Sliding mode control for mobile welding robot
VRTEX 移动虚拟现实焊接培训器说明说明书

EASILY TRANSPORTED from classroom toclassroom or to a recruitment event or openhouse. The VRTEX Mobile can be ready to goin a matter of minutes.BLENDED TRAINING SOLUTIONS FOR WELDING EDUCATIONTOUCHSCREEN USER INTERACTION providesequipment and procedural set-up on an intuitive,resistive touchscreen. All screens mirror theVRTEX 360, making transfer of interactionseamless between the systems.UNIVERSAL GUN HANDLE allows for connectionof a MIG/MAG gun attachment for GMAW andFCAW, and a stick attachment for SMAW welding.TABLETOP COUPON STAND easily attaches andstands on a standard table for welding and istaken apart for quick and simple storage insidethe VRTEX Mobile.The VRTEX systems are virtual reality arc welding training simulators. Thesecomputer based training systems are educational tools designed to supplementand enhance traditional welding training. They allow students to practice theirwelding technique in a simulated and immersive environment. The VRTEX systemspromote the efficient transfer of quality welding skills and body positioning tothe welding booth while reducing material waste associated with traditionalwelding training. The combination of realistic puddle, arc welding sound, andreal-time feedback tied to the welder’s movement provides a realistic andexciting, hands-on training experience.The VRTEX® Mobile is a basic, entry level welding training system. It is designedto provide mobility in an easy to use and engaging welding training tool. TheVRTEX Mobile is ideal for initial, basic welding training, as a recruitment andengagement tool for educational and industry and for employment and screeningfor human resources or as an evaluation tool for instructors and educators to geta baseline on student knowledge. The VRTEX Mobile is definitely on the move!VRTEX MOBILE PROVIDES:FLEXIBILITY» M ultiple welding processes and positions» V ariety of joint configurations» I nstructor tools allow modification basedon preferred welding program and styleINNOVATION» R ealistic welding puddle appearance and sounds» M agnetic tracking system provides accuratemeasurements for student score and evaluation» V irtual weld discontinuities appear in the weldwhen improper welding technique is usedCLASSROOM PERFORMANCE» Visual cues give real-time technique feedback» Advanced scoring system for student evaluation» E ncourages interaction — the instructor cancoach the welder while conducting virtualweld inspection» R ecord, archive and verify student work.CONSUMABLE ANDENVIRONMENTAL SAVINGS» No welding consumables, wire or waste» Track savings with the Weldometer™LANGUAGE SUPPORTEnglish, French, German, Spanish, Turkish,Japanese, Chinese (Mandarin), Portuguese(Brazilian), Russian, Korean, Hindi and ArabicDEMO MODE:Allows the instructor or student to view anexample weld or a demonstration of propertechnique, prior to a weld being madeREPLAY MODEAllows for instructor or student to reviewand analyze the welding processSET-UP AND INSTALLATION REQUIREMENTS:• T he VRTEX system requires minimal space for set-up. Dimensions are 8 W x 8 D x 8 H ft. (2.4 x 2.4 x 2.4 m).• W hen operating multiple units in one location, switch between standard and alternate frequency systems (unique part numbers are identified).• T he VRTEX Mobile system is not designed for operation in harsh environments. Recommendations are listed in the instruction manual.• A void magnetic fields, conductive and high frequency objects and processes.• A n uninterruptible power supply (UPS) may be required for protection of the system from power irregularities and/or disruptions.MC12-93 (06/15) © Lincoln Global, Inc. All Rights Reserved. Printed in U.S.A.CUSTOMER ASSISTANCE POLICYThe business of The Lincoln Electric Company is manufacturing and selling high quality welding equipment, consumables, and cutting equipment. Our challenge is to meet the needs of our customers and to exceed their expectations. On occasion, purchasers may ask Lincoln Electric for information or advice about their use of our products. Our employees respond to inquiries to the best of their ability based on information provided to them by the customers and the knowledge they may have concerning the application. Our employees, however, are not in a position to verify the information provided or to evaluate the engineering requirements for the particular weldment. Accordingly, Lincoln Electric does not warrant or guarantee or assume any liability with respect to such information or advice. Moreover, the provision of such information or advice does not create, expand, or alter any warranty on our products. Any express or implied warranty that might arise from the information or advice, including any implied warranty of merchantability or any warranty of fitness for any customers’ particular purpose is specifically disclaimed.Lincoln Electric is a responsive manufacturer, but the selection and use of specific products sold by Lincoln Electric is solely within the control of, and remains the sole responsibility of the customer. Many variables beyond the control of Lincoln Electric affect the results obtained in applying these types of fabrication methods and service requirements.Subject to Change – This information is accurate to the best of our knowledge at the time of printing. Please refer to for anyupdated information.。
点焊机的原理与制作方法

点焊机的原理与制作方法英文回答:The principle of a spot welding machine is based on the resistance heating principle. It involves joining two or more metal pieces together by applying pressure and passing an electric current through them. The heat generated by the electric current melts the metal at the contact points, and when the current is stopped, the molten metal solidifies, forming a strong bond.A spot welding machine consists of several key components. The main components include the power supply, electrodes, and a control system. The power supply provides the electric current required for welding. The electrodes, usually made of copper, are used to apply pressure and conduct the electric current to the metal pieces. The control system regulates the welding parameters such as the welding current, welding time, and electrode pressure.To create a spot welding machine, one needs to follow a few steps. First, the power supply needs to be selected based on the desired welding current and voltage. The power supply should be capable of delivering the required current to melt the metal at the contact points. Next, the electrodes need to be designed and fabricated. The electrodes should have good thermal conductivity to ensure efficient heat transfer and should be able to withstand the pressure applied during welding. Finally, a control system needs to be integrated to regulate the welding parameters and ensure consistent and reliable welds.Spot welding machines are widely used in various industries, such as automotive, construction, and manufacturing. They are particularly useful for joiningthin metal sheets or wires, such as in the production of car bodies or wire mesh. The speed and efficiency of spot welding make it a preferred method for mass production.中文回答:点焊机的原理基于电阻加热原理。
Sliding Mode Control for Nonholonomic Mobile Robot
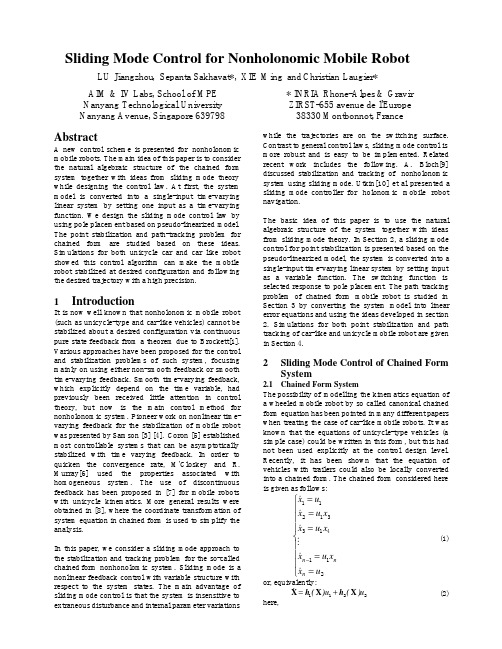
Kylia MINT和WT-MINT延时线干涉仪产品说明书

w w w.k y l i a.c o m i n f o@k y l i a.c o m Delay Line InterferometersMINT and WT-MINT1 – Description……………………………………………………………………………………………………………………………………… p12 – Block diagrams……………………………………………………………………………………………………………………………….. p23 – Absolute maximum ratings……………………………………………………………………………………………………………… p34 – Operating conditions………………………………………………………………………………………………………………………. p35 – MINT specifications………………………………………………………………………………………………………………………… p46 – MINT statistic data………………………………………………………………………………………………………………………….. p67 – WT-MINT specifications………………………………………………………………………………………………………………….. p78 – Phase tuning options………………………………………………………………………………………………………………………. p99 – ER attenuation option…………………………………………………………………………………………………………………….. p1110 – IL attenuation option……………………………………………………………………………………………………………………. p1311 – Tunable coupling option……………………………………………………………………………………………………………….. p1312 – TAP option……………………………………………………………………………………………………………………………………. p1513 – Second input option……………………………………………………………………………………………………………………… p1514 – Wavelength range………………………………………………………………………………………………………………………… p1515 – Fiber type and connectors…………………………………………………………………………………………………………….. p1616 – Custom products…………………………………………………………………………………………………………………………… p1617 – Packages layout……………………………………………………………………………………………………………………………. p1618 – Revision………………………………………………………………………………………………………………………………………… p171 – DescriptionThe Micro Interferometer (MINT) is a Delay Line Interferometer (DLI) that performs the interference between an incoming signal and itself delayed by one bit-time. Dedicated to D(Q)PSK demodulation it can be used in many other applications. MINT is tunable to enable a precise matching of the carrier frequency. Two phase tuning options are available: the ultra-fast option (U), which exhibits very low tuning time constant (20µs), and the low voltage option (L), which needs only 3V to reach the tuning range.The WT-MINT is a Widely Tunable MINT that enables to set the delay of the interferometer to the desired value. This can be done either with a micrometer head (manual option) or with a motorized translation stage (piloted version). In both case U and L option are available to precisely match the carrier frequency. There are three ranges of WT-MINT:-WT-MINT 100ps: it enables to set an optical delay range of 100ps (corresponding to a Free Spectral Range of 10GHz to infinite, or – for instance – 5GHz to 10GHz). Available with manual or piloted option.-WT-MINT 300ps: it enables to set an optical delay range of 300ps (corresponding to a Free Spectral Range of 3.3GHz to infinite, or 2.5GHz to 10GHz). Available with manual or piloted option.-WT-MINT 3000ps: it enables to set an optical delay range of 3000ps (corresponding to a Free Spectral Range of 0.33GHz to infinite). Available with piloted option only.MINT and WT-MINT products are also available with PM fibers.MINT packagingWT-MINT packaging2 – Block diagrams50/50 platemirroroptical connectorBlock diagram: MINTBlock diagram: WT-MINTThe incoming signal is split in two parts. One is delayed regarding the other and then both are recombined on two outputs where they interfere one with each other. Both outputs are phase shifted by 180° and thus can be plugged to balanced or differential photodiodes that will convert a phase modulation into an amplitude modulation.The delay between both arms of the interferometer should be equal to the time-bit (T bit) of the incoming signal. Then the interferometer is characterized by its Free Spectral Range (FSR) which is linked to T bit by the relation FSR=1/T bit.3 – Absolute maximum ratingsParameter Symbol Min Typ. Max Unit Remarks/Conditions Maximal optical input power OpIn 300 mWStorage temperature range MINTSTR-40 80°C WT-MINT -10 40Humidity RH 5 85 % Non condensing Fiber bend radius 20 mmMaximum input voltage U optionV max100VL option44 – Operating conditionsParameter Symbol Min Typ. Max Unit Remarks/Conditions Operating wavelength OWR 1520 1570 nmOperating temperature range MINTOTR0 70°C WT-MINT 10 355 – MINT specificationsMINT, FSR > 2.5GHzParameterSymbol Min Typ. Max Unit Remarks/Conditions Free Spectral Range 1FSR 2.5 GHz Any FSR > 2.5GHz can be provided FSR accuracy 1ΔFSR 1 %FSR Insertion Losses 1 IL 2.0 dB IL uniformity 1ΔIL 0.5 dB Polarization Dependant Losses 1,2PDL 0.3 dB Polarization DependantFrequency Shift 1,2FSR>10GHz PDFS 2.0 %FSR FSR<10GHz4.0 Extinction Ratio 1ER 18 dB Polarization Extinction Ratio 1,3PER 20 25 dB Temperature Dependant Frequency Shift L TDFS 10 %FSR U50 Tuning range 1.5 FSRTuning voltage L V 3 V Voltage needed to reach the tuning range U 75 90 Tuning time constant L τ 1.0 s To reach 50% of the final state U 0.02 ms Power consumptionL P 0.5 W U 0.001 Polarization Mode Dispersion PMD 0.1 ps Chromatic Dispersion CD 1 ps/nm Optical Return Loss ORL 35 dB Skew0.5 1.0ps Packaging size 4FSR >= 20GHz44 x 26 x 9.5mm 3FSR < 20GHzor PM fiber any FSR100 x 55 x 16 Phase tuning connector 0.1 inch PIN headerFiber Pigtail Type SM SMF-28With 900µm loose tube PMPANDA PMFiber Pigtail Length0.91.01.1m1 measured over OTR and OWR for all states of polarization 2for Single Mode MINT 3for Polarization Maintaining MINT 4excluding fiber bootMINT, FSR < 2.5GHzParameterSymbol Min Typ. Max Unit Remarks/ConditionsFree Spectral Range 1FSR 0.4 2.5 GHz Any FSR between 400MHz and 2.5GHz can be providedFSR accuracy 1ΔFSR 5 %FSRInsertion Losses on short arm 1IL1 9.0 dB Including 6dB of natural losses due to beamsplitter Insertion Losses on long arm 1 IL2 9.0 dB Polarization Extinction Ratio 1,3 PER 20 25 dB Tuning range 1.5 FSRTuning voltage L V 3 V Voltage needed to reach the tuning range U 75 90 Tuning time constant L τ 1.0 s To reach 50% of the final state U 0.02 ms Power consumptionL P 0.5 W U0.001 Polarization Mode Dispersion PMD 0.1 ps Chromatic Dispersion CD 1 ps/nm Optical Return Loss ORL 35 dB Skew0.51.0ps Packaging size 4130 x 65 x 19.5 mm 3Phase tuning connector 0.1 inch PIN headerFiber Pigtail Type SM SMF-28With 900µm loose tube PMPANDA PMFiber Pigtail Length0.91.01.1m1 measured over OTR and OWR for all states of polarization 2for Single Mode MINT 3for Polarization Maintaining MINT 4excluding fiber boot6 – MINT statistic dataHere are the statistic data of our MINT delivered between January 2009 and March 2013 (any FSR from 2.5Hz to 100GHz, any phase tuning option).For PDFS and ER, we do not observe Gaussian repartition because these parameters depend on the FSR (larger is the FSR, better are PDFS and ER).0%5%10%15%20%25%30%> -2> -1.8> -1.6> -1.4> -1.2> -1> -0.8> -0.6> -0.4> -0.2% o f M I N T d e l i v e r e dIL (dB)(> -1 means -1.2dB > IL > -1.0dB)0%10%20%30%40%50%0< 0.05< 0.1< 0.15< 0.2< 0.25< 0.3< 0.35% o f M I N T d e l i v e r e dPDL (dB)(< 0.3 means 0.3dB > PDL > 0.25dB)0%5%10%15%20%< 0< 0.2< 0.4< 0.6< 0.8< 1< 1.2< 1.4< 1.6< 1.8< 2< 2.2< 2.4< 2.6< 2.8< 3% o f M I N T d e l i v e r e d (F S R > 10G H z )PDFS (%FSR)(< 3 means 3% > PDFS > 2.8%)0%5%10%15%20%> 17> 18> 19> 20> 21> 22> 23> 24> 25> 26> 27> 28> 29> 30% o f M I N T d e l i v e r e dER (dB)(> 18 means 19dB > ER > 18dB)7 – WT-MINT specificationsThe 100ps WT-MINT allows a tunable FSR from 10GHz to infinite.WT-MINT, 100ps Optical Delay RangeParameter Symbol Min Typ. Max Unit Remarks/Conditions Optical Delay RangeODR 100 ps Manual WT-MINT ODR sensitivity 8 fs M o t o r i z e d W T -M I N TMinimum incremental motion 2 fs Relative accuracy75 fs Unidirectional repeatability 15 fs Bidirectional repeatability20 fs Insertion Losses 1 IL 2.5 dB IL uniformity 1ΔIL0.5 dB Polarization Dependant Losses 1,2PDL 0.5 dB Polarization Dependant Frequency Shift 1,2PDFS 3.0 %FSR Extinction Ratio 1ER18 dB Polarization Extinction Ratio 1,3PER 20 25 dB Tuning range 1.5 FSRTuning voltage L V 3 V Voltage needed to reach the tuning range U 75 90 Tuning time constant L τ 1.0 s To reach 50% of the final state U 0.02 ms Power consumptionL P 0.5 W U0.001 Polarization Mode Dispersion PMD 0.1 ps Chromatic Dispersion CD 1 ps/nm Optical Return Loss ORL 35 dB Skew0.5 1.0ps Packaging size 4216 x 92 x 40mm 3Phase tuning connectorBNCFiber Pigtail TypeSM SMF-28With 900µm loose tubePMPANDA PM1 measured over ODR, OTR and OWR for all states of polarization 2for Single Mode WT-MINT 3for Polarization Maintaining WT-MINT 4excluding micrometer head or piloted actuatorThe 300ps WT-MINT allows a tunable FSR from 3.3GHz to infinite or 2.5GHz to 10GHz.WT-MINT, 300ps Optical Delay RangeParameter Symbol Min Typ. Max Unit Remarks/Conditions Optical Delay RangeODR 300 ps Manual WT-MINT ODR sensitivity 15 fs M o t o r i z e d W T -M I N TMinimum incremental motion 3 fs Relative accuracy150 fs Unidirectional repeatability 30 fs Bidirectional repeatability40 fs Insertion Losses 1 IL 4.0 dB IL uniformity 1ΔIL1.0 dB Polarization Dependant Losses 1,2PDL 0.8 dB Polarization Dependant Frequency Shift 1,2PDFS 5.0 %FSR Extinction Ratio 1ER15 dB Polarization Extinction Ratio 1,3PER 20 25 dB Tuning range 1.5 FSRTuning voltage L V 3 V Voltage needed to reach the tuning range U 75 90 Tuning time constant L τ 1.0 s To reach 50% of the final state U 0.02 ms Power consumptionL P 0.5 W U0.001 Polarization Mode Dispersion PMD 0.1 ps Chromatic Dispersion CD 1 ps/nm Optical Return Loss ORL 35 dB Skew0.5 1.0ps Packaging size 4216 x 92 x 40mm 3Phase tuning connectorBNCFiber Pigtail TypeSM SMF-28With 900µm loose tubePMPANDA PM1 measured over ODR, OTR and OWR for all states of polarization 2for Single Mode WT-MINT 3for Polarization Maintaining WT-MINT 4excluding micrometer head or piloted actuatorThe 3ns WT-MINT allows a tunable FSR from 0.33GHz to infinite. The 12ns WT-MINT allows a tunable FSR from 83MHz to infinite.WT-MINT, 3ns to 12ns Optical Delay RangeParameter Symbol Min Typ. Max Unit Remarks/Conditions Optical Delay Range ODR 3000 ps Minimum incremental motion3ns delay 10 fs 12ns delay 40 Relative accuracy 3ns delay 250 fs 12ns delay 1000 Unidirectional repeatability3ns delay 30 fs 12ns delay 120 Bidirectional repeatability3ns delay 150 fs12ns delay600 Insertion Losses on short arm 1 IL1 9.0 dB Including 6dB of natural losses due to beamsplitter Insertion Losses on long arm 1IL2 9.0 dB Polarization Extinction Ratio 1,2PER 20 25 dB Tuning range1.5 FSRTuning voltage L V 3 V Voltage needed to reach the tuning range U 75 90 Tuning time constant L τ 1.0 s To reach 50% of the final state U 0.02 ms Power consumptionL P 0.5 W U0.001 Polarization Mode Dispersion PMD 0.1 ps Chromatic Dispersion CD 1 ps/nm Optical Return Loss ORL 35 dB Skew0.5 1.0ps Packaging size 750 x 400 x 129Phase tuning connectorBNCFiber Pigtail TypeSM SMF-28With 900µm loose tubePMPANDA PM1measured over ODR, OTR and OWR for all states of polarization 2for Polarization Maintaining WT-MINT8 – Phase tuning optionsFor DPSK demodulation, the phase tuning is essential in order to control the contrast between both outputs of the interferometer/demodulator.The FSR variation is not significant (and can be considered as invariant) when the user adjust the phase of the demodulator/interferometer.KYLIA proposes for all its DPSK demodulators (MINT and WT-MINT) two different phase tuning options: U option:Ultra-fast response based on a piezo actuator.This option is helpful for fast shifting systems (instability of the laser for instance). The DLI can adapt itself instantaneously to the environment, if a closed loop between BER and phase shifting is set up. This solution is mainly used in labs.Using the phase tuning, theuser can adjust the demodulator phase in order to match with the low contrast between outputshigh contrast between outputs thanks to phase tuningWith this option, the utuning time is better thTuning sL option: Low-voltage tuning basPhase shift is obtainedvoltage changes the locWith this option, the utuning time is better9 – ER attenuation optionIt is possible to tune the extinction ratipower is the same the ER will be the grThe ER attenuation option for MINT anof one arm of the interferometer. It enan accuracy of 1dB.Block dthe user can accomplish a shift of one FSR by applyiter than 20µs.ning speed for a U option DPSK demodulatorng based on a resistive heatertained using a resistive heater fixed on an optical ehe local temperature and thus the optical index, thenthe user can accomplish a shift of one FSR by applyter than 1s.n ratio of an interferometer by adjusting the power inthe greatest. By attenuating the power in one arm, ERINT and WT-MINT consist of a micrometer head that. It enables to tune the ER down to 0dB (one arm is tock diagram: DLI with ER attenuation optionapplying a 60V voltage. Theical element. Changing thethen the optical delay.applying a 2V voltage. Thewer in both arms. When them, ER will be reduced.d that can adjust the powerm is totally shut down) withOn the following graph, we show the variation of the spectral response of our DLI by attenuating the optical beam for one arm of the interferometer.MINT spectral response with ER attenuationMINT with ER attenuation option-40-35-30-25-20-15-10-50193360193370193380193390193400193410I L (d B )frequency (GHz)position (mm)=0position (mm)=0.05position (mm)=0.10position (mm)=0.15position (mm)=0.20position (mm)=0.25position (mm)=0.27position (mm)=0.28position (mm)=0.29position (mm)=0.30position (mm)=0.31position (mm)=0.32position (mm)=0.33position (mm)=0.34position (mm)=0.35position (mm)=0.36position (mm)=0.37position (mm)=0.38position (mm)=0.39position (mm)=0.40micrometer head for ER attenuationWT-MINT with ER attenuation option10 – IL attenuation optionIL attenuation enables to increase the IL on each output individually. This can be done thanks to a micrometer head. The attenuation can be total (no power exits from the output) and adjusted with an accuracy of 0.1dB.Block diagram: DLI with IL attenuation option11 – Tunable coupling optionThis option is available for PM MINT or PM WT-MINT only. It enables to adjust the splitting ratio of the interferometer (which is 50/50 for standard interferometers) from 100/0 to 0/100. This can be very useful if a precise 50/50 ratio is needed.micrometer head for ER attenuationmicrometer head for FSR tuningBNC connector for phase tuningBlock diagram: DLI with tunable coupling optionWT-MINT PM with tunable coupling and ER attenuation optionsBNC connector for phase tuning12 – TAP optionThanks to the flexibility of our technology, we can propose to add optical TAP outputs in our products. The TAP ratio can be 4% or 50%.Block diagram: MINT with TAP option for input and output signals13 – Second input optionA second input can also be added in our product.Block diagram: MINT with a second optical input14 – Wavelength rangeMINT and WT-MINT can be proposed at different wavelength range, from the visible to the IR 800nm, 1064nm, 1300nm…). The device will be operational on a wavelength range of a tens of nanometers centered on the wavelength required by customer.15 – Fiber type and connectorsEvery MINT or WT-MINT can be proposed either with SM or PM fibers.The devices can be proposed with any kind of connectors (FP/UPC, FC/APC, SC/PC, SC/APC, LC/PC, E2000/PC, E2000/APC, etc…).16 – Custom productsThanks to our free-space technology we can easily customize most of our products and so it is for the MINT and WT-MINT. Customer can feel free to ask for any customization they need. We will examine the request and do our best to have a positive answer.17 – Packages layoutMINT packaging : FSR > 20GHz MINT packaging : FSR > 2.5GHzMINT packaging : FSR < 2.5GHzWT-MINT packaging (with ER attenuation option)18 – Revisiondate version ObjectMarch 21, 2013 MINT V1.0 CreationMay 15, 2014 MINT V1.1 Phase tuning option explanationMINT packaging for FSR < 2.5GHz February 3rd, 2015 MINT V1.2 Added 12ns delay WTMINT。
林肯电子Vantage 300多功能焊接机说明书

© Lincoln Global, Inc. All Rights Reserved.300ENGINE DRIVEN WELDERSProcessesStick, TIG, MIG, Flux-Cored, Gouging Product Number K2409-3See back for complete specsShown: K2409-3PH: +1.216-481-8100 • Output Range See Back PageRated Output Current/Voltage/Duty Cycle 300A/32V/100% 350A/28V/100%Number of Cylinders 4HP @ Speed (RPM) 22 HP @ 1800 RPM Weight/Dimensions (H x W x D) 1035 lbs. (469 kg) 35.9 x 25.3 x 60.0 in. (913 x 642 x 1524 mm) 44.3 (1124 mm) To Top ofExhaust Tubethe U.S.A. and Canada.Chopper Technology® delivers extremely fast response for tighter output control.VRD™ portion of nameplatewith green light on.Vantage ® 300 | [ 3 ]Single-side engine access with lockable sliding door.Fuel, oil pressure and engine temperature gauges help you monitor performance.Latched and lockable radiator cap cover.Convenient battery tray below control panel.Handy oil drain valve and tube makes oil changes neat.Output automatically switches toremote mode when remote device is connected. For the CC-stick,downhill pipe and Touch Start TIG ®modes, the machine output dial becomes a maximum current limit for more fine tuning with the remote control dial or Amptrol ™.1. Glow Plug Button2. Weld Mode Selector Switch3. Run/Stop Switch4. Hour Meter5. Start Pushbutton6. Engine Idler Switch7. Fuel Level, Engine Temperature and Oil Pressure Gauges 8. Engine Protection Light 9. Engine Battery Charging Light 10. 120 VAC Circuit Breakers 11. 120 VAC Receptacles12. Covered Weld Output Terminals + and - 13. Sealed GFCI Modules 14. Ground Stud15. 120/240 VAC Full-KVA 1-Phase Receptacle 16. 240 VAC Full-KVA 3-Phase Receptacle 17. Full-KVA 1- & 3-Phase Circuit Breaker 18. 14-Pin Wire Feeder Connector 19. 6-Pin Remote Control Connector20. Arc Force & Inductance/Pinch Control Dial 21. Welding Terminals Control Switch 22. Wire Feeder Voltmeter Polarity Switch 23. Digital Amps and Volts Output Meters 24. VRD ™ Indicator Lights 25. Output Control DialNote: Control panel door not shown.211232221201917161514181********• Simple Controls – Keeps training time to a minimum. The flip-down control panel door keeps less frequently used dials out of the way. Scratch-resistant Lexan ® nameplate.• Digital meters for amps and volts output make it easy to precisely set your procedures.• Large 20 gallon (76 liter) fuel tank provides run time for an extended day – over 16 hours of welding at 300A/32V/100% duty cycle output, or 49 hours at high idle.• The Kubota ® V1505 engine is a 22 horsepower, water-cooled, 4cylinder diesel engine with an automatic idler for greater fuel economy and reduced noise. • Engine hour meter makes it easy to schedule maintenance.• LN-25 Ironworker ™ arcoss-the-arc wire feeder is a recommended option.• 14-pin connector for Lincoln Electric wire feeders with control cables: LF-72, LF-74, LN-8, LN-15, LN-25 PRO Dual Power, and LN-742. Also compatible with Magnum ® SG spool gun system.• Two Vantage ® 300 units can be paralleled in the CC-stick mode to increase output.• Kilowatts available for Multi-Weld ® 350 use: 4.8 KW @ 60 VDC, 7.0 KW @ 58 VDC.KEY CONTROLS[ 4 ] | Vantage ® 300• Simple wire harnessing keeps connections to a minimum for greater reliability. Lead and harness strain reliefs on all control connections help ensure trouble-free performance.• Engine protection system includes automatic shutdown for low oil pressure or high engine temperature.• Indicator light turns on for low oil pressure or high engine temperature. A second indicator light turns on if the engine battery charging system malfunctions.• Circuit breaker protection on the battery ignition system provides added component protection.• Environmental friendly engine! The engine has a closed breathersystem to keep the engine compartment and ground clean. This system eliminates oil mist from collecting inside the engine compartment, especially on surfaces that would lower engine cooling efficiency.• Self-bleeding engine simplifies startup if your fuel tank runs dry.• Kubota ® engine camshaft is gear-driven. No timing belt maintenance.• Printed circuit boards are environmentally-shielded using Lincoln Electric’s engineered potting and protective frame trays.• Dependability and long life are aided by all-copper windings in rotor and stator with high quality insulation.• Standard stainless steel roof, side panels and engine-access doordeliver added protection, durability and corrosion-resistance. Eliminates the need to paint or replace rusting panels.• Manufactured under a quality system certified to ISO 9001 requirements and ISO 14001 environmental standards.• Canadian Standards Association (CSA) certified.• Three-year Lincoln Electric warranty (parts and labor) on welder(engine is warranted separately by the manufacturer).(1)High Altitude: For maximum rating, derate the output 2.5% to 3.5% for every 1,000 ft. (300 m). High Temperature: For maximum rating, derate 2 volts for every 18°F (10°C) above 104°F (40°C).(2) DC Constant Voltage capability provides convenience and added safety when welding in electrically hazardous conditions.(3) When welding, available AC generator power will be reduced. Output voltage is within +/- 10% at all loads up to rated capacity.(4) 120V will operate either 60 Hz or 50/60 Hz power tools, lights, etc.(5) Circuits cannot be wired in parallel to operate the same device.(6)Kubota ® warranty is 2 years/2,000 hours for machines shipped within the U.S., Canada, Pacific Ocean region and Western Europe. Warranty is 1 year/1,000 hours for Central and South America, Asia, Africa and Middle East.Vantage ® 300 |[ 5 ]One-Pak ® Welding PackageOrder a Lincoln Electric One-Pak ® and get everything you need to complete a welding package - all with one order number.(Package requires assembly.)Unassembled Package Contains:• Vantage ® 300• Medium Welder Trailer (K2636-1)• Duo-Hitch ™ 2 in. (51 mm) Ball/Lunette Eye Hitch (included)• Fender and Light Kit (K2639-1)• Cable Rack (K2640-1)• Cable Connectors - two (K2487-1)• Electrode Cable 2/0, two 50 ft. (15.3 m) lengths (K2485-2)• Electrode Cable 2/0, 10 ft. (3 m) (K2483-2)• Work Cable 2/0, 50 ft. (15.3 m) (K2484-2)• 300A Electrode Holder (K909-7)• 300A Work Clamp (K910-1)Order:K2452-3 Vantage ® 300 Kubota ® One-Pak ® PackageReady-Pak ® Welding PackageOrder a Lincoln Electric Ready-Pak ® Package and get an assembled welding pletely Assembled Package Contains:• Vantage ® 300• Medium Welder Trailer (K2636-1)• Duo-Hitch ™ 2 in. (51 mm) Ball/Lunette Eye Hitch (included)• Fender and Light Kit (K2639-1)• Cable Rack (K2640-1)• Cable Connectors - two (K2487-1)• Electrode Cable 2/0, two 50 ft. (15.3 m) lengths (K2485-2)• Electrode Cable 2/0, 10 ft. (3 m) (K2483-2)• Work Cable 2/0, 50 ft. (15.3 m) (K2484-2)• 300A Electrode Holder (K909-7)• 300A Work Clamp (K910-1)Order:K2453-3 Vantage ® 300 Kubota ® Ready-Pak ®PackageK2636-1 Medium Welder TrailerVantage ® 300Duo-Hitch ™ 2 in. (51 mm) Ball/Lunette Eye Hitch(included)K2640-1 Cable RackCompletely Assembled Ready-Pak ®Pkg.[ 6 ] | Vantage ® 300GENERAL OPTIONSPower Plug Kit (20A)Provides four 120V plugs rated at 20 amps each, and one dual voltage, full KVA (1-Phase) plug rated at 120/240V, 50 amps. 120V plug may not be compatible with common household receptacles. Order K802NFull-KVA Power Plug (1-Phase) One dual voltage plug rated at120/240V, 50 amps. NEMA 14-50P. Order T12153-9Full-KVA Power Plug (3-Phase) One plug rated at 240V, 50 amps. NEMA 15-50P. Order T12153-10Full - KVA Adapter Kit (1-Phase) Provides convenient connection of Lincoln Electric equipment having a 240V AC 1-phase plug (NEMA 6-50P) to the full-KVA receptacle on Lincoln engine-driven welders. Order K1816-1Medium Welder TrailerFor heavy-duty road, off-road, plant and yard use. Includes pivoting jack stand, safety chains, and 13 in. (330 mm) wheels. Stiff .120 in. (3.0 mm) welded rectangular steel tube frame construction is phosphate etched and powder coat painted for superior rust and corrosion resistance. Low sway suspension gives outstanding stability with manageable tongue weight. Wheel bearings are packed with high viscosity, high pressure, low washout Lubriplate ® grease. Includes a Duo-Hitch ™ – a 2 in. (51 mm) Ball/Lunette Eyecombination hitch. Overall width 60 in. (1524 mm). Overall length 124 in. (3150 mm). Order:K2636-1 TrailerK2639-1 Fender & Light Kit K2640-1 Cable RackFour-Wheeled Steerable Yard TrailerFor off-road, plant and yard use. Includes an automatically engaging drawbar lock when the drawbar is raised to the verticle position. 13 in. (330 mm) wheels. Wheel bearings are packed with high viscosity, high pressure, low washout Lubriplate ® grease. Stiff 3/16 in. (4.8 mm) welded rectangular steel frame construction is phosphate etched and powder-coat painted for superior rust and corrosion resistance. Also includes aDuo-Hitch ™ – a 2 in. (51 mm) Ball/Lunette Eye combination hitch. Overall width 55 in. (1397 mm). Overall length 124 in. (3150 mm). Order K 2641-2Spark Arrestor KitMounts to muffler exhaust tube. Virtually eliminates spark emissions. Order K1898-1Digital Weld Meters Kit Easy-to read digital meters for volts and amps. Easy to install. (For K2409-1 and K2499-1). Order K2467-1Polarity/Multi-Process Switch For easy polarity switching. Example: DC-stick root pass on pipe & DC+ stick for hot, fill and cap passes. Also for an easy process change. Example: DC+ stick root pass on pipe and DC- Innershield ® self-shielded flux-cored wire for hot, fill and cap passes. 6 & 14-pin remote connections can be made to this unit. For all Lincoln ElectricChopper Technology ® engine-driven welders. Mounts on roof with K2663-1 Docking Kit. Order K2642-1Docking KitSecures the K2642-1 Polarity/Multi-Process Switch to the engine-driven welder roof. Release latch permits removal of K2642-1 Polarity/Multi-Process Switch. Made from stainless steel for rust-free operation. For all Lincoln Electric ChopperTechnology ® engine-driven welders.Order K2663-1STICK OPTIONSAccessory KitIncludes 35 ft. (10.7 m) 2/0 electrode cable with lug, 30 ft. (9.1 m) 2/0 work cable with lugs, headshield, filter plate, cover plate, work clamp and electrode holder. 400 amp capacity. Order K704Remote Output ControlConsists of a control box with choice of two cable lengths. Permits remote adjustment of output.Order K857 for 25 ft. (7.6 m) K857-1 for 100 ft. (30.5 m)Remote Output Control with 120VAC ReceptaclesRemote weld output control box with two 120V AC receptacles having GFCI (Ground Fault Circuit Interrupter) protection. One cord for both remote and power. 100 ft. (30.5 m) length. Permits remote adjustment of weld output andpower for tools (such as a grinder) at the work. 20 amp capacity. Order K2627-2TIG OPTIONSPro-Torch ™ PTA-26V TIG Torch Air-cooled 200 amp torch (2 piece) equipped with valve for gas flow control. 25 ft. (7.6 m) length. Order K1783-9Magnum ® Parts Kit for PTA-26V TIG TorchMagnum ® Parts Kit provides all the torch accessories you need to start welding. Parts Kit provides collets, collet bodies, a back cap, alumina nozzles and tungstens in a variety of sizes, all packaged in an easy to carry reclosable sack. Order KP509Foot Amptrol ™Provides 25 ft. (7.6 m) of remote output control for TIG welding. (6-pin plug connection). Order K870Hand Amptrol ™Provides 25 ft. (7.6 m) of remote current control for TIG welding. 6-pin plug connection). Velcro straps secure torch. Order K963-3(one size fits all Pro-Torch ™ TIG Torches)Square Wave ™ TIG 175For AC TIG Welding with square wave performance, use the AC generator of the engine-driven welder to supply the power (full rated output may not be available). Easy setup. Includes torch, foot Amptrol ™ and gas regulator and hose. Requires the K1816-1 Full KVA Adapter Kit. Order K1478-5Invertec ® V205-T AC/DC One-Pak ® Pkg.For AC TIG welding with square wave performance, use the AC generator of the engine-driven welder to supply the power. Easy setup. Includes torch, parts kit, regulator and hose kit, Twist Mate ™ torch adapter, work cable with Twist Mate ™ end and Foot Amptrol ™. Requires K1816-1 Full-KVA Adapter Kit.Order K2350-2WIRE FEEDER OPTIONSLN-25 Ironworker™ Wire Feeder P ortable CV unit for flux-cored and MIG welding with MAXTRAC® wiredrive system. Includes digital metersfor wire feed speed/amperageand voltage, gas solenoid, internalcontactor and 5/64 in. (2.0 mm)drive roll kit for cored wire. Has 83%reduced wire feed speed capabilityfor 6 o’clock pipe welding withInnershield® wire.Order K2614-9K126 PRO Innershield® GunFor self-shielded wire with 15 ft.(4.5 m) cable. For .062-5/64 in.(1.6-2.0 mm) wire. IncludesK466-10 Connector Kit.Order K126-12Drive Roll and Guide Tube KitFor .068-.072 in. (1.7-1.8 mm)cored or solid steel wire.Order KP1697-068Magnum® PRO 350 Ready-Pak®15 ft., .035-5/64 in.Magnum® PRO MI G/flux-coredwelding guns are rated 100%duty cycle. The guns are designedfor high amperage, high dutycycle applications in extremeenvironments where heat-resistanceand fast serviceability are key.Order K2652-2-10-45Drive Roll and Guide Tube KitFor .035 in. and .045 in.(0.9-1.1 mm) solid steel wire.Order KP1696-1Magnum® SG Spool GunHand held semiautomatic wirefeeder. Requires SG Control Moduleand Input Cable.Order K487-25SG Control ModuleThe interface between the powersource and the spool gun. Providescontrol of the wire speed and gasflow. For use with a spool gun.Order K488Input Cable(For SG Control Module)For Lincoln Electric engine powersources with 14-pin MS-typeconnection, separate 115V NEMAreceptacles and output studconnections.Order K691-10PLASMA CUTTINGTomahawk® 1000Cuts metal using the AC generatorpower from the engine-drivenwelder. Requires the T12153-9Full-KVA Power Plug (1-Phase).Order K2808-1Vantage® 300 | [ 7 ]C U S T O M E R A S S I S T A N C E P O L I C YThe business of The Lincoln Electric Company is manufacturing and selling high quality welding equipment, consumables, and cutting equipment. Our challenge is to meet the needs of our customers and to exceed their expectations. On occasion, purchasers may ask Lincoln Electric for information or advice about their use of our products. Our employees respond to inquiries to the best of their ability based on information provided to them by the customers and the knowledge they may have concerning the application. Our employees, however, are not in a position to verify the information provided or to evaluate the engineering requirements for the particular weldment. Accordingly, Lincoln Electric does not warrant or guarantee or assume any liability with respect to such information or advice. Moreover, the provision of such information or advice does not create, expand, or alter any warranty on our products. Any express or implied warranty that might arise from the information or advice, including any implied warranty of merchantability or any warranty of fitness for any customers’ particular purpose is specifically disclaimed.Lincoln Electric is a responsive manufacturer, but the selection and use of specific products sold by Lincoln Electric is solely within the control of, and remains the sole responsibility of the customer. Many variables beyond the control of Lincoln Electric affect the results obtained in applying these types of fabrication methods and service requirements.Subject to Change – This information is accurate to the best of our knowledge at the time of printing. Please refer to for any updated information.For best welding results with Lincoln Electric equipment,always use Lincoln Electric consumables. Visit for more details.。
模具成形不良用语英汉对照

模具成形不良用语英汉对照 时间:2005-07-11 14:35 阿里巴巴-机械论坛aberration 色差 atomization ?化bank mark ?料纹 bite 咬入blacking hole 涂料孔(铸疵) blacking scab 涂料疤blister 起泡 blooming 起霜blow hole 破孔 blushing 泛白body wrinkle 侧壁皱纹 breaking-in 冒口带肉bubble 膜泡 burn mark 糊斑burr 毛边 camber 翘曲cell 气泡 center buckle 表面中部波皱check 细裂痕 checking 龟裂chipping 修整表面缺陷 clamp-off 铸件凹痕collapse 塌陷 color mottle 色斑corrosion 腐蚀 crack 裂痕crazing 碎裂 crazing 龟裂deformation 变形 edge 切边碎片edge crack 裂边 fading 退色filler speak 填充料斑 fissure 裂纹flange wrinkle 凸缘起皱 flaw 刮伤flow mark 流痕 galling 毛边glazing 光滑 gloss 光泽grease pits 污斑 grinding defect 磨痕haircrack 发裂 haze 雾度incrustation 水锈 indentation 压痕internal porosity 内部气孔mismatch 偏模mottle 斑点 necking 缩颈nick 割痕 orange peel 橘皮状表面缺陷overflow 溢流 peeling 剥离pit 坑 pitting corrosion 点状腐蚀plate mark 模板印痕 pock 麻点pock mark 痘斑 resin streak 树脂流纹resin wear 树脂脱落 riding 凹陷sagging 松垂 saponification 皂化scar 疤痕 scrap 废料scrap jam 废料阻塞 scratch 刮伤/划痕scuffing 深冲表面划伤 seam 裂痕shock line 模口挤痕 short shot 充填不足shrinkage pool 凹孔 sink mark 凹痕skin inclusion 表皮折叠straightening 矫直streak 条状痕 surface check 表面裂痕surface roughening 橘皮状表皮皱折surging 波动sweat out 冒汗 torsion 扭曲warpage 翘曲 waviness 波痕webbing 熔塌 weld mark 焊痕whitening 白化 wrinkle 皱纹组装、冲压、喷漆等专业词汇Assembly line组装线Layout布置图Conveyer流水线物料板Rivet table拉钉机Rivet gun拉钉枪Screw driver起子Electric screw driver电动起子Pneumatic screw driver气动起子worktable 工作桌OOBA开箱检查fit together组装在一起fasten锁紧(螺丝)fixture 夹具(治具)pallet栈板barcode条形码barcode scanner条形码扫描仪fuse together熔合fuse machine热熔机repair修理operator作业员QC品管supervisor 课长ME制造工程师MT制造生技cosmetic inspect外观检查inner parts inspect内部检查thumb screw大头螺丝lbs.inch镑、英寸EMI gasket导电条front plate前板rear plate后板chassis |'∫[$aelig]si| 基座bezel panel面板power button电源按键reset button重置键Hi-pot test of SPS高源高压测试Voltage switch of SPS电源电压接柆键sheet metal parts 冲件plastic parts塑料件SOP制造作业程序material check list物料检查表work cell工作间trolley台车carton纸箱sub-line支线left fork叉车personnel resource department 人力资源部production department生产部门planning department企划部QC Section品管科stamping factory冲压厂painting factory烤漆厂molding factory成型厂common equipment常用设备uncoiler and straightener整平机punching machine 冲床robot机械手hydraulic machine油压机lathe车床planer |'plein[$#61611]|刨床miller铣床grinder磨床driller钻床linear cutting线切割electrical sparkle电火花welder电焊机staker=reviting machine铆合机position职务president董事长general manager总经理special assistant manager特助factory director厂长department director部长deputy manager |'depjuti| =vice manager副理section supervisor课长deputy section supervisor =vice section superisor 副课长group leader/supervisor组长line supervisor线长assistant manager助理to move, to carry, to handle搬运be put in storage入库pack packing包装to apply oil擦油to file burr 锉毛刺final inspection终检to connect material接料to reverse material 翻料wet station沾湿台Tiana天那水cleaning cloth抹布to load material上料to unload material卸料to return material/stock to退料scraped |'skr[$aelig]pid|报废scrape ..v.刮;削deficient purchase来料不良manufacture procedure制程deficient manufacturing procedure制程不良oxidation |' ksi'dei[$#61611]n|氧化scratch刮伤dents压痕defective upsiding down抽芽不良defective to staking铆合不良embeded lump|in'bed| |l[$#61657]mp|镶块feeding is not in place送料不到位stamping-missing漏冲production capacity生产力education and training教育与训练proposal improvement提案改善spare parts=buffer备件forklift叉车trailer=long vehicle拖板车compound die合模die locker锁模器pressure plate=plate pinch压板bolt螺栓name of a department部门名称administration/general affairs dept总务部automatic screwdriver电动启子thickness gauge厚薄规gauge(or jig)治具power wire电源线buzzle蜂鸣器defective product label不良标签identifying sheet list标示单screwdriver holder起子插座pedal踩踏板stopper阻挡器flow board流水板hydraulic handjack油压板车forklift叉车pallet栈板glove(s)手套glove(s) with exposed fingers割手套thumb大拇指forefinger食指midfinger中指ring finger无名指little finger小指band-aid创可贴iudustrial alcohol工业酒精alcohol container沾湿台head of screwdriver起子头sweeper扫把mop拖把vaccum cleaner吸尘器rag 抹布garbage container灰箕garbage can垃圾箱garbage bag垃圾袋chain链条jack升降机production line流水线chain链条槽magnetizer加磁器lamp holder灯架to mop the floor拖地to clean the floor扫地to clean a table擦桌子air pipe 气管packaging tool打包机packaging打包missing part漏件wrong part错件excessive defects过多的缺陷critical defect极严重缺陷major defect主要缺陷minor defect次要缺陷not up to standard不合规格dimension/size is a little bigger尺寸偏大(小) cosmetic defect外观不良slipped screwhead/slippery screw head螺丝滑头slipped screwhead/shippery screw thread滑手speckle斑点mildewed=moldy=mouldy发霉rust生锈deformation变形burr(金属)flash(塑件)毛边poor staking铆合不良excesssive gap间隙过大grease/oil stains油污inclusion杂质painting peel off脏污shrinking/shrinkage缩水mixed color杂色scratch划伤poor processing 制程不良poor incoming part事件不良fold of pakaging belt打包带折皱painting make-up补漆discoloration羿色water spots水渍polishing/surface processing表面处理exposed metal/bare metal金属裸露lack of painting烤漆不到位safety安全quality品质delivery deadline交货期cost成本engineering工程die repair模修enterprise plan = enterprise expansion projects企划QC品管die worker模工production, to produce生产equipment设备to start a press开机stop/switch off a press关机classification整理regulation整顿cleanness清扫conservation清洁culture教养qualified products, up-to-grade products良品defective products, not up-to-grade products不良品waste废料board看板feeder送料机sliding rack滑料架defective product box不良品箱die change 换模to fix a die装模to take apart a die拆模to repair a die修模packing material包材basket蝴蝶竺plastic basket胶筐isolating plate baffle plate; barricade隔板carton box纸箱to pull and stretch拉深to put material in place, to cut material, to input 落料to impose lines压线to compress, compressing压缩character die字模to feed, feeding送料transportation运输(be)qualfied, up to grade合格not up to grade, not qualified不合格material change, stock change材料变更feature change 特性变更evaluation评估prepare for, make preparations for 准备parameters参数rotating speed, revolution转速manufacture management制造管理abnormal handling异常处理production unit生产单位lots of production生产批量steel plate钢板roll material卷料manufacture procedure制程operation procedure作业流程to revise, modify修订to switch over to, switch---to throw--over switching over切换engineering, project difficulty工程瓶颈stage die工程模automation自动化to stake, staking, reviting铆合add lubricating oil加润滑油shut die架模shut height of a die架模高度analog-mode device类模器die lifter举模器argon welding氩焊vocabulary for stamping冲压常词汇stamping, press冲压punch press, dieing out press冲床uncoiler & strainghtener整平机feeder送料机rack, shelf, stack料架cylinder油缸robot机械手taker取料机conveyer belt输送带transmission rack输送架top stop上死点bottom stop下死点one stroke一行程inch寸动to continue, cont.连动to grip(material)吸料location lump, locating piece, block stop 定位块reset复位smoothly顺利dent压痕scratch刮伤deformation变形filings铁削to draw holes抽孔inquiry, search for查寻to stock, storage, in stock库存receive领取approval examine and verify审核processing, to process加工delivery, to deliver 交货to return delivenry to. to send delinery back to retrn of goods退货registration登记registration card登记卡to control管制to put forward and hand in提报safe stock安全库存acceptance = receive验收to notice通知application form for purchase请购单consume, consumption消耗to fill in填写abrasion磨损reverse angle = chamfer倒角character die字模to collect, to gather收集failure, trouble故障statistics统计demand and supply需求career card履历卡to take apart a die卸下模具to load a die装上模具to tight a bolt拧紧螺栓to looser a bolt拧松螺栓to move away a die plate移走模板easily damaged parts易损件standard parts标准件breaking.(be)broken,(be)cracked 断裂to lubricate润滑common vocabulary for die engineering模具工程常用词汇die 模具figure file, chart file图档cutting die, blanking die冲裁模progressive die, follow (-on)die连续模compound die复合模punched hole冲孔panel board镶块to cutedges=side cut=side scrap切边to bending折弯to pull, to stretch拉伸Line streching, line pulling线拉伸engraving, to engrave刻印upsiding down edges翻边to stake铆合designing, to design设计design modification设计变化die block模块folded block折弯块sliding block滑块location pin定位销lifting pin顶料销die plate, front board模板padding block垫块stepping bar垫条upper die base上模座lower die base下模座upper supporting blank上承板upper padding plate blank上垫板spare dies模具备品spring 弹簧bolt螺栓document folder活页夹file folder资料夹to put file in order整理资料spare tools location手工备品仓first count初盘人first check初盘复棹人second count 复盘人second check复盘复核人equipment设备waste materials废料work in progress product在制品casing = containerazation装箱quantity of physical invetory second count 复盘点数量quantity of customs count会计师盘,点数量the first page第一联filed by accounting department for reference会计部存查end-user/using unit(department)使用单位summary of year-end physical inventory bills年终盘点截止单据汇总表bill name单据名称This sheet and physical inventory list will be sent to accounting department together (Those of NHK will be sent to financial department)本表请与盘点清册一起送会计部-(NHK厂区送财会部)Application status records of year-end physical inventory List and physical inventory card 年终盘点卡与清册使用-状况明细表blank and waste sheet NO.空白与作废单号plate电镀mold成型material for engineering mold testing工程试模材料not included in physical inventory不列入盘点sample样品incoming material to be inspected进货待验description品名steel/rolled steel钢材material statistics sheet物料统计明细表meeting minutes会议记录meeting type 会别distribution department分发单位location地点chairman主席present members出席人员subject主题conclusion结论decision items决议事项responsible department负责单位pre-fixed finishing date预定完成日approved by / checked by / prepared by核准/审核/承办PCE assembly production schedule sheetPCE组装厂生产排配表model机钟work order工令revision版次remark备注production control confirmation生产确认checked by初审approved by核准department部门stock age analysis sheet库存货龄分析表on-hand inventory现有库存available material良品可使用obsolete material良品已呆滞to be inspected or reworked待验或重工total合计cause description原因说明part number/ P/N 料号type形态item/group/class类别quality品质prepared by制表notes说明year-end physical inventory difference analysis sheet年终盘点差异分析表physical inventory盘点数量physical count quantity账面数量difference quantity差异量cause analysis原因分析raw materials原料materials物料finished product成品semi-finished product半成品packing materials包材good product/accepted goods/ accepted parts/good parts良品defective product/non-good parts不良品disposed goods处理品warehouse/hub仓库on way location在途仓oversea location海外仓spare parts physical inventory list备品盘点清单spare molds location模具备品仓skid/pallet栈板tox machine自铆机wire EDM线割EDM放电机coil stock卷料sheet stock片料tolerance工差score=groove压线cam block滑块pilot导正筒trim剪外边pierce剪内边drag form压锻差pocket for the punch head挂钩槽slug hole废料孔feature die公母模expansion dwg展开图radius半径shim(wedge)楔子torch-flame cut火焰切割set screw止付螺丝form block折刀stop pin定位销round pierce punch=die button圆冲子shape punch=die insert异形子stock locater block定位块under cut=scrap chopper清角active plate活动板baffle plate挡块cover plate盖板male die公模female die母模groove punch压线冲子air-cushion eject-rod气垫顶杆spring-box eject-plate弹簧箱顶板bushing block衬套insert 入块club car高尔夫球车capability能力parameter参数factor系数phosphate皮膜化成viscosity涂料粘度alkalidipping脱脂main manifold主集流脉bezel斜视规blanking穿落模dejecting顶固模demagnetization去磁;消磁high-speed transmission高速传递heat dissipation热传rack上料degrease脱脂rinse水洗alkaline etch龄咬desmut剥黑膜D.I. rinse纯水次Chromate铬酸处理Anodize阳性处理seal封孔revision版次part number/P/N料号good products良品scraped products报放心品defective products不良品finished products成品disposed products处理品barcode条形码flow chart流程窗体assembly组装stamping冲压molding成型spare parts=buffer备品coordinate坐标dismantle the die折模auxiliary fuction辅助功能poly-line多义线heater band 加热片thermocouple热电偶sand blasting喷沙grit 砂砾derusting machine除锈机degate打浇口dryer烘干机induction感应induction light感应光response=reaction=interaction感应ram连杆edge finder巡边器concave凸convex凹short射料不足nick缺口speck瑕疪shine亮班splay 银纹gas mark焦痕delamination起鳞cold slug冷块blush 导色gouge沟槽;凿槽satin texture段面咬花witness line证示线patent专利grit沙砾granule=peuet=grain细粒grit maker抽粒机cushion缓冲magnalium镁铝合金magnesium镁金metal plate钣金lathe车mill锉plane刨grind磨drill铝boring镗blinster气泡fillet镶;嵌边through-hole form通孔形式voller pin formality滚针形式cam driver铡楔shank摸柄crank shaft曲柄轴augular offset角度偏差velocity速度production tempo生产进度现状torque扭矩spline=the multiple keys花键quenching淬火tempering回火annealing退火carbonization碳化alloy合金tungsten high speed steel钨高速的moly high speed steel钼高速的organic solvent有机溶剂bracket小磁导liaison联络单volatile挥发性resistance电阻ion离子titrator滴定仪beacon警示灯coolant冷却液crusher破碎机模具工程类plain die简易模pierce die冲孔模forming die成型模progressive die连续模gang dies复合模shearing die剪边模riveting die铆合模pierce冲孔forming成型(抽凸,冲凸)draw hole抽孔bending折弯trim切边emboss凸点dome凸圆semi-shearing半剪stamp mark冲记号deburr or coin压毛边punch riveting冲压铆合side stretch侧冲压平reel stretch卷圆压平groove压线blanking下料stamp letter冲字(料号) shearing剪断tick-mark nearside正面压印tick-mark farside反面压印冲压名称类extension dwg展开图procedure dwg工程图die structure dwg模具结构图material材质material thickness料片厚度factor系数upward向上downward向下press specification冲床规格die height range适用模高die height闭模高度burr毛边gap间隙weight重量total wt.总重量punch wt.上模重量五金零件类inner guiding post内导柱inner hexagon screw内六角螺钉dowel pin固定销coil spring弹簧lifter pin顶料销eq-height sleeves=spool等高套筒pin销lifter guide pin浮升导料销guide pin导正销wire spring圆线弹簧outer guiding post外导柱stop screw止付螺丝located pin定位销outer bush外导套模板类top plate上托板(顶板)top block上垫脚punch set上模座punch pad上垫板punch holder上夹板stripper pad脱料背板up stripper上脱料板male die公模(凸模)feature die公母模female die母模(凹模)upper plate上模板lower plate下模板die pad下垫板die holder下夹板die set下模座bottom block下垫脚bottom plate下托板(底板)stripping plate内外打(脱料板)outer stripper外脱料板inner stripper内脱料板lower stripper下脱料板零件类punch冲头insert入块(嵌入件)deburring punch压毛边冲子groove punch压线冲子stamped punch字模冲子round punch圆冲子special shape punch异形冲子bending block折刀roller滚轴baffle plate挡块located block定位块supporting block for location定位支承块air cushion plate气垫板air-cushion eject-rod气垫顶杆trimming punch切边冲子stiffening rib punch = stinger 加强筋冲子ribbon punch压筋冲子reel-stretch punch卷圆压平冲子guide plate定位板sliding block滑块sliding dowel block滑块固定块active plate活动板lower sliding plate下滑块板upper holder block上压块upper mid plate上中间板spring box弹簧箱spring-box eject-rod弹簧箱顶杆spring-box eject-plate弹簧箱顶板bushing bolck衬套cover plate盖板guide pad导料块塑件&模具相关英文compre sion molding压缩成型flash mold溢流式模具plsitive mold挤压式模具split mold分割式模具cavity型控母模core模心公模taper锥拔leather cloak仿皮革shiver饰纹flow mark流痕welding mark溶合痕post screw insert螺纹套筒埋值self tapping screw自攻螺丝striper plate脱料板piston活塞cylinder汽缸套chip细碎物handle mold手持式模具移转成型用模具encapsulation molding低压封装成型射出成型用模具two plate两极式(模具)well type蓄料井insulated runner绝缘浇道方式hot runner热浇道runner plat浇道模块valve gate阀门浇口band heater环带状的电热器spindle阀针spear head刨尖头slag well冷料井cold slag冷料渣air vent排气道h=0.02~0.05mmw=3.2mmL=3~5mmwelding line熔合痕eject pin顶出针knock pin顶出销return pin回位销反顶针sleave套筒stripper plate脱料板insert core放置入子runner stripper plate浇道脱料板guide pin导销eject rod (bar)(成型机)顶业捧subzero深冷处理three plate三极式模具runner system浇道系统stress crack应力电裂orientation定向sprue gate射料浇口,直浇口nozzle射嘴sprue lock pin料头钩销(拉料杆)slag well冷料井side gate侧浇口edge gate侧缘浇口tab gate搭接浇口film gate薄膜浇口flash gate闸门浇口slit gate缝隙浇口fan gate扇形浇口dish gate因盘形浇口H=F=1/2t~1/5tT=2.5~3.5mmdiaphragm gate隔膜浇口ring gate环形浇口subarine gate潜入式浇口tunnel gate隧道式浇口pin gate针点浇口Φ0.8~1.0mmRunner less无浇道(sprue less)无射料管方式long nozzle延长喷嘴方式sprue浇口;溶渣品质人员名称类QC quality control 品质管理人员FQC final quality control 终点质量管理人员IPQC in process quality control 制程中的质量管理人员OQC output quality control 最终出货质量管理人员IQC incoming quality control 进料质量管理人员TQC total quality control 全面质量管理POC passage quality control 段检人员QA quality assurance 质量保证人员OQA output quality assurance 出货质量保证人员QE quality engineering 品质工程人员品质保证类FAI first article inspection 新品首件检查FAA first article assurance 首件确认TVR tool verification report 模具确认报告3B 3B 模具正式投产前确认CP capability index 能力指数CPK capability index of process 模具制程能力参数SSQA standardized supplier quality 合格供货商品质评估OOBA out of box audit 开箱检查QFD quality function deployment 品质机能展开FMEA failure model effectiveness analysis 失效模式分析8 disciplines 8项回复内容FA final audit 最后一次稽核CAR corrective action request 改正行动要求corrective action report 改正行动报告FQC运作类AQL Acceptable Quality Level 运作类允收品质水准S/S Sample size 抽样检验样本大小ACC Accept 允收REE Reject 拒收CR Critical 极严重的MAJ Major 主要的MIN Minor 轻微的AOQ Average Output Quality 平均出厂品质AOQL Average Output Quality Level 平均出厂品质Q/R/S Quality/Reliability/Service 品质/可靠度服务MIL-STD Military-Standard 军用标准S I-S IV Special I-Special IV 特殊抽样水准等级P/N Part Number 料号L/N Lot Number 特采AOD Accept On Deviation 特采UAI Use As It 首件检查报告FPIR First Piece Inspection Report 百万分之一PPM Percent Per Million 批号制程统计品管专类SPC Statistical Process Control 统计制程管制SQC Statistical Quality Control 统计质量管理R Range 全距AR Averary Range 全距平均值UCL Upper Central Limit 管制上限LCL Lower Central Limit 管制下限MAX Maximum 最大值MIN Minimum 最小值GRR Gauge Reproducibility&Repeatability 量具之再制性及重测性判断量可靠与否DIM Dimension 尺寸DIA Diameter 直径FREQ Frequency 频率N Number 样品数其它品质术语类QCC Quality Control Circle 品质圈QIT Quality Improvement Team 品质改善小组PDCA Plan Do Check Action 计划执行检查总结ZD Zero Defect 零缺点QI Quality Improvement 品质改善QP Quality Policy 目标方针TQM Total Quality Management 全面品质管理MRB Material Reject Bill 退货单LQL Limiting Quality Level 最低品质水准RMA Return Material Audit 退料认可QAN Quality Amelionrate Notice 品质改善活动ADM Absolute Dimension Measuremat 全尺寸测量QT Quality Target 品质目标7QCTools 7 Quality Controll Tools 品管七大手法通用之件类ECN Engineering Change Notes 工程变更通知(供货商)ECO Engineering Change Order 工程改动要求(客户)PCN Process Change Notice 工序改动通知PMP Product Management Plan 生产管制计划SIP Specification In Process 制程检验规格SOP Standard Operation Procedure 制造作业规范IS Inspection Specification 成品检验规范BOM Bill Of Material 物料清单PS Package Specification 包装规范SPEC Specification 规格DWG Drawing 图面系统文件类QC Quality System 品质系统ES Engineering Standarization 工程标准CGOO China General PCE龙华厂文件H Huston (美国)休斯敦C Compaq (美国)康伯公司C China 中国大陆A Assembly 组装(厂)S Stamping 冲压(厂)P Painting 烤漆(厂)I Intel 英特尔公司T TAIWAN 台湾IWS International Workman Standard 工艺标准ISO International Standard Organization 国际标准化组织GS General Specification 一般规格CMCS C-China M-Manufact C-Compaq S-Stamping Compaq产品在龙华冲压厂制造作业规范CQCA Q-Quality A-Assembly Compaq产品在龙华组装厂品管作业规范CQCP P-Painting Compaq产品在龙华烤漆厂品管作业规范部类PMC Production & Material Control 生产和物料控制PPC Production Plan Control 生产计划控制MC Material Control 物料控制ME Manafacture Engineering 制造工程部PE Project Engineering 产品工程部A/C Accountant Dept 会计部P/A Personal & Administration 人事行政部DC Document Center 资料中心QE Quality Engineering 品质工程(部)QA Quality Assurance 品质保证(处)QC Quality Control 质量管理(课)PD Product Department 生产部LAB Labratry 实验室IE Industrial Engineering 工业工程R&D Research & Design 设计开发部P Painting 烤漆(厂)A Asssembly 组装(厂)S Stamping 冲压(厂)生产类PCS Pieces 个(根,块等)PRS Pairs 双(对等)CTN Carton 卡通箱PAL Pallet/skid 栈板PO Purchasing Order 采购订单MO Manufacture Order 生产单D/C Date Code 生产日期码ID/C Identification Code (供货商)识别码SWR Special Work Request 特殊工作需求L/N Lot Number 批号P/N Part Number 料号其它OEM Original Equipment Manufacture 原设备制造PCE Personal Computer Enclosure 个人计算机外设PC Personal Computer 个人计算机CPU Central Processing Unit 中央处理器SECC SECC` 电解片SGCC SGCC 热浸镀锌材料NHK North of Hongkong 中国大陆PRC People's Republic of China 中国大陆U.S.A the United States of America 美国A.S.A.P As Soon As Possible 尽可能快的E-MAIL Electrical-Mail 电子邮件N/A Not Applicable 不适用QTY Quantity 数量VS 以及REV Revision 版本JIT Just In Time 零库存I/O Input/Output 输入/输出OK Ok 好NG Not Good 不行,不合格C=0 Critical=0 极严重不允许ESD Electry-static Discharge 静电排放5S 希腊语整理,整顿,清扫,清洁,教养ATIN Attention 知会CC Carbon Copy 副本复印相关人员APP Approve 核准,认可,承认CHK Check 确认AM Ante Meridian 上午PM Post Meridian 下午CD Compact Disk 光盘CD-ROM Compact Disk Read-Only Memory 只读光盘FDD Floppy Disk Drive 软盘机HDD Hard Disk Drive 碟碟机REF Reference 仅供参考CONN Connector 连接器CAV Cavity 模穴CAD Computer Aid Design 计算器辅助设计ASS'Y Assembly 装配,组装MAT'S Material 材料IC Integrated Circuit 集成电路T/P True Position 真位度TYP Type 类型WDR Weekly Delivery Requitement 周出货需求C?T Cycle Time 制程周期L/T Lead Time 前置时间(生产前准备时间)S/T Standard Time 标准时间P/M Product Market 产品市场3C Computer,Commumcation,Consumer electronic's 消费性电子5WIH When,Where,Who,What,Why,How to5M Man,Machine,Material,Method,Measurement4MIH Man,Materia,Money,Method,Time 人力,物力,财务,技术,时间(资源)SQA Strategy Quality Assurance 策略品质保证DQA Desigh Quality Assurance 设计品质保证MQA Manufacture Quality Assurance 制造品质保证SSQA Sales and service Quality Assurance 销售及服务品质保证LRR Lot Rejeet Rate 批退率BS Brain storming 脑力激荡EMI Electronic Magnetion Inspect 高磁测试FMI Frequency Modulatim Inspect 高频测试B/M Boar/Molding(flat cable)C/P Connector of PCA/P AssemblySPS Switching power supply 电源箱DT Desk Top 卧式(机箱)MT Mini-Tower 立式(机箱)DVD Digital Vedio DiskVCD Vdeio Compact DiskLCD Liquid Crystal DisplayCAD Computer AID DesignCAM Computer AID ManufacturingCAE Computer AID EngineeringABIOS Achanced Basic in put/output system 先进的基本输入/输出系统CMOS Complemeruary Metoll Oxide Semiconductor 互补金属氧化物半导体PDA Personal Digital Assistant 个人数字助理IC Integrated Circuit 集成电路ISA Industry Standard Architecture 工业标准体制结构MCA Micro Channel Architecture 微信道结构EISA Extended Industry Standard Architecture 扩充的工业标准结构SIMM Single in-line memory module 单项导通汇流组件DIMM Dual in-line Memory Module 双项导通汇流组件LED Light-Emitting Diode 发光二级管FMEA Failure Mode Effectivenes 失效模式分析W/H Wire Harness 金属线绪束集组件F/C Flat Calle 排线PCB Printed Circuit Board 印刷电路板CAR Correction Action Report 改善报告NG Not Good 不良WPR Weekly Delivery Requirement 周出货要求PPM Parts Per Million 百万分之一TPM Total Production Maintenance 全面生产保养MRP Material Requiremcnt Planning 物料需计划OC Operation System 操作系统TBA To Be Design 待定,定缺D/C Drawing ChangeP/P Plans & ProceduneEMI Electrical-Music Industry 电子音乐工业RFI Read Frequency Input 读频输入MMC Maximum Material ConditionMMS Maximum Material SizeLMC Least Material ConditionLMS Least Material Size------------------------------------------------------------------------------------------模具技术用语各种模具常用成形方式accurate die casting 精密压铸powder forming 粉末成形calendaring molding 压延成形powder metal forging 粉末锻造cold chamber die casting 冷式压铸precision forging 精密锻造cold forging 冷锻press forging 冲锻compacting molding 粉末压出成形rocking die forging 摇动锻造compound molding 复合成形rotary forging 回转锻造compression molding 压缩成形rotational molding 离心成形dip mold 浸渍成形rubber molding 橡胶成形encapsulation molding 注入成形sand mold casting 砂模铸造extrusion molding 挤出成形shell casting 壳模铸造foam forming 发泡成形sinter forging 烧结锻造forging roll 轧锻six sides forging 六面锻造gravity casting 重力铸造slush molding 凝塑成形hollow(blow) molding 中空(吹出)成形squeeze casting 高压铸造hot chamber die casting 热室压铸swaging 挤锻hot forging 热锻transfer molding 转送成形injection molding 射出成形warm forging 温锻investment casting 精密铸造matched die method 对模成形法laminating method 被覆淋膜成形low pressure casting 低压铸造lost wax casting 脱蜡铸造matched mould thermal forming 对模热成形模各式模具分类用语bismuth mold 铋铸模landed plunger mold 有肩柱塞式模具burnishing die 挤光模landed positive mold 有肩全压式模具button die 镶入式圆形凹模loading shoe mold 料套式模具center-gated mold 中心浇口式模具loose detail mold 活零件模具chill mold 冷硬用铸模loose mold 活动式模具clod hobbing 冷挤压制模louvering die 百叶窗冲切模composite dies 复合模具manifold die 分歧管模具counter punch 反凸模modular mold 组合式模具double stack mold 双层模具multi-cavity mold 多模穴模具electroformed mold 电铸成形模multi-gate mold 复式浇口模具expander die 扩径模offswt bending die 双折冷弯模具extrusion die 挤出模palletizing die 迭层模family mold 反套制品模具plaster mold 石膏模blank through dies 漏件式落料模porous mold 通气性模具duplicated cavity plate 复板模positive mold 全压式模具fantail die 扇尾形模具pressure die 压紧模fishtail die 鱼尾形模具profile die 轮廓模flash mold 溢料式模具progressive die 顺序模gypsum mold 石膏铸模protable mold 手提式模具hot-runner mold 热流道模具prototype mold 雏形试验模具ingot mold 钢锭模punching die 落料模lancing die 切口模raising(embossing) 压花起伏成形re-entrant mold 倒角式模具sectional die 拼合模runless injection mold 无流道冷料模具sectional die 对合模具segment mold 组合模semi-positive mold 半全压式模具shaper 定型模套single cavity mold 单腔模具solid forging die 整体锻模split forging die 拼合锻模split mold 双并式模具sprueless mold 无注道残料模具squeezing die 挤压模stretch form die 拉伸成形模sweeping mold 平刮铸模swing die 振动模具three plates mold 三片式模具trimming die 切边模unit mold 单元式模具universal mold 通用模具unscrewing mold 退扣式模具yoke type die 轭型模模具厂常用之标准零配件air vent vale 通气阀anchor pin 锚梢angular pin 角梢baffle 调节阻板angular pin 倾斜梢baffle plate 折流檔板ball button 球塞套ball plunger 定位球塞ball slider 球塞滑块binder plate 压板blank holder 防皱压板blanking die 落料冲头bolster 上下模板bottom board 浇注底板bolster 垫板bottom plate 下固定板bracket 扥架bumper block 缓冲块buster 堵口casting ladle 浇注包casting lug 铸耳cavity 模穴(模仁)cavity retainer plate 模穴扥板center pin 中心梢clamping block 锁定块coil spring 螺旋弹簧cold punched nut 冷冲螺母cooling spiral 螺旋冷却栓core 心型core pin 心型梢cotter 开口梢cross 十字接头cushion pin 缓冲梢diaphragm gate 盘形浇口die approach 模头料道die bed 型底die block 块形模体die body 铸模座die bush 合模衬套die button 冲模母模die clamper 夹模器die fastener 模具固定用零件die holder 母模固定板die lip 模唇die plate 冲模板die set 冲压模座direct gate 直接浇口dog chuck 爪牙夹头dowel 定位梢dowel hole 导套孔dowel pin 合模梢dozzle 辅助浇口dowel pin 定位梢draft 拔模锥度draw bead 张力调整杆drive bearing 传动轴承ejection pad 顶出衬垫ejector 脱模器ejector guide pin 顶出导梢ejector leader busher 顶出导梢衬套ejector pad 顶出垫ejector pin 顶出梢ejector plate 顶出板ejector rod 顶出杆ejector sleeve 顶出衬套ejector valve 顶出阀eye bolt 环首螺栓filling core 椿入蕊film gate 薄膜形浇口finger pin 指形梢finish machined plate 角形模板finish machined round plate 圆形模板fixed bolster plate 固定侧模板flanged pin 带凸缘销flash gate 毛边形浇口flask 上箱floating punch 浮动冲头gate 浇口gate land 浇口面gib 凹形拉紧销goose neck 鹅颈管guide bushing 引导衬套guide pin 导梢guide post 引导柱guide plate 导板guide rail 导轨head punch 顶镦冲头headless punch 直柄冲头heavily tapered solid 整体模蕊盒hose nippler 管接头impact damper 缓冲器injection ram 压射柱塞inlay busher 嵌入衬套inner plunger 内柱塞inner punch 内冲头insert 嵌件insert pin 嵌件梢king pin 转向梢king pin bush 主梢衬套knockout bar 脱模杵land 合模平坦面land area 合模面leader busher 导梢衬套lifting pin 起模顶销lining 内衬locating center punch 定位中心冲头locating pilot pin 定位导梢locating ring 定位环lock block 压块locking block 定位块locking plate 定位板loose bush 活动衬套making die 打印冲子manifold block 歧管档块master plate 靠模样板match plate 分型板mold base 塑料模座mold clamp 铸模紧固夹mold platen 模用板moving bolster 换模保持装置moving bolster plate 可动侧模板one piece casting 整体铸件。
VW_01014 大众图纸图框及字体规范
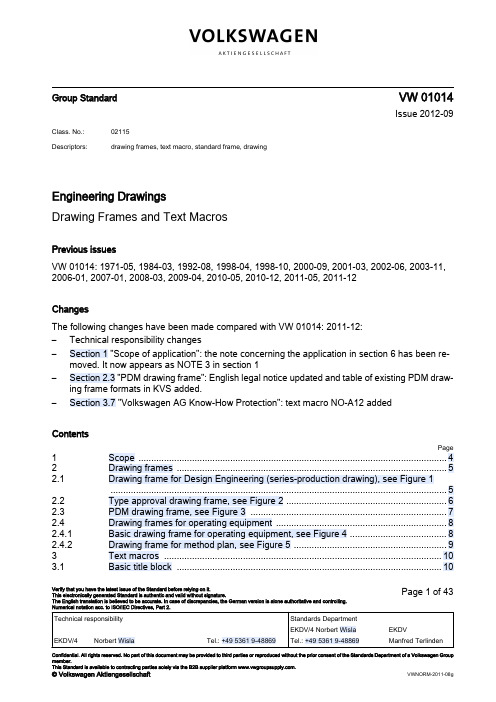
Engineering DrawingsDrawing Frames and Text MacrosPrevious issuesVW 01014: 1971-05, 1984-03, 1992-08, 1998-04, 1998-10, 2000-09, 2001-03, 2002-06, 2003-11,2006-01, 2007-01, 2008-03, 2009-04, 2010-05, 2010-12, 2011-05, 2011-12ChangesThe following changes have been made compared with VW 01014: 2011-12:–Technical responsibility changes–Section 1 "Scope of application": the note concerning the application in section 6 has been re‐moved. It now appears as NOTE 3 in section 1–Section 2.3 "PDM drawing frame": English legal notice updated and table of existing PDM draw‐ing frame formats in KVS added.–Section 3.7 "Volkswagen AG Know-How Protection": text macro NO-A12 added ContentsPageScope .........................................................................................................................4Drawing frames ..........................................................................................................5Drawing frame for Design Engineering (series-production drawing), see Figure 1....................................................................................................................................5Type approval drawing frame, see Figure 2 ...............................................................6PDM drawing frame, see Figure 3 .............................................................................7Drawing frames for operating equipment ...................................................................8Basic drawing frame for operating equipment, see Figure 4 ......................................8Drawing frame for method plan, see Figure 5 ............................................................9Text macros .............................................................................................................10Basic title block .. (10)122.12.22.32.42.4.12.4.233.1Group StandardVW 01014Issue 2012-09Class. No.:02115Descriptors:drawing frames, text macro, standard frame, drawingVerify that you have the latest issue of the Standard before relying on it.This electronically generated Standard is authentic and valid without signature.The English translation is believed to be accurate. In case of discrepancies, the German version is alone authoritative and controlling.Page 1 of 43Confidential. All rights reserved. No part of this document may be provided to third parties or reproduced without the prior consent of the Standards Department of a Volkswagen Group member.This Standard is available to contracting parties solely via the B2B supplier platform .© Volkswagen AktiengesellschaftVWNORM-2011-08gTitle blocks for drawings with restrictions on use .....................................................11Title block for layout drawings (ENT) > A0 ...............................................................12Symbol for European projection method ..................................................................13Change block for formats > A0 .................................................................................13Tolerancing principle as per VW 01054 ...................................................................13Volkswagen Group know-how protection .................................................................13Drawing field ............................................................................................................14Lower left corner of drawing for formats > A0 ..........................................................14Left drawing edge for formats > A0 ..........................................................................14Explanation of parenthesized dimensions for formats > A0 (lower left corner ofdrawing field) ............................................................................................................14References for formats > A0 ....................................................................................15Migration from CATIA V4 to CATIA V5 ....................................................................15Parts marking ...........................................................................................................15Part number assignment drawn / symmetrically opposite ........................................15Note on utilization of scrap material .........................................................................16NO-F1 Drawings with multiple sheets ......................................................................16Repeating and unchanging notes, mostly on body components ..............................16Drawing only for the company stated .......................................................................16Note on parts which are subject to build sample approval (BMG) ...........................17Notes on testing as per Technical Supply Specifications (TL) .................................17Note on type approval ..............................................................................................17Note on undimensioned design models in the data record ......................................17Note on open-air weathering ....................................................................................17Note on model approval ...........................................................................................17Note on master model ..............................................................................................18Note on second original, font size 7 mm ..................................................................18Note on second original, font size 3,5 mm ...............................................................18Note on heavy-duty component ...............................................................................18Note on mandatory type approval ............................................................................19Note on avoidance of hazardous substances ..........................................................19Note on other relevant drawings ..............................................................................19Note on undimensioned bend and trim radii ............................................................19Note on simplified representation .............................................................................19Note on flawless condition of surfaces .....................................................................19Note on material for form tool in grain area ..............................................................20Table for RPS ...........................................................................................................20Note on emission behavior .......................................................................................20Note on length dimensions to be measured up to relevant functional datum plane ..................................................................................................................................20Note on related tolerances for nominal dimension ranges up to relevant functional datum plane .............................................................................................................21Note on tolerances of surfaces as compared to the data record and defined RPS..................................................................................................................................21Note on tolerances of marked surfaces as compared to the data record anddefined RPS .............................................................................................................21Note on tolerances of marked and limited surfaces as compared to the datarecord and defined RPS ...........................................................................................21Note on tolerances of marked edges as compared to the data record and defined RPS ..........................................................................................................................21Note on alternative materials and surface protection types .....................................22Note on color and grain .. (22)3.23.33.43.53.63.744.14.24.34.44.54.64.74.84.94.104.114.124.134.144.154.164.174.184.194.204.214.224.234.244.254.264.274.284.294.304.314.324.334.344.354.364.374.38Page 2VW 01014: 2012-09Note on temperature resistance ...............................................................................22Note on color consistency ........................................................................................22Note on lightfastness ................................................................................................22Note on fixing, clamping and contact surface ..........................................................23Note on related finished part drawing ......................................................................23Note on material specifications, complete ................................................................23Note on material specifications, subdivided .............................................................24Note on optional welding technology .......................................................................24Note on flammability features ...................................................................................24Note on table containing gear tooth data .................................................................25Note on weight indication .........................................................................................25Note on amine emission of foam parts .....................................................................25Note on cleanliness requirements for engine components ......................................25Countersinks for internal threads .............................................................................26Testing of rolled bushings ........................................................................................26Table for limit dimensions ........................................................................................26Detail drawing for radius under screw head, mostly for standard part drawings (27)Test specification for disk wheels .............................................................................27Test specification for brake drums ...........................................................................28General tolerances for castings ...............................................................................28General tolerances for forgings ................................................................................29Coordinate dimensioning for tubes and bars ...........................................................30Bill of materials for layout drawings (ENT) ...............................................................30Distribution list for layout drawings (ENT) ................................................................31Text macros for operating equipment ......................................................................31Title block for individual part .....................................................................................31Note on pass direction, left .......................................................................................32Note on pass direction, right ....................................................................................32Title block for operating equipment label .................................................................32General tolerances for nominal dimensions without tolerance specification ............32Note on simplified drawing specifications on surface roughnesses .........................33Permissible deviations for nominal sizes without tolerance specification onweldments ................................................................................................................33Permissible deviations for nominal dimensions without tolerance specificationson flame-cut parts ....................................................................................................33Note on parts used ...................................................................................................34Note on rolled flame-cutting template plots ..............................................................34Note on "Add ½ kerf" ................................................................................................34Note on "designed" and "symmetrical opposite" ......................................................34Text macros for the "3D drawingless process" (3DZP – German abbreviation) ......35VW copyright ............................................................................................................35Note on restriction on use ........................................................................................35Note on type approval documentation and type approval number ...........................35Draft number ............................................................................................................36Note on engineering project number ........................................................................36Note on safety documentation .................................................................................36Recycling requirements as per VW 91102 ...............................................................36All dimensions apply to the finished part including surface protection .....................36Surface roughness as per VW 13705 and VDA 2005 ..............................................36Surface roughness as per VW 13705 and VDA 2005 (reference without symbol) (37)4.394.404.414.424.434.444.454.464.474.484.494.504.514.524.534.544.554.564.574.584.594.604.614.6255.15.25.35.45.55.65.75.85.95.105.115.1266.16.26.36.46.56.66.76.86.96.9.1Page 3VW 01014: 2012-09Surface roughness as per VW 13705 and VDA 2005 (reference with symbol) .......37Surface roughness as per VW 13705 and VDA 2005 (reference with symbol,collective specification 1) .........................................................................................38Surface roughness as per VW 13705 and VDA 2005 (reference with symbol,collective specification 2) .........................................................................................39Workpiece edges as per VW 01088 .........................................................................39Workpiece edges as per VW 01088 (reference without symbol) .............................40Workpiece edges as per VW 01088 (reference with symbol) ..................................40Workpiece edges as per VW 01088 (reference with symbol, collectivespecification 1) .........................................................................................................41Workpiece edges as per VW 01088 (reference with symbol, collectivespecification 2) .........................................................................................................42Applicable documents ..............................................................................................426.9.26.9.36.9.46.106.10.16.10.26.10.36.10.47ScopeThis standard applies to the computer-aided graphical representation and presentation of drawing templates, standard frames and text macros for drawings within the Volkswagen Group.NOTE 1 The standardized text macros are subject to drawing standard regulations and are centrally managed by the "Virtual Systems and Standardization" department.NOTE 2 All drawing frames and text macros shown here are available in the appropriate standard system environment of the CAD systems CATIA and Creo Elements/Pro (formerly PRO/E). The PDM drawing frames are also available as IsoDraw and Excel templates in the KVS, and also as Catia V5templates.NOTE 3 The text macros shown in section 6 are for the drawingless process only. The creator and the user of the data must agree whether their process chain allows for the use of documents as per the 3DZP method, and whether this is permissible.1Page 4VW 01014: 2012-09Drawing framesDrawing frame for Design Engineering (series-production drawing), see Figure 1Figure 1 – Drawing frame for Design Engineering (series-production drawing)2 2.1Page 5VW 01014: 2012-09Type approval drawing frame, see Figure 2Figure 2 – Type approval drawing frame2.2 Page 6VW 01014: 2012-09PDM drawing frame, see Figure 3Figure 3 – PDM drawing frame2.3 Page 7VW 01014: 2012-09Drawing frames for operating equipmentBasic drawing frame for operating equipment, see Figure 4Figure 4 – Basic drawing frame for operating equipment2.4 2.4.1Page 8VW 01014: 2012-09Drawing frame for method plan, see Figure 5Figure 5 – Drawing frame for method plan2.4.2 Page 9VW 01014: 2012-09Text macrosBasic title blockFigure 6 – Code no: NO-A1Basic title block for formats > A03 3.1Page 10VW 01014: 2012-09Title blocks for drawings with restrictions on useFigure 7 – Code no: NO-A7 A3The title block may only be used if supplier original drawings are used as modified finished part drawings.Notes on the usage of these title blocks see VW 01058.3.2Title block for layout drawings (ENT) > A0Figure 8 – Code no: NO-A3ENT = Draft3.3Symbol for European projection methodFigure 9 – Code no: NO-A5Change block for formats > A0Figure 10 – Code no: NO-A6Tolerancing principle as per VW 01054Figure 11 – Code no: NO-A11Volkswagen Group know-how protectionFigure 12 – Code no: NO-A123.4 3.5 3.6 3.7Drawing fieldLower left corner of drawing for formats > A0Figure 13 – Code no: NO-B1Left drawing edge for formats > A0Figure 14 – Code no: NO-B3Explanation of parenthesized dimensions for formats > A0 (lower left corner of drawingfield)Figure 15 – Code no: NO-B644.1 4.2 4.3References for formats > A0Figure 16 – Code no: NO-B7Migration from CATIA V4 to CATIA V5Figure 17 – Code no: NO-B8Parts markingFigure 18 – Code no: NO-E2Part number assignment drawn / symmetrically oppositeFigure 19 – Code no: NO-E54.4 4.5 4.6 4.7Note on utilization of scrap materialFigure 20 – Code no.:NO-F1 Drawings with multiple sheetsFigure 21 – Code no: NO-F2Repeating and unchanging notes, mostly on body componentsFigure 22 – Code no: NO-F3Drawing only for the company statedFigure 23 – Code no: NO-F4 (do not use for new designs!)4.8 4.9 4.10 4.11Note on parts which are subject to build sample approval (BMG)Figure 24 – Code no: NO-F5Notes on testing as per Technical Supply Specifications (TL)Figure 25 – Code no: NO-F6Note on type approvalFigure 26 – Code no: NO-F7Note on undimensioned design models in the data recordFigure 27 – Code no: NO-F8Note on open-air weatheringFigure 28 – Code no: NO-F9Note on model approvalFigure 29 – Code no: NO-F104.12 4.13 4.14 4.15 4.16 4.17Note on master modelFigure 30 – Code no: NO-F11Note on second original, font size 7 mmFigure 31 – Code no: NO-F12Note on second original, font size 3,5 mmFigure 32 – Code no: NO-F13Note on heavy-duty componentFigure 33 – Code no: NO-F144.18 4.19 4.20 4.21Note on mandatory type approvalFigure 34 – Code no: NO-F15Note on avoidance of hazardous substancesFigure 35 – Code no: NO-F16Note on other relevant drawingsFigure 36 – Code no: NO-F17Note on undimensioned bend and trim radiiFigure 37 – Code no: NO-F18Note on simplified representationFigure 38 – Code no: NO-F19Note on flawless condition of surfacesFigure 39 – Code no: NO-F204.22 4.23 4.24 4.25 4.26 4.27Note on material for form tool in grain areaFigure 40 – Code no: NO-F22Table for RPSFigure 41 – Code no: NO-F23Note on emission behaviorFigure 42 – Code no: NO-F24Note on length dimensions to be measured up to relevant functional datum planeFigure 43 – Code no: NO-F254.28 4.29 4.30 4.31Note on related tolerances for nominal dimension ranges up to relevant functional datumplaneFigure 44 – Code no: NO-F26Note on tolerances of surfaces as compared to the data record and defined RPSFigure 45 – Code no: NO-F27Note on tolerances of marked surfaces as compared to the data record and defined RPSFigure 46 – Code no: NO-F28Note on tolerances of marked and limited surfaces as compared to the data record anddefined RPSFigure 47 – Code no: NO-F29Note on tolerances of marked edges as compared to the data record and defined RPSFigure 48 – Code no: NO-F304.32 4.33 4.34 4.35 4.36Note on alternative materials and surface protection typesFigure 49 – Code no: NO-F31Note on color and grainFigure 50 – Code no: NO-F32Note on temperature resistanceFigure 51 – Code no: NO-F33Note on color consistencyFigure 52 – Code no: NO-F35Note on lightfastnessFigure 53 – Code no: NO-F364.37 4.38 4.39 4.40 4.41Note on fixing, clamping and contact surfaceFigure 54 – Code no: NO-F37Note on related finished part drawingFigure 55 – Code no: NO-F38Note on material specifications, completeFigure 56 – Code no: NO-F394.42 4.43 4.44Note on material specifications, subdividedFigure 57 – Code no: NO-F40Note on optional welding technologyFigure 58 – Code no: NO-F41Note on flammability featuresFigure 59 – Code no: NO-F424.45 4.46 4.47Note on table containing gear tooth dataFigure 60 – Code no: NO-F43Note on weight indicationFigure 61 – Code no: NO-F44Note on amine emission of foam partsFigure 62 – Code no: NO-F45Note on cleanliness requirements for engine componentsFigure 63 – Code no: NO-F464.48 4.49 4.50 4.51Countersinks for internal threadsFigure 64 – Code no: NO-G0Testing of rolled bushingsFigure 65 – Code no: NO-G1Table for limit dimensionsFigure 66 – Code no: NO-G24.52 4.53 4.54Detail drawing for radius under screw head, mostly for standard part drawingsFigure 67 – Code no: NO-G4Test specification for disk wheelsFigure 68 – Code no: NO-G64.55 4.56Test specification for brake drumsFigure 69 – Code no: NO-G7General tolerances for castingsFigure 70 – Code no: NO-G84.57 4.58General tolerances for forgingsFigure 71 – Code no: NO-G94.59Coordinate dimensioning for tubes and barsFigure 72 – Code no: NO-G10Bill of materials for layout drawings (ENT)Figure 73 – Code no: NO-H14.60 4.61Distribution list for layout drawings (ENT)Figure 74 – Code no: NO-H2Text macros for operating equipmentTitle block for individual partFigure 75 – Code no: R001 individual part4.62 55.1Note on pass direction, leftFigure 76 – Code no: R002 pass direction, leftNote on pass direction, rightFigure 77 – Code no: R003 pass direction, rightTitle block for operating equipment labelFigure 78 – Code no: R004 operating equipment labelGeneral tolerances for nominal dimensions without tolerance specificationFigure 79 – Code no: R005 machining operation5.2 5.35.45.5Note on simplified drawing specifications on surface roughnessesFigure 80 – Code no: R006 surfacesPermissible deviations for nominal sizes without tolerance specification on weldmentsFigure 81 – Code no: R007 welded partsPermissible deviations for nominal dimensions without tolerance specifications on flame-cut partsFigure 82 – Code no: R008 flame-cut parts5.6 5.75.8Note on parts usedFigure 83 – Code no: R009 parts usedNote on rolled flame-cutting template plotsFigure 84 – Code no: R010 flame-cutting templateNote on "Add ½ kerf"Figure 85 – Code no: R011 kerfNote on "designed" and "symmetrical opposite"Figure 86 – Code no: R012 symmetrical opposite5.9 5.105.115.12Text macros for the "3D drawingless process" (3DZP – German abbreviation)The following text macros are not created in CAD systems, but only in the PDM system KVS.The design engineer must add the necessary parameters to the text macros.VW copyrightFigure 87 – Code no: NOZ-01Note on restriction on useLegend P01Company nameFigure 88 – Code no: NOZ-02Note on type approval documentation and type approval numberLegend P01Type approval doc. and type approval numberFigure 89 – Code no: NOZ-036 6.16.26.3Draft numberLegend P01Draft numberFigure 90 – Code no: NOZ-04Note on engineering project numberLegend P01Engineering project numberFigure 91 – Code no: NOZ-05Note on safety documentationLegend P01TLD number (technical guideline for documentation – German abbreviation)Figure 92 – Code no: NOZ-06Recycling requirements as per VW 91102Figure 93 – Code no: NOZ-07All dimensions apply to the finished part including surface protectionFigure 94 – Code no: NOZ-08Surface roughness as per VW 13705 and VDA 2005The design engineer must add the required parameters to the symbols shown here (e.g., Rz value).Two types of text macros (with and without graphical representation) have been defined. Variant NOZ-09 is a reference to Standard VW 13705, additional information possible, but restricted. Variants NOZ-09-01 a to f are reserved for the main surface roughness value. Due to system restrictions,identical symbols cannot be used more than once. For this reason, the symbols in section 6.9.3 and6.4 6.56.66.76.86.9section 6.9.4 must be used for cases of multiple use. If surface roughness values are added as a note, the text macros are placed beneath each other instead of beside each other. This deviating representation has been released for the 3DZP drawingless process.Surface roughness as per VW 13705 and VDA 2005 (reference without symbol)Figure 95 – Code no: NOZ-09Surface roughness as per VW 13705 and VDA 2005 (reference with symbol)Figure 96 – Code no: NOZ-09-01-aFigure 97 – Code no: NOZ-09-01-bFigure 98 – Code no.: NOZ-09-01-cLegend P01Machining allowance (numerical value in mm)P02Production processP03Surface parameter and numerical valueP04if applicable, additional requirement as per VDA 2005P05if applicable, additional requirement as per VDA 2005P06if applicable, second requirement on surface texture (surface parameter,numerical value)P07Specification of the surface groovesLegend P01Letter for simplified drawing specification. Method defined in section "simplified specifi‐cation" in VDA 2005Figure 99 – Code no: NOZ-09-01-d6.9.16.9.2Figure 100 – Code no: NOZ-09-01-e Figure 101 – Code no: NOZ-09-01-fSurface roughness as per VW 13705 and VDA 2005 (reference with symbol, collectivespecification 1)Figure 102 – Code no: NOZ-09-02-aFigure 103 – Code no: NOZ-09-02-bFigure 104 – Code no: NOZ-09-02-cLegend P01Machining allowance (numerical value in mm)P02Production processP03Surface parameter and numerical valueP04if applicable, additional requirement as per VDA 2005P05if applicable, additional requirement as per VDA 2005P06if applicable, second requirement onsurface texture (surface parameter,numerical value) P07Specifica‐tion of thesurface groovesCode no.:Legend P01Letter for simplified drawing specification. Method defined in section "simplified specifi‐cation" in VDA 2005Figure 105 – NOZ-09-02-dFigure 106 – Code no: NOZ-09-02-e Figure 107 – Code no: NOZ-09-02-f6.9.3。
SPECIFICATION NO. 207 Model 207自动焊接系统说明书

Model 207 Automatic GTAW Welding System1.0 IntroductionThe Model 207 is a completely self-contained Gas Tungsten Arc Welding (GTAW) Systemrequiring only input power, inert gas and AMI Welding Head (or manual torch) for operation. Itssmall size makes it especially useful in field applications where portability is required. It is intended for (but not limited to) totally automatic fusion (Autogenous) welding of tube, pipe fittings using AMI Model 9 Tube Welding Heads.The M-207 employs a constant-current Line Inverter as the Weld Current Power source and a 16-bit microprocessor with memory for control of all system functions. All functions are accurate and repeatable to better than +/- 1% providing that line voltage fluctuations and ambient temperatureare within the stated limits.All welding function parameters (weld schedules) are entered via the computer keypad anddisplay. All steps for entering these values are prompted by the display in plain language, nocomputer language or codes are needed. Weld parameters for each specific application are onlyentered one time and are then retained within the system memory (by schedule number).The M-207 is built in a rugged housing that is designed to be portable. Operating AC power issupplied by line cord and gas is supplied by flexible hosing, so permanent connections are notrequired. The system requires an inert gas source with pressure regulator and flow meter (notsupplied).The chassis and power source are air-cooled. Torches and weld heads requiring liquid-coolingmust use the Model 207-CW Cooling Unit which attaches to the M-207 to retain system portability.Multi-level pulsed current, torch rotation speed and timing controls allow the establishment ofoptimum welding procedures on a large variety of materials, sizes and wall thicknesses.This specification details operating ranges, construction and general use. For specific information about operation, consult the Model 207 Operation Manual.2.0 Features and System Configuration2.1 Standard Features: The following are general features described in thisspecification.1. All functions microprocessor-controlled.2. Memory storage for up to 100 weld procedures.3. Ability to create, copy and modify schedules.4. 100/150 Amperes of straight polarity GTAW current.5. Pulsed current controls from 0.05 to 50 PPS.6. Multi-Levels of pulsed current values.7. Continuous or stepped arc rotation controls.Model 207 Automatic GTAW Welding System2.0 Features and System Configuration (continued)8. Operates all AMI Model 9 Fusion Weld Heads.9. Operates Manual Welding Torch.10. Complete automatic operation and timing controls including pre-purge,post-purge, upslope, downslope, function start, and rotation delays andlevel times.11. Built-in fault checks for system status and common operation errors (gascheck, coolant check, etc.)12. Multi-lingual display instructions in English, French or German (otherlanguages will be available at later dates).13. Built-in printer for recording weld procedures.2.2 System Configuration:1. Main Power Supply console including:1. 25-foot input power cord.2. 150 Ampere inverter power source.3. Computer memory module.4. Main computer electronics (weld functions)5. Input gas panel (two port).6. Weld head connect panel including ground, electrode, weld headelectrical connectors, gas output connectors, remote pendantconnector and auxiliary connector.7. 2 line by 40 character display (2 each).8. Membrane key panel including numeric keys and all set up, start/stopkeys (jog, purge, etc.) and program selection keys.9. Printer.2. 15-Foot Weld Head Adapter Cable including1. Weld head arc gas hose.2. Electrode cable.3. Ground cable.4. Weld head electrical cable.2.3 Enclosure Physical Construction1. Material: Aluminum2. Height: 10.9” (276.9 mm) cover closed9.3” (236.2 mm) cover removedModel 207 Automatic GTAW Welding System2.0 Features and System Configuration (continued)3. Width: 22.75” (577.9 mm)4. Depth: 19.25” (489.0 mm) including handle5. Weight: 78 lb. (35.4 kg)3.0 Input Power, Inert Gas and Temperature Requirements3.1 Input Power: The M-207, as standard, can operate on a variety of single phaseAC input power as follows:100 VAC + 32%, -10%, 50/60 Hz, 30 ampere service110 VAC + 20%, -18%, 50/60 Hz, 30 ampere service115 VAC + 15%, -22%, 50/60 Hz, 30 ampere service120 VAC + 10%, -25%, 50/60 Hz, 30 ampere service200 VAC + 32%, -10%, 50/60 Hz, 20 ampere service208 VAC + 27%, -13%, 50/60 Hz, 20 ampere service220 VAC + 20%, -18%, 50/60 Hz, 20 ampere service230 VAC + 15%, -22%, 50/60 Hz, 20 ampere service240 VAC + 10%, -25%, 50/60 Hz, 20 ampere service+/- % indicates the allowable input voltage fluctuation to maintain performanceas specified. “Ampere service” rating is based on maximum welding currentoutput (100 or 150 Ampere) with maximum Arc Voltage (20 VDC).3.2 Inert Gas: The M-207 is a Gas Tungsten Arc Welding (GTAW) Power Sourceonly and as such requires Inert or Inert/Active Mixed Gas for operation. TheArc Gas Line is provided with an Automatic/Manual Solenoid which controls thepre-weld, weld and post-weld purging of the weld zone.Input gas pressure must be regulated, by the user, to a maximum of 50 PSI +/-5 PSI (3.4 +/- 0.3 bar).Connection to the gas source is via color-coded impermeable hosing (toprevent oxygen and water diffusion) and standard 5/8-16 NPT Gas fittings.3.3 Temperature: The M-207 is designed to operate in an ambient temperaturerange between 0°C (32°F) and 45°C (110°F).4.0 Weld Current Source and Controls4.1 Output current: 3 to 100 Amperes using 100 to 120 VAC. 3 to 150 Amperesusing 200 to 240 VAC.4.2 Voltage: 20 to 30 VDC open circuit (no current) depending on input VAC value.5 (min.) to 20 (max.) VDC at 150 Amperes.4.3 Regulation: Constant current, straight polarity. +/- 1% of program setting or 0.5Ampere (whichever is greater) with input power fluctuations of +/- 10%.Model 207 Automatic GTAW Welding System4.0 Weld Current Source and Controls (continued)4.4 Regulation type: Line inverter using 35 KHz switching frequency,microprocessor closed loop, real-time monitoring with solid-state, high-speedswitching regulation devices.4.5 Duty cycle: 100% at specified operating temperature and specified input VAC.4.6 Current controls: The system provides two (2) methods of current operation.Continuous (Cont.) mode or Pulsed mode. The Cont. mode sets the system toregulate a single desired value of current. In the Pulsed mode, the system willautomatically pulse between one desired current and another to perform pulsedarc-welding.In addition, the system provides (in either mode) the ability to automaticallyprogram changes in the current value. These changes are called “Levels” andthe system can provide up to 100 Level changes per automatic weld sequence.The desired current values, current mode, desired pulsation rate (pulse times)and current Level values are entered into the microprocessor memory (viakeypad) and filed by weld number/type/description.5.0 Pulsed Arc CurrentIf desired, two (2) current values can be selected. The “high” current is designated thePrimary current and the “low” current is designated the Background current. Thefrequency or pulse rate of switching between these currents is controlled by the Primaryand Background Pulse time function with the following range:Primary Pulse Time: 0.01 to 10.00 seconds, +/- 0.001Background Pulse Time: 0.01 to 10.00 seconds, +/- 0.001This equates to a pulse frequency range of 0.05 to 50.00 pulses per second. Pulse width adjustment is a function of the Primary time versus the Background time.6.0 Fixture Rotation Servo and ControlsThe M-207 is intended to (but not limited to) operate AMI Model 9 Fusion Tube WeldingHeads. These heads encapsulate the weld zone (with inert gas) and the welding arc(electrode) is rotated around the stationary tube, pipe or fitting to be welded. The M-207 is equipped standard with a Rotation Servo and controls to drive the Weld Head Rotation Motor.6.1 Rotation Speed: 0.10 to 20.00 RPMThere are over 23 versions of Model 9 Weld Heads and not all heads have thesame rotation speed ranges.Model 207 Automatic GTAW Welding System6.0 Fixture Rotation Servo and Controls (continued)6.2 Rotation Regulation: Closed-loop servo using tachometer feedback withregulation to +/- 1%.NOTE: The Servo is rated to +/- 1% over its specified range, however, someM-9 Weld Heads have low speed minimums greater than 1%.Consult the individual head specification for details.6.3 Rotation Controls: The system provides two (2) methods of rotation control.Continuous (Cont.) mode and Stepped mode. The Cont. mode sets the systemto regulate a single desired value of speed. In the Stepped mode, the systemwill automatically pulse between a desired Primary speed and a desiredBackground speed to perform Stepped arc-welding. The Stepping issynchronized to the Current Pulsation’s.The desired speed value and speed mode are entered into the microprocessormemory (via keypad) and filed by weld number/type/description.7.0 Arc Start SystemA High Frequency (HF) Arc Starter is provided, with a booster that momentarily increasesthe open circuit voltage during Arc Start. The HF starter will reliably start the arc atcurrent levels of 5 amps in Argon and 10 amps in Helium using a suitably preparedthoriated or ceriated tungsten electrode with an arc gap of 0.080 inch or less, with weldhead cables of 100 feet or less.Protective devices are installed in the HF starter and at suitable points in the system toprevent HF feed through the power lines or to internal, sensitive components.The Starting Frequency is approximately 10 MHz and will vary with components andcables.8.0 MeteringDuring the weld sequence, one of the displays provides sliding scale indicators whichdisplay Amperes, Arc Volts and Rotation Speed.The meters are intended as an information and trouble-shooting guide and are notintended to be used for Quality Control or calibration purposes.9.0 MicroprocessorThe M-207 contains a 16-bit microprocessor with BATRAM memory. The microprocessor has operating software which supplies all of the standard functions of this Specification.All standard commands are inputted into the microprocessor via the display panel keys.All steps of operation and programming are prompted by the displays (in English, French or German) contained in the display panel.Model 207 Automatic GTAW Welding System10.0 EMI SuppressionThe M-207 is equipped with a heavy-duty Pi-Network filter, connected to the input power line, to prevent propagation of EMI either into or out of the M-207. All-metal enclosures and internal shields prevent radiated EMI.11.0 Operation, ModesThe M-207 has three (3) basic modes of operation. The modes are selected via a 3-way keylock mode switch. The key can be removed to lock the system into any of its threemodes as described below:11.1 Operate Mode: The operate mode is really two-fold: Non-welding Functions andAutomatic Weld Sequence. The following describes these two Operate Modes:Non-Welding1. Operator selection of any one of the possible 100 weld schedules containedin the system memory.2. Operator “override” control for Current and Rotation Speed. Limits to“override” can be pre-programmed (see programming).3. Weld set-up controls for jogging the weld head electrode to the desired startposition.4. Manual purge control for pre-setting of desired gas flow rates.5. Manual sequence stop for operator interruption of the weld sequence withnormal stopping functions.6. “All Stop” function for operator interruption of normal weld sequence withoutnormal stopping sequence (post-purge only).7. Automatic fault detection for gas flow, coolant flow, overheating, etc.Engages “All Stop” automatically.Automatic Weld Sequence: Sequence Start is initiated by the operator and thefollowing events occur automatically in the sequence described below:8. Pre-purge Time: 0 to 999 seconds with automatic initiation of arc gassolenoid at beginning of sequence.9. Arc Initiation (after pre-purge): Via impulse HF Starter.10. Arc Detection: After Arc Initiation, the M-207 will detect if there is an arc. Ifarc start is not successful, it will notify the operator to start over; ifsuccessful, the following will all start at the same time:Current Upslope Time: 0.0 to 99.9 seconds. The current will rise during thistime to its maximum programmed value.Rotation Start Delay Time: 0.0 to 99.9 seconds. Arc rotation will be delayedfor the programmed time to achieve penetration before moving.Model 207 Automatic GTAW Welding System11.0 Operation, Modes (continued)Pulsation Timers: 0.01 to 9.99 Primary, 0.01 to 9.99 Background (if pulsemode is programmed, the current will start to pulse at the programmedrate).Level 1 Time: 000 to 999 seconds. This programmed function sets theperiod of time that the level 1 primary current value will be used beforeswitching to level 2 or end of sequence.11. Levels: After upslope the Primary current will be at its full programmedvalue and will remain at that value until the level 1 time is over. Up to 99levels of Primary current and Time for each can be programmed and thesystem will advance from level to level as each level time is completed. Alllevels do not have to be programmed.When the last level time (1, 2, 3, 8, 12, etc.) is complete, the system will“Sequence Stop” automatically.12. Sequence Stop: When the last programmed level time is over, the systemwill do the following:Downslope Time: 0 to 99.9 seconds. The current will progress to 0Amperes during this time. When the current is less than 3 Amperes, theArc will go off.Rotation Delay: The arc will continue to rotate for the same time as thedownslope and stop rotating when the arc goes out.13. Post-purge Time: 0 to 999 seconds. When the arc goes out the gas willcontinue to flow until this programmed time is complete.14. Return-to-Home and Reset: When the post-purge time is complete, the arcgas solenoid will turn off and Model 9 rotors will automatically return to the“open” position for Head removal. The system will reset to be able torepeat the sequence on the next weld.11.2 Operate Lock ModeWhen the three-way keylock is in this position, the selected weld schedulecannot be changed. If the key is removed, this will prevent anyone fromchanging the set-up of the system.Model 207 Automatic GTAW Welding System11.0 Operation, Modes (continued)11.3 Weld ProgrammingThe programming mode is engaged by the operating mode keylock switchwhich can be locked in the programming position. When engaged in theprogramming mode, the M-207 will perform the following.1. The display will ask if the user wants to Create a new weld schedule, Copyan existing schedule, Modify an existing schedule, Transfer the weldschedule memory to another M-207 or Delete a weld schedule.2. When the above choice is made the display will prompt the programmer foreach step.3. See the M-207 operation manual for further programming details.11.4 PrinterThe M-207 is supplied standard with a printer and print select key. The printercan issue a copy of the following items:1. A complete list of all weld schedules in memory including day and date ofprint.2. A complete copy of all program parameters for any particular weld scheduleincluding day and date of print. The system can be set up to issue a copyof this automatically after every weld.3. A complete copy of all actual function values during a weld including dayand date of print and a statement as to whether or not the functionsperformed as programmed.4. A complete copy of all weld numbers contained in the optional M-207-EMM(External Memory Module).12.0 Additional Standard Features12.1 Weld Count: The system will keep track of how many times a particular weldschedule has been used.12.2 Tenth Increments: The system can be set up to be able to program amperesand weld level time in increments of 0.1 instead of the standard 1 amp or 1second.12.3 External Sensor Fault: In addition to the built-in faults (gas, coolant, voltage,etc.) the system can be set up to accept fault information from other sourcessuch as an Oxygen Analyzer or Temperature Monitor.Model 207 Automatic GTAW Welding System12.0 Additional Standard Features (continued)12.4 Speed Math Function: M-9 Heads rotation is entered in RPM. Since the actualwelding speed (surface speed) for any given RPM value changes as the welddiameter changes, the system can calculate the required RPM setting for anygiven weld diameter. By entering the weld O.D. and the desired welding speed,the system will automatically calculate and display the correct RPM setting.12.5 Tungsten Length Math Function: Allows the system to calculate requiredtungsten length.12.6 Rotation Calibration: Weld Head contain tachometers and they must becalibrated to the M-207 they are being run on. A built-in Automatic Calibrationfeature is included in the M-207.12.7 Remote Equipment Start/Stop: The M-207 has input and output connectors toallow for the connection of external devices such as lathes or mills that mayneed to turn on during the welding sequence.13.0 OptionsThe M-207 can operate a variety of options as follows:13.1 Remote Operators Pendant: This option allows the operator to set-up, selectweld schedule from a remote location.13.2 M-207-CW Optional Cooling Package: An add-on liquid-cooling unit for weldheads with duty cycles and weld currents requiring liquid-cooling of the weldhead or manual torch.13.3 M-207-EMM External Memory Module: Used to store, transfer or back-upcopies of the M-207 memory.13.4 Chart Recorder: The M-207 is supplied standard with a Chart Recorder OutputPort. When the optional chart recorder is connected, the user can record theAmperes, Voltage and Travel Speed in continuous “real time” information.13.5 Manual Welding Foot Controller: Provides sequence start/stop and variablecurrent. This option is required for manual welding.13.6 Manual Welding Torch13.7 Extension Cables: For operation of weld heads or manual torches up to 100feet from the M-207.THIS SPECIFICATION IS SUBJECT TO CHANGE WITHOUT NOTICE。
贝利摩电子调节器LM24A-SR数据表说明书

LM24A-SR ArrayModulating damper actuator for adjustingdampers in technical building installations• Air damper size up to approx. 1 m²• Torque motor 5 Nm• Nominal voltage AC/DC 24 V• Control modulating 2...10 V• Position feedback 2...10 VTechnical dataElectrical data Nominal voltage AC/DC 24 VNominal voltage frequency50/60 HzNominal voltage range AC 19.2...28.8 V / DC 19.2...28.8 VPower consumption in operation 1 WPower consumption in rest position0.4 WPower consumption for wire sizing 2 VAConnection supply / control Cable 1 m, 4 x 0.75 mm²Parallel operation Yes (note the performance data)Functional data Torque motor5 NmOperating range Y 2...10 VInput Impedance100 kΩPosition feedback U 2...10 VPosition feedback U note Max. 1 mAPosition accuracy±5%Direction of motion motor selectable with switch 0/1Direction of motion note Y = 0 V: At switch position 0 (ccw rotation) /1 (cw rotation)Manual override with push-button, can be lockedAngle of rotation Max. 95°Angle of rotation note can be limited on both sides with adjustablemechanical end stopsRunning time motor150 s / 90°Sound power level, motor35 dB(A)Mechanical interface Universal shaft clamp 6...20 mmPosition indication Mechanically, pluggableSafety data Protection class IEC/EN III, Safety Extra-Low Voltage (SELV)Power source UL Class 2 SupplyDegree of protection IEC/EN IP54Degree of protection NEMA/UL NEMA 2Enclosure UL Enclosure Type 2EMC CE according to 2014/30/EUCertification IEC/EN IEC/EN 60730-1 and IEC/EN 60730-2-14Certification UL cULus according to UL60730-1A, UL60730-2-14and CAN/CSA E60730-1The UL marking on the actuator depends onthe production site, the device is UL-compliantin any caseMode of operation Type 1Rated impulse voltage supply / control0.8 kVPollution degree3LM24A-SR•••••••Mode of operationSimple direct mountingManual overrideAdjustable angle of rotation High functional reliabilitySafety dataAmbient temperature -30...50°C Storage temperature -40...80°CAmbient humidity Max. 95% RH, non-condensing Servicingmaintenance-free WeightWeight 0.47 kgSafety notesThis device has been designed for use in stationary heating, ventilation and air-conditioning systems and must not be used outside the specified field of application, especially in aircraft or in any other airborne means of transport.Outdoor application: only possible in case that no (sea) water, snow, ice, insolation or aggressive gases interfere directly with the device and that it is ensured that the ambient conditions remain within the thresholds according to the data sheet at any time.Only authorised specialists may carry out installation. All applicable legal or institutional installation regulations must be complied during installation.The device may only be opened at the manufacturer's site. It does not contain any parts that can be replaced or repaired by the user.Cables must not be removed from the device.To calculate the torque required, the specifications supplied by the damper manufacturers concerning the cross-section, the design, the installation situation and the ventilation conditions must be observed.The device contains electrical and electronic components and must not be disposed of as household refuse. All locally valid regulations and requirements must be observed.Product featuresThe actuator is connected with a standard modulating signal of 0...10 V and drives to the position defined by the control signal. Measuring voltage U serves for the electrical display of the damper position 0.5...100% and as control signal for other actuators.Simple direct mounting on the damper shaft with a universal shaft clamp, supplied with an anti-rotation device to prevent the actuator from rotating.Manual override with push-button possible (the gear is disengaged for as long as the button is pressed or remains locked).Adjustable angle of rotation with mechanical end stops.The actuator is overload protected, requires no limit switches and automatically stops when the end stop is reached.AccessoriesElectrical accessoriesDescriptionType Auxiliary switch 1 x SPDT add-on S1A Auxiliary switch 2 x SPDT add-onS2A Feedback potentiometer 140 Ω add-on P140A Feedback potentiometer 200 Ω add-on P200A Feedback potentiometer 500 Ω add-on P500A Feedback potentiometer 1 kΩ add-on P1000A Feedback potentiometer 2.8 kΩ add-on P2800A Feedback potentiometer 5 kΩ add-on P5000A Feedback potentiometer 10 kΩ add-onP10000A Signal converter voltage/current 100 kΩ Supply AC/DC 24 V Z-UIC Range controller for wall mounting SBG24Positioner for wall mounting SGA24Positioner for built-in mounting SGE24Positioner for front-panel mounting SGF24Positioner for wall mountingCRP24-B1LM24A-SRMechanical accessories Description TypeShaft extension 170 mm Ø10 mm for damper shaft Ø 6...16 mm AV6-20Shaft clamp one-sided, clamping range Ø6...20 mm, Multipack 20 pcs.K-ELAShaft clamp one-sided, clamping range Ø6...10 mm, Multipack 20 pcs.K-ELA10Shaft clamp one-sided, clamping range Ø6...13 mm, Multipack 20 pcs.K-ELA13Shaft clamp one-sided, clamping range Ø6...16 mm, Multipack 20 pcs.K-ELA16Anti-rotation mechanism 180 mm, Multipack 20 pcs.Z-ARS180Form fit insert 8x8 mm, Multipack 20 pcs.ZF8-LMAForm fit insert 10x10 mm, Multipack 20 pcs.ZF10-LMAForm fit insert 12x12 mm, Multipack 20 pcs.ZF12-LMAForm fit insert 8x8 mm, with angle of rotation limiter and positionindication, Multipack 20 pcs.ZFRL8-LMAForm fit insert 10x10 mm, with angle of rotation limiter and position indication, Multipack 20 pcs.ZFRL10-LMAForm fit insert 12x12 mm, with angle of rotation limiter and positionindication, Multipack 20 pcs.ZFRL12-LMAPosition indicator, Multipack 20 pcs.Z-PI Electrical installationSupply from isolating transformer.Parallel connection of other actuators possible. Observe the performance data.Wiring diagramsAC/DC 24 V, modulatingCable colours:1 = black2 = red3 = white5 = orangeDimensionsSpindle lengthMin. 37-Clamping range。
KAT SmartWelding V Series TIG 产品说明书

UNPARALLELED TIG TECHNOLOGY Packaged in a groundbreaking industrial design SUPERIOR TIG PRODUCTIVITYThanks to remote control, cold wire feeding, and perfect automationINCREDIBLY EASY TO USEWith plain text display and ergonomically designed control panel V seriesFOR EVERYONE WITH BIG THINGS IN MIND.Pulsing and fast pulsing up to 20 kHz. The standard pulse function with up to20 kHz that is built into every machine offers you additional benefits when welding thin hat is built into every machine offers you additional benefits when welding thinsheets and de nd delivers greater welding speeds during automated applications.In a robust, co t, completely transportable industrial housing.The tough metal metal housing safely protects the high-end technological innards of your system. Completely transportable at the handles, our system. Completely transportable at the handles, the machine is also suitable for crane transport.Remote control. Welders often experience that the conditions on site do not allow them to place their welding machine right beside them. When faced with this type of situation, they find the use of ▪Automatic final current reduction. Lorch’s automatic final current reduction produces perfectly clean weld ends by filling the end crater.▪Low energy consumption. The included on-demand function automatically turns the components of the unit on and off as needed. Thermal control sensors monitor the temperature of the components and regulate the speed of the fan accordingly. This YEARS INDUSTRIAL WARRANTYV standard▪“3 steps to weld” operating concept▪User-oriented guidance using illuminated symbols and detailed welding sequence control ▪Remote control connection▪LorchNet, e.g. for controlling the optional Feed wire feeder and connecting Lorch automation componentsPulse functionTiptronic job memory for 100 welding tasksEverything to benefit your TIG productivityMobile Car: Carriage for supporting the V mobile and the water re-circulationcooling unit WUK 5Water cooling unit WUK 5:cooling unit for water-cooled TIG torch UK 5: High performanceWater cooling unit WUK 5 Carriage for supportinMarkfield Road,GrobyLeicestershireLE6 0FSTel:+44(0) 116 2696941**********************。
搅拌摩擦焊英文作文

搅拌摩擦焊英文作文Friction stir welding (FSW) is a solid-state joining process that produces high-quality, high-strength welds in materials that are difficult to weld using conventional techniques. This innovative welding method was invented by Wayne Thomas at The Welding Institute in 1991 and has since been widely adopted in various industries for joining aluminum, copper, and other materials.During the FSW process, a non-consumable rotating tool is driven along the joint between two workpieces, generating frictional heat that softens the material without reaching its melting point. The plasticized material is then stirred by the rotating tool, creating a bond between the two workpieces. The weld is formed without the need for filler material, reducing the risk of defects and improving the overall quality of the weld.One of the key advantages of FSW is its ability to join materials that are typically considered non-weldable, such as high-strength aluminum alloys. The process results in welds that have superior mechanical properties, including high tensile strength, fatigue resistance, and toughness. This makes FSW an attractive option for industries that require high-performancewelded components, such as aerospace, automotive, and marine applications.In addition to its mechanical properties, FSW also offers several other benefits over traditional welding methods. It produces minimal distortion and heat-affected zones, reducing the need for post-welding processes such as heat treatment and machining. FSW is also environmentally friendly, as it does not produce harmful fumes or waste materials commonly associated with arc welding.Despite its numerous advantages, FSW does have some limitations. It is a relatively slow process compared to traditional welding methods, and the equipment required can be expensive. Additionally, FSW is not suitable for all materials and joint configurations, limiting its applicability in certain industries.Overall, friction stir welding is a versatile and effective joining method that offers numerous advantages for a wide range of applications. As technology continues to evolve, FSW is likely to play an increasingly important role in the manufacturing industry, providing high-quality welds that meet the demanding requirements of modern engineering.。
林肯电子焊接和切割产品说明书

Copyright © Lincoln Global Inc.LN ™- 25 PIPEIM10056April, 2011For use with machines having Code Number:11693Safety Depends on YouLincoln arc welding and cutting equipment is designed and built with safety in mind. However, your overall safety can be increased by proper installation ... and thoughtful operation on your part. DO NOT INSTALL, OPERATE OR REPAIR THIS EQUIPMENT WITHOUT READING THIS MANUAL AND THE SAFETY PRECAUTIONS CONTAINED THROUGHOUT.And, most importantly, think beforeyou act and be careful.IP23IEC 60974-5SECTION A:WARNINGSC ALIFORNIA PROPOSITION 65 WARNINGSWARNING: This product, when used for welding or cutting, produces fumes or gases which contain chemicals known to the State of California to cause birth defects and, in some cases, cancer. (California Health & Safety Code § 25249.5 et seq.)ARC WELDING CAN BE HAZARDOUS. PROTECTYOURSELF AND OTHERS FROM POSSIBLE SERIOUS INJURY OR DEATH. KEEP CHILDREN AWAY.PACEMAKER WEARERS SHOULD CONSULT WITH THEIR DOCTOR BEFORE OPERATING.Read and understand the following safety highlights. For additional safety information, it is strongly recommended that you purchase a copy of “Safety in Welding & Cutting - ANSI Standard Z49.1” from the American Welding Society, P.O. Box 351040, Miami, Florida 33135 or CSA Standard W117.2-1974. A Free copy of “Arc Welding Safety” booklet E205 is available from the Lincoln Electric Company, 22801 St. Clair Avenue, Cleveland, Ohio 44117-1199.BE SURE THAT ALL INSTALLATION, OPERATION,MAINTENANCE AND REPAIR PROCEDURES ARE PERFORMED ONLY BY QUALIFIED INDIVIDUALS.FOR ENGINE POWERED EQUIPMENT.1.a.Turn the engine off before troubleshootingand maintenance work unless themaintenance work requires it to be running.1.b.Operate engines in open, well-ventilated areas or vent the engineexhaust fumes outdoors. 1.c.Do not add the fuel near an open flame weldingwith hot engine parts and igniting. Do not spill fuel when filling tank. If fuel is spilled, wipe it up and do not start engine until fumes have been eliminated.1.d. Keep all equipment safety guards, coversand devices in position and in good repair.Keep hands, hair, clothing and tools away from V-belts, gears, fans and all other moving parts when starting, operating or repairing equipment.1.e.In some cases it may be necessary to remove safety guards toperform required maintenance. Remove guards only when necessary and replace them when the maintenance requiring their removal is complete. Always use the greatest care when working near moving parts. 1.f. Do not put your hands near the engine fan. Do not attempt tooverride the governor or idler by pushing on the throttle control rods while the engine is running. 1.g.To prevent accidentally starting gasoline engines while turningthe engine or welding generator during maintenance work,disconnect the spark plug wires, distributor cap or magneto wire as appropriate. 1.h.To avoid scalding, do not remove the radiatorpressure cap when the engine is hot.ELECTRIC ANDMAGNETIC FIELDS MAY BE DANGEROUS2.a.Electric current flowing through any conductorcauses localized Electric and Magnetic Fields (EMF).Welding current creates EMF fields around welding cables and welding machines 2.b.EMF fields may interfere with some pacemakers, andwelders having a pacemaker should consult their physician before welding. 2.c.Exposure to EMF fields in welding may have other health effectswhich are now not known. 2.d.All welders should use the following procedures in order tominimize exposure to EMF fields from the welding circuit:2.d.1.Route the electrode and work cables together - Securethem with tape when possible.2.d.2.Never coil the electrode lead around your body.2.d.3.Do not place your body between the electrode and workcables. If the electrode cable is on your right side, the work cable should also be on your right side.2.d.4.Connect the work cable to the workpiece as close as pos-sible to the area being welded.2.d.5.Do not work next to welding power source.SAFETYConformanceProducts displaying the CE mark are in conformity with European Community Council Directive of 15 Dec 2004 on the approximation of the laws of the Member States relating to electromagnetic compatibility,2004/108/EC. It was manufactured in conformity with a national standard that implements a harmonized standard: EN 60974-10 Electromagnetic Compatibility (EMC) Product Standard for Arc Welding Equipment. It is for use with other Lincoln Electric equipment. It is designed for industrial and professional use. IntroductionAll electrical equipment generates small amounts of electromagnetic emission. Electrical emission may be transmitted through power lines or radiated through space, similar to a radio transmitter. When emissions are received by other equipment, electrical interference may result. Electrical emissions may affect many kinds of electrical equipment; other nearby welding equipment, radio and TV reception, numerical controlled machines, telephone systems, computers, etc. Be aware that interference may result and extra precautions may be required when a welding power source is used in a domestic establishment.Installation and UseThe user is responsible for installing and using the welding equipment according to the manufacturer’s instructions. If electromagnetic disturbances are detected then it shall be the responsibility of the user of the welding equipment to resolve the situation with the technical assistance of the manufacturer. In some cases this remedial action may be as simple as earthing (grounding) the welding circuit, see Note. In other cases it could involve construction of an electromagnetic screen enclosing the power source and the work complete with associated input filters. In all cases electromagnetic disturbances must be reduced to the point where they are no longer troublesome.Note: The welding circuit may or may not be earthed for safety reasons according to national codes.Changing the earthing arrangements should only be authorized by a person who is compe-tent to access whether the changes will increase the risk of injury, e.g., by allowing parallelwelding current return paths which may damage the earth circuits of other equipment. Assessment of AreaBefore installing welding equipment the user shall make an assessment of potential electromagnetic prob-lems in the surrounding area. The following shall be taken into account:a) other supply cables, control cables, signaling and telephone cables; above, below and adjacent to thewelding equipment;b) radio and television transmitters and receivers;c) computer and other control equipment;d) safety critical equipment, e.g., guarding of industrial equipment;e) the health of the people around, e.g., the use of pacemakers and hearing aids;f) equipment used for calibration or measurementg) the immunity of other equipment in the environment. The user shall ensure that other equipment beingused in the environment is compatible. This may require additional protection measures;h) the time of day that welding or other activities are to be carried out.The size of the surrounding area to be considered will depend on the structure of the building and other activities that are taking place. The surrounding area may extend beyond the boundaries of the premises. Methods of Reducing EmissionsMains SupplyWelding equipment should be connected to the mains supply according to the manufacturer’s recommenda-tions. If interference occurs, it may be necessary to take additional precautions such as filtering of the mains supply. Consideration should be given to shielding the supply cable of permanently installed welding equip-ment, in metallic conduit or equivalent. Shielding should be electrically continuous throughout its length. The shielding should be connected to the welding power source so that good electrical contact is maintained between the conduit and the welding power source enclosure.Maintenance of the Welding EquipmentThe welding equipment should be routinely maintained according to the manufacturer’s recommendations. All access and service doors and covers should be closed and properly fastened when the welding equip-ment is in operation. The welding equipment should not be modified in any way except for those changes and adjustments covered in the manufacturers instructions. In particular, the spark gaps of arc striking and stabilizing devices should be adjusted and maintained according to the manufacturer’s recommendations. Welding CablesThe welding cables should be kept as short as possible and should be positioned close together, running at or close to floor level.Equipotential BondingBonding of all metallic components in the welding installation and adjacent to it should be considered. However, metallic components bonded to the work piece will increase the risk that the operator could receive a shock by touching these metallic components and the electrode at the same time. The operator should be insulated from all such bonded metallic components.Earthing of the WorkpieceWhere the workpiece is not bonded to earth for electrical safety, not connected to earth because of its size and position, e.g., ships hull or building steelwork, a connection bonding the workpiece to earth may reduce emissions in some, but not all instances. Care should be taken to prevent the earthing of the workpiece increasing the risk of injury to users, or damage to other electrical equipment. Where necessary, the connec-tion of the workpiece to earth should be made by a direct connection to the workpiece, but in some countries where direct connection is not permitted, the bonding should be achieved by suitable capacitance, selected according to national regulations.Screening and ShieldingSelective screening and shielding of other cables and equipment in the surrounding area may alleviate prob-lems of interference. Screening of the entire welding installation may be considered for special applications1._________________________1 Portions of the preceding text are contained in EN 60974-10: “Electromagnetic Compatibility (EMC) prod-uct standard for arc welding equipment.”TECHNICAL SPECIFICATIONS – LN™-25 PIPE (K2614-5)Thermal tests have been performed at ambient temperature. The Duty Cycle (duty factor) @ 40ºC (104°F) has been determined by simulation.WELD CAbLE SIzETable A.1 located below are copper cable sizes rec-ommended for different currents and duty cycles.Lengths stipulated are the distance from the welder to work and back to the welder again. Cable sizes are increased for greater lengths primarily for the purpose of minimizing cable drop.** Tabled values are for operation at ambient temperatures of 104°F(40°C) and below. Applications above 104°F(40°C) may require cables larger than recommended, or cables rated higher than 167°F(75°C).CV Power Sources with Stud Connectors and no Remote/Local Switch. (See Figure A.7)Place CV/CC switch in the feeder in the "CV" position.Work clipWorkElectrodeJumperLN™-25 PIPERanger 250, 250 LPG Ranger 305G, 305D Ranger 10,000Ranger 3 Phase Ranger 225GXT Ranger 225Commander 300Vantage 300, 400, 500Air Vantage 500FIGURE A.7POWER SOURCE TO LN™-25 PIPE CAbLE CONNECTION DIAGRAMS*If Power Source has a 14-Pin Cable connector and no“Output Terminal” switch.• ELECTRIC SHOCK CAN KILL. Unless using COLD FEED fea-ture, when feeding with gun trig-ger, the electrode anddrivemechanism are always electri-cally energized and could remain energized several sec-onds after the welding ceases..• Do not touch electrically live partor electrodewith skin or wet clothing.• Insulate yourself from work and ground.• Always wear dry insulating gloves.• Do not operate with covers, panels or guards removed or open.AND GASSES can bedangerous.ventilation or exhaust toremove fumes from breathingzone.SPARKS can causefire or explosion.eye, ear and body protec-tion.SEE ADDITIONAL WARNING INFORMATIONUNDER ARC WELDING SAFETY PRECAUTIONSAND IN THE FRONT OF THIS OPERATING MAN-UAL.---------------------------------------------------------------------READ AND UNDERSTAND ENTIRE SECTIONbEFORE OPERATING MACHINE.INPUT POWERONOFFWIRE FEEDERPOSITIVE OUTPUTNEGATIVE OUTPUTINPUT POWERDIRECT CURRENTOPEN CIRCUITVOLTAGEINPUT VOLTAGEOUTPUT VOLTAGEINPUT CURRENTOUTPUT CURRENTPROTECTIVEGROUNDWARNING ORCAUTIONU0U1U2I1I2GRAPHIC SYMbOLS THAT APPEAR ONTHIS MACHINE OR IN THIS MANUALDEFINITION OF WELDING TERMSWFS• Wire Feed SpeedCC• Constant CurrentCV• Constant VoltageGMAW• Gas Metal Arc weldingSMAW• Shielded Metal Arc weldingFCAW• Flux Core Arc WeldingGENERAL DESCRIPTIONGeneral Physical DescriptionThe LN™-25 PIPE is specially engineered to be the most rugged portable wire feeder available and meets the individual welder needs. This model includes a gas solenoid for flexibility to run most wire processes.The plastic case is molded from a high impact, flame retardant plastic for durability and low weight. The patent pending design keeps the internal components protected and dry.The heart of the LN™-25 PIPE is the 2 roll MAX-TRAC™ drive. The patented features on the wire drive offer tool-less changing of the drive rolls and wire guides for quick spool changes. A tachometer controlled motor powers the patent pending drive rolls for smooth, steady feeding without slippage.The LN™-25 PIPE has only two p.c. boards that are designed to be simple, reliable and easy to service. General Functional DescriptionThe LN™-25 PIPE as designed is a simple, robust feeder. Standard features include a calibrated wire feed speed dial, 2 step/trigger interlock switch, Gas Purge and Cold Feed.RECOMMENDED PROCESSES• GMAW• FCAWPROCESS LIMITATIONS• GMAW-P procedures must be qualified by the cus-tomer.• Across-the-Arc models are not recommended for stitch or spot welding.EQUIPMENT LIMITATIONS• The duty cycle of the wire feeder is 450A, 60%. Duty cycle is based upon the amount of welding performed in a 10 minute period.• The maximum spool size is 45 lb, 12" diameter.• Maximum FCAW gun length is 15 ft.• Maximum GMAW gun length is 25 ft.• K2330-1 Timer Kits do not work with the feeder. Use K2330-2 kits.• Push-pull guns do not work with the wire feeder.• The digital displays do not show preset voltage RECOMMENDED POWER SOURCES• CV-250• CV-300• CV-305• CV-400• CV-655• DC-400• DC-600• DC-655• Invertec V-350 PRO• Invertec V-450 PRO• Multi-Weld 350• Ranger 10,000• Ranger 3 Phase• Ranger 225• Ranger 225 GXT• Ranger 250• Ranger 250 GXT• Ranger 305• SAE-400• Pipeliner 200G• Classic 300• Vantage 300• Vantage 400• Vantage 500• Air Vantage 500Big Red’sEagle 10,000 PlusClassic’sWIRE FEED SPEED KNObWire Feed Speed, CV OperationWhen Across the Arc models are operated with CV power sources, the wire feed speed will remain a con-stant value, independent of arc voltage changes, as along as the arc voltage does not drop below the val-ues per the following table.83% Wire Feed SpeedThe 83% wire feed speed reduces the wire feed speed to 83% of the original set value when activated.For example, if the original wfs = 200 in/min, the feed-er will regulate to 0.83 x 200 = 166 in/min.The 83% trigger requires a gun with a dual procedure switch.This feature is often useful when welding pipe, and a “cooler” procedure is required on the bottom portion.The thermal light illuminates when the wiredrive motor draws too much current. If thewill automatically shutdown for up to 30 seconds to allowWFSA VWeldingvalue in the left display will be either ampsAMPS VOLTAGEA VAfter WeldingThe display continues to hold the value of theWFS and arc voltage for five secondsINTERNAL CONTROLSGAS PURGE PUSHbUTTONThe gas solenoid valve will energize but neither the power source output nor the drive motor will be turned on. The Gas Purge switch is useful for setting the proper flow rate of shielding gas. Flow meters should always be adjusted while the shielding gas is flowing.FACTORY INSTALLED EQUIPMENT • K1500-2 Gun Receiver Bushing.DRIVE ROLL KITS (See Parts Pages)ing with hose nipple, set screw ing with hose nipple, set screwing with hose nipple, set screwELECTRIC SHOCK can kill.• Turnthe input power OFF at the welding power source before installation or changing drive rolls and/or guides.•Do not touch electrically live parts.• When inching with the gun trigger, electrode and drive mechanism are "hot" to work and ground and could remain energized several seconds after the gun trigger is released.• Do not operate with covers, panels or guards removed or open.• Only qualified personnel should perform mainte-nance work.-----------------------------------------------------------------------ROUTINE MAINTENANCE• Check weld cables, control cables and gas hoses for cuts.• Clean and tighten all weld terminals.PERIODIC MAINTENANCE• Clean drive rolls and inner wire guide and replace if worn.• Blow out or vacuum the inside of the feeder.This Troubleshooting Guide is provided to help you locate and repair possible machine malfunctions.Simply follow the three-step procedure listed below.Step 1.LOCATE PROBLEM (SYMPTOM).Look under the column labeled “PROBLEM (SYMP-TOMS)”. This column describes possible symptoms that the machine may exhibit. Find the listing that best describes the symptom that the machine is exhibiting.Step 2.POSSIBLE CAUSE.The second column labeled “POSSIBLE CAUSE” lists the obviousexternal possibilities that may contribute to the machine symptom.Step 3.RECOMMENDED COURSE OF ACTIONThis column provides a course of action for the Possible Cause, generally it states to contact your local Lincoln Authorized Field Service Facility.If you do not understand or are unable to perform theRecommended Course of Action safely, contact your local Lincoln Authorized Field Service Facility.HOW TO USE TROUbLESHOOTING GUIDEService and Repair should only be performed by Lincoln Electric Factory Trained Personnel.Unauthorized repairs performed on this equipment may result in danger to the technician and machine operator and will invalidate your factory warranty. For your safety and to avoid Electrical Shock, please observe all safety notes and precautions detailed throughout this manual.__________________________________________________________________________JapaneseChineseKoreanArabicREAD AND UNDERSTAND THE MANUFACTURER’S INSTRUCTION FOR THIS EQUIPMENT AND THE CONSUMABLES TO BE USED AND FOLLOW YOUR EMPLOYER’S SAFETY PRACTICES.SE RECOMIENDA LEER Y ENTENDER LAS INSTRUCCIONES DEL FABRICANTE PARA EL USO DE ESTE EQUIPO Y LOS CONSUMIBLES QUE VA A UTILIZAR, SIGA LAS MEDIDAS DE SEGURIDAD DE SU SUPERVISOR.LISEZ ET COMPRENEZ LES INSTRUCTIONS DU FABRICANT EN CE QUI REGARDE CET EQUIPMENT ET LES PRODUITS A ETRE EMPLOYES ET SUIVEZ LES PROCEDURES DE SECURITE DE VOTRE EMPLOYEUR.LESEN SIE UND BEFOLGEN SIE DIE BETRIEBSANLEITUNG DER ANLAGE UND DEN ELEKTRO-DENEINSATZ DES HERSTELLERS. DIE UNFALLVERHÜTUNGSVORSCHRIFTEN DES ARBEITGEBERS SIND EBENFALLS ZU BEACHTEN.JapaneseChineseKoreanArabicLEIA E COMPREENDA AS INSTRUÇÕES DO FABRICANTE PARA ESTE EQUIPAMENTO E AS PARTES DE USO, E SIGA AS PRÁTICAS DE SEGURANÇA DO EMPREGADOR.。
Miller 200A Welding Controller 产品说明书

Simply fill in the blanks
>
>
>>
Options
• Cart with bottle rack • Remote Pendant • Extension cables • R ugged Storage/Shipping Case • O ffline Programming Software • M anual Tack Welding Torch Kit
procedures • P rogrammable “override limits” provide
supervisory control • W eld parameter monitoring/reporting for
QA/QC purpose • T ransfer programs and data to PCs using USB
MODEL 514 NOW OPERATES ANALOG HEADS
The new model has the ability to operate both analog Heads (using tachometer motors), as well as Magnatech’s current digital encoder motors. This allows the operation of many weld Heads from other manufacturers, with “drop-down” model selection and Autoprogramming for these other Heads. On-screen calibration of competitor’s Heads eliminates trim potentiometer adjustments.
SAF PLASMA 自动焊接器产品说明书

0704/18G 138G 137G 136G 139AUTOMATIC PLASMA WELDING in the stainless steel boiler maker industryWHAT MUST BE ACHIEVED ?SAVINGS ? Rapidity of operation, low deformation to avoid or reduce the reconforming post operations, low reinforcement to reduce or suppress polishing operations, keep the original chemical analysis of the base material to garantee corrosion characteristics, good visual aspect of the welds since most of the welds are more and more visible. It is a quality criteria, repeatibility of the quality obtained.G 86In the constant search for optimal productivity, every industry must strive to reduce production time while maintaining extremely high quality. In the case of plasma welding, unlike the tricathode process, the multiplication of torches would have little effect on the performance levels.Nevertheless, a solution exists for increasing speeds by 30 to 50 % in comparison with a single torch : PLASMA + TIG process.Thanks to this technique, the PLASMA arc melts the joint throughout its thickness, while the TIG arc, equipped with a magnetic oscillation system and additional filler metal prepares the final appearance of the surface. This yields results that are perfectly suited to the specifications of speed and quality. SAF , an innovative specialist in TIG and PLASMA welding, naturally offers installations combining these techniques, which are particularly suitable for production of large stainless steel vessels. Nonetheless,certain strict criteria are required for ensuring the profitability and the technical feasibilityof these materials. These criteria may be summed up as follows : manufacture of stainless steel tanks from 3 to 8 mm thick, with a welding length of at least three meters, or parts with a diameter greater than 2200 mm.TOP QUALITY RESULTS AND INCREASED PRODUCTIVITY Initial plate preparation/fit-up greatly reduced by suppression of bevel up to 7 mm.Reduction of welding times compared to manual welding (up to 4 to 5 times).A garanted regular penetration thanks to the «key hole» technique on all but joints with TIG pre-tacking. A very high quality weld in regard to most stringent controls. It eliminates hazards of lack of penetration at the beginning of welds as well as the systematic delicate repairs after grinding of beginnings and ends of welds. A guaranted reproductibility,thanks to memorization *of complete welding parameters programs (simply defined by material,diameter and thickness).High quality finish on circular welds thanks to the automatic key hole closure system*.*PLASMA with microprocessor installation only.G 1370725/10G 2000725/08Welding current (100 %)30 - 350 A DC 100 % 3 - 300 A DC (±1 %)500 A DC 100 %Pulsed current frequency10 Hz max (option) 1 - 500 Hz 10 Hz max. Primary voltage (50 - 60 Hz)380/400/415 V 220/230/380/400/415/440/500 V 220/380/415 V or 380/440/500 V Supply current (380 V)39 A 17.6 A 36 A Plasma pilot arc12 A 1 - 25 A adjustable 15 A Gas circuitswith built-in gyrometers with built-in gyrometers gyrometers in the controls Welding current controloption yes Process controlyes option no Dust protection- 2 interchangeable filters -Dimensions (h x w x d)940 x 517 x 820 mm 1225 x 700 x 790 mm 1320 x 670 x 780 mm Weight175 kg 245 kg 450 kg Cat. NumberTIG :9121-1049/50/51 (1)9114-05569114-0532plasma :9121-1046/47/48 (1)9114-0533Insulationclass H class H class H ProtectionIP 23IP 23IP 23Torch cooling unit nooptional for TIG no Thanks to its characteristicsand its high degreeof automation whick makesit relatively easy to master,the PLASMA processis now commonly usedin the boiler making industry and SAF since 1965, has installed more than 800 installations throughout the world. SAF offers now a wide range of turn key welding installations,but it has to be choosen carefully according to the work to be done.It involves 3 levels of sub assemblies :•the PLASMA welding equipment,• the support structure of the PLASMA equipment,• the positionning equipment to rotate the rounded sheetsand/or the seamer bench.THE PLASMA WELDING INSTALLATION FOR THE BOILER MAKER INDUSTRY BUFFALO TIG or plasma installation.Programmation and adjustments by potentiometers.Direct current.350 Amps (100%).NERTAMATIC 300 TR This high-technology power source offers a totally regulated welding current facility at frequencies from 1 Hz to 500 Hz **.NERTINOX TH 500 Thyristor power source.Programmed and adjusted by potentiometers.500 A DC (100 %).**Pulsing the PLASMA arc currentat two levels (e.g. 100-200 A)produces a very high levelof confinement of the energyin the arc (the electromagnetic pinch effect combiningwith the pneumaticand mechanical confinementimparted by the nozzle).It offers great operator comfortcombined with better penetrationcontrol and appearance (back of weld).POWER SOURCES1202-501202-45Q -1311-05Do not operate the key-hole closure at the end of weld bead.(1)Harness length 10/17/22 m0704-15Q -1422-012264-102264-011202-473670-421202-49S A F r e s e r v e s i t s e l f t h e r i g h t t o e m b o d y m o d i f i c a t i o n s w i t h o u t p r i o r n o t i c e . T h e i l l u s t r a t i o n s , d e s c r i p t i o n s a n d c h a r a c t e r i s t i c s a r e g i v e n f o r i n f o r m a t i o n o n l y a n d d o n o t e n g a g e t h e r e s p o n s i b i l i t y o f t h e c o n s t r u c t o r .© S A F - 1515-47760006S 01 E d . 4Q B: 1590P hotosS A F : R o c s k a y - F r a n ço i s SAF - 13-17, RUE D’EPLUCHES 95310 SAINT-OUEN L’AUMÔNE - FRANCE TEL. : + 33 1 34 21 33 33 - FAX : + 33 1 34 21 31 30SAF WELDING PRODUCTS LTD - LOW MARCH - LONDON ROAD DAVENTRY - NORTHANTS NN11 4SD TEL. : 01327 705511 - TELEFAX : 01327 701310Email:***********************Internet : DISTRIBUTOR’S STAMP。
STUDPRO SERIES 操作手册说明书

OPERATOR’S MANUAL STUDPRO SERIESCONTENTSDescription Pages Safety2 Specifications and Features3 Product Components 4-5 Screen Operation6-8 Setup and Welding9-11 CD Stud Gun Exploded View12 CD Accessories13-15Read the safety notices before operating welderElectrical•Due to potential dangerous electrical input and output the equipment must be disconnected from all incoming power when servicing . Do not operate the equipment with the outer cover removed or with the case open.•Capacitors store electrical energy, completely discharge before performing any maintenance.•Do not use fluids to clean electrical components as these may penetrate the electrical system and cause shorts.•Connection of the unit into service must be in accordance with the setup procedures as de-tailed in this manual. Operation of this equipment must be in accordance with all local, region-al, and national safety codes.Fire•During welding, small particles of hot metal can be expelled. Ensure that no combustible materials are near the welding area.Personal Safety•Arc rays can burn eyes and skin. Wear protective clothing and eye pro-tection when welding.•Loud noises from welding can damage hearing. Wear earplugs or oth-er protective gear, if applicable.•Fumes and gases expelled during welding can be health hazards. Make sure welding is done in a well -ventilated area.•Hot metal splatter can cause fires and burns. Wear protective clothing, work in an area free of combustible materials, and have a fire extinguisher nearby.Maintenance•All cables must be inspected regularly to ensure that no danger exists from damaged insula-tion or unsafe electrical connections. Take special note of the cables near the stud gun, this is where maximum wear occurs.Training•Use of this equipment must be limited to authorized personnel only. They must be adequately trained, and have read and understood everything in this manual.•The manual must be available to operators at all times.Installation•Select a site which is capable of supporting the weight of the equipment.•Select a site which is clear from heavy foot traffic areas to avoid tripping hazards.•Select a site that prevents cable damage from equipment and vehicles.•Do not hang connecting cables over sharp edges or place near heat sources.SAFETYFIRE HAZARD FROM SPARKS 2SPECIFICATIONS AND FEATURESStudPro XI- Capacitor Discharge Stud Welder SeriesThe StudPro XI series of capacitor discharge stud welders incorporates the latest solid statetechnology into a compact, lightweight, and rugged CD stud welder. This full line of equipment is capable of welding pins, cup head pins, and CD studs ranging from 14-gauge up to 3/8” full -flanged stainless steel studs.SpecificationsFeatures•Intuitive Touchscreen Interface with preset values for fast, accurate, and repeatable weld settings •Set -Point Discharge: Unit discharges directly to a new set point without needing to discharge com-pletely•Universal Input Voltage: Plug and play, no need to re -tap the machine for 110V or 220V input volt-ages•Low input voltage capability enables operation with long extension cords•Contact and Trigger indicators for fast troubleshooting of hand tool and weld cable maintenance issues•Thermal and Voltage protection indicators to protect the unit from damage due to overheating or poor input power•Rigid internal construction minimizes the possibility of components coming loose during rough han-dling or operation•Hand tool has been ergonomically designed to reduce operator fatigue for increased welding effi-ciency•Hand tool has an adjustable internal spring to apply the correct spring pressure for every welding application•Hand tool can be configured for B collets, CI (Collet Inserts), Euro collets, or standard tapered chucksSIZE 14” L, 10.5” W, 11.5” H 356mm x 267mm x 292mmWEIGHT(Power Supply Only)18 lbs. (8.1Kg) 18 lbs. (8.1Kg) 20.8 lbs. (9.4Kg) 23.4 lbs. (10.6Kg) CAPACITANCE/ENERGY76,000µF/1520Ws 76,000µF/1520Ws114,000µF/2280Ws152,000µF/3040WsWELD RANGE14Ga - 1/4” Stainless14Ga - 1/4” Stainless(including cup head pins)14Ga - 5/16” Stainless 14Ga - 3/8” StainlessDUTY CYCLE 18 studs per minute (1/4” settings) 18 studs per minute (1/4” settings) 14 studs per minute (5/16” settings) 10 studs per minute (3/8” settings)PRIMARY POWER (Universal Input) 85-250 VAC, 6.0-2.0A, 50/60HzCHARGE VOLTAGE35-200 VDC3* Specifications are subject to change without prior notificationFront ViewBack ViewComponents1.Touch Screen Interface2.Weld Ground Connector3.Cup Pin Weld Ground Connector (Model 250CP only, on all other TW -i models this connector is a secondary Weld Ground Connector)4.Stud Gun Control Cable Connector5.Stud Gun Weld Cable Connector6.ON/OFF Switch7.10A Fuse8.Manufacturer Model Number and Serial Number Plate 9.Power Cord SocketPRODUCT COMPONENTS14 25 736984Internal ViewComponents1.Ventilation Fan2.ON/OFF Switch3.10A Fuse4.AC Inline Filter/Power Cord Socket5.Capacitor Bank6.Freewheeling Diodes7.SCR/Clamp8.Discharge Resistor9.Control BoardPRODUCT COMPONENTS43125987 6 5SCREEN OPERATIONTrigger IndicatorStud PresetsMetric Stud Mode Contact IndicatorStud Preset ScreenVoltage Preset ScreenCharge IndicatorWelding VoltageStud CounterVoltageAdjustment AdjustmentVoltagePresetsMode SelectionVoltageMode Selection6SCREEN OPERATIONStud Counter ScreenStud CountStud Counter ResetResetting the Stud Counter•While on the stud counter screen, press the RESET tab located at the bottom of the screen.•The screen will then prompt the user for a confirmation to clear the stud counter.•To cancel the resetting of the stud counter, simply press NO on the screen.•To confirm the resetting of the stud counter, simply press YES on the screen.7Screen Status IndicatorsSCREEN OPERATIONStatus Indicator8Connecting the Welding Leads1.Connect the stud gun weld cable into the gun terminal socket on the front of the welding unit. The cable end plug has a flat which aligns with a dot on the panel mount socket. Secure the connector into the panel mount socket, and then turn it clockwise until it locks into proper position. Failure to properly make these connections could result in damage to the connectors.2.Connect the weld gun control cable into the center socket connector. The control cable plug has a large pin and a small pin that match the socket on the unit. Push the plug firmly into the socket and twist clockwise to secure the plug into the correct position.3.Connect the ground clamp into the ground terminal socket on the front of the unit, this connec-tion is identical to step 1.Connecting the Ground Clamp1.Prior to securing the clamp, make certain that the contact area is free of rust, paint, grease, or any other impurities to ensure a good ground connection.2.Attach the clamp of the welding ground lead to the work piece.3.Most applications will require only one ground clamp , but certain applications will require an additional dual clamp.SETUP AND WELDING9Stud Gun Weld Cable ConnectionGround Cable ConnectionStud Gun Control Cable ConnectionSelecting the Proper Stud Collet (Stud Holder)Listed below are the common collet styles, the choice between these setups is usually a matter of per-sonal preference1.The B collet which is a two -piece assembly (collet and insert). The insert determines how much of the stud is engaged in the collet.2.The CI (Collet Insert) which is a single part and the amount of the stud that is engaged is predeter-mined.3.Standard Adjustable Chucks have an adjustable internal screw to manually adjust for the engage-ment of the stud.The collet sizes are based on the diameter of the stud to be welded.CD Stud Gun Setup1.Place the collet into the colletadapter of the stud gun and set thelocking screws to hold the collet inplace.2.Mount the two legs and foot piece onto the stud gun. The collet should be centered through the opening of the foot piece.3.Insert the stud to be welded into the collet.4.Adjust the leg and foot piece by sliding it into position until approximately 1/8” of the stud pro-trudes from beyond the foot piece. Lock legs in place with the set screws.5.The tension setting is adjusted by turning the adjustment cap on the back of the stud gun. On the side of the stud gun is the tension setting indicator, this displays the tension setting of the internal spring.6.The spring tension setting of the stud gun will vary depending on the application. Generally, mild steel and stainless steel should be set in the 1 to 2 range. Aluminum and other nonferrous metals will require settings in the 3 to 5 range.SETUP AND WELDINGCollet AdapterCollet Leg Piece Adjustment CapTension Indicator10Foot PiecePowering On the WelderWhen all of the previous setup steps in this manual are complete the welder can be powered on. 1.Ensure that the power cord is connected to the power cord socket and the supply power.2.Check the 10A fuse below the ON/OFF switch located on the back of the e the ON/OFF switch to power the unit on.Voltage Selection•The voltage is determined by the diameter of the stud and the base material thickness. The unit is programmed with the recommended voltage settings for various stud sizes. Fine tuning the volt-age for each application from this starting point is recommended.•Setting the required weld voltage is achieved by selecting the desired stud size on the screen or manually setting the voltage by using the + or - arrows.•Fast voltage selection can be done from the voltage mode screen. This will replace the preset val-ues on the screen with voltages in increments of 10V and can be manually adjusted by using the arrows.Testing the Weld Settings1.After performing all of the setup steps listed in this manual, it is recommended that several test welds be performed with the same diameter stud and base material used for the application. This will verify that all of the settings are correct to achieve the desired results.2.Welding is done by placing the stud into the collet and pressing the stud gun to the work piece.3.Hold the gun perpendicular to the work piece, align the stud to the desired location, press down so that the foot piece is flush with the base material, and squeeze the trigger.4.Spreading the collet tines when lifting the stud gun from the welded stud will shorten the life of the collet and will eventually create an undesirable weld. For maximum collet life remove the stud gun from the welded stud by pulling the stud gun straight off of the welded stud.5.Properly welded studs are tested by either torqueing or bending the stud. Using either method the threaded portion of the stud may break. However, the welded flange of the stud should stay in place. Additionally, if the base material is very thin, a full slug the diameter of the flange will pull from the base metal.Inspecting the Weld1.Visually inspect the weld. If there is a significant amount of splatter then the weld is too hot, lower the voltage. If there is no splatter then the weld is too cold, increase the voltage.2. A good weld will result in a small, visible, and 360° flashing surrounding the flange of the stud. If there is weld flash on only one side of the base of the flange, this is called “arc blow,” and can be solved by repositioning the ground clamp or using a dual ground clamp.SETUP AND WELDING11CD GUN EXPLODED VIEW12“B” COLLETS STUD DIA PART NO.3 MM CDB-003M 14 GACDB-00812 GA & #4CDB-0101/8 GA & #5CDB-01210 GA & #6CDB-0134 MM CDB-004M #8CDB-015#10CDB-0185 MM CDB-005M 6 MM CDB-006M .215CDB-0211/4CDB-0255/16CDB-0318 MM CDB-008M 3/8CDB-03710 MMCDB-010MSOYER COLLETS STUD DIA.PART NO.#6CDBS-0134 MM CDBS-004M #8CDBS-015#10CDBS-0185 MM CDBS-005M 6 MM CDBS-006M 1/4CDBS-0255/16CDBS-031CAPACITOR DISCHARGE ACCESSORIES3/8 DIA1-3/81.781.390LENGTH DIA.PART NO.7”5/16L-031079”5/16L-0310914”5/16L-0311418”5/16L-03118CD WELDING LEGS 5/16 LEG WASHER 5/16 LEG SCREW 3/8 LEG WASHER 3/8 LEG SCREWL-031-2L-037-1L-037-2L-031-113CAPACITOR DISCHARGE ACCESSORIESONE PIECE CONTACT/MAGNETIC CHUCK PART NO.039-613“B” COLLETS PROTECTOR STUD SIZE PART NO.14 GA X 12 GA 028-83710 GA028-838BODY ONLY 028-83612 GA INSERT 028-83410 GA INSERT028-835“B” STOP STUD STOP LENGTH LENGTH PART NO.1/41-1/4033-7813/81-1/8033-7821/21”033-7835/87/8033-7843/43/4033-7857/85/8033-7751”1/2033-7761-1/83/8033-7771-1/41/4033-7781-3/8(BUTTON STOP)1/8033-779UNIVERSAL033-780SHORT BUTTON STOPUNIVERSAL “B” STOPMAGNETIC CHUCK PART NO.DESCRIPTION 035-301COMPLETE ASSY 017-633MAGNET ONLY029-615CONDUCTOR PLATE 039-609INSUL. TUBE 039-610INSUL. DISC SCREW10-32 X 7/814TEMPLATE TUBE ADAPTORSTUD RANGE PART NO.14 GA –#6033-764#8–3/8033-765STANDARD SPARK SHIELDSTUD DIA.X DEPTH PART NO.#4 X 1/4CI-010-025#4 X 3/8CI-010-037#4 X 1/2CI-010-050#4 X 1”CI-010-100#6X 1/4CI-013-025#6 X 3/8CI-013-037#6 X 1/2CI-013-050#6 X 5/8CI-013-062#6 X 3/4CI-013-075#6X 1”CI-013-10010GA X 1/2CI-014-05010GA X 3/4CI-014-07510GA X 1CI-014-100#8X 1/4CI-015-025#8 X 3/8CI-015-037#8 X 1/2CI-015-050#8 X 5/8CI-015-062#8 X 3/4CI-015-075#8X 1”CI-015-100#10 X 1/4CI-018-025#10 X 3/8CI-018-037#10 X 1/2CI-018-050#10 X 5/8CI-018-062#10 X 3/4CI-018-075#10X 1”CI-018-1001/4 X 1/4CI-025-0251/4 X 3/8CI-025-0371/4 X 1/2CI-025-0501/4 X 5/8CI-025-0621/4 X 3/4CI-025-0751/4 X 1”CI-025-1005/16 X 3/8CI-031-0375/16 X 1/2CI-031-0505/16 X 5/8CI-031-0625/16 X 3/4CI-031-0755/16 X 1”CI-031-1003/8 X 1/2CI-037-0503/8 X 3/4CI-037-0753/8 X 1”CI-037-100COLLETS INSERTS FOR WELD STUDSCAPACITOR DISCHARGE ACCESSORIESSTUD RANGE PART NO.14 GA –10 GA 033-769#6–3/8033-769LVENTED SPARK SHIELDPART NO.039-481TEMPLATE I.D. 1” DIA.30MM 80-40-5131-3/4”1/4 DIA028-833CD FOOT PIECEPART NO.028-83315。
kemppi fastmig x 智能、灵活、可升级 welding 说明书

FastMig XINTELLIGENT, FLEXIBLE, UPGRADABLE17.06.2019FastMig XINTELLIGENT, FLEXIBLE, UPGRADABLE Kemppi's FastMig X product series offers highly specialized welding solutions and superior welding quality for demanding industrial applications. It features three alternative high-end configuration recommentations for three different purposes:FastMig X Regular for robust workshop use a MIG/MAG pulse welding, mainly for welding thick plates, FastMig X Pipe for pipe and root welding and FastMig X Intelligent for demanding welding applications, for all metals and processes,including welding of thin sheets.All configurations are equipped with either the FastMig X 350 or the FastMig X 450 power source, which is a multi-process CC/CV power source that is ideal for synergic and pulsed MIG/MAG welding, MMA welding, and TIG welding. Used in configuration with WFX wire feeders, they form a welding system that easily meets every welding need and the quality management requirements of any metal fabrication workshop.Additionally, all three configurations come with the Cool X cooling unit.2FastMig X17062019KEY BENEFITSFASTER WELDINGBoost your efficiency by utilizingup to 30 % faster travel speedswith WiseFusionLOWER HEAT INPUTReduce distortion and timeconsuming straightening workand improve the impacttoughness of high strength steelswith WiseFusionBEST REACH ON THEMARKETDistance and access will nolonger be a problem with theSuperSnake subfeederaccessoryBENEFITS•Multi-process power solution: MIG, 1-MIG, pulsed MIG, MMA, and TIG•Arc Mobile Control brings flexible way to use and control the welding machine•WiseRoot+ for optimized root welding•WiseThin + for optimized sheet and position welding: Mixed gas quality with lower cost CO2 shielding gas•Precise arc voltage function measures and shows the actual arc voltage on the display•Save time by combining two wire feeders on the same power sourcefor alternative fillerwires•SuperSnake subfeeder connectivity for maximum reach17062019FastMig X3PRODUCT OPTIONSFastMig X 350 Power source Provides 350 A with 80% duty cycle. Suitablefor generator use.FastMig X 450 Power sourceProvides 450 A with 60% duty cycle.Suitable for generator use.FastMig X 350 (400 V) MVPower sourceFastMig X 350 (400 V) MV power source is amulti-voltage unit for demanding applicationsand welding.WFX 200 Wire feederFor Ø 200 mm wire spools. Strong double-skin plastic casing with a reliable DuraTorque wire feed mechanism. Built-in arc voltagemeasurement.WFX 300 Wire feederFor Ø 200/300 mm wire spools. Strongdouble-skin plastic casing with a reliableDuraTorque wire feed mechanism. Built-inarc voltage measurement.WFX 200 P Fe Wire feederFor steel pipe welding with Ø 200 mm wirespools. Strong double-skin plastic casing witha reliable DuraTorque wire feed mechanism.Built-in arc voltage measurement.WFX 200 P Ss Wire feeder For stainless steel pipe welding with Ø 200 mm wire spools. Strong double-skin plastic casing with a reliable DuraTorque wire feed mechanism. Built-in arc voltagemeasurement.WFX 300 P Fe Wire feederFor steel pipe welding with Ø 200/300 mmwire spools. Durable double-skin plasticcasing with a strong two-motor GT04 wirefeed mechanism. Built-in arc voltagemeasurement.WFX 300 P Ss Wire feederFor stainless steel pipe welding with Ø 200/300 mm wire spools. Durable double-skinplastic casing with a strong two-motor GT04wire feed mechanism. Built-in arc voltagemeasurement.4FastMig X17062019WFX 200 AMC Wire feederFor welding high-strength steels and aluminum with Ø 200 mm wire spools. Strong double-skin plastic casing with a reliable DuraTorque wire feed mechanism. Built-in arc voltage measurement. Compatible with the ARC Mobile Control app.WFX 300 AMC Wire feederFor welding high-strength steels andaluminum with Ø 200/300 mm wire spools.Strong double-skin plastic casing with areliable DuraTorque wire feed mechanism.Built-in arc voltage measurement.Compatible with the ARC Mobile Controlapp.WiseFusionA welding function that ensures consistentweld quality in all positions by automaticallyregulating arc length. Creates and maintainsan optimal short-circuit characteristic inpulsed MIG/MAG and spray-arc welding.WiseRoot+Optimized short arc process for productive root pass welding. Excellent weld quality through control of arc voltage and timing of filler metal droplet transfer. Gives higher speed than MMA, TIG or MIG/MAG short arcwelding.WisePenetrationA welding function for ensured penetration insynergic MIG/MAG welding. Deliversconstant power to the weld pool regardlessof changes in welding gun orientation ordistance between the welding gun and workpiece.WiseThin+Optimized short arc process suitable forwelding sheet metals and thicker plates inposition welding, even in case of wider gapsand gap variations. Produces a spatterlessarc with precise digital control. 17062019FastMig X5FEATURESFully upgradableAll three configuration options are fully upgradable and can be optimized for specific welding applications by choosing suitable software packagesand applications.Further flexibility with Wise solutionsThe Wise solutions provide further flexibility forspecific welding applications: for example, WiseRoot+ meets the special requirements of root welding, and exact arc voltage measurement provides easy and precise control of the device. Arc voltage measurement ensures that the set WPS parameters are always kept, regardless of the lengthof the welding cables.Matching high product quality withsuperior serviceFastMig X is fully compatible with the world's most comprehensive welding management software, WeldEye. Among other things, it monitors compliance to the WPS, ensures that welders have appropriate qualifications, and collects quality documentation.The Kemppi worldwide servicenetwork also ensures immediate support andconsultation.High-speed aluminum welding Aluminum pulse welding shot with a high-speed camera attached to the welding gun. Real time video shows how the welding arc is removed with pulsedlaser light.6FastMig X17062019ACCESSORIESCool X Cooling unitCool X cooling unit for liquid-cooled setups is the ultimate choice providing 1 kW of cooling power with 3 liters of cooling liquid.MMT/PMT gun rangeWhether you're welding ships' hulls orpleasure boats, rail cars or racing cars, youcan trust Kemppi MMT and PMT guns todeliver value to every weld. This rangeincludes guns for both manual andmechanized welding.SuperSnake GT02S/GT02SWAn innovative and award-winning subfeederthat offers wire feed assist you can count on.Extends regular reach with up to 25 meters.Compatible with Kemppi FastMig and Prowelding equipment and standard Euro MIGwelding guns.Earth return cable 5 m, 50 mm²Earth return cable 5 m, 70 mm²Cable for Stick (MMA) welding 5m, 70 mm²Cable for Stick (MMA) welding 5m, 50 mm²PMT MN (MN stands for Multi-Neck)The 320 A ‘fast change’ gun neck system,allowing one of five neck variants to beselected and fitted to the gun handle inseconds.Remote control extension cable10 m17062019FastMig X7ARC Mobile ControlFor the first time in welding history, you can now control and monitor your welding machine wirelessly via a smartphone ortablet computer.Download the app from Google Play.KWF 200/300 cabinet heaterThe cabinet heater maintains a temperaturelevel inside the wire feed cabinet forconditions where the ambient temperaturecycles up and down.This unit is suitable for MXF 63, 65, 67, MXP37 PIPE, and MXP 38.GH 30 Gun holderGH 30 Gun holder increases the usabilityaround the workshop. The gun holder can bemounted on a welding machine, transportunit, or welding table.DataGunKemppi DataGun is a programming device that is used together with Kemppi DataStore online shop to purchase and install welding software and upgrades to your Kemppiwelding machines.Remote control RMT10Fingertip control compatible with KemppiPMT welding gun range for MIG/MAGwelding.Increase welding quality, work efficiency,comfort, and safety with appropriate, easy-to-use Kemppi remote controls.Remote control R30Suitable for use with Kemppi FastMig X andFastMig M with MXF wire feeder. Available in5 m and 10 m.Increase welding quality, work efficiency,comfort, and safety with appropriate, easy-to-use Kemppi remote controls.Remote X 37 control panel FASTMIG X 70-1.8-GHinterconnection air-cooledcable, 1.8 mFASTMIG X 70-5-GH interconnection air-cooled cable,5 m8FastMig X17062019FASTMIG X 70-10-GH interconnection air-cooledcable, 10 mFASTMIG X 70-20-GHinterconnection air-cooledcable, 20 mFASTMIG X 70-30-GHinterconnection air-cooled cable,30 mFASTMIG X 70-1.8-WH interconnection liquid-cooledcable, 1.8 mFASTMIG X 70-5-WHinterconnection liquid-cooledcable, 5 mFASTMIG X 70-10-WHinterconnection liquid-cooledcable, 10 mFASTMIG X 70-20-WH interconnection liquid-cooledcable, 20 mFASTMIG X 70-30-WHinterconnection liquid-cooledcable, 30 mMagnetic clamp (earth returncable)600 A17062019FastMig X9Magnetic clamp (voltage sensing cable)200 AMatchLogMatchLog includes Minilog andMatchChannel activation in WFX feeders(Minilog can be used only with MXFfeeders).MatchChannel allows changing of thememory channel during welding and Minilogenables to change welding power in thesame memory channel.KV 200The KV 200 mounting plate for two wirefeeders.This unit is suitable for MXF 63, 65, 67, MXP37 PIPE, MXP 38, and ArcFeed.PM500The PM500 is a 4-wheel transport unit suitable for FastMig M and the FastMig X series as well as for KempArc.P501Suitable for FastMig MXF65, MXF67, WFX300, and WFX 300 AMC.The P501 is a transport unit for wire feedersand compact power sources.KFH 1000KFH 1000 is a movable option for hangingcables. This solution helps to create moreversatile work spaces around the workshop.This unit is suitable for MXF 63, 65, 67, MXP37 PIPE, MXP 38, WFX 200, 200 P, 200AMCWFX 300, 300 P, 300 AMC and ArcFeed.T 10Suitable for FastMig M and FastMig X (T10installation set W002085).10FastMig X17062019TECHNICAL SPECIFICATIONSPOWER SOURCESFastMig X 350 Power sourceProduct code6103350Connection voltage 3~ 50/60 Hz400 V (-15…+20%)Fuse (delayed)35AMinimum generator power35 kVAOutput 80% ED350 AOutput 100% ED330 AOpen circuit voltage MMA U0 = 70-98 VUav = 50 VOpen circuit voltage MIG/MAG U0 = 80 - 98 VOperating temperature range-20 ... +40 °CExternal dimensions LxWxH590 × 230 × 430 mmDegree of protection IP23SStandards IEC 60974-1, IEC 60974-5, IEC 60974-10FastMig X 450 Power sourceProduct code6103450Connection voltage 3~ 50/60 Hz400 V, (-15…+20%)Fuse (delayed)35AMinimum generator power35 kVAOutput 60% ED450 AOutput 100% ED350 AOpen circuit voltage MMA U0 = 70-98 VUav = 50 VOpen circuit voltage MIG/MAG U0 = 80 - 98 VOperating temperature range-20 ... +40 °CExternal dimensions LxWxH590 × 230 × 430 mmDegree of protection IP23SStandards IEC 60974-1, IEC 60974-5, IEC 60974-1017062019FastMig X11FastMig X 350 (400 V) MV Power sourceProduct code6103353Connection voltage 3~ 50/60 Hz220 V -10% … 440 V +10%Fuse (delayed)35AMinimum generator power35 kVAOutput 80% ED350 AOutput 100% ED330 AOpen circuit voltage U0 = 70-98 VUav = 50 VOperating temperature range-20 ... +40 °CExternal dimensions LxWxH590 × 230 × 580 mmWeight (no accessories)U0 = 80 - 98 VDegree of protection IP23SStandards IEC 60974-1, IEC 60974-5, IEC 60974-10WIRE FEEDERSWFX 200 Wire feederProduct code6103520Output 60% ED520 AOutput 100% ED440 AWire feed mechanism 4 rollGun connection EuroFiller wire sizes (Ss)0.6 - 1.6 mmFiller wire sizes (Al)0.8 - 2.4 mmFiller wire sizes (Fe)0.6 - 1.6 mmFiller wire sizes (Cored wire)0.8 - 2.0 mmWire feed speed 1 - 25 m/minSoftware WiseFusionWorkPack (21pcs)Operating temperature range-20 ... +40 °CExternal dimensions LxWxH510 × 200 × 310 mmDegree of protection IP23SStandards IEC 60974-5Wire spool weight, max. 5 kgWeight (empty)9.4 kgWire spool diameter, max.200 mm12FastMig X17062019WFX 300 Wire feederProduct code6103530Output 60% ED520 AOutput 100% ED440 AWire feed mechanism DuraTorqueGun connection EuroFiller wire sizes (Ss)0.6 - 1.6 mmFiller wire sizes (Al)0.8 - 2.4 mmFiller wire sizes (Fe)0.6 - 1.6 mmFiller wire sizes (Cored wire)0.8 - 2.0 mmWire feed speed 1 - 25 m/minSoftware WiseFusionWorkPack (21pcs)Operating temperature range-20 ... +40 °CExternal dimensions LxWxH625 × 243 × 476 mmDegree of protection IP23SStandards IEC 60974-5Wire spool weight, max.20 kgWeight (empty)12.5 kgWire spool diameter, max.300 mmWFX 200 P Fe Wire feederProduct code6103521Output 60% ED520 AOutput 100% ED440 AWire feed mechanism 4 rollGun connection EuroFiller wire sizes (Ss)0.6 - 1.6 mmFiller wire sizes (Al)0.8 - 2.4 mmFiller wire sizes (Fe)0.6 - 1.6 mmFiller wire sizes (Cored wire)0.8 - 2.0 mmWire feed speed 1 - 25 m/minSoftware WiseFusionWiseRoot+MatchLogPipe Steel pack Fe (25pcs)Operating temperature range-20 ... +40 °CExternal dimensions LxWxH510 × 200 × 310 mmDegree of protection IP23SStandards IEC 60974-5Wire spool weight, max. 5 kgWeight (empty)9.4 kgWire spool diameter, max.200 mm17062019FastMig X13Product code6103522Output 60% ED520 AOutput 100% ED440 AWire feed mechanism4-rollGun connection EuroFiller wire sizes (Ss)0.6 - 1.6 mmFiller wire sizes (Al)0.9 - 2.4 mmFiller wire sizes (Fe)0.6 - 1.6 mmFiller wire sizes (Cored wire)0.8 - 2.0 mmWire feed speed 1 - 25 m/minSoftware WiseFusionWiseRoot+MatchLogPipe Stainless pack Ss (17pcs)Operating temperature range-20 ... +40 °CDegree of protection IP23SWire spool weight, max. 5 kgWeight (empty)9.4 kgWire spool diameter, max.200 mmExternal dimensions510 × 200 × 310 mmWFX 300 P Fe Wire feederProduct code6103531Output 60% ED520 AOutput 100% ED440 AWire feed mechanism GT04Gun connection EuroFiller wire sizes (Ss)0.6 - 2.0 mmFiller wire sizes (Al)0.8 - 2.4 mmFiller wire sizes (Fe)0.6 - 2.0 mmFiller wire sizes (Cored wire)0.8 - 2.4 mmWire feed speed0.5 - 25 m/minSoftware WiseFusionWiseRoot+MatchLogPipe Steel pack Fe (25pcs)Operating temperature range-20 ... +40 °CExternal dimensions LxWxH590 × 240 × 445 mmDegree of protection IP23SStandards IEC 60974-5Wire spool weight, max.20 kgWeight (empty)13.1 kgWire spool diameter, max.300 mm14FastMig X17062019Product code6103532Output 60% ED520 AOutput 100% ED440 AWire feed mechanism GT04Gun connection EuroFiller wire sizes (Ss)0.6 - 2.0 mmFiller wire sizes (Al)0.8 - 2.4 mmFiller wire sizes (Fe)0.6 - 2.0 mmFiller wire sizes (Cored wire)0.8 - 2.4 mmWire feed speed 1 - 25 m/minSoftware WiseFusionWiseRoot+MatchLogPipe Stainless pack Ss (17pcs)Operating temperature range-20 ... +40 °CDegree of protection IP23SWire spool weight, max.20 kgWeight (empty)13.1 kgWire spool diameter, max.300 mmExternal dimensions590 × 240 × 445 mmWFX 200 AMC Wire feederProduct code6103523Output 60% ED520 AOutput 100% ED440 AWire feed mechanism 4 rollGun connection EuroFiller wire sizes (Ss)0.6 - 1.6 mmFiller wire sizes (Al)0.8 - 2.4 mmFiller wire sizes (Fe)0.6 - 1.6 mmFiller wire sizes (Cored wire)0.8 - 2.0 mmWire feed speed 1 - 25 m/minSoftware WiseFusionWisePenetrationWiseThin+MatchLogSteel Pack (14 pcs)Steel Pack for Wise thin+ (14 pcs)Stainless Pack (12 pcs)Aluminum Pack (12 pcs)Operating temperature range-20 ... +40 °CExternal dimensions LxWxH510 × 200 × 310 mmDegree of protection IP23SStandards IEC 60974-5Wire spool weight, max. 5 kgWeight (empty)9.4 kgWire spool diameter, max.200 mm17062019FastMig X15Product code6103533Output440 AOutput 60% ED520 AWire feed mechanism DuraTorqueGun connection EuroFiller wire sizes (Ss)0.6 - 1.6 mmFiller wire sizes (Al)0.8 - 2.4 mmFiller wire sizes (Fe)0.6 - 1.6 mmFiller wire sizes (Cored wire)0.8 - 2.0 mmWire feed speed 1 - 25 m/minSoftware WiseFusionWisePenetrationWiseThin+MatchLogSteel Pack (12 pcs)Steel Pack for Wise thin+ (8 pcs)Stainless Pack (12 pcs)Aluminum Pack (12 pcs)Operating temperature range-20 ... +40 °CExternal dimensions LxWxH625 × 243 × 476 mmDegree of protection IP23SStandards IEC 60974-5Wire spool weight, max.20 kgWeight (empty)12.5 kgWire spool diameter, max.300 mmSOFTWAREWiseFusionProduct code9991014 (FastMig M, FastMigX)X8500000 (X8 MIG Welder)A7500000 (A7 MIG Welder)WiseRoot+Product code9990418 (FastMig X)X8500003 (X8 MIG Welder)WisePenetrationProduct code9991000 (FastMig M, FastMigX)A7500001 (A7 MIG Welder)WiseThin+Product code9990419 (FastMig X)X8500004 (X8 MIG Welder)16FastMig X17062019ACCESSORIESCool X Cooling unitProduct code6068200Cooling liquid - 10 liter can - SP9810765Operating voltage (safety voltage)400 V -15 …+20 %Maximum pressure0.4 MpaExternal dimensions LxWxH570 x 230 x 280 mmWeight (no accessories)11 kgDegree of protection IP23STank volume~3 LEMC class ACooling power 1 kWStorage temperature range-40 …+60 °COperating temperature-20 …+40 °C17062019FastMig X17Kemppi is the pioneering company within the welding industry. It is our role to develop solutions that make you win business. Headquartered in Lahti, Finland, Kemppi employs over 800 welding experts in 17 countries and has a revenue of more than 150 MEUR. Our offering includes welding solutions - intelligent equipment, welding management software and expert services - for both demanding industrial applications and ready-to-weld needs. Local expertise is available via our global partner network covering over 60 countries.。
焊接导电嘴的作用 英文作文

The Role of Welding Nozzles in Conducting ElectricityWelding nozzles play a pivotal role in the process of conducting electricity during welding operations. These specialized components are integral to ensuring efficient and effective welding outcomes across various industries, from construction to manufacturing.Introduction:Welding is a fundamental industrial process that joins materials, typically metals, through the application of heat and pressure. Central to this process is the use of welding nozzles, which facilitate the flow of electricity necessary for generating the heat required to melt and fuse metal components.Body Paragraphs:1.Functionality of Welding Nozzles:o Welding nozzles are designed to direct and control the flow of gases, such as argon or carbon dioxide, which shield the welding area from atmospheric contaminants and prevent oxidation during the welding process. Additionally, they serve as conduits for the electrical current that generates the intense heat essential for melting the welding materials.1.Types and Applications:o There are various types of welding nozzles tailored to different welding techniques and materials. For instance, in gas metal arc welding (GMAW), commonly known as MIG welding, nozzles guide the shielding gas and facilitate electrical conductivity between the welding gun and the workpiece. In TIG (tungsten inert gas) welding, nozzles maintain the flow of shielding gas while directing the electric arc precisely.1.Impact on Welding Quality:o The proper selection and maintenance of welding nozzles significantly impact the quality of welds. Efficient electrical conductivity ensures consistent heat distribution, minimizing defects such as porosity or incomplete fusion. Additionally, the shielding gas directed by the nozzle protects the molten weld pool, enhancing the strength and durability of the weld joint.1.Technological Advancements and Innovations:o Advancements in welding technology continually refine the design and performance of welding nozzles. Modern innovations focus on enhancing durability, optimizing gas flow dynamics, and improving electrical conductivity to meet the demands of complex welding applications in industries ranging from automotive manufacturing to aerospace. Conclusion:In conclusion, welding nozzles are indispensable components in welding processes, serving dual roles in guiding shielding gases and conducting electricity. Their functionality not only ensures the integrity of weld joints but also contributes to the overall efficiency and precision of welding operations across diverse industrial sectors.Understanding the critical role of welding nozzles in conducting electricity underscores their significance in achieving high-quality welds and advancing technological capabilities in welding practices worldwide.。
Yaskawa PX1700 电阻焊控制器说明书

Resistance Welding Solutions2020PX1700WELDING CONTROLMAIN FEATURESPX1700 ECO➢Digital resistance welding control with three numeric displays.➢Control of nine time-parameters: Squeeze, pre-weld, slope-up, weld, pulses, down-slope, post weld, hold time, pause time (with autorepeat function).➢Welding time adjustable in whole or half periods (single-phase AC welding machines) or in milliseconds (three-phase MFDC weldingmachines).➢10 welding programs storable.➢Double cycle start input available for recalling two consecutive programs.➢Weld -No Weld input.➢Control of two solenoid valves with control circuit diagnostics.➢Two end sequence output signals.➢Error signal on display.➢Weld counter.➢USB port for program backup or firmware updates on a USB stick.➢Integrated SCR trigger circuit.➢Pulses for switching on the external SCR ignition card.------------------------------------------------------------------------PX1700 PRO➢Same functions as the PX1700 ECO, in addition:➢100 welding programs storable.➢Weld quality control monitoring by weld current limits (tolerance) in self-teaching mode ➢Weld Counter-RMS weld current measurement➢USB port for backing up programs, firmware updates, welding reports performed in Excel format on a USB stick.➢Date and time clock, with backup battery.➢Analogue output for controlling the HP400 inverter.➢Analogue output for proportional solenoid valve control.➢Alarm output.➢Dedicated inputs for the selection of 31 programs from external devices (such as PLC).➢Programmed electrode force control (in combination with optional proportional solenoid valve).➢RS485 port for expansion.➢Prepared for wireless communication modules.❖REPLACES PX1600 CONTROL ❖SAME PANEL SIZE AND FIT❖MORE FEATURES❖PX1700ECO FITTED TO PBP & PFB MODELS ❖PX1700PRO FITTED TO PF & PFP/PFXMODELSPX1700PX1700 ECO PX1700 PRO Power Supply24V-AC 50/60 Hz24V-AC 50/60 Hz Number of Welding Programs10100 Number of external selectable programs ---31 Number of Solenoid Valves with control circuit diagnostics22 Number of Cycle Initiating inputs 22 Number of Outputs -Weld end sequence22 Weld / No Weld input√√Alarm Output---√Thermostat / Flowswitch Input√√Analogue Output 0÷10V EVP control---√Pre -Post Weld parameters√√Upslope Downslope and Pulsations parameters√√Weld time in whole/half cycle (AC transformers) or milliseconds (MFDC transformers)√√Single weld and Auto-repeat function√√Weld counter √√Measure weld current (RMS value)---√Weld monitor out of limits---√Excel weld log---√USB port√√Built in Thyristor firing circuit√√Output with ignition pulses for external board√√Analogue output controling MF inverter unit---√Date and time clock, with backup battery---√Westermans International LtdUnit 4, Midland Distribution Centre, Markfield Road, Groby, Leicester LE6 0FS, UK.T: +44(0) 1162 696941 E:**********************W: 。
3M Speedglas Welding Shield Series 9100与相关滤片说明书

Description•Is designed to be used together with 3M™ Speedglas™ WeldingShield Series 9100.•Is suitable for most welding applications up to Shade 13 in thedark state.•Has permanent protection (Shade 13 equivalent) against harmfulUV- and IR- radiation, regardless of whether the filter is in thelight or dark state or whether the auto-darkening function isoperational.•Is easy to operate and maintain.•Has seven different Shade Number settings in the dark state,split into two groups 5, 8 and 9-13.•Has seven user selectable levels of detector sensitivity to ensurea reliable arc detection.•Can be locked in a constant dark or light state.•Has excellent visibility in light state, shade 3, for easy weldingpreparation and after treatment.•Has three optical sensors.•Multiple adjustments for highest comfort on helmet and headband.•Solar panel power assistance (except 3M™ Speedglas™ Welding Filter 9100XX and 9100 XXi).•External button to reach grinding mode (3M™ Speedglas™ Welding Filter 9100XXi). Common ApplicationsWhen used with recommended filters, are designed for most welding processes such as:•MMA•MIG/MAG•TIG•Plasma welding•Oxyacetylene welding/cutting•Grinding applicationseye protection.Approvals/Standards•ANSI Z87.12 3M™ Speedglas™ Welding Filter 9100 Technical Specification - Release 1, January 2018Equipment MarkingsAdditional MarkingsLimitations of Use•Only use with original 3M branded spare parts and accessories listed in the user instructions and within the usage conditions given in the technical specifications.•The use of substitute components, decals, paint or other modifications not specified in these user instructions might seriously impair protection and may invalidate claims under the warranty or cause the product to be non-compliant with protection classifications and approvals.•Eye protectors worn over standard ophthalmic spectacles may transmit impacts thus creating a hazard to the wearer.•Use of this product in applications outside its intended use, such as laser welding/cutting, may result in permanent eye injury and vision loss.•Should the product fail to switch to the dark state in response to an arc, stop welding immediately and inspect the welding filter as described in the instructions. Continued use of a welding filter that fails to switch to the dark state may cause temporary vision loss. If the problem cannot be identified and corrected, do not use the welding filter, contact your supervisor, distributor or 3M for assistance.Technical SpecificationsApproximate Weight3M™ Speedglas™ 9100V Welding Filter 3M™ Speedglas™ 9100X Welding Filter 3M™ Speedglas™ 9100XX Welding Filter 3M™ Speedglas™ 9100XXi Welding Filter 160 g (5.64 oz.)180 g (6.53 oz.)200g 200gViewing Area3M™ Speedglas™ 9100V Welding Filter 3M™ Speedglas™ 9100X Welding Filter 3M™ Speedglas™ 9100XX Welding Filter 3M™ Speedglas™ 9100XXi Welding Filter 1.77 x 3.66 in (45 x 93 mm)2.13 x 4.21 in (54 x 107 mm)2.87 x 4.21 in (73 x 107 mm)2.87 x 4.21 in (73 x 107 mm)Switching Time (light-dark)0.1 ms (+23° C)UV/IR Protection Shade 13 (permanent)Light State Shade 3Dark State Shade 5, 8–13Fail/Safe State Shade 5Battery TypeLithium 3V Type CR2032 (2)Battery Lifetime3M™ Speedglas™ 9100V Welding Filter 3M™ Speedglas™ 9100X Welding Filter 3M™ Speedglas™ 9100XX Welding Filter 3M™ Speedglas™ 9100XXi Welding Filter 2800 hours 2500 hours 2000 hours 1800 hoursOperating Temperature 23ºF to 131ºF (-5ºC to +55ºC)Material Filter:Protection plage:PA PCShall be disposed of as electrical and electronic wasteRead the instructions before usePersonal Safety Division3M Center, Building 235-2W-70St. Paul, MN 55144-10003M PSD products are occupational use only.© 3M 2019. All rights reserved.3M and Speedglas are trademarks of 3M Company and its affiliates. Used under license in Canada. All other trademarks are property of their respective owners.Please recycle.May 2019In United States of America Technical Service:1-800-243-4630Customer Service:/workersafety In CanadaTechnical Service:1-800-267-4414Customer Service:1-800-364-35773M.ca/SafetySpare Parts and AccessoriesSpare Parts 60-0000-10Speedglas auto-darkening welding filter 9100V 5, 8, 9-1306-0200-52Outer protection plate scratch resistant, pkg of 1060-0000-20Speedglas auto-darkening welding filter 9100X 5, 8, 9-1306-0200-53Outer protection plate heat resistant, pkg of 1060-0000-30Speedglas auto-darkening welding filter 9100XX 5, 8, 9-1306-0200-10Inner protection plate for 9100V filter, pkg of 5 (marked 117x 50)60-0000-30i Speedglas auto-darkening welding filter 9100XXi 5, 8, 9-1306-0200-20Inner protection plate for 9100X filter, pkg of 5 (marked 117x 61)60-0000-30i-KIT Speedglas welding filter and silver front 9100 XXi 06-0200-30Inner protection plate for 9100XX/ 9100XXi filters, pkg of 5 (marked 117x 77)06-0400-55Battery holder for Speedglas welding filter series 9100 pkg of 206-300-55i Speedglas silver front 9100XXi 06-0200-51Outer protection plate standard, pkg of 1004-0320-00Battery, pkg of 2Accessories and Consumables06-0500-56Magnifying lens x1.506-0500-58Magnifying lens x2.006-0500-57Magnifying lens x1.506-0500-59Magnifying lens x2.5。
堆焊总结篇

堆焊的发展概述随着自动化制造的大力发展,堆焊作为表面工程中的重要分支,其自动化智能化受到了国内外很多学者的重视。
近年来研究者在堆焊技术上取得了很多新的进展与突破。
国内方面,2006年河南科技大学[1]提出了将可编程控制器(PLC)运用到自动堆焊焊中,以PLC和气保焊为主控单元,以2台步进电机驱动器带动步进电机执行单元,在x-y平面通过滚丝杠带动滑台和焊枪移动,实现了对火车车钩进行的自动堆焊。
徐立权[2]在机器人熔丝堆焊成形机及其路径规划研究一文中,将UG NX4.0 CAM 铣削轨迹的获得方法用运到了堆焊的轨迹上,并分析了它们的异同,利用 UG CAM 的仿真功能对堆焊轨迹进行了仿真,并在汽车翼子板的自动堆焊上实现了应用。
王新辉[3]在基于Pro/E的相贯曲面堆焊运动仿真分析一文中,针对石油钻采专用阀门内壁复杂曲面的自动堆焊,在堆焊设备的研发过程中,建立了阀门内壁相贯曲线的数学模型,规划了堆焊焊枪的运动轨迹.在Pro/E软件工作环境下,建立了堆焊设备的三维实体模型,定义了运动连接,设定了伺服电机参数,进行了堆焊设备虚拟样机的计算机运动仿真试验,通过仿真分析,生成了运动轨迹曲线并进行了仿真误差分析,验证了该数学模型建立的正确性,为堆焊设备的研制提供了相应的虚拟样机仿真技术支撑。
南昌航空大学王龙杰[4]综合目前计算机辅助工艺技术CAPP的优缺点,针对堆焊焊接工艺特点以及参照相关标准的基础上,以Oracle10g为数据库平台,在Windows XP环境下,开发出了一款集工艺数据的存储、查询和管理为一体的计算机辅助堆焊工艺设计系统。
用户通过本系统完成堆焊工艺设计后,将自动生成堆焊焊接工艺卡,工艺卡可以通过系统中的Office、AutoCAD、PDF等接口输出,大大提高了堆焊的自动化程度。
周方明[5]将气缸盖的机器人堆焊中,应用KUKA SIM Pro软件,在 Pro/E 中建立所需的三维模型,模型导入KUKA SIM Pro对所建立的模型添加约束,使模型能够按照所要求的方式运动,进行了焊接机器人工作系统仿真实验,优化了焊接路径和焊枪姿态,使得系统可有效地防止机器人与障碍物发生碰撞并保证其手臂具有良好的可达性。