多晶硅铸锭炉热场底部改进的数值模拟研究
多晶铸锭炉技术改进及优化方法分析

工程研究Engineering research■ 张卫东多晶铸锭炉技术改进及优化方法分析摘要:本文结合目前多晶 硅铸锭炉生产期间所用的设备、工艺步骤与控制系统进行了分析,同时对锭炉技术、优化方法进行了说明。
关键词:多晶硅;铸锭炉;技术改进;优化方法1多晶硅铸锭炉设备1.1设备就机械构造来看,铸锭炉有热区、炉体、功率柜、真空泵、控制柜与人机界面等区域。
就功能来看,它有保温、测温、压力控制、真空、辅助操作与加热等各种子系统[1]。
1.2作用从多晶硅体铸锭成型来看,铸锭炉发挥了关键性作用,利用硅料高温熔融、加热、结晶与定向冷凝等各种加工工艺以实现硅锭稳定、持续生产。
同时这也为规范多晶硅太阳能生产提供了很好的硅片原料。
1.3特点从多晶硅铸锭炉性能来看:它具有效率高、加热快、技术成熟等优势,它可以使用纯度较低的硅料,也就是说对材料的限制程度不高,利用一定的控制方式与技术就能减小杂志与晶界影响。
通过冷凝定向结晶技术就能很好的控制产品质量,所以铸锭炉综合效率与产值始终较大,产品成本小,可以大范围生产。
2多晶硅铸锭炉的工艺及常见故障事实上,规范太阳能生产对产品一致性与硅片性能有很大要求,所以必须严格多晶硅生产工艺与流程,并且严格生产设施与故障监控工作,这样才能在最短的时间内解决问题,最后达到保障质量的要求。
2.1工艺流程及参数总体工艺包含:填料、预热、融化、长晶与冷却[2],因为生产需要,所以在参数设置与流程配备上存在很大不同。
典型的参数配置与工艺流程如下所述:预热:其温度一般在1200°左右,真空度1.05mpa,时长15小时,整体保温;融化:温度在1200°-1500°间,真空度44.1mpa,时长5小时,开始时充入保护气,同时保障温度;长晶,其温度在1440°-1400°间,真空度为44.1mpa,时长10小时,持续充入保护气,并且保持常温;退火:温度一般在1400°-1000°间,时长8.5小时,冲入保护气,以达到降温的目的,真空度在44.1mpa;冷却:其温度为1000°-400°,真空度为52.5mpa,时长约6小时,充入保护气,以达到缓慢降温的目的。
多晶硅铸锭炉热场底部改进的数值模拟研究
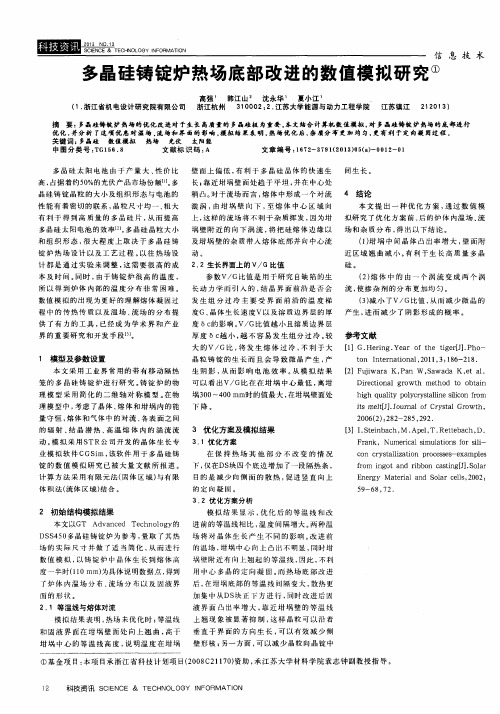
量 守恒 , 熔体 和 气 体 中 的 对 流 、 各表 面之 间
的辐 射 、 结 晶潜热 、 高 温 熔 体 内 的 湍 流 流
度5 c 的影 响 。 V/ G比值 越 小 且溶 质 边 界 层
厚度 5 e 越小, 越不容 易发生组分过 冷 。 较 参考文献
大 的 V/G比 , 将发 生熔 体过 冷 , 不 利 于 大
[ 1 ]G. H e r i n g . Y e a r o f t h e t i g e r [ J 】 . P h o —
所 以得到炉体 内部的温度分 布非常 困难。
参数 V/ G比值 是 用 于 研 究 自缺 陷 的 生
( 2 ) 熔 体 中 的 由 一 个 涡 流 变 成 两 个 涡
( 3 ) 减 小 了V/ G比 值 , 从 而 减 少 微 品 的
长动 力学而引入的 , 结 晶 界 面 前 沿 是 否 会 流 , 使 掺 杂 剂 的分 布 更加 均 匀 。
锭炉热 场设计 以及工艺过程 。 以 往 热 场 设
动。
本文提 出一种优 化方案 , 通 过 数 值 模
场和杂质分布 , 得出以下结论 。
有 利 于 得 到 高 质量 的 多 晶 硅 片 , 从 而 提 高 上 , 这样 的流 场 将 不 利 于 杂 质挥 发 , 因 为坩 拟研 究 了优 化 方 案 前 、 后 的炉 体 内温 场 、 流
晶 硅铸 锭 晶 粒 的 大小 及 组 织 形 态 与 电池 的
壁面上偏低 , 有 利 于 多 晶 硅 晶体 的 快 速 生 长; 靠近坩埚壁面处趋于平坦 , 并 在 中心 处
间生长。 ຫໍສະໝຸດ 稍凸。 对于流场而言 , 熔 体 中 形 成一 个 对 流 4 结论
多晶铸锭工程多晶硅片硬质点解决建议
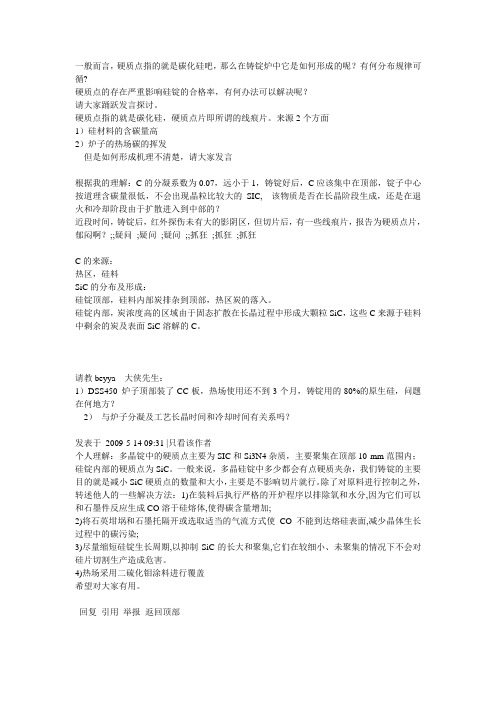
一般而言,硬质点指的就是碳化硅吧,那么在铸锭炉中它是如何形成的呢?有何分布规律可循?硬质点的存在严重影响硅锭的合格率,有何办法可以解决呢?请大家踊跃发言探讨。
硬质点指的就是碳化硅,硬质点片即所谓的线痕片。
来源2个方面1)硅材料的含碳量高2)炉子的热场碳的挥发但是如何形成机理不清楚,请大家发言根据我的理解:C的分凝系数为0.07,远小于1,铸锭好后,C应该集中在顶部,锭子中心按道理含碳量很低,不会出现晶粒比较大的SIC, 该物质是否在长晶阶段生成,还是在退火和冷却阶段由于扩散进入到中部的?近段时间,铸锭后,红外探伤未有大的影阴区,但切片后,有一些线痕片,报告为硬质点片,郁闷啊?;;疑问;疑问;疑问;;抓狂;抓狂;抓狂C的来源:热区,硅料SiC的分布及形成:硅锭顶部,硅料内部炭排杂到顶部,热区炭的落入。
硅锭内部,炭浓度高的区域由于固态扩散在长晶过程中形成大颗粒SiC,这些C来源于硅料中剩余的炭及表面SiC溶解的C。
请教beyya 大侠先生:1)DSS450 炉子顶部装了CC板,热场使用还不到3个月,铸锭用的80%的原生硅,问题在何地方?2)与炉子分凝及工艺长晶时间和冷却时间有关系吗?发表于2009-5-14 09:31 |只看该作者个人理解:多晶锭中的硬质点主要为SIC和Si3N4杂质,主要聚集在顶部10 mm范围内;硅锭内部的硬质点为SiC。
一般来说,多晶硅锭中多少都会有点硬质夹杂,我们铸锭的主要目的就是减小SiC硬质点的数量和大小,主要是不影响切片就行。
除了对原料进行控制之外,转述他人的一些解决方法:1)在装料后执行严格的开炉程序以排除氧和水分,因为它们可以和石墨件反应生成CO溶于硅熔体,使得碳含量增加;2)将石英坩埚和石墨托隔开或选取适当的气流方式使CO不能到达熔硅表面,减少晶体生长过程中的碳污染;3)尽量缩短硅锭生长周期,以抑制SiC的长大和聚集,它们在较细小、未聚集的情况下不会对硅片切割生产造成危害。
多晶硅铸锭炉加热器的优化及其热场模拟
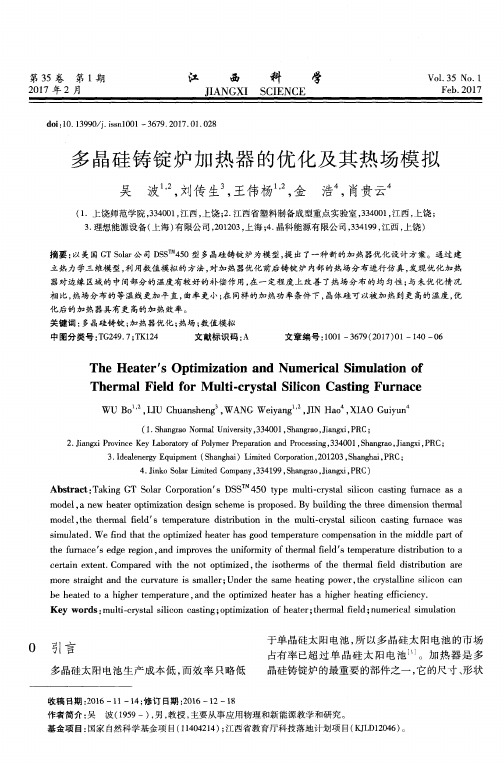
3 . I d e a l e n e r g y E q u i p me n t( S h a n g h a i )L i m i t e d C o r p o r a t i o n , 2 0 1 2 0 3 , S h a n g h a i , P R C ; 4 . J i n k o S o l a r L i m i t e d C o m p a n y , 3 3 4 1 9 9, S h a n g r a o , J i a n g x i , P R C)
Th e r ma l Fi e l d f o r Mu l t i - c r y s t a l S i l i c o n Ca s t i ng Fu r n a c e
WU B o , L I U C h u a n s h e n g , W ANG We i y a n g , J I N Ha o , X I AO Gu i y u n
( 1 . S h a n g r a o N o r ma l U n i v e r s i t y , 3 3 4 0 0 1 , S h a n g r a o , J i a n g x i , P R C ;
2 . J i a n g x i P r o v i n c e K e y La b o r a t o r y o f P o l y me r P r e p a r a t i o n a n d P r o c e s s i n g , 3 3 4 0 0 1, S h a n g r a o , J i a n g x i , P RC;
第3 5卷
第1 期
江
西
科
学
Vo l - 3 5 No. 1 F e b. 20l 7
基于SMED技术的多晶硅铸锭炉生产效率改善
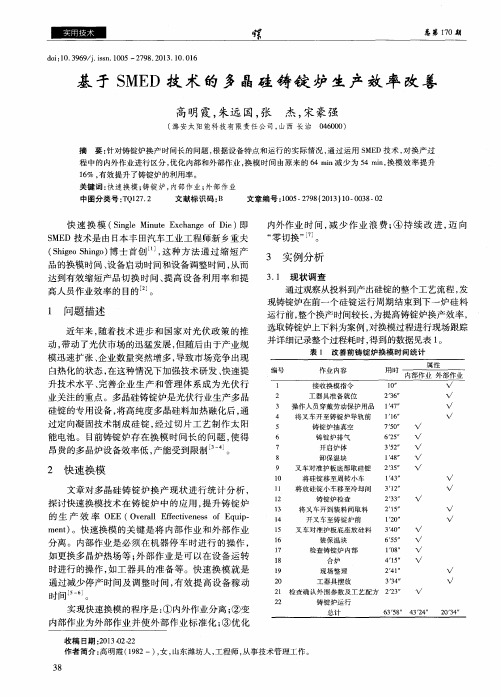
2 快速换模
文章对 多 晶硅 铸 锭 炉换 产 现 状 进行 统 计 分 析 ,
探 讨快 速换 模技 术 在铸 锭 炉 中的应 用 , 提 升铸 锭 炉
的生 产 效 率 O E E( O v e r a l l E f f e c t i v e n e s s o f E q u i p .
白热化 的状 态 , 在 这种 情况下 加强 技术 研发 、 快速 提
现铸锭炉在前 一个 硅锭 运 行周 期结 束到 下一 炉 硅料 运行前, 整个换产时间较长 , 为提高铸锭炉换产效率 , 选取铸锭炉上下 料为案例 , 对换模 过程进 行现场 跟踪 并详细记 录整个 过程耗 时 , 得 到的数据见表 1 。
摘
要: 针对铸锭炉换产时间长的 问题 , 根据设备特点 和运行 的实际情况 , 通过运用 S ME D技术 , 对换 产过
程 中的内外作业进行 区分 , 优化 内部 和外部作业 , 换模 时问 由原来 的 6 4 mi n减少 为 5 4 a r i n , 换模效 率提升 1 6 %, 有效提升 了铸锭炉 的利用率 。
3 8
2 0 1 3年 1 0月
高 明霞等: 基于 S ME D技术 的多晶硅 铸锭 炉生产效率 改善
第2 2卷 第 1 0期
通 过对换 模 时 间 进行 统计 分 析发 现 , 操 作 过程 存在 大 量浪 费 , 如外 部 作 业 装 料 间取 料 是 在 铸 锭 炉
进行 分 析 , 对 现有 换模 流 程进行 分 析及优 化 , 通过 对 内外作 业进 行分 离 、 变 内部为外 部 作业 、 并行 作业 等 技术 改 善 , 使设备换模效率 提升 1 6 %, 为提 升 光伏
关于多晶硅铸锭热场系统
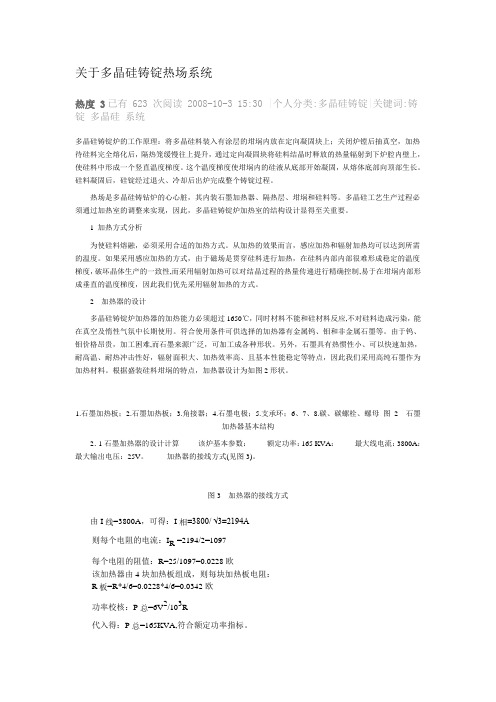
2.3石墨加热器的应力校核
石墨在低温导热性良好,在高温时导热性下降,造成其表面与心部温度差使断面伸长不一致。产生热应力,从而导致石墨加热器损坏,故应计算其产生的热应力。
对于宽度比厚度大得多的板状电热元件:
式中:t中心为电热元件心部温度:t表面为电热元件表面温度,此处取t表面=1540℃
1.石墨加热板;2.石墨加热板;3.角接器;4.石墨电极;5.支承环;6、7、8.碳、碳螺栓、螺母图2石墨加热器基本结构
2.1石墨加热器的设计计算该炉基本参数:额定功率:165 KVA:最大线电流:3800A:最大输出电压:25V。加热器的接线方式(见图3)。
图33800/ √3=2194A
确定隔热层固化碳毡的厚度:
间歇生产的真空电炉,通常隔热层外壁面温度为200~300℃,水冷炉壳内温度为100-150℃,隔热层外表面的辐射换热系数可由下式计算:
(1)
(2)
(3)
tw1为隔热层内壁画温度,此处取tw1=1600℃; tw2为隔热层外壁面温度,此处取tw2=250℃; Q为隔热层散失的总热量,此处已求得Q=3486.OW/m2。将各值代入(5)式,得:故该铸锭炉隔热层固化碳毡厚度取90mm。隔热层组件利用一个方形的小锈钢笼来支撑和固定。
热场是多晶硅铸钻炉的心心脏,其内装石墨加热器、隔热层、坩埚和硅料等。多晶硅工艺生产过程必须通过加热室的调整来实现,因此,多晶硅铸锭炉加热室的结构设计显得至关重要。
1加热方式分析
为使硅料熔融,必须采用合适的加热方式。从加热的效果而言,感应加热和辐射加热均可以达到所需的温度。如果采用感应加热的方式,由于磁场是贯穿硅料进行加热,在硅料内部内部很难形成稳定的温度梯度,破坏晶体生产的一致性,而采用辐射加热可以对结晶过程的热量传递进行精确控制,易于在坩埚内部形成垂直的温度梯度,因此我们优先采用辐射加热的方式。
多晶硅铸锭炉热场
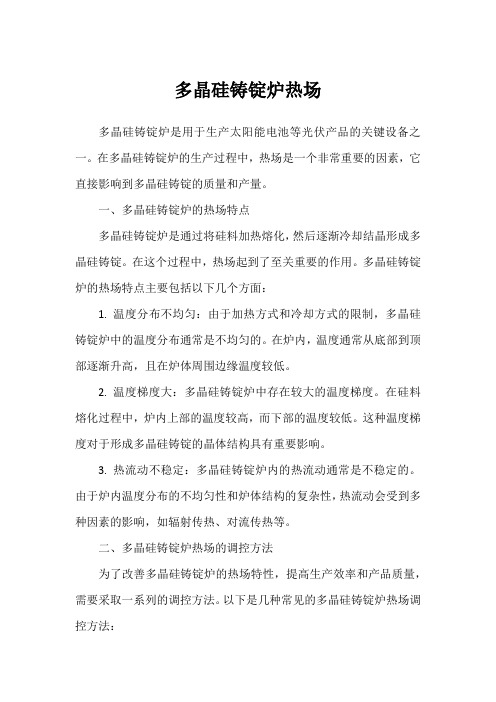
多晶硅铸锭炉热场多晶硅铸锭炉是用于生产太阳能电池等光伏产品的关键设备之一。
在多晶硅铸锭炉的生产过程中,热场是一个非常重要的因素,它直接影响到多晶硅铸锭的质量和产量。
一、多晶硅铸锭炉的热场特点多晶硅铸锭炉是通过将硅料加热熔化,然后逐渐冷却结晶形成多晶硅铸锭。
在这个过程中,热场起到了至关重要的作用。
多晶硅铸锭炉的热场特点主要包括以下几个方面:1. 温度分布不均匀:由于加热方式和冷却方式的限制,多晶硅铸锭炉中的温度分布通常是不均匀的。
在炉内,温度通常从底部到顶部逐渐升高,且在炉体周围边缘温度较低。
2. 温度梯度大:多晶硅铸锭炉中存在较大的温度梯度。
在硅料熔化过程中,炉内上部的温度较高,而下部的温度较低。
这种温度梯度对于形成多晶硅铸锭的晶体结构具有重要影响。
3. 热流动不稳定:多晶硅铸锭炉内的热流动通常是不稳定的。
由于炉内温度分布的不均匀性和炉体结构的复杂性,热流动会受到多种因素的影响,如辐射传热、对流传热等。
二、多晶硅铸锭炉热场的调控方法为了改善多晶硅铸锭炉的热场特性,提高生产效率和产品质量,需要采取一系列的调控方法。
以下是几种常见的多晶硅铸锭炉热场调控方法:1. 加热方式优化:多晶硅铸锭炉的加热方式通常有电阻加热、感应加热等。
合理选择和优化加热方式可以改善炉内温度分布的均匀性,减小温度梯度。
2. 冷却方式控制:多晶硅铸锭炉的冷却方式通常有水冷和气冷两种。
通过调整冷却方式和冷却速度,可以控制炉内的温度梯度和冷却速率,影响多晶硅铸锭的晶体结构和质量。
3. 炉体结构优化:多晶硅铸锭炉的炉体结构对热场的分布和稳定性有着重要影响。
通过改变炉体结构和加强热场的隔离,可以减小炉内温度分布的不均匀性,提高热场的稳定性。
4. 热流动调控:通过优化炉内的热流动方式,可以改善热场的稳定性和温度分布的均匀性。
可以采用流体力学模拟和实验方法来研究和优化炉内的热流动,如调整气体流速、引入局部加热等。
5. 温度监测和控制:在多晶硅铸锭炉中,温度监测和控制是非常重要的环节。
多晶硅铸锭炉热场底部改进的数值模拟研究
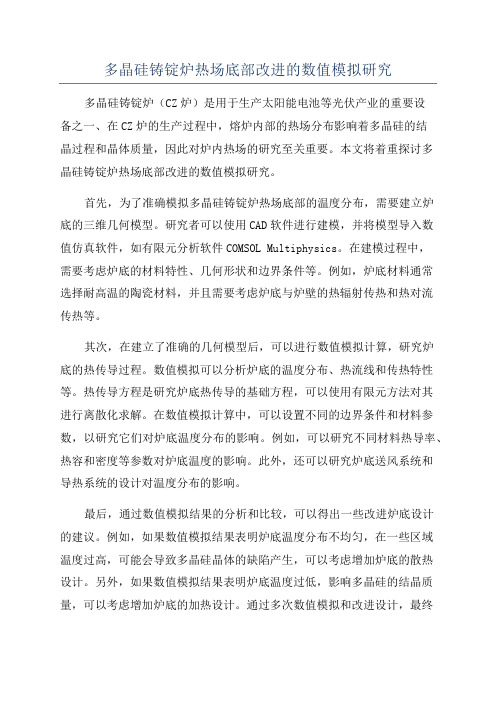
多晶硅铸锭炉热场底部改进的数值模拟研究多晶硅铸锭炉(CZ炉)是用于生产太阳能电池等光伏产业的重要设备之一、在CZ炉的生产过程中,熔炉内部的热场分布影响着多晶硅的结晶过程和晶体质量,因此对炉内热场的研究至关重要。
本文将着重探讨多晶硅铸锭炉热场底部改进的数值模拟研究。
首先,为了准确模拟多晶硅铸锭炉热场底部的温度分布,需要建立炉底的三维几何模型。
研究者可以使用CAD软件进行建模,并将模型导入数值仿真软件,如有限元分析软件COMSOL Multiphysics。
在建模过程中,需要考虑炉底的材料特性、几何形状和边界条件等。
例如,炉底材料通常选择耐高温的陶瓷材料,并且需要考虑炉底与炉壁的热辐射传热和热对流传热等。
其次,在建立了准确的几何模型后,可以进行数值模拟计算,研究炉底的热传导过程。
数值模拟可以分析炉底的温度分布、热流线和传热特性等。
热传导方程是研究炉底热传导的基础方程,可以使用有限元方法对其进行离散化求解。
在数值模拟计算中,可以设置不同的边界条件和材料参数,以研究它们对炉底温度分布的影响。
例如,可以研究不同材料热导率、热容和密度等参数对炉底温度的影响。
此外,还可以研究炉底送风系统和导热系统的设计对温度分布的影响。
最后,通过数值模拟结果的分析和比较,可以得出一些改进炉底设计的建议。
例如,如果数值模拟结果表明炉底温度分布不均匀,在一些区域温度过高,可能会导致多晶硅晶体的缺陷产生,可以考虑增加炉底的散热设计。
另外,如果数值模拟结果表明炉底温度过低,影响多晶硅的结晶质量,可以考虑增加炉底的加热设计。
通过多次数值模拟和改进设计,最终可以得到合适的炉底结构和运行参数,以提高多晶硅铸锭炉的生产效率和产品质量。
总之,多晶硅铸锭炉热场底部的改进是一个复杂而重要的问题,需要借助数值模拟进行研究。
通过准确的几何建模、热传导方程的数值求解,可以得到炉底温度分布的详细信息,为炉底设计和运行参数的优化提供科学依据。
这将对多晶硅铸锭炉的生产效率和多晶硅晶体的质量起到积极的促进作用。
多晶硅铸锭炉热场底部改进的数值模拟研究

多晶硅铸锭炉热场底部改进的数值模拟研究作者:高强韩江山沈永华夏小江来源:《科技资讯》2013年第13期摘要:多晶硅铸锭炉热场的优化改进对于生长高质量的多晶硅极为重要。
本文结合计算机数值模拟,对多晶硅铸锭炉热场的底部进行优化,并分析了这项优惠对温场、流场和界面的影响。
模拟结果表明,热场优化后,杂质分布更加均匀,更有利于定向凝固过程。
关键词:多晶硅数值模拟热场光伏太阳能中图分类号:TG156.8 文献标识码:A 文章编号:1672-3791(2013)05(a)-0012-01多晶硅太阳电池由于产量大、性价比高,占据着约50%的光伏产品市场份额[1]。
多晶硅铸锭晶粒的大小及组织形态与电池的性能有着密切的联系,晶粒尺寸均一、粗大有利于得到高质量的多晶硅片,从而提高多晶硅太阳电池的效率[2]。
多晶硅晶粒大小和组织形态,很大程度上取决于多晶硅铸锭炉热场设计以及工艺过程。
以往热场设计都是通过实验来调整,这需要很高的成本及时间。
同时,由于铸锭炉很高的温度,所以得到炉体内部的温度分布非常困难。
数值模拟的出现为更好的理解熔体凝固过程中的传热传质以及温场、流场的分布提供了有力的工具,已经成为学术界和产业界的重要研究和开发手段[3]。
1 模型及参数设置本文采用工业界常用的带有移动隔热笼的多晶硅铸锭炉进行研究。
铸锭炉的物理模型采用简化的二维轴对称模型。
在物理模型中,考虑了晶体、熔体和坩埚内的能量守恒,熔体和气体中的对流、各表面之间的辐射、结晶潜热、高温熔体内的湍流流动。
模拟采用STR公司开发的晶体生长专业模拟软件CGSim,该软件用于多晶硅铸锭的数值模拟研究已被大量文献所报道。
计算方法采用有限元法(固体区域)与有限体积法(流体区域)结合。
2 初始结构模拟结果本文以GT Advanced Technology的DSS450多晶硅铸锭炉为参考,量取了其热场的实际尺寸并做了适当简化,从而进行数值模拟,以铸锭炉中晶体生长到熔体高度一半时(110 mm)为具体说明数据点,得到了炉体内温场分布、流场分布以及固液界面的形状。
多晶硅铸锭装备的产能扩大和工艺改进技术研究
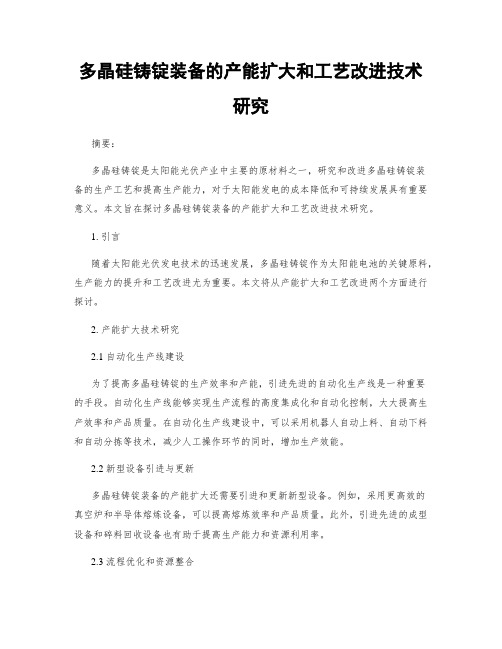
多晶硅铸锭装备的产能扩大和工艺改进技术研究摘要:多晶硅铸锭是太阳能光伏产业中主要的原材料之一,研究和改进多晶硅铸锭装备的生产工艺和提高生产能力,对于太阳能发电的成本降低和可持续发展具有重要意义。
本文旨在探讨多晶硅铸锭装备的产能扩大和工艺改进技术研究。
1. 引言随着太阳能光伏发电技术的迅速发展,多晶硅铸锭作为太阳能电池的关键原料,生产能力的提升和工艺改进尤为重要。
本文将从产能扩大和工艺改进两个方面进行探讨。
2. 产能扩大技术研究2.1 自动化生产线建设为了提高多晶硅铸锭的生产效率和产能,引进先进的自动化生产线是一种重要的手段。
自动化生产线能够实现生产流程的高度集成化和自动化控制,大大提高生产效率和产品质量。
在自动化生产线建设中,可以采用机器人自动上料、自动下料和自动分拣等技术,减少人工操作环节的同时,增加生产效能。
2.2 新型设备引进与更新多晶硅铸锭装备的产能扩大还需要引进和更新新型设备。
例如,采用更高效的真空炉和半导体熔炼设备,可以提高熔炼效率和产品质量。
此外,引进先进的成型设备和碎料回收设备也有助于提高生产能力和资源利用率。
2.3 流程优化和资源整合在多晶硅铸锭的生产过程中,流程的优化和资源的整合也是提高产能的重要手段。
通过分析生产过程中的瓶颈环节和资源浪费现象,采取合理的优化措施,例如改进操作流程、减少能源消耗和材料浪费等,可以提高生产效率和产品质量。
3. 工艺改进技术研究3.1 温度控制技术改进多晶硅铸锭的生产过程中,温度控制是一个关键问题。
传统的温度控制方法存在一定的局限性,容易导致产品质量不稳定。
因此,通过引入先进的温度控制技术,例如PID控制和模型预测控制等,可以提高温度控制的精度和稳定性,进而提高产品质量。
3.2 智能化监测和反馈系统多晶硅铸锭的生产过程中,监测和反馈系统的改进能够帮助及时发现生产过程中的异常情况,并采取相应的控制措施。
智能化监测系统可以实现实时数据的采集和分析,通过数据模型的建立和监测算法的优化,预测产品质量的变化趋势,从而及时调整生产参数,提高产品的一致性和稳定性。
多晶硅铸锭炉加热器的优化及其热场模拟

多晶硅铸锭炉加热器的优化及其热场模拟吴波;刘传生;王伟杨;金浩;肖贵云【摘要】以美国GT Solar公司DSSTM450型多晶硅铸锭炉为模型,提出了一种新的加热器优化设计方案.通过建立热力学三维模型,利用数值模拟的方法,对加热器优化前后铸锭炉内部的热场分布进行仿真,发现优化加热器对边缘区域的中间部分的温度有较好的补偿作用,在一定程度上改善了热场分布的均匀性;与未优化情况相比,热场分布的等温线更加平直,曲率更小;在同样的加热功率条件下,晶体硅可以被加热到更高的温度,优化后的加热器具有更高的加热效率.【期刊名称】《江西科学》【年(卷),期】2017(035)001【总页数】6页(P140-145)【关键词】多晶硅铸锭;加热器优化;热场;数值模拟【作者】吴波;刘传生;王伟杨;金浩;肖贵云【作者单位】上饶师范学院,334001,江西,上饶;江西省塑料制备成型重点实验室,334001,江西,上饶;理想能源设备(上海)有限公司,201203,上海;上饶师范学院,334001,江西,上饶;江西省塑料制备成型重点实验室,334001,江西,上饶;晶科能源有限公司,334199,江西,上饶;晶科能源有限公司,334199,江西,上饶【正文语种】中文【中图分类】TG249.7;TK124多晶硅太阳电池生产成本低,而效率只略低于单晶硅太阳电池,所以多晶硅太阳电池的市场占有率已超过单晶硅太阳电池[1]。
加热器是多晶硅铸锭炉的最重要的部件之一,它的尺寸、形状及功率设计对热场分布有重要影响,直接关系到多晶硅铸锭的质量。
戴鑫等通过数值模拟的方法,分析了加热器尺寸和位置对多晶硅晶体生长过程中的温度分布和固液界面的影响,发现采用顶-侧加热器相比单独的顶加热器或侧加热器拥有更佳的热效率和固液界面[2];陈国红等对加热器的电功率设计、表面热功率负荷以及电学参数和热应力参数等进行了理论计算[3];娄中士等利用数值模拟方法研究了移动加于侧加热器与散热器之间的隔热环与底部喷射氩气冷却时温度分布及晶体生长过程,得到了更加均匀的温度分布和更高的晶体生长速率[4];罗玉峰、张志强等都对晶体生长过程中的热场分布进行了深入研究,提出了许多优化热场的方案[5-7]。
冶金法提纯多晶硅退火工艺优化的数学模型分析与试验验证
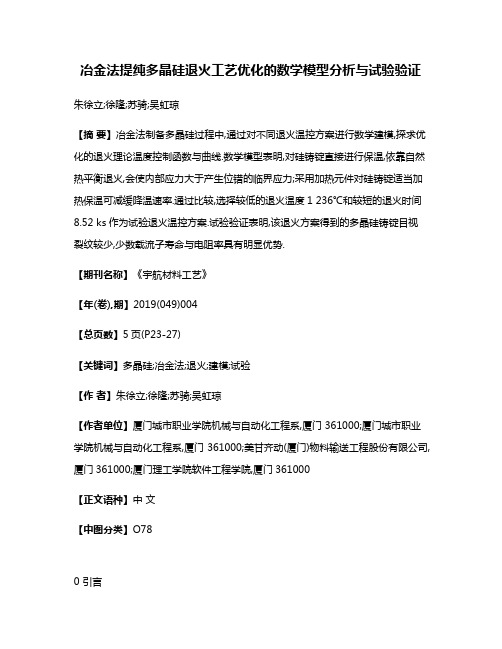
冶金法提纯多晶硅退火工艺优化的数学模型分析与试验验证朱徐立;徐隆;苏骑;吴虹琼【摘要】冶金法制备多晶硅过程中,通过对不同退火温控方案进行数学建模,探求优化的退火理论温度控制函数与曲线.数学模型表明,对硅铸锭直接进行保温,依靠自然热平衡退火,会使内部应力大于产生位错的临界应力;采用加热元件对硅铸锭适当加热保温可减缓降温速率.通过比较,选择较低的退火温度1 236℃和较短的退火时间8.52 ks作为试验退火温控方案.试验验证表明,该退火方案得到的多晶硅铸锭目视裂纹较少,少数载流子寿命与电阻率具有明显优势.【期刊名称】《宇航材料工艺》【年(卷),期】2019(049)004【总页数】5页(P23-27)【关键词】多晶硅;冶金法;退火;建模;试验【作者】朱徐立;徐隆;苏骑;吴虹琼【作者单位】厦门城市职业学院机械与自动化工程系,厦门 361000;厦门城市职业学院机械与自动化工程系,厦门 361000;美甘齐动(厦门)物料输送工程股份有限公司,厦门361000;厦门理工学院软件工程学院,厦门361000【正文语种】中文【中图分类】O780 引言在冶金法(物理法)多晶硅铸锭的提纯中,多晶硅铸锭内部热应力的大小和分布与晶体缺陷息息相关,是影响产品质量的关键因素,并最终影响光电转换效率。
通过温控进行热应力的控制涵盖了定向凝固与退火全过程,退火过程的工艺甚至对铸锭的成功与否起决定性作用。
定向凝固完成后,如不作任何热处理,直接放由铸锭炉的炉温自然降至室温拆炉,硅铸锭内部冷热不均现象严重,上下表面的温度差异很大,可达380~430℃[1],造成热应力增大[2-3],极有可能产生大量位错,甚至使铸锭碎裂[4-5]。
因此,合理而周全的退火措施是保证铸锭成功的必要手段,进而减少热胀冷缩现象,不但能避免裂锭,还能改善晶体生长和排列条件,在一定程度上降低位错概率。
退火工艺因定向凝固炉的不同而各异,大多数需要依据经验通过多次试验或试生产来制定[6-7]。
太阳能多晶硅铸锭制备系统的热场与控制研究
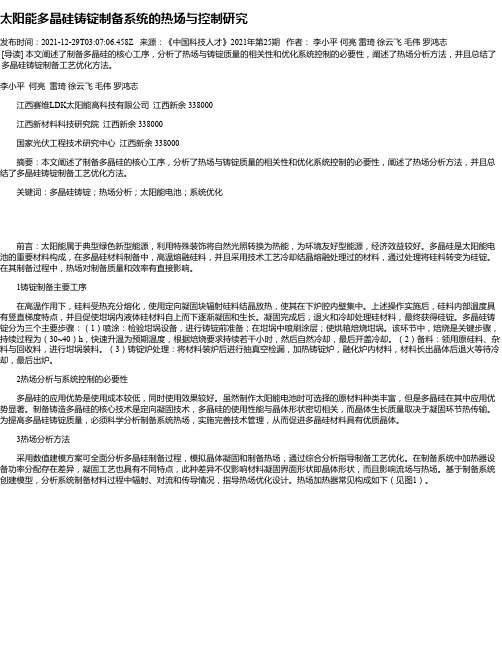
太阳能多晶硅铸锭制备系统的热场与控制研究发布时间:2021-12-29T03:07:06.458Z 来源:《中国科技人才》2021年第25期作者:李小平何亮雷琦徐云飞毛伟罗鸿志[导读] 本文阐述了制备多晶硅的核心工序,分析了热场与铸锭质量的相关性和优化系统控制的必要性,阐述了热场分析方法,并且总结了多晶硅铸锭制备工艺优化方法。
李小平何亮雷琦徐云飞毛伟罗鸿志江西赛维LDK太阳能高科技有限公司江西新余 338000江西新材料科技研究院江西新余 338000国家光伏工程技术研究中心江西新余 338000摘要:本文阐述了制备多晶硅的核心工序,分析了热场与铸锭质量的相关性和优化系统控制的必要性,阐述了热场分析方法,并且总结了多晶硅铸锭制备工艺优化方法。
关键词:多晶硅铸锭;热场分析;太阳能电池;系统优化前言:太阳能属于典型绿色新型能源,利用特殊装饰将自然光照转换为热能,为环境友好型能源,经济效益较好。
多晶硅是太阳能电池的重要材料构成,在多晶硅材料制备中,高温熔融硅料,并且采用技术工艺冷却结晶熔融处理过的材料,通过处理将硅料转变为硅锭。
在其制备过程中,热场对制备质量和效率有直接影响。
1铸锭制备主要工序在高温作用下,硅料受热充分熔化,使用定向凝固块辐射硅料结晶放热,使其在下炉腔内壁集中。
上述操作实施后,硅料内部温度具有竖直梯度特点,并且促使坩埚内液体硅材料自上而下逐渐凝固和生长。
凝固完成后,退火和冷却处理硅材料,最终获得硅锭。
多晶硅铸锭分为三个主要步骤:(1)喷涂:检验坩埚设备,进行铸锭前准备;在坩埚中喷刷涂层;使烘箱焙烧坩埚。
该环节中,焙烧是关键步骤,持续过程为(30~40)h,快速升温为预期温度,根据焙烧要求持续若干小时,然后自然冷却,最后开盖冷却。
(2)备料:领用原硅料、杂料与回收料,进行坩埚装料。
(3)铸锭炉处理:将材料装炉后进行抽真空检漏,加热铸锭炉,融化炉内材料,材料长出晶体后退火等待冷却,最后出炉。
- 1、下载文档前请自行甄别文档内容的完整性,平台不提供额外的编辑、内容补充、找答案等附加服务。
- 2、"仅部分预览"的文档,不可在线预览部分如存在完整性等问题,可反馈申请退款(可完整预览的文档不适用该条件!)。
- 3、如文档侵犯您的权益,请联系客服反馈,我们会尽快为您处理(人工客服工作时间:9:00-18:30)。
多晶硅铸锭炉热场底部改进的数值模拟研究摘要:多晶硅铸锭炉热场的优化改进对于生长高质量的多晶硅极为重要。
本文结合计算机数值模拟,对多晶硅铸锭炉热场的底部进行优化,并分析了这项优惠对温场、流场和界面的影响。
模拟结果表明,热场优化后,杂质分布更加均匀,更有利于定向凝固过程。
关键词:多晶硅数值模拟热场光伏太阳能
多晶硅太阳电池由于产量大、性价比高,占据着约50%的光伏产品市场份额[1]。
多晶硅铸锭晶粒的大小及组织形态与电池的性能有着密切的联系,晶粒尺寸均一、粗大有利于得到高质量的多晶硅片,从而提高多晶硅太阳电池的效率[2]。
多晶硅晶粒大小和组织形态,很大程度上取决于多晶硅铸锭炉热场设计以及工艺过程。
以往热场设计都是通过实验来调整,这需要很高的成本及时间。
同时,由于铸锭炉很高的温度,所以得到炉体内部的温度分布非常困难。
数值模拟的出现为更好的理解熔体凝固过程中的传热传质以及温场、流场的分布提供了有力的工具,已经成为学术界和产业界的重要研究和开发手段[3]。
1 模型及参数设置
本文采用工业界常用的带有移动隔热笼的多晶硅铸锭炉进行研究。
铸锭炉的物理模型采用简化的二维轴对称模型。
在物理模型中,考虑了晶体、熔体和坩埚内的能量守恒,熔体和气体中的对流、各表面之间的辐射、结晶潜热、高温熔体内的湍流流动。
模拟采用STR
公司开发的晶体生长专业模拟软件CGSim,该软件用于多晶硅铸锭的数值模拟研究已被大量文献所报道。
计算方法采用有限元法(固体区域)与有限体积法(流体区域)结合。
2 初始结构模拟结果
本文以GT Advanced Technology的DSS450多晶硅铸锭炉为参考,量取了其热场的实际尺寸并做了适当简化,从而进行数值模拟,以铸锭炉中晶体生长到熔体高度一半时(110 mm)为具体说明数据点,得到了炉体内温场分布、流场分布以及固液界面的形状。
2.1 等温线与熔体对流
模拟结果表明,热场未优化时:等温线和固液界面在坩埚壁面处向上翘曲,高于坩埚中心的等温线高度,说明温度在坩埚壁面上偏低,有利于多晶硅晶体的快速生长;靠近坩埚壁面处趋于平坦,并在中心处稍凸。
对于流场而言,熔体中形成一个对流漩涡,由坩埚壁向下,至熔体中心区域向上,这样的流场将不利于杂质挥发,因为坩埚壁附近的向下涡流,将把硅熔体边缘以及坩埚壁的杂质带入熔体底部并向中心流动。
2.2 生长界面上的V/G比值
参数V/G比值是用于研究自缺陷的生长动力学而引入的,结晶界面前沿是否会发生组分过冷主要受界面前沿的温度梯度G、晶体生长速度V以及溶质边界层的厚度δc的影响。
V/G比值越小且溶质边界
层厚度δc越小,越不容易发生组分过冷。
较大的V/G比,将发生熔体过冷,不利于大晶粒铸锭的生长而且会导致微晶产生,产生阴影,从而影响电池效率。
从模拟结果可以看出V/G比在在坩埚中心最低,离坩埚300~400 mm时的值最大,在坩埚壁面处下降。
3 优化方案及模拟结果
3.1 优化方案
在保持热场其他部分不改变的情况下,仅在DS块四个底边增加了一段隔热条,目的是减少向侧面的散热,促进竖直向上的定向凝固。
3.2 优化方案分析
模拟结果显示,优化后的等温线和改进前的等温线相比,温度间隔增大。
两种温场将对晶体生长产生不同的影响。
改进前的温场,坩埚中心向上凸出不明显,同时坩埚壁附近有向上翘起的等温线,因此,不利用中心多晶的定向凝固。
而热场底部改进后,在坩埚底部的等温线间隔变大,散热更加集中从DS块正下方进行,同时改进后固液界面凸出率增大,靠近坩埚壁的等温线上翘现象被显著抑制,这样晶粒可以沿着垂直于界面的方向生长,可以有效减少侧壁形核;另一方面,可以减少晶粒向晶锭中间生长。
4 结论
本文提出一种优化方案,通过数值模拟研究了优化方案前、后的
炉体内温场、流场和杂质分布,得出以下结论。
(1)坩埚中间晶体凸出率增大,壁面附近区域翘曲减小。
有利于生长高质量多晶硅。
(2)熔体中的由一个涡流变成两个涡流,使掺杂剂的分布更加均匀。
(3)减小了V/G比值,从而减少微晶的产生,进而减少了阴影形成的概率。
参考文献
[1] G.Hering.Year of the tiger[J].Photon International,2011,3:186-218.
[2] Fujiwara K,Pan W,Sawada K,et al.Directional growth method to obtain high quality polycrystalline silicon from its melt[J].Journal of Crystal Growth,2006(2):282-285,292.
[3] I.Steinbach,M.Apel,T.Rettebach,D. Frank, Numerical simulations for silicon crystallization processes-examples from ingot and ribbon casting[J].Solar Energy Material and Solar cells,2002:59-68,72.。