蜗杆传动设计计算
蜗杆传动设计

14
3.34
15
3.22
16
3.07
17
2.96
18
2.89
19
2.82
20
2.76
22
2.66
24
2.57
26
2.51
Z2 YF2
28 2.48
30 2.44
35 2.36
40 2.32
45 2.27
50 2.24
60 2.20
70 2.17
80 2.14
90 2.12
100 2.10
150 2.07
Fnc = K Fn
载荷系数K=l~1.4
3、蜗轮齿面的接触强度计算
校核公式: 设计公式:
H 500
KT2 KT 500 2 2 2 [ H ] d1d2 2 m d1 z2
2
500 2 m d1 KT2 z2 [ H ]
4、蜗轮轮齿齿根弯曲强度计算
1.53KT2 cos YF 2 F 校核公式: F d1d 2 m 1.53KT2 cos 设计公式: m2 d1 YF 2 z2 F
表2-9-6 蜗轮的齿形系数YF2(α=20°,ha*=1)
Z2
YF2
10
4.55
11
4.14
12
3.70
13
3.55
(a)圆柱蜗杆传动
(b)圆环面蜗杆传动
(c)锥面蜗杆传动
阿基米德蜗杆
渐开线蜗杆
法向直廓蜗杆 圆弧圆柱蜗杆
(2)按蜗杆旋向不同来分类,蜗杆传动可以分成左旋和右旋蜗杆 传动两种类型 。 (3)按工作条件不同分类蜗杆传动可以分为闭式蜗杆传动和开式 蜗杆传动两种类型。 2、蜗杆传动的特点 (1)蜗杆传动的最大特点是结构紧凑、传动比大。i=10~40,最 大可达80。若只传递运动(分度运动),其传动比可达1000。 (2)传动平稳、噪声小 (3)可制成具有自锁性的蜗杆 (4)传动效率低 (5)制造成本高 二、蜗杆传动的主要参数和几何尺寸 中间平面:通过蜗杆轴线并垂直于蜗轮轴线的平面称为中间平面。 在中间平面上蜗轮与蜗杆的啮合相当于渐开线齿轮与齿条的啮合。 因此蜗杆传动的设计计算都以中间平面上的参数和几何关系为准。
蜗轮蜗杆计算

2、根据齿面形状不同分为:
普通蜗杆传动
圆弧圆柱蜗杆传动
3、阿基米德蜗杆
在轴剖面:直线齿廓 法剖面:凸曲线 垂直轴剖面:阿基米德螺线 车削加工,不能磨削,精度低。
蜗轮滚刀:与蜗杆尺寸相同 在中间平面上可看成直齿齿条与渐开线齿轮啮合
9.2 普通圆柱蜗杆传动的主要参数和几何尺寸计算
中间平面上的参数作为设计基准
单位时间由箱体外壁散发到空气中的热量为
H 2 K s A(t t0 )
W
式中 Ks—散热系数 A—散热面积 t—达到平衡时,箱体内的 油温,t在800以内 t0—周围空气温度, t0=200
根据热平衡条件H1=H2可求得既定工作条件下 的油温
t
t0
1000 P1 (1 )
Ks A
C
在既定工作条件下,保持正常油温所需要的 散热面积
一、蜗杆传动的特点和应用
1、特点:
单级传动比大; 结构紧凑; 传动平稳,无噪音; 可自锁; 传动效率低; 成本高。
2、应用:
机床:数控工作台、分度 汽车:转向器 冶金:材料运输 矿山:开采设备 起重运输:提升设备、电梯、 自动扶梯
二、蜗杆传动的类型
1、按蜗杆形状分
圆柱蜗杆传动
环面蜗杆传动 锥蜗杆传动
A 1000 P1 (1 )
K s (t t0 )
m2
一般应使t在80℃以下
若t>80℃或有效的散热面积不足时,则必须
采取措施,以提高其散热能力
常用措施: 1 、合理设计箱体结构,铸 出或焊上散热片,以增大散 热面积
2 、在蜗轮轴上装置风扇, 进行人工通风,以提高散 热系数
3 、在箱体油池内装 设蛇形冷却水管
[ ]H —蜗轮材料的许用接触应力,MPa
蜗杆计算公式
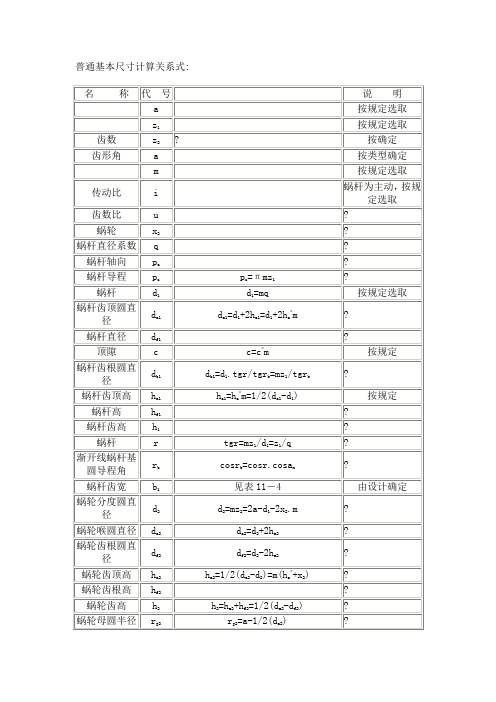
d2'=d2
b1
见表11-4
由设计确定
蜗轮分度圆直径
d2
d2=mz2=2a-d1-2x2.m
?
蜗轮喉圆直径
da2
da2=d2+2ha2
?
蜗轮齿根圆直径
df2
df2=d2-2ha2
?
蜗轮齿顶高
ha2
ha2=1/2(da2-d2)=m(ha*+x2)
?
蜗轮齿根高
hf2
?
蜗轮齿高
h2
h2=ha2+hf2=1/2(da2-df2)
普通基本尺寸计算关系式:
名 称
代 号
说 明
a
按规定选取
z1
按规定选取
齿数
z2
?
按确定
齿形角
a
按类型确定
m
按规定选取
传动比
i
蜗杆为主动,按规定选取
齿数比
u
?
蜗轮
x2
?
蜗杆直径系数
q
?
蜗杆轴向
pa
?
蜗杆导程
pz
pz=πmz1
?
蜗杆
d1
d1=mq
按规定选取
蜗杆齿顶圆直径
da1
da1=d1+2ha1=d1+2ha*m
?
蜗杆直径
df1
?
顶隙
c
c=c*m
按规定
蜗杆齿根圆直径
db1
db1=d1.tgr/tgrb=mz1/tgrb
?
蜗杆齿顶高
ha1
ha1=ha*m=1/2(da1-d1)
按规定
蜗杆高
机械设计(7.2.1)--圆柱蜗杆传动主要参数和几何尺寸计算
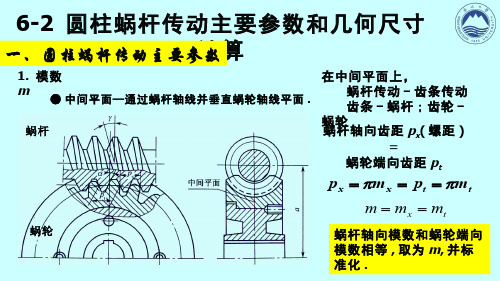
变 圆分离 ;
位 : 蜗杆分度线与蜗轮分度
中心距较标准值改 变;
位 , 减小 .
正变位 , 增大 ; 负变
(4) 变位后 , 蜗轮分度圆仍然与其节圆重 合,
但轮尺尺寸有变化 .
负变位 x2<0
标准 x2=0
正变位 x2>0 变位系数 , 过小 ,
( 变位后的 ) 实际中心距
a
a
a
1 2
(d1
● 蜗杆径向尺寸: d1= 按标准或自定 齿全高 , 齿顶高 , 齿根高及顶圆、
根圆同标准齿轮 , 无关变位 .
da1 d1 2ha1;ha1 ha*m d f 1 d1 2hf 1;hf 1 (ha* c* )m
ha* 1.0,0.8(短);c* 0.2,0.15,0.25
与链传动不同
7. 蜗轮齿数 表z26-3 给出了 z2 荐用值 ( 结合传动比和 蜗杆头数, z1=1,2,4,6) 。
为避免根切:
z1=1 , z2>17~18
z1=2 , z2>27
动力传动时,
z2<80, 根强度
避免尺寸过大 , 削弱齿
6-2 圆柱蜗杆传动主要参数和几何尺寸计算 一、圆柱蜗杆传动主要参 数
6-2 圆柱蜗杆传动主要参数和几何尺寸计算 一、圆柱蜗杆传动主要参 数
一、圆柱蜗杆传动主要参数
4. 蜗杆分度圆直径 d1(1) 为保证正确啮合,用蜗杆尺寸基
本相同的滚刀来加工蜗轮 .
(2) 为减少滚刀的数量和使之标准化 ,每个标准模数的规定了一定数量 的滚刀直径 ( 即蜗杆直径 ).
(3) 表 6-2 列出了 m 和 d1 常用标准 值.
蜗轮蜗杆扭矩计算公式
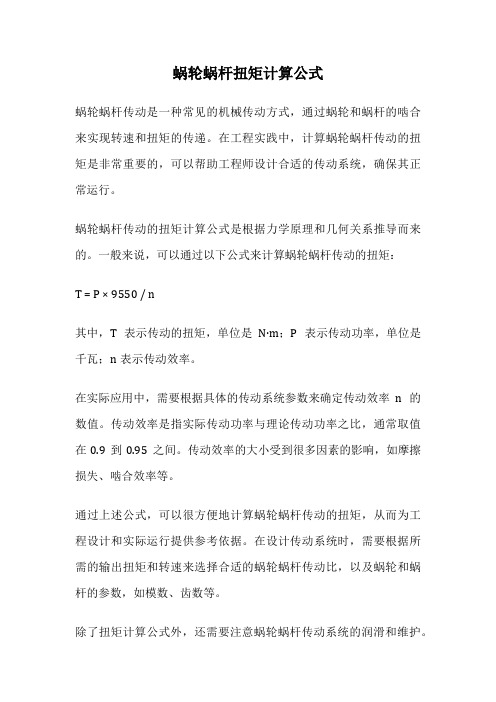
蜗轮蜗杆扭矩计算公式
蜗轮蜗杆传动是一种常见的机械传动方式,通过蜗轮和蜗杆的啮合来实现转速和扭矩的传递。
在工程实践中,计算蜗轮蜗杆传动的扭矩是非常重要的,可以帮助工程师设计合适的传动系统,确保其正常运行。
蜗轮蜗杆传动的扭矩计算公式是根据力学原理和几何关系推导而来的。
一般来说,可以通过以下公式来计算蜗轮蜗杆传动的扭矩:
T = P × 9550 / n
其中,T表示传动的扭矩,单位是N·m;P表示传动功率,单位是千瓦;n表示传动效率。
在实际应用中,需要根据具体的传动系统参数来确定传动效率n的数值。
传动效率是指实际传动功率与理论传动功率之比,通常取值在0.9到0.95之间。
传动效率的大小受到很多因素的影响,如摩擦损失、啮合效率等。
通过上述公式,可以很方便地计算蜗轮蜗杆传动的扭矩,从而为工程设计和实际运行提供参考依据。
在设计传动系统时,需要根据所需的输出扭矩和转速来选择合适的蜗轮蜗杆传动比,以及蜗轮和蜗杆的参数,如模数、齿数等。
除了扭矩计算公式外,还需要注意蜗轮蜗杆传动系统的润滑和维护。
良好的润滑可以减小传动系统的摩擦损失,提高传动效率,延长传动件的使用寿命。
定期检查传动系统的工作状态,及时更换磨损严重的传动件,可以保证传动系统的正常运行。
总的来说,蜗轮蜗杆传动扭矩的计算是工程设计和运行中的重要一环,只有合理计算和选择扭矩,才能确保传动系统的安全可靠性。
在实际应用中,需要结合具体情况进行计算和设计,以获得最佳的传动效果。
蜗杆传动主要参数及几何尺寸.

为了限制 滚刀数目
d1=mq
4. 蜗杆的导程角γ 轴面齿距 pa1=πm 导程 s=z1pa1=z1πm
tan z1 pa1 z1πm z1m z1
πd1 πd1 mq q
二. 蜗杆传动的几何尺 寸
三、蜗杆蜗轮啮合传动 1. 正确啮合条件
中间平面:蜗杆传动似齿轮齿条传动
ma1=mt2=m αa1=αt2=α γ=β (旋向相同)
中间平面:
在阿基米德蜗杆传动中,通过蜗杆轴线垂直蜗 轮轴线的平面
在中间平面内,阿基米德蜗杆传动 相当于齿轮于齿条传动。因此,蜗杆传 动的设计计算以中间平面的参数和几何 几何关系为准。
一、蜗杆传动的主要参数
1. 模数m、压力角a、齿顶高系数h*a和顶隙系数c*
蜗杆的参数
蜗轮的参数
①轴面模数ma1=m ②轴面压力角αa1= α ③齿顶高系数h*a=1 ④顶隙系数c*=0.2
2. 标准中心距
a
1 2
(d1
d2)
m 2
(q
z2 )
传动比i 5~6
z1
6
z2 30~36
7~13 4
28~52
14~27 2
28~54
28~40 2、1 28~80
>40 1
>40
3. 蜗杆的分度圆直径d1 蜗轮配对加工法
①采用与蜗杆参数相同的滚刀;
②滚刀的安装位置同蜗杆传动的 工作位置;直径系数
有多少d1就有多少滚刀
①端面模数mt2=m ②端面压力角αt2=α ③齿顶高系数h*a =1 ④顶隙系数c*=0.2
2. 传动比i、蜗杆头数z1和蜗轮齿数z2
i 1 z2 2 z1
z1少,传动比大,效率低; z1多, 加工难,常取1、2、 4、6。
蜗杆计算公式教程
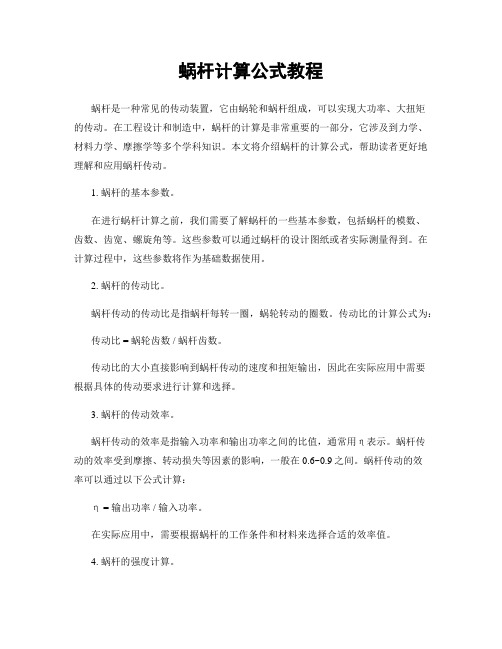
蜗杆计算公式教程蜗杆是一种常见的传动装置,它由蜗轮和蜗杆组成,可以实现大功率、大扭矩的传动。
在工程设计和制造中,蜗杆的计算是非常重要的一部分,它涉及到力学、材料力学、摩擦学等多个学科知识。
本文将介绍蜗杆的计算公式,帮助读者更好地理解和应用蜗杆传动。
1. 蜗杆的基本参数。
在进行蜗杆计算之前,我们需要了解蜗杆的一些基本参数,包括蜗杆的模数、齿数、齿宽、螺旋角等。
这些参数可以通过蜗杆的设计图纸或者实际测量得到。
在计算过程中,这些参数将作为基础数据使用。
2. 蜗杆的传动比。
蜗杆传动的传动比是指蜗杆每转一圈,蜗轮转动的圈数。
传动比的计算公式为:传动比 = 蜗轮齿数 / 蜗杆齿数。
传动比的大小直接影响到蜗杆传动的速度和扭矩输出,因此在实际应用中需要根据具体的传动要求进行计算和选择。
3. 蜗杆的传动效率。
蜗杆传动的效率是指输入功率和输出功率之间的比值,通常用η表示。
蜗杆传动的效率受到摩擦、转动损失等因素的影响,一般在0.6~0.9之间。
蜗杆传动的效率可以通过以下公式计算:η = 输出功率 / 输入功率。
在实际应用中,需要根据蜗杆的工作条件和材料来选择合适的效率值。
4. 蜗杆的强度计算。
蜗杆的强度计算是蜗杆设计中最重要的一部分,它涉及到蜗杆的受力分析、材料力学等知识。
蜗杆的强度可以通过以下公式进行计算:蜗杆的齿面接触应力σH = (2T) / (πdLb)。
其中,T为蜗杆的扭矩,d为蜗杆的分度圆直径,Lb为蜗杆的齿宽。
蜗杆的齿面接触应力必须小于蜗杆材料的许用应力,否则会导致蜗杆的断裂。
此外,蜗杆的齿根弯曲应力、蜗杆的齿面弯曲应力等也需要进行计算和分析,以保证蜗杆在工作时不会发生破坏。
5. 蜗杆的热量计算。
蜗杆传动在工作时会产生一定的摩擦热量,因此需要进行热量计算,以确定蜗杆的冷却方式和散热能力。
蜗杆的热量计算可以通过以下公式进行:Q = (τμ) / (2πn)。
其中,Q为单位时间内的摩擦热量,τ为摩擦力矩,μ为摩擦系数,n为转速。
蜗轮蜗杆设计计算
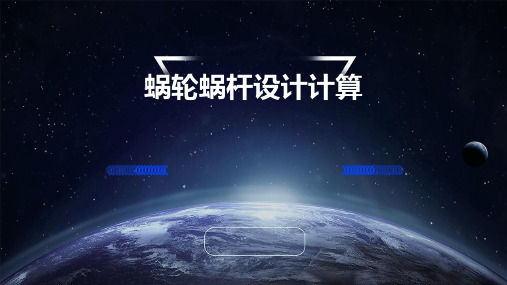
蜗杆传动的效率计算
总结词
根据蜗轮蜗杆的设计参数和工况,计算出蜗杆传动的效率。
详细描述
蜗杆传动的效率计算是评估蜗杆传动性能的重要指标之一。通过分析蜗轮蜗杆的设计参 数和工况,如蜗杆的导程角、模数、转速和载荷等参数,可以计算出蜗杆传动的效率。
蜗轮齿面接触疲劳强度的计算
总结词
根据蜗轮齿面上的载荷分布和材料属性 ,计算出蜗轮齿面的接触疲劳强度。
刚度分析
进行蜗轮蜗杆的刚度分析, 以减小传动过程中的变形 和振动。
可靠性设计
为确保自动化设备的可靠 性,对蜗轮蜗杆进行可靠 性设计和寿命预测。
THANKS
感谢观看
材料应具备较好的抗疲劳性能,以承受交 变载荷的作用;
04
材料应具有良好的工艺性能,易于加工制 造。
04
蜗轮蜗杆设计计算方法
蜗轮齿面载荷分布计算
总结词
根据蜗杆传动的实际工况,通过分析蜗轮齿面上的受力情况,计算出蜗轮齿面上的载荷分布。
详细描述
在进行蜗轮齿面载荷分布计算时,需要考虑蜗杆传动的实际工况,如传动比、转速、载荷大小和方向 等因素。通过分析蜗轮齿面上的受力情况,可以确定蜗轮齿面上的载荷分布,为后续的设计计算提供 基础。
蜗轮蜗杆设计计算
• 蜗轮蜗杆简介 • 蜗轮蜗杆设计参数 • 蜗轮蜗杆材料选择 • 蜗轮蜗杆设计计算方法 • 蜗轮蜗杆设计实例分析
01
蜗轮蜗杆简介
蜗轮蜗杆的定义
01
蜗轮蜗杆是一种常用的传动装置 ,由两个交错轴线、相互咬合的 齿轮组成,其中一个是蜗杆,另 一个是蜗轮。
02
蜗轮蜗杆具有传动比大、传动效 率高、传动平稳、噪音低等优点 ,因此在各种机械传动系统中得 到广泛应用。
VS
蜗轮蜗杆的计算

蜗轮蜗杆的计算公司标准化编码 [QQX96QT-XQQB89Q8-NQQJ6Q8-MQM9N]蜗轮、蜗杆的计算公式:1,传动比=蜗轮齿数÷蜗杆头数2,中心距=(蜗轮节径+蜗杆节径)÷2 3,蜗轮吼径=(齿数+2)×模数 4,蜗轮节径=模数×齿数5,蜗杆节径=蜗杆外径-2×模数 6,蜗杆导程=π×模数×头数7,螺旋角(导程角)tg β=(模数×头数)÷蜗杆节径 一.基本参数:(1)模数m 和压力角α:在中间平面中,为保证蜗杆蜗轮传动的正确啮合,蜗杆的轴向模数m a1和压力角αa1应分别相等于蜗轮的法面模数m t2和压力角αt2,即 m a1=m t2=m αa1=αt2蜗杆轴向压力角与法向压力角的关系为: tgαa =tgαn /cosγ 式中:γ-导程角。
(2)蜗杆的分度圆直径d 1和直径系数q为了保证蜗杆与蜗轮的正确啮合,要用与蜗杆尺寸相同的蜗杆滚刀来加工蜗轮。
由于相同的模数,可以有许多不同的蜗杆直径,这样就造成要配备很多的蜗轮滚刀,以适应不同的蜗杆直径。
显然,这样很不经济。
为了减少蜗轮滚刀的个数和便于滚刀的标准化,就对每一标准的模数规定了一定数量的蜗杆分度圆直径d1,而把及分度圆直径和模数的比称为蜗杆直径系数q ,即: q=d1/m常用的标准模数m 和蜗杆分度圆直径d1及直径系数q ,见匹配表。
(3)蜗杆头数z 1和蜗轮齿数z 2蜗杆头数可根据要求的传动比和效率来选择,一般取z1=1-10,推荐 z1=1,2,4,6。
选择的原则是:当要求传动比较大,或要求传递大的转矩时,则z1取小值;要求传动自锁时取z1=1;要求具有高的传动效率,或高速传动时,则z1取较大值。
蜗轮齿数的多少,影响运转的平稳性,并受到两个限制:最少齿数应避免发生根切与干涉,理论上应使z2min≥17,但z2<26时,啮合区显着减小,影响平稳性,而在z2≥30时,则可始终保持有两对齿以上啮合,因之通常规定z2>28。
蜗杆各部分尺寸计算公式
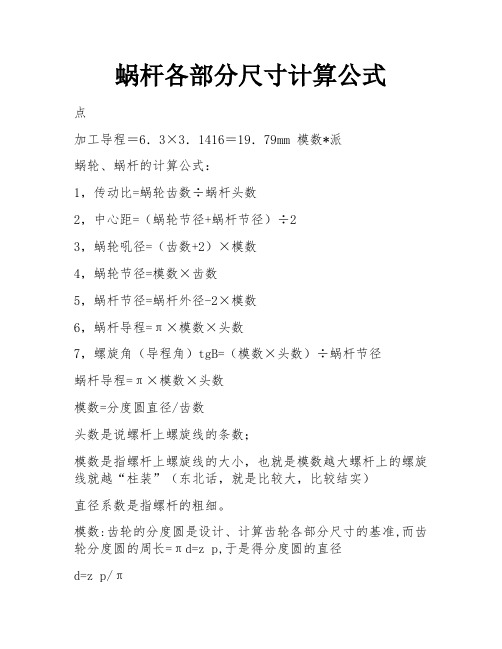
蜗杆各部分尺寸计算公式点加工导程=6.3×3.1416=19.79mm 模数*派蜗轮、蜗杆的计算公式:1,传动比=蜗轮齿数÷蜗杆头数2,中心距=(蜗轮节径+蜗杆节径)÷23,蜗轮吼径=(齿数+2)×模数4,蜗轮节径=模数×齿数5,蜗杆节径=蜗杆外径-2×模数6,蜗杆导程=π×模数×头数7,螺旋角(导程角)tgB=(模数×头数)÷蜗杆节径蜗杆导程=π×模数×头数模数=分度圆直径/齿数头数是说螺杆上螺旋线的条数;模数是指螺杆上螺旋线的大小,也就是模数越大螺杆上的螺旋线就越“柱装”(东北话,就是比较大,比较结实)直径系数是指螺杆的粗细。
模数:齿轮的分度圆是设计、计算齿轮各部分尺寸的基准,而齿轮分度圆的周长=πd=z p,于是得分度圆的直径d=z p/π由于在上式中π为一无理数,不便于作为基准的分度圆的定位.为了便于计算,制造和检验,现将比值p/π人为地规定为一些简单的数值,并把这个比值叫做模数(module),以m表示,即令其单位为mm.于是得:模数m是决定齿轮尺寸的一个基本参数.齿数相同的齿轮模数大,则其尺寸也大.为了便于制造,检验和互换使用,齿轮的模数值已经标准化了.建筑模数建筑模数指建筑设计中选定的标准尺寸单位。
它是建筑设计、建筑施工、建筑材料与制品、建筑设备、建筑组合件等各部门进行尺度协调的基础。
就象随便来个尺寸,建筑构件就无法标准化了,难统一。
基本模数的数值规定为100mm,以M表示,即1M= 100mm。
导出模数分为扩大模数和分模数,扩大模数的基数为3M,6M,12M,15M,30M,60M共6个;分模数的基数为1/10M,1/5M,1/2M共3个.使用3M是《中华人民共和国国家标准建筑统一模数制》中为了既能满足适用要求,又能减少构配件规格类型而规定的。
蜗轮蜗杆的计算
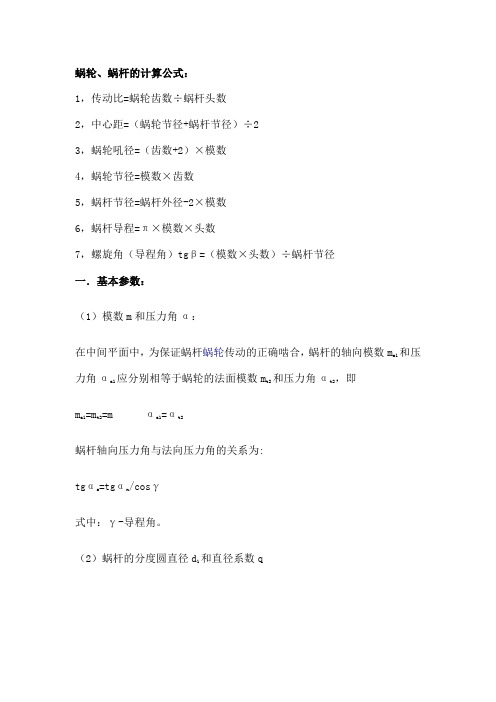
蜗轮、蜗杆的计算公式: 1,传动比=蜗轮齿数÷蜗杆头数 2,中心距=(蜗轮节径+蜗杆节径)÷2 3,蜗轮吼径=(齿数+2)×模数 4,蜗轮节径=模数×齿数 5,蜗杆节径=蜗杆外径-2×模数 6,蜗杆导程=π×模数×头数7,螺旋角(导程角)tg β=(模数×头数)÷蜗杆节径 一.基本参数:(1)模数m 和压力角α:在中间平面中,为保证蜗杆蜗轮传动的正确啮合,蜗杆的轴向模数m a1和压力角αa1应分别相等于蜗轮的法面模数m t2和压力角αt2,即 m a1=m t2=m αa1=αt2蜗杆轴向压力角与法向压力角的关系为: tgαa =tgαn /cosγ 式中:γ-导程角。
(2)蜗杆的分度圆直径d 1和直径系数q为了保证蜗杆与蜗轮的正确啮合,要用与蜗杆尺寸相同的蜗杆滚刀来加工蜗轮。
由于相同的模数,可以有许多不同的蜗杆直径,这样就造成要配备很多的蜗轮滚刀,以适应不同的蜗杆直径。
显然,这样很不经济。
为了减少蜗轮滚刀的个数和便于滚刀的标准化,就对每一标准的模数规定了一定数量的蜗杆分度圆直径d1,而把及分度圆直径和模数的比称为蜗杆直径系数q,即:q=d1/m常用的标准模数m和蜗杆分度圆直径d1及直径系数q,见匹配表。
(3)蜗杆头数z1和蜗轮齿数z2蜗杆头数可根据要求的传动比和效率来选择,一般取z1=1-10,推荐 z1=1,2,4,6。
选择的原则是:当要求传动比较大,或要求传递大的转矩时,则z1取小值;要求传动自锁时取z1=1;要求具有高的传动效率,或高速传动时,则z1取较大值。
蜗轮齿数的多少,影响运转的平稳性,并受到两个限制:最少齿数应避免发生根切与干涉,理论上应使z2min≥17,但z2<26时,啮合区显着减小,影响平稳性,而在z2≥30时,则可始终保持有两对齿以上啮合,因之通常规定z2>28。
另一方面z2也不能过多,当z2>80时(对于动力传动),蜗轮直径将增大过多,在结构上相应就须增大蜗杆两支承点间的跨距,影响蜗杆轴的刚度和啮合精度;对一定直径的蜗轮,如z2取得过多,模数m 就减小甚多,将影响轮齿的弯曲强度;故对于动力传动,常用的范围为z2≈28-70。
普通圆柱蜗轮蜗杆传动设计计算

蜗轮蜗杆传动的传动比等于蜗轮齿数与蜗杆头数之比。它是蜗轮蜗杆传动设计中的重要参数,决定了传动的方向 和减速比。
传动效率
蜗轮蜗杆传动的效率取决于多个因素,如模数、压力角、润滑条件等。在理想情况下,单头蜗杆传动的效率约为 90%,多头蜗杆传动的效率会相应降低。
03
蜗轮蜗杆传动的强度计 算
蜗杆的强度计算
02
蜗轮蜗杆传动的设计参 数
蜗杆的几何参数
模数
模数是蜗杆设计中的重要参数,它决定了蜗杆的尺寸和传动效率。模数越大, 蜗杆的直径就越大,传动效率越高,但同时也会增加蜗杆的弯曲和剪切应力。
压力角
压力角是蜗杆螺旋线与蜗轮齿面接触点处的法线方向与蜗轮轴线之间的夹角。 压力角的大小对蜗杆传动的平稳性和传动效率有影响。通常,较小的压力角可 以获得更好的传动平稳性,但也会降低传动效率。
蜗轮的几何参数
齿数
蜗轮的齿数是蜗轮的一个重要参数, 它决定了蜗轮的传动比和传动能力。 齿数越多,传动比就越大,但同时也 会增加蜗轮的尺寸和重量。
分度圆直径
分度圆直径是蜗轮的一个关键参数, 它决定了蜗轮的大小和强度。分度圆 直径越大,蜗轮的承载能力就越强, 但同时也会增加蜗轮的尺寸和重量。
传动的基本参数
定期更换润滑剂:根据工作条件和润滑剂的使用 情况,定期更换润滑剂以保证良好的润滑效果。
06
蜗轮蜗杆传动设计计算 的实例分析
设计实例一
总结词:基础设计
详细描述:该实例主要介绍了普通圆柱蜗轮蜗杆传动的基本设计计算过程,包括 蜗杆的几何参数、传动效率、承载能力等方面的计算。
设计实例二
总结词
高温环境适应性
防尘密封
通过密封圈、密封垫等密封件,防止灰尘、杂质等进入蜗轮蜗杆 的接触表面。
《机械设计基础》第12章 蜗杆传动

3、摩擦磨损问题突出,磨损是主要 的失效形式。为了减摩耐磨,蜗轮齿圈常需用青铜制造,成本较高;
4、传动效率低,具有自锁性时,效率低于50%。
由于上述特点,蜗杆传动主要用于传递运动,而在动力传输中的应用受到限制。
其齿面一般是在车床上用直线刀刃的 车刀切制而成,车刀安装位置不同, 加工出的蜗杆齿面的齿廓形状不同。
γ
β
γ=β (蜗轮、蜗杆同旋向)
一、蜗杆传动的主要参数及其选择
1、模数m和压力角α
§12-2 蜗杆传动的参数分析及几何计算
ma1= mt2= m αa1=αt2 =α=20°
在蜗杆蜗轮传动中,规定中间平面上的模数和压力角为标准值,即:
模数m按表12-1选取,压力角取α=20° (ZA型αa=20º;ZI型αn=20º) 。
阿基米德蜗杆(ZA蜗杆) 渐开线蜗杆(ZI蜗杆)
圆柱蜗杆传动
环面蜗杆传动
锥蜗杆传动
其蜗杆体在轴向的外形是以凹弧面为母线所形成的旋转曲面,这种蜗杆同时啮合齿数多,传动平稳;齿面利于润滑油膜形成,传动效率较高。
同时啮合齿数多,重合度大;传动比范围大(10~360);承载能力和效率较高。
三、分类
在轴剖面上齿廓为直线,在垂直于蜗 杆轴线的截面上为阿基米德螺旋线。
§12-5 圆柱蜗杆传动的强度计算
一、蜗轮齿面接触疲劳强度的计算
1、校核公式:
2、设计公式:
式中:a—中心距,mm;T2 —作用在蜗轮上的转矩,T2 = T1 iη; zE—材料综合弹性系数,钢与铸锡青铜配对时,取zE=150;钢与铝青铜或灰铸铁配对时, 取zE=160。 zρ—接触系数,由d1/a查图12-11,一般d1/a=0.3~0.5。取小值时,导程角大,故效率高,但蜗杆刚性较小。 kA —使用系数,kA =1.1~1.4。有冲击载荷、环境温度高(t>35oC)、速度较高时,取大值。
蜗轮蜗杆的设计计算
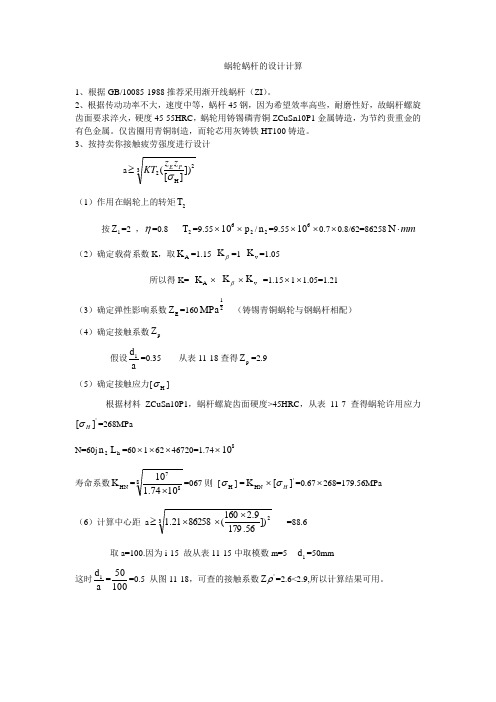
蜗轮蜗杆的设计计算1、根据GB/10085-1988推荐采用渐开线蜗杆(ZI )。
2、根据传动功率不大,速度中等,蜗杆45钢,因为希望效率高些,耐磨性好,故蜗杆螺旋 齿面要求淬火,硬度45-55HRC ,蜗轮用铸锡磷青铜ZCuSn10P1金属铸造,为节约贵重金的有色金属。
仅齿圈用青铜制造,而轮芯用灰铸铁HT100铸造。
3、按持卖你接触疲劳强度进行设计a ≥32H 2])][(σP E z z KT (1)作用在蜗轮上的转矩2T按1Z =2 ,η=0.8 2T =9.55⨯610⨯2p /2n =9.55⨯610⨯0.7⨯0.8/62=86258mm ⋅N(2)确定载荷系数K ,取A K =1.15 βK =1 v K =1.05所以得K= A K ⨯ βK ⨯v K =1.15⨯1⨯1.05=1.21(3)确定弹性影响系数E Z =16021MPa (铸锡青铜蜗轮与钢蜗杆相配)(4)确定接触系数p Z假设ad 1=0.35 从表11-18查得p Z =2.9 (5)确定接触应力[H σ]根据材料ZCuSn10P1,蜗杆螺旋齿面硬度>45HRC ,从表11-7查得蜗轮许用应力'][H σ=268MPaN=60j 2n h L =60⨯1⨯62⨯46720=1.74⨯810寿命系数HN K =8871074.110⨯=067则 [H σ] =HN K ⨯'][H σ=0.67⨯268=179.56MPa (6)计算中心距 a ≥32])56.1799.2160(8625821.1⨯⨯⨯ =88.6 取a=100.因为i-15 故从表11-15中取模数m=5 1d =50mm 这时a d 1=10050=0.5 从图11-18,可查的接触系数'Z ρ=2.6<2.9,所以计算结果可用。
4、蜗杆蜗轮的主要参数(1)蜗杆:轴向齿距Pa=15.7得直径系数q=10 齿顶园直径a1d =60,齿根圆f1d =38,分度圆导角r=11 18 36 ,蜗杆轴向齿厚Sa=5π/2=7.85mm(2)蜗轮齿数2Z =31 变位系数2x =-0.500 验算传动比i=2Z /1Z =31/2=15.5 误差为15155.15-=3.33%,在允许范围内,所以可行。
蜗杆蜗轮传动设计计算
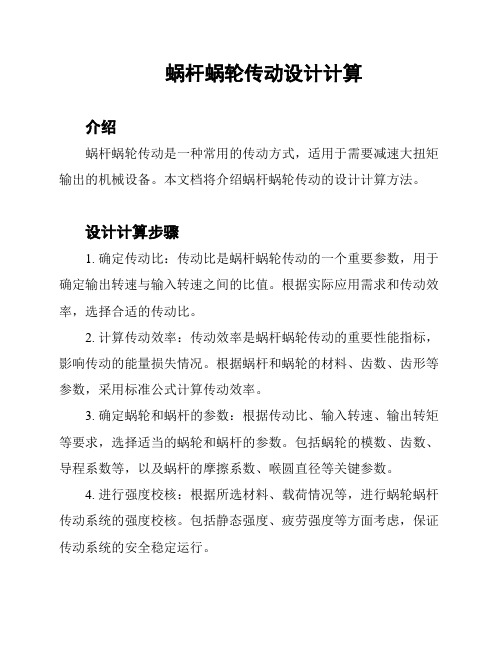
蜗杆蜗轮传动设计计算介绍蜗杆蜗轮传动是一种常用的传动方式,适用于需要减速大扭矩输出的机械设备。
本文档将介绍蜗杆蜗轮传动的设计计算方法。
设计计算步骤1. 确定传动比:传动比是蜗杆蜗轮传动的一个重要参数,用于确定输出转速与输入转速之间的比值。
根据实际应用需求和传动效率,选择合适的传动比。
2. 计算传动效率:传动效率是蜗杆蜗轮传动的重要性能指标,影响传动的能量损失情况。
根据蜗杆和蜗轮的材料、齿数、齿形等参数,采用标准公式计算传动效率。
3. 确定蜗轮和蜗杆的参数:根据传动比、输入转速、输出转矩等要求,选择适当的蜗轮和蜗杆的参数。
包括蜗轮的模数、齿数、导程系数等,以及蜗杆的摩擦系数、喉圆直径等关键参数。
4. 进行强度校核:根据所选材料、载荷情况等,进行蜗轮蜗杆传动系统的强度校核。
包括静态强度、疲劳强度等方面考虑,保证传动系统的安全稳定运行。
设计计算示例以一个减速器设计为例,输入转速为1000 rpm,输出扭矩为5000 Nm,要求传动比为10。
假设蜗杆材料为45号钢,蜗轮材料为ZCuSn10Pb1。
1. 计算传动效率:传动效率 = (传动比 x 蜗杆效率 x 蜗轮效率)/ 100%,根据实际参数计算传动效率为80%。
2. 确定蜗轮和蜗杆的参数:蜗轮模数 m = (输出扭矩 x 1000)/ (传动比 x 输入转速 x 齿数) = (5000 x 1000)/ (10 x 1000 x 100) = 5 mm;蜗杆摩擦系数μ = 0.1,喉圆直径 d = (输出扭矩 x 输入转速)/ ( x 传动比 x 齿数x μ) = (5000 x 1000)/ ( x 10 x 20 x 0.1) = 8 mm。
3. 进行强度校核:根据蜗杆和蜗轮的尺寸、材料强度等参数,进行静态强度和疲劳强度的校核。
确保蜗杆蜗轮传动系统的强度满足设计要求。
结论本文档介绍了蜗杆蜗轮传动的设计计算步骤,并以一个减速器设计为例进行了示例计算。
蜗杆与蜗轮主要参数计算

蜗杆头数
z1
按规定选取
蜗杆齿数
z2
按传动比确定
齿形角
a
aa=20o或 aa=20o
按蜗杆类型确定
模数
m
m=ma=mn/cosγ
按规定选取
传动比
i
i=n1/n2
蜗杆为主动,按规定选取
齿数比
u
u=z2/z1当蜗杆主动时,i=u
蜗轮变位系数
x2
x2=a/m-(d1+d2)/2m
蜗杆直径系数
q
q= d1/m
d1’
d1’= d1+2x2m=m(q+2x2)
蜗轮节圆直径
d2’
d2’= d2
蜗轮宽度B、顶圆直径de2及蜗杆齿宽b1的计算公式
z1
B
de2
X2
b1
1
≤
≤da2+2m
0
≥(11+m
≥(8+m
≥+z1)m
≥(11+m
≥(12+m
当变位系数X2为中间值时,b1取X2邻近两公式所求值的较大者。经磨削的蜗杆,按左式所求的长度应在增加下列值:当m<10mm时,增加25mm当m=10~16mm时,增加35~40mm;当m>16mm时,增加50mm
蜗杆轴向齿距
pa
pa=πm
蜗杆导程
pz
pz=πm z1
蜗杆分度圆直径
d1
d1=mq
按规定选取
蜗杆齿顶圆直径
da1
da1= d1+2ha1= d1+2ha*m
蜗杆齿根圆直径
df1
df1= df-2hf1= d1-2(ha*m +c)
蜗轮蜗杆的计算

蜗轮、蜗杆的计算公式:1,传动比=蜗轮齿数÷蜗杆头数2,中心距=(蜗轮节径+蜗杆节径)÷ 2 3,蜗轮吼径=(齿数+2)×模数4,蜗轮节径=模数×齿数5,蜗杆节径=蜗杆外径-2×模数6,蜗杆导程=π×模数×头数为了减少蜗轮滚刀的个数和便于滚刀的标准化,就对每一标准的模数规定了一定数量的蜗杆分度圆直径d1,而把及分度圆直径和模数的比称为蜗杆直径系数q,即:q=d1/m常用的标准模数m和蜗杆分度圆直径d1及直径系数q,见匹配表。
(3)蜗杆头数z1和蜗轮齿数z2蜗杆头数可根据要求的传动比和效率来选择,一般取z1=1-10,推荐z1=1,2,4,6。
选择的原则是:当要求传动比较大,或要求传递大的转矩时,则z1取小值;要求传动自锁时取z1=1;要求具有高的传动效率,或高速传动时,则z1取较大值。
蜗轮齿数的多少,影响运转的平稳性,并受到两个限制:最少齿数应避免发生根切与干涉,理论上应使z2min≥17,但z2<26时,啮合区显着减小,影响平稳性,而在z2≥30时,则可始终保持有两对齿以上啮合,因之通常规定z2>28。
另一方面z2也不能过多,当z2>80时(对于动力传动),蜗轮直径将增大过多,在结构上相应就须增大蜗杆两支承点间的跨距,影响蜗杆轴的刚度和啮合精度;对一定直径的蜗轮,如z2取得过多,模数m就减小甚多,将影响轮齿的弯曲强度;故对于动i=n1/n2=z2/z1 =u式中:n1 -蜗杆转速;n2-蜗轮转速。
减速运动的动力蜗杆传动,通常取5≤u≤70,优先采用15≤u≤50;增速传动5≤u≤15。
普通圆柱蜗杆基本尺寸和参数及其与蜗轮参数的匹配表。
2 蜗杆传动变位的特点蜗杆传动变位变位蜗杆传动根据使用场合的不同,可在下述两种变位方式中选取一种。
1)变位前后,蜗轮的齿数不变(z2 '=z2),蜗杆传动的中心距改变(a '≠a),如图9-8a、c所示,其中心距的计算式如下:a '=a+x2m=(d1+d2+2x2m)/22)变位前后,蜗杆传动的中心距不变(a '=a),蜗轮齿数发生变化(z2'≠z2),如图9-8d、e所示,z2' 计算如下:因a'=a则z2' =z2-2x2蜗杆传动变位:3 普通圆柱蜗杆传动的几何尺寸计算普通圆柱蜗杆传动基本几何尺寸计算关系式:。
蜗轮蜗杆设计

蜗轮蜗杆设计(2)设计原则:根据给定的中心距及传动比(或按照结构及设计的要求自定中心距和传动比)然后从蜗杆传动中心距标准值系列表中选取中心距的标准系列值,然后从经验公式先估算相关参数值,估算后在参考标准值系列表,确定标准值。
1计算传动比上式中:δp 为脉冲当量,β为步距角,L 为滚珠丝杠导程。
2初选几何参数参照蜗轮蜗杆参数推荐值表[1],i =4时,选z 1=6;则z 2= i z 1=24;3蜗轮输出转矩T 21955021i P T n η=[2] 123ηηηη=[3] tan =1tan +γηγρ()[3] =arctan ρμ[4]=μμ[5] 式中:P 1, n 1分别为蜗杆轴输入功率,转速。
η1为螺旋副啮合效率;η2为轴承效率,滚动轴承时取0.990.9952η≈ ;η3为搅油及溅油效率,0.960.993η≈ ;μ为啮合摩擦系数;η0为标准圆盘滚子试件摩擦系数;R z 为设计蜗杆的齿面粗糙度;R z0为标准圆盘试件的表面粗糙度;代入数据得η=0.76根据所选电机得P 1=8kW ,n 1=800r/min 所以30.7649550290.322300T Nm ⨯⨯== 4载荷系数123456K K K K K K K =[6]上式中:K 为载荷系数;K 1为动载荷系数,当蜗轮圆周速度23m /s v ≤时K 1取1.0;K 2为啮合质量系数,查表得0.95;K 3为小时载荷率系数,查表得0.78;K 4为环境温度系数,查表得1.09;K 5为工作情况系数,查表得1.0;K 6为风扇系数,查表得0.92。
代入数据得:10.950.78 1.0910.920.74K =⨯⨯⨯⨯⨯=5计算m 和q代入数据:14.65≥==查表取16.443= m =6.3 q =186主要几何尺寸 18 6.3113.41d qm ==⨯=6.324151.222m d z ==⨯=7蜗杆传动强度及刚度验算确定许用接触应力σHp采用锡青铜蜗轮:Hp Hbp z z s n σσ=[8]分别查滑动速度曲线表,滑动速度影响系数表及寿命系数得2220/Hbp N mm σ= 0.96z s =0.78z n = 3603600.00511.264p i L δβ⨯===⨯0.5(2)0.56.3(18240)132.322a m q x z =++=⨯⨯++=所以22200.960.78165/Hp N mm σ=⨯⨯=确定许用接触应力σHH σ=代入数据得:2134.57/H mm N σ=== 可见134.57165H HP σσ=<=,所以接触强度足够。
蜗杆蜗轮传动设计计算
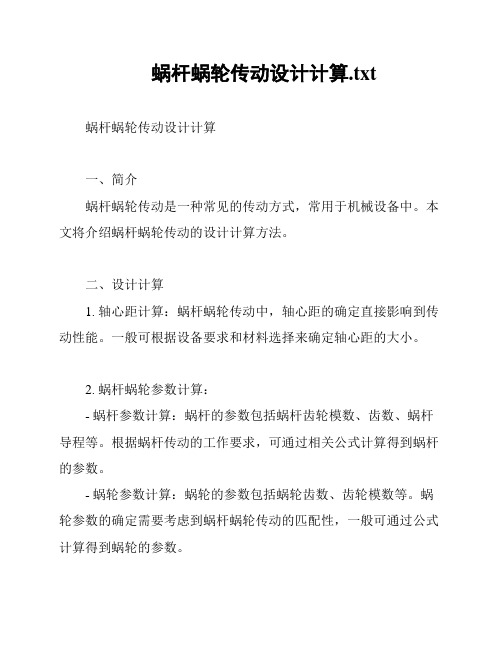
蜗杆蜗轮传动设计计算.txt蜗杆蜗轮传动设计计算一、简介蜗杆蜗轮传动是一种常见的传动方式,常用于机械设备中。
本文将介绍蜗杆蜗轮传动的设计计算方法。
二、设计计算1. 轴心距计算:蜗杆蜗轮传动中,轴心距的确定直接影响到传动性能。
一般可根据设备要求和材料选择来确定轴心距的大小。
2. 蜗杆蜗轮参数计算:- 蜗杆参数计算:蜗杆的参数包括蜗杆齿轮模数、齿数、蜗杆导程等。
根据蜗杆传动的工作要求,可通过相关公式计算得到蜗杆的参数。
- 蜗轮参数计算:蜗轮的参数包括蜗轮齿数、齿轮模数等。
蜗轮参数的确定需要考虑到蜗杆蜗轮传动的匹配性,一般可通过公式计算得到蜗轮的参数。
3. 力学计算:- 扭矩计算:根据传动功率和旋转速度,可以计算传动中所需的扭矩。
- 轴强度计算:蜗杆蜗轮传动的轴强度是设计中需要考虑的重要因素之一。
根据传动扭矩、材料强度等参数,可以进行轴强度的计算。
4. 效率计算:蜗杆蜗轮传动的效率影响着传动的能量损失。
通过相关公式和参数,可以计算蜗杆蜗轮传动的效率。
三、注意事项在进行蜗杆蜗轮传动设计计算时,需要注意以下几点:1. 使用合理的参数值和公式,确保计算结果准确可靠。
2. 考虑到材料的强度和耐磨性等因素,在选择蜗杆和蜗轮的材料时要谨慎。
3. 需要根据实际情况对设计参数进行适当调整,以满足工作要求和设备性能。
四、总结蜗杆蜗轮传动设计计算是机械设备设计中的重要内容,通过合理的设计计算能够确保传动的准确性和可靠性。
要注意选择合适的参数和材料,并根据实际情况对设计参数进行调整。
以上为蜗杆蜗轮传动设计计算的简要介绍,希望对您有所帮助。
- 1、下载文档前请自行甄别文档内容的完整性,平台不提供额外的编辑、内容补充、找答案等附加服务。
- 2、"仅部分预览"的文档,不可在线预览部分如存在完整性等问题,可反馈申请退款(可完整预览的文档不适用该条件!)。
- 3、如文档侵犯您的权益,请联系客服反馈,我们会尽快为您处理(人工客服工作时间:9:00-18:30)。
计算项目中心距
模数
轴截面齿形角
传动比
变位系数
径向间隙头数
Z1特性系数
q 齿顶高
h di 齿根高
hg 分度圆直径
D fe1节圆直径
D je1齿顶圆直径
D di1齿根圆直径
D g1分度圆螺旋导角
λ法向模数
m f 轴截面齿距P
螺旋导程
P Z 螺牙沿分度圆柱上的轴向齿厚S z1螺牙沿分度圆柱上的法向齿厚S f1齿厚测量高度
h~齿数
Z 2分度圆直径
D fe2节圆直径
D je2齿根圆直径
D g2齿顶圆直径
D di2最大外圆直径
Dw 2轮缘宽度
b 齿顶圆弧半径R 1代 号A M du α螺旋长度L☆蜗 轮
圆柱蜗杆传动基本几
i ξc
蜗
杆
齿根圆弧半径
R 2
轮
基本几何尺寸计算公式
公 式计算结果备注A=0.5M du(Z2+q+2ξ)175.00
Mdu=2A/(Z2+q+2ξ) 3.15
α=20°20.00
i=Z2/Z1=n1/n297.00
ξ=(A/Mdu)-0.5(q+z2) 2.06
C=0.25Mdu0.79
Z1=1,2,4 1.00
q=Dfe1/Mdu10.00
hdi=Mdu 3.15
hg=1.25Mdu 3.94
Dfe1=qMdu31.50
Dje1=Dfe1+2Mduξ=Mdu(q+2ξ)44.45
Ddi1=Mdu(q+2)37.80
Dg1=Mdu(q-2.5)23.63
λ=arctgZ1/q0.10
mf=Mducosλ 3.13
L=(12+0.1z2)Mdu68.36Z1=1,2 L=(13+0.1z2)Mdu71.51Z1=4 P=πMdu9.90
PZ=πMduZ19.90
Sz1=0.45πMdu97.00
Sf1=Sz1cosλ96.52
h~=Mdu 3.15
Z2=iZ197.00
Dfe2=MduZ2305.55
Dje2=Dfe2=MduZ2305.55
Dg2=2(A-0.5Ddi1-0.25Mdu)310.63
Ddi2=2(A-0.5Dfe1+Mdu)324.80
Dw2=Ddi2+Mdu327.95
b=0.65Ddi124.57
R1=0.5Dfe1-Mdu12.60
R1=0.5Ddi1+0.25Mdu19.69。