金属切屑原理4
金属切削原理

金属切削原理一、引言金属切削是一种重要的加工方法,广泛应用于机械制造、航空航天、汽车制造等领域。
金属切削的原理是将金属材料通过刀具的切削力和磨擦力进行去除,从而得到所需形状和尺寸的工件。
本文将详细介绍金属切削的原理。
二、金属材料的物理特性金属材料具有高强度、高硬度、高塑性等特点。
在进行切削加工时,需要考虑到这些特性对加工过程和结果的影响。
1.硬度硬度是指材料抵抗外界力量侵蚀和破坏的能力。
在进行金属切削时,硬度会影响到刀具对材料的切削深度和速度。
硬度越大,材料越难被去除,需要采用更高强度和更耐磨损的刀具。
2.韧性韧性是指材料抵抗断裂和变形的能力。
在进行金属切削时,韧性会影响到刀具对材料的变形程度和断裂情况。
韧性越大,材料越容易被刀具弯曲和拉伸,需要采用更大的切削力和更耐磨损的刀具。
3.塑性塑性是指材料在受到外力作用下发生变形的能力。
在进行金属切削时,塑性会影响到材料的变形程度和表面质量。
塑性越大,材料越容易被切削并留下较光滑的表面。
三、切削力的产生金属切削过程中,主要有三种力对工件进行去除:正向切削力、侧向切削力和径向切削力。
这些力产生的原因如下:1.正向切削力正向切削力是指沿着工件表面方向施加在主轴上的推进力。
它是由于主轴上旋转的刀具与工件之间产生了摩擦而引起的。
2.侧向切削力侧向切削力是指垂直于工件表面方向施加在主轴上的推进力。
它是由于主轴上旋转的刀具与工件之间产生了摩擦而引起的。
3.径向切削力径向切削力是指垂直于工件表面方向施加在主轴上的推进力。
它是由于主轴上旋转的刀具与工件之间产生了摩擦而引起的。
四、切削过程中的热效应金属切削过程中,由于摩擦和变形,会产生大量的热量。
这些热量会对材料和刀具造成影响。
1.材料的热变形在金属切削过程中,由于高速旋转的刀具与工件之间产生了摩擦,会使得材料表面温度升高。
当温度达到一定值时,材料就会发生热变形,导致尺寸和形状发生变化。
2.材料的热软化在金属切削过程中,由于高速旋转的刀具与工件之间产生了摩擦,会使得材料表面温度升高。
金属切削原理

三、切削层参数
•切削层厚度hD 垂直于正在加工的表面(过渡表面)度量 的切削层参数。 hD=f•sinκ r •切削层宽度bD 平行于正在加工的表面(过渡表面)度 量的切削层参数。 bD=ap/sinκ r •切削层横截面积AD 在切削层参数平面内度量的横截面 积。 AD=hD•bD=ap•f
常用刀具材料有碳素工具钢(如T10A、T12A)、合金工具钢 (如9SiCr、CrWMn)、高速钢、硬质合金、陶瓷、金刚石、 立方炭化硼等。
二、常用刀具材料
常用刀具材料的种类及其特性 • 碳素工具钢 • 高速钢 • 硬质合金 • 其它刀具材料(涂层刀具、陶瓷、金刚石、立方氮
化硼 )
• 优点、缺点、种类、常用牌号、应用等
1. 金属切削过程
刀具从工件上切除多余的金属的过程,并使工件得到符 合图纸要求的尺寸、形状和表面质量。
必须具备以下三个条件: 1.工件和刀具之间要有相对运动及,即切削运动; 2.刀具材料必须具备一定的切削性能; 3.刀具必须有合理的几何参数,即切削角度等。
一、切削运动与切削用量 1.工件加工表面
在切削过程中,工件上存在三个不断变化的表面:
上述公式中可看出 hD、bD均与主偏角有关,但切削层 横截面积 AD 只与 hD、bD 或 f、ap有关。
§1-2 刀具材料
•刀具材料通常是指刀具切削部分的材料。 •加工质量、加工效率、加工成本,在很大程度上取决于 刀具材料的合理选择。因此,材料、结构和几何形状是决 定刀具切削性能的主要因素。 •金属切削过程除了要求刀具具有适当的几何参数外,还 要求刀具材料具备一定性能。
金属切削原理与刀具

金属切削原理与刀具金属切削是指通过刀具对金属材料进行加工削除的过程,是金属加工领域中常见且基础的一种加工方式。
人们在制造和加工各种金属制品的过程中,常常需要通过切削来将金属材料加工成所需的形状和尺寸。
本文将深入探讨金属切削的原理以及相关的刀具类型。
一、金属切削原理金属切削的原理是利用刀具对金属工件进行力学削除材料的过程。
主要原理可以归纳为以下几点:1. 刀具与工件的相互作用力:切削过程中,刀具施加在工件上的作用力可以分为切割力、摩擦力、压力等。
切割力使刀具沿着切削方向削除金属,摩擦力影响工件表面的质量,而压力则有助于防止振动和提高切削质量。
2. 刀具与工件的接触面积:切削过程中,刀具与工件的接触面积较小,集中在切削刃上。
通过提高切削刃的硬度和耐磨性,可以减少切削面的磨损,延长刀具的使用寿命。
3. 金属切削时的切削角度:切削角度是指刀具切削刃与工件表面法线之间的夹角。
合理选择切削角度可以使切削过程更加顺利,减少切削力和切削温度。
二、常见的刀具类型不同的金属切削需求需要选择不同类型的刀具。
以下将介绍几种常见的刀具类型及其特点:1. 钻头:用于钻孔加工的刀具,主要特点是具有较高的刚性和旋转精度。
根据孔径的大小,可以选择不同类型的钻头,如常规钻头、中心钻头和孔径加工钻头等。
2. 铣刀:用于面铣、端铣、槽铣等加工的刀具,形状像一把小锯齿,可通过旋转进行切削。
铣刀可分为平面铣刀、球头铣刀、棒铣刀等多种类型,适用于不同形状和尺寸的金属切削。
3. 刀片:用于车削加工的刀具,通常由硬质合金制成,具有较高的耐磨性。
刀片形状多样,如可直线切削的刀片、可拐弯切削的刀片等,适用于不同形状和尺寸的车削加工。
4. 锯片:用于锯切金属材料的刀具,常用于金属管、金属板的切割。
根据不同的锯片规格和齿型,可以实现不同精度和效率的锯切加工。
5. 切割刀具:包括切割刀片和切割车刀等,主要用于金属材料的切割和切断。
根据切割的需求和要求,选择合适的切割刀具可以提高加工效率和切割质量。
金属切削加工原理

三、刀具的角度
(5)刃倾角λs 在切削平面内测量的主切削刃与基面之间的夹角。
当主切削刃呈水平时,λs=0;刀尖为主切削刃最低点时, λs〈0;刀尖为主切削刃上最高点是,λs 〉0 。
三、刀具的角度
(6)刀具角度的选择 1)前角 前角γo对切削的难易程度有很大影响。增大前角能
使刀刃变得锋利,使切削更为轻快,并减小切削力和切 削热。但前角过大,刀刃和刀尖的强度下降,刀具导热 体积减少,影响刀具使用寿命。前角的大小对表面粗糙 度、排屑和断屑等也有一定影响。工件材料的强度、硬 度低,前角应选得大些,反之小些;刀具材料韧性好 (如高速钢),前角可选得大些,反之应选得小些(如 硬质合金);精加工时,前角可选得大些。粗加工时应 选得小些。
三、刀具的角度
三、刀具的角度
(一)刀具的主剖面参考系
(1)基面Pr:通过切削刃某一点,垂直于假定 主运动方向的平面。
(2)切削平面Ps:通过切削刃某一点,与工件 加工表面(或与主切削刃)相切的平面。切削平 面Ps与基面Pr垂直。
(3)主剖面P0:通过切削刃某一点,同时垂直 于切削平面Ps与基面Pr的平面。
பைடு நூலகம்
二、切削用量三要素
主运动为回转运动时: Vc时(m/s或
m/min)
Vc=(3.14·d·n)/1000
式中 d—切削刃上选定点的回转直径(mm); n—主运动的转速(r/s或r/min)。
二、切削用量三要素
2、进给速度vf 、进给量f 进给速度vf—切削刃上选定点相对于工件
的进给运动瞬时速度,mm/s或mm/min.。 进给量f—刀具在进给运动方向上相对于
一、切削表面与切削运动
2、进给运动 进给运动是配合主运动实现依次连续不断地 切除多余金属层的刀具与工件之间的附加相对运 动。进给运动与主运动配合即可完成所需的表面 几何形状的加工,根据工件表面形状成形的需要, 进给运动可以是多个,也可以是一个;可以是连 续的,也可以是间歇的。
金属切削原理

金属切削原理金属切削是一种常见的金属加工方法,广泛应用于机械制造、航空航天、汽车制造等领域。
金属切削的原理是利用刀具对金属材料进行切削,从而得到所需形状和尺寸的工件。
在金属切削过程中,刀具与工件之间发生相对运动,刀具对工件进行切削,将金属屑削除,最终得到所需的工件形状。
金属切削的原理包括刀具、工件和切削速度等因素。
首先,刀具是金属切削的主要工具,其质量和形状对切削质量有着重要影响。
刀具的材料应选择硬度高、耐磨性好的材料,以保证刀具在切削过程中不易磨损。
此外,刀具的刃部形状和刃口角度也会影响切削力和切削质量。
其次,工件的材料和形状也会对切削过程产生影响。
不同材料的硬度、塑性等性质会影响切削时的刀具选择、切削力和切削质量。
另外,工件的形状和尺寸对切削过程中的切削力、切削稳定性等也有影响。
最后,切削速度是影响切削质量的重要因素之一。
切削速度的选择应考虑刀具材料、工件材料、切削方式等因素,以保证切削过程中的切削质量和刀具寿命。
在金属切削过程中,切削力是一个重要的参数。
切削力的大小和方向直接影响刀具的切削质量和刀具寿命。
切削力的大小受到切削速度、切削深度、切削宽度等因素的影响。
切削力的大小和方向可以通过切削力模型和实验测试来确定,以指导切削过程中的刀具选择、切削参数的确定等。
此外,切削温度也是金属切削过程中需要重点关注的问题。
切削过程中,刀具和工件之间的摩擦和变形会产生热量,导致切削区温度升高。
高温会影响刀具的硬度和耐磨性,同时也会影响工件的表面质量。
因此,控制切削温度是保证切削质量的重要手段之一。
总的来说,金属切削原理涉及到刀具、工件、切削速度、切削力、切削温度等多个方面的内容。
了解金属切削的原理,有助于合理选择刀具、确定切削参数,保证切削质量,提高加工效率。
同时,金属切削原理也为金属加工技术的发展提供了理论基础,推动了金属加工技术的不断进步。
金属切削原理

金属切削原理金属切削是一种常见的金属加工方法,通过切削工具对金属材料进行加工,以获得所需形状和尺寸的工件。
金属切削原理是指在切削过程中,切削刀具对工件进行切削,形成切屑并使工件形成所需形状和尺寸的过程。
金属切削原理的理解对于提高切削加工效率、提高加工质量具有重要意义。
首先,金属切削原理的基本过程是切削刀具对工件进行切削。
在切削过程中,切削刀具与工件之间产生相对运动,切削刀具对工件表面进行切削,形成切屑。
切削刀具的刀尖与工件接触处称为刀尖触点,刀尖触点是切削过程的关键部位,刀尖触点的运动状态直接影响着切削过程的稳定性和加工质量。
其次,金属切削原理的关键参数包括切削速度、进给量和切削深度。
切削速度是切削刀具在单位时间内对工件进行切削的速度,通常用米/分钟表示;进给量是切削刀具在单位时间内对工件进行进给的距离,通常用毫米/转表示;切削深度是切削刀具在切削过程中对工件进行切削的深度,通常用毫米表示。
这三个参数的选择直接影响着切削过程的效率和加工质量。
另外,金属切削原理的切削力是切削过程中的重要参数。
切削力的大小和方向直接影响着切削刀具和工件的磨损情况、加工精度和加工表面质量。
切削力的大小受到切削条件、切削刀具和工件材料等因素的影响,合理控制切削力是提高切削加工效率和加工质量的关键。
最后,金属切削原理的切削热是切削过程中的重要问题。
切削热的产生直接影响着切削刀具和工件的温度、切削刀具的寿命和加工表面质量。
切削热的产生受到切削速度、切削深度、切削方式和切削刀具材料等因素的影响,合理控制切削热是提高切削加工效率和加工质量的关键。
总之,金属切削原理是切削加工的基础,对于提高切削加工效率、提高加工质量具有重要意义。
合理控制切削条件、切削力和切削热是提高切削加工效率和加工质量的关键。
只有深入理解金属切削原理,才能更好地应用于实际生产中,提高加工效率,降低成本,提高产品质量。
金属材料与金属切削加工原理
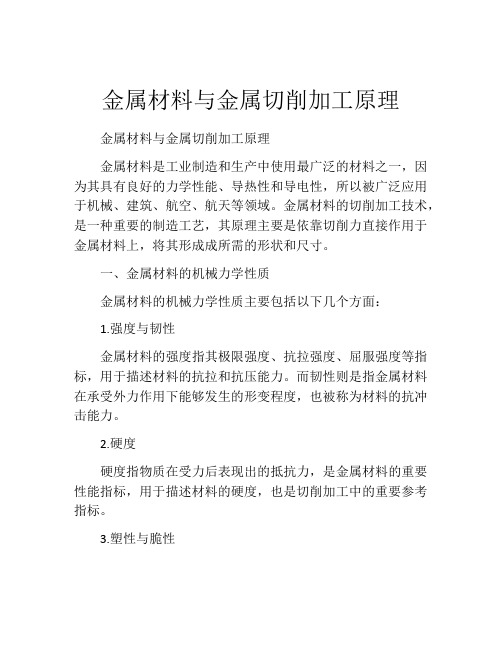
金属材料与金属切削加工原理金属材料与金属切削加工原理金属材料是工业制造和生产中使用最广泛的材料之一,因为其具有良好的力学性能、导热性和导电性,所以被广泛应用于机械、建筑、航空、航天等领域。
金属材料的切削加工技术,是一种重要的制造工艺,其原理主要是依靠切削力直接作用于金属材料上,将其形成成所需的形状和尺寸。
一、金属材料的机械力学性质金属材料的机械力学性质主要包括以下几个方面:1.强度与韧性金属材料的强度指其极限强度、抗拉强度、屈服强度等指标,用于描述材料的抗拉和抗压能力。
而韧性则是指金属材料在承受外力作用下能够发生的形变程度,也被称为材料的抗冲击能力。
2.硬度硬度指物质在受力后表现出的抵抗力,是金属材料的重要性能指标,用于描述材料的硬度,也是切削加工中的重要参考指标。
3.塑性与脆性金属材料的塑性表示其抵抗外力作用下形变的能力,包括延伸性和压缩性。
而脆性则是指金属材料受到外力作用后容易发生断裂的程度和能力。
二、金属切削加工原理金属切削加工依赖于机床和刀具,主要包括车削、铣削、钻孔、刨削、镗削等类型。
其主要原理是以旋转刀具的切削力作用于金属材料上,通过对金属材料的去除甚至改变形态、表面质量等特性来达到所需的目的。
金属切削加工的原理主要涉及以下几个方面:1.切削力与切削参数切削力是实现切削加工的基础,它反映出切削加工的耗能和加工结果的质量。
受切削力影响的主要参数包括切削速度、进给量和切削深度,同时还受到切削工具和工件材料的影响。
2.切削加工中的热效应金属切削加工时还有一些额外的效应值得注意,例如热效应。
在切削加工过程中,由于金属材料受到切削力的摩擦作用,会产生大量的热量,导致工件表面温度升高,可能影响工件的材料性质等特性。
3.切削刃具的材料和几何形状切削刃具是金属切削加工的重要组成部分之一,其材料和几何形状都会直接影响切削加工的效果。
常用的切削刃具材料包括高速钢、硬质合金、陶瓷等。
4.切削产品表面和尺寸精度金属切削加工的最终目的是形成所需的尺寸和表面形态,因此必须对切削产品的表面精度和尺寸精度进行精确的控制。
金属切削原理的基本原理与应用探析

金属切削原理的基本原理与应用探析金属切削是指在机械加工过程中,通过刀具对金属材料进行切削加工的一种方法。
切削加工是现代工业生产中非常重要的一环,广泛应用于制造业的各个领域,如汽车制造、航空航天、机械制造等。
本文将探析金属切削原理的基本原理和应用。
一、金属切削原理的基本原理1. 切削力与材料性质的关系切削力是刀具和工件之间产生的力,它直接影响到切削加工的效率和质量。
切削力与金属材料的性质有密切关系,例如硬度、韧性和塑性等特性。
一般来说,材料硬度越高,切削力越大。
2. 切削热的生成与影响在切削过程中,由于刃口与工件接触产生摩擦,会产生大量的切削热。
切削热的大小和分布对切削加工有着重要影响。
过高的切削热可能导致刀具磨损加剧、工件变形,甚至热裂纹的产生。
因此,有效控制切削热对于提高切削加工质量至关重要。
3. 切削液的作用切削液在切削过程中起到冷却、润滑和防腐的作用。
通过降低切削热,它可以有效地控制切削加工过程中的温度,减少工件表面的热变形,提高切削加工质量和效率。
4. 切削刃部分的结构与刀具磨损切削刃是切削工具的重要部分,其结构设计直接影响到切削加工的效果。
一般来说,切削刃的设计要使切削力分布均匀,降低切削热和切削力,延长切削工具的寿命。
此外,选择合适的材料和硬度对切削刃的寿命也有很大影响。
二、金属切削的应用探析1. 汽车制造汽车制造是金属切削应用的重要领域之一。
在汽车制造中,金属切削广泛应用于发动机、底盘、车身等零部件的加工。
通过金属切削,可以精确加工出复杂形状的零部件,提高汽车的质量和性能。
2. 航空航天工业航空航天工业对金属切削的要求更为严格。
在航空航天工业中,金属切削应用于航空发动机、机翼、航天器等部件的加工。
金属切削技术的发展和应用,推动了航空航天工业的进步和发展。
3. 机械制造金属切削在机械制造领域中扮演着重要角色。
在机械制造中,金属切削应用于制造各种机床、工具以及零部件等。
通过金属切削技术,可以提高机械制造的精度和效率,满足不同行业和领域的生产需求。
金属切削原理的基本概述

金属切削原理的基本概述金属切削是一种常见的金属加工技术,广泛应用于制造业和机械加工领域。
金属切削的原理是通过切削工具对金属材料施加力量,以去除材料表面的金属层,实现工件的加工和成形。
金属切削原理可以分为以下几个方面:1. 切削力:在金属切削过程中,切削工具施加力量以去除金属材料。
切削力是指切削工具对工件施加的力的大小和方向。
切削力的大小取决于刀具的几何形状、切削速度、切削深度、切削角度等因素。
在金属切削中,通常会产生切向力(与切削方向垂直的力)和径向力(指向工件中心的力)。
2. 切削削角:切削削角是切削刀具与工件表面之间的夹角。
切削削角的大小和形状会影响切削力的大小、切削刃的寿命和切削表面的质量。
常见的切削削角有前角、主削角、副削角等。
3. 切削速度:切削速度是指切削工具和工件相对运动的线速度。
切削速度的选择会影响切削力、切削表面的质量和刀具的寿命。
过低的切削速度可能导致刀具与工件之间产生太多的摩擦热,使刀具磨损加快;而过高的切削速度则可能导致工件表面粗糙、切削力过大。
4. 切削深度:切削深度是指切削工具将金属材料削除的深度。
切削深度的选择取决于工件的要求和切削工具的强度。
过大的切削深度可能导致切削力过大,增加切削工具的磨损和变形的风险;而过小的切削深度则可能导致加工效率低。
5. 切削热效应:切削过程中,因为摩擦和形变,切削区域会产生热量。
切削热效应可能对切削工具和工件产生不良影响,如切削刃磨损、加工表面质量下降等。
因此,在金属切削过程中,需要采取适当的切削冷却液和润滑剂等措施来降低切削热效应。
总结起来,金属切削原理是通过切削工具施加力量,削除金属材料表面的方法。
切削力、切削削角、切削速度、切削深度和切削热效应是决定切削过程中刀具寿命、工件表面质量和加工效率的重要因素。
掌握金属切削原理,对于提高金属加工的质量和效率具有重要意义。
金属切削原理
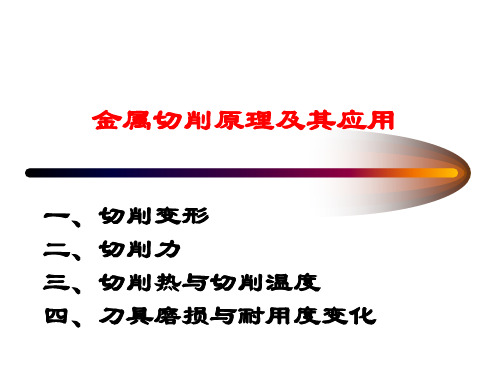
切削时消耗的功率
金属切削原理及其应用
一、切削变形 二、切削力 三、切削热与切削温度 四、刀具磨损与耐用度变化
1.1 金属切削过程的基本规律
一、切削变形 变形Ⅰ,Ⅱ,Ⅲ区, 剪切面间距0.02-0.2mm。
1. 切屑的形成
图为金属切削过程中的滑移线
1.1 金属切削过程的基本规律.
• (1)第一变形区 从OA线开始发生塑性变形,到 OM线金属晶粒的剪切滑移基本完成。OA线和OM 线之间的区域(图中Ⅰ区)称为第一变形区。
碳素钢,合金钢,铜 铝合金; 黄铜,低速切削钢; 铝; 铸鉄,黄铜
图为切屑类型
2. 积屑瘤
图为积屑瘤与切削刃的金 相显微照片
2. 积屑瘤
积屑瘤高度及其实际工作前角
2. 积屑瘤
(1)积屑瘤对切削过程的影响: 1) 积屑瘤包围着切削刃,可以代替前面、后面和切
削刃进行切削,从而保护了刀刃,减少了刀具的磨 损。 2) 积屑瘤使刀具的实际工作前角增大,而且,积屑 瘤越高,实际工作前角越大,刀具越锋利。 3) 积屑瘤前端伸出切削刃外,直接影响加工尺寸精 度。 4) 积屑瘤直接影响工件加工表面的形状精度和表面 粗糙度。
Fx Fxy sin r
3. 影响切削力的因素
3)刀具几何参数对切削力的影响。
c)刃倾角ls 对切削力的影响; ls↑ 背前角gp↑ 侧前角gf↓
Fp↓ Ff↑
3. 影响切削力的因素
3)刀具几何参数对切削力的影响。
d)刀尖圆弧半径r 对切削力的影响;
3. 影响切削力的因素
3)刀具几何参数对切削力的影响。 e)使用切削液 对切削力的影响;
v a 273
f 0.26 0.07
c
0.01
金属切削的基本原理

金属切削的基本原理金属切削的基本原理1. 引言金属切削作为一种重要的制造工艺,在现代工业中得到广泛应用。
了解金属切削的基本原理对于提高生产效率和产品质量至关重要。
本文将深入探讨金属切削的原理和相关概念。
2. 金属切削的定义和概述金属切削是指通过工具在金属材料上切削形成所需形状的制造过程。
这种切削通过将刀具与金属工件相对移动来去除材料,从而实现目标形状。
金属切削常用于车削、铣削、钻削等加工过程中。
3. 切削过程的基本元素金属切削包括以下基本元素:3.1 切削工具切削过程中使用的工具通常由坚固的材料制成,如高速钢、硬质合金等。
切削工具的类型和几何形状根据切削操作的需求而变化,比如刀片、铣刀、钻头等。
3.2 金属工件金属工件是经过切削加工的目标。
它可以是圆柱形、平面形或复杂形状的。
不同材料的切削特性也会影响切削过程的选择和参数设定。
3.3 切削速度切削速度是指工具切削过程中与工件接触部分的相对速度。
合适的切削速度可以提高加工效率和工件表面质量,但过高的切削速度可能导致工具磨损和加工表面粗糙度增加。
3.4 进给速度进给速度是指工具与工件相对运动的速度。
适当的进给速度可以控制切削过程中材料的去除率,同时避免过度磨损和切削力过大。
3.5 切削深度切削深度是指工具进入工件的深度,即每次切削过程中所移除的金属厚度。
切削深度的选择应根据工件的要求、切削力和工具稳定性等因素考虑。
4. 金属切削的力学原理金属切削的力学原理主要涉及三个力:切削力、切向力和主动力。
4.1 切削力切削力是指在金属切削过程中作用在切削工具上的力。
它由切削材料的去除、摩擦和变形引起。
切削力的大小和方向取决于切削工艺参数、切削材料和刀具等。
4.2 切向力切向力是指垂直于切削方向的力。
它使工件保持在切削位置,并防止工件偏离切削方向。
切向力的大小和方向直接影响切削的稳定性和表面质量。
4.3 主动力主动力是指在金属切削过程中将工具向工件施加的力。
它与切削深度和切削速度等直接相关。
金属切削原理

金属切削原理金属切削是一种常见的加工方法,广泛应用于机械制造、航空航天、汽车制造等领域。
金属切削原理是指在切削过程中,通过刀具对金属工件进行切削,以达到加工工件的目的。
金属切削原理涉及到切削力、切削热、切削变形等多个方面的知识,下面将就金属切削原理进行详细介绍。
首先,切削力是金属切削过程中最重要的因素之一。
切削力的大小直接影响到刀具的寿命、加工表面的质量以及加工效率。
切削力的大小受到刀具材料、刀具几何角度、切削速度、进给量等多个因素的影响。
在金属切削过程中,切削力的大小会导致刀具的磨损,因此需要合理选择切削参数,以减小切削力对刀具的影响。
其次,切削热是金属切削过程中不可忽视的因素。
在金属切削时,由于刀具与工件的摩擦以及金属的塑性变形,会产生大量的热量。
切削热的积累会导致刀具的温度升高,从而影响刀具的硬度和耐磨性。
因此,合理选择切削液、控制切削速度、提高刀具的散热能力是减小切削热对刀具的影响的有效方法。
另外,切削变形也是金属切削过程中需要考虑的因素之一。
在金属切削过程中,由于切削力的作用,工件会发生形状和尺寸的变化,这就是切削变形。
切削变形的大小受到材料的塑性变形能力、切削参数、切削方式等因素的影响。
合理选择切削工艺、提高工件的刚性、控制切削温度是减小切削变形的有效途径。
综上所述,金属切削原理涉及到切削力、切削热、切削变形等多个方面的知识。
合理选择切削参数、提高刀具的耐磨性、控制切削温度是减小切削力、切削热、切削变形对刀具的影响的有效方法。
只有深入理解金属切削原理,合理应用切削知识,才能更好地进行金属加工,提高加工效率,提高加工质量。
金属切削机床 原理
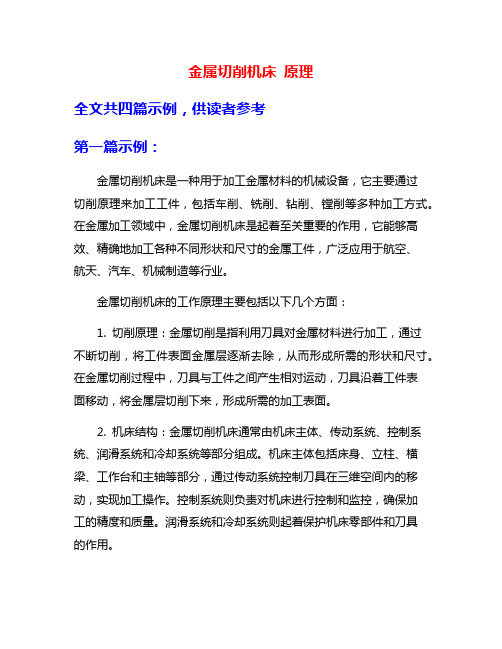
金属切削机床原理全文共四篇示例,供读者参考第一篇示例:金属切削机床是一种用于加工金属材料的机械设备,它主要通过切削原理来加工工件,包括车削、铣削、钻削、镗削等多种加工方式。
在金属加工领域中,金属切削机床是起着至关重要的作用,它能够高效、精确地加工各种不同形状和尺寸的金属工件,广泛应用于航空、航天、汽车、机械制造等行业。
金属切削机床的工作原理主要包括以下几个方面:1. 切削原理:金属切削是指利用刀具对金属材料进行加工,通过不断切削,将工件表面金属层逐渐去除,从而形成所需的形状和尺寸。
在金属切削过程中,刀具与工件之间产生相对运动,刀具沿着工件表面移动,将金属层切削下来,形成所需的加工表面。
2. 机床结构:金属切削机床通常由机床主体、传动系统、控制系统、润滑系统和冷却系统等部分组成。
机床主体包括床身、立柱、横梁、工作台和主轴等部分,通过传动系统控制刀具在三维空间内的移动,实现加工操作。
控制系统则负责对机床进行控制和监控,确保加工的精度和质量。
润滑系统和冷却系统则起着保护机床零部件和刀具的作用。
3. 切削参数:金属切削的质量和效率与切削参数密切相关。
切削参数包括切削速度、进给量、切削深度和切削角度等。
切削速度是指刀具在单位时间内相对于工件表面的线速度;进给量是刀具在切削方向的移动距离;切削深度是刀具切入工件的深度;切削角度是刀具相对于工件表面的角度。
通过合理调整这些参数,可以实现不同加工需求的加工效果。
4. 切削工艺:金属切削工艺是一项复杂的加工过程,需要运用切削原理来实现。
在实际加工中,需要选择合适的切削工艺,根据工件材料、形状和尺寸来确定刀具的选择、切削速度、进给量和切削深度等参数,以获得高质量的加工效果。
还需要考虑切削过程中产生的热量和切屑的处理,保证加工过程的稳定性和安全性。
金属切削机床是一种重要的加工设备,它通过切削原理来实现对金属材料的加工。
了解金属切削机床的工作原理,可以帮助我们更好地理解其加工过程和性能特点,进而提高加工效率和加工质量。
金属切削加工的工作原理

金属切削加工的工作原理金属切削加工是指通过对金属材料施加一定的力和转动工具,从工件上去除材料以达到所需形状和尺寸的加工方法。
这是一种广泛应用于制造业的重要工艺,用于制作各种金属制品,如零件、工具和零部件。
金属切削加工的工作原理包括以下几个方面:1. 切削力的产生和传递金属切削加工过程中,切削刀具通过在工件表面施加力来切削金属材料。
切削力是金属切削加工中最主要的力。
切削力的产生和传递从切削刀具到工件时,经过以下几个部分的相互作用:刀具的刃口,刀具周边的切削区域,刀具的后角和刃口的前角。
切削力的大小和方向受到切削速度、切削深度、进给量、切削刃口形状、工件材料和切削液等因素的影响。
2. 切削刃口的工作机制切削刃口是切削刀具上起切削作用的部分。
切削刃口的工作机制主要是依靠切削力的作用,将金属材料切削下来。
切削刃口通常有直刃、斜刃和弯刃等不同形状,不同形状的刃口适用于不同的切削工艺和工件材料。
3. 金属切削加工过程中的热力学效应金属切削加工过程中,刀具和工件之间的相互作用会产生热量。
这是由于切削过程中发生的金属材料的塑性变形、摩擦和切削刃口与工件表面接触的原因。
通过切削过程中产生的热传导、热对流和热辐射,会让切削区域的温度升高。
为了避免过高的温度对刀具和工件的影响,通常会使用切削液进行冷却和润滑。
4. 金属切削加工的切削方式金属切削加工可以通过不同的方式实现,常见的切削方式有手动切削、机械切削和数控切削等。
手动切削是在操作者的手动控制下进行的,适用于小批量加工和简单形状的工件。
机械切削是通过机床实现的,具有高效率和精度高的优点,适用于大批量生产。
数控切削是在计算机的控制下进行的,通过预先编程的方式控制切削过程,可以实现高度精确的加工。
5. 切削液的作用和选择切削液在金属切削加工中具有重要的作用。
切削液可以冷却切削区域,降低温度,减少刀具磨损和工件变形的可能性。
同时,切削液也可以提供润滑,减少切削刃口与工件表面之间的摩擦,有助于提高加工表面的质量。
机械制造技术基础金属切削原理

机械制造技术基础金属切削原理金属切削是机械加工中常见的一种工艺,广泛应用于机械制造领域。
金属切削的原理主要包括金属材料的切削力、金属切削的切削速度和金属切削的切削温度等方面。
本文将以机械制造技术基础为主题,详细介绍金属切削的原理。
一、金属切削的切削力在金属切削过程中,切削力是指作用在切削刃上的力。
切削力是切削过程中最重要的性能之一,它直接影响到加工精度、表面质量和切削工具的寿命。
切削力的大小与切削深度、进给量、切削速度、切削力角等因素有关。
1.切削深度:切削深度是指切削刀具与原材料表面的距离。
切削深度的增大会使得切削力增大,但是切削力增加并不是线性关系,切削深度较小时,切削力随着切削深度的增大呈线性增大;切削深度较大时,切削力随着切削深度的增大呈指数增大。
2.进给量:进给量是指切削刀具在单位时间内与工件的相对运动位移,通常用每转进给量表示。
进给量的增大会使得切削力增加,但是这种关系是线性关系。
3.切削速度:切削速度是指切削刀具与工件相对运动的速度。
切削速度的增大会使得切削力增加,但是这种关系并不是线性关系,一般呈现出二次方的增长。
4.切削力角:切削力角是指切削刃与切削面之间的夹角。
切削力角的大小主要取决于材料的性质,一般情况下切削硬材料时,切削力角偏大,切削软材料时,切削力角偏小。
二、金属切削的切削速度切削速度是指切削刀具与工件之间相对运动的速度。
切削速度对于金属切削的性能和加工效果具有重要影响。
切削速度的选择要根据切削材料的硬度、材料的大面积、工件的形状和工件表面的粗糙度等因素来进行选择。
1.切削硬度:切削硬度越大,切削速度越低。
这是由于硬度大的材料在切削过程中会提供更大的阻力,增加切削过程中所需的能量。
2.材料的大面积:当切削材料的大面积增大时,切削速度应适当降低,以避免因切削速度过高导致的工件变形、断裂等问题。
3.工件的形状:工件形状的不同会导致切削刃与工件之间的接触面积不一样,从而影响切削力的大小。
金属切削原理
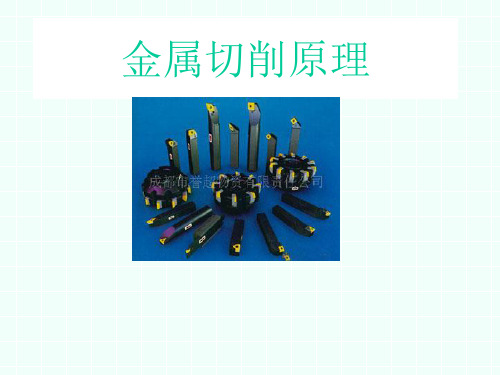
车削时的进给速度vf
νf=fn
(1-2)
3.背吃刀量αp
工件上已加工表面和待加工表面间
垂直距离。车外圆时:
αp= d w d m
2
(1-3)
式中 dm——已加工表面直径。
dw——待加工表面直径。
小结:
• 车削运动 • 车削中形成的表面 • 切削用量
主运动 进给运动 切削速度Vc 进给量f 背吃刀量αp
练习
在车床上车一直径为60毫米的轴, 现要一次走刀到直径为52毫米,如果选 切削速度ν=80米/分,求背吃刀量αp (吃刀深度)和车床主轴转速(n)各f
3.背吃刀量αp
1.切削速度Vc
切削刃选定点相对工件主运动的瞬时 速度。单位为m/s (m/min)
车削时切削速度计算式为:
ν= dn
1000
(1-1)
式中 d —待加工表面直径(mm) n —主运动的旋转速度( r /min 或r /s )。
2.进给量f
工件或刀具每转一转或刀具往复一次, 刀具相对工件在进给运动方向上的位移, 单位mm/r。
金属切削原理
切削加工一般可分为:
车削、铣削、钻削、镗削、铰削、刨削、 插削、拉削、锯切、磨削、研磨、珩磨、 超精加工、抛光、齿轮加工、蜗轮加工、 螺纹加工、超精密加工、钳工和刮削等。
一、金属切削加工的 基本概念
车削运动 车刀角度 切削方式
一、车削运动
切削运动—是指利用刀具切除工件 上多余的金属层,以获得所要求的尺寸、 形状精度和表面质量的运动。
1.主运动 2.进给运动
车削运动
v 主运动 vf 进给运动
1.主运动(唯一性)
进行切削时最主要的、消耗动力最 多的运动,它使刀具与工件之间产生相 对运动。
金属切削原理与刀具

金属切削原理与刀具
金属切削原理与刀具:
一、金属切削原理
1. 切削力学:切削力定义为金属切削过程中由刀具与工件之间产生的
相互作用力,根据其本质不同可分为动切削力、静切削力和剪切力。
2. 切削热:金属切削过程发生了热量交换,热量大部分是从刀具释放
到工件上,少量热量是从环境里侧移到刀具或者从工件侧移到刀具,
这个过程称为切削热。
3. 切削噪声:切削时由工件与刀具磨擦、刀具与被切物断裂等发出的
噪声,又称切削噪声,是金属切削的重要的污染源之一。
二、金属切削刀具
1. 铣刀:铣刀是一种坚硬的刀具,用于进行几何体表面的金属切削。
它由刀片、刀头、刀杆组成,可根据刀的形状及功能分类为直角铣刀、圆角铣刀、角铣刀、平铣刀等。
2. 内丝锥:内丝锥是用来进行内孔加工的刀具,其分类主要有逆槽内
丝锥和普通内丝锥两种。
它们的工作原理是通过在回转时刮刀后,将
产生的碎屑转到内部进行切削,从而实现内丝的加工。
3. 铰刀:铰刀是一种特殊的铣刀,用于执行开铰、圆弧削、下铰和虚
边倒铰等加工。
它包括刀体和刀杆两个部分,刀体由刀片和刀杆组成,刀杆可以向任意一个方向旋转以达到改变切削角度的目的。
4. 牙铰刀:牙铰刀是切削螺纹的特殊刀具,其外形比普通铰刀大,假牙形状有利于防止刀具与螺纹滑动,即牙铰刀具有牙齿状的刀具,利用微调牙齿的方法调节刀具的切削角度,从而形成不同形状的螺纹。
金属切削原理及刀具分类解析

金属切削原理及刀具分类解析金属切削是一种常见的加工工艺,广泛应用于制造业领域。
本文将对金属切削的原理和刀具分类进行解析,以帮助读者更好地理解和应用金属切削技术。
一、金属切削的原理金属切削是一种通过旋转刀具对工件进行削除金属的加工方式。
其原理主要包括以下几个方面:1. 切削力的产生切削力是刀具对工件施加的力,其产生主要与以下因素相关:切削速度、刀具形状和刀具材料。
高速旋转的刀具与工件碰撞时,会产生一个切削区域,切削力在切削区域内产生,使刃口与工件发生剪切作用,将工件上的金属削除。
2. 削除金属的形式金属切削过程中,金属层与刀具间的作用力导致金属的塑性变形和断裂。
切削时,刀具的刃口对工件表面施加一定的切削力,削除金属。
削除的金属以切屑的形式从切削区域排出。
3. 切削速度和进给速度切削速度是刀具刃口与工件接触的速度,进给速度是切削工具在单位时间内削除金属的量。
切削速度和进给速度的选择对切削过程中的切削力、表面质量和加工效率有重要影响。
二、刀具分类解析刀具是金属切削过程中最重要的工具,根据不同的切削任务和材料特性,可以进行不同类型的刀具选择。
下面将介绍常见的几种刀具分类及其特点。
1. 钻头钻头是一种主要用于钻孔的刀具,通常由高速钢或硬质合金制成。
根据不同的加工要求,钻头可以分为标准钻头、中心钻和铰孔钻。
钻头具有较高的强度和硬度,能够在金属表面快速形成孔洞。
2. 铰刀铰刀是一种用于加工内外螺纹孔的刀具,常用于车削、铣削等操作中。
铰刀的材质通常为高速钢,其刃口具有特殊的结构,可以进行内部和外部螺纹的加工。
3. 铣刀铣刀是一种用于铣削或者切削金属的刀具,广泛应用于零部件加工中。
根据不同的形状和用途,铣刀可分为平行刃铣刀、球头铣刀、刃部刃铣刀等。
铣刀通过旋转或移动刃部与工件接触,实现金属的切削。
4. 刀片刀片是一种常用的切削工具,被广泛应用于车削、铣削等加工工艺中。
刀片通常由硬质合金制成,具有较高的硬度和耐磨性。
金属切削原理

金属切削原理1. 引言金属切削是一种常见的金属加工方法,广泛应用于制造业领域。
本文将深入探讨金属切削原理,包括切削过程的基本概念、切削力的产生机制、刀具和工件的相互作用以及切削力的影响因素等内容。
2. 切削过程的基本概念2.1 切削的定义切削是指通过刀具对工件进行切削行为,将工件的某部分削除或形成所需形状的加工过程。
2.2 切削的分类根据切削速度和切削温度的不同,切削可以分为常规切削和高速切削两种。
常规切削适用于低切削速度和温度的条件下,而高速切削则适用于高速和高温的情况。
2.3 切削力的定义切削力是指刀具在切削过程中对工件施加的力,通常包括主切削力、侧切削力和切削力矩等。
3. 切削力的产生机制切削力的产生是由刀具与工件之间的相互作用所引起的。
在切削过程中,刀具对工件施加的切削力可以分解为切削力和切削阻力两个方向。
4. 刀具和工件的相互作用刀具和工件之间的相互作用对切削过程的效果具有重要影响。
刀具的选择应根据工件的材料和几何形状来确定,不同的刀具结构和刀具材料将产生不同的切削效果。
5. 切削力的影响因素切削力的大小受多种因素的影响,包括刀具、切削条件、工件材料和几何形状等。
了解这些影响因素将有助于优化切削过程,提高加工效率和质量。
5.1 刀具的影响因素•刀具材料和硬度•刀具尺寸和几何形状•刀具刃口的磨损情况5.2 切削条件的影响因素•切削速度•进给量•切削深度5.3 工件材料的影响因素•材料的硬度和强度•材料的塑性和韧性5.4 工件几何形状的影响因素•工件的形状复杂程度•工件表面的光滑度6. 切削过程的优化与发展趋势为了提高切削过程的效率和质量,不断进行切削过程的优化是非常重要的。
随着技术的发展,一些新的切削方法和工具逐渐被引入,例如高速切削、超硬刀具和涂层刀具等。
结论金属切削原理是金属加工的核心内容之一,通过对切削过程的研究和了解,可以有效提高切削过程的效率和质量。
切削过程涉及多个因素,包括刀具和工件的相互作用、切削力的产生机制以及切削力的影响因素等。