熔模铸造新型型芯工艺
熔模铸造工艺技术

熔模铸造工艺技术熔模铸造是一种常用的铸造工艺,可用于生产各种复杂形状的零件。
它与传统的砂型铸造相比,具有更高的精度和表面质量。
本文将介绍熔模铸造的工艺技术及其应用领域。
熔模铸造是一种以聚苯乙烯(EPS)或其它材料为原型制作模具的铸造工艺。
首先,根据产品设计要求和CAD模型,制作出芯型,然后将芯型放入砂箱,灌注耐高温石膏产生密封模具。
模具灌注时要控制温度和压力,以确保芯型的完整性。
接下来,将模具放入高温炉中,在高温下,芯型内的EPS膨胀和燃烧,同时石膏固化和脱水。
最后,通过真空吸铸或压铸法,将金属液注入模具中,待凝固后,打开模具,得到最终产品。
熔模铸造具有许多优点。
首先,由于熔模铸造采用模具制作的方法,因此可以生产出各种几何形状复杂的零件,如叶片、涡轮、阀门、轴承等。
其次,熔模铸造的精度高,尺寸准确,表面光洁,减少了后续加工的需要。
第三,熔模铸造的生产周期短,效率高,可以大规模生产,并且每次生产的零件质量稳定。
最后,熔模铸造可用于生产各种金属材料,如铝合金、钢、镍基高温合金等。
熔模铸造在航空航天、能源、汽车等领域有广泛应用。
在航空航天领域,熔模铸造可制造出高温合金零件,如航空发动机叶轮、复杂的涡轮叶片等。
这些零件因其复杂的形状和高要求的工作条件,传统的铸造工艺难以满足其需求,而熔模铸造则能够提供更好的选择。
在能源领域,熔模铸造可生产出高温、高压的涡轮壳体、汽轮机叶片等零件,提高了能源设备的工作效率。
在汽车领域,熔模铸造可生产出发动机缸体、曲轴等零件,提高了发动机的功率和可靠性。
总之,熔模铸造是一种重要的铸造工艺,广泛应用于各个领域。
它通过模具制作和高温烧脱的工艺,可以生产出各种复杂形状的零件,具有高精度和表面质量。
随着科技的进步,熔模铸造的工艺技术也在不断发展,将为各行各业提供更好的解决方案。
1.6型芯解析

(3)装钵和填充填料
装钵是将压制成型的陶瓷型芯坯体埋入盛 有填料的钵中,防止型芯在焙烧过程中变形损 坏。
型芯在匣钵内的放置示意图
常用填料: 经1300℃下保温4~6h焙烧过的工业氧化铝。 填充:
在振幅为0.2~0.5mm的振动台上填充填料并
紧实。
(4)烧结
焙烧可分为排蜡和烧结两个阶段。通过加热
低温强化
目的:提高型芯的室温强度。
方法:将焙烧好的陶瓷型芯浸渗在溶有热固性树脂
和固化剂溶液中。一般将型芯浸泡在强化剂
中30min,常温强度可提高1.5~3倍。
高温强化
目的:提高型芯的高温强度。
方法: 可浸硅酸乙酯水解液或硅溶胶,能使高温强度提高 30%~50%。
经强化后的型芯
5)型芯脱除
除形状简单而尺寸较大的型芯用机械脱除
将陶瓷型芯坯体中的增塑剂去除称排蜡。
热压注硅质陶瓷型芯的焙烧工艺规范
T<600 ℃: 为排蜡阶段。为使坯体不产生起皮、鼓泡等 缺陷,此时升温要缓慢而均匀。 T>900 ℃: 为烧结阶段。可以快速升温至终烧温度。通常 终烧结温度在1100~1400℃之间,保温2~4h。
(5)强化
将某种粘结剂溶液浸入已烧成的陶瓷型芯中 以提高其强度。强化分低温强化和高温强化。
法外,大多数陶瓷型芯采用化学腐蚀法脱除,
如混合碱法,碱溶液法,压力脱芯法,氢氟 酸法。
热压注法陶瓷型芯常用脱芯方法
脱芯 方法 混合 碱法 碱 溶 液 压力 脱芯 法 氢氟 酸法 脱芯材料 W(NaOH)35% +w(KOH)65% W(NaOH)30%~ 40%水溶液 w(KOH)60%~70% 水溶液 W(NaOH)30% ~40%的水溶液 氢氟酸 脱芯温度 /℃ 400~500 脱芯时间 /h 0.5~1.0 优点和应用范围 腐蚀性大,脱芯速度较 快,受设备限制,多用 于小批量生产 腐蚀性较小,但脱芯速 度慢,可用于大批量 生产 腐蚀性较小,脱芯速 度较快,适合大批量 生产,但需专门设备 腐蚀性和毒性大,但无 专门设备,适合单件小 批量生产 清洗与中和 1-热水冲洗 2-冷水冲洗 3-中和 W(HCl)25%+ W(H3PO4)25% + W(水)50% 4-冷水冲洗 5-用酚酞液 滴入检测应 为中性 水冲洗
熔模精密铸造

熔模精密铸造熔模精密铸造也叫失蜡铸造,采用可溶一次性蜡模和一次性陶瓷型壳及陶瓷型芯铸造成型的方法。
这种方法非常适合生产尺寸公差小、薄壁、拔模斜度小和表面光洁度大的铸件用该方法生产的铸件尺寸精度高,表面质量好,,经常不需要特殊的处理就能直接装配使用。
基本工艺流程为:将耐火材料和粘结剂配制成粘度适中的浆料,把表面清洁、尺寸精确的蜡模在浆料里浸蘸,撒砂。
待其干燥后,重复多次蘸浆、撒砂步骤,每一层浆料的粘度与所撒得砂的粒度都有变化,一般面层为细沙,背层为粗砂;最后一层只挂浆,不撒砂;待型壳充分干燥后,用水蒸汽或热水进行脱蜡,最后进行焙烧,使型壳具有一定强度。
浇注铸件前,型壳要预热到一定温度,以保证金属具有较好的流动性;浇注金属液,待铸件凝固后,除壳,清砂,得到所需铸件。
其工艺程见图所示。
熔模铸造方法生产的铸件内部难免有缩松、缩孔产生,因此铸件在使用前一般要经过热等静压处理,以减少内部缺陷对铸件性能的影响。
由于,在热等静压后的铸件容易变形,因此还需要采取一些辅助措施来防止铸件变形。
1.模料制备1.1.精铸中常用的模料对于航空航天产品,其铸件尺寸精度和表面光度要求较高,因此熔模尺寸精度和表面光洁度比铸件要求更高,通常要高1-2级。
为此作为精密铸造用模料要求选用热稳定性好、强度高、流动性好、膨胀收缩小的优质材料。
按照模料的基体材料组成,可分为蜡基模料、树脂基模料、塑料模料、填衬模料及水溶性模料。
其中蜡基模料和树脂基模料被广泛使用,其模料性能日益完参,其种类已被人们所熟知。
主要就近几年发展的后三种介绍一下:水溶性模料受到重视是由于航空航天工业的发展,要求生产越来越多尺寸大而壁薄的精铸件,一般蜡制熔模收缩较大,容易变形,难以满足要求。
主要水溶性模料有尿素基水溶性模料、纯尿素模料、熔模精密铸造的工艺路线、尿素—聚合物模料、聚乙醇基模料(由于价钱较贵,故只作水溶性型芯而不作熔模)。
日本已研制出适于在0.7-1.SMPa范围内压注成型甚至可自由浇注的水溶性模料和DRN一1177模料。
熔模铸造工艺

所有铸件材料
铸件内部较大的缩孔、裂纹等缺 铸钢件、铸铁件等通磁
陷
材料
渗透探伤
铸件表面裂纺
B、防锈
不锈钢等非磁性材料
目的:保证铸件库存状态不锈蚀; 方法:防锈液浸入法。
3.3.12、品质检查
A、外观质量
标准:Q/DFLCM0108-2006 熔模精密铸件技术条件
检验内容 铸件尺寸、形状和
重量 表面粗糙度
密封性检验 盐雾试验 抗氧化试验 磁性能测定
成品(不需加工):按标准包装要求,定箱入库; 半成品(需后序加工):装箱发下序加工
四、熔模铸造应用范围
从产品类别来看,熔模精密铸件主要分为两大 类:军工、航空类产品与商品类产品。前者质量 要求高,后者质量不如前者。随着冷战时代的结 束,各国军工产品大幅度减少,但民航、大型电 站及工业涡轮发动机的发展,使得军工、航空类 产品所占比例变化不大。现在熔模铸造除用于航 空、军工部门外,几乎应用于所有工业部门,如 电子、石油、化工、能源、交通运输、轻功、纺 织、制药、医疗器械等领域。
B、制壳操作流程
硅溶胶制壳工艺没有化学硬化, 干燥脱水
3.3.5、脱蜡
A、脱蜡是模型蜡从模壳中脱出形成型腔的过程,脱蜡前 模壳存在时间不低于24h; B、脱蜡方法:热水法和高压蒸气法
脱蜡时注意事项: ➢ 清理浇口杯顶残砂:防止浮砂落入型腔; ➢ 加入补充硬化剂:热水脱蜡时加入1%盐酸,型壳得到 补充硬化,并可防止蜡料皂化; ➢ 脱蜡水严禁沸腾:防止将槽底的砂粒翻起进入型腔; ➢ 脱蜡后的型壳禁止杯口向上放置:防止脏物落入型腔。 ➢ 槽液定期清理与更换。
五、熔模铸造工艺发展趋势
1、更大更薄:目前,熔模铸造生产的精密铸件,最大轮廓尺寸可 达1.8m,而最小壁厚却不到2mm,最大铸件重量接近1000kg。
“型芯”在熔模铸造中的应用

“型芯”在熔模铸造中的应⽤摘要:熔模铸造中,常使⽤的型芯有:耐⽕型芯、陶瓷型芯以及⽔溶型芯(⽔溶蜡、尿素等);但是陶瓷型芯由于价格昂贵,⽔溶型芯由于制壳困难等。
如何使⽤价格低廉、清理⽅便的铸件型芯是我们铸造⼯作者们值得探讨的问题。
各种制芯⼯艺及其特点:熔模铸造的特点:主要⽣产质量要求较⾼、结构复杂的不锈钢,碳素结构钢和低合⾦钢等铸件。
硅溶胶粘结剂制壳⼯艺,⽣产的铸件表⾯粗糙度为Ra1.6-6.3µm ,尺⼨精度为CT4-CT6;⽔玻璃粘结剂与⽯英质耐⽕材料制壳⼯艺,铸件表⾯粗糙度为Ra3.2-12.5µm,尺⼨精度仅为CT7-CT8,主要⽣产质量要求不⾼的碳钢和低合⾦钢铸件。
由于某些铸件的内腔和孔洞形状不规则,⽆法⽤抽芯机构来完成。
因此,我们必须采⽤型芯来解决这⼀难题。
1.型芯的主要⽤途:是形成铸件的内腔和孔洞。
2.对型芯的要求:1)型芯的形状、尺⼨及在型腔中的位置应符合铸件的要求;2)要有⾜够的强度和刚度;3)要有⾜够⾼的耐⽕度以保证型壳焙烧和合⾦液浇注。
3.各种型芯的⽣产⼯艺及优缺点:1)覆膜砂芯:⽤酚醛树脂作粘结剂,乌洛托品作固化剂。
(采⽤覆膜砂—热芯盒射芯⼯艺,制造砂芯,再将表⾯上涂料;涂料的作⽤:①防粘砂;②降低铸件表⾯粗糙度;③加固砂芯表⾯等)。
2)采⽤⽔玻璃砂CO2硬化⼯艺制作砂芯,再将表⾯涂料。
(⽔玻璃砂芯的优缺点:优点:⼯艺简单、砂型强度⾼,劳动环境好等;缺点:浇注后型砂溃散性差,铸件落砂困难,砂芯容易吸潮造成强度降低。
因此,⽔玻璃加⼊量要求≤3.5%。
) 3)有机脂⽔玻璃砂芯:在⽔玻璃砂中加⼊固化剂,在室温下能⾃硬,砂芯在硬化后起模。
(有机脂硬化⽔玻璃砂⾃硬原理:有机脂与⽔玻璃混合后,在⽔玻璃之碱性介质中,有机脂发⽣⽔解,分解为醇和酸。
有机酸和⽔玻璃反应析出硅酸,却相互结合形成⽹状的硅酸凝胶、逐步硬化。
此时由于砂粒被分别包围在⽹状结构中,于是型砂建⽴起强度。
熔模精密铸造新技术新工艺

熔模精密铸造新技术新工艺一、概述熔模精密铸造是我国的一种古老的传统工艺。
早在2400多年以前,我国就采用失蜡法铸造出精美的工艺品。
在此基础上运用现代技术发展成为无余量熔模精密铸造这一新的铸造技术,这种方法可以铸造出几何形状非常复杂的零件,而且,除装配面需经机械加工外,其它内外表面均不需加工,节约了大量的设备和人力,大大缩短了制造周期。
五十年代初,我国已将熔模铸造用于机械制造,特别是航空涡轮发动机叶片的生产。
而西方国家六十年代已出现了无余量精密铸造技术。
我国运用、掌握这一技术是在七十年代末期以引进英国R·R公司斯贝发动机制造技术专利为标志的。
随后,在航空发动机制造厂(410、420、430、331厂、航材院)内得到了迅速的推广应用和发展,大大提高了我国航空发动机制造工艺水平,提高了产品的质量,明显降低了产品的制造成本。
随着现代航空发动机涡轮前进口温度的不断提高,单靠提高材料的性能来满足发动机性能的提高已不可能,于是从发动机的设计结构和制造工艺的结合上力争找到突破点,表现在无余量精密铸造上的突破点就是:(1)将涡轮工作叶片和导向叶片由实心设计成空心,采用严格的强制冷却技术,这样就使得精铸叶片的内腔越来越复杂,这就是无余量精铸空心叶片。
(2)人为改变晶粒的生长方向,让一个叶片的晶粒,全部沿着叶片受力的主应力轴方向平行生长,甚至整个叶片就是一个晶粒,没有第二个晶粒,这就是定向凝固叶片或叫单晶叶片,这种技术就叫定向凝固(单晶)技术。
如果和第一个结合起来,它就叫“无余量(精铸)定向(单晶)空心叶片”。
与这个方法相比,第1种方法又叫“无余量(精铸)等轴晶空心叶片”。
(3)将多个单个零件分别加工出来或若干个单元体制造出来再组装成一个整体组件,而改为整体铸造出来,原来需经加工的型面而改为直接铸出,这就是无余量整体精密铸件,这种技术就是无余量整铸技术。
上述技术已在我国航空、航天发动机制造技术上得到充分的体现:无余量精铸空心叶片技术在FWS9发动机、WP13发动机、FS-2发动机上得以应用。
国外熔模铸造新材料和新工艺的发展概况
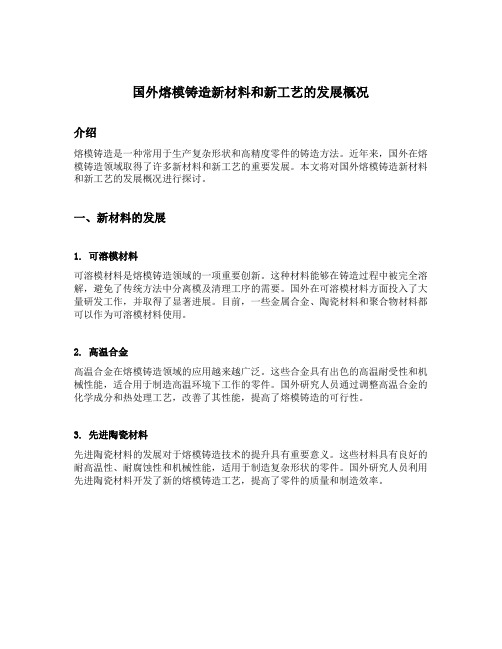
国外熔模铸造新材料和新工艺的发展概况介绍熔模铸造是一种常用于生产复杂形状和高精度零件的铸造方法。
近年来,国外在熔模铸造领域取得了许多新材料和新工艺的重要发展。
本文将对国外熔模铸造新材料和新工艺的发展概况进行探讨。
一、新材料的发展1. 可溶模材料可溶模材料是熔模铸造领域的一项重要创新。
这种材料能够在铸造过程中被完全溶解,避免了传统方法中分离模及清理工序的需要。
国外在可溶模材料方面投入了大量研发工作,并取得了显著进展。
目前,一些金属合金、陶瓷材料和聚合物材料都可以作为可溶模材料使用。
2. 高温合金高温合金在熔模铸造领域的应用越来越广泛。
这些合金具有出色的高温耐受性和机械性能,适合用于制造高温环境下工作的零件。
国外研究人员通过调整高温合金的化学成分和热处理工艺,改善了其性能,提高了熔模铸造的可行性。
3. 先进陶瓷材料先进陶瓷材料的发展对于熔模铸造技术的提升具有重要意义。
这些材料具有良好的耐高温性、耐腐蚀性和机械性能,适用于制造复杂形状的零件。
国外研究人员利用先进陶瓷材料开发了新的熔模铸造工艺,提高了零件的质量和制造效率。
二、新工艺的发展1. 数字化熔模铸造数字化熔模铸造是近年来国外熔模铸造领域的一个重要趋势。
通过使用计算机辅助设计(CAD)和计算机辅助制造(CAM)技术,熔模铸造的整个流程可以被数字化和自动化。
这种新工艺提高了生产效率,减少了人员介入,同时提高了零件的精度和一致性。
2. 快速凝固技术快速凝固技术是一种有效改善铸造品质的方法。
通过控制熔体的冷却速率,可以获得细小而均匀的晶粒结构,提高零件的强度和耐磨性。
国外研究人员在快速凝固技术方面做了大量工作,开发出了多种新型凝固设备和工艺。
3. 热电耦合熔模铸造热电耦合熔模铸造是一种将热电偶技术与熔模铸造相结合的新工艺。
通过在熔化金属中插入热电偶,可以实时监测熔体温度和热流,调节铸造参数,提高铸件的品质。
热电耦合熔模铸造在国外得到了广泛应用,并取得了良好的效果。
国外熔模铸造新材料和新工艺的发展概况

国外熔模铸造新材料和新工艺的发展概况一、熔模铸造技术概述熔模铸造是一种传统的金属铸造技术,它通过将金属加热到液态,然后倒入预先制作好的熔模中进行成型。
这种技术具有成型精度高、表面光洁度好等优点,广泛应用于汽车、航空航天、电子设备等领域。
二、国外熔模铸造新材料和新工艺的发展概况1. 新材料的应用在熔模铸造中,新材料的应用可以提高产品的性能和质量。
例如,在航空航天领域,采用高温合金材料可以提高部件的耐高温性能;在汽车领域,采用铝合金可以降低车身重量。
此外,还有一些新型材料如钛合金、镍基合金等也得到了广泛应用。
2. 新工艺的发展随着科技不断进步,新工艺也不断涌现。
其中最具代表性的是快速凝固技术和数控加工技术。
快速凝固技术是利用高速冷却来制备非晶态或细晶粒材料,提高材料的强度和硬度。
这种技术可以应用于熔模铸造中,制备出更加高性能的铸件。
数控加工技术则是通过计算机控制机床进行加工,可以实现高精度、高效率、低成本的生产方式。
这种技术可以应用于熔模铸造中,提高产品的加工精度和生产效率。
三、国外熔模铸造新材料和新工艺的应用案例1. 高温合金材料在航空领域的应用高温合金材料具有优异的耐腐蚀性和耐高温性能,在航空领域得到了广泛应用。
例如,美国通用电气公司采用了一种名为“单晶涡轮叶片”的部件,该部件采用了先进的熔模铸造技术,结合快速凝固技术制备出非晶态合金材料,从而实现了更好的性能。
2. 铝合金在汽车领域的应用铝合金具有轻质、强度高等特点,在汽车领域得到广泛应用。
例如,德国宝马公司采用了一种名为“i3”的电动车型,该车身采用了铝合金材料,从而实现了更轻量化的设计。
四、国外熔模铸造新材料和新工艺的未来发展趋势1. 绿色环保随着环保意识的不断提高,绿色环保已经成为了未来发展的重要趋势。
在熔模铸造中,采用可再生材料和节能减排技术将成为未来发展的方向。
2. 数字化制造数字化制造是将数字技术应用于制造业中,可以实现高效率、高精度、低成本的生产方式。
- 1、下载文档前请自行甄别文档内容的完整性,平台不提供额外的编辑、内容补充、找答案等附加服务。
- 2、"仅部分预览"的文档,不可在线预览部分如存在完整性等问题,可反馈申请退款(可完整预览的文档不适用该条件!)。
- 3、如文档侵犯您的权益,请联系客服反馈,我们会尽快为您处理(人工客服工作时间:9:00-18:30)。
23 "?!" / "?&’
45 "?!" / "?’"
6$ "?", / "?"@
7$ "?"!
89 痕迹量
(&)矿化剂
石英玻璃的烧结和析晶几乎同时于 !!"" / !&""( 开始,这就使石英
玻璃的陶瓷型芯烧成温度很难掌握。若温度偏低,则型芯没有烧结或烧结不足,其强度 低;若温度偏高,则型芯虽烧结,但又析出过量方石英,冷却后型芯的常温强度也很 低。为解决这一矛盾,需加入能适当降低陶瓷型芯烧结温度的某些添加剂,即矿化剂。 矿化剂能促成烧结并兼有提高型芯高温抗变形能力、以及提高石英玻璃析晶率等作用。 国内常用的矿化剂有氧化铝系、氧化钙系、氧化锆系等几种。 氧化铝系的矿化剂有工业氧化铝、合成莫来石、铝矾土等。加入氧化铝系矿化剂的 — 0,@ —
图!"#
一些典型的陶瓷型芯
因此,熔模铸造型芯是生产复杂熔模铸件所必须的,据介绍,美国熔模铸件中约 $%& ’ (%& 的件使用陶瓷型芯。随着熔模铸造向更精密、更复杂、更大型发展,对熔模 铸造型芯也提出了更高的要求。熔模铸造型芯技术也一直在发展着。
— )($ —
第八章
熔模铸造新型型芯工艺
! ! ! ! ! ! ! ! ! ! ! ! ! ! ! ! ! ! ! ! ! ! ! ! ! ! ! ! ! ! ! ! ! ! ! ! ! ! ! ! ! ! ! ! ! ! ! ! ! ! ! ! 二、对熔模铸造型芯的基本要求 熔模铸造用型芯除与常规铸造一样,受金属液包围,工况条件恶劣外,还需经受脱 蜡和焙烧的作用。为此,型芯应满足下列要求: !" 耐火度高 型芯的耐火度至少应高于合金的浇注温度,以保证在浇注时和铸件凝固过程中不软 化和变形。一般情况下型芯的耐火度应达到 !#$$% 以上,在定向凝固和单晶铸造时, 则要求能承受 !&’$ ( !)$$% 的高温 *$+,- 以上。 ’" 热膨胀率低、尺寸稳定 为保证铸件内腔尺寸精度,型芯的热膨胀率应尽可能小,且无相变,以免造成型芯 开裂或变形。一般来说其线膨胀系数以小于 # . !$ / ) 0 / ! 为宜。 *" 足够的强度 型芯应具有足够的常温强度,以承受压注时蜡液的冲击和挤压而不致断裂或破损。 型芯还要有足够的高温强度,以承受浇注时金属液的冲击力和静压力。 #" 化学稳定性好 型芯在与金属液接触过程中应不污染合金,也不与金属液或金属的氧化物发生化学 反应,以防止铸件表面产生化学粘砂或反应性气孔。 &" 易脱除 铸件铸成后,型芯应便于从铸件中脱除。由于铸件中的陶瓷型芯绝大多数采用化学 腐蚀法溶失,为此,型芯必须有相当大的孔隙率(约 ’$1 ( #$1 ) ,体积密度应比真密 度小。 表 2 / ! 为硅质陶瓷型芯的基本要求,以供参考。
图/2*
石英玻璃的析晶转变及相应的尺寸变化
3)差热曲线 456 7)热膨胀曲线
— 1"8 —
标准分享网 免费下载
第三篇
ห้องสมุดไป่ตู้
铸造模具制造工艺图集与产品造型加工技术
! ! ! ! ! ! ! ! ! ! ! ! ! ! ! ! ! ! ! ! ! ! ! ! ! ! ! ! ! ! ! ! ! ! ! ! ! ! ! ! ! ! ! ! ! ! ! ! ! ! ! ! 析晶产生的体积变化会使陶瓷型芯产生网状裂纹,石英玻璃中方石英析出量越多, 各部分析晶程度越不均匀,产生的裂纹就越多,烧成后的陶瓷型芯的强度也就越低,严 重时甚至型芯会断裂,这是析晶过程对陶瓷型芯的有害影响。另外,石英玻璃的熔融过 程是一个逐渐软化进而熔融的渐进过程,熔融前的软化状态会引起变形,这也可看作是 ・% 即进入变形点。纯净的石英玻璃, 粘度很大的粘性流动。石英玻璃的粘度达到 !"!! #$ 温度达 !&’"( 左右就到变形点。析晶使二氧化硅由玻璃态转变为晶态,对粘性流动有 明显的抑止作用,从而能显著提高型芯的高温抗变形能力。同时析晶的体积膨胀可以抵 消一部分因烧结而引起的收缩(图 ) * &+) 。 为使陶瓷型芯获得足够的强度,必须将成型的型芯坯体加热至高温进行烧结。但陶 瓷型芯与一般陶瓷制品不同,要求有一定孔隙率,强度也不宜过高。否则,不仅不易从 铸件中清除,还会造成铸件热裂。故陶瓷型芯烧结程度要适当,通常只需初步烧结,此 时粉料外廓形状基本保持原状。由石英玻璃制成的型芯坯体,只需加热至 !!""( 以上 就能烧结。 石英玻璃的粒度、杂质含量均影响到析晶、烧结和陶瓷型芯性能。常用的石英玻璃 粒度配比有混合粉和细粉两种(表 ) * ,) ,可根据型芯大小和复杂程度选择。其杂质含 量应严加限制,表 ) * - 为定向凝固铸造用陶瓷型芯的杂质含量限量。
表2/! 性 能 硅质陶瓷型芯的基本要求 用于钴基合金和不锈钢 #"2 ( )"’ $"$# ( $"$2 ’# ( ’)
*
用于真空浇注镍基合金 2"* ( !$"* $"$2 ( $"$; !< ( ’$ !";2 ( ’"$’ ’"*2 ( ’"#&
焙烧后强度 (3456 7*2’ / &2) 8 69: 线膨胀率 (室温 ( ;&$% , 1) 孔隙率 (1) 体积密度( 8 = 8 >+ ) 密度( 8 = 8 >+*) 溶出性 反应性
表)*, 粒度 (筛号) 混合粉 细粉 表)*杂质元素 限量 制芯用石英玻璃粉料的粒度配比(质量分数, .) !-" / &"" 号 &’ — &"" / &0" 号 ’" — 1 &0" 号 &’ !""
定向凝固铸造用陶瓷型芯的杂质限量(质量分数, .) 25、 :;、 <+ "?"""! #+、 <=、 >= "?""-
第八章
熔模铸造新型型芯工艺
! ! ! ! ! ! ! ! ! ! ! ! ! ! ! ! ! ! ! ! ! ! ! ! ! ! ! ! ! ! ! ! ! ! ! ! ! ! ! ! ! ! ! ! ! ! ! ! ! ! ! ! 陶瓷型芯经 !"##$ 烧成后,%&" ’( 仍保持原状。但由于随矿化剂带入的杂质使陶芯的烧 结温度下降,玻璃相含量增多,强度提高。而 %&" ’( 粉粒熔点高而坚硬,它们分散在基 体粉粒间有阻滞其相互滑移的作用,有利于提高高温抗变形能力,并使型芯烧成收缩减 小。需指出的是 %&" ’( ) *+’" 二元系的最低共熔温度为 !,-#$ ,此类型芯长期在 !,,#$ 以上工作,有可能形成液相,使型芯软化变形。但氧化铝系添加物容易获得,故在一般 情况下仍为较常用的添加剂。 氧化钙系矿化剂有 ./’ 和 %.*。%.* 组成的质量分数为 %&" ’(!0123 、 ./’ "(1"(3 、 *+’"4#1#23 ,熔点 !!2#$ 。 ./’ 和 %.* 的作用相近。对烧成后的硅质陶瓷型芯进行物 相鉴定,均发现 ./’ 与 *+’" 固相反应生成的 ./’ ・ ・ *+’" 。由于 ./’ *+’" 的熔点约 !,0#$ , 故此类添加剂也不适用于极限工作温度超过 !,,#$ 的陶瓷型芯。 氧化 锆 矿 化 剂 的 作 用 与 氧 化 铝 类 似。但 56’" ) *+’" 二 元 系 的 最 低 共 熔 温 度 为 !40-$ ,故此类矿化剂的型芯极限工作温度可达 !4,#$ 左右。而且矿化剂加入量不宜过 多,否则矿化剂带入的杂质会使陶瓷型芯高温抗变形能力下降。 此外,特殊矿化剂,如 7" ’( 、 .6" ’( 等氧化物,在高温下能活化 *+ ) ’ 键的网络骨 架,从而显著提高石英玻璃析晶速率。加有此类矿化剂的陶瓷型芯在 !!## 8 !"##$ 下烧 成,析出的方石英量变化不大,但在 !0##$ 以上工作时会迅速大量析出方石英,能有 效地抑制石英玻璃的粘性流动,明显地改善型芯的抗变形能力。 各种矿化剂的用量、使用温度和用途见表 9 ) ,。矿化剂的成分和处理方法见表 9 ) 4。
第三篇
铸造模具制造工艺图集与产品造型加工技术
! ! ! ! ! ! ! ! ! ! ! ! ! ! ! ! ! ! ! ! ! ! ! ! ! ! ! ! ! ! ! ! ! ! ! ! ! ! ! ! ! ! ! ! ! ! ! ! ! ! ! !
第八章
熔模铸造新型型芯工艺
第一节 概 述
一、熔模铸造型芯 一般情况下熔模铸造的内腔是与外形一道通过涂挂涂料、撒砂等工序形成的,不用 专制型芯。但当铸件内腔过于窄小或形状复杂,常规的涂挂涂料、撒砂等工序根本无法 实施,或内腔型壳无法干燥硬化时,就必须使用预制的型芯来形成铸件内腔。这些型芯 要等铸件铸成后再设法去除。例如航空发动机空心涡轮叶片,叶片的冷却通道迂回曲 折,形若迷宫,就必须采用陶瓷型芯。图 ! " # 是一些典型的陶瓷型芯。
第二节
一、硅质陶瓷型芯 () 型芯材料 (()石英玻璃
陶瓷型芯
石英玻璃是硅质陶瓷型芯的基体材料。石英玻璃分透明的和不透明
的两种,前者密度为 *)*(+ , -#" ,后者介于 *)&* . *)&/+ , -#" 之间。石英玻璃是一种过冷 液体,比晶态石英内能高,稳定性差,有自发地向内能更低的晶态转变的趋势。但在常 温下由于它的粘度极大,内部质点很难重新排列。当加热到高温时,石英玻璃的粘度下 降,同时质点热运动动能增大,其内部质点就有可能重新排列,从非晶态转为晶态。一 般透明石英玻璃于 (*&&0 、不透明石英玻璃从 ((&&0 开始转变为方石英,此转变过程 称“析晶” ,同时体积增大。当冷却至 (/& . *1&0 时,方石英又由 !型转变为 "型,同 时体积缩小,见图 / 2 *。