但是随着使用时间的推移,经各种复合路况后连接螺栓均会有一定层度的扭矩衰减,严重时直接产生异响,引发客户抱怨,影响行车安全。
本文主要针对某车型在研发过程中出现的标准件扭矩衰减问题,通过对标准件扭矩衰减的机理研究,提供有效的解决措施,最终将标准件扭矩衰减控制在合理范围内,提升整车系统可靠性。
1、力矩不足的危害性事实上联接件与被联接件在随螺栓角度变化的同时,螺栓本身也经历着三个阶段的变形。
螺栓正常情况下紧固到设定力矩时应处于弹性变形状态,当力矩继续增大时,螺栓本身受力后开始转变为塑性变形、拉伸变形直至螺栓断裂失效。
因此在汽车总装螺栓紧固中,若螺栓紧固角度偏小即螺栓本身弹性变形不足,则会使联接件与被联接件之间形成的夹紧力达不到设计要求,从而使车辆售出后顾客乘坐时螺栓经过一段时间颠簸后突然脱落而引发事故。
若螺栓紧固角度过大,直接后果就是螺栓当场断裂,需要返修。
更重要的是螺栓处于塑性变形或拉伸变形阶段,这种隐性的变形会使联接件与被联接件夹紧力减小,且螺栓在此两个阶段内部已经形成较大的抗拉力,虽然从表面上并不能发现外观发生什么变化,但事实上车辆经过一段时间运行后仍然可能会导致螺栓突然断裂引发事故。
2、原因分析依据紧固件相关资料研究、结合故障车实车情况,大致可以将副车架安装标准件扭矩衰减归结于以下几方面:1)螺纹啮合长度不足;2)副车架安装面精度差(表面凹凸、安装面处钣金间有间隙);3)配合螺纹管摩擦系数超标;4)装配工艺选择不当。
某车型减振器支架断裂原因分析及改进方案

某车型减振器支架断裂原因分析及改进方案作者:龙先军来源:《时代汽车》2021年第07期摘要:悬架系统的减振器支架作为连接车架及减振器的零件,在车辆运行过程中,因受到减振器的拉力及压力,经常导致断裂失效,致使减振器无法正常工作。
文章以某车型减振器支架的故障断裂为例,采用HyperMesh有限元分析方法對支架进行应力分析,计算结果表明:支架最大应力384MPa,应力最大位置与故障件断裂位置吻合,因此,判断支架因强度不足导致的断裂。
针对支架的断裂原因,提出了3种加强改进方案,从应力、重量、成本、整改周期等因素考虑,选择最优的改进方案。
整改后的减振器支架3年内售后故障率为0,达到预期效果,整改方案有效。
关键词:悬架减振器支架断裂有限元分析1 引言售后调研反馈,某车型减振器上支架出现3起断裂故障,需进行立项整改。
经对故障样件进行检查,所有支架断裂位置均在两个过渡面的折弯处。
为了查明减振器支架断裂的原因,需要对减振器支架进行外观查验,材质检测等[1],排除支架本身部品质量、制造工艺等问题之后再进行应力情况校核。
2 原因分析为了确定支架的应力情况,查明断裂原因,采用HyperMesh有限元分析方法对支架进行模拟分析。
有限元分析可以在模拟零件实际工况下,对零部件进行受力分析,确定零件的应力分布情况,从而对支架进行优化设计和改进,应力较大的部位进行重点加强,应力较小的部位进行减材优化,以达到零件性能与重量成本的最优状态。
在HyperMesh软件中导入减振器支架的3D数模,先进行几何清理及网格划分;其次,对支架进行材料设置及属性赋予[2]:弹性模量E=2.11*105,松泊比0.3,密度7.9*103Kg/m3;最后,按减振器压缩工况下的10倍阻尼力值对减振器支架进行负荷加载;完成上述步骤后,即可提交求解器计算。
计算结果显示,支架的最大应力值384MPa,最大应力位置在支架两个面的结合处右侧,与故障件断裂位置一致。
153-某车后横拉杆支架失效分析
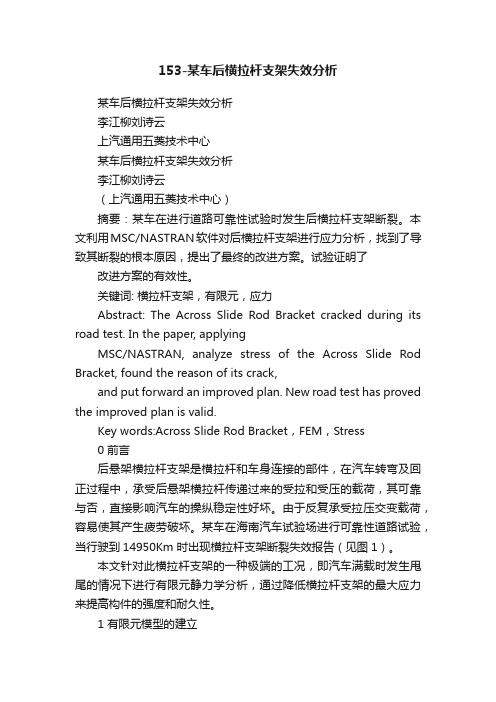
153-某车后横拉杆支架失效分析某车后横拉杆支架失效分析李江柳刘诗云上汽通用五菱技术中心某车后横拉杆支架失效分析李江柳刘诗云(上汽通用五菱技术中心)摘要:某车在进行道路可靠性试验时发生后横拉杆支架断裂。
本文利用MSC/NASTRAN软件对后横拉杆支架进行应力分析,找到了导致其断裂的根本原因,提出了最终的改进方案。
试验证明了改进方案的有效性。
关键词: 横拉杆支架,有限元,应力Abstract: The Across Slide Rod Bracket cracked during its road test. In the paper, applyingMSC/NASTRAN, analyze stress of the Across Slide Rod Bracket, found the reason of its crack,and put forward an improved plan. New road test has proved the improved plan is valid.Key words:Across Slide Rod Bracket,FEM,Stress0 前言后悬架横拉杆支架是横拉杆和车身连接的部件,在汽车转弯及回正过程中,承受后悬架横拉杆传递过来的受拉和受压的载荷,其可靠与否,直接影响汽车的操纵稳定性好坏。
由于反复承受拉压交变载荷,容易使其产生疲劳破坏。
某车在海南汽车试验场进行可靠性道路试验,当行驶到14950Km 时出现横拉杆支架断裂失效报告(见图1)。
本文针对此横拉杆支架的一种极端的工况,即汽车满载时发生甩尾的情况下进行有限元静力学分析,通过降低横拉杆支架的最大应力来提高构件的强度和耐久性。
1 有限元模型的建立1.1 网格划分本文利用MSC.Patran 进行有限元分析的前后处理.有限元模型采用四边形板单元(CQUAD4)和三角形板单元(CTRIA3)的混合单元进行网格划分(见图2),该模型共有个4651节点,4493个单元。
汽车车架损坏原因分析及对策

汽车车架损坏原因分析及对策沈贱民;叶爱凤【摘要】车架损坏的原因很多,结合对一些典型损坏问题的分析,对其影响因素加以发掘,找出产生车架早期损坏的原因,为避免类似问题再次发生提供参考.【期刊名称】《汽车科技》【年(卷),期】2009(000)005【总页数】5页(P59-63)【关键词】车架;损坏;原因;对策【作者】沈贱民;叶爱凤【作者单位】东风汽车有限公司,东风商用车技术中心,武汉,430056;东风汽车有限公司,东风商用车技术中心,武汉,430056【正文语种】中文【中图分类】工业技术汽车车架损坏原因分析及对策/沈贱民,叶爱凤使用· 维修汽车车架损坏原因分析及对策沈贱民,叶爱凤东风汽车有限公司东风商用车技术中心,武汉 430056摘要:车架损坏的原因很多,结合对一些典型损坏问题的分析,对其影响因素加以发掘,找出产生车架早期损坏的原因,为避免类似问题再次发生提供参考。
关键词:车架:损坏:原因:对策中图分类号:U472.41 文献标志码:E文章编号:1005-2550(2009)05-0059-05车架是整个汽车的基本部件,它承受着所装载的全部质量,并承受着传递给它的各种力和力矩,是否具有足够的强度、刚度、柔性以保证其本身及安装其上的所有总成部件都能在各个相互位置上正常工作,将直接影响到整车的使用寿命。
车架损坏的原因,主要分析如下。
1设计缺陷引起的应力集中应力集中是车架损坏的主要原因。
当汽车在不平、尤其是扭转的道路上行驶时,很易出现裂纹,原因之一就是设计缺陷引起的应力集中:①在结构上出现尖角:②局部刚度突变所引起的应力突变。
经常承受交变应力作用的车架,应力集中常会诱发裂纹扩张,导致疲劳损坏。
因此在车架设计中,应尽量防止刚度的突变。
比如纵梁内加强板两端应采取尺寸逐渐减小的形状,并使之不处于横梁附近。
纵梁截面高度转折处或水平弯曲处,应尽量使转变缓和,以降低翼缘“ 波纹” 高度,并使其处于拉应力区或低压应力区,波纹高度应限制在 Imm 以下。
汽车悬架推力杆支架失效分析
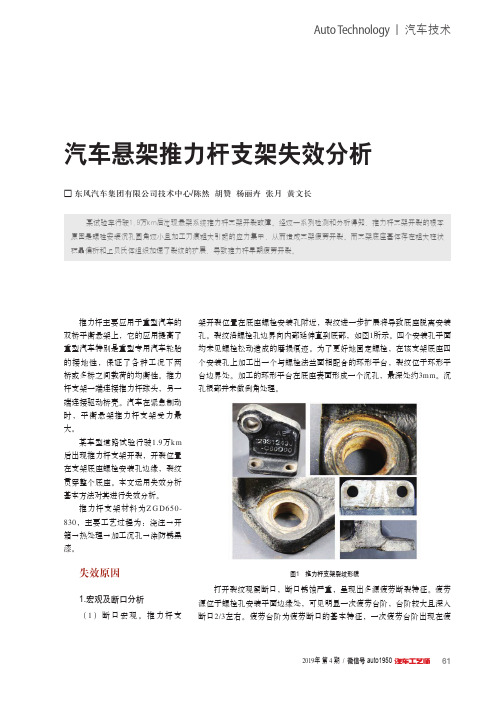
汽车悬架推力杆支架失效分析
□ 东风汽车集团有限公司技术中心/陈然 胡赞 杨丽卉 张月 黄文长
某试验车行驶1.9万k m后出现悬架系统推力杆支架开裂故障。经过一系列检测和分析得知,推力杆支架开裂的根本 原因是螺栓安装沉孔圆角过小且加工刀痕粗大引起的应力集中,从而造成支架疲劳开裂。而支架底座基体存在粗大柱状 枝晶偏析和上贝氏体组织加速了裂纹的扩展,导致推力杆早期疲劳开裂。
失效原因
1.宏观及断口分析 (1)断口宏观。推力杆支
图1 推力杆支架裂纹形貌
打开裂纹观察断口,断口锈蚀严重,呈现出多源疲劳断裂特征。疲劳 源位于螺栓孔安装平面边缘处,可见明显一次疲劳台阶,台阶较大且深入 断口2/3左右。疲劳台阶为疲劳断口的基本特征,一次疲劳台阶出现在疲
2019年 第 4 期 / 微信号 auto1950
图6 推力杆支架失效沉孔基体金相组织
为950MPa,高于GB/T 14408-1993对抗拉强度的要求,见表1。 表1 推力杆支架硬度检测结果
零件名称
实测硬度值HV0.5
换算抗拉强度(根据GB/T 33362-2016)/MPa
判断
推力杆支架 273/289/294/301/317(均值295)
950
推力杆主要应用于重型汽车的 双桥平衡悬架上,它的应用提高了 重型汽车特别是重型专用汽车轮胎 的接地性,保证了各种工况下两 桥或多桥之间载荷的均衡性。推力 杆支架一端连接推力杆球头,另一 端连接驱动桥壳。汽车在紧急制动 时,平衡悬架推力杆支架受力最 大。
某车型道路试验行驶1.9万km 后出现推力杆支架开裂,开裂位置 在支架底座螺栓安装孔边缘,裂纹 贯穿整个底座。本文运用失效分析 基本方法对其进行失效分析。
支架常见故障及其排除

4.2.4 支架常见故障及其排除支架经过样机的各种受力状态下的性能试验、强度试验和耐久性试验,全工作面支架出厂,又经过严格的出厂验收。
因此,支架经受了各种考验,主要结构件和液压元件的强度足够,性能可靠,在正常情况下,一般不会发生大的故障。
但是,支架在井下使用过程中,由于煤层地质条件复杂,影响因素也较多,加之如果在维护方面存在隐患或违章操作,则支架出故障也是难免的。
因此,必须加强对综采设备的维护管理,使支架不出现或少出现故障。
然而,一旦出现故障,不管故障的大小,都要及时查明原因迅速排除、使支架保持完好,保证综采工作面的设备正常运转。
支架在使用中可能出现故障的部位、原因和排除方法,分别简单介绍。
1、结构件支架的结构件通常不会出现大的问题,主要构件的设计强度足够,但在使用过程中也可能出现局部焊缝裂纹。
可能出现裂纹的部位主要为:顶梁柱帽和底座柱窝附近;各种千斤顶支承耳座四周;底座前部中间低凹部分等。
其原因可能是:使用中出现特殊集中受力状态:焊缝的质量差;焊缝应力集中或操作不当等。
处理办法:采取措施防止焊缝裂纹扩大;不能拆换上井的结构件,待支架转移工作面时上井补焊。
2、连接销轴结构件间以及与液压元件连接所用的销轴,可能出现磨损、弯曲、断裂等情况。
结构件的连接销轴有可能磨损,一般不为弯断;千斤顶和立柱两头的连接销轴出现弯断的可能性大;销轴的方销座脱落。
销轴磨损和弯断的原因:材质和热处理不符合设计要求;操作不当等。
如发现连接销轴磨损、弯断,要及时更换。
方销座脱落的主要原因是方销座焊接不牢,销轴轴向受力过大。
3、液压系统及液压元件支架的常见故障,多数与液压系统的液压元件有关,诸如胶管和管接头漏液、液压控制元件失灵、立柱及千斤顶不动作等等。
因此,支架的维护重点,应放在液压系统和液压元件方面。
1)胶管及管接头造成支架胶管和管接头漏液的原因是:O型圈或挡圈大小不当或被切、挤坏,管接头密封面磨损或尺寸超差;胶管接头扣压不牢;在使用过程中胶管被挤坏、接头被碰坏;胶管质量不好或过期老化、起包渗漏等。
QC工具在降低副车架螺栓返工率中的应用

10.16638/ki.1671-7988.2020.23.053QC工具在降低副车架螺栓返工率中的应用雍亮,李浩江(上汽大众汽车有限公司,上海201805)摘要:某车型生产线车身底盘副车架螺栓由人工操作拧紧切换为全自动拧紧设备后,频繁出现套筒找帽失败,导致返工率激增。
针对该问题,通过应用QC工具,调查确定了前纵梁单件孔尺寸偏差、检具导向头与套筒直径匹配度差和六角套筒找帽角度少是导致找帽失败的关键因素,制定了优化改善措施,使返工率由攻关前的11.99%降低至0.82%。
关键词:QC工具;副车架螺栓;套筒;改善中图分类号:U463.1 文献标识码:A 文章编号:1671-7988(2020)23-168-04The application of QC tools in reducing the rework rate of the subframe boltsYong Liang, Li Haojiang(Saic V olkswagen Automotive Co., Ltd., Shanghai 201805)Abstract:After changing the bolt tightening of a subframe of a certain model assembly line from manual operation to automatic equipment operation, an alignment failure of bolts and sockets frequently occurred. Aiming at this problem, QC tools were applied to investigate the key reasons, including the dimensional deviation of holes in frontal longitudinal beams, the mismatching of the gauge orienting tips and the sockets, and the rare matching chance of hexagonal sockets. The optimization and improvement measures were established, which reduced the rework rate from 11.99% to 0.82%. Keywords: QC tools; Subframe bolt; Socket; ImprovementCLC NO.: U463.1 Document Code: A Article ID: 1671-7988(2020)23-168-04前言随着汽车市场竞争日趋白热化,车型的质量和生产效率直接影响用户满意度,其重要性愈加凸显。
基于CAE的汽车底盘关键紧固点失效研究

- 6 -高 新 技 术现阶段针对汽车底盘关键点出现松脱、异响问题,常用的方式是通过扭矩校核比较残余预紧力与最小不滑移预紧力的大小,再以路试试验验证。
该方法效率低,花费周期长,成本代价高。
基于此,国内外学者采用仿真的方法对螺纹连接结构进行了研究。
黄敬尧等人[1]建立了螺纹联接简化模型,通过实际试验验证,得出的结论为该模型精度满足实际工程要求。
徐卫秀等人[2]建立了考虑螺纹细节的仿真模型,研究了参数对预紧力衰减的影响,并验证了该模型的精确性。
Izumi 等人[3] 在三维有限元分析框架内,研究了横向载荷下支承面微滑移引起的松动机理。
Dinger 等人[4]的报告称,对于特定的螺栓接头,引起松动的横向位移可能低至0.55 mm,而与完全支承面滑动相对应的值为0.86 mm。
综上所述,采用仿真的方式可以通过对紧固件尺寸结构,接触状态,载荷工况,边界条件进行模拟,最大限度地模拟实际情况,对改进后方案进行验证。
该文将运用ABAQUS 对上横臂—后副车架异响点采用扭矩法与扭矩转角法拧紧工艺对比仿真,通过对比两者预紧力衰减情况,找出导致异响的关键问题。
1 基于ADAMS的工况载荷提取ADAMS 是一款由多个汽车公司合作开发的,专门运用于建立整车动力学模型的软件,能够在极大程度简化建模的基础上,准确地提取动力学信息。
一般情况下,要想建立满足工程精度要求的动力学模型需构建以下系统,即整车的前、后悬架子系统,车身子模型系统,轮胎子模型系统和制动子模型系统。
基于此,该文运用ADAMS 对公司某车型建立整车动力学模型,如图1所示,上横臂—后副车架连接点动力学仿真结果见表1。
为保证螺纹联接的可靠性,选择其中过单侧深坑为目标载荷。
图1 整车动力学模型表1 上横臂-后副车架连接点动力学仿真结果工况合力矩(N)绕X 轴力矩(N)绕Y 轴力矩(N)绕Z 轴力矩(N)合力(N·mm)沿X 轴力(N·mm)沿Y 轴力(N·mm)沿Z 轴力(N·mm)向前紧急制动12 534 4 876-11 51585515 009-14 5368 3 736向后紧急制动 6 442-3 2265 5741706 173-4 938336-3 689过单侧深坑18 522 2 681-18 010 3 39424 722-24 544373 2 936极限转向12 014-14111 911-1 56721 626-21 470348-2 564转向制动 5 1462 528-4 43366519 232-19 119235 2 068转向驱动13 250-2 45213 0216810 158-9 220399-4 2432 仿真分析2.1 上横臂与后副车架有限元模型将上横臂—后副车架螺栓连接结构作为研究对象,如图2所示,包括上横臂总成、后副车架、螺栓和螺母。
装载机副车架断裂失效分析

断裂处
断裂处
图 1 副车架零件简图及断裂位置
某型轮式装载机副车架在使用过程中发生早期 异常断裂失效,本文对断裂副车架从宏观断口、材 料、金相组织、裂纹形态、力学性能等方面进行综合 分析,找出副车架开裂的原因,为设计、材料、工艺等 方面优化与改进提供依据,提高质量及性能,避免零
图 2 失效零件及宏观断口形貌
表 2 力学性能试验结果
100滋m
图 4 拉伸试样横截面组织 500×
100滋m
项目
抗拉强度 Rm/MPa
行标标准值 54.3
逸700 /
屈服强度 ReL/MPa
逸480 /
断后伸长率 A /%(L0 =50mm) 逸15 /
断面收缩 率 Z/%
逸20 调质
热处理状态 调质实测值
灰色
图 5 拉伸试样横截面晶粒形貌 400×
表 1 断裂副车架化学成分检测结果(质量分数%)
验参照 TB/T 3212.3[2《] 机车车辆用低合金铸钢金相组 织检验图谱 第 3 部分:E 级铸钢》标准,1 级耀7 级为 合格。零件奥氏体晶粒度采用过饱和苦味酸水溶液 浸蚀显示,奥氏体晶粒度要求不大于 5 级。
拉伸试样异常断口附近的横截面的金相组织为 回火索氏体+极少量先共析铁素体,1 级,属于正常调 质组织;其奥氏体晶粒度为 7 级耀8 级,见图 4 和图 5.
100滋m
图 8 内框表面组织 500×
100滋m
100滋m
图 10 裂纹 1 抛光态形貌 100×
100滋m
100滋m
图 9 内框表面组织晶粒形貌 400×
纵向切割断口位置,纵截面可见裂纹 1 源于内 部铸态晶棱,呈直角状,向两边延伸直到断面,多处 呈直线扩展,其组织为回火索氏体+极少量先共析铁 素体,1 级,见图 10、图 11;裂纹 2 源于原铸态晶棱, 尾部呈光滑直线状,其组织为回火索氏体+极少量先 共析铁素体,1 级,见图 12、图 13;裂纹 3 源于原铸态 晶棱,尾部光滑,其组织为回火索氏体,6 级,见图 14;断口纵截面正常组织位置的奥氏体晶粒度为 7 级耀8 级,见图 15.
沈智达_某车型副车架模态拓扑优化设计

某车型副车架模态拓扑优化设计沈智达陈海树刘双宇华晨汽车工程研究院某车型副车架模态拓扑优化设计Sub-frame Eigenvalue Design Base on TopologyOptimization沈智达陈海树刘双宇(华晨汽车工程研究院)摘要:本文以某车型副车架为例,介绍了基于拓扑优化方法,应用有限元软件HyperWorks 的OptiStruct模块建立有限元模型的过程。
通过优化计算,使一阶扭转模态值达到最佳水平,并对优化结果进行了台架试验对比验证,优化结果可为同类产品设计提供参考。
关键词:拓扑优化,模态频率,副车架,有限元分析,OptiStructAbstract: Based on the optimization theory, this paper introduced the process of building FEA model for sub-frame using the OptiStruct software. The results show that the 1st torsion value reaches the best level, and the actual verification was carried out through the test. The optimized results can be a reference for the similar products.Key words: Topology Optimization, Modal Frequency, Sub-Frame, FEA, OptiStruct1 引言汽车底盘的主要性能是舒适性和操控性,在悬挂系统的设计和匹配上,设计师们都尽可能的用一些复杂结构来实现舒适性和操控性的平衡,而一些对舒适性和操控性影响较大的装备和设计也应运而生,副车架就是一个典型的代表。
副车架实际是一个支撑车桥和悬架的支架,汽车的行走系统(也就是车桥,包括车轮、轮轴、差速器等部件)通过悬架元件先安装在这个支架上,再作为一个整体总成,用起减振抗扭作用的弹性橡胶垫连接到车身上。
某车型副车架横梁的应力分析及优化
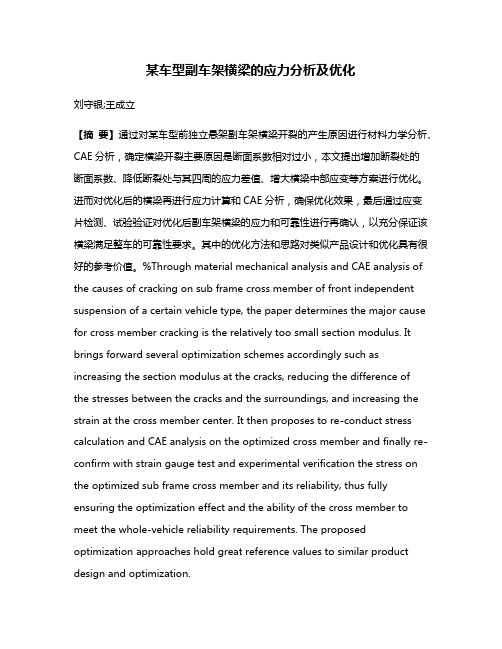
某车型副车架横梁的应力分析及优化刘守银;王成立【摘要】通过对某车型前独立悬架副车架横梁开裂的产生原因进行材料力学分析、CAE分析,确定横梁开裂主要原因是断面系数相对过小,本文提出增加断裂处的断面系数、降低断裂处与其四周的应力差值、增大横梁中部应变等方案进行优化。
进而对优化后的横梁再进行应力计算和CAE分析,确保优化效果,最后通过应变片检测、试验验证对优化后副车架横梁的应力和可靠性进行再确认,以充分保证该横梁满足整车的可靠性要求。
其中的优化方法和思路对类似产品设计和优化具有很好的参考价值。
%Through material mechanical analysis and CAE analysis of the causes of cracking on sub frame cross member of front independent suspension of a certain vehicle type, the paper determines the major cause for cross member cracking is the relatively too small section modulus. It brings forward several optimization schemes accordingly such as increasing the section modulus at the cracks, reducing the difference ofthe stresses between the cracks and the surroundings, and increasing the strain at the cross member center. It then proposes to re-conduct stress calculation and CAE analysis on the optimized cross member and finally re-confirm with strain gauge test and experimental verification the stress on the optimized sub frame cross member and its reliability, thus fully ensuring the optimization effect and the ability of the cross member to meet the whole-vehicle reliability requirements. The proposed optimization approaches hold great reference values to similar product design and optimization.【期刊名称】《汽车实用技术》【年(卷),期】2014(000)008【总页数】4页(P41-44)【关键词】副车架;横梁;应力;断面系数;应力分析;优化【作者】刘守银;王成立【作者单位】安徽江淮汽车股份有限公司技术中心,安徽合肥 230022;安徽江淮汽车股份有限公司技术中心,安徽合肥 230022【正文语种】中文【中图分类】U463.33CLC NO.:U463.33Document Code:AArticle ID:1671-7988(2014)08-41-04某车型的前轴为麦弗逊前独立悬架,在试验场强化路试验过程中前轮受到撞击后,副车架横梁发生开裂现象,如图1所示。
铁路货车K2型转向架交叉支撑装置故障原因分析及改进建议

铁路货车K2型转向架交叉支撑装置故障原因分析及改进建议摘要:本文对交叉支撑装置进行了简要的介绍,通过本人在工作中接触和了解的交叉支撑转向架故障多发部位和情况,针对交叉支撑转向架在实际运用中发生的故障进行详细介绍与分析,提出与实际情况相符的建议方案,从而减少转向架交叉支撑装置故障对铁路行车安全的影响。
关键词:铁路货车,交叉支撑装置,故障,建议为了适应我国铁路运输高速重载要求,提高运输效率,采用交叉支撑装置的转向架能够较大的增加转向架的抗凌刚度,从而提高转向架临界速度和货车直线运行稳定性;有效保持转向架正位状态,减少在曲线运行时轮对与钢轨冲角,从而改善转向架曲线通过性能,显著降低车轮轮缘磨耗。
转K2型转向架属于铸钢三大件式转向架,在两侧架之间安装了弹性下交叉支撑机构,交叉杆从摇枕下面穿过,4个端点轴向橡胶垫与侧架连接。
侧架弹性交叉支撑装置由1个下交叉杆、1个上交叉杆、8个轴向橡胶垫、4个双耳垫圈、4个锁紧板、4个标志板、4个紧固螺栓(强度等级10.9级)组成。
在上、下交叉杆中部焊有夹板,利用2组M12螺栓、螺母、垫圈将夹板紧固,同时把螺母用电焊点焊加固,夹板间有4处塞焊点和2条平焊缝,把上、下交叉杆连接成一个整体。
1.交叉支撑装置交叉杆磨耗原因分析1.1侧架上的横跨梁安装座焊装位置偏差较大,与侧架顶面的距离较小,当车轮直径较大,下心盘无垫板时,重车枕簧压缩情况下,上旁承也随之下降。
此外,横跨梁安装座立面翼板宽度尺寸过大,车辆通过曲线时上旁承最下部的磨耗板就会碰横跨梁安装座使之弯曲变形。
1.2交叉杆压痕前后位置设计不合理,现压痕前后位置没有完全躲开闸瓦托底部过渡圆弧,随着车辆的长时间运行,闸瓦托底部与交叉杆不断产生摩擦,最终导致交叉杆磨耗超限。
1.3货车车辆运行中受到的振动和冲击较大,而交叉杆属于簧下装置,振动更为严重。
剧烈的振动导致马蹄环螺栓松动,马蹄环随之与杆体间接触产生碰撞,使交叉杆横向以及马蹄环弧面根部产生较为严重的磨损。
汽车前副车架开裂失效分析

图3 CAE分析状态
Research and / nZL^>?4Si \ +
Discussion /
kU
4.1断口分析 在开裂位置上表面进行观察,焊道附件钢 板表面存在焊渣,裂纹扩展已延伸至焊道上, 裂纹存在转折(见图4);下表面观察,裂纹 为贯穿状态,长度为4 mm (见图5);边缘 冲切面状态较好,无明显冲切痕迹(见图6)。 对断口进行宏观分析,断口表面腐蚀,但 钢板边缘可见疲劳台阶,断裂起始于冲切面与 上表面交界处,断裂性质为疲劳断裂(见图7 )。 4.2材质分析 4.2.1化学成分分析 在断口附近取样进行化学成分分析,测试 结果见表1,满足SAPH440材料的化学成分 要求,结果合格。 4.2.2硬度分析 为分析焊接对开裂位置材料性能的影响, 在断口附近与远离断口与焊道的基材位置分别 进行维氏硬度测试,测试结果见表2,硬度值 接近。 4.2.3金相分析 对开裂件进行金相分析,开裂源区附近平 行于断口方向存在另一条裂纹,表面存在腐蚀 坑(见图8),断口处金相组织为铁素体+珠 光体(见图9),远离断口位置金相组织为铁 素体+珠光体(见图10),组织基本一致。
剧开裂对应位置应力集中,导致疲劳寿命降低,是副车架在试验过程中开裂的主要因素。通过CAE分析,得知在加速
与制动工况下,开裂位置受力最大。分别选取2台设计状态与失效状态的副车架,模拟加速与制动工况进行台架试验
验证。试验验证结果显示,设计状态下的副车架循环次数最低提升41 %,能够满足整车耐久试验要求。 关键词:前副车架;焊接;开裂;应力集中
表3对比验证结果
样件
试验结果
备注
161 环境技术 / Environmental Technology
绑 0宀
- 1、下载文档前请自行甄别文档内容的完整性,平台不提供额外的编辑、内容补充、找答案等附加服务。
- 2、"仅部分预览"的文档,不可在线预览部分如存在完整性等问题,可反馈申请退款(可完整预览的文档不适用该条件!)。
- 3、如文档侵犯您的权益,请联系客服反馈,我们会尽快为您处理(人工客服工作时间:9:00-18:30)。
某车型副车架防转支架失效原因分析
作者:马江丰王亮
来源:《科学与财富》2017年第26期
摘要:某车型耐久试验车副车架在摆臂拆卸过程中出现防转支架失效,摆臂拆卸困难。
本文主要对此问题产生的原因进行分析,通过工艺过程分析、防转支架受力分析,确定失效原因为副车架及摆臂小轴套实际轴线与理论轴线存在偏差,防转支架焊道长度短,打紧螺栓时,力矩全部由防转支架承受,导致防转支架失效。
关键词:副车架、防转支架、同轴、变形
1 失效案例
某车型副车架与摆臂连接位置设计为防转支架结构(内含方螺母),其作用是防止方螺母旋转,便于零件的装配。
但在此车型的耐久试验车拆卸过程中,出现防转支架未满焊翻边发生翘起变形,导致螺母与螺栓连轴转问题,摆臂拆卸困难。
2 失效原因分析
2.1 工艺过程分析
副车架总成及摆臂总成小轴套轴线与大轴套轴线理论上应相交,即处于同一平面。
通过5套零件数据测量,副车架焊接总成中左右小轴套轴线相对大轴套轴线均偏向于远离球销方向,左右摆臂焊接总成中小轴套轴线相对大轴套轴线均偏向于接近球销方向,即副车架小轴套实际轴线与摆臂小轴套实际轴线偏向相反的方向。
在副车架与摆臂合装过程中,因大轴套安装位设计有环形限位结构,需先将摆臂大轴套安装到位后使用定位销定位,然后小轴套旋入副车架总成小轴套安装位,小轴套内管外端面与副车架小轴套外安装孔对正时,因副车架小轴套实际轴线与摆臂小轴套实际轴线偏向相反的方向,小轴套内管内端面相对副车架小轴套内安装孔产生错位,即合装后,摆臂小轴套内管轴线与副车架小轴套安装位轴线不同轴,三条轴线相对位置关系如图1所示。
摆臂小轴套内管轴线与副车架小轴套安装位轴线不同
轴,会使摆臂安装螺栓与副车架板不垂直,使方螺母无法紧贴副车架板表面,安装过程中无法通过摩擦力承受全部拧紧力矩,会使大部分扭矩由防转支架承受。
2.2 防转支架受力分析
如图2所示,防转支架右、上两侧满焊,左侧8mm焊道,下侧无焊道。
图示工况下,左侧翻边受力点与焊道固定点存在17mm长的力臂,在承受至一定力后因杠杆效应,左侧翻边局部应力超过材料屈服强度,发生翘起变形,同时下侧无焊道亦会产生变形。
防转支架设计时至少需要保证相对两侧翻边强度,即可实现其防转功能。
而通过上述受力分析,此失效防转支架仅有相邻翻边满足强度要求,没有相对的两个满足强度要求的翻边。
这是防装支架发生失效的一个主要因素。
3 问题再现及对策验证
3.1 原工艺过程问题再现
副车架与摆臂合装过程中,安装位轴线是否同轴的两种情况:
(1)完全同轴:方螺母与副车架贴合,经实际验证,防转支架无变形;
(2)不同轴:方螺母与副车架呈一定角度,不完全贴合,经实际验证,防转支架在拧紧力矩达到150N.m(设计扭矩为210 N.m±15 N.m)变形失效。
3.2 对策制定及验证
(1)调整副车架或摆臂焊接工装,使副车架小轴套实际轴线与摆臂小轴套实际轴线偏向方向一致,保证副车架和摆臂合装后的同轴度,使拧紧力矩大部分由摩擦力承受;
(2)将防转支架左侧翻边焊道由8mm焊道更改为满焊,保证防转支架左右两侧翻边强度。
为验证防转支架更改方案可行性,验证其在极端工况下是否满足使用要求(即拧紧力矩全部由防转支架承受)。
验证时使方螺母与副车架不贴合,验证结果见表1;结果表明拧紧扭矩达到240 N.m时(要求210 N.m±15 N.m),防转支架仍具备防转功能,更改方案满足使用要求。
4 总结
从设计及过程实现两方面进行问题分析解决。
设计时,需保证相对两侧翻边的强度,才能实现防转支架的防转功能。
过程实现方面,需保证副车架小轴套安装位轴线与摆臂小轴套轴线同轴,从而确保总成的功能实现。
参考文献:
[1] 约森-赖姆佩尔.悬架元件及底盘力学[M].长春:吉林科学技术出版社,1992.
[2] 刘惟信.汽车设计[M].北京:清华大学出版社,2001.。