铁水预处理脱硫过程氮含量预测
铁水预处理

镁脱硫法
镁以镁焦、镁锭、镁粉、镁合金及白云石的团块等形式加 入铁水中进行脱硫。用镁脱硫的最重要问题是要控制镁的 气化速度,以免发生爆炸。 镁脱硫时采用的主要方法有插罩法、插杆法、三明治法、 压力室法、可倾罐法、T-Nock流槽法和喷吹法等。 优点:镁脱硫法速度快、渣量少、温度损失少, 缺点:费用高、操作控制困难。
吹气搅拌法
吹气搅拌法主要有顶吹法、底吹法(PDS或CLDS)和气升 泵法三种。 顶吹法和底吹法预先将脱硫剂加到铁水表面,然后通过顶 枪或罐底的透气砖往铁水中喷吹气体进行搅拌。这两种方 法设备费用低,操作简便,但脱硫效果不如搅拌法好。 气升泵法向气升泵吹入气流将铁水不断升入泵筒体。当筒 体内铁水超过罐内液面高度时,铁水通过筒体上部的许多 孔眼喷撒到熔池表面的脱硫剂上而发生脱硫反应。
铁水预处理(一) 脱硫
铁水预脱疏工艺优点
(1)用户对钢的品种和质量要求提高,连铸技术的发展也要求 钢中硫含量低(硫含量高容易使连铸坯产生裂纹)。铁水脱 硫可满足冶炼低硫钢和超低硫钢种的要求。 (2)转炉炼钢整个过程是氧化气氛,脱硫效率仅为30%~40 %;而铁水中的碳、硅等元素含量高,氧含量低,提高了 铁水中硫的活度系数,故铁水脱硫效率高;铁水脱硫费用 低于高炉、转炉和炉外精炼的脱硫费用。 (3)减轻高炉脱硫负担后,能实现低碱度、小渣量操作,有利 于冶炼低硅生铁,使高炉稳定、顺行,可保证向炼钢供应 精料。 (4)有效地提高钢铁企业铁、钢、材的综合经济效益。
铁水预脱硫的主要方法
(1)搅拌法 搅拌法又分机械搅拌法和吹气搅拌法 (2)喷吹法 (3)铁水沟铺撒冲混法 (4)铁水沟喷粉脱硫法 (5)镁脱硫法
机械搅拌法脱硫(KR法)
机械搅拌法脱硫(KR法):将浇注耐火材料并经过烘烤的十 字形搅拌头,浸入铁水包熔池一定深度,借其旋转产生的 漩涡,使氧化钙或碳化钙基脱硫粉剂与铁水充分接触反应, 达到脱硫目的。 脱硫剂:CaO-CaF2系脱硫剂。 优点:动力学条件优越,有利于采用廉价的脱硫剂如CaO, 脱硫效果比较稳定,效率高(脱硫到≤0.005%),脱硫剂消 耗少,适应于低硫品种钢要求高、比例大的钢厂采用。 缺点:设备复杂,一次投资较大,脱硫铁水温降较大。
铁水预处理脱硫的热力学条件

铁水预处理脱硫的热力学条件以铁水预处理脱硫的热力学条件为标题,我们来探讨一下在这个过程中的一些重要热力学条件。
铁水预处理脱硫是指在铁水冶炼过程中,通过加入适量的脱硫剂,使铁水中的硫含量降低到规定的范围内。
这一过程在保证铁水质量的同时,也对热力学条件有一定要求。
铁水预处理脱硫的热力学条件之一是温度。
在铁水预处理脱硫过程中,温度的选择对反应的进行有着重要影响。
通常情况下,高温有利于脱硫反应的进行。
因为高温可以提高反应速率,增加反应的活性。
但是过高的温度也会导致过多的热量损失,增加能源消耗。
因此,在选择温度时需要在脱硫效果和能源消耗之间进行平衡。
铁水预处理脱硫的热力学条件还包括氧气含量。
氧气是铁水预处理脱硫反应中的重要参与物质,它可以与脱硫剂中的硫反应生成气体SO2,并通过气体逸出的方式将硫从铁水中去除。
因此,适量的氧气含量对于脱硫反应的进行至关重要。
过低的氧气含量会导致脱硫反应的进行受限,而过高的氧气含量则会增加能源消耗和气体处理的成本。
铁水预处理脱硫的热力学条件还包括脱硫剂的选择。
脱硫剂是铁水预处理脱硫中的关键因素,它可以与铁水中的硫反应生成易挥发的化合物,从而实现脱硫的目的。
常用的脱硫剂有碳酸钙、氧化钙等。
在选择脱硫剂时,需要考虑脱硫剂的稳定性、反应活性以及成本等因素。
合理选择脱硫剂可以提高脱硫效果,降低成本。
铁水预处理脱硫的热力学条件还包括反应时间。
反应时间是指脱硫反应进行的时间长度。
脱硫反应的进行需要一定的时间来完成,过短的反应时间会导致脱硫效果不理想,而过长的反应时间则会增加生产周期和能源消耗。
因此,在实际操作中需要合理控制反应时间,以达到脱硫效果最佳化。
铁水预处理脱硫的热力学条件包括温度、氧气含量、脱硫剂选择和反应时间等因素。
在实际操作中,需要根据具体情况合理选择这些条件,以达到脱硫效果最佳化的目标。
同时,也需要在脱硫过程中平衡脱硫效果和能源消耗之间的关系,以提高生产效率和降低成本。
通过科学合理地控制这些热力学条件,可以实现铁水预处理脱硫的高效、稳定和可持续发展。
铁水预处理脱硫分析
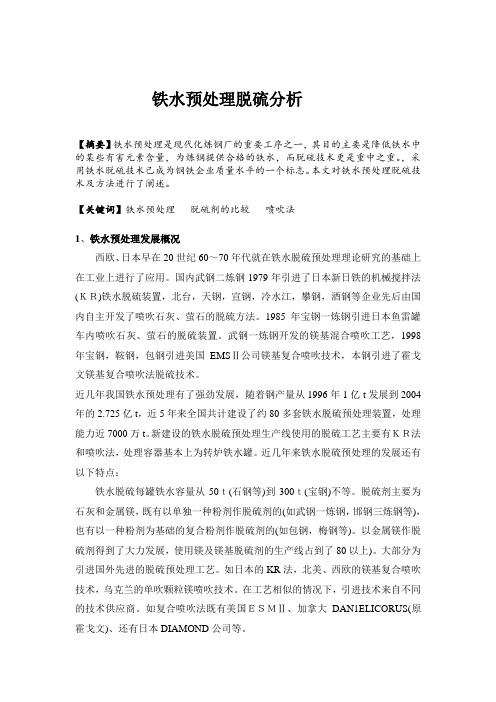
铁水预处理脱硫分析【摘要】铁水预处理是现代化炼钢厂的重要工序之一,其目的主要是降低铁水中的某些有害元素含量,为炼钢提供合格的铁水,而脱硫技术更是重中之重。
,采用铁水脱硫技术已成为钢铁企业质量水平的一个标志。
本文对铁水预处理脱硫技术及方法进行了阐述。
【关键词】铁水预处理脱硫剂的比较喷吹法1、铁水预处理发展概况西欧、日本早在20世纪60~70年代就在铁水脱硫预处理理论研究的基础上在工业上进行了应用。
国内武钢二炼钢1979年引进了日本新日铁的机械搅拌法(KR)铁水脱硫装置,北台,天钢,宣钢,冷水江,攀钢,酒钢等企业先后由国内自主开发了喷吹石灰、萤石的脱硫方法。
1985年宝钢一炼钢引进日本鱼雷罐车内喷吹石灰、萤石的脱硫装置。
武钢一炼钢开发的镁基混合喷吹工艺,1998年宝钢,鞍钢,包钢引进美国EMSⅡ公司镁基复合喷吹技术,本钢引进了霍戈文镁基复合喷吹法脱硫技术。
近几年我国铁水预处理有了强劲发展,随着钢产量从1996年1亿t发展到2004年的2.725亿t,近5年来全国共计建设了约80多套铁水脱硫预处理装置,处理能力近7000万t。
新建设的铁水脱硫预处理生产线使用的脱硫工艺主要有KR法和喷吹法,处理容器基本上为转炉铁水罐。
近几年来铁水脱硫预处理的发展还有以下特点:铁水脱硫每罐铁水容量从50t(石钢等)到300t(宝钢)不等。
脱硫剂主要为石灰和金属镁,既有以单独一种粉剂作脱硫剂的(如武钢一炼钢,邯钢三炼钢等),也有以一种粉剂为基础的复合粉剂作脱硫剂的(如包钢,梅钢等)。
以金属镁作脱硫剂得到了大力发展,使用镁及镁基脱硫剂的生产线占到了80以上)。
大部分为引进国外先进的脱硫预处理工艺。
如日本的KR法,北美、西欧的镁基复合喷吹技术,乌克兰的单吹颗粒镁喷吹技术。
在工艺相似的情况下,引进技术来自不同的技术供应商。
如复合喷吹法既有美国ESMⅡ、加拿大DAN1ELICORUS(原霍戈文)、还有日本DIAMOND公司等。
我国在早期引进国外先进技术的基础上改进的自主知识产权开发技术也在发挥着作用。
铁水脱硫数值模拟

用后面一组12m/s8m/s10m/s10m二次15m/s1000mm-----5m/s10m/s15m/s1500-----5m/s10m/s15m/s我们模拟了不同工况下的内部流场的情况。
根据喷枪的插入深度,分别有h=100, 200, 300mm;根据载气流速,分别有v=5,10,15m/s。
除了喷枪插入深度和载气体流速外,喷粉速度、喷枪喉口及喷枪出口直径、气泡内携带的粉末颗粒比率以及粉剂颗粒直径等工艺等对脱硫的效率都会产生影响,但是在本文中,对其不做研究。
我们很容易的知道,当喷枪的插入深度减小时,容器下半部分的流场速度为零的区域会增大,即喷吹搅拌的死区增大。
而且喷管口生成的气泡上浮至自由液面的距离减小,这样,使得镁颗粒的反应行程和在液相中的停留时间都缩短了,降低了脱硫效率。
载气的速度对脱硫的效率也有影响。
随着载气体流速的增加,铁水预处理脱硫的效率也随之增加。
其脱硫效率的增加的原因可以解释为:载气体流速的增加,使得容器内的液体的搅拌强度增加。
但是载气体的速度不能超过临界值,否则气泡和粉末在液相中的停留时间变得过短,这样反而会降低脱硫效率。
而且过高的载气体流速会使容器内的液体产生喷溅。
在实际的脱硫生产过程中,铁水产生喷溅是很危险,应该尽量避免发生。
由于在载气体速度不同的情况下,流场和载气泡的变化趋势是大致一样的。
本文仅对喷管插入深度为200mm 时的气泡上升直至破裂的演变过程和喷管插入深度为200mm 时的流场变化过程进行分析。
以下的各图中,载气体的速度比较小,为5m/s,所以,载气体总的体积也比小,液相的自由液面的变化很小,当载气体的速度加大时,液面的变化会变得剧烈。
在气泡上升的过程中,由于其到自由液面的距离减小,我们很容易的知道,气泡所受到的静压也会减小。
此时,气泡会膨胀。
当气泡膨胀到一定程度,即气泡内的压强大于气泡所受的静压强时,气泡会破裂,形成小气泡。
气泡继续上升,直至穿过液相自由表面,进入大气。
铁水预处理工艺操作规程

铁水复吹脱硫预处理工艺技术规程1. 脱硫原理铁水预处理是在转炉兑铁罐内复合喷吹镁粉和石灰粉方式。
石灰粉(CaO)脱硫反应为:CaO(s) +[S] +[C] =CaS(s) + CO(g)2CaC(s) +[S] +1/2[Si] =CaS(s) + 1/2Ca2SiO4(s)镁脱硫反应为:Mg(s)→Mg(l) →{Mg}→[Mg]Mg与S的相互反应存在两种情况:第一种情况:{Mg}+[S]=MgS(s)第二种情况:{Mg}→[Mg][Mg]+[S] = MgS(s)2. 铁水条件2.1混铁炉铁水2.2处理后的铁水S:范围 0.001%~0.010%平均≥0.005%2.3 产品和产量的要求炉容量 75t转炉冶炼周期:平均 30min最小 26min3 .复合喷吹石灰粉和镁粉脱硫工艺原材料3.1镁粉3.2石灰粉(活性石灰)粒度: <0.25mm 100%<0.075mm >80%3.3脱硫粉剂储存两种料仓:镁粉料仓和石灰料仓,脱硫站两个喷吹工位,共用一套镁粉料仓和石灰料仓。
袋装镁粉储存在专门的仓库内,每天用汽车将袋装的镁粉运至脱硫站,用10t起重机逐袋卸入镁粉料仓。
石灰粉采用槽式运输车气力输送上料。
脱硫剂靠重力就可以从每个料仓中加入到选中的喷吹罐中。
每个料仓和喷吹罐均有一套流化装置对粉料进行流化。
3.4喷吹系统一个脱硫工位设一个镁粉喷吹罐和一个石灰粉喷吹罐,一套镁粉和石灰粉在线混合喷吹管路。
一套喷枪装置,一套测温取样装置。
3.5扒渣工艺当喷吹处理完后,倾动铁水罐,然后用扒渣机将脱硫产生的渣扒到渣罐里。
3.6氮气系统氮气系统提供干燥、惰性气体是为以下几个目的:3.6.1料仓和喷吹罐加料操作期间流化储料仓中的粉剂,这将导致粉剂均匀分配输送。
3.6.2喷吹期间流化喷吹罐内的粉剂,这将起到控制喷吹期间粉剂输送的速度和喷吹罐内粉剂均匀分配。
3.6.3为储料仓内粉剂顶部构建气体密封环境。
铁水预处理脱硫工艺的探讨

铁水预脱硫工艺的探讨摘要:本文重点讨论铁水预处理中脱硫工艺的方法及特点,为国内各个钢厂选择合理有效的工艺,提高铁水质量,增加市场竞争力提供重要的参考信息。
关键词:铁水预处理脱硫剂搅拌法喷吹法扒渣1 前言铁水预脱硫工艺是指铁水进入炼钢炉前的脱硫处理,它是铁水预处理中最先发展成熟的工艺。
对于优化钢铁冶金工艺、提高钢的质量、发展优质钢种、提高钢铁冶金综合效益起着重要作用,是不可缺少的工序。
国内昆钢通过铁水预处理脱硫工艺,铁水中的含硫量从110多个降为15个(含硫量0.001%称为1个硫),使钢材的内在质量得到了提升,明显增加了市场竞争力和经济效益。
2 铁水预脱硫的必要性钢的很多性能都受含硫量及其在钢中形成的硫化物夹的杂物理和化学影响,硫化物—硫化锰夹杂在热轧温度下很容易变形,成为延伸性夹杂,引起钢性能各向异性。
除易切削钢外,硫是影响钢质量和性能主要有害元素,影响钢的加工性能和使用性能。
普通钢:特别是连铸坯内部裂纹和表面质量均与[S]有关,要求[S]≤0.02%;低硫钢:结构钢为实现均匀机械性能,减少各相异性,则要求[S]≤0.011%;极低硫钢:石油和天然气输送管线、海上采油平台、厚船板和航空用钢等要求有更好均匀机械性能和更高冲击韧性,而硅钢要求有良好的磁性,薄钢板则要求良好深冲性能等,都要求[S]≤0.005%。
铁水中硫主要来自加入高炉的焦炭、煤粉和矿石等,高炉内脱硫必须通过增加渣量、提高炉渣碱度和炉温来降低铁水硫含量值,高碱度会增加铁水硅含量,消耗额外热量,导致炼钢石灰耗量增加,对炼钢带来一系列问题,同时降低金属收得率。
所以,一般情况下高炉采用低碱度操作,可以显著降低焦比,减少渣量,降低铁水温度和硅含量,使高炉产量增加。
但产出的铁水含硫较高,如果转炉采用高硫铁水冶炼低硫钢,势必采用造碱度渣,并经多次扒渣、再造渣操作,这样势必带来许多不利影响,严重影响钢的质量,降低炉龄,不能把硫降到较低水平。
所以,只有采用低硫铁水炼钢才能提高钢的质量和各项技术经济指标,降低炼钢成本。
RHLF和LFVD工艺生产管线钢洁净度的比较

・54・特殊钢第30卷晕、■缸簟壬墨冶炼流程备工位图3RH—LF(a)和LF・VD(b)流程钢中磷含量Fig.3Avergephosphorou8contentinsteelduringRH—LF(a)andLF-VD(b)process磷含量平均为0.0090%。
RH—LF精炼流程LF吊包时渣碱度平均为3.73,LF—VD过程渣碱度高,出VD时渣碱度平均为9.02,有利于控制合金中带入的磷,连铸时LF.VD工艺比RH—LF工艺磷含量平均低0.001O%,LF-VD过程磷含量控制要优于RH—LF精炼过程。
2.4夹杂物控制管线钢对钢中夹杂物控制要求较高,LF-VD流程中夹杂物在VD处理后期弱搅拌上浮去除;RH-LF工艺流程中RH循环搅拌提高了夹杂物去除的动力学条件,在Lf'流程钙处理有效地促进了夹杂物球化;LF・VD精炼工艺流程钢中夹杂物总量可以控制到2mg/10kg,RH-LF精炼工艺钢中夹杂物总量可以控制到4.5rag/10kg。
RH-LF精炼工艺夹杂物偏高,因为Ⅱ’・VD流程LF、VD能弱搅拌以促进夹杂物上浮,而RH-LF精炼工艺中,LF脱氧生成的夹杂物仅在Ⅱ.流程弱搅拌后就进人连铸工序,上浮去除的时间比LF-VD工艺少了VD处理时间。
图4(a,b)为夹杂物类型分布图,由图4(a,b)中可知,RH—LF和LF-VD工艺钢中夹杂物以钙铝酸盐或钙铝酸盐的复合物为主,RH-LF工艺有部分二氧化硅,LF—VD工艺有部分氧化铝夹杂物。
图4(C,d)为显微夹杂物尺寸分布图,由图4(C,d)中可知,RH-LF夹杂物尺寸主要为5~10岬,而LF—VD工艺显微夹杂物尺寸偏大一些主要集中在5—20岬。
图4RH—LF(a)和LF・VD(b)工艺钢中夹杂物分布;RH.LF(c)和LF-VD(d)工艺钢中夹杂物尺寸分布Fig.4DistributionofinclusionsinsteelrefinedbyRH—LF(a)andLF・VD(b)process;distributionofsizesofinclusioninsteelre-finedbyRH—LF(C)andLF—VD(d)process3结论(1)LF.VD流程控制钢中氮的效果稍优于RH-LF流程,钢中全氧含量均能控制在0.001O%内。
铁水预处理(脱硫)

【本章学习要点】本章学习铁水预处理脱硫的优点,常用脱硫剂种类及其反应特点,脱硫生产指标,KR法脱硫的生产工艺流程和脱硫的基本操作,混铁车喷吹脱硫的工艺特点和工艺操作。
第一节铁水预脱硫的概念和优点铁水预处理,炼钢生产中主要是指铁水在进入转炉之前的脱硫处理。
广义的铁水预处理是指包括对铁水脱硫、脱硅、脱磷的三脱处理,另外还有特殊铁水的预处理,如含V铁水的提V等。
铁水脱硫是二十世纪70年代发展起来的铁水处理工艺技术,它已成为现代钢铁企业优化工艺流程的重要组成部分。
铁水脱硫的主要优点如下:1.铁水中含有大量的硅、碳和锰等还原性的元素,在使用各种脱硫剂时,脱硫剂的烧损少,利用率高,有利于脱硫。
2.铁水中的碳、硅能大大提高铁水中硫的活度系数,改善脱硫的热力学条件,使硫较易脱致较低的水平。
3.铁水中含氧量较低,提高渣铁中硫的分配系数,有利于脱硫。
4.铁水处理温度低,使耐火材料及处理装置的寿命比较高。
5.铁水脱硫的费用低,如在高炉、转炉、炉外精炼装置中脱除一公斤硫,其费用分别是铁水脱硫的2.6、16.9和6.1倍。
6.铁水炉外脱硫的过程中铁水成份的变化,比炼钢或钢水炉外处理过程中钢水成份的变化对最终的钢种成份影响小。
采用铁水脱硫,不仅可以减轻高炉负担,降低焦比,减少渣量和提高生产率,也使转炉也不必为脱硫而采取大渣量高碱度操作,因为在转炉高氧化性炉渣条件下脱硫是相当困难的。
因此铁水脱硫已成为现代钢铁工业优化工艺流程的重要手段,是提高钢质量、扩大品种的主要措施。
早期的铁水脱硫方法有很多种:如将脱硫剂直接加在铁水罐罐底,靠出铁铁流的冲击形成混合而脱硫的铺撒法。
也有将脱硫剂加入装有铁水的铁水罐中,然后将铁水罐偏心旋转或正向反向交换旋转的摇包法。
之后逐步发展至今天采用的KR搅拌法及喷枪插入铁水中的喷吹法。
第二节常用脱硫剂及脱硫指标一、常用脱硫剂经过长期的生产实践,目前选用作为铁水脱硫剂的主要是Ca、Mg、Na等元素的单质或化合物,常用的脱硫剂主要有:Ca系:电石粉(CaC2)、石灰(CaO)、石灰石(CaCO3)等Mg系:金属Mg粉Na系:苏打(Na2CO3)二、常用脱硫剂反应特点1.电石粉碳化钙脱硫反应为用CaC2脱硫有如下特点:1)在高碳系铁水中,CaC2分解出的Ca离子与铁水中的硫有极强的亲和力。
铁水预处理喷吹脱硫过程动力学数值模拟

A Thesis Submitted in Partial Fulfillment of the Requirements forthe Degree of Master of EngineeringNumerical Simulation of Desulfurization Process with Jet Stirring Flows in Hot Metal PretreatmentCandidate : Y ao FengMajor : Fluid MechanicsSupervisor : Prof. Wu JiankangAssociate Prof. Chen HanHuazhong University of Science and TechnologyWuhan 430074, P.R.ChinaFebruary, 2012独创性声明本人声明所呈交的学位论文是我个人在导师指导下进行的研究工作及取得的研究成果。
尽我所知,除文中已经标明引用的内容外,本论文不包含任何其他个人或集体已经发表或撰写过的研究成果。
对本文的研究做出贡献的个人和集体,均已在文中以明确方式标明。
本人完全意识到,本声明的法律结果由本人承担。
学位论文作者签名:日期:年月日学位论文版权使用授权书本学位论文作者完全了解学校有关保留、使用学位论文的规定,即:学校有权保留并向国家有关部门或机构送交论文的复印件和电子版,允许论文被查阅和借阅。
本人授权华中科技大学可以将本学位论文的全部或部分内容编入有关数据库进行检索,可以采用影印、缩印或扫描等复制手段保存和汇编本学位论文。
保密□,在_____年解密后适用本授权书。
本论文属于不保密□。
(请在以上方框内打“√”)学位论文作者签名:指导教师签名:日期:年月日日期:年月日摘要钢材市场竞争越来越激烈,用户对钢材的质量的要求也愈来愈高。
在现在的钢铁冶炼生产中,铁水预处理技术被越来越广泛的应用。
铁水预处理工艺技术操作规程(标准版)
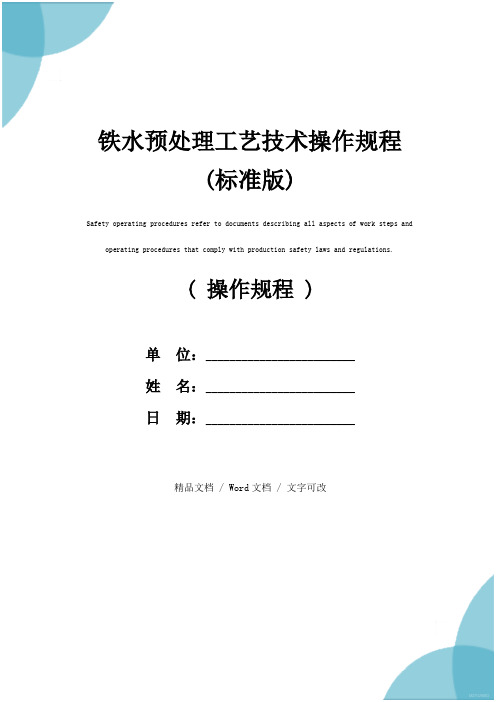
( 操作规程 )单位:_________________________姓名:_________________________日期:_________________________精品文档 / Word文档 / 文字可改铁水预处理工艺技术操作规程(标准版)Safety operating procedures refer to documents describing all aspects of work steps and operating procedures that comply with production safety laws and regulations.铁水预处理工艺技术操作规程(标准版)1.原料要求:1.1铁水条件铁水温度:T≥1300℃、[S]≤0.150%处理铁水量:与转炉铁水装入量相符1.2脱硫剂采用CaO系脱硫剂(因使用的脱硫剂是不一样的。
各有各的特点,配方都有不一样。
这要在实际中来总结。
)1.3脱硫剂加入量范围处理前铁水S含量目标S脱硫剂加入量(Kg/t铁)≤40≤204~4.5 ≤105~5.5 41~50 ≤204.0~5.0 ≤105.0~6.5 51~60 ≤205.0~6.5 ≤106.0~8.0 61~70 ≤206.0~8.0 ≤107.5~9.0 71~80≤207.5~9.0 ≤109.0~10.5 81~90≤209.0~10.5 ≤1010.0~12.5 91~100≤2010.5~11.5≤1012.0~13.5101~110≤2011.5~12.5≤1012.5~13.5>110≤2012.0~14.0≤1013.5~14.5注:(1)视脱硫剂理化指标,可将前[S]减少或提高0.010%。
(2)前[S]≤0.045%时,可将前[S]提高0.004~0.005%。
(3)根据搅拌头状况、铁水带渣量的多少,脱硫剂加入量可适当调整。
铁水炉外预处理脱硫技术

铁水炉外预处理脱硫技术机械搅拌法与吹气搅拌法的经济效益分析1.建设投资机械搅拌法简称KR法,由于设备体积庞大,数量多且复杂,因此基本建设投资是吹气搅拌法的一倍。
如果安装一套吹气搅拌法脱硫设备用500万元,而KR法就要1000万元。
2.占地面积KR法由于要保证搅拌头既能上下升降,又能围绕圆心旋转,还要把特制的石灰粉用专门设备加入铁水罐中。
因此,KR法本体设备占地面积大。
不像吹气搅拌法设备比较灵巧,占地空间小。
吹气搅拌法尤其适合老厂改造采用。
3.脱硫剂KR法使用的脱硫剂是石灰粉。
此法对石灰粉粒度的要求是十分严格的,必须经过专用设备加工而成。
石灰粉不易保存,非常易水化,尤其是在夏季CaO更容易受潮,变成Ca(OH)2。
氢氧化钙易结块,其化学性质与氧化钙有根本的变化,严重影响铁水脱硫效果。
因此,使用KR法脱硫,必须建一座专用的石灰粉供应基地。
包括石灰焙烧窑、破碎机、球磨机、储料仓等。
石灰粉供应基地的建设大约也要900-1000万元。
另外,石灰粉对环境污染也比较厉害。
因此,采用KR法脱硫除尘设备的投入也是相当可观的。
另外,石灰粉的用量大约是钝化镁的10倍。
用钝化颗粒镁脱硫,一般耗量0.4千克/吨铁。
用石灰粉耗量为4千克/吨铁。
如果对50吨铁水进行脱硫处理。
用钝化颗粒镁只需20千克。
而用石灰粉至少需要200千克。
而吹气搅拌法使用的钝化颗粒镁就没有上面提到的,石灰粉易水化而改性的问题。
因为颗粒镁表面被一层钝化膜包覆。
钝化颗粒镁有专业生产厂商供应,十分方便,随用随要,而且易于保存。
4.铁水处理时间KR法铁水脱硫处理时间比较长,是吹气搅拌法铁水脱硫处理时间的3-4倍。
吹气搅拌铁水脱硫反应时间,一般只需5-8分钟。
那么KR法就要20-32分钟。
为什么KR法脱硫反应时间长?主要原因是石灰粉只能加在铁水的表面,由于石灰粉比重轻,很难完全与铁水接触,所以反应速度慢。
脱硫时间长。
另外,脱硫反应是一个吸热反应,铁水温度若偏低,反应速度更慢,脱硫时间会更长。
预处理过程铁水中氮含量的变化

: 喷吹苏打可以脱氮; 喷吹石灰时基本没有
脱氮, 但采用天然气为载气时则会产生脱氮; 喷吹 电石粉也不会脱氮; 而喷吹 (6 ( (+) , 时则会产生 增氮。 ! !-" 转炉冶炼过程钢中增氮的分析 影响钢中氮含量的因素及降低氮含量的工 艺措施 二次精炼真空处理时去氮能力有限, 而 N0 则 会产生一定量的增氮, 因此氮含量的控制主要依 赖转炉吹炼环节。影响转炉氮含量的因素有转炉 尺寸及新旧程度、 喷枪结构、 氧气纯度、 副原料氮 气、 空气中氮气、 渣泡沫化程度、 铁水中氮、 废钢中
[.] 最大限度地减少增氮 。
转炉渣的行为影响着氮在吹炼中的变化和终 点氮含量。转炉渣为高氧化性渣, 吸氮很少。尽 快形成均匀而持久的泡沫渣可以很好地防止钢的 吸氮。吹炼的初期, 氮含量随之降低, 尤其是在氧 枪射流的作用区域。但随脱碳反应的进行, 渣逐 渐返干, 石灰也逐渐溶解, 并进入硅酸二钙或硅酸 三钙析出区域, 会一定程度上破坏泡沫渣引起增 氮。随着渣中氧化铁含量的升高, 通常又会形成 均一的渣相覆盖钢液。从接近吹炼终点时, 脱碳 反应已明显减弱, 又会产生一定的吸氮。研究表 明 , 在吹炼后期, 保持较低的枪位容易得到较低 的钢中氮。 氧气纯度也十分关键, 计算表明 不得超过 &)!" 。 采用不同的冷却材料关系到钢中的氮含量。 与废钢相比, 用铁矿石做冷却材料时钢中的氮含 量要低得多。因为废钢加入钢水后, 其中的氮在 废钢熔化后进入钢水, 而后期钢水中的碳氧反应 已经减弱, 因此废钢加入往往会引起增氮。而加 入矿石时相当于强化了钢水供氧, 对氮的去除是 十分有利的。 氧枪的结构对氮的影响相对复杂, 氧枪的结 构影响以下因素: 炉渣的形成、 搅拌强度和空气的 卷入。相比单孔氧枪, 多孔氧枪可以较快地成渣, 搅拌较均匀, 但氧枪冲击区域的搅拌强度较弱, 也 容易引起空气卷入。 转炉的几何尺寸也对钢中氮含量产生影响, 一般而言, 转炉为瘦长型和转炉炉口直径较小时, 吹炼中渣层厚度相对较高, 空气也比较不容易卷 入转炉引起增氮。在转炉炉役后期, 由于内衬侵 蚀造成炉容比增大, 熔池搅拌相对减弱, 钢中的氮 含量会有所上升。 综上所述, 降低氮含量的主要措施有:
铁水预处理的工艺设计

铁水预处理的工艺设计1、铁水脱硫预处理宜采用喷吹法或机械搅拌法,经预脱硫处理后铁水的硫含量不应高于0.015%,对于生产超低硫钢种用的铁水,硫含量不应高于0.005%。
2、高炉铁水包、鱼雷罐、转炉铁水包均可作为铁水预脱硫的反应容器,宜选用转炉铁水包。
铁水包内铁水面以上自由空间高度,当采用喷吹法时不应小于50 0mm,采用机械搅拌法时不应小于700mm。
3、铁水脱磷预处理应符合下列规定:(1)铁水磷含量高于0.12%,或生产含磷不大于0.005%的超低磷钢种时,应采用铁水包喷吹法、铁水包搅拌法、鱼雷罐喷吹法或转炉炉内预脱磷工艺。
(2)铁水包喷吹法预脱磷时,应采用专用铁水包,铁水面上自由空间高度不应小于1500mm。
处理后的铁水磷含量不应高于0.030%。
(3)铁水包搅拌法预脱磷时,应采用专用铁水包,铁水面上自由空间高度不应小于700mm。
处理后的铁水磷含量不应高于0.040%。
(4)鱼雷罐喷吹法预脱磷时,铁水面上自由空间高度不应小于1000mm。
处理后的铁水磷含量不应高于0.030%。
(5)转炉炉内脱磷预处理后的铁水磷含量不应高于0.030%。
对于超低磷钢种,预处理后铁水磷含量不应高于0.005%。
4、采用转炉炉内脱磷预处理时,加入转炉的废钢比不应大于10%,宜采用轻废钢。
转炉采用氮气进行底吹搅拌,底吹强度不应小于0.2Nm3/(t·min),氮气压力不应小于1.6MPa,每个底吹支路应单独控制。
脱磷转炉宜采用专用氧枪,供氧强度不应大于2.5Nm3/(t·min)。
5、采用铁水包和鱼雷罐内脱磷预处理时,铁水应先进行脱硅预处理,铁水硅含量不应高于0.20%。
6、需要生产超低硫、超低磷钢种的转炉炼钢车间,宜采用铁水三脱(脱硅、脱磷、脱硫)预处理工艺。
7、喷吹法预处理宜采用氮气作为载流气体。
氮气纯度不应低于99.9%,压力不应小于1.0MPa,供气流量应按输送气粉比和供粉强度要求确定。
铁水预处理工艺技术规程

铁水预处理工艺技术规程铁水预脱硫工艺岗位操作规程1、工艺流程铁水纸盒铁水客运车辆测温采样喷粉烟气挖渣测温采样炼钢2、铁水烟气建议序号项目123浅脱硫中脱硫深脱硫成品硫要求温度要求[s]≤0.015%≥1250℃[s]≤0.01%≥1250℃[s]≤0.005%≥1250℃3、脱硫工艺的选择烟气工艺方法的挑选:既能够分别单独DAT160氧化钙粉和熔融颗粒镁,也能够无机DAT160。
4、烟气东站主要技术参数1234567烟气平均值周期每天最小烟气纸盒数年处置能力(每套)喷枪使用寿命钙基脱硫剂耗量铁损耗铁水温再降分钟/手袋/每工位万吨/每工位℃/min≤2840100>100炉次~5kg/t铁3.6kg/t铁≤2-1-5、脱硫操作前的准备5.1、关上烟气东站供电总电源,给有关系统供电。
5.2、检查其它各种能源介质的供给情况,如氮气等,是否符合需要的参数。
5.3、检查擦吹起罐和储料仓中存料情况,如果悬浮物偏少,应及时补足皮德盖。
5.4、检查所有机、电、液设备的状况,是否处于可使用的完好的状况。
5.5、按照杀菌和保护的建议展开工作前的必要的杀菌和保护工作。
5.6、联系铁水准备工作主控室,介绍铁水情况:例如铁水罐号、起始硫值、铁水重量,铁水温度,其他化学成分等。
5.7、铁水准备主控室联系行车指挥人员将铁水罐吊至脱硫站铁水罐车上。
5.8、检查渣盘车及渣盘与否妥当。
5.9、检查除尘系统闸阀的控制器及吸力。
5.10、确认上述工作准备就绪的情况下可以开始脱硫站的处理操作。
6、喷吹脱硫工艺6.1、行车统一指挥人员统一指挥皮德盖180t行车将炼钢厂房内的铁水重罐缠至烟气东站的铁水罐车上,证实铁水罐安全座稳于通告烟气操作方式人员;烟气操作方式人员将铁水罐车上开向烟气工位。
6.2、接受铁水罐后的铁水罐车开向脱硫工位时除尘系统开始启动;6.3、到接近位置时,交流变频调车速到慢速,接触到限位开关停车;3确认渣盘车开到接渣位置。
铁水预处理公式

铁水预处理公式铁水预处理是指在铁水进入转炉或电炉之前,对铁水进行一系列的处理工艺,以提高铁水的质量和适应后续冶炼工艺的要求。
铁水预处理公式是在铁水预处理过程中所使用的化学反应式或物理公式,用于计算和控制铁水中各种元素的含量和性质。
铁水预处理的目的是去除或减少铁水中的杂质,调整铁水中的成分,提高铁水的温度和液态性能,以及改善铁水的流动性。
常用的铁水预处理方法有脱硫、除磷、脱氧、减氧、去除夹杂物等。
脱硫是指将铁水中的硫元素去除的过程。
硫对铁的冶炼性能有不利影响,会导致铁的脆性增加。
常用的脱硫方法有氧化法、碱法和石灰法。
其中,氧化法是指通过在铁水中加入氧化剂,使硫元素氧化为气态的二氧化硫,从而达到脱硫的目的。
除磷是指将铁水中的磷元素去除的过程。
磷对铁的冶炼性能也有不利影响,会导致铁的冷脆性增加。
常用的除磷方法有氧化法、碱法和酸法。
其中,氧化法是指通过在铁水中加入氧化剂,使磷元素氧化为气态的五氧化二磷,从而达到除磷的目的。
脱氧是指将铁水中的氧元素去除的过程。
氧对铁的冶炼性能同样有不利影响,会影响铁的延展性和可塑性。
常用的脱氧方法有硅脱氧、铝脱氧和钛脱氧等。
其中,硅脱氧是指在铁水中加入硅,使氧元素与硅反应生成二氧化硅,从而达到脱氧的目的。
减氧是指将铁水中的氧化铁还原为金属铁的过程。
减氧的目的是减少铁水中的氧含量,提高铁水的纯度。
常用的减氧方法有碳减氧、铝减氧和硅减氧等。
其中,碳减氧是指在铁水中加入适量的碳,使氧化铁与碳反应生成金属铁和一氧化碳,从而达到减氧的目的。
去除夹杂物是指将铁水中的夹杂物去除的过程。
夹杂物对铁的冶炼性能有很大影响,会导致铁的脆性增加。
常用的去除夹杂物的方法有过滤、离心和气泡法等。
其中,过滤是指通过过滤器将铁水中的夹杂物截留下来,从而达到去除夹杂物的目的。
铁水预处理公式是铁水预处理过程中的重要工具,通过使用各种化学反应式和物理公式,可以计算和控制铁水中各种元素的含量和性质,以达到提高铁水质量的目的。
- 1、下载文档前请自行甄别文档内容的完整性,平台不提供额外的编辑、内容补充、找答案等附加服务。
- 2、"仅部分预览"的文档,不可在线预览部分如存在完整性等问题,可反馈申请退款(可完整预览的文档不适用该条件!)。
- 3、如文档侵犯您的权益,请联系客服反馈,我们会尽快为您处理(人工客服工作时间:9:00-18:30)。
第 6卷 第 4期
20 0 7年 l 2月
材
料
与 冶 金No 4
De . Oo c2 7
J u a fMaei sa d Mealry o r lo tra n tl g n l u
铁 水 预 处 理 脱硫 过程 氮 含 量预 测
关键 词 :铁水预处理 ;脱硫 ;B P神经 网络 ;氮含量预测
中 图 分 类 号 :T 1. 8 F 11 1 文献 标 识 码 :A 文 章 编 号 :17 -60 20 )40 5 -5 6 1 2 (0 7 0 -25 6 0
Nir g n c n e t p e i to n ho e a t o e o t n r d c i n i tm t l d s p r z t0 e r a m e t e ul hu i a i n pr t e t n
t r d c e n t g n c n e t fh tmea n d s p u i t n p er ame tb P a i ca e r e w r . o p e itt i o e o t n o t i e u h r a i r t t n y B a f i n u a n t o k h r o l l z o e il l Af rt i i g te n t r sn rd ci n d t ,t e mo e a r d c t e n t g n c ne to o t n t an n h ewok u ig p o u t aa h d lc n p e it h ir e o tn fh t mea i e r o o l d s lh r ain p er a me t h eaie p e it n e r rc n b o t l d u d r2 % , a d t e a s lt e u p u i t r t t n ,t e rl t rd ci ro a e c n r l n e 2 z o e v o oe n h b ou e
Ab t a t s r c :Ac od n o t e p a t a r d cin p o e s o o t r t ar e t d l s e tb ih d c r i g t h r ci lp o u t r c s fh tmea p er t n ,a mo e s l e c o l e n wa a s
P N n , N h- n ,D N u nci, I i i H U Y n E G J WA G S iu O G Y a —h LU L— a ,Z O u u j x
( . col f tlri l n clg a nier gUn esyo ine& T cnlg e ig,B in 00 3 hn 1Sho o a ug a dE o i l g ei i ri f c c Me l c a oc E n n v t se ehooyB in j eig10 8 ,C ia j 2 C l g f tl ryadR sucs nu nvr t o eh o g , a sa 4 0 2 hn ) . o eeo al g n eore ,A hiU ie i f cnly Manhn2 30 ,C ia l Me u sy T o
t e i i a mp r t r i o e o tn ,c r o o tn n h s h r sc n e t a e te ma i m f e c . h nt t i e e au e n t g n c ne t a b n c n e ta d p o p o u o t n v x mu il n e l r h h nu Th e e rt r n ab n c n e tae o e aie e e t n h i o e o tn a o i v f c .Hih e tmp au e a d c r o o tn t fn g t f c ,a d t en t g n c n e t sp st e e e t v r h i g tmp rt r n a b n c n e tae f v r b e t e i iiain e e au e a d c r o o t n a oa l o d n t fc t . r r o Ke r s o t r t ame t e u p ui ain;BP n u a ew r y wo d :h tme a p e r t n ;d s h r t l e l z o e r n t o k; nto e o tn rd c in l i g n c ne t e it r p o
量的预报模型 。利用生产数据对网络进行 训练后 ,可以用于预测铁水 预处理脱 硫后铁 水 中氮 含量 ,
预报相对误差可 以控制在 2 % 以下 ,W [ 2 N]的绝对 误差值控 制在 8×1 % 以内.给各 输人参 量 0 增加扰动后 ,模型计算表明 ,初始温度和初始 [ ,[ ] [ ] 含量 ,四因素影响 最大 ,且温 度 N] C , P 和 [ ]含量为负扰 动 ,[ ]为正扰动 ,说明增加温度和碳 含量 有利 于脱氮. C N
err sblw8×1 % . C a ̄ g h aus fn u prm t s dc clt g terslidctsh t r eo oi 0 h n n e l e pt aa e r a a ua n . h utn i e a t v oi e n l i e a t
彭 军 ,王世俊 r ,董元篪 ,刘丽霞 云 ,周
( .北京科技 大学 1 摘 冶金 与生态工程学院 ,北 京 10 8 ;2 0 0 3 .安徽工业大学 冶金 与资源学院 ,安徽 马鞍 山 2 3 0 ) 40 2
要 :根据铁水预处理的实际生产 工艺 ,利用 B P神经 网络建立 了铁水预处理 脱硫时铁 水 中氮含