第十章 金属基复合材料
[材料科学]金属基复合材料
![[材料科学]金属基复合材料](https://img.taocdn.com/s3/m/bd12e168f121dd36a22d8208.png)
33
三种热等静压工艺
• 先升压后升温:其特点是无需将工作压力 开到最高压力,随着温度升高,气体膨胀, 压力不断升高,直至达到需要压力,适用 于金属包套的工艺制备;
• 先升温后升压:适用于玻璃包套制备复合 材料;
• 同时升温升压:适合于低压成形、装入量 大、保温时间长的工件制备。
34
热等静压工艺优缺点
混合
热压 冷压-烧结
坯或零件
封装除氧
挤压
粉末冶金法的工艺流程
23
粉末冶金法的优缺点
• 粉末冶金复合法的工艺主要优点是:基体金属或合金 的成分可自由选择,基体金属与强化颗粒之间不易发 生反应;可自由选择强化颗粒的种类、尺寸,还可多 种颗粒强化;强化颗粒添加量的范围大;较容易实现 颗粒均匀化。
• 但材料的成本较高,制备大尺寸的零件和坯料有一定 困难,而且粉末混合和防止氧化是工艺的关键,必须 采取有效措施加以控制,以及微细强化颗粒的均匀分 散困难;颗粒与基体的界面不如铸造复合材料等。
密封袋材的设计较困难
(HIP)
温下,高压气体加压烧结
超高压烧结 用超高压装置在高温下加压 可不用烧结助剂
制品尺寸不能过大
(UHP)
烧结
冲击加压烧结 置粉末于容器中,利用机械 短时间内可以烧结
不易控制
(Dina-Pac) 或炸药产生瞬时高温高压
液相烧结 烧结助剂发挥烧结作用
较低温度下可以进行高密度 若液相以玻化状态残留,
19
不连续增强相复合材料的制备工艺
颗粒 晶须 短纤维
铝合金—固态、液态、原位生长、喷射成型法 镁合金—液态法 钛合金—固态、液态法、原位生长法 高温合金—原位生长法 金属间化合物—粉末冶金、原位生长法
金属基复合材料
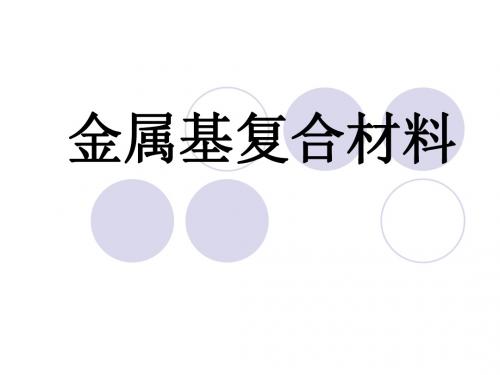
四、挤压铸造法
挤压铸造法是制造金属基复合材料较理 想的途径,此工艺先将增强体制成预成型 体,放入固定模型内预热至一定温度,浇 人金属熔体,将模具压下并加压,迅速冷 却得到所需的复合材料。
挤压铸造法特点:可以制备出增强相非常 高体积分数(40 %~50 %)的金属基复合 材料,由于在高压下凝固,既改善了金属 熔体的浸润性,又消除了气孔等缺陷,因 此,挤压铸造法是制造金属基复合材料质 量较好,可以一次成型。
六、熔体浸渗法
熔体浸渗工艺包括压力浸渗和无压浸渗。 当前是利用惰性气体和机械装置作为压力 媒体将金属熔体浸渗进多气孔的陶瓷预制 块中,可制备体积分数高达50 %的复合材 料,随后采用稀释的方法降低体积分数。
三、原位生成法
原位生成法指增强材料在复合材料制造 过程中,并在基体中自己生成和生长的方 法,增强材料以共晶的形式从基体中凝固 析出,也可与加入的相应元素发生反应、 或者合金熔体中的某种组分与加入的元素 或化合物之间的反应生成。前者得到定向 凝固共晶复合材料,后者得到反应自生成 复合材料。
原位生成复合材料的特点:增强体是 从金属基体中原位形核、长大的热力学稳 定相,因此,增强体表面无污染,界面结 合强度高。而且,原位反应产生的增强相 颗粒尺寸细小、分布均匀,基体与增强材 料间相容性好,界面润湿性好,不生成有 害的反应物,不须对增强体进行合成、预 处理和加入等工序,因此,采用该技术制 备的复合材料的综合性能比较高,生产工 艺简单,成本较低。
一、搅拌铸造法
搅拌铸造法制备金属基复合材料起源于 1968年,由S.Ray在熔化的铝液中加入氧化 铝,并通过搅拌含有陶瓷粉末的熔化状态 的铝合金而来的。
搅拌铸造法的特点是:工艺简单,操作 方便,可以生产大体积的复合材料(可到 达500 kg),设备投入少,生产成本低, 适宜大规模生产。但加入的增强相体积分 数受到制,一般不超过20 %,并且搅拌后 产生的负压使复合材料很容易吸气而形成 气孔,同时增强颗粒与基体合金的密度不 同易造成颗粒沉积和微细颗粒的团聚等现 象。
金属基复合材料

Metal-Matrix
发展方向
1、大力研究发展颗粒增强的铝基、镁基复合材料。
• 国际ALCON公司已建成年产1.1万吨颗粒增强铝基复合材 料型材、棒材、锻材、铸锭以及零件的专业工厂。生产的 SiCp/Al(Mg)锭块单重达596公斤。
2、高温金属基复合材料的研究
Metal-Matrix
缺点
1、金属基复合材料在基体屈服以前的一个较小范围内,应力应变关系才 是线性的。除非采用很硬的基体,否则在拐点以上,金属基复合材料的 有效弹性模量就不再明显大于树脂基复合材料。 一般来说,树脂基复合材料在纤维方向具有很好的线性弹性,具有很高 的比强度和比刚度。这是金属基复合材料所不及的。 2、剪切强度和层间拉伸强度较低 与金属基体材料相比,金属基复合材料的面内剪切强度、层间剪切强度、 横向拉仲强度和层间拉仲强度都比较低。与纤维方向金属基复合材料的 拉、压强度比就更低。但与树脂基复合材料的这些性能比,又强得多。 提高界面的结合强度,可提高这些性能,但冲击强度下降。 3、在抵抗某些环境腐蚀方面,金属基复合材料不如树脂基复合材料。 4、在金属基复合材料制造过程中,涉及到高温、增强材料的表面处理、 复合成型等复杂工艺。因此,金属基复合材料很难制造、成本很高。 5、金属基复合材料密度较大。 6、由于金属基复合材料的研究起步较晚,再加上实际应用范围和制造成 本等因素的影响,目前金属基复合材料的技术水平落后于聚合物基复合 材料和陶瓷基复合材料。
应用
3、电子材料工业 • 电子材料工业,特别是近年来蓬勃发展的微电子工业,对材料有较高的使用
要求。SiC颗粒增强铝基复合材料,可通过调节SiC颗粒的含量使其热膨胀系 数于与基材匹配,并且具有导热性好、尺寸稳定性优良、低密度、适合钎焊 等性能。用它代替钢/钼基座,可以改善微电子器件的性能。 • 硼/铝复合材料用作多层半导体芯片的支座,是一种很好的散热冷却材料,由 于这种材料导热性好、热膨胀系数与半导体芯片非常接近,故能大大减少接 头处的热疲劳。 • 石墨纤维增强铜基复合材料的强度和模量比铜高,又保持了铜的优异的导电 和导热性能。通过调节复合材料中石墨纤维的含量及排布方向,可使其热膨 胀系数非常接近任何一种半导体材料,因此被用来制造大规模集成电路的底 板和半导体装置的支持电板,防止了底板的翘曲和半导体基片上裂纹的产生, 提高器件稳定性。 • 在大型蓄电池中的铅电极自重大、刚性差,容易翘曲引起短路,影响电解过 程的正常进行。用碳纤维增强铅的复合材料,既保持原来优良的电化学性能, 又使强度和模量提高,不易翘曲,同时减小蓄电池的体积。
金属基复合材料
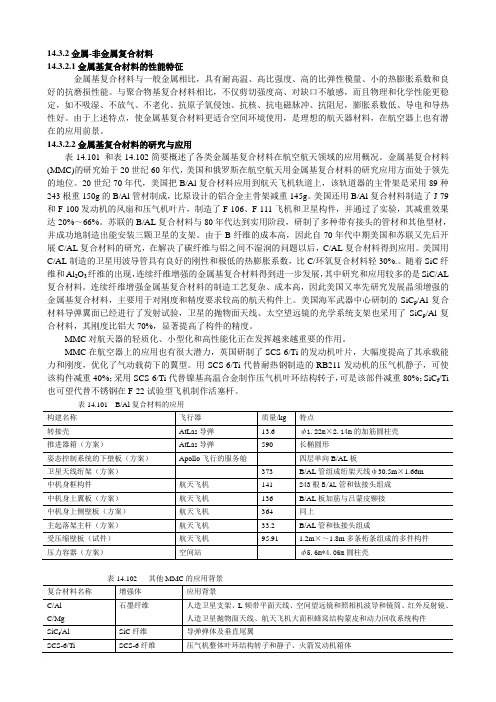
14.3.2金属-非金属复合材料14.3.2.1金属基复合材料的性能特征金属基复合材料与一般金属相比,具有耐高温、高比强度、高的比弹性模量、小的热膨胀系数和良好的抗磨损性能。
与聚合物基复合材料相比,不仅剪切强度高、对缺口不敏感,而且物理和化学性能更稳定,如不吸湿、不放气、不老化、抗原子氧侵蚀、抗核、抗电磁脉冲、抗阻尼,膨胀系数低、导电和导热性好。
由于上述特点,使金属基复合材料更适合空间环境使用,是理想的航天器材料,在航空器上也有潜在的应用前景。
14.3.2.2金属基复合材料的研究与应用表14.101 和表14.102简要概述了各类金属基复合材料在航空航天领域的应用概况。
金属基复合材料(MMC)的研究始于20世纪60年代,美国和俄罗斯在航空航天用金属基复合材料的研究应用方面处于领先的地位。
20世纪70年代,美国把B/Al复合材料应用到航天飞机轨道上,该轨道器的主骨架是采用89种243根重150g的B/Al管材制成,比原设计的铝合金主骨架减重145g。
美国还用B/Al复合材料制造了J-79和F-100发动机的风扇和压气机叶片,制造了F-106、F-111飞机和卫星构件,并通过了实验,其减重效果达20%~66%。
苏联的B/AL复合材料与80年代达到实用阶段,研制了多种带有接头的管材和其他型材,并成功地制造出能安装三颗卫星的支架。
由于B纤维的成本高,因此自70年代中期美国和苏联又先后开展C/AL复合材料的研究,在解决了碳纤维与铝之间不湿润的问题以后,C/AL复合材料得到应用。
美国用C/AL制造的卫星用波导管具有良好的刚性和极低的热膨胀系数,比C/环氧复合材料轻30%.。
随着SiC纤维和Al2O3纤维的出现,连续纤维增强的金属基复合材料得到进一步发展,其中研究和应用较多的是SiC/AL 复合材料。
连续纤维增强金属基复合材料的制造工艺复杂、成本高,因此美国又率先研究发展晶须增强的金属基复合材料,主要用于对刚度和精度要求较高的航天构件上。
金属基复合材料
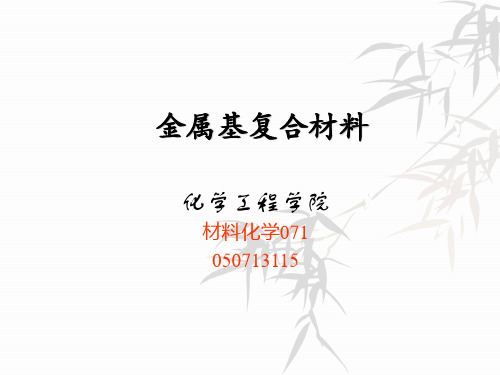
铝的基本特点:熔点660℃ ,密度 2.7g/cm3
具有面心立方结构.所以其塑性优异,适 合各种形式的冷、热加工 导电、导热性能好,约为铜的60%左右 化学活性高,在大气中铝表面与氧形成一 层薄而又致密的氧化铝膜,防止铝继续氧 化 强度低
1.颗粒增强铝基复合材料
颗粒(晶须)增强铝基复合材料的制备 方法可用固态法也可用液态法。
2)界面的形成及机制,界面产物的控制及界面设计; 3)增强剂在基体中的均匀分布: 在选择制备方法时,应选择那些使得增强剂更均匀、均质排 布(分布)的方法。在这方面,液态法与固态法相比较差。 4)制备工艺方法及参数的选择和优化; 5)制备成本的控制和降低,工业化应用的前景。
金属基复合材料制备工艺的分类:
金属基复合材料制备工艺的分类: 1)固态法:真空热压扩散结合、超塑性 成型 / 扩散结合、模压、热等静压、粉末 冶金法。 2)液态法:液态浸渗、真空压铸、反压 铸造、半固态铸造。 3)喷射成型法:等离子喷涂成型、喷射 成型。 4)原位生长法。
固态法 主要为扩散结合和粉末治金两种方法。
扩散结合(Diffusion Bonding)
在制造铝基复合材料时,通常并不是使用纯铝而是用 各种铝合金。这主要是由于与纯铝相比,铝合金具有更好 的综合性能。至于选择何种铝合金做基体,则根据实际中 对复合材料的性能需要来决定。
在制造铝基复合材料时,通常并不是使 用纯铝而是用各种铝合金。
这主要是由于与纯铝相比,铝合金具有 更好的综合性能。至于选择何种铝合金做 基体,则根据实际中对复合材料的性能需 要来决定。
典型金属基复合材料性能与应用
5.2 金属基复合材料的制造工艺
1 金属基复合材料制备工艺概述 1 - 1 金属基复合材料制备工艺的研究内容以及选择原则:
金属基复合材料
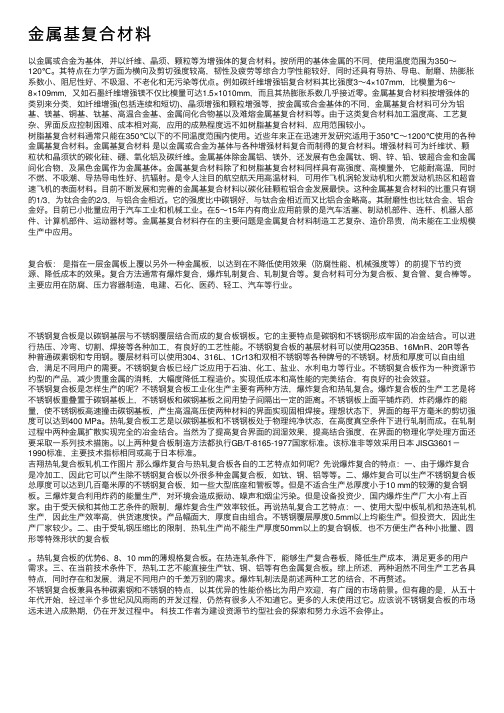
⾦属基复合材料以⾦属或合⾦为基体,并以纤维、晶须、颗粒等为增强体的复合材料。
按所⽤的基体⾦属的不同,使⽤温度范围为350~120℃。
其特点在⼒学⽅⾯为横向及剪切强度较⾼,韧性及疲劳等综合⼒学性能较好,同时还具有导热、导电、耐磨、热膨胀系数⼩、阻尼性好、不吸湿、不⽼化和⽆污染等优点。
例如碳纤维增强铝复合材料其⽐强度3~4×107mm,⽐模量为6~8×109mm,⼜如⽯墨纤维增强镁不仅⽐模量可达1.5×1010mm,⽽且其热膨胀系数⼏乎接近零。
⾦属基复合材料按增强体的类别来分类,如纤维增强(包括连续和短切)、晶须增强和颗粒增强等,按⾦属或合⾦基体的不同,⾦属基复合材料可分为铝基、镁基、铜基、钛基、⾼温合⾦基、⾦属间化合物基以及难熔⾦属基复合材料等。
由于这类复合材料加⼯温度⾼、⼯艺复杂、界⾯反应控制困难、成本相对⾼,应⽤的成熟程度远不如树脂基复合材料,应⽤范围较⼩。
树脂基复合材料通常只能在350℃以下的不同温度范围内使⽤。
近些年来正在迅速开发研究适⽤于350℃~1200℃使⽤的各种⾦属基复合材料。
⾦属基复合材料是以⾦属或合⾦为基体与各种增强材料复合⽽制得的复合材料。
增强材料可为纤维状、颗粒状和晶须状的碳化硅、硼、氧化铝及碳纤维。
⾦属基体除⾦属铝、镁外,还发展有⾊⾦属钛、铜、锌、铅、铍超合⾦和⾦属间化合物,及⿊⾊⾦属作为⾦属基体。
⾦属基复合材料除了和树脂基复合材料同样具有⾼强度、⾼模量外,它能耐⾼温,同时不燃、不吸潮、导热导电性好、抗辐射。
是令⼈注⽬的航空航天⽤⾼温材料,可⽤作飞机涡轮发动机和⽕箭发动机热区和超⾳速飞机的表⾯材料。
⽬前不断发展和完善的⾦属基复合材料以碳化硅颗粒铝合⾦发展最快。
这种⾦属基复合材料的⽐重只有钢的1/3,为钛合⾦的2/3,与铝合⾦相近。
它的强度⽐中碳钢好,与钛合⾦相近⽽⼜⽐铝合⾦略⾼。
其耐磨性也⽐钛合⾦、铝合⾦好。
⽬前已⼩批量应⽤于汽车⼯业和机械⼯业。
金属基复合材料概述
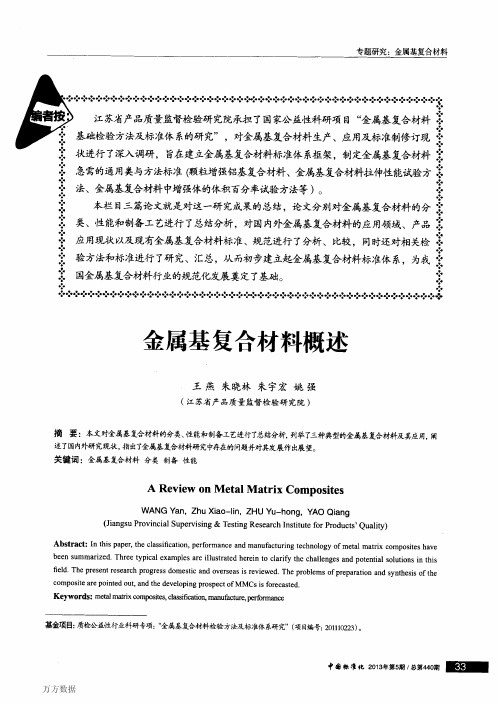
Si、Al—cu和Al—Fe等体系。增强体主要有Sic颗粒、 A1203颗粒、Bc4颗粒、TiC颗粒等。其中采用SiC颗 粒增强的铝基复合材料具有性能高、价格低、密度 小等优点,是目前应用最广泛的铝基复合材料,在 国外已经实现规模化生产。美国DwA公司用SiC颗 粒增强6092铝基复合材料代替铝合金制造F—16战 斗机的垂直尾翼,提高寿命17倍。Eurocopter公司已
按照基体和增强体的不同,金属基复合材料可 按照如下分类。 按基体材料分为:黑色金属基(钢、铁)、有色 金属基(铝基、锌基、镁基、铜基、钛基、镍基)、耐 热金属基、金属间化合物基复合材料等。目前铝基、 镁基、钛基复合材料发展较为成熟,已逐步应用于 航空航天、电子、汽车等工业领域。 按增强体分为:连续纤维增强金属基复合材料; 非连续增强金属基复合材料(颗粒、短纤维、晶须增 强金属基复合材料);混杂增强金属复合材料、层板金 属基复合材料;自生增强金属基复合材料(包括反应、 定向凝固、大变形等途径自生颗粒、晶须、纤维状增 强体)等。其中,自生复合材料的增强相在热力学上 是稳定的,界面结合强度高,而且增强体的尺寸和体 积分数可以通过工艺参数控制,是目前研究的热点。
Hale Waihona Puke 在金属基体中加入适量的高强度、高模量、低 密度的纤维、晶须及颗粒等增强体,可显著提高 复合材料的比强度和比模量。如:碳纤维密度只有
1.85咖m3,最高强度可达7,oooMPa,比铝合金强度
高出10倍以上。石墨纤维的最高模量可达900GPa, 比普通钢材要高4倍以上,而B纤维、Sic颗粒的密度
2金属基复合材料的分类
4典型的金属基复合材料
4.1铝基复合材料 铝及铝合金具有密度低、塑韧性好、导热导电 性较好等优点,但其熔点低、耐磨性差的缺陷限制 了其在更广范围和更高领域的应用。而铝基复合材 料通过增强相的加入使之具有高比强度、高比刚度、 耐磨性好、尺寸稳定性好以及易于加工等一系列优 良特性,在航空航天、汽车、电子等工业领域具有十 分广泛的应用前景。 铝基复合材料常用的基体有Al—M
金属基复合材料
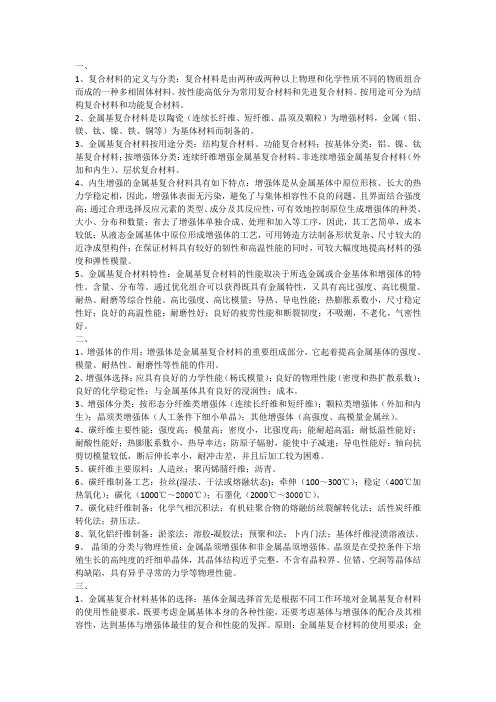
一、1、复合材料的定义与分类:复合材料是由两种或两种以上物理和化学性质不同的物质组合而成的一种多相固体材料。
按性能高低分为常用复合材料和先进复合材料。
按用途可分为结构复合材料和功能复合材料。
2、金属基复合材料是以陶瓷(连续长纤维、短纤维、晶须及颗粒)为增强材料,金属(铝、镁、钛、镍、铁、铜等)为基体材料而制备的。
3、金属基复合材料按用途分类:结构复合材料、功能复合材料;按基体分类:铝、镍、钛基复合材料;按增强体分类:连续纤维增强金属基复合材料、非连续增强金属基复合材料(外加和内生)、层状复合材料。
4、内生增强的金属基复合材料具有如下特点:增强体是从金属基体中原位形核、长大的热力学稳定相,因此,增强体表面无污染,避免了与集体相容性不良的问题,且界面结合强度高;通过合理选择反应元素的类型、成分及其反应性,可有效地控制原位生成增强体的种类、大小、分布和数量;省去了增强体单独合成、处理和加入等工序,因此,其工艺简单,成本较低;从液态金属基体中原位形成增强体的工艺,可用铸造方法制备形状复杂、尺寸较大的近净成型构件;在保证材料具有较好的韧性和高温性能的同时,可较大幅度地提高材料的强度和弹性模量。
5、金属基复合材料特性:金属基复合材料的性能取决于所选金属或合金基体和增强体的特性、含量、分布等。
通过优化组合可以获得既具有金属特性,又具有高比强度、高比模量、耐热、耐磨等综合性能。
高比强度、高比模量;导热、导电性能;热膨胀系数小,尺寸稳定性好;良好的高温性能;耐磨性好;良好的疲劳性能和断裂韧度;不吸潮,不老化,气密性好。
二、1、增强体的作用:增强体是金属基复合材料的重要组成部分,它起着提高金属基体的强度、模量、耐热性、耐磨性等性能的作用。
2、增强体选择:应具有良好的力学性能(杨氏模量);良好的物理性能(密度和热扩散系数);良好的化学稳定性;与金属基体具有良好的浸润性;成本。
3、增强体分类:按形态分纤维类增强体(连续长纤维和短纤维);颗粒类增强体(外加和内生);晶须类增强体(人工条件下细小单晶);其他增强体(高强度、高模量金属丝)。
金属基复合材料

金属基复合材料
金属基复合材料是一种由金属基体和其他非金属材料(如陶瓷、碳纤维等)组
成的复合材料。
它具有金属的高强度、刚性和导热性,同时又具有非金属材料的轻量化和耐腐蚀性能。
金属基复合材料在航空航天、汽车制造、电子设备等领域有着广泛的应用。
首先,金属基复合材料的制备方法有多种,其中包括粉末冶金法、热压法、热
处理法等。
粉末冶金法是将金属粉末与非金属粉末混合后,通过压制和烧结得到复合材料。
热压法是将金属基体和非金属材料层叠在一起,然后通过高温和高压进行热压,使两者紧密结合。
热处理法则是将金属基体与非金属材料进行热处理,使其在高温下发生化学反应,形成复合材料。
其次,金属基复合材料具有优异的性能。
首先,它具有高强度和高刚性,能够
承受较大的载荷,因此在航空航天领域得到广泛应用。
其次,金属基复合材料具有良好的导热性和导电性,能够有效地传递热量和电流,因此在电子设备中有着重要的作用。
此外,金属基复合材料还具有耐磨损、耐腐蚀等特性,能够在恶劣环境下长期稳定运行。
最后,金属基复合材料的发展前景广阔。
随着科技的不断进步,金属基复合材
料的制备工艺和性能将不断得到提升,其应用领域也将不断扩大。
未来,金属基复合材料有望在汽车制造、建筑领域等方面发挥更加重要的作用,为人类社会的发展做出更大的贡献。
综上所述,金属基复合材料具有制备方法多样、优异的性能和广阔的发展前景。
它在现代工业中有着重要的地位,为各个领域的发展提供了重要支撑。
相信随着科技的不断进步,金属基复合材料将会迎来更加美好的未来。
金属基复合材料
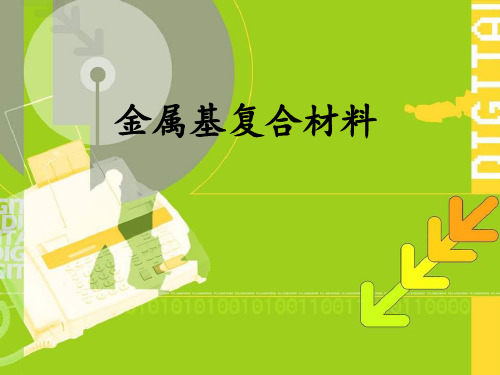
扩散结合的工艺过程
扩散结合工艺中,增强纤维与基体的结合主要分为三个关键
步骤:①纤维的排布;②复合材料的叠合和真空封装;③热压。 a)金属箔复合法 b)金属无纬带重叠法 c)表面镀有金属的纤维结合法
扩散结合的特点
采用扩散结合方式制备金属基复合材料,工艺相对复 杂,工艺参数控制要求严格,纤维排布、叠合以及封装 手工操作多,成本高。 但扩散结合是连续纤维增强并能按照铺层要求排布的 唯一可行的工艺。
3、金属基复合材料的界面优化及界面设计
改善增强剂与基体的润湿性以及控制界面反应
的速度和反应产物的数量,防止严重危害复合材料 性能的界面或界面层的产生,进一步进行复合材料 的界面设计,是金属基复合材料界面研究的重要内 容。
从界面优化的观点来看,增强剂与基体在润湿
后又能发生适当的界面反应,达到化学结合,有利 于增强界面结合,提高复合材料的性能。
界面优化以及界面设计一般有以下几种途径:
增强剂的表面改性处理 (1)改善增强剂的力学性能(保护层);
(2)改善增强剂与基体的润湿性和粘着性(润湿层);
(3)防止增强剂与基体之间的扩散、渗透和反应(阻挡 层); (4)减缓增强剂与基体之间因弹性模量、热膨胀系数 等的不同以及热应力集中等因素所造成的物理相容性 差的现象(过渡层、匹配层)。 常用的增强材料的表面(涂层)处理方法有:PVD、 CVD、电化学、溶胶-凝胶法等。 23
机械“锚固”力结合。
(2)浸润与溶解结合:第二类界面。如相互溶解严重,也可 能发生溶解后析出现象,严重损伤增强剂,降低复合材料的 性能。如采用熔浸法制备钨丝增强镍基高温合金复合材料以 及碳纤维/镍基复合材料在600C下碳在镍中先溶解后析出的 现象等。 (3)化学反应结合:第三类界面。大多数金属基复合材料 的基体与增强相之间的界面处存在着化学势梯度。只要存在 着有利的动力学条件,就可能发生相互扩散和化学反应。
金属基复合材料

图4-5 挤压铸造成型工艺流程
4.3.2.2 真空吸铸成型
成型方法:在铸型内形成一定负压条件,使液 态金属或颗粒增强金属基复合材料自下而上吸 入型腔增强材料预制件缝隙中制备复合材料部 件。真空度0.06~0.08MPa。
优点:制品无气孔、疏松和缩孔等缺陷,组织 致密,工艺参数易于控制,适合于各种增强材 料和形状复杂零部件的制造。
4.3.3 原位复合法 在一定条件下,通过元素与化合物之间的化学 反应,在金属基体内原位生成一种或几种高硬 度、高弹性模量的陶瓷增强相,从而达到强化 金属基体的目的。 4.3.3.1 定向凝固法 将某种共晶成分的合金原料在真空或惰性气氛 中通过感应加热熔化,通过控制冷却方向,进 行定向凝固,在基体中生长出排列整齐的条状 或层状共晶增强材料。其中连续相为基体,条 状或片状的分散相为增强体。主要作为高温结 构材料,用于发动机或涡轮叶片用三元共晶合 金Al-Ni-Nb,形成α相和β相的Ni3Al和Ni3Nb。 特点:增强体不是预先放置,而是在基体内部 就地生成与生长,具有优良的高温力学性能。 但可用的系统有限。
Al2O3短纤维体积 分数/%
屈服强度σb/MPa
断裂伸长率δ/%
0
230
15.0
8
266
5.0
15
297
4.0
20
321
3.0
表4-4 SiCw/Al复合材料和铝合金(6061T6)的力学性能
力学性能 拉伸强度/MPa 屈服强度/MPa 弹性模量/GPa 切变模量/GPa
泊松比 密度/g·cm-3
图4-3 热压扩散工艺过程示意图
图4-4 纤维表面包覆金属粉末的热压扩散 结合法
金属基复合材料
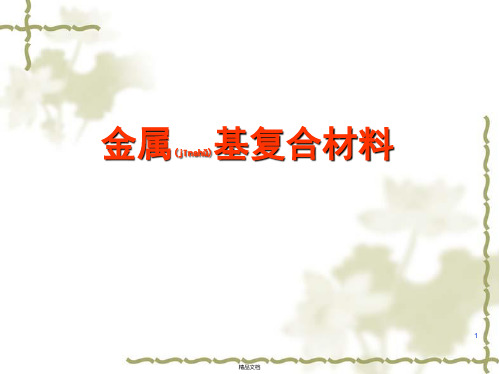
塑性优异,适用各种形式的冷、热加工;
导电、导热性能好,代替铜制作导线;
27
精品文档
搅拌铸造(zhùzào)颗粒增强金属基复合材料
28
精品文档
高能 超声法 (gāonéng)
➢ 利用超声波在铝合金熔体中产生的声空化效应和声流效应所引 起的力学效应中的搅拌、分散、除气等来促使颗粒混入铝合金 熔体,改善颗粒与熔体间的润湿性,迫使颗粒在熔体中均匀分 散。
➢ 是高效的复合方法(fāngfǎ),能在极短时间内实现颗粒在基 体中的润湿和分散,并能除气、除渣,是一种工艺简单、 成本低廉的制备方法(fāngfǎ)。
15
精品文档
热等静压法
➢热等静压法也是热压的一种,可用于制造形状复杂的金属基复 合材料零件。 ➢热等静压法用惰性气体加压,工件在各个方向上受到均匀压 力的作用。在高压容器内设置(shèzhì)加热器,将金属基体与增 强材料按一定比例混合或排布后,或将预制片叠层后放入金 属包套中,抽气密封后装入热等静压装置中加热、加压,复 合成金属基复合材料。
需形状的复合材料构件毛坯。
21
精品文档
粉末冶金 法的缺点 (fěn mò yě jīn)
①工艺过程比较复杂; ②金属基体必须制成粉末,增如了工艺的复杂性和成 本; ③在制备铝基、镁基复合材料时,还要防止粉末引 起(yǐnqǐ)的爆炸。
22
精品文档
液态 法 (yètài)
➢ 也称熔铸法,是指金属基复合材料在制造过程中,金属基体处于熔融
金属基复合材料
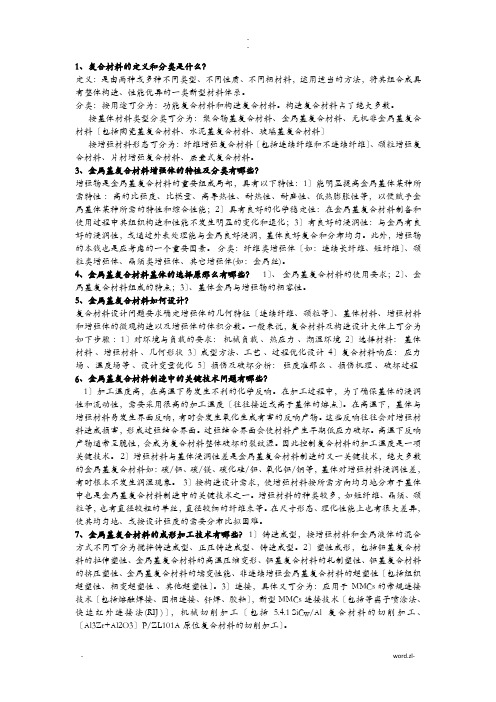
1、复合材料的定义和分类是什么?定义:是由两种或多种不同类型、不同性质、不同相材料,运用适当的方法,将其组合成具有整体构造、性能优异的一类新型材料体系。
分类:按用途可分为:功能复合材料和构造复合材料。
构造复合材料占了绝大多数。
按基体材料类型分类可分为:聚合物基复合材料、金属基复合材料、无机非金属基复合材料〔包括陶瓷基复合材料、水泥基复合材料、玻璃基复合材料〕按增强材料形态可分为:纤维增强复合材料〔包括连续纤维和不连续纤维〕、颗粒增强复合材料、片材增强复合材料、层叠式复合材料。
3、金属基复合材料增强体的特性及分类有哪些?增强物是金属基复合材料的重要组成局部,具有以下特性:1〕能明显提高金属基体某种所需特性:高的比强度、比模量、高导热性、耐热性、耐磨性、低热膨胀性等,以便赋予金属基体某种所需的特性和综合性能;2〕具有良好的化学稳定性:在金属基复合材料制备和使用过程中其组织构造和性能不发生明显的变化和退化;3〕有良好的浸润性:与金属有良好的浸润性,或通过外表处理能与金属良好浸润,基体良好复合和分布均匀。
此外,增强物的本钱也是应考虑的一个重要因素。
分类:纤维类增强体〔如:连续长纤维、短纤维〕、颗粒类增强体、晶须类增强体、其它增强体(如:金属丝)。
4、金属基复合材料基体的选择原那么有哪些? 1〕、金属基复合材料的使用要求;2〕、金属基复合材料组成的特点;3〕、基体金属与增强物的相容性。
5、金属基复合材料如何设计?复合材料设计问题要求确定增强体的几何特征〔连续纤维、颗粒等〕、基体材料、增强材料和增强体的微观构造以及增强体的体积分数。
一般来说,复合材料及构造设计大体上可分为如下步骤:1〕对环境与负载的要求:机械负载、热应力、潮湿环境 2〕选择材料:基体材料、增强材料、几何形状 3〕成型方法、工艺、过程优化设计 4〕复合材料响应:应力场、温度场等、设计变量优化 5〕损伤及破坏分析:强度准那么、损伤机理、破坏过程6、金属基复合材料制造中的关键技术问题有哪些?1〕加工温度高,在高温下易发生不利的化学反响。
金属基复合材料概述

金属基复合材料的分类:按基体分:黑色金属基、有色金属基按增强体分:连续纤维增强金属基复合材料、非连续金属基复合材料(颗粒、短纤维、晶须);混合增强、层板增强、自生增强金属基复合材料。
金属基复合材料的性能特点:力学性能:金属具有良好的塑形和韧性,加入适量的高强度、高模量、低密度的增强体,可显著提高复合材料的比强度和比模量。
导热、导电性能好,热膨胀系数小、尺寸稳定性好。
耐磨性好。
良好的高温性能良好的断裂韧性和抗疲劳性能(取决于增强体与金属基体的界面结合情况)。
制备方法:2.1、原位自生法2.2、粉末冶金法2.3、喷射沉积法2.4、搅拌铸造法2.5、挤压铸造法一.内生增强的金属基复材的特点.答:1.增强体试从金属体中原位形核、长大的热力学稳定相,因此,增强体表面无污染,避免了与基体相容性不良的问题,且界面结合强度高。
2.通过合理选择反应元素(或化合物)的类型、成分及其反应性,可有效地控制原位生成增强体的种类、大小、分布和数量。
3.省去了增强体单位合成、处理和加入等工序,因此其工艺简单,成本较低。
4.从液态金属基体中原位形成增强体的工艺,可用铸造方法制备形状复杂、尺寸较大的近净成形构件。
5.在保证材料具有较好的韧性和高温性能的同时,可较大程度地提高材料的强度和弹性模量。
补:外加增强的金属基复材的特点:1.颗粒表面有污染;2.界面结合差;3.润湿性。
二.金属基复材的特点. 答:1.高比强度、高比模量;2.导热、导电性能;3.热膨胀系数小,尺寸稳定性好;4.良好的高温性能;5.耐磨性好;6.良好的疲劳性能和断裂韧度;7.不吸潮,不老化,气密性好。
三增强体的作用.答:传递作用承受力,提高金属基体的强度、模量、耐热性、耐磨性等性能。
四.金属基复材增强体应有的基本特性答:1.增强体具有能明显提高金属基体某种所需特性的性能;2.增强体应具有良好的化学稳定性;3.与金属有良好的浸润性。
五选择增强体的原则. 答:1.力学性能:杨氏模量和塑性强度;2.物理性能:密度和热扩散系数;3.几何性:形貌和尺寸;4.物理化学相容性;5.成本因素。
- 1、下载文档前请自行甄别文档内容的完整性,平台不提供额外的编辑、内容补充、找答案等附加服务。
- 2、"仅部分预览"的文档,不可在线预览部分如存在完整性等问题,可反馈申请退款(可完整预览的文档不适用该条件!)。
- 3、如文档侵犯您的权益,请联系客服反馈,我们会尽快为您处理(人工客服工作时间:9:00-18:30)。
汽车发动机 工作温度较高 气体腐蚀、耐磨、导热 工作温度450℃以下的
高温强度、抗
铝合金、镁合金
工作温度450~650℃ 不锈钢
工作温度800℃以上的 合金
更耐热的钛合金、
铁基和镍基耐热
(2)针对增强体类型 连续纤维增强型:纤维具有高强度和高模量, 连续纤维是主要承载体,基体应有良好的 塑性和纤维相容性。一般采用纯铝或低合 金防锈铝合金作基体。 非连续增强型:金属基体是主要承载体,基 体强度对材料有决定性影响,一般选择高 强度铝合金作基体。
玻璃纤维 :
• 较高的强度,相对密度小,化学稳定性高, 耐热性好,价格低 。 • 缺点是脆性较大,耐磨性差,纤维表面光 滑而不易与其它物质结合。 • 玻璃纤维可制成长纤维和短纤维,也可以 织成布,制成毡。 其它纤维:氧化铝纤维、天然纤维、高分子 纤维
(2)晶须 • 晶须:直径只有0.2~1.0微米的针状单晶体, 长度约几十微米。 • 晶体缺陷很少,强度接近完整晶体的理论 值,可明显提高复合材料的强度和弹性模 量。 • 晶须包括金属晶须和陶瓷晶须。陶瓷晶须 比金属晶须强度高,相对密度低,弹性模 量高,耐热性好。
2.增强体材料 连续长纤维、短纤维、晶须、颗粒 作用:提高材料强度、模量、高温强度、 耐磨性 性能要求:增强体应具有高比强度、高模 量、高温强度、高硬度、低热膨胀,良好 的化学稳定性、浸润性、相容性,无严重 的不良界面反应。 配合基体,增强性能
(1)连续纤维 沿轴向有很高的强度和弹性模量。长度较长, 直径范围:5.6~14μm(束丝),95~140 μm(单丝)。
• 短纤维的增强作用不如连续纤维有效,因 此短纤维的f’比连续纤维的高。
3.颗粒增强金属基复合材料的强度 • 强化机制是弥散强化 • 复合材料破坏从颗粒界面开始,表现为界 面破坏或颗粒脱落
• 切应力导致颗粒破坏,引起材料变型
第三节 金属基复合材料界面、强化、断裂 1.金属基复合材料界面
界面位于基体与增强之间,起传递载荷的 作用。 金属基复合材料在制作或使用过程中,需 要控制界面的化学反应,以获得适宜的界 面粘结强度。
• 纤维和基体的热膨胀系数应相适应。 • 纤维所占的体积百分比必须大于一定的体 积含有率。 • 不连续短纤维必须大于一定的长度。
(2)强余热应 力都会产生位错。 如果增强体与金属基体间的错配应变由放 出位错环来松弛,就会产生强化作用。
错配应变:增强体的自然形状与它在金属 基体中所占空穴的形状间的差别。
3.金属基复合材料的断裂
(1)连续长纤维金属基复合材料的断裂
• 金属基体的韧性比纤维高很多,因此基体 的失效应变大于纤维的时效应变 • 复合材料的断裂主要是由连续纤维断裂所 引起
(2)不连续金属基复合材料的断裂 • 短纤维(晶须)很少开裂 • 大尺寸颗粒才会开裂,尺寸>20μm • 基体内孔洞的形成和连接是不连续金属基 复合材料断裂的主要机制。
镁基复合材料的界面反应 • 低温镁与碳不起反应 • 镁与碳化硅一般不反应 • 镁与氧反应强烈,生成MgO或 MgO•Al2O3尖晶石
钛基复合材料的界面反应 • 钛和硼反应生成TiB2,从室温到高温都稳 定。 • 钛及钛合金很容易与大部分增强体反应, 但不同体系的反应速度有显著差异 • 增强体是SiC时,产生明显的界面反应。 对性能有害。
• TiB2-Ti的反应速率明显比SiC-Ti的反应速 率慢。B4C-Ti的反应速率处于两者之间。
2.金属基复合材料的强化 (1)影响强化的因素 a.粒子增强复合材料 基体材料承受主要载荷,增强粒子高度弥 散地分布在基体中,阻碍导致塑性变形的 位错运动。 粒子直径一般在0.01μ~0.1μ范围内时增强 效果最好;直径过大时,引起应力集中; 直径小于0.01μ时,则近似于固溶体结构, 作用不大。
b.细晶强化 不连续增强金属基复合材料具有极细的晶粒 尺寸,远比非增强基体金属细小。 晶粒尺寸不同,对再结晶有两种影响:
若颗粒尺寸较小,颗粒会钉扎大角晶界;
若颗粒尺寸较大,颗粒会促进再结晶形核, 使复合材料获得极细小晶粒。
c.弥散强化 时效强化相,在颗粒增强金属基复合材料 中的效果作用并不显著。 颗粒尺寸和颗粒间距大于时效强化合金。
基体:铝基、镁基、钛基、钢基、铜基
增强体:连续纤维、短纤维、晶须、颗粒
金属基复合材料性能特点:高比强度、高模 量、高韧性、高导热导电性、膨胀系数小、 耐磨性好、高温强度高、表面稳定性好。
第一节 金属基复合材料体系选择
1.基体选择
工作环境、工作要求 增强体类型 (1)工作环境、要求 航空航天领域 要求高比强度、高比模量和 高尺寸稳定性 体积质量小的金属合金 镁、铝合金
(1)混粉与压制法 将金属粉末与陶瓷纤维或颗粒混合(干混或 悬浮液),抽真空后,高温致密化。 热等静压,热挤压 (2)薄膜扩展粘合 用于制造纤维增强钛合金。将排列的纤维置 于钛合金薄膜之间,然后热压。 在热压过程中,钛合金发生塑性流变,使之 致密化。
(3)物理气相沉积法 基体金属升华为气相,将长纤维连续的输送 入气相中,金属或合金便在纤维表面沉积 下来,生成较厚的涂层。 然后将经过涂层的纤维束集合起来,进行热 压或热等静压,形成金属基复合材料。
硼纤维: • 强度高,弹性模量大,耐高温性能好
• 在现代航空结构材料中,硼纤维的弹性模 量绝对值最高 • 硼纤维的相对密度大,延伸率差,价格昂 贵 • 硼纤维是用化学沉积的方法将还原生产的 硼元素涂覆到钨和碳丝上面制得的
碳化硅纤维: • 优良的高温强度,高熔点、高强度、高硬 度、高弹性模量,是一种陶瓷纤维。 • 化学沉积法:氢和硅烷混合气体在1300℃ 的钨丝上反应生成碳化硅纤维。 烧结法(有机聚合物转化法):有机硅聚 合物纺丝1000℃以上烧结。
• 铝与碳反应生成Al4C3
• 铝与硼界面反应生成AlB2和AlB12,铝基 成分不同,产物不同。
• 铝与碳化硅反应生成Al4C3和Si。温度低于 620℃时,铝与碳化硅不能反应。在热处理 过的Al-Mg/SiC复合材料中,界面反应产物 有薄层Al4C3,提高了界面粘结强度,阻碍 界面滑动并明显提高弹性模量。 • 镁在铝合金基体中可显著提高界面活性。
第二节 金属基复合材料性能设计
• 复合材料力学行为的核心:基体与增强体 进行载荷分配。
• 混合定律: 外加载荷等于基体和增强体按体积平均载 荷的总和。
A f f (1 f ) M
1.连续纤维增强金属基复合材料的强度 • 主要靠连续纤维承受外加载荷 • 金属基体作为传递和分散载荷的媒体 • 纤维增强金属基复合材料的破坏,主要是由 纤维断裂所引起。 • 对片层金属基复合材料,抗拉强度σCu为:
碳纤维: • 碳纤维和石墨纤维的总称。 • 高强度、高弹性模量,优良的导热性和导 电性,低膨胀系数,优异的高温力学性能
• 碳纤维的相对密度小,弹性模量高,而且 在2500℃无氧气氛中也不降低。 石墨纤维的耐热性和导电性比碳纤维高, 并具有自润滑性。 • 碳纤维在高温下与金属有不同程度的界面 反应,导致损伤碳纤维。 • 制备方法:有机纤维在惰性气体中,经高 温碳化可以制成碳纤维和石墨纤维。在 2000℃以下制得碳纤维,再经2500℃以上 处理得石墨纤维。
增强体与基体之间的结合强度对复合材料 的性能影响很大。
如果界面结合强度低,则增强体与基体 很容易分离, 起不到增强作用, 如果界面结合强度太高,则增强体与基 体之间的应力无法松弛,容易形成脆性 断裂。
铝基复合材料的界面反应 • 铝是高度活泼的金属,可与大部分增强 体起反应。由于表面有Al2O3层,故反应 速度比较慢。
b.纤维增强复合材料 复合效果取决于纤维和基体的性质、界面 物理、化学的作用以及纤维的含量、长度、 排列方式等因素。
为了达到纤维增强的目的,必须注意以下问 题: • 纤维增强复合材料中承受外加载荷主要靠 增强纤维。因此应选择强度和弹性模量都 高于基体的纤维材料作增强剂。
• 纤维和基体之间要有一定的粘结作用,两 者之间的结合力要能保证基体所受的力通 过界面传递给纤维。 但结合力不能过大,如果界面结合强度太 高,增强体与基体之间的应力无法松弛, 容易形成脆性断裂。 • 纤维的排布方向要和构件的受力方向一致, 才能发挥增强作用。
Cu f fu M * (1 f )
σfu为纤维拉伸强度, σM*为纤维断裂时金属 基体的拉伸强度。
• 最小体积分数f’:
当纤维体积分数f很小时,由混合定律算出 的失效应力比相应于以孔洞取代纤维的金 属基体值还小。这是不真实的。 f须大于f’
Mu M * f ' fu M * Mu
第十章 金属基复合材料
复合材料:由两种或两种以上性质不同的材 料复合而成的多相材料。
复合材料的分类: 按用途 复合材料
结构复合材料 功能复合材料
金属基复合材料 按基体类型 非金属基复合材料
按增强体种 类和形状
纤维增强复合材料
颗粒增强复合材料
晶须增强复合材料
金属基复合材料:连续的金属、合金 基体 + 增强体
• 对于纵向弹性模量,也可使用混合定律。
2.非连续金属基复合材料的强度 • 混合定律应用于短纤维(包括晶须)时, 应考虑长度对直径比L/d和基体抗剪强度。 • 短纤维长度不同时,最终表达式不同。
– 若纤维长度L小于临界长度Lc,则纤维的最大应 力达不到纤维的平均强度,纤维不会断裂,破 坏是由于界面或基体破坏所造成的。 – 若纤维长度L大于临界长度Lc,纤维的应力达到 平均强度时,材料开始断裂。
• 陶瓷晶须包括:碳化硅、氧化铝、氮化硅、 硼酸铝晶须。
制备方法:化学气相法。
• 金属晶须中可批量生产的是铁晶须,其最 大特点是可在磁场中取向,可以很容易地 制取定向纤维增强复合材料。
(3)颗粒 • 一般采用陶瓷颗粒材料。尺寸小于50微米, 一般在10微米以下。 • 氧化铝、碳化硅、氮化硅、碳化钛、硼化 钛、碳化硼、氧化钇颗粒。 • 优点:高强度、高弹性模量、高硬度、耐 热。