模具验收标准修订稿
模具验收标准

模具验收标准一、模具外观:1铭牌内容是否打印模具编号、模具重量(KG、模具外形尺寸(mm,字符均用1/8英寸的字码打上,字符清晰、排列整齐。
2 铭牌是否固定在模腿上靠近后模板和基准角的地方(离两边各有15mm的距离),用四个柳钉固定,固定可靠,不易剥落。
3 冷却水嘴是否用塑料块插水嘴,C 10管,规格可为G1/8''、G1/4''、G3/8''。
如合同有特殊要求,按合同。
4 冷却水嘴是否伸出模架表面,水嘴头部凹进外表面不超过3mm。
5 冷却水嘴避空孔直径是否为C 25、C 30、C 35mm三种规格,孔外沿有倒角,倒角大于1.5 X 45,倒角一致。
6 冷却水嘴是否有进出标记,进水为IN ,出水为OUT IN、OUT后加顺序号,如IN1、OUT17 标识英文字符和数字是否大写(5/6 ),位置在水嘴正下方10mm处,字迹清晰、美观、整齐、间距均匀。
8 进出油嘴、进出气嘴是否同冷却水嘴,并在IN、OUT前空一个字符加G(气)、0(油)。
9 模具安装方向上的上下侧开设水嘴,是否内置,并开导流槽或下方有支撑柱加以保护。
10 无法内置的油嘴或水嘴下方是否有支撑柱加以保护。
11模架上各模板是否有基准角符号,大写英文DATUM字高5/16 〃,位置在离边10mm处,字迹清晰、美观、整齐、间距均匀。
12 各模板是否有零件编号,编号在基准角符号正下方离底面10mm处,要求同11号。
13 模具配件是否影响模具的吊装和存放, 如安装时下方有外漏的油缸、水嘴、预复位机构等,应有支撑腿保护。
14 支撑腿的安装是否用螺丝穿过支撑腿固定在模架上,或过长的支撑腿车加工外螺纹紧固在模架上。
15 模具顶出孔是否符合指定的注塑机, 除小型模具外, 原则上不能只用一个中心顶出(模具长度或宽度尺寸有一个大于500mm时),顶出孔直径应比顶出杆大5-10mm16 定位圈是否可靠固定(一般用三个M6或M8的内六角螺丝),直径一般为C 100或C 150mm高出顶板10mm如合同有特殊要求,按全同。
模具质量验收标准(附件二、三)
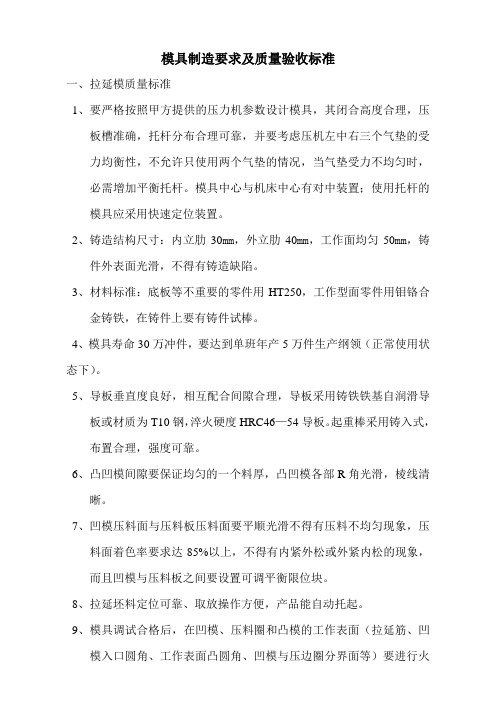
模具制造要求及质量验收标准一、拉延模质量标准1、要严格按照甲方提供的压力机参数设计模具,其闭合高度合理,压板槽准确,托杆分布合理可靠,并要考虑压机左中右三个气垫的受力均衡性,不允许只使用两个气垫的情况,当气垫受力不均匀时,必需增加平衡托杆。
模具中心与机床中心有对中装置;使用托杆的模具应采用快速定位装置。
2、铸造结构尺寸:内立肋30mm,外立肋40mm,工作面均匀50mm,铸件外表面光滑,不得有铸造缺陷。
3、材料标准:底板等不重要的零件用HT250,工作型面零件用钼铬合金铸铁,在铸件上要有铸件试棒。
4、模具寿命30万冲件,要达到单班年产5万件生产纲领(正常使用状态下)。
5、导板垂直度良好,相互配合间隙合理,导板采用铸铁铁基自润滑导板或材质为T10钢,淬火硬度HRC46—54导板。
起重棒采用铸入式,布置合理,强度可靠。
6、凸凹模间隙要保证均匀的一个料厚,凸凹模各部R角光滑,棱线清晰。
7、凹模压料面与压料板压料面要平顺光滑不得有压料不均匀现象,压料面着色率要求达85%以上,不得有内紧外松或外紧内松的现象,而且凹模与压料板之间要设置可调平衡限位块。
8、拉延坯料定位可靠、取放操作方便,产品能自动托起。
9、模具调试合格后,在凹模、压料圈和凸模的工作表面(拉延筋、凹模入口圆角、工作表面凸圆角、凹模与压边圈分界面等)要进行火焰淬火,淬火硬度HRC43-48。
10、拉延筋布置合理,保证板材在拉伸过程中得到充足的塑性变形。
11、拉延模应有行程到底标记销(在拉延件切去部份或非重要表面)。
12、用图纸规定的坯料试冲,不得随意改变坯料的规格型号,如有改变需经甲方同意。
二、成形翻边模的质量标准1、严格按着甲方提供的压力机参数设计模具,压板槽准确;当需要使用托杆时,托杆分布合理可靠,并要考虑压机左中右三个气垫的受力均衡性,不允许只使用两个气垫的情况,当气垫受力不均匀时,必需增加平衡托杆。
模具中心与机床中心有对中装置;使用托杆的模具应采用快速定位装置。
注塑模(塑料模)模具验收标准
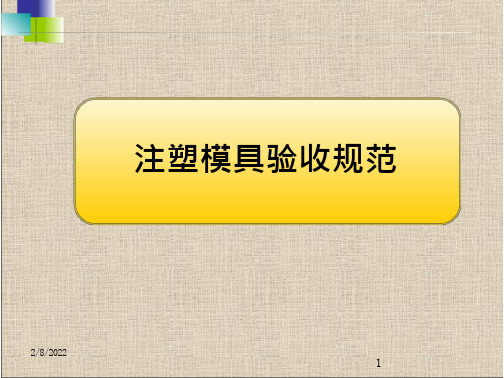
同意烧焊的除外,需注明指出) 6. 流道与入水位必须抛光,不能有作何的刀纹及火花纹。 7. 分模面流道需有排气,是否有? 8. 导套需有排气,是否有?
1
验收检查表
e) 一般CORE面需省光,无明显火花纹及加工刀痕,特殊要求的除
外。
f) 透明胶件或装配后的外观面符合设计要求。
1
注塑成型工艺
1. 模具在一定的注塑工艺条件范围内,应具有啤作的稳定性和工艺参 数调校的可重复性。
2. 模具啤作时注射压力,一般不应超过注塑机额定最大注射压力的 85%。
3. 模具啤作时的注射速度,其四分之三行程的注射速度不低于额定最 大注射速度的10%或超过额定最大注射速度的90%。
b) 顶针机构应保证灵活、可靠、不发生错误动作。 c) 顶针、司筒顶面非平面时,顶针、司筒应定位。
8. 底板上应均匀设置垃圾钉,垃圾钉高度应一致。
1
• 模具应具备结构
9. 4545或以上级大模应加设中托边,一套模中司筒数量达 到或超过16支应增设中托边。
10.流道直径、长度加工应合理,在保证成形质量的前提下 尽量缩短流程,减少断面积以缩短填充及冷却时间,同 时浇注系统损耗的塑料应最少。流道一般应设置冷料井 。
符合要求的标准尺寸? 9. 各顶针、司筒、顶块、斜顶及B板上等是否有打印有装配
对应序号?
1
验收检查表
16.防水“O”形槽及胶圈尺寸是否符合要求? 17防水胶圈尺寸是否正确?有无破损等不良现象? 18水路经过压力测试,是否漏水? 19所有的镙丝头都低于模板面 20所有的螺丝不可以有过加工、切短、等现象。 21模板需打上编号及模号,是否已加工好? 22带热嘴的必须要有接线盒,是否已好? 23水路必须有“IN”“OUT”标识,是否已标? 24所有超过50LBS(约20KG)的配件、模板都需有吊装孔 ,是否有? 25模具上所有的吊模孔需打印上螺纹大小标识,是否已 打印?
模具验收准则
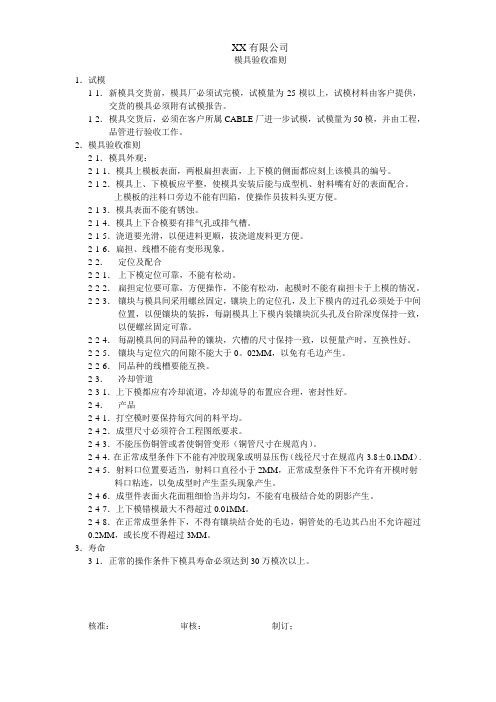
XX有限公司模具验收准则1.试模1-1.新模具交货前,模具厂必须试完模,试模量为25模以上,试模材料由客户提供,交货的模具必须附有试模报告。
1-2.模具交货后,必须在客户所属CABLE厂进一步试模,试模量为50模,并由工程,品管进行验收工作。
2.模具验收准则2-1.模具外观:2-1-1.模具上模板表面,两根扁担表面,上下模的侧面都应刻上该模具的编号。
2-1-2.模具上、下模板应平整,使模具安装后能与成型机、射料嘴有好的表面配合。
上模板的注料口旁边不能有凹陷,使操作员拔料头更方便。
2-1-3.模具表面不能有锈蚀。
2-1-4.模具上下合模要有排气孔或排气槽。
2-1-5.浇道要光滑,以便进料更顺,拔浇道废料更方便。
2-1-6.扁担、线槽不能有变形现象。
2-2.定位及配合2-2-1.上下模定位可靠,不能有松动。
2-2-2.扁担定位要可靠,方便操作,不能有松动,起模时不能有扁担卡于上模的情况。
2-2-3.镶块与模具间采用螺丝固定,镶块上的定位孔,及上下模内的过孔必须处于中间位置,以便镶块的装拆,每副模具上下模内装镶块沉头孔及台阶深度保持一致,以便螺丝固定可靠。
2-2-4.每副模具间的同品种的镶块,穴槽的尺寸保持一致,以便量产时,互换性好。
2-2-5.镶块与定位穴的间隙不能大于0。
02MM,以免有毛边产生。
2-2-6.同品种的线槽要能互换。
2-3.冷却管道2-3-1.上下模都应有冷却流道,冷却流导的布置应合理,密封性好。
2-4.产品2-4-1.打空模时要保持每穴间的料平均。
2-4-2.成型尺寸必须符合工程图纸要求。
2-4-3.不能压伤铜管或者使铜管变形(铜管尺寸在规范内)。
2-4-4.在正常成型条件下不能有冲胶现象或明显压伤(线径尺寸在规范内3.8±0.1MM).2-4-5.射料口位置要适当,射料口直径小于2MM,正常成型条件下不允许有开模时射料口粘连,以免成型时产生歪头现象产生。
2-4-6.成型件表面火花面粗细恰当并均匀,不能有电极结合处的阴影产生。
模具验收标准
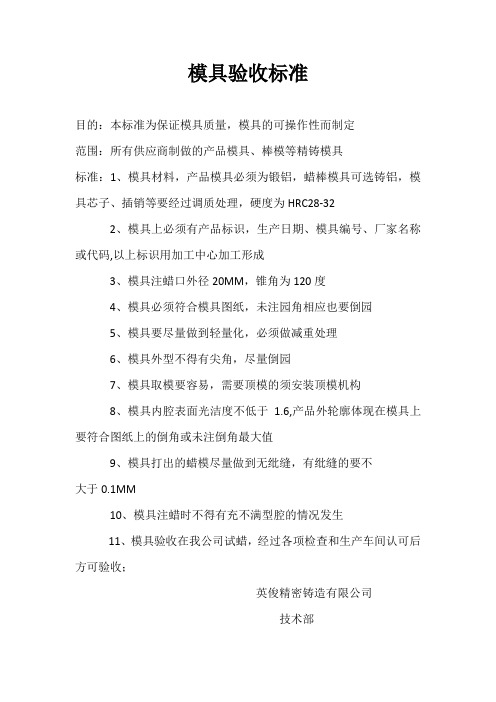
模具验收标准
目的:本标准为保证模具质量,模具的可操作性而制定
范围:所有供应商制做的产品模具、棒模等精铸模具
标准:1、模具材料,产品模具必须为锻铝,蜡棒模具可选铸铝,模具芯子、插销等要经过调质处理,硬度为HRC28-32
2、模具上必须有产品标识,生产日期、模具编号、厂家名称或代码,以上标识用加工中心加工形成
3、模具注蜡口外径20MM,锥角为120度
4、模具必须符合模具图纸,未注园角相应也要倒园
5、模具要尽量做到轻量化,必须做减重处理
6、模具外型不得有尖角,尽量倒园
7、模具取模要容易,需要顶模的须安装顶模机构
8、模具内腔表面光洁度不低于1.6,产品外轮廓体现在模具上要符合图纸上的倒角或未注倒角最大值
9、模具打出的蜡模尽量做到无纰缝,有纰缝的要不
大于0.1MM
10、模具注蜡时不得有充不满型腔的情况发生
11、模具验收在我公司试蜡,经过各项检查和生产车间认可后方可验收;
英俊精密铸造有限公司
技术部。
模具制作的验收标准

模具制作的验收标准集团标准化办公室:[VV986T-J682P28-JP266L8-68PNN]模具制作的验收标准产品要求:尺寸必须符合图纸要求。
塑件产品外观必须符合图纸要求或封样样品要求。
注塑产品不能出现冷料、气雾、缺料、收缩、溢料飞边、熔接痕、变形翘曲、顶白、斑痕、浇口雾斑等其它表观缺陷。
产品光面不能有划痕、细微麻点、波纹、桔皮纹。
产品砂面要求无砂眼、凹坑,纹理、疏密度应均匀一致。
产品内外表面棱角分明、工整一致。
产品上的字必须符合图纸所要求的字迹大小和深度,字迹必须清晰、棱角分明、工整一致、凹字底部平整光亮。
面板、面架熔接痕长度要小于5mm,盖板、基座、小件光面的产品(如按纽)不应有熔接痕,内件产品允许有不能避免的模具设计与注塑工艺上的熔接痕。
浇口去除后留下的痕迹不应影响产品的品质。
潜伏浇口处产品不应该有拉伤。
产品通过验收后,要对模具进行验收。
包括模具结构设计、外观、结构件、零件的加工精度、镶拼方式、材料、热处理手段等等。
模具外观检查:1观察模板机械加工质量,模板平直,上下端面状况,外形尺寸整齐,周边2×450倒角,外观要给人感觉良好。
60万模次以下生产的模具可按龙记模架的标准来自制模架或按龙记模架制作的其他标准模架;60万模次(含60万)以上生产用龙记标准模架。
注意:公司如无另外要求,二板模要用CI型模架,三板模要用DCI型模架,A、B板不能挖通框,B模与动模座板之间加设支承柱。
2模具起吊方向上要装吊环,可一次性将模具平衡吊起。
大中型模具在动定模之间要装有锁紧装置,防止模具起吊时开启。
3冷却水的进出口位置应在注塑工操作的另一侧,其次是在注塑生产时在模具的下方。
热流道模具要配有接线板,并固定在模具上,传感器、加热元件电线通过快换插头迅速安装,要尽量简化安装。
电线导出后要用管子套上,防止散乱。
4模具及型腔的编号的要求按《模具编号的说明》及《模具型腔编号的说明》。
5模板的尺寸请按《模具制作的模板要求》。
模具验收标准

模具验收标准一、前言。
模具是制造工业中非常重要的一种生产工具,它的质量直接关系到产品的成型质量和生产效率。
因此,模具的验收是非常重要的环节,只有通过严格的验收,才能确保模具的质量达到要求,从而保证产品的质量和生产效率。
本文将介绍模具验收的标准和要求。
二、验收标准。
1. 外观质量。
(1)模具表面应无刮痕、裂纹、气泡、凹凸不平等缺陷,应保持清洁光滑。
(2)模具的尺寸应符合设计要求,无变形、偏差等情况。
(3)模具的各部件应安装牢固,无松动、脱落等现象。
2. 加工精度。
(1)模具的加工精度应符合设计要求,各零件之间的配合间隙应符合标准。
(2)模具的表面粗糙度应符合要求,不得影响产品的表面质量。
3. 使用性能。
(1)模具应能够正常使用,无卡滞、卡死、卡模等现象。
(2)模具的使用寿命应符合设计要求,能够满足生产需求。
4. 安全性能。
(1)模具应符合安全生产的要求,无锋利边缘、突出物等危险因素。
(2)模具的使用应符合相关安全操作规程,能够保障操作人员的安全。
5. 其他要求。
(1)模具的材料应符合设计要求,无掺杂、夹杂等缺陷。
(2)模具的标识应清晰完整,包括生产厂家、生产日期、型号等信息。
三、验收流程。
1. 准备工作。
(1)准备验收所需的工具和设备,包括千分尺、游标卡尺、平行度尺等。
(2)准备验收所需的文件和资料,包括设计图纸、加工工艺文件等。
2. 验收过程。
(1)对模具的外观进行检查,包括表面质量、尺寸等。
(2)对模具的加工精度进行检测,包括尺寸、配合间隙等。
(3)对模具的使用性能进行测试,包括装卸模具、模具运行测试等。
(4)对模具的安全性能进行评估,包括危险因素、安全操作规程等。
(5)对模具的材料和标识进行检查,确保符合要求。
3. 验收结论。
(1)根据验收结果,对模具的质量进行评定,包括合格、不合格等结论。
(2)对不合格的模具,提出整改要求和建议,确保模具质量达标。
四、总结。
模具验收是保证模具质量的重要环节,只有严格按照验收标准进行检验,才能确保模具的质量和使用效果。
模具验收标准
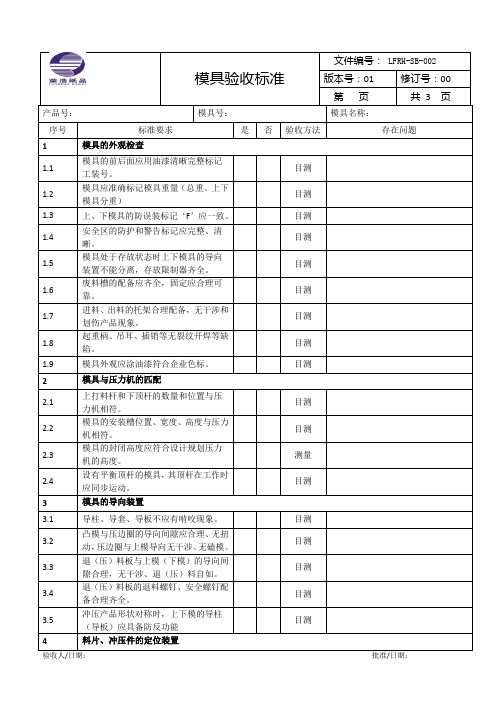
模具验收标准版本号:01 修订号:00第页共3 页产品号:模具号:模具名称:序号标准要求是否验收方法存在问题1 模具的外观检查1.1 模具的前后面应用油漆清晰完整标记工装号。
目测1.2 模具应准确标记模具重量(总重、上下模具分重)目测1.3 上、下模具的防误装标记‘F’应一致。
目测1.4 安全区的防护和警告标记应完整、清晰。
目测1.5 模具处于存放状态时上下模具的导向装置不能分离,存放限制器齐全。
目测1.6 废料槽的配备应齐全,固定应合理可靠。
目测1.7 进料、出料的托架合理配备,无干涉和划伤产品现象。
目测1.8 起重柄、吊耳、插销等无裂纹开焊等缺陷。
目测1.9 模具外观应涂油漆符合企业色标。
目测2 模具与压力机的匹配2.1 上打料杆和下顶杆的数量和位置与压力机相符。
目测2.2 模具的安装槽位置、宽度、高度与压力机相符。
目测2.3 模具的封闭高度应符合设计规划压力机的高度。
测量2.4 设有平衡顶杆的模具,其顶杆在工作时应同步运动。
目测3 模具的导向装置3.1 导柱、导套、导板不应有啃咬现象。
目测3.2 凸模与压边圈的导向间隙应合理、无扭动,压边圈与上模导向无干涉、无磕模。
目测3.3 退(压)料板与上模(下模)的导向间隙合理,无干涉、退(压)料自如。
目测3.4 退(压)料板的退料螺钉、安全螺钉配备合理齐全。
目测3.5 冲压产品形状对称时,上下模的导柱(导板)应具备防反功能目测4 料片、冲压件的定位装置模具验收标准版本号:01 修订号:00第页共3 页4.1 定位装置应可靠,与模具其它部位无干涉。
目测4.2 定位装置布置合理,能够实现所要求自由度的控制。
目测4.3 采用模腔定位时,冲压件与模腔间隙合理,应保证定位一致性。
目测5 退料装置5.1 退(压)料装置型面与冲压件型面相符,无损制件。
目测5.2 退(压)料装置能够充分实现退压料功能,无损制件。
目测5.3 退(压)料装置上、下运动平稳,重心不偏移。
新开模具要求与验收标准
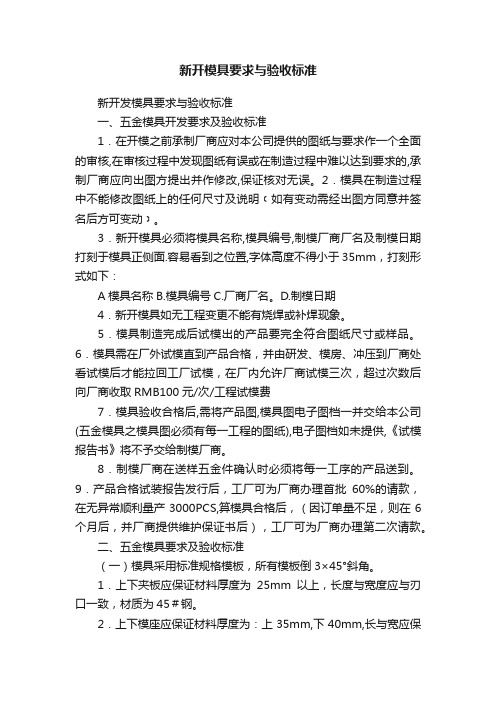
新开模具要求与验收标准新开发模具要求与验收标准一、五金模具开发要求及验收标准1.在开模之前承制厂商应对本公司提供的图纸与要求作一个全面的审核,在审核过程中发现图纸有误或在制造过程中难以达到要求的,承制厂商应向出图方提出并作修改,保证核对无误。
2.模具在制造过程中不能修改图纸上的任何尺寸及说明﹝如有变动需经出图方同意并签名后方可变动﹞。
3.新开模具必须将模具名称,模具编号,制模厂商厂名及制模日期打刻于模具正侧面.容易看到之位置,字体高度不得小于35mm,打刻形式如下:A模具名称B.模具编号C.厂商厂名。
D.制模日期4.新开模具如无工程变更不能有烧焊或补焊现象。
5.模具制造完成后试模出的产品要完全符合图纸尺寸或样品。
6.模具需在厂外试模直到产品合格,并由研发、模房、冲压到厂商处看试模后才能拉回工厂试模,在厂内允许厂商试模三次,超过次数后向厂商收取RMB100元/次/工程试模费7.模具验收合格后,需将产品图,模具图电子图档一并交给本公司(五金模具之模具图必须有每一工程的图纸),电子图档如未提供,《试模报告书》将不予交给制模厂商。
8.制模厂商在送样五金件确认时必须将每一工序的产品送到。
9.产品合格试装报告发行后,工厂可为厂商办理首批60%的请款,在无异常顺利量产3000PCS,算模具合格后,(因订单量不足,则在6个月后,并厂商提供维护保证书后),工厂可为厂商办理第二次请款。
二、五金模具要求及验收标准(一)模具采用标准规格模板,所有模板倒3×45°斜角。
1.上下夹板应保证材料厚度为25mm以上,长度与宽度应与刃口一致,材质为45#钢。
2.上下模座应保证材料厚度为:上35mm,下40mm,长与宽应保证相对之位置,异柱不能靠刀口板太近(最小距离为:15mm)3.刀口模板厚度为30mm以上,长度与宽度保证与刃口最近距离50mm,材质SKD11,热处理硬度58~60HRC。
4.下料及冲孔模上下模板必须采用SKD11,折弯冲头可采用D2,冲头热处理比下模低2~3HRC,为56~58HRC。
模具验收标准
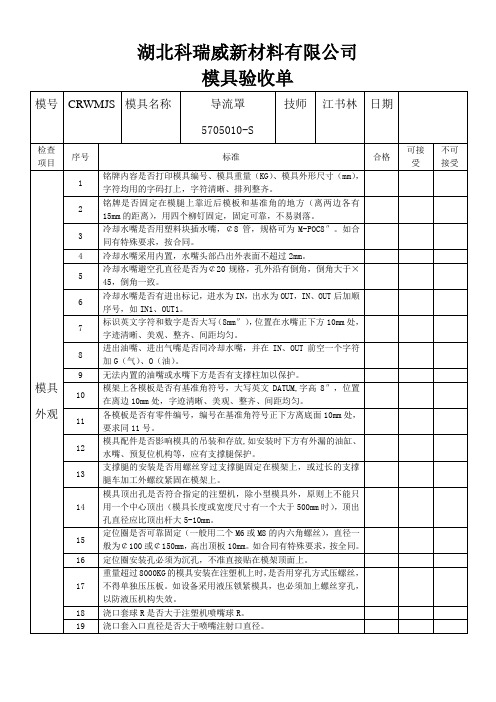
透明制品冷料穴的直径、深度是否符合设计标准。
17
料把是否易于去除,制品外观面无浇口痕迹,制品有装配处无残余料把。
18
弯钩潜伏式浇口,两部分镶块是否进行氮化处理,硬度HRC55。
热流道系统
1
热流道接线布局是否合理,易于检修,接线有线号并一一对应。
2
是否进行安全测试,以免发生漏电等安全事故。
3
温控柜及热喷咀、集流板是否符合客户要求。
10
点浇口浇口处是否按浇口规范加工。
检验项目
序号
标准
合格
可接受
不可接受
一般浇注系统(不含热流道)
11
点浇口处前模有一小凸起,后模相应有一凹坑。
12
分流道前端是否有一段延长部分作为冷料穴。
13
拉料杆Z形倒扣是Biblioteka 圆滑过渡。14分型面上的分流道是否表面为圆形,前后模无错位。
15
出在顶杆上的潜伏式浇口是否存在表面收缩,厚度不能大于胶位2/3。
检验项目
序号
标准
合格
可接受
不可接受
热流道系统
21
控制线是否有护套,无损坏,一般为电缆线。
22
温控柜结构是否可靠,螺丝无松动。
23
插座安装在电木板上,是否超出模板最大尺寸。
24
5
球头拉料杆是否可靠固定,可以压在定位圈下面,可以用无头螺丝固定,也可以用压板压住。
6
顶板和水口板间是否有10-12mm左右开距。
7
水口板和前模板之间的开距是否适于取料把,一般情况下,开距=料把长度+5~10,且大于120mm以上。
8
三板模前模板限位是否用限位拉杆。
9
浇口、流道是否按图纸尺寸用机床(CNC、铣床、EDM)加工,不允许手工甩打磨机加工。
模具验收标准
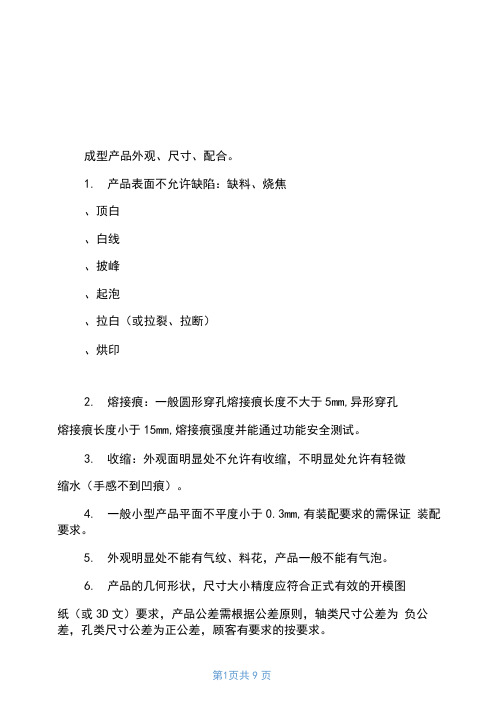
16. 固定在顶杆上的顶块,应牢固可靠,四周非成型部分应 加工 3° ~5°的斜度,下部周边应倒角。
17. 模架上的油路孔内应无铁屑杂物。 18. 回程杆端面平整,无点焊。胚头底部无垫片,点焊。 19. 三板模浇口板导向滑动顺利,浇口板易拉开。 20. 三板模限位拉杆应布置在模具安装方向的两侧,或在模 架外加拉板,防止限位拉杆与操作工干涉。 21. 油路气道应顺畅,液压顶出复位应到位。 22. 导套底部应开制排气口。 23. 定位销安装不能有间隙。 五. 冷却加热系统。 1. 冷却或加热系统应充分畅通。 2. 密封应可靠,系统在 0. 5MPa 压力下不得有渗漏现象,易 于检修。 3. 开设在模架上的密封槽的尺寸和形状应符合相关标准要 求。 4. 密封圈安放时应涂抹黄油,安放后高出模架面。 5. 水、油流道隔片应釆用不易受腐蚀的材料。 6. 前后模应采用集中送水、方式。 六. 浇注系统。
成型产品外观、尺寸、配合。 1. 产品表面不允许缺陷:缺料、烧焦 、顶白 、白线 、披峰 、起泡 、拉白(或拉裂、拉断) 、烘印
2. 熔接痕:一般圆形穿孔熔接痕长度不大于 5mm,异形穿孔 熔接痕长度小于 15mm,熔接痕强度并能通过功能安全测试。
3. 收缩:外观面明显处不允许有收缩,不明显处允许有轻微 缩水(手感不到凹痕)。
14. 模架表面不应有凹坑、锈迹、多余的吊环、进出水汽、 油孔等以及影响外观的缺陷。
15. 模具应便于吊装、运输,吊装时不得拆卸模具零部,吊 环不得与水嘴、油缸、预复位杆等干涉。
三. 模具材料和硬度。 1. 模具模架应选用符合标准的标准模架。 2. 模具成型零和浇注系统(型芯、动定模镶块、活动镶块、 分流锥、推杆、浇口套)材料采用性能高于 40Cr 以上的材料。 3. 成型对模具易腐蚀的塑料时,成型零应采用耐腐蚀材料制 作,或其成型面应采取防腐蚀措施。 4. 模具成型零硬度应不低于 50HRC,或表面硬化处理硬度应 高于 eOOHVo 四. 顶出、复位、抽插芯、取。 1. 顶岀时应顺畅、无卡滞、无异常声响。
模具验收标准及相关标准文件
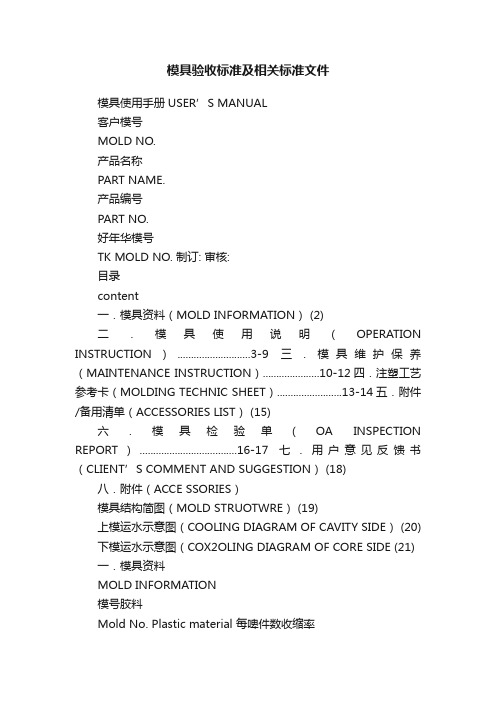
模具验收标准及相关标准文件模具使用手册USER’S MANUAL客户模号MOLD NO.产品名称PART NAME.产品编号PART NO.好年华模号TK MOLD NO. 制订: 审核:目录content一.模具资料(MOLD INFORMATION) (2)二.模具使用说明(OPERATION INSTRUCTION)...........................3-9 三.模具维护保养(MAINTENANCE INSTRUCTION).....................10-12四.注塑工艺参考卡(MOLDING TECHNIC SHEET)........................13-14五.附件/备用清单(ACCESSORIES LIST) (15)六.模具检验单(OA INSPECTION REPORT)....................................16-17七.用户意见反馈书(CLIENT’S COMMENT AND SUGGESTION) (18)八.附件(ACCE SSORIES)模具结构简图(MOLD STRUOTWRE) (19)上模运水示意图(COOLING DIAGRAM OF CAVITY SIDE) (20) 下模运水示意图(COX2OLING DIAGRAM OF CORE SIDE (21) 一.模具资料MOLD INFORMATION模号胶料Mold No. Plastic material 每啤件数收缩率Number of cavity shrinkage:每啤重量:上模钢材:Shot weight cavity steel 水口流道重量:下模钢材Runner and sprue weight core steel 模具尺寸:mold dimension:Width mm x Height mm x thickness mm.模具重量 mold weight : kg最少开模行程minimum daynight:mm顶针板行程ejector stroke:mm唧嘴偏左/偏右/中心sprue offset:mm法兰直径Locating ring’s diameter:?mm 高度height:mm 唧嘴球面半径和孔径Sprue bushing:SPHR mm & mm码模Mold mounting method:凸边宽度Flange width mm坑深Clamping Slot depth/ mm x高height / mm丝孔Screw holes?x 中心距distance between centers.mm吊模孔喉嘴配机型Eyebolt:Water connection:Suitable machine size:二.模具使用说明THE OPERATION OF MOLD 1.注塑机要求Injection Machine Spec注塑机Injection Machine机型(Type of Machine)HNH啤机: 客户啤机:法兰直径Locateing Ring Diaφmm唧咀Sprue SR 唧咀孔sprueφSRφmm炮咀伸入量Nozzle Movement Distancemm顶棍孔直径Ejector Hole Diaφmm顶出行程Ejector strokemm2. 模具的结构特点MOLD STRUCTURE流道类型Runner Method□冷流道Cold □热流道Hot热流道品牌Hot trademark□DME □YUDO □MoldMaster□HASCO 其它other:___________手册内容二.模具使用说明THE OPERATION OF MOLD水口类型Gate Method□直接入水Direct□潜水Submarine gate□针点Pin point□侧水Edge gate□封针Valve Gate□细水转侧Pin point transfer side gate模具类型Type of mold base□二板模2 plate (□倒装Reverse )□三板模3 plate模胚/钢材Mold Base/Material上模板Cavity plate:__ _________下模板Core plate:_____ _______模胚品牌Mold Base trademark□LKM □其他other_______钢材/ 硬度Material / Hardness上模Cavity :___48__ __/____52_____HRC 下模Core :___48__ /___52___HRC镶件Insert:____50__ __52___HRC行位Slide :_____________HRC手册内容二.模具使用说明THE OPERATION OF MOLD 倒扣处理Under-cut Treatment □斜边Angle pin□气/油压Air / oil□弹前模FloatinCAV.□斜顶Cam顶出Ejector□圆顶针Ejector pin□扁顶针Blade ejector□司简Sleeve ejector□斜顶Lifter□直顶Straight Lifter□推方Stripper bar□推板Stripper plate□推圈Stripper ring□推板Stripper plate□气拍Air valve取产品方法Products Ejection□自动落下Gravity Drop□手取Manual□机械手Automatic Eject取水口方法Runner Ejection□自动落下Gravity Drop□手取Manual□机械手Automatic Eject手册内容二.模具使用说明THE OPERATION OF MOLD 运水Cooling□水Water□温水Hot Water□油Hot oil喉牙Thread standard英制BSP____yes____美制NPT________顶针板复位方式Return Method□弹簧Spring□剑仔Early Ejector□油压Hydraulic□强制Compel手册内容二.模具使用说明THE OPERATION OF MOLD 3.模具的动作要点Mold action sequenceA. 开模;Mold openingB. 油唧抽CAVITY (上模) ;Slide Extracted by Hydraulic Cylinder(Cavity)C. 油唧抽哥CORE(下模);Slide Extracted by Hydraulic Cylinder (Core)D. 油唧回CAVITY (上模);Slide Returned by Hydraulic Cylinder (Cavity)E. 油唧回CORE (下模);Slide Returns by Hydraulic Cylinder (Core)F. 顶出(顶针顶出);Ejection (Ejector Pin)G. 顶针回;Ejector Pin Return动作先后顺序sequeneJ→K→M→A→F→L→G→J H. 热咀封针打开;Hot Drop Valve Pin OpeningI. 热咀封针关闭;Hot Drop Valve Pin ClosingJ. 合模mold closingK. 射胶;InjectionM. 冷却;CoolingN. 入气;Gas InjectionL. 取件.taking part二.模具使用说明THE OPERATION OF MOLD开模动作注意mold opening notice:1、□前模行位(油唧,气缸)需抽开到位后,才能开模;The cavity slide opened prior to the mold open;2、□前模()组行位,有动作先后次序的要求:先()抽开,后()抽开;最后()抽开;( )Cavity slides’action order: the first ( )open, then( )open; a last( )open;3、□此模分()次开模;开模次序见模具结构简图;mold opening sequence shown in the drawing of mold structure。
模具检查验收标准-1
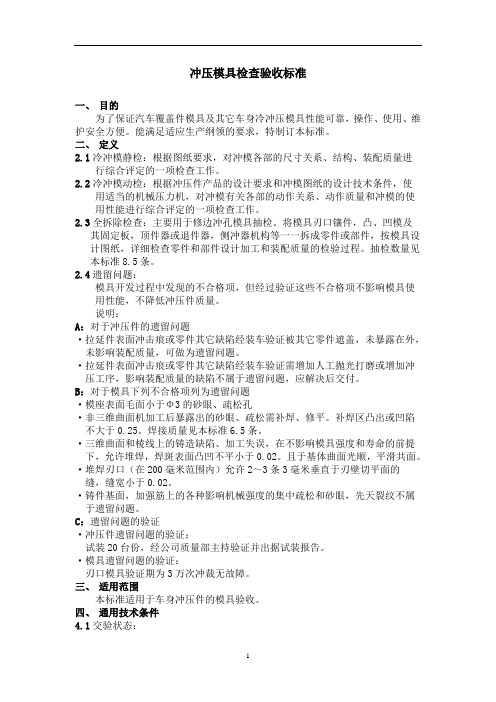
冲压模具检查验收标准一、目的为了保证汽车覆盖件模具及其它车身冷冲压模具性能可靠,操作、使用、维护安全方便。
能满足适应生产纲领的要求,特制订本标准。
二、定义2.1冷冲模静检:根据图纸要求,对冲模各部的尺寸关系、结构、装配质量进行综合评定的一项检查工作。
2.2冷冲模动检:根据冲压件产品的设计要求和冲模图纸的设计技术条件,使用适当的机械压力机,对冲模有关各部的动作关系、动作质量和冲模的使用性能进行综合评定的一项检查工作。
2.3全拆除检查:主要用于修边冲孔模具抽检。
将模具刃口镶件,凸、凹模及其固定板,顶件器或退件器,侧冲器机构等一一拆成零件或部件,按模具设计图纸,详细检查零件和部件设计加工和装配质量的检验过程。
抽检数量见本标准8.5条。
2.4遗留问题:模具开发过程中发现的不合格项,但经过验证这些不合格项不影响模具使用性能,不降低冲压件质量。
说明:A:对于冲压件的遗留问题·拉延件表面冲击痕或零件其它缺陷经装车验证被其它零件遮盖,未暴露在外,未影响装配质量,可做为遗留问题。
·拉延件表面冲击痕或零件其它缺陷经装车验证需增加人工抛光打磨或增加冲压工序,影响装配质量的缺陷不属于遗留问题,应解决后交付。
B:对于模具下列不合格项列为遗留问题·模座表面毛面小于Φ3的砂眼、疏松孔·非三维曲面机加工后暴露出的砂眼、疏松需补焊、修平。
补焊区凸出或凹陷不大于0.25。
焊接质量见本标准6.5条。
·三维曲面和棱线上的铸造缺陷、加工失误,在不影响模具强度和寿命的前提下,允许堆焊,焊斑表面凸凹不平小于0.02。
且于基体曲面光顺,平滑共面。
·堆焊刃口(在200毫米范围内)允许2~3条3毫米垂直于刃壁切平面的缝,缝宽小于0.02。
·铸件基面,加强筋上的各种影响机械强度的集中疏松和砂眼,先天裂纹不属于遗留问题。
C:遗留问题的验证·冲压件遗留问题的验证:试装20台份,经公司质量部主持验证并出据试装报告。
模具验收标准指导书(新版)
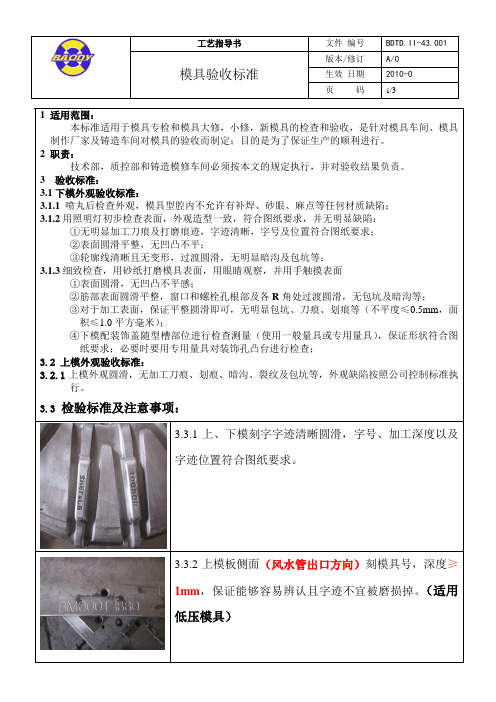
页码1/31 适用范围:本标准适用于模具专检和模具大修,小修,新模具的检查和验收,是针对模具车间、模具制作厂家及铸造车间对模具的验收而制定;目的是为了保证生产的顺利进行。
2 职责:技术部,质控部和铸造模修车间必须按本文的规定执行,并对验收结果负责。
3 验收标准:3.1下模外观验收标准:3.1.1 喷丸后检查外观,模具型腔内不允许有补焊、砂眼、麻点等任何材质缺陷;3.1.2用照明灯初步检查表面,外观造型一致,符合图纸要求,并无明显缺陷:①无明显加工刀痕及打磨痕迹,字迹清晰,字号及位置符合图纸要求;②表面圆滑平整,无凹凸不平;③轮廓线清晰且无变形,过渡圆滑,无明显暗沟及包坑等;3.1.3细致检查,用砂纸打磨模具表面,用眼睛观察,并用手触摸表面①表面圆滑,无凹凸不平感;②筋部表面圆滑平整,窗口和螺栓孔根部及各R角处过渡圆滑,无包坑及暗沟等;③对于加工表面,保证平整圆滑即可,无明显包坑、刀痕、划痕等(不平度≤0.5mm,面积≤1.0平方毫米);④下模配装饰盖随型槽部位进行检查测量(使用一般量具或专用量具),保证形状符合图纸要求;必要时要用专用量具对装饰孔凸台进行检查;3.2 上模外观验收标准:3.2.1上模外观圆滑,无加工刀痕、划痕、暗沟、裂纹及包坑等,外观缺陷按照公司控制标准执行。
3.3检验标准及注意事项:3.3.1上、下模刻字字迹清晰圆滑,字号、加工深度以及字迹位置符合图纸要求。
3.3.2上模板侧面(风水管出口方向)刻模具号,深度≥1mm,保证能够容易辨认且字迹不宜被磨损掉。
(适用低压模具)页码2/33.3.3顶杆板上表面(风水管出口方向)刻模具号,深度≥1mm,保证能够容易辨认且字迹不宜被磨损掉(如图所示)(适用低压模具)3.3.4顶杆压板(风水管接头两侧)上表面,均刻模具号,深度≥1mm,保证能够容易辨认且字迹不宜被磨损掉(如图所示)(适用低压模具)3.3.5上模如图位置刻模具号,深度≥1m m,以便于模具拆装时模具型号确认(如图)。
压铸模具验收标准
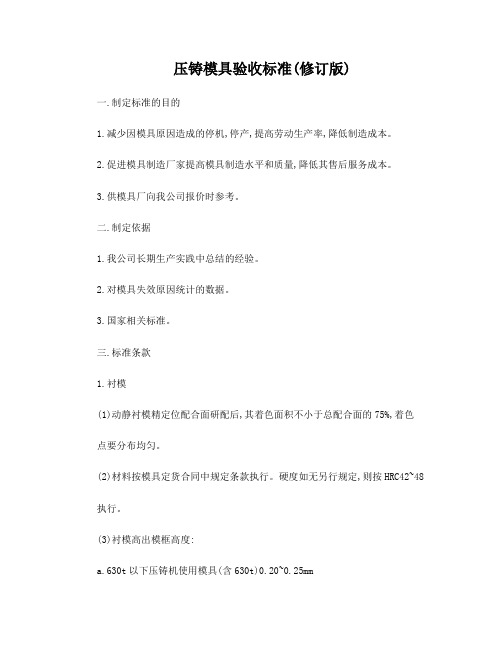
压铸模具验收标准(修订版)一.制定标准的目的1.减少因模具原因造成的停机,停产,提高劳动生产率,降低制造成本。
2.促进模具制造厂家提高模具制造水平和质量,降低其售后服务成本。
3.供模具厂向我公司报价时参考。
二.制定依据1.我公司长期生产实践中总结的经验。
2.对模具失效原因统计的数据。
3.国家相关标准。
三.标准条款1.衬模(1)动静衬模精定位配合面研配后,其着色面积不小于总配合面的75%,着色点要分布均匀。
(2)材料按模具定货合同中规定条款执行。
硬度如无另行规定,则按HRC42~48 执行。
(3)衬模高出模框高度:a.630t以下压铸机使用模具(含630t)0.20~0.25mmb.630t以上压铸机模具0.25~0.35mmc.满足上述条件前提是衬模装配模框后,其底面应与模框对应配合面全接触。
(4)衬模顶杆孔配合段长度L及孔径:a.Ф6以下顶杆(含Ф6)L ≧20mmb.Ф8~Ф12(含Ф12)L = 30~35mmc.Ф12以上L ≧50mm(5)配合段孔径精度:H7(6) 衬模封铝面长度La. 630t(含630t)以下L ≧55mmb. 630t~1600t L ≧80mmc. 2000t(含2000t)以上L ≧120mm(7) 衬模分型面研配精度分型面研配后任一30*30mm区域内,至少有一点接触2.模框(1) 硬度: HRC28~35(2) 要留有拆除衬模用工艺孔,孔径为:a. 630t(含630t)以下模具φ20~φ30mmb.900t φ30~φ40mmc.1600t(含1600t)以上≧φ50mm3.成型滑块材料和硬度同衬模.4.压板,滑板,导板(1) 材料: T10/H13(2) 硬度: T10 HRC50~55, H13 HRC46-48(3) 采用H13钢时,热处理为:整体淬火+表面氮化5. 滑块座(1) 材料: H13(2) 硬度: HRC40~44(3) 滑块座长度尺寸至少是宽度的1.5倍。
模具验收标准

模具验收标准1、目的本文件是为了保证模具的品质、达到模具设计要求、验收合格模具。
2、适应范围适用于供方需供样生产的样品模、量产模。
3、职责3.1 项目负责人:负责产品结构图纸及相关的资料提供,以及模具样品的验收确认。
3.2 模具负责人:负责模具的验收、协助钳工对模具进行调试3.3 模修负责人:负责模具调试3.4 品质负责人:负责模具验收、负责样品检测(外观、尺寸)4、验收标准4.1 模具验收前,应有样品检测报告、工件检测报告、模板检验报告。
产品重点尺寸、封胶位尺寸必须符合图纸要求4.2 模具设计符合内部设计标准,具体料带图参照DFM.4.3 模具确认4.3.1 模具负责人对模具进行确认:要求外观良好,内部零件完好,不能有垫片、焊点、无裂痕、崩角现象,落料顺畅模具所有镶件间隙配合合理,无过松过紧现象;电子图档与零件相符,提供最终版的电子档图纸,图档符合“模具图档接收要求”。
4.3.2 样品模与量产模模板厚度一致;吊装孔孔径、位置按照厂内设计标准设计,孔径M16;误送检测、下死点装置,样品模具转量产模时必须添加,转量产模时结构等必须符合《冲压部模具接收技术规范》。
4.3.3 品质检验人员对照《冲压模具出货检验记录》对模具进行点检,模具检验OK后再进行连续生产。
4.3.4 项目负责人对模具生产出来的产品做结构确认,其中包含毛刺方向确认,对确认OK的样品进行结构承认签样保存。
4.3.5 品质负责人对模具生产的产品做外观确认,确认OK的样品进行外观签样保存,如有压伤,毛刺大小等有需要可以签限度样方便生产。
4.3.6 模具连续生产80K冲次或4小时每40K作产品全尺寸检测并符合图面CPK值检测,同时确保产品外观符合要求。
4.3.7 模具初步验收后产品设变,需由模具责任人负责调试并供样20K设变后合格产品。
模具经初步验收合格后,生产人员方可进入模具小批量生产。
4.4 易损零件应有最少一件备件。
4.5 验收合格后,需将模具图档整理后的图档同模具一起交接给模具接收部门,模具图档中应包含模具履历表、完整的零件设变与修改过程等,模具图档符合“模具图档接收要求”。
模具验收要求
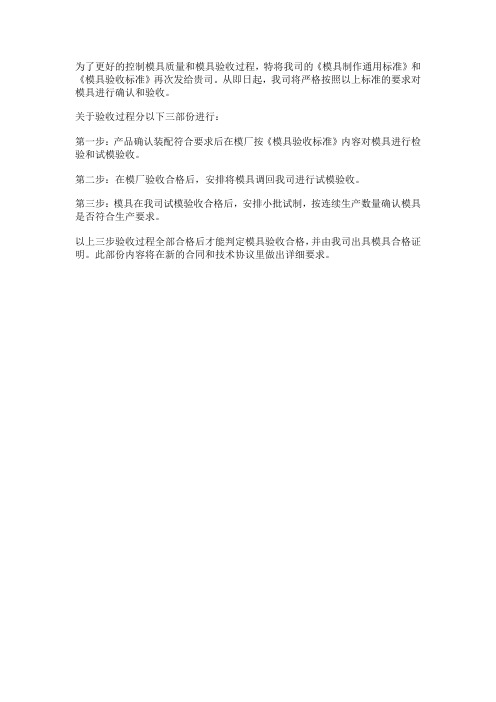
为了更好的控制模具质量和模具验收过程,特将我司的《模具制作通用标准》和《模具验收标准》再次发给贵司。
从即日起,我司将严格按照以上标准的要求对模具进行确认和验收。
关于验收过程分以下三部份进行:
第一步:产品确认装配符合要求后在模厂按《模具验收标准》内容对模具进行检验和试模验收。
第二步:在模厂验收合格后,安排将模具调回我司进行试模验收。
第三步:模具在我司试模验收合格后,安排小批试制,按连续生产数量确认模具是否符合生产要求。
以上三步验收过程全部合格后才能判定模具验收合格,并由我司出具模具合格证明。
此部份内容将在新的合同和技术协议里做出详细要求。
- 1、下载文档前请自行甄别文档内容的完整性,平台不提供额外的编辑、内容补充、找答案等附加服务。
- 2、"仅部分预览"的文档,不可在线预览部分如存在完整性等问题,可反馈申请退款(可完整预览的文档不适用该条件!)。
- 3、如文档侵犯您的权益,请联系客服反馈,我们会尽快为您处理(人工客服工作时间:9:00-18:30)。
模具验收标准
WEIHUA system office room 【WEIHUA 16H-WEIHUA WEIHUA8Q8-
一.成型产品外观、尺寸、配合。
1. 产品表面不允许缺陷:缺料、烧焦、顶白、白线、披峰、起泡、拉白(或拉裂、拉断)、烘印、皱纹。
?
2. 熔接痕:一般圆形穿孔熔接痕长度不大于5mm,异形穿孔熔接痕长度小于15mm,熔接痕强度并能通过功能安全测试。
3. 收缩:外观面明显处不允许有收缩,不明显处允许有轻微缩水(手感不到凹痕)。
4.一般小型产品平面不平度小于,有装配要求的需保证装配要求。
5. 外观明显处不能有气纹、料花,产品一般不能有气泡。
6. 产品的几何形状,尺寸大小精度应符合正式有效的开模图纸(或3D文件)要求,产品公差需根据公差原则,轴类尺寸公差为负公差,孔类尺寸公差为正公差,顾客有要求的按要求。
7. 产品壁厚:产品壁厚一般要求做到平均壁厚,非平均壁厚应符合图纸要求,公差根据模具特性应做到。
8. 产品配合:面壳底壳配合:表面错位小于,不能有刮手现象,有配合要求的孔、轴、面要保证配合间隔和使用要求。
1.模具铭牌内容完整,字符清晰,排列整齐。
?
2. 铭牌应固定在模脚上靠近模板和基准角的地方。
铭牌固定可靠、不易剥落。
3. 冷却水嘴应选用塑料块插水嘴,顾客另有要求的按要求。
4. 冷却水嘴不应伸出模架表面
5. 冷却水嘴需加工沉孔,沉孔直径为25mm、30mm、35mm三种规格,孔口倒角,倒角应一致。
6. 冷却水嘴应有进出标记。
7. 标记英文字符和数字应大于5/6,位置在水嘴正下方10mm处,字迹应清晰、美观、整齐、间距均匀。
8. 模具配件应不影响模具的吊装和存放。
安装时下方有外露的油缸、水嘴,预复位机构等,应有支撑腿保护。
9. 支撑腿的安装应用螺钉穿过支撑腿固定在模架上,过长的支撑腿可用车加工外螺纹柱子紧固在模架上。
10. 模具顶出孔尺寸应符合指定的注塑机要求,除小型模具外,不能只用一个中心顶出。
11. 定位圈应固定可靠,圈直径为100mm、250mm两种,定位圈高出底板
10~20mm。
顾客另有要求的除外。
12. 模具外形尺寸应符合指定注塑机的要求。
13. 安装有方向要求的模具应在前模板或后模板上用箭头标明安装方向,箭头旁应有“UP”字样,箭头和文字均为黄色,字高为50 mm。
14. 模架表面不应有凹坑、锈迹、多余的吊环、进出水汽、油孔等以及影响外观的缺陷。
15. 模具应便于吊装、运输,吊装时不得拆卸模具零部件,吊环不得与水嘴、油缸、预复位杆等干涉。
2. 模具成型零件和浇注系统(型芯、动定模镶块、活动镶块、分流锥、推杆、浇口套)材料采用性能高于40Cr以上的材料。
3. 成型对模具易腐蚀的塑料时,成型零件应采用耐腐蚀材料制作,或其成型面应采取防腐蚀措施。
4. 模具成型零件硬度应不低于50HRC,或表面硬化处理硬度应高于600HV。
2. 斜顶表面应抛光,斜顶面低于型芯面。
3. 滑动部件应开设油槽,表面需进行氮化处理,处理后表面硬度为HV700以上。
4. 所有顶杆应有止转定位,每个顶杆都应进行编号。
5. 顶出距离应用限位块进行限位。
6. 复位弹簧应选用标准件,弹簧两端不得打磨,割断。
7. 滑块、抽芯应有行程限位,小滑块用弹簧限位,弹簧不便安装时可用波子螺丝;油缸抽芯必须有行程开关。
8. 滑块抽芯一般采用斜导柱,斜导柱角度应比滑块锁紧面角度小2°~3°。
滑块行程过长应采用油缸抽拔。
9. 油缸抽芯成型部分端面被包覆时,油缸应加自锁机构。
10. 滑块宽度超过150 mm的大滑块下面应有耐磨板,耐磨板材料应选用T8A,经热处理后硬度为HRC50~55,耐磨板比大面高出~ mm,并开制油槽。
11. 顶杆不应上下串动。
12. 顶杆上加倒钩,倒钩的方向应保持一致,倒钩易于从制品上去除。
13. 顶杆孔与顶杆的配合间隙,封胶段长度,顶杆孔的表面粗糙度应按相关企业标准要求。
14. 制品应有利于操作工取下。
15. 制品顶出时易跟着斜顶走,顶杆上应加槽或蚀纹。
16. 固定在顶杆上的顶块,应牢固可靠,四周非成型部分应加工3°~5°的斜度,下部周边应倒角。
17. 模架上的油路孔内应无铁屑杂物。
18. 回程杆端面平整,无点焊。
胚头底部无垫片,点焊。
19. 三板模浇口板导向滑动顺利,浇口板易拉开。
20. 三板模限位拉杆应布置在模具安装方向的两侧,或在模架外加拉板,防止限位拉杆与操作工干涉。
21. 油路气道应顺畅,液压顶出复位应到位。
22. 导套底部应开制排气口。
23. 定位销安装不能有间隙。
2. 密封应可靠,系统在压力下不得有渗漏现象,易于检修。
3. 开设在模架上的密封槽的尺寸和形状应符合相关标准要求。
4. 密封圈安放时应涂抹黄油,安放后高出模架面。
5. 水、油流道隔片应采用不易受腐蚀的材料。
6. 前后模应采用集中送水、方式。
2. 流道截面、长度应设计合理,在保证成形质量的前提下尽量缩短流程,减少截面积以缩短填充及冷却时间,同时浇注系统损耗的塑料应最少。
3. 三板模分浇道在前模板背面的部分截面应为梯形或半圆形。
4. 三板模在浇口板上有断料把,浇道入口直径应小于3 mm,球头处有凹进浇口板的一个深3 mm的台阶。
5. 球头拉料杆应可靠固定,可压在定位圈下面,可用无头螺丝固定,也可以用压板压住。
6. 浇口、流道应按图纸尺寸要求用机应加工,不允许手工甩打磨机加工。
7. 点浇口浇口处应按规范要求。
8. 分流道前端应有一段延长部分作为冷料穴。
9. 拉料杆Z形倒扣应有圆滑过渡。
10. 分型面上的分流道应为圆形,前后模不能错位。
11. 在顶料杆上的潜伏式浇口应无表面收缩。
12. 透明制品冷料穴直径、深度应符合设计标准。
13. 料把易于去除,制品外观无浇口痕迹,制品装配处无残余料把。
14. 弯勾潜伏式浇口,两部分镶块应氮化处理,表面硬度达到HV700。
2. 镶块与模框配合,四周圆角应有小于1 mm的间隙。
3. 分型面保持干净、整洁、无手提砂轮磨避空,封胶部分无凹陷。
4. 排气槽深度应小于塑料的溢边值。
5. 嵌件研配应到位,安放顺利、定位可靠。
6. 镶块、镶芯等应可靠定位固定,圆形件有止转,镶块下面不垫铜片、铁片。
7. 顶杆端面与型芯一致。
8. 前后模成型部分无倒扣、倒角等缺陷。
9. 筋位顶出应顺利。
10. 多腔模具的制品,左右件对称,应注明L或R,顾客对位置和尺寸有要求的,应符合顾客要求,一般在不影响外观及装配的地方加上,字号为1/8。
11. 模架锁紧面研配应到位,75%以上面积碰到。
12. 顶杆应布置在离侧壁较近处及筋、凸台的旁边,并使用较大顶杆。
13. 对于相同的件应注明编号1、2、3等。
14. 各碰穿面、插穿面、分型面应研配到位。
15. 分型面封胶部分应符合设计标准。
中型以下模具10~20mm,大型模具30~50 mm,其余部分机加工避空。
16. 皮纹及喷砂应均匀达到顾客要求。
17. 外观有要求的制品,制品上的螺钉应有防缩措施。
18. 深度超过20 mm的螺钉柱应选用顶管。
19. 制品壁厚应均匀,偏差控制在± mm以下。
20. 筋的宽度应在外观面壁厚的百分之六十以下。
21. 斜顶、滑块上的镶芯应有可靠的固定方式。
22. 前模插入后模或后模插入前模,四周应有斜面锁紧并机加工避空。
八.注塑生产工艺。
1. 模具在正常注塑工艺条件范围内,应具有注塑生产的稳定性和工艺参数调校的可重复性。
?
2. 模具注塑生产时注射压力,一般应小于注塑机额定最大注射压力的85%。
3. 模具注塑生产时的注射速度,其四分之三行程的注射速度不低于额定最大注射速度的10%或超过额定最大注射速度的90%。
4. 模具注塑生产时的保压压力一般应小于实际最大注射压力的85%。
5. 模具注塑生产时的锁模力,应小于适用机型额定锁模力的90%。
6. 注塑生产过程中,产品及水口料的取出要容易、安全(时间一般各不超过2秒钟)。
7. 带镶件产品的模具,在生产时镶件安装方便、镶件固定要可靠。
九.包装、运输。
1. 模具型腔应清理干净喷防锈油。
?
2. 滑动部件应涂润滑油。
3. 浇口套进料口应用润滑脂封堵。
4. 模具应安装锁模片,规格符合设计要求。
5. 备品备件易损件应齐全,并附有明细表及供应商名称
6. 模具水、液、气、电进出口应采取封口措施封口防止异物进入;
7. 模具外表面喷制油漆,顾客有要求的按要求。
8. 模具应采用防潮、防水、防止磕碰包装,顾客有要求的按要求。
9. 模具产品图纸、结构图纸、冷却加热系统图纸、热流道图纸、零配件及模具材料供应商明细、使用说明书,试模情况报告,出厂检测合格证,电子文档均应齐全。