Connectorless Logic Analyzer Probing – Mechanical and Electrical Advantages
Sennheiser ew 系列无线麦克风系统用户手册说明书

The ew 322 G3 consists of the same components as ew 312 G3but with a compact cardioid clip-on microphone.The ew 352 G3 consists of the same components as ew 312 G3but with a headworn cardioid microphone.FEATURESSturdy metal housing(transmitter and receiver)42 MHz bandwidth: 1,680 tunable UHF frequencies for interference-free reception20 frequency banks with up to 24 compatible frequenciesEthernet port for connecting to theWireless Systems Manager (WSM) software for control via computer High-quality true diversity receptionPilot tone squelch for eliminating RF inter- ference when transmitter is turned off Automatic frequency scan feature searches for available frequencies Enhanced AF frequency rangeIncreased range for audio sensitivity Wireless synchronization of transmitter parameter from receiverUser-friendly menu operation with more control optionsIlluminated graphic display, receiver also shows transmitter settingsAuto-Lock function avoids accidental changing of settingsHDX compander for crystal-clear sound Transmitter feature battery indicatation in 4 steps, also shown on receiver display Programmable Mute function Integrated Equalizer and Soundcheck modeContacts for recharging BA 2015 accupack directly in the transmitter Wide range of accessories adapts the system to any requirementThe ew 312 G3 is a wireless microphone set, consisting of a True Diversityreceiver, a bodyworn transmitter, a compact omni directional clip-on micropho-ne plus accessories.The bodypack transmitter features charging contacts for the optional recharge-able battery. Sync up the bodypack to the receiver wirelessly with the new wireless sync. Backlit graphic displays make them easy to read under all lighting conditions.ew 300 Setsew 312 G3 Presentation Set ew 322 G3 Presentation Set ew 352 G3 Head Setew 335/345/365 G3 Vocal SetsFEATURESew 335 G3/ew 345 G3/ew 365 G3 Vocal SetsSee above mentioned list of features plus Programmable Mute switch, easyaccessableHandheld transmitter with easy-exchangeable microphone heads from evolution series The ew 335 G3 is a wireless microphone set, consisting of a True Diversity receiver, a handheld transmitter with e 835 microphone head plus accessories. It is versatile for every style of music and presentations. A wireless link from receiver to the transmitter allows synchronization of frequencies for easy setup. Backlit graphic displays make them easy to read under all lighting conditions. The ew 345 G3 consists of the same components as ew 335 G3but with an e 845 microphone head.The ew 365 G3consists of the same components as ew 335 G3but with an e 865 microphone head.ARCHITECT’S SPECIFICATIONSew 312 G3 Presentation SetComplete plug & play wireless microphone set with clip-on microphone (condenser, omni-directional) from Sennheiser evolution series for multi-purpose application. The devices shall have metal housings for rugged use. 42 MHz bandwidth with 1,680 tunable frequencies. 20 banks with up to 24 compatible frequencies, 1 bank for individual selectable frequencies, scan function and wireless synchronization to the transmitter for easy setup. HDX compander delivers high-quality sound performance. All parameters of transmitter and receiver can be monitored and controlled via Wireless Systems Manager (WSM) software from PC. The transmitter shall have a sensitivity range of 48 dB. The receiver offers a maximum output level of +18 dBu (+6 dB gain). True Diversity and pilot tone squelch for interference-free reception. Charging contacts on transmitter for recharging BA 2015 accupack directly in the transmitter shall be available. 3-step battery + LowBattery indication on transmitter and receiver shall give reliable information on operation time.Menu operation, auto-lock function and illuminated graphic displays on transmitter and receiver for user-friendly operation.A RF Mute function on transmitter and receiver allows offline settings.An easy accessable Mute switch on the transmitter can be programmed for AF on/off, RF on/off.A suitable Remote Mute Switch option also allows push-to-talk and push-to-muteAn equalizer and soundcheck mode is inte g rated in the receiver.ew 322 G3 Presentation SetComplete plug & play wireless microphone set with clip-on microphone (electret, cardioid) from Sennheiser evolution series for multi-purpose application. Further discription see paragraph ew 312 G3.ew 352 G3 Head SetComplete plug & play wireless microphone set with headworn microphone (condenser, cardioid) for hands-free application. Further discription see paragraph ew 312 G3.ew 335 G3 Vocal SetComplete plug & play wireless microphone set with easy-exchangeable e 835 microphone head (dynamic, cardioid) from Sennheiser evolution series for multi-purpose application. Further discription see paragraph ew 312 G3.ew 345 G3 Vocal SetComplete plug & play wireless microphone set with easy-exchangeable e 845 microphone head (dynamic, supercardioid) from Sennheiser evolution series for multi-pur p ose application. Further discription see paragraph ew 312 G3.ew 365 G3 Vocal SetComplete plug & play wireless microphone set with easy-exchangeable e 865 microphone head (electret-condenser, supercardioid) from Sennheiser evolution series for multi-purpose application. Further discription see paragraph ew 312 G3.SySTEMRF frequency range ................................................516.....865 MHzTransmission/receiving frequencies ...................1,680Frequency banks ..................................................... 20 (factory presets)6 (user presets)Presets .......................................................................24 max.Switching bandwidth .............................................42 MHzCompander ...............................................................HDXSignal-to-noise ratio ..............................................> 115 dB(A)THD, total harmonic distortion ............................< 0.9 %RECEIvERAF Frequency response..........................................25…18,000 HzAntenna connectors ...............................................BNC, 50 OhmAudio outputs .......................................................... X LR: +18 dBu max6.3 mm jack: +10 dBu maxDimensions ...............................................................212 x 202 x 43 mmWeight .......................................................................980 gTRANSMITTERRF output power .....................................................10/30 mW switchableOperating time ........................................................typ. 8hInput voltage range ................................................1.8 v lineInput voltage range ................................................2.4 v lineDimensions ...............................................................82 x 64 x 24 mmWeight .......................................................................~ 160 gMICROPHONETransducer; Microphone type ...............................permanent polarizedAF sensitivity ...........................................................1.6 mv/PaFrequency response ...............................................80.....18,000 HzPick-up pattern ........................................................omni-directionalContinued on page 5EM 300Modulation ...............................................................wideband FMRF frequency range ................................................ 516 – 558, 566 – 608, 626 – 668, 734 –776, 780 – 822, 823 – 865 MHz Transmission/receiving frequencies ...................1,680, tuneable in steps of 25 kHzReceiving frequencies ............................................ 1,680 frequencies, tuneable in steps of 25 kHz20 frequency banks, each with up to 24 factory-preset channels,intermodulation-free20 frequency banks with up to 24 user programmable channelsSwitching bandwidth .............................................42 MHzNominal/peak deviation .......................................±24 kHz/±48 kHzReceiver principle ....................................................true diversitySensitivity (with HDX, peak deviation) .............< 2 μv for 52 dBA rms S/NAdjacent channel rejection ...................................typ. ≥ 75 dBIntermodulation attenuation ...............................typ. ≥ 70 dBBlocking .....................................................................≥ 75 dBSquelch ...................................................................... O ff, 5 to 25 dBμv, adjustable in steps of 2 dBPilot tone squelch ...................................................can be switched offAntenna inputs .......................................................2 BNC socketsCompander system .................................................Sennheiser HDXEQ presets (switchable, affect the line and monitor outputs):Preset 1: “Flat”Preset 2: “Low Cut” ................................................–3 dB at 180 HzPreset 3: “Low Cut/High boost” .......................... –3 dB at 180 Hz+6 dB at 10 kHzPreset 4: “High Boost” ...........................................+6 dB at 10 kHzS/N ratio (1 mv, peak deviation) ........................≥ 115 dBATHD .............................................................................≤ 0.9 %AF output voltage (at peak deviation,1 kHz AF) .................................................................. ¼” (6.3 mm) jack socket (unbalanced): +12 dBuXLR socket (balanced): +18 dBuAdjustment range of audio output level ........... 48 dB, adjustable in steps of 3 dB +6 dB gain reserveTemperature range .................................................–10 °C to +55 °CPower supply............................................................12 vPower consumption:...............................................350 mADimensions ...............................................................approx. 202 x 212 x 43 mmWeight (incl. batteries) .........................................approx. 980 gIn compliance with .................................................. C E, FCC, ETS 300422, ETS 300445MAINS UNITInput voltage............................................................100 to 240 v~, 50/60 HzPower/current consumption ................................max. 120 mAOutput voltage ........................................................12 vSecondary output current .....................................400 mATemperature range .................................................–10 °C to +40 °CIn compliance with .................................................. C E, FCC, IC, ETS 300422, ETS 300445Continued on page 6SK 300 and SKM 300Modulation ...............................................................wideband FMRF frequency range ................................................ 516 – 558, 566 – 608, 626 – 668, 734 –776, 780 – 822, 823 – 865 MHz Transmission/receiving frequencies ...................1,680, tuneable in steps of 25 kHzReceiving frequencies ............................................ 1,680 frequencies, tuneable in steps of 25 kHz20 frequency banks, each with up to 24 factory-preset channels, intermodulation-free6 frequency banks with up to 24 user programmable channelsSwitching bandwidth .............................................42 MHzNominal/peak deviation .......................................±24 kHz/±48 kHzFrequency stability .................................................≤ ±15 ppmRF output power at 50 O......................................typ. 10/30 mW, switchablePilot tone squelch ...................................................can be switched offAF characteristicsCompander system .................................................Sennheiser HDXAF frequency responseSK ................................................................................ m icrophone: 80 –18,000 Hzline: 25 –18,000 HzSKM ............................................................................80 –18,000 HzS/N ratio (1 mv, peak deviation) ........................≥ 115 dBATHD .............................................................................≤ 0.9 %Max. input voltage (SK) microphone/line ........3 vrmsInput impedance (SK) microphone/line ...........40 k O, unbalanced/1 M OInput capacitance (SK) ..........................................switchableAdjustment range of input sensitivity .............. S K: 60 dB, adjustable in steps of 3 dBSKM: 48 dB, adjustable in steps of 6 dBIn compliance with .................................................. C E, FCC, IC, ETS 300422, ETS 300445OvERALL DEvICETemperature range .................................................−10 °C to + 55 °CPower supply ........................................................... 2 AA size batteries, 1.5 v orBA 2015 accupackNominal voltage .....................................................2.4 vCurrent consumption: at nominal voltage ........typ. 180 mA (30 mW)with switched-off transmitter .............................≤ 25 μAOperating time .......................................................typ. 8 hrsDimensions ............................................................... S K: approx. 82 x 64 x 24 mmSKM: approx. Ø 50 x 265 mmWeight (incl. batteries) ......................................... S K: approx. 160 gSKM: approx. 450 gIn compliance with .................................................. C E, FCC, IC, ETS 300422, ETS 300445Continued on page 7Microphones (SK 300)ME 2ME 3-ew ME 4Microphone type .............................condenser condenser condenserSensitivity .........................................20 mv/Pa 1.6 mv/Pa40 mv/PaPick-up pattern ................................omni-directional cardioid cardioidMax. SPL ............................................130 dB SPL150 dB SPL120 dB SPL Microphone heads (SKM 300)MMD 835-1MMD 845-1MMK 865-1Radio microphone type .................dynamic dynamic condenserSensitivity ......................................... 2.1 mv/Pa 1.6 mv/Pa 1.6 mv/PaPick-up pattern ................................cardioid super-cardioid cardioid/super-cardioid,switchableMax. SPL ............................................154 dB SPL154 dB SPL152 dB SPL Frequency response .......................80.....18,000 Hz80.....18,000 Hz80.....18,000 HzDELIVERY INCLUDES for ew 312 / ew 322 / ew 352 G31 EM 300 G3 rack-mount receiver1 SK 300 G3 bodypack transmitter1 ME2 clip-on microphone (omni-directional) or1 ME 4 clip-on microphone (cardioid) or1 ME 3-ew headset microphone (cardioid)1 GA 3 rack mount1 NT2 power supply unit2 Antennas2 AA batteries1 Instruction manualDELIVERY INCLUDES for ew 335 / ew 345 / ew 365 G31 S KM 300-835 handheld transmitterwith cardioid dynamic head or1 S KM 300-845 handheld transmitterwith super-cardioid dynamic head or1 S KM 300-865 handheld transmitterwith super-cardioid condenser head1 EM 300 G3 rack receiver1 MZQ 1 microphone clip1 NT2 power supply unit2 Antennas1 GA 3 Rack mount kit2 AA batteries1 Instruction ManualPOLAR PATTERN0510152025dB30°30°60°60°90°90°120°150°120°150°0°180°125 Hz 250 Hz 500 Hz 1000 Hz2000 Hz 4000 Hz 8000 Hz 16000 HzMMD 835-1MME 865-1MMD 845-10510152025dB30°30°60°60°90°90°120°150°120°150°0°180°125 Hz 250 Hz 500 Hz 1000 Hz2000 Hz 4000 Hz 8000 Hz 16000 Hz0510152025dB30°30°60°60°90°90°120°150°120°150°0°180°125 Hz 250 Hz 500 Hz 1000 Hz2000 Hz 4000 Hz 8000 Hz 16000 HzME 3-ewME 4-ew0510152025dB30°30°60°60°90°90°120°150°120°150°0°180°125 Hz 250 Hz 500 Hz 1000 Hz2000 Hz 4000 Hz 8000 Hz 16000 Hz0510152025dB30°30°60°60°90°90°120°150°120°150°0°180°125 Hz 250 Hz 500 Hz 1000 Hz2000 Hz 4000 Hz 8000 Hz 16000 HzPRODUCT VARIANTSew 312 G3 Presentation Set Cat. No. ew 312 G3-A-EU 516 – 558 MHz 503112 ew 312 G3-A-US 516 – 558 MHz 503330 ew 312 G3-G-EU 566 – 608 MHz 503331 ew 312 G3-G-US 566 – 608 MHz 503332 ew 312 G3-B-EU 526 – 668 MHz 503333 ew 312 G3-B-US 526 – 668 MHz 503334 ew 312 G3-C-EU 734 –776 MHz 503335 ew 312 G3-C-US 734 –776 MHz 503336 ew 312 G3-D-EU 780 – 822 MHz 503337 ew 312 G3-D-EU-X 780 – 822 MHz 503338 ew 312 G3-D-UK 780 – 822 MHz 503339 ew 312 G3-E-EU 823 – 865 MHz 503340 ew 312 G3-E-EU-X 823 – 865 MHz 503341 ew 312 G3-E-UK 823 – 865 MHz 503342 ew 312 G3-GB 606 – 648 MHz 504649 ew 322 G3 Presentation Set Cat. No. ew 322 G3-E-UK 823 – 865 MHz 503357 ew 322 G3-A-EU 516 – 558 MHz 503113 ew 322 G3-A-US 516 – 558 MHz 503345 ew 322 G3-G-EU 566 – 608 MHz 503346 ew 322 G3-G-US 566 – 608 MHz 503347 ew 322 G3-B-EU 626 – 668 MHz 503348 ew 322 G3-B-US 626 – 668 MHz 503349 ew 322 G3-C-EU 734 –776 MHz 503350 ew 322 G3-C-US 734 –776 MHz 503351 ew 322 G3-D-EU 780 – 822 MHz 503352 ew 322 G3-D-EU-X 780 – 822 MHz 503353 ew 322 G3-D-UK 780 – 822 MHz 503354 ew 322 G3-E-EU 823 – 865 MHz 503355 ew 322 G3-E-EU-X 823 – 865 MHz 503356 ew 322 G3-GB 606 – 648 MHz 504650 ew 352 G3 Presentation Set Cat. No. ew 352 G3-A-EU 516 – 558 MHz 503114 ew 352 G3-A-US 516 – 558 MHz 503360 ew 352 G3-G-EU 566 – 608 MHz 503361 ew 352 G3-G-US 566 – 608 MHz 503362 ew 352 G3-B-EU 526 – 668 MHz 503363 ew 352 G3-B-US 526 – 668 MHz 503364 ew 352 G3-C-EU 734 –776 MHz 503365 ew 352 G3-C-US 734 –776 MHz 503366 ew 352 G3-D-EU 780 – 822 MHz 503367 ew 352 G3-D-EU-X 780 – 822 MHz 503368 ew 352 G3-D-UK 780 – 822 MHz 503369 ew 352 G3-E-EU 823 – 865 MHz 503370 ew 352 G3-E-EU-X 823 – 865 MHz 503371 ew 352 G3-E-UK 823 – 865 MHz 503372 ew 352 G3-GB 606 – 648 MHz 504651ew 335 G3 Vocal Set Cat. No. ew 335 G3-A-EU 516 – 558 MHz 503115 ew 335 G3-A-US 516 – 558 MHz 503375 ew 335 G3-G-EU 566 – 608 MHz 503376 ew 335 G3-G-US 566 – 608 MHz 503377 ew 335 G3-B-EU 526 – 668 MHz 503378 ew 335 G3-B-US 526 – 668 MHz 503379 ew 335 G3-C-EU 734 –776 MHz 503380 ew 335 G3-C-US 734 –776 MHz 503381 ew 335 G3-D-EU 780 – 822 MHz 503382 ew 335 G3-D-EU-X780 – 822 MHz 503383 ew 335 G3-D-UK 780 – 822 MHz 503384 ew 335 G3-E-EU 823 – 865 MHz 503385 ew 335 G3-E-EU-X823 – 865 MHz 503386 ew 335 G3-E-UK 823 – 865 MHz 503387 ew 335 G3-GB 606 – 648 MHz 504652 ew 345 G3 Vocal Set Cat. No. ew 345 G3-A-EU 516 – 558 MHz 503116 ew 345 G3-A-US 516 – 558 MHz 503390 ew 345 G3-G-EU 566 – 608 MHz 503391 ew 345 G3-G-US 566 – 608 MHz 503392 ew 345 G3-B-EU 526 – 668 MHz 503393 ew 345 G3-B-US 526 – 668 MHz 503394 ew 345 G3-C-EU 734 –776 MHz 503395 ew 345 G3-C-US 734 –776 MHz 503396 ew 345 G3-D-EU 780 – 822 MHz 503397 ew 345 G3-D-EU-X780 – 822 MHz 503398 ew 345 G3-D-UK 780 – 822 MHz 503399 ew 345 G3-E-EU 823 – 865 MHz 503400 ew 345 G3-E-EU-X823 – 865 MHz 503401 ew 345 G3-E-UK 823 – 865 MHz 503402 ew 345 G3-GB 606 – 648 MHz 504653 ew 365 G3 Vocal Set Cat. No. ew 365 G3-A-EU 516 – 558 MHz 503117 ew 365 G3-A-US 516 – 558 MHz 503405 ew 365 G3-G-EU 566 – 608 MHz 503406 ew 365 G3-G-US 566 – 608 MHz 503407 ew 365 G3-B-EU 526 – 668 MHz 503408 ew 365 G3-B-US 526 – 668 MHz 503409 ew 365 G3-C-EU 734 –776 MHz 503410 ew 365 G3-C-US 734 –776 MHz 503411 ew 365 G3-D-EU 780 – 822 MHz 503412 ew 365 G3-D-EU-X780 – 822 MHz 503413 ew 365 G3-D-UK 780 – 822 MHz 503414 ew 365 G3-E-EU 823 – 865 MHz 503415 ew 365 G3-E-EU-X823 – 865 MHz 503416 ew 365 G3-E-UK 823 – 865 MHz 503417 ew 365 G3-GB 606 – 648 MHz 504654RECOMMENDED ACCESSORIESCat. No. ME 4-ew – Clip-on microphone,cardioid, black 503156 AM 2 – Antenna Mount kit 009912 CC 3 – System Case 503168L 2015 – Charging unit 009928 BA 2015 – Rechargeable battery pack 009950 ASA 1 – Active antenna splitter 503165 NT 1-1 – plug-in mains unit forASA 1 & L 2015 E U: 503158US: 503873UK: 503874 NT 3-1 – Plug-in mains unit for L 2015 E U: 503159US: 503876UK: 503877 A 1031-U – Antenna 004645A 2003-UHF – Directional Antenna 003658 AB 3 – Antenna booster 505550 Ear Set 1-ew – Ear-worn microphone,omni, black 504232 Ear Set 1-ew-3 – Ear-worn microphone,omni, beige 504237 Ear Set 4-ew – Ear-worn microphone,cardioid, black 504236 Ear Set 4-ew-3 – Ear-worn microphone,cardioid, beige 504234 MKE 1-ew – Clip-on microphone,omni-directional, black 502876 MKE 1-ew-1 – Clip-on microphone,omni, white 502877 MKE 1-ew-2 – Clip-on microphone,omni, brown 502878 MKE 1-ew-3 – Clip-on microphone, beige 502879 MKE 2-ew Gold – Clip-on microphone,omni, black 009831 MKE 2-ew-3 Gold – Clip-on microphone,omni, beige 009832 MKE 40-ew – Clip-on microphone,cardioid, black 500527Cat. No. HSP 4-ew – Headworn microphone,cardioid, black 009864 HSP 4-ew-3 – Headworn microphone,cardioid, beige 009867 HSP 2-ew – Headworn microphone,omni, black 009866 HSP 2-ew-3 – Headworn microphone,omni, beige 009872 CI 1 – Instrument cable 503163ew 335 / ew 345 / ew 365 G3 Vocal SetsMMD 835-1 – evolution microphone head 502575 MMD 845-1 – evolution microphone head 502576 MME 865-1 – evolution microphone head 502581 MZW 1 – Windshield 004839 KEN 2 – Identification rings 530195 LA 2 – Charging adapter forhandheld microphones 503162 CC 3 – System case 503168Sennheiser electronic GmbH & Co. KG Am Labor 1, 30900 Wedemark, Germany 0 4 / 1 3 S e n n h e i s e r i s a r e g i s t e r e d t r a d e m a r k o f S e n n h e i s e r e l e c t r o n i c G m b H & C o . K G . w w w . s e n n h e i s e r . c o m . C o p y r i g h t ©0 4 / 2 0 1 3 . A l l r i g h t s r e s e r v e d . E r r o r s a n d o m i s s i o n s e x c e p t e d .Contact your local Service Partner:。
Software Defined Radio Measurement Solutions

1.0 Introduction ....................................................................................................................22.0 Software Radio Architectures .....................................................................................33.0 Software Radio Impairments .......................................................................................54.0 Bit Error Rate Testing ....................................................................................................65.0 Multiple Domain Analysis Tools .................................................................................76.0 Vector Signal Analysis ..................................................................................................97.0 Vector Signal Analysis Across Multiple Domains .................................................118.0 Digital VSA ....................................................................................................................139.0 Signal Generation Tools for SDR ...............................................................................15 10.0 Simulation Tools and Instrument Connectivity ......................................................17 11.0References (19)Software Defi ned Radio Measurement SolutionsOscilloscope Logic Analyzer Spectrum AnalyzerInteroperability concerns and high costs, associated with existing communication systems, are driving the integration of software defi ned radio (SDR) technology into commercial and military wireless systems. On the commercial side,the mobile communications industry has seen the parallel evolution of a wide variety of incompatible radio standards throughout the world and even within specifi c geographies. Consumers want the ability to use the most reliable service in a given location. Developing a truly international handset is nearly impossible. Multi-mode handsets provide some relief, but with increased cost, higher power consumption and limited fl exibility as standards evolve.On the military side, yesterday’s model of using indepen-dent communication systems for different tactical func-tions simply doesn’t fi t with the network-centric warfare model being pursued by virtually every modern military. Today forces are fast, mobile, tightly integrated and closely coordinated, which requires the ability to quickly and freely communicate across organizational boundaries. Addition-ally, maintaining today’s diverse systems requires a large support footprint with its corresponding high cost. A similar situation exists for public-service organizations, such as law enforcement and fi re departments, who also use a large number of non-interoperable radios at federal, state, and local levels.In the original context, the term software defi ned radio (SDR) refers to a reconfi gurable radio based solely on soft-ware and having the analog-to-digital conversion occurring directly at the antenna [1, 2]. While practical limitationsin the current performance of analog-to-digital convert-ers (ADC) prevent sampling wideband waveforms directly at the antenna, the development of a radio system that can change its operating frequency, modulation, operat-ing bandwidth and network protocol without the need to change the system hardware is highly desirable.As digital signal processing (DSP) and ADC speeds in-crease, more of the signal processing will be done digitally. Where a radio once processed analog signals from the RF through to baseband, newer SDR-based systems implement a digital baseband and digital IF with an evolution of mov-ing the transition between the digital and analog domains as close to the antenna as technically possible. However more digital content in the radio leads to new measure-ment and troubleshooting challenges for the traditional RF designer who now has to deal with the digital signals and bus structures of reconfi gurable logic. In addition, DSP and digital hardware designers are now faced with understand-ing and measuring signal quality in terms of high-level func-tional performance that includes vector diagrams and error vector magnitude (EVM) metrics.This application note introduces the SDR architecture and types of analysis tools that are available when measuring the digital, analog and RF sections of a software radio. This note also shows how vector signal analysis tools can be applied across multiple domains when designing and trou-bleshooting SDR components and systems. Also discussed are vector signal generation and how software radio design has infl uenced the connection of this predominately RF/ analog hardware into the digital domain. Lastly, this note will introduce how instruments and radio hardware can be directly integrated into advanced software simulation tools.1.0 Introduction2.0 Software Radio ArchitecturesThe ideal SDR radio architecture would allow digitizationof the full bandwidth covering all the radio channels to be supported by the terminal. The speeds of today’s ADCs limit the operating bandwidth of the digital front-end; therefore most radios require an RF to IF conversion. The ADC’s performance (i.e. bit resolution, sampling rate) and the architecture for the RF to IF conversion require a tradeoff between performance, power consumption and cost. An example of a practical SDR receiver using IF sampling is shown in fi gure 1. The fi gure shows two possible locations for the ADC within the downconversion path. In one case, the ADC is placed after the IQ demodulator. This confi guration requires more analog circuitry and two ADC channels at the baseband or low-frequency IF. As ADC speeds improved, the ADC may also be placed before the IQ demodulator. In this case, the IQ demodulation occurs completely in the digital domain. This second approach removes much of the analog circuitry and the architecture begins to approach that of an ideal SDR as the transition point to digital occurs much closer to the antenna. Alternate receiver architectures use a direct-conversion of the RF signal to baseband in one step. In this case the fi rst local oscillator (LO1), as shown in fi gure 1, is eliminated and the second oscillator (LO2)is tuned to the RF carrier frequency. The direct-conversion receiver eliminates the need for an IF and an image fi lter at the RF front-end; however, they require good LO rejection and two ADCs: one for the I channel and one for the Q channel. After digitization of the IF or baseband, the digitized waveforms enter the DSP domain where channelization and signal processing are performed. If digitization occurs before the IQ demodulator, the demodulator is fully digital and uses a digital LO, digital mixers, and decimation fi lters. The IQ demodulator converts the input signal into a complex, I and Q, baseband representation. These signals are then digitally fi ltered to pass the desired channel. The last step involves symbol demodulation into bits, de-interleaving and decoding. In comparison to more traditional receiver architectures, the SDR performs channelization in the digital domain and therefore can be reconfi gured as requiredwithout the need to change the radio hardware. Figure 1. Simplifi ed block diagram of a typical SDR receiverThe radio designer must decide the appropriate architecture for the target performance and cost. Because of different requirements between the RF and digital sections, a complete radio may be constructed from two or more modules or ICs. Figure 2 shows how the transceiver of a software radio can be partitioned into a mixed signal RFIC or module and a baseband circuit. The baseband circuit will contain the DSP algorithms for data recovery using the specifi ed network protocol. It’s the use of adaptable software algorithms, as typically found in fi eld programmable gate arrays (FPGA) and/or DSP chips, that makes the SDR reconfi gurable “on the fl y”. With the current trend to place the ADCs into the mixed-signal RF front-end, communication between the front-end and baseband occurs over a digital bus. Communication over this bus can be serial or parallel depending on the application. One example of a commercial digital interface is the DigRF standard [3], which was created by a consortium of chipset manufacturers that defi ned a standard for serial communication in 2.5G and 3G cellular chipsets. Whether standards-based or a proprietary implementation, a digital interface between the front-end and baseband requires special signal analysis and signal generation tools to properly characterize this interface. By combining Agilent’s signal analysis tools and signal generation products, designers can comprehensively characterize the behavior of their SDR system from baseband to antenna.Figure 2. SDR chipset with digital interface3.0 Software Radio ImpairmentsA practical software radio system can suffer from a number of impairments that can give rise to error generation and degradation in overall system performance. Typical RF impairments can be created by LO phase noise, amplifi er compression, spurious signals, fi lter tilt, fi lter ripple, channel fading and co-channel interference. Analog impairmentsat the IF can have many of the same issues as RF signals but also include modulator and demodulator imbalances between the I and Q channels. These RF and analog impair-ments are not confi ned to SDR systems but may be found in any digital radio system. The fact that the SDR uses such a large portion of digital logic and DSP introduces additional impairment concerns that may not be found in a traditional radio design. For example, the performance of a software radio is largely a function of the ADC and DAC used to transition signals between the analog and digital domains. The bit resolution and operating bandwidth of the ADC may be the limiting factor when determining the dynamic range of the SDR receiver. The performance of the ADCis also tied to the RF or analog signals driving it. A high-power blocking signal operating in an adjacent channelwill limit the dynamic range of the ADC, as this interfering signal could be more than 80 dB above the desired signal. Including the fact that the ADC creates its own internally generated spurious signals due to quantization effects; the system performance is largely limited by the ADC performance under these dynamic conditions. There are numerous other RF, analog and digital impairments that can degrade system performance. Table 1 provides a list of some of the more common problems that may exist in a practical SDR design.Table 1. Typical Radio ImpairmentsA popular technique for evaluating the overall performance of a digital radio system is a loop-back Bit Error Rate (BER) test. BER testing is typically considered the ‘acid test’ when evaluating the performance of a data link. It measures how well the data bits are transported through the transmitter, across the channel and out of the receiver. Bit error rate testers (BERTs) input a known data stream into the trans-mitter and compare the data emerging out of the receiver to fi nd the ratio of errors to the total bits sent (see fi gure 3). There are many different BERTs available for various data rates and digital data formats. Some instruments, such as the Agilent ESG signal generator, have an optional built-in BER tester. These fl exible signal generators can inject modulated signals at various points in the system and measure the BER using the recovered data stream. Other BER test confi gurations use recorded waveforms that can be played into the receiver under a variety of conditions. The use of recorded waveforms provides a good platform for interoperability testing among the various equipment vendors. Several techniques for capturing and creating these waveforms will be provided later in this application note. Unfortunately the diagnostic capabilities of loop-back BER testing are very limited. This system-level measurement of end-to-end performance cannot pinpoint the root causes of impairments in the system. For example, a poor BER performance may result from compression of the power amplifi er in the transmitter or incorrect symbol timing in the DSP logic of the receiver’s demodulator. In either case, a BER measurement does not link the degradation in performance to the cause of the impairment.The limitations found in loop-back BER testing really come from the nature of the signal impairments. Some signal impairments are additive in nature and are spread across the wireless system. Complicating matters further, many signal impairments add in different ways. Linearity distor-tion and group-delay impairments are deterministic and add arithmetically, while phase-noise impairments are probabilistic and add geometrically. Many loop-back tests remove impairments during the data recovery process and that can inadvertently lead to false measurement results. For example, a direct digital modulator to demodulator loop-back test might result in a reasonable error rate. Next, an IF loop-back test is performed and presents excessive errors, possibly indicating a problem within the IF. However, to assume so could be a false conclusion, as smaller impairments at the IF and at the modulator may have summed up to an out of specifi cation (i.e., bit error) condition. The only way to correctly ensure consistent error rate performance is to use system budgets that allocate a maximum amount of permissible modulation impairment from each element in the wireless chain. To do this, we must use more sophisticated measurements than loop-back BER tests. This is why design engineers customarily use more advanced measurements than simple BER tests to effectively characterize the complex effects of signal impairments. The next several sections in this application note discuss the various types of instruments and signal analysis tools that can be used to measure and characterize the performance at different domains within the software radio.4.0 Bit Error Rate Testing Figure 3 Bit Error Rate (BER) test confi guration5.0 Multiple Domain Analysis ToolsHaving a wide variety of signal types with the emphasis on signals operating in the digital domain make it necessary to have a set of fl exible diagnostic tools for examining the quality of the signal as it moves across each of the three domains: digital, analog and RF. Typically instruments are specifi cally designed to measure a signal with a certain format. For example, the data bus of the digital hardware is typically probed using a logic analyzer. The logic analyzer displays the binary encoding of the numerous signal lines that digitally represent the signal to be transmitted. Figure 4 shows a block diagram of an SDR transmitter with a logic analyzer measurement taken at the input to the I-channel DAC. Since the logic analyzer can support multiple bus measurements at one time, it is possible to simultaneously measure both the digital I and Q channels data busses by attaching multiple measurement pods to probe the device under test. Agilent has several application notes that ex-plain the basics of logic analysis and probing [4, 5]. Another signal format consideration usually encountered with SDR designs is analog I and Q baseband signals that require two independent analog measurements. Wide-band multi-channel oscilloscopes are ideal for measuring analog I and Q waveforms. Figure 4 also shows a measurement of the analog I and Q waveforms after the DAC using an Agilent Infi niium oscilloscope.Figure 4. Block diagram of a SDR transmitter and associated multiple domain measurementsA very useful feature supported by some logic analyzers, such as the Agilent 16900, is the ability to import an analog waveform from an oscilloscope. The analog waveform is transferred from the scope to the logic analyzer through a LAN connection between the two instruments. Integrationof these two measurement systems can be helpful when triggering on analog events and precisely correlating them to DSP-related activities. Figure 5 shows an example using the logic analyzer with the scope for time-correlated measurements. The fi gure shows the logic analyzer measurement for the digital bus associated with the DAC inputs. The fi gure also shows the analog representation of this signal based on the digital information measured by the logic analyzer. The lower two curves are the time correlated oscilloscope measurements from the output of the two DACs. This technique provides a comparative analysis of the two digital IQ signals with the two analog IQ waveforms. Synchronized markers provide precise timing measurements between the digital and analog waveforms. Note that the logic analyzer measurements shown in fi gure 5 are actually analog representations created from the measurementsof the digital signals. The logic analyzer creates these representations from the bus measurements once the user associates the multiple data bus lines with a single measurement channel. The third signal format is the RF waveform that contains the information modulated as symbols onto the RF carrier. Typical measurements relating to this signal type are spectrum measurements including RF center frequency, bandwidth, harmonics, spurious and adjacent channel power to name a few. A spectrum analyzer or vector signal analyzer (VSA) is an ideal instrument for measuring the signal ampli-tude over frequency. Figure 4 also shows a typical spectrum measurement using the Agilent 89600 VSA. The VSA is also a powerful analysis tool in that measurements canbe displayed in combinations of time, frequency, amplitude and modulation. A vector signal analyzer, such as the Agilent 89600 VSA, has many similarities to a SDR since the VSA software can be confi gured to provide demodulation analysis over a wide range of digital signaling formats covering most of today’s wireless standards including WiMAX, Mobile WiMAX, 802.11a/b/g, Bluetooth, TETRA, W-CDMA/HSDPA, GSM/EDGE, 1xEV-DO, cdma2000/1xEV-DV, TD-SCDMA, PHP, Digital Video, UWB and RFID.Figure 5. Logic analyzer display showing imported oscilloscope measurements6.0 Vector Signal AnalysisThe power in VSA measurements comes from its large array of demodulators, fi lters, displays, and analysis tools that make it ideally suited for evaluating and troubleshooting modulated signals within the SDR system. The VSA usesa popular measurement called the error vector magnitude (EVM) to characterize the quality of the modulated signal. EVM is the difference between a reference vector and the actual received signal vector. EVM allows the engineer to compare the modulation with a known “good” modulation generated in the test equipment. Because EVM provides an aggregate summary of many types of modulation impairments, it is ideal for detecting issues with a modulated signal. EVM provides a convenient metric to quickly compare signal degradation between points in the block diagram. Modulation imperfections can be identifi ed and traced back to their fundamental mechanism by careful examination of EVM measurements. EVM can pinpoint where signals are degraded with much greater accuracy than top-level loop-back BER testing. To measure EVM, vector signal analyzers must generate a reference signal for the desired modulation. The reference signal is created by demodulating the incoming waveform and generating an ideal signal to be used to compare with the incoming signal. Subtracting the measured signal from the ideal signal provides the error vector. Agilent’s VSAs offer EVM measurements and other quality metrics for a wide variety of modulation types and other variations such as fi ltering and symbol rates. This includes many popular modulation formats such as AM, FM, PM, QPSK, QAM and OFDM.Figure 6 shows a set of typical VSA measurements for a demodulated QPSK signal. The display in the upper left shows the vector diagram of the complex recovered signal at all moments in time. The vector diagram can be used to quickly observe if the signal has been properly modulated. The display in the lower left shows the EVM as a function of time. For the purposes of accurately recovering transmitted data from a signal, the error only matters to a receiver at the symbol times, and that is how some EVM specifi cations are written. However an R&D or test engineer may be very interested in the error between signals, as it may indicate the source of the impairment such as the case where improper baseband fi ltering is applied in the digital portion of the SDR transmitter. The display in the upper right of fi gure 6 shows error vector spectrum. This spectrum is calculated by taking the FFT of the error vector time trace. This spectrum display can reveal the spectral content of the unwanted signals that drive the modulated carrier apart from its ideal path. If those error components are deterministic, they will show up in the error vector spectrum as discrete line spectra.Measuring these spectra can give added insight into the nature and origin of the signal impairments. The lower right display shows a summary table of the demodulated signal. This table can be the most powerful of the digital demodulation tools. Here, demodulated bits can be seen along with error statistics for all of the demodulated symbols. Modulation accuracy can be quickly assessed by reviewing the RMS value of the EVM. The display at the lower right shows both the demodulated symbol table and a table of calculated error parameters. Note that EVM and magnitude/phase error are calculated in terms of peak and RMS values for the measured burst. The peak error value includes the symbol where the error occurred, potentially a very helpful result for fi nding the source of signal impairments. Other composite error parameters are also derived and shown, including frequency offset, quadrature error and IQ offset. Agilent supplies additional application notes that will be helpful to engineers looking to develop a further understanding of the measurement capability found in the VSA [6, 7,10].Figure 6. Typical VSA demodulation measurement7.0 Vector Signal Analysis Across Multiple DomainsWhile basic digital logic and analog analysis is very useful for troubleshooting bit level and timing anomalies in the baseband, it does not provide any insight into how the qual-ity of this signal will ultimately affect the signal transmitted from the radio. By combining VSA software tools with logic analyzer and oscilloscope measurements, it now becomes possible to perform the full range of vector signal analysis using data captured across the full range of high-perfor-mance instrumentation.Continuing from the previous SDR transmitter example as shown in fi gure 4, the VSA software is now integrated into all three types of test instrumentation and a comparative analysis is preformed at the digital, analog and RF domains. Figure 7 shows the vector diagrams at all three domains using the same vector signal analysis tool. Also shownis the measured RMS value of the EVM for each signal. Higher quality signals result in lower EVM values. Thefi gure shows how the EVM changes as the signal transi-tions across the various domains in the SDR transmitter. It is observed in this example that the EVM is approximately 0.4% and 0.5% in the digital and analog domains respec-tively but takes a large jump to 5.0% in the RF domain when measured after the power amplifi er. This large degradation in EVM would alert the engineer that a problem exists somewhere between the measured analog section and the power amplifi er output. For this example, it was determined that the EVM was 1% before the power amplifi er and fur-ther analysis showed that the amplifi er was going into com-pression. After a re-design in the output amplifi er, the EVM dropped below 1.4%. It is expected that some degradation in EVM will occur as the signal is transitioned between domains but this unexpected large increase allowed the engineer to pinpoint the exact problem area using the VSA tools. One important fact to note is that using a common VSA tool would yield the best comparative analysis across domains because a common algorithm is used to determine the reference signal from the measured signals. Uncertainty in the results may be introduced when measurementsare made on different types of vector analysis equipment, which may use different software algorithms.Figure 7. Block Diagram of a SDR transmitter and VSA measurements across multiple domainsAnother example of using the VSA as a comparative and troubleshooting tool across signal domains is shown in fi gure 8. This fi gure shows the connections between the test equipment and the I and Q channels directly before and after the ADC. On the analog side of the ADC, the VSA software is confi gured to vectorially add the two independent oscilloscope measurements into a complex form using the C1+jC2 function available in the Agilent 89600 VSA software. By mathematically combining these two waveforms, the VSA operates as an ideal software modulator that reas-sembles the I and Q waveforms into a modulated signal. The reassembled signal can now be examined using all the available VSA tools. Figure 8 shows a measurement of the modulated spectrum at the input to the ADC. The spectrum looks correct and is free of any close-in spurious responses. The next step is to measure the output spectrum from the two ADCs. In this case a logic analyzer, such as the Agilent 16800, is used to probe the digital bus lines leaving the ADCs. Once again, these separate I and Q channelmeasurements are reassembled into a modulated spectrum. Figure 8 shows the measured spectrum taken from the out-put of the ADCs. This time the VSA displays strong clock spurs near the desired spectrum. These clock spurs could introduce errors in the bit recovery process if not properly fi ltered in the digital domain. Without advanced cross format diagnostic techniques, such an impairment would be very diffi cult to identify with such clear certainty.In some cases, it is hard to determine the quality of asignal just by looking at a spectrum response. For example, the spectrum plot on the left of fi gure 8 shows a clean response free of any signifi cant in-band and out-of-band spurious signals. After demodulating this signal using a VSA, such as the Agilent 89600, it was found to have an unexpectedly high EVM value of 3.6%. For the system being tested, the EVM should fall below 1%, therefore, additional demodulation analysis was required. Examining the vector diagram, it was observed that the distribution of constella-tion points followed a doughnut shaped pattern as shown on the left in fi gure 9. This type of distribution is indicative of a spurious interference. If the only interference were additive noise, the constellation points would follow a random distribution. Continuing the analysis using an EVM spectrum, as shown on the right of fi gure 9, it was found that a spurious signal, offset 11kHz from the carrier, was the cause for the high EVM value. In-channel spurious, such as this, combines with the modulated signal, and is rarely high enough to be detected in the frequency domain (as shown on the left plot in fi gure 8). Using the variety of measurement tools available on the VSA, such as the vector diagram and EVM spectrum, engineers can troubleshoot and uncover numerous impairments found across the digital, analog and RF domains.Figure 9. Vector diagram (left) and EVM spectrum (right) of a QPSK modulated signal corrupted by an in-band spurious signalFigure 8. Block diagram of SDR receiver and VSA spectrum measurementsbefore and after the ADC8.0 Digital VSAWith the trend in the wireless industry to implement more of the software radio’s functionality in the digital domain, the ADC and DAC are moving closer to the antenna. As a result, more of the testing and troubleshooting are performed using a logic analyzer. Bridging the signal formats from analog to digital also requires the ability to correctly interpret the signal value from a digital bus. Some signals use a two’s compliment encoding and others use an offset binary encoding, each requiring a different interpretation. Correctly decoding the format of the signal is also important when applying VSA analysis tools directly to logic analyzer measurements [8]. Fortunately, modern VSA tools, suchas the Agilent 89600 series, can directly interface with the logic analyzer system software to easily set the encoding format assignments.Another signal format consideration usually encountered with SDR designs is that I and Q baseband signals require two independent measurement ports, one for each channel. Logic analyzers can support multiple bus measurementsby using multiple measurement pods to probe the device under test. Increasing the number of bus measurements increases the number of Input and Output (I/O) pins that must be probed resulting in an increase in board size and cost. More importantly, probing is often complicated when using FPGAs, as many of the desired test points may not be readily accessible outside of the chip. Since I/O pinson the FPGA are typically an expensive resource, there are a relatively small number available for debug. This limits internal visibility as, historically, one pin has been required for each internal signal to be probed. To access different internal signals, the FPGA design must be modifi ed and recompiled in order to route these signals to the available external pins. This is a time-consuming process and could also affect the timing of the FPGA design. Fortunately, itis possible to multiplex internal test points onto a shared external bus using a dynamic probe assignment tool. This multiplexing tool is part of the additional design core, such as the Agilent Trace Core 2 (ATC2), that is compiled into the FPGA design [9, 10].The ATC2 design core is embedded in the FPGA design and offers access to as many as 128 test points per external pin without altering the internal timing of the design. The test points can be arranged in banks to facilitate rapid switching between different I and Q test points. The probe banks are automatically confi gured and multiplexed from the logic analyzer’s display. Combining the ATC2 design core, the logic analyzer and the VSA analysis software, it becomes possible to compare the modulation and spectral properties of the SDR’s digital baseband at all points within the FPGA design.。
5968-4632E逻分探头
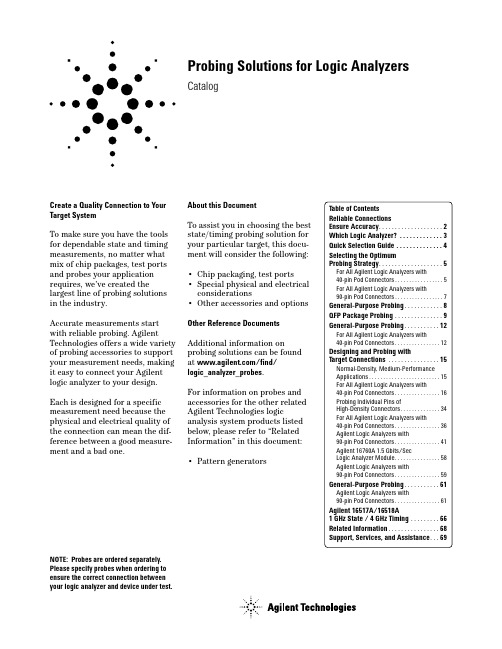
Probing Solutions for Logic Analyzers CatalogCreate a Quality Connection to Your Target SystemTo make sure you have the tools for dependable state and timing measurements, no matter what mix of chip packages, test ports and probes your application requires, we’ve created the largest line of probing solutions in the industry.Accurate measurements start with reliable probing. Agilent Technologies offers a wide variety of probing accessories to support your measurement needs, making it easy to connect your Agilent logic analyzer to your design. Each is designed for a specific measurement need because the physical and electrical quality of the connection can mean the dif-ference between a good measure-ment and a bad one.About this DocumentTo assist you in choosing the best state/timing probing solution for your particular target, this docu-ment will consider the following:•Chip packaging, test ports •Special physical and electrical considerations•Other accessories and options Other Reference Documents Additional information on probing solutions can be found at /find/logic_analyzer_probes.For information on probes and accessories for the other related Agilent Technologies logic analysis system products listed below, please refer to “Related Information” in this document:•Pattern generatorsNOTE: Probes are ordered separately. Please specify probes when ordering to ensure the correct connection between your logic analyzer and device under test.2•ImpedanceHigh input impedanceensures minimum intrusion on your circuit. Although many probes might be acceptable for lower frequencies, capacitive loading becomes significant at higher frequencies. The Agilent Technologies probing products perform over a wide frequency spectrum.•RuggednessProbes with qualitymechanical design provide solid electrical connections.Intermittent open circuits would only add one more variable to your debugging equation. Agilent probes are mechanically designed to relieve strain and ensure rugged, reliable connection.•Immunity to NoiseElectromagnetic noise can corrupt data captured by the logic analyzer. Agilent probing solutions aredesigned for a high immunity to transient noise.•PerformanceAgilent logic analyzers have front-end circuitry that supports the state and timing specifications of the analyzer. This circuitry,together with the Agilentprobing solutions described in this document, will accurately capture the target signals at the specified clock rates.Reliable Connections Ensure AccuracyOther ConsiderationsPhysical connection compatibility between various Agilent probes may allow you to mix and match a variety of probes and accessories. However, a probe accessory designed for slower clock speeds will not deliver high-speed target performance simply because it is used with a higher speed analyzer module.Also, the serial connection of multiple probe leads and/or accessories will degrade signal integrity.3Agilent logic analyzers have two methods of connection to the probes. One uses a 3M-style connector with 2 rows of 20 pins on 0.1-inch centers, as illustrated in Figure 1.1. Probes for these analyzers are identified in this document as “for analyzers with 40-pin pod connectors.”The other style uses a 90-pin,high-density connector, asillustrated in Figure 1.2. Probes for these analyzers are identified in this document as “for analyzers with 90-pin pod connectors.”Currently available Agilent logic analyzers in these two groups are as follows:Which Logic Analyzer?Figure 1.1. 40-pin pod connector Figure 1.2. 90-pin pod connector40-pin pod connector 16911A 16910A1680, 1690 series benchtop analyzersQuick selection guide45Go to page 9 for a discussion of Agilent’s QFP package probingsolutions for logic analyzers.Go to page 12 for a discussion of Agilent’s flying-lead logic analysis probes and accessories for logic analyzers.Go to page 16 for a discussion ofAgilent’s target connector solutions forlogic analyzers with 40-pin pod connectors.Using Processor/Bus Specific ProbesRefer to Processor and Bus Support forAgilent Technologies Logic Analyzers,publication number 5966-4365E at:/find/pnbsThat document will tell you what additionalprobing accessories you need to connectlogic analyzers with 40-pin pod connectorsto the analysis probes.67Go to page 61-65 for a discussion of Agilent’s flying lead probe sets for logic analyzers with 90-pin pod connectors.Connecting to Individual IC Pins, Test Points, Browsing or Solder Attach to Components, Traces or VIAsGo to page 54 for the target connection probing solutions for logic analyzers with90-pin pod connectors. Go to page 41 for connectorless solutions for logic analyzers with 90-pin pod connectors.Designing Connections Directly into the Target System8General-Purpose ProbingWedge AdaptersThe Agilent Technologies Wedge technology provides very reliable probing of a few channels on 0.5mm and 0.65mm pitch QFPs.No clear area is required around the device. Each Wedge of the probe slides between the legs of the QFP. The side of each Wedge probe contacts the package legs.An insulation core electrically isolates the sides of each Wedge (see Figures 2.1 and 2.2). Various 3-signal, 8-signal, and 16-signalprobes are available (see Table 1).Figure 2.1. Three-signal Wedgeelectrical connectionFigure 2.2. Eight-signal and 16-signal Wedge (16-signal Wedge has a common ground plane)Miscellaneous Probing Accessories The ferrite core assembly can be added to the probe cable to sup-press EMI and RFI noise that can corrupt the measurement.Figure 2.3. Ferrite core assembly, 16555-60001IC Leg Number Number Model Spacing of Signalsof Wedges Number in Pack0.5 mm 31E2613A 0.5 mm 32E2613B 0.5 mm 81E2614A 0.5 mm 161E2643A 0.65 mm 31E2615A 0.65 mm 32E2615B 0.65 mm81E2616A 0.65 mm161E2644ATable 1. Wedge probe adapter9Figure 3.2. Elastomeric probing solutionFigure 3.1. Locator tool aligningretainer on the deviceLocator toolRetainerTQFP ICconnections to the pins on its respective side of the QFP device.Additional retainers and locator tools are also available. A kit of five retainers and adhesive is available as option #201. The locator tool is option #202. These option numbers apply to any of the listed elastomeric probe adapter model numbers, for example, Agilent E5374A #202.Package Pin Pitch Elastomeric Probe Adapter 1/4 Flex Adapter 144-pin TQFP 0.5 mm E5336A E5340A 144-pin PQFP/CQFP 0.65 mm E5361A E5340A 160-pin PQFP/CQFP 0.65 mm E5373A E5349A 160-pin TQFP 0.5 mm E5377A E5349A 176-pin TQFP 0.5 mm E5348A E5349A 208-pin PQFP/CQFP 0.5 mm E5374A E5371A 240-pin PQFP/CQFP0.5 mmE5363AE5371AIf your target contains ASICs,FPGAs, or other devices in an industry-standard QFP configura-tion, Agilent Technologies has a series of elastomeric probes from which you can choose. Agilent’s state-of-the-art elastomeric probing technology offers an inexpensive, convenient, and reliable solution for 0.5mm and 0.65mm high-density TQFP/CQFP/PQFP packages.The elastomer material on the probe makes contact between the probe and the pins of a device.Embedded on the surface of the elastomer are redundant connec-tions for each pin, which ensure a reliable and rugged connection.A locator tool, included with the probe adapter, correctly aligns the retainer to the device. A small amount of adhesive on the bottom of the retainer holds the retainer firmly to the device. After the adhesive is set, the locator tool can be removed. The elastomeric probe adapter then attaches to the device, held in place by the retainer and its knurled nut. Five retainers, a locator tool, and adhesive are included with each elastomeric probe adapter.Additional AccessoriesQuarter flex adapters, shown in Figure 3.2, are available to bring the signals from the elastomeric probe adapter to general-purpose headers for easy connection to logic analyzers, oscilloscopes, or other test equipment. Four 1/4flex adapters are required to view all signals on a device. Each 1/4 flex adapter providesElectrical characteristics for this Array probing technology are listed in Table 3.Note:The Agilent logic analyzer probes are connected to the adapters shown in this section. The target system impedance load is increased slightly (see Table 3). Fast transition times (< 2 - 3 ns) may suffer some loss of signal fidelity.The probe adapters require a minimal “keep out” area around the device, as shown in the dimension tables of Figures 3.3and 3.4.10QFP Package Probing1112E5383A 17-Channel Single-Ended Flying Lead ProbeIdeal when only a few lines may need to be probed or probe points are distributed across a target.The E5383A includes a set of 20IC test clips and five ground leads.Logic AnalysisGeneral-Purpose ProbesGeneral-purpose probing requires connecting probe leads to individual signal lines. This method is most convenient for a small to moderate number of signals, very flexible, and can be used in conjunction with other probing methods.Note:Any probed signal linemust be able to supply a minimum of 600 mV to the probe with the specified loading.The Standard Probing System The standard probing system consists of IC clips, probe leads,probe housing and probe cable.Because it is passive, the stan-dard probing system is smaller,lighter, and much easier to use than active probing systems. This passive probing system is similar to a probing system used on a high frequency oscilloscope. It consists of an isolation network (as shown in Figure 4.1) at the probe tip and a shielded resistive transmission line.The advantages of this system are:•High input impedance. See Figure 4.1.•Signal ground at the probe tip for high-speed signals.•Inexpensive, removable probe tip assemblies.Probe Leads and Lead SetsProbe leads are configured into lead sets, which can probe 16data channels with ground, one clock channel, and a common ground. A 17-channel probe lead set (E5383A) is shown in Figure 4.2, along with the replace-ment part numbers for individual components in Figure 4.3.Each probe lead is a 12-inch, twisted-pair cable connected to the probe cable at the probe hous-ing (see Figure 4.3). The probe tip includes a signal lead, a connec-tor for a ground lead, and the isolation network.The signal and ground leads can be connected directly to the target system. This requires installing 0.63 mm (0.025 in)square pins, or round pins with a diameter of between 0.66 mm (0.026 in) and 0.84 mm (0.033 in)directly on the board. An IC test clip can also be used. The same specifications apply for the pin dimensions of the test clip. (See Figure 4.6 for IC test clipsavailable from Agilent.)Figure 4.1. Probe tip Isolation network and equivalent loadFigure 4.2. E5383A 17-channel probe lead setIC ClipsThe surface-mount device IC clip with twin hooks (part number 5090-4833, containing 20 IC clips) is designed for fine surface-mounted component leads. The twin hook 0.5 mm IC clip (part number 10467-68701, containing four 0.5 mm IC clips), is very use-ful for 0.5mm pitch components. See Figure 4.5.The E2421A kit contains one each: 8-pin, 14-pin, 16-pin, 20-pin, 24-pin, and 28-pin SOIC test clips. See Figure 4.6.The E2422A kit contains one each: 20-pin, 28-pin, 44-pin,52-pin, 66-pin, and 84-pin QUAD IC test adapters. See Figure 4.6. GroundingThere are three methods of grounding the probe system. First, the entire probe lead set can be grounded through the common ground. This requires only one connection, but is not recommended because it will cause poor signal fidelity in systems with fast transition times. The recommended method is to individually ground each probe lead. This yields optimal signal fidelity and is required for signals with faster transition times (< 4 - 5 ns).For moderate rise times(greater than 2 ns), it may be acceptable to ground every other (or every fourth) ground connection to the target.Figure 4.4. Connecting IC clips and ground leads to probesFigure 4.5. SMD IC clip and 0.5 mm IC clipFigure 4.6. Typical IC test clips available in E2421A SOIC kit (left) andE2422A QUAD kit (right)13Signal Line LoadingAny probed signal line must be able to supply a minimum of600mV (unless noted otherwise —see probe of interest) to the probe tip while the probe is connected to the system. The maximum input voltage of each probe is±40 volts peak (unless noted oth-erwise — see probe of interest). Probe CablesThe probe cable (see Figure 4.7 and Table 4) contains 16 signallines and two clk lines, two +5volt power lines, and ground linesfor each of the signal/clock and power lines. All of these lines are contained in a 4.5-foot cable. The probe cable is included with the logic analyzer. The cable grounds are chassis (earth) grounds, not “floating” grounds. The two+5volt power lines can be used to power active probing systems. Consult the specifications for the individual logic analyzers or logic analyzer cards for the maximum allowable current through each+5 volt power supply.Caution:These +5 volt power lines MUST NOT be connected to the target’s power supply. Caution:Be careful when using straight wire probe leads, one common ground, or RC networks located far from the target. These circumstances increase the impact of analog effects such as crosstalk and EMT susceptibility, which contribute to measurement errors.Logic Analyzer01660-6160516555-6160616710-6160316715-61601 Stand Alone or Module16550A x16554A x16555A/D x16556A/D x16557D x16710A x16711A x16712A x16715A x16716A x16717A x16718A x16719A x16740 Series x16750A/B x16751A/B x16752A/B x16910A x16911A x1670 Series x1680 Series x1690 Series xTable 4. Probe cables supplied with Agilent logic analyzersFigure 4.7. Logic analyzer probe cable14Normal-Density, Medium-Performance ApplicationsIn some cases, you may not have a standard QFP package on the target available for probing access, or your device may be available only in BGA packaging. Agilent recommends that targets with probing constraints have connectors designed into the prototype versions of the product for effective hardware and soft-ware debug. The following should be considered when designing with connectors:•Select the appropriate connec-tor technology for your targetspeed and target density.•Carefully select all lines for routing to the connectors thatmay be needed for debug.•Group the lines at eachconnector for your probingconvenience. For example,Agilent may have written aninverse assembler for yourdevice that has a preconfig-ured signal order. Beforedesigning, refer to the docu-mentation for this inverseassembler for essential signallines and order.•Keep the routing to connectors as short as possible to mini-mize target impact and provide accurate data.•Examine the impact of probing isolation networks designedinto the target vs. the isolation network products offered byAgilent Technologies.An isolation network must belocated between the target andthe logic analyzer. It can belocated on the target board inthrough-hole or SMT parts; orit can be attached to the logicanalyzer cable with the probeleads (the isolation network ismolded into the end of the probe);or the Agilent01650-63203 isola-tion adapter with self containedisolation networks can be used.Probe leads can be used withconnectors but are not the mostconvenient method. Direct con-nection of the connectors withthe analyzer cable (isolation net-work parts on the target) or witha probe or isolation adapter is thefaster, more convenient method.15High-Density, High-Performance ProbesAgilent Pro Series Soft Touch Connectorless Logic Analyzer Probes Agilent Technologies has devel-oped connectorless logic analyzer probes based on soft touch probing technology. Connectorless logic analyzer probing removes the connector that is traditionally attached to the target board and replaces it with an array of probe pads. This reduces the probe load on the target by eliminating the loading associated with the physical body of the connector. Additionally, this streamlines the design flow by eliminating the need to assign a logic analyzer connector to the bill of material of your board, procuring those connectors and then having them loaded onto your board. Agilent’s soft touch connectorless probes use micro spring-pin tech-nology to provide reliable contact which is not dependent on the planarity of the PC board or the plating processes used to fabri-cate the board. No special clean-ing processes are required whenusing Agilent’s soft touch probes.The new Agilent Technologies ProSeries soft touch connectorlessprobes offer a 30% smaller foot-print than the original soft touchprobes and are the basis for theindustry standard connectorlessprobing footprint.The probes use a retention modulethat ensures soft touch pin-to-PCboard pad alignment and holdsthe probe in place while in use.The Pro Series soft touch uses a“top-side” mountable retentionmodule. The retention module ismounted on the same side of theboard as the probing footprint sothere is no need to access theback-side of the board. Becausethere is no requirement for theretention module pins to extendbeyond the back-side of theboard, the retention module iscompatible with virtually anyboard thickness.E5404A Pro Series Soft TouchConnectorless ProbeThe E5404A is a 34-channelsingle-ended Pro Series soft touchconnectorless probe compatiblewith all Agilent logic analyzersthat have a 40-pin pod connector.It is capable of acquiring data atthe maximum rates of the logicanalyzer it is connected to.Features•No connector on thetarget board•Top-side mount retentionmodule•Industry-standardconnectorless footprint•34 channels, single-endedclock and data•Extremely low, <0.7pF,equivalent load capacitance•Capable of data rates >2.5Gb/s(maximum rate dependent onanalyzer used)•500mV p-p minimumsignal amplitude•Robust and reliable softtouch technologyUnused clock inputs can be usedas data inputs.The E5404A (used with logic ana-lyzers with a 40-pin cable connec-tor) uses the same footprint,pinout, and retention module asthe E5406A Pro Series soft touchconnectorless probe (used withlogic analyzers with a 90-pincable connector).A kit of five retention modules isshipped with each Pro Series softtouch probe. Additional kits canbe ordered using Agilent partnumber E5403A.Figure 5.1. “Top-side” mountable retention module.16Figure 5.2. Agilent E5394A soft touch probe connection Logic analyzer probe cables (40-pin pod connector)E5394A Soft Touch Connectorless ProbeThe E5394A is a 34-channel single-ended soft touch connec-torless probe compatible with all Agilent logic analyzers that have a 40-pin pod connector. It is capable of acquiring data at the maximum rates of the logic analyzer it is connected to. The probe has the following inputs:•32 single-ended data inputs •two single-ended clock inputs •< 0.7pf input capacitance •500 mV p-p minimum signal amplitudeUnused clock inputs can be used as data inputs.The E5394A (used with logic analyzers with a 40-pin pod con-nector) uses the same footprint, pinout and retention module as the E5390A single-ended soft touch connectorless probe (used with logic analyzers with a 90-pin pod connector).A kit of five retention modulesis shipped with each soft touch probe. Additional kits can be ordered using Agilent part number E5387-68701.E5396A Half-Size Soft TouchConnectorless ProbeThe E5396A is a small spacesaving probe compatible with allAgilent logic analyzers that havea 40-pin cable connector. It is a17-channel, single-ended probecapable of capturing data atthe maximum rates of the logicanalyzer it is connected to. Theprobe has the following inputs:•16 single-ended data inputs•one single-ended clock input•<0.7 pf equivalent loadcapacitance•500 mV p-p minimum signalamplitudeThe unused clock input can beused as a data input.The E5396A (used with logicanalyzers with a 40-pin cable con-nector) uses the same footprint,pinout, and retention module asthe E5398A single-ended softtouch connectorless probe (usedwith logic analyzers with a 90-pincable connector).More information about softtouch connectorless probesis available on the web at/find/softtouch.1718Probe DimensionsThe following figures showdimensions, footprint, and pinout information you will need to design your target system board for use with the Agilent ProSeries soft touch probes.Figure 5.3. E5404A probe dimensionsFigure 5.4. Pro Series soft touch retention module dimensionsFigure 5.5. Pro Series soft touch side-by-side dimensionsProbe and Retention Module DimensionsThe following dimensions show the Pro Series soft touch probe attached to the retention module.The retention module is mounted on the PC board.Top view E5394ATop view E5396AFigure 5.6. E5394A and E5396A soft touch probe dimensions1920Retention Module Dimensions The soft touch probes areattached to the PC board using a retention module which ensures pin-to-pad alignment and holds the probe in place. A board thickness of up to 2.54mm (0.100in.) is recommended.Insert the retention module into the board, noting the keying pin,and solder the four alignment pins to the backside of the board.Probe and Retention Module DimensionsThe following dimensions show the soft touch probe attached to the retention module. The retention module is mounted onthe PC board.Figure 5.7. Retention module dimensionsFigure 5.8. Side-by-side dimensions17-channel retention module dimensions34-channel retention module dimensions17-channel probe and retention module dimensions34-channel probe and retention module dimensionsFigure 5.9. Pro Series soft touch footprint dimensions (see drawing notes).Figure 5.10. Pad numbers for E5404/06A 34-channelsingle-ended probes.2122Probe Footprint DimensionsUse these probe footprintdimensions for the PC boardpads and holes for attaching theretention module.Soft touchHalf-size soft touchFigure 5.11. Footprint dimensions23Pinout for the E5394A Single-Ended Array Soft Touch ProbeThe following graphic and tableshow the E5394A single-endedsoft touch probe pad numbersand logic analyzer pod inputs.Figure 5.12. Pinout24E5396A 17-channelSingle-Ended Probe Logic AnalyzerSignal Name Pad #Channel PodD1A1➞1Whichever pod D3A2➞3is plugged into Ground A3the E5396AD5A4➞5probeD7A5➞7Ground A6D9A7➞9D11A8➞11Ground A9D13A10➞13D15A11➞15Ground A12NC A13➞n/a E5396A 17-channelSingle-Ended Probe Logic AnalyzerSignal Name Pad #Channel PodD0B1➞0Whichever pod D2B2➞2is plugged into Ground B3the E5396AD4B4➞4probeD6B5➞6Ground B6D8B7➞8D10B8➞10Ground B9D12B10➞12D14B11➞14Ground B12Clock B13➞Clock2526Equivalent Probe LoadsThe following probe loadmodels are based on in-circuit measurements made with an Agilent 8753E 6GHz network analyzer and an Agilent 54750A TDR/TDT using a 50Ωtestfixture. The following schematic accurately models the probe load out to 6GHz.Figure 5.14. Simple (does not include capacitive coupling between channels or inductance of the spring pins)Figure 5.15. Complex (includes capacitive coupling between channels and inductance of spring pins)High Density, High Performance Agilent Technologies has developed high-density probing solutions based on the 100-pin Samtec and AMP Mictor 38-pin connectors. The Agilent probes and adapter cables, E5346A,E5339A, E5351A, and E5385A provide a connection strategy to route your important signals to the Agilent logic analyzer. Simply design the connectors onto the board for the critical signals such as address, data, and status bits. The connectors consume a minimal amount of board space. Each connector provides 32 channels of logic analysis per connector and two clocks (unused clocks can be used as data). Connectors for use with the E5385A, E5346A, E5339A and E5351A can be purchased directly from AMP, Samtec, or Agilent Technologies. See the “Related Information” at the end of this document.Figure 5.17. E5346A, E5351A, E5339A mechanical dimensionsFigure 5.16. E5385A 100-pin probe mechanical dimensions2728Agilent Technologies E5346A, E5339A, and E5385A Probes The E5346A, E5339A, and E5385A probes include the required isolation networks for the logic analyzer right at the probe tip, close to the target. The E5346A and E5385A are designed to acquire signals with peak-to-peak amplitude as low as 500 mV. The E5339A is designed to acquire signals as small as 250mV peak-to-peak. Figure 5.18shows the equivalent load for the E5339A, and Figure 5.19 shows the equivalent load for the E5346A. Figure 5.20 shows the equivalent load for the E5385A.To use the E5346A, E5339A, or E5385A at high clock speeds, the following design guidelines should be observed:•Calculate the electrical length of the probe hookup stub.•For PC board material with E r =4.9, use a propagation delay of 160 ps/inch.•Check that the propagation delay of the probe hookup stub is less than 20% of the bus sig-nal risetime (T r ). If it is, the E5346A, E5339A, or E5385A can be used for connection.For example, if E r =4.9, a 2.5 inch probe hookup stub generates a propagation delay of 400 ps. If T r is > 2 ns, the E5346A,E5339A, or E5385A is a viable probing choice.The E5346A and E5339A use the AMP Mictor 38-pin connector.The E5385A uses a 100-pin connector manufactured by Samtec. Agilent recommends the E5394A or E5385A for new applications, due to the reduced input capacitive loading and improved isolation between adjacent channels.For additional information on designing connectors into a target system, refer to the following documents:Agilent Technologies E5346A/E5351A Installation Note E5346-92014/litweb/pdf/E5346-92014.pdf Probe/Adapter Cable Agilent Technologies E5339A Installation Note E5339-92002/litweb/pdf/E5339-92002.pdf Low Voltage ProbeAgilent Technologies E5385A ProbeInstallation Note E5385-92001/litweb/pdf/E5385-92001.pdfFigure 5.19. E5346A input equivalent loadFigure 5.18. E5339A input equivalent loadk1.5Figure 5.20. E5385A input equivalent loadEquivalent LoadFigure 5.22. Agilent E5339A, E5346A, and E5385A design rules29Figure 5.23. Agilent E5385A connection and pinout ShroudSee Table 5on page 33for partnumberE5385A 100-Pin Probe Pin AssignmentsSignal Pin Number SignalGround12GroundDo Not Connect34Do Not ConnectGround56GroundOdd D078Even D0Ground910GroundOdd D11112Even D1Ground1314GroundOdd D21516Even D2Ground1718GroundOdd D31920Even D3Ground2122GroundOdd D42324Even D4Ground2526GroundOdd D52728Even D5Ground2930GroundOdd D63132Even D6Ground3334GroundOdd D73536Even D7Ground3738GroundOdd D83940Even D8Ground4142GroundOdd D94344Even D9Ground4546GroundOdd D104748Even D10Ground4950GroundOdd D115152Even D11Ground5354GroundOdd D125556Even D12Ground5758GroundOdd D135960Even D13Ground6162GroundOdd D146364Even D14Ground6566GroundOdd D156768Even D15Ground6970GroundNC7172NCGround7374GroundNC7576NCGround7778GroundOdd D16P/7980Even D16P/Odd CLK Even CLKGround8182GroundNC8384NCGround8586GroundNC8788NCGround8990GroundNC9192NCGround9394GroundGround9596Ground+5V9798+5V+5V99100+5V30。
ARTISAN TECHNOLOGY GROUP 商业说明书

OverviewThe National Instruments Educational Laboratory Virtual Instrumentation Suite (NI ELVIS) is a LabVIEW-based design and prototyping environment or university science and engineering laboratories.NI ELVIS consists o f LabVIEW-based virtual instruments,a multifunction data acquisition device and a custom-designed benchtop workstation and prototyping board.This combination provides a ready-to-use suite of instruments found in all educational laboratories.Because it is based on LabVIEW and provides complete data acquisition and prototyping capabilities,the system is ideal for academic coursework from lower-division classes to advanced project-based curriculum.Applications•Circuit design and analysis for learning analog and digital electronics•Measurements in mechanical,electrical,biomedical, and physics laboratories•Teaching data acquisition and signal conditioning •Live demonstration of concepts in a lecture hall •Communications and control applications for Electrical and Mechanical Engineering•Hands-on LabVIEW trainingIntegrated Tools for University Laboratories•Offers integrated,multi-instrument functionality •Combines instrumentation,data acquisition and prototyping station •Virtual Instrument Suite •Oscilloscope,DMM,FunctionGenerator,Variable PowerSupply,Bode Analyzer,ArbitraryWaveform Generator,DSA,Voltage/Current Analyzer •LabVIEW source code provided •Completely open and customizable in the LabVIEW environment •Data storage in Excel or HTML Workstation•Short-circuit andhigh-voltage protection •Variable power supplies •Manual or programmatic control •Function generator•Manual or programmatic control •±15 and +5 V supply available •BNC inputs for DMM and scope •Detachable,customizable prototyping board•Affordable for student ownership •Designed to fit in a2 or 3-ring binderNI Educational Laboratory Virtual Instrumentation Suite (NI ELVIS)LabVIEW VIs• Oscilloscope• DMM• Function Generator • Arbitrary WaveformGenerator• Bode Analyzer• Dynamic Signal Analyzer • Power SupplyInstrumentationCircuit DesignSignal ProcessingCommunicationControlsMechatronics Prototyping Board WorkstationLabVIEW ApplicationNI Data Acquisition BoardCurriculum ApplicationsNI Educational Laboratory Virtual Instrumentation Suite (NI ELVIS)AnalyzersOscilloscopeTwo channelsData storage, cursors, auto scalingMax input bandwidth.......................................50 kHz 1Max sampling rate...........................................500 kHz / channel 1Range................................................................±10 VInput resolution................................................12 or 16 bits1Specification depends on Data Acquisition device functionality.Bode AnalyzerFrequency and phase plotsFrequency range and step controlLogarithmic or linear frequency spacing Data storage, cursors, auto scalingFrequency range............................................... 5 Hz to 35 kHz 11Specification depends on Data Acquisition device functionality.Dynamic Signal AnalyzerInput range.......................................................±10 VInput resolution................................................12 or 16 bitsImpedance AnalyzerMeasurement frequency range........................ 5 Hz to 35 kHz2-Wire Current Voltage AnalyzerVoltage range...................................................±10 V Current range...................................................±10 mA3-Wire Current Voltage AnalyzerNPN BJT transistor onlyData storage, cursors, auto scalingMaximum Collector Voltage.............................10 V Minimum base increment................................15 µADigital MultimeterResistanceAccuracy...........................................................1%Range................................................................ 5 Ωto 3 M ΩDC VoltageAccuracy...........................................................0.3%Range................................................................±20 V Input impedance...............................................1M ΩAC VoltageAccuracy...........................................................0.3%Range................................................................±14 V mrsCurrentDC accuracy......................................................0.25% ±3 mA 1AC accuracy......................................................0.25% ±3 mA 1Range................................................................±250 mA Shunt resistance..............................................0.5 ΩMaximum common mode voltage....................±20 V Common mode rejection..................................70 dB1Proper null correction at the common mode voltage can reduce ±3 mA error to 200 µA noise.CapacitanceAccuracy...........................................................2%Range................................................................50 pF to 500 µF Test voltage range............................................1V ppContinuityResistance threshold........................................15 ΩmaxInductanceAccuracy...........................................................1%Range................................................................100 µH to 100 mH Test frequency..................................................950 Hz Test frequency voltage.....................................1 V ppDigital I/ODigital input resolution....................................8 bits Digital output resolution..................................8 bits Digital addressing............................................ 4 bitsSourceFunction GeneratorManual or software controlSine, triangle, square waveforms Frequency sweep TTL sync pulse out AM, FM modulationFrequency range............................................... 5 Hz to 250 kHz Frequency accuracy..........................................3%Output amplitude.............................................±2.5 V Software amplitude resolution........................8 bits Offset range.....................................................±5 V AM voltage.......................................................10 V max Amplitude modulation......................................Up to 100%FM Voltage.......................................................10 V max Amplitude flatnessTo 50 kHz...................................................0.5 dB To 250 kHz.................................................3 dBArbitrary Waveform GeneratorTwo channelsOne-shot or continuous generation Waveform editorAmplitude.........................................................±10 VFrequency range...............................................DC to 100 kHz 1Output drive current.........................................25 mA max Output impedance.. (1)Slew rate..........................................................1.5 V/µs1Specification depends on Data Acquisition device functionality.Power Supplies±15 V SupplyOutput current...........................................Fused at 500 mA Ripple and noise........................................1%Line regulation...........................................0.5% max 5 V SupplyOutput current...........................................Fused at 2 A Ripple and noise........................................1%Line regulation...........................................0.5% maxVariable power supplies 0 to +12 V and -12 VRipple and noise........................................0.25% Software resolution...................................7 bitsCurrent limiting..........................................0.5 V at 130 mA, 5 V at 275 mA, 12 V at 450 mASpecificationsIntegrated Tools for University Laboratories2National Instruments •Tel: (800) 433-3488•***********•For Desktop ComputersNI ELVIS/PCI-6251 Bundle ........................................778748-02Qty 1-4:$1995 each Qty 5+:$1495 each For Laptop ComputersNI ELVIS/DAQCard-6062E Bundle ............................779064-01Qty 1-4:$2260 each Qty 5+:$1695 eachIncludes NI ELVIS workstation,DAQ device,cable,and LabVIEW drivers.For individual unit pricing please visit /academic .BUY NOW!For complete product specifications,pricing,and accessoryinformation,call (800) 813-3693 (U.S.only) or go to /academic .Ordering InformationNI Services and Supportapplication lif e cycle – f rom planningand development through deploymentand ongoing maintenance.We of erservices and service levels to meetcustomer requirements in research,design,validation,and manuVisit /services.Training and CertificationNI training is the fastest,most certain route to productivity with our products.NI training can shorten your learning curve,save development time,and reduce maintenance costs over the application lif e cycle.We schedule instructor-led courses in cities worldwide,or we can hold a course at your facility.We also offer a prof essional certif ication program that identif ies individuals who have high levels of skill and knowledge on using NI products. Visit /training.Professional ServicesOur Prof essional Services Team is comprised of NI applications engineers,NI Consulting Services,and a worldwide NI Alliance Partner Program of more than 600 independent consultants andintegrators.Services rangerom start-up assistance toturnkey system integration.Visit /alliance.OEM SupportWe of er design-in consulting and product integration assistance if you want to use our products or OEM applications.For information about special pricing and services for OEM customers, visit /oem.Local Sales and Technical SupportIn of f ices worldwide,our staf f is local to the country,giving you access to engineers who speak your language.NI delivers industry-leading technical support through online knowledge bases,our applications engineers,and access to 14,000 measurement andautomation prof essionals within NI Developer Exchange f orums.Find immediate answers to your questions at /support.We also offer service programs that provide automatic upgrades toyour application development environment and higher levels oftechnical support.Visit /ssp.Hardware ServicesNI Factory Installation ServicesNI Factory Installation Services (FIS) is the fastest and easiest way touse your PXI or PXI/SCXI combination systems right out of the box.Trained NI technicians install the so tware and hardware andconfigure the system to your specifications.NI extends the standardwarranty by one year on hardware components (controllers,chassis,modules) purchased with FIS.To use FIS,simply conf igure yoursystem online with /pxiadvisor.Calibration ServicesNI recognizes the need to maintain properly calibrated devices forhigh-accuracy measurements.We provide manual calibrationprocedures,services to recalibrate your products,and automatedcalibration so tware speci ically designed or use by metrologylaboratories.Visit /calibration.Repair and Extended WarrantyNI provides complete repair services for our products.Express repairand advance replacement services are also available.We o erextended warranties to help you meet project life-cycle requirements.Visit /services.© 2005 National Instruments Corporation. All rights reserved. LabVIEW, National Instruments Alliance Partner, NI, , and SCXI aretrademarks of National Instruments. Other product and company names listed are trademarks or trade names of their respective companies.A National Instruments Alliance Partner is a business entity independent from NI and has no agency, partnership, or joint-venture relationship with NI.National Instruments • Tel: (512) 683-0100 • ***********• (800) 433-348825_4929_35_11_D。
高级导电度分析仪AX430、AX433、AX413和AX436的说明书

Single and Dual Input Analyzersfor High-level ConductivityAX430, AX433, AX413 and AX436■ Cost effective– select one or two Conductivity inputs or combine pH/Redox (ORP) with Conductivity in one analyzer –integral PID controller (AX430)■ Advanced measuring capabilities– conductivity range up to 1,999 mS cm –1– selectable concentration ranges:0 to 15% NaOH, 0 to 18% HCl, 0 to 20% H 2SO 4,0 to 40% H 3PO 4, 0 to 20% NaCl and user-defined ■ Dosing Control functionality – long dose diagnostic alarm – initial charge function■ Reduced installation cost– easy access terminations; reduced panel space ■ High functionality at minimum cost– three alarms and two fully-isolated current outputs – direct linear, reverse acting or bi-linear output ■ Expanded monitoring and control– add-on option board provides a total of five alarm relays and four current outputs– service logbook providing historical data ■ Reduced yearly maintenance costs– 12 to 30V DC option negates the need for costly safety tests ■ Wide range of applicability – regeneration of ion exchangers– municipal water phosphoric acid control– food & beverage product/water interface detection – clean-in-place concentration monitoringMore processing power,higher performanceData SheetSS/AX4CO4_5Single and Dual Input Analyzers for High-level Conductivity AX430, AX433, AX413 and AX436SS/AX4CO4_52The AX400 SeriesAX400 analyzers incorporate the latest technology to provide highly reliable, flexible, feature-packed devices that satisfy a diverse range of process monitoring and control applications.The complete range encompasses solutions for pH/Redox (ORP), conductivity and dissolved oxygen.AX43x analyzers enable continuous measurements of one or two conductivity points with simultaneous local display and retransmission. AX43x is used with the TB4 and AC400* Series of insertion, immersion and flow-through, four-electrode conductivity cells providing measurements with exceptional accuracy and performance.AX400 Series analyzers are available for either wall-/pipe- or panel-mounting and are rated to IP66/NEMA 4X.* Check with factory for availability.High Functionality as StandardAll versions are supplied with two, fully-isolated current outputs as standard, that can be assigned to the measured parameter,sample temperature or any appropriate calculated variables.Three programmable relay set points are available which can also be assigned as required.Innovative features such as a power saving display and a diagnostic current output option all contribute to a low cost of ownership.Plug-and-Produce Expanded ControlAn advanced function card provides an additional two current outputs and two further alarm relays that can be assigned to either measured values or sample temperature.ABB Plug-and-Produce software automatically reconfigures the analyzer if an option board is added later. No user programming is necessary.A real-time clock and logbook are also included making the full-facility versions extremely powerful and versatile.Significantly Reduced Maintenance CostsThe AX400 Analyzers are supplied as standard for 85 to 265V AC operation. There are no inner switches to set.They can also be provided for 24V AC, or 12 to 30V DC, supply and recognize automatically which of the two supplies is being used. 24V DC operation reduces maintenance costs significantly by negating the need for costly, yearly safety tests to ensure compliance with safety procedures.Energy Saving DisplayThe backlit display has been designed to operate in all types of environments and shows both the measured parameter(s) and,on a separate 16-character display line, diagnostic and computed information.On dual-input analyzers both measured parameters are displayed simultaneously.For conservation of energy, the backlight can be set to switch off automatically after 60s of inactivity.Backlight Can be Set to Switch-off When InactiveEasy Access Installation TerminalsE asy access to the terminations ensures rapid and cost-effective installation. The wall-/pipe-mount version has been designed to ensure that cable connection is simple and convenient. Ingress protection of the electronics section is retained even when the terminal compartment is opened.AX400 Termination Chamber Makes Access EasyAX400 OutputsSingle and Dual Input Analyzers for High-level Conductivity AX430, AX433, AX413 and AX436SS/AX4CO4_53Advanced Conductivity and Concentration MonitoringIn addition, these analyzers enable operation directly in terms of concentration: 0 to 15% NaOH, 18% HCl, 20% H 2SO 4,40% H 3PO 4, 20% NaCl and user-defined. This is particularly suited for strength-monitoring of ion exchange regenerant acid and alkali.Cost-effective Control of CIP PlantAX43x conductivity analyzers measure up to 1,999mS cm –1enabling operation in the majority of high concentration processes. Automatic and manual temperature compensations enable effective measurements up to 300°C (572°F).Single and Dual Input Analyzers for High-level Conductivity AX430, AX433, AX413 and AX436SS/AX4CO4_54AX436 Combined Conductivity and pHThe AX436 version measures conductivity and pH with the same analyzer. The option board provides the capability to retransmit conductivity, pH and both sample temperatures. This is particularly useful in the paper industry, reducing the investment in separate instruments, for example, when used on white water or the head box.Simultaneous Conductivity and pH MeasurementDual Input MeasurementSingle and Dual Input Analyzers for High-level Conductivity AX430, AX433, AX413 and AX436SS/AX4CO4_55Long-dose Alarm FunctionAn important diagnostic capability incorporated in AX43x analyzers is the long-dose alarm function. This is useful for occasions when faults occur in the dosing system.The analyzers can be configured to provide an alarm if a set point has not been reached within a specified time. This valuable facility provides a warning that could indicate a loss of dosing chemicals, a leakage or a costly pump failure.Long-dose Alarms Warns of Dosing Systems FaultsInitial Charge FunctionIn some applications, fresh dosing chemical reagent is made up every few days. For example, in bottle-washing plants the caustic solution can become dirty and must be replaced regularly. In the case of a new charge, i.e. making up a fresh reagent dilution, a general long-dose alarm could be initiated before the reagent had attained the correct concentration.AX43x analyzers provide a simple solution by having a pre-configurable Initial Charge function. A simple button press from Initial Charge Function When Making Fresh ReagentSingle and Dual Input Analyzers for High-level Conductivity AX430, AX433, AX413 and AX436SS/AX4CO4_56AX430 Integral P, PI and PID ControlThe single input AX430 analyzers incorporate three-term PID Control, offering three modes of sophisticated control: analog,pulse length (time proportional) and pulse frequency. These are supplied as standard and can be operated in direct- or reverse-acting mode, depending upon the application.Auto/Manual and Bumpless TransferAn auto/manual feature is incorporated for rapid manual access to the control functions. The controller facilitates bumpless transfer between manual and auto modes, providing the measured variable is within the proportional band and some integral action time has been programmed.Current Output Proportional ControlIn this case, the control signal is provided by the 4 to 20mA output of AX430 analyzers rather than using the alarm/control contacts. The magnitude of the current output changes in proportion to the deviation from set point. This method is used generally with motorized valves or when controlling the speed of dosing pumps with a 4 to 20mA proportional input.Pulse-frequency Proportional ControlImpulse pumps dosing chemical reagents are controlled easily by the AX430 analyzer’s pulse-frequency proportional control output. In this case, the pulse length of the alarm/control contact is fixed and the frequency of the delivered pulses increases in proportion to the system error, as set by the proportional band.Diaphragm metering pumps must have a remote pulse input capability in order to utilize this function.Pulse-frequency control in the AX430 analyzer operates by pulsing a relay on for 300ms and off for a period of time determined by the pulse frequency. The pulse frequency (PFr) is adjustable between 1 and 120 pulses per minute. The greater the difference between the measured variable and the set point,the greater the pulse frequency.ExampleIf the pulse frequency is set at 120 pulses per minute and the percentage output is 100% then the pulse rate is 2 pulses per second. If the percentage output is reduced to 50%, the pulse rate falls to one pulse per second.Pulse-frequency Proportional ControlPower Failure RecoveryIn the event of a power failure the user can configure the control mode to be Auto, Manual or Last. This optimizes control conditions on power-up to ensure rapid recovery of process control.Time Proportioning ControlOutput = 0%Output = 50%Output = 100%Energized De-energized EnergizedDe-energizedPermanently De-energized Pulse Frequency = 120 pulses per minute0.3s 0.7ms0.3s 0.2s 0.3s 0.2sSingle and Dual Input Analyzers for High-level Conductivity AX430, AX433, AX413 and AX436SS/AX4CO4_57SpecificationConductivityRangeConductivity Programmable 0.000 to 1999mScm –1(uncompensated)Concentration0.000 to 1.999 digits (user configurable)Selectable concentration ranges 0 to 15% NaOH0 to 18% HCl 0 to 20%H 2SO 40 to 40% H 3PO 40 to 20% NaCl User-defined table Temperature–20 to 300°C (–4 to 572°F )Sensor Full Scale Measurement Ranges(a) TB4 Group A and AC400 cells 0 to 1,999mS cm –1(uncompensated)(b) TB4 Group B cells 0 to 1,999μS cm –1(uncompensated)Minimum span (a)TB4 Group A and AC400 cells 100.0μS cm –1(b)TB4 Group B cells 10.00μS cm –1Concentration 5% of the maximum set concentration range Temperature10°C (50°F)Note . Refer to corresponding data sheets for process limit specifications of TB4 and AC400 cells.Resolution, Display Conductivity(a)TB4 Group A cells 0.1 μS cm –1AC400 cells 0.1mS cm –1(b)TB4 Group B cells 0.01μS cm–1Concentration 0.001 digits(configuration dependent)Temperature 0.1°C (0.1°F)Accuracy, Display Conductivity ± 0.5% measurement range per decade Temperature10°C (21°F)Display temperature range –20 to 300°C (4 to 572°F)Temperature sensor Pt1000 or 3k BalcoTemperature coefficientProgrammable 0 to 9.99%/°C and fixed temperaturecompensation curves (programmable) for acids and neutral salt Reference temperature 25°C (77°F)Dosing control functions Long-dose alarm 0 to 10 mins. (user-configurable)Initial charge function0 to 30 mins. (user-configurable)DisplayTypeDual 5-digit, 7-segment backlit LCD Information16-character, single line dot-matrixEnergy-saving functionBacklit LCD configurable as ON or Auto-Off after 60sLogbook*Electronic record of major process events and calibration data Real-time clock*Records time for logbook and auto-manual functions *Available if option board is fitted Retransmission outputs2 (4 optional) fully-isolated standardRelay Outputs – On/OffNumber of relaysThree, supplied as standardFive, when ordered with option boardNumber of set points3 supplied as standard or 5 with option card fittedSet point adjustmentConfigurable as normal or failsafe high/low, bandwidth alarm (composite high/low) or diagnostic alert Hysteresis of readingProgrammable 0 to 5% in 0.1% increments DelayProgrammable 0 to 60s in 1s intervals Relay contactsSingle-pole changeover Rating 5A, 115/230V AC, 5A DC Insulation2kV RMS contacts to earth/groundAnalog OutputsNumber of current outputs (fully isolated)Two supplied as standard or 4 with option board fitted Output ranges0 to 10mA, 0 to 20mA or 4 to 20mAAnalog output programmable to any value between 0 and 22mA to indicate system failureAccuracy±0.25% FSD, ±0.5% of reading (whichever is the greater)Resolution0.1% at 10mA, 0.05% at 20mASingle and Dual Input Analyzers for High-level Conductivity AX430, AX433, AX413 and AX436SS/AX4CO4_58…Specification…Analog OutputsMaximum load resistance 750Ω at 20mAConfigurationCan be assigned to either measured variable or either sample temperatureDigital CommunicationsCommunicationsProfibus DP (with option board fitted)Control Function – AX430 OnlyController TypeP, PI, PID (Configurable)Control OutputsAnalogCurrent output control (0 to 100%)Time proportioning cycle time1.0 to 300.0s, programmable in increments of 0.1s Pulse frequency1 to 120 pulses per minute, programmable in increments of 1 pulse per minute Controller action Direct or reverseProportional band0.1 to 999.9%, programmable in increments of 0.1%Integral action time (Integral reset)1 to 7200s, programmable in increments of 1s (0 = Off)Derivative0.1 to 999.9s in increments of 0.1s,available only for single set point control Auto/ManualUser-programmableAccess to FunctionsDirect keypad accessMeasurement, maintenance, configuration,diagnostics or service functionsPerformed without external equipment or internal jumpersMechanical DataWall-/Pipe-mount versions IP66/NEMA4XDimensions 192mm high x 230mm wide x 94mm deep (7.56 in. high x 9.06 in. wide x 3.7 in. deep)Weight 1kg (2.2 lb)Cable Entry Types Standard 5 or 7 x M20 cable glands N. American7 x knockouts suitable for 1/2 in. Hubble glandPanel-mount versions IP66/NEMA4X (front only)Dimensions 96mm x 96mm x 162mm deep (3.78 in. x 3.78 in. x 6.38 in. deep)Weight 0.6kg (1.32 lb)Power SupplyVoltage requirements 85 to 265V AC 50/60 Hz24V AC or 12 to 30V DC (optional)Power consumption <10VAInsulationMains to earth (line to ground) 2kV RMSEnvironmental DataOperating temperature limits –20 to 65°C (–4 to 149°F)Storage temperature limits –25 to 75°C (–13 to 167°F)Operating humidity limitsUp to 95%RH non condensingEMCEmissions and immunity Meets requirements of:EN61326 (for an industrial environment)EN50081-2EN50082-2Hazardous area approvalsCENELEC ATEX IIG EEx n IIC T4Pending FM non-incendive Class I Div. 2 Groups A to D Pending CSA non-incendive Class I Div. 2 Groups A to DPendingSafetyGeneral safety EN61010-1Overvoltage Class II on inputs and outputs Pollution category 2LanguagesLanguages configurable:English Italian French SpanishGermanSingle and Dual Input Analyzers for High-level ConductivityAX430, AX433, AX413 and AX436SS/AX4CO4_5 Overall Dimensions9Single and Dual Input Analyzers for High-level ConductivityAX430, AX433, AX413 and AX436SS/AX4CO4_5 Electrical Connections10Single and Dual Input Analyzers for High-level Conductivity AX430, AX433, AX413 and AX436SS/AX4CO4_511Ordering Information4X A .g .e ,1V P r o f t i g i d e d o c e h t 614X A ,e l b i s s i m r e p 16.e l b i s s i m r e p t o n **.)2V P (e l b a i r a V s s e c o r P d n o c e S s a d e t c e l e s s i m c /S m 999,1o t 0n e h w g n i s u o h t n u o m -l e n a p n i e l b a l i a v a t o n P D s u b if o r P †.n o i t a z i l a c i p o r t f o y t i l i b a l i a v a r o f y r o t c a f k c e h CSingle and Dual Input Analyzers for High-level Conductivity AX430, AX433, AX413 and AX436SS/AX4CO4_5S S /A X 4C O 4I s s u e 5ABB LimitedOldends Lane, Stonehouse Gloucestershire GL10 3TA UKTel:+44 (0)1453 826661Fax:+44 (0)1453 829671ABB Inc.Analytical Instruments9716 S. Virginia St. Ste., E Reno, Nevada 89521USATel:+1 775 850 4800Fax:+1 775 850 4808ABB has Sales & Customer Supportexpertise in over 100 countries worldwide The Company’s policy is one of continuous product improvement and the right is reserved to modify theinformation contained herein without notice.Printed in UK (08.05)© ABB 2005。
芯片分析器Manual-Analyzer

集成电路自动化分析再设计系统ChipLogic Family 4.0网表提取器ChipLogic Analyzer北京芯愿景软件技术有限公司BEIJING CELLIX SOFTWARE CO., LTD.本手册仅限于ChipLogic Family软件的购买、租赁和试用用户在单位内部使用。
未得到北京芯愿景软件技术有限公司的书面许可,不得为任何目的、以任何形式或手段复制和传播本手册的任何部分。
本手册内容若有变动,恕不另行通知。
文档编号:CHIPLOGIC-MAN-AN© 2002-2003 北京芯愿景软件技术有限公司前言本手册主要介绍ChipLogic Family系列软件中的一个非常重要的客户端软件――ChipLogic Analyzer,利用本软件可以基于芯片的图像背景提取网表数据。
手册主要根据芯片网表提取的标准操作流程详细介绍了软件的各个功能,以使用户迅速理解并掌握ChipLogic Analyzer软件来进行芯片网表数据提取。
ChipLogic Analyzer内的网表数据可以导出为指定格式的数据文件,并导入到Cadence等EDA软件内进行仿真等进一步处理。
技术支持信息用户可通过下述方式获得本公司的技术支持:电 话:+86-10-82755750/55 ext 601传 真:+86-10-82755750/55 ext 604电子邮件:support@公司网址:目录前言 (3)第一章网表提取的标准工作流程 (7)1.1 网表提取标准流程图 (7)1.2 工作划分 (8)1.3 单元识别 (9)1.4 线网绘制 (9)1.5 线网连PIN (10)1.6 电学规则检查 (10)1.7 模块合并 (10)1.8 数据导出 (11)第二章软件启动与主界面介绍 (12)2.1软件启动 (12)2.2主界面一览 (12)2.3 标题栏 (13)2.4 菜单栏和常用工具栏 (13)2.4.1 常用用工具栏 (14)2.4.2 文件菜单 (14)2.4.3 编辑菜单 (15)2.4.4 查看菜单 (15)2.4.5 工程菜单 (16)2.4.6 网表菜单 (17)2.4.7 单元菜单 (17)2.4.8 工具菜单 (18)2.4.9 窗口菜单 (18)2.4.10 帮助菜单 (19)2.5 工程面板 (19)2.5.1 工程标签项 (20)2.5.2 单元标签项 (21)2.5.3 显示标签项 (21)2.6 雷达图 (22)2.7 工程窗口和窗口工具条 (23)2.7.1 工作区窗口 (23)2.7.2 模板编辑窗口 (24)2.7.3 芯片概貌图窗口 (24)2.8 输出窗口 (25)2.9 状态栏 (26)2.10 多层图像面板 (26)第三章工作区管理 (27)3.1 创建工作区 (27)3.1.1 以菜单方式创建工作区 (27)3.1.2 在概貌图上创建工作区 (28)3.2 工作区参数设置 (29)3.2.1 线网标签项 (29)3.2.2 参数标签项 (31)3.3 合并工作区 (31)3.4 复制工作区 (32)3.5 删除工作区 (33)3.6 比较工作区 (33)3.7 工作区数据导入导出 (33)第四章单元提取 (35)4.1 创建单元区 (35)4.2 单元模板的创建和删除 (37)4.3 编辑单元模板 (38)4.4 单元自动搜索 (40)4.5 确认单元实例 (41)4.6 检查单元实例 (42)4.7 单元实例添加、移动和删除 (42)4.7.1 添加和复制单元实例 (42)4.7.2 单元实例的移动和单元精定位 (43)4.7.3 删除单元实例 (43)4.8 单元比较窗口 (44)4.9 合并单元模板 (44)4.10 发送单元模板 (46)4.11自动比较单元模板 (46)4.12 单元列表窗口 (47)第五章线网提取 (48)5.1 自动搜索线网 (48)5.2 线网数据手工操作 (49)5.2.1 鼠标画线 (50)5.2.2 画笔画线 (50)5.2.3 引线头连接 (51)5.3 线网同单元引脚的连接 (54)5.4 其它功能 (54)5.4.1 突出显示线网 (54)5.4.2 查找功能 (54)5.4.3文本标注 (55)5.4.4 标尺 (55)第六章电学规则检查 (57)第七章工作区数据导出和导入 (58)7.1 工作区数据导出 (58)7.2 工作区数据导入 (59)7.3 将V ERILOG网表导入C ADENCE软件 (60)附录A 快捷键一览表 (63)A.1 系统功能键 (63)A.2 视图操作键 (63)A.3 编辑操作键 (65)A.4 画笔操作键 (66)A.5 其他操作键 (67)第一章 网表提取的标准工作流程1.1 网表提取标准流程图每个芯片可以划分为若干个模块,如下图所示的Analyzer标准工作流程,可以按如下步骤进行网表提取:1、项目经理进行模块划分2、对每个模块分别进行网表提取3、将各模块的网表数据合并到一起4、进行电学规则检查5、导出网表数据下面例图中的芯片可分为三个模块:Digital Big、Digital Small及Analog。
ROYER R-122 MKII活动式磁带速度录音室麦克风说明书

ROYER R-122 MKIIActive Ribbon-Velocity Studio Microphone The R-122 MKII is a compact, monaural, phantom powered ribbonmicrophone with a switchable -15 dB pad and a low cut filter. Soni-cally similar to our groundbreaking R-121, the R-122 MKII exhibits aflat frequency response and a well-balanced, panoramic soundfield,but it’s 13 dB more sensitive and has a faster transient response,giving a sense of more open highs. Like the R-121, it is capable ofhandling high SPL applications.The R-122 MKII’s -15 dB pad is positioned before any other electron-ics, giving the microphone 15 dB more headroom for high SPL work.The low cut filter is configured to reduce proximity effect for closemiking and vocal applications and effectively filters rumble.The R-122 MKII’s active electronics produce an output comparable tostudio condenser microphones and provide an optimum impedance to the ribbonelement, preventing overdamping of the ribbon and assuring consistent micro-phone performance. The high gain and low output impedance of the R-122 allow itto operate with any microphone preamplifier with phantom power, and also allowsfor use with long cable runs.The R-122 MKII utilizes a low mass, 2.5-micron, pure (99.99%) aluminum ribbonelement in a patented offset-ribbon transducer assembly. The smooth frequencyresponse and phase linearity of the R-122 MKII, coupled with its sophisticatedactive electronics system, enable it to deliver a consistent natural acoustic perfor-mance with extraordinary realism. Frequency response is excellent regardless ofthe angle of sound striking the ribbon, and off-axis coloration is negligible.The R-122’s patented offset-ribbon design positions the ribbon element toward thefront of the microphone body, which allows for high SPL handling on the front (logo)side and the option of a slightly brighter response when recording lower SPL soundsources on the back side (3 feet and closer; phase reversed in this position).R-122 MKII FEATURES• Active electronics provide high output capability, optimal impedance to theribbon element, extremely low self-noise and low output impedance• -15 dB pad and low cut filter provide greater flexibility and increased headroom• High SPL capabilities for electric guitar and percussion instruments• Absence of high frequency peaks, "ringing" and phase shifts• Ribbon element unaffected by impedance/load, heat or humidity• Operates on standard 48-volt phantom power• Gold plated XLR contactsRECOMMENDED APPLICATIONS• Close and distant miking• Electric and acoustic guitar• Vocals, commercial broadcast, voiceover• Brass, horn sections• Drum overheads, kick drum (see manual for position), room miking• Percussion instruments• Strings - solo & sections• Acoustic piano, harp• Live events - recording and sound reinforcementActual sizewith filterAcoustic Operating PrinciplePolar PatternGenerating ElementMagnetsFrequency ResponseSensitivitySwitchable PadSwitchable Bass Cut Self-Noise Output Impedance Output ConnectorRated Load Impedance Maximum SPLPower RequirementsSupply CurrentDimensionsWeightFinishAccessoriesOptional AccessoriesMicrophone Warranty Ribbon Element WarrantyElectrodynamic pressure gradient with active electronics.Figure-82.5-micron aluminum ribbon Rare Earth Neodymium 30 - 15,000 Hz ±3 dB -34 dB (re. 1v/pa ±1 dB)-15 dB100 Hz (6 dB per octave)< 18 dB200 Ohms, balanced Male XLR 3-pin (Pin 2 Hot)1K-Ohm minimum 135 dB @ 30 Hz 48-Volt Phantom Only 4 mA206mm L X 25mm W (8 1/8” L X 1” W) 309 grams (10.9 oz)Burnished Satin Nickel / Matte Black Chrome (optional)Protective wood case, mic sock Wind screen, shock mountLifetime to original owner (repair or replace at Royer’s option) First re-ribbon free to original owner within first year of purchase ROYER R-122 MKIITechnical SpecificationsFrequency Response and Polar PatternMatched pairs are available at extra chargeRoyer Labs2711 Empire Ave, Burbank, CA 91504Tel. (818) 847-0121 Fax (818) 847-0122COPYRIGHT ROYER LABS 2019All specifications subject tochange without noticePatent Number: 6,434,2520˚30˚60˚ 90˚ 120˚150˚180˚210˚240˚270˚ 300˚ 330˚ 10kHz200Hz 1kHz 205010050010005K10K20K0+5+10-5-1015K。
Digilent Digital Discovery 参考手册说明书

Digital Discovery Reference ManualThe Digilent Digital Discovery™ is a combined logic analyzer and pattern generator instrument that was created to be the ultimate embedded development companion. The Digital Discovery was designed to optimize channels, speed, and portability. The small form factor facilitates easy storage and provides a whole suite of advanced features to allow you to debug, visualize, and simulate digital signals for most embedded projects. The digital inputs and outputs can be connected to a circuit using simple wire probes or breadboard wires; alternatively, the Digital Discovery High Speed Adapter and impedance-matched probes can be used to connect and utilize the inputs and outputs for more advanced projects. The Digital Discovery is driven by the free WaveForms software and can be configured to be any of the below instruments:∙24-channel digital logic analyzer (1.2…3.3V CMOS, up to 800MS/s(with the High Speed Adapter))∙16-channel pattern generator (1.2…3.3V CMOS, 100MS/s)∙16-channel virtual digital I/O including buttons, switches, and LEDs – perfect for logic training applications∙Two input/output digital trigger signals for linking multiple instruments(1.2…3.3V CMOS)∙ A programmable power supply of 1.2…3.3V/100mA. The same voltage sup plies the Logic Analyzer input buffers and the Pattern Generator input/outputbuffers, for keeping the logic level compatibility with the circuit under test.∙Digital Bus Analyzers (SPI, I²C, UART, I2S, CAN, Parallel)The Digital Discovery was designed for anyone embarking on embeddeddevelopment. Its features and specifications were deliberately chosen to maintain a small and portable form factor, withstand use in a variety of environments, and keep costs down, while balancing the requirements of operating on USB Power.1.1 Architectural Overview and Block DiagramDigital Discovery's high-level block diagram is presented in Figure 2, below. The core of the Digital Discovery 2 is the Xilinx® Spartan®-6 FPGA (specifically, theXC6SLX25-2 device). The WaveForms application automatically programs the Discovery’s FPGA at start-up with a configuration file designed to implement a multi-function test and measurement instrument. Once programmed, the FPGA inside the Discovery communicates with the PC-based WaveForms application via a USB 2.0 connection. The WaveForms software works with the FPGA to control all the functional blocks of the Digital Discovery, including setting parameters, acquiring data, and transferring and storing data into the DDR3 memory. Signals and equations also use certain naming conventions. Signals in the Input block use “DIN” prefix to indicate these are inputs only. Signals in the Input/Output block use “DIO” prefix. Signals at the user co nnectors include “USR” in their names, while signals at the FPGA pins include “FPGA”. Signals at the FPGA pins driving the pull resistors for DIO signals, include “PULL” in their names. DIN inputs are indexed 0 to 23, DIO input/outputs are indexed 24 to 39. Memory signals have the “DDR” prefix. Supply rails show the voltage with the VCC prefix. Referring to the block diagram in Figure 2 below:∙The I/O Level Translators build the bidirectional interface for input/output pins (used in the Pattern Generator, Static IO, and Logic Analyzer) ∙The Input Dividers are the conditioning circuits for the input pins (used in the Logic Analyzer)∙The FPGA banks are supplied at different voltages:o Bank 0, Bank1: VCCIO_PROG, a variable voltage, settable in the range1.2V…3.3V. The logic standard is set to: LVCMOS18_JEDEC. Thethreshold voltage is about 0.45*VCCIO_PROG.o Bank 2: VCC3V3, a fixed voltage of 3.3V.o Bank 3: VCC1V5, a fixed voltage of 1.5V.∙ A replica of VCCIO_PROG is also available to the user, as VCCIO_USR, under the V user switch control.∙The DDR3 Data Memory block stores the Logic analyzer acquired data.∙The Power Supplies and Control block generates all internal supply voltages as well as user supply programmable voltage. The control block also monitorsthe device power consumption for USB compliance.∙The USB Controller interfaces with the PC for programming the volatile FPGA memory after power on or when a new configuration is requested. After that, it performs the data transfer between the PC and FPGA.∙The Calibration Memory stores all calibration parameters. The Digital Discovery includes no analog calibration circuitry. Instead, a calibrationoperation is performed at manufacturing (or by the user), and parameters are stored in memory. The WaveForms software uses these parameters to adjustthe acquired data and the generated signals.In the sections that follow, schematics are not shown separately for identical blocks. For example, the Input Divider is only shown for DIN0 since the schematic for all other DIN1…DIN23 is identical.Figure 2. Digital Discovery Hardware block diagram.2. I/O Level TranslatorsFigure 3 shows the DIO user connectors and Figure 4 shows the I/O level translator for DIO24. DIO25 to DIO31 use similar discrete components, connected to pins1A2…2A3, respectively 1B2…2B3 of IC2.The I/O Level Translators block includes: - Input protection: series PTC (33Ω, positive thermal coefficient thermistor) and parallel ESD/overvoltage diodes to 5.2V and GND. - Voltage level translators, SN74CBT3384C. When DIO_USR signals are driven by the DUT, the voltage at the FPGA pins is limited at VCCIO_SW-1V = 3.3V. When the FPGA drives DIO_USR signals, they pass unlimited trough the low impedanceSN74CBT3384C buffer. - Pull resistors: 10k, individually settable as Pull-Up, Pull-Down or High-Z. This is done with a second FPGA pin associated to each DIO, which can be driven High, Low or HiZ. The Pull-Up voltage is VCCIO_PROG. - DIO_FPGA pin: the bank supply voltage is VCCIO_PROG> The WaveForms software can set VCCIO_PROG from 1.2 to 3.3V. The FPGA input threshold level is about 45% of VCCIO_PROG. The output strength can be set from 2mA to 16mA. The output slew rate can be set as: Quiet, Slow or Fast.Figure 3. DIO user connectors.Figure 4. I/O level translator.The LDO in Figure 5 generates the 4.3V to supply the level translator in Figure 4.The charge-pump in Figure 6 provides the the 6V reference for the clipper in Figure 7.When all ESD diodes protecting DIO_USR in Figure 3 are OFF, Q3B is OFF, and also Q4. If overvoltage is applied on some DIO_USR pins, rising VU5V2_ESD in Figure 7 above 5.2V, Q3B and Q4 turn ON , clipping VU5V2_ESD at approximately 5V.Figure 5. VCCIO_SW supply.Figure 6. VU6V0 supply.Figure Figure 7. Backpowering voltage clipper.3. Input DividersFigure 8 shows the DIN user connector and Figure 9 shows the Input Divider for DIN0. DIN1 to DIN23 use similar input circuitry.The Input Dividers block includes:∙Frequency compensated voltage dividers: 10/11 resistive dividers with compensation for FPGA input capacitance. All the dividers together have thesettable reference voltage VREFIO. Setting VREFIO close to the logicalthreshold voltage provides the highest sensitivity, while setting VREFIO atGND or logical supply voltage increase the noise immunity. The voltage at the FPGA pin:$$V_{DIN\text{_}FPGA}=\dfrac{10}{11}∙V_{DIN\text{_}USR}+\d frac{1}{11}∙V_{REFIO}\label{1}\tag{1}$$∙The reference voltage VREFIO is generated as in Figure 10. DIN_VREF_H and DIN_VREF_L are connected to FPGA pins in bank 1. Bank1 is supplied atVCCIO. VREFIO can be set at:o0V, when DIN_VREF_H = DIN_VREF_L = lowo0.43*VCCIO_PROG, when DIN_VREF_H = high, DIN_VREF_L = lowo VCCIO_PROG, when DIN_VREF_H = DIN_VREF_L = high.∙ESD/Overvoltage protection: Shottky diodes to VCC3V3.∙DIN_FPGA pin: the bank supply voltage is VCCIO_PROG. The WaveForms software can set VCCIO_PROG from 1.2 to 3.3V. The FPGA input thresholdlevel is about 45% of VCCIO_PROG.Figure 8. DIN user connector.Figure 9. Input Divider.Figure 10 VREFIO reference.4. Power supplies and control4.1 Internal power suppliesIn Figure 11, IC16 limits the in-rush current when the device is connected to the USB port. INA214 is a current shunt amplifier, with a gain of 100. With Vref = 0.75V and R163 = 15mΩ, the output voltage is:$$V_{ISNS\text{_}VBUS}=100∙(V_{IN+}-V_{IN-})+0.75V=1.5∙I_{VU5V0}+0.75V\label{2}\tag{2}$$The VBUS voltage is halved to VSNS_VBUS, for being also monitored. IC12 in Figure 11 is a triple power supply, generating the rails of 1.2V for the FPGA core, 1.5V for Bank 3 and DDR3 memory and 3.3V, for various circuits.Figure 11 VBUS monitoring..Figure 12. Internal voltage supplies.4.2 Programmable power supplyIC13 in Figure 13 generates the VCCIO_PROG, the variable voltage to supply the input and IO banks of the FPGA:$$V_{VCCIO\text_PROG}=V_{FB}∙(1+\dfrac{R_{144}}{R_{146}}+\dfrac{R_{144}}{R_{149}} )-V_{VSET\text_VCCIO}∙\dfrac{R_{144}}{R_{146}} =3.42V-V_{VSET\text_VCCIO}∙0.82 \label{3}\tag{3}$$With VVSET_VCCIO ϵ(0…3V), VCCIO_PROG could be theoretically set in the range: VCCIO_PROG ϵ(1.02V…3.42V). IC15 is a current shunt amplifier, with a gain of 100. With Vref = 0.75V and R115 = 50mΩ, the output voltage is:$$V_{ISNS\text_USR}=100∙(V_{IN+}-V_{IN-})+0.75V=5∙I_{VCCIO\text_USR}+0.75V\label{4}\tag{4}$$IC14 is a window comparator: FAULT_USR is logical LOW, when VISNS_USR is either more than 1.5V (IVCCIO_USR>150mA) or less than 0.66V (IVCCIO_USR←18mA). If this happens, the FPGA turns EN_PWR_USR to LOW, which turns both Q1A and Q1B OFF,to protect VCCIO_USR against overcurrent and reverse current respectively. VCCIO_USR is halved to VSNS_USR, for being monitored.Figure 13. VCCIO_PROG supply.Figure 14. VCCIO_USR protection and switch.4.3. Monitoring the power suppliesThe microcontroller in Figure 15 has two roles:1.A/D Conversion of VVSNS_VBUS, VISNS_VBUS, VVSNS_USR, VISNS_USR,representing the voltages and currents consumed from VBUS and VCCIO_USR respectively. The digital results are passed to the FPGA via an SPI interface.2.Storing the calibration parameters computed as a part of the manufacturingtest. During regular behavior, the WaveForms Software reads the parameters and corrects both generated and acquired signals.The DAC in Figure 16 generates the setting voltage for programming the value of VCCIO. IC22 in Figure 17 provides 3V reference voltage for both ADC and DAC above.Figure 15. ATtiny microcontroller.Figure 16. VSET_VCCIO setting DAC.Figure 17. VREF3V0 .5. LEDs and DDR3 MemoryFigure 18 shows the two tricolor LEDs used to symbolize the Digital discovery status. Figure 19 shows the DDR3 memory for the Logic Analyzer buffer.Figure 18. LEDs.Figure 19. DDR3 memory.6. USB ControllerThe USB interface performs two tasks:Programming the FPGA: There is no non-volatile FPGA configuration memory on the Digital Discovery. The WaveForms software identifies the connecteddevice and downloads an appropriate .bit file at power-up, via a Digilent USB-JTAG interface. Adept run-time is used for low level protocols.∙Data exchange: All instrument configuration data, acquired data and status information is handled via a Digilent synchronous parallel bus and USBinterface. Speed up to 20MB/sec. is reached, depending on USB port type and load as well as PC performance.7. FPGAThe core of the Digital Discovery is the Xilinx Spartan6 FPGA circuit XC6SLX25. The configured logic performs:∙Clock management (12MHz and 60 MHz for USB communication, 100MHz and 800MHz for data sampling)∙Acquisition control and Data Storage (Logic Analyzer)∙Digital signal synthesis (for pattern generator and bus protocol controllers) ∙Trigger system (trigger detection and distribution for all instruments)∙Power supplies control and instruments enabling∙Power and temperature monitoring∙Calibration memory control∙Communication with the PC (settings, status data)Block RAM of the FPGA is used for signal synthesis. External DDR3 memory is used for data acquisition.Detail of the trigger system is shown in Figure 20. Each instrument generates a trigger signal when a trigger condition is met. Each trigger signal (including external triggers) can trigger any instrument and drive the external trigger outputs. This way, all the instruments can synchronize to each other.Figure 20. FPGA configuration trigger block diagram.Figure 21 shows the connections to the FPGA banks 0, 1 and 3.Bank 0 is used for IOs. DIO_FPGA pins are the actual input/output pins to be used with the Pattern Generator, Static IO and Logic Analyzer. A DIO_PULL pin can add Pull-Up or Pull-Down resistors to the associated DIO_FPGA pin (see Figure 4).Bank 1 is used for high speed Logic Analyzer inputs. DIN_FPGA are the actual input pins, while DIN_VREF_H and DIN_VREF_L set the reference voltage for the input dividers (see Figure 9).Bank 3 is used as port for the DDR3 memory.Figure 21. FPGA banks 0, 1 and 3.Figure 22 shows the voltage rails and decoupling for the FPGA.The internal core of the FPGA is supplied 1.2V.Banks 0 and 1 are supplied with the programmable VCCIO_PROG. By setting this from 1.2V to 3.3V, both inputs and IOs are set to be compatible with the I/O standard LVCMOS of the respective voltage. Notice that a protected version of VCCIO_PROG is also available to the user, as VCCIO_USR. This can be used to supply the Device/Circuit Under Test.Bank 3 is supplied 1.5V, for compatibility with the DDR3 IC.Bank 2 and VCCAUX are supplied 3.3V.Figure 22. FPGA powering and decoupling.8. AccessoriesThe Digital Discovery package includes;∙One 2×16 fly-wire assembly (datasheet), for the DIN_USR connector. 24DIN signals (various colors), 8 GND wires (black). The connector is keyed so thatthe correct pins are connected to the correct color wires.∙One 2×6 fly-wire assembly (datasheet), for the DIO connectors. Each one includes two VCCIO_USR (red) wires, two GND (black) wires and 8 (colored)signal wires. It has a 2×6 female connector for the Digital Discovery DINconnector, and 1 pin female connectors for the device under test. Additional Accessories that can be added at checkout;∙One High Speed Adapter, for the DIN_USR connector. The High Speed Adapter is an alternative to the 2×16 fly-wire assembly. It provides access for24 twisted cables. The adapter is not keyed, and both orientations can beused as the twisted wires are not color coded. However, if the adapter isplugged in with the ground arrows pointing down, the pins will be located as shown below:∙High Speed Logic Probes (datasheet). Each twisted cable has a GND (black) wire twisted to a DIN_USR (colored) wire. The wire connects to the HighSpeed Adapter via a 2 pin female header, and two 1 pin female connectors to the device under test. A 100Ω resistor is embedded in the signal wire, on the end closest to the device under test. All GND wires should be connected toGround of the device under test.9. Features and PerformancesThis chapter shows the features and performances as described in the Digital Discovery Datasheet. Footnotes add detailed information and annotate the HW description in this Manual.9.1. Logic Analyzer∙24 high-speed input channels (DIN0…23), accessible through one 2×16 connector, used with the Logic Analyzer in Waveforms (560kΩ||10pF)∙16 digital I/Os (DIO24…39) arranged in two Pmod-style (2×6) connectors, used with the Logic Analyzer in Waveforms 1)∙800MSps input sample rate when using maximum 8 inputs (and the High Speed Adapter), 400 MSps with maximum 16 inputs (with the High SpeedAdapter), 200MSps and lower with maximum 32 inputs 2)∙User programmable input and output LVCMOS voltage levels from 1.2V to3.3V 3) (5V compatible 4) )∙100MHz signal input bandwidth∙2Gbit DDR3 acquisition buffer for Logic Analyzer∙Multiple trigger options including pin change, bus pattern, etc 5)∙Digital Bus Analyzers (SPI, I²C, UART, Parallel)9.2. Multi-purpose Digital I/O∙16 digital I/Os arranged in two Pmod-style (2×6) connectors.∙Each of the 16 pins can be configured for input (Logic analyzer) or set as output 6).∙Algorithmic pattern generator (no buffers used) 7)∙Custom pattern buffer/ch.: 32Ksamples∙ROM Logic for implementing user defined Boolean functions and State Machines∙Bus Protocol Controllers (SPI, UART, I²C)∙100MSps max. output sample rate (50MHz maximum output frequency).∙Automatic or manual strength and slew settings for outputs. 8)∙User programmable logic I/O levels from 1.2V to 3.3V (5V compatible) 9),10).9.3. Other features∙USB bus powered∙User power supplies, 1.2V to 3.3V, available in the two Pmod-style connectors (100mA max)∙Twisted wire high-speed cable option for input channels to insure signal integrity∙Free Waveforms 2015 software runs on Windows, MacOS, and Linux∙Cross-triggering between Logic Analyzer, Pattern Generator or external trigger ∙Data file import/export using standard formats∙80X80X25mm, 80g (without accessories)∙includes: USB cable, fly-wire accessoryWritten by Mircea Dabacan, PhD, Technical University of Cluj-Napoca Romania 1) , 6)The 16 DIO lines are primarily intended for the Pattern Generator, protocol controllers and Static IO instruments. For user convenience, some or all of them can be used by the Logic Analyzer also (see footnote 2). However, DIO input circuitry is different compared to DIN. Even more, when driving a DIO pin with the Pattern Generator and reading it back with the Logic Analyzer, the signal is read at the FPGA pin and does not propagate trough the external DIO circuitry. Consequently, when combining DIN and DIO pins in the Logic Analyzer, misalignments can be observed, at high acquisition rate.2)Available combinations in WaveForms:1.200MHz, DIN0...23, DIO24 (31)2.200MHz, DIO24...39, DIN0 (15)3.400MHz, DIN0 (15)4.400MHz, DIO24 (39)5.800MHz, DIN0 (7)6.800MHz, DIO24 (31)3) , 8) , 9)The FPGA DIN and DIO pins are set to LVCMOS18_JEDEC IOSTANDARD. The supply voltage of the associated FPGA banks is set (by user) to any value from 1.2V to 3.3V. The threshold level (at the FPGA pins) is about 45% of the bank supply voltage. For standard voltages of: 1.2V, 1.5V, 1.8V, 2.5V, 3.3V, the threshold levels (at the FPGA pins) are: 0.58V, 0.7V, 0.82V, 1.1V and 1.42V respectively.4) , 10)Setting the voltage to 3.3V, 5V logic inputs are tolerated but the input threshold is 1.42V. LVCMOS 3.3V output signals are compatible to most external logical circuits supplied with 5V.5)Trigger Detectors and Trigger Distribution Networks are implemented in the FPGA. This allows real time triggering and cross-triggering of different instruments within the Digital Discovery device. Using external Trigger inputs/outputs, cross-triggering between multiple Digital Discovery devices is possible.7)Real time implemented in the FPGA configuration.。
质谱分析法中英文专业词汇
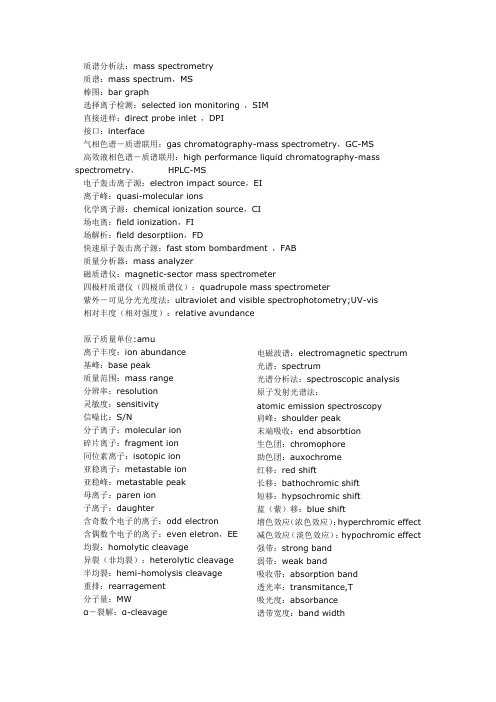
质谱分析法:mass spectrometry质谱:mass spectrum,MS棒图:bar graph选择离子检测:selected ion monitoring ,SIM直接进样:direct probe inlet ,DPI接口:interface气相色谱-质谱联用:gas chromatography-mass spectrometry,GC-MS 高效液相色谱-质谱联用:high performance liquid chromatography-mass spectrometry,HPLC-MS电子轰击离子源:electron impact source,EI离子峰:quasi-molecular ions化学离子源:chemical ionization source,CI场电离:field ionization,FI场解析:field desorptiion,FD快速原子轰击离子源:fast stom bombardment ,FAB质量分析器:mass analyzer磁质谱仪:magnetic-sector mass spectrometer四极杆质谱仪(四极质谱仪):quadrupole mass spectrometer紫外-可见分光光度法:ultraviolet and visible spectrophotometry;UV-vis 相对丰度(相对强度):relative avundance原子质量单位:amu离子丰度:ion abundance基峰:base peak质量范围:mass range分辨率:resolution灵敏度:sensitivity信噪比:S/N分子离子:molecular ion碎片离子:fragment ion同位素离子:isotopic ion亚稳离子:metastable ion亚稳峰:metastable peak母离子:paren ion子离子:daughter含奇数个电子的离子:odd electron含偶数个电子的离子:even eletron,EE 均裂:homolytic cleavage异裂(非均裂):heterolytic cleavage 半均裂:hemi-homolysis cleavage重排:rearragement分子量:MWα-裂解:α-cleavage 电磁波谱:electromagnetic spectrum光谱:spectrum光谱分析法:spectroscopic analysis原子发射光谱法:atomic emission spectroscopy肩峰:shoulder peak末端吸收:end absorbtion生色团:chromophore助色团:auxochrome红移:red shift长移:bathochromic shift短移:hypsochromic shift蓝(紫)移:blue shift增色效应(浓色效应):hyperchromic effect 减色效应(淡色效应):hypochromic effect 强带:strong band弱带:weak band吸收带:absorption band透光率:transmitance,T吸光度:absorbance谱带宽度:band width杂散光:stray light噪声:noise暗噪声:dark noise散粒噪声:signal shot noise闪耀光栅:blazed grating全息光栅:holographic graaing光二极管阵列检测器:photodiode array detector偏最小二乘法:partial least squares method ,PLS褶合光谱法:convolution spectrometry 褶合变换:convolution transform,CT离散小波变换:wavelet transform,WT 多尺度细化分析:multiscale analysis供电子取代基:electron donating group 吸电子取代基:electron with-drawing group荧光:fluorescence荧光分析法:fluorometryX-射线荧光分析法:X-ray fulorometry 原子荧光分析法:atomic fluorometry分子荧光分析法:molecular fluorometry 振动弛豫:vibrational relexation内转换:internal conversion外转换:external conversion 体系间跨越:intersystem crossing激发光谱:excitation spectrum荧光光谱:fluorescence spectrum斯托克斯位移:Stokes shift荧光寿命:fluorescence life time荧光效率:fluorescence efficiency荧光量子产率:fluorescence quantum yield荧光熄灭法:fluorescence quemching method散射光:scattering light瑞利光:Reyleith scanttering light拉曼光:Raman scattering light红外线:infrared ray,IR中红外吸收光谱:mid-infrared absorption spectrum,Mid-IR远红外光谱:Far-IR微波谱:microwave spectrum,MV红外吸收光谱法:infrared spectroscopy 红外分光光度法:infrared spectrophotometry振动形式:mode of vibration伸缩振动:stretching vibrationdouble-focusing mass spectrograph 双聚焦质谱仪trochoidal mass spectrometer 余摆线质谱仪ion-resonance mass spectrometer 离子共振质谱仪gas chromatograph-mass spectrometer 气相色谱-质谱仪quadrupole spectrometer 四极(质)谱仪Lunar Mass Spectrometer 月球质谱仪Frequency Mass Spectrometer 频率质谱仪velocitron 电子灯;质谱仪mass-synchrometer 同步质谱仪omegatron 回旋质谱仪。
P6450-Logic-Analyzer-Probe-with-D-Max-Probing-Technology-Instructionsl

*P071247801*
071-2478-01
Copyright © Tektronix. All rights reserved. Licensed software products are owned by Tektronix or its subsidiaries or suppliers, and are protected by national copyright laws and international treaty provisions.
Tektronix products are covered by U.S. and foreign patents, issued and pending. Information in this publication supersedes that in all previously published material. Specifications and price change privileges reserved.
TEKTRONIX and TEK are registered trademarks of Tektronix, Inc.
D-Max is a registered trademark of Tektronix, Inc. MagniVu is a trademark of Tektronix, Inc.
cLGA is a registered trademark of Amphenol Intercon Systems, Inc.
Velcro is a registered trademark of Velcro Industries B.V.
Contacting Tektronix
AUR°EL S.p.A 868 MHz SAW 传输模块用户手册说明书

TX AM 868/NPSAW transmitter module with external antenna for applications with OOK modulation and with a 868.35 MHz carrier .Pin-outTX AM 868/NP ModulePin out descriptionPin 2 DATA IN Input data. +5V Pin 3 NC Not connected.Pin 4-11 GNDConnected to GND. Internally connected to a single ground. Pin 13 Uscita RF 50 ohm antenna connection. Pin 15 +VVoltage supply (+5.0 V)TX AM 868/NP technical featuresDESCRIPTIONMIN. TIPICO MAX. U.M. Reception Frequency 868,25 868,35 868,45 MHz Voltage supply range4,50 5,00 5,50 Volts Current consumption – Tx mode (CW) 21 24 mA Stand by current consumption 0 mA E.R.P. Harmonic < 1GHz -54 -36 dBm E.R.P. Harmonic >1GHz -30 dBm I.F bandwidth5 KHz Effective Power measured directly on 50 ohms antenna pin 10 12 dBm Data_In, low logic level voltage 0 0,1 V Data_In, high logic level voltage 4,2 V Working temperature -20+85°C Dimensions36 x 9.5 x 3 mm2 15Device usageIn order to take advantage of the performances described in the technical features and to comply with the operating conditions which characterize the certification, the receiver has to be fitted up on a printed circuit, considering what follows:Voltage supply:1. The transmitter must be supplied by very low voltage security source protected against short circuits.2. Maximum voltage variation admitted: ± 0.5 V.3. De-coupling, next to the transmitter, by means of a ceramic capacitor of minimum 100.000 pF value.Ground:It must surround in the better way the welding area of the receiver. The circuit must be achieved in double layer, with throughout vias to the ground planes, approximately each 15 mm. It must be properly dimensioned inthe antenna connection area, in case a radiant whip antenna is fitted in(and area of approximately 50 mm is suggested).Picture 2: Lay-out advised for a correct working of the receiver50 Ohm Line:1. It must be as shorter as possible.2. 1,8 mm wide for 1 mm thick FR4 printed circuits and 2,9 mm wide for 1,6 mm thick FR4 printed circuits. On the same side it must be kept 2mm away from the ground.3. On the opposite side a ground circuit area must be present.Antenna connections:It may be utilized as the direct connection point for the radiating whip antenna.It can bear the connection of the central wire of a 50 ohm coaxial cable. Be sure that the braid is welded to the ground in a close point.1. A whip antenna, 80 mm long and approximately 1 mm dia, brass or copper wire made, must be connected to the RF input of the receiver.2. The antenna body must be kept straight as much as possible and must be free from other circuits or metal parts (5cm minimum suggested distance).3.It can be utilized both vertically or horizontally (the previous is highly suggested), providing that connection point between antenna and receiver input is surrounded by a good ground plane.N.B: As an alternative to the above mentioned antenna it is possible to use the whip model manufactured by Aurel (see related Datasheet and Application Notes).By fitting whips too different from the described ones, the EEC Certification is not assured.Technical Suggestions1. Keep the transmitter separates from all other components of the circuit (more than 5mm).2. Keep particularly far away and shielded all microprocessors and their clock circuits.3. Do not fit components around the 50 Ohm line. At least keep them at 5 mm distance.4. If the antenna connection is directly used for a radiating whip connection, keep at least a 5 cm radius free area. In case of coaxial cable connection, 5 mm radius will suffice.REFERENCE NORMATIVEThe TX AM 868/NP transmitter is approved by CE and in particular satisfies the European normative EN 300-220 and EN 301-489 with 5,0V voltage supply. The product was tested in according with EN 60950 normative and it’s usable fitted in an isolated housing to ensure the above normative. The transmitter must be supplied by very low voltage security source against the short circuits. Usage of transmitter module is foreseen fitted in the housing which ensure the agreement of EN 61000 normative is not directly applicable to the module itself. In particular, it’s at the user’s care the isolating of the extern antenna connection and antenna too, in fact the RF output of the transmitter is not able to directly bear electrostatic charges foreseen in the above normative.CEPT 70-03 RecommendationIn order to comply with such normative, the device must be used on the time scale with maximum duty cycle time of 1% on an hourly basis.。
ChipLogic Analyzer软件培训教程

49
单元比较窗口
多个单元 模板图像 并列显示 有助于发 现重复单 元模板
50
合并单元模板(1)
合并单元模板
在单元比较窗口内利用合并图标 按Ctrl+T,输入两个单元模板名 在工程面板单元栏内选中一个模板,在其右键 菜单内选择“合并单元模板” 在弹出的合并模板对话框内设置模板相对方向
被合并模板的所有实例将添加到目标模板内
36
其他工作区操作
复制工作区
复制一个与当前工作区数据完全相同的工作区
删除工作区
必须工作区创建者或者项目经理才能删除工作区
比较工作区
用来比较两个工作区内的线网数据是否相同
37
四、单元识别
38
单元识别标准步骤
标注单元区 圈定单元模板 搜索单元实例 确认单元实例 直接添加实例 检查单元实例
39
标注单元区
每个工作区数据提交前都应严格检查,确保尽可能 少的识别错误传递到下一个步骤 DS_M12即为模块Digtal_Small的最终线网数据
10
线网连PIN
如果将整个芯片作为一个模块
需 先 完 成 单 元 工 作 区 WHOLE_CELL、 线 网 工 作 区 WHOLE_M12数据提取 将上述两个工作区合并到最终网表工作区WHOLE_NET内 在WHOLE_NET内按照单元类型逐类进行线网连PIN
19
工程面板——单元栏(2)
单元模板项的右键菜单
可进行各项单元模板的 数据管理 将在单元识别操作中详 细介绍
20
工程面板——显示栏(1)
21
工程面板——显示栏(2)
双击一个显示层名可设置显示属性
颜色 线宽 线型 是否可见 是否可选
22
Professional元件库列表及中英文对照合并版
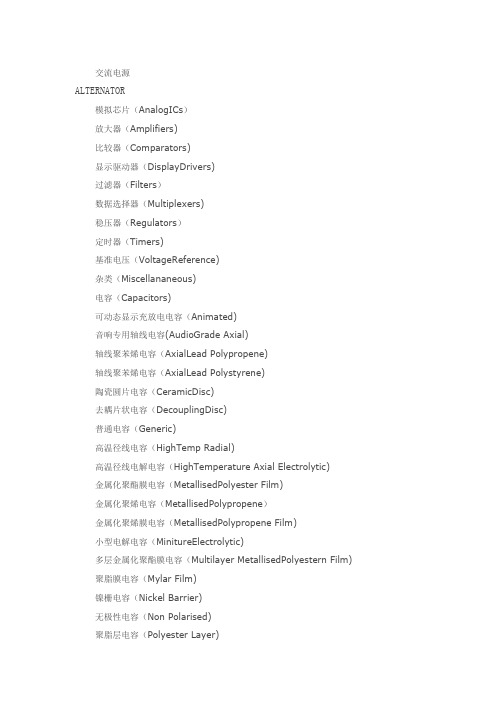
交流电源ALTERNATOR模拟芯片(AnalogICs)放大器(Amplifiers)比较器(Comparators)显示驱动器(DisplayDrivers)过滤器(Filters)数据选择器(Multiplexers)稳压器(Regulators)定时器(Timers)基准电压(VoltageReference)杂类(Miscellananeous)电容(Capacitors)可动态显示充放电电容(Animated)音响专用轴线电容(AudioGrade Axial)轴线聚苯烯电容(AxialLead Polypropene)轴线聚苯烯电容(AxialLead Polystyrene)陶瓷圆片电容(CeramicDisc)去耦片状电容(DecouplingDisc)普通电容(Generic)高温径线电容(HighTemp Radial)高温径线电解电容(HighTemperature Axial Electrolytic)金属化聚酯膜电容(MetallisedPolyester Film)金属化聚烯电容(MetallisedPolypropene)金属化聚烯膜电容(MetallisedPolypropene Film)小型电解电容(MinitureElectrolytic)多层金属化聚酯膜电容(Multilayer MetallisedPolyestern Film) 聚脂膜电容(Mylar Film)镍栅电容(Nickel Barrier)无极性电容(Non Polarised)聚脂层电容(Polyester Layer)径线电解电容(Radial Electrolytic)树脂蚀刻电容(Resin Dipped)钽珠电容(Tantalum Bead)可变电容(Variable)VX轴线电解电容(VXAxial Electolytic) 连接器(Connectors)音频接口(Audio)D 型接口(D-Type)双排插座(DIL)插头(Header Blocks)PCB转接器(PCBTransfer)带线(Ribbon Cable)单排插座(SIL)连线端子(Terminal Blocks)杂类(Miscellananeous)数据转换器(Data Converter)模/数转换器(A/D converters)数/模转换器(D/A converters)采样保持器(Sample & Hold)温度传感器(Temperature Sensore)调试工具(Debugging Tools)断点触发器(Breakpoint Triggers)逻辑探针(Logic Probes)逻辑激励源(Logic Stimuli)二极管(Diode)整流桥(Bridge Rectifiers)普通二极管(Generic)整流管(Rectifiers)肖特基二极管(Schottky)开关管(Switching)隧道二极管(Tunnel)变容二极管(Varicap)齐纳击穿二极管(Zener)ECL 10000系列(ECL 10000 Series) 各种常用集成电路机电(Electromechanical)各种直流和步进电机电感(Inductors)普通电感(Generic)贴片式电感(SMT Inductors)变压器(Transformers)拉普拉斯变换(Laplace Primitives)一阶模型(1st Order)二阶模型(2st Order)控制器(Controllers)非线性模式(Non-Linear)算子(Operators)极点/零点(Poles/Zones)符号(Symbols)存储芯片(Memory Ics)动态数据存储器(Dynamic RAM)电可擦除可编程存储器(EEPROM)可擦除可编程存储器(EPROM)I2C总线存储器(I2C Memories)SPI总线存储器(SPIMemories)存储卡(Memory Cards)静态数据存储器(Static Memories)微处理器芯片(Microprocess ICs) 6800 系列(6800Family)8051 系列(8051Family)ARM 系列(ARM Family)AVR 系列(AVR Family)Parallax 公司微处理器(BASIC Stamp Modules)HCF11 系列(HCF11Family)PIC10 系列(PIC10Family)PIC12 系列(PIC12Family)PIC16 系列(PIC16Family)PIC18 系列(PIC18Family)Z80系列(Z80 Family)CPU 外设(Peripherals)杂项(Miscellaneous)含天线、ATA/IDE硬盘驱动模型、单节与多节电池、串行物理接口模型、晶振、动态与通用保险、模拟电压与电流符号、交通信号灯建模源(Modelling Primitives)模拟(仿真分析)(Analogy-SPICE)数字(缓冲器与门电路)(Digital--Buffers&Gates)数字(杂类)(Digital--Miscellaneous)数字(组合电路)(Digital--Combinational)数字(时序电路)(Digital--Sequential)混合模式(Mixed Mode)可编程逻辑器件单元(PLD Elements)实时激励源(Realtime Actuators)实时指示器(Realtime Indictors)运算放大器(Operational Amplifiers)单路运放(Single)二路运放(Dual)三路运放(Triple)四路运放(Quad)八路运放(Octal)理想运放(Ideal)大量使用的运放(Macromodel)光电子类器件(Optoelectronics)七段数码管(7-Segment Displays)英文字符与数字符号液晶显示器(Alphanumeric LCDs) 条形显示器(Bargraph Displays)点阵显示屏(Dot Matrix Display)图形液晶(Grphical LCDs)灯泡(Lamp)液晶控制器(LCD Controllers)液晶面板显示(LCD Panels Displays)发光二极管(LEDs)光耦元件(Optocouplers)串行液晶(Serial LCDs)可编程逻辑电路与现场可编程门阵列(PLD&FPGA)无子类电阻(Resistors)0.6W金属膜电阻(0.6WMetal Film)10W 绕线电阻(10WWirewound)2W 金属膜电阻(2W MetalFilm)3W 金属膜电阻(3W MetalFilm)7W 金属膜电阻(7W MetalFilm)通用电阻符号(Generic)高压电阻(High Voltage)负温度系数热敏电阻(NTC)排阻(Resisters Packs)滑动变阻器(Variable)可变电阻(Varistors)仿真源(Simulator Primitives)触发器(Flip-Flop)门电路(Gates)电源(Sources)扬声器与音响设备(Speaker&Sounders)无子分类开关与继电器(Switch&Relays)键盘(Keypads)普通继电器(Generic Relays)专用继电器(Specific Relays)按键与拨码(Switchs)开关器件(Switching Devices)双端交流开关元件(DIACs)普通开关元件(Generic)可控硅(SCRs)三端可控硅(TRIACs)热阴极电子管(Thermionic Valves)二极真空管(Diodes)三极真空管(Triodes)四极真空管(Tetrodes)五极真空管(Pentodes)转换器(Transducers)压力传感器(Pressures)温度传感器(Temperature)晶体管(Transistors)双极性晶体管(Bipolar)普通晶体管(Generic)绝缘栅场效应管(IGBY/Insulated Gate BipolarTransistors 结型场效应晶体管(JFET)金属-氧化物半导体场效应晶体管(MOSFET)射频功率LDMOS晶体管(RF Power LDMOS)射频功率VDMOS晶体管(RF Power VDMOS)单结晶体管(Unijunction)CMOS 4000系列(CMOS 4000 seriesTTL 74系列(TTL 74series)TTL 74增强型低功耗肖特基系列(TTL74ALS Series)TTL 74增强型肖特基系列(TTL74AS Series)TTL 74高速系列(TTL 74FSeries)TTL 74HC系列/CMOS工作电平(TTL 74HCSeries)TTL 74HCT系列/TTL工作电平(TTL 74HCTSeries)TTL 74低功耗肖特基系列(TTL74LS Series)TTL 74肖特基系列(TTL 74SSeries)加法器(Adders)缓冲器/驱动器(Buffers&Drivers)比较器(Comparators)计数器(Counters)解码器(Decoders)编码器(Encoders)存储器(Memory)触发器/锁存器(Flip-Flop&Latches)分频器/定时器(Frequency Dividers & Timers)门电路/反相器(Gates&Inverters)数据选择器(Multiplexers)多谐振荡器(Multivibrators)振荡器(Oscillators)锁相环(Phrase-Locked-Loop,PLL)寄存器(Registers)信号开关(Signal Switches)收发器(Tranxceivers)杂类逻辑芯片(Misc.Logic)Proteusisis的元件库中英对照Proteus 元件名称对照1元件名称中文名说明7407 驱动门1N914 二极管74Ls00 与非门74LS04 非门74LS08 与门74LS390 TTL 双十进制计数器7SEG 4针BCD-LED 输出从0-9 对应于4根线的BCD码7SEG 3-8译码器电路BCD-7SEG[size=+0]转换电路ALTERNATOR 交流发电机AMMETER-MILLI mA安培计AND 与门BATTERY 电池/电池组BUS 总线CAP 电容CAPACITOR 电容器CLOCK 时钟信号源CRYSTAL 晶振D-FLIPFLOP D触发器FUSE 保险丝GROUND 地LAMP 灯LED-RED 红色发光二极管LM016L 2行16列液晶可显示2行16列英文字符,有8位数据总线D0-D7,RS,R/W,EN三个控制端口(共14线),工作电压为5V。
Anritsu MS2711 RF Spectrum Analyzer操作手册说明书
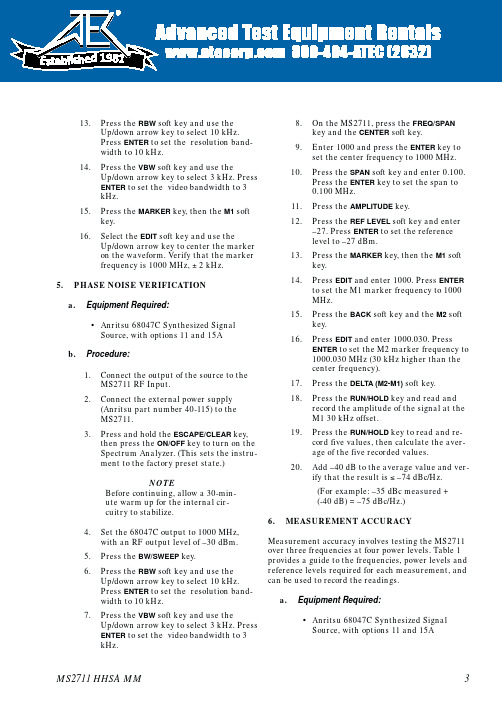
13.Press the RBW soft key and use theUp/down arrow key to select10kHz.Press ENTER to set the resolution band-width to10kHz.14.Press the VBW soft key and use theUp/down arrow key to select3kHz.PressENTER to set the video bandwidth to3kHz.15.Press the MARKER key,then the M1softkey.16.Select the EDIT soft key and use theUp/down arrow key to center the markeron the waveform.Verify that the markerfrequency is1000MHz,±2kHz.5.PHASE NOISE VERIFICATIONa.Equipment Required:·Anritsu68047C Synthesized SignalSource,with options11and15Ab.Procedure:1.Connect the output of the source to theMS2711RF Input.2.Connect the external power supply(Anritsu part number40-115)to theMS2711.3.Press and hold the ESCAPE/CLEAR key,then press the ON/OFF key to turn on theSpectrum Analyzer.(This sets the instru-ment to the factory preset state.)NOTEBefore continuing,allow a30-min-ute warm up for the internal cir-cuitry to stabilize.4.Set the68047C output to1000MHz,with an RF output level of–30dBm.5.Press the BW/SWEEP key.6.Press the RBW soft key and use theUp/down arrow key to select10kHz.Press ENTER to set the resolution band-width to10kHz.7.Press the VBW soft key and use theUp/down arrow key to select3kHz.PressENTER to set the video bandwidth to3kHz.8.On the MS2711,press the FREQ/SPANkey and the CENTER soft key.9.Enter1000and press the ENTER key toset the center frequency to1000MHz.10.Press the SPAN soft key and enter0.100.Press the ENTER key to set the span to0.100MHz.11.Press the AMPLITUDE key.12.Press the REF LEVEL soft key and enter–27.Press ENTER to set the referencelevel to–27dBm.13.Press the MARKER key,then the M1softkey.14.Press EDIT and enter1000.Press ENTERto set the M1marker frequency to1000MHz.15.Press the BACK soft key and the M2softkey.16.Press EDIT and enter1000.030.PressENTER to set the M2marker frequency to1000.030MHz(30kHz higher than thecenter frequency).17.Press the DELTA(M2-M1)soft key.18.Press the RUN/HOLD key and read andrecord the amplitude of the signal at theM130kHz offset.19.Press the RUN/HOLD key to read and re-cord five values,then calculate the aver-age of the five recorded values.20.Add–40dB to the average value and ver-ify that the result is£–74dBc/Hz.(For example:–35dBc measured+(-40dB)=–75dBc/Hz.)6.MEASUREMENT ACCURACYMeasurement accuracy involves testing the MS2711 over three frequencies at four power levels.Table1 provides a guide to the frequencies,power levels and reference levels required for each measurement,and can be used to record the readings.a.Equipment Required:·Anritsu68047C Synthesized SignalSource,with options11and15AMS2711HHSA MM3 1981b.Procedure:1.Connect the output of the source to the MS2711RF Input.2.Connect the external power supply (Anritsu part number 40-115)to the MS2711.3.Press and hold the ESCAPE/CLEAR key,then press the ON/OFF key to turn on the Spectrum Analyzer.(This sets the instru-ment to the factory preset state.)NOTEBefore continuing,allow a 30-min-ute warm up for the internal cir-cuitry to stabilize.4.Press the BW/SWEEP key.5.Press the RBW soft key and use the Up/down arrow key to select 10kHz.Press ENTER to set the resolution band-width to 10kHz.6.Press the VBW soft key and use the Up/down arrow key to select 3kHz.Press ENTER to set the video bandwidth to 3kHz.7.Press the FREQ/SPAN key.8.Press the SPAN soft key and enter 5,then press the ENTER key to set the span to 5MHz.9.Press the AMPLITUDE key.10.Press the REF LEVEL soft key and enter 20.Press ENTER to set the reference level to +20dBm.11.Press the FREQ/SPAN key and the CENTER soft key.12.Enter 1000and press the ENTER key to set the center frequency to 1000MHz.13.Set the 68047C output to 1000MHz and the power level to +10dBm.14.Press the MARKER key,then the M1soft key.15.Select the MARKER TO PEAK soft key to position the marker at the center of the response for the test frequency.NOTEOptionally,markers 2,3and 4may be set to OFF for a cleaner display.16.Verify that the M1reading is ±2dB maximum from the input signal.17.Set the 68047C power level to –10dBm.18.Verify that the M1reading is ±2dB maximum from the input signal.19.Press the AMPLITUDE key.20.Press the REF LEVEL soft key and enter –20.Press ENTER to set the reference level to –20dBm.21.Set the 68047C power level to –30dBm.22.Verify that the M1reading is ±2dB maximum from the input signal.23.Set the 68047C power level to –50dBm.24.Verify that the M1reading is ±2dB maximum from the input signal.25.Repeat steps 9through 24for frequen-cies of 1800MHz and 2700MHz.4PRELIMINARY MS2711HHSA MMFreq (MHz)Power Level (dBm)MS2711Ref Level (dBm)M1Reading1000+10+20–10+20–30–20–50–201800+10+20–10+20–30–20–50–202700+10+20–10+20–30–20–50–20Table 1.Measurement Accuracy Settings7.POWER MONITOR VERIFICATION If the Power Monitor (Option 5)is installed in the Spectrum Analyzer,the following test can be used to verify the accuracy of the power measurements.Measurement calibration of the Spectrum Analyzer is not required for this test.a.Equipment Required:·RF Detector,10MHz to 20GHz,Anritsu 560-7N50B ·10dB Attenuator,Weinschel 1R-10·30dB Attenuator,Weinschel 1R-30·RF Reference Source,0.050GHz,Anritsu MA2418A ·DC Power Supply,Anritsu 2000-933b.Procedure 1.Connect the DC power supply to the MA2418A Reference Source.(Refer to Figure 3,page 5.)2.Connect the MA2418A Reference Source to the input of the 560-7N50B RF detec-tor.3.Connect the RF Detector output to the RF Detector input of the MS2711Spec-trum Analyzer.4.Connect the DC power supply to the ap-propriate line voltage to supply power to the MA2418A Reference Source.5.Press and hold the ESCAPE/CLEAR key,then press the ON/OFF key to turn on the Spectrum Analyzer.(This sets the instru-ment to the factory preset state.)6.Press the MODE soft key.e the Up/Down Arrow key to highlight POWER MONITOR ,then press ENTER .8.Press the ZERO soft key to zero the power monitor.When complete,ZERO ADJ:ON is dis-played in the message area.9.Verify that the power monitor reading is 0.0dBm ±1dB.10.Connect the output of the MA2418A Ref-erence Source to the two attenuators so as to add 40dB of attenuation (Figure 3).11.Connect the MA2418A Reference Source and the attenuators to the input of the 560-7N50B RF detector.12.Verify that the power monitor reading is now –40.0dBm ±2dB.MS2711HHSA MM5Figure 3.Power Monitor V erification8.BATTERY PACK REMOVAL AND REPLACEMENTThis procedure provides instructions for removing and replacing the Spectrum Analyzer battery pack.NOTEThe following procedures apply to many similar instruments.Photos and illustra-tions may show instruments other than the MS2711Spectrum Analyzer.1.With the Spectrum Analyzer standing up-right on a stable surface,locate the battery access door (Figure 4).2.Lift up the access door handle and rotate it 90degrees counterclockwise,as illustrated in Figure 5.3.Lift the door and remove,as illustrated in Figure 6.4.Grasp the battery lanyard and pull the bat-tery straight up and out of the unit,as illus-trated in Figure 7.5.Replacement is the opposite of removal.Note the orientation of the battery contacts,and be sure to insert the new battery with the contacts facing the rear of the unit (Figure 8).6MS2711HHSAMMFigure 4.Battery Access Door LocationFigure 5.Rotate the Battery AccessDoor HandleFigure 6.Removingthe Battery Access DoorFigure 7.Removing the BatteryBA TTERY Figure 8.Battery Orientation9.BATTERY INFORMATIONThe following information relates to the care and handling of the Spectrum Analyzer battery,and NiMH batteries in general.·The Nickel Metal Hydride (NiMH)battery sup-plied with the Spectrum Analyzer is shipped in a discharged state.Before using the Spectrum Analyzer,the internal battery must first be charged for three hours,either in the Spectrum Analyzer or in the optional battery charger (Anritsu part number:2000-1029).·Use only Anritsu approved battery packs.·Recharge the battery only in the Spectrum Ana-lyzer or in an Anritsu approved charger.·With a new NiMH battery,full performance is achieved after three to five complete charge and discharge cycles.·When the Spectrum Analyzer or the charger is not in use,disconnect it from the power source.·Do not charge batteries for longer than 24hours;overcharging may shorten battery life.·If left unused a fully charged battery will dis-charge itself over time.·Temperature extremes will affect the ability of the battery to charge:allow the battery to cool down or warm up as necessary before use or charging.·Discharge an NiMH battery from time to time to improve battery performance and battery life.·The battery can be charged and discharged hundreds of times,but it will eventually wear out.·The battery may need to be replaced when the operating time between charging becomes no-ticeably shorter than normal.·Never use a damaged or worn out charger or battery.·Storing the battery in extreme hot or cold places will reduce the capacity and lifetime of the battery.·Never short-circuit the battery terminals.·Do not drop,mutilate or attempt to disassemble the battery.·Do not dispose of batteries in a fire!·Batteries must be recycled or disposed of prop-erly.Do not place batteries in household gar-bage.·Always use the battery for its intended purpose only.MS2711HHSA MM7Figure 9.Spectrum Analyzer Battery10.FRONT PANEL ASSEMBLY REMOVALAND REPLACEMENT This procedure provides instructions for removing and replacing the Spectrum Analyzer front panel as-sembly.With the front panel assembly removed,the LCD display,keypad PCB,keypad membrane,and main PCB assemblies can be removed and replaced.1.Place the Spectrum Analyzer face up on a work surface.2.Remove the four rubber corner bumpers by carefully sliding the bumpers off of the case corners (Figure 12).3.With the bumpers removed,the access holes for the case screws are e a Phil-lips screwdriver to remove the four screws securing the two halves of the Spectrum An-alyzer case together.4.Carefully lift up on the right side (as viewed from the front)of the front half of the case and begin to separate the two halves.CAUTIONDo not force or pull the two halves of the case apart as there are delicate cables at-tached between the two halves that must be disconnected first.5.Carefully depress the latch tab and discon-nect the LCD display cable from J12on the main PCB.6.Carefully disconnect the keypad interface ca-ble from J1on the main PCB.7.Carefully disconnect the LCD displaybacklight cable from J15on the main PCB.8.Remove the front panel assembly.9.Reverse the above steps to replace the front panel assembly.NOTEThe corner bumpers only mount one way.That is,the raised area inside one end of the bumper (Figure 11)is made to conform to the contour of the front cover only.8MS2711HHSAMMFigure 10.Removing the Corner BumpersJ12Figure 11.Spectrum Analyzer Front Panel Cable Con-nectionsFigure 12.Corner Bumper Detail11.LCD ASSEMBLY REPLACEMENTThis procedure provides instructions for removing and replacing the Liquid Crystal Display (LCD)once the front panel assembly has been separated from the Spectrum Analyzer.1.Remove the front panel assembly as directed in section 10.2.Place the front panel assembly face down on a protected work surface.3.Remove the 14Phillips screws that attach the backing plate to the front panel assem-bly.4.Release the LCD display cable from the re-taining clip on the front panel backing plate.5.Remove the front panel backing plate,care-fully feeding the LCD cable through the ac-cess hole to avoid damage to the cable or connector.6.Remove the rubber cushion pad from the LCD assembly and remove the assembly.7.Reverse the above steps to install the re-placement assembly.12.KEY PAD PCB REPLACEMENTThis procedure provides instructions for removing and replacing the key pad PCB.1.Remove the front panel assembly as directed in section 10.2.Place the front panel assembly face down on a protected work surface.3.Remove the 14Phillips screws that attach the backing plate to the front panel assem-bly.4.Release the LCD display cable from the re-taining clip on the front panel backing plate (Figure 13).5.Remove the front panel backing plate,care-fully feeding the LCD cable through the ac-cess hole to avoid damage to the cable or con-nector.6.Remove the rubber cushion pad from the key pad PCB and remove the PCB.7.Reverse the above steps to install the re-placement assembly.MS2711HHSA MM 9Figure 13.Front Panel Backing PlateFigure 14.Front Panel Keypad PCB Location13.KEY PAD MEMBRANE REPLACEMENT This procedure provides instructions for replacing the key pad membrane.1.Remove the front panel assembly as directed in section 10.2.Remove the key pad PCB as directed in sec-tion 12.3.Remove the keypad membrane by gently pulling the membrane up and out of the holes in the front panel.4.Reverse the above steps to install the re-placement membrane.14.MAIN PCB ASSEMBLY REPLACEMENT This procedure provides instructions for replacing the main PCB assembly with the connector panel at-tached.The assembly consist of two PCBs (Control and RF)which must be replaced together.1.Remove the front panel assembly as directed in section 10.2.Disconnect the battery connector from J13on the main PCB.3.Disconnect the semi-rigid coaxial cable from the RF connector on the connector panel.4.Remove the three PCB mounting screws and remove the Control PCB assembly with the connector panel attached.5.Remove the three .25”standoffs and four Phillips screws and remove the RF PCB.6.Reverse the above steps to install the new main PCB.NOTEThe main PCB connector panel fits into grooves in the two halves of the Spectrum Analyzer case.Make sure the panel is cor-rectly aligned with the grooves before reas-sembling the two halves together.10MS2711HHSA MMFigure 15.Front Panel Keypad MembranePCB MOUNTINGSCREWS (3)TTERY CONNECTORFigure 16.Control PCBCONNECTOR P2TO RF IN CONNECTORFigure 17.RF PCB15.REPLACEABLE PARTSReplaceable parts for the Model MS2711Spectrum Analyzer are listed below.MS2711HHSA MM 11Part NumberDescription QtyAccessories10580-00026User's Guide,MS2711Spectrum Analyzer110580-00036Programming Manual,MS2711Spectrum Analyzer (available on disk only)12300-347Software Tools,MS2711Spectrum Analyzer 140-115Power Supply 12000-1029Battery Charger22N50Precision Short/Open,N Male 1SM/PL Connector,RF Termination 1806-62Cable Assy,Cig Plug,Female 1800-441Serial Interface Cable Assy 148258Soft Carrying Case 1Replaceable Parts510-87N-Connector2551-152Option 05Input Connector 115-102Liquid Crystal Display Assy 1633-27Rechargeable Battery,NiMH 1ND51899MS2711Logic and Digital Con-trol PCB Assembly1ND53263MS2711Logic and Digital Con-trol PCB Assembly with Option 051ND53250Option 05PCB Assembly 147812-3Keypad PCB Assy 146649-1Membrane Keypad,Main1Table 2.Replaceable Parts ListPart NumberDescription QtyHardware900-861Pan Head Screw,4-20,0.36515900-869Screw,4-40,0.8754900-720Screw,4-40,0.1873900-697Screw,4-40,0.3123785-929M-F Stand off,4-40,11/163900-326Kep Nut,4-40,0.1878790-516Hole Plug,0.6875L 1790-42Hole Plug,0.6251761-79Cap Vinyl,Black,round1Case Parts 46652-1Top Case only 146665Top Case w/hardware 146653-1Bottom Case only 146664Bottom Case w/hardware 148231-1Battery Door1790-509790-510790-511Battery Door Latch (3pieces)146655Case Corner Bumpers 446662LCD Retainer Plate 148241Foam,LCD Corners 848278Foam,LCD Window 146659Foam,LCD Backing 146661Foam,Keypad Backing 148246Foam,Battery Door 148271Foam,Battery Compartment 1720-19Cable Clamp1790-515Spring,Battery Compartment 148274ID Label,Model MS27111NOTESUNITED STATES ANRITSU COMPANY685Jarvis DriveMorgan Hill,CA95037-2809 Telephone:(408)776-8300 1-800-ANRITSUFAX:408-776-1744FRANCEANRITSU S.A9Avenue du QuebecZone de Courtaboeuf91951Les Ulis CedexTelephone:016-44-66-546FAX:016-44-61-065JAPANANRITSU CORPORATION1800Onna Atsugi-shiKanagawa-Prf.243JapanTelephone:0462-23-1111FAX:0462-25-8379ANRITSU COMPANY10New Maple Ave.,Unit305Pine Brook,NJ07058Telephone:(201)227-8999,1-800-ANRITSU FAX:201-575-0092GERMANYANRITSU GmbHGrafenberger Allee54-56D-40237Dusseldorf,GermanyTelephone:0211-68550FAX:0211-685555SINGAPOREANRITSU(SINGAPORE)PTE LTD.3Shenton Way#24-03Shenton HouseSingapore0106Telephone:2265206FAX:2265207ANRITSU COMPANY1155E.Collins Blvd Richardson,TX75081 Telephone:1-800-ANRITSU FAX:972-671-1877INDIAMEERA AGENCIES(P)LTD.A-23Hauz KhasNew Delhi110016Telephone:011-685-3959FAX:011-686-6720SOUTH AFRICAETECSA12Surrey Square Office Park330Surrey AvenueFerndale,Randburt,2194South AfricaTelephone:011-27-11-787-7200FAX:011-27-11-787-0446AUSTRALIA ANRITSU PTY.LTD.Unit3,170Foster Road Mt Waverley,VIC3149 AustraliaTelephone:03-9558-8177 FAX:03-9558-8255ISRAELTECH-CENT,LTD.Haarad St.No.7,Ramat HaahayalTel-Aviv69701Telephone:(03)64-78-563FAX:(03)64-78-334SWEDENANRITSU ABBotivid CenterS-1585Stockholm,SwedenTelephone:(08)534-717-00FAX:(08)534-717-30BRAZILANRITSU ELECTRONICA LTDA.Praia de Botafogo,440,Sala2401CEP22250-040,Rio de Janeiro,RJ,Brasil Telephone:021-28-69-141FAX:021-53-71-456ITALYANRITSU Sp.ARoma OfficeVia E.Vittorini,12900144Roma EURTelephone:(06)50-22-666FAX:(06)50-22-4252TAIWANANRITSU CO.,LTD.8F,No.96,Section3Chien Kuo N.RoadTaipei,Taiwan,R.O.C.Telephone:(02)515-6050FAX:(02)509-5519CANADAANRITSU INSTRUMENTS LTD. 215Stafford Road,Unit102 Nepean,Ontario K2H9C1 Telephone:(613)828-4090 FAX:(613)828-5400KOREAANRITSU CORPORATION LTD.#901Daeo Bldg.26-5Yeoido Dong,YoungdeungpoSeoul Korea150010Telephone:02-782-7156FAX:02-782-4590UNITED KINGDOMANRITSU LTD.200Capability GreenLuton,BedfordshireLU13LU,EnglandTelephone:015-82-41-88-53FAX:015-82-31-303CHINAANRITSU BEIJING SERVICE CENTER Beijing Fortune Building416W,5Dong San Huan Bei LuChaoyang qu,Beijing100004,China Telephone:011861065909237FAX:011861065909236Table3.Anritsu Service CentersNOTES。
logic analyzer 文件格式解析

logic analyzer 文件格式解析
1、每个支持的歌曲格式不同,在音乐播放器里面可以查看歌词的,这是一种多媒体格式。
2、根据你的软件,一般来说会要求你转换成 wma 格式才能正常播放。
2、根据你的软件,一般来说会要求你转换成 wma 格式才能正常播放。
3、你需要把 logic analyzer 格式的歌曲,从专辑里复制到目录下,然后转换成 mp3 格式,最好再另存为 wav 格式( wma 格式),你就可以正常播放了。
其实 logic 文件属于计算机操作界面特效,如果当中含有中英文对照,那应该是调用的 DirectX 程序。
- 1 -。
Gold Line Polarity Analyzer 操作手册说明书
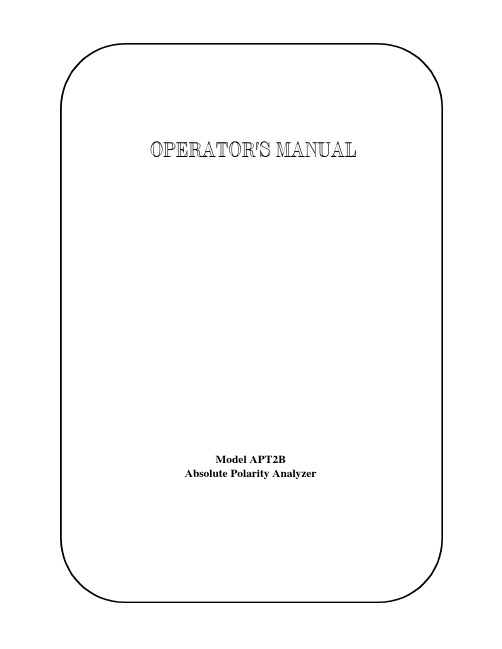
OPERATOR'S MANUALModel APT2BAbsolute Polarity AnalyzerOPERATOR'S MANUAL - MODEL APT2BThe Gold Line Polarity Analyzer utilizes state of the art signal processing to accurately determine absolute polarity which is unimpaired by passive crossovers or signal waveform distortions produced by the device under test. The Absolute Polarity Analyzer works on tweeters, mid-ranges, woofers, subwoofer speakers and cabinets, equalizers, amplifier and crossovers. With this handy instrument an entire speaker system can be checked in only seconds.THEORY OF OPERATIONThe Gold Line Polarity Analyzer analyzes the initial rise and the peak amplitude of a repetitive acoustic pulse picked up by the microphone to determine and indicate the absolute polarity of the acoustic pulse. A repetitive test pulse signal, with a fast rise and a known polarity is applied to the loudspeaker under test, with or without an amplifier. The Polarity Analyzer contains special discriminating circuitry to minimize the influence of loudspeaker transient distortion (preshoot) which varies greatly from speaker to speaker and unless properly screened, is a potential source of false polarity indication. To check acoustical or electrical polarity, the generator is connected to the input of the device under test. The detector is utilized to pick up the output signal. The analyzer section processes the information and decides whether the device under test reverses signal polarity or not. The results are displayed via two LEDs: (+) or POSITIVE-GOING POLARITY and ( - ) or NEGATIVE-GOING POLARITY. THE APT2B features the Polarity Analyzer and the Pulse Generator as separate units allowing the user greater mobility in halls or stadiums since either module can be placed in the most convenient location. The polarity analyzer module contains two LEDs to indicate POSITIVE-GOING POLARITY or NEGATIVE-GOING POLARITY, the pick up microphone, the push to activate button and a mic selector switch. Select between using the built-in (internal) microphone or an external microphone that can be plugged into either a ¼” phone or a 3 pin XLR input jack. Both jacks provide for a balanced input. The pulse generator module has a RED flashing LED to indicate when the generator is in operation. The generator output is selectable between either a line level output signal or a signal capable of driving speakers without amplification. The pulse output is also sent to a ¼” phone and a 3 pin XLR output jack. Both jacks provide for balanced line output and unbalanced speaker output.OPERATING INSTRUCTIONSSPEAKER POLARITY TEST1. Speaker leads should be terminated with a ¼ inch phone plug or 3 pin XLR male connector. The ¼ inch tip should be (+) positive with the sleeve as ground. The XLR should be P1 - ground, P2 - hot.2. Activate the PULSE GENERATOR by switching from OFF to LINE or SPKR. A one second interval strobing pulse should be indicated by the RED LED and heard from the speaker.3. Activate the POLARITY ANALYZER by depressing the PUSH to activate button on the front panel, and hold the analyzer or separate microphone in front of the speaker, preferably centered and if possible as close as two or three feet. One of the LEDs should light for about 1/3 second on each pulse indicating the absolute acoustic polarity: (+) indicates positive-going acoustic polarity (the speaker cone is displaced towards the analyzer creating a positive air pressure pulse). This also means that the positive (+) terminal of the speaker (usually coded with a red dot) is connected to the TIP of the phone plug. Conversely, (-) indicates negative-going polarity and means that the positive (+) terminal of the speaker is the one connected to the SLEEVE of the phone jack.SPEAKER PLUS AMPLIFIER TEST1. Make sure the system is off. Set the amplifier volume control to minimum.2. Plug one end of a shielded audio cable into the input of the amplifier for the system under test.3. Activate the PULSE GENERATOR. A one second interval pulse should be indicated by the RED LED.4. Activate the amplifier and advance the volume control to set a normal acoustic level. A one second interval pulse should be heard from the speaker.5. Activate the POLARITY ANALYZER by pressing the PUSH to activate button and sequentially hold it in front of each speaker to be tested, preferably centered, and about two or three feet away from the speaker. Note the LED indication for each speaker. One of the LEDs should light for about 1/3 second on each pulse indicating the overall absolute polarity relation between the acoustic output and the amplifier input receiving the test signal: (+) indicates positive-going acoustic polarity and (-) indicates negative-going polarity. Generally all speakers in a multiple system are intended to have the same polarity.ANALYZER SPECIFICATIONSLED Indication: 300ms ON duration per pulse typical.( + ): indicates positive-going pulse polarity.( - ): indicates negative-going pulse polarity.REQUIRED ACOUSTIC LEVEL AT ANALYZER: useful range 70dBc to greater than 110dBc. BATTERY:9VoltBATTERY DRAIN: Mainly from LED approx. 20mA peak instantaneous.PULSE GENERATOR SPECIFICATIONSPULSE WAVEFORM:Repetition rate: 1s nominalPolarity: Positive-goingLINE OUTPUT PULSE for driving an amplifier input:Amplitude: 0.8V peak typicalRise time: <100 µsFall time: 40 ms typicalSource impedance: 50 Ω nominalDuty factor: 0.3% typicalBattery drain line output: 1.5mA averageSPEAKER OUTPUT PULSE for driving a loudspeaker directly:Amplitude: 6.5V peak to 4Ωspeaker (9V battery)Rise time: <100 µsFall time: 1.5ms typicalPOWER: 14 watts peak instantaneous (4Ωspeaker, 9V battery.)Duty factor: 0.15% typicalBattery saver circuit: Cuts in when no speaker is connected.Battery drain: 3.7mA with 4Ωspeaker.WARRANTY and Factory ServiceGOLD LINE products are proudly made in the USA and are covered by a one year limited warranty. For details of this warranty, consult the enclosed warranty registration card or your local dealer.GOLD LINE Customer Service will help you get the most from your new analyzer. For answers to questions regarding use of the unit, or for information not covered in this manual, please write us. If you are experiencing difficulties with your analyzer, please consult your dealer regarding factory service. If factory service is needed, you may call or fax us between 9:00am and 4:30pm US Eastern Time for instructions and a return authorization.U.S. Patent 5,319,714Enter your serial#________________ date of purchase________________12-709 m_apt2b_7h27.docBox 500 West Redding, CT. 06896 203-938-2588 phone - 203-938-8740 faxhttp://******************************************。
GPXLogicAnalyzers3000Series商品说明书
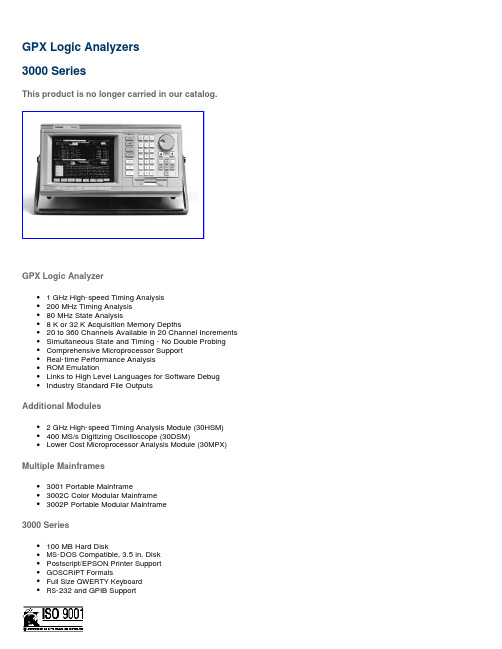
GPX Logic Analyzers3000 SeriesThis product is no longer carried in our catalog.GPX Logic Analyzer1 GHz High-speed Timing Analysis200 MHz Timing Analysis80 MHz State Analysis8 K or 32 K Acquisition Memory Depths20 to 360 Channels Available in 20 Channel IncrementsSimultaneous State and Timing - No Double ProbingComprehensive Microprocessor SupportReal-time Performance AnalysisROM EmulationLinks to High Level Languages for Software DebugIndustry Standard File OutputsAdditional Modules2 GHz High-speed Timing Analysis Module (30HSM)400 MS/s Digitizing Oscilloscope (30DSM)Lower Cost Microprocessor Analysis Module (30MPX) Multiple Mainframes3001 Portable Mainframe3002C Color Modular Mainframe3002P Portable Modular Mainframe3000 Series100 MB Hard DiskMS-DOS Compatible, 3.5 in. DiskPostscript/EPSON Printer SupportGOSCRIPT FormatsFull Size QWERTY KeyboardRS-232 and GPIB SupportTektronix Measurement products are manufactured in ISO registered facilities. For additional information or to order, contact your local Tektronix representative. 3000 Series Application Module Selection Guide3000 Series System Selection GuideOrdering InformationOur most popular configurations are listed here. For complete ordering information please see configuration guide. Part number 5EA 8297-3 (U.S.) or 5EW 8297-3 (International).3001 Series Logic Analyzers3001GPX General Purpose and Microprocessor Analysis InstrumentIncludes: 16-CH @ 1 GHz Timing, 80-CH @ 200 MHz Timing, 80-CH @ 80 MHz State, 8 K Acquisition Memory, 4 P6490 Probes, and 720 KB Floppy.Opt. 1A: 32PA Performance Analysis SoftwareOpt. 1D: Delete 20 Channels (60 total)Opt. 2D: Delete 40 Channels (40 total)Opt. 3D: Delete 60 Channels (20 total)Opt. 1K: Add QWERTY KeyboardOpt. 1M: Add Hard DiskOpt. 1S: Substitute 32 K Acquisition MemoryOpt. 1Z: Add Keyboard and Hard Disk (Value Pack)3001MPX 8/16/32-Bit Microprocessor Analysis InstrumentIncludes: 96-CH State and 9-CH @ 200 MHz Timing (req. Opt. 1H), P6480 State Probe without Leadset, and 720 KB Floppy.Opt. 1A: 30DA01 Performance Analysis SoftwareOpt. 1F: P6480 General Purpose Probe AdapterOpt. 1H: One P6486 Timing ProbeOpt. 1K: Add QWERTY KeyboardOpt. 1L: One P6486 High Performance LeadsetOpt. 1M: Add Hard Disk3001HSM High-speed Acquisition InstrumentIncludes: 20-CH @ 400 MHz, or 4-CH @ 2 GHz, or 20-CH @ 200 MHz Dual Threshold Timing, TwoP6487 High-speed Probes with Standard Leadsets, and 720 KB Floppy.Opt. 1K: Add QWERTY KeyboardOpt. 1L: Add Two 400 MHz LeadsetsOpt. 4L: Add One 2 GHz LeadsetOpt. 5L: Add Two 2 GHz LeadsetsOpt. 1M: Add Hard DiskOpt. 2A: Add 18-CH 95 MHz Sync Mode (req. 1L)Preconfigured 3002 Logic Analyzers3002CG 3002C M/F with One 32GPXIncludes: 3002C, 14 in. Color Monitor, HDD, 720 KB Floppy, Keyboard, One 32GPX, Four P6490s and Performance Analysis SW.Opt. 1S: Substitute one 32GPD with 32 K Acquisition Memory3002CGG 3002C M/F with Two 32GPXsIncludes: 3002C, 14 in. Color Monitor, HDD, 720 KB Floppy, Keyboard, Two 32GPXs, Eight P6490s and Performance Analysis SW.Opt. 1S: Substitute two 32GPDs with 32 K Acquisition Memory3002CGH 3002C M/F with One 32GPX and One 30HSMIncludes: 3002C, 14 in. Color Monitor, HDD, 720 KB Floppy, Keyboard, One 32GPX, Four P6490s , One 30HSM, Two P6487s and Performance Analysis SW.Opt. 1S: Substitute one 32GPD with 32 K Acquisition Memory3002CGD 3002C M/F with One 32GPX and One 30DSMIncludes: 3002C, 14 in. Color Monitor, HDD, 720 KB Floppy, Keyboard, One 32GPX, Four P6490s, One 30DSM, Two P6109Bs, and Performance Analysis SW.Opt. 1S: Substitute One 32GPD with 32 K Acquisition Memory3002CX 3002C M/F with One 30MPXIncludes: 3002C, 14 in. Color Monitor, HDD, 720 KB Floppy, Keyboard, One 30MPX, One P6480 and Performance Analysis SW.3002CXX 3002C M/F with Two 30MPXsIncludes: 3002C, 14 in. Color Monitor, HDD, 720 KB Floppy, Keyboard, Two 30MPXs, Two P6480s, and Performance Analysis SW.3002CH 3002C M/F with One 30HSMIncludes: 3002C, 14 in. Color Monitor, HDD, 720 KB Floppy, Keyboard, One 30HSM, and Two P6487s. 3002CHH 3002C M/F with Two 30 HSMsIncludes: 3002C, 14 in. Color Monitor, HDD, 720 KB Floppy, Keyboard, Two 30HSMs, and Four P6487s.3002CXH 3002C with One 30MPX and One 30HSMIncludes: 3002C, 14 in. Color Monitor, HDD, 720 KB Floppy, Keyboard, One 30MPX, One P6480, One 30HSM, Two P6487s and Performance Analysis SW.3002CXD 3002C with One 30MPX and One 30DSMIncludes: 3002C, 14 in. Color Monitor, HDD, 720 KB Floppy, Keyboard, One 30MPX, One P6480, One P6486, One 30DSM, Two P6109Bs, and Performance Analysis SW.3002CHD 3002C with One 30HSM and One 30DSMIncludes: 3002C, 14 in. Color Monitor, 100 MB HDD, 720 KB Floppy, Keyboard, One 30HSM, TwoP6487s, One 30DSM, and Two P6109Bs.The above 3002 systems have options to substitute the color monitor with a flat panel display, add additional leadsets, and other options to customize the systems to your needs.3002 Series Mainframes3002C Two-slot System Mainframe with Color MonitorIncludes: 14 in. Color Monitor, Hard Disk, 720 KB Floppy, QWERTY Keyboard.3002P Two-slot System Mainframe with EL Flat-panel DisplayIncludes: 9 in. Electroluminescent Flat-panel Display, Hard Disk, 720 KB Floppy, and QWERTY Keyboard.3002E Two-slot System Expansion MainframeIncludes: 9 in. and 4 ft. TekLink Cable, Mainframe Mounting Plate.International Power Plugs OptionsOpt. A1: Universal Euro 220 V, 50 HzOpt. A2: United Kingdom 240 V, 50 HzOpt. A3: Australian 240 V, 50 HzOpt. A4: North American 240 V, 60 HzOpt. A5: Switzerland 220 V, 50 HzSee Customer Information Section for additional description.3002 Series Instrument Modules32GPX General Purpose and Microprocessor Analysis ModuleIncludes: 8 K Acquisition Memory and Four P6490 Probes and Leadsets.Opt. 1A: 32PA Performance Analysis SoftwareOpt. 2W: Add One Welding Connector32GPD General Purpose and Microprocessor Analysis ModuleIncludes: 32 K Acquisition Memory and Four P6490 Probes and Leadsets.Opt. 1A: 32PA Performance Analysis SoftwareOpt. 2W: Add One Welding Connector30MPX 8/16/32-Bit Microprocessor Analysis Application ModuleIncludes: P6480 State Probe without Leadset.Opt. 1A: 30DA01 Performance Analysis SoftwareOpt. 1F: P6480 General Purpose Probe AdapterOpt. 1H: One P6486 Timing ProbeOpt. 1L: One P6486 High-performance Leadset30HSM High-speed Application ModuleIncludes: Two P6487 with Standard Leadset.Opt. 2A: 18-CH 95 MHz Sync Mode Adapter (req. Opt. 1L)Opt. 1L: Add Two High-performance LeadsetsOpt. 4L: Add One 2 GHz LeadsetOpt. 5L: Add Two 2 GHz Leadsets30DSM Digitizing Oscilloscope ModuleIncludes: Two P6109B: 10:1 Probes.Service Assurance OptionsOpt. R2: Adds two years of post-warranty Repair Protection30DSM/30HSM/30MPX,3001GPX/3001HSM3001MPX3002C3002CG3002CGD/3002CGG/3002CGH3002CH/3002CHD3002CHH/3002CX/3002CXD/3002CXH/3002CXX3002E3002ED3002P32GPD32GPXOpt. Q0 Onsite Installation32GPX32GPDAdditional AccessoriesP649032GPX Data Acquisition ProbeP648030MPX State Data Acquisition Probe Without LeadOpt. 1F: Add General Purpose Probe AdapterP6486High-speed Data Acquisition Probe with Standard Leadset for 30MPX Opt. 1L: Add One High-performance LeadsetP6487High-speed Data Acquisition Probe with Standard Leadset for 30HSM Opt. 1L: Add One High-performance LeadsetFasTrak: Micro-Training PackageCenTrak: High-speed Demo Fixture1200C01RS-232 COMM Pack30C02GPIB COMM PackPrototype Debug Tool Support Packages30RP2General Purpose PDT with ROM ProbeOpt. 01: Add 24/28/32-Pin General Purpose ROM Probe AdapterOpt. 02: Add 40-Pin DIP ROM Probe Adapter32GPX/32GPD Microprocessor Support Packages32DM028085 Disassembly Software, Socketed 40-Pin DIP32DM048086/8088/80C86/80C88 Disassembly Software, Socketed 40-Pin DIP32DM0680186/80188/80C186/80C188 Disassembly Software, Socketed 68-Pin PGAOpt. 1S Substitute Socketed 68-Pin PLCC32DM078031/8051 Disassembly Software, Socketed 40-Pin Dip32DM0880286/80C286 Disassembly Software, Supports Socketed 69-Pin PGAOpt. 1S: Substitute Socketed 68-Pin PLCC32DM0980386DX Disassembly Software, Socketed 132-Pin PGAOpt. 1S: Substitute Soldered 132-Pin JEDEC PQFP (AMD Devices only)32DM1080386SX Disassembly Software, Soldered 100-Pin JEDEC PQFP32DM12A80486DX/DX2/486SX/487SX Disassembly Software, Socketed 168-Pin PGA32DM13APentium Disassembly Software, Socketed 273-Pin PGA32DM216800/2/8 Disassembly Software, Socketed 40-Pin DIP32DM246809/6809E Disassembly Software, Socketed 40-Pin DIP32DM2768000/68010/68HC000/68HC001/68EC000 Disassembly SW, Socketed 64-Pin DIP (68000/010/HC000) Opt. 1S: Substitute Socketed 68-Pin PGA (68000/010/HC000/HC001)Opt. 2S: Substitute Socketed 68-Pin PLCC (68EC000)Opt. 3S: Substitute Socketed 68-Pin PLCC (68HC000)32DM3168020/68EC020 Disassembly Software, Socketed 114-Pin PGA (68020)Opt. 1S: Substitute Socketed 100-Pin PGA (68EC020)Opt. 2S: Substitute Soldered 132-Pin JEDEC CQFP (68020)32DM3368030/68EC030 Disassembly Software, Socketed 128-Pin PGAOpt. 1S: Substitute Soldered 132-Pin JEDEC CQFPRequest SalesContact Request a Demo Email This Page Printable Page URL for Favorites Tektronix SiteHome | Products | Support | Buy | Contact Us | Investors | Careers | International | myTek© Copyright Tektronix, Inc. | Terms of Use | Privacy Statement | Sitemap | Learn More。
Signaling Analyzer使用指南
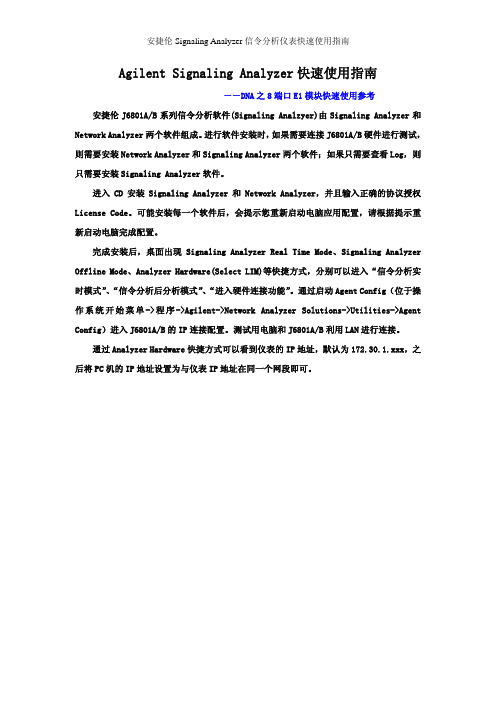
Agilent Signaling Analyzer快速使用指南――DNA之8端口E1模块快速使用参考 安捷伦J6801A/B系列信令分析软件(Signaling Analzyer)由Signaling Analyzer和Network Analyzer两个软件组成。
进行软件安装时,如果需要连接J6801A/B硬件进行测试,则需要安装Network Analyzer和Signaling Analyzer两个软件;如果只需要查看Log,则只需要安装Signaling Analyzer软件。
进入CD安装Signaling Analyzer和Network Analyzer,并且输入正确的协议授权License Code。
可能安装每一个软件后,会提示您重新启动电脑应用配置,请根据提示重新启动电脑完成配置。
完成安装后,桌面出现Signaling Analyzer Real Time Mode、Signaling Analyzer Offline Mode、Analyzer Hardware(Select LIM)等快捷方式,分别可以进入“信令分析实时模式”、“信令分析后分析模式”、“进入硬件连接功能”。
通过启动Agent Config(位于操作系统开始菜单->程序->Agilent->Network Analyzer Solutions->Utilities->Agent Config)进入J6801A/B的IP连接配置。
测试用电脑和J6801A/B利用LAN进行连接。
通过Analyzer Hardware快捷方式可以看到仪表的IP地址,默认为172.30.1.xxx,之后将PC机的IP地址设置为与仪表IP地址在同一个网段即可。
1、运行Signaling Analzyer软件Signaling Analyzer Real Time Mode,进入配置界面1、这里可以看到当前连接的DNA(J6801A)模块列表。
proteus元器件清单

Proteus 仿真库简介元件名称中文名说明7407 驱动门1N914 二极管74Ls00 与非门74LS04 非门74LS08 与门74LS390 TTL 双十进制计数器7SEG 4针BCD-LED 输出从0-9 对应于4根线的BCD码7SEG 3-8译码器电路BCD-7SEG[size=+0]转换电路ALTERNATOR 交流发电机AMMETER-MILLI mA安培计AND 与门BATTERY 电池/电池组BUS 总线CAP 电容CAPACITOR 电容器CLOCK 时钟信号源CRYSTAL 晶振D-FLIPFLOP D触发器FUSE 保险丝GROUND 地LAMP 灯LED-RED 红色发光二极管LM016L 2行16列液晶可显示2行16列英文字符,有8位数据总线D0-D7,RS,R/W,EN三个控制端口(共14线),工作电压为5V。
没背光,和常用的1602B功能和引脚一样(除了调背光的二个线脚)LOGIC ANALYSER 逻辑分析器LOGICPROBE 逻辑探针LOGICPROBE[BIG] 逻辑探针用来显示连接位置的逻辑状态LOGICSTATE 逻辑状态用鼠标点击,可改变该方框连接位置的逻辑状态LOGICTOGGLE 逻辑触发MASTERSWITCH 按钮手动闭合,立即自动打开MOTOR 马达OR 或门POT-LIN 三引线可变电阻器POWER 电源RES 电阻RESISTOR 电阻器SWITCH 按钮手动按一下一个状态SWITCH-SPDT 二选通一按钮VOLTMETER 伏特计VOLTMETER-MILLI mV伏特计VTERM 串行口终端Electromechanical 电机Inductors 变压器Laplace Primitives 拉普拉斯变换Memory IcsMicroprocessor IcsMiscellaneous 各种器件AERIAL-天线;ATAHDD;ATMEGA64;BATTERY;CELL;CRYSTAL-晶振;FUSE;METER-仪表;Modelling Primitives 各种仿真器件是典型的基本元器模拟,不表示具体型号,只用于仿真,没有PCBOptoelectronics 各种发光器件发光二极管,LED,液晶等等PLDs & FPGAsResistors 各种电阻Simulator Primitives 常用的器件Speakers & SoundersSwitches & Relays 开关,继电器,键盘Switching Devices 晶阊管Transistors 晶体管(三极管,场效应管)TTL 74 seriesTTL 74ALS seriesTTL 74AS seriesTTL 74F seriesTTL 74HC seriesTTL 74HCT seriesTTL 74LS seriesTTL 74S seriesAnalog Ics 模拟电路集成芯片Capacitors 电容集合CMOS 4000 seriesConnectors 排座,排插Data Converters ADC,DACDebugging Tools 调试工具ECL 10000 Series------------------------------------------------------------PROTEUS元件库元件名称及中英对照AND 与门ANTENNA 天线BATTERY 直流电源BELL 铃,钟BVC 同轴电缆接插件BRIDEG 1 整流桥(二极管)BRIDEG 2 整流桥(集成块)BUFFER 缓冲器BUZZER 蜂鸣器CAP 电容CAPACITOR 电容CAPACITOR POL 有极性电容CAPVAR 可调电容CIRCUIT BREAKER 熔断丝COAX 同轴电缆CON 插口CRYSTAL 晶体整荡器DB 并行插口DIODE 二极管DIODE SCHOTTKY 稳压二极管DIODE VARACTOR 变容二极管MPX_3-SEG 3段LEDMPX_7-SEG 7段LEDMPX_7-SEG_DP 7段LED(带小数点) ELECTRO 电解电容FUSE 熔断器INDUCTOR 电感INDUCTOR IRON 带铁芯电感INDUCTOR3 可调电感JFET N N沟道场效应管JFET P P沟道场效应管LAMP 灯泡LAMP NEDN 起辉器LED 发光二极管METER 仪表MICROPHONE 麦克风MOSFET MOS管MOTOR AC 交流电机MOTOR SERVO 伺服电机NAND 与非门NOR 或非门NOT 非门NPN NPN三极管NPN-PHOTO 感光三极管OPAMP 运放OR 或门PHOTO 感光二极管PNP 三极管NPN DAR NPN三极管PNP DAR PNP三极管POT 滑线变阻器PELAY-DPDT 双刀双掷继电器RES1.2 电阻RES3.4 可变电阻RESISTOR BRIDGE ? 桥式电阻RESPACK ? 电阻SCR 晶闸管PLUG ? 插头PLUG AC FEMALE 三相交流插头SOCKET ? 插座SOURCE CURRENT 电流源SOURCE VOLTAGE 电压源SPEAKER 扬声器SW ? 开关SW-DPDY ? 双刀双掷开关SW-SPST ? 单刀单掷开关SW-PB 按钮THERMISTOR 电热调节器TRANS1 变压器TRANS2 可调变压器TRIAC ? 三端双向可控硅TRIODE ? 三极真空管VARISTOR 变阻器ZENER ? 齐纳二极管DPY_7-SEG_DP 数码管SW-PB 开关----------------------------------------------------------------------PROTEUS原理图元器件库详细说明Device.lib 包括电阻、电容、二极管、三极管和PCB的连接器符号ACTIVE.LIB 包括虚拟仪器和有源器件DIODE.LIB 包括二极管和整流桥DISPLAY.LIB 包括LCD、LEDBIPOLAR.LIB 包括三极管FET.LIB 包括场效应管ASIMMDLS.LIB 包括模拟元器件VALVES .LIB 包括电子管ANALOG.LIB 包括电源调节器、运放和数据采样IC CAPACITORS.LIB 包括电容COMS.LIB 包括 4000系列ECL.LIB 包括ECL10000系列MICRO.LIB 包括通用微处理器OPAMP.LIB 包括运算放大器RESISTORS.LIB 包括电阻FAIRCHLD .LIB 包括FAIRCHLD 半导体公司的分立器件LINTEC.LIB 包括 LINTEC公司的运算放大器NATDAC.LIB 包括国家半导体公司的数字采样器件NATOA.LIB 包括国家半导体公司的运算放大器TECOOR.LIB 包括TECOOR公司的 SCR 和TRIAC TEXOAC.LIB 包括德州仪器公司的运算放大器和比较器ZETEX .LIB 包括ZETEX 公司的分立器件。
- 1、下载文档前请自行甄别文档内容的完整性,平台不提供额外的编辑、内容补充、找答案等附加服务。
- 2、"仅部分预览"的文档,不可在线预览部分如存在完整性等问题,可反馈申请退款(可完整预览的文档不适用该条件!)。
- 3、如文档侵犯您的权益,请联系客服反馈,我们会尽快为您处理(人工客服工作时间:9:00-18:30)。
DesignCon 2005 Connectorless Logic Analyzer Probing – Mechanical and Electrical AdvantagesBrock J. LaMeres, Agilent TechnologiesBrent A. Holcombe, Agilent TechnologiesGeorge Marshall, Precision InterconnectAbstractLogic Analysis is a powerful tool in aiding engineers while debugging digital systems. As system data rates continue to increase, making a successful logic analyzer measurement is becoming more and more difficult. The physical connection between the logic analyzer and the target PCB is now a major concern for engineers. The industry standard connection for logic analyzers over the past 10 years has been the Mictor connector. While this connector provides the high density connection desired, its electrical loading and mechanical reliability make it ill-suited for today’s systems. Connectorless probing has emerged as the new industry standard to replace the Mictor connector. This new technology offers a host of electrical and mechanical advantages over the Mictor connector. This paper will describe the details of why this technology is superior and aid engineers in making a decision on when to upgrade to this new methodology.Author(s) BiographyBrock J. LaMeres received his BSEE from Montana State University in 1998 and his MSEE from the University of Colorado in 2001. He is currently a Ph.D. candidate at the University of Colorado where his research focus is VLSI Circuit Design and High-Speed I/O for next generation IC’s. For the past 6 years he has worked as a hardware design engineer for Agilent Technologies in Colorado Springs where he designs logic analyzer probes and acquisition boards. LaMeres has published 25 technical articles in the area of signal integrity and has a patent in the field of logic analyzer probing. LaMeres is a registered Professional Engineer in the State of Colorado.Brent A. Holcombe received his BSME from the University of Washington in 1996. He is currently working on his Masters in Engineering Management from the University of Colorado, Boulder. For the past 8 years he has worked as a R&D Mechanical Engineer focused on development of high speed digital probing systems for multi channel test and measurement devices used to test computer systems. Brent has been issued 5 patents and has 5 patents pending in the area of Digital Probing design.George M. Marshall received his BSEE in 1984 and his MSNE in 1987 from Louisiana State University. For the past 4 years he has worked as a product design engineer on cable assembly designs for Precision Interconnect, a Tyco Electronics company located in Portland, Oregon. George is a registered Professional Engineer in the State of Oregon.I. IntroductionIn order to make a high-density logic analyzer probing connection, digital system designers have traditionally had to place Mictor connectors on their PCB. The signals of interest on the target board are routed to the Mictor connector to be observed by a logic analyzer. The logic analyzer probe, whose interconnect consists of a mating Mictor connector, is then plugged into the target and logic analysis is performed. While this interconnect methodology has been sufficient for the past decade, today’s data rates are pushing the limitations of the Mictor Connector. The physical structure of the Mictor connector possesses large electrical parasitics which load the target system and reduce the maximum speed of the logic analyzer. In addition, the combination of fine-pitch surface-mount and through-hole technology required to mount the connector make it sub-optimal for hand loading in the lab or in the field. This results in the Mictor needing to be machine loaded, which adds additional supply chain management and makes post production probing difficult.Today’s new connectorless probing technology addresses these limitations and is being adopted as the new industry standard for logic analysis probing. In connectorless probing, the designer includes surface mount pads on the target system that the signals of interest are routed to. The logic analyzer probe has compression interconnect that makes contact with the SMT pads and forms the electrical connection. A separate mechanical retention module is placed on the target PCB that aligns and retains the compression interconnect onto the SMT pads. This new methodology reduces the electrical loading on the target by reducing the physical structure of the interconnect. In addition, by eliminating the fine-pitch SMT pads of a Mictor connector, machine loading is not required. This simplifies the supply chain associated with having probe points on the board. In addition, post production probing is now enabled due to the simplicity of loading the retention module.Figure 1. Physical Connection of a Connectorless Probing TechnologyThis paper describes the mechanical and electrical advantages of connectorless logic analyzer probing. Comparisons are made to the existing Mictor connector to present the improvements made in this new technology.II. Mechanical Advantages of Connectorless Probing Connectorless probing offers a number of mechanical advantages over traditional connector based probing. These advantages include simplification of the supply chain for printed circuit board components, the flexibility to probing on a target board post manufacturing, and increased mechanical reliability for probing on multiple PCB plating finishes.A. Supply Chain SimplificationUntil now, digital system designers have had two options for probing with a logic analyzer. The first is to include connectors in the design and have them loaded in the surface mount technology (SMT) process. The second is to attach flying leads to package pins or solder them to exposed pads and traces. Including a connector on the PCB requires a commitment to board real estate and the coordination to ensure that the part is available, purchased, and loaded onto the PCB. Using flying leads can sometimes be difficult when accessing large numbers of signals in small geographical regions. Connectorless probing involves turning the printed circuit board into one half of the probing interconnect. This can essentially eliminate the need to include probing related components on the bill of materials for the PCB. This greatly reduces the supply chain headaches that are typically associated with making the decision to include probing capability early on. With connectorless probing, the PCB designer needs only to place and route signals to a non-intrusive footprint comprised of landing pads and small retention holes.Figure 2. Footprint on Target PCB for Connectorless ProbeThe footprint requires no planning, purchasing or logistical coordination with other parts of the manufacturing organization. Before connectorless technology, the designer would be forced to commit to probing capability before the PCB was loaded with components. Now the designer has the flexibility to enable it after getting boards back from the load shop. This enabling is done by simply adding a small plastic retention mechanism (RM) with the use of a standard soldering iron found in most labs. Once the RM is soldered down, the connectorless probe can be attached and used to capture signals. Compare the ease of installation of soldering down the RM with attempting to hand solder a hundred or more fine pitch connector leads by hand.B. Post-Production ProbingThe non-intrusive nature of connectorless technology enables engineers to leave the footprint in a production design. This allows designers to include probing capability at any point in the future after the product has been released. This helps reduce the cost associated with probing. For higher volume printed circuit boards, it is not cost effective to include even one extra connector on every board for probing. Now with connectorless probing, designers are no longer forced to make a cost trade off for debug. A product can ship with only the footprint on the board, which costs only the time to route signals to the pads. In the event that debug is needed in the field, all that is needed is to solder the RM onto the board and attach the probe.TOPSIDE OR BOTTOMSIDESOLDERING OF RETENTION PINSFigure 3. Process for attaching the Retention Module for Connectorless ProbesC. Mechanical ReliabilityNot all products requiring debug and validation ever leave the lab. In many situations, the probing paradigm is one of developing large test systems with multiple probe points where probes are mated and de-mated hundreds of times. Connector-based probes are limited by a maximum number of mate and de-mate cycles before the connector is no longer capable of making reliable contact. This limit is typically around 50 – 100 cycles. This cycle limit can be reached quickly in a debug environment where probe cables are being shared across multiple platforms as a cost saving measure. The problem comes when a connector on a test board must be replaced due to damage from over cycling it. This puts the user back into the position where they must hand load a replacement connector. Not only is this a logistical challenge, but also creates the possibility that pins could be solder-shorted together, introducing false errors into the tests being run. Additionally, this limited number of cycles will damage the mating connector on the probe as well, requiring that replacement probes be purchased, increasing the overall cost of debug. Connectorless probing solves this cycle limit problem in two different ways. First, the interconnect used in a connectorless probe can typically be used for thousands of cycles as opposed to just hundreds. Second, since there is no connector on the board, there is nothing to replace. The compression interconnect on a connectorless probe hasup to .025” of compliance, capable of absorbing the variability of pads coated with HASL finish. It also has the ability to pierce through oxides and contaminates on the pad eliminating the need for cleaning of the surface to be probed.Figure 4. SEM Photo of Physical Connection between Connectorless CompressionInterconnect and Target PCBIII. Electrical Advantages of Connectorless ProbingA. Electrical Considerations of ProbingThe goal of the probing connection is to present the least electrically intrusive load on the target system. This is accomplished by putting the highest possible impedance at the point at which the probe contacts the system. If the impedance is infinite, then the target system will not be perturbed by this connection. However, there is a tradeoff that is made between the loading that the target experiences and the signal swing that the logic analyzer acquires. The industry has converged on a 20kΩ tip impedance for high speed logic analyzer probing. This impedance is typically implemented using a discrete resistor. If there are no parasitics present, the load will look like a 20kΩ resistor from DC to infinite frequency. However, the practicality of the implementation means that there is stray capacitance and inductance between the ideal tip resistor and the point at which the probe contacts the system. The largest contribution to these electrical parasitics is the physical interconnect between the resistor and the target signal. In the case of the two technologies in this paper, the Mictor connector and the compression interconnect add excess capacitance to the probing system. Figure 5 shows the ideal probing scenario.Figure 5. Theoretical Probing ConnectionB. Reduced Loading on Target when Taking a Measurement Loading is a term that refers to how much the original target signal is affected due to the probe. An ideal situation would be that the when the probe is connected to a target system, the original signals are in no way altered. This is impractical in the real world, however if the loading contribution of the probe is small relative to the speeds at which the target system is running, then the probe can be ignored.The majority of probe loading comes in the form of parasitic capacitance due to the interconnect structure. Probes contain tip circuitry that form the transport system into thelogic analyzer mainframe. This tip circuitry is implemented using discrete components, which contains self-capacitance on the order of ~350 fF. The remaining loading capacitance comes from the structure that connects the tip circuitry to the target signals. In the case of a Mictor-based probe, this structure consists of the mating Mictor connectors. In a connectorless probe, this structure comes from the compression interconnect used to contact the landing pads on the target PCB. The difference between these two types of probing technologies is significant. The loading of a Mictor-based probe is 3 pF while the loading of a connectorless probe is only 0.7 pF. Reducing the physical size of the probing interconnect yields greater than a 400% loading reduction when comparing connectorless to Mictor based probing technology. Figure 6 shows a profile view of the two probing technologies and illustrates the difference in the physical interconnect structure that results in excess capacitance.Figure 6. Side Profile View of Connectorless vs. Mictor Based Probing Interconnect This capacitive loading has the effect of causing reflections and degrading the rise time of the signal on the target system. Since the load of the probe is an RLC system, its impedance will vary with frequency. In the case of a digital system, a faster rise time on the target will cause more of a discontinuity than a slower rise time. Logic analyzer vendors characterize the complex load impedance of each probe and provide SPICE models so that system engineers can simulate the probe’s effect on their signals. The SPICE models are typically accurate up to 6GHz. Figure 7 shows the Time Domain Reflectrometry (TDR) simulations comparing the loads of the two probing technologies. The Mictor’s reflection is show in Blue while the connectorless’ reflection is shown in Red. Figure 8 shows the Time Domain Transmission (TDT) simulations comparing the two loads on the signal as seen at the receiver. In Figure 8, the Green waveform shows the signal without the probe connected. For both sets of simulations, various rise times are used to illustrate how the loading is more severe as the rise time gets faster.Rise time = 175ps = 2GHzRise time = 117ps = 3GHzRise time=88ps=4GHz Rise time = 70ps = 5GHzRise time = 58ps = 6GHzFigure 7. TDR Simulation of Mictor vs. Connectorless ProbingRise time = 175ps = 2GHzRise time=117ps=3GHzRise time = 88ps = 4GHz Rise time = 70ps = 5GHzRise time = 58ps = 6GHzFigure 8. TDT Simulation of Mictor vs. Connectorless ProbingC. Reduced Loading when DisconnectedAnother electrical advantage of connectorless probing is the reduced loading of the footprint when the probe is not connected. In Mictor-based probes, when the probe is disconnected, a mating connector still resides on the target PCB. In most cases, unused traces connected to the connector are also on the board. The parasitics of the unused probe point are large enough so that they cannot be ignored. Most designers take the connector and traces out of the design before going to production. Connectorless probes do not have this problem. Since only the landing pads are left on the board when the probe is disconnected, there is little to no loading due to the pads (~80fF). In addition, since the connectorless footprint allows minimal routing effort, there are no stubs present to add additional loading. This has the advantage that the connectorless footprint can be left in a production design without degrading the performance of the system. Designers can analyze field failures using the same test benches that they used during prototyping because the design still possesses logic analyzer probing points.Figure 9. Physical Structure Remaining on Target PCB When Probe is DisconnectedD. Flow Through RoutingIn connectorless probing, only landing pads are placed on the target PCB. These landing pads are spaced such that signals can be routed between the pads without changing signal layers. This is a new ability over traditional connector-based probes like the Mictor. In Mictor-based probes, the connector that resides on the target PCB actually prohibits any routing through the connector due to its use of SMT and through-hole technology. This means that when observing signals in a routing channel, the Mictor connector needs to be placed to the side of the traces and stub-traces are used to make the connection to the connector. Placing the connector off to the side has the disadvantage of increased loading due to the need for stub-traces. In addition, more PCB area is required to accommodate the connector placement. With connectorless probing, the footprint can be placed directly in the signal path with minimal disturbance to the routing of the signals.10(a) Mictor-Based Probing 10(b) Connector-less Probing Figure 10. Routing Implications Between Mictor and Connectorless ProbingAs edge rates increase, it becomes more and more important to reduce impedance mismatches along the transmission line. Any energy that is reflected as the wave front travels down the transmission line leads to degradation of the initial edge. When using differential signaling, one potential source of discontinuity is the uncoupling of the signal pair. As a differential signal propagates, it exchanges charge with its reference plane in addition to its compliment signal within the pair. There is deterministic impedance for both charge-exchanging paths. These are referred to as Even and Odd mode impedances. If the signal pair experiences trace separation during the route, these impedances change. When the impedances change, there will be a reflection at the point at which the impedances are different from the original transmission line. The following example illustrates this point.Example)A standard 5” differential pair is routed using 0.005” traces widths with 0.010” trace separation. The signals are routed as microstrip transmission lines over 0.003” of dielectric with a dielectric constant of 4.0. This transmission line design yields Zo even=53.1Ω, Zo odd=48Ω, and Zo=50.6Ω’s. The differential pair is terminated into a 100 Ω resistor.Suppose the differential pair above undergoes a trace separation that increases the separation to 0.030” (instead of 0.010”) for a length of 1” in the middle of the route. The resulting 1” of trace has a Zo even=51.4Ω, Zo odd=51Ω, and Zo=51Ω’s. This impedance mismatch causes a reflection as the traces are separated. The following simulation shows the result of this case. The 1” trace separation causes a reflection that re-reflects off of the low impedance driver and appears at the receiver sometime after the initial edge. The risetime of the driver is 58ps (6GHz). In this case, the differential receiver will loose 5% of its voltage noise margin due to uncoupling of the differential pair.DiscontinuityFigure 11. Discontinuity Caused by Separation of Differential TracesThe above example illustrates the importance of preserving the differential impedance of a signal pair as it is routed. Only the connectorless probing footprint allows differential pairs to be routed through the footprint without spacing separation.IV. ConclusionAs digital data rates continue to increase, the standard technique for performing logic analyzer probing is becoming obsolete. Traditional Mictor-based probing is being replaced with connectorless probing technology. Connectorless probing possesses a suite of mechanical and electrical advantages over Mictor-based probes. Designers that are migrating to the new connectorless probing technology are reaping the benefits of a more reliable connection with minimal loading and simple to implement features on the target PCB. This new technology is allowing designers to achieve successful logic analysis as they push their systems to higher data rates.References[1] W. Dally and J. Poulton, Digital Systems Engineering, Cambridge UniversityPress, Cambridge, U.K., 1998.[2] H. Johnson and M. Graham, High-Speed Digital Design, Prentice Hall PTR,2001.[3] H. Johnson and M. Graham, High-Speed Signal Propagation, Prentice Hall PTR,2003.[4] L. Nagel, "SPICE: A Computer Program to Simulate Computer Circuits",University of California, Berkeley UCB/ERL Memo M520, May, 1995.。