刀具的基本原理及概述
机械加工刀具工作原理

机械加工刀具工作原理机械加工刀具是用于进行各种金属材料切削、车削、钻孔、铣削等工序的工具。
在机械加工过程中,刀具起着至关重要的作用。
了解机械加工刀具的工作原理,对于提高加工效率和质量具有重要意义。
1. 切削原理机械加工刀具的基本原理是通过切削材料来实现加工目的。
刀具切削时,其刃口与工件接触并对工件进行剪切,将工件上的材料切割下来,从而使工件形状或尺寸发生变化。
切削过程主要涉及到力的施加和刃口形状的设计。
2. 切削力切削力是刀具在切削过程中作用于工件的力。
切削力大小直接影响加工负荷和刀具的耐用性。
切削力分为主切削力和辅助切削力。
主切削力是指沿着刀具运动轴向的切削力,决定刀具在切削过程中的切削能力。
辅助切削力是指与主切削方向垂直的力,如横切力和进给力等。
3. 刀具材料机械加工刀具使用的材料通常需具有较高的硬度、强度和耐磨性。
常见的刀具材料包括高速钢、硬质合金、陶瓷、多晶体立方氮化硼等。
不同的切削材料要求选择不同的刀具材料,以满足不同的加工需求。
4. 刃口形状刃口是机械加工刀具上起切削作用的部分,其形状对切削性能有着重要影响。
常见的刃口形状有直刃、斜刃、弯刃等。
直刃广泛应用于车削、钻孔等工序,而斜刃适用于铣削等切槽工序。
刃口的选择应根据具体加工要求和工件材料进行合理匹配。
5. 切削液切削液是机械加工过程中不可或缺的辅助工具。
它可以降低切削温度、减少摩擦、延长刀具寿命,并改善加工表面质量。
常见的切削液包括切削油、切削液剂和切削油乳液等。
选择合适的切削液要考虑刀具材料、工艺要求和环境要素。
6. 刀具磨损与修复由于长时间使用和切削过程中的摩擦作用,刀具会逐渐磨损。
刀具磨损会导致切削力增大、加工精度下降和加工表面粗糙等问题。
因此,及时检查和修复刀具磨损是保证加工质量和刀具寿命的关键。
常见的刀具修复方法包括研磨、镀覆等。
7. 刀具选择和应用不同的加工任务需要选择合适的刀具类型和规格。
刀具的选择应该综合考虑工件材料、切削模式、切削参数和加工要求等因素。
刀的切割工作原理

刀的切割工作原理刀的切割工作原理是利用刀刃的锋利边缘对物体施加压力和剪切力,实现将物体分割为两个或更多部分的过程。
刀具是用来切割的工具,广泛应用于工业制造、家庭生活以及医学和手术等领域。
刀刃的锋利边缘是刀具切削的关键部分。
刀刃通常由高硬度、高耐磨的材料制成,如高速钢、碳化硅、氧化锆等。
这些材料具有优异的硬度和切削性能,能够有效地切割各种物体。
刀的切割原理包括割裂、剪切和挤压等过程。
割裂是指刀刃对物体的冲击和切削,通过割断物体内部的连接结构来实现切割。
剪切是指刀刃在物体表面施加剪切力,使物体沿切割线产生滑动分离。
挤压是指刀刃在物体上施加压力,将物体挤压变形而实现切割。
刀具的切削形式包括拉切、压切和剪切等。
拉切是指刀具在物体上施加拉力,使物体发生断裂分离。
压切是指刀具在物体上施加压力,将物体连续压迫扭曲分离。
剪切是指刀具的两侧同时对物体施加反向的剪切力,使物体沿切割线产生剪切断裂。
刀的切割过程中,刀刃与物体之间需要克服切割阻力。
切割阻力包括摩擦阻力、变形阻力和黏附阻力等。
摩擦阻力是刀刃在物体表面与物体之间的阻力,与物体表面的粗糙度、润滑条件和刀具的材质有关。
变形阻力是指物体的可塑性造成的阻力,切割时需要克服物体的变形能力。
黏附阻力是指物体表面的粘附力,使刀刃在切割过程中容易粘附在物体表面。
刀的切割性能与刀具的几何形状、角度和刀刃的刃口质量有关。
切割性能主要包括切割力、切削速度和切割效率等。
切割力是指刀具对物体施加的力和压力,是刀具切削性能的重要指标。
切削速度是指刀具在单位时间内切削物体的长度,是切削效率的影响因素之一。
切割效率是指刀具单位时间内切削物体的能力,高效率的切割可以提高工作效率和生产能力。
在刀的切割过程中,还需要考虑一些因素,如切削液的使用和切削温度的控制。
切削液可以降低切削阻力,冷却刀具和物体,减少摩擦和热量的产生,提高切削质量和刀具寿命。
切削温度的控制可以避免物体过热和变形,保证切割质量和生产效率。
加工中心刀具工作原理详解
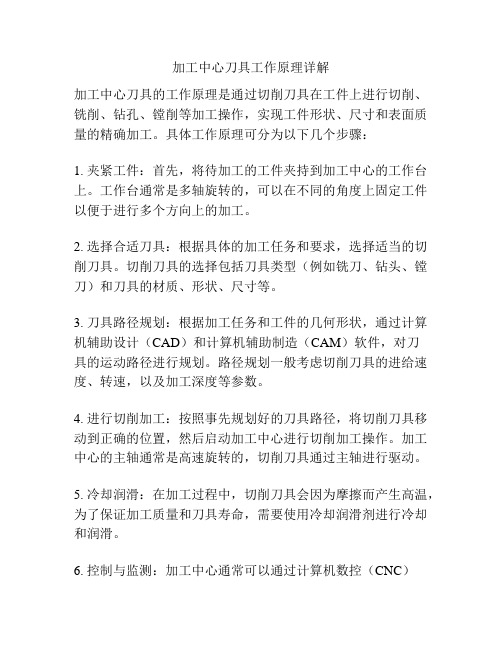
加工中心刀具工作原理详解
加工中心刀具的工作原理是通过切削刀具在工件上进行切削、铣削、钻孔、镗削等加工操作,实现工件形状、尺寸和表面质量的精确加工。
具体工作原理可分为以下几个步骤:
1. 夹紧工件:首先,将待加工的工件夹持到加工中心的工作台上。
工作台通常是多轴旋转的,可以在不同的角度上固定工件以便于进行多个方向上的加工。
2. 选择合适刀具:根据具体的加工任务和要求,选择适当的切削刀具。
切削刀具的选择包括刀具类型(例如铣刀、钻头、镗刀)和刀具的材质、形状、尺寸等。
3. 刀具路径规划:根据加工任务和工件的几何形状,通过计算机辅助设计(CAD)和计算机辅助制造(CAM)软件,对刀
具的运动路径进行规划。
路径规划一般考虑切削刀具的进给速度、转速,以及加工深度等参数。
4. 进行切削加工:按照事先规划好的刀具路径,将切削刀具移动到正确的位置,然后启动加工中心进行切削加工操作。
加工中心的主轴通常是高速旋转的,切削刀具通过主轴进行驱动。
5. 冷却润滑:在加工过程中,切削刀具会因为摩擦而产生高温,为了保证加工质量和刀具寿命,需要使用冷却润滑剂进行冷却和润滑。
6. 控制与监测:加工中心通常可以通过计算机数控(CNC)
系统进行精确控制。
CNC系统可以控制刀具的运动路径、进给速度、切削力等参数,以及对加工过程实时监测和检测,如工件尺寸、表面粗糙度等。
通过以上步骤,加工中心刀具可以对工件进行精确高效的加工操作。
加工过程中,刀具的切削、铣削、钻孔等操作可根据具体的工件需求进行不同的组合,实现各种复杂的形状和结构的加工。
金属切削原理与刀具的基本概述
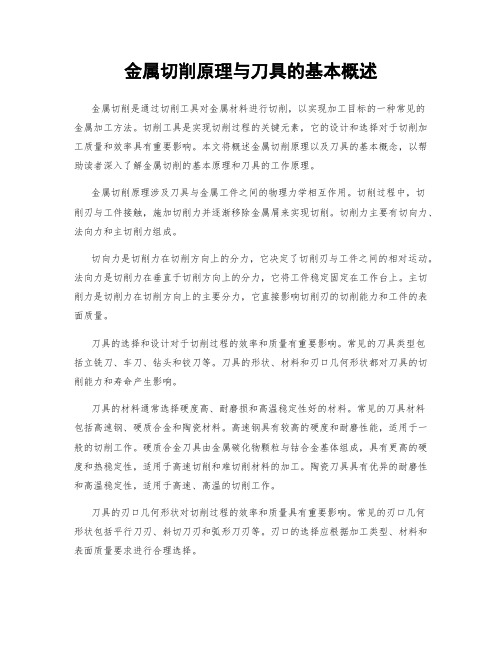
金属切削原理与刀具的基本概述金属切削是通过切削工具对金属材料进行切削,以实现加工目标的一种常见的金属加工方法。
切削工具是实现切削过程的关键元素,它的设计和选择对于切削加工质量和效率具有重要影响。
本文将概述金属切削原理以及刀具的基本概念,以帮助读者深入了解金属切削的基本原理和刀具的工作原理。
金属切削原理涉及刀具与金属工件之间的物理力学相互作用。
切削过程中,切削刃与工件接触,施加切削力并逐渐移除金属屑来实现切削。
切削力主要有切向力、法向力和主切削力组成。
切向力是切削力在切削方向上的分力,它决定了切削刃与工件之间的相对运动。
法向力是切削力在垂直于切削方向上的分力,它将工件稳定固定在工作台上。
主切削力是切削力在切削方向上的主要分力,它直接影响切削刃的切削能力和工件的表面质量。
刀具的选择和设计对于切削过程的效率和质量有重要影响。
常见的刀具类型包括立铣刀、车刀、钻头和铰刀等。
刀具的形状、材料和刃口几何形状都对刀具的切削能力和寿命产生影响。
刀具的材料通常选择硬度高、耐磨损和高温稳定性好的材料。
常见的刀具材料包括高速钢、硬质合金和陶瓷材料。
高速钢具有较高的硬度和耐磨性能,适用于一般的切削工作。
硬质合金刀具由金属碳化物颗粒与钴合金基体组成,具有更高的硬度和热稳定性,适用于高速切削和难切削材料的加工。
陶瓷刀具具有优异的耐磨性和高温稳定性,适用于高速、高温的切削工作。
刀具的刃口几何形状对切削过程的效率和质量具有重要影响。
常见的刃口几何形状包括平行刀刃、斜切刀刃和弧形刀刃等。
刃口的选择应根据加工类型、材料和表面质量要求进行合理选择。
此外,切削参数的选择也是确保切削过程顺利进行的关键因素。
切削参数包括切削速度、进给速度和切削深度等。
切削速度决定了刀具与工件之间的相对运动速度,进给速度则决定了切削刃每分钟移除的金属量,切削深度是切削刃切入工件的深度。
在切削过程中,润滑和冷却也是必不可少的。
刀具和工件之间的摩擦和热量会导致刀具磨损和工件热变形。
速锋刀设备的基本原理-概述说明以及解释
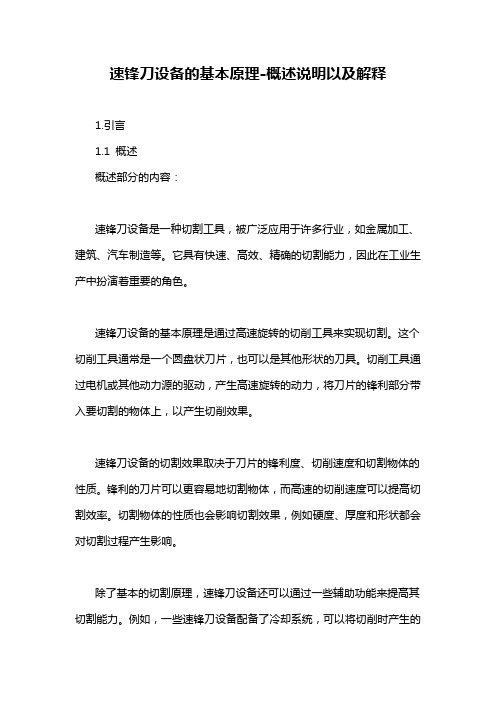
速锋刀设备的基本原理-概述说明以及解释1.引言1.1 概述概述部分的内容:速锋刀设备是一种切割工具,被广泛应用于许多行业,如金属加工、建筑、汽车制造等。
它具有快速、高效、精确的切割能力,因此在工业生产中扮演着重要的角色。
速锋刀设备的基本原理是通过高速旋转的切削工具来实现切割。
这个切削工具通常是一个圆盘状刀片,也可以是其他形状的刀具。
切削工具通过电机或其他动力源的驱动,产生高速旋转的动力,将刀片的锋利部分带入要切割的物体上,以产生切削效果。
速锋刀设备的切割效果取决于刀片的锋利度、切削速度和切割物体的性质。
锋利的刀片可以更容易地切割物体,而高速的切削速度可以提高切割效率。
切割物体的性质也会影响切割效果,例如硬度、厚度和形状都会对切割过程产生影响。
除了基本的切割原理,速锋刀设备还可以通过一些辅助功能来提高其切割能力。
例如,一些速锋刀设备配备了冷却系统,可以将切削时产生的热量迅速散发,以避免物体受到热损伤。
另外,一些设备还带有吸尘装置,可以及时清理切削产生的碎片,保持工作区域的清洁。
总之,速锋刀设备是一种高效、精确的切割工具,通过旋转的切削工具实现切割效果。
它在各个行业中都扮演着重要的角色,并且通过辅助功能不断完善和提高其切割能力。
在未来,随着科技的不断发展,速锋刀设备的性能和功能还将得到进一步的提升,为人们的生产生活带来更多便利和效益。
1.2 文章结构文章结构的设计是为了将信息有条理地呈现给读者,使读者能够清晰地理解和掌握文章的内容。
本文的文章结构主要包括引言、正文和结论三个部分。
引言部分旨在引领读者进入主题,概述文章的内容、目的和涉及的范围。
通过简要介绍速锋刀设备的基本原理,提出本文的目的和重要性,为读者打开认识和理解速锋刀设备的大门。
正文是文章的主体部分,包含了详细的速锋刀设备的基本原理的讲解和论述。
要点1将详细介绍速锋刀设备的基本原理中的重要概念、原理和关键技术,将逐步展开,以帮助读者逐步理解速锋刀设备的工作原理。
刀的切割工作原理

刀的切割工作原理
刀的切割工作原理是利用刀的锋利边缘对物体进行分割。
刀具通常由坚硬材料制成,如钢、陶瓷或碳纤维复合材料,以确保切割时能保持锋利。
切割过程中,刀的锋利边缘与物体表面接触,并施加一定的压力。
当物体的抗剪强度小于刀的压力时,刀具就能够将物体分割为两个或多个部分。
根据切割目标的不同,刀具可以有不同的形状和结构。
常用的刀形包括直刀、弯刀、锯齿刀等。
刀的锋利边缘可以是平整的直线,也可以是曲线或锯齿状,以适应不同的切割需求。
切割过程中,刀具的运动方式也会影响切割效果。
手动切割时,操作者会通过手腕和手臂的运动来施加力度和方向。
自动切割时,刀具通常由机械装置或电动机驱动,以保证更稳定和精准的切割。
除了刀具的形状和运动方式,切割的材料性质也会影响切割效果。
柔软材料如纸张、布料可以通过较小的力度和较少的刃数实现切割。
而硬质材料如金属、石材则需要更大的力度和更多的刃数来完成切割。
综上所述,刀的切割工作原理是利用刀的锋利边缘施加压力,将物体分割为两个或多个部分。
切割效果受刀具形状、运动方式和切割材料性质等因素的影响。
成型刀的原理

成型刀的原理成型刀是一种常见的用来切割和加工材料的工具,它的原理是通过刀具与工件之间的相对运动,使切削刃对工件施加作用力,并切削掉工件上的材料,从而实现切削和加工的目的。
以下是对成型刀原理的详细介绍。
1.成型刀的分类在了解成型刀的原理之前,首先需要了解成型刀的分类。
按照使用方式和原理,成型刀可以分为手工刀具、机械刀具和电动刀具等。
其中,手工刀具主要通过人力来驱动刀具进行切削,机械刀具则需要配合机械设备来驱动。
电动刀具则是通过电力驱动,具有高效、方便的特点。
2.切削原理成型刀的切削原理基于科学力学和材料力学的基本原理。
当切削刃与工件接触时,使切削刃对工件施加一定的作用力。
通过施加作用力,切削刃对工件的剪切力和切削力产生作用,从而切削掉工件上的材料。
切削过程涉及到速度、力量和热量等因素。
一般来说,切削速度的选择取决于材料的种类和硬度。
同时,切削速度和进给速度的选择也是为了避免热量的积聚,以保证工件不会受到过热的影响。
3.切削角度切削角度也是影响成型刀切削性能的重要因素之一。
常见的切削角度包括切刃角、前角和侧角等。
切刃角是指切削刃与工件接触的切线和切削方向之间的夹角,它的主要作用是分割切削,减小切削阻力和磨损。
前角和侧角是刀具与工件接触时,刀具的切削地面和垂直于切削方向面的夹角,它们的大小对切削力和切削表面的光滑度有明显的影响。
4.刀具材料与涂层刀具材料的选择也是影响成型刀性能的重要因素之一。
常见的刀具材料包括高速钢、硬合金和陶瓷等。
不同的材料具有不同的硬度和耐磨性能,可以适应不同材料的切削加工需求。
此外,一些刀具还会通过涂层来提高其性能。
常见的涂层材料包括氮化物、碳氮化物和钛铝氮等,它们能够提高刀具的硬度和耐磨性,延长刀具的使用寿命。
5.成型刀的运动方式成型刀的运动方式也是影响切削效果的重要因素之一。
成型刀的运动方式可以分为直线运动和循环性运动。
在直线运动中,成型刀通过直线运动来切削工件,这种方式适用于一些简单的加工任务。
刀具切削的工作原理

刀具切削的工作原理刀具切削是现代工业中常见的加工方式之一,它广泛应用于各个行业,如机械制造、汽车制造、航空航天等等。
本文将详细介绍刀具切削的工作原理,并分点列出其重要的方面。
一、切削工具与刀具材料1. 切削工具:包括刀具刀片、钻头、铣刀等。
它们的形状、尺寸和材料的选择直接影响到切削加工的效果。
2. 刀具材料:常见的刀具材料包括硬质合金、高速钢、陶瓷等。
不同材料具有不同的硬度、韧性和耐磨性,能够应对不同材料的切削需求。
二、切削原理1. 花削原理:切削刀具在工件上作圆周运动,通过将切屑削掉的方式实现切削。
适用于外圆、内圆等工件的加工。
2. 铣削原理:切削刀具以较高速度旋转,通过将工件上一层或多层金属削下来的方式实现切削。
适用于直线、曲线等多种形状的加工。
3. 钻削原理:切削刀具以旋转的方式进入工件内部,通过刮削或削下的方式实现切削。
适用于孔加工。
4. 切下原理:切削刀具削下工件上的金属,如钻孔、车削等。
适用于各种形状的加工。
三、切削过程的物理现象1. 切削力:切削过程中,切削刀具对工件施加一定的力。
切削力的大小和方向会影响切削刀具和工件的磨损、加工精度等。
切削力分为切削力和切向力两个方向。
2. 切削热:切削过程中,由于切削力和摩擦力的作用,会产生大量的热量。
高温会导致刀具变软、变形,也会对工件表面造成损伤。
因此,切削过程需要保持适当的冷却和润滑。
3. 切削震动:切削过程中,由于刀具和工件的摩擦以及其它因素,会产生切削震动。
切削震动会导致切削失准、加工表面质量差等问题。
因此,需要采取措施来减小切削震动。
四、切削参数的选择1. 切削速度:切削速度是指切削刀具和工件之间的相对速度。
选择合适的切削速度可以提高生产效率,同时也要考虑刀具材料的耐磨性。
2. 进给量:进给量是指刀具单位时间内移动的距离。
合理的进给量能够控制加工负荷和加工精度。
3. 切削深度:切削深度是指刀具在一次切削过程中进入工件的深度。
切削深度的选择与切削力、切削热等因素密切相关。
刀具工作原理

刀具工作原理
对于不同地层的开挖,盾构的刀具采用不同型式:开挖地层为硬岩时,采用盘形滚刀;地层为较软岩石时,采用齿刀;地层为软土或破碎软岩时,可采用切刀(或刮刀)。
不同类型刀具的工作原理如下:
滚刀工作原理
安装在刀盘上的盘形滚刀在盾构千斤顶的作用下紧压在岩面上,随着刀盘的旋转,盘形滚刀一方面绕刀盘中心轴公转,同时绕自身轴线自转。
盘形滚刀在刀盘的推力、扭矩作用下,在掌子面上切出一系列的同心圆。
当推力超过岩石的强度时,盘形滚刀刀尖下的岩石直接破碎,刀尖贯入岩石,掌子面上岩石被盘形滚刀挤压碎裂而形成多道同心圆沟槽。
随着刀具寿命沟槽深度的增加,岩体表面裂纹加深扩大,当刀具压力超过岩石的剪切和拉伸强度时,相邻同心圆沟槽间的岩石成片崩落,完成盘形滚刀的破岩过程。
齿刀工作原理
在岩石较软的情况下掘进时,如果盘形滚刀与岩石掌子面之间不能产生一定的附着力,使滚刀产生滚动,滚刀将会产生弦磨。
滚刀不能滚动,将失去有效的破岩功能,此时在较软的岩层中可以采用齿刀进行破岩,齿刀安装方式同滚刀。
由于齿刀上装有二个切削刃,因此刀盘正反转时齿刀都能进行破岩。
切刀(刮刀)工作原理
在软土地层或滚刀破碎后的渣土通过切刀(刮刀)进行开挖,渣土随切刀(刮刀)正面进入渣槽,因此切刀(刮刀)既具有切削的功能也具有装载的功能。
切削原理与刀具
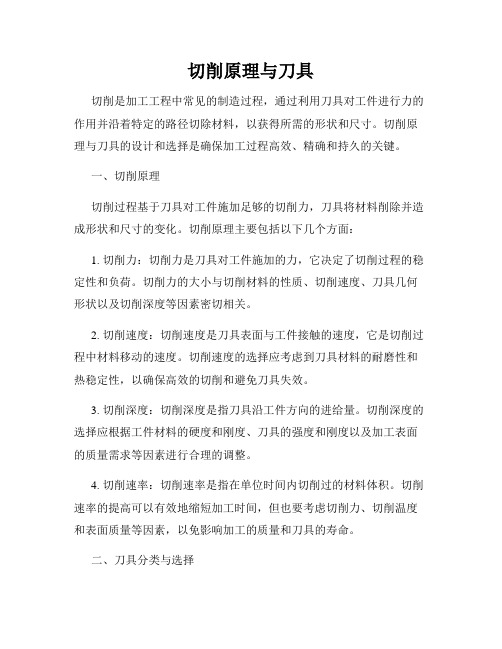
切削原理与刀具切削是加工工程中常见的制造过程,通过利用刀具对工件进行力的作用并沿着特定的路径切除材料,以获得所需的形状和尺寸。
切削原理与刀具的设计和选择是确保加工过程高效、精确和持久的关键。
一、切削原理切削过程基于刀具对工件施加足够的切削力,刀具将材料削除并造成形状和尺寸的变化。
切削原理主要包括以下几个方面:1. 切削力:切削力是刀具对工件施加的力,它决定了切削过程的稳定性和负荷。
切削力的大小与切削材料的性质、切削速度、刀具几何形状以及切削深度等因素密切相关。
2. 切削速度:切削速度是刀具表面与工件接触的速度,它是切削过程中材料移动的速度。
切削速度的选择应考虑到刀具材料的耐磨性和热稳定性,以确保高效的切削和避免刀具失效。
3. 切削深度:切削深度是指刀具沿工件方向的进给量。
切削深度的选择应根据工件材料的硬度和刚度、刀具的强度和刚度以及加工表面的质量需求等因素进行合理的调整。
4. 切削速率:切削速率是指在单位时间内切削过的材料体积。
切削速率的提高可以有效地缩短加工时间,但也要考虑切削力、切削温度和表面质量等因素,以免影响加工的质量和刀具的寿命。
二、刀具分类与选择刀具作为切削加工中最重要的工具之一,其设计和选择的合理性对加工过程的成败起着决定性作用。
根据切削原理和要加工的材料,刀具可分为以下几类:1. 钨钢刀具:钨钢刀具由高速钢和钨合金组成,广泛应用于加工常见金属材料,如铁、铝、铜等。
其优点是硬度高、耐磨性好,适用于高速切削。
2. 硬质合金刀具:硬质合金刀具以钨钢为基材,通过添加碳化钨和钴等粉末,经过高温烧结制成。
它的耐磨性和耐高温性能优异,适用于切削高硬度金属和复杂形状的工件。
3. PCD刀具:PCD刀具采用多晶立方体碳化硅材料制成,具有高硬度、低摩擦系数和良好的导热性能。
适用于加工铝合金、铜合金和非金属材料等。
4. CBN刀具:CBN刀具是由立方氮化硼制成,具有极高的硬度和热稳定性,特别适用于切削高硬度材料如工具钢和高速度刚性合金。
刀具的切割原理是什么

刀具的切割原理是什么刀具的切割原理是将刀具与被切割物之间的相对运动转化为对被切割物进行切割的力。
刀具通常是由金属或其他硬材料制成的,它们具有尖利的边缘或刃口,能够快速切割各种物体。
切割是刀具应用的一种常见操作,它涉及到材料的剪切、破裂或磨削等物理过程。
切割的原理可以分成以下几个方面:1. 剪切原理:剪切是刀具切割的基本原理之一。
当刀具施加足够大的剪切力时,会使材料产生剪切变形,切割物体。
切割刀与物体表面产生接触,刀具边缘施加剪切力,使材料沿着切口方向发生剪切变形,使材料分离。
这种剪切过程可以用剪切力和切口形状来描述。
2. 破裂原理:某些切割工艺主要通过切割物体内部结构或化学键的破裂来进行切割。
例如,激光切割利用激光束的高能量使材料内的化学键发生断裂,达到切割效果。
这种原理常用于高硬度、高强度和易损坏的材料切割。
3. 磨削原理:磨削是通过粒子、颗粒或刷毛等硬度较高的材料与被切割物体表面之间的相对运动,将被切割物体的表面层剥离或磨除,达到切割的目的。
磨削刀具一般由磨料颗粒和粘结剂组成。
在切削过程中,磨料颗粒与被切割物体表面摩擦磨削,附着在刀具上的磨粒不断更新,使刀具保持锐利。
4. 推切原理:推切是切割工艺中常用的一种原理。
它通过在被切割物体上施加持续的压力,使刀具边缘沿着切割线或切割面推动切割物体。
通过推切力提供的动能,从而使切割物体发生位移和剪切,实现切割效果。
推切常用于木材、纸张、塑料等易于应变的材料。
刀具的切割原理不仅涉及到物理力学和材料科学,还需要考虑材料本身的特性和工具的设计。
刀具的尖锐度、硬度和几何形状等都会影响切割的效果。
此外,切割的速度、角度和压力等参数也对切割的精度和效率有着重要影响。
总之,刀具的切割原理是将刀具与被切割物之间的相对运动转化为切割物体的力。
剪切、破裂、磨削和推切等原理是常见的切割方法,不同的切割原理适用于不同的材料和状况。
通过理解切割原理,可以选择合适的切割工艺和刀具,实现高效、精确的切割操作。
金属切削原理与刀具

金属切削原理与刀具
金属切削原理与刀具:
一、金属切削原理
1. 切削力学:切削力定义为金属切削过程中由刀具与工件之间产生的
相互作用力,根据其本质不同可分为动切削力、静切削力和剪切力。
2. 切削热:金属切削过程发生了热量交换,热量大部分是从刀具释放
到工件上,少量热量是从环境里侧移到刀具或者从工件侧移到刀具,
这个过程称为切削热。
3. 切削噪声:切削时由工件与刀具磨擦、刀具与被切物断裂等发出的
噪声,又称切削噪声,是金属切削的重要的污染源之一。
二、金属切削刀具
1. 铣刀:铣刀是一种坚硬的刀具,用于进行几何体表面的金属切削。
它由刀片、刀头、刀杆组成,可根据刀的形状及功能分类为直角铣刀、圆角铣刀、角铣刀、平铣刀等。
2. 内丝锥:内丝锥是用来进行内孔加工的刀具,其分类主要有逆槽内
丝锥和普通内丝锥两种。
它们的工作原理是通过在回转时刮刀后,将
产生的碎屑转到内部进行切削,从而实现内丝的加工。
3. 铰刀:铰刀是一种特殊的铣刀,用于执行开铰、圆弧削、下铰和虚
边倒铰等加工。
它包括刀体和刀杆两个部分,刀体由刀片和刀杆组成,刀杆可以向任意一个方向旋转以达到改变切削角度的目的。
4. 牙铰刀:牙铰刀是切削螺纹的特殊刀具,其外形比普通铰刀大,假牙形状有利于防止刀具与螺纹滑动,即牙铰刀具有牙齿状的刀具,利用微调牙齿的方法调节刀具的切削角度,从而形成不同形状的螺纹。
刀具的切割原理是什么

刀具的切割原理是什么一、切削力学切削力学是研究刀具切削过程中作用力和材料之间相互作用的学科。
在切削过程中,刀具通过对工件施加切削力以剪切和剥离工件材料,实现加工的效果。
切削力学主要包括力的产生和传递、切削机理以及切削力的计算等内容。
1.力的产生和传递:在切削过程中,切削力由刀具与工件间的接触引起。
切削力的产生主要源于以下两个方面:一是由于切削载荷引起的切削力,如轴向力、径向力和切削力;二是由于毛坯加工引起的工件反力,如副边力和径向力。
切削力的传递主要是通过机床主轴系统以及切削液的力学特性等途径作用于刀具。
2.切削机理:切削机理指的是切削力在切削区域内的作用机理。
切削过程中,切削刀具顶角和刃部与工件之间的接触形成了切削区域。
在该区域内,切削力通过摩擦力和剪切力对工件材料进行变形。
切削力的作用导致工件材料发生塑性变形和应力集中,最终使切屑形成并从工件上脱离。
3.切削力的计算:切削力的计算是切削力学中的一个重要问题。
切削力的计算不仅可以帮助工程师合理选择刀具、机床和切削参数,还能评估切削过程中刀具和工件材料的损耗情况。
切削力的计算方法通常包括解析法、实验法和数值模拟法等。
二、刀具材料刀具材料的选择与切削原理密切相关。
刀具的切削原理决定了切削过程中对刀具材料的要求,如强度、硬度、耐磨性等。
下面是一些常用的刀具材料及其特点:1.高速钢(HSS):高速钢是一种常用的刀具材料,具有较高的硬度和耐磨性。
它可以在高速切削下长时间保持刀具的切削性能,适用于中等磨削和一般加工。
2.硬质合金:硬质合金刀具由高硬度的钨钢颗粒和金属结合相组成。
硬质合金具有极高的硬度和强度,耐磨性好,适用于高速切削、重切削条件下的加工。
3.陶瓷刀具:陶瓷刀具具有良好的高温硬度和耐磨性,适用于高温切削和非金属材料的加工。
但由于其易脆性,陶瓷刀具主要用于切削非常硬的材料,如铸钛合金等。
4.刃片合金:刃片合金主要由具有高硬度和灵活性的金属粉末与粘结剂制成。
加工数控刀具的工作原理
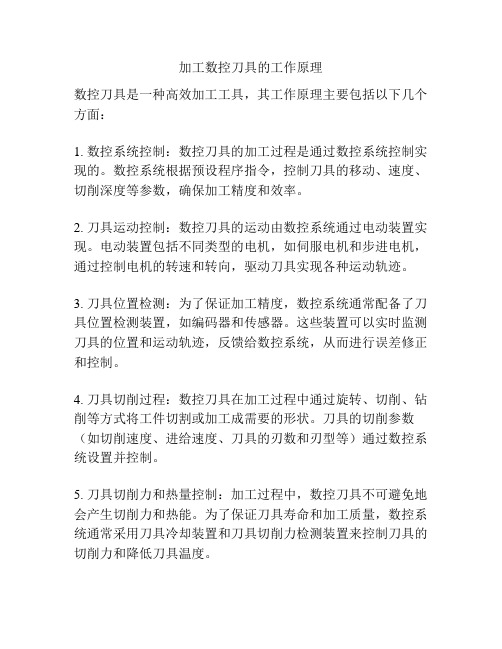
加工数控刀具的工作原理
数控刀具是一种高效加工工具,其工作原理主要包括以下几个方面:
1. 数控系统控制:数控刀具的加工过程是通过数控系统控制实现的。
数控系统根据预设程序指令,控制刀具的移动、速度、切削深度等参数,确保加工精度和效率。
2. 刀具运动控制:数控刀具的运动由数控系统通过电动装置实现。
电动装置包括不同类型的电机,如伺服电机和步进电机,通过控制电机的转速和转向,驱动刀具实现各种运动轨迹。
3. 刀具位置检测:为了保证加工精度,数控系统通常配备了刀具位置检测装置,如编码器和传感器。
这些装置可以实时监测刀具的位置和运动轨迹,反馈给数控系统,从而进行误差修正和控制。
4. 刀具切削过程:数控刀具在加工过程中通过旋转、切削、钻削等方式将工件切割或加工成需要的形状。
刀具的切削参数(如切削速度、进给速度、刀具的刃数和刃型等)通过数控系统设置并控制。
5. 刀具切削力和热量控制:加工过程中,数控刀具不可避免地会产生切削力和热能。
为了保证刀具寿命和加工质量,数控系统通常采用刀具冷却装置和刀具切削力检测装置来控制刀具的切削力和降低刀具温度。
通过以上的工作原理,数控刀具可以实现高精度、高效率的加工操作,并且适用于各种材料和形状的加工需求。
刀具的工作原理及应用
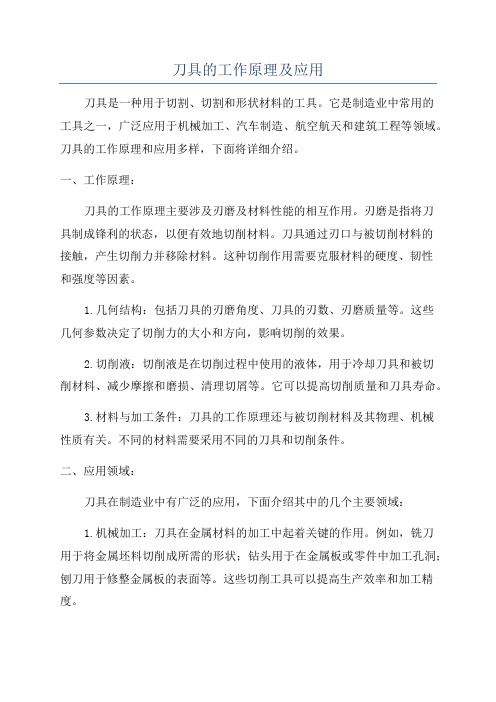
刀具的工作原理及应用刀具是一种用于切割、切割和形状材料的工具。
它是制造业中常用的工具之一,广泛应用于机械加工、汽车制造、航空航天和建筑工程等领域。
刀具的工作原理和应用多样,下面将详细介绍。
一、工作原理:刀具的工作原理主要涉及刃磨及材料性能的相互作用。
刃磨是指将刀具制成锋利的状态,以便有效地切削材料。
刀具通过刃口与被切削材料的接触,产生切削力并移除材料。
这种切削作用需要克服材料的硬度、韧性和强度等因素。
1.几何结构:包括刀具的刃磨角度、刀具的刃数、刃磨质量等。
这些几何参数决定了切削力的大小和方向,影响切削的效果。
2.切削液:切削液是在切削过程中使用的液体,用于冷却刀具和被切削材料、减少摩擦和磨损、清理切屑等。
它可以提高切削质量和刀具寿命。
3.材料与加工条件:刀具的工作原理还与被切削材料及其物理、机械性质有关。
不同的材料需要采用不同的刀具和切削条件。
二、应用领域:刀具在制造业中有广泛的应用,下面介绍其中的几个主要领域:1.机械加工:刀具在金属材料的加工中起着关键的作用。
例如,铣刀用于将金属坯料切削成所需的形状;钻头用于在金属板或零件中加工孔洞;刨刀用于修整金属板的表面等。
这些切削工具可以提高生产效率和加工精度。
2.汽车制造:刀具在汽车制造行业中也起着重要作用。
例如,车削刀用于车削曲线面、外圆和内孔等;切削刀用于削除铸造件上的余料;车刀用于车削汽车座椅和车身等部件等。
刀具的使用可以提高汽车零部件的生产效率和质量。
3.航空航天:航空航天领域对刀具的要求非常高,因为它们需要加工坚固而耐高温、抗腐蚀的特殊材料。
例如,铣刀和钻头用于将航空发动机的零部件加工成所需的形状和尺寸;刀片用于削除航空零部件上的余料;钻头用于加工飞机结构的孔洞等。
刀具的应用可以提高航空航天产品的性能和安全性。
4.建筑工程:刀具在建筑工程中也有许多应用场景。
例如,锤头用于击打和破碎混凝土;切削刀用于切割砖块、瓷砖等材料;切割机用于切割金属板材等。
刀具的自由交换原理

刀具的自由交换原理刀具的自由交换原理是指在机械加工过程中,根据加工需要,可以自由更换刀具,以适应不同的加工任务和工件要求。
通过刀具的自由交换,可以提高生产效率、降低成本、提高产品质量,并实现多种工艺的加工。
刀具的自由交换原理涉及到以下几个方面:1. 刀具座与主轴接口的匹配:刀具座与主轴接口的匹配是实现刀具自由交换的基础。
在机床上,通常会采用标准化的接口,如BT、CAT、ISO等。
这些接口的标准化设计保证了刀具座和主轴之间的互换性,使得不同品牌、不同类型的刀具可以在同一台机床上使用。
2. 刀具形状和尺寸的统一:为了实现刀具的自由交换,需要统一刀具的形状和尺寸。
例如,在铣削加工中,刀具的切削部分通常采用标准化的刀片,如APKT、SEKT等。
这些标准化的刀片具有相同的切削角度和切削几何形状,可以在不同的刀具座上使用。
3. 快速刀具更换装置的设计:为了方便刀具的更换,机床上通常会配备快速刀具更换装置。
这些装置可以通过简单的操作实现刀具的快速更换,提高切换刀具的效率。
常见的快速刀具更换装置包括机械夹紧装置、液压夹紧装置和气动夹紧装置等。
4. 刀具参数的编程设置:在刀具的自由交换过程中,需要将刀具的参数进行编程设置。
这些参数包括刀具的长度、半径、角度等。
通过编程设置刀具的参数,可以实现不同类型刀具的自动切换。
刀具的自由交换原理的应用可以体现在许多机械加工领域,例如铣削、车削和钻削等。
在这些加工过程中,刀具的自由交换可以实现以下几个方面的优势:1. 提高生产效率:通过刀具的自由交换,可以避免因为刀具磨损而停机更换刀具的时间,同时可以避免对生产线进行调整和更改。
这样可以提高机床的利用率和生产效率。
2. 降低成本:通过刀具的自由交换,可以节省更换刀具的时间和人力成本。
因为刀具的自由交换不需要重新调整机床的工艺参数,所以可以减少生产线的停机时间和调整时间,降低生产成本。
3. 提高产品质量:刀具的自由交换可以确保机床按照预定的工艺参数进行加工,避免了由于刀具磨损或不适当的刀具选择而导致的加工问题。
刀柄夹紧刀具的工作原理

刀柄夹紧刀具的工作原理
刀柄夹紧刀具的工作原理:
刀柄夹紧刀具通常采用刀夹锁紧机构来实现刀具与刀柄的紧固。
下面是其工作原理的简要描述:
1. 刀具安装: 首先,将刀具插入刀柄内的刀槽中,确保刀具与
刀柄之间的配合精确。
刀具通常具有锥形或柱形刀柄,以便与刀柄配合。
2. 刀夹锁紧机构: 刀柄夹紧刀具通常配备有刀夹锁紧机构,它
由刀夹和刀夹杆组成。
刀夹固定在刀柄上,可以通过刀夹杆向刀具施加压力。
3. 松开操作: 在刀具更换时,需要先松开刀夹锁紧机构。
通常,刀夹杆上有一个松开按钮或旋钮,操作者通过按下按钮或旋转旋钮来释放刀夹对刀具的紧固力。
4. 夹紧操作: 当刀具正确安装后,操作者可以通过按下刀夹杆
或旋转刀夹杆上的锁紧按钮或旋钮来夹紧刀具。
刀夹将迅速对刀具施加压力,确保刀具与刀柄间的紧固。
5. 紧固力控制: 有些刀夹锁紧机构具有可调节的紧固力设置。
操作者可以根据需要调整刀夹杆上的锁紧按钮或旋钮,以增加或减小刀具与刀柄之间的紧固力。
通过刀夹锁紧机构的工作原理,刀柄夹紧刀具能够确保刀具与
刀柄之间的稳固连接,提供足够的切削力并防止刀具滑动或松脱。
这种机构在机械加工、金属加工等领域中得到广泛应用。
对刀的原理是什么

对刀的原理是什么对刀的原理是通过两个或多个刀片之间的摩擦和相对运动,将物体分割或加工成所需形状。
刀具起到切割、刮削、磨削、刮擦等作用,从而实现对物体的改变。
刀具通常由刀刃和刀柄组成。
刀刃是刀具的关键部分,它负责实际的切割工作。
刀刃的形状和材料选择取决于刀具的使用和要求。
常见的刀刃形状有直刃、曲刃、锯齿刃等。
刀刃的材料则可以是高速钢、硬质合金、陶瓷等。
不同的刀刃形状和材料适用于不同的切割任务和材料。
刀柄是刀具的支撑部分,它连接着刀刃并提供操作的便利性。
刀柄的设计通常考虑到舒适性、抓握力和稳定性等因素。
刀柄可以是直柄、弯柄、圆柱柄等形状,也可以根据使用需求进行定制设计。
刀柄的材料通常是木材、金属、塑料等。
刀具的使用需要考虑诸多因素,例如切割对象的硬度、形状、尺寸等。
不同的切削条件会产生不同的切削力和温度。
因此,刀具的选择和使用应根据具体情况进行合理安排。
在刀具使用中,其切削原理可以总结为以下几点:第一,通过刀刃形状和材料的选择,使刀刃能够尽量降低摩擦阻力,提高切削效率。
刀刃通常具有尖锐的刃口,以减少切削对象与刀刃之间的接触面积,从而降低摩擦力。
此外,刀刃的材料选择要具备优越的硬度和耐磨性,以保持刀刃的锋利度和寿命。
第二,通过控制刀具的相对运动,使刀刃与切削对象发生接触。
切削对象可以是固体、液体或气体。
固体的切削对象通常放置在固定的工作台上,而刀具则由刀柄进行控制。
液体和气体的切削对象则通过流体动力控制和切割。
第三,通过刀刃与切削对象之间的相对运动,进行实际的切割。
常见的相对运动方式有直线运动、旋转运动等。
直线运动适用于对固体物体进行直线或曲线切割。
旋转运动适用于对固体物体进行旋转切割或表面处理。
第四,通过稳定的切削力和速度控制,实现切割过程的稳定性。
切削力和速度的合理配比可以保证切削效果的一致性和品质。
切削力过大会导致物体变形或破坏,切削速度过快则容易产生过热现象。
总结起来,对刀的原理是通过刀刃形状和材料选择,控制切削对象的相对运动,运用切削力和速度控制,实现对物体的切割、加工和改变。
旋切刀原理

旋切刀原理旋切刀,顾名思义,是一种利用旋转刀片进行切割的厨房工具。
它的原理是利用刀片的旋转运动和切割物体的相对运动,从而实现切割食材的目的。
在日常生活中,旋切刀被广泛应用于水果、蔬菜等食材的切割工作,它的使用不仅方便快捷,而且可以保持食材的原汁原味,因此备受厨师和家庭主妇们的青睐。
旋切刀的原理主要包括刀片、刀柄、切割角度和切割速度等方面。
首先,刀片是旋切刀最关键的部件之一,它通常由锋利的不锈钢材料制成,刀片的质量和锋利度直接影响着切割效果。
其次,刀柄是用来固定刀片并提供操作支撑的部件,它的设计合理与否直接关系到使用者的使用体验和安全性。
再者,切割角度是指刀片与被切割物体的夹角,不同的切割角度适用于不同的食材,合理的切割角度可以提高切割效率并减少食材损耗。
最后,切割速度是指使用者手持旋切刀进行切割时的速度,过快或者过慢都会影响切割效果,因此合适的切割速度也是保证切割效果的重要因素。
在使用旋切刀时,首先需要将食材清洗干净并去除不需要的部分,然后将食材放置在切割板上固定好,接着将旋切刀握在手中,用力将刀片贴近食材并进行旋转切割。
在切割过程中,要注意保持稳定的切割角度和适当的切割速度,以免影响切割效果和安全性。
另外,为了保证切割的均匀和美观,还可以适当调整切割角度和刀片的贴合度,以满足不同食材的切割需求。
总的来说,旋切刀作为一种常见的厨房工具,其原理简单而实用。
通过合理的设计和使用,旋切刀可以快速、方便地完成食材的切割工作,为厨师和家庭主妇们提供了极大的便利。
因此,在日常生活中,我们可以根据食材的不同选择合适的切割工具,以达到更好的切割效果和食材利用率。
希望本文对大家了解旋切刀的原理和使用方法有所帮助,谢谢阅读!。
- 1、下载文档前请自行甄别文档内容的完整性,平台不提供额外的编辑、内容补充、找答案等附加服务。
- 2、"仅部分预览"的文档,不可在线预览部分如存在完整性等问题,可反馈申请退款(可完整预览的文档不适用该条件!)。
- 3、如文档侵犯您的权益,请联系客服反馈,我们会尽快为您处理(人工客服工作时间:9:00-18:30)。
刀具的基本原理及常用问题讲解刀具的基本原理及常用问题讲解其实,要讲解切削刀具的基本原理真是一件不容易的事,真正要了解切削原理,必定要从实践开始。
麦董就要求我们要“用好刀”。
其意一:刀具部在选用刀具的时候,必须根据公司实际加工情况,选用适合我们的好用的刀。
一把好的刀,不仅是指刀粒材质硬度的韧性好、切削角度、断屑槽设计精妙等,而最重要的是此刀具能否切削你所需的工件,达到预期的目的,如加工效率、光洁度、精度、刀刃寿命、可靠性、甚至稳定性等…….其意二:必须正确使用刀具。
这就是今晚我们所要讨论的范围。
一、影响刀具切削条件的各项可能性(一)刀具本身的设计:如刀具的材质的耐磨度、坚硬度,还有刀刃的切削角度、刀刃在刀体上支承的稳固度。
(二)刀具与刀柄的配合:刀柄是机械将切削力传到刀具的媒介,如果刀柄设计得不妥,将会大大减低了刀具的威力及寿命;例如,产生震动,刀具中心偏移;刀刃后角刃口支承不足而使刀刃过早崩裂等。
(三)机械本身的刚性:若果机械不能提供一个稳定的切削环境给刀具;例如进刀量不稳定,切削速度不稳定甚至震动等,也会是加工的致命伤。
(四)被加工工件夹紧的方式及稳定性:很多刀具寿命不稳定的主要原因(人为)是工件未有被夹紧在机械之上,引致移位或震动做成超差或刃崩。
(五)切削条件设定错误:由于操作者对切削速度、进刀量不甚了解,错误地设定了切削条件,引致刀具不正常损耗等现象,在我司经常发生。
(六)错误选刀,不考虑切削特性:由于刀具部未能将刀具调度,往往出现用长刀做浅孔浅框的现象。
(七)切削液:在精加工中,切削液的浓度对表面光洁度,精度影响很重要,而且对延长刀刃寿命也有一定的帮助。
(八)其他因素:如工件的特性、进刀方向等也是因素之一。
二、被切削材与切削材被切削材分为 P类――钢材、长削类金属M类――不锈钢、有色金属K类――铸铁、铸钢切削材(硬质合金、Cermet(金属陶瓷)、或陶瓷)也用P 、M、 K分类。
用以切削P 类的可分为P1-P50,通常P40-P50刀片韧性强,但易于被磨损,所以适用于一些不稳定的切削情况下使用,反之P5-P10刀片硬度高,抗磨损能力强,但易于崩脱,所以在切削条件稳定或切削一些较硬材料才会使用。
一般来说P20-P30(P35)的材质最广泛被使用。
其他如M类及K 类原理大致相同除了用切削的长度来区分P、M及K类之特性外,更可用切削力来区分。
铣削的使用功率P=(ap X ae X Vf X Kc) / 60,000,000*ηKc=1700-2500(P类材料)=2000-3200(M类材料)=1000-1500(K类材料)η=机械效率=0.85(一般铣床)ap=切削深度(刀刃)mmae=切削宽度(刀盆)mmVf=进刀速度(每分钟) mm / min在金属切削过程中产生大量的热能,此热量主要来自磨擦阻力及将被切削材的切屑与主体分离所释放的能量,切削刀刃面的温度可达到1000℃,现今使用的切削刀具通常会使80%热量由切屑带走,以免影响刀刃及工件。
传统刀具因切削速度不高及普遍使用切削液,所以热量不是一个重要问题,但在高效能切削时,最好不要采用少量切削液,因切削液在刀刃很快蒸发,不但达不到预期效果,反而使刀刃因热度不均而崩裂。
所以通常粗加工是不用切削液而精加工或钻孔时才用大量切削液以提高精度及增加刀刃寿命。
三、材料与刀具在模具所使用的钢材之中,切削性能最好的可以算是#45 中碳钢 ; 其次是2312 。
合金元素在材料中,对切削性能起了很大的影响,例如硫是杂质,但硫的存在帮助切削。
铬是抗锈蚀的主要元素,但铬会使切削困难,易使切屑粘在刀刃之上,形成切削瘤;所以2316,2083,S136H等钢是不利于切削。
★★选用一些刀刃锋利的刀具(大正前角);但钢材本身的硬度也对切削有很大影响,NAK80有HRC38-40度,718H也有差不多HRC40的硬度,对高速钢及锋钢刀具来说,切削是非常困难的。
★★尽量选用自身硬度较高的刀具(如圆刀加工王牌选用SM30材质的刀粒,加工硬料选用4030材质的刀粒);一些钢材,不是用锯切开,而是用火焰切割的,所以有切边不平而且硬化的现象,增加加工难度。
★★选用一些切削刃可抵受冲击力或刀刃韧性较强的刀具(负前角)四、刀刃磨损切削过程中刀具在切除工件上的金属层,同时工件与切屑也对刀具起作用,使刀具磨损。
刀具严重磨损,会缩短刀具使用时间,恶化加工表面质量,增加刀具材料损耗。
因此,刀具磨损是影响生产效率、加工质量和成本的一个重要因素。
(一)刀具磨损的分类刀具磨损分为正常磨损和非正常磨损两大类:1、正常磨损正常磨损是指在刀具设计与使用合理,制造与刃磨质量符合要求的情况下,刀具在切削过程中逐渐产生的磨损。
正常磨损主要包括下述三种形式。
(1)后刀面磨损在与切削刃连接的后刀面上,磨出长度为b、后角等于或小于零的棱面。
根据棱面上各部位磨损特点,可分为三个区域,如图1所示:C 区在近刀尖处是磨损较大的区域,这是由于温度高、散热差而造成的。
其磨损量用高度VC表示。
N 区近待加工表面,约占全长1/4的区域。
在它的边界处磨出较长沟痕,这是由于表面氧化皮或上道工序留下的硬化层等原因造成的。
它亦称边界磨损,磨损量用VN表示。
B 区在C、N区间较均匀的磨损区。
磨损量用VB表示。
其中局部出现的划痕、深沟的高度用VBmax表示。
(2)前刀面磨损切屑在前刀面上流出时,由于磨擦、高温和高压作用,使前刀面上近切削刃处磨出月牙洼。
前刀面的磨损量用月牙洼深度KT表示,月牙洼的宽度为KB。
(3)前、后刀面同时磨损经切削后刀具上同时出现前刀面和后刀面磨损。
这是在切削塑性金属时,采用大于中等切削速度和中等进给量时较常出现的磨损形式。
在生产中,较常见到的是后刀面磨损,尤其是在切削脆性金属和每齿进给量fz较小的情况下;月牙洼磨损通常是在高速、大进给(fz>0.5mm)切削塑性金属时产生的。
2、非正常磨损非正常磨损是指刀具在切削过程中突然或过早产生损坏现象。
其中有:(1)破损在切削刃或刀面上产生裂纹、崩刃或碎裂。
(2)卷刃切削时在高温作用下,使切削刃或刀面产生塌陷或隆起的塑性变形现象。
(二)刀刃磨损的过程正常磨损情况下,刀具磨损量随切削时间增多而逐渐扩大。
典型磨损过程如图3所示,图中大致分为三个阶段:初期磨损阶段(I段)在开始切削的短时间内,磨损较快。
这是由于刀具表面粗糙不平或表层组织不耐磨引起的;正常磨损阶段(Ⅱ段)随着切削时间增长,磨损量以均匀的速度加工。
这是由于刀具表面磨平后,接触面增大,压强减小所致。
AB线段基本上呈直线,单位时间内磨损量称为磨损强度,该磨损强度近似为常数。
急剧磨损阶段(Ⅲ段)磨损量达到一定数值后,磨损急剧加速、继而刀具损坏。
这是由于切削时间过长,磨损严重,切削温度剧增,刀具强度、硬度降低所致。
刀具磨损过程曲线是衡量刀具切削性能好坏的重要依据。
在使用刀具时,应该控制刀具在产生急剧磨损前必须重磨或更换新刀刃。
这时刀具的磨损量称为磨损限度或磨钝标准。
由于后刀面磨损是常见的,且易于控制和测量,因此,规定后刀面上均匀磨损区的宽度VB 值作为刀具的磨钝标准。
在ISO标准中,供作研究用推荐的高速钢和硬质合金刀具磨钝标准为:(1)在后刀面B区内均匀磨损VB=0.3mm;(2)在后刀面B区内非均匀磨损VBmax=0.6mm;(3)月牙洼深度标准KT=0.06+0.3f,(f为mm/r);(4)精加工时根据需达到的表面粗糙度等级确定。
实际生产中磨钝标准应根据加工要求制订:粗加工磨钝标准是根据能使刀具切削时间与可磨或可用次数的乘积最长为原则确定的,从而能充分发挥刀具的切削性能,该标准亦称为经济磨损限度;精加工磨钝标准是在保证零件加工精度和表面粗糙度条件下制订的,因此VB值较小。
该标准亦称工艺磨损限度。
刀具磨损十步曲:(1)开始切削不久,刀刃前角开始磨损(2)切削力增加,机械功率相应提升(3)工件精度开始难以控制(4)工件表面光洁度下降(5)工件边缘有披锋(6)工件温度提升(7)切屑温度高,颜色改变(8)切屑外形不规则,切屑边缘有披锋(9)刀具切削时发出不寻常声响(10)工件机械不停跳动(三)刀具磨损原因切削时刀具的磨损是在高温高压条件下产生的。
因此,形成刀具磨损的原因就非常复杂,它涉及机械、物理、化学和金相等的作用。
现将其中主要的原因简述如下:1、磨粒磨损(Abrasive Wear)在切削过程中,刀具上经常被一些硬质点刻划出深浅不一的沟痕。
这主要由于“磨粒”的切削作用造成的。
构成这些“磨粒”硬质点的来源,是切屑底层和切削表面材料中含有氧化物(SiO、Al2O3等)、碳化物(Fe 3C、TiC等)和氮化物(Si2N4、Al N等)的硬元素。
此外,还有粘附着积屑瘤的碎片和锻造表皮和铸件表面上残留的夹砂。
磨粒磨损对高速钢作用较明显。
因为高速钢在高温时的硬度较有些硬质点(SiO、Al2O3、TiC、Si2N4、)低,耐磨性差。
此外,硬质合金中粘结的钴也易被硬质点磨损。
为此,在生产中常采用细晶粒碳化物的硬质合金或减少钴的含量来提高抗磨损能力。
当两个颊互相磨擦时,被切削物表面较硬的粒子就会向刀刃表面磨擦(磨削一样),令刀刃刃口磨损,所以刀刃材质越硬,抗磨损的能力越强。
2、粘结磨损(Adhesion Wear)切屑与前刀面、加工表面与后刀面之间在正压力和温度作用下,接触面间吸附膜被挤破,形成了新鲜表面接触,当接触面间达到原子间距离时就产生粘结。
粘结磨损就是由于接触面滑动时在粘结处产生剪切破坏造成的。
通常剪切破坏在较软金属一方,但刀面受到磨擦、压力和温度连续作用下使强度降低,也会破坏。
图为两种材料粘结情况。
此外,当前刀面上粘结的积屑瘤脱落后,带走了刀具材料也形成粘结磨损。
粘结磨损的程度与压力、温度和材料间亲合程度有关。
例如在低速切削时,由于切削温度低,故粘结是在正压力下接触点处产生塑性变动所致,亦称为冷焊;在中速时由于切削温度较高,促使材料软化和分子间的热运动,更易造成粘结。
用YT类硬质合金加工钛合金或含钛不锈钢,在高温作用中钛元素之间的亲合作用,也会产生粘结磨损。
所以,低、中速切削时,粘结磨损是硬质合金刀具的主要磨损原因。
3、扩散磨损(Diffusion Wear )切削时在高温作用下,接触面间分子活动能量在,造成了合金元素相互扩散置换,使刀具材料机械性能降低,若再经磨擦作用,刀具容易被磨损。
扩散磨损是一种化学性质的磨损。
如图所示,以钨钴硬质合金与钢之间扩散过程为例,图1为切屑与刀面上元素分布情况。
由于温度的作用,如图2所示,使硬质合金中W、Co和C原子向钢中扩散,然后被切屑和加工表面带走。
硬质合金中失去W后,在结晶组织中出现空穴。
此外,失去了Co后削弱了粘结强度。
与此同时,材料中Fe原子向刀具中扩散,使刀面表层形成了新的材质。