MBSDLecture 202-Motor Model, Display Subsystem
贝尔DSLAM维护命令手册
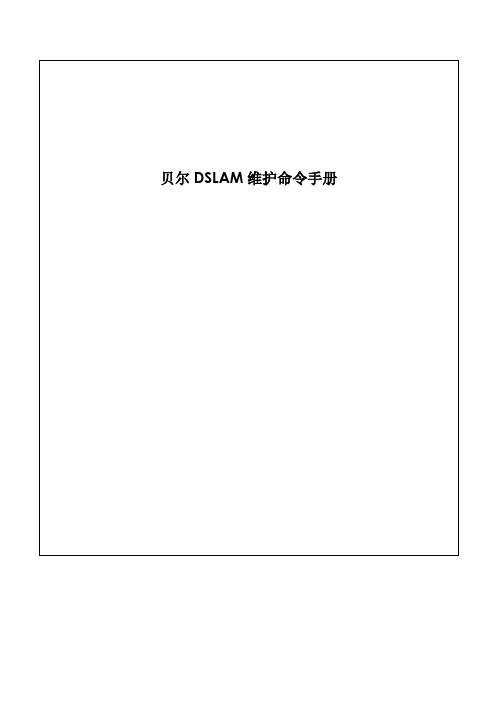
目录Contents一、编写概述 (3)二、适用范围 (3)三、常用操作及命令 (3)(一)配置操作 (3)1.配置IP地址 (3)2.配置模板 (3)3.配置用户板 (4)4.配置上联口 (5)5.配置VLAN (6)6.配置SNMP (6)7.配置XDSL端口 (7)8.配置ATM PVC (7)9.配置bridge port (7)(二)查看操作 (7)1.查看软件版本 (7)2 .查看上联端口 (8)3.查看板卡 (9)4.查看用户端口 (10)5.查看MAC地址 (11)6.查看用户Bridge端口信息 (12)(三)常用操作命令 (12)1.打开/关闭端口 (12)2.修改端口速率模板 (13)(四)其他操作 (13)1.登陆用户名和口令 (13)2.系统时钟 (14)3.命令提示符 (14)4.ACL访问控制 (14)5.数据备份和恢复 (15)6.告警查询 (15)7.系统重启 (15)四、常见故障及维护建议 (16)(一)常见故障 (16)1.无法同步 (16)2.频繁掉线 (16)3.同步无法拨号 (18)4.自动工单系统操作失败 (18)5.用户上网慢 (19)(二)维护建议 (20)1.检查节点备份文件 (20)2.检查节点板卡温度 (20)附录Trace&Debug命令介绍 (20)一、编写概述为帮助更好维护7302ISAM设备,编写本文档。
本文档所有命令以R2.4为基础,可能因为版本不同而有所变化,具体请参各个版本的命令手册。
二、适用范围本手册适用于所有现场工程师、局方维护人员。
三、常用操作及命令(一)配置操作1.配置IP地址从R2.4开始,7302支持单IP管理地址。
configure system single-public-ipconfigure system management host-ip-address manual:192.168.1.100/24查看配置info configure system management2.配置模板线速模板configure xdsl service-profile 1 name 2M-640K-Fastconfigure xdsl service-profile 1 min-bitrate-up 64 min-bitrate-down 64 plan-bitrate-up 640 plan-bitrate-down 2048 max-bitrate-up 640 max-bitrate-down 2048 max-delay-up 1max-delay-down 1 active其中max-delay-up、max-delay-down定义交织延时,=1表示Fast模式查看配置info configure xdsl service-profile 1协议模板configure xdsl spectrum-profile 1 name adsl2plus g992-5-aconfigure xdsl spectrum-profile 1 active其中7302默认配置如下协议,见表3-2-1:g992-5-a为ADSL2+ over POTS协议,需要单独添加,也可以按需添加其他协议,如AnnexM协议等,具体参照标准协议手册。
SIM800_硬件设计手册_V1.05

SIM800_硬件设计手册_V1.05
2
2015-02-27
目录
Smart Machine Smart Decision
1. 绪论............................................................................................................................................................... 10
Bulletin 140MT Enclosed Motor Protection Circuit B

Technical DataOriginal InstructionsBulletin 140MT Enclosed Motor Protection Circuit Breakers Bulletin Number 140MTTopic PageProduct Overview2Features2Standards Compliance and Certifications2Catalog Number Explanation3Product Selection3Accessories4Specifications6Approximate Dimensions7Additional Resources9Bulletin 140MT Enclosed Motor Protection Circuit Breakers Product OverviewBulletin 140MT enclosed Motor Protection Circuit Breakers (MPCBs) consist of a Bulletin140MT MPCB in a metallic Type 1/3/3R/4/12 enclosure.Bulletin 140MT MPCBs or Motor Protective Switching Devices (MPSDs) are UL Listed asManual, Self-Protected Combination Motor Controllers (Type E) and Manual MotorControllers (with approvals for Suitable as Motor Disconnect and Suitable for use inGroup Installation).When they are cULus Listed as Manual, Self-Protected Combination Motor Controllers,the 140MT MPCBs provide all of the necessary NEC/CEC requirements for the protectionand control of individual motor branch circuits without additional branch circuitprotective devices.According to UL 60947-4-1, CSA C22.2 No.60947-4-1, these devices may provide thefollowing control and protection functions.•Disconnect for motor branch circuit•Short-circuit protection (magnetic protection)•Overload protection (thermal protection)•Manual switching (motor control means)Features• Current range 0.1…25 A• cULus Listed for control and protection of motor loads-Motor disconnect-Short-circuit and overload protection-Motor switching (magnetic)Standards Compliance and Certifications•Enclosure types 1/3/3R/4/12•cULus Listed:-UL60947-4-1-CSA C22.2,No.60947-4-1Bulletin 140MT Enclosed Motor Protection Circuit Breakers Catalog Number ExplanationCatalog Number ExplanationProduct Selection140MT-F -CA16X a baBBulletin NumberCurrent Range [A]Code DescriptionCode Description 140MT-FMetal enclosed C/D framesCA16X 0.10…0.16CB16X 1.0…1.6DB25X 1.6…2.5DB40X 2.5…4.0DB63X 4.0…6.3DC10X 6.3…10DC16X 10…16DC20X 14.5…20DC25X18 (25)Table 1 - Motor Protective Switching DevicesRated Operational Current (I e ) [A]Motor Current Adjustment Range [A]Nominal Magnetic Trip Current [A]Max Short-circuit Current [kA]Max. 3-phase Hp Ratings (1)(1)Horsepower/kW ratings shown are for reference. The final selection of the MPCB/MPSD depends on the actual motor full load current.Max. kW, 3-Phase — AC-3(1)Cat. No.EnclosureSize480Y/277V 600Y/347V 200V 230V 480V 600V 230V 400/415V 500V 690V3PH 1PH 25 A Frame Size0.160.10…0.16 2.2 3.46550—————0.020.060.06140MT-F-CA16X A 10.63…1.014216550——0.50.750.180.250.370.55140MT-F-CB10X A 1.6 1.0…1.622346550——110.250.550.75 1.1140MT-F-CB16X A 2.5 1.6…2.5355365300.50.75 1.520.370.75 1.1 1.8140MT-F-DB25X A 4 2.5…4.05684653011330.75 1.5 2.23140MT-F-DB40X A 6.3 4.0…6.3881326530 1.5255 1.5 2.234140MT-F-DB63X A 10 6.3…101402106530337.510 2.24 6.37.5140MT-F-DC10X A 1610…16224336653035101547.51013140MT-F-DC16X A 2014.5…2028042065—57.51520 5.5101117140MT-F-DC20X A 2518…2535052550—7.57.51520 5.5111522140MT-F-DC25X ABulletin 140MT Enclosed Motor Protection Circuit Breakers AccessoriesAccessoriesTable 2 - Auxiliary ContactsX = Contact Closed; O = Contact Open (2)Connection Diagram Reference:Table 3 - Shunt Trip UnitsConnection Diagram Reference:I >>140M/MT Operator Overload (thermal) Trip Short-circuit (magnetic) TripI >>140M/MT Operator Overload (thermal) Trip Short-circuit (magnetic) TripBulletin 140MT Enclosed Motor Protection Circuit Breakers AccessoriesTable 4 - Trip Contacts(2)Connection Diagram Reference:Table 5 - Undervoltage Trip UnitsConnection Diagram Reference:I >>140M/MT Operator Overload (thermal) Trip Short-circuit (magnetic) TripI >>140M/MT Operator Overload (thermal) Trip Short-circuit (magnetic) TripBulletin 140MT Enclosed Motor Protection Circuit Breakers SpecificationsSpecificationsTable 6 - Motor Protection Circuit Breaker General DataAttribute140MT-C 140MT-D Standards compliance cULusUL 60947-4-1, CSA C22.2, No. 60947-4-1Rated Insulation Voltage U iUL/CSA[V]600Y/347VRated Impulse Withstand Voltage U imp Pollution degree3Main circuits U imp /Overvoltage Category 6 kV/III, 8 kV (Disconnect)Auxiliary circuits U imp /Overvoltage Category6 kV/III Rated Frequency [Hz]45-65Life Span Mechanical[operations]100,000Electrical (I e max.)[operations]100,000Switching Frequency [operations/hour]max. 25Ambient Temperature Storage [ °C ( °F)]-40…+85 (-40…+185)Operation [ °C ( °F)]-25…+40 (-13…+104)Climatic resistance Operating Humidity/Moisture heat (60068-2-3)5…95% Non-condensing Site Altitude [m]to 2000 N.N. (6561 ft)Protection ClassIP2X from all directionsResistance to Shock, Transport (60068-2-27)ON 15 G/11 ms OFF 30 G/11 ms Resistance to Vibration, Operation (60068-2-6) 5 G Rated Thermal Current I th up to 40 °C (104 °F) ambient temperature [A]0.1…320.63…40Rated Supply Current I e [A]0.1 (25)0.63 (40)Dependence on Temperature 40 °C (104 °F)[A]no reduction Phase-loss Protection Differential release Trip class10 fixed setting Magnetic Release Fixed setting Release current (±20%)[A]14 x I e max.(1)(1)I e max. = maximum values of setting ranges; see ratings.Total Power loss P vCircuit Breaker at rated load/operating temp.[W]4 (11)4…14Main Disconnect Switch ApplicationYes, with accessoriesBulletin 140MT Enclosed Motor Protection Circuit Breakers Approximate DimensionsApproximate DimensionsDimensions are in millimeters (inches) and are not intended to be used for manufacturing purposes.Enclosure Style ATable 7 - MPCB Connecting CharacteristicsTable 8 - Enclosure SpecificationsDescription140MT-F Construction Material MetalStructure Finish Painted textured light gray Ingress Rating IP66 (Type 1/3/3R/4/12)HandleIP66 Protection Type 1/4/4X/12, Interlock override capabilityHandle LockingFor 3 padlocks 4…8 mm (5/16 in.) in diameterAmbient Temperature0…+40 °C (32…+104 °F)Storage Temperature Range -50…+80 °C (-58…+176 °F)Altitude2000 m (6561 ft)Bulletin 140MT Enclosed Motor Protection Circuit Breakers Approximate Dimensions Notes:Bulletin 140MT Enclosed Motor Protection Circuit Breakers Technical DataAdditional ResourcesThese documents contain additional information concerning related products from Rockwell Automation.You can view or download publications at rok.auto/literature .ResourceDescriptionMotor Protection Circuit Breaker and Motor Circuit Protector Specifications, publication 140-TD005Provides assistance with selecting a motor protection circuit breaker, including catalog number explanation, specifications, wiring diagrams, accessories, and product dimensions.UL Standards Listing for Industrial Control Products, publication CMPNTS-SR002Assists original equipment manufacturers (OEMs) with construction of panels, to help ensure that they conform to the requirements of Underwriters Laboratories.American Standards, Configurations, and Ratings: Introduction to Motor Circuit Design, publication IC-AT001Provides an overview of American motor circuit design based on methods that are outlined in the NEC.Industrial Components Preventive Maintenance, Enclosures, and Contact Ratings Specifications, publication IC-TD002Provides a quick reference tool for Allen-Bradley industrial automation controls and assemblies.Safety Guidelines for the Application, Installation, and Maintenance ofSolid-state Control, publication SGI-1.1Designed to harmonize with NEMA Standards Publication No. ICS 1.1-1987 and providesgeneral guidelines for the application, installation, and maintenance of solid-state control in the form of individual devices or packaged assemblies incorporating solid-state components.Industrial Automation Wiring and Grounding Guidelines, publication 1770-4.1Provides general guidelines for installing a Rockwell Automation industrial system.Product Certifications website, rok.auto/certifications .Provides declarations of conformity, certificates, and other certification details.Publication 140-TD006A-EN-P - June 2022Rockwell Automation SupportUse these resources to access support information.Documentation FeedbackYour comments help us serve your documentation needs better. If you have any suggestions on how to improve our content, complete the form at rok.auto/docfeedback .Technical Support Center Find help with how-to videos, FAQs, chat, user forums, and product notification updates.rok.auto/supportKnowledgebaseAccess Knowledgebase articles.rok.auto/knowledgebase Local Technical Support Phone Numbers Locate the telephone number for your country.rok.auto/phonesupport Literature LibraryFind installation instructions, manuals, brochures, and technical data publications.rok.auto/literature Product Compatibility and Download Center (PCDC)Download firmware, associated files (such as AOP, EDS, and DTM), and access product release notes.rok.auto/pcdcRockwell Automation maintains current product environmental compliance information on its website at rok.auto/pec .Allen-Bradley, expanding human possibility, and Rockwell Automation are trademarks of Rockwell Automation, Inc.Trademarks not belonging to Rockwell Automation are property of their respective companies.Rockwell Otomasyon Ticaret A.Ş. Kar Plaza İş Merkezi E Blok Kat:6 34752, İçerenköy, İstanbul, Tel: +90 (216) 5698400 EEE Yönetmeli ğine Uygundur。
MSA2000简易管理手册v1.1_20140315
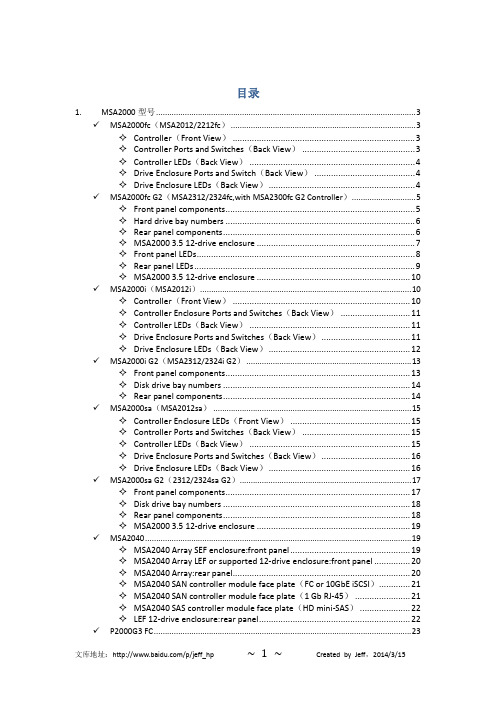
Created by Jeff,2014/3/15
Front panel components............................................................................. 23 Disk drive bay numbers .............................................................................. 24 Rear panel view – controller module .......................................................... 24 Rear panel components.............................................................................. 25 P2000 6Gb 3.5 12-drive enclosure .............................................................. 25 MSA2000 3Gb 3.5 12-drive enclosure ......................................................... 26 P2000G3 iSCSI .................................................................................................................27 Front panel components............................................................................. 27 Disk drive bay numbers .............................................................................. 28 Rear panel views – controller modules ....................................................... 28 Rear panel components.............................................................................. 29 P2000 6Gb 3.5 12-drive enclosure .............................................................. 30 MSA2000 3Gb 3.5 12-drive enclosure ......................................................... 30 P2000G3 SAS...................................................................................................................31 Front panel components............................................................................. 31 Disk drive bay numbers .............................................................................. 32 Rear panel view – controller module .......................................................... 32 Rear panel components.............................................................................. 33 P2000 6Gb 3.5 12-drive enclosure .............................................................. 33 MSA2000 3Gb 3.5 12-drive enclosure ......................................................... 34 2. MSA2000 管理方式............................................................................................................35
DS202用户手册说明书

ratings information before making connections to the device.
W a r n i n g
● Do not operate in wet/damp conditions. ● Do not operate in a potentially inflammable/explosive atmosphere. ● Please keep the surface of the product clean and dry.
Downward selection(Slide Down)
Reset Parameter(Tap Right/increase, slide Right)
Alter set up parameter(Tap Left/Reduce, Slide Left)
M
On/Off Sub-menu
Note that each item's color in Parameter Area is the same as that in Measurement Area
Chapter 4 Basic Function P14
Chapter 5 Product Inspection P20
Chapter 7 Technical Support P22
Chapter 6 Battery Disposal P21
This user manual is based onAPP V1.28
●
W a r n i n g Use proper power cord. Please use power cord specified for this product and
诺基亚智能手机使用指南说明书
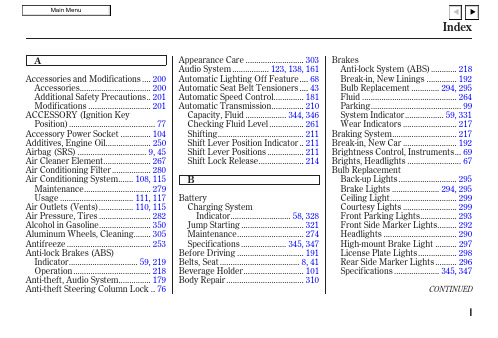
C
Capacities Chart .................... 344, 346 Carbon Monoxide Hazard .............. 52 Carrying Cargo .............................. 202 Cassette Player
Charging System Indicator .... 58, 328 Checklist, Before Driving............. 206 Child Safety ...................................... 20 Child Seats........................................ 25
Before Driving ............................... 191 Belts, Seat ..................................... 8, 41 Beverage Holder............................ 101 Body Repair .................................... 310
Maintenance............................... 279 Usage .................................. 111, 117 Air Outlets (Vents)................ 110, 115 Air Pressure, Tires ........................ 282 Alcohol in Gasoline........................ 350 Aluminum Wheels, Cleaning........ 305 Antifreeze ....................................... 253 Anti-lock Brakes (ABS) Indicator................................ 59, 219 Operation .................................... 218 Anti-theft, Audio System............... 179 Anti-theft Steering Column Lock .. 76
数位示波器使用说明
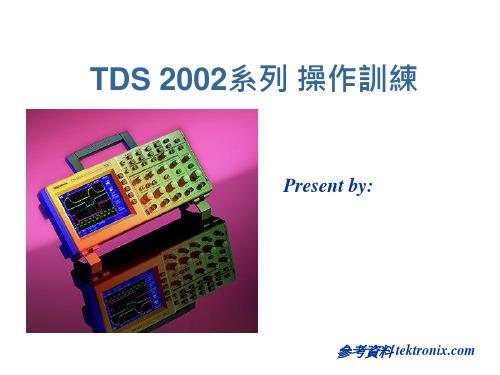
40-100
>100
160-300
>300
Respiratory Block 呼吸阻塞 Usually fatal 致命
數位示波器前面板的四大系統
選單按鈕
D. 選單和控制鈕
A.垂直
B.水平 C.觸發
探棒檢查
輸入接頭
前面板功能解說
1.多功能旋鈕 2.垂直位置 3.垂直刻度 4.智慧型自動設定 5.單擊觸發 6.執行/停止 11. 探棒補償信號 7. 水平位置 12. 探棒檢查鈕(Probe ch. 外部觸發
斜率 模式 耦合
選擇訊號的上升緣或下降緣來觸 發 選取觸發的方式 選取套用至觸發電路的觸發訊號 元件
C 觸發系統-選單(MENU) –類型/視頻
選項 視頻 設定 註解 當反白顯示視頻的情況下,在NTSC、 PAL、或SECAM標準視頻訊號上產生觸發 觸發耦合會預設為”交流”。 CH1 CH2 Ext Ext/5 一般 反向 掃描線 線數 奇數場 偶數場 所有場 選取輸入來源做為觸發訊號。 Ext和Ext/5使用套用至EXT TRIG接頭的訊 號做來源 “一般”是在同步脈波的負邊緣觸發,而反 向則是在同步脈波的正邊緣觸發 選取適當的視頻同步 當您選取”同步“選項的”線數”時,可旋轉 USER SELECT旋鈕來指定線數
TDS 2002系列 操作訓練
Present by:
參考資料
訓練內容大綱
如何安全使用示波器
數位示波器四大系統
面板功能解說 背板功能解說
選單操作模式
測棒補償 各選單功能解說及應用
選購模組
問題與解答
安全重要的量測觀念
馬達控制 交換式電源供應器 變頻器 三相電源 不斷電系統(UPS) 程控設備
ABBDCS400直流调速器调试(工程师培训)

ABBDCS400直流调速器调试(工程师培训)ABB DCS 400 系列直流调速器自整定调试步骤参数Par No 参数功能阐述1.01Arm cur Nom(电机额定电流) 根据电机铭牌设定1.02Arm V olt Nom (电机额定电压) 根据电机铭牌设定1.03Field Cur Nom (励磁额定电流) 根据电机铭牌设定1.04Field V olt Nom(额定励磁电压) 根据电机铭牌设定1.05Base Speed (电机额定转速) 根据电机铭牌设定1.06Max Speed (电机最大转速) 根据电机铭牌设定1.10Net Under Trip=10%(主电源欠压跳闸门限)6.11DO1 Assign =10 (数字输出1的设定,无故障或报警) 6.05 AO1 Assign =1 (AO1模拟输出定义) 实际速度值6.07 AO1 Scale 100% (AO1输出信号为100%时对应的电压)如AO1接转速显示时,根据实际比列调节6.08 AO2 Assign =5 (AO2模拟输出定义) 实际电枢电流6.10 AO2 Scale 100% (AO2模拟输出定义)实际电枢电流值如AO2接电流显示时,根据实际比例调节百分比引导调试开始1 首先调到菜单Long/Short Par Ling (长短菜单选择)=Long2 选择功能菜单Commissioning(通过控制盘进入调试向导)7.01 Language (语言选择)=English >>>2.01 Macro Select (应用宏)=Standard(工厂宏)>>>1.02 Arm V olt Nom (电枢额定电压)=440V>>>1.01 Arm Cur Nom(电枢额定电流)=见电机铭牌>>>1.04 Field V olt Nom(磁场额定电压)=见电机铭牌>>>1.03 Field Cur Nom(磁场额定电流)=见电机铭牌>>>1.05 Base Speed (电机额定转速)=见电机铭牌>>>Field weakening(是否弱磁)=Yes>>>1.06 Max Speed直接按确定>>>4.06 Field Trip 直接按确定>>>2.03 Stop Ramp 直接按确定>>> 5.09 Accel Ramp 直接按确定>>> 2.04 Eme Stop Mode 直接按确定>>> Field Autotuning (励磁电流调节器自动整定)=Yes>>> Start Drive (按启动键,使电机磁场上电) 然后屏幕显示Please wait .稍等片刻后,屏幕出现Press Enter(请按确认键)。
潍坊特斯拉模型的内部配置指南说明书

VISUAL INDEX1Headlights/fog lights*/turn signals/ LaneWatch* 2 TRIP knobBrightness control3 Wipers/washers4 Cruise control buttons*Adaptive Cruise Control (ACC) with Low Speed Follow (LSF) buttons*5 Horn6Voice recognition/Bluetooth HandsFreeLink buttons7 A udio controls8 Instrument panelInformation display*Driver Information Interface*9Lane Keeping Assist System (LKAS) button*10Vehicle Stability Assist (VSA) OFF buttonRoad Departure Mitigation (RDM) button*Collision Mitigation Braking System (CMBS) OFF button*Tire Pressure Monitoring System (TPMS) button*11 Display/information button*VISUAL INDEX*if equippedQuickly locate items in the vehicle’s interior.Steering Wheel and Nearby Controls2571310648911INSTRUMENT PANELVehicle Settings*Use the Driver Information Interface to customize certain features. Use thesteering wheel controls to select the Vehicle Settings screen when the vehicle is stopped.Press to go to the next display.ENTER buttonPress to make a selection.Scroll to Vehicle Settings.buttonPress to scroll upwards.*if equippedBelow is an example of how to change a setting.1.Press the display/info button until you see the Vehicle Settings screen. Press the ENTER button to select it.2.Press the p or q button to scroll to Meter Setup, and select it.3.Scroll to “Trip A” Reset Timing, and select it.4.Scroll to the option you want, and select it.5.Scroll to the Exit option, and select it. Repeat to exit the menus.AUDIO AND CONNECTIVITYSteering Wheel ControlsYou can operate certain functions of the audio system using the steering wheel controls.Models with information displaySOURCE button: Cycle through available audiomodes.+ / - buttons: Adjust audio volume.t / u buttons: Change presets, tracks, albums, orfolders.FM/AM RadioPress t or u for the next or previous preset station.Press and hold t or u to seek the next or previous strong station.iPod/USB/Bluetooth AudioPress t or u for the next or previous track.Press and hold t or u for the next or previous folder (USB).Models with Driver Information Interfacebutton: Press until the audio screen is displayedin the Driver Information Interface.+ / - bar: Press the ends of the bar to adjust audiovolume.t / u buttons: Change presets, tracks, albums, orfolders.ENTER button: Make audio selections in the Driver Information Interface.*if equippedAUDIO AND CONNECTIVITYp / q buttons: Cycle through available audio modes, or scroll through audio options in the Driver Information InterfaceFrom the audio screen in the Driver Information Interface:FM/AM/SiriusXM Radio*Press the ENTER button to display a preset list. Press p or q to scroll the list, and press the ENTER button to select a B Flash DrivePress the ENTER button to display the folder list. Press p or q to scroll the list, and press the ENTER button to select a folder. Repeat to select a track.iPodPress the ENTER button to display the iPod list. Press p or q to scroll thecategory, and press the ENTER button to select an item. Repeat to select a track.Bluetooth AudioPress the ENTER button to display the track list. Press p or q to scroll the list, and press the ENTER button to select a track.Pandora*Press the ENTER button to display the station list. Press p or q to scroll the list, and press the ENTER button to select a station.*if equippedFM/AM/SiriusXM Radio*Press t or u for the next or previous preset station.Press and hold t or u to seek the next or previous strong station.iPod/USB/Bluetooth AudioPress t or u for the next or previous track.Press and hold t or u for the next or previous folder (USB).Pandora*Press u for the next song.Press and hold t or u for the previous or next station.Models with Display AudioBasic HFL OperationMake and receive phone calls using the vehicle’s audio system, without handling your phone. Visit /handsfreelink to check compatibility.To reduce the potential for driver distraction, certain manual functions may be inoperable or grayed out while the vehicle is moving. Stop or pull over to perform the function. Voice commands are also available.Hang-Up/Back button: End or decline a call, or cancelan operation.Pick-Up button: Answer an incoming call.Talk button: Make a call using a stored voice tag, orsay voice commands*.button: Press until the phone screen is displayed in the Driver InformationInterface.p / q buttons: Scroll the phone list in the Driver Information Interface.ENTER button: From the phone screen in the Driver Information Interface,select from Speed Dial, Call History, or Phonebook.*vehicles with navigationModels with Display AudioSiri ® Eyes FreeActivate Siri through your vehicle when an iPhone is paired to the system. Visit /handsfreelink to check phone compatibility.Here are some examples of Siri commands:“Call John Smith”“Read my new text message”“Find a nearby sushi restaurant”Notes:•Any requests that include visual feedback from Siri on your phone are not displayed in the vehicle.•Certain commands rely on the iPhone’s features and existing apps.•To hear turn-by-turn directions or songs through the vehicle, set the audio source to Bluetooth Audio.•If using Siri Eyes Free through Apple CarPlay, use the Talk button to activate and deactivate Siri Eyes Free mode.“Remind me to pick up dinner”“Set up a meeting today at 3 p.m.”“Play song XYZ”Free modeTalk button: Press and hold to activate Siri Eyes Free mode. Say your command after you hear the Siri tone.Siri and iPhone are trademarks of Apple, Inc.Learn how to enter a destination and operate the navigation system.Basic Navigation OperationA real-time navigation system uses GPS and a map database to show your current location and help guide you to a desired destination. You can operate the system using voice commands or the system controls.To reduce the potential for driver distraction, certain manual functions may be inoperable or grayed out while the vehicle is moving. Voice commands are always available.Steering Wheel ControlsUse the steering wheel controls to say voice commands.Talk Button Tips•When using the Talk button, wait for a beep before saying a command.•To bypass the system prompts, simply press the Talk button again to say your command.•Speak in a clear, natural voice.•The system recognizes only those commands in the Voice Command Index.•Reduce all background noise.••Close the windows and moonroof.Back button: Press to cancel a command or operation. Talk button: Press to say navigation commands.NAVIGATION**if equippedSystem Guidance VolumeAdjust the navigation system volume.1.From the HOME screen, select Settings. 2.Select System.3.Select the Sound/Beep tab.4.Select Guidance Volume, and adjust the level. Select OK when complete.5.Press BACK to exit the menus.Cruise Control*Maintain a constant vehicle speed without having to keep your foot on theaccelerator pedal. Use cruise control on highways or open roads where you can travel at a constant speed with little acceleration or deceleration.*if equippedAdjusting the Vehicle SpeedPress the RES/+ button to increase speed, or the -/SET button to decrease speed.Each time you press the button, the vehicle speed is increased or decreased by about 1 mph (1.6 km/h). If you keep the button pressed, the vehicle speed increases or decreases until you release it. Canceling Cruise ControlPress the CANCEL button or the brake pedal. The CRUISE CONTROL indicator goes off.After cruise control has been canceled, you can still resume the prior set speed by pressing RES/+ while driving at a speed of at least 25 mph (40 km/h).Press the CRUISE button to turn the system off.。
宝马4S店维修培训手册:F02 电视系统 技术培训

8
为了排除后窗玻璃加热装置产生的干扰信号, 在带有 ISDB-T 视频模块的日规车辆上,行驶
TV2 和 TV3 天线使用了带阻滤波器。
期间不使用 TV3 天线接收电视信号。
只有带 DVB-T RSE 的车辆才需要 TV3 天 线,以便可以在行驶期间接收电视信号。
9
带有后座区娱乐系统 Professional(SA 6FH)的电视系统电路图
15 视频模块(VM)
车辆信息计算机(CIC)
16 视频开关(VSW)
自动恒温空调(IHKA)控制单元 17 全景摄像机控制单元(TRSVC)
控制器(CON)
18 后座区显示屏(FD)
后座区显示屏 2(FD2)
19 夜视系统电子装置控制单元(NVE)
后座区娱乐系统(RSE)控制单元 20 转向柱开关中心(SZL)
• 英国 • 美国 / 加拿大 • 澳大利亚 • 日本
• 拉紧驻车制动器或 • 在带有自动变速箱的车辆上选档杆位于“驻
车”位置。
在第二组国家中不启用 CIC 的视频功能。
视频 DVD 光盘可以按以下方式播放:
CIC
DVD 换碟机
从前部访问(CIC) 发出媒体“无法识别” 播放提示信息、音频 信息
从后部访问(RSE)发出媒体“无法识别” 播放媒体
彩色电视系统有世界通用的三种不同制式:
• PAL • NTSC • SECAM.
视频开关不再安装在新视频模块内。现在该模 块是一个独立部件。
如果电台已存储在电台列表中,则即使切换到 其它发射频率的接收范围内,也可以重新查找。
视频模块为这些彩色电视系统提供支持。根据 国家设置选择相应的电视系统。用户可更改该 设置。
信息
Model 6080–202 救护车床轮胎刹车改进说明书

Model 6080–202Ambulance Cot WHEEL BRAKE RETROFIT INSTRUCTION MANUAL For Parts or Technical Assistance1–800–327–0770Table of Contents. . . . . . . . . . . . . . . . . . . . . . . . . . . . . . . . . . . . . . . . . . . . . . . . . . . . . . . . . . . . . . . . . . . . . . . . . . . . . . . . Introduction2. . . . . . . . . . . . . . . . . . . . . . . . . . . . . . . . . . . . . . . . . . . . . . . . . . . . . . . . . . . . . . . . . . . . . . . Safety Precautions3, 4Warranty. . . . . . . . . . . . . . . . . . . . . . . . . . . . . . . . . . . . . . . . . . . . . . . . . . . . . . . . . . . . . .Obtaining Parts and Service5. . . . . . . . . . . . . . . . . . . . . . . . . . . . . . . . . . . . . . . . . . . . . . . . . . . . . . . . .Supplemental Warranty Coverage5. . . . . . . . . . . . . . . . . . . . . . . . . . . . . . . . . . . . . . . . . . . . . . . . . . . . . . . . . . . . . . . . . . . .Return Authorization6. . . . . . . . . . . . . . . . . . . . . . . . . . . . . . . . . . . . . . . . . . . . . . . . . . . . . . . . . . . . . . . . . .Freight Damage Claims6. . . . . . . . . . . . . . . . . . . . . . . . . . . . . . . . . . . . . . . . . . . . . . . . . . . . . . . . . . . . . . . . . . . . . Mounting Instructions7, 8. . . . . . . . . . . . . . . . . . . . . . . . . . . . . . . . . . . . . . . . . . . . . . . . . . . . . . . . . . . . . . . . . . . . . . . . . . . . . . . . . Operation9. . . . . . . . . . . . . . . . . . . . . . . . . . . . . . . . . . . . . . . . . . . . . . . . . . . . . . . . Wheel Brake Assembly and Parts List10 . . . . . . . . . . . . . . . . . . . . . . . . . . . . . . . . . . . . . . . . . . . . . . . . . . . . . . . . . . . . . . . . . . . . . . . . . . . . . . . . . Cleaning11. . . . . . . . . . . . . . . . . . . . . . . . . . . . . . . . . . . . . . . . . . . . . . . . . . . . . . . . . . . Preventive Maintenance Checklist12IntroductionINTRODUCTIONThis manual is designed to provide instructions for the installation, usage and maintenance of the Stryker Rugged t Cot wheel brake.WARNING / CAUTION / NOTE DEFINITIONThe words WARNING, CAUTION and NOTE carry special meanings and should be carefully reviewed.WARNINGThe personal safety of the patient or user may be involved. Disregarding this information could result in injury to the patient or user.CAUTIONThese instructions point out special procedures or precautions that must be followed to avoid damaging the equipment.NOTEThis provides special information to make maintenance easier or important instructions clearer.The following is a list of safety precautions that must be observed when operating or servicing this unit. Care-fully read this list before using or servicing the unit.WARNINGS Improper usage of the Cot can cause injury to the patient or operator. Operate the cotonly as described in this manual.S Always use all restraint straps to secure the patient on the cot. An unrestrained patient may fall from the cot and be injured.S Never leave a patient unattended on the cot or injury could result. Hold the cot securely while a patient is on the cot.S Never install the wheel brake on a cot with excessively worn wheels. Installing the brake on a wheel with less than a 6” diameter could compromise the holding ability of the brake.S Never apply the optional wheel brake while a patient is on the cot. Tipping could occur if the cot is moved while the brake is applied, resulting in injury to the patient or operator and/or damage to the cot.S The wheel brake is only intended to help prevent the cot from rolling while unattended. The brake may not provide sufficient resistance on all surfaces or under loads.S Be sure the undercarriage has engaged and locked before removing the loading wheels from the patient compartment floor of the vehicle. An unlocked undercarriage will not support the cot and injury to the pa-tient and/or operator could result.S Loading, unloading and changing the position of the cot requires a minimum of two trained operators work-ing together. The operator(s) must be able to lift the total weight of the patient, cot and any other items on the cot.S Do not allow untrained helpers to assist in the operation of the cot. Untrained technicians/helpers can cause injury to the patient or themselves.S Grasping the Cot improperly can cause injury or damage to the cot. Grasp only the lifting bars to lift the cot. Keep hands/fingers away from moving parts.S Do not modify the Cot. Modifying the cot can cause unpredictable operation resultingin injury to the patient or operator. Modifying the cot will also void its warranty.S Improper maintenance can cause injury or damage to the unit. Maintain the cot as described in this manu-al. Use only Stryker approved parts and maintenance procedures. Using unapproved parts and proce-dures could cause unpredictable operation and/or injury and will void the product warranty.S Do not step or ride on the base of the cot. Damage to the cot could occur, resulting ininjury to the patient or operator.S Failure to properly clean or dispose of contaminated mattress or cot components will increase the risk of exposure to bloodborne pathogens and may cause injury to the patient or the operator.Never apply the optional wheel brake while a patient is on the cot. Tipping could occur if the cot is movedwhile the brake is applied, resulting in injury to the patient or operator and/or damage to the cot.MODEL 6090MODEL 6080Limited Warranty:Stryker Medical Division, a division of Stryker Corporation, warrants to the original purchaser that its products should be free from defects in material and workmanship for a period of one (1) year after date of delivery. Stryker’s obligation under this warranty is expressly limited to supplying replacement parts and labor for, or replacing, at its option, any product which is, in the sole discretion of Stryker, found to be defective. Stryker warrants to the original purchaser that the frame and welds on its beds will be free from structural defects for as long as the original purchaser owns the bed. If requested by Stryker, products or parts for which a warranty claim is made shall be returned prepaid to Stryker’s factory. Any improper use or any alteration or repair by others in such manner as in Stryker’s judgement affects the product materially and adversely shall void this warranty. No employee or representative of Stryker is authorized to change this warranty in any way. This statement constitutes Stryker’s entire warranty with respect to the aforesaid equipment. STRYKER MAKES NO OTHER WARRANTY OR REPRESENTATION, EITHER EXPRESSED OR IMPLIED, EXCEPT AS SET FORTH HEREIN. THERE IS NO WARRANTY OF MERCHANTABILITY AND THERE ARE NO WARRANTIES OF FITNESS FOR ANY PARTICULAR PURPOSE. IN NO EVENT SHALL STRYKER BE LIABLE HEREUNDER FOR INCIDENTAL OR CONSEQUENTIAL DAMAGES ARISING FROM OR IN ANY MANNER RELATED TO SALES OR USE OF ANY SUCH EQUIPMENT.To Obtain Parts and Service:Stryker products are supported by a nationwide network of dedicated Stryker Field Service Representatives. These representatives are factory trained, available locally, and carry a substantial spare parts inventory to minimize repair time. Simply call your local representative, or call Stryker Customer Service at (800) 327–0770.Supplemental Warranty Coverage:Stryker has developed a comprehensive program of extended warranty options designed to keep your equip-ment operating at peak performance at the same time it eliminates unexpected costs. We recommend that these programs be activated before the expiration of the new product warranty to eliminate the potential of additional equipment upgrade charges. Stryker offers the following Supplemental Warranties:Extended (Parts and Labor)S All replacement parts (excluding mattresses and consumable items)S Labor and travel for all scheduled and unscheduled callsS Annual Preventive Maintenance Inspections and repairsS JCAHO paperwork for preventive maintenanceS Priority Emergency ServiceStandard (Labor Only):S Labor and travel for all scheduled and unscheduled callsS Annual Preventive Maintenance Inspections and repairsS JCAHO paperwork for preventive maintenanceS Priority Emergency ServiceBasic (Parts Only):S All replacement parts (excluding mattresses and consumable items)S Priority Emergency ServicePlease call your local representative, or call (800) 327–0770 for further informationReturn Authorization:Merchandise cannot be returned without approval from the Stryker Customer Service Department. An autho-rization number will be provided which must be printed on the returned merchandise. Stryker reserves the right to charge shipping and restocking fees on returned items.SPECIAL, MODIFIED, OR DISCONTINUED ITEMS NOT SUBJECT TO RETURN.Damaged Merchandise:ICC Regulations require that claims for damaged merchandise must be made with the carrier within fifteen (15) days of receipt of merchandise. DO NOT ACCEPT DAMAGED SHIPMENTS UNLESS SUCH DAMAGE IS NOTED ON THE DELIVERY RECEIPT AT THE TIME OF RECEIPT. Upon prompt notification, Stryker will file a freight claim with the appropriate carrier for damages incurred. Claim will be limited in amount to the actual replacement cost. In the event that this information is not received by Stryker within the fifteen (15) day period following the delivery of the merchandise, or the damage was not noted on the delivery receipt at the time of receipt, the customer will be responsible for payment of the original invoice in full.Claims for any short shipment must be made within thirty (30) days of invoice.International Warranty Clause:This warranty reflects U.S. domestic policy. Warranty outside the U.S. may vary by country. Please contact your local Stryker Medical representative for additional information.INTERNATIONAL6060, 6070 & 6080 FOOT ENDRequired ToolsElectric Drill Pop Rivet T ool#8 or 5/16” Drill Bit5/8” Wrench11/16” Wrench3/4” Wrench Mounting Procedureing a #8 drill bit and electric drill, drill out the pop rivet (F) from the caster mount cover (G) and removethe cover.ing a 5/8” wrench and an 11/16” wrench, remove the axle bolt (A) and nut (D) from the caster wheeland remove the wheel.ing a 3/4” wrench, remove the bolt (B) and nut (C) holding the caster horn to the base frame.4.Reverse steps 1–3 to install the new brake caster horn.5.Repeat for the caster wheel on the opposite side of the cot.WARNINGNever install the wheel brake on a cot with excessively worn wheels. Installing the brake on a wheel with less than a 6” diameter could compromise the holding ability of the brake.INTERNATIONAL6090FOOT ENDRequired Tools5/8” Wrench11/16” Wrench3/4” Wrench5/16” Hex Allen Wrench1” Socket and RatchetMounting Procedureing a 5/8” wrench and an 11/16” wrench, remove the axle bolt (A) and nut (C) from the caster wheeland remove the wheel.ing a 5/16” hex Allen wrench and 1” socket and ratchet, remove the bolt (B) and nut (F) holding thecaster horn to the base frame.3.Reverse steps 1 and 2 to install the new brake caster horn.4.Repeat for the caster wheel on the opposite side of the cot.WARNINGNever install the wheel brake on a cot with excessively worn wheels. Installing the brake on a wheel with less than a 6” diameter could compromise the holding ability of the brake.OperationOPERATING WHEEL BRAKE(SHOWN ON MODEL 6090 COT)A1.To activate the optional wheel brake, press fully down on the pedal (A) until it stops.2.To release the optional wheel brake, depress the upper face of the brake pedal with your foot or lift upwith your toe under the pedal. The upper portion of the pedal will rest against the caster frame when the wheel brake is released.WARNINGNever apply the optional wheel brake while a patient is on the cot. Tipping could occur if the cot is moved while the brake is applied, resulting in injury to the patient or operator and/or damage to the cot.Never leave a patient unattended on the cot or injury could result. Hold the cot securely while a patient is on the cot.The wheel brake is only intended to help prevent the cot from rolling while unattended. The brake may not provide sufficient resistance on all surfaces or under loads.Wheel Brake AssemblyAssembly part number 6080–100–10 (reference only)Item Part No.Part Name Qty.A4–325Hex Soc. But. Hd. Screw2B25–153Rivet2C6080–100–12Brake Caster Horn Ass’y1D6080–100–30Pedal1E6080–100–31Sleeve1F6080–100–32Brake Spring1G6080–90–101Brake Warning Label2CleaningHand wash all surfaces of the cot with warm water and mild detergent. Dry thoroughly. DO NOT STEAM CLEAN, PRESSURE WASH, HOSE OFF OR ULTRASONICALLY CLEAN. Using these methods of cleaning is not recommended and may void this product’s warranty.Clean Velcro AFTER EACH USE. Saturate Velcro with disinfectant and allow disinfectant to evaporate. (Ap-propriate disinfectant for nylon Velcro should be determined by the hospital.)In general, when used in those concentrations recommended by the manufacturer, either phenolic type or quaternary type disinfectants can be used. Iodophor type disinfectants are not recommended for use be-cause staining may result. The following products have been tested and have been found not to have a harm-ful effect WHEN USED IN ACCORDANCE WITH MANUFACTURERS RECOMMENDED DILUTION.*Quaternary Germicidal Disinfectants, used as directed, and/or Chlorine Bleach products, typically 5.25% So-dium Hypochlorite in dilutions ranging between 1 part bleach to 100 parts water, and 2 parts bleach to 100 parts water are not considered mild detergents. These products are corrosive in nature and may cause damage to your stretcher if used improperly. If these types of products are used to clean Stryker patient handling equipment, measures must be taken to insure the stretchers are rinsed with clean water and thoroughly dried following cleaning. Failure to properly rinse and dry the stretchers will leave a cor-rosive residue on the surface of the stretcher, possibly causing premature corrosion of critical components. NOTEFailure to follow the above directions when using these types of cleaners may void this product’s warranty. REMOVAL OF IODINE COMPOUNDS1. Use a solution of 1–2 tablespoons Sodium Thiosulfate in a pint of warm water to clean the stained area.Clean as soon as possible after staining occurs. If stains are not immediately removed, allow solution to soak or stand on the surface. Rinse surfaces which have been exposed to the solution in clear water be-fore returning unit to service.WARNINGFailure to properly clean or dispose of contaminated mattress or cot components will increase the risk of expo-sure to bloodborne pathogens and may cause injury to the patient or the operator.Preventative MaintenanceParts, Service or Technical Assistance:Contact Stryker Customer Service at 1–800–327–0770 orStryker Medical6300 Sprinkle RoadKalamazoo, MI 49001ATTN: Customer ServiceCHECKLISTAll fasteners secureAll welds intact, not cracked or brokenNo bent or broken tubing or sheet metalNo debris in wheelsAll wheels secure, rolling and swivelling properlyOptional wheel brake holds wheel securely when on and clears wheel when off Siderails move and latch properlyBackrest operating properlyOptional accessories intact and operating properlyHeight positioning latch functioning properlyCot secure in each height positionUndercarriage folds properlyBreakaway head section operating properlySafety bar operating properlyFoot rest operating properlyNo rips or cracks in mattress coverBody restraints intact and working properlySerial No.______________Completed By:_________________________________ Date:_____________DH 4/99 6080–100–91 REV__European RepresentativeStryker FrancePhone:33148632290BP 50040–95946 Roissy Ch. de Gaulle Fax:33148632175Cedex –France6300 Sprinkle Road, Kalamazoo, MI 49001–9799 (800) 327–0770。
Model 400 Series Digital Process Indicator说明书

Model: 400B-CV and 402B-CVTABLE OF CONTENTSSECTION 11.1GENERAL DESCRIPTION1.2OPTIONSSECTION 2SPECIFICATIONSSECTION 3INSTALLATION3.1 UNPACKING/ REPACKING3.2 CONFIGURING3.3 MOUNTING3.4 WIRINGSECTION 4CALIBRATION AND SCALINGNote: This manual is for the enhanced version of the Model 400and 402 units. For models 400 and 402 before 3-2002 with serialnumbers without the letter “N” please refer to manual partnumber M0035.M3778/0602SECTION 1DESCRIPTION1.1 DESCRIPTION.This manual contains installation, operation, and calibration information for Series 400 digital process indicators. These solid-state instruments are designed for accurate, reliable, and trouble-free display of voltage or milliamps. All instruments feature a dual-slope A/D converter digital linearization, and a large 0.8” (20mm) easy-to-read 4-digit LED display. Input voltage or current can be scaled to Engineering units from–999 to +9999 counts.The displays are in-line, uniplanar, 7-segment red LEDS, easy to read through the front Plexiglas panel. A -OL displayed on the read-out indicates a negative polarity overload. Positive readings are inferred (no sign displayed). OL indicate a positive overload condition.All units operate from 100, 120, 220, or 240VAC 50-60 Hz power source. A power connector and ground screw for shield are located at the rear of the instrument. The instrument case is made of solid die-cast aluminum, which is rugged enough to withstand the most hostile environments. It is designed to mount in a panel. The optional rack mounts can accommodate up to 3 units. Bench mount option 400-W5 provides for convenient bench top use.1Multiple Input Options,Models 402 and 405Model 402 can accept five inputs of the same input either voltage or current. Buttons numbered 1-5 are located below display. Individual input is selected by pressing appropriate button.The Model 405A provide 10-switchable inputs to a single indicator. Model 405A are housed in the same rugged case design as the basic indicator. Each may be rack-mounted beside another 405A or indicator. Pushbuttons are in two rows of five and are numbered 1-10, 11-20, etc. Each row is interlocked to prevent simultaneous input selection.Model 40223Figure 2. Input Sensor Connections 402AVOLTAGE CURRENTUSING THE EXTERNAL SWITCHING UINTS (MODELS 405 The External Switching Units provide 10 switchable inputs to a single indicator. Inputs are selected by two rows of front panel pushbuttons labeled 1-10. (For special numbering contact factory). Pressing a particular pushbutton selects that input point for display. Each row of pushbuttons is interlocked so that only one pushbutton within that row is selected at once time.Model 4054SECTION 2SPECIFICATIONS Input Range:mA: 0-20mADCVoltage: 0-10 VDCSensitivity:Maximum: 200uV/count; 0.4uA/countMinimum: 1 countInput Impedance:MA: 5ΩVoltage: > 1MΩA/D Read Rate:2 per second nominalPower:115VAC ± 10%, 50-60 Hz230VAC ± 10%, 50-60 Hz30mA Max input current @ 115VAC Operating Ranges:Temperature: 0 to 50°CRelative Humidity: 10-80% RH non-condensing 5Storage Range:-40 to 65°CSize:Case: 144mm W x 72mm H x 173 mm D(5.768” x 2.84” x 6.82”)Maximum Weight:1.7 kg /2.5 lbPanel cutout:68mm H x 138mm W2.68” H x 5.44” W PERFORMANCE SPECIFICATIONS Reference Operating Conditions (ROC):±10% line voltage23 ±2 °C ambient temperature<80% RH non- condensingAccuracy (at ROC):0.02% RDG +/- 1 count6Noise Rejection:NMRR: ≥ 60 db @ 50/60 Hz, ± 0.1HzCMRR: ≥ 120 db@ 50/60 Hz, ± 0.1Hz with 250Ω unbalance. Overload Protection:Power Lead to ground: 1500VDC or AC RMSVoltage: Up to 250VDC or VAC for I minute, V+ to V-mA: Up to 150mADC mAAC for 1 minute, +I to -I Stability With Temperature:Zero: 1µV/°CSpan: 0.01% rdg /°CStability With Time:10 counts/year maxRepeatability:±1 count7SECTION 3 INSTALLATION3.1 UNPACKING / REPACKINGThe Series 400 indicators are rugged, but they must be properly packed. Instruments are shipped in a custom-designed carton for shipping, but damage may occur. When you receive your instrument, look for evidence of transit damage. If damage is found, ask the carrier to prepare a Damage Inspection Report and notify our Instrument Repair Department immediately. If your instrument has arrived in good condition, you may perform the functional test described in 3.2.2 to verify proper operation.REPACKING AND RETURNING THE INSTRUMENTThe original shipping container should be retained in case the instrument must be returned for repair or modification. When returning an instrument for any reason, advise us of the model number, serial number, your name, billing address, shipping address, phone number and a description of the problem. This information will enable our Instrument Repair Department to expedite the return of your instrument. Instruments being returned to the factory are required to be shipped freight prepaid.Instruments being returned for warranty service must also refer to the original purchase date on packing lists and 8purchase orders. Instruments without this information will be processed as a non-warranty repair at current service rates.If the original shipping container has been discarded, pack your instrument for shipping as follows:Select a strong cardboard box of sufficient size to allow an inch of packing material around all sides of the unit.a. Ensure that the printed circuit boards are securedand front and rear panels are firmly in place.b. Wrap the instrument in plastic or strong paper.Place it centrally in the shipping container, andpack poly foam, bubble pack, or rubberized hairaround all six sides of the instrument.c. Tape the carton flaps securely and label thecontainer “FRAGILE, DELICATE INSTRUMENT”.Ship the instrument, freight prepaid (do not ship byU.S mail)9Input Voltage Selection (requires removal)Input voltage 115 or 220VAC, is selectable by cutting and adding jumpers on the main board as shown on the next page. Locate JP18 on the printed circuit board. Cut and make connection as shown on table depending on input voltage. REMOVING THE ELECTRONICS FROM THE ENCLOSURE 1- Make sure to disconnect power from the unit2- Remove the three back cover screws and remove the rear panel3- Remove the screw located directly above the AC plug4- Remove two screws from the front panel lens and remove lens5- Remove two screws from the front holding the Board assembly and pull it out of the case.6- Reinstall the assembly when finished.10113.3 INSTALLATIONPanel MountingPanel mounting hardware is supplied standard with the instrument. The instrument bezel butts against the front of the mounting panel; the mounting bracket fits over the instrument rear panel. The bracket screws force it against the rear of the mounting panel,locking the instrument in place. Panel cutout dimensions are 68mm x 138mm (2.68” x 5.44”).BRACKET3.4 WIRING THE INSTRUMENT.All signal input connections are made to the instrument using screw terminals. To gain access to the recessed terminal strip, the rear cover panel must be removed. The four signal input terminals are located in the upper-left corner, and are labeled +I, +V, -V, and -I.REMOVE THE POWER CORD BEFORE WIRINGBasic Single Channel Wiring13Model 402 Switching Unit Wiring14SECTION 4CALIBRATION AND SCALING4.1 APPLYING POWER TO THE INSTRUMENTPower is applied to the instrument as long as the instrument is plugged into an active source. To remove power, unplug the power cord from the instrument or AC outlet.To eliminate shock hazard or possible instrument damage, always remove the power cord either from the instrument or power source before configuring the indicator.4.2 Selecting mA or Volts Input ModeTo select between mA or Volts input mode, remove the front panel lens to gain access to the display board. Behind the display is a DIP switch used to set the indicator’s input measuring mode. See the drawing on the following page showing DIP switch location as well as the location of the SET and ENTER scaling buttons.151617DIP SWITCHPUSH DOWN HEREFOR PROCESSMEASURING MODEPUSH DOWN HERE TO CONFIGURE INSTRUMENT FOR mA PUSH DOWN HEREFOR SCALING MODE PUSH DOWN HERE TO CONFIGUREINSTRUMENT FORVOLTAGE INPUTCalibrating and Scaling the IndicatorScaling the indicator to display in your desired engineering units requires simulation of two different input VALUES (typically the lowest input and highest input) and using the two “SET” and “ENTER” buttons to scroll the digital display.With the front lens removed and the mA/V switchIn the position compatible with your input…Step 1: Hook up a DC milliamp or Voltage source Calibrator or actual transducer, capable of supplying a low scale andfull scale input, to the appropriate rear panel screwterminals on the indicator.Step 2: Set the “PROCESS/SCALING” switch to the SCALING position. The word “Lo” will appear on the display. Step 3: a) Simulate the low scale input (e.g. 4 mA)b) Push the “ENTER” button.c) Use the “SET” button to change the value of theflashing digit. When the flashing digit is correct,push the “ENTER” button. The flashing digit will 18now move to the next right hand digit. Continueuntil all digits are correct with the right most digitstill flashing.d) Push both “SET” and “ENTER” buttons at the sametime to program in this scale factor. In other words,when the indicator receives a process input signalidentical to the simulated (calibration) one it willdisplay the same value shown now. (e.g.4mA=0000)NOTE:While the indicators calibrating itself “oo” will appear in the display. After a few seconds it will return to display “Hi”(go to step 4) or “ERR” (see error message table).Step 4: With “Hi” displayed change the input to simulate +Full scale (High e.g. 20mA).Step 5: Repeat steps as shown in Steps 3b, 3c, 3d changing the digits to represent the Full Scale desired display(e.g. 7500). When complete, the indicator will then goto the decimal point position.19Step 6: With decimal points displayed…a) Push “SET” button until desired position is displayedb) Push “SET” and “ENTER” buttons at the same timeto program into memoryStep 7: Return the “PROCESS/SCALING” switch to the PROCESS position. Replace the front lens. Removethe calibrator from the input terminals.NOTES:1) Pushing both the SET and ENTER buttons at the sametime always causes the indicator to recalibrate itself to the given input at that moment. As a protective measure, if scaling changes are made and not terminated this way no recalibration will occur, previous values will remain.2)As a further protective measure, the “SET” and “ENTER”buttons are not functional unless the PROCESS/SCALING switch is in the SCALING position.2021Button Function Legend"SET""ENTER"Same time SET & ENTERRecalibrate to the displayed value for the existing Input Voltage or CurrentUse "SET" key to change value of flashing digit or decimal pointERROR MESSAGE TABLE22。
More time on the road RTLOF-13610B-T2 图解零部件清单说明书

More time on the road®Illustrated Parts ListRTLOF-13610B-T2November 2012ContentsHow To Use The Illustrated Parts List (3)AUXILIARY DRIVE GEAR (4)CASE (AUX) (5)CASE (FRONT) (8)COUNTERSHAFT & BRGS(AUX) (11)COUNTERSHAFT ASSY (12)FILTER REGULATOR (14)HOSES & CONNECTIONS (15)INPUT SHAFT & DRIVE GEAR (17)INTEGRAL OIL PUMP (18)ISOLATORS (20)KITS & ASSEMBLIES (21)LEVERS/HOUSINGS (24)MAINSHAFT & SYNCHRO(AUX) (26)MAINSHAFT ASSY (28)MISCELLANEOUS (30)OIL COOLER (31)RANGE CYLINDER (33)REVERSE IDLER (35)ROADRANGER VALVE (38)SHIFT BAR HOUSING (F) (39)SPLITTER CYLINDER (42)TOP 2 VALVE (44)2How To Use The Illustrated Parts ListThe information contained in this document is subject to frequent updates. Therefore, for the latest information available, please visit the interactive Electronic Parts Catalog at /epc.Model Designation or Nomenclature•For information regarding Model Designation and Nomenclature, visit .Kits and Assemblies (K/A's)•Kits and Assemblies contain groups of individual or assembled parts developed for optimal replacement or repair of a service problem.•Kits and Assemblies are shown with applicable parts groupings in the parts listings.Identifying Kits and AssembliesA- Part numbers beginning with the letter 'A' are pre-assembled Production AssembliesK- Part numbers beginning with the letter 'K' are kits that are not assembledS- Part numbers beginning with the letter 'S' are pre-assembled Service Assemblies•Note: Some Production Assemblies do not begin with a letter prefix (Midrange only).Illustrations•Illustrations show parts in assembly groups.•Item numbers on illustrations correspond with parts listings on pages adjacent to the illustration.•Notes are included on illustrations where additional information is needed.Parts ListingParts listings are defined by parts groupings and are broken down by service assemblies. Parts listings identify a part for servicing with the following categories•Item Number - corresponding with numbers on illlustrations for part identification.•Current Part - indentifies part as it is available for service.•Description - specifies part name or description.•Replaced Part - quantity quantity required for assembly.•Quantity - defines unique characteristics or requirements.•Notes - indicates Kits or Assemblies that contain a particular part.•Kits/Assy's Where Used34Group: AUXILIARY DRIVE GEARAUXILIARY DRIVE GEARItemCurrent PartDescription Replaced Part Qty. NotesKits/Assys WhereNeeded1 16763 SNAP RING 2K-2755,K-2764,K-2772 2 21320 SNAP RING RETAINER 1 K-2640 3 16628 SNAP RING1K-275545566507-BOXBEARING 5566504,5566507 1K-2764,K-27725 16138 BEARING RETAINER 1 6X-8-645CAPSCREWX 8 612 63/8"-16X1"7 17453 -O- RING2K-2640,K-2764,K-2772 8 21599 WASHER2 9 K-2640REPL KIT-DRIVE GEAR4301397 ,430152012134567110481-12/92 Aux DG8895Group: CASE (AUX)CASE (AUX)ItemCurrent PartDescription Replaced Part Qty. NotesKits/Assys WhereNeeded 1 X-8L-605 CAPSCREW5 3/8"-16X3" 2S-2136REAR BRG COVER ASSY21950 ,22040 ,22041,22042 ,4302006 4302007 ,S - 1563 1 EXTENDED3 15532 GASKET1K-1603,K-2262,K-2295,S-2136 4 20224 PLUG-MAGNETIC 2S-2136,S-2775 5 13679 -O- RING1 USE W/OEM SUPPLIEDADJUSTABLE SPEEDOMETER10402A-3-99See Service Manual for Proper Shimming Procedure 20225 "O" ring w/ OEM supplied non-adjustable speedometer sensor or Eaton part #20224 Plug *SENSORRING 2 USE W/20224 PLUG OR OEM5 20225 -O-SUPPLIED NON-ADJUSTABLESPEEDOMETER SENSOR NOT TOBE USED WITH 4301954 SEALREQUIRED S-21365 4301954 SENSORNOTSEAL 2 O-RING6 20226 PLUG-MECHANICAL 2237 1 S-2136,S-2775RING 1 S-2136,S-27757 14142 -O-8 7992 BUSHING 1 S-21369 X-8L-604 CAPSCREW 8 3/8"-16X1-1/4"10 20815 LIFTINGEYE 17105 211 4300925 REAR BEARING COVER 4300185 2 PRIOR TO SERIAL NUMBERS51135817, 70768176 & PRIOR TOSERIAL NUMBERS STARTINGWITH AN ALPHA CHARACTERK-1603,K-229512 4300186 GASKET 2 PRIOR TO SERIAL NUMBERS51135817, 70768176 & PRIOR TOSERIAL NUMBERS STARTINGWITH AN ALPHA CHARACTERKIT 21452 1 K-2764,K-2772,S-13 K-2430 SHIM277514 X-8L-602 CAPSCREW 9 3/8"-16X1-1/2"14 X-8L-602 CAPSCREW 8 3/8"-16X1-1/2" - BEGINNINGW/SERIAL NUMBERS 51135817,70768176 & ALL SERIAL NUMBERSSTARTING WITH AN ALPHACHARACTER14 X-8L-604 CAPSCREW 8 3/8"-16X1-1/4" - PRIOR TO SERIALNUMBERS 51135817, 71768176 &PRIOR TO SERIAL NUMBERSSTARTING WITH AN ALPHACHARACTER14 X-8L-614 CAPSCRCREW 2 3/8"-16X2"HOUSING 1 PRIOR TO SERIAL NUMBERS15 4300702 REAR51135817, 70768176 & PRIOR TOSERIAL NUMBERS STARTINGWITH AN ALPHA CHARACTERHOUSING 1 BEGINNING W/SERIAL NUMBERS15 4303642 REAR51135817, 70768176 & ALL SERIALNUMBERS STARTING WITH ANALPHA CHARACTER16 14335 GASKET 1 K-1603,K-2295,S-277517 X-8-682 CAPSCREW 1 3/8"-16X3"618 17106 GASKET 1 K-2262,K-2295,S-213619 19709 COLLAR 1 K-1603,K-2262,K-2295,S-213620 K-2262 OIL SEAL W/SLINGER 19109 20807 20808 1 "FOR MECHANICAL COVER" K-2764,K-277221 K-3651 OIL SEAL TOOL KIT 122 4302320 COVER 21346 2 BEGINNING W/SERIAL NUMBERS51135817, 70768176 & ALL SERIALNUMBERS STARTING WITH ANALPHA CHARACTERS-277523 4305978 GASKET 4302246 1 BEGINNING W/SERIAL NUMBERS51135817, 70768176 & ALL SERIALNUMBERS STARTING WITH ANALPHA CHARACTER K-1603,K-2295,S-277578Group: CASE (FRONT)CASE (FRONT)ItemCurrent PartDescription Replaced Part Qty. NotesKits/Assys WhereNeeded 1 S-2061 CASE ASSY 4301557 1 1S-2062CASE ASSY4301790 1FOR USE W/INTEGRAL PUMP2 4304023 PLUG43037471 1-1/16" MAGNETIC, O-RINGINCLUDED2 X-12-2007 PIPE PLUG X12 2006 13 4304023 PLUG43037471 1-1/16" MAGNETIC, O-RINGINCLUDED3 X-12-1207 PIPE PLUG X12 1202 ,X12 1206 13/4" MAGNETIC4 4305310 GASKET 4302810 1 K-2295 5 4302809 PTO COVER 16596 ,4300571 16X-8-725CAPSCREWX 8 72487/16"-14X7/8"7 4306584 CLUTCH HOUSINGGASKET4304815,4305668 1K-2295,K-405110300B-8-0014Note: Some part requirements are specific to #1 or #2 Aluminum or Iron Clutch Housings and Push or Pull type Clutch.* Bushing quantity requirements: #1 Housing – Upper bore use 4 #12815 / Lower bore use 2 #8677.#2 Housing – Upper bore use 2 #12815 and 1 #8677 / Lower bore use 2 #8677.8 A-3713 CLUTCH HOUSING ASSY A - 3700 1 #1 PUSH-PULL IRON8 A-3723 CLUTCH HOUSING ASSY A - 3721 ,A - 3722 1 #2 PUSH-PULL IRON8 A-5992 CLUTCH HOUSING ASSY 4301103 1 #1 PULL ALUM.(SPECIAL-LIGHTERWEIGHT)9 239614 SCREW X-8L-509 4 5/16-18X.81 QUANTITYDEPENDENT ON DESIGN10 14506 HAND HOLE COVER 1 #2 PUSH10 14507 HAND HOLE COVER 1 #2 PULL10 4305230 HAND HOLE COVER 11453 1 #1 PULL10 4305231 HAND HOLE COVER 1565 1 #1 PUSH11 4306583 STUD 5966 612 X-10-1005 WASHER X 3 1000 ,X10 1000,X10 10046 1.23 X 6.60 K-405113 X-1-1012 HEXNUT X-1-1005 6 .625-18 K-405114 20550 FRONT BRG COVER 1 2" PULL K-2468,K-412515 X-8L-604 CAPSCREW 6 3/8"-16X1-1/4"16 20549 FRONT BRG COVER 1 2" PUSH17 14311 GASKET 1 K-229518 12815 BUSHING 4 FOR #1 HOUSING UPPER A-3713,A-3723,A-5992,K-246818 12815 BUSHING 2 FOR #2 HOUSING UPPER A-3713,A-3723,A-5992,K-246818 8677 BUSHING 1 FOR #2 HOUSING UPPER A-3713,A-372319 8677 BUSHING 2 FOR #1 AND #2 HOUSING LOWER A-3713,A-372320 X-8C-830 HEX HEADSCREW/WASHER ASSY X-8C-826 4.500-13 X 1.490, USE 2 PCS FORIRON HOUSING, USE 4 PCS FORALUMINUM HOUSINGK-405120 X-8C-831 HEX HEADSCREW/WASHER ASSY X-8C-822 2.500-13 X 3.460, FOR IRONHOUSINGK-405122 X-8-686 CAPSCREW 6 3/8"-16X3/4"23 14575 PTOCOVER 4302254 124 4305309 GASKET 1684 1 K-229527 14373 MAGNET 3 S-2061,S-206228 18128 PIN 229 X-1-1012 HEXNUT 2 .625-18 K-405130 X-10-1005 WASHER X 3 1000 ,X10 1000,X10 10042 1.23 X 6.60 K-4051931 14554 STUD 1632 ,6579 2 5/8" X 2-3/16"36 23104 PLUG 1712 237 X-8-1005 CAPSCREW 2 5/8"-11X1-1/4"38 20814 SPACER 239 X-12-802 PIPE PLUG X12 800 1 1/2"10Group: COUNTERSHAFT & BRGS(AUX)COUNTERSHAFT & BRGS(AUX)ItemCurrent Part Description Replaced Part Qty. NotesKits/Assys WhereNeeded1 4302074-BOXBEARING 21343,4302074 4K-2764,K-27722 A-6387 WELDEDCOUNTERSHAFT ASSY 2 C/S 4301398 - D/G 4301399 S/G43026963 4300184 SPACER2110441-4/92 Aux CS 13/18 spdGroup: COUNTERSHAFT ASSYCOUNTERSHAFT ASSYItemCurrent PartDescription Replaced Part Qty. NotesKits/Assys WhereNeeded1 14317 SNAP RING 2K-2755,K-2764,K-27722 14366 BEARING2 K-2764,K-2772 3K-2932CNTRSHFT W/REV & LO4301395 ,4303966,4303967 25 62511 ROLL PIN4 ROLL PINS NO LONGERREQUIRED A-6340,S-2484,S-2485,S-2486 6 4303968 KEY2 9 4303961 2ND GEAR-CNTRSHFT 4303960 2 10 15953 PTO GEAR - LOWER 1 1020840PTO GEAR - UPPER15952111 21586 DRIVE GEAR-CNTRSHFT 22271 2 12 19198SNAP RING213 4304599 BEARING 4302677 ,4304598 2 K-2764,K-2772 14 4304605 RETAINER 19548 215 X-7-1005 CAPSCREW 2 5/8"-18X1-3/4" 16 4303964 SPACER210343-11/92 CS-LO InertiaGroup: FILTER REGULATORFILTER REGULATORItemCurrent Part Description Replaced Part Qty. NotesKits/Assys WhereNeeded 1 K-2170 FILTER REG KIT A - 5454 12 K-1698 -O- RING/ELEMENT KIT1 FOR FILTER REGULATOR 3 X-8C-412CAPSCREWX 8S 41221/4"-20X2-1/4"10130-1-92 AFR2221NSS - Not Sold Separately 3NSS2 -O- Ring/Element KitGroup: HOSES & CONNECTIONSHOSES & CONNECTIONSItemCurrent PartDescription Replaced Part Qty. NotesKits/Assys WhereNeeded 1 X-8-434 CAPSCREW 2 1/4"-20X2"10116A-5/93 Super10 HC11210Item CurrentPart Description ReplacedPartQty.Notes Kits/Assys WhereNeeded2 22818 NO LONGER AVAILABLE 13 22817 RETAINERPLATE 14 K-3121 AIR VALVE CONV KIT 23545 15 84002 CONNECTORASSY 82502 1 1/8"TUBE-1/8"NPTF 5 84004 CONNECTORASSY 82504 1 5/32"TUBE-1/8"NPTF5 84006 CONNECTORASSY 1 "PUSH-TO-CONNECT" 5/32"TUBE-1/8"NPTF K-3121,K-3198,S-2485,S-24866 22870 TEE 17 7935 BREATHER 1 K-31988 4301989 PIN 22813 19 19727 HOSECLAMP 2 S-2485,S-2486 10 75120 NYLONTUBE 1 5/32"11 75320 NYLONTUBE 5546014 1 5/32"12 85001 ELBOWASSY 84501 5 5/32"TUBE-1/8"NPTF12 85002 ELBOWASSY 84502 5 1/8"TUBE-1/8"NPTF12 85003 ELBOWASSY 5 "PUSH-TO-CONNECT" 5/32"TUBE-1/8"NPTF K-2764,K-3121,K-3198,K-3333,K-3334,S-2485,S-248614 15114 -O-RING 2 K-2170,K-2295,K-333415 X-12-208 PIPE PLUG 1 1/8" NPT16 55527 HOSEASSY 1 15"Group: INPUT SHAFT & DRIVE GEARINPUT SHAFT & DRIVE GEARItemCurrent Part Description Replaced Part Qty. NotesKits/Assys WhereNeeded 1 23559SEAL 1 NOT SOLD FOR SERVICE2 16980 SNAP RING1K-2468,K-2755,K-2764,K-2772,K-4125 3 81504 BEARING 1K-2468,K-2764,K-2772,K-4125 4 16463 SPACER 15 14750 SNAP RING1K-2468,K-2755,K-2764,K-2772,K-4125 6 20458 MAIN DRIVE GEAR 1963018S-1659INPUT SHAFT20535 23566 ,430266112" PULL - USE W/FBC 20550K-2468,K-2764,K-4125 8 S-1660 INPUT SHAFT 20536 ,23567 1 2" PUSH - USE W/FBC 205499 16566 BUSHING1K-2772,S-1659,S-166010370-1/92 IS* For Shipping Only -- Do Not Replace*Group: INTEGRAL OIL PUMPINTEGRAL OIL PUMPItemCurrent PartDescription Replaced Part Qty. NotesKits/Assys WhereNeeded 1 X-8C-409 CAPSCREW5 1/4"-20X5/8" 2K-2402COVER & SCREW KIT20513 ,4300751 13 20514 GASKET 1 K-2402 4 20823 PLUG 15 14765 -O- RING1 K-2297,K-2298 6K-4126FASTENER KIT20824, X-8-4481KIT CONTAINS 3 FASTENERS AND3 WASHERSK-33678 20825 DOWEL PIN 1Indicates part of item 999Item CurrentPart Description ReplacedPartQty.Notes Kits/Assys WhereNeeded9 4303773 RETAINER 110 K-3367 OIL PUMP KIT 4301829 ,4301948,4303776 ,4304529,4304572 A - 6963 ,A -7173111 K-3367 OIL PUMP KIT 4301829 ,4301948,4303776 ,4304529,4304572 A - 6963 ,A -7173112 20509 KEY 113 14853 SNAPRING 214 4303774 PUMP DRIVE GEAR 4304880 115 K-3367 OIL PUMP KIT 4301829 ,4301948,4303776 ,4304529,4304572 A - 6963 ,A -7173116 X-14-700 STEELBALL 1 7/16"17 4303775 SPRING 118 4305713 SUCTIONTUBE 4304628 1 O-RING INCLUDED ON SUCTIONTUBEK-3367 19 4304629 PLUG 126 X-8-447 SCREW 227 20225 -O-RING 1999 K-3367 OIL PUMP KIT 4301829 ,4301948,4303776 ,4304529,4304572 A - 6963 ,A -71731Group: ISOLATORS ISOLATORSItem CurrentPart Description ReplacedPartQty.Notes Kits/Assys WhereNeeded1 19124 -E-RING 22 K-3467 PIN REPLACEMENT KIT 21245 13 21246 BUSHING 2 K-2003,K-33994 S-1794 ISOLATORASSY 16 21247 LEVER 1 STRAIGHT18.67"7 21235 STUBLEVER 1 LOWTOWER7 21236 STUBLEVER 1 HIGHTOWER9 21767 90 DEG LEVER 1 STRAIGHT 33"10 K-3399 ISOLATOR BUSHING KIT 21244 ,23311 111 X-8-560 SCREW 1 K-200312 X-9-503 NUT 1 K-2003KITS & ASSEMBLIESItem CurrentPart Description ReplacedPartQty.Notes Kits/Assys WhereNeededK-1603 GASKET KIT 1 FOR AUXILIARY SECTIONK-1698 -O- RING/ELEMENT KIT 1 FOR FILTER REGULATORK-1956 COOLER INSTLN KIT 1K-2003 PIN & BUSHING KIT 1K-2078 -O- RING KIT - SPLITTER 1 SPLITTERK-2170 FILTER REG KIT A - 5454 1K-2262 OIL SEAL W/SLINGER 19109 20807 20808 1 "FOR MECHANICAL COVER" K-2764,K-2772K-2295 GASKETKIT 1 K-2764,K-2772 K-2297 -O- RING KIT - RANGE 1 RANGEK-2298 -O- RING KIT -COMPLETE 1COMPLETE K-2764,K-2772K-2347 MASTER VALVE REPAIRKIT1 FOR A-5510 VALVEK-2366 KEY & WASHER KIT 21326 ,4300763,43046141 CONTAINS 3-SIDED KEYK-2394 AIR SYSTEMS TOOL KIT 1K-2402 COVER & SCREW KIT 20513 ,4300751 1K-2430 SHIMKIT 21452 1 K-2764,K-2772,S-2775K-2468 CLUTCH INSTALLATIONKIT 1FOR USE WITH S-1659 INPUTSHAFT ASSY AND 81504 INPUTSHAFT BEARINGK-2640 REPL KIT-DRIVE GEAR 4301397 ,4301520 1K-2755 SMALLPARTSKIT 1 K-2764 BASIC OVERHAUL KIT 1K-2772 BASIC REBUILD KIT 1K-2932 COUNTERSHAFT REPLKIT 4301395 ,4303966,43039671K-2972 SHIFT LEVER HSG KIT 4304911 1 HIGH TOWERK-2973 SHIFT LEVER HSG KIT 17166 ,17167,4303050 ,4304910 ,K- 1630 K - 1941 1 HIGHTOWERK-3190 MASTER VALVE REPAIRKIT1 FOR A-6910 VALVEK-3198 T-2 VALVE KIT 691300 ,691359 1K-3209 IDLER SHAFT REPL KIT 16405 ,4302981,43055131 K-3333 SPLITTER VLV REPL KIT A - 6861 1K-3334 RANGE VALVE REPL KIT A - 6864 1K-3367 OIL PUMP KIT 4301829 ,4301948,4303776 ,4304529,4304572 A - 6963 ,A -71731K-3376 O-RING & WASHER KIT 4301211 1K-3399 ISOLATOR BUSHING KIT 21244 ,23311 1K-3467 PIN REPLACEMENT KIT 21245 1K-3492 SYNCHRONIZER KIT K - 2446 1K-3494 SYNCHRONIZERREPLACEMENT KIT K - 2448 1 SLIDING CLUTCH INCLUDED INKITK-3635 SHIFT LEVER HSG KIT 4304908 1 MID TOWERK-3636 SHIFT LEVER HSG KIT 4304904 1 LOW TOWERK-3651 OIL SEAL TOOL KIT 1K-4051 RT CLUTCH HOUSINGSERVICE KIT1K-4125 CLUTCH INSTALLATIONKIT (RT), HYDRAULICRELEASE 1STANDARD RT INPUT SHAFT ANDYOKE FOR HYDRAULIC CLUTCHRELEASES-1404 OILFILTER 17238 1S-1659 INPUT SHAFT 20535 23566 4302661 1 2" PULL - USE W/FBC 20550 K-2468,K-2764,K-4125 S-1660 INPUT SHAFT 20536 ,23567 1 2" PUSH - USE W/FBC 20549S-1786 SHIFTYOKEASSY 22801 1S-1794 ISOLATORASSY 1S-1984 COVER ASSY-RANGECYL1S-2061 CASEASSY 4301557 1S-2062 CASE ASSY 4301790 1 FOR USE W/INTEGRAL PUMPS-2136 REAR BRG COVER ASSY 21950 ,22040 ,22041,22042 ,43020064302007 ,S - 15631 EXTENDEDS-2281 SHIFT TOWER ASSY 1 LOW TOWERS-2282 SHIFT TOWER ASSY 1 MID TOWERS-2283 SHIFT TOWER ASSY 1 HIGH TOWERS-2484 SHIFT BAR HSG ASSY(F) 4303112 1HOUSINGONLYS-2485 SHIFT BAR HSG ASSY(F) S - 2442 1 COMPLETE - FOR USE W/REMOTECONTROLS-2486 SHIFT BAR HSG ASSY(F) 4303112 ,S - 2416 1 COMPLETE - FOR USE W/SHIFTLEVERS-2530 SHIFT TOWER ASSY 1 HIGH TOWER - PINCH BOLTS-2568 ROADRANGER VALVEASSY 1RTLO - W/SHIFT DIAGRAMMEDALLIONS-2737 MAINSHAFTASSY 4304597 1 S-2775 RANGE SECTION ASSY 1Group: LEVERS/HOUSINGSLEVERS/HOUSINGSItemCurrent Part Description Replaced Part Qty. NotesKits/Assys WhereNeeded 1 K-3376O-RING & WASHER KIT 4301211 12 18299 PIN1K-3635,K-3636,S-2281,S-2282,S-2283,S-2530 3 X-8C-604 CAPSCREW 4 3/8"-16X1-1/4" 4 X-1-600 NUT4 3/8"-24-N.F.PLAIN5 X-3-600 LOCKWASHER 4 3/8"6 11934 STUD 7467 4 7K-3636SHIFT LEVER HSG KIT4304904 1LOW TOWER8 4303432 GASKET 227991K-2295,K-2972,K-3635,K-3636,S-1141510212-10-078419S-2281 - Low S-2282 - Mid S-2530 - High - Pinch BoltS-2283 - High18Item CurrentPart Description ReplacedPartQty.Notes Kits/Assys WhereNeeded2281,S-2282,S-2283,S-25309 K-3635 SHIFT LEVER HSG KIT 4304908 1 MID TOWER10 K-2972 SHIFT LEVER HSG KIT 4304911 1 HIGH TOWER11 17560 LEVERGRIP 1 1/2"-1312 10427 BOOT 1 K-2972,K-2973,K-3635,K-3636,S-2281,S-2282,S-2283,S-253013 6541 PIN 1 3/8"14 2538 RETAINER 1 K-2972,K-2973,K-3635,K-3636,S-2281,S-2282,S-2283,S-253015 2536 SPRING 1 K-2972,K-2973,K-3635,K-3636,S-2281,S-2282,S-2283,S-253016 X-1-500 NUT 1 5/16"-2417 X-3-500 LOCKWASHER 1 5/16"18 4302532 STUB SHIFT LEVER 1 LOW S-228118 4302700 STUB SHIFT LEVER 1 MID S-228218 4303556 STUB SHIFT LEVER 1 HIGH S-228318 4303600 STUB SHIFT LEVER 1 HIGH - PINCH BOLT S-253019 S-2281 SHIFT TOWER ASSY 1 LOW TOWER19 S-2282 SHIFT TOWER ASSY 1 MID TOWER19 S-2283 SHIFT TOWER ASSY 1 HIGH TOWER19 S-2530 SHIFT TOWER ASSY 1 HIGH TOWER - PINCH BOLTGroup: MAINSHAFT & SYNCHRO(AUX)MAINSHAFT & SYNCHRO(AUX)ItemCurrent PartDescription Replaced Part Qty. NotesKits/Assys WhereNeeded 1 21930 SLIDING CLUTCH 12 X-7-1005 CAPSCREW 1 5/8"-18X1-3/4"3 A-6340 RETAINER ASSY 4302057 1 K-2764,K-27724 62511 ROLL PIN1A-6340,S-2484,S-2485,S-2486 5 4302058 BEARING2 K-2764,K-2772 6 4302695 SPLITTER GEAR-MAINSHAFT 4301940 ,430206617 14897 SPRING3K-2755,K-2764,K-2772,K-3492,K-3494 8 A-7331 SYNCHRONIZER ASSY 4304396 4304397 A -5917 1 HI RANGEK-3492,K-34949 20323 SLIDING CLUTCH1 K-3494 10 A-7254 SYNCHRONIZERA - 4937 A - 58761LO RANGEK-3492,K-349410423-10/92 Aux MS RTLO 10Item CurrentPart Description ReplacedPartQty.Notes Kits/Assys WhereNeeded ASSEMBLY11 4302076 AUXILIARYMAINSHAFT 112 22262 SPACER 1 K-275513 4301400 REDUCTIONGEAR 114 22263 WASHER 1 K-275515 14367 BEARING 1 K-2764,K-277216 20192 ROTOR 14375 117 22254 NUT 11956 1 S-2775Group: MAINSHAFT ASSYMAINSHAFT ASSYItemCurrent PartDescription Replaced Part Qty. NotesKits/Assys WhereNeeded1 4304614 3-SIDED KEY 4300890 1 K-2366,K-2755 1K-2366KEY & WASHER KIT21326 ,4300763,4304614 1CONTAINS 3-SIDED KEY2 S-2737 MAINSHAFT ASSY 4304597 13 62504 ROLL PIN 1 S-2737 4 14750 SNAP RING3K-2468,K-2755,K-2764,K-2772,K-4125 5 16756 REVERSE GEAR-MAINSHAFT 22408 16 14749 SPACER3 K-2755 7 4300382 WASHER .249-WHITE 5K-2366,K-2755 7 4300383 WASHER .254-GREEN5 OPTIONAL 4300382-4300387 OR4300830 USE ANY 5 WASHERS. USE WITH 3-SIDED KEY K-2366,K-27557 4300384 WASHER .259-ORANGE 5 OPTIONAL 4300382-4300387 OR4300830 USE ANY 5 WASHERS. USE WITH 3-SIDED KEY K-2366,K-27557 4300385 WASHER .264-PURPLE 5 OPTIONAL 4300382-4300387 OR4300830 USE ANY 5 WASHERS.10322A-3-97 MS - LO InertiaItem CurrentPart Description ReplacedPartQty.Notes Kits/Assys WhereNeededUSE WITH 3-SIDED KEY7 4300386 WASHER.269-YELLOW 5 OPTIONAL 4300382-4300387 OR4300830 USE ANY 5 WASHERS.USE WITH 3-SIDED KEY7 4300387 WASHER.274-BLACK 5 OPTIONAL 4300382-4300387 OR4300830 USE ANY 5 WASHERS.USE WITH 3-SIDED KEY7 4300830 WASHER.244-BLUE 5 K-2366,K-2755 8 16118 SLIDINGCLUTCH 2 K-27649 4301396 LOGEAR-MAINSHAFT 4301519 112 4303969 2ND GEAR-MAINSHAFT 4301394 ,4301517 113 16288 SPACER 2 K-2755MISCELLANEOUSItem CurrentPart Description ReplacedPartQty.Notes Kits/Assys WhereNeeded4303343 SHIFT DIAGRAM LABEL 171203 SILICONE LUBE 1 8 OZ (236.59 CC)-FLEET SIZE71204 ADHESIVESEALANT 1 0.5 CC (SINGLE APPLICATIONSIZE)K-3198 71205 SEALANT 1 2 CC (SINGLE APPLICATION SIZE) K-2764,K-277271206 SILICONE LUBE 1 4 CC (SINGLE APPLICATION SIZE) K-2078,K-2297,K-2298,K-3333,K-333431Group: OIL COOLEROIL COOLERItemCurrent PartDescription Replaced Part Qty. NotesKits/Assys WhereNeeded 1 18025 OIL COOLER 1 K-1956 2 19424 HOSE 1 25 FEET K-1956 3 X-8-535 CAPSCREW 2 5/16"-16X2-1/2" 4 X-3-506 LOCKWASHER 2 5/16" 5 18211 BRACKET 4 K-1956 6 19419 CONNECTOR 6 K-1956,S-1404 7 19415 SWIVEL 4 K-1956 8 X-10-501 WASHER2 5/16" 9 18209 PLUG-RUBBER MOUNT 2 K-1956 10 17190 STRAP 8 K-1956 11 19423 CLAMP 5 K-1956 12 18210NUT2K-1956*Adding Oil Filter and parts as shown is optional.Return / Outlet Location10525-4/92 CoolerItem CurrentPart Description ReplacedPartQty.Notes Kits/Assys WhereNeeded13 19422 ELBOW 4 K-195614 S-1404 OILFILTER 17238 115 17237 FILTERELEMENT 1 S-140432Group: RANGE CYLINDER RANGE CYLINDERItem CurrentPart Description ReplacedPartQty.Notes Kits/Assys WhereNeeded1 X-7-809 BOLT X 7 810 ,X 7 8112 1/2"-20X1-3/4"2 22823 SHIFTYOKE 16775 13 14347 GASKET 1 K-1603,K-2295,K-2297,K-22984 K-3334 RANGE VALVE REPL KIT A - 6864 15 14197 -O-RING 1 K-2297,K-2298,K-33346 4303682 RANGECYLINDER 4301789 17 14765 -O-RING 1 K-2297,K-22988 4301558 YOKEBAR 19 14341 PISTON 23353 110 14345 -O-RING 1 K-2297,K-229833Item CurrentPart Description ReplacedPartQty.Notes Kits/Assys WhereNeeded11 14344 -O-RING 1 K-2297,K-229812 X-1-1010 NUT 1 5/8"-1813 22826 GASKET 1 K-1603,K-2295,K-2297,K-2298,S-198414 22825 RANGE CYLINDERCOVER1 S-198415 4300810 INSERT VALVE 22641 4303615 2 K-2764,K-2772,S-198416 23009 PLUG 2 S-198417 X-8L-607 CAPSCREW X 8 607 4 3/8"-16X2-1/4", 3/8"-16X2-1/4"18 5568539 O-RING 1 K-2297,K-2298,K-333419 X2014210 BREATHER 7935 1999 K-3334 RANGE VALVE REPL KIT A - 6864 134Group: REVERSE IDLERREVERSE IDLERItem CurrentPart Description ReplacedPartQty.Notes Kits/Assys WhereNeeded1 X-1-1008 NUT2 5/8"-182 14283 WASHER 235Item CurrentPart Description ReplacedPartQty.Notes Kits/Assys WhereNeeded3 4302982 WASHER 142824 K-3209,S-2061,S-20624 14287 BEARING 4305020 2 K-2764,K-27725 16757 REVERSE IDLER GEAR 22409 26 4303336 RETAININGRING 4 K-32097 K-3209 IDLER SHAFT REPL KIT 16405 ,4302981,430551328 5202 PLUG 29 14282 NO LONGER AVAILABLE 410 X-7-1008 CAPSCREW 2 5/8"-18X1-1/411 4303336 RETAININGRING 2 K-320912 4305513 IDLERSHAFT 2 K-32093637Group: ROADRANGER VALVE5111112999132 K-2347 Rep Kit Master Valve10104-11/92 RRV*For Connector and Elbow Assy component information see Appendix.***ROADRANGER VALVEItem CurrentPart Description ReplacedPartQty.Notes Kits/Assys WhereNeeded1 20107 MEDALLION,LOGO 1 (OLD DESIGN) FULLER LOGOONLY1 5586100 MEDALLION,LOGO 1 (LATEST DESIGN) FULLER LOGOONLYA-69101 5586109 SHIFT DIAGRAMMEDALLION 1RTLO S-25682 K-2347 MASTER VALVE REPAIRKIT1 FOR A-5510 VALVE2 K-3190 MASTER VALVE REPAIRKIT1 FOR A-6910 VALVE3 20112 COVER 1 A-69104 X-8-213 SCREW X 8 202 2 8-32X3/8"5 X-9-802 NUT 1 1/2"-136 84001 CONNECTORASSY 82501 2 1/8"TUBE-1/16"NPTF6 84003 CONNECTORASSY 82503 2 5/32"TUBE-1/16"NPTF6 84005 CONNECTORASSY 2 "PUSH-TO-CONNECT" 5/32"TUBE-1/16"NPTFK-276411 85001 ELBOWASSY 84501 2 5/32"TUBE-1/8"NPTF11 85002 ELBOWASSY 84502 2 1/8"TUBE-1/8"NPTF11 85003 ELBOWASSY 2 "PUSH-TO-CONNECT" 5/32"TUBE-1/8"NPTF K-2764,K-3121,K-3198,K-3333,K-3334,S-2485,S-248612 84101 UNION ASSY 1 1/8" TUBING12 84102 UNION ASSY 1 5/32" TUBING12 84103 UNIONASSY 1 "PUSH-TO-CONNECT" 5/32"TUBING13 80120 SHEATHING (50 FTROLL)1 5/32" - BLACK 50'14 13571 -O- RING CLAMP 2999 A-6910 ROADRANGER VALVEASSYA - 5510 1 STANDARD-W/LOGO999 S-2568 ROADRANGER VALVEASSY 1RTLO - W/SHIFT DIAGRAMMEDALLION38Group: SHIFT BAR HOUSING (F)SHIFT BAR HOUSING (F)Item CurrentPart Description ReplacedPartQty.Notes Kits/Assys WhereNeeded99910236-2-9539Item CurrentPart Description ReplacedPartQty.Notes Kits/Assys WhereNeeded1 S-2484 SHIFT BAR HSG ASSY(F) 4303112 1HOUSINGONLY2 4302676 GASKET 14918 1 K-2295,S-2484,S-2485,S-24863 4304602 BREATHER 23605 1 1/4"NPT3 X-12-404 PIPEPLUG 1 1/4"NPT4 62511 ROLLPIN 1 A-6340,S-2484,S-2485,S-24865 22812 PIN 1 S-2485,S-24866 X-12-603 PIPE PLUG X12 602 1 3/8" NPT7 4301999 PIN 22871 18 15900 GASKET 2 S-2484,S-2485,S-24869 22940 REV/NEUTRAL LIGHTSWITCH 16830 2SWITCHNORMALLYOPEN10 4303656 PLUG 15917 2 S-2484,S-2485,S-248611 20815 LIFTINGEYE 17105 212 X-8L-602 CAPSCREW 2 3/8"-16X1-1/2"12 X-8L-604 CAPSCREW 16 3/8"-16X1-1/4" OR USE 14 PCS OFX-8L-604 AND 2 PCS OF X-8L-60213 15899 PIN 1 S-2485,S-248614 15918 SPRING 2 K-2755,K-2764,S-2485,S-248615 X-14-800 STEELBALL 2 1/2"19 22815 SNAPRING 1 S-1786,S-2485,S-248620 22814 WASHER 1 S-1786,S-2485,S-248621 22809 SPRING 1 W/SHIFTLEVER K-2755,S-1786,S-248621 4302195 SPRING 1 W/REMOTECONTROL K-2755,S-2485 22 22811 PLUNGER 1 S-1786,S-2485,S-248623 4301549 SHIFTYOKE 1 S-2485,S-248624 3220 LOCKSCREW 3 S-2485,S-248625 4303114 YOKEBAR 1 S-2485,S-2486 26 4303115 GEAR SHIFT LEVER 140。
UT202A数字夹子电阻抗阻计说明书

OverviewThis Operating Manual covers information on safety and cautions. Please read the relevant information carefully and observe all the Warnings and Notes strictly.WarningTo avoid electric shock or personal injury, read the “Safety Information” carefully before using the Meter.Model UT202A is 2000-count stable, safe and reliable digital clamp multimeter(hereafter referred to as "the Meter"). It is designed with large-scale integrated circuits and A/D converter as the core as well as the overload protection and novel structure, which makeit a superb tool for electricians.The Meter can measure AC/DC Voltage, AC Current, Resistance, Diodes, and Continuity. Unpacking InspectionOpen the package case and take out the Meter. Check the following items carefully for any missing or damaged part:Item Description Qty1 English Operating Manual 1 piece2 Test Lead 1 pairIn the event you find any missing or damaged part please contact your dealer immediately. Safety InformationThis Meter complies with the standard IEC61010: Pollution Degree 2, Overvoltage Category (CATII 600V, CAT III 300V) and Double Insulation.CATII: Local level, appliance, PORTABLE EQUIPMENT etc., with smaller transient overvoltages than CATIII.CAT III: Distribution level, fixed installation, with smaller transient overvoltages than CAT IVUse the Meter only as specified in this operating manual, otherwise the protection provided by the Meter may be impaired.In this manual, a Warning identifies conditions and actions that pose hazards to the user, or may damage the Meter or the equipment under test.A Note identifies the information that user should pay attention to.WarningTo avoid possible electric shock or personal injury, and to avoid possible damage to the Meter or to the equipment under test, adhere to the following rules:.e s a ce h t t c e p s n i r e t eMe h tg n i s ue r of eB●Do not use the Meter if it is damaged or the case (or part of the case) is removed. Look for cracks or missing plastic. Pay attention to the insulation around the connectors.●Inspect the test leads for damaged insulation or exposed metal. Check the test leads for continuity. Replace damaged test leads with identical model number or electrical specifications before using the Mete r.● Do not apply more than the rated voltage, as marked on the Meter, between the terminals or between any terminal and grounding. If the value to be measured is unknown, use the● When measurement has been completed,disconnect the connection between the testleads and the circuit under test, remove thetesting leads away from the input terminals ofthe Meter and turn the Meter power off.●The rotary switch should be placed inthe right position and no any changeover ofrange shall be made when measurement isconducted to prevent damage of the Meter.● Do not carry out the measurement whenthe Meter’s back case and battery compartment are not closed to avoid electric shock.● Do not input higher than 600V between theMeter’s terminals and the grounding to avoidelectric shock and damages to the Meter.●When the Meter is working at an effectivevoltage over 60V in DC or 30V rms in AC,special care should be taken for there is dangerof electric shock.●Use the proper terminals, function, andrange for your measurements.●Do not use or store the Meter in anenvironment of high temperature, humidity,explosives, inflammables and strong magneticfield. The performance of the Meter maydeteriorate after dampened.●When using the test leads, keep yourfingers behind the finger guards.●Disconnect circuit power and dischargeall high-voltage capacitors before testingresistance, continuity and diode.●indicator appears. With a low battery, theMeter false readings that canlead to electric shock and personal injury.●When servicing the Meter, use only usethe replacement parts with the same modelor identical electrical specifications.● The internal circuit of the Meter shall not bealtered at will to avoid damage of the Meter andany accident.●Soft cloth and mild detergent should beused to clean the surface of the Meter whenservicing. No abrasive and solvent should beused to prevent the surface of the Meter fromcorrosion, damage and accident.● The Meter is suitable for indoor use.● Turn the Meter off when it is not in use and take out the battery when not using for a long time.● Constantly check the battery as it may leakwhen it has been using for some time, replacethe battery as soon as leaking appears. Aleaking battery will damage the Meter.Continuity TestDiodeThe Meter Structure (See Figure 1)Figure 11. Input Terminals2. LCD Display3. Functional Buttons4. Rotary Switch5. Trigger: press the lever to open thetransformer jaws. When the pressure on thelever is released, the jaws will close.6. Hand Guards: to protect user’s hand fromtouching the dangerous area.7. Transformer Jaws: designed to pick up theAC current flowing through the conducto r.It could transfer current to voltage. Thetested conductor must vertically go throughthe jaw center.maximum measurement position and reduce the range step by step until a satisfactory reading is obtained.Functional Buttons and Auto Power Off1. HOLDPress HOLD to enter and exit hold mode. Pressand hold HOLD button while turning on theMeter, auto power off will be canceled.2. MAXPress MAX to start recording and updating ofmaximum values.3. SELECTUnder Ω ranging, resistancemeasurement mode is default, press SELECTto select continuity measurement mode or diodemeasurement mode.4. Auto Power OffTo preserve battery life, the Meter automaticallygoes into a “sleep” mode if you do not press anybutton for around 10 minutes. The Meter can beactivated by pressing any effective button (referto The Effectiveness of Functional Buttons),then return to the display for the functionselected previously.5. BuzzerThe buzzer sounds every time a effective buttonis pressed down. When the meter will autopower off in 1 minute the buzzer beeps fivetimes. Before power off there will be a long timebuzzer beeps.6. The Effectiveness of Functional ButtonsNot every functional buttons can be used onevery rotary switch positions. Below tabledescribe which functional buttons can be usedΩ •Display Symbols (See Figure 2)Figure 2Measurement OperationA. Measuring DC Voltage (See Figure 3)WarningTo avoid harm to you or damage to the Meterfrom eletric shock, do not attempt to measurevoltages higher than 600V AC/DC.To measure DC voltage, connect the Meter asfollows:1. Insert the red test lead into theterminal and the black test lead into theCOM terminal.2. Set the rotary switch to .3. Connect the test leads across with the objectbeing measured.VΩThe measured value shows on the display.Figure 3Note:When DC voltage measurement has beencompleted, disconnect the connection betweenthe testing leads and the circuit under test andremove testing leads from the input terminals.B. Measuring AC Voltage (See Figure 4)WarningTo avoid harm to you or damage to the Meterfrom eletric shock, do not attempt to measurevoltages higher than 600V AC/DC.To measure AC voltage, connect the Meter asfollows:1. Insert the red test lead into theterminal and the black test lead into theCOM terminal.2. Set the rotary switch to .3. Connect the test leads across with the objectbeing measured.The measured value shows on the display.VΩFigure 4Note:When AC voltage measurement has beencompleted, disconnect the connection betweenthe testing leads and the circuit under test andremove testing leads from the input terminals.C. Measuring Resistance (See Figure 5)WarningTo avoid damage to the Meter or to thedevices under test, disconnect circuit power anddischarge all the high-voltage capacitors beforemeasuring resistance.To measure resistance, connect the Meter asfollows:1. Insert the red test lead into theterminal and the black test lead into theCOM terminal.2. Set the rotary switch to ; resistancemeasurement (Ω) is default or pressSELECT button to select Ω measurementmode3. Connect the test leads across with the objectbeing measured.The measured value shows on the display.Note:● Separating the objects being tested fromthe circuit when measuring can obtain a moreaccurate result.ΩVΩFigure 5● When resistance measurement has beencompleted, disconnect the connection betweenthe testing leads and the circuit under test andremove testing leads from the input terminals.~ END ~This operating manual is subject to change without notice.To test the diode out of a circuit, connect the Meter as follows:1. Insert the red test lead into theterminal and the black test lead into the COM terminal.2. Set the rotary switch to and pressSELECT button to select measurement mode.3. For forward voltage drop readings on any semiconductor component, place the red test lead on the component’s anode and place the black test lead on the component’s cathode.ΩVΩNote:● Separating the objects being tested from the circuit when measuring can obtain a more accurate result.● When diode testing has been completed, disconnect the connection between the testing leads and the circuit under test and remove testing leads from the input terminals.E. Testing for Continuity (See Figure 7)WarningTo avoid damage to the Meter or to the devices under test, disconnect circuit power and discharge all the high-voltage capacitors before measuring continuity.To test for continuity, connect the Meter as follows:1. Insert the red test lead into the terminal and the black test lead into the COM terminal.VΩFigure 6ΩFigure 72. Set the rotary switch to and pressSELECT button to select measurement mode.3. The buzzer sounds if the resistance of a circuit under test is less than 10Ω.4. The buzzer may or may not sounds if the resistance of a circuit under test is more than 10Ω.Note:When continuity testing has been completed, disconnect the connection between the testing leads and the circuit under test and remove testing leads from the input terminals.F. Measuring AC Current (See Figure 8) WarningTo avoid electric shock, never measure current while the test leads are inserted into the input terminals and disconnect test leads and tested circuit connection.Never attempt an in-circuit current measurement where the open-circuit voltage between the circuit and the ground is greater than 600V User proper function, and range for the measurement.otherwise it will casue deviation. The Meter can only measure one conductor at a time, to meausre more than one condutor at a time will cause deviation.Note:When current measurement has beencompleted,disconnect the connection between the conductor under test and the jaw, and remove the conductor away from the transformer jaw of the Meter.Figure 8General Specifications● Display: 3 1/2 digits LCD displa y , Maximum display 1999● Auto Polarity Display● Overloading: Display OL or● ● Measuremnet Deviation: When theconductor being meaured is not placed in a correct position during AC currentmeasurement, it will cause ±3% reading deviation.● Drop Test: 1 meter drop test passed ● Max. Jaw Opening: 28mm diameter ● Max. Tested Current Conductor: 26mm diameter.● Power: 9V battery● Sleep Mode (can be disabled)● Dimensions: 76mm x 208mm x 30mm.● Weight: Approximate 260g (battery included)● The Meter is suitable for indoor use.● Altitude: Operating: 2000m Storage: 10000m● Safety/ Compliances: IEC 61010 C ATII 600V, CATIII 300V and Double Insulation ● Pollution degree: 2● Temperature and humidity:Operating: 0℃~30℃ (≤75%R.H); 30℃~40℃ (≤70%R.H); 40℃~50℃ (≤45%R.H); Storage: -20℃~+60℃ (≤75%R.H)Accuracy SpecificationsAccuracy: ±(a% reading + b digits), guarantee for 1 year.Operating temperature: 23℃±5℃Relative humidity: ≤75%R.HT emperature coefficient: 0.1×(specified accuracy) /1℃A. AC Voltage: Auto Ranging Range Resolution Accuracy 2.000V 1mV20.00V 10mV ±(1.2%+5) 200.0V 100mV 600V1V ±(1.5%+5)Remarks:● Overload protection:600V rms ● Input impedance: 10MΩ // <100pF● Displays RMS value of sine wave (mean value response).● Frequency response: 40Hz~400Hz.B. DC Voltage: Auto Ranging Range ResolutionAccuracy200.0mV 0.1mV ±(0.8%+3) 2.000V 1mV20.00V 10mV ±(0.8%+1) 200.0V 100mV 600V1V±(1%+3)Remarks:● Input impedance: 10MΩ● Overload protection: 600V rms C. Resistance: Auto Ranging Range Resolution Accuracy 200.0Ω 100mΩ±(1.2%+2)2.000kΩ 1Ω20.00kΩ 10Ω ±(1%+2) 200.0kΩ 100Ω2.000MΩ 1kΩ ±(1.2%+2) 20.00MΩ 10kΩ ±(1.5%+2)Remark:● Overload protection: 600Vp D. ContinuityRange Resolution Accuracy Around <10Ω,the buzzer beeps.Remark:● Overload Protection: 600Vp● Open circuit voltage approximate 0.45V.● The buzzer may or may not beeps when the resistance of a circuit under test is more than 10Ω.● Overload Protection: 600Vp● Open circuit voltage approximate 1.48V.100mΩ F. AC Current: Auto RangingRange Resolution Accuracy 20.00A 0.01A ±(2.0%+5) 200.0A 0.1A ±(1.5%+5) 600A 1A ±(2.0%+8)Remarks:● Overload protection: 600A rms ● Frequency Response: 50Hz~60Hz● Displays RMS value of sine wave (mean value response).● To adjust reading in accordance with RMS value.MaintenanceThis section provides basic maintenance information including battery replacement instruction.WarningDo not attempt to repair or service your Meter unless you are qualified to do so and have the relevant calibration, performance test, and service information.To avoid electrical shock or damage to the Meter, do not get water inside the case.A. General Service● Periodically wipe the case with a damp cloth and mild detergent. Do not use abrasives or solvents.● To clean the terminals with cotton bar with detergent, as dirt or moisture in the terminals can affect readings.● Turn the Meter power off when it is not in use.● Take out the battery when it is not using for a long time.● Do not use or store the Meter in a place of humidity , high temperature, explosive, inflammable and strong magnetic field.To measure current, do the following:1. Set the rotary switch to 20A ,200 A or600 A .2. Press the trigger to open the transformer jaws.3. Center the conductor within the transformer jaw, then release the Meter slowly until the trasnformer jaw is completely closed, Makesure the conductor to be tested is placed at the center of the transformer jaw,D. Testing Diodes (See Figure 6)WarningTo avoid damage to the Meter or to the devices under test, disconnect circuit power and discharge all the high-voltage capacitors before testing diodes.replace as soon as the battery Make sure the transformer jaw and the tets leads are disconected from the circuit being tested before opening the case bottom.To replace the battery:.1. Turn the Meter off and remove all the connections from the input terminals.2. Turn the Meter’s case top down.3. Remove the screw from the battery compartment, and separate the battery compartment from the case bottom.4. Remove the old battery from the battery compartment.5. Rejoin the case bottom and the battery compartment, and reinstall the screw.Figure 9B. Replacing the Battery (See Figure 9)WarningTo avoid false readings, which could lead to possible electric shock or personal injury,。
Digital Multimeter User's Manual

This Digital Multimeter is intended for INDOOR USE ONL Y.stamped on the front and rear of the These warnings, as well as all warnings and precautions usedbe followed to avoid electric shock and/or per-ARTY shall be made aware that, if the equipment is used in a manner not specified by the manufacturer, the protection provided o prevent electrical shock and/or damage to the tester or the equipment under1.Plug the BLACK test lead into "COM" jack of the multimeter;plug the REDtest lead into the "V" jack.2.Set the meter’s Function/Range Selector Switch to the appropriate ACV orDCV position as desired.3.Place the RED test lead onto the positive (+) side of the item being testedand the BLACK test lead onto the negative (-) (across the source/load) side of the item.BE CAREFUL not to touch any energized conductors with any part of your body.4.Read the results on the display.B.RESISTANCE MEASUREMENT Ω(OHMS)1.Plug the RED test lead into the "Ω" jack of the multimeter;plug the BLACKtest lead into the "COM" jack.2.Set the meter’s Function/Range Selector Switch to the OHM "Ω" rangefunction.3.Place the RED test lead onto one side of the item being tested and theBLACK test lead onto the other side of the item.(Polarity does not matter when checking resistance).4.Read the results on the display.C.DIODE TEST1.Plug the RED test lead into the jack of the multimeter;plug the BLACKtest lead into the "COM" jack.2.Set the meter’s Function/Range Selector Switch to the position.3.Place the RED test lead onto one side of the diode being tested and theBLACK test lead onto the other side.4.Read the results on the display.5.Reverse the test leads and again read the results on the parethe two readings.One reading should indicate a voltage drop value;the other reading should indicate an overrange (1) condition.D.DC CURRENT MEASUREMENT (AMPS)1.Plug the RED test lead into the "mA" or the "DC10A" jack of the multime-ter, as applicable;plug the BLACK test lead to the "COM" jack.2.Set the meter's Function/Range Selector Switch to the appropriate Ampsrange position as desired.•T o measure from 0 to 200mA, set the Selector Switch to the desired "DCmA" position.•T o measure from 200mA to 10 Amps DC, set the Selector Switch to the "DC10A" position.3.Disconnect the battery, or shut off the power to the circuit being tested.4.Disconnect one end of the wire or device, from the circuit where current willbe measured.5.Place the RED test lead on the disconnected wire and place the BLACKtest lead at the location from which the wire was disconnected (series con-nection).6.Reconnect the battery, or apply power to the circuit being tested.7.Read the results on the display.CAUTION:After the test is completed,shut the power off to the circuit before removing the test leads and before reconnecting any disconnected wires or devices.E.BATTERY TEST1.Plug the RED test lead into the "BAT." jack of the multimeter;plug theBLACK test lead into the "COM" jack.2.Determine the voltage rating of the battery to be tested.3.Set the meter’s Function/Range Selector Switch to the desired "BatteryTest" range.4.Place the RED test lead on the positive post of the battery under test;placethe BLACK lead on the negative post.5.Read the results on the display.MAINTENANCE1.No periodic maintenance is required other than the replacement of the battery,the fuse, and visual inspection of the meter.2.Keep the meter clean and dry.DO NOT use solvent to clean, use a damp(not wet) cloth and fully dry after cleaning.BATTERY AND FUSE REPLACEMENT1.T urn the Digital Multimeter “OFF”and remove the test leads.2.Remove the two screws on the back of the meter and separate the case.3.Replace the fuse or battery as necessary:•For battery replacement:Remove the battery from the battery com-partment and replace only with one 9-volt alkaline battery.•For fuse replacement:Remove the fuse from the fuse holder and replace with a 0.315A/250V - UL Listed Bussmann,GMA Type(Radio Shack GMA/270 series;#270-1046 ) fuse.NOTE:Use a 0.315A/250V,5x20mm type fuse ONL Y - Bussmann, GMA Type (Radio Shack #270-1046 or similar).Using an incorrect fuse may result in seri-ous injury and/or damage to the unit.4.Reassemble the case and secure with the two screws.LIMITED ONE YEAR WARRANTYThe Manufacturer warrants to the original purchaser that this unit is free of defects in materials and workmanship under normal use and maintenance fora period of one (1) year from the date of original purchase.If the unit fails with-in the one (1) year period, it will be repaired or replaced, at the Manufacturer’s option, at no charge, when returned prepaid to the Service Center with Proof of Purchase.The sales receipt may be used for this purpose.Installation labor is not covered under this warranty.All replacement parts, whether new or remanufactured, assume as their warranty period only the remaining time of this warranty.This warranty does not apply to damage caused by improper use, accident, abuse, improper voltage, service, fire, flood, lightning, or other acts of God, or if the product was altered or repaired by anyone other than the Manufacturer’s Service Center.The Manufacturer, under no circumstances shall be liable for any consequential damages for breach of any written war-ranty of this unit.This warranty gives you specific legal rights, and you may also have rights, which vary from state to state.This manual is copyrighted with all rights reserved.No portion of this document may be copied or reproduced by any means without the express written permission of the Manufacturer.THIS WARRANTY IS NOT TRANSFERABLE.For service, send via U.P.S.(if possible) prepaid to Manufacturer.Allow 3-4 weeks for service/repair.Copyright © IEC.All Rights Reserved.WARNINGResistance measurements must be made on "de-energized" (dead) cir-cuits ONL Y.Impressing a voltage across the multimeter's terminals while set to any resistance range may result in electric shock,instrument dam-age and/or damage to equipment under test.MAKE SURE equipment is completely de-energized before taking any resistance measurements.WARNINGTo avoid electrical shock and/or damage to the multimeter,ensure the power is removed from the circuit before any DIODE testing procedure is conducted.Test diodes on de-energized (dead) circuits only,never on live circuits.WARNINGTo prevent electrical shock when performing current measurements, follow all steps as indicated below DO NOT skip any steps or take any short cuts.The DC10A range is not fused.To avoid current hazard and/or damage to the tester,DO NOT try to take measurements on circuits that have more than 10 amps.DO NOT take more than 15 seconds to take the reading.A waiting period of AT LEAST 15 MINUTES is necessary between every 15 second testing period.WARNINGWhen replacing the battery or the fuse,remove only the rear panel.Do not remove or disassemble the circuit board or the front panel,these items are not serviceable and if disassembled there is the possibility of loose metal parts shorting the circuit board and causing an electrocu-tion danger to the user.。
Model SD-220-120M Vibration Test System 产品说明说明书

Typical System Application TheModel SD-220-120M Vibration test system is a versatile wide bandwidth electrodynamic vibration test system. It is designed for testing small to medium sized payloads of the automotive, aviation, military, medical and electronic manufacturing industries.It is capable of a Random RMS force of 220 lbf and Sine Vector force of 220 lbf operating in the frequency range 5 Hz to 6,000 Hz under controlled conditions. The system consists of a model SD-220-120Mshaker and is driven by the Model SPA102B power amplifier and a 0.75 KW cooling blower. Optional items including slip tables, head expanders, accelerometers and vibration controller can be added upon request.State of the Art Magnesium ArmatureThe unique reinforced magnesium armature structure design is state-of-the-art, providing increased reliability, unsurpassed performance, optimized rigidity and force transmissibility. Designed for continuousduty and ideal for research and development, production, stress screening and qualification testing, the ruggedized armatures canendure severe vibration and shock forces as well as extreme temperature conditions.How to select the suitable modelIt is critical to consider the size and position of the test article and the total moving mass of the payload as well as the payload’s inertial and overturning moments when selecting a system for your application. It is recommended the force selected should be 1.2 times the theoretical value, to insure appropriate safety margins. For assistance selecting the best system for your needs, please contact our sales representative.High FRF & Wide UFThe new shaker design significantly raises the Fundamental Resonance Frequency and Useable Frequency range of the long s t r o k e s y s t e m s a n d outperforms similar products from other manufacturers.Efficient Air CoolingThe SD-220-120M shaker system is totally air cooled for easy installation and economical operation. Cooling Blower UnitThe suitable ACU751 cooling blower is specified below.Rigid and Rotating TrunnionAll shakers come standard in a rotating trunnion for easy 90° rotation between the horizontal and vertical test axes. The trunnion is rigidly connected to the trunnion frame. Rubber isolation pads are suppliedSYSTEM OPTIONS ✦Slip Table Configuration✦V-Groove Caster and Rail System ✦Head Expander ✦Thermal Barrier ✦Assistant Load Support Under Head Expander ✦Air Caster SD-220-120M/SPA102B/ACU751allowing for direct mounting onto conventional industrial concrete floors. All shakers are optionally available with an integrated or stand-alone slip table assembly. D-Class Switching AmplifierThe state-of-art modular switching amplifiers are 100% air-cooled with redundant safety systems and system interlocks insuring performance that is reliable and stable. All amplifiers adopt discrete IGBT power modules of high quality with a 120 KHz switching frequency. There are two boxes - amplifier and field supply. SafetyProducts comply with European tests standards and ISO regulations.TECHNICAL SPECIFICATIONSNOTE: Standard vibration systems consist of an electro-dynamic exciter, a state-of-the-art air-cooled switching power amplifier with field power supply and cooling unit. Optional items including slip tables, head expanders, accelerometers and vibration controller can be added upon request.In keeping with our commitment to continuousproduct improvement, the information herein is subjectto change. Copyright 2018 Spectral Dynamics, Inc. Allrights reserved.Switching Power Amplifier SPA102BRated OutputCapacity 1 kV ASignal to NoiseRatio Greater than 65 dBSwitchingFrequency 120 kHzAmplifierEfficiency Greater than 90%Interlock Protection (to prevent the output devices from working outside their specified limits)•Shaker Over Travel •Shaker Over Temp •Shaker Air pressure •Shaker Oil pressure •Shaker E Stop •Amplifier E Stop •Transformer Over Temp •UART Power •PM Over Temp •PM Over Current•PM Drive Power•Input Under V oltage•Input Over V oltage•Output Over V oltage•Output Over Current •Cooling Fan•Power Over Temp•Logic FaultShaker SD-220-120MSine (Pk)220 lbf (100 kgf)Vertical Load Support 100 kg (220 lbs)Random (RMS)220 lbf (100 kgf)Body Suspension NaturalFrequency (Thrust Axis)Rigid trunnionShock (Pk)440 lbf (200 kgf)Table Diameter 120 mm (4.7”)Usable Frequency 5 to 6,000 Hz Armature Effective NominalWeight 1.5 kg (3.3 lbs)Max. Displacement (p-p)25 mm (1”)Load Attachment Points (Standard)Stainless steel M6 Inserts or optionalUNC.Maximum Velocity 1.6 m/s (63 in/s)Overall Dimensions 400mmL x 360mmD x 470mmH(15.7”L x 14.2”D x 18.5”H)Maximum Acceleration 65 g Weight of Shaker (Uncrated)175 kg (385 lbs)Fundamental ResonanceFrequency (Bare Table)4,700 Hz (nom.) +/- 5%Air Requirement Manual PumpedDegauss Coil Standard Stray Field@6 inch (152 mm)above table < 1 mT (10 gauss)System Environmental Requirement Air Cooling Blower ACU751Operating Room Temperature 0 to 40 degree C Blower Power (Full Load) 1 HP(0.75 kW)Humidity 0 to 90%, noncondensing Air Flow Rate 0.1 m 3 /s (215 CFM)Amplifier 1 kV A Field Supply 1 kV A Air Pressure 0.001 Mpa(0.15 PSI)Blower 1 kV A Power Supply Requirement Single phase, Neutral and Ground is required. 230V AC (50/60 Hz) and 115V AC (50/60 Hz) available. Amplifier, field and blower are powered separately. The values are actual ones, the mains need a safety margin.。
贝利默CMB24-SR-R非失效模式调节阀门驱动器说明书

CMB24-SR-RBasic Non Fail-Safe modulating actuator forcontrolling dampers in typical commercial HVAC applications.• Torque motor 18 in-lb [2 Nm]• Nominal voltage AC/DC 24 V • Control Modulating• Position feedback 2...10 VTechnical dataElectrical dataNominal voltageAC/DC 24 V Nominal voltage frequency 50/60 HzNominal voltage rangeAC 19.2...28.8 V / DC 19.2...28.8 V Power consumption in operation 1.5 W Power consumption in rest position 0.5 W Transformer sizing 1.5 VAElectrical Connection 18 GA plenum cable , 1 m, degree of protection NEMA 2 / IP54Overload Protectionelectronic throughout full rotation Functional dataTorque motor 18 in-lb [2 Nm]Operating range Y 2...10 VOperating range Y note 4...20 mA w/ ZG-R01 (500 Ω, 1/4 W resistor)Position feedback U 2...10 V Position feedback U note Max. 0.5 mADirection of motion motor by electrical installation Manual override disengage with magnet Angle of rotation 0...287.5°Angle of rotation note Without limitation: endlessWith one end stop clip Z-ESCM: 315°Running Time (Motor)35 s / 90°Running time motor note constant, independent of load Noise level, motor 45 dB(A)Position indicationMechanical, pluggable (with integrated magnet for gear train disengagement)Safety data Power source ULClass 2 Supply Degree of protection IEC/EN IP54Degree of protection NEMA/UL NEMA 2Enclosure UL Enclosure Type 2Agency ListingcULus acc. to UL60730-1A/-2-14, CAN/CSA E60730-1:02CE acc. to 2014/30/EU and 2014/35/EU Quality Standard ISO 9001UL 2043 CompliantSuitable for use in air plenums per Section 300.22(C) of the NEC and Section 602 of the IMCAmbient humidity Max. 95% RH, non-condensing Ambient temperature -22...122°F [-30...50°C]Storage temperature -40...176°F [-40...80°C]Servicingmaintenance-free WeightWeight0.57 lb [0.26 kg]CMB24-SR-RFootnotesApplicationOperationTypical specificationMaterialsHousing material UL94-5VA†Rated Impulse Voltage 800V, Type of Action 1, Control Pollution Degree 2.Product featuresDamper actuator for operating air control dampers in ventilation and air-conditioning systems for building services installations.• For air control dampers up to approximately 4.5 sq ft • Torque 18 in-lb [2 Nm]• Nominal voltage AC/DC 24 V • Control: 2...10 V • Running time 35 s @ 90°Simple direct mounting on the damper spindle with a universal spindle clamp or form fit, supplied with an anti-rotation bracket to prevent the actuator from rotating.Manual operation is possible with a magnet (the gearing latch remains disengaged as long as the magnet is in place).Adjustable angle of rotation with mechanical end stops, that requires no tools to move or remove.The actuator is overload-proof, requires no limit switches and automatically stops when the end stops is reached.The CMB24-SR (-R or -L) actuator uses a brushless DC motor, which is controlled by anApplication Specific Integrated Circuit (ASIC). The ASIC monitors and controls the actuator’s rotation sensing (DRS) function to prevent damage to the actuator in a stall condition. Power consumption is reduced in holding mode.Belimo’s Halomo sensorless brushless DC motor spins by reversing the poles of stationary electromagnets housed inside rotational permanent magnets. The electromagnetic poles are switched by the an ASIC developed by Belimo. Unlike the conventional DC motor, there are no brushes to wear or commutators to foul. This means the brushless DC motor adds accuracy and reduces power consumption in a holding mode.Proportional control damper actuators shall be electronic direct-coupled type, which require no crank arm and linkage and be capable of direct mounting to a shaft from 1/4" to 1/2" diameter. Actuators must provide proportional damper control response to a 2 to 10 VDC or, with the addition of a 500Ω resistor, a 4 to 20 mA control input from an electronic controller orpositioner. Actuators shall have brushless DC motor technology and be protected from overload at all angles of rotation. Actuators shall have manual override on the cover. Run time shall be constant and independent of torque. Actuators shall be cULus listed, have a 5-year warranty, and be manufactured under ISO 9001 International Quality Control Standards. Actuators shall be as manufactured by Belimo.Electrical installationProvide overload protection and disconnect as required.Actuators may also be powered by DC 24 V.Only connect common to negative (-) leg of control circuits.A 500 Ω resistor (ZG-R01) converts the 4...20 mA control signal to 2...10 V.Actuators may be connected in parallel if not mechanically linked. Power consumption and input impedance must be observed.CMB24-SR-R2...10 V / 4...20 mA ControlDimensions。
MD ADAMS软件模块功能说明

10. 卡车插件 MD ADAMS/Truck Plugin .............................................................................. 10
四、 实用工具包(MD ADAMS /Toolkit) .................................................................. 11
MD ADAMS 软件模块功能说明............................................................................................ 2 一、 MD ADAMS 基本包(MD ADAMS Basic Package) .......................................... 2
2. 求解器模块 MD ADAMS/Solvห้องสมุดไป่ตู้r(10110)
MD ADAMS/Solver 是 MD ADAMS 的求解器, 包括稳定可靠的 Fortran 求解器和功能更为 强大丰富的 C++求解器。该模块既可以集成在 MD ADAMS 的前处理模块下使用,也可以外部 直接调用。既可以进行交互方式的解算过程,也可以进行批处理方式的解算过程。求解器先导 入模型并自动校验模型,进行初始条件分析,再进行后续的各种解算过程。独特的调试功能, 可以输出求解器解算过程中重要数据量的变化,方便把控定位模型中深层次的问题所在。MD ADAMS/Solver 同时提供了用于进行机械系统的固有频率(特征值)和振型(特征矢量)的线 性化专用分析工具。 功能及特色: 静力学、准静力学、运动学和非线性瞬态动力学的求解; 借助空间笛卡儿坐标系及欧拉角描述空间刚体的运动状态,使用 Euler-Lagrange 方程自动 形成系统的运动学或动力学方程,采用牛顿—拉夫森迭代算法求解模型; 多种显式、隐式积分算法:刚性积分方法(Gear ’s 和 Modified Gear ’s) 、非刚性积分方法 (Runge-Kutta 和 ABAM) 和固定步长方法 (Constant_BDF) 以及二阶 HHT 和 NewMark 等 积分方法; 多种积分修正方法:3 阶指数法、稳定 2 阶指数法和稳定 1 阶指数法; 新的静平衡(Equilibrium)算法;特别是在困难情形,如系统处于奇异的、病态的或者是初始 状态与平衡状态相距甚远情形下的非线性系统非常有效。 支持弹性体-刚性体、弹性体-弹性体接触碰撞的支持,弹性体可以是3D实体单元或2D壳单 元。最值得注意的是,后处理功能同样支持对2D壳单元节点应力应变等的绘图以及动画功 能,以及可藉由FEMDATA 功能输出负载到有限元分析软件的功能。 支持本构几何外形,如球、椭球体、圆柱体、长方体等直接进行碰撞载荷的计算。该方法 借助简单几何形状具备特征尺寸之优势,采用侦测接触碰撞的分析方法进行嵌入体积的计 算及接触碰撞力本身的值等,达到提高计算的精度并减少计算时间的目的。应用实例则包 括了通用机械、履带式车辆、滚柱轴承和球轴承、皮带和绳索等模型。 支持用户自定义的 Fortran 或 C++子程序; 解算稳定,结果精确,经过大量实际工程问题检验; 提供大量的求解参数选项供用户进一步调试求解器,以改进求解的效率和精度。
- 1、下载文档前请自行甄别文档内容的完整性,平台不提供额外的编辑、内容补充、找答案等附加服务。
- 2、"仅部分预览"的文档,不可在线预览部分如存在完整性等问题,可反馈申请退款(可完整预览的文档不适用该条件!)。
- 3、如文档侵犯您的权益,请联系客服反馈,我们会尽快为您处理(人工客服工作时间:9:00-18:30)。
Lecture 2:Motor Model andLecture 2: Motor Model and Display SubsystemMotor Motor Battery Motor V I ωτ=−f h b Thfrom the battery. ÎThe motor current should be negative to discharge the battery.Motor Motor Battery Motor V I ωτ=−into the battery.The motor current into the battery. ÎThe motor current should be positive to charge the battery.MotorMotor Battery Motor V I ωτ=−complicated as our understanding of the complicated as our understanding of the system increases.M d l O t t(Si D i li)•Model Outputs (SimDriveline):–Motor Torque7 Place a new subsystem part (Simulink/Commonly Used Blocks)in your circuit and change the nameto “Electric_Motor.”Double-click on the subsystem block to open it:•Motor_CurrentM t C t•Motor_Diagnostics9 We also have one SimDriveline connection port(SimDriveline/Utilities).Place this part in your model and rename it as“Motor_Port.”10 We now have all of the input and output ports forWe now have all of the input and output ports forour motor model. All that is left is for us to buildthe actual model.•The inertia part is located in theSimDriveline/Solver & Inertias library.12 The inertia part specifies the inertia for all rotating parts of the motor. We will define this inertia in the init file. Double-click on the inertia part and change the value to “Motor_Inertia.”13We should find the inertia from the motor specifications ormeasure the inertia. Once a value is obtained, we will specify it in the init file:Next, we can calculate the motor current asBatteryMotorMotorMotor V I ωτ−=Use a Motion Sensor (SimDriveline/Sensors &Actuators ) to measure the motor shaft speed in r/s.14_q_–Motor torque Nm–Motor_Current_Adouble-click on the bus creator part and change the number from 2 to 3.Bus creator after makingchange.18 Complete the model as shown below.input and outputs as shown:input and outputs as shown:Top Level Block Diagram20•Connect the blocks as shown:22 The motor port is not in a convenient location to connect it to the reardiff. We can fix this problem by:•Double-clicking on the Electric_Motor subsystem to open it.•Double-clicking on the “Motor_Port” part to open its dialog box.You will see the dialog box shown next:23Double-click here.Change this to right.After making this change, we can easily connect the motor and rear diff.busses using the bus creator part busses using the bus creator part (Simulink/Commonly Used Blocks).28 Top Level Block Diagramphysical system.It is for simulation purposes physical system. It is for simulation purposes only and generates a torque request that would normally come from the vehicle’s accelerator and brake pedals.•The desired speed will be stored in a variable.•Rename the subsystem Driver. Rename the subsystem“Driver”±1.•Use the Saturation part located in the Simulink/Commonly Used Blocks library.and1and -1.•Rename the output terminal to “Driver Torque Request.”36•The saturation limits are specified asshown:as shown: as shown:create several plots to display varioussignals in different configurations.•We will also use this subsystem to logdata.We will show two methods of creating adisplay The first method will use a Scope display. The first method will use a Scopeblock. The seconds will be shown laterand use the Signal and Scope Manager.(Simulink/Commonly Used Blocks) and the Scope(Simulink/Commonly Used Blocks) to create a display of the important signals.43 Creating the Display•Double-click on the Bus Selector part •Click on the +Click on the+signs in the“Signals in theBus” windowto view theil blavailablesignals.•Select the signals in the order you want Select the signals in the order you want them to appear on the bus extractor.Selector part.•Next, double-click on the Scope part:Double-click here.47 Click on this button.•Click on the Parameters buttonChange this to 5.48Click on the Data historyTab.Click here to uncheck thisbox. Deselecting this boxbox.Deselecting this boxwill display all data in oursimulation.49 Box unchecked.Click the OK Button.Close the scopewindow and returnwindow and returnto the model.Resize the scopepart and connectthe signals.5052Set to 60.Select ode23tbSet to Auto.54Set to error.Diagnostics selected.Set to error.•These selections will highlight an algebraic if one is detected.Running the Simulation•Click the OK button.•Select Simulation and then Start from the Simulink menus or click the play button 55Simulink menus or click the play button.•It appears that we have an error.two of our subsystems The Algebraic loop two of our subsystems. The Algebraic loop is highlighted in red:57 Algebraic Loop•If you look inside the Electric_Motor subsystem, you will see the offending components in that subsystem:In order for Simulink to calculate the motor current, it needs to know the battery voltage.58 Algebraic Loop•If you look inside the Battery subsystem, you will see the offending components in that subsystem:In order to calculate the battery voltage, Simulink needs to know the motor current!information it needs to perform this information it needs to perform this calculation.part (to either the Battery model or the motor61•The memory block is a one time step delay. In the division calculation, Simulink will use the battery voltage from the previous time step. Thus the batterywill use the battery voltage from the previous time step.Thus the battery voltage is know, and Simulink can calculate the motor current.•Rerun the simulation and see if this fixes the problem.•You may want to ask yourself the question, what is the output value of the memory block at time zero (when the simulation starts)? (Obviously this implies that the block knows the input at time less than zero, which has all kinds of philosophical implications about the space-time continuum….)62•The problem is fixed, but we get anothererror.•Click on the link to jump to the error.63 According to the errormessage, this signal mustmessage,this signal mustbe Infinite, or Nan.65•For the first time step, what is the input to the Divide block?For the first time step what is the input to the Divide block?•The Memory block outputs the value from the previous time step.•For the first time step, what is the previous value.•If the block outputs a 0, we get a divide by zero, and the Divide block either outputs Inf or Nan.•We need to move the Memory block somewhere else to eliminate the algebraic loop.66Memory block removed.67 Memory block added to thebattery model.Rerun the Simulation68rpm signal.rpm signal.Demo___________ Debugging the ModelDebugging the Model72 Vehicle speedOK.Motor rpm spike.Motor rpm spike74•If there is no skidding, the tire speeds should be the same as the vehiclespeed.•Run the simulation75Zoom in here.76Tire speed same as vehicle speed.Tire speeddifferent than vehicle speed.Open the driver block and add a scope to •Open the driver block and add a scope tothe driver torque request signal.Rerun the simulation and view the scope.78 Max torque (1).Tire skiddinghappens here.Vehicle cruising gat 60 mph here.Rate Limiter80•The rate limiter places a limit on how fasta signal can increase or decrease.•The default rising and falling rates are1/second.•We will use the default values.•Since the driver torque request signal isbetween -1 and +1•Our motor will go from no torque (0)•Our motor will go from no torque(0)to full torque (1) in one second.•Our motor will go from full forwardtorque (1) to full reverse torque (-1) intwo seconds.Run a simulation with the rate limiter.81Things areworse!82 Motor rpm goingnegative.What do younotice aboutthis?•Let s plot the motor torque using a scope.Let’s plot the motor torque using a scopeRate limiterremoved.84 Scope added.85Tire skiddinghappens here.h hZoom in on thissection.86Traces in natureare very rarelystraight. Usuallythings are curved.Zoom in someZoom in somemore.87Simulation point.Simulation point.pLooks like at i ht listraight lineconnecting twosimulation points.Model Debugging•Another hint comes from the MATLAB command window.88What is this?p glike we had a step of 0.35 seconds that was too large.•Let’s try a smaller step size.•Select Simulation and then Configuration Parameters from the Simulink menus.•Change the Max Step size from Auto to 0.01 (seconds)90This was set to Auto.Change it to 0.01.•This parameter specifies that the maximum time between simulation points will be 0.01 seconds. (It between simulation points will be001seconds(Itcan be smaller if necessary.)•Rerun the simulation with this change.91 and negative battery voltages.•How does our model breakdown if the motor current is too large?Demo___________。